Semiconductor Adhesive
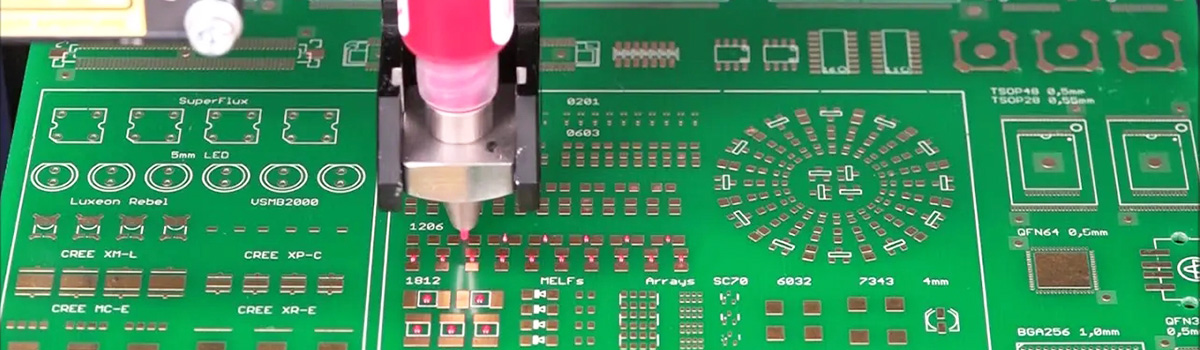
Semiconductor adhesive is a critical component in the manufacturing and assembly of semiconductor devices, such as microprocessors, memory chips, and other integrated circuits. These adhesives provide robust and reliable bonding capabilities and protection against environmental factors and thermal stress. With the increasing demand for smaller, faster, and more complex semiconductor devices, high-performance and reliable adhesive solutions have become more critical than ever. This article will explore the various types, applications, and challenges of semiconductor adhesives, highlighting their crucial role in enabling miniaturization and high performance of semiconductor devices.
Types of Semiconductor Adhesives
Semiconductor adhesives play a crucial role in electronic device manufacturing and assembly processes. These adhesives are designed to provide robust and reliable bonding between various components in semiconductor devices, such as chips, substrates, and packages. They can withstand harsh environmental conditions, thermal cycling, and mechanical stresses. Several types of semiconductor adhesives are available in the market, each with unique properties and applications. Let’s explore some of the commonly used semiconductor adhesives:
- Epoxy Adhesives: Epoxy-based adhesives are widely used in semiconductor applications due to their excellent bonding strength, high chemical resistance, and good electrical insulation properties. They offer strong adhesion to various materials, including metals, ceramics, and plastics. Epoxy adhesives cure at room temperature or under heat, forming a rigid and durable bond.
- Silicone Adhesives: Silicone-based adhesives are known for their flexibility, thermal stability, and resistance to extreme temperatures. Depending on the formulation, they can withstand a wide temperature range from -50°C to 200°C or even higher. Silicone adhesives exhibit excellent electrical insulation properties and are commonly used in applications where thermal management is crucial, such as power electronic devices.
- Acrylic Adhesives: Acrylic adhesives provide fast curing, high bond strength, and good resistance to temperature and moisture. They are known for their versatility and can bond to various substrates, including metals, plastics, and glass. Acrylic adhesives, such as automotive electronics and LED assembly, are often used in applications requiring high strength and durability.
- Polyurethane Adhesives: Polyurethane-based adhesives offer a balance between flexibility and strength. They provide good adhesion to various materials, including metals, plastics, and glass. Polyurethane adhesives are resistant to impact, vibration, and thermal cycling, making them suitable for applications where mechanical stresses are involved, such as in automotive and aerospace electronics.
- Conductive Adhesives: Conductive adhesives are formulated with conductive fillers, such as silver, copper, or carbon, to enable electrical conductivity in bonded joints. They are commonly used for electronic devices’ die-attach, flip-chip bonding, and interconnecting components. Conductive adhesives offer low resistance and excellent adhesion, providing reliable electrical connections.
- Underfill Adhesives: Underfill adhesives are designed explicitly for flip-chip applications, where the chip is mounted upside down on a substrate. These adhesives flow under the chip during curing, filling the gaps between the chip and the substrate. Underfill adhesives provide mechanical support, enhance thermal conductivity, and prevent solder joint failures caused by thermal stress.
- UV Curable Adhesives: UV curable adhesives cure rapidly when exposed to ultraviolet light. They offer high bond strength, optical clarity, and chemical resistance. UV-curable adhesives are often used in applications requiring fast processing and precision bonding, such as display assembly, fiber optics, and optoelectronic devices.
Epoxy Adhesives: The Most Common Choice
Epoxy adhesives are widely recognized as one of the most common and versatile types. They are extensively used in various industries and applications due to their exceptional bonding strength, durability, and versatility. Here, we will explore why epoxy adhesives are the most common choice within a limited word count.
- Bonding Strength: Epoxy adhesives offer exceptional bonding strength, making them suitable for various materials. Whether it’s metals, plastics, ceramics, wood, or composites, epoxy adhesives provide solid and reliable bonds, ensuring the longevity and stability of the joined parts.
- Versatility: Epoxy adhesives exhibit excellent versatility in their application methods and curing options. They are available in different forms, such as one-part or two-part systems, allowing flexibility in their usage. Additionally, epoxy adhesives can be cured at room temperature or with heat, depending on the application’s specific requirements.
- Chemical Resistance: Epoxy adhesives possess exceptional chemical resistance, making them ideal for applications where exposure to harsh chemicals or solvents is a concern. They maintain their structural integrity even when exposed to various chemicals, oils, fuels, and acids, ensuring the durability of bonded assemblies.
- Temperature Resistance: Epoxy adhesives can withstand a wide temperature range, making them suitable for applications that require resistance to high or low temperatures. Whether in the automotive, aerospace, or electronic industries, epoxy adhesives provide reliable bonding even in extreme temperatures.
- Gap Filling Ability: Another advantage of epoxy adhesives is their ability to fill gaps and irregularities between mating surfaces. This characteristic ensures a strong bond even when the contact surfaces are not ideally matched, providing enhanced structural integrity to the joined parts.
- Mechanical Properties: Epoxy adhesives offer excellent mechanical properties, such as high tensile and shear strength and good impact resistance. These properties make them suitable for load-bearing applications, where the adhesive needs to withstand significant stress or impact without compromising the bond strength.
- Electrical Insulation: Epoxy adhesives exhibit excellent electrical insulation properties, making them popular in electronic and electrical applications. They provide effective insulation, protecting sensitive electronic components from electrical currents or short circuits.
- Ease of Use: Epoxy adhesives are relatively easy to use and apply. They can be dispensed precisely, allowing for controlled application and minimizing wastage. Furthermore, epoxy adhesives have a long open time, providing sufficient working time to assemble the parts before the adhesive sets.
Conductive Adhesives: Enabling Electrical Connectivity
Conductive adhesives are a specialized type of adhesive material with both adhesive and conductive properties. They are designed to enable electrical connectivity in various applications where traditional soldering methods may not be feasible or desirable. These adhesives offer numerous advantages, including ease of use, environmental friendliness, and versatility.
One of the critical benefits of conductive adhesives is their ease of use. Unlike soldering, which requires heat and can be complex, conductive adhesives can be applied simply by dispensing or spreading the adhesive onto the desired surfaces. This makes them suitable for a wide range of users, from professionals to hobbyists and eliminates the need for specialized equipment.
Environmental friendliness is another advantage of conductive adhesives. Unlike soldering, which typically involves lead-based solders, conductive adhesives can be formulated with non-toxic materials. This makes them more environmentally friendly and safer to handle, reducing health risks for users. Additionally, the absence of lead makes these adhesives compliant with regulations restricting hazardous substances’ use.
Conductive adhesives also offer versatility in the materials they can bond together. They can join conductive materials like metals and non-conductive materials like plastics, ceramics, and glass. This broad compatibility allows for creating multi-material assemblies with integrated electrical connectivity, opening up new design possibilities in various industries.
The conductivity of these adhesives is achieved by including conductive fillers, such as silver or carbon particles, within the adhesive matrix. These fillers form conductive pathways that enable the flow of electrical current across the bonded surfaces. The choice of filler material and concentration can be tailored to meet specific conductivity requirements, allowing for fine-tuning of the adhesive’s electrical properties.
Applications of conductive adhesives are widespread. They are commonly used in the electronics industry for bonding components, replacing or complementing soldering processes. Conductive adhesives are particularly beneficial for joining delicate electronic components that cannot withstand the high temperatures associated with soldering. They are also used to manufacture flexible circuits, RFID tags, and touchscreens, where their ability to bond to various substrates is advantageous.
In the automotive industry, conductive adhesives assemble sensors, control units, and lighting systems. Their non-mechanical bonding capabilities reduce stress concentration points, improving electrical connection reliability and longevity. Furthermore, conductive adhesives enable weight reduction in vehicles by eliminating the need for heavy metal connectors.
Beyond electronics and automotive applications, conductive adhesives find use in medical devices, aerospace components, and even consumer products like wearable electronics. Their versatility, ease of use, and environmental advantages make them attractive to industrial designers and engineers.
Die Attach Adhesives: Bonding Semiconductor Chips to Substrates
Die attach adhesives play a crucial role in the semiconductor industry by providing a reliable and efficient method for bonding semiconductor chips to substrates. These adhesives serve as the interface between the chip and the substrate, ensuring a secure and electrically conductive connection.
The primary function of die-attached adhesives is to provide mechanical support and electrical connectivity between the chip and the substrate. They must possess excellent adhesion properties to ensure the chip remains securely attached to the substrate under various operating conditions, including thermal cycling, mechanical stress, and environmental exposure.
One critical requirement for die-attach adhesives is their ability to withstand high temperatures. During chip assembly processes such as solder reflow or thermocompression bonding, the adhesive must maintain its integrity and adhesion strength. Typically, die-attach adhesives are designed to withstand temperatures above 200°C, ensuring bond reliability.
Die attach adhesives are commonly classified into epoxy-based and solder-based adhesives. Epoxy-based adhesives are thermosetting materials that cure upon exposure to heat. They offer excellent adhesion, high thermal conductivity, and electrical insulation. On the other hand, solder-based adhesives consist of a metal alloy that melts during the bonding process. They provide a low-resistance electrical path and high thermal conductivity, making them suitable for high-power dissipation applications.
The selection of die-attached adhesive depends on several factors, including the specific application, operating conditions, and substrate material. The adhesive must be compatible with the materials it will be bonded to, ensuring proper adhesion and preventing any adverse interactions. The adhesive must also have good dispensing and flow characteristics to facilitate bonding and minimize voids or gaps between the chip and substrate.
To achieve a reliable bond, surface preparation is essential. The substrate and chip surfaces must be thoroughly cleaned to remove contaminants, oxides, and other impurities hindering adhesion. Surface treatment techniques such as plasma cleaning, chemical etching, or ultrasonic cleaning are commonly employed to enhance the adhesive’s bonding performance.
Once the die attach adhesive is applied, the chip is carefully positioned and aligned on the substrate. Pressure or heat may be used to ensure proper wetting and contact between the adhesive and the surfaces being bonded. The adhesive is then cured or solidified, completing the bonding process.
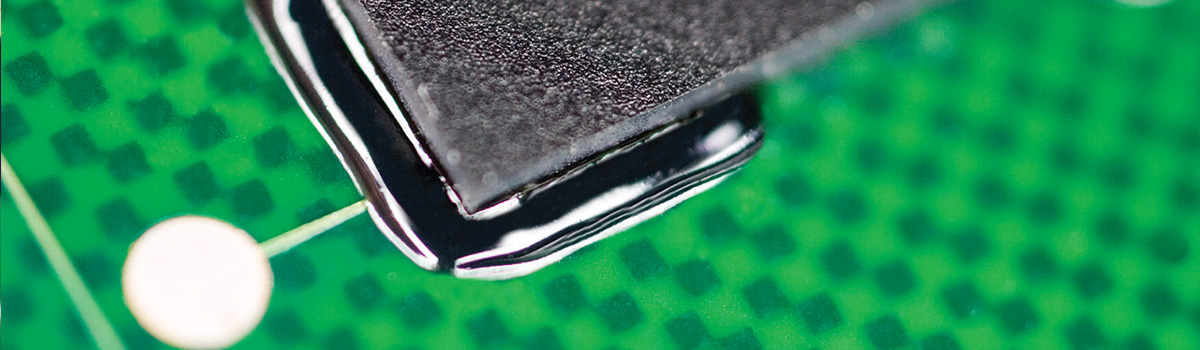
Underfill Adhesives: Protecting Against Thermal Stress
Underfill adhesives are essential materials used in electronic packaging to protect against thermal stress. They provide mechanical reinforcement and improve the reliability of electronic devices by minimizing the impact of thermal cycling and mechanical shocks.
Thermal stress is a significant concern in electronic assemblies due to the mismatch in coefficients of thermal expansion (CTE) between different materials. When a device undergoes temperature fluctuations, the materials expand and contract at different rates, developing stresses that can fail. Underfill adhesives help mitigate this issue by acting as a buffer between the chip and the substrate, absorbing and distributing the stress caused by thermal cycling.
Underfill adhesives’ primary function is to reinforce the solder joints that connect the integrated circuit (IC) chip to the substrate. During manufacturing, the chip is mounted on the substrate using solder, which creates a bond between the two components. However, the CTE mismatch between the chip and the substrate can cause stress concentrations at the solder joints. Underfill adhesives are injected into the gap between the chip and the substrate, filling the voids and forming a robust and elastic layer. This layer reduces the stress concentration, enhancing the overall mechanical integrity of the assembly.
Underfill adhesives also offer excellent thermal conductivity, crucial for dissipating heat generated by electronic components. Efficient heat dissipation is vital to prevent overheating and maintain the performance and longevity of the device. By facilitating heat transfer from the chip to the substrate, underfill adhesives help maintain a stable operating temperature and prevent thermal stress from damaging the IC.
Moreover, underfill adhesives protect against moisture and contaminants. Electronic devices are often exposed to harsh environments, including humidity and various chemicals, which can degrade their performance and reliability. Underfill materials are a barrier, preventing moisture ingress and the diffusion of harmful substances into the chip package. This protection helps maintain electrical performance and extend the device’s lifespan.
Flip Chip Adhesives: Enabling Miniaturization
Flip chip adhesives are crucial in enabling miniaturization in various electronic devices. As technology advances, there is a constant demand for smaller, lighter, and more powerful machines. Flip-chip bonding has emerged as a preferred method for achieving high-density interconnections in such devices. These adhesives facilitate the direct electrical and mechanical connection between the chip and the substrate, offering numerous benefits to miniaturization.
One of the critical advantages of flip-chip adhesives is their ability to reduce the overall size of electronic packages. Traditional wire bonding techniques require space for wire loops, limiting the achievable device size. In contrast, flip-chip bonding eliminates the need for wire loops, significantly reducing package size. The smaller footprint is significant in portable electronic devices, such as smartphones, tablets, and wearables, where space is a premium.
Additionally, flip-chip adhesives enable increased device performance. The direct electrical connection between the chip and the substrate reduces signal path lengths and inductance, improving electrical performance. This is particularly important for high-speed applications, such as microprocessors and memory chips, where minimizing signal delay and loss is critical. Flip chip bonding contributes to faster data transfer rates, lower power consumption, and enhanced device reliability by reducing parasitic effects.
Moreover, flip-chip adhesives offer excellent thermal management capabilities. Managing heat dissipation becomes a significant challenge as electronic components become more powerful and densely packed. Flip chip bonding allows for a direct attachment of the chip to the substrate, which enhances heat transfer efficiency. This enables efficient heat dissipation, preventing overheating and improving the overall reliability and lifespan of the device. Effective thermal management is essential for high-performance devices like graphics processing units (GPUs) and central processing units (CPUs).
Another advantage of flip-chip adhesives is their mechanical stability. The adhesive materials used in flip-chip bonding provide solid and reliable interconnections. The absence of wire bonds eliminates the risk of wire breakage or fatigue, ensuring long-term mechanical integrity. The robustness of flip-chip adhesives makes them suitable for applications subjected to harsh operating conditions, such as automotive electronics or aerospace systems.
Furthermore, flip-chip adhesives support high-density interconnects. With flip-chip bonding, it is possible to achieve a large number of connections in a small area, allowing for the integration of more functionality within a limited space. This is particularly beneficial for complex electronic devices that require numerous input/output connections, such as integrated circuits, sensors, or microelectromechanical systems (MEMS). The high-density interconnects enabled by flip-chip adhesives contribute to the overall miniaturization of the device.
Encapsulation Adhesives: Protecting Sensitive Components
Encapsulation adhesives are essential in protecting sensitive electronic components from various environmental factors, mechanical stress, and chemical exposure. These adhesives provide a protective barrier, encapsulating the elements and ensuring their longevity and reliability. This article will explore the importance of encapsulation adhesives and their role in safeguarding sensitive components.
Sensitive electronic components, such as integrated circuits, sensors, and delicate wiring, are vulnerable to damage caused by moisture, dust, temperature fluctuations, and physical impact. Encapsulation adhesives offer a reliable solution by forming a protective layer around these components. They act as a barrier, shielding the components from external elements that could compromise functionality or lead to premature failure.
One of the critical properties of encapsulation adhesives is their ability to resist moisture ingress. Moisture can cause corrosion, short circuits, and electrical leakage, leading to device malfunction. Encapsulation adhesives provide excellent moisture resistance, preventing the entry of water or moisture vapor into the sensitive components. This feature is crucial in applications exposed to high humidity or moisture-rich environments, such as automotive electronics or outdoor industrial equipment.
In addition to moisture protection, encapsulation adhesives also offer excellent chemical resistance. They can withstand exposure to various chemicals, including solvents, acids, bases, and cleaning agents. This resistance ensures that the sensitive components remain unaffected by chemical interactions, preserving their integrity and functionality.
Encapsulation adhesives also provide mechanical protection to sensitive components. They act as shock absorbers, dissipating mechanical stress and vibrations that could damage the components. This feature is vital in applications subjected to frequent movements, such as aerospace, automotive, and consumer electronics.
Furthermore, encapsulation adhesives offer excellent thermal management properties. They possess high thermal conductivity, allowing efficient heat dissipation from the sensitive components. These adhesives help maintain optimal operating temperatures by dissipating heat effectively, preventing thermal stress, and ensuring long-term reliability.
Another advantage of encapsulation adhesives is their ability to enhance the structural integrity of electronic assemblies. Encapsulating and bonding various components together provides additional strength and stability to the overall system. This feature is especially beneficial in applications where mechanical robustness is essential, such as industrial control systems or military-grade electronics.
Encapsulation adhesives come in various formulations to cater to different application requirements. They can be liquid adhesives that cure at room temperature or thermally conductive compounds used for high-power applications. The selection of the appropriate adhesive depends on factors such as the desired level of protection, operating conditions, cure time, and assembly process.
Low Outgassing Adhesives: Critical for Space Applications
Low-outgassing adhesives play a critical role in space applications where maintaining a clean and controlled environment is essential. Outgassing refers to releasing volatile organic compounds (VOCs) and other contaminants from materials, including adhesives, under vacuum or low-pressure conditions. Outgassing can harm sensitive equipment, optical systems, and spacecraft surfaces in the extreme conditions of space, where there is no atmospheric pressure. Therefore, using low-outgassing adhesives is paramount to ensure space missions’ reliable performance and longevity.
One of the primary concerns with outgassing is the deposition of contaminants onto critical surfaces, such as optical lenses and sensors. Impurities can form a thin film on these surfaces, reducing their transparency, degrading performance, and interfering with scientific measurements. In the case of optical systems, even a slight reduction in openness can significantly impact the quality of images and data collected from space. Low-outgassing adhesives are designed to minimize the release of volatile compounds, reducing the risk of contamination and preserving the functionality of sensitive instruments.
Another critical aspect of low-outgassing adhesives is their impact on electronic components and circuitry. VOCs released during outgassing can corrode or degrade delicate electronic systems, leading to malfunctions or complete failure. This is particularly concerning for spacecraft, where electronic components are exposed to the vacuum of space, extreme temperature variations, and radiation. Low-outgassing adhesives are formulated with low vapor pressure materials, minimizing the release of corrosive compounds and protecting the integrity of electronic systems.
Furthermore, outgassing can also threaten astronauts’ health and the habitability of crewed spacecraft. In closed environments like space capsules or space stations, the accumulation of VOCs from outgassing can create an unpleasant or hazardous atmosphere. Low-outgassing adhesives help mitigate this risk by reducing the emission of volatile compounds, ensuring a safe and healthy environment for astronauts during their missions.
To achieve low outgassing properties, adhesives used in space applications undergo rigorous testing and qualification processes. These processes involve subjecting the adhesives to simulated space conditions, including vacuum chambers, extreme temperatures, and various environmental stresses. Adhesives that meet the stringent requirements for low outgassing are certified and approved for use in space missions.
Wafer Level Bonding Adhesives: Reducing Costs and Enhancing Yield
Wafer-level bonding is a crucial process in the semiconductor industry, where multiple chips or wafers are interconnected to form complex integrated circuits. Traditionally, this bonding process involved solder bumps or wire bonding techniques, which require precise alignment and individual bonding of each chip, resulting in higher costs and lower yields. However, advancements in adhesive technologies have paved the way for wafer-level bonding adhesives that offer cost reduction and enhanced yield in semiconductor manufacturing.
Wafer-level bonding adhesives are designed to provide a reliable and robust bond between wafers or chips at the wafer level, eliminating the need for individual bonding processes. These adhesives are typically applied as a thin layer between the wafers and are cured under controlled conditions to achieve the desired bond strength. Here are some key factors contributing to the cost reduction and enhanced yield:
- Process Simplification: Wafer-level bonding adhesives simplify the bonding process by enabling the simultaneous bonding of multiple chips or wafers in a single step. This eliminates the need for intricate alignment and individual bonding of each chip, saving time and reducing production costs. Additionally, the adhesive can be applied uniformly over a large area, ensuring consistent adhesion across the wafer.
- High Bond Strength and Reliability: Wafer-level bonding adhesives offer excellent adhesion properties, resulting in high bond strength between the wafers. This robust bond ensures reliable interconnectivity and minimizes the risk of delamination or failure during subsequent manufacturing steps or device operation. The adhesive’s mechanical, thermal, and electrical properties can be tailored to meet specific application requirements, further enhancing reliability.
- Cost-Effective Materials: Wafer-level bonding adhesives often utilize cost-effective materials compared to traditional bonding techniques. These adhesives can be formulated using a variety of polymers, such as epoxies, polyimides, or acrylates, which are readily available and offer good performance at a reasonable cost. Choosing from various materials enables manufacturers to optimize the adhesive selection based on performance, price, and compatibility with different substrates.
- Yield Improvement: Wafer-level bonding adhesives contribute to improved yield in semiconductor manufacturing. The uniform application of adhesive across the wafer minimizes the risk of voids, air entrapment, or uneven bonding, which can lead to defects or failures. Moreover, eliminating individual chip bonding reduces the chances of misalignment or damage during the bonding process, resulting in higher yields and reduced scrap rates.
- Compatibility with Advanced Packaging Technologies: Wafer-level bonding adhesives are compatible with various advanced packaging technologies, such as wafer-level chip-scale packaging (WLCSP), fan-out wafer-level packaging (FOWLP), or 3D integration processes. These adhesives enable the integration of multiple chips or diverse components within a compact form factor, facilitating miniaturization and enabling advanced functionality in electronic devices.

UV Curing Adhesives: Rapid and Precise Bonding
UV-curing adhesives are revolutionary adhesives that offer rapid and precise bonding capabilities. They have gained popularity in various industries due to their unique properties and advantages over traditional adhesives. UV-curing adhesives are typically composed of a monomer, a photoinitiator, and a stabilizer. When exposed to ultraviolet (UV) light, these adhesives undergo a photochemical reaction that leads to rapid curing and bonding.
One of the critical benefits of UV-curing adhesives is their fast curing time. Unlike traditional bonds that require hours or even days to cure fully, UV-curing adhesives cure within seconds to minutes. This rapid curing time significantly increases production efficiency and reduces assembly line waiting times, resulting in significant cost savings for manufacturers. The instant bond formation also allows for immediate handling and further processing of bonded components.
The precise bonding ability of UV-curing adhesives is another significant advantage. The adhesive remains liquid until exposed to UV light, providing ample time for the alignment and positioning of the parts to be bonded. Once the adhesive is exposed to UV light quickly solidifies, creating a solid and durable bond. This precise bonding capability benefits applications requiring high accuracy and tight tolerances, such as electronics, optics, and medical devices.
UV-curing adhesives also offer excellent bond strength and durability. The cured adhesive forms a strong bond that can withstand various environmental factors, including temperature extremes, moisture, and chemicals. This ensures the longevity and reliability of the bonded components, making UV-curing adhesives suitable for demanding applications.
Furthermore, UV-curing adhesives are solvent-free and have low volatile organic compound (VOC) emissions. Unlike solvent-based adhesives that require drying and release potentially harmful vapors, UV-curing adhesives are environmentally friendly and safe. This makes them an attractive choice for industries aiming to reduce their environmental footprint and comply with regulations.
The versatility of UV-curing adhesives is another notable aspect. They can bond various materials, including glass, metals, plastics, ceramics, and even dissimilar substrates. This broad compatibility makes UV-curing adhesives suitable for diverse applications across the automotive, aerospace, electronics, and medical industries.
Conductive Paste Adhesives: Enabling Flexible and Printed Electronics
Conductive paste adhesives have emerged as a critical enabling technology for developing flexible and printed electronics. These innovative materials combine traditional adhesives’ properties with metals’ conductivity, opening up new possibilities for the manufacturing and integration of electronic devices on various substrates.
One of the main advantages of conductive paste adhesives is their ability to provide both mechanical adhesion and electrical conductivity. Traditional adhesives are typically insulating, which limits their use in electronic applications. Conductive paste adhesives, conversely, contain conductive particles such as silver, copper, or carbon that facilitate the flow of electricity. This dual functionality allows them to serve as both an adhesive and a conductive pathway, making them ideal for bonding electronic components or creating conductive traces on flexible substrates.
The flexibility of conductive paste adhesives is another critical characteristic that makes them suitable for flexible electronics. These adhesives can maintain their electrical conductivity even when subjected to bending, stretching, or twisting. This flexibility is crucial for applications such as wearable devices, flexible displays, and conformal electronics, where traditional rigid circuits would be impractical or impossible to implement. Conductive paste adhesives enable the creation of robust and reliable electrical connections on flexible substrates, ensuring the performance and durability of flexible electronic devices.
Moreover, conductive paste adhesives are compatible with various printing techniques, such as screen printing, inkjet printing, and flexographic printing. This compatibility allows for the high-volume and cost-effective manufacturing of printed electronics. Printing processes enable the deposition of conductive paste adhesives in precise patterns, making it possible to create complex circuits and electronic designs with minimal material wastage. The ability to print conductive traces directly onto flexible substrates simplifies the fabrication process and reduces production time, making printed electronics a viable solution for large-scale manufacturing.
Conductive paste adhesives also offer advantages in terms of thermal management. The presence of conductive particles in these adhesives facilitates heat dissipation generated by electronic components. This property is crucial for ensuring the reliability and performance of devices that generate significant heat, such as power electronics or high-power LEDs. Using conductive paste adhesives as thermal interfaces, heat can be efficiently transferred from the heat-generating component to a heat sink, improving overall device performance and longevity.
Soldering Pastes: Alternative to Adhesive Bonding
Soldering pastes, also known as solder pastes, offer an alternative to adhesive bonding in various applications. While adhesive bonding involves using adhesives to join materials, soldering pastes utilize a different mechanism to achieve a robust and reliable bond. In this response, we will explore soldering pastes as an alternative to adhesive bonding within a limit of 450 words.
Soldering pastes consist of a mixture of metal alloy particles, flux, and a binder. The metal alloy particles typically consist of tin, lead, silver, or a combination of these metals. The change aids in the soldering process by removing oxides from the metal surfaces and promoting wetting and adhesion. The binder holds the paste together and allows it to be applied easily.
One of the primary advantages of soldering pastes over adhesive bonding is the strength and durability of the bond. Soldering creates a metallurgical bond between the joined materials, resulting in a strong joint that can withstand various mechanical, thermal, and electrical stresses. The soldered joint is often more robust and reliable than adhesive bonds, which may degrade over time or under certain conditions.
Soldering pastes also offer a quicker and more efficient bonding process. The paste can be applied precisely to the desired areas, and the joint can be formed by heating the assembly to the solder’s melting temperature. This process is often faster than adhesive bonding, which may require curing or drying times. Moreover, soldering pastes enable the simultaneous joining of multiple components, reducing assembly time and increasing productivity.
Another advantage is the versatility of soldering pastes in joining different materials. Adhesive bonding may have limitations when bonding dissimilar materials or materials with different coefficients of thermal expansion. Soldering pastes can form reliable joints between various materials, including metals, ceramics, and some plastics, making them suitable for diverse applications.
Additionally, soldering pastes can improve thermal and electrical conductivity compared to adhesive bonding. This property is especially beneficial in applications where heat dissipation or electrical continuity is crucial, such as electronic assemblies—the soldered joint forms a direct metallic pathway, facilitating efficient heat transfer and electrical conduction.
However, it is essential to note that soldering pastes also have some considerations and limitations. For instance, some solder alloys contain lead, which may be restricted due to environmental and health concerns. Lead-free soldering pastes have been developed as alternatives, but they may have different characteristics and require specific process considerations.
Adhesive Dispensing Techniques: Precision and Efficiency
Adhesive dispensing techniques are crucial in various industries, from manufacturing to construction. Achieving precision and efficiency in adhesive application is essential for ensuring reliable bonds, minimizing waste, and improving overall productivity. This article will explore critical techniques that help achieve precision and efficiency in adhesive dispensing.
- Automated Dispensing Systems: Automated dispensing systems utilize robotic arms or computer-controlled equipment to apply adhesives precisely. These systems offer high repeatability, accuracy, and speed, ensuring consistent adhesive application across multiple parts or products. By eliminating human error, automated systems minimize waste and enhance efficiency in adhesive dispensing processes.
- Metering and Mixing Systems: Some applications require dispensing two or more components that need to be mixed in a specific ratio. Metering and mixing systems precisely measure and combine the adhesive components before distributing, ensuring accurate ratios and consistent quality. These systems are particularly beneficial for two-part epoxies, polyurethanes, and other reactive adhesives.
- Pressure-Controlled Dispensing: Pressure-controlled dispensing techniques involve using pneumatic or hydraulic systems to control the flow rate and pressure of the adhesive. The adhesive is dispensed at a controlled rate by maintaining a consistent force, ensuring precise application, and minimizing excess adhesive. Pressure-controlled dispensing is commonly used for applications that require fine lines, dots, or intricate patterns.
- Jetting and Needle Dispensing: Jetting and needle dispensing techniques are suitable for applications that require high-speed and precise adhesive placement. Jetting systems use pressure pulses to dispense tiny droplets or continuous adhesive lines. On the other hand, needle dispensing involves using a needle or nozzle to deposit adhesive in controlled amounts. These techniques are commonly used in electronics assembly, where small, precise adhesive deposits are required.
- Spray and Coating Systems: For large-area bonding or coating applications, spray and coating systems provide efficient adhesive dispensing. These systems utilize atomization techniques to create a fine mist or spray of adhesive, ensuring even coverage and minimal waste. Spray and coating systems are widely used in the automotive, aerospace, and furniture manufacturing industries.
- Dispensing Valves and Nozzles: The choice of dispensing valves and nozzles is crucial for achieving precision in adhesive dispensing. Different types of valves and nozzles, such as needle valves, diaphragm valves, or tapered nozzles, offer varying control over flow rate, pattern, and droplet size. Selecting the appropriate valve or nozzle for the specific adhesive and application requirements is essential for achieving precise and efficient dispensing.
- Vision-Guided Systems: Vision-guided dispensing systems use cameras and advanced software to detect and track the position of parts or substrates. Analyzing the captured images, the system adjusts the adhesive dispensing parameters in real time, ensuring accurate placement even on irregular surfaces or varying part dimensions. Vision-guided systems enhance precision and efficiency while accommodating process variations.
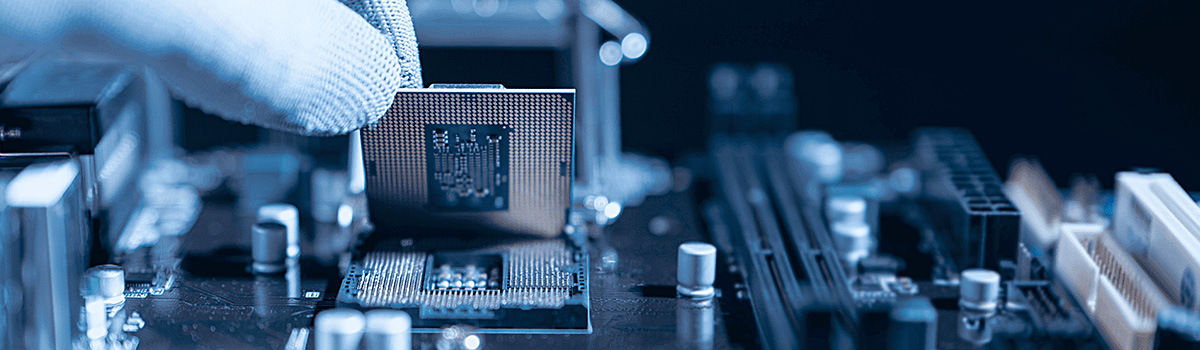
Challenges in Semiconductor Adhesive Application
Semiconductor adhesive application faces several challenges that can impact the performance and reliability of electronic devices. These challenges arise due to the unique requirements and characteristics of semiconductors and the demanding operating conditions they are subjected to. Here are some of the critical challenges in semiconductor adhesive application:
- Thermal Management: Semiconductors generate heat during operation, and effective thermal management is crucial to prevent overheating. Adhesive materials used in semiconductors must have excellent thermal conductivity to transfer heat from the device efficiently. Ensuring proper adhesion without compromising thermal performance is a significant challenge.
- Chemical Compatibility: Semiconductors are exposed to various chemicals during their lifespan, including cleaning agents, solvents, and fluxes. Adhesive materials should be chemically compatible with these substances to avoid degradation or loss of adhesion over time. Selecting adhesive materials that can withstand exposure to specific chemicals is a complex task.
- Mechanical Stress: Electronic devices often experience mechanical stress due to thermal expansion, vibrations, and external forces. To withstand these stresses, adhesive materials must have suitable mechanical properties, such as flexibility and strength. Poor adhesive performance can lead to the semiconductor device’s delamination, cracking, or mechanical failure.
- Miniaturization: With the ongoing trend of miniaturization, semiconductor devices are becoming increasingly smaller and more complex. Adhesive application in such miniature structures requires high precision and control. Ensuring uniform coverage, avoiding voids, and maintaining consistent bond line thickness become critical challenges.
- Process Compatibility: Semiconductor manufacturing involves multiple processing steps, including cleaning, deposition, and packaging. Adhesive materials should be compatible with these processes without negatively affecting their performance. Challenges arise in finding adhesives that can withstand high-temperature processes, resist moisture, and maintain stability throughout the manufacturing cycle.
- Reliability and Aging: Semiconductor devices are expected to have long lifespans and reliable performance under various operating conditions. Adhesive materials must exhibit long-term stability, resistance to aging, and reliable adhesion over extended periods. The challenge lies in predicting and mitigating potential degradation mechanisms that could impact the performance and reliability of the semiconductor device.
- Environmental Considerations: Adhesive materials used in semiconductor applications must adhere to environmental regulations and standards.
- This includes limiting hazardous substances, such as lead and other toxic materials. Developing environmentally friendly adhesive solutions that meet regulatory requirements without compromising performance can be challenging.
- Cost and Scalability: Adhesive materials should be cost-effective and scalable to meet the demands of high-volume semiconductor production. Balancing cost considerations with performance requirements poses a challenge in selecting suitable adhesive materials and optimizing the application process.
Reliability Testing: Assessing Adhesive Performance
Reliability testing is an essential process for assessing the performance of adhesives. Adhesives are commonly used in various industries, including automotive, aerospace, electronics, and construction, where they play a critical role in joining different materials together. The reliability of adhesives is crucial to ensure bonded assemblies’ durability and long-term functionality.
One key aspect of reliability testing is evaluating the adhesive’s strength and adhesion properties. This involves subjecting adhesive samples to different stress conditions to simulate real-world scenarios and determine their performance under various loads, temperatures, and environmental conditions. Tensile, shear, and peel tests are commonly conducted to assess the adhesive’s mechanical properties and ability to withstand forces in different directions.
In addition to mechanical testing, environmental factors play a significant role in adhesive performance. Adhesives may be exposed to extreme temperatures, humidity, chemical substances, and UV radiation during service life. Therefore, reliability testing involves subjecting sticky samples to accelerated aging tests, where they are exposed to harsh environmental conditions for an extended period. This helps to predict the adhesive’s long-term performance and assess its resistance to degradation, such as loss of adhesion strength or chemical deterioration.
Another important aspect of reliability testing is assessing the adhesive’s durability under cyclic loading. In many applications, adhesives are subjected to repeated mechanical stress, such as vibration or thermal cycling. Fatigue testing evaluates the adhesive’s resistance to failure under these cyclic loads. The samples are typically subjected to a specified number of load cycles, and their performance is monitored for any signs of adhesive shortcomings, such as crack propagation or bond delamination.
Furthermore, reliability testing involves evaluating the adhesive’s performance in real-world conditions. This may include testing the adhesive’s ability to bond different materials commonly used in the industry, such as metals, plastics, composites, or glass. The samples are prepared using standardized procedures and subjected to testing protocols that simulate the specific application requirements. This allows engineers to assess the adhesive’s compatibility with different substrates and evaluate its bond strength, flexibility, and resistance to environmental factors.
Reliability testing also includes assessing the adhesive’s chemical compatibility with other substances it may contact during its application or service life. This involves conducting compatibility tests to determine if the adhesive reacts adversely with solvents, cleaning agents, fuels, or other chemicals that may be present in the environment. Chemical compatibility testing helps identify potential issues that could lead to adhesive failure or degradation.
In conclusion, reliability testing is a crucial step in assessing adhesive performance. It involves evaluating mechanical properties, conducting accelerated aging tests, assessing durability under cyclic loading, evaluating performance in real-world conditions, and testing chemical compatibility. By conducting comprehensive reliability testing, manufacturers and engineers can ensure adhesives’ suitability and long-term performance in their intended applications.
Environmental Considerations in Semiconductor Adhesive
Semiconductor adhesives play a critical role in the assembly and packaging of electronic devices, particularly in the semiconductor industry. While these adhesives provide essential functions such as bonding and thermal management, it is vital to consider their environmental impact throughout their lifecycle. Here are some crucial environmental considerations in semiconductor adhesive:
- Toxicity: Many semiconductor adhesives contain hazardous substances, including volatile organic compounds (VOCs), heavy metals, and other toxic chemicals. These substances can have adverse effects on human health and the environment. Minimizing or eliminating harmful ingredients in adhesive formulations is crucial to reduce their environmental impact.
- Emissions: During the manufacturing and application of semiconductor adhesives, volatile components can be released into the air, contributing to air pollution. VOC emissions, for example, can contribute to ground-level ozone and harmful particulate matter formation. Manufacturers should strive to develop low-VOC adhesive formulations and implement stringent emission control measures to mitigate these environmental impacts.
- Energy Consumption: Producing semiconductor adhesives requires energy-intensive processes, including synthesis, blending, and curing. Reducing energy consumption through process optimization and using energy-efficient technologies can minimize the environmental footprint associated with adhesive manufacturing.
- Waste Generation: The semiconductor industry generates significant waste, and adhesives contribute to this waste stream. Waste can include unused or expired adhesives, packaging materials, and manufacturing byproducts. Implementing waste management practices such as recycling, reusing, or safe disposal of adhesive waste is essential to minimize environmental pollution and resource depletion.
- Lifecycle Analysis: Considering semiconductor adhesives’ entire lifecycle is crucial in comprehensively assessing their environmental impact. This analysis includes evaluating the ecological footprint of raw material extraction, manufacturing, transportation, application, and end-of-life disposal. Identifying opportunities for improvement at each stage can lead to more sustainable adhesive solutions.
- Sustainable Alternatives: Exploring and adopting sustainable alternatives is essential in reducing the environmental impact of semiconductor adhesives. This can involve using bio-based or renewable raw materials, developing water-based or solvent-free formulations, and employing environmentally friendly manufacturing processes. Promoting adhesive recycling or implementing circular economy practices can also contribute to resource conservation.
- Regulatory Compliance: Adhesive manufacturers must comply with environmental regulations and standards governing chemical use, disposal, and labeling. To ensure ecological and human health protection, staying updated with relevant regulations, such as REACH (Registration, Evaluation, Authorization, and Restriction of Chemicals) in the European Union and similar regulations in different regions, is crucial.
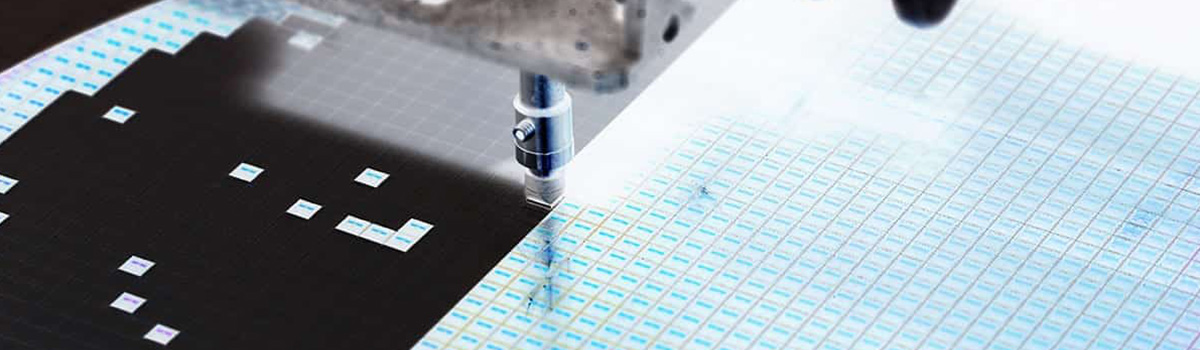
Trends and Innovations in Semiconductor Adhesive
Semiconductor adhesive plays a crucial role in the assembly and packaging of electronic devices, ensuring the proper bonding and stability of semiconductor components. As technology advances, several key trends and innovations emerge in the semiconductor adhesive field.
- Miniaturization and Higher Device Complexity: One significant trend in the semiconductor industry is the ongoing miniaturization of electronic devices and the increasing complexity of their designs. This trend requires adhesives with improved properties, such as lower viscosity, higher bond strength, and enhanced thermal conductivity, to accommodate smaller and more densely packed components.
- Advanced Packaging Techniques: Advanced packaging techniques, such as system-in-package (SiP), fan-out wafer-level packaging (FOWLP), and 3D packaging, are gaining popularity due to their ability to improve device performance and reduce form factor. These techniques often require specialized adhesives that can handle the unique challenges of interconnecting multiple dies and components within a small footprint.
- Thermal Management: As electronic devices become more powerful and compact, effective thermal management becomes increasingly critical. Semiconductor adhesives with excellent thermal conductivity properties are being developed to facilitate heat dissipation from the semiconductor devices, preventing overheating and ensuring optimal performance.
- Low-Temperature Curing: Traditional semiconductor adhesives often require high-temperature curing processes, which can be problematic for temperature-sensitive components or substrates. Innovations in low-temperature curing adhesives enable bonding at significantly lower temperatures, reducing the risk of thermal damage to delicate semiconductor materials.
- Novel Material Formulations: Researchers are exploring new material formulations for semiconductor adhesives to meet evolving requirements. This includes the development of electrically conductive adhesives (ECAs) that provide bonding and electrical conductivity, eliminating the need for soldering in specific applications. Additionally, new materials such as flexible adhesives are being introduced to accommodate the increasing demand for flexible and bendable electronic devices.
- Environmental Considerations: Sustainability and environmental impact are gaining more attention in the semiconductor industry. Adhesive manufacturers focus on developing eco-friendly formulations with reduced volatile organic compounds (VOCs) and hazardous substances while maintaining excellent performance characteristics.
- Process Optimization and Automation: With the increasing demand for semiconductor devices, there is a growing need for efficient and automated manufacturing processes. Adhesive manufacturers collaborate with equipment suppliers to optimize adhesive dispensing and curing processes, ensuring consistent and reliable results while reducing production cycle times.
- Reliability and Durability: Semiconductor devices are expected to operate reliably over extended periods, often in harsh environments. Adhesive innovations aim to improve device reliability by enhancing adhesion strength, resistance to moisture, temperature, and various environmental factors.
Application Areas: Consumer Electronics, Automotive, Aerospace, and More
Consumer Electronics:
Consumer electronics is one of the most prominent application areas for technological advancements. It encompasses many devices such as smartphones, tablets, laptops, smart TVs, wearable devices, and home appliances. In recent years, consumer electronics have seen significant performance, functionality, and connectivity developments. For example, smartphones have become more powerful, offering advanced features like high-resolution cameras, artificial intelligence integration, and augmented reality capabilities. Intelligent TVs now support 4K and even 8K resolution and smart home integration for enhanced entertainment experiences. Wearable devices such as smartwatches and fitness trackers have gained popularity for their health monitoring and fitness-tracking capabilities.
Automotive:
The automotive industry has experienced remarkable advancements, primarily driven by technology. Modern vehicles have sophisticated electronics and software systems that enhance safety, efficiency, and user experience. One of the critical areas of development is autonomous driving, with self-driving cars becoming a reality. These vehicles rely on advanced sensors, artificial intelligence algorithms, and connectivity to navigate roads and make intelligent decisions. Additionally, automotive applications include:
- Infotainment systems.
- Advanced driver-assistance systems (ADAS).
- In-car connectivity.
- Electric vehicle technology.
- Vehicle-to-vehicle communication.
Aerospace:
The aerospace industry relies heavily on advanced technologies to improve safety, efficiency, and performance. Aerospace applications include aircraft design and manufacturing, space exploration, satellite systems, and air traffic management. Computer-aided design (CAD) and simulation tools help engineers create more aerodynamic and fuel-efficient aircraft in aircraft design. Satellite systems provide global communication, weather monitoring, and navigation services. The aerospace industry also leverages advanced materials, such as composites and lightweight alloys, to reduce weight and increase fuel efficiency. In space exploration, robotics, remote sensing, and propulsion systems enable missions to explore celestial bodies and gather scientific data.
Healthcare:
Technology plays a crucial role in healthcare, transforming the industry in various ways. Medical devices and equipment, such as MRI machines, ultrasound scanners, and robotic surgery systems, have revolutionized diagnostics and treatment procedures. Electronic health records (EHRs) and telemedicine allow healthcare professionals to access patient information and provide remote care. Wearable devices and health monitoring systems enable individuals to track their vital signs and receive personalized healthcare recommendations. Artificial intelligence and machine learning algorithms are employed for disease diagnosis, drug discovery, and predictive analytics, leading to improved patient outcomes and customized medicine.
Industrial Automation:
Industrial automation involves using advanced technologies to automate manufacturing processes and improve productivity. Robotics and robotic arms are extensively used for tasks like assembly, welding, and material handling. Internet of Things (IoT) devices and sensors are deployed to collect real-time data and optimize operational efficiency. Machine vision systems enable quality control and inspection, ensuring products meet stringent standards. Advanced control systems and predictive maintenance algorithms help minimize downtime and maximize production output. Industrial automation can increase efficiency, reduce costs, and enhance safety across various industries, including manufacturing, logistics, and energy.
Future Prospects and Opportunities
The future is full of exciting prospects and opportunities, driven by rapid technological advancements, shifting societal needs, and evolving global trends. Here, we explore some key areas with significant growth and development potential.
- Artificial Intelligence (AI) and Automation: AI is transforming industries across the board, enhancing efficiency, productivity, and decision-making. As AI technologies mature, there will be increasing opportunities for AI specialists, data scientists, and engineers. Automation will continue to streamline processes, leading to job creation in robotics, machine learning, and intelligent systems.
- Renewable Energy and Sustainability: With the growing concern over climate change, there is a massive demand for renewable energy solutions. The transition to cleaner sources like solar, wind, and hydroelectric power presents numerous prospects. Careers in renewable energy engineering, energy management, and sustainable development will be pivotal in shaping a greener future.
- Healthcare and Biotechnology: Advancements in medical research, personalized medicine, and gene editing are revolutionizing the healthcare industry. Opportunities abound in bioinformatics, genetic counseling, telemedicine, and pharmaceutical development. The intersection of technology and healthcare will drive innovation, leading to better patient care and improved outcomes.
- Cybersecurity and Data Privacy: As our reliance on digital systems continues to increase, so does the need for robust cybersecurity measures. Cyber threats are becoming more sophisticated, creating a demand for cybersecurity experts, ethical hackers, and data privacy specialists. Protecting sensitive information and developing secure infrastructure will be crucial for organizations and individuals.
- E-commerce and Digital Marketing: E-commerce has transformed how we shop, creating new avenues for businesses. Online retail platforms, digital marketing, and social media advertising have become essential for thriving companies. Careers in e-commerce management, digital content creation, and customer experience optimization will continue to be in high demand.
- Space Exploration and Commercialization: Space exploration has shifted from government-led initiatives to commercial ventures, opening up opportunities in aerospace engineering, satellite technology, and space tourism. Private companies are investing in space travel, resource mining, and satellite communication, paving the way for a new era of space exploration.
- Sustainable Agriculture and Food Systems: With the global population expected to reach 9 billion by 2050, ensuring food security and sustainable agriculture practices is critical. Vertical farming, precision agriculture, and alternative protein sources offer potential for innovation. Careers in agricultural technology, agronomy, and food science will play a vital role in meeting future food demands.
- Virtual Reality (VR), Augmented Reality (AR), and Extended Reality (XR): These technologies have the potential to revolutionize entertainment, education, training, and various industries. VR/AR developers, content creators, and immersive experience designers will shape the future of entertainment, gaming, and virtual collaboration.
- Financial Technology (Fintech): The integration of technology and finance has resulted in the rise of Fintech, offering new financial services, digital payment solutions, and blockchain technology. Careers in financial analytics, cybersecurity in banking, and blockchain development are expected to be in high demand.
- Sustainability Consulting and Green Architecture: As sustainability becomes a priority, companies and individuals seek guidance on reducing their carbon footprint and adopting eco-friendly practices. Sustainable consultants, green architects, and environmental engineers will be instrumental in designing and implementing sustainable solutions.
Importance of Collaboration in Advancing Semiconductor Adhesive Technology
Collaboration is vital in advancing semiconductor adhesive technology, driving innovation, and ensuring its successful implementation in various industries. The semiconductor industry is highly complex and rapidly evolving, requiring interdisciplinary expertise and stakeholder cooperation.
- Diverse Expertise: Semiconductor adhesive technology encompasses multiple disciplines, including materials science, chemistry, engineering, and manufacturing. Collaboration brings together experts from various fields, each contributing specialized knowledge and skills. By combining diverse expertise, the partnership enables the development of novel adhesive materials and techniques that can enhance semiconductor devices’ performance, reliability, and durability.
- Knowledge Exchange: Collaboration facilitates the exchange of knowledge and information among researchers, engineers, and industry professionals. Through collaborative efforts, individuals can share their insights, experiences, and research findings, leading to a deeper understanding of adhesive materials and their applications. This knowledge exchange can help identify emerging trends, address technical challenges, and accelerate the development of innovative solutions.
- Enhanced Research and Development: Collaborative research and development efforts enable the pooling of resources in terms of funding and equipment. This allows for more extensive experimentation, testing, and analysis, leading to faster discovery and innovation. By working together, researchers can access specialized facilities, cutting-edge technologies, and advanced characterization tools that may not be available individually. Such resources can significantly contribute to the advancement of semiconductor adhesive technology.
- Industry-University Collaboration: Collaboration between industry and academia is crucial for translating research findings into practical applications. Universities can conduct fundamental research and explore new concepts, while industry partners bring real-world perspectives and practical considerations. This collaboration ensures that adhesive technology developments align with market needs and can be integrated into industrial processes. Industry-university association also promotes technology transfer, enabling academic research to have a tangible impact on commercial applications.
- Standardization and Quality Assurance: Collaboration among industry players fosters the development of standards and guidelines for semiconductor adhesive technology. Standards help ensure consistency, compatibility, and reliability across different products and manufacturing processes. Collaborative efforts can establish best practices, testing methodologies, and quality control procedures, which are essential for guaranteeing semiconductor devices’ performance and long-term reliability.
- Market Expansion and Competitiveness: Collaboration among companies operating in the semiconductor industry can lead to market expansion and increased competitiveness. Companies can combine their resources, knowledge, and market insights by working together to develop adhesive solutions that meet specific industry requirements. Collaborative efforts can also facilitate the adoption of adhesive technology in new applications and emerging markets, further driving the semiconductor industry’s growth.
Conclusion:
Semiconductor adhesive plays a vital role in enabling the miniaturization and high-performance of semiconductor devices. The ability of these adhesives to provide strong bonding capabilities, protection against environmental factors and thermal stress, and electrical conductivity is crucial in the manufacturing and assembly of microprocessors, memory chips, and other integrated circuits. As technology continues to advance, the development of innovative adhesive solutions and collaboration between manufacturers, researchers, and end-users will be crucial in meeting the growing demands and challenges of the semiconductor industry. By harnessing the potential of semiconductor adhesive, we can pave the way for even smaller, faster, and more complex semiconductor devices that drive our modern world.