Comparing Industrial Adhesive Solutions: Epoxies vs. Acrylics vs. Silicones
Comparing Industrial Adhesive Solutions: Epoxies vs. Acrylics vs. Silicones
Industrial adhesives are indispensable across numerous sectors, serving as a foundational element for a myriad of applications. These adhesives are meticulously engineered to endure the rigorous demands of industrial settings, guaranteeing robust and enduring bonds among diverse materials. The selection of an appropriate adhesive solution is paramount to achieving optimal performance and durability in the intended application.
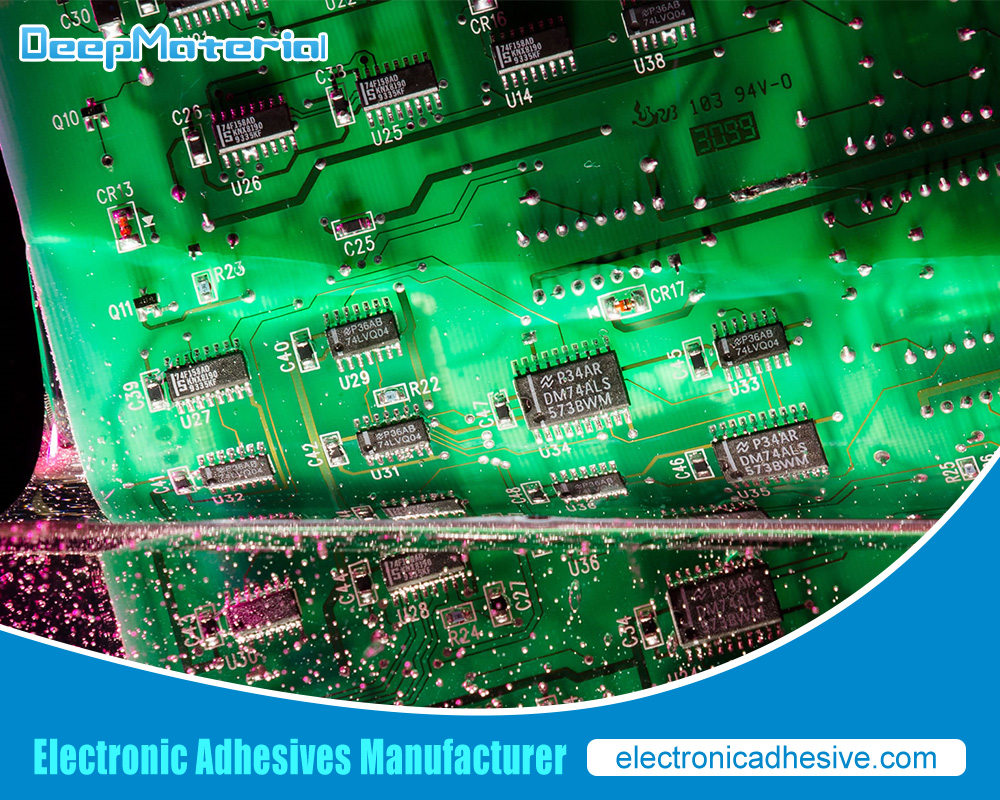
Exploring the Attributes and Uses of Epoxies
Epoxies stand out as a premier category of industrial adhesives, distinguished by their remarkable strength and resilience. Comprising two primary components, the resin and the hardener, epoxies initiate a chemical reaction upon mixing, culminating in an exceedingly strong bond. Their superior adhesion capabilities facilitate effective bonding with an array of materials, including metals, plastics, ceramics, and composites.
The resilience of epoxies against heat, chemicals, and moisture positions them as an optimal choice for scenarios demanding high durability and reliability. Their application spans various industries such as aerospace, automotive, construction, and electronics. For instance, in the aerospace industry, epoxies are instrumental in bonding composite materials, yielding structures that are both lightweight and capable of withstanding the extreme conditions of flight.
Within the automotive sector, epoxies are utilized to bond metal components, producing robust and durable parts capable of enduring the rigors of driving. Overall, epoxies are a critical component in numerous industrial processes, thanks to their exceptional strength, durability, and adaptability. They provide a dependable bonding solution for a wide spectrum of materials in applications where superior performance is mandatory.
Acrylics in Industrial Adhesives: Advantages and Limitations
Acrylic adhesives have garnered widespread utilization in industrial arenas, attributable to their adaptability and user-friendly nature. They are celebrated for their rapid curing capabilities, facilitating swift and efficient material bonding. These adhesives demonstrate a commendable capacity to adhere to a diverse array of materials, encompassing metals, plastics, glass, and wood. Consequently, acrylic adhesives have emerged as a favored option across myriad applications, ranging from automotive manufacturing to construction endeavors.
A prominent advantage of acrylic adhesives lies in their outstanding resistance to impact, vibration, and the test of time, rendering them particularly suitable for scenarios demanding flexibility and endurance. Such applications include the aerospace sector and the fabrication of electronic apparatus. Nonetheless, it is imperative to recognize that acrylic adhesives may exhibit limited resistance to elevated temperatures and aggressive chemical environments when compared to alternative adhesive formulations.
Despite these constraints, acrylic adhesives continue to be embraced for numerous industrial applications owing to their inherent versatility and straightforward application process. They represent a dependable and efficacious bonding solution for an extensive spectrum of materials, affirming their indispensability across various industrial domains.
Silicones: A Versatile Solution for Industrial Bonding
Silicone adhesives have ascended in popularity within the industrial adhesive landscape, distinguished by their exceptional attributes. Distinct from other adhesive options, silicones excel in temperature resilience, pliability, and electrical insulating capacities, which endow them with remarkable versatility applicable across a broad spectrum of industrial uses.
A salient feature of silicones is their exceptional tolerance to extreme temperature variations, ranging from -60°C to 300°C. This attribute positions them as an exemplary choice for sectors such as automotive, aerospace, and electronics, where exposure to high thermal conditions is prevalent. Moreover, silicones exhibit commendable resistance to moisture, ultraviolet radiation, and chemical exposures, enhancing their suitability for applications in outdoor settings and environments subject to harsh conditions.
Comparing Epoxies, Acrylics, and Silicones: Key Differences
Epoxies, acrylics, and silicones represent three fundamentally diverse classes of materials, each distinguished by its unique chemical makeup, properties, and utility across various applications. Epoxies are celebrated for their unparalleled strength and resilience, rendering them exceptionally suitable for scenarios demanding significant load-bearing capabilities.
They find widespread application across the construction, automotive, and aerospace sectors for bonding and sealing tasks. Moreover, their outstanding electrical insulation attributes make them a preferred choice in the fabrication of electronic components.
Acrylics are characterized by their rapid curing times and commendable flexibility, positioning them as an optimal solution for projects necessitating swift assembly or adaptability. They play a pivotal role in the production of plastic merchandise, including toys, signage, and display items. The automotive industry leverages acrylics for crafting headlight lenses and taillight covers, benefiting from their superior optical clarity.
Silicones stand out for their exceptional resistance to temperature fluctuations and their electrical insulation capabilities, making them ideal for applications that encounter extreme temperatures or necessitate electrical safeguarding. The manufacturing of electronic components, such as computer chips and circuit boards, often employs silicones due to these properties. Furthermore, their remarkable weather resistance is advantageous in the construction sector for sealing windows and doors.
In summary, epoxies, acrylics, and silicones each possess distinct properties that tailor them to specific applications. A thorough understanding of the differences among these materials is crucial for selecting the most appropriate material for a given application.
Strength and Durability: Selecting the Optimal Adhesive Solution
For strength and durability, epoxies frequently emerge as the favored option. They deliver superior bonding prowess and are adept at handling substantial loads and stress, making them an ideal candidate for applications requiring robust support. Acrylics contribute respectable strength and durability as well, yet they might not reach the same level of sturdiness provided by epoxies in some scenarios. Conversely, silicones present moderate strength but standout remarkably for their flexibility and capability to endure extreme temperature variations.
Ease of Use: Analyzing the Application and Curing Process
The simplicity of utilizing an adhesive solution is significantly influenced by the particular demands of the application at hand. Epoxies generally necessitate accurate blending of the resin and hardener elements and are characterized by more extended curing periods.
Conversely, acrylics provide the advantage of rapid curing times and straightforward application procedures. Similarly, silicones are recognized for their ease of application and swift curing rates, rendering them an excellent choice for projects demanding speedy assembly or prompt repairs.
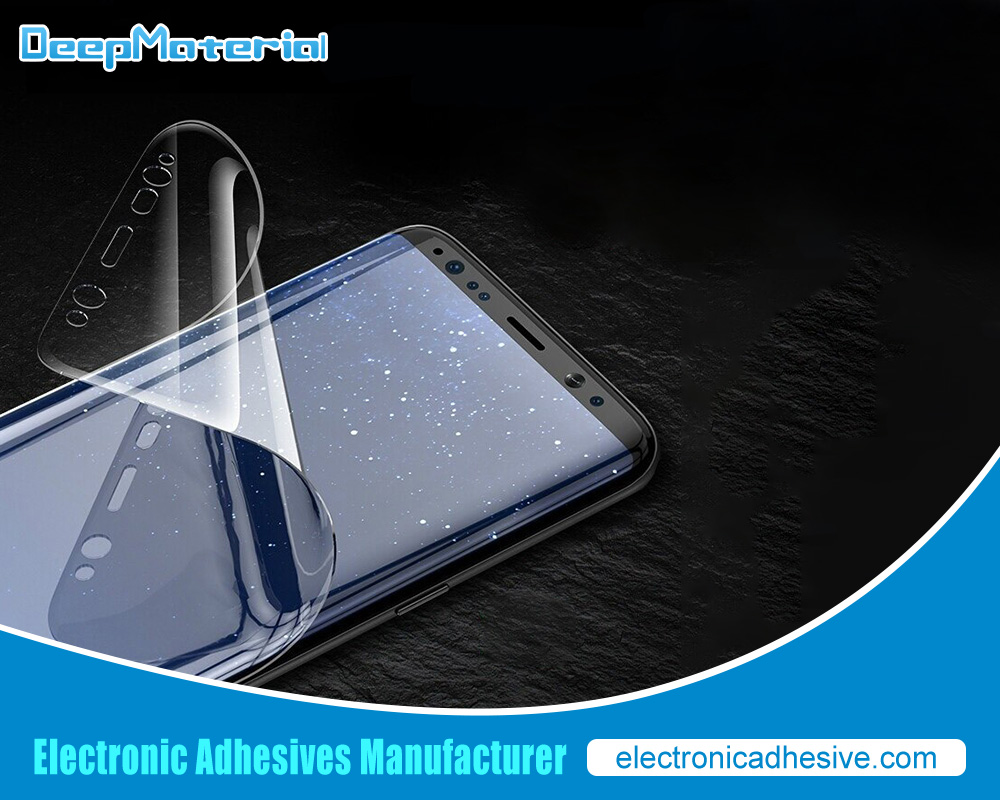
Conclusion
In sum, gaining a deep understanding of the characteristics and uses of epoxies, acrylics, and silicones is vital in identifying the most suitable industrial adhesive solution for your application. Through a comparative evaluation of their distinct advantages in terms of strength and durability, temperature and chemical resistance, ease of application, and cost-efficiency, you can make a knowledgeable decision on the adhesive that presents the greatest value for your specific needs.
For more about comparing industrial adhesive solutions: epoxies vs. acrylics vs. silicones, you can pay a visit to DeepMaterial at https://www.electronicadhesive.com/ for more info.