MEMS Adhesive
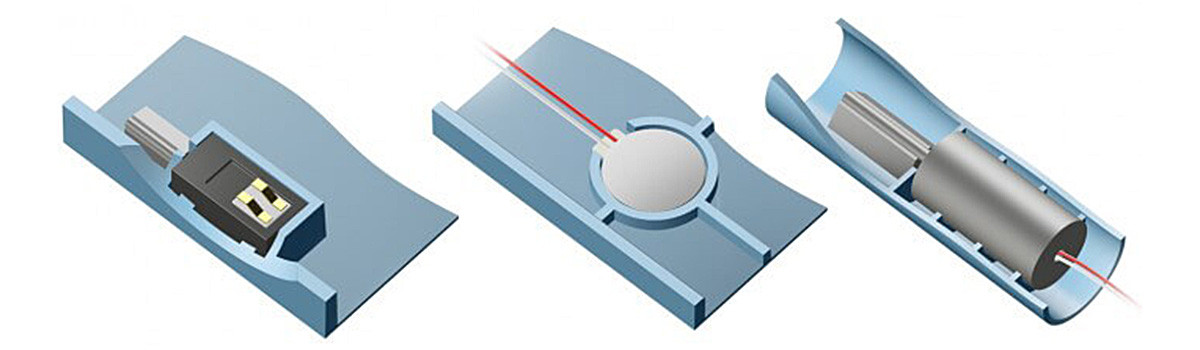
Micro-Electro-Mechanical Systems (MEMS) have revolutionized various industries by enabling the development of smaller, more efficient devices. One critical component that has contributed to the success of MEMS technology is MEMS adhesive. MEMS adhesive plays a crucial role in bonding and securing microstructures and components in MEMS devices, ensuring their stability, reliability, and performance. In this article, we explore the significance of MEMS adhesive and its applications, highlighting the key subheadings that shed light on its various aspects.
Understanding MEMS Adhesive: Fundamentals and Composition
Microelectromechanical systems (MEMS) have revolutionized various industries by enabling the production of tiny devices with powerful capabilities. MEMS adhesive plays a critical role in the assembly and packaging of these miniature devices. Understanding the fundamentals and composition of MEMS adhesive is essential for achieving reliable and robust bonding in MEMS fabrication. This article delves into MEMS adhesive to shed light on its importance and critical considerations.
The Fundamentals of MEMS Adhesive
MEMS adhesive is specifically designed to facilitate robust and durable bonds between various components of microdevices. These adhesives possess unique properties to meet the stringent requirements of MEMS applications. One of the fundamental properties of MEMS adhesive is its ability to withstand harsh environmental conditions, including temperature fluctuations, moisture, and chemical exposure. Additionally, MEMS adhesives should exhibit excellent mechanical properties, such as high adhesion strength, low shrinkage, and minimal creep, to ensure long-term reliability.
Composition of MEMS Adhesive
The composition of MEMS adhesive is carefully formulated to meet the specific needs of MEMS packaging. Typically, MEMS adhesives consist of several key components, each serving a particular purpose:
Polymer Matrix: The polymer matrix forms the bulk of the adhesive and provides the necessary structural integrity. Common polymers used in MEMS adhesives include epoxy, polyimide, and acrylic. These polymers offer excellent adhesion properties, chemical resistance, and mechanical stability.
Filler Materials: To enhance the adhesive properties, fillers are incorporated into the polymer matrix. Fillers such as silica, alumina, or metal particles can improve the adhesive’s thermal conductivity, electrical conductivity, and dimensional stability.
Curing Agents: MEMS adhesives often require a curing process to attain their final properties. Curing agents, such as amines or anhydrides, initiate cross-linking reactions in the polymer matrix, resulting in a strong adhesive bond.
Adhesion Promoters: Some MEMS adhesives may include adhesion promoters to enhance bonding between the adhesive and the substrates. These promoters are typically silane-based compounds that improve adhesion to various materials, such as metals, ceramics, or polymers.
Considerations for MEMS Adhesive Selection
Suitable MEMS adhesive ensures MEMS devices’ long-term performance and reliability. When choosing a bond, several factors should be considered:
Compatibility: The adhesive must be compatible with the materials being bonded, as well as the operating environment of the MEMS device.
Process Compatibility: The adhesive should be compatible with the manufacturing processes involved, such as dispensing, curing, and bonding methods.
Thermal and Mechanical Properties: The adhesive should exhibit suitable thermal stability, low coefficient of thermal expansion (CTE), and excellent mechanical properties to withstand the stresses encountered during device operation.
Adhesion Strength: The adhesive must provide sufficient strength to ensure a robust bond between the components, preventing delamination or failure.
Types of MEMS Adhesive: An Overview
MEMS (Microelectromechanical Systems) devices are miniature devices that combine mechanical and electrical components on a single chip. These devices often require precise and reliable bonding techniques to ensure proper functionality. MEMS adhesives play a crucial role in the assembly and packaging of these devices. They provide a solid and durable bond between different components while accommodating MEMS technology’s unique requirements. Here is an overview of some common types of MEMS adhesives:
- Epoxy Adhesives: Epoxy-based adhesives are widely used in MEMS applications. They offer excellent bonding strength and good chemical resistance. Epoxy adhesives are typically thermosetting, requiring heat or a hardening curing agent. They provide high structural integrity and can withstand harsh operating conditions.
- Silicone Adhesives: Silicone adhesives are known for their flexibility, high-temperature resistance, and excellent electrical insulation properties. They are particularly suitable for MEMS devices that undergo thermal cycling or require vibration damping. Silicone adhesives offer good adhesion to various substrates and can maintain their properties over a wide temperature range.
- Acrylic Adhesives: Acrylic-based adhesives are popular due to their fast curing times, good bonding strength, and optical transparency. They are often used in applications requiring visual clarity, such as optical MEMS devices. Acrylic adhesives provide reliable bonding and can bond with different substrates, including glass, metals, and plastics.
- UV-Curable Adhesives: UV-curable adhesives are designed to cure rapidly when exposed to ultraviolet (UV) light. They offer fast curing times, which can enhance production efficiency. UV adhesives are commonly used in MEMS applications where precise alignment is necessary because they remain liquid until exposed to UV light. They provide excellent adhesion and are suitable for bonding delicate components.
- Anisotropic Conductive Adhesives (ACA): ACA adhesives are designed for bonding microelectronic components that require mechanical support and electrical conductivity. They consist of conductive particles dispersed within a non-conductive adhesive matrix. ACA adhesives provide reliable electrical connections while maintaining mechanical stability, making them ideal for MEMS devices that involve electrical interconnects.
- Pressure-Sensitive Adhesives (PSA): PSA adhesives are characterized by their ability to form a bond upon application of slight pressure. They do not require heat or curing agents for bonding. PSA adhesives offer ease of use and can be repositioned if needed. They are commonly used in MEMS devices that require temporary bonding or where non-destructive separation is desired.
MEMS adhesives are available in various forms, including liquid adhesives, films, pastes, and tapes, allowing flexibility in choosing the most suitable option for specific assembly and packaging processes. The selection of a particular adhesive depends on factors such as the substrate materials, environmental conditions, thermal requirements, and electrical conductivity considerations.
It is essential to consider the compatibility of the adhesive with the MEMS materials and the processing requirements and constraints to ensure the successful integration and long-term reliability of MEMS devices. Manufacturers often perform extensive testing and qualification processes to validate the adhesive’s performance and suitability for specific MEMS applications.
Bonding Techniques: Surface Energy and Adhesion
Surface energy and adhesion are fundamental concepts in bonding techniques, and understanding these concepts is crucial for solid and reliable bonds between materials. Here is an overview of surface energy and adhesion in bonding:
Surface Energy: Surface energy is a measure of the energy required to increase the surface area of a material. It is a property that determines how a material interacts with other substances. Surface energy arises from the cohesive forces between atoms or molecules at the surface of a material. It can be thought of as the tendency of a material to minimize its surface area and form a shape with the least amount of surface energy.
Different materials exhibit different surface energy levels. Some materials have high surface energy, meaning they have a strong affinity for other substances and readily form bonds. Examples of high surface energy materials include metals and polar materials like glass or certain plastics. On the other hand, some materials have low surface energy, making them less prone to bond with other substances. Examples of low surface energy materials include specific polymers, such as polyethylene or polypropylene.
Adhesion: Adhesion is the phenomenon of molecular attraction between different materials that causes them to stick together when they come into contact. The force holds two surfaces together, and adhesion is essential for achieving solid and durable bonds in bonding techniques.
Adhesion can be categorized into several types based on the mechanisms involved:
- Mechanical Adhesion: Mechanical adhesion relies on interlocking or physical interlocking between surfaces. It occurs when two materials have rough or irregular surfaces that fit together, creating a solid bond. Mechanical adhesion is often enhanced by adhesives or techniques that increase the contact area between the characters, such as adhesive tapes with high conformability.
- Chemical Adhesion: Chemical adhesion occurs when there is a chemical interaction between the surfaces of two materials. It involves the formation of chemical bonds or attractive forces at the interface. Chemical adhesion is commonly achieved through adhesives that chemically react with the surfaces or by surface treatments that promote chemical bonding, such as plasma treatment or primers.
- Electrostatic Adhesion: Electrostatic adhesion relies on the attraction between positive and negative charges on different surfaces. It occurs when one character becomes electrically charged, attracting the oppositely charged surface. Electrostatic adhesion is commonly utilized in electrostatic clamping or bonding techniques involving charged particles.
- Molecular Adhesion: Molecular adhesion involves the van der Waals forces or dipole-dipole interactions between molecules at the interface of two materials. These intermolecular forces can contribute to adhesion between surfaces. Molecular bonding is particularly relevant for materials with low surface energy.
To achieve adequate adhesion, it is essential to consider the surface energy of the materials being bonded. Materials with similar surface energies tend to exhibit better adhesion however, when bonding materials with significantly different surface energies, surface treatments or adhesion promoters may be necessary to enhance adhesion.
Benefits of MEMS Adhesive in Miniaturization
Microelectromechanical systems (MEMS) have revolutionized the field of miniaturization, enabling the development of compact and sophisticated devices across various industries. MEMS adhesive plays a crucial role in the successful integration and assembly of MEMS devices, offering several benefits that contribute to their miniaturization. In this response, I will outline the key advantages of MEMS adhesive in miniaturization within 450 words.
- Precise Bonding: MEMS adhesive offers precise and reliable bonding capabilities, allowing for the secure attachment of microcomponents with high accuracy. With miniaturized devices, where the size of individual components is often on the micron or submicron scale, the adhesive must be able to form strong and consistent bonds between delicate structures. MEMS adhesive formulations are designed to provide excellent adhesion properties, ensuring the structural integrity and functionality of the assembled MEMS devices.
- Low Outgassing: Miniaturized devices often operate in high-performance or sensitive environments, such as aerospace, automotive, or medical applications. In such cases, the adhesive used must exhibit minimal outgassing to prevent contamination, degradation, or interference with surrounding components or surfaces. MEMS adhesives are formulated to have low outgassing characteristics, minimizing the release of volatile compounds and reducing the risk of adverse effects on device performance.
- Thermal Stability: MEMS devices frequently encounter varying temperature conditions during their operation. MEMS adhesive materials are designed to exhibit excellent thermal stability, withstanding temperature extremes and thermal cycling without compromising the bond strength. This characteristic is essential in miniaturized systems where space is limited, and the adhesive must endure demanding thermal environments without degradation.
- Mechanical Flexibility: The ability to withstand mechanical stress and vibration is crucial for miniaturized devices that may be subjected to external forces. MEMS adhesive formulations offer mechanical flexibility, allowing them to absorb and dissipate stress, reducing the likelihood of structural damage or failure. This flexibility ensures the long-term reliability and durability of miniaturized MEMS devices, even in dynamic environments.
- Electrical Insulation: Many MEMS devices incorporate electrical components, such as sensors, actuators, or interconnects. MEMS adhesive materials possess excellent electrical insulation properties, effectively preventing short circuits or electrical interference between different components. This characteristic is particularly important in miniaturized devices, where the proximity of electrical pathways may increase the risk of unwanted electrical coupling.
- Chemical Compatibility: MEMS adhesive formulations are designed to be chemically compatible with a wide range of materials commonly used in MEMS fabrication, such as silicon, polymers, metals, and ceramics. This compatibility allows for versatile integration of different components, enabling the miniaturization of complex MEMS systems. Additionally, the adhesive’s chemical resistance ensures the stability and longevity of the bonded interfaces, even when exposed to harsh operating environments or corrosive substances.
- Process Compatibility: MEMS adhesive materials are developed to be compatible with various assembly processes, including flip-chip bonding, wafer-level packaging, and encapsulation. This compatibility facilitates streamlined manufacturing processes for miniaturized devices, enhancing productivity and scalability. MEMS adhesive formulations can be tailored to meet specific processing requirements, enabling seamless integration into existing fabrication techniques.
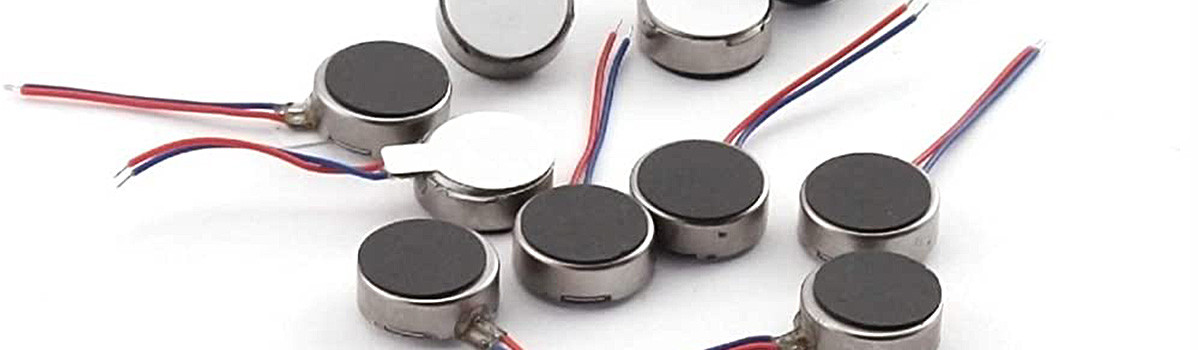
MEMS Adhesive for Sensor Applications
MEMS (Micro-Electro-Mechanical Systems) sensors are widely used in various applications such as automotive, consumer electronics, healthcare, and industrial sectors. These sensors are typically miniaturized devices that combine electrical and mechanical components to measure and detect physical phenomena like pressure, acceleration, temperature, and humidity.
One critical aspect of MEMS sensor fabrication and integration is the adhesive material used to bond the sensor to the target substrate. The adhesive ensures reliable and robust sensor performance, providing mechanical stability, electrical connectivity, and protection against environmental factors.
When it comes to selecting an adhesive for MEMS sensor applications, several factors must be considered:
Compatibility: The adhesive material should be compatible with the sensor and substrate to ensure proper adhesion. Different MEMS sensors may have distinct materials, such as silicon, polymers, or metals, and the adhesive should bond effectively with these surfaces.
Mechanical Properties: The adhesive should possess suitable mechanical properties to accommodate the stresses encountered during the operation of the MEMS sensor. It should exhibit good shear strength, tensile strength, and flexibility to withstand thermal expansion, vibration, and mechanical shocks.
Thermal Stability: MEMS sensors can be exposed to varying temperatures during operation. The adhesive material must have a high glass transition temperature (Tg) and maintain its adhesive strength over a wide temperature range.
Electrical Conductivity: In some MEMS sensor applications, electrical connectivity between the sensor and the substrate is necessary. An adhesive with good electrical conductivity or low resistance can ensure reliable signal transmission and minimize electrical losses.
Chemical Resistance: The adhesive should resist moisture, chemicals, and other environmental factors to provide long-term stability and protect the sensor components from degradation.
Silicone-based adhesives are commonly used in MEMS sensor applications due to their excellent compatibility with various materials, low outgassing, and resistance to environmental factors. They offer good adhesion to silicon-based MEMS devices and provide electrical insulation if needed.
Additionally, epoxy-based adhesives are widely used for their high strength and excellent thermal stability. They offer a solid bond to various substrates and can withstand different temperatures.
In some instances, conductive adhesives are utilized when electrical connectivity is required. These adhesives are formulated with conductive fillers such as silver or carbon, enabling them to provide both mechanical bonding and electrical conduction.
It is essential to consider the specific requirements of the MEMS sensor application and consult adhesive manufacturers or suppliers to select the most suitable adhesive. Factors such as curing time, viscosity, and application method should also be considered.
MEMS Adhesive in Medical Devices: Advancements and Challenges
MEMS (Micro-Electro-Mechanical Systems) technology has significant applications in medical devices, enabling advancements in diagnostics, monitoring, drug delivery, and implantable devices. The adhesive materials used in MEMS-based medical devices play a crucial role in ensuring these devices’ reliability, biocompatibility, and long-term performance. Let’s explore the advancements and challenges of MEMS adhesives in medical devices.
Advancements:
- Biocompatibility: Adhesive materials used in medical devices must be biocompatible to ensure they do not elicit adverse reactions or cause harm to the patient. Significant advancements have been made in developing adhesive materials with improved biocompatibility, allowing for safer and more reliable integration of MEMS sensors in medical devices.
- Miniaturization: MEMS technology enables the miniaturization of medical devices, making them more portable, minimally invasive, and capable of real-time monitoring. Adhesive materials designed for MEMS applications have advanced to accommodate the miniaturization trend, providing robust and reliable bonding in confined spaces.
- Flexible Substrates: Flexible and stretchable medical devices have gained prominence due to their ability to conform to curved surfaces and enhance patient comfort. Adhesive materials with high flexibility and stretchability have been developed to enable secure bonding between MEMS sensors and flexible substrates, expanding the possibilities for wearable and implantable medical devices.
- Biodegradability: In specific medical applications where temporary devices are used, such as drug delivery systems or tissue scaffolds, biodegradable adhesives have gained attention. These adhesives can gradually degrade over time, eliminating the need for device removal or explantation procedures.
Challenges:
- Biocompatibility Testing: Ensuring the biocompatibility of adhesive materials used in MEMS-based medical devices is a complex process that requires extensive testing and regulatory compliance. Adhesive manufacturers face challenges in meeting the stringent standards set by regulatory bodies to ensure patient safety.
- Long-Term Reliability: Medical devices often require long-term implantation or continuous use. Adhesive materials must exhibit reliable bonding and maintain their mechanical and adhesive properties over extended periods, considering the physiological conditions and potential degradation factors present in the body.
- Chemical and Thermal Stability: MEMS-based medical devices may encounter harsh chemical environments, bodily fluids, and temperature fluctuations during operation. Adhesives must possess excellent chemical resistance and thermal stability to maintain their integrity and bonding strength.
- Sterilization Compatibility: Medical devices need to undergo sterilization processes to eliminate potential pathogens and ensure patient safety. Adhesive materials should be compatible with standard sterilization methods such as autoclaving, ethylene oxide (EtO) sterilization, or gamma irradiation without compromising their adhesive properties.
MEMS Adhesive for Microfluidics: Enhancing Fluid Control
Microfluidics, the science, and technology of manipulating small volumes of fluids, has gained significant attention in various fields, including biomedical research, diagnostics, drug delivery, and chemical analysis. MEMS (Micro-Electro-Mechanical Systems) technology enables precise fluid control in microfluidic devices. The adhesive materials used in these devices are instrumental in achieving reliable fluidic connections and maintaining fluid control. Let’s explore how MEMS adhesives enhance fluid power in microfluidics and the associated advancements.
- Leak-Free Sealing: Microfluidic devices often require multiple fluidic channels, valves, and reservoirs. Adhesive materials with excellent sealing properties are crucial for leak-free connections, preventing cross-contamination and ensuring precise fluid control. MEMS adhesives provide robust sealing, enabling the reliable operation of microfluidic devices.
- Bonding Dissimilar Materials: Microfluidic devices may consist of various materials such as glass, silicon, polymers, and metals. MEMS adhesives are formulated to have good adhesion to different substrate materials, allowing for bonding dissimilar materials. This capability enables the integration of diverse components and facilitates the fabrication of complex microfluidic structures.
- High Chemical Compatibility: MEMS adhesives used in microfluidics must exhibit high chemical compatibility with the manipulated fluids and reagents. They should resist chemical degradation and remain stable, ensuring the integrity of the fluidic channels and preventing contamination. Advanced MEMS adhesives are designed to withstand various chemicals commonly used in microfluidic applications.
- Optimal Flow Characteristics: In microfluidic devices, precise control of fluid flow and minimizing flow disruptions are essential. MEMS adhesives can be tailored to have smooth and uniform surface properties, reducing the occurrence of bubbles, droplets, or irregular flow patterns. This optimization improves fluid control and enhances the accuracy of microfluidic operations.
- Microscale Feature Replication: Microfluidic devices often require replicating intricate microscale features, such as channels, chambers, and valves. MEMS adhesives with low viscosity and high wetting properties can fill microscale features effectively, ensuring the accurate reproduction of complex fluidic structures and maintaining fluid control at small scales.
- Temperature and Pressure Resistance: Microfluidic devices may encounter temperature variations and pressure fluctuations during operation. MEMS adhesives designed for microfluidics offer high-temperature stability and can withstand the pressures experienced within the microfluidic system, ensuring the durability and reliability of fluid control.
- Integration with Functional Components: Microfluidic devices often incorporate additional sensors, electrodes, and actuators. MEMS adhesives can facilitate the integration of these functional elements, providing secure and reliable connections, enabling multi-modal functionality, and enhancing the overall performance of microfluidic systems.
Advancements in MEMS adhesive technology continue to improve the precision, reliability, and versatility of fluid control in microfluidic devices. Ongoing research focuses on developing adhesives with tailored properties, such as bioadhesives for biocompatible microfluidics, stimuli-responsive adhesives for dynamic fluid power, and self-healing adhesives for improved device longevity. These advancements contribute to improving microfluidics and its broad range of applications.
Thermal Management and MEMS Adhesive: Addressing Heat Dissipation
Thermal management is critical to MEMS (Micro-Electro-Mechanical Systems) devices, as they often generate heat during operation. Efficient heat dissipation is essential to maintain optimal performance, prevent overheating, and ensure the reliability and longevity of MEMS devices. MEMS adhesives are vital in addressing heat dissipation challenges by providing effective thermal management solutions. Let’s explore how MEMS adhesives can help address heat dissipation in MEMS devices.
- Thermal Conductivity: MEMS adhesives with high thermal conductivity can efficiently transfer heat from the heat-generating components to heat sinks or other cooling mechanisms. These adhesives act as effective thermal bridges, reducing thermal resistance and enhancing heat dissipation.
- Bonding to Heat Sinks: Heat sinks are commonly used in MEMS devices to dissipate heat. MEMS adhesives provide reliable bonding between the heat-generating components and the heat sinks, ensuring efficient heat transfer to the sink. The adhesive material must have good adhesion properties to withstand thermal cycling and maintain a strong bond under elevated temperatures.
- Low Thermal Resistance: MEMS adhesives should possess low thermal resistance to minimize the thermal impedance between the heat source and the cooling interface. Low thermal resistance enables efficient heat transfer and improves thermal management in MEMS devices.
- Thermal Stability: MEMS devices may operate at high temperatures or experience temperature fluctuations. The adhesive material must exhibit excellent thermal stability to withstand these conditions without degrading or losing its adhesive properties. This stability ensures consistent heat dissipation performance over the lifetime of the MEMS device.
- Dielectric Properties: In some cases, MEMS devices may require electrical insulation between heat-generating components and heat sinks. MEMS adhesives with appropriate dielectric properties can provide thermal conductivity and electrical insulation, enabling effective heat dissipation while maintaining electrical integrity.
- Gap-Filling Capability: MEMS adhesives with good gap-filling capability can eliminate air gaps or voids between heat-generating components and heat sinks, enhancing thermal contact and minimizing thermal resistance. This capability ensures more efficient heat transfer and dissipation within the MEMS device.
- Compatibility with MEMS Materials: MEMS devices incorporate silicon, polymers, metals, and ceramics. MEMS adhesives should be compatible with these materials to ensure proper adhesion and thermal management. Compatibility also prevents adverse chemical interactions or degradation affecting heat dissipation performance.
Advancements in MEMS adhesive technology are focused on developing materials with enhanced thermal conductivity, improved thermal stability, and tailored properties to address specific thermal management requirements. Researchers are exploring novel adhesive formulations, such as nanocomposite adhesives containing thermally conductive fillers, to enhance heat dissipation capabilities further.
MEMS Adhesive in Optical Systems: Ensuring Precise Alignment
In optical systems, precise alignment is crucial for achieving optimal performance and functionality. One key component that plays a critical role in ensuring precise alignment is the microelectromechanical systems (MEMS) adhesive. MEMS adhesive refers to the bonding material used to attach MEMS devices, such as mirrors, lenses, or microactuators, to their respective substrates in optical systems. It enables the accurate positioning and alignment of these devices, thereby enhancing the overall performance and reliability of the visual system.
When it comes to ensuring precise alignment in optical systems, several factors need to be considered in selecting and applying MEMS adhesives. First and foremost, the adhesive material should possess excellent optical properties, such as low refractive index and minimal light scattering or absorption. These characteristics help to minimize unwanted reflections or distortions, which can degrade the performance of the optical system.
Moreover, the MEMS adhesive should exhibit high mechanical stability and durability. Optical systems often undergo various environmental conditions, including temperature fluctuations, humidity changes, and mechanical stresses. The adhesive material must withstand these conditions without compromising the alignment of the optical components. Additionally, it should have a low coefficient of thermal expansion to minimize the impact of thermal cycling on the alignment stability.
Furthermore, the adhesive should offer precise control over the bonding process. This includes low viscosity, good wetting properties, and controlled curing or hardening time. Low density ensures uniform and reliable adhesive coverage between the MEMS device and the substrate, facilitating better contact and alignment. Good wetting properties enable proper adhesion and prevent voids or air bubbles from forming. Controlled curing time allows for sufficient adjustment and alignment before the adhesive sets.
In terms of application, careful consideration should be given to adhesive dispensing and handling techniques. MEMS adhesives are typically applied in small quantities with high precision. Automated dispensing systems or specialized tools may be employed to ensure accurate and repeatable application. Proper handling techniques, such as using cleanrooms or controlled environments, help prevent contamination that could adversely affect alignment and optical performance.
To validate and ensure the precise alignment of optical components using MEMS adhesives, thorough testing, and characterization are essential. Techniques such as interferometry, optical microscopy, or profilometry can be employed to measure the alignment accuracy and assess the visual system’s performance. These tests help identify deviations or misalignments, enabling adjustments or refinements to achieve the desired alignment.
MEMS Adhesive in Consumer Electronics: Enabling Compact Designs
MEMS adhesives have become increasingly important in consumer electronics, enabling the development of compact and slim designs for various devices. These adhesives are instrumental in bonding and securing microelectromechanical systems (MEMS) components within consumer electronic devices, such as smartphones, tablets, wearables, and smart home appliances. By ensuring reliable attachment and precise alignment, MEMS adhesives contribute to these devices’ miniaturization and improved performance.
One key advantage of MEMS adhesives in consumer electronics is their ability to provide robust and durable bonding while occupying minimal space. As consumer electronic devices become smaller and more portable, the adhesive materials must offer high adhesion strength in a thin layer. This allows for compact designs without compromising structural integrity. MEMS adhesives are designed to provide excellent adhesion to various substrates commonly used in consumer electronics, including metals, glass, and plastics.
In addition to their bonding capabilities, MEMS adhesives offer benefits in terms of thermal management. Consumer electronic devices generate heat during operation, and efficient heat dissipation is crucial to prevent performance degradation or component failure. MEMS adhesives with high thermal conductivity can attach heat-generating components, such as processors or power amplifiers, to heat sinks or other cooling structures. This helps to dissipate heat effectively, improving the overall thermal management of the device.
Furthermore, MEMS adhesives contribute to consumer electronic devices’ overall reliability and durability. These adhesives resist environmental factors such as temperature variations, humidity, and mechanical stresses, and they can withstand the rigorous conditions encountered during everyday use, including drops, vibrations, and thermal cycling. By providing robust bonding, MEMS adhesives help ensure the longevity and reliability of consumer electronics.
Another advantage of MEMS adhesives is their compatibility with automated manufacturing processes. As consumer electronic devices are mass-produced, efficient and reliable assembly methods are crucial. MEMS adhesives can be dispensed precisely using mechanical dispensing systems, enabling high-speed and accurate assembly. The adhesive materials are designed to have suitable viscosity and curing characteristics for automated handling, allowing for streamlined production processes.
Moreover, the versatility of MEMS adhesives enables their use in a wide range of consumer electronic applications. Whether it is attaching sensors, microphones, speakers, or other MEMS components, these adhesives offer the flexibility to accommodate various device designs and configurations. They can be applied to different substrate materials and surface finishes, providing compatibility with various consumer electronic products.
MEMS Adhesive for Aerospace and Defense Applications
MEMS adhesive technology has proven highly valuable in aerospace and defense applications, where precision, reliability, and performance are paramount. The unique properties of MEMS adhesives make them well-suited for bonding and securing microelectromechanical systems (MEMS) components in aerospace and defense systems, ranging from satellites and aircraft to military equipment and sensors.
One critical aspect of aerospace and defense applications is the ability of adhesives to withstand extreme environmental conditions. MEMS adhesives are designed to offer high-temperature stability, withstanding the elevated temperatures experienced during space missions, supersonic flights, or operations in harsh environments. They exhibit excellent thermal cycling resistance, ensuring the bonded components’ reliability and long-term performance.
Additionally, aerospace and defense systems often face high mechanical stresses, including vibrations, shocks, and acceleration forces. MEMS adhesives provide exceptional mechanical stability and durability, maintaining the integrity of the bond under these demanding conditions. This ensures that the MEMS components, such as sensors or actuators, remain securely attached and operational, even in challenging working environments.
Another crucial factor in aerospace and defense applications is weight reduction. MEMS adhesives offer the advantage of being lightweight, allowing for the overall weight of the system to be minimized. This is particularly significant in aerospace applications, where reducing weight is essential for fuel efficiency and payload capacity. MEMS adhesives enable bonding lightweight materials, such as carbon fiber composites or thin films, while maintaining structural integrity.
Furthermore, MEMS adhesives are crucial in miniaturizing aerospace and defense systems. These adhesives enable the unique bonding and positioning of MEMS components, which are often small and delicate. By facilitating compact designs, MEMS adhesives contribute to space optimization within limited aircraft, satellites, or military equipment areas. This allows for integrating more functionalities and improved system performance without compromising size or weight constraints.
The ability of MEMS adhesives to maintain precise alignment is also critical in aerospace and defense applications. The adhesive material must ensure accurate positioning, whether aligning optical components, MEMS-based sensors, or microactuators. This is crucial for achieving optimal performance, such as precise navigation, targeting, or data acquisition. MEMS adhesives with excellent dimensional stability and low outgassing properties help to maintain alignment over extended periods, even in vacuum or high-altitude environments.
Stringent quality standards and testing procedures are paramount in the aerospace and defense industries. MEMS adhesives undergo rigorous testing to ensure their compliance with industry requirements. This includes mechanical testing for strength and durability, thermal testing for stability in extreme temperatures, and environmental testing for humidity, chemicals, and radiation resistance. These tests validate the performance and reliability of the adhesive material, ensuring its suitability for aerospace and defense applications.
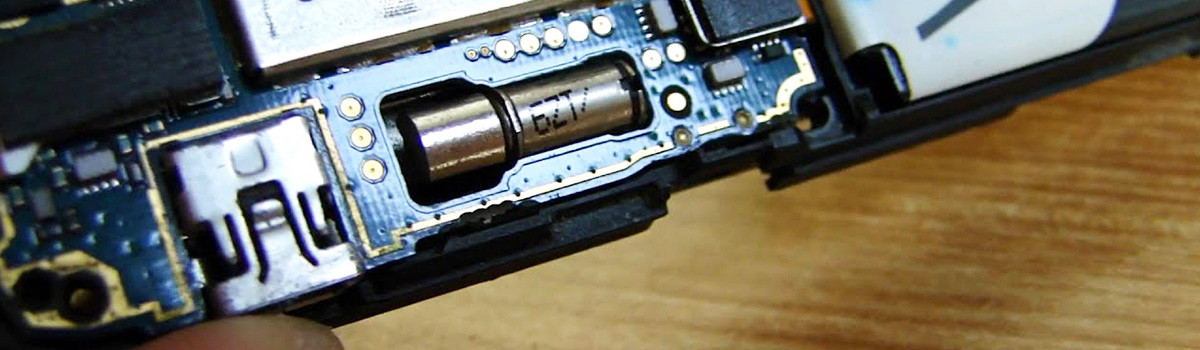
MEMS Adhesive for Automotive Industry: Enhancing Safety and Performance
MEMS adhesive technology has emerged as a valuable asset in the automotive industry, pivotal in enhancing safety, performance, and reliability. With the increasing complexity and sophistication of automotive systems, MEMS adhesives provide crucial bonding and securing solutions for microelectromechanical systems (MEMS) components, contributing to vehicles’ overall functionality and efficiency.
One of the primary areas where MEMS adhesives enhance automotive safety is in sensor applications. MEMS sensors, such as those used in airbag deployment, stability control, or advanced driver-assistance systems (ADAS), require precise and reliable attachment. MEMS adhesives ensure the secure bonding of these sensors to various substrates within the vehicle, such as the chassis or body frame. This provides accurate sensor performance, enabling timely and accurate data acquisition for critical safety functions.
Moreover, MEMS adhesives contribute to automotive components’ overall durability and reliability. They resist environmental factors, including temperature variations, humidity, and vibration. In automotive applications where details are subjected to continuous and varying stresses, MEMS adhesives provide robust bonding, preventing component detachment or failure. This enhances the longevity and performance of automotive systems, leading to improved overall vehicle reliability.
MEMS adhesives also aid in weight reduction and design optimization in the automotive industry. As automotive manufacturers strive to improve fuel efficiency and reduce emissions, lightweight materials are increasingly used. MEMS adhesives offer the advantage of being lightweight, allowing for efficient bonding of lightweight materials like composites or thin films. This helps reduce the vehicle’s overall weight without compromising structural integrity or safety requirements.
Additionally, MEMS adhesives contribute to the miniaturization of automotive systems. As vehicles incorporate more advanced technologies and functionalities, compact designs become crucial. MEMS adhesives enable the precise attachment and positioning of small and delicate components, such as microsensors or actuators. This facilitates space optimization within the vehicle, allowing for the integration of additional features while maintaining a smaller form factor.
In terms of manufacturing efficiency, MEMS adhesives offer advantages in assembly processes within the automotive industry. They can be applied using automated dispensing systems, ensuring accurate and consistent bonding, and this streamlines production processes reduces assembly time and improves manufacturing yields. The properties of MEMS adhesives, such as controlled curing time and good wetting properties, contribute to efficient and reliable bonding during high-volume production.
Lastly, MEMS adhesives undergo stringent testing and quality control processes to meet automotive industry standards. Mechanical tests ensure the strength and durability of the adhesive bond, while thermal testing evaluates its stability under temperature variations. Environmental tests assess the adhesive’s resistance to chemicals, humidity, and other factors. By meeting these rigorous requirements, MEMS adhesives provide the necessary reliability and performance for automotive applications.
Biocompatible MEMS Adhesive: Enabling Implantable Devices
Biocompatible MEMS adhesive technology has revolutionized the field of implantable medical devices by enabling secure and reliable attachment of microelectromechanical systems (MEMS) components within the human body. These adhesives play a critical role in ensuring the success and functionality of implantable devices by providing biocompatible bonding solutions compatible with human tissue and fluids.
One of the critical requirements for implantable devices is biocompatibility. MEMS adhesives used in such applications are carefully formulated to be non-toxic and non-irritating to the surrounding tissues. They undergo thorough biocompatibility testing to ensure they do not induce adverse reactions or harm the patient. These adhesives are designed to be stable in physiological environments and maintain integrity without releasing harmful substances into the body.
Implantable devices often require solid and long-lasting bonds to ensure stability and functionality over extended periods. Biocompatible MEMS adhesives offer excellent adhesion to various substrates, including metals, ceramics, and biocompatible polymers commonly used in implantable devices. These adhesives provide secure attachment of MEMS components, such as sensors, electrodes, or drug delivery systems, to the device or the surrounding tissue, allowing for accurate and reliable performance.
In addition to biocompatibility and bonding strength, biocompatible MEMS adhesives possess excellent mechanical properties. Implantable devices can experience mechanical stresses, such as bending, stretching, or compression, due to the movement or natural processes within the body. The adhesive material must withstand these stresses without compromising the integrity of the bond. Biocompatible MEMS adhesives offer high mechanical stability and flexibility, ensuring the adhesive bond’s durability in the human body’s dynamic environment.
Furthermore, biocompatible MEMS adhesives enable precise positioning and alignment of MEMS components within the implantable device. Accurate placement is crucial for optimal device functionality and performance. The adhesive material allows for the fine adjustment and secure attachment of features, such as biosensors or microactuators, ensuring proper positioning and alignment relative to the target tissue or organ.
Implantable devices often require hermetic sealing to protect sensitive components from the surrounding body fluids. Biocompatible MEMS adhesives can provide a reliable and biocompatible seal, preventing the ingress of fluids or contaminants into the device. These adhesives exhibit excellent barrier properties, ensuring the long-term integrity of the implantable device and minimizing the risk of infection or device failure.
Finally, biocompatible MEMS adhesives undergo rigorous testing to ensure their suitability for implantable applications. They are subjected to biocompatibility evaluations according to international standards, including cytotoxicity, sensitization, and irritation assessments. The adhesive materials are also tested for stability under physiological conditions, including temperature, pH, and humidity variations. These tests ensure the adhesive’s safety, reliability, and long-term performance within the implantable device.
MEMS Adhesive Testing and Reliability Considerations
MEMS adhesive testing and reliability considerations are crucial to ensure the performance and longevity of microelectromechanical systems (MEMS) devices. These devices often operate in demanding environments and are subjected to various stresses and conditions. Thorough testing and careful consideration of reliability factors are essential to validate the adhesive’s performance and ensure the reliability of MEMS devices.
A critical aspect of adhesive testing is mechanical characterization. Adhesive bonds must be evaluated for their mechanical strength and durability to withstand the stresses encountered during the device’s lifetime. Tests such as shear, tensile, or peel tests measure the adhesive’s resistance to different mechanical forces. These tests provide insights into the adhesive’s ability to maintain a strong bond and withstand mechanical stresses, ensuring the reliability of the MEMS device.
Another crucial factor in adhesive testing is thermal performance. MEMS devices can experience significant temperature variations during operation. Adhesive materials need to be tested to ensure their stability and integrity under these temperature conditions. Thermal cycling tests, where the adhesive is subjected to repeated temperature cycles, help evaluate its ability to withstand thermal expansion and contraction without delamination or degradation. Additionally, thermal aging tests assess the adhesive’s long-term stability and reliability under prolonged exposure to elevated temperatures.
Environmental testing is also essential to assess the adhesive’s resistance to various environmental factors. Humidity, chemicals, and gases commonly encountered in real-world applications can affect the adhesive’s performance and integrity. Accelerated aging tests, where the bond is exposed to harsh environmental conditions for an extended period, help simulate the long-term effects of these factors. These tests provide valuable information on the adhesive’s resistance to environmental degradation, ensuring its reliability in different operating conditions.
Reliability considerations go beyond testing, including factors such as adhesion failure modes, aging mechanisms, and long-term performance. Understanding adhesive bond failure modes is crucial to designing robust MEMS devices. Failure analysis techniques, such as microscopy and material characterization, help identify failure mechanisms, such as adhesive delamination, cohesive failure, or interface failure. This knowledge guides improving adhesive formulations and bonding processes to mitigate failure risks.
Aging mechanisms can also impact the adhesive’s long-term performance, and factors such as moisture absorption, chemical reactions, or UV exposure can degrade the adhesive. As mentioned earlier, accelerated aging tests help assess the adhesive’s resistance to these aging mechanisms. Manufacturers can design MEMS devices with extended operational lifetimes and reliable performance by understanding and addressing potential aging issues.
Moreover, reliability considerations include selecting appropriate adhesive materials for specific MEMS applications. Different adhesives have varying properties, such as viscosity, curing time, and compatibility with substrates, and these factors need to be carefully considered to ensure optimal bonding and long-term reliability. Adhesive manufacturers provide technical data and application guidelines to aid in material selection, considering MEMS devices’ specific requirements and operating conditions.
MEMS Adhesive Manufacturing Processes and Techniques
MEMS adhesive manufacturing processes and techniques involve a series of steps to produce high-quality adhesive materials for microelectromechanical systems (MEMS) applications. These processes ensure the adhesive’s consistency, reliability, and performance, meeting the specific requirements of MEMS devices. Below are the critical steps involved in MEMS adhesive manufacturing:
- Formulation: The first step in adhesive manufacturing is formulating the adhesive material. This involves selecting the appropriate base resin and additives to achieve desired properties such as adhesion strength, flexibility, thermal stability, and biocompatibility. The formulation considers the application requirements, substrate materials, and environmental conditions.
- Mixing and Dispersion: Once the adhesive formulation is determined, the next step is the mixing and dispersion the ingredients. This is typically done using specialized mixing equipment to ensure a homogeneous blend. The mixing process is crucial for uniform additives distribution and maintaining consistent properties throughout the adhesive material.
- Adhesive Application: The adhesive is prepared for application after the formulation and mixing stages. The application technique depends on the specific requirements and characteristics of the adhesive. Standard application methods include dispensing, screen printing, spin coating, or spraying. The goal is to evenly apply the adhesive to the desired surfaces or components with precision and control.
- Curing: Curing is a critical step in adhesive manufacturing, transforming the adhesive from a liquid or semi-liquid state to a solid form. Curing can be achieved through various techniques such as heat, UV, or chemical curing. The curing process activates cross-linking reactions within the adhesive, developing strength and adhesion properties.
- Quality Control: Throughout the adhesive manufacturing process, strict quality control measures are implemented to ensure the consistency and reliability of the adhesive material. This includes monitoring parameters such as viscosity, adhesive strength, curing time, and chemical composition. Quality control procedures help identify deviations or inconsistencies, allowing for adjustments or corrective actions to maintain product integrity.
- Packaging and Storage: Once the adhesive is manufactured and quality tested, it is packaged and prepared for storage or distribution. Proper packaging protects the adhesive from external factors such as moisture, light, or contaminants. Adhesive storage conditions, including temperature and humidity, are carefully considered to maintain the stability and performance of the adhesive over its shelf life.
- Process Optimization and Scale-Up: Adhesive manufacturers continually strive to optimize the manufacturing process and scale production to meet increasing demand. This involves process refinement, automation, and efficiency improvements to ensure consistent quality, reduce production costs, and enhance overall productivity.
It’s worth noting that the specific manufacturing processes and techniques can vary depending on the type of adhesive, intended application, and the manufacturer’s capabilities. Adhesive manufacturers often have proprietary methods and expertise to tailor the manufacturing process to their specific product formulations and customer requirements.
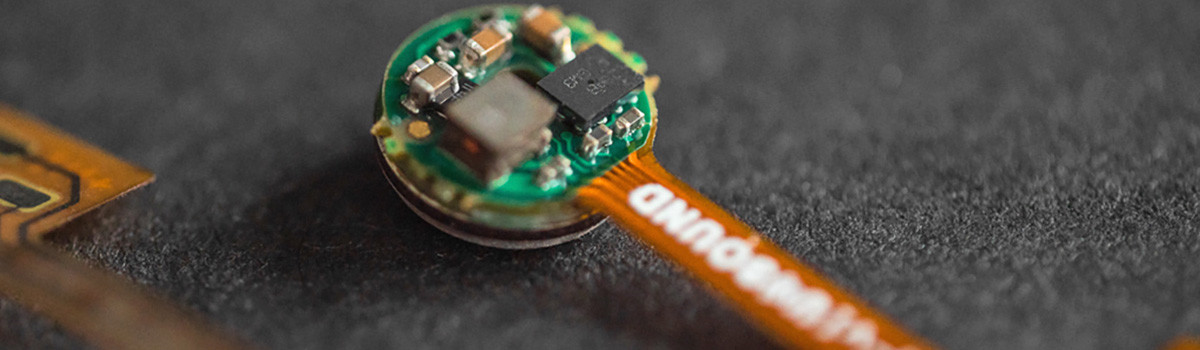
Challenges in MEMS Adhesive Bonding: Material Compatibility and Stress Management
MEMS adhesive bonding presents several challenges, particularly regarding material compatibility and stress management. These challenges arise due to the diverse range of materials used in microelectromechanical systems (MEMS) devices and the complex stress conditions they experience. Overcoming these challenges is crucial to ensure reliable and durable adhesive bonds in MEMS applications.
Material compatibility is a critical consideration in MEMS adhesive bonding. MEMS devices often consist of various materials, such as silicon, glass, polymers, metals, and ceramics, each with unique properties. The adhesive must be compatible with these materials to establish a strong and reliable bond. Adhesive selection involves considering factors such as thermal expansion coefficients, adhesion to different materials, and compatibility with the device’s operating conditions.
Differences in thermal expansion coefficients can lead to significant stresses and strains during temperature cycling, causing delamination or cracking at the adhesive interface. Managing these thermal stresses requires careful material selection and design considerations. Adhesives with lower modulus and coefficients of thermal expansion closer to the bonded materials can help reduce stress mismatch and enhance the bond’s long-term reliability.
Another challenge in MEMS adhesive bonding is managing the mechanical stresses experienced by the device. MEMS devices can be subject to various mechanical stresses, including bending, stretching, and compression. These stresses can result from environmental conditions, device operation, or assembly processes. Adhesive materials must possess sufficient strength and flexibility to withstand these stresses without delamination or failure.
To address stress management challenges, several techniques can be employed. One approach uses compliant or elastomeric adhesives that absorb and distribute stresses across the bonded area. These adhesives provide enhanced flexibility, allowing the device to withstand mechanical deformations without compromising the adhesive bond. Additionally, optimizing the design of MEMS devices, such as incorporating stress-relief features or introducing flexible interconnects, can help alleviate stress concentrations and minimize the impact on adhesive bonds.
Ensuring proper surface preparation is also critical in addressing material compatibility and stress management challenges. Surface treatments, such as cleaning, roughening, or applying primers or adhesion promoters, can improve the adhesion between the adhesive and the substrate materials. These treatments promote better wetting and bonding at the interface, enhancing material compatibility and stress distribution.
Furthermore, precise control over the adhesive application is vital for successful bonding. Factors such as adhesive dispensing technique, curing conditions, and process parameters can influence the adhesive bond’s quality and performance. Consistency in adhesive thickness, uniform coverage, and proper curing is essential to achieve reliable bonds that can withstand material compatibility challenges and mechanical stresses.
Overcoming material compatibility and stress management challenges in MEMS adhesive bonding requires a multidisciplinary approach involving materials science, device design, and process optimization. Collaboration between adhesive manufacturers, MEMS device designers, and process engineers is essential to address these challenges effectively. Through careful material selection, design considerations, surface preparation, and process control, adhesive bonding in MEMS applications can be optimized to achieve reliable and durable bonds, ensuring the performance and longevity of MEMS devices.
Advances in MEMS Adhesive Technology: Nanomaterials and Smart Adhesives
Advances in MEMS adhesive technology have been driven by the need for enhanced performance, miniaturization, and improved functionality in microelectromechanical systems (MEMS) applications. Two significant areas of advancement in MEMS adhesive technology include the integration of nanomaterials and the development of intelligent adhesives. These advancements offer unique capabilities and improved performance in bonding MEMS devices.
Nanomaterials have played a crucial role in advancing MEMS adhesive technology. Integrating nanomaterials, such as nanoparticles, nanofibers, or nanocomposites, into adhesive formulations has improved properties and functionalities. For example, the addition of nanoparticles can enhance the mechanical strength, thermal stability, and electrical conductivity of the adhesive material. Nanofibers like carbon nanotubes or graphene can provide enhanced reinforcement and improved electrical or thermal properties. Using nanocomposites in adhesives offers a unique combination of properties, including high strength, flexibility, and compatibility with various substrate materials. Integrating nanomaterials into MEMS adhesives enables the development of high-performance bonding solutions for demanding MEMS applications.
Another significant advancement in MEMS adhesive technology is the development of intelligent adhesives. Innovative adhesives are designed to exhibit unique properties or functionalities in response to external stimuli, such as temperature, light, or mechanical stress. These adhesives can undergo reversible or irreversible changes in their properties, allowing for dynamic responses and adaptability in different operating conditions. For example, shape memory adhesives can change shape or recover their original form upon exposure to temperature variations, offering reversible bonding capabilities. Light-activated adhesives can be triggered to bond or debond by specific wavelengths of light, providing precise control and reworkability. Innovative adhesives can enable advanced functionalities in MEMS devices, such as reconfigurability, self-healing, or sensing capabilities, enhancing their performance and versatility.
Integrating nanomaterials and innovative adhesive technologies offer synergistic benefits in MEMS applications. Nanomaterials can be incorporated into intelligent adhesives to further enhance their properties and functionalities. For instance, nanomaterials can be used to develop stimuli-responsive nanocomposite adhesives that exhibit unique behavior based on external stimuli. These adhesive systems can provide self-sensing capabilities, enabling the detection of mechanical stress, temperature, or other environmental changes. They can also offer self-healing properties, where the adhesive can repair micro-cracks or damage upon exposure to specific conditions. Combining nanomaterials and innovative adhesive technologies opens up new possibilities for advanced MEMS devices with improved performance, durability, and adaptability.
These advances in MEMS adhesive technology have implications across various industries. They enable the development of smaller, more reliable MEMS devices with enhanced functionality. In healthcare, nanomaterial-enhanced adhesives can support the fabrication of implantable devices with improved biocompatibility and long-term reliability. Innovative adhesives can enable self-repairing or reconfigurable devices in consumer electronics, enhancing user experience and product longevity. Nanomaterial-enhanced bonds can offer lightweight bonding solutions with improved strength and durability in automotive and aerospace applications.
Environmental Considerations: MEMS Adhesive for Sustainability
Environmental considerations are becoming increasingly important in developing and using adhesive materials for microelectromechanical systems (MEMS) devices. As sustainability and ecological consciousness continue to gain traction, it is crucial to address the impact of MEMS adhesive materials throughout their lifecycle. Here are some key factors to consider when aiming for sustainability in MEMS adhesive applications:
- Material Selection: Choosing environmentally friendly adhesive materials is the first step towards sustainability. Opting for adhesives with low environmental impact, such as water-based or solvent-free formulations, can help reduce emissions and minimize the use of hazardous substances. Additionally, selecting bonds with a longer shelf life or derived from renewable resources can contribute to sustainability efforts.
- Manufacturing Processes: Assessing and optimizing the manufacturing processes associated with MEMS adhesive production is vital for sustainability. Employing energy-efficient manufacturing techniques, minimizing waste generation, and implementing recycling or reuse practices can significantly reduce the environmental footprint of adhesive manufacturing. Process optimization can also lead to resource savings and increased efficiency, contributing to sustainability goals.
- End-of-Life Considerations: Understanding the end-of-life implications of MEMS adhesive materials is essential for sustainability. Adhesives compatible with recycling processes or easily removed during device disassembly promote circularity and reduce waste. Considering the recyclability or biodegradability of adhesive materials allows for environmentally responsible disposal or recovery of valuable components.
- Environmental Impact Assessment: Conducting a comprehensive environmental impact assessment of MEMS adhesive materials helps identify potential ecological risks and evaluate sustainability performance. Life cycle assessment (LCA) methodologies can be employed to analyze the environmental impact of adhesive materials throughout their entire lifecycle, including raw material extraction, manufacturing, use, and disposal. This assessment provides insights into hotspots and areas for improvement, guiding the development of more sustainable adhesive solutions.
- Regulation Compliance: Adhering to relevant regulations and standards related to environmental protection is crucial for sustainable adhesive applications. Compliance with laws such as REACH (Registration, Evaluation, Authorization, and Restriction of Chemicals) ensures the safe use and handling of adhesive materials, reducing potential harm to the environment and human health. Additionally, adhering to eco-labeling schemes or certifications can demonstrate a sustainability commitment and provide end-users transparency.
- Research and Innovation: Continued research and innovation in adhesive technology can drive sustainability in MEMS applications. Exploring alternative adhesive materials, such as bio-based or bio-inspired adhesives, can offer more sustainable options. Developing adhesive materials with improved recyclability, biodegradability, or lower environmental impact can lead to greener and more sustainable MEMS devices.
Future Trends in MEMS Adhesive Development
In recent years, Microelectromechanical Systems (MEMS) technology has gained significant attention and has become an integral part of various industries, including electronics, healthcare, automotive, and aerospace. MEMS devices typically consist of miniaturized mechanical and electrical components that require precise bonding to ensure reliability and functionality. Adhesive materials are crucial in MEMS assembly, providing strong and durable bonds between parts.
Looking into the future, several trends can be identified in the development of adhesives for MEMS applications:
- Miniaturization and Integration: The trend of miniaturization in MEMS devices is expected to continue, leading to the demand for adhesive materials that can bond smaller and more intricate components. Adhesives with high-resolution capabilities and the ability to create strong bonds on microscale surfaces will be crucial for fabricating miniaturized MEMS devices. Additionally, adhesive materials that enable the integration of multiple components within a single MEMS device will be in high demand.
- Enhanced Reliability and Durability: MEMS devices are often exposed to harsh operating conditions, including temperature fluctuations, humidity, and mechanical stress. Future adhesive developments will focus on improving the reliability and durability of bonds under such conditions. Adhesives with increased resistance to thermal cycling, moisture, and mechanical vibrations will be essential for ensuring MEMS devices’ long-term performance and stability.
- Low-Temperature Curing: Many MEMS materials, such as polymers and delicate electronic components, are sensitive to high temperatures. Consequently, there is a growing demand for adhesives that can cure at low temperatures without compromising the bond strength. Low-temperature curing adhesives will enable the assembly of temperature-sensitive MEMS components and reduce the risk of thermal damage during fabrication.
- Compatibility with Multiple Substrates: MEMS devices often involve bonding different materials, such as metals, ceramics, and polymers. Adhesive materials that exhibit excellent adhesion to various substrates will be highly sought. Moreover, developing adhesives that can bond dissimilar materials with mismatched coefficients of thermal expansion will help mitigate the potential for stress-induced failure in MEMS devices.
- Bio-Compatible Adhesives: The field of biomedical MEMS is rapidly advancing, with applications in drug delivery, tissue engineering, and implantable devices. Adhesive, biocompatible, non-toxic materials will be crucial for these applications, ensuring the safety and compatibility of MEMS devices with biological systems. Future developments will focus on designing and synthesizing adhesives that exhibit excellent biocompatibility while maintaining strong adhesion and mechanical properties.
- Releasable and Reusable Adhesives: In some MEMS applications, the ability to release and reposition or reuse components after bonding is desirable. Releasable and reusable adhesives will provide flexibility during MEMS fabrication and assembly processes, allowing for adjustments and corrections without damaging the parts or substrates.
Conclusion: MEMS Adhesive as a Driving Force in Microelectronics Advancement
MEMS adhesive materials have become a driving force in the advancement of microelectronics, playing a critical role in the assembly and functionality of MEMS devices. These tiny mechanical and electrical components require special bonding to ensure reliability and performance. Future trends in MEMS adhesive development are expected to enhance these devices’ capabilities and applications further.
Miniaturization and integration will continue to push the boundaries of MEMS technology. Adhesive materials with high-resolution capabilities will be crucial for bonding smaller and more intricate components. Additionally, adhesives that enable the integration of multiple components within a single MEMS device will drive innovation in this field.
Reliability and durability are paramount in MEMS applications, as these devices are exposed to harsh operating conditions. Future adhesive developments will improve thermal cycling, moisture, and mechanical stress resistance. The goal is to ensure MEMS devices’ long-term performance and stability in various environments.
Low-temperature curing adhesives will address the sensitivity of MEMS materials to high temperatures. Curing at lower temperatures without compromising bond strength will facilitate the assembly of temperature-sensitive components, reducing the risk of thermal damage during fabrication.
Compatibility with multiple substrates is crucial in MEMS assembly, as different materials are often involved. Adhesive materials that exhibit excellent adhesion to a wide range of substrates will enable the bonding of dissimilar materials and help mitigate stress-induced failure in MEMS devices.
In biomedical MEMS, the demand for bio-compatible adhesives is rapidly growing. These adhesives must be non-toxic and compatible with biological systems while maintaining strong adhesion and mechanical properties. The development of such bonds will expand the applications of MEMS in areas such as drug delivery, tissue engineering, and implantable devices.
Lastly, releasable and reusable adhesives will provide flexibility during MEMS fabrication and assembly processes. The ability to release and reposition components or even reuse them after bonding supports adjustments and corrections without damaging the parts or substrates.
In conclusion, MEMS adhesive materials are driving advancements in microelectronics by enabling the assembly and functionality of MEMS devices. Future developments in MEMS adhesives will further enhance miniaturization, reliability, low-temperature curing, substrate compatibility, bio-compatibility, and the flexibility of assembly processes. These advancements will unlock new possibilities and applications for MEMS technology, revolutionizing various industries and shaping the future of microelectronics.