Adhesives for Coating Application
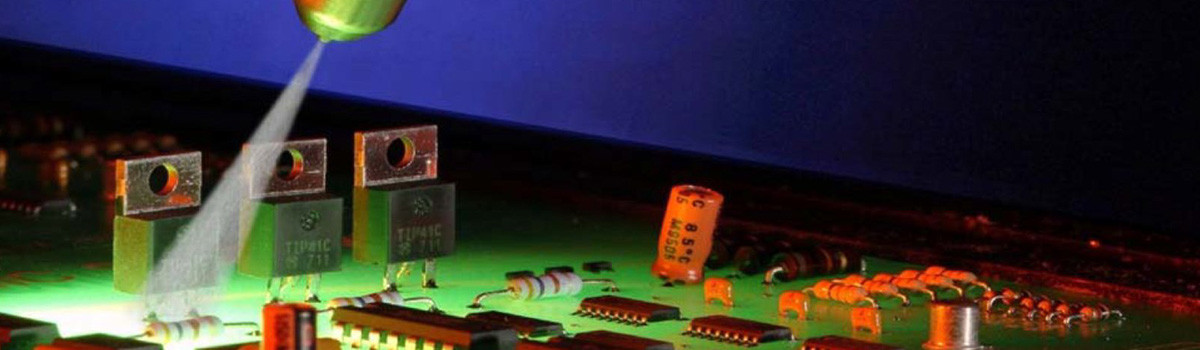
Many adhesive coatings are custom-engineered to solve limitless application challenges. The coating type and technique are carefully selected, often through extensive trial and error, to provide optimal results. Experienced coaters must account for a wide variety of variables and customer preferences before selecting and testing a solution. Adhesive coatings are common and used globally in a multitude of functions. Vinyl can be coated with pressure sensitive adhesives for use in signage, wall graphics, or decorative wraps. Gaskets and “O”-rings can be adhesive coated so they can be permanently affixed to various products and equipment. Adhesive coatings are applied to fabrics and non-woven materials so they can be laminated to hard substrates and provide a soft, protective, finish to secure cargo during transportation.
Variables
There are many factors that go into selecting a viable adhesive coating solution:
Substrates are often materials like paper, wall coverings, corrugated plastic, films and foils. Each has its own unique characteristics such as porosity, tensile strength and chemical resistance.
Release Liners are applied to protect the adhesive from contact and contamination before application. Liners can be made from a variety of materials and work in conjunction with the adhesive coating to control peel strength.
The application surface may be a concrete wall, carpeted floor, vehicle door, window, human skin or many others. The make-up of these surfaces must be taken into consideration when selecting/developing the right chemistry.
Environmental conditions like extreme temperatures, moisture, direct or indirect sunlight, exposure to chemicals, indoor/ outdoor use, etc. will have some impact on adhesion and durability.
Green initiatives may determine selection of emulsion-based (water-based) adhesives over sol- vent (chemical-based) adhesives.
Other factors to consider are compatibility between the adhesive coating and a functional top-coat, type of printer/ink being deployed, and storage conditions.
Chemistry
There are numerous “off-the-shelf” chemistry options available in the marketplace. Sometimes, these chemistries can be used without modification. In many cases, they are modified with additives to optimize their performance.
Surfactants reduce surface tension to improve the rheology of the adhesive. This enables the adhesive to flow better and coat more evenly.
Defoamers may be added to reduce or eliminate the potential for air bubbles to occur within the coating.
Scents can be added for applications where the smell of the adhesive is scrutinized. Stick-to- skin cosmetic products sometimes require “scented” adhesive.
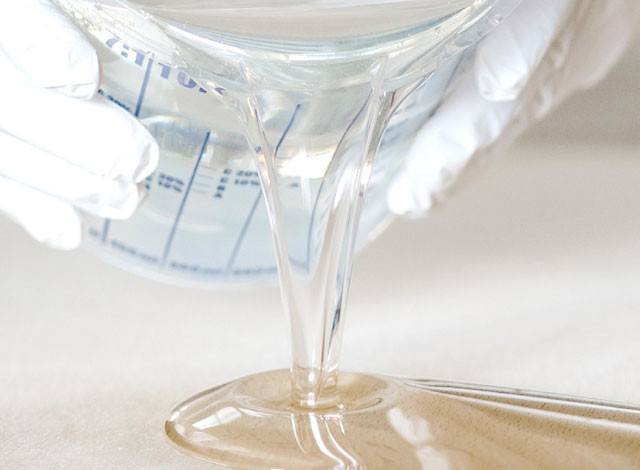
Methods
There are many types of coaters and coating methods. Basic requirements include choosing a coater that can accommodate the size and weight of the web (roll of raw material). State-of-the-art coaters typically have superior speed and tension controls necessary to handle a variety of substrates. Precise tension control is critical when applying coatings to thinner materials like films and foils. Coater selection is contingent on much more than just the physical fit. Different coating methods can be deployed depending on the intended result:
Gravure coating utilizes engraved cylinders that apply a specific amount of coating to the web depending on their engraved volume and the characteristics of the coating fluid. The cylinders are metered with a doctor blade which enables the user to apply precise and consistent coating weights across the web. Gravure coaters are most often used to apply thinner coatings to a web. Gravure coaters can be used for full web coating or pattern coating.
Reverse roll coating incorporates a pickup roll that is partially submerged in a coating pan. The coating fluid is applied to the pickup roll that, in turn, applies the chemistry to an applicator roll. The applicator roll applies the coating fluid to the web. The coating weight is controlled by roll speeds and the gap between the applicator roll and the pickup roll. A third roll, the backup roll, engages the web to the applicator roll and also controls the coating width. This method of coating is most often used to apply medium to heavy coating weights to the web.
Deepmaterial coating uses either an engraved rod or wound rod to meter off excess coating that has been applied to the web via an applicator roll or directly out of a pan. The larger the engraved or wound gaps in the rod, the thicker or heavier the coating weight that is applied to the web. This type of coating offers the ability to do a wide range of coating weights and is very flexible when it comes to the characteristics of the coating chemistries used.
Deepmaterial coating is most often used to apply a very thin coating to a web. A metered roll applies the coating to the web. Coat weights are normally controlled by the speed of the roll. This type of coating is very commonly used to add moisture back into a web, especially papers, to control the curl of the finished product.
In Deepmaterial coating, the web has an excess amount of coating fluid applied to the surface. A knife is situated directly against the surface of the web with a specific gap that meters off excess coating fluid. This gap controls the coating weight. In a similar technique called Air Knife coating, instead of a steel or polymer blade, a focused stream of impinged air is used to meter off the excess coating fluid from the surface of the web. The coat weight is controlled by adjusting the velocity of the impinged air and the distance of the impingement gap from the surface of the web.
Slot Die coating method pumps the coating fluid through a precisely machined gap in a die and on to the surface of the web. The coating weight is controlled by changing the amount of flow through the die or the thickness of the gap in the die. This method of coating is used when precise coating weight control and consistency is required.
Immersion coating is sometimes referred to as “dip coating”. The web is immersed or dipped into a pan or reservoir containing the coating fluid. The web is then passed through two rolls that meter excess coating off the web. The coating weight is controlled by the gap be- tween the two rolls and the speed of rotation of the rolls. This method of coating is often used when saturation of the coating chemistry into the web is required.
Curtain coating uses a precisely slotted coating head that creates a curtain of coating chemistry that falls onto the web traveling perpendicular to the falling coating fluid. This type of coating is used when precise coating weights are required and is also useful for applying multiple wet layers of coating fluid onto the web. This is accomplished by using multiple slots in one coating head, each with separate coating fluids flowing through them.
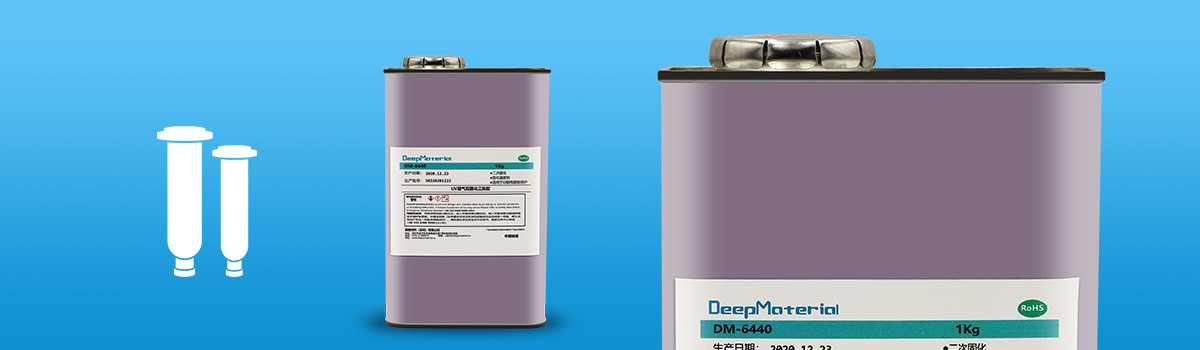
Finishing
Now that the chemistry has been engineered and the coating method is dialed in, drying is the next part of the process. Most coaters have in-line ovens designed to dry or cure the adhesive. Temperature, speed and oven length are all accounted for when optimizing the drying process. Infrared heat is applied in air flotation ovens for even coverage without contacting the web. Type of liner, adhesive, humidity and ambient temperature all have some impact on the drying process. Drying times and speeds are often adjusted during the trial process. Adhesive coatings are initially applied to the liner instead of directly to the substrate. This process is called transfer coating. When the drying process is complete, the substrate is then laminated to the adhesive/liner to produce the finished product.
The process for developing adhesive coatings begins with a concept. From there, a design-of-experiments (DoE) is created as a roadmap toward success. Often, multiple trials are required to perfect the chemistry and application of that chemistry. The end result is a highly engineered solution designed for success.
Deepmaterial manufactures specialty coatings for use in advanced technological applications. Our systems feature protection against moisture, chemicals, abrasion, thermal cycling, elevated temperatures, mechanical shock, etc. They are 100% reactive and contain no solvents or diluents. Ultra low viscosity coatings are available for confined spaces.