Plastic Bonding Adhesive
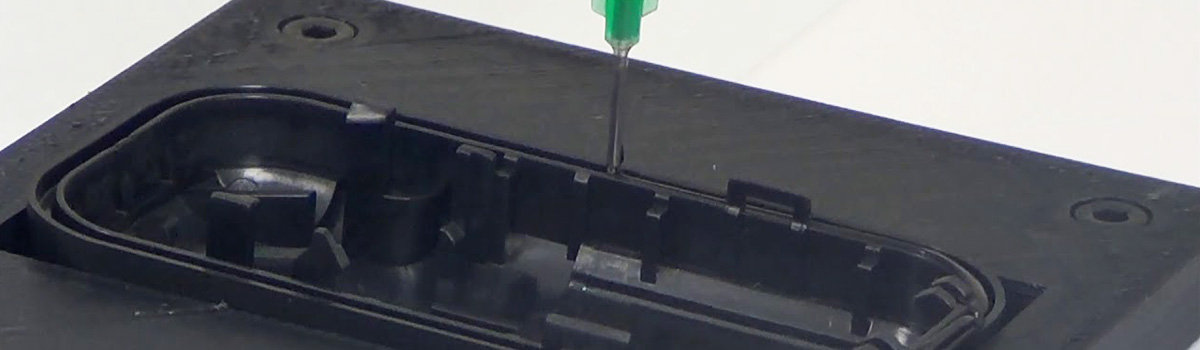
Introduction: Plastic bonding adhesives are essential for joining plastic materials together in a range of industries, including automotive, aerospace, and electronics. These adhesives have become increasingly popular due to their ability to create a strong bond between plastic materials. In this ultimate guide to plastic bonding adhesives, we will cover everything you need to know about these adhesives, including their types, benefits, and applications.
What are Plastic Bonding Adhesives?
Plastic bonding adhesives are specially formulated adhesives designed to bond different types of plastics together. They are used in various industries, including automotive, aerospace, electronics, and consumer goods.
Plastic bonding adhesives work by chemically bonding with the surface of the plastic, creating a solid and durable bond. These adhesives can bond with different plastics, including polyethylene, polypropylene, polycarbonate, ABS, and PVC.
Several types of plastic bonding adhesives are available, including cyanoacrylate, epoxy, and acrylic adhesives. Cyanoacrylate adhesives are fast-setting and provide strong bonds, while epoxy adhesives are known for their strength and durability. Acrylic adhesives offer good resistance to weathering and UV light.
When choosing a plastic bonding adhesive, it is essential to consider the specific requirements of the application, such as the type of plastic being bonded, the strength required, and the environmental conditions the bond will be subjected to.
Types of Plastic Bonding Adhesives
Several types of plastic bonding adhesives are available, each with unique properties and intended applications. Here are some common types of plastic bonding adhesives:
- Cyanoacrylate (super glue) – This fast-acting adhesive is excellent for bonding plastics together quickly. It forms a strong bond in seconds but can be brittle and unsuitable for high-stress applications.
- Epoxy is a two-part adhesive that creates a strong bond between plastics. It can be used on various plastic surfaces, including polyethylene and polypropylene.
- Acrylic – Acrylic adhesives are versatile and can bond various plastics. They can also bond plastics to other materials, such as metal and glass.
- Polyurethane – This adhesive is known for its robust and flexible bond. It can be used on various plastic surfaces, including PVC and ABS.
- Structural adhesives are designed for high-stress applications, such as bonding plastic parts in the automotive and aerospace industries. They offer excellent bonding strength and can withstand extreme temperatures and pressures.
Choosing the correct type of plastic bonding adhesive for your specific application is essential, as each style has strengths and limitations.
Benefits of Using Plastic Bonding Adhesives
Plastic bonding adhesives offer several benefits over other adhesives or bonding methods. Here are some of the key benefits of using plastic bonding adhesives:
- Versatility: Plastic bonding adhesives can bond a wide range of plastics, including many types that are difficult to connect with other adhesives or bonding methods.
- Strength: Plastic bonding adhesives can provide high-strength bonds, often more substantial than bonded materials. This is especially true for structural bonding applications.
- Durability: Many plastic bonding adhesives are highly resistant to environmental factors such as moisture, temperature, and chemicals, making them ideal for harsh or demanding environments.
- Speed: Many plastic bonding adhesives cure quickly, allowing for rapid assembly and production.
- Aesthetics: Plastic bonding adhesives can provide nearly invisible bonds, improving the aesthetics of finished products.
- Cost savings: Plastic bonding adhesives can be more cost-effective than other bonding methods because they often require less material and labor and can reduce or eliminate the need for mechanical fasteners.
Plastic bonding adhesives offer a versatile, high-strength, durable, and cost-effective solution for bonding plastics in various applications.
Applications of Plastic Bonding Adhesives
Plastic bonding adhesives are specialized types of adhesives that are designed to bond plastics together. They are widely used in a variety of industries and applications, including:
- Automotive industry: Plastic bonding adhesives manufacture vehicles for bonding plastic parts together, such as bumpers, dashboards, and interior trims.
- Electronics industry: These adhesives are used to produce electronic devices, such as smartphones and laptops, to bond plastic components together.
- Medical industry: Plastic bonding adhesives are used in medical devices and equipment, such as syringes and catheters, for bonding plastic parts together.
- Aerospace industry: These adhesives are used in aircraft and spacecraft manufacturing for bonding plastic parts together.
- Packaging industry: Plastic bonding adhesives produce packaging materials, such as plastic containers and bottles, for bonding plastic parts.
- Construction industry: These adhesives are used to construct buildings and structures for bonding plastic materials together, such as plastic roof tiles and panels.
Overall, plastic bonding adhesives are essential in industries where plastic materials are widely used, as they provide a solid and durable bond between plastic components, creating complex and innovative designs.
Factors to Consider When Choosing Plastic Bonding Adhesives
When choosing plastic bonding adhesives, several factors must be considered to ensure that you select the suitable adhesive for your specific application. Some of the critical factors to consider include:
- Type of plastics being bonded: The variety of related plastic materials will determine the adhesive needed. Some plastics are more difficult to bond than others and may require specialized adhesives.
- Bonding strength: The required strength will depend on the application. For instance, a weak bond may be sufficient for a low-stress application, while a strong bond may be necessary for a high-stress application.
- Cure time: The time required for the adhesive to fully cure will determine the speed of the bonding process. Some adhesives cure quickly, while others need a longer healing time.
- Chemical resistance: The adhesive must resist exposure to any chemicals or solvents that may come into contact with the bonded plastics.
- Temperature resistance: The adhesive must be able to withstand the temperature range of the application. Some adhesives may break down or weaken under high temperatures, while others may become brittle at low temperatures.
- Ease of use: The adhesive should be easy to apply and work with and should not require specialized equipment or extensive training.
- Cost: The adhesive’s cost should be considered, as some adhesives may be more expensive than others.
Overall, selecting the suitable plastic bonding adhesive involves understanding the application’s specific requirements and choosing an adhesive that is easy to work with and cost-effective.
Surface Preparation for Plastic Bonding Adhesives
Surface preparation is a critical step in the plastic bonding adhesive process, as it ensures that the adhesive can form a solid and durable bond with the plastic surface. Some of the critical surface preparation steps for plastic bonding adhesives include:
- Cleaning: The plastic surfaces to be bonded must be thoroughly cleaned to remove any dirt, dust, grease, or other contaminants that may interfere with the bonding process. Cleaning can be done using a mild detergent or solvent, and the surfaces should be wiped dry with a clean cloth.
- Abrasion: In some cases, it may be necessary to abrade the plastic surface to increase the surface area and promote adhesion. Abrasion can be done using sandpaper or a wire brush, but care should be taken not to damage the plastic surface.
- Degreasing: Some plastics may require degreasing to remove any oils or other surface contaminants that may be present. Degreasing can be done using a solvent or a specialized degreasing solution.
- Etching: Etching the plastic surface can also improve adhesion by creating a rougher surface texture. Etching can be done using a chemical etchant or flame treatment.
- Drying: After surface preparation, the plastic surface must dry completely before applying the adhesive. Any residual moisture can interfere with the bonding process and weaken the bond.
Proper surface preparation is critical to the success of plastic bonding adhesives. By following these steps, you can ensure that the adhesive can form a strong and durable bond with the plastic surface, resulting in a high-quality and long-lasting bond.
Techniques for Applying Plastic Bonding Adhesives
Plastic bonding adhesives are used to join plastic materials together. These adhesives come in various types, including cyanoacrylate, epoxy, polyurethane, and acrylic adhesives. Here are some techniques for applying plastic bonding adhesives:
- Surface preparation: Before applying any plastic bonding adhesive, it is essential to prepare the surfaces that will be bonded. This involves cleaning the surfaces to remove any dust, dirt, or grease that could interfere with the bonding process. Sanding the surface with fine-grit sandpaper can also help to create a rougher surface that will provide better adhesion.
- Mixing: If using a two-part epoxy adhesive, thoroughly mixing the two components before application is essential. This can be done by mixing the components with a stirring stick or using a mixing nozzle that attaches to the adhesive container.
- Dispensing: When dispensing the adhesive, it is essential to apply it evenly and correctly. For example, a small drop is usually sufficient for a strong bond if using a cyanoacrylate adhesive. If using an epoxy or polyurethane adhesive, the adhesive should be applied in a thin layer that covers the entire surface area to be bonded.
- Clamping: Depending on the type of adhesive used, clamping may be necessary to hold the surfaces together while the adhesive cures. This can help to ensure a strong bond and prevent any movement that could cause the bond to fail. The time required for clamping will vary depending on the adhesive used, so be sure to follow the manufacturer’s instructions.
- Curing: Once the adhesive has been applied and any necessary clamping has been done, the adhesive will need time to cure. The time required for curing will depend on the type of adhesive used and factors such as temperature and humidity. Following the manufacturer’s instructions for fixing time is essential to ensure a strong bond.
Following these techniques for applying plastic bonding adhesives can create strong and durable bonds between plastic materials.
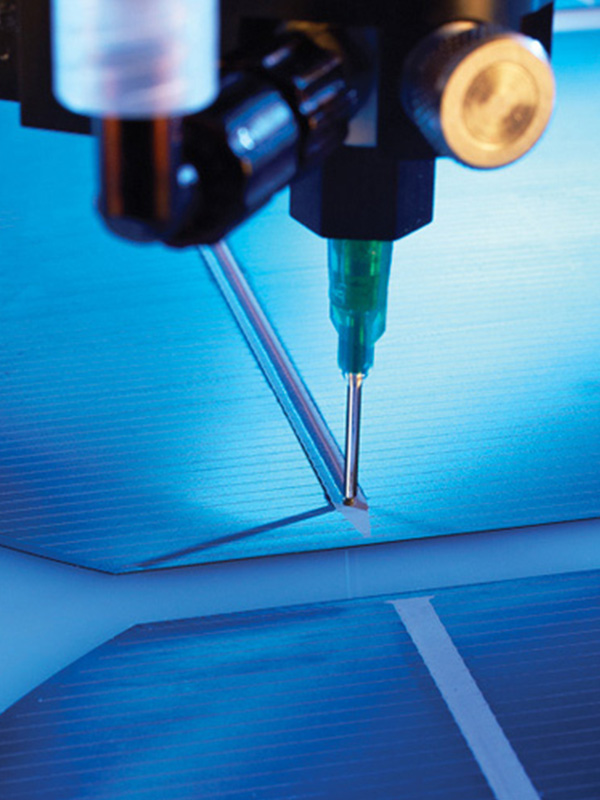
Common Mistakes to Avoid When Using Plastic Bonding Adhesives
When using plastic bonding adhesives, there are some common mistakes that you should avoid to ensure a successful bond. Here are a few examples:
- Not preparing the surface: The surface of the plastic must be clean, dry, and free of any contaminants, such as dust, oil, or grease. Please properly prepare the surface to ensure a strong bond.
- Using the wrong adhesive: Different plastics require different types of adhesives. Choose the correct adhesive compatible with the plastic you are bonding.
- Applying too much adhesive: Using too much adhesive can result in a messy bond, and excess adhesive can create a weak spot. Apply the adhesive sparingly and follow the instructions carefully.
- Rushing the bonding process: Bonding plastic takes time, and rushing the process can result in a weak bond. Follow the instructions on the adhesive and allow sufficient time for the bond to cure.
- Not clamping the pieces together: Clamping the pieces together during bonding can help ensure a strong bond. Make sure to use the appropriate clamping pressure for the type of adhesive being used.
- Not testing the bond: Before relying on the bond for a critical application, testing its strength is essential. This can be done by applying a small amount of pressure to the bonded pieces or performing a stress test.
Avoiding these common mistakes can ensure a strong and long-lasting bond when using plastic bonding adhesives.
Advancements in Plastic Bonding Adhesives
Some of the critical advancements in plastic bonding adhesives include:
- Improved strength and durability: Modern plastic bonding adhesives are designed to provide more robust and durable bonds than traditional adhesives. They are formulated with advanced polymers that withstand extreme temperatures, moisture, and chemicals.
- Faster curing time: Many new plastic bonding adhesives are designed to cure quickly, reducing the time needed for assembly and allowing for shorter production times.
- Improved environmental friendliness: Many new plastic bonding adhesives are formulated with eco-friendly materials that minimize the ecological impact of manufacturing and usage.
- Better adhesion to a broader range of materials: New plastic bonding adhesives have been developed to bond to a broader range of materials, including difficult-to-bond plastics such as polypropylene and polyethylene.
- Increased versatility: Plastic bonding adhesives can now be used in various applications, including aerospace, automotive, electronics, and medical devices.
- Enhanced safety and health features: New plastic bonding adhesives have been developed with improved safety and health features, such as low VOC emissions and non-toxic formulations.
Overall, advancements in plastic bonding adhesives have led to more robust, durable, and versatile bonds that can be used in a broader range of applications while minimizing environmental impact and promoting safety and health.
How Plastic Bonding Adhesives Compare to Other Joining Techniques
Plastic bonding adhesives can be a very effective way to join plastic parts, and they offer several advantages over other joining techniques:
- Robust and Durable Bond: Plastic bonding adhesives create a solid and durable bond between the plastic parts, often more potent than other joining techniques such as welding or mechanical fasteners.
- No Need for Drilling or Welding: Bonding adhesives can be applied without drilling or welding, saving time and reducing the risk of damage to plastic parts.
- Improved Aesthetics: Bonding adhesives create a seamless and smooth bond between the plastic parts, which can enhance the overall appearance of the finished product.
- Increased Design Flexibility: Bonding adhesives can join plastic parts with different shapes and sizes, increasing design flexibility and simplifying assembly.
- Reduced Weight: Bonding adhesives can be a lightweight option for joining plastic parts, as they do not add weight to the finished product.
However, plastic bonding adhesives also have some potential drawbacks to consider:
- Surface Preparation: Proper surface preparation is critical for achieving a solid bond and may require additional time and resources.
- Little Gap Filling: Bonding adhesives could more effectively fill significant gaps between plastic parts.
- Temperature Sensitivity: Some bonding adhesives may be sensitive to temperature and perform poorly in extreme heat or cold.
- Curing Time: Bonding adhesives may require some curing time before the parts can be used, impacting production timelines.
Ultimately, the choice of joining technique will depend on the product’s specific application and requirements. Plastic bonding adhesives can be a good option for many applications, but it is essential to carefully consider the advantages and potential drawbacks before deciding.
Strength and Durability of Plastic Bonding Adhesives
The strength and durability of plastic bonding adhesives depend on several factors, including the type of adhesive, the substrate materials being bonded, and the environmental conditions to which the adhesive will be exposed.
Generally, plastic bonding adhesives are designed to provide robust, long-lasting bonds between plastic materials. Standard plastic bonding adhesives include cyanoacrylate (super glue), two-part epoxies, polyurethane adhesives, and acrylic adhesives.
When selecting a plastic bonding adhesive, it is essential to consider the specific type of plastic being bonded, as different plastics have different properties and may require other adhesives. Additionally, the surface preparation of the substrate materials can also impact the strength and durability of the bond.
In terms of environmental conditions, factors such as temperature, humidity, and exposure to UV radiation can all affect the performance of plastic bonding adhesives. Choosing an adhesive designed to withstand the specific conditions the bond will be exposed to is essential.
Overall, when used correctly and in the appropriate conditions, plastic bonding adhesives can provide strong, durable bonds between plastic materials.
Resistance to Environmental Factors
Resistance to environmental factors refers to an organism’s ability to withstand and survive in various environments or conditions. Organisms that have developed resistance to environmental factors have evolved mechanisms that allow them to adapt to changes in their surroundings and maintain their biological functions.
Some common examples of environmental factors that organisms may need to resist include:
- Temperature: Organisms must maintain a stable internal temperature to function correctly. Some organisms have evolved mechanisms to regulate their body temperature, while others have developed resistance to extreme temperatures.
- Water availability: Organisms require water to survive, and some have evolved the ability to withstand drought conditions or live in environments with low water availability.
- pH: Organisms have an optimal pH range to survive and function. Some have adapted to living in environments with extreme pH levels, such as acidic or alkaline conditions.
- Salinity: Some organisms, such as marine animals and plants, have developed resistance to high salinity levels.
- Toxins: Many organisms have resisted toxins through natural selection or by developing mechanisms to detoxify harmful substances.
Overall, resistance to environmental factors is essential to an organism’s survival and can play a crucial role in determining which species can thrive in a given environment.
Chemical Resistance of Plastic Bonding Adhesives
The chemical resistance of plastic bonding adhesives depends on the type of adhesive and the specific chemicals it will be exposed to. Most plastic bonding adhesives are generally resistant to water, oils, and some solvents but may not be immune to other chemicals or substances.
Some common types of plastic bonding adhesives and their chemical resistance include:
- Epoxy: Epoxy adhesives are highly resistant to water and most solvents but may not be immune to solid acids or bases.
- Cyanoacrylate: Cyanoacrylate adhesives resist oils and most solvents but may not be immune to water or strong acids.
- Polyurethane: Polyurethane adhesives resist water, oils, and most solvents but may not be immune to some acids and bases.
- Acrylic adhesives are resistant to water, oils, and most solvents but may not be immune to solid acids or bases.
It is essential to select the appropriate adhesive for the specific application and environment in which it will be used. The manufacturer’s datasheet or technical information should provide guidance on the adhesive’s chemical resistance properties, and compatibility testing with the materials and chemicals involved is always recommended to ensure the bond will perform as expected.
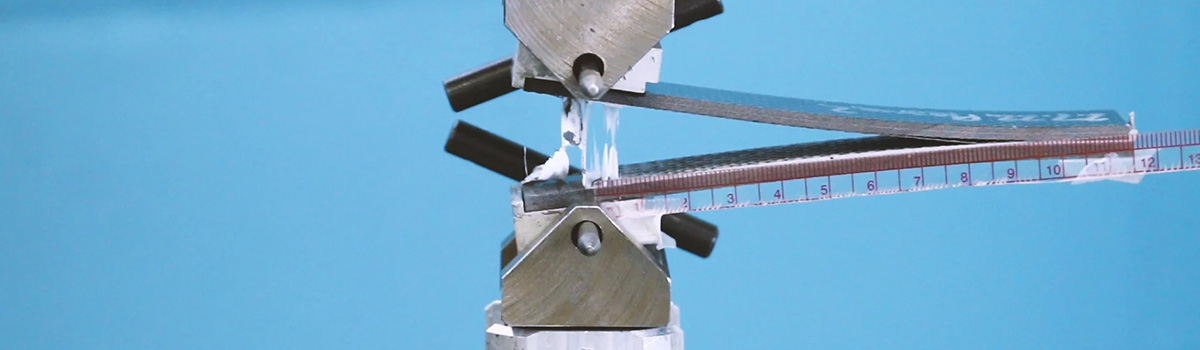
Temperature Resistance of Plastic Bonding Adhesives
The temperature resistance of plastic bonding adhesives depends on various factors such as the type of adhesive, the substrate being bonded, the temperature range, and the duration of exposure.
Some plastic bonding adhesives can withstand temperatures ranging from -40°C to 150°C, while others can withstand even higher temperatures up to 250°C or more. However, it is important to note that the strength and durability of the bond may deteriorate at higher temperatures.
In general, epoxy and acrylic adhesives have good temperature resistance and can withstand high temperatures. Cyanoacrylate adhesives, also known as superglues, have lower temperature resistance and may become brittle or weaken at high temperatures.
When selecting a plastic bonding adhesive, it is important to consider the specific temperature range and duration of exposure to ensure that the adhesive will maintain its strength and durability under the intended conditions of use. Additionally, it is important to follow the manufacturer’s recommendations for application and curing to ensure the best possible bond strength and temperature resistance.
Cure Time for Plastic Bonding Adhesives
The cure time for plastic bonding adhesives can vary depending on the specific adhesive and the conditions in which it is used. In general, cure time refers to the time it takes for the adhesive to reach its maximum strength and for the bonded surfaces to fully adhere.
Some plastic bonding adhesives can cure quickly in a few minutes, while others may take several hours or even days to reach maximum strength. The curing time can also be affected by temperature, humidity, and the type and condition of the bonded surfaces.
It is essential to follow the manufacturer’s instructions for the specific adhesive, including recommended curing time and other important information about application and handling. Failure to follow the manufacturer’s instructions could result in a weaker bond or other issues with the adhesion.
Shelf Life of Plastic Bonding Adhesives
The shelf life of plastic bonding adhesives can vary depending on the specific product and storage conditions. However, most plastic bonding adhesives have a shelf life of around one year if stored properly.
To ensure the longest possible shelf life of plastic bonding adhesives, storing them in a cool, dry place, away from direct sunlight and extreme temperatures, is essential. Additionally, it is necessary to keep the adhesive containers tightly sealed to prevent air exposure, which can cause the adhesive to dry out or cure prematurely.
It is always a good practice to check the expiration date or recommended shelf life of the adhesive before using it and discard any expired adhesive that shows signs of deterioration, such as thickening, discoloration, or separation of components. Using expired or deteriorated adhesives can result in poor bonding performance and compromise the quality and durability of the bond.
Compatibility of Plastic Bonding Adhesives with Different Plastics
The compatibility of plastic bonding adhesives with different plastics can vary depending on the adhesive type and the plastic being bonded. Generally, plastic bonding adhesives can be divided into two main categories: structural and non-structural.
Structural adhesives are used for high-stress applications and typically provide a robust and permanent bond. They can be further divided into two categories: two-part and one-part adhesives. Two-part adhesives consist of a resin and a hardener that must be mixed together before application. They can bond with various plastics, including ABS, PVC, polycarbonate, and nylon. One-part structural adhesives typically do not require mixing and can connect a variety of plastics, including polypropylene, polyethylene, and PET.
Non-structural or “instant adhesives” are used for low-stress applications and provide a fast, easy bond. They can bond various plastics, including polystyrene, PVC, and acrylic.
It is important to note that the compatibility of plastic bonding adhesives with different plastics can be affected by various factors, such as surface preparation, curing time, and temperature. Therefore, it is recommended to consult the manufacturer’s recommendations and conduct a compatibility test before bonding different types of plastics together.
Safety Considerations for Plastic Bonding Adhesives
When using plastic bonding adhesives, it is essential to take safety precautions to prevent potential hazards. Here are some safety considerations for working with plastic bonding adhesives:
- Read the safety data sheet (SDS) provided by the manufacturer before handling the adhesive. The SDS includes essential information on handling, storage, disposal, and first aid measures in case of accidental exposure.
- Wear appropriate personal protective equipment (PPE), such as gloves, safety glasses, and respirators, as specified in the SDS. Avoid skin and eye contact with the adhesive and its vapors.
- Work in a well-ventilated area to prevent inhalation of adhesive vapors. Use exhaust fans, open windows, or wear respirators as necessary to reduce exposure.
- Store adhesives in a cool, dry, and well-ventilated area, away from sources of ignition and incompatible materials. Follow storage instructions provided by the manufacturer.
- Avoid smoking, eating, or drinking in areas where adhesives are used or stored.
- Clean up spills or leaks promptly using appropriate cleanup methods and PPE. Do not touch or inhale spilled adhesive.
- Dispose of adhesive and empty containers according to local regulations and manufacturer’s instructions. Do not dispose of bonds in household or municipal waste.
- Follow the adhesive’s recommended curing time and temperature before handling bonded parts. Improper curing can result in weak bonds and potential safety hazards.
Following these safety considerations can minimize the risk of injury or exposure when working with plastic bonding adhesives.
Storage and Handling of Plastic Bonding Adhesives
Plastic bonding adhesives are often used in industrial settings to combine plastic parts. Proper storage and handling of these adhesives are critical to ensure their effectiveness and shelf life. Here are some guidelines for storing and handling plastic bonding adhesives:
- Storage: Store plastic bonding adhesives in original containers, tightly sealed and kept in a cool, dry, and well-ventilated area. Heat, moisture, and air exposure can cause the adhesive to degrade and lose effectiveness. Ensure to follow the manufacturer’s recommended storage conditions, including storing the adhesive at a specific temperature range.
- Handling: When handling plastic bonding adhesives, it is essential to wear appropriate personal protective equipment (PPE), such as gloves, goggles, and a respirator, to avoid skin contact, eye irritation, and inhalation of fumes. Follow the manufacturer’s recommended handling procedures, including mixing the adhesive components in a specific order or using a particular application method.
- Dispensing: Use the appropriate equipment to apply the adhesive accurately and consistently. Follow the manufacturer’s recommended application instructions, including the recommended temperature range and curing time.
- Clean-up: After using plastic bonding adhesives, immediately clean up any spills or excess adhesives utilizing the manufacturer’s recommended cleaning agent. Dispose of any waste material according to local regulations.
Following these guidelines ensures that your plastic bonding adhesives remain effective and provide a strong bond between plastic parts.
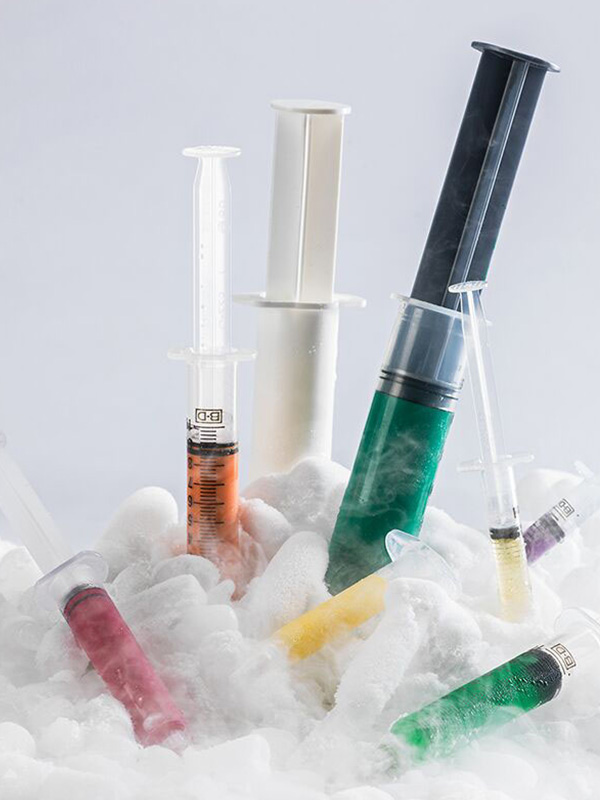
Regulatory Compliance for Plastic Bonding Adhesives
Regulatory compliance for plastic bonding adhesives depends on several factors, including its intended use and the regulatory environment in which it is sold or used. Here are some general considerations:
- Chemical composition: The chemical composition of plastic bonding adhesives is critical in determining whether they comply with various regulations. For example, certain regulatory bodies may restrict or ban some adhesive chemicals. It’s essential to ensure that your adhesive does not contain any prohibited or banned chemicals.
- Safety data sheet: A safety data sheet (SDS) is a document that provides information about the chemical properties of a substance and its potential hazards. Plastic bonding adhesives should have an SDS that complies with relevant regulations. The SDS should include information about the product’s composition, safety, and handling instructions.
- VOC emissions: Some regulatory bodies limit the amount of volatile organic compounds (VOCs) emitted by adhesives. This is because VOCs can contribute to air pollution and pose health risks to people. Make sure the adhesive you use complies with any applicable VOC regulations.
- Packaging and labeling: Adhesive packaging and labeling must comply with relevant regulations. The label should include information about the product’s composition, intended use, safety warnings, and handling instructions.
- International regulations: If you plan to sell or use the adhesive in other countries, you must ensure it complies with relevant international laws. Different countries have different regulatory requirements, so it’s essential to research and abide by each country’s rules.
It’s important to note that regulations vary by country and region, so it’s critical to understand the regulatory environment in which you intend to use or sell the adhesive. Working with a reputable adhesive manufacturer can help ensure that your bond complies with all relevant regulations.
Cost-effectiveness of Plastic Bonding Adhesives
Plastic bonding adhesives can be cost-effective in many applications, especially compared to traditional joining methods such as welding or mechanical fastening. The cost-effectiveness of plastic bonding adhesives depends on several factors, including the adhesive type, the bonded materials, and the specific application.
One of the main advantages of plastic bonding adhesives is that they often provide a stronger and more durable bond than traditional joining methods. This can result in longer-lasting and more reliable products, ultimately saving maintenance and repair costs.
In addition, plastic bonding adhesives can often be applied more quickly and with less specialized equipment than other joining methods. This can reduce labor costs and increase productivity in manufacturing processes.
However, it’s important to note that the cost-effectiveness of plastic bonding adhesives can vary depending on the specific application and the quality of the adhesive used. In some cases, the cost of the adhesive itself may be higher than other joining methods. It’s important to consider all factors, including the long-term benefits and potential cost savings when evaluating the cost-effectiveness of plastic bonding adhesives.
Troubleshooting Common Issues with Plastic Bonding Adhesives
Plastic bonding adhesives are commonly used to join plastic parts together. However, sometimes issues may arise during the bonding process, leading to weak bonds or failure. Here are some common problems that may occur during plastic bonding and some troubleshooting tips to address them:
- Poor Adhesion: If the adhesive is not sticking to the plastic, it may be due to contaminants or inadequate surface preparation. The plastic surface should be cleaned with a suitable solvent to remove dirt, grease, or oils before bonding. Also, ensure the surface is roughened or abraded to create a better bond.
- Slow Cure Time: If the adhesive takes too long to cure, it may be due to low temperature or high humidity. Increase the temperature and reduce the moisture to speed up the curing process. Alternatively, consider using a different adhesive with a faster cure time.
- Excessive Adhesive Application: Applying too much adhesive can lead to uneven curing and weak bonds. Use the recommended amount of adhesive, and spread it evenly over the surface to create a uniform bond.
- Brittle Bonds: If the bond is too rigid or brittle, it may be due to using an adhesive that is too rigid for the plastic type. Choose an adhesive compatible with plastic to ensure a flexible and durable bond.
- Adhesive Failure: If the adhesive fails, it may be due to improper curing or insufficient bond strength. Ensure that the adhesive is allowed enough time to cure fully, and use a suitable adhesive compatible with the plastic material.
- Adhesive Not Compatible with Plastic: Not all plastic bonding adhesives are suitable for all types of plastic. Ensure that the adhesive you use is compatible with the specific type of plastic you are bonding.
- Incompatible Surface Finish: Certain plastic finishes, such as smooth, glossy, or non-stick, can be difficult to bond. Consider roughening or abrading the surface to improve adhesion or using an adhesive specifically designed for smooth surfaces.
Testing and Certification of Plastic Bonding Adhesives
Testing and certification of plastic bonding adhesives are crucial to ensure they meet the necessary safety and performance standards for their intended use. Various tests can be performed to evaluate plastic bonding adhesives’ bonding strength, durability, and other properties.
Here are some standard tests used for testing and certification of plastic bonding adhesives:
- The lap shear test involves bonding two pieces of material together and then pulling them apart to measure the force required to break the bond. The lap shear test is commonly used to determine the strength of plastic bonding adhesives.
- T-peel test: A strip of material is bonded to another material at a 90-degree angle. The force required to peel the two materials apart is then measured to determine the strength of the bond.
- Impact resistance test: This test evaluates the ability of the bonded materials to withstand impact or shock. It involves weighting the related materials and measuring the damage caused.
- Environmental exposure tests: These tests evaluate the performance of plastic bonding adhesives under various environmental conditions, such as temperature, humidity, and UV exposure.
- Aging tests: These tests assess the durability of the bond over time. They involve subjecting the bonded materials to accelerated aging conditions to simulate the effects of long-term exposure.
Certification of plastic bonding adhesives can be obtained from organizations such as ASTM International, UL (Underwriters Laboratories), and ANSI (American National Standards Institute). These organizations provide standards and guidelines for testing and certification of plastic bonding adhesives, ensuring they meet the necessary safety and performance requirements.
Training for Working with Plastic Bonding Adhesives
Working with plastic bonding adhesives requires specific skills and knowledge to ensure the bonding process succeeds. Here are some tips on how to train to work with plastic bonding adhesives:
- Learn about the different types of adhesives: Many different types of plastic bonding adhesives are available, each with unique properties and characteristics. Understanding the differences between these adhesives will help you select the right one for your specific application.
- Familiarize yourself with safety precautions: Working with adhesives can be hazardous, so it’s essential to take necessary precautions to ensure your safety. Learn about the potential hazards of the adhesives you’ll be using and follow all recommended safety procedures.
- Practice proper surface preparation: Proper surface preparation is critical to achieving a solid bond. Ensure you understand the necessary steps to prepare the surfaces to be bonded, including cleaning and roughening the characters as needed.
- Understand the application process: Each adhesive has a specific application process, and it’s essential to understand the recommended application method for the adhesive you’re using. This may include applying the adhesive in a certain temperature range or using a specific application tool.
- Practice bonding techniques: Bonding plastics can be challenging, so practicing your bonding techniques before working on a final product is essential. Consider practicing on sample materials to gain experience and confidence.
- Stay up-to-date on industry trends and advancements: The adhesives industry constantly evolves, so staying informed on new products and techniques is essential. Attend industry conferences and seminars, read industry publications, and network with other professionals in the field to keep up-to-date.
By following these tips and gaining experience through practice, you can become proficient in working with plastic bonding adhesives.
Case Studies of Plastic Bonding Adhesive Applications
Sure, here are a few examples of plastic bonding adhesive applications:
- Automotive Industry: Plastic bonding adhesives are widely used for bonding plastic components together in the automotive industry. One example is bonding plastic bumper covers to the car’s body. Adhesives are used instead of mechanical fasteners, which can be unsightly and add weight to the vehicle.
- Medical Industry: In the medical industry, plastic bonding adhesives are used to assemble medical devices and equipment. One example is bonding plastic tubing to metal fittings in medical equipment such as oxygen concentrators or respiratory equipment.
- Consumer Electronics: Plastic bonding adhesives assemble various consumer electronic devices such as mobile phones, laptops, and tablets. For example, adhesives bond the plastic housing to the electronic components.
- Construction Industry: Plastic bonding adhesives are used in the construction industry to bond plastic components such as windows, doors, and siding to the building structure.
- Aerospace Industry: In the aerospace industry, plastic bonding adhesives are used to assemble aircraft components. For example, adhesives bond plastic composites to metal components in aircraft fuselage construction.
These are just a few examples of the many applications of plastic bonding adhesives. The versatility of these adhesives makes them a popular choice for a wide range of industries.
Future of Plastic Bonding Adhesives
The future of plastic bonding adhesives looks promising as manufacturers continue to develop new and improved products that offer enhanced performance, sustainability, and versatility. Here are some of the trends that are likely to shape the future of plastic bonding adhesives:
- Sustainability: With the growing awareness of the impact of plastic waste on the environment, there is a strong demand for more sustainable bonding solutions. Manufacturers are responding by developing adhesives that use renewable materials, such as bio-based resins, that can be recycled or reused.
- High-performance: Customers are looking for adhesives that can bond a wide range of plastics, including those that are difficult to bond, such as polypropylene and polyethylene. Manufacturers are developing new formulations and technologies that offer improved adhesion and durability, even under harsh conditions.
- Innovative adhesives: With the advent of the Internet of Things (IoT), there is growing interest in bonds that can sense and respond to changes in their environment. For example, some adhesives can change color or texture when exposed to certain stimuli, such as heat or moisture, which can indicate a change in the performance of the bond.
- Customization: As the demand for personalized products grows, there is a need for adhesives that can be tailored to specific applications and substrates. Manufacturers are developing adhesives with customizable properties, such as viscosity, cure time, and adhesion strength, to meet the needs of individual customers.
Overall, the future of plastic bonding adhesives looks bright as manufacturers continue to innovate and improve their products to meet the evolving needs of customers and the environment.
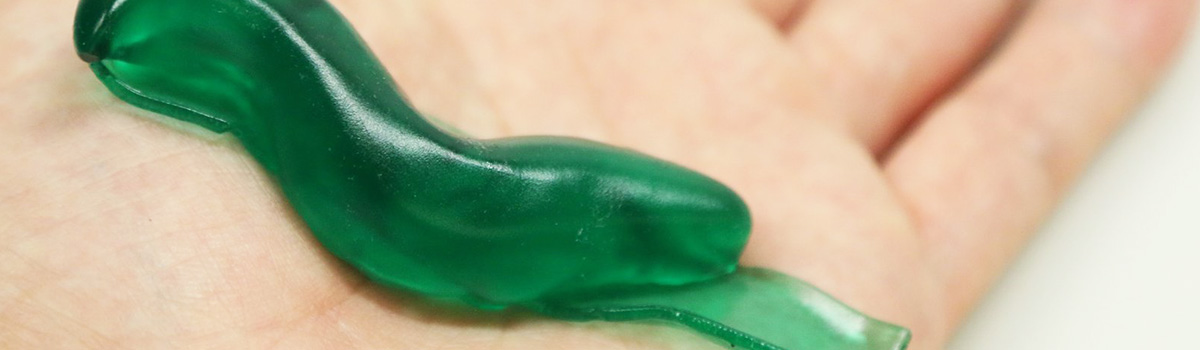
Innovations and Advancements in Plastic Bonding Adhesives
In recent years, several innovations and advancements in plastic bonding adhesives have significantly improved their performance and versatility. Some of the most notable improvements include:
- Structural adhesives: These adhesives are designed to provide a high-strength bond between plastics and other materials, such as metals and composites. They can be used in various automotive, aerospace, and construction applications.
- UV-curing adhesives cure quickly when exposed to UV light, making them ideal for high-volume manufacturing processes. They are commonly used in the electronics and medical device industries.
- Hybrid adhesives: These adhesives combine the benefits of both structural and silicone sealants. They provide high strength and flexibility, making them ideal for bonding plastics and other materials in applications with movement or vibration.
- Toughened adhesives: These adhesives are designed to provide a tough and durable bond, even in harsh environments. They are commonly used in the automotive and aerospace industries.
- Low-odor adhesives: These adhesives have a reduced odor compared to traditional solvent-based adhesives, making them more user-friendly and environmentally friendly. They are commonly used in the construction and woodworking industries.
These innovations and advancements in plastic bonding adhesives have significantly improved their performance, making them more versatile and valuable in various applications.
Market Trends for Plastic Bonding Adhesives
The market trends for plastic bonding adhesives have been driven by several factors, including:
- Increasing demand for lightweight and fuel-efficient vehicles: The automotive industry is a major manufacturer of plastic bonding adhesives. As automakers seek to reduce the weight of their cars to improve fuel efficiency, they are turning to lightweight materials such as plastics. This has increased the demand for adhesives that can effectively bond plastic components.
- Growth in the construction industry: Plastic bonding adhesives are also used in the construction industry for bonding plastic materials such as polycarbonate, PVC, and acrylics. The growth in the construction industry, particularly in developing countries, has increased the demand for these adhesives.
- Advancements in adhesive technology: There have been significant advancements in the development of plastic bonding adhesives, with manufacturers introducing new formulations that offer better adhesion and strength. These new adhesives are also designed to be more environmentally friendly, with low VOC emissions and reduced waste.
- Shift towards sustainable and eco-friendly products: With increasing concerns about the environmental impact of plastic waste, there is a growing demand for sustainable and eco-friendly products. Many adhesive manufacturers are responding to this trend by introducing new products made from renewable materials that are biodegradable.
Overall, the market for plastic bonding adhesives is expected to grow in the coming years, driven by the increasing use of plastics in various industries and the demand for advanced and eco-friendly adhesive products.
Environmental Impact of Plastic Bonding Adhesives
The use of plastic bonding adhesives can have both positive and negative environmental impacts.
On the positive side, adhesives can reduce the need for mechanical fasteners such as screws, nails, and bolts. This can lead to a reduction in materials like metal and wood, which can have environmental benefits in terms of reduced resource consumption and energy use.
However, plastic bonding adhesives can also have negative impacts on the environment. Many adhesives contain toxic chemicals such as solvents and volatile organic compounds (VOCs), which can contribute to air and water pollution. These chemicals can also have adverse health effects for workers exposed to them during production or application.
Another concern is the disposal of plastic bonding adhesives. If properly disposed of, adhesives can avoid ending up in landfills, which can take hundreds of years to break down. In addition, some adhesives can release harmful substances into the environment during degradation.
To mitigate the negative environmental impacts of plastic bonding adhesives, manufacturers can use alternative adhesives with lower levels of toxic chemicals that are more biodegradable. It is also essential to properly dispose of adhesives by following local regulations and guidelines.
Recycling and Disposal of Plastic Bonding Adhesives
The most environmentally friendly way to dispose of plastic bonding adhesives is through specialized disposal services that can safely manage hazardous waste. These services are equipped to handle adhesives containing chemicals and other dangerous materials that could harm the environment if disposed of incorrectly.
However, you can do a few things to reduce the amount of waste created by plastic bonding adhesives. Here are some tips:
- Use only the necessary amount of adhesive needed for the job. Avoid using excess amounts that will only end up in the trash.
- Rather than plastic, look for adhesives in recyclable packaging, such as metal or glass containers.
- Choose adhesives that are labeled as environmentally friendly or that use biodegradable materials.
- Consider using alternative bonding methods, such as mechanical fasteners or heat welding, that don’t require adhesives.
Ultimately, the best way to reduce the impact of plastic bonding adhesives on the environment is to use them responsibly and dispose of them properly.
Examples of Successful Plastic Bonding Adhesive Applications
- Automotive industry: Plastic bonding adhesives are used extensively in the automotive industry for bonding various plastic components such as body panels, dashboards, and instrument panels. These adhesives are known for their excellent strength, durability, and resistance to temperature changes and harsh environmental conditions.
- Electronics industry: Plastic bonding adhesives are also used in the electronics industry for bonding plastic components in devices such as smartphones, tablets, and laptops. These adhesives are known for their high strength, flexibility, and resistance to moisture and chemicals.
- Medical industry: Plastic bonding adhesives are widely used in the medical sector for bonding plastic components in medical devices such as syringes, IV bags, and catheters. These adhesives are known for their biocompatibility and resistance to harsh sterilization methods.
- Aerospace industry: Plastic bonding adhesives are used in the aerospace industry for bonding plastic components in aircraft, satellites, and other aerospace applications. These adhesives are known for their excellent strength-to-weight ratio, resistance to temperature extremes, and resistance to vibration and shock.
- Construction industry: Plastic bonding adhesives are used in the construction industry for bonding plastic components in windows, doors, and other building materials. These adhesives are known for their excellent adhesion to various substrates and resistance to weathering and UV radiation.
- Packaging industry: Plastic bonding adhesives are used in the packaging industry for bonding plastic films, foils, and laminates used in food and beverage packaging. These adhesives are known for their excellent adhesion, seal strength, and resistance to heat and moisture.
- Sporting goods industry: Plastic bonding adhesives are used in the sporting goods industry for bonding plastic components in equipment such as helmets, skis, and snowboards. These adhesives are known for their excellent strength, flexibility, and resistance to impact and vibration.
Choosing the Right Plastic Bonding Adhesive for Your Project
Choosing the suitable plastic bonding adhesive for your project depends on several factors, such as the type of plastic you’re bonding, the desired strength of the bond, the operating conditions of the related parts, and the application method. Here are some tips to help you choose the suitable plastic bonding adhesive for your project:
- Identify the type of plastic you’re bonding: Different plastics require different adhesives. For example, polyethylene and polypropylene are notoriously tricky to bond, requiring specialized adhesives formulated to create a strong bond with these materials.
- Determine the strength of the bond you need: The bond’s power will depend on the application. If bonding parts are subjected to heavy loads or high stresses, you’ll need an adhesive with high bonding strength.
- Consider the operating conditions of the bonded parts: The working conditions of the related parts will also affect your adhesive choice. If the details are exposed to high temperatures, moisture, or chemicals, you’ll need an adhesive that can withstand those conditions.
- Choose the correct application method: Some adhesives are designed for specific application methods, such as spray, brush, or roller. Make sure you choose a bond compatible with your preferred application method.
- Test the adhesive: It’s always a good idea to test the glue before using it on your project. This will give you a good idea of how well it bonds to the plastic and whether it meets your project’s strength and operating condition requirements.
Standard plastic bonding adhesives include cyanoacrylate (super glue), epoxy, acrylic, and silicone. Each of these adhesives has unique properties and characteristics, so choosing the one that best fits your specific application is essential.