Lens Bonding Adhesive
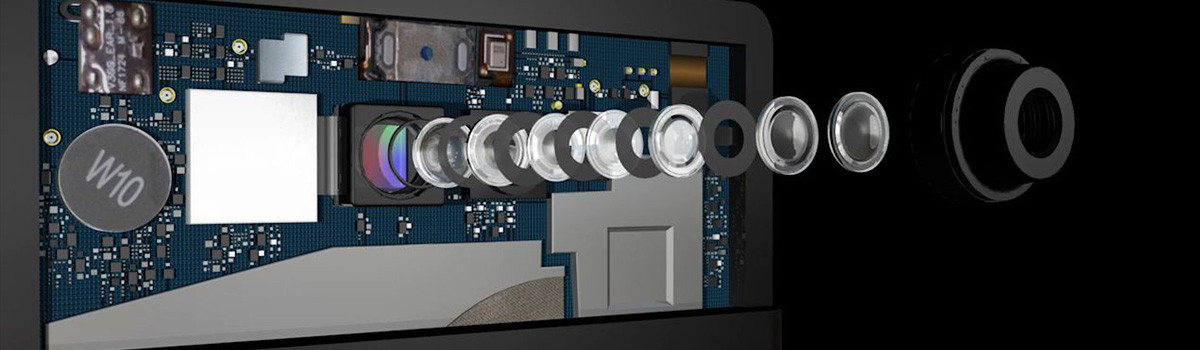
Lens bonding adhesive is a vital component in the field of optics, allowing for the joining of lenses or other optical components to create complex assemblies. This process involves the use of a specialized adhesive that offers high optical clarity, durability, and resistance to environmental factors such as moisture, chemicals, and UV radiation.
However, with the wide range of lens bonding adhesives available, it can be challenging to choose the right one for a specific application.
This article provides an overview of lens bonding adhesive, including its types, factors to consider when choosing, techniques for applying, advantages, and applications in various industries. It also explores the challenges of using lens bonding adhesive and the prospects of this technology in the future.
What is Lens Bonding Adhesive?
Lens bonding adhesive is a type of adhesive specifically designed for bonding lenses to frames in eyeglasses and other optical applications. The adhesive is typically a two-part epoxy that is applied to the frame or lens surface, and then cured to form a strong and durable bond.
The adhesive is formulated to be optically clear and resistant to heat, moisture, and impact, to ensure that the bond remains secure over time. Lens bonding adhesive is used by optical professionals and eyewear manufacturers to create high-quality, long-lasting eyeglasses, sunglasses, and other optical devices.
Types of Lens Bonding Adhesives
There are several types of lens bonding adhesives available in the market, including:
- Epoxy adhesives: These are the most commonly used lens bonding adhesives. They are two-part adhesives that require mixing before use. Epoxy adhesives offer excellent bonding strength, durability, and resistance to heat and moisture.
- Cyanoacrylate adhesives: Also known as superglue, these adhesives are quick-setting and offer strong bonding strength. However, they are not recommended for bonding lenses to frames as they may cause discoloration and can be brittle.
- UV-curing adhesives: These adhesives require exposure to UV light to cure and form a bond. They offer fast bonding and curing times and are suitable for bonding lenses to frames made of plastic or metal.
- Acrylic adhesives: These adhesives are commonly used in the medical industry for bonding medical devices. They offer excellent bonding strength and are resistant to heat, chemicals, and moisture.
The choice of adhesive depends on the type of lens material, the frame material, and the application requirements. It is essential to consult with an optical professional to determine the appropriate adhesive for the specific application.
Acrylic Lens Bonding Adhesive
Acrylic lens bonding adhesives are specialized for bonding acrylic (polymethyl methacrylate or PMMA) lenses. These adhesives typically have high transparency and excellent adhesion to PMMA, making them ideal for optical devices, medical equipment, and signage applications.
Several types of acrylic lens bonding adhesives are available on the market, including two-part epoxy adhesives, UV-curing adhesives, and solvent-based adhesives. Each class has advantages and disadvantages, and the choice of adhesive will depend on the specific application and performance requirements.
Two-part epoxy adhesives are often used in applications that require high strength and durability, and they typically have a longer cure time and require mixing before use. On the other hand, UV-curing adhesives cure quickly under UV light and are ideal for applications that require rapid bonding. Solvent-based adhesives are often used in applications that require low viscosity and easy application.
It’s important to note that when bonding acrylic lenses, proper surface preparation is essential to ensure a strong bond. The surfaces to be bonded should be clean, dry, and free of any contaminants that could interfere with the bonding process. Additionally, the adhesive should be applied in a thin, even layer and allowed to fully cure before any stress is applied to the bond.
UV Curable Lens Bonding Adhesive
UV curable lens bonding adhesive is a type of adhesive that is used to bond lenses to various surfaces. This adhesive cures quickly under UV light and forms a strong, durable bond between the lens and the surface it is being bonded to.
These adhesives are often used to manufacture eyeglasses, contact lenses, and camera lenses, as they provide a reliable and cost-effective way to bond these components together. They are also used in the automotive industry for bonding windshields and other glass components to the vehicle’s body.
UV curable lens bonding adhesives typically contain a mixture of acrylic monomers, photoinitiators, and other additives that create a strong bond. When exposed to UV light, the photoinitiators in the adhesive begin a polymerization reaction, causing the monomers to cross-link and form a solid, durable sealant.
One of the benefits of using UV-curable lens bonding adhesives is that they cure quickly, often in a matter of seconds, which can help to speed up production times. They are also highly resistant to heat, chemicals, and UV light, making them ideal for outdoor and high-temperature outdoor applications.
Overall, UV-curable lens bonding adhesives offer a reliable and efficient way to bond lenses and other components together, providing a robust and durable bond that can withstand a variety of environmental factors.
Epoxy Lens Bonding Adhesive
Epoxy lens bonding adhesive is a type of adhesive that is specifically designed to bond lenses to other materials. It is typically made of a two-part epoxy resin mixed together just before use. The adhesive is then applied to the lens and the material it is bonded to and allowed to cure.
One of the main advantages of epoxy lens bonding adhesive is its strength and durability. Once cured, the adhesive creates a strong and permanent bond between the lens and the material it is being bonded to. This makes it ideal for use in applications where the lens is subject to high stress or requires a long-lasting bond.
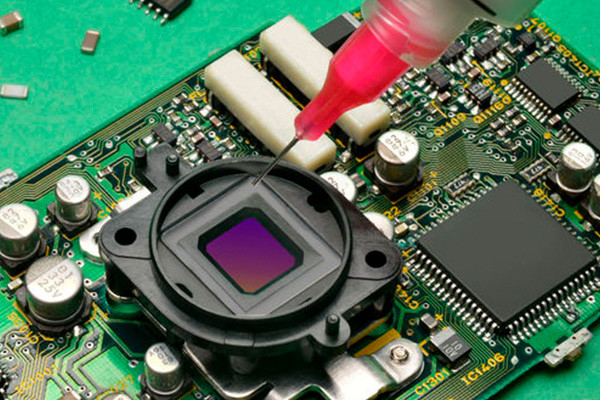
In addition to its strength, epoxy lens bonding adhesive has good optical clarity, essential when bonding lenses. It is also resistant to yellowing and other forms of discoloration over time, which helps maintain the lens’s transparency.
When using epoxy lens bonding adhesive, following the manufacturer’s instructions is essential. This will ensure the adhesive is mixed and applied correctly and that the bond is solid and durable. It is also necessary to use the adhesive in a well-ventilated area, as some types of epoxy can release fumes that can be harmful if inhaled.
Silicone Lens Bonding Adhesive
Silicone lens bonding adhesive is specifically designed to bond lenses made of various materials, such as glass, plastic, and metal, to a variety of substrates, including other lenses, prisms, mirrors, and optical fibers.
Their excellent optical clarity, low outgassing, and high resistance to temperature, moisture, and chemicals characterize silicone lens bonding adhesives. They are typically one-part, room-temperature-curing adhesives that offer a fast cure time and a strong bond.
Silicone lens bonding adhesives are widespread in the optical industry, where they manufacture a wide range of optical components such as microscopes, telescopes, cameras, and sensors. They are also used in medical devices, electronics, and aerospace applications.
Choosing the Right Lens Bonding Adhesive
Choosing the suitable lens bonding adhesive depends on various factors, such as the type of lenses being bonded, the materials being used, and the environment in which they will be used. Here are some key considerations:
- Compatibility with lens materials: The adhesive should be compatible to ensure a strong bond without damaging the lenses.
- Bond strength: The adhesive should provide a solid, durable bond that can withstand the use stresses.
- Cure time: The cure time should be suitable for the production schedule and requirements of the application.
- Resistance to environmental factors: The adhesive should be resistant to factors such as moisture, temperature changes, and chemicals, depending on the intended use of the lenses.
- Transparency: For optical applications, the adhesive should be transparent to avoid affecting the optical properties of the lenses.
- Ease of use: The adhesive should be easy to use, with appropriate viscosity and application methods.
Standard lens bonding adhesives include cyanoacrylate adhesives, UV-curable adhesives, and two-part epoxies. It is essential to consult with adhesive manufacturers and technical experts to select the suitable adhesive for your specific application.
Factors to Consider When Choosing Lens Bonding Adhesive
Choosing the suitable lens bonding adhesive is crucial to ensure that the lenses are firmly attached to the frame and provide optimal vision. Here are some factors to consider when choosing a lens-bonding adhesive:
- Adhesion strength: The adhesive should have strong adhesion to the lens and the frame to ensure a secure bond.
- Compatibility: The adhesive should be compatible with the lens and frame materials. Different bonds work better with other materials, so choosing an adhesive specifically designed for the materials being used is essential.
- Curing time: The adhesive’s curing time should be considered, as some adhesives may take longer to cure than others. A longer curing time may be necessary for specific materials or applications.
- Viscosity: The viscosity of the adhesive should be appropriate for the application method and the size of the bond area. A low-viscosity adhesive may be better for small bond areas, while a higher-viscosity adhesive may be better for larger bond areas.
- UV resistance: The adhesive should have good UV resistance to prevent yellowing and degradation of the bond over time.
- Water resistance: The adhesive should be water-resistant to prevent bond degradation when exposed to moisture.
- Temperature resistance: The adhesive should withstand the temperatures that the lens and frame may be exposed to during everyday use.
- Ease of use: The adhesive should be easy to apply and work with and should not require special tools or equipment.
- Safety: The adhesive should be safe to use and handle and should not contain any harmful chemicals or substances.
Considering these factors, you can choose a suitable lens-bonding adhesive that will provide a solid and durable bond between the lens and the frame, ensuring optimal vision and comfort for the wearer.
Surface Preparation for Lens Bonding Adhesive
Surface preparation is essential for achieving a strong and durable bond when bonding lenses using adhesives. The following are some common steps for surface preparation:
- Cleaning: Ensure that the surface of the lens is free of any dirt, dust, grease, or oils that may interfere with bonding. Clean the surface of the lens with a lint-free cloth or wipe using a solvent such as isopropyl alcohol, acetone, or a lens cleaner.
- Abrading: Abrade the surface of the lens using a fine abrasive material such as sandpaper or a diamond-coated tool. This step creates micro-roughness on the lens surface, which enhances the adhesion of the adhesive.
- Priming: Apply a primer to the lens’s surface to improve the adhesive’s adhesion. The primer is typically a solvent-based solution that is applied to the surface of the lens and allowed to dry before applying the adhesive.
- Masking: Mask any areas on the lens that do not require bonding to prevent the adhesive from spreading to unwanted areas.
- Mixing and Applying Adhesive: Follow the adhesive manufacturer’s instructions for mixing and applying the adhesive. Apply a thin and even adhesive layer to the lens surface, avoiding any bubbles or excess adhesive.
- Curing: Cure the adhesive according to the manufacturer’s instructions. The curing process may involve exposing the adhesive to heat, light, or a combination.
By following these steps, you can ensure that the surface of the lens is correctly prepared for bonding, resulting in a solid and durable bond.
Surface Cleaning for Lens Bonding Adhesive
When bonding lenses with adhesive, surface cleaning is crucial to ensure a strong bond. Here are some steps that can be taken to clean the lens surface before bonding:
- Start by removing loose debris or particles on the lens surface using a soft-bristled brush or compressed air.
- Use a lint-free cloth or a lens-cleaning solution to remove any dirt, oil, or other contaminants from the surface. Using a solution specifically designed for cleaning lenses is essential, as some cleaning solutions may leave a residue that could affect the bonding process.
- Wipe the lens surface with a clean, lint-free cloth to remove any remaining moisture or cleaning solution. Avoid using paper towels or tissues as they may leave fibers on the surface.
- If necessary, use a solvent such as isopropyl alcohol to remove any stubborn contaminants or residues. However, follow the manufacturer’s instructions for using the solvent and ensure that the solvent does not damage the lens material.
- Allow the lens surface to dry completely before applying the adhesive. Any moisture or residue left on the surface can affect the strength of the bond.
It is important to note that the surface cleaning process may vary depending on the lens material type and adhesive used. Always refer to the manufacturer’s instructions and follow the recommended surface preparation process for the bonded materials.
Surface Activation for Lens Bonding Adhesive
Surface activation is a process used to prepare surfaces for bonding by increasing their surface energy and improving the adhesive’s adhesion. Regarding lens bonding adhesives, surface activation can be significant as lenses are typically made of materials that are inherently difficult to bond, such as glass or certain plastics.
One standard method of surface activation for lens bonding adhesives is plasma treatment. This involves exposing the surface of the lens to a low-pressure plasma, which causes the surface molecules to become highly reactive. This increased reactivity allows the adhesive to form strong bonds with the lens surface.
Another method of surface activation is chemical treatment. Applying a chemical solution to the lens surface modifies the surface chemistry and increases the surface energy. Chemical treatments can be particular to the lens material being used and can be customized for optimal adhesion.
In addition to surface activation, it’s essential to ensure that the lens and adhesive are compatible. This can involve selecting a bond with the appropriate properties, such as flexibility or thermal stability, for the specific lens material used. The bonding process should also be carefully controlled to ensure optimal adhesion and minimize the risk of delamination or other bonding failures.

Curing and Drying of Lens Bonding Adhesive
The curing and drying process of lens bonding adhesive is critical in ensuring that the adhesive bond is strong and durable. Here are the general steps involved in the curing and drying process of lens bonding adhesive:
- Apply the adhesive: First, apply the adhesive to the lens surface that needs to be bonded. Ensure the surface is clean and free from dust, oil, and other contaminants.
- Align and position: Align the lens properly and position it in place. Apply slight pressure to ensure that the adhesive spreads evenly over the surface.
- Curing: The curing process of the adhesive is usually done at room temperature, but some bonds may require elevated temperatures or UV light exposure to cure properly. The curing time and temperature will vary depending on the type of adhesive used.
- Drying: After the adhesive is cured, allowing it to dry completely before handling the lens is essential. Drying time will depend on the adhesive, but it typically takes a few hours.
- Post-curing: Some adhesives may require post-curing to improve their strength and durability. Post-curing is done by exposing the adhesive to elevated temperatures for a specific period.
It is essential to follow the manufacturer’s instructions for the adhesive to ensure that the curing and drying process is done correctly. Proper curing and drying will ensure the adhesive bond is strong, durable, and long-lasting.
Techniques for Applying Lens Bonding Adhesive
Lens bonding adhesive is commonly used to attach lenses to various surfaces, such as eyeglass frames, cameras, and other optical devices. Here are some techniques for applying lens bonding adhesive:
- Clean the surface: Before applying the adhesive, clean the surface thoroughly using a lint-free cloth and a cleaning solution designed for lenses or optics. This will ensure that no dirt or residue on the surface could interfere with the bond.
- Apply the adhesive: Apply a small amount of adhesive to the surface using a syringe or dispenser. Be careful not to apply too much, as this can cause the adhesive to spread and potentially create air bubbles or gaps.
- Position the lens: Carefully position it on the adhesive-coated surface, carefully aligning it properly. Use a lens holder or other tool to hold the lens in place while the adhesive cures.
- Cure the adhesive: Allow the adhesive to cure according to the manufacturer’s instructions. This may involve applying heat or UV light to accelerate the curing process.
- Clean up: Once the adhesive has cured, clean up any excess adhesive using a solvent or scraper, not damaging the lens or surface.
- Test the bond: Finally, test the bond to ensure it is solid and secure. Apply gentle pressure to the lens to check for any movement or looseness.
Dispensing Techniques for Lens Bonding Adhesive
Lens bonding adhesive is used to bond two lenses to form a single, multi-focal lens. There are various dispensing techniques used for lens bonding adhesive, including:
- Manual Dispensing: In this technique, the adhesive is dispensed manually using a syringe or a dispensing gun. The operator controls the amount of adhesive dispensed and the location of the dispense using a foot pedal or a hand trigger.
- Automated Dispensing: This technique uses automated dispensing equipment that dispenses a precise amount of adhesive at a set location. This method is commonly used in high-volume production where consistency and accuracy are critical.
- Jetting Dispensing: This technique uses a jet valve to dispense a small amount of adhesive in a precise location. Jetting is commonly used when dispensing small amounts of adhesive, and accuracy is crucial.
- Film Dispensing: In this technique, the adhesive is dispensed as a continuous film, then placed between the two lenses. This method is commonly used in high-volume production and efficiently applies adhesive to a large surface area.
- Screen Printing Dispensing: This technique uses a screen printing process to apply a precise amount of adhesive in a specific pattern. This method commonly applies adhesive to a large surface area and requires a particular pattern.
The dispensing technique choice depends on the lens bonding adhesive type, the application requirements, and the production volume. Each dispensing technique has advantages and disadvantages; choosing the appropriate design that provides consistent and accurate results is essential.
Potting Techniques for Lens Bonding Adhesive
Potting techniques for lens bonding adhesive can vary depending on the specific adhesive used and the desired application. However, some general potting techniques that can be followed include:
- Surface preparation: Before potting the lens, it is essential to ensure the surface is clean and free of contaminants. The cover can be cleaned using a solvent or a cleaning agent and dried thoroughly.
- Mixing the adhesive: The adhesive should be mixed according to the manufacturer’s instructions. It is essential to incorporate the adhesive thoroughly to ensure it is properly activated and will cure correctly.
- Applying the adhesive: The adhesive should be applied to the surface of the lens in a controlled manner to ensure that it covers the entire surface evenly. This can be done using a dispensing system or a manual applicator.
- Potting the lens: Once the adhesive has been applied, it can be potted in the desired position in the mold or fixture. The adhesive should cure according to the manufacturer’s instructions before removing the lens from the mold.
- Post-curing: After potting the lens, it may be necessary to post-cure the adhesive to ensure that it reaches its full strength and durability. This can be done by exposing the lens to elevated temperatures for a specified period.
It is important to note that different adhesive formulations may require other potting techniques.
Lamination Techniques for Lens Bonding Adhesive
Lamination techniques for lens bonding adhesive involve using a specialized adhesive to bond two lenses together to create a single lens with enhanced optical properties. There are several techniques used in the industry, including:
- Vacuum Lamination: This technique involves placing the two lenses on top of each other and then applying vacuum pressure to eliminate air bubbles between the layers. The lenses are then cured with UV light.
- Pressure Lamination: This technique involves using a specialized laminating machine to apply pressure to the lenses and adhesive to create a strong bond. The device can apply precise pressure and temperature to ensure optimal bonding.
- Hot Melt Lamination: A thermoplastic adhesive is heated and applied to the lenses in this technique. The lenses are then placed under pressure to create a strong bond.
- Solvent Bonding: This technique involves using a solvent-based adhesive to dissolve the surface of the lenses, creating a chemical bond between the two layers.
The choice of lamination technique depends on the type of adhesive used, the type of lenses, and the intended application of the final product. It is essential to ensure that the adhesive used is compatible with the lenses to avoid any adverse reactions or damage to the lenses.
Advantages of Lens Bonding Adhesive
Lens bonding adhesive offers several advantages, including:
- Improved Optical Properties: Lens bonding adhesive allows two lenses to be bonded to create a single lens with enhanced optical properties. This can improve clarity, reduce distortion, and improve light transmission.
- Increased Durability: Bonding lenses with adhesive can improve their overall durability and resistance to scratches, impact, and other types of damage.
- Reduced Weight: By bonding two lenses together, it is possible to create a lighter lens with similar optical properties to a single, thicker lens.
- Customization: Lens bonding adhesive allows for customization of the optical properties of a lens by combining two different types of lenses. This can be useful for applications that require specific optical properties, such as camera lenses or medical devices.
- Cost-Effective: Lens bonding adhesive can be a cost-effective alternative to manufacturing a single, thicker lens with similar optical properties.
Overall, lens bonding adhesive offers several benefits for applications that require enhanced optical properties, improved durability, and customization options.
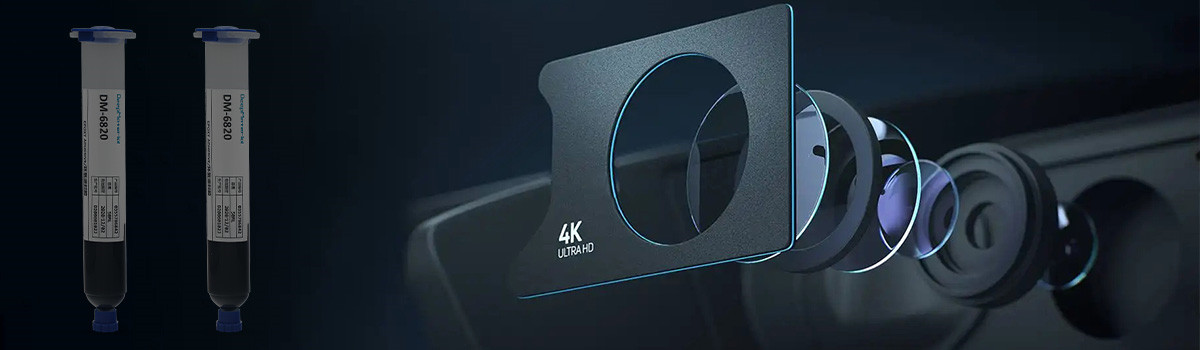
High Optical Clarity of Lens Bonding Adhesive
Lens bonding adhesives are designed to join lens components, ensuring they remain firmly in place. The high optical clarity is essential in lens bonding adhesives as it enables the lenses to transmit light without distortion or attenuation.
The optical clarity of a bonding adhesive depends on its refractive index, which measures how much the adhesive bends light. To achieve high optical clarity, the refractive index of the adhesive must be very close to that of the lens material. This minimizes the amount of light reflected at the interface between the adhesive and the lens, which maximizes the amount of light transmitted through the lens.
In addition to the refractive index, other factors that affect the optical clarity of lens-bonding adhesives include the adhesive’s viscosity, surface tension, and curing time. These properties can affect how the adhesive spreads and how it bonds to the lens surface, both of which can impact the clarity of the lens.
To ensure high optical clarity in lens bonding adhesives, manufacturers carefully control the formulation and processing of the adhesive. They also use specialized testing methods to measure the adhesive’s refractive index and other optical properties. This ensures that the adhesive meets the high standards for precision optical applications, such as camera lenses, microscope lenses, and laser optics.
Durability of Lens Bonding Adhesive
The durability of lens bonding adhesive depends on various factors, such as the type of adhesive used, the type of lens material, the conditions under which the lens is used, and the quality of the bonding process.
Generally, the lens bonding adhesive is designed to be solid and durable, withstand normal wear and tear, and provide a secure bond between the lens and the frame. However, over time, the adhesive may begin to degrade or break down due to exposure to heat, moisture, and other environmental factors.
The durability of the lens bonding adhesive can also be affected by factors such as exposure to chemicals, prolonged exposure to UV radiation, and improper storage. Additionally, if the bonding process is not done correctly, it can result in a weak bond that may break down over time.
To ensure the maximum durability of the lens bonding adhesive, it is essential to follow the manufacturer’s instructions for use and storage and to have the bonding process done by a trained professional. Proper care and maintenance of the lens and frame can also extend the life of the adhesive bond.
High Bond Strength of Lens Bonding Adhesive
The high bond strength of lens bonding adhesive is critical for ensuring that lenses remain securely attached to their respective frames or other devices. This bond strength is typically achieved through specialized adhesive materials explicitly designed for bonding lenses to structures or other components.
Selecting an adhesive capable of creating a solid bond between the lens and the frame or other components is essential to achieve high bond strength. This typically requires the use of sealants formulated explicitly for bonding to the materials used in the lens and structure, as well as those capable of providing strong adhesion even in the presence of moisture or other environmental factors.
Factors that can impact the bond strength of lens bonding adhesive include the lens material used, the frame material used, the surface preparation of both materials and the curing process used for the adhesive. By carefully selecting the suitable adhesive and optimizing the bonding process, it is possible to achieve a high bond strength that will ensure that lenses remain securely attached to their frames or other components.
Resistance to Moisture and Chemicals of Lens Bonding Adhesive
The resistance of lens bonding adhesive to moisture and chemicals depends on the specific adhesive material used. Generally, adhesives designed explicitly for bonding lenses are formulated to resist water and certain chemicals.
In particular, cyanoacrylate-based adhesives, commonly used for lens bonding, have good moisture resistance but can be sensitive to certain chemicals, such as solvents or acids. On the other hand, epoxy-based adhesives generally have better chemical resistance but may be less resistant to moisture.
It is essential to choose an adhesive designed explicitly for lens bonding and follow the manufacturer’s instructions for application and curing. It is also recommended to test the adhesive’s resistance to moisture and chemicals before use to ensure that it meets the intended application’s requirements.
UV Stability of Lens Bonding Adhesive
The UV stability of lens bonding adhesive refers to the adhesive’s ability to resist degradation or damage from exposure to ultraviolet (UV) radiation. UV stability is an essential property of lens bonding adhesive because the adhesives are often used in applications that expose them to UV light, such as in optical lenses.
The level of UV stability of lens bonding adhesive can vary depending on the specific type of adhesive used. Some adhesives are formulated to have excellent UV stability, while others may degrade over time when exposed to UV radiation. The UV stability of an adhesive is typically determined by the type and amount of UV absorbers or stabilizers added during the formulation process.
When selecting a lens bonding adhesive, it is essential to consider the level of UV stability required for the specific application. For example, adhesives used in outdoor lenses, such as sunglasses, must have high UV stability to ensure long-term durability and performance. Conversely, adhesives used in indoor lenses, such as prescription eyeglasses, may require less UV stability.
The UV stability of lens bonding adhesive is important when selecting an adhesive for optical applications. It is essential to choose a bond with the appropriate level of UV stability for the specific application to ensure long-term durability and performance.
Low Shrinkage of Lens Bonding Adhesive
The UV stability of lens bonding adhesive refers to the adhesive’s ability to resist degradation or damage from exposure to ultraviolet (UV) radiation. UV stability is an essential property of lens bonding adhesive because the adhesives are often used in applications that expose them to UV light, such as in optical lenses.
The level of UV stability of lens bonding adhesive can vary depending on the specific type of adhesive used. Some adhesives are formulated to have excellent UV stability, while others may degrade over time when exposed to UV radiation. The UV stability of an adhesive is typically determined by the type and amount of UV absorbers or stabilizers added during the formulation process.
When selecting a lens bonding adhesive, it is essential to consider the level of UV stability required for the specific application. For example, adhesives used in outdoor lenses, such as sunglasses, must have high UV stability to ensure long-term durability and performance. Conversely, adhesives used in indoor lenses, such as prescription eyeglasses, may require less UV stability.
The UV stability of lens bonding adhesive is important when selecting an adhesive for optical applications. It is essential to choose a bond with the appropriate level of UV stability for the specific application to ensure long-term durability and performance.
Applications of Lens Bonding Adhesive in Optics
Lens bonding adhesive is a type of optical adhesive that is commonly used in various applications in the field of optics. Some of the applications of lens bonding adhesive include:
Lens assembly: Lens bonding adhesive is often used to assemble lenses in optical devices such as cameras, telescopes, and microscopes. The adhesive helps to bond multiple lens elements together and hold them in place, ensuring they remain aligned.
Optical filters: Lens bonding adhesive is also used to fabricate optical filters. The adhesive is applied to the surface of a substrate, and the filter material is then connected to the substrate using the adhesive.
Fiber optics: Lens bonding adhesive fabricates fiber optic components such as connectors and splices. The adhesive bonds the fiber to the connector or splice, ensuring a secure and precise connection.
Prism assembly: Lens bonding adhesive is also used to assemble prisms. The adhesive is applied to the surface of the prism, which is then bonded to the substrate using the adhesive.
Medical devices: Lens bonding adhesive is used to manufacture endoscopes and surgical microscopes. The adhesive is used to bond the lenses and other optical components in the apparatus, ensuring they remain aligned and function properly.
Overall, lens bonding adhesive plays a critical role in manufacturing and assembling optical devices, ensuring that the lenses and other optical components remain securely bonded together and function as intended.
Applications of Lens Bonding Adhesive in Automotive Industry
Lens bonding adhesive, or optical adhesive, is a specialized type used in the automotive industry for various applications involving the bonding of lenses and other optical components. Here are some of the typical applications of lens bonding adhesive in the automotive industry:
- Headlights: Lens bonding adhesive is often used to bond the lens covers onto a car’s headlights. This provides a secure and durable seal that prevents water and debris from entering the headlight housing and damaging the bulbs.
- Rearview mirrors: The rearview mirrors in cars are typically attached to the windshield using lens bonding adhesive. This provides a strong bond that can withstand the typical driving vibrations and shocks.
- Cameras and sensors: Many modern cars have cameras and sensors that rely on optical components to function. Lens bonding adhesive is often used to bond these components, ensuring they remain stable and accurate.
- Instrument panels: The displays and gauges in a car’s instrument panel often rely on optical components that require bonding with lens bonding adhesive. This provides a clear and durable bond that can withstand constant exposure to heat and vibration.
Overall, using lens bonding adhesive in the automotive industry provides a reliable and cost-effective solution for bonding optical components in place.
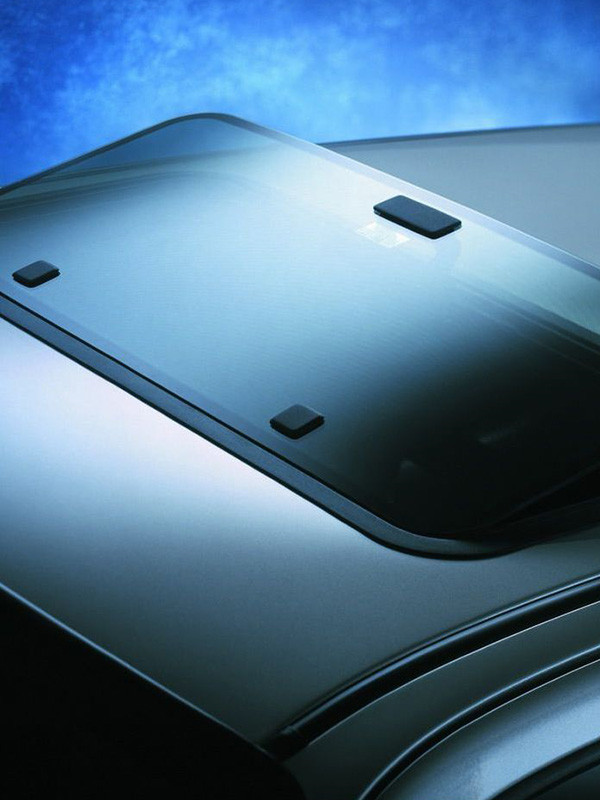
Applications of Lens Bonding Adhesive in Electronics Industry
Lens bonding adhesives have several applications in the electronics industry, particularly in producing electronic devices with display screens. Here are some of the typical applications of lens bonding adhesive in electronics:
- LCD Displays: Lens bonding adhesives are used to attach the cover lens to the display module in LCD displays. This adhesive provides optical clarity, strong bonding, and protection against environmental elements such as dust and moisture.
- Touchscreens: Touchscreens are used in various electronic devices such as smartphones, tablets, and laptops. Lens bonding adhesives are used to attach the cover glass to the touch sensor in these devices, providing durability and sensitivity to touch.
- LED Lighting: Lens bonding adhesives attach lenses to LED modules in lighting applications. The adhesive helps secure the lens, protecting the LED and improving light output.
- Cameras: Lens bonding adhesives attach lenses to camera modules in electronic devices such as smartphones and digital cameras. The adhesive helps to improve image quality by reducing reflections and increasing light transmission.
- Optical Devices: Lens-bonding adhesives produce optical devices such as binoculars, telescopes, and microscopes. The adhesive provides a strong bond between the lens and the housing, improving visual performance and durability.
Overall, lens-bonding adhesives are essential in the electronics industry for ensuring electronic devices’ durability, clarity, and functionality.
Applications of Lens Bonding Adhesive in Medical Industry
Lens bonding adhesive has a variety of applications in the medical industry. Some of the most common applications include:
- Optical Lenses: Lens bonding adhesive attaches optical lenses to frames, which is critical for eyeglasses, binoculars, and other optical devices. The adhesive provides a strong bond between the lens and frame, ensuring the lens remains securely in place.
- Endoscopes: Endoscopes are medical instruments used to examine the interior of a body cavity or organ. Lens bonding adhesive is used to attach the lenses to the endoscope, allowing doctors to visualize the patient’s internal organs.
- Dental Implants: Lens bonding adhesive is also used in the dental industry to attach prosthetic teeth to implants. This adhesive provides a strong and durable bond that allows the patient to chew and speak normally.
- Microscopes: Microscopes are essential tools in the medical industry, and lens bonding adhesive is used to attach the lenses to the microscope body. This ensures that the microscope provides a clear and accurate image.
- Medical Devices: Lens bonding adhesive is also used to attach lenses to various medical devices, including cameras, surgical scopes, and diagnostic equipment. This ensures that the devices are accurate and reliable.
Overall, lens bonding adhesive plays a critical role in the medical industry by providing a solid and durable bond between lenses and other components of medical devices.
Challenges of Using Lens Bonding Adhesive
Lens bonding adhesive is a type of adhesive used in the optical industry to bond lenses to frames. While it offers many benefits, such as a secure hold and a clean finish, it also presents some challenges. Here are some of the challenges of using lens bonding adhesive:
- Surface preparation: Lens bonding adhesive requires careful surface preparation to ensure a strong bond. The surface must be free from any dirt, oil, or residue that could interfere with the bond. This can be time-consuming and requires attention to detail.
- Temperature and humidity: Lens bonding adhesive can be sensitive to temperature and humidity changes. Sometimes, it may need specific temperature and humidity conditions to bond correctly. This can be a challenge in specific environments or during certain seasons.
- Bond strength: While lens bonding adhesive can create a strong bond, it may be weaker than other bonding methods. This can be a concern for high-stress applications, such as sports eyewear.
- Curing time: Lens bonding adhesive typically requires a curing time before it reaches its full strength. Depending on the adhesive used, this can range from a few hours to a few days. This can be a challenge when quick turnaround times are needed.
- Shelf life: Lens bonding adhesive typically has a limited shelf life and can expire if not used within a specific timeframe. This can concern small optical businesses that may use the adhesive sparingly.
While lens bonding adhesive offers many benefits, it also presents some challenges. Careful attention to surface preparation, temperature and humidity control, and curing times can help ensure a successful bond.
Conclusion: Prospects of Lens Bonding Adhesive in the Future
Lens bonding adhesive has already shown significant promise in the optical industry, particularly in manufacturing eyeglasses and camera lenses. As technology continues to advance, the use of lens bonding adhesive will become more widespread and even more advanced.
One of the main advantages of lens bonding adhesive is its ability to create a seamless bond between lenses and frames, resulting in improved durability and overall performance of the finished product. Additionally, advances in lens bonding adhesive technology have enabled manufacturers to use thinner and lighter materials to produce lenses, which can lead to greater comfort for wearers.
Furthermore, the growing demand for high-quality optical products, such as camera lenses and eyeglasses, is driving research and development in lens-bonding adhesives. As a result, we will see further technological advancements, such as developing new adhesive formulas and improved application techniques.
Overall, lens bonding adhesive has a bright future in the optical industry. We expect to see even more innovative uses for this versatile and powerful adhesive as technology evolves.