Adhesives for Gasketing Application
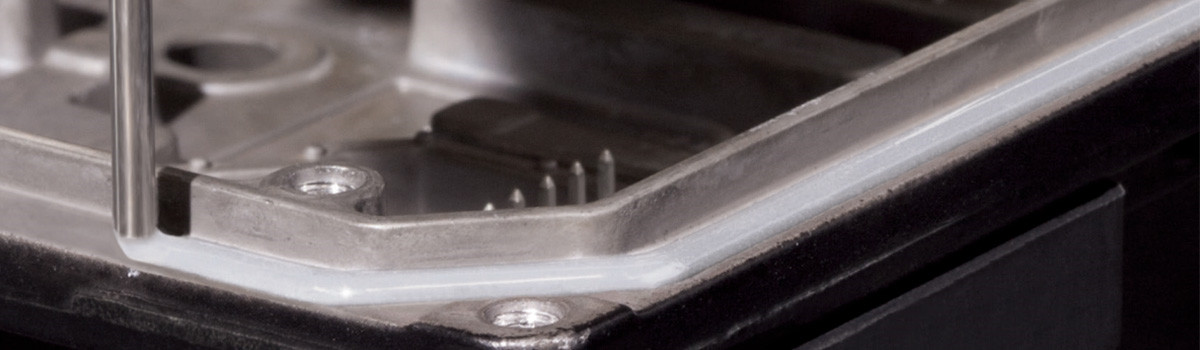
Deepmaterial manufactures a number of form-in-place and cure-in-place gaskets that adhere to glass, plastics, ceramics and metals. These formed-in-place gaskets will seal complex assemblies, prevent leakage of gasses, fluids, moisture, resist pressure and protect against damage from vibration, shock and impact.
Specific formulations feature superior electrical insulation properties, high elongation/softness, low outgassing and outstanding sound damping capabilities. Additionally thermally conductive gasketing systems are used for heat dissipation.
Gasketing Adhesives have many essential responsibilities. In fluid processing and handling equipment, they create a pressure-tight seal between two surfaces — preventing fluids from escaping and preventing contaminants from intruding. Plus, they insulate, cushion, and reduce noise. Not much to ask, right?
Materials used to perform all of these functions have included rubber, cork, electrical insulation, EMI/RFI shielding materials, foam, felt, plastics, and other high-temperature materials. The material you choose depends on the performance demands of the intended application: What is the temperature range? What pressure range is expected? Will it be exposed to corrosives? Will it be exposed to UV radiation? Are there industry-specific requirements?
Whichever material is selected, the second essential function of the gasketing adhesives are to partner with an adhesive to create a reliable bond on the two surfaces.
Electrically Conductive Form-in-Place Gasketing
Deepmaterial form-in-place gasketing materials feature low volume resisitivity, superior mechanical properties and resist aging degradation from high temperatures, humidity, fluids, dust and pressure. These formulations contain a wide range of special fillers such as silver, nickel, graphite, silver coated nickel particles to optimize EMI shielding effectiveness.
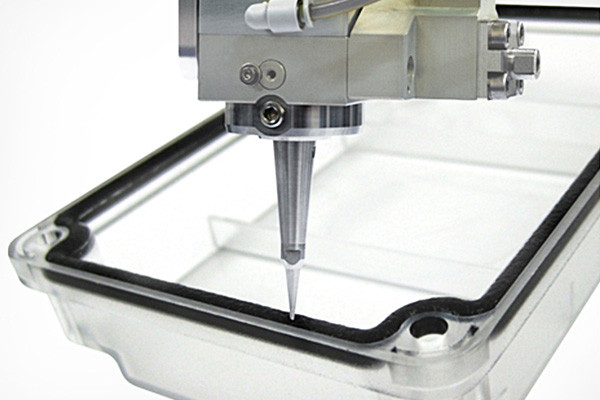
Moisture and thermal cure products exhibit high bond strength to plated metals, injection molded plastics and vacuum metalized surfaces. Resilient, non-corrosive, high tear strength compositions offer excellent compression set performance. Low modulus products absorb CTE mismatches. Conductive gasketing is designed to lower labor expenses, reduce raw material costs and shorten production cycle times. Applications range from automotive control systems to military electronics to medical electronic devices.
Silicones for Liquid Gasketing
With special systems featuring superior electrical insulation properties, tough, elastomeric silicone compounds may also be formulated for high thermal stability, durability, good adhesion to metal, plastic, ceramic substrates and absorb vibration/shock. They are designed to minimize material consumption, resist environment degradation and provide long term reliability for interior/exterior applications.
One and two component silicone systems offer void free barriers to protect joints against dust, dirt, leakage from oil, air, water pressure. One component systems have rapid tack free times at ambient temperatures. Two component systems are engineered to cure more quickly at elevated temperatures.
Benefits of Liquid Silicone Gaskets Over Precut Conventional Gaskets
*Simplify design
*Reduce inventory–do not need to store preformed gaskets
*Increase seal strength–withstand high pressure
*Fill gaps, surface irregularities, voids, scratches
*Labor and cost saving
*High elongation for micromovement–flexible joints
*Good compression set resistance
*Low temperature elasticity
*High temperature serviceability
*Prevent gasket slippage
*Can be used for multiple flange sizes and shapes
*Can be automatically applied—minimizes sealants consumption
*Excellent electrical insulation properties
*Non-flammable (certain grades)
*Resist aging
Fluorosilicone Gasketing Compounds
Special flourosilicone gasketing compounds were developed to provide enhanced chemical resistance. They will withstand exposure to gasoline, diesel fuel, motor oil, isopropyl alcohol, skydrol 500B and sodium hydroxide 25%. Ideal for the aerospace, automotive, oil/gas processing industries, these products also exhibit high resiliency, resist temperature excursions up to 450°F, aggressive thermal cycling situations and extreme pressure. Job proven, state of the art compositions contribute to design flexibility to meet demanding requirements.
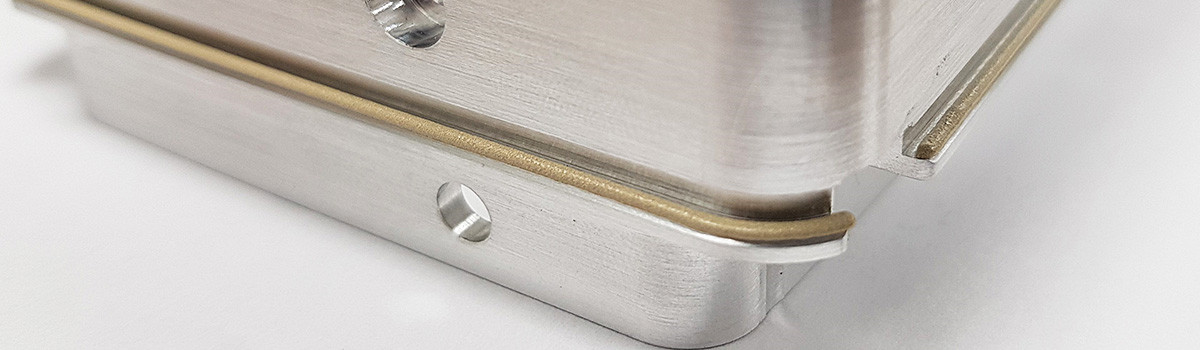
UV Curing Form-In-Place and Cure-in-Place Gaskets
Deepmaterial custom formulates products to meet individual design specifications. UV curing grades for form-in-place and cure-in-place gaskets replace die-cut gaskets, RTV sealants and tape. These ecologically friendly, single component, 100% solid silicone free elastomers provide a highly reliable barrier for protection against dust, liquids, gases, contaminants. Flowable or high viscosity products have been engineered to be precisely dispensed in a bead profile on vertical/horizontal grooves, channels, flat surfaces. Adhesion to metals, plastics, glass, ceramic surfaces is excellent. Durable, soft, tack-free Deepmaterial compositions were developed to optimize throughput speed while lowering labor/production cost. Specific grades cure only in sections upon UV light exposure. Job proven Deepmaterial FIP/CIP thin/thick gaskets meet a wide variety of performance properties such as the ability to withstand pressure, thermal cycling, shock, impact, transmitting loads.
Advantages of UV Curing Adhesives for Form-in-Place Gasket Applications
UV curable adhesives provide a number of advantages over traditional RTV silicones used to produce form-in-place gaskets, including:
*Gasket design flexibility
*Faster cure times
*Better chemical resistance
*Elimination of ovens, stacking and racking
*Saving factory space
*Reducing inventory
*Easy automation for high volume production
*No emission of corrosive elements
Ease of Use and Other Benefits of Adhesives for Gasketing
Easy to apply, these solvent free compounds lower costs, simplify processing, speed productivity and reduce inventory. High volume production schedules are optimized with rapid setting systems.
Available in flowable to non-sag viscosities these form-in-place and cure-in-place gasketing materials can be precisely dispensed manually or automatically on different shaped components. Highly durable, our gasketing systems will not shrink, crack or become brittle over time and can be used in high temperature environments. They are able to fill gaps in variable heights and widths, even on tightly packaged electronic devices. Accurate repeatable bead profiles eliminate rejects, regardless of how complex the configurations may be.