Adhesives for Impregnating Application
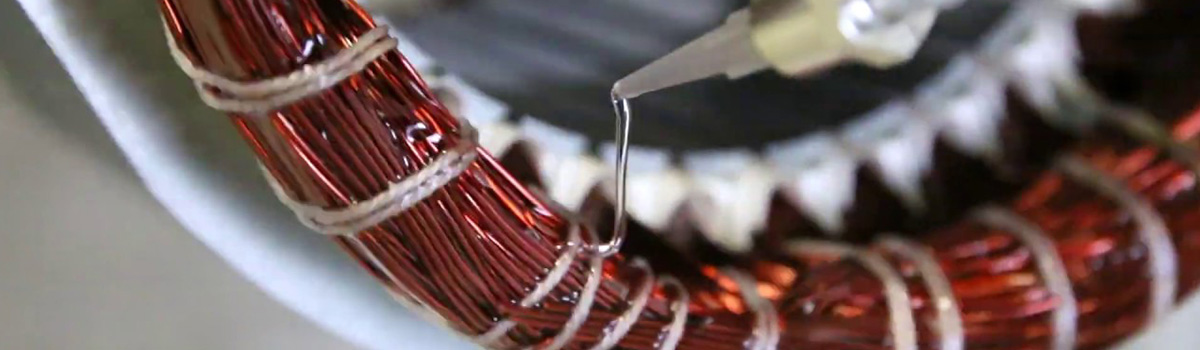
Deepmaterial offers porosity-sealing products and services to effectively seal cast-metal parts and electronic components against leakage.
From automotive to electronics to construction equipment to communications systems, Deepmaterial has developed cost effective solutions for sealing macroporosity and microporosity for metals and other materials. These low viscosity systems cure at elevated temperatures to a tough, strong chemical resistant thermoset plastic.
Advantages of Deepmaterial Impregnation Resins
Deepmaterial impregnation compounds feature long-term storage stability, exceptional chemical/moisture resistance and the ability to withstand elevated temperatures. Additionally, they are fast curing, 100% reactive and easy to process.
A wide range of high quality products have been developed to offer the most reliable sealing solutions and meet specific customer specifications in metal casting, powdered metal parts, electronic/electrical components, ceramic and plastic composite applications. These impregnants have proven attractive in extending design options, accelerating productivity, lowering warranty expenses and shortening testing procedures. In many cases they have successfully outperformed competitive chemistries in difficult part configurations and have prevented part failure from fluids/gases while filling voids between two dissimilar surfaces.
Find out more about epoxy systems for:
*Filament winding
*Vacuum impregnation
*Prepregs
Epoxies for Filament Winding
Deepmaterial offers a broad range of epoxy resin systems for the fabrication of filament wound composite parts. Oven/autoclave curing epoxy coated/impregnated reinforced fibers including glass, carbon, aramid, boron are uniformly, precisely wrapped around a cylindrical, spherical, conical rotating mandrel automatically to produce composite structures. Thin walled, light weight, high strength composite tubes, pressure vessels, tanks, cylinders, pipes exhibit superior dimensional stability, dielectric properties and corrosion resistance. They are employed for filter housings, bushings, drive shafts, high voltage insulators, rolls, wastewater treatment components and pipelines.
Formulating epoxies with special properties
Available in a variety of viscosities, Deepmaterial toughened, resilient, 100% solid two component epoxy systems for filament winding have convenient mix ratios, good wetting characteristics and cure rapidly at moderate temperatures. . In order to achieve consistent, repeatable results proper processing techniques should be strictly followed. Winding angle/tension, following proper cure schedules are essential to assure optimum performance. Special systems are engineered to reduce dripping, waste, lower labor costs. Custom products offer outstanding tensile, impact, compressive, flexural strength and protect against weather, fire, wear. Select grades have high glass transition temperatures, low thermal coefficients of expansion and withstand thermal shock. Specialty cryogenically serviceable, low outgassing grade epoxies are also available for aerospace applications.
Filament Winding Hollow Tube Structures
Epoxy resin impregnated rovings or monofilaments such as carbon, E-glass, S-glass, aramid are wound around a mandrel to fabricate standard/custom composite hollow tube structures. Deepmaterial oven curing epoxy resin systems offer consistency, repeatability, cost effectiveness for usage in hoop, helical, polar winding patterns. They accommodate high fiber to resins ratio and allow precise fiber orientation at different rotational mandrel speeds. Filament wound epoxy matrix tubing in a variety of diameters/wall thicknesses protect against surface impacts, corrosion, fatigue, temperature extremes, moisture, internal pressure loads. They also feature high strength to weight ratios, dimensional stability, wear/chemical resistance, superior dielectric properties, ready machinability.
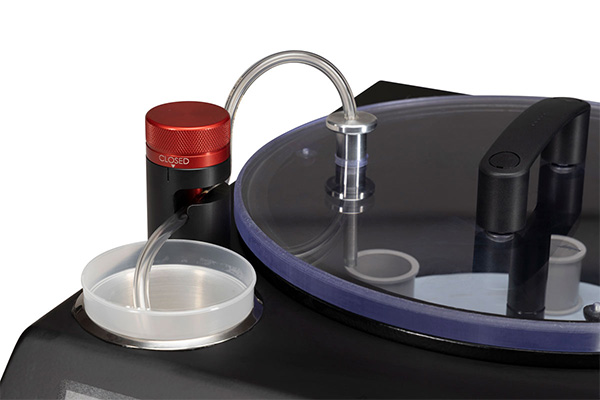
Typical Applications for Epoxy Matrix Tubing
*Bearings and collars
*Pressure tubing
*Bushings
*Impeder tubes
*Structural tubing
Wet winding process plays an important role in the manufacturing of tubing providing improved durability, flexural, tensile, compressive circumferential strength enabling usage in the electrical, aerospace, marine, defense, mining, oil/chemical processing, transportation industries. Unique Deepmaterial formulations are available for low CTE, high modulus cryogenic and aggressive tubing usage.
Epoxy Systems for Vacuum Impregnation
Single part, no mix, solvent free epoxy impregnation compounds are used to seal porosity in metals and non-metals. Compounds offer excellent void filling capability, low shrinkage upon cure and cause no dimensional change to parts being sealed. Powdered metal parts and metal castings including aluminum, zinc, cast iron, steel and magnesium can effectively become pressure tight following vacuum impregnation. This reduces scraps, does not effect appearance, lowers warranty costs and improves profitability. Powdered metal components also will have improved machinability. Additionally, ceramics and plastics can also be protected against porosity.
Our epoxy impregnants seal against:
*Air
*Water
*Oils
*Solvents
*Cleaners
*Coolants
*Lubricants and much more
Typical applications include:
*Valves
*Fuel system components
*Microwave systems
*Meters
*Graphite plates
*Engine blocks
*Compressor parts
*Lens housings
They are also used for:
*High temperature coils
*Termination stacks for brushless motors
*Electronic connectors
*Thermistors
*Sensors
*Wire harnesses
*Ferrites
After impregnation dielectric properties are frequently enhanced.
Deepmaterial impregnants are known for their unmatched reliability. They are available for purchase in a range of thicknesses and hardnesses.
To achieve the most desirable results considerations should be given to type of porosity material, size, geometry, sealing rate in choosing the proper impregnation process.
Prepregs
Deepmateriale epoxy systems are pre-impregnated on a reinforcing fabric such as carbon, glass, aramid, hybrid fibers, layered on a mold and cured with heat/pressure for repeatable, uniform laminations. Prepregs offer many advantages over other processes for composite fabrication. Easy to use thermoset epoxy prepreg materials liquidify at low temperatures, fully cure at modest temperatures, speed cycle times, reduce waste and improve aesthetics. Prepregs are often cured using a press or vacuum bagging. Ramp up/ramp down temperatures, type of fiber, fiber orientation, resin, resin content are crucial to achieving the best results for specific end use requirements. Durable, stiff, light weight, fatigue resistant, water impervious prepreg advanced composite components offer exceptional performance/reliability for energy, industrial machinery, sporting goods, defense, aerospace, marine manufacturing companies. Select Deepmaterial formulations withstand solvents/corrosives, wear exposure and feature toughness and high Tg properties.