Conformal Coatings for Electronics
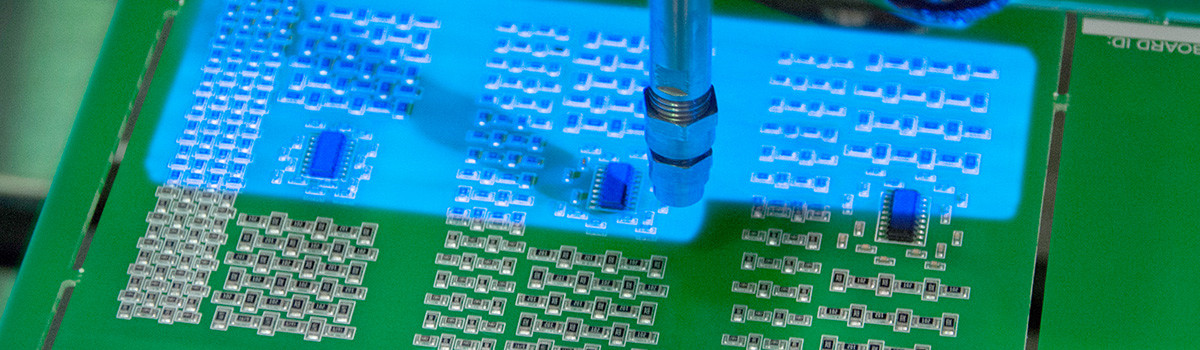
In today’s world, electronic devices are integral to our daily lives. As electronic devices become more complex and miniaturized, the need for protection against environmental factors such as moisture, dust, and chemicals becomes more critical. This is where conformal coatings come in. Conformal coatings are specially formulated materials that protect electronic components from external factors that may compromise their performance and functionality. This article will explore the benefits and importance of conformal coatings for electronics.
What are conformal coatings for electronics?
Conformal coatings are specialized protective coatings used in the electronics industry to safeguard electronic components and circuit boards from environmental factors such as moisture, dust, chemicals, and temperature extremes. These coatings are applied in a thin, uniform layer over the surface of the electronics, conforming to the contours of the components to provide complete coverage and protection.
The primary purpose of conformal coatings is to prevent damage or malfunction of electronic devices caused by external elements. Moisture and humidity, for example, can cause corrosion and short circuits, while dust and debris can impair the performance of sensitive components. A conformal coating shields the electronic assembly from these hazards, ensuring its reliability and longevity.
Conformal coatings are typically made from various chemical formulations, including acrylics, silicones, urethanes, and epoxies. Each type of coating offers distinct properties and advantages. Acrylic coatings are widely used due to their versatility, ease of application, and cost-effectiveness. They provide good moisture resistance and are relatively simple to remove and reapply if necessary. Silicones are known for their excellent flexibility, thermal stability, and resistance to high temperatures. Urethane coatings offer exceptional chemical resistance and protection against solvents and fuels. Epoxies provide superior hardness and durability, making them suitable for rugged environments.
Conformal coatings require careful attention to ensure proper coverage and adhesion. Various techniques include brushing, spraying, dipping, and selective coating. Different methods may be employed depending on the specific requirements and complexity of the assembly. Some coatings are applied manually, while others are performed through automated processes, such as robotic spraying or dip coating systems.
Once applied, the conformal coating creates a protective barrier that encapsulates the electronic components without obstructing their functionality. It forms a protective film that adheres to the surface and maintains its protective properties over time. The coatings are typically transparent or translucent, allowing for visual assembly inspection.
In addition to protecting against environmental factors, conformal coatings also offer other benefits. They can provide electrical insulation, preventing current leakage and short circuits. Layers can also enhance the assembly’s resistance to vibrations and mechanical stresses, reducing the risk of damage during transportation or operation. Furthermore, they can offer protection against fungus, mold, and other contaminants that can compromise the performance of electronic devices.
The importance of conformal coatings for electronic devices
Conformal coatings play a crucial role in enhancing the reliability and durability of electronic devices, and they offer a range of essential benefits for ensuring optimal performance and longevity. Here are some key reasons why conformal coatings are necessary for electronic devices:
- Protection against moisture and humidity: One of the primary purposes of conformal coatings is to safeguard electronic components from moisture and humidity. Water can lead to corrosion, oxidation, and the formation of conductive paths, resulting in short circuits and malfunctioning of the devices. Conformal coatings act as a barrier, preventing moisture from reaching the sensitive components and reducing the risk of damage.
- Prevention of dust and debris accumulation: Electronics are often exposed to dust, dirt, and airborne contaminants. These particles can settle on circuit boards and components, leading to insulation issues, increased heat generation, and potential short circuits. Conformal coatings create a protective layer that inhibits the accumulation of dust and debris, maintaining the cleanliness and performance of the electronics.
- Chemical resistance: Many conformal coatings resist various chemicals, including solvents, fuels, acids, and alkalis. This is particularly important in environments where electronic devices may come into contact with corrosive substances. The coatings act as a shield, preventing chemical reactions and ensuring the longevity of the components.
- Thermal protection: Electronic devices generate heat during operation, and excessive heat can degrade the performance and reliability of components. Conformal coatings can provide a thermal barrier, dissipating heat and reducing the risk of overheating. Specific layers, such as silicone-based ones, are known for their excellent thermal stability and can withstand high temperatures without compromising their protective properties.
- Electrical insulation: Conformal coatings can offer electrical insulation, preventing current leakage and short circuits. They help maintain the desired electrical characteristics of the components and reduce the potential for electrical failures caused by environmental factors or contamination.
- Mechanical protection: Electronics may be subject to mechanical stresses, such as vibrations, shocks, or impacts. Conformal coatings enhance the mechanical robustness of electronic devices by providing an additional layer of protection. They help absorb vibrations and impact forces, reducing the risk of damage to delicate components and ensuring reliable operation.
- Environmental resistance: Conformal coatings enable electronic devices to withstand various environmental conditions. They can resist temperature extremes, UV radiation, salt spray, and other harsh elements. This is particularly important for devices used in outdoor or industrial applications, where they may be exposed to challenging environments.
Benefits of using conformal coatings
Using conformal coatings for electronic devices offers several benefits that contribute to their overall reliability and longevity. Here are some key advantages of using conformal coatings:
- Environmental Protection: Conformal coatings provide a protective barrier that shields electronic components from environmental factors such as moisture, dust, dirt, and chemicals. They prevent the ingress of water, which can cause corrosion and short circuits, and protect against the accumulation of dust and debris that can impair performance. This environmental protection extends the lifespan of electronic devices.
- Increased Reliability: By safeguarding against environmental hazards, conformal coatings enhance the reliability of electronic devices. They minimize the risk of failures caused by moisture-related issues, such as corrosion-induced component damage or electrochemical migration. Additionally, coatings protect against dust and debris that can cause electrical shorts or insulation breakdowns, ensuring consistent and reliable performance.
- Electrical Insulation: Conformal coatings offer electrical insulation properties, preventing current leakage and short circuits. They help maintain the desired electrical characteristics of the components, reducing the possibility of electrical malfunctions or failures due to contamination or moisture absorption. Electrical insulation also aids in meeting safety and regulatory requirements.
- Thermal Management: Some conformal coatings have thermal management properties, allowing them to dissipate heat generated by electronic components. This thermal protection helps prevent overheating, which can degrade performance and reduce the lifespan of sensitive devices. By effectively managing temperatures, conformal coatings contribute to the overall reliability of the electronics.
- Chemical Resistance: Many conformal coatings exhibit excellent chemical resistance. They provide a barrier against corrosive substances, solvents, fuels, and other chemicals that can degrade electronic components. This chemical resistance prevents chemical reactions, material degradation, and potential failures caused by exposure to harsh environments or contact with chemicals.
- Vibration and Shock Protection: Conformal coatings offer mechanical protection by absorbing vibrations and reducing the impact of shocks and mechanical stresses. This is particularly beneficial for electronic devices subjected to transportation or harsh operational conditions. Conformal coatings help prevent damage to delicate components, solder joints, and connections by minimizing the effects of vibrations and shocks.
- Ease of Inspection and Repair: Conformal coatings are often transparent or translucent, allowing for visual inspection of the underlying components. This facilitates easier detection of potential issues such as solder joint defects, component damage, or foreign material contamination. Furthermore, conformal coatings can be removed and reapplied if repairs or modifications are required, simplifying maintenance.
How do conformal coatings work?
Conformal coatings create a protective barrier on the surface of electronic components and circuit boards. These coatings are typically applied as thin, uniform layers that conform to the contours of the devices, ensuring complete coverage and protection. The coatings adhere to the surface and form a continuous film that shields against environmental factors and potential contaminants.
The application of conformal coatings involves several steps:
- Surface Preparation: Before applying the conformal coating, the surface of the electronic assembly needs to be adequately prepared. This typically involves cleaning and removing contaminants such as dust, oils, and residues. The cover may be cleaned using solvents, ultrasonic cleaning, or other appropriate methods to ensure a clean and smooth substrate for coating adhesion.
- Selection of Coating Material: Different types of conformal coatings are available, such as acrylics, silicones, urethanes, and epoxies, each with its properties and advantages. The choice of coating material depends on factors such as environmental conditions, desired protection level, electrical insulation requirements, and specific application considerations.
- Application Method: Conformal coatings can be applied using various methods, including brushing, spraying, dipping, and selective coating. The selection of the application method depends on factors such as the complexity of the assembly, the type of coating material, and the desired level of precision. Manual application methods are suitable for smaller-scale production or specific areas that require targeted coating. Automated processes, such as robotic spraying or dip coating systems, are often used for larger-scale production to ensure consistent and uniform coating coverage.
- Curing and Drying: After applying the coating, it must undergo a curing or drying process. This process allows the coating material to solidify and form a protective film. The curing time and conditions depend on the specific coating material and the manufacturer’s recommendations. Curing methods can include air drying, thermal curing using ovens, or exposure to UV light for certain types of coatings.
Once applied and cured, the conformal coating creates a protective barrier encapsulating the electronic components. The layer is a barrier against moisture, dust, chemicals, and other environmental factors that can damage or degrade the components. It helps to prevent corrosion, electrical shorts, and insulation breakdown, ensuring the reliability and longevity of electronic devices.
Conformal coatings maintain their protective properties over time, offering continued protection for electronic assembly. In the event of repairs or modifications, the layer can be selectively removed and reapplied, allowing for maintenance or component replacement without compromising the overall protection the coating provides.
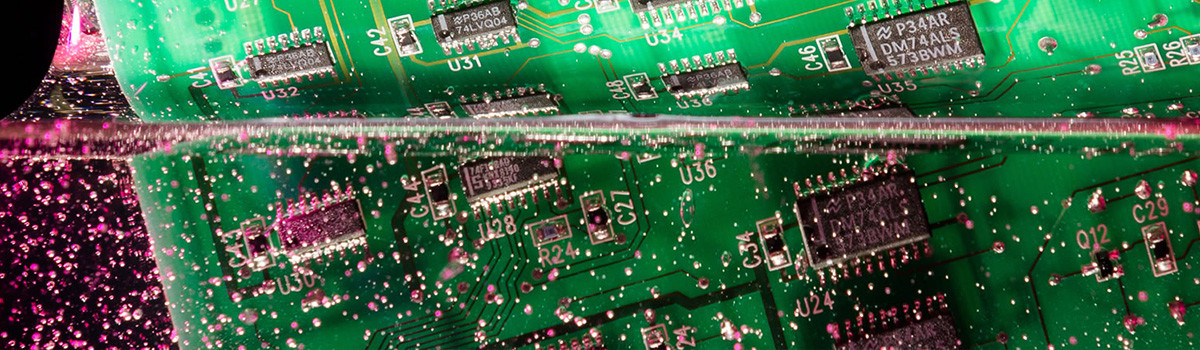
Types of conformal coatings
Several types of conformal coatings are available, each with its properties, advantages, and applications. The selection of the coating type depends on factors such as the specific requirements of the electronic assembly, environmental conditions, desired protection level, and manufacturing processes. Here are some commonly used types of conformal coatings:
- Acrylic Conformal Coatings: Acrylic coatings are one of the most widely used types due to their versatility and cost-effectiveness. They provide good moisture resistance, electrical insulation, and protection against environmental factors. Acrylic coatings are easy to apply and can be removed and reworked. They are suitable for various applications and offer good general-purpose protection.
- Silicone Conformal Coatings: Silicone coatings have excellent flexibility, thermal stability, and resistance to high temperatures. They can withstand extreme temperature variations without losing their protective properties. Silicone coatings provide excellent moisture resistance and electrical insulation. They are often used in applications where high thermal stability and flexibility are critical, such as in automotive, aerospace, and outdoor electronic devices.
- Urethane Conformal Coatings: Urethane coatings offer exceptional chemical resistance, making them suitable for applications where exposure to solvents, fuels, or other harsh chemicals is a concern. They provide good moisture protection, electrical insulation, and mechanical durability. Urethane coatings are often used in demanding environments such as automotive, industrial, and military applications.
- Epoxy Conformal Coatings: Epoxy coatings are known for their excellent hardness and durability. They offer solid mechanical protection and resistance to abrasion and impact. Epoxy coatings provide good chemical resistance and moisture protection. They are commonly used in applications requiring robust protection and mechanical strength, such as in industrial control systems, ruggedized electronics, and high-stress environments.
- Parylene Conformal Coatings: Parylene is a unique type of conformal coating deposited as a vapor and forms a thin, pinhole-free polymer film. Parylene layers provide excellent moisture barrier properties, electrical insulation, chemical resistance, and biocompatibility. They offer a high level of protection and conform to complex geometries. Parylene coatings are commonly used in medical devices, aerospace, and sensitive electronic applications.
- UV-Curable Conformal Coatings: UV-curable coatings are applied as a liquid and then cured using UV light. They offer fast curing times, which can increase production efficiency. UV-curable layers provide good moisture resistance, electrical insulation, and chemical resistance. They are suitable for applications requiring rapid curing, high throughput, and consistent coating quality.
It is important to note that selecting the appropriate conformal coating depends on the specific requirements of the electronic assembly and the intended application. Environmental conditions, operating temperature range, chemical exposure, and desired protection level should be considered when choosing the type of conformal coating to ensure optimal performance and longevity of the electronic devices.
Acrylic conformal coatings
Acrylic conformal coatings are widely used in the electronics industry due to their versatility, cost-effectiveness, and ease of application. They provide a range of benefits and are suitable for various electronic assemblies and applications. Here are some key features and advantages of acrylic conformal coatings:
- Moisture Protection: Acrylic coatings offer good moisture resistance, helping to prevent water or moisture penetration into electronic components. Moisture can cause corrosion, electrical shorts, and degradation of performance. Acrylic coatings act as a barrier, safeguarding against moisture-related issues and enhancing the reliability and lifespan of electronic devices.
- Electrical Insulation: Acrylic coatings provide electrical insulation, preventing current leakage and short circuits. They help maintain the desired electrical characteristics of the components and reduce the risk of electrical malfunctions or failures caused by contamination or moisture absorption. This electrical insulation property is essential for maintaining the integrity of electronic circuits.
- Environmental Protection: Acrylic conformal coatings protect electronic assemblies from environmental factors such as dust, dirt, chemicals, and temperature variations. They create a barrier against airborne contaminants, preventing them from settling on the surface of components. Acrylic coatings also offer some level of resistance to chemicals, providing additional protection against corrosive substances.
- Ease of Application: Acrylic coatings are known for their ease of application. They can be applied using various methods, including brushing, spraying, dipping, or selective coating. This flexibility allows for manual and automated application processes, depending on the specific requirements and production scale. Acrylic coatings generally have a good wetting ability, ensuring uniform coverage and adherence to the surfaces of electronic components.
- Repair and Rework Capability: One of the advantages of acrylic coatings is their reworkability. If repairs or modifications are required, acrylic coatings can be easily removed using appropriate solvents, allowing for repair work on the underlying components. The ability to remove and reapply acrylic coatings simplifies the repair process and facilitates maintenance activities.
- Transparent or Translucent: Acrylic conformal coatings are typically transparent or translucent. This feature allows for visual inspection of the underlying components without needing coating removal. The visual inspection identifies potential issues, such as solder joint defects, component damage, or foreign material contamination.
- Cost-Effectiveness: Acrylic conformal coatings offer a cost-effective solution for protecting electronic assemblies. They balance performance and affordability well, making them suitable for a wide range of applications. The relatively low cost of acrylic coatings allows for cost-efficient production processes without compromising the desired protection and reliability of electronic devices.
While acrylic conformal coatings provide several benefits, it is essential to consider the electronic assembly’s specific requirements and environmental conditions when choosing a coating type. Factors such as operating temperature range, chemical exposure, and mechanical stresses should be considered to ensure optimal protection and performance.
Silicone conformal coatings
Silicone conformal coatings are widely used in the electronics industry due to their unique properties and ability to withstand challenging environmental conditions. They offer a range of benefits that make them suitable for various electronic assemblies and applications. Here are some key features and advantages of silicone conformal coatings:
- Thermal Stability: Silicone coatings are known for their excellent thermal stability, allowing them to withstand high operating temperatures without losing their protective properties. They can handle temperature variations more effectively than many other conformal coating types. This makes silicone coatings well-suited for applications with high thermal stability, such as automotive, aerospace, and industrial electronics.
- Flexibility and Conformability: Silicone conformal coatings are highly flexible and can conform to the shape of complex electronic assemblies. They can be applied as thin, uniform layers that provide complete coverage even on intricate circuitry and components. The flexibility and conformability of silicone coatings ensure that critical areas are adequately protected, reducing the risk of damage or failure.
- Moisture and Environmental Protection: Silicone coatings offer excellent moisture resistance, making them practical barriers against the penetration of water and humidity. This moisture protection helps prevent corrosion, oxidation, and electrical shorts caused by moisture-related issues. Silicone coatings also resist environmental factors such as dust, dirt, and chemicals, enhancing the longevity and reliability of electronic devices.
- Electrical Insulation: Silicone conformal coatings provide electrical insulation properties, preventing current leakage and short circuits. They maintain the electrical integrity of the components and protect against electrical failures caused by contamination or moisture absorption. The electrical insulation offered by silicone coatings is crucial for maintaining the reliability and performance of electronic circuits.
- Chemical Resistance: Silicone coatings exhibit good resistance to various chemicals, including solvents, fuels, acids, and alkalis. This chemical resistance makes silicone coatings suitable for applications where exposure to corrosive substances is a concern. The layers act as a protective barrier, preventing chemical reactions and material degradation and ensuring the longevity of electronic components.
- UV and Weather Resistance: Silicone coatings offer excellent resistance to ultraviolet (UV) radiation and weathering. They can withstand prolonged exposure to sunlight and outdoor environments without significant degradation or loss of protective properties. This makes silicone coatings ideal for electronic devices used in outdoor applications or exposed to UV radiation.
- Dielectric Properties: Silicone conformal coatings have good dielectric properties, meaning they provide effective electrical insulation without significantly affecting the electrical performance of the components. This property is essential for maintaining the desired electrical characteristics and preventing electrical breakdown in electronic circuits.
Silicone conformal coatings are available in different formulations to suit specific application requirements. They can be applied using various methods, including brushing, spraying, or dipping. Silicone coatings provide a reliable and durable protective layer for electronic assemblies, ensuring their functionality and reliability even in harsh operating conditions.
When considering silicone conformal coatings, evaluating factors such as operating temperature range, exposure to chemicals, and mechanical stresses is essential to determine the most suitable coating formulation for the specific application.
Epoxy conformal coatings
Epoxy conformal coatings are widely used in electronics due to their excellent hardness, durability, and chemical resistance. They offer a range of benefits that make them suitable for various electronic assemblies and applications. Here are some key features and advantages of epoxy conformal coatings:
- Hardness and Mechanical Protection: Epoxy coatings provide exceptional hardness and mechanical protection, making them highly resistant to abrasion, impact, and physical damage. They offer a robust barrier that shields electronic components from mechanical stresses, ensuring their longevity and reliability. Epoxy coatings are particularly suitable for applications requiring enhanced automatic protection, such as in industrial control systems and ruggedized electronics.
- Chemical Resistance: Epoxy conformal coatings exhibit excellent resistance to various chemicals, including solvents, fuels, acids, and alkalis. This chemical resistance protects electronic components from degradation or damage caused by exposure to corrosive substances. Epoxy coatings act as a barrier, preventing chemical reactions and ensuring the integrity of the underlying components.
- Moisture and Environmental Protection: Epoxy coatings provide adequate moisture and environmental protection. They create a barrier against water, moisture, dust, and other environmental contaminants that can harm electronic components. Epoxy coatings help prevent corrosion, electrical shorts, and performance degradation by preventing moisture ingress.
- Electrical Insulation: Epoxy conformal coatings offer excellent electrical insulation properties, preventing current leakage and short circuits. They maintain the desired electrical characteristics of the components, reducing the risk of electrical malfunctions or failures caused by contamination or moisture absorption. The electrical insulation provided by epoxy coatings is crucial for maintaining the reliability and performance of electronic circuits.
- Thermal Resistance: Epoxy coatings have good thermal resistance, allowing them to withstand elevated temperatures without significant degradation or loss of protective properties. They help dissipate heat generated by electronic components, contributing to thermal management and preventing overheating. This thermal resistance makes epoxy coatings suitable for applications where temperature variations and heat dissipation are critical considerations.
- Adhesion and Coverage: Epoxy conformal coatings exhibit excellent adhesion to various substrates, including metal, plastic, and PCB materials. They adhere well to the surface of electronic assemblies, forming a uniform and continuous protective layer. Epoxy coatings can provide complete coverage, ensuring that all critical areas and components are adequately protected.
- Repairability: Epoxy coatings offer the advantage of being reworkable and repairable. If repairs or modifications are required, epoxy coatings can be selectively removed using appropriate solvents, allowing for repair work on the underlying components. This repairability feature simplifies maintenance activities and facilitates component replacement if necessary.
Epoxy-conformal coatings are typically applied using brushing, spraying, or selective coating methods. The coatings cure through a chemical reaction or heat-curing process, forming a durable protective film. They provide long-lasting protection for electronic assemblies, ensuring their functionality and reliability in challenging environments.
When considering epoxy conformal coatings, evaluating factors such as operating temperature range, exposure to chemicals, mechanical stresses, and the desired level of mechanical and chemical protection is essential to select the most suitable coating formulation for the specific application.
Urethane conformal coatings
Urethane conformal coatings, also known as polyurethane coatings, are widely used in the electronics industry due to their exceptional chemical resistance and mechanical durability. They offer a range of benefits that make them suitable for various electronic assemblies and applications. Here are some key features and advantages of urethane conformal coatings:
- Chemical Resistance: Urethane coatings resist various chemicals, including solvents, fuels, oils, acids, and alkalis. This chemical resistance makes urethane coatings well-suited for applications where exposure to aggressive chemicals is a concern. They act as a barrier, protecting electronic components from chemical degradation, corrosion, and other forms of damage.
- Moisture Protection: Urethane conformal coatings provide effective moisture resistance, preventing water or moisture penetration into electronic components. Moisture can cause corrosion, electrical shorts, and degradation of performance. Urethane coatings act as a barrier, safeguarding against moisture-related issues and enhancing the reliability and lifespan of electronic devices.
- Mechanical Durability: Urethane coatings offer excellent mechanical durability, with resistance to abrasion, impact, and physical damage. They provide a tough protective layer that withstands harsh handling and environmental conditions. Urethane coatings are suitable for applications where enhanced mechanical protection is required, such as in industrial settings or devices exposed to high levels of wear and tear.
- Thermal Resistance: Urethane coatings exhibit good thermal resistance, allowing them to withstand elevated temperatures without significant degradation or loss of protective properties. They help dissipate heat generated by electronic components, contributing to thermal management and preventing overheating. This thermal resistance makes urethane coatings suitable for applications where temperature variations and heat dissipation are critical considerations.
- Flexibility: Urethane conformal coatings offer a balance of hardness and flexibility. They have some elasticity, allowing them to accommodate minor movements and stresses in the electronic assembly. This flexibility helps to reduce the risk of coating cracking or delamination, ensuring long-term protection of the components.
- UV Stability: Urethane coatings exhibit good resistance to ultraviolet (UV) radiation, protecting against the potentially damaging effects of sunlight and other UV sources. They resist yellowing or degradation when exposed to UV light, making them suitable for outdoor applications or devices exposed to UV radiation.
- Adhesion and Coverage: Urethane coatings demonstrate excellent adhesion to various substrates, including metals, plastics, and PCB materials. They adhere well to the surface of electronic assemblies, forming a uniform and continuous protective layer. Urethane coatings can provide complete coverage, ensuring that all critical areas and components are adequately protected.
Urethane conformal coatings are typically applied using brushing, spraying, or selective coating methods. The layers can be cured through heat curing or moisture curing processes, forming a durable and protective film. They provide long-lasting protection for electronic assemblies, ensuring their functionality and reliability in demanding environments.
When considering using urethane conformal coatings, it is essential to evaluate the specific chemical exposure, operating temperature range, mechanical stresses, and the desired level of chemical and mechanical protection to select the most suitable coating formulation for the particular application.
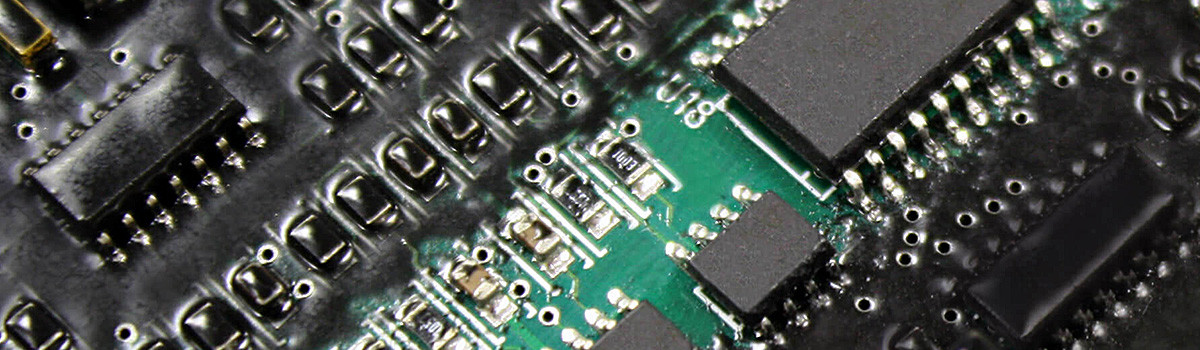
Parylene conformal coatings
Parylene conformal coatings are unique and provide exceptional protection for electronic devices. Parylene coatings are deposited as a vapor and form a thin, pinhole-free polymer film. They offer a range of benefits that make them highly suitable for various electronic assemblies and applications. Here are some key features and advantages of Parylene conformal coatings:
- Moisture and Chemical Barrier: Parylene coatings provide an excellent barrier against moisture, gasses, and chemicals. The thin, uniform film formed by Parylene coatings offers a highly effective moisture barrier, preventing water and moisture ingress into electronic components. They also provide exceptional resistance to chemicals, including solvents, acids, bases, and corrosive substances. This moisture and chemical resistance protects electronic devices from corrosion, oxidation, and degradation, ensuring their long-term reliability.
- Conformity and Coverage: Parylene coatings have outstanding conformal properties, meaning they conform to the shape of complex and irregular surfaces. The vapor deposition process allows the layer to cover the entire electronic assembly uniformly, including intricate features, sharp edges, and crevices. Parylene coatings can penetrate deep into tight spaces, ensuring complete coverage and protection for all critical areas.
- Electrical Insulation: Parylene conformal coatings provide excellent electrical insulation properties. They have high dielectric strength and can effectively insulate electrical components and prevent current leakage or short circuits. Parylene coatings maintain the desired electrical characteristics of the details, reducing the risk of electrical malfunctions or failures caused by contamination or moisture absorption.
- Biocompatibility: Parylene coatings are biocompatible and chemically inert, making them suitable for medical devices and implantable electronics. They do not cause adverse reactions when in contact with biological tissues or fluids. Parylene coatings are used in applications such as pacemakers, neural implants, and biosensors, where biocompatibility is critical.
- Thermal Stability: Parylene coatings exhibit excellent thermal stability and can withstand a wide temperature range. They remain stable at low and high temperatures, maintaining their protective properties without significant degradation. This thermal stability makes Parylene coatings suitable for applications where temperature variations and heat dissipation are essential considerations.
- Low Friction Coefficient: Parylene coatings have a low coefficient of friction, providing lubricity and reducing the surface friction between components. This low friction coefficient helps to minimize wear, prevent sticking or binding, and improve the overall performance and lifespan of coated electronic devices.
- Transparency and Traceability: Parylene conformal coatings are transparent, allowing for visual inspection of the underlying components without needing coating removal. This transparency enables assessing and identifying potential issues such as solder joint defects, component damage, or foreign material contamination. Additionally, Parylene coatings can be doped or marked with traceable elements, facilitating quality control, tracking, and identification purposes.
Parylene conformal coatings are typically applied using a specialized vapor deposition process. The layers are formed through a chemical vapor deposition (CVD) method, which ensures uniform and pinhole-free coverage. Parylene coatings provide long-lasting protection for electronic assemblies, even in harsh environments and demanding applications.
When considering Parylene conformal coatings, it is essential to evaluate factors such as the specific requirements of the electronic assembly, environmental conditions, and the desired level of protection to select the appropriate Parylene type and deposition process.
Factors to consider when choosing a conformal coating
When choosing a conformal coating for electronic devices, several factors should be considered to ensure the coating meets the application’s specific requirements. Here are some key factors to consider:
- Environmental Conditions: The environmental conditions in which the electronic device will operate play a crucial role in selecting the appropriate conformal coating. Consider factors such as temperature extremes, humidity levels, chemical exposure, salt spray, and UV radiation. Different layers have varying degrees of resistance to these environmental factors, and choosing a coating that can withstand specific conditions is essential for long-term reliability.
- Electrical Properties: Consider the electrical properties required for the electronic assembly. Some coatings offer better electrical insulation properties than others. Evaluate the dielectric strength, surface resistance, and ability to maintain insulation even in the presence of humidity or contaminants. Ensure the chosen coating does not negatively affect the electrical performance of the components.
- Thickness and Coverage: The thickness and coverage requirements of the conformal coating are essential considerations. Thin layers are desirable for applications where limited space or maintaining close tolerances is critical. However, thicker coatings may be necessary for applications that require enhanced protection against mechanical stress or harsh environments. The layer should be able to uniformly cover all critical areas, including complex geometries and components.
- Application Method: Consider the available methods and choose a coating compatible with the selected mode. Standard application methods include spraying, brushing, dipping, and selective coating. Some layers may be better suited for specific application methods, while others may require specialized equipment or techniques.
- Rework and Repair: Evaluate the rework and repairability requirements of the coating. In some instances, removing or repairing the layer may be necessary for component replacement, repairs, or modifications. Some coatings can be easily reworked or removed, while others may be more difficult or require specialized solvents or methods.
- Substrate Compatibility: Consider the compatibility of the coating with the materials and substrates used in the electronic assembly. The coating should adhere to the substrate and exhibit good compatibility with components, solder joints, and other materials. Compatibility issues can lead to delamination, reduced adhesion, or poor coating performance.
- Regulatory Compliance: Consider any specific regulatory requirements that apply to the electronic device or the industry in which it will be used. Typical applications like medical devices or aerospace electronics may have specific regulatory standards for conformal coatings. Ensure the chosen coating complies with relevant regulations and standards.
- Cost and Availability: Evaluate the cost of the coating and its availability in the required quantities. Consider the cost-effectiveness of the coating, the desired level of protection, and the overall project budget. Additionally, ensure the coating is readily available from reliable suppliers to avoid delays or supply chain issues.
By considering these factors, you can select a conformal coating that provides optimal protection, performance, and reliability for the specific requirements of your electronic device and its operating environment.
Application methods for conformal coatings
Conformal coatings are thin protective layers applied to electronic circuit boards and components to provide insulation and protect them from environmental factors such as moisture, dust, chemicals, and temperature fluctuations. These coatings are designed to “conform” to the shape of the substrate, providing a uniform and continuous protective barrier. There are several methods for applying conformal coatings, each with advantages and considerations. This article will explore some standard application methods for conformal coatings.
- Brushing/Dipping: Brushing or dipping is one of the simplest and most traditional methods of applying conformal coatings. The coating material is manually brushed, or the components are dipped into a container of the coating solution. This method is cost-effective and suitable for low-volume production. However, it may result in inconsistent coating thickness and require post-application curing.
- Spray Coating: Spray coating involves using compressed air or a specialized spray system to apply the coating material as a fine mist onto the substrate. This method offers faster application and is suitable for manual and automated processes. Spray coating provides more control over the coating thickness and uniformity, but it requires proper ventilation and filtration systems to control overspray and ensure operator safety.
- Selective Coating: Selective coating is used when only specific substrate areas require protection. It involves using a controlled dispensing system or a robotic arm with a precision applicator to apply the coating material precisely to the desired locations. Selective coating minimizes wastage, reduces the need for masking, and allows for targeted protection. It is commonly used for complex circuit boards with sensitive components.
- Vapor Deposition: Vapour deposition methods, such as chemical vapor deposition (CVD) and physical vapor deposition (PVD), involve depositing a conformal coating layer onto the substrate through a vapor phase. These methods typically require specialized equipment and controlled environments. Vapor deposition techniques offer excellent coating uniformity, thickness control, and coverage on complex geometries. They are commonly used for high-performance applications and advanced electronic devices.
- Coating Parylene: Parylene coating is a unique method that involves depositing a thin conformal polymer film onto the substrate through vapor deposition. Parylene coatings offer exceptional protection, insulation, and biocompatibility. The coating material penetrates crevices and covers the entire surface uniformly, even on intricate components. Parylene coatings are commonly used in medical devices, aerospace, and high-reliability applications.
When selecting an application method for conformal coatings, several factors need to be considered, including the complexity of the substrate, production volume, coating material properties, cost, and environmental requirements. It is essential to choose the method that provides optimal coating coverage, uniformity, and reliability while considering the application’s specific needs.
Conformal coating thickness
Conformal coating thickness is critical in ensuring the effectiveness and reliability of the protective coating applied to electronic components and circuit boards. The coating thickness directly affects the level of protection provided against environmental factors, such as moisture, dust, chemicals, and temperature variations. This article will explore the importance of conformal coating thickness and the considerations involved in achieving the desired coating thickness.
The primary purpose of conformal coatings is to create a uniform and continuous protective layer over the substrate. The coating thickness should be sufficient to provide insulation and prevent any potential electrical shorts or leakage currents while not being so thick as to cause electrical interference or thermal issues. The ideal coating thickness depends on factors such as the coating material, the specific application, and the environmental conditions the coated electronics will encounter.
Conformal coatings are generally applied as thin layers, typically ranging from a few micrometers (µm) to tens of micrometers in thickness. The coating material manufacturer often specifies the recommended coating thickness or may be defined by industry standards such as IPC-CC-830 for conformal coatings.
Achieving the desired coating thickness involves considering several factors:
- Coating Material: Different conformal coating materials have varying viscosities and flow characteristics. These properties influence how the coating spreads and levels on the substrate surface, affecting the resulting thickness. It is essential to understand the specific application requirements and select a coating material that can be applied with the desired thickness control.
- Application Method: The chosen application method also plays a significant role in determining the coating thickness. Practices like brushing or dipping may result in variations in coating thickness due to manual application techniques. Automated processes such as spray or selective coating can provide more control over the coating thickness, resulting in a more even and uniform layer.
- Process Control: Proper process control is crucial to achieving the desired coating thickness. Factors such as spray pressure, nozzle size, spray distance, and coating material viscosity must be carefully controlled during the application process. Process parameters may need to be adjusted based on the substrate’s geometry and the desired coating thickness.
- Curing/Shrinking: Some conformal coating materials undergo a curing or drying process after application. The coating material may shrink during this process, affecting the final coating thickness. It is essential to consider the potential shrinkage when determining the initial coating thickness.
- Verification and Inspection: Once the coating is applied, it is essential to verify its thickness to ensure it meets the required specifications. Various inspection techniques, such as visual inspection, cross-sectioning, or specialized measurement equipment like profilometers or optical microscopy with calibrated measurement software, can be used.
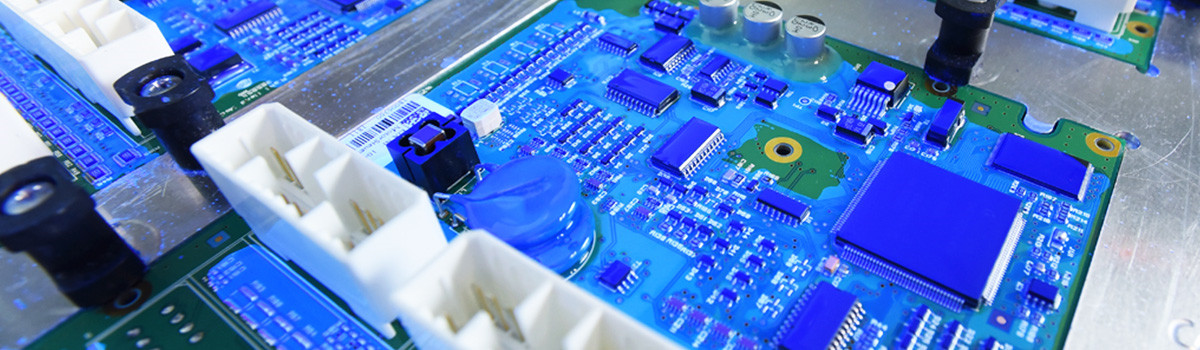
Common issues with conformal coatings
While conformal coatings are essential for protecting electronic components and circuit boards, they can sometimes encounter issues that may affect their performance and reliability. This article will discuss some common problems with conformal coatings and their potential causes.
- Inadequate Coverage: Inadequate coverage occurs when the coating fails to cover the entire surface of the substrate or leaves gaps and voids. This issue can result from improper application techniques, such as uneven spraying or insufficient coating viscosity. It can also occur due to surface contamination, inadequate drying or curing, or inadequate coating thickness control.
- Thickness Variation: Non-uniform coating thickness is another common issue. Inconsistent application techniques, such as uneven spraying or inadequate control of process parameters, can cause it. There needs to be more drying or curing time, improper coating material viscosity, or insufficient surface preparation can also contribute to thickness variations.
- Blistering and Delamination: Blistering and delamination occur when the conformal coating forms bubbles or separates from the substrate. This issue can arise due to improper surface cleaning and preparation, moisture or contamination on the surface, inadequate curing or drying, or improper compatibility between the coating material and the substrate.
- Cracking and Bridging: Cracking refers to developing fissures or fractures in the conformal coating, while bridging occurs when the coating material spans gaps or adjacent components, resulting in unintended electrical connections. These issues can be caused by excessive coating thickness, inadequate curing or drying, thermal stress, improper coating material selection, or inadequate coating flexibility.
- Poor Adhesion: Poor adhesion occurs when the coating fails to adhere to the substrate, resulting in reduced protection and potential coating detachment. Inadequate surface cleaning and preparation, contaminants, incompatible coating-substrate materials, or insufficient curing or drying can cause it.
- Electrochemical Migration: Electrochemical migration is the movement of ions or contaminants across the surface of the coated substrate, leading to potential short circuits and corrosion. It can occur due to inadequate coating thickness, the presence of conductive contaminants, or the presence of moisture or humidity.
- Insufficient Chemical Resistance: Conformal coatings may need to resist exposure to various chemicals and solvents. If the coating material does not have sufficient chemical resistance, it may degrade or dissolve when exposed to specific substances, compromising its protective capabilities. Proper material selection is crucial to ensure compatibility with the expected chemical environment.
To mitigate these issues, following best practices and guidelines for conformal coating application is essential, including proper surface cleaning and preparation, accurate control of process parameters, suitable coating material selection, and adequate curing or drying. Regular inspection and quality control measures should be implemented to identify and address potential coating issues early on. Adhering to industry standards, such as IPC-CC-830, can also help ensure the reliability and performance of conformal coatings.
Maintenance of conformal coatings
Conformal coatings protect electronic components and circuit boards from environmental factors such as moisture, dust, chemicals, and temperature fluctuations. However, like any protective coating, conformal coatings require proper maintenance to ensure their long-term effectiveness. Here are some key points to consider when it comes to the upkeep of conformal coatings:
- Regular Inspection: Perform routine inspections of the coated surfaces to check for any signs of damage, wear, or delamination. Look for cracks, chips, or areas where the coating may have worn off. Inspections should be carried out periodically, especially after handling, transportation, or exposure to harsh conditions.
- Cleaning: Keep the coated surfaces clean to prevent the accumulation of contaminants that could compromise the effectiveness of the coating. Use gentle cleaning methods, such as a soft brush or compressed air, to remove dust, debris, or particulate matter. Avoid using harsh solvents or abrasive materials that can damage the coating.
- Repairing Damaged Areas: If any damage or wear is detected during inspections, it’s essential to address it promptly. Repair the damaged areas by recoating them with the same conformal coating material. Ensure the damaged area is adequately cleaned and prepared before applying the new coating. This will help maintain the integrity of the protective layer.
- Temperature and Humidity Control: Maintain proper temperature and humidity conditions in the environment where the coated components are stored or operated. Extreme temperatures or high humidity levels can impact the performance of the coating and lead to delamination or reduced protection. Follow the manufacturer’s recommendations regarding the acceptable temperature and humidity ranges for the specific conformal coating material.
- Avoid Chemical Exposure: Prevent exposure of the coated surfaces to harsh chemicals or solvents that can deteriorate the coating. Be cautious while using cleaning agents or performing maintenance procedures near the covered components. Take necessary precautions to protect the conformal coating from direct contact with chemicals.
- Retesting and Recertification: In some industries, such as aerospace or medical, conformal coatings may require periodic retesting and recertification to ensure they meet the necessary standards and specifications. Follow the guidelines of the relevant industry standards and conduct the necessary tests or inspections at regular intervals.
- Documentation and Record-Keeping: Maintain detailed records of the conformal coating application, maintenance activities, inspections, and repairs. This documentation will help track the maintenance history, identify failure or wear patterns, and ensure compliance with industry regulations and standards.
Testing and inspection of conformal coatings
Testing and inspection of conformal coatings are essential to ensure their effectiveness and reliability in protecting electronic components and assemblies. Here are some commonly used methods for testing and inspecting conformal coatings:
- Visual Inspection: Visual inspection is an essential step in evaluating the quality of conformal coatings. It involves examining the coating surface for visible defects such as pinholes, bubbles, cracks, or uneven coverage.
- Thickness Measurement: The thickness of the conformal coating is crucial as it affects its ability to provide adequate protection. Consistency can be measured using eddy current, magnetic induction, or optical profilometry techniques. The measurement should be compared against the specified coating thickness requirements.
- Adhesion Testing: Tests assess the bonding strength between the conformal coating and the substrate. Methods for adhesion testing include tape tests, cross-hatch tests, and pull-off tests. These tests determine if the layer adheres appropriately to the surface and can withstand stresses during operation and handling.
- Insulation Resistance Testing: This test evaluates the electrical resistance of the conformal coating. It ensures the layer provides effective electrical insulation to prevent leakage or short circuits. Insulation resistance testing is typically conducted using a high-voltage tester or a megohmmeter.
- Dielectric Withstand Voltage Testing: Dielectric withstand voltage testing, also known as high-potential or hipot testing, checks the coating’s ability to withstand high voltage without breakdown. The conformal coating is subjected to a specified voltage for a fixed duration to ensure it meets the required electrical insulation standards.
- Thermal Cycling Testing: Thermal cycling exposes the conformal coating to temperature variations to assess its resistance to thermal stress. The layer is subjected to repeated cycles of temperature extremes, and any changes, such as cracking or delamination, are observed.
- Humidity and Moisture Resistance Testing: These tests evaluate the conformal coating’s ability to withstand humidity and moisture. The layer is exposed to high humidity or moisture conditions for a specified period, and its performance is assessed for protection against corrosion or electrical failures.
- Chemical Resistance Testing: Chemical resistance testing checks how well the conformal coating withstands exposure to various chemicals, such as solvents or cleaning agents. The layer is exposed to the substances for a specified duration, and its appearance, adhesion, and functionality are assessed.
- Salt Spray Testing: Salt spray testing evaluates the coating’s resistance to corrosion in a salt-laden environment. The conformal coating is exposed to a salt mist or fog for a specified duration, and any signs of corrosion or degradation are examined.
It’s important to note that specific testing requirements may vary depending on the industry, application, and standards applicable to the conformal coating. Manufacturers or industry standards organizations often provide guidelines or specifications for testing and inspection procedures.
Industry standards for conformal coatings
Several industry standards and specifications exist for conformal coatings to ensure their quality, reliability, and performance. Here are some of the commonly referenced standards:
- IPC-CC-830: This standard, published by the Association of Connecting Electronics Industries (IPC), is widely used for conformal coating materials and application requirements. It covers the general conditions, material properties, application methods, and inspection criteria for conformal coatings.
- MIL-STD-883: This military standard outlines microelectronic device test methods and procedures, including conformal coatings. It includes specifications for adhesion, insulation resistance, thermal shock, humidity, and other tests relevant to conformal coatings.
- MIL-STD-810: This standard provides environmental engineering considerations and laboratory test methods to simulate and assess the performance of materials, equipment, and systems in various environmental conditions. It includes testing procedures for conformal coatings regarding temperature, humidity, vibration, shock, etc.
- IEC 61086: This international standard specifies the requirements and test methods for conformal coatings used in electronic assemblies. It covers coating materials, thickness, adhesion, flexibility, thermal endurance, and chemical resistance.
- UL 746E: This standard, published by Underwriters Laboratories (UL), focuses on evaluating polymeric materials for use in electrical equipment. It includes testing requirements for conformal coatings regarding flammability, aging characteristics, and electrical performance.
- ISO 9001: While not specific to conformal coatings, ISO 9001 is an internationally recognized standard for quality management systems. It ensures that organizations follow consistent quality control processes, including producing and inspecting conformal coatings.
It is important to note that different industries and applications may have specific standards or specifications tailored to their unique requirements. Additionally, many conformal coating manufacturers may provide technical data sheets or application guidelines, which can serve as valuable references for conformal coating selection and testing.
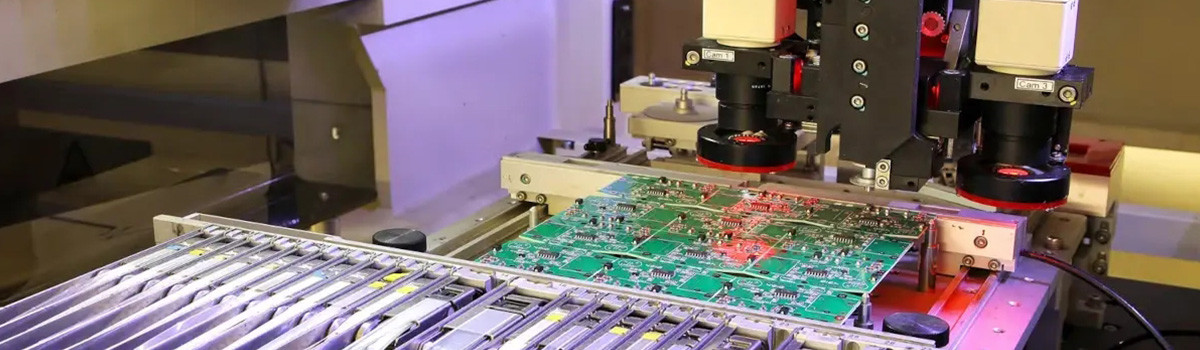
Advancements in conformal coating technology
In recent years, there have been significant advancements in conformal coating technology, driven by the need for improved protection, reliability, and performance of electronic components and assemblies. Here are some key improvements:
- Nano-Coatings: Nano-coatings have emerged as a promising advancement in conformal coating technology. These coatings consist of ultra-thin layers, typically at the nanoscale, providing excellent moisture and corrosion resistance while maintaining electrical performance. Nano-coatings offer superior coverage and conformability, ensuring adequate protection even on intricate and densely packed electronic assemblies.
- Multifunctional Coatings: Conformal coatings are being developed with multifunctional properties to address multiple challenges simultaneously. For example, some coatings offer moisture and chemical resistance and enhanced electrical conductivity or thermal management capabilities. These multifunctional coatings reduce the need for additional protective layers and improve overall performance.
- Self-Healing Coatings: Self-healing conformal coatings are designed to repair minor damages automatically. These coatings contain encapsulated healing agents released upon the damage, filling in cracks or voids and restoring the coating’s protective properties. Self-healing coatings prolong the lifespan of electronic components by mitigating the effects of wear and tear or environmental stresses.
- Flexible and Stretchable Coatings: With the rise of flexible electronics and wearable devices, conformal coatings must accommodate the bending, stretching, and twisting of substrates. Flexible and stretchable layers have been developed to provide robust protection while maintaining their integrity under mechanical strain. These coatings allow for conformal coverage on flexible substrates, expanding the range of applications.
- Low-VOC and Environmentally Friendly Coatings: There is an increasing focus on developing conformal coatings with reduced volatile organic compounds (VOCs) and environmentally friendly formulations. These coatings aim to minimize environmental impact during application and use while maintaining high-performance characteristics. Water-based or solvent-free coatings are being developed as alternatives to traditional solvent-based coatings.
- UV-Curable Coatings: UV-curable conformal coatings offer rapid curing times, enabling higher throughput in manufacturing processes. These coatings utilize ultraviolet (UV) light to initiate the curing reaction, allowing for faster production cycles and reduced energy consumption. UV-curable coatings also provide excellent coverage and adhesion, enhancing the overall reliability of coated assemblies.
- Conformal Coating Inspection Technologies: Advancements in inspection technologies are aiding in assessing conformal coating quality and performance. Automated optical inspection (AOI) systems with high-resolution cameras and image analysis algorithms can detect defects such as pinholes, bubbles, or coating thickness variations. This improves inspection efficiency and reliability, ensuring consistent coating quality.
- Thinner and Lighter Coatings: The demand for miniaturization and lightweight designs in electronic devices has driven the development of thinner and lighter conformal coatings. These coatings provide sufficient protection while minimizing the impact on the weight and size of the coated components. Thinner layers also offer improved heat dissipation, critical for high-power applications.
These conformal coating technology advancements contribute to the development of more reliable and durable electronic devices. As the electronics industry continues to evolve, the ongoing research and innovation in conformal coatings are expected to address emerging challenges and enable enhanced protection in various applications.
Environmental concerns and conformal coatings
Environmental concerns play a significant role in developing and using conformal coatings. As the electronics industry continues to grow, it is necessary to balance the benefits of conformal coatings with their potential environmental impacts. Here are some critical aspects related to environmental concerns and conformal coatings:
- Volatile Organic Compounds (VOCs): Traditional solvent-based conformal coatings often contain high levels of VOCs, contributing to air pollution and harming human health. In response, there is a growing demand for low-VOC or VOC-free formulations. Water-based coatings and coatings with low VOC content are being developed as alternatives to reduce the environmental impact.
- Hazardous Substances: Some conformal coatings may contain dangerous substances, such as heavy metals or persistent organic pollutants (POPs). These substances can have long-lasting environmental effects and pose risks during manufacturing, application, and end-of-life disposal. To address this, regulations and standards, such as the Restriction of Hazardous Substances (RoHS) directive, restrict the use of certain hazardous substances in electronic products.
- Life Cycle Assessment (LCA): Life cycle assessment evaluates the environmental impacts of conformal coatings throughout their entire life cycle, from raw material extraction to disposal. It helps identify areas for improvement and guides the development of environmentally friendly layers. LCA considers energy consumption, resource depletion, emissions, and waste generation.
- Eco-Friendly Formulations: Conformal coating manufacturers actively develop eco-friendly formulations that minimize environmental impact. This includes using bio-based materials, renewable resources, and environmentally friendly solvents. Bio-based coatings derived from natural sources offer potential advantages regarding a reduced ecological footprint and improved sustainability.
- Recycling and Waste Management: Proper disposal and recycling of conformal coatings are essential to prevent environmental pollution. The recycling of electronic components and assemblies should consider removing or separating conformal coatings to enable efficient material recovery. Developments in recycling technologies and processes are helping to address the challenges associated with coating removal and waste management.
- Environmental Regulations: Regulatory frameworks and standards, such as the European Union’s Registration, Evaluation, Authorization, and Restriction of Chemicals (REACH) regulation, aim to protect human health and the environment from potentially harmful substances. Compliance with these regulations ensures that conformal coatings meet specific environmental requirements and safety standards.
- Sustainable Manufacturing Practices: Adopting sustainable manufacturing practices reduces the environmental impact associated with the production of conformal coatings. This includes optimizing resource usage, minimizing waste generation, implementing energy-efficient processes, and promoting renewable energy sources.
- Environmental Certifications: Environmental certifications, such as ISO 14001, provide a framework for organizations to manage and continuously improve their environmental performance. Conformal coating manufacturers can seek certification to demonstrate their commitment to environmental responsibility and sustainable practices.
As the industry continues to evolve, there is a growing emphasis on developing conformal coatings that offer adequate protection while minimizing their environmental impact. Manufacturers, regulatory bodies, and end-users are working together to promote the use of environmentally friendly coatings and ensure responsible and sustainable practices throughout the lifecycle of electronic products.
The future outlook for conformal coatings in electronics
The future outlook for conformal coatings in electronics is promising, driven by technological advancements, increasing demand for high-performance electronic devices, and emerging trends in the industry. Here are some key aspects shaping the future of conformal coatings:
- Miniaturization and Higher Integration: The trend towards smaller and more compact electronic devices with higher integration levels poses challenges for conformal coatings. Future coatings must provide adequate protection while maintaining their integrity on miniaturized components and densely packed assemblies. This includes the development of thinner layers with improved coverage and conformability.
- Flexible and Stretchable Electronics: The rise of flexible and stretchable electronics, including wearable devices, require conformal coatings that can withstand the mechanical strain and repeated bending without compromising their protective properties. Future layers will focus on flexibility, durability, and adhesion to accommodate the unique requirements of these emerging applications.
- Advanced Materials: Developing new materials with enhanced properties will drive the future of conformal coatings. This includes using nanomaterials, such as nanoparticles and nanocomposites, to improve coating performance regarding moisture resistance, electrical conductivity, thermal management, and barrier properties. Advanced materials will enable coatings to meet the evolving needs of electronic devices.
- Multifunctional Coatings: The demand for multifunctional coatings that provide multiple benefits beyond protection will continue to grow. Future layers may incorporate self-healing capabilities, thermal conductivity, anti-static properties, antimicrobial properties, or energy harvesting features. Multifunctional coatings offer improved performance, reduced complexity, and increased reliability in electronic assemblies.
- Environmental Considerations: The focus on ecological sustainability and regulations regarding hazardous substances will influence the future of conformal coatings. The development of eco-friendly formulations with reduced VOCs and the use of bio-based materials will become more prevalent. Recycling and waste management strategies for conformal coatings will also play a significant role in minimizing environmental impact.
- Advanced Application Techniques: Innovations in application techniques will enhance the efficiency and quality of conformal coating processes. This includes robotic dispensing systems, selective coating methods, and advanced spray technologies to ensure precise and uniform coating coverage, reduce material waste, and improve productivity.
- Advanced Inspection and Testing Methods: As the complexity of electronic assemblies increases, there will be a need for more sophisticated inspection and testing methods for conformal coatings. This includes developing automated optical inspection (AOI) systems with advanced imaging and analysis capabilities to detect and assess coating defects, thickness variations, and adhesion quality.
- Industry Standards and Certifications: Ongoing developments in industry standards and certifications will continue to shape the future of conformal coatings. Manufacturers and end-users will rely on updated standards to ensure layers’ quality, reliability, and compliance with evolving requirements and regulations.
Overall, the future of conformal coatings in electronics looks promising, focusing on improved performance, adaptability to new technologies, environmental sustainability, and developing advanced materials and application techniques. These advancements will enable conformal coatings to provide robust protection for electronic devices in diverse and challenging environments.
Conclusion: Conformal electronic coatings offer an excellent solution for protecting electronic devices from environmental factors that can lead to their failure or malfunction. As technology advances, the need for more effective and reliable conformal coatings will only increase. Manufacturers, designers, and engineers must keep up with the latest developments in the field to ensure the optimal protection of their electronic devices. Conformal coatings are a crucial part of the electronic manufacturing process and can help to extend the lifespan and performance of electronic devices.