Display Bonding Adhesive
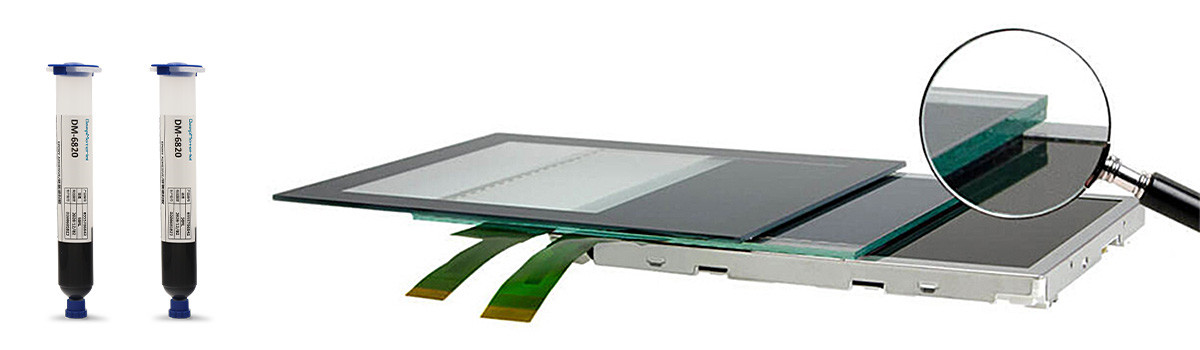
Display bonding adhesive (DBA) is a type of adhesive that is used to bond the display module to the touch panel or cover glass in electronic devices such as smartphones, tablets, and laptops. The use of DBA has become increasingly popular in recent years due to its ability to create a strong and durable bond between the display and the touch panel. This results in a seamless and flush surface, providing a high-quality user experience. In this article, we will explore the different aspects of display bonding adhesive, including its properties, applications, and advantages.
What is Display Bonding Adhesive?
Display Bonding Adhesive (DBA) is a type of adhesive used in the manufacturing process of electronic devices, such as smartphones, tablets, and televisions. It is specifically designed to bond the display (or touch panel) to the device’s housing or chassis.
DBA is typically a high-strength, clear adhesive that provides a strong bond between the display and the device’s housing or chassis. It is often used in devices that require a high level of durability and resistance to impact or shock, such as smartphones or tablets.
DBA can be applied using various techniques, such as film laminating or injection molding, and is cured using heat or UV light. The properties of the adhesive can be adjusted to suit specific application requirements, such as flexibility, strength, and resistance to temperature and moisture.
The Role of Display Bonding Adhesive in Electronic Devices
Display bonding adhesive (DBA) is critical in electronic devices, especially smartphones and tablets. It is an adhesive used to attach the display panel to the device’s frame or chassis. The DBA plays a crucial role in holding the display firmly in place and preventing accidental separation or damage.
DBA is typically a thin, flexible adhesive layer between the display panel and the device’s frame or chassis. It is designed to withstand the stresses and strains of electronic devices during everyday use, such as drops, impacts, and temperature changes.
In addition to its primary function of holding the display panel in place, DBA also provides other benefits. For example, it can reduce the amount of glare on the display, improve the viewing angle, and enhance the overall appearance of the device.
Various types of DBA are available, each with its unique properties and characteristics. For example, some kinds of DBA are designed to provide a strong, permanent bond, while others are designed to be more flexible and removable. The choice of DBA will depend on the specific requirements of the device and the intended application.
Types of Display Bonding Adhesive
Display bonding adhesive is used to bond the display or touch screen to the device’s frame or casing in electronic devices. Here are some types of display bonding adhesives:
- Acrylic Adhesives: These adhesives provide excellent adhesion to various substrates and have high bonding strength. They are commonly used in electronics because they resist heat and humidity.
- Epoxy Adhesives: Epoxy adhesives are known for their high strength and durability. They can bond to various substrates, including metal, plastic, and glass. They have excellent resistance to water, chemicals, and heat.
- Silicone Adhesives: Silicone adhesives are known for their flexibility and elasticity. They can bond to various substrates, including glass, metal, and plastic. They have excellent resistance to moisture, chemicals, and temperature changes.
- UV-Curable Adhesives: These adhesives cure when exposed to ultraviolet light. They provide high bond strength and fast curing time. They are commonly used in electronics because they can bond to various substrates and resist heat and humidity.
- Pressure-Sensitive Adhesives: These adhesives are tacky and provide instant bonding when applying pressure. They are commonly used in electronic devices because they can bond to various substrates and are easy to apply.
Properties of Display Bonding Adhesive
Some of the properties of Display Bonding Adhesive include the following:
- High bond strength: DBA has excellent adhesion properties and creates a strong bond between the display panel and the device’s frame. This ensures the display panel stays firmly in place, even when subjected to vibrations or impacts.
- Optical clarity: DBA is designed to have minimal impact on the clarity and brightness of the display panel. This ensures the device’s screen remains straightforward and easy to read without distortion or haziness.
- Chemical resistance: DBA is resistant to various chemicals, including oils, solvents, and cleaners. This makes it ideal for use in electronic devices, which are often exposed to these substances.
- Temperature resistance: DBA is designed to withstand high temperatures, making it suitable for use in devices that generate significant heat, such as smartphones and tablets.
- Flexibility: DBA is formulated to be flexible, which allows it to absorb some of the stresses that can occur when a device is dropped or subjected to other forms of impact. This helps to protect the display panel and prevent cracks or further damage.
Overall, Display Bonding Adhesive is a critical component in the manufacturing of electronic devices, providing a solid and durable bond between the display panel and the device’s frame.
Advantages of Display Bonding Adhesive
The advantages of using DBA include:
- Enhanced durability: DBA helps to create a strong bond between the touch screen and the device, which makes the display more durable and resistant to damage from drops and impacts.
- Improved visual quality: DBA allows for a thinner layer of adhesive, which reduces the distance between the touch screen and the device’s display. This helps to improve the display’s visual quality by reducing reflections and increasing contrast.
- Higher touch sensitivity: DBA enables touch screens to be attached to devices with greater accuracy, which can improve touch sensitivity and responsiveness.
- Increased production efficiency: DBA can be applied using automated equipment to increase production efficiency and reduce production costs.
- Better resistance to environmental factors: DBA can provide resistance to environmental factors such as moisture, dust, and temperature changes, which can help to extend the life of the device.
- Reduced weight and size: DBA allows for a thinner layer of adhesive, which can reduce the overall weight and size of the device.
Overall, DBA offers many advantages over other types of adhesives, making it a popular choice for attaching touch screens and displays to electronic devices.
Disadvantages of Display Bonding Adhesive
While DBA has many advantages, including better durability and a slimmer profile, it also has some disadvantages, including:
- Repair difficulty: Once the display panel is bonded to the cover lens using DBA, it is easier to separate them by damaging the display. This makes repairs more complicated and expensive.
- Limited reworkability: DBA has limited reworkability, which means that if a mistake is made during the bonding process, it cannot be undone, and the entire assembly may need to be scrapped.
- Delamination: In some cases, DBA may cause delamination of the display panel, resulting in screen defects, including discoloration, bubbles, and dead pixels.
- Moisture sensitivity: DBA is sensitive to moisture, which can cause the adhesive to weaken over time, potentially leading to display panel separation and device failure.
- Cost: DBA is more expensive than other types of adhesive, which can add to the overall cost of the device.
Overall, while DBA offers many benefits, including better durability and a slimmer profile, it also has some significant disadvantages, including difficulty in repair, limited reworkability, delamination, moisture sensitivity, and cost.
Challenges in the Application of Display Bonding Adhesive
While DBA has several advantages over traditional attachment methods, such as mechanical fastening or thermal bonding, its application also presents some challenges. Here are some of the difficulties in the application of display bonding adhesive:
- Surface preparation: Before applying DBA, the surface of the device and the display panel must be thoroughly cleaned and prepared. Any contamination or residue left on the surface can interfere with the adhesion process and compromise the strength of the bond.
- Compatibility: DBA must be compatible with the materials of both the device and the display panel. If the adhesive is incompatible, it may not bond properly or damage the surfaces it is applied to.
- Application method: The application method for DBA requires precision and accuracy. To ensure a strong bond, the adhesive must be applied evenly and without air bubbles. Additionally, the pressure used during application must be carefully controlled to avoid damaging the delicate display panel.
- Curing time: DBA requires a specific time to cure before it can achieve its full strength. The curing time can vary depending on the type of adhesive used and the environmental conditions during curing. The bond may only be strong enough if the adhesive is given sufficient time to cure.
- Repairability: If the display panel needs to be repaired or replaced, the use of DBA can complicate the process. Removing the adhesive without damaging the device or display panel can be difficult and require specialized equipment.
Applying DBA requires careful attention to detail and expertise to ensure a robust and reliable bond.
Factors to Consider When Selecting Display Bonding Adhesive
When selecting a display bonding adhesive, there are several factors to consider, including:
- Substrate compatibility: The adhesive should be compatible with bonded materials, such as glass, metal, or plastic.
- Adhesion strength: The adhesive should have sufficient power to securely bond the display components.
- Cure time: The cure time of the adhesive should be appropriate for the production process and the required production throughput.
- Optical properties: The adhesive should have good optical properties to minimize the impact on display performance.
- Temperature resistance: The adhesive should have the necessary temperature resistance to withstand the operating temperature range of the display.
- Environmental resistance: The adhesive should be able to resist moisture, UV light, and other environmental factors that could affect display performance.
- Ease of application: The adhesive should be easy to apply manually or with automated dispensing equipment.
- Cost: The cost of the adhesive should be reasonable, considering its performance and other factors.
- Regulatory compliance: The adhesive should comply with relevant regulations, such as RoHS and REACH, and be safe for use in the intended application.
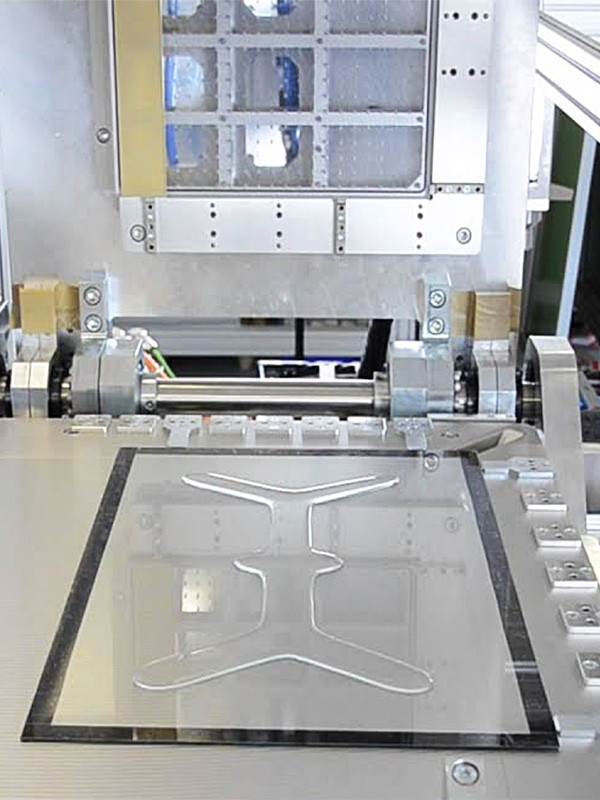
Surface Preparation for Display Bonding Adhesive
Surface preparation is an essential step when bonding display components with adhesives. The following are some general guidelines for surface preparation for display bonding adhesive:
- Clean the Surface: The surface should be free of dust, dirt, and other contaminants. Clean the surface using a lint-free cloth or other appropriate cleaning materials. Use a cleaning solution recommended by the adhesive manufacturer. Avoid using solvents that may damage the surface.
- Remove any existing adhesive: Any existing adhesive on the surface must be removed before applying a new bond. Use an appropriate solvent to dissolve the adhesive and a scraper or other suitable tool to remove it.
- Surface Roughening: The surface may need roughened to provide a better bonding surface. Use sandpaper or abrasive blasting to create a rough surface. Be sure to remove any dust or debris from the surface after roughening.
- Surface Activation: Some adhesives require the surface to be activated before application. Surface activation can be done using plasma treatment, corona discharge, or other methods.
- Surface Primer: Some adhesives require a primer to be applied to the surface before the adhesive. Follow the adhesive manufacturer’s instructions for using the primer.
- Allow the Surface to Dry: After cleaning, roughening, activating, or priming the surface, allow it to dry completely before applying the adhesive.
Following the adhesive manufacturer’s instructions for surface preparation is essential to ensure proper bonding and avoid any problems during the bonding process.
Cleaning and Handling Techniques for Display Bonding Adhesive
Here are some techniques for cleaning and handling display bonding adhesive:
- Storage: Store the adhesive in a cool, dry place away from direct sunlight and moisture.
- Cleaning: Before applying the adhesive, clean the surfaces thoroughly to ensure they are free of dust, oil, and other contaminants. Use a lint-free cloth and a cleaning solution compatible with the adhesive.
- Application: Apply the adhesive according to the manufacturer’s instructions. Use the recommended amount of adhesive and avoid applying too much or too little.
- Drying: Allow the adhesive to dry completely before handling the device. The drying time may vary depending on the adhesive type and application method.
- Handling: Handle the device carefully to avoid damaging the adhesive. Avoid twisting or bending the machine; do not apply excessive pressure to the display.
- Removal: If you need to remove the adhesive, use a solvent that is compatible with the adhesive. Follow the manufacturer’s instructions carefully, and use protective equipment such as gloves and goggles.
- Disposal: Dispose of the adhesive and any cleaning materials according to local regulations. Do not pour them down the drain or dispose of them in the trash.
By following these techniques for cleaning and handling display bonding adhesive, you can ensure that your electronic device is assembled correctly and will function effectively.
Curing Time and Temperature for Display Bonding Adhesive
The curing time and temperature for display bonding adhesive depend on the specific adhesive type. Generally, the manufacturer determines the curing time and temperature, which should be followed closely to ensure the best possible bonding results.
In general, display bonding adhesives are designed to cure at room temperature, typically within 24 to 48 hours. However, some adhesives may require a higher temperature for curing, ranging from 60°C to 120°C.
It is important to note that the curing time and temperature can affect the bond strength between the display and the substrate. If the adhesive is not cured correctly, it may result in weak adhesion or bond failure.
Testing and Quality Control for Display Bonding Adhesive
Testing and quality control of DBA are critical to ensure the integrity and performance of the displays. Here are some of the essential testing and quality control measures for DBA:
- Adhesion testing: Adhesion testing measures the strength of the bond between the DBA and the substrate. Different adhesion tests include peel strength, shear strength, and cleavage strength.
- Moisture resistance testing: Moisture resistance testing measures the ability of the DBA to resist damage from exposure to moisture or humidity. This test is essential for displays that may be used in high-moisture environments.
- Thermal cycling testing: Thermal cycling testing measures the ability of the DBA to withstand temperature changes. This test is essential for displays subjected to extreme temperature fluctuations.
- Aging testing: Aging testing measures the long-term durability of the DBA. This test evaluates the ability of the DBA to maintain its performance over time.
- Optical performance testing: Optical performance testing measures the impact of the DBA on the display’s optical properties, including brightness, contrast, and color accuracy.
- Contamination testing: Contamination testing measures the presence of foreign materials, such as dust, oil, or particles, on the DBA. Contamination can affect the adhesion of the DBA and the overall performance of the display.
- Quality control measures: Quality control measures are essential to ensure consistency and reliability in the manufacturing process. These measures include inspecting the DBA before use, monitoring the manufacturing process, and conducting quality audits.
Overall, thorough testing and quality control measures are critical to ensuring the reliability and performance of DBA displays.
Innovations in Display Bonding Adhesive Technology
Display bonding adhesive technology has seen significant advancements in recent years, driven by the demand for thinner, more durable electronic devices with improved display performance. Some of the critical innovations in display bonding adhesive technology include:
- Optically Clear Adhesives (OCAs): OCAs are optically transparent adhesive, allowing for an uninterrupted view of the display. They are used in displays where image quality is critical, such as smartphones and tablets. The development of OCAs has led to thinner and more lightweight displays with higher color saturation and contrast ratios.
- Flexible Adhesives: Flexible adhesives are used in flexible displays and wearable devices where the display needs to bend and flex without cracking or breaking. These adhesives are designed to maintain their bond strength even under extreme bending or stretching conditions.
- UV-Curable Adhesives: UV-curable adhesives are a type of adhesive that cure quickly when exposed to ultraviolet (UV) light. They are widely used to manufacture displays because they offer fast curing times, high bond strength, and improved durability.
- Non-Conductive Adhesives: Non-conductive adhesives are used in touchscreens and other displays that require electrical conductivity. These adhesives are designed to provide a strong bond while allowing for the passage of electrical current through the display.
- Nanoparticle Adhesives: Nanoparticle adhesives are a type of adhesive that use nanoparticles to improve bond strength and durability. These adhesives are advantageous in displays exposed to extreme temperatures or high humidity levels.
Overall, these display bonding adhesive technology advancements have produced more lightweight and durable electronic devices with improved display performance.
Applications of Display Bonding Adhesive in Smartphones
Display Bonding Adhesive (DBA) is a type of adhesive used in smartphones to bond the display panel to the device’s body. DBA is commonly used in smartphones because it provides strong adhesion and a seamless appearance. Here are some of the applications of DBA in smartphones:
- Ensuring display stability: DBA helps to ensure that the display panel is securely attached to the device’s body, preventing any movement or shaking of the display while in use.
- Enhancing water and dust resistance: By creating a tight seal between the display panel and the device’s body, DBA helps to improve the smartphone’s water and dust resistance.
- Improving touch screen sensitivity: DBA is often used to bond the touch screen layer to the display panel, which can help enhance the touch screen’s sensitivity and accuracy.
- Reducing device thickness: DBA is a thin adhesive that can be applied in a skinny layer, which can help reduce the smartphone’s overall thickness.
- Providing a seamless appearance: DBA is often used to bond the display panel to the device’s body with a seamless appearance, which can enhance the smartphone’s aesthetics and overall user experience.
Overall, DBA plays a crucial role in ensuring the stability, durability, and appearance of the smartphone display panel, which is one of the most essential components of a modern smartphone.
Applications of Display Bonding Adhesive in Tablets
Display Bonding Adhesive (DBA) is a type of adhesive commonly used in manufacturing tablets, smartphones, and other electronic devices. DBA is designed to bond the display panel to the device’s frame, providing a secure and durable connection. Here are some applications of DBA in tablets:
- Display Assembly: DBA attaches the display panel to the tablet’s frame, creating a strong bond that ensures the display remains in place and does not come loose over time. The adhesive also helps to prevent dust and other debris from entering the device’s interior.
- Touch Screen Assembly: In tablets that feature a touchscreen display, DBA is used to bond the touchscreen digitizer to the display panel. This creates a secure connection, enabling the touchscreen to accurately register touch inputs.
- Waterproofing: DBA can create a seal around the display assembly, preventing water and other liquids from entering the device’s interior. This is especially important for tablets that are designed to be used in outdoor or rugged environments.
- Structural Support: DBA can also provide structural support to the tablet’s display assembly, helping to prevent damage from drops and impacts. The adhesive can help to distribute the force of an impact across the entire display assembly, reducing the risk of cracks and other types of damage.
Overall, DBA is a critical component of tablet manufacturing, enabling manufacturers to create durable and reliable devices.
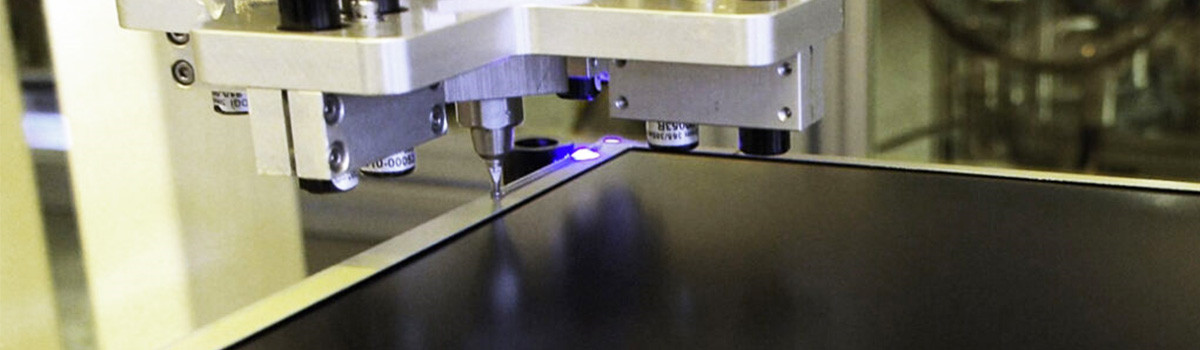
Applications of Display Bonding Adhesive in Laptops
Display bonding adhesive (DBA) is used in laptops to attach the display panel to the bezel or the cover glass. Here are some of the applications of display bonding adhesive in laptops:
- Structural integrity: DBA provides structural integrity to the display panel, which is essential in laptops that are frequently transported or used on the go. Without DBA, the display panel could come loose or detach from the bezel, causing damage to the screen or other components.
- Improved durability: DBA helps to enhance the laptop’s durability by protecting the display panel from damage caused by impacts, drops, or other types of physical stress.
- Enhanced display quality: By bonding the display panel to the bezel or cover glass, DBA helps to improve the display quality by reducing the amount of reflection and glare on the screen.
- Thinner design: DBA allows for a more delicate structure of the laptop by eliminating the need for additional mechanical fasteners or brackets to attach the display panel to the bezel.
- Increased manufacturing efficiency: DBA is easy to apply during the manufacturing process, which helps to improve manufacturing efficiency and reduce production costs.
Applications of Display Bonding Adhesive in Wearable Devices
The primary application of DBA is to attach the display module to the device’s housing and protect it from damage. Here are some specific applications of DBA in wearable devices:
- Smartwatches: DBA is commonly used to assemble smartwatches to bond the display module to the device’s casing. This adhesive provides a strong and durable bond that can withstand the daily wear and tear of the device.
- Fitness trackers: Fitness trackers often have small displays that require a precise and secure attachment to the device’s housing. DBA is ideal for this application, as it provides a high-strength bond and can be applied in weak layers.
- Virtual reality headsets: VR headsets have complex displays that require a robust and flexible adhesive to hold them in place. DBA is an excellent choice for this application because it can adhere to various materials and maintain its bond even under extreme conditions.
- Smart glasses: Smart glasses have displays attached to the frame or lenses. DBA bonds the show to the structure and ensures it stays in place during use.
Overall, DBA is a crucial component in manufacturing wearable devices with display screens. Its high-strength bond and ability to adhere to a wide range of materials make it an ideal choice for applications where durability and precision are essential.
Applications of Display Bonding Adhesive in Automotive Displays
Here are some applications of Display Bonding Adhesive in automotive displays:
- LCD and OLED Displays: DBA is commonly used to assemble LCD and OLED displays in automotive applications. The adhesive is used to bond the cover lens to the display panel, providing a seamless and durable finish.
- Head-Up Displays (HUDs): HUDs are increasingly used in modern vehicles to project information such as speed, navigation, and warnings directly onto the windshield. DBA is used to bond the projector unit to the windscreen, ensuring a stable and reliable display.
- Center Stack Displays: The center stack display is the central interface in most modern vehicles, providing access to infotainment, climate control, and other features. DBA is used to bond the cover lens to the display panel, ensuring a durable and reliable interface.
- Instrument Cluster Displays: Instrument cluster displays provide critical information such as speed, fuel level, and engine temperature. DBA is used to bond the cover lens to the display panel, protecting against environmental factors and ensuring an accurate and reliable display.
- Touchscreen Displays: Touchscreen displays are becoming increasingly common in automotive applications, providing intuitive and easy-to-use interfaces. DBA is used to bond the cover lens to the display panel, providing a durable and responsive touchscreen experience.
Applications of Display Bonding Adhesive in Medical Devices
Display bonding adhesive (DBA) has several applications in medical devices due to its ability to securely bond different materials such as glass, plastic, and metal. Some of the applications of DBA in medical devices are:
- Touchscreens: Medical devices such as infusion pumps, ultrasound machines, and patient monitors require touchscreens resistant to water, chemicals, and disinfectants. DBA can bond the touchscreen display to the device housing, providing a secure seal and preventing moisture and dust ingress.
- Wearable Medical Devices: DBA can be used to bond the display and other electronic components to the wearable device’s housing. This ensures that the device remains compact and lightweight while maintaining its durability.
- Endoscopes: Endoscopes are used for visualizing and diagnosing various medical conditions. DBA can bond the optical lens to the device’s housing, ensuring that the device remains airtight and waterproof.
- Surgical instruments: DBA can bond the display and other electronic components to surgical instruments, ensuring they remain lightweight and easy to handle during surgeries.
- Imaging equipment: DBA can bond the display to imaging equipment such as MRI, CT scanners, and X-ray machines. This ensures that the collection remains securely attached to the device and can withstand the rigors of daily use.
Applications of Display Bonding Adhesive in Gaming Devices
Some of the applications of DBA in gaming devices include:
- Screen bonding: DBA is used to bond the display screen to the device’s chassis, ensuring the screen remains firmly in place, even during intense gaming sessions. This is particularly important for mobile gaming devices, where the screen is more susceptible to impact and pressure.
- Frame bonding: In addition to bonding the screen, DBA is also used to bond the frame of the gaming device to the screen. This provides additional support and stability to the screen and the device.
- Water resistance: DBA is often used in gaming devices to provide water resistance. By bonding the screen and frame of the machine together, DBA can prevent water from entering the device and damaging the internal components.
- Improved durability: Gaming devices are often subjected to rough handling, drops, and impacts. DBA provides a robust and durable bond that can help prevent damage to the device and prolong its lifespan.
- Aesthetics: DBA is often used in gaming devices to improve the device’s aesthetics. By seamlessly bonding the screen and frame, DBA can create a smooth, sleek appearance that enhances the device’s overall look and feel.
Overall, DBA plays an essential role in the assembly of gaming devices, providing a strong, durable, and long-lasting bond that helps ensure the machine performs optimally and lasts for a long time.
Applications of Display Bonding Adhesive in Industrial Displays
Here are some of the applications of Display Bonding Adhesive in industrial displays:
- Ruggedization: Industrial displays are often used in harsh environments exposed to extreme temperatures, vibration, and shock. The use of Display Bonding Adhesive helps improve the display’s ruggedness by providing a strong bond between the display panel and the cover glass. This helps to prevent damage to the display from external forces.
- Optics: Display Bonding Adhesive can also be used to improve the optical performance of industrial displays. By bonding the display panel and the cover glass, it is possible to reduce the air gap between them, which can cause reflection and reduce the display’s contrast. This results in better image quality and readability in bright environments.
- Touch screen integration: Industrial displays often come with touch screen capabilities. Display Bonding Adhesive ensures that the touch screen is securely bonded to the display panel, providing a seamless and durable touch interface.
- Durability: Display Bonding Adhesive provides a strong and durable bond between the display panel and the cover glass or touch screen, ensuring that the display can withstand the rigors of industrial use. This helps to reduce the need for repairs and replacements, resulting in cost savings for the manufacturer and the end user.
Advancements in Display Bonding Adhesive for Foldable Screens
Foldable screens have become increasingly popular with the rise of foldable smartphones, tablets, and laptops. These screens are made possible by flexible OLED panels, which can bend and fold without breaking. However, the OLED panel must be bonded to a flexible substrate such as plastic or thin glass to create a foldable screen, and this bonding is typically done using a display bonding adhesive (DBA).
Advancements in DBA technology have been crucial in making foldable screens more durable and reliable. Early foldable screens had issues with the adhesive layer cracking or delaminating, leading to visible creases or screen failure. However, new DBAs are specifically designed to be flexible and withstand the stresses of repeated folding and unfolding.
One of the significant challenges in developing DBAs for foldable screens is achieving a balance between flexibility and strength. The adhesive must be strong enough to hold the OLED panel to the substrate and flexible sufficient to allow the screen to bend and fold without cracking or delaminating. This requires careful selection of materials and optimization of the bonding process.
DBA manufacturers have developed new formulations to address these challenges, incorporating high-performance polymers and other additives to improve flexibility, strength, and durability. For example, some DBAs use polyurethane or silicone elastomers to provide flexibility, while others incorporate nanoparticles or other reinforcements to enhance stability and resistance to wear.
In addition to improving the adhesive properties of DBAs, manufacturers have also developed new application methods to ensure even and consistent bonding across the entire screen. Some ways use precision dispensing equipment to apply the adhesive in a controlled manner, while others use roll-to-roll processing to apply the adhesive in a continuous, automated process.
Sustainability and Environmental Considerations for Display Bonding Adhesive
Here are some sustainability and environmental considerations for display bonding adhesives:
- Chemical composition: The chemical composition of display bonding adhesives can significantly impact their environmental impact. For example, some adhesives contain harmful substances such as volatile organic compounds (VOCs) or heavy metals that can pollute the air, water, and soil during manufacturing and disposal.
- Energy consumption: The manufacturing process of display bonding adhesives requires significant energy, which can lead to a high carbon footprint. It is crucial to consider the energy source used in manufacturing and explore ways to reduce energy consumption.
- Waste reduction: The production of display bonding adhesives generates waste, such as packaging and leftover adhesive material. It is essential to implement waste reduction strategies, such as recycling, to reduce the amount of waste generated.
- End-of-life management: The disposal of electronic devices containing display bonding adhesives can have significant environmental impacts. It is crucial to develop end-of-life management strategies that consider the recycling and proper disposal of electronic devices to minimize their ecological impact.
- Sustainable sourcing: It is crucial to ensure that the materials used in manufacturing display bonding adhesives are sustainably sourced. This includes sourcing materials from suppliers that practice sustainable forestry and avoid harmful substances like conflict minerals.
Regulatory Requirements for Display Bonding Adhesive
Display bonding adhesive is a critical component in manufacturing electronic devices with displays, such as smartphones, tablets, and laptops. As such, regulatory requirements must be met to ensure the safety and efficacy of these products.
One of the key regulatory bodies governing the use of display bonding adhesive is the International Electrotechnical Commission (IEC). The IEC has developed a series of standards that define the performance and safety requirements for adhesives used in electronic devices.
In particular, the IEC 62368-1 standard sets out safety requirements for audio/video, information, and communication technology equipment. It covers various aspects of safety, including electrical security, mechanical protection, and thermal safety. Adhesives used in display bonding must meet the requirements outlined in this standard to ensure that the final product is safe for consumers.
Another regulatory body that oversees the use of display bonding adhesive is the Restriction of Hazardous Substances (RoHS) Directive. This directive restricts certain hazardous substances in electronic and electrical equipment. Adhesives used in display bonding must comply with the requirements of the RoHS Directive to ensure that they do not contain dangerous substances such as lead, mercury, and cadmium.
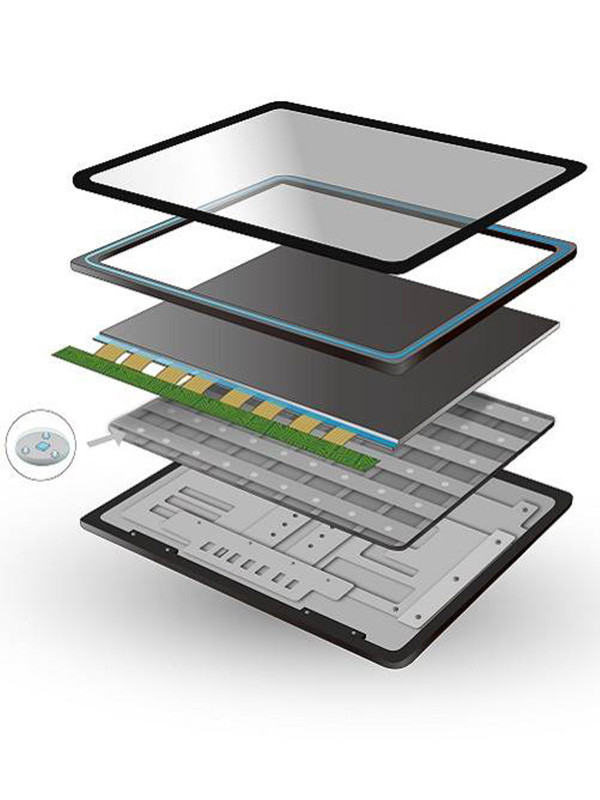
In addition to these regulatory requirements, manufacturers of display bonding adhesive must also consider the specific needs of their customers, which may vary depending on the application and industry. For example, adhesives used in medical devices must meet the requirements of the US Food and Drug Administration (FDA), while those used in aerospace applications must meet the needs of the National Aerospace and Defense Contractors Accreditation Program (NADCAP).
Market Trends and Opportunities for Display Bonding Adhesive
Here are some market trends and opportunities for display bonding adhesive:
- Increasing demand for smartphones and tablets: With the increasing popularity of smartphones and tablets, the need for DBA is expected to increase. DBA is used to attach the display to the device, and as the number of smartphones and tablets sold worldwide increases, so will the demand for DBA.
- Advancements in technology: Electronic devices are becoming thinner and lighter as technology advances. DBA must also become thinner and more flexible to keep up with the market’s demands. The development of new, high-performance DBA will create opportunities for manufacturers to provide products that meet the needs of the latest electronic devices.
- Growth of the TV market: As the television market continues to grow, so will the demand for DBA. As television manufacturers look for ways to create thinner and more aesthetically pleasing products, DBA will be essential in attaching the display to the device.
- Increased focus on sustainability: Many consumers are becoming more environmentally conscious and are looking for eco-friendly products. This presents an opportunity for manufacturers to develop DBA made from sustainable materials that can be recycled at the end of the product’s life cycle.
- Growth in emerging markets: As emerging markets such as China and India continue to grow, so will the demand for electronic devices. This presents an opportunity for manufacturers to expand their business into these markets and provide DBA to meet the needs of these consumers.
Cost Factors and Pricing Strategies for Display Bonding Adhesive
Here are some cost factors and pricing strategies for display bonding adhesive:
- Type and Quality of Adhesive: There are various types of DBA available in the market, such as acrylic, epoxy, and polyurethane, each with unique properties and advantages. The quality of the adhesive is also an essential factor in determining its price. High-quality bonds generally cost more than low-quality ones.
- Quantity and Packaging: The DBA required for a particular application can affect the cost. Bulk orders usually result in lower costs per unit compared to smaller orders. The packaging of the adhesive can also affect its price, with smaller or specialized packaging options costing more.
- Supplier and Manufacturing Costs: The supplier of DBA can also influence its cost, with larger and established suppliers often charging higher prices than smaller ones. Manufacturing costs such as raw materials, labor, and equipment can also affect the price of the adhesive.
Pricing strategies for DBA:
- Cost-Plus Pricing: This pricing strategy involves adding a markup to the cost of the adhesive to determine its selling price. This markup can be based on the desired profit margin, competition, and market demand.
- Value-Based Pricing: This strategy involves setting a price based on the perceived value of the adhesive to the customer. The value can be determined by the adhesive’s unique properties, quality, and performance.
- Competitive Pricing: This strategy involves setting a price based on the costs of competitors’ products. This approach can help the supplier remain competitive in the market.
- Bundling Pricing: This strategy involves offering DBA as part of a bundle with other products or services, which can increase the perceived value and justify a higher price.
Future Developments in Display Bonding Adhesive Technology
In the future, several developments are expected to occur in display bonding adhesive technology:
- Thinner and Stronger Adhesives: One of the most critical developments in display bonding adhesive technology is the development of lighter and stronger adhesives. These adhesives will enable manufacturers to create devices with slimmer bezels and smaller form factors without sacrificing structural integrity.
- Increased Flexibility: Besides being thinner and more robust, future display bonding adhesives are expected to be more flexible. This will make it possible to create curved or flexible displays, which can be used in various applications, including wearable devices and automotive displays.
- Improved Durability: Display bonding adhesives will also be developed with enhanced durability to withstand the wear and tear of everyday use. This will ensure that devices with bonded displays have a longer lifespan and require less frequent repairs or replacements.
- Better Optical Performance: Another critical development in display bonding adhesive technology is improving optical performance. Adhesives will be developed that minimize the amount of light reflection and distortion, resulting in displays with better clarity and color accuracy.
- More Environmentally-Friendly Adhesives: As consumers become more conscious of their environmental impact, there will be a growing demand for environmentally friendly display bonding adhesives. Future adhesives will be developed that are free of toxic chemicals and can be recycled or disposed of in an environmentally-responsible manner.
Conclusion: Key Takeaways about Display Bonding Adhesive
Display bonding adhesive (DBA) is used to bond the display panel of electronic devices, such as smartphones and tablets, to the device’s frame or housing. Here are some key takeaways about DBA:
- DBA is a critical component in the manufacturing of electronic devices, as it helps to hold the display panel in place and protect it from damage.
- DBA can be made from various materials, including acrylics, epoxies, and polyurethanes.
- The properties of DBA can vary depending on the material used, including its adhesion strength, flexibility, and resistance to heat and moisture.
- The application process for DBA typically involves dispensing the adhesive onto the frame or housing of the device, then placing the display panel on top and applying pressure to ensure a strong bond.
- DBA plays a crucial role in electronic devices’ overall durability and reliability, as a weak or faulty bond can lead to display damage or malfunction.
Overall, display bonding adhesive is an essential component in the manufacturing of electronic devices and plays a critical role in ensuring their durability and functionality.
FAQs about Display Bonding Adhesive
Q: What is Display Bonding Adhesive?
A: Display Bonding Adhesive (DBA) is an adhesive used to bond the display panel to the cover glass or touch sensor in electronic devices such as smartphones, tablets, and laptops.
Q: How does Display Bonding Adhesive work?
A: Display Bonding Adhesive creates a solid and durable bond between the display panel and the cover glass or touch sensor, using a combination of chemical and physical adhesion. The adhesive is typically applied to the surface of the display panel or cover glass/touch sensor and then cured using heat or UV light.
Q: What are the benefits of using Display Bonding Adhesive?
A: The benefits of using Display Bonding Adhesive include improved durability and reliability of electronic devices, increased resistance to shock and impact, enhanced optical clarity, and reduced manufacturing costs.
Q: What are the types of Display Bonding Adhesive?
A: There are several types of Display Bonding Adhesives, including acrylic-based, epoxy-based, and silicone-based adhesives. The choice of adhesive depends on the application’s specific requirements, such as bonding strength, temperature resistance, and optical properties.
Q: What are the challenges in using Display Bonding Adhesive?
A: Some challenges in using Display Bonding Adhesive include the potential for air bubbles or dust particles to become trapped between the display panel and cover glass/touch sensor during the bonding process, which can affect the optical quality and reliability of the device. In addition, the adhesive must be compatible with the materials used in the device and withstand the thermal and mechanical stresses encountered during use.
Q: What are some best practices for using Display Bonding Adhesive?
A: Some best practices for using Display Bonding Adhesive include ensuring that the surfaces to be bonded are clean and free from contaminants, using a consistent and controlled adhesive application, and optimizing the curing process to achieve the desired bonding strength and optical quality. It is also important to carefully test and validate the adhesive performance under various environmental and usage conditions.
Glossary of Terms related to Display Bonding Adhesive
- Display Bonding Adhesive (DBA) – An adhesive used to bond the display panel to the device’s frame or body.
- Liquid Optically Clear Adhesive (LOCA) – A type of DBA liquid adhesive that cures to form a transparent solid.
- Film Optically Clear Adhesive (FOCA) – A type of DBA that is a thin film adhesive with high optical clarity used in curved display devices.
- Viscosity – The thickness or fluidity of the adhesive, which affects its ability to spread and bond surfaces.
- Cure time – The adhesive must reach full strength and hardness after application.
- Adhesion strength – The ability of the adhesive to bond two surfaces together.
- Peel strength – The force required to peel the bonded surfaces apart.
- UV resistance – The ability of the adhesive to withstand exposure to ultraviolet radiation without degradation or discoloration.
- Thermal conductivity – The ability of the adhesive to transfer heat from one surface to another.
- Outgassing – The release of volatile compounds from the adhesive, which can cause damage to sensitive electronic components.
- Hydrophobic – The ability of the adhesive to repel water.
- Solvent resistance – The ability of the adhesive to withstand exposure to solvents without degradation or weakening of the bond.
- Dielectric constant – The ability of the adhesive to insulate electrical charges.
- Tackiness – The stickiness of the adhesive, which affects its ability to adhere to surfaces.
References and Resources for Display Bonding Adhesive
Display bonding adhesive (DBA) attaches touchscreens, display panels, and other components to electronic devices such as smartphones, tablets, and laptops. Here are some references and resources for learning more about DBA:
- “Display Bonding Adhesives: Key Considerations for Smart Mobile Device Design” by 3M: This white paper provides an overview of DBA technology, the critical considerations for selecting a DBA, and best design practices with DBA.
- “Adhesives for Display Bonding” by DeepMaterial: This webpage provides information about DeepMaterial’s DBA product line, including technical data sheets, application guides, and case studies.
- “Display Bonding Adhesives” by Dow: This webpage provides an overview of Dow’s DBA technology, including technical data sheets, application guides, and case studies.
- “Adhesives for Display Bonding” by Momentive: This webpage provides information about Momentive’s DBA product line, including technical data sheets, application guides, and case studies.
- “Adhesives for Display Bonding” by Dupont: This webpage provides information about Dupont’s DBA product line, including technical data sheets, application guides, and case studies.
- “Display Bonding Adhesives: Choosing the Right Adhesive for Your Display Application” by Techsil: This article provides an overview of DBA technology, the critical considerations for selecting a DBA, and a comparison of different types of DBA.
- “Display Bonding Adhesives: Improving Durability and Performance of Electronics” by Master Bond: This article provides an overview of DBA technology, the critical considerations for selecting a DBA, and a comparison of different types of DBA and their applications.
- “Display Bonding Adhesives for Smart Mobile Devices” by Avery Dennison: This white paper provides an overview of DBA technology, the critical considerations for selecting a DBA, and best practices for designing with DBA.
- “Adhesives for Display Bonding” by H.B. Fuller: This webpage provides information about H.B. Fuller’s DBA product line, including technical data sheets, application guides, and case studies.
- “Display Bonding Adhesives” by DeepMaterial: This webpage provides an overview of DeepMaterial’s DBA technology, including technical data sheets, application guides, and case studies.
Many resources are available to learn more about DBA technology and select the suitable adhesive for your display application.