Polypropylene Bonding Adhesive
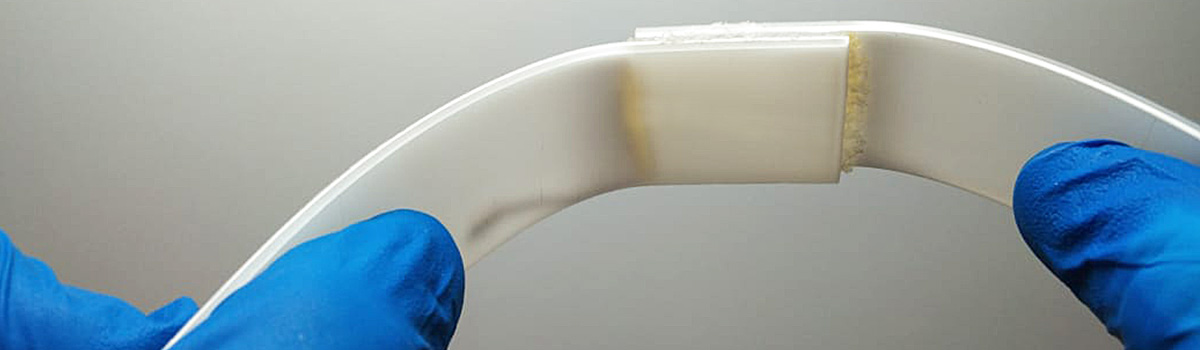
Polypropylene (PP) is a versatile thermoplastic polymer widely used in various applications due to its exceptional properties, including lightweight, durability, and resistance to chemical and thermal degradation. However, bonding polypropylene can be challenging due to its low surface energy, which makes it difficult for adhesives to form a strong bond. Polypropylene bonding adhesives have been developed to overcome this challenge, revolutionizing the manufacturing and industry landscape. This article explores the various applications of polypropylene bonding adhesives, their benefits, and the different types available.
The Role of Polypropylene Bonding Adhesives in Industry
Polypropylene bonding adhesives are crucial in various industries, offering reliable bonding solutions for multiple applications. Polypropylene (PP) is a popular thermoplastic polymer known for its low density, high chemical resistance, and excellent durability. However, bonding PP can be challenging due to its low surface energy, which makes it difficult for conventional adhesives to adhere effectively. This is where polypropylene bonding adhesives come into play, providing the necessary adhesion strength and durability required for industrial applications.
Polypropylene bonding adhesives are specifically formulated to address the unique properties of PP. They contain specialized adhesion promoters and additives that enhance the bonding process. These adhesives are designed to create intermolecular solid bonds with the PP surface, ensuring reliable and long-lasting adhesion.
Polypropylene bonding adhesives are widely used in the automotive industry for various applications. They are employed in the assembly of interior and exterior components, such as dashboards, door panels, and bumpers. The adhesives enable secure bonding of these parts, ensuring structural integrity and improving overall vehicle safety. Additionally, the flexibility of PP bonding adhesives allows for absorbing vibrations and shocks, enhancing the durability of automotive assemblies.
The packaging industry also benefits from polypropylene bonding adhesives. PP is commonly used for food packaging, as it is resistant to moisture and chemicals. Adhesives formulated for bonding PP enable the production of solid and secure seals in packaging applications, preventing leakage and maintaining product freshness. These adhesives provide excellent bond strength, even at low temperatures, making them suitable for refrigerated and frozen food packaging.
Polypropylene bonding adhesives are extensively utilized in the medical field as well. Medical devices and equipment often incorporate PP components due to their biocompatibility and resistance to sterilization processes. Adhesives designed for bonding PP in medical applications offer exceptional chemical resistance and durability, ensuring reliable performance in demanding environments. They are used to assemble devices such as syringes, catheters, and IV sets, where secure bonding is critical for patient safety.
Moreover, the electronics industry relies on polypropylene bonding adhesives for various applications. With the increasing demand for lightweight and compact electronic devices, PP is used to manufacture casings, connectors, and circuit boards. Bonding adhesives enable the reliable attachment of these components, providing electrical insulation, thermal management, and protection against environmental factors.
The Challenge of Bonding Polypropylene: Surface Energy
Bonding polypropylene (PP) poses a significant challenge due to its low surface energy. Surface energy refers to the energy required to break the intermolecular bonds on the surface of a material. PP has a relatively low surface energy, making it difficult for adhesives to wet and adhere to its surface effectively. This creates a barrier to achieving robust and durable bonds with conventional adhesives, as they rely on intimate contact between the adhesive and the substrate.
The low surface energy of PP arises from its molecular structure, which consists mainly of hydrocarbon chains. These chains have weak van der Waals forces, producing a low affinity for polar substances like adhesives. As a result, bonds tend to bead up and form droplets on the PP surface, preventing proper wetting and adhesion.
To overcome the challenge of bonding PP, specialized adhesive formulations have been developed. These adhesives are designed to increase the surface energy of PP, allowing for improved wetting and bonding. One common approach is the inclusion of adhesion promoters in the adhesive formulation. Adhesion promoters are typically surface-active compounds that migrate to the PP surface and reduce their contact angle, promoting better wetting. These promoters contain functional groups that can react with the PP surface, creating chemical bonds and enhancing the adhesive’s affinity for the substrate.
Another strategy involves modifying the PP surface itself to increase its surface energy. This can be achieved through surface treatments such as corona discharge, plasma, or flame treatment. These methods introduce reactive species onto the PP surface, creating functional groups that facilitate bonding with adhesives. The treated PP surface exhibits increased surface energy, promoting better wetting and adhesion.
Additionally, some manufacturers have developed specialized adhesives formulated explicitly for bonding low-surface energy materials like PP. These adhesives often incorporate unique chemistry or additives that enhance their compatibility with PP. They are designed to penetrate the surface of PP, improving wetting and promoting intermolecular bonding.
It is worth noting that proper surface preparation is essential when bonding PP. The PP surface should be thoroughly cleaned to remove contaminants, oils, or residues that may hinder adhesion. Additionally, surface treatments or primers may be necessary to optimize the bonding process.
How Polypropylene Bonding Adhesives Overcome the Challenge
Polypropylene (PP) is a challenging material to bond due to its low surface energy and non-polar nature. However, with the development of polypropylene bonding adhesives, it is now possible to achieve firm and durable bonds with this difficult-to-adhere-to material. Here’s how polypropylene bonding adhesives overcome the challenges:
- Surface Preparation: The first step in bonding polypropylene is surface preparation. Polypropylene has low surface energy, which makes it difficult for adhesives to wet and adhere to the surface. Polypropylene bonding adhesives are formulated with special additives that help increase the polypropylene’s surface energy, allowing for better adhesion. These additives can modify the surface of the polypropylene, enabling the adhesive to spread and create a stronger bond.
- Chemical Compatibility: Polypropylene bonding adhesives are designed to have excellent chemical compatibility with polypropylene. They are formulated with adhesion promoters and primers that ensure a strong chemical interaction between the adhesive and the polypropylene surface. This chemical compatibility improves the wetting and spreading ability of the adhesive, resulting in improved bond strength.
- Structural Formulation: Polypropylene bonding adhesives are engineered to have a unique structural formulation that enables them to bond effectively with polypropylene. They often contain specialized polymers and resins with a strong affinity for polypropylene, allowing them to penetrate and interlock with the material’s surface. This structural design ensures a cohesive bond, enhancing the adhesive joint’s initial strength and long-term durability.
- Heat Activation: In some cases, polypropylene bonding adhesives require heat activation to achieve optimal bonding. Heat can increase the polypropylene’s surface energy, allowing the adhesive to wet and bond to the material. Polypropylene bonding adhesives are formulated to withstand the necessary heating process without losing their adhesive properties, ensuring a reliable bond even in demanding applications.
- Adhesive Selection: Selecting the suitable adhesive is crucial for successful polypropylene bonding. Polypropylene bonding adhesives come in various formulations, each tailored to specific bonding requirements. When choosing the glue, factors such as application method, environmental conditions, and desired bond strength must be considered. Manufacturers provide a range of options, including cyanoacrylates, polyolefin adhesives, and modified acrylics, allowing users to select the most suitable adhesive for their specific needs.
- Testing and Validation: Polypropylene bonding adhesives undergo rigorous testing and validation to ensure their performance and reliability. Adhesive manufacturers conduct comprehensive tests to assess the bond’s strength, durability, and resistance under different conditions, such as temperature, humidity, and chemical exposure. These tests provide valuable data and guidance for selecting the appropriate adhesive and optimizing the bonding process for polypropylene.
Benefits of Polypropylene Bonding Adhesives
Polypropylene bonding adhesives offer several benefits, making them an excellent choice for bonding polypropylene and overcoming its inherent challenges. Here are some key advantages of using polypropylene bonding adhesives:
- Solid and Durable Bonds: Polypropylene bonding adhesives are specifically formulated to provide robust and durable bonds with polypropylene. These adhesives penetrate the material’s surface, creating a cohesive bond that can withstand various stresses, including mechanical forces, temperature fluctuations, and chemical exposure. The resulting bonds exhibit excellent shear strength, peel strength, and impact resistance.
- Versatility: Polypropylene bonding adhesives offer versatility in bonding different types of polypropylene, including homopolymer and copolymer variations. They can connect various polypropylene-based products, such as automotive parts, consumer goods, packaging materials, and industrial components. This versatility makes them suitable for diverse industries and applications.
- Improved Manufacturing Efficiency: These adhesives can streamline the manufacturing process by enabling the adequate bonding of polypropylene. They eliminate the need for mechanical fasteners like screws, rivets, or welds, reducing assembly time and costs. Polypropylene bonding adhesives also provide uniform stress distribution across the bonded area, which helps to reduce stress concentrations and potential failure points in the assembly.
- Enhanced Design Flexibility: Polypropylene bonding adhesives offer greater design flexibility than traditional bonding methods. They can bond dissimilar materials, such as polypropylene, to other plastics, metals, or composites, creating hybrid structures. This flexibility opens up opportunities for lightweight design, improved aesthetics, and innovative product development.
- Improved Aesthetics: Polypropylene bonding adhesives create clean, seamless bonds without visible fasteners or marks. This improves the overall appearance of the bonded assembly, making it more aesthetically pleasing. These adhesives provide an advantage over traditional joining techniques in applications where visual appeal is essential, such as consumer electronics or automotive interiors.
- Chemical Resistance: Polypropylene bonding adhesives resist various chemicals, solvents, oils, and environmental factors. They maintain their bonding integrity even when exposed to harsh conditions, ensuring the long-term durability and reliability of the bonded assembly. This chemical resistance is particularly advantageous in industries such as automotive, chemical processing, and medical devices, where exposure to aggressive substances occurs daily.
- Increased Product Performance: Polypropylene bonding adhesives can enhance the overall performance of polypropylene-based products. The adhesive joints distribute stress evenly, reducing the risk of localized failure. They also provide vibration damping and noise reduction properties, improving the assembled product’s overall functionality and user experience.
- Environmental Friendliness: Many polypropylene bonding adhesives are formulated to be environmentally friendly. They are free from volatile organic compounds (VOCs) and hazardous substances, making them safe for various applications. Furthermore, eliminating mechanical fasteners reduces material waste and simplifies the disassembly and recycling of end-of-life products.
Types of Polypropylene Bonding Adhesives
Polypropylene (PP) is a popular thermoplastic polymer widely used in various industries due to its excellent chemical resistance, low density, and high stiffness. However, bonding polypropylene can be challenging because it has low surface energy, making it difficult for adhesives to form strong bonds. To overcome this challenge, specialized polypropylene bonding adhesives have been developed. In this article, we will explore some common adhesive types used for bonding polypropylene.
- Cyanoacrylate Adhesives: Cyanoacrylate adhesives, commonly known as superglues, are popular for bonding polypropylene. These adhesives polymerize quickly in moisture, forming a solid bond. However, to enhance the bonding strength, a surface activator is often used to promote adhesion between the adhesive and the polypropylene surface.
- Structural Adhesives: Structural adhesives, such as two-component epoxies and acrylics, are widely used for bonding polypropylene in applications that require high strength and durability. These adhesives perform excellently by creating solid chemical bonds with the polypropylene surface. They typically require surface preparation, such as cleaning and roughening, to enhance adhesion.
- Polyolefin Bonding Adhesives: Polyolefin bonding adhesives are designed for bonding polyolefin materials like polypropylene. These adhesives contain functional additives that improve their adhesion to low-energy surfaces. They often require surface treatment, such as flame treatment or corona discharge, to increase the surface energy of polypropylene, enabling better adhesion.
- Hot Melt Adhesives: Hot melt adhesives are thermoplastic adhesives that are melted and applied in a molten state. They solidify upon cooling, forming a solid bond. Some hot melt adhesives are specifically formulated for bonding polypropylene. These adhesives provide good adhesion and fast curing time, making them suitable for high-speed manufacturing.
- Modified Polyolefin Adhesives: Modified polyolefin adhesives are specialized adhesives containing additives that enhance their bonding performance with polypropylene. These adhesives typically require surface treatment to improve adhesion. They resist environmental factors such as moisture and chemicals, making them suitable for demanding applications.
- Polyurethane Adhesives: Polyurethane adhesives are versatile adhesives that can bond a wide range of materials, including polypropylene. They provide excellent flexibility and durability in bonded joints. Polyurethane adhesives for polypropylene often require surface activation techniques, such as plasma treatment, to achieve strong adhesion.
- UV-Curable Adhesives: UV-curable adhesives are single-component adhesives that cure rapidly when exposed to ultraviolet light. They offer fast processing times and can bond polypropylene effectively with the help of surface activators. These adhesives are often used in applications requiring instant curing and high bond strength.
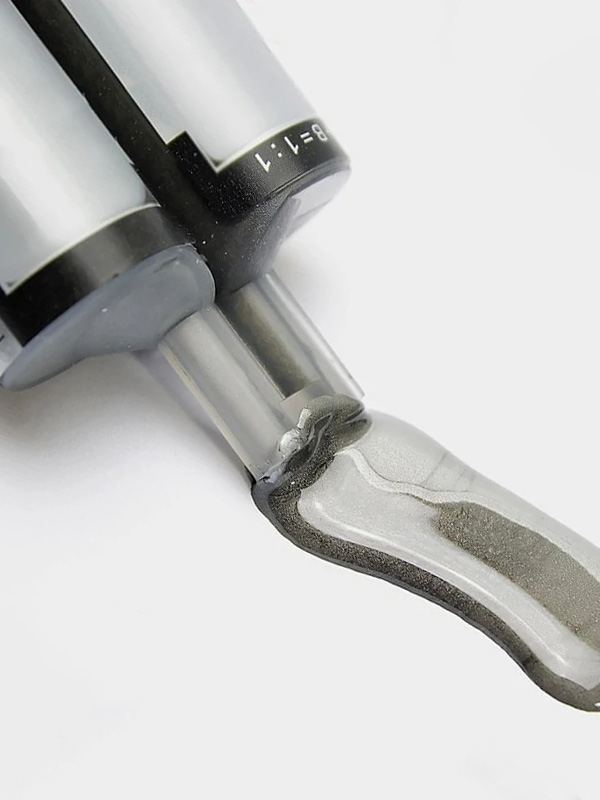
Structural Adhesives: Joining Dissimilar Materials
Structural adhesives play a crucial role in joining dissimilar materials, providing a solid, durable bond that withstands various conditions and loads. Combining different materials is essential in multiple industries, including automotive, aerospace, construction, and electronics. This article will explore the characteristics, advantages, and applications of structural adhesives for joining dissimilar materials.
Structural adhesives are specially formulated adhesives designed to bond different types of materials, such as metals, plastics, composites, ceramics, and even different combinations of these materials. They offer several advantages over traditional joining methods like mechanical fasteners or welding. One of the primary benefits is their ability to distribute stress evenly across the joint, resulting in enhanced load-bearing capacity and improved overall structural integrity.
One of the critical characteristics of structural adhesives is their high strength. They are designed to provide a bond often more robust than the joined materials. This high strength is crucial when joining dissimilar materials, as it helps compensate for any mechanical properties differences between them. By evenly distributing the stress, structural adhesives prevent stress concentration and reduce joint failure risk.
Another important characteristic of structural adhesives is their excellent chemical resistance. They can withstand exposure to various chemicals, solvents, fuels, and environmental conditions, making them suitable for multiple applications. This resistance to chemicals ensures the longevity of the bond, even when the joined materials may have different chemical properties.
Structural adhesives also offer flexibility in terms of design and manufacturing. They can be applied in various forms, such as liquids, pastes, films, or tapes, allowing for precise application and adaptability to different joint configurations. Additionally, they provide uniform stress distribution along the entire bond line, eliminating the need for additional reinforcement or support structures, which can simplify the overall design and reduce weight.
The applications of structural adhesives for joining dissimilar materials are vast. In the automotive industry, they are used to bond metals and composites, improving vehicle safety, reducing weight, and enhancing fuel efficiency. In aerospace, they play a critical role in joining materials with different coefficients of thermal expansion, providing reliable bonds that withstand extreme temperatures and vibrations. Structural adhesives are also widely used in the construction sector, where they join dissimilar materials like concrete, metal, and wood, creating solid and durable structures.
Pressure-Sensitive Adhesives: Easy Application and Removal
Pressure-sensitive adhesives (PSAs) are versatile adhesives that offer easy application and removal properties. These adhesives adhere to surfaces when slight pressure is applied and can be removed without leaving residue behind or damaging the substrate. In this article, we will explore pressure-sensitive adhesives’ characteristics, advantages, and applications, focusing on their ease of use in both application and removal processes.
One of the critical characteristics of pressure-sensitive adhesives is their ability to bond instantly upon contact with a surface under light pressure. This makes them highly convenient and easy to use. Unlike other adhesives that require curing or drying time, PSAs provide immediate bonding, allowing for efficient and quick assembly processes. This property is particularly beneficial in industries where fast production rates are required.
Another advantage of pressure-sensitive adhesives is their ease of application. They are typically supplied as tapes, films, or sheets, which can be easily cut to size and applied to various substrates. The adhesive properties of PSAs are activated by applying slight pressure, such as finger pressure or the weight of an object, making them highly user-friendly. This ease of application eliminates the need for additional tools or equipment, reducing complexity and saving time during the bonding process.
Furthermore, pressure-sensitive adhesives offer excellent removability without causing damage or leaving residue on the substrate. When removing PSA-bonded materials, they can be peeled off easily without requiring solvents or other removal agents. This feature is essential in applications where temporary bonds or repositioning of components are necessary, such as in labeling, graphics, or protective films. The clean and residue-free removal of PSAs also ensures that surfaces can be reused or easily prepared for subsequent processes.
PSAs find a wide range of applications due to their easy application and removal properties. In the consumer goods industry, they are used in everyday products such as tapes, labels, and sticky notes. These products rely on the convenience and reliability of PSAs for temporary or semi-permanent bonding. In the medical field, PSAs are utilized in bandages, wound dressings, and medical tapes, providing secure adhesion and pain-free removal. The electronics industry also benefits from PSAs, used in mounting components, display screens, and touch panels, offering easy assembly and repair.
Solvent-Based Adhesives: Fast Curing and High Strength
Solvent-based adhesives are a type of adhesive that offer fast curing and high strength properties. These adhesives are formulated with solvents that evaporate during curing, resulting in a strong bond between the joined surfaces. This article will explore solvent-based adhesives’ characteristics, advantages, and applications, focusing on their fast curing and high-strength capabilities.
One of the critical advantages of solvent-based adhesives is their fast curing time. Solvents in the adhesive formulation enable rapid evaporation, accelerating the curing process. When the solvent evaporates, the adhesive undergoes a phase change and transforms into a solid, creating a strong bond between the joined surfaces. This fast curing time is particularly beneficial in industries where quick assembly or production rates are essential, reducing downtime and increasing efficiency.
Solvent-based adhesives also offer high-strength bonds. The evaporation of solvents during the curing process allows the sealant to penetrate and bond effectively with the substrate materials. This strong bond contributes to enhanced load-bearing capacity and durability of the joint. Solvent-based adhesives are known for their ability to withstand various stresses, including shear, tension, and impact, making them suitable for applications that require reliable and long-lasting bonds.
Another advantage of solvent-based adhesives is their versatility in bonding different materials. They can effectively bond materials such as metals, plastics, composites, rubber, and porous substrates. This versatility makes solvent-based adhesives widely used in the automotive, aerospace, construction, and electronics industries. They can join dissimilar materials, providing a robust and reliable bond that withstands the unique challenges of different material combinations.
Solvent-based adhesives also resist heat, chemicals, and environmental conditions. Once cured, they exhibit excellent resistance to high temperatures, moisture, and solvents, ensuring the longevity of the bond even in harsh operating environments. This resistance to various external factors contributes to the overall durability and reliability of the adhesive joint.
The applications of solvent-based adhesives are vast. The automotive industry commonly uses them for bonding parts, such as interior trim, exterior panels, and structural components. In the construction sector, they play a vital role in bonding materials like wood, glass, and metal, providing strong and durable connections in applications such as furniture, windows, and doors. Solvent-based adhesives are also widely utilized in the electronics industry for bonding components, circuit boards, and wire harnesses, where high strength and fast curing are crucial.
Hot Melt Adhesives: Low Cost and Versatile
Hot melt adhesives (HMAs) are a type of adhesive that offers low cost and versatility in a wide range of applications. These adhesives are solid at room temperature but melt when heated, allowing for easy application and rapid bonding. In this article, we will explore hot melt adhesives’ characteristics, advantages, and applications, focusing on their low cost and versatility.
One of the critical advantages of hot melt adhesives is their low cost. Compared to other types of bonds, HMAs are generally more affordable. They are made from a combination of thermoplastic polymers, resins, and additives, which are readily available and cost-effective to produce. This cost advantage makes hot melt adhesives a preferred choice in industries where cost efficiency is a priority, such as packaging, woodworking, and product assembly.
Hot melt adhesives also offer versatility in terms of application and bonding capabilities. They are available in various formulations, including different viscosities, open times, and setting speeds, allowing customization based on specific application requirements. HMAs can bond many materials, including paper, cardboard, wood, plastics, fabrics, and metals, making them suitable for diverse applications in packaging, automotive, textiles, and electronics.
Another advantage of hot melt adhesives is their rapid bonding time. Once applied, HMAs cool and solidify quickly, forming a solid bond within seconds to minutes, depending on the specific formulation and ambient conditions. This fast bonding time increased productivity and reduced assembly time in manufacturing processes. The quick setting speed also enables efficient handling and packaging of bonded products without clamps or additional support.
HMAs are also known for their good heat resistance and durability. Once cooled and solidified, they exhibit excellent resistance to heat, allowing them to maintain their bond strength even under elevated temperatures. This property makes hot melt adhesives suitable for applications where heat exposure is a concern, such as automotive interiors, electronics, and appliances.
Hot melt adhesives have numerous applications due to their low cost and versatility. In the packaging industry, they are widely used for sealing cartons, boxes, and envelopes, providing secure and efficient closure. In woodworking, HMAs are employed for edge banding, laminating, and assembly of furniture and cabinetry. Textile applications include bonding fabrics in garment manufacturing, footwear, and automotive interiors. Hot melt adhesives are also utilized in electronics assembly for bonding components, wire tacking, and potting.
UV-Curable Adhesives: Environmentally-Friendly and High Performance
UV-curable adhesives have gained significant attention in recent years due to their unique combination of environmental friendliness and high performance. These adhesives offer numerous advantages over traditional solvent-based adhesives, making them an excellent choice for various applications.
UV-curable adhesives are formulated using a combination of oligomers, monomers, and photoinitiators. Unlike solvent-based adhesives that rely on volatile organic compounds (VOCs) for curing, UV-curable adhesives cure rapidly upon exposure to ultraviolet light. This characteristic eliminates the need for extended drying or curing times, resulting in significant time savings during production processes.
One of the most compelling advantages of UV-curable adhesives is their environmentally-friendly nature. Since they do not contain harmful VOCs, these adhesives minimize air pollution and contribute to improved air quality. UV-curable bonds have low levels of hazardous materials and are free from toxic chemicals such as solvents and isocyanates. This eco-friendly composition makes them an ideal choice for industries aiming to reduce their environmental footprint.
In terms of performance, UV-curable adhesives exhibit exceptional bonding strength and durability. They provide strong adhesion to various substrates, including plastics, metals, glass, and composites. The rapid curing process ensures that the adhesive forms a strong bond quickly, enhancing production efficiency. Moreover, UV-curable adhesives offer excellent resistance to chemicals, temperature variations, and moisture, making them suitable for demanding applications in harsh environments.
UV-curable adhesives also enable precise and controlled curing. The curing process occurs only when exposed to UV light, allowing manufacturers complete control over the bonding process. This characteristic is particularly advantageous for applications that require accurate alignment of components or intricate geometries. The instant curing ability eliminates the need for clamping or additional fixturing, streamlining assembly processes.
Another essential benefit of UV-curable adhesives is their versatility. Adjusting the formulation and curing parameters can be tailored to meet specific application requirements. The adhesive’s viscosity can be modified to achieve the desired flow characteristics, ensuring optimal coverage and penetration. Furthermore, the curing intensity can be adjusted to accommodate different material thicknesses and substrates.
The use of UV-curable adhesives also promotes energy efficiency. Since the curing process is triggered by UV light exposure, energy consumption is significantly reduced compared to heat-curing methods. This energy efficiency contributes to cost savings and aligns with sustainability initiatives.
Polyolefin Plastics: Ideal Substrates for Polypropylene Bonding Adhesives
Polyolefin plastics, particularly polypropylene (PP), are widely used in various industries due to their excellent chemical resistance, low cost, and lightweight nature. However, bonding polypropylene can be challenging because of its soft surface energy and poor adhesion properties. To overcome this hurdle, specialized polypropylene bonding adhesives have been developed.
Polypropylene has low surface energy, making it difficult for conventional adhesives to form strong and durable bonds. However, polypropylene bonding adhesives are specifically formulated to address this issue. These adhesives contain unique chemistries that enable adequate bonding to polyolefin substrates, especially polypropylene.
One key characteristic of polypropylene bonding adhesives is their ability to promote adhesion on low-energy surfaces. They contain specific additives that enhance the surface energy of polypropylene, allowing for improved wetting and spreading of the adhesive. This increased surface energy facilitates better adhesion between the adhesive and the polypropylene substrate, resulting in more robust and durable bonds.
Polypropylene bonding adhesives also exhibit excellent chemical resistance. Polypropylene is known for its resistance to a wide range of chemicals, and the adhesives used for bonding polypropylene are formulated to complement this property. They can withstand exposure to various solvents, oils, and harsh chemicals without compromising the integrity of the bond. This chemical resistance is crucial for applications where the bonded assembly may contact aggressive substances.
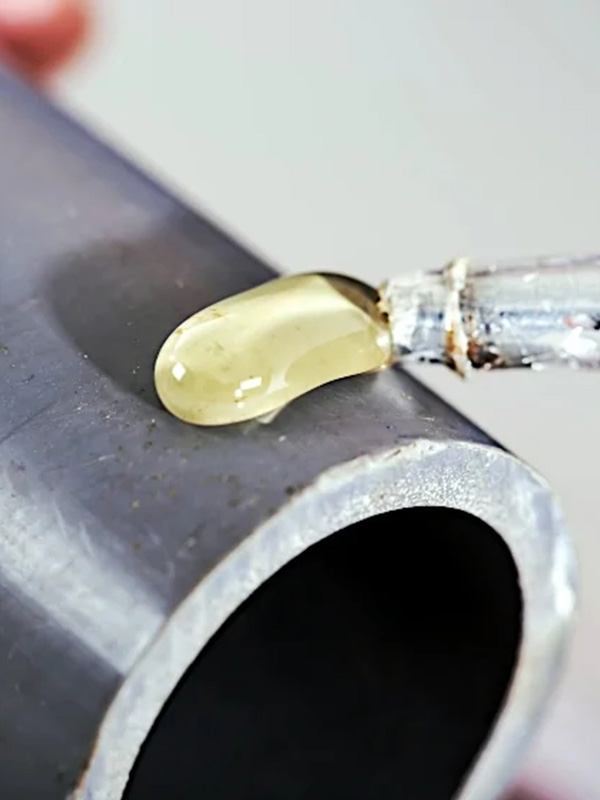
Another advantage of polypropylene bonding adhesives is their compatibility with different fabrication processes. They can be used with various techniques, such as adhesive bonding, hot air welding, or ultrasonic welding. This versatility allows manufacturers to choose the most suitable bonding method for their application requirements. Polypropylene bonding adhesives are also available in different forms, including tapes, films, liquids, and hot-melt adhesives, providing flexibility in application and assembly processes.
In addition to their bonding capabilities, polypropylene bonding adhesives offer excellent mechanical properties. They provide high bond strength, ensuring reliable and long-lasting adhesion. These adhesives can withstand significant loads, vibrations, and thermal stresses, making them suitable for demanding automotive, electronics, and packaging applications.
Moreover, polypropylene bonding adhesives provide a cost-effective solution for bonding polypropylene substrates. They eliminate the need for mechanical fasteners, which can be time-consuming and expensive. Adhesive bonding also allows for more design flexibility and the joining of complex shapes, contributing to overall cost savings and improved product aesthetics.
Automotive Industry: Polypropylene Bonding Adhesives in Car Manufacturing
Polypropylene bonding adhesives are crucial in the automotive industry, specifically car manufacturing. With the increasing use of polypropylene (PP) and other polyolefin plastics in automotive components, specialized bonding adhesives have been developed to ensure robust and reliable adhesion.
Polypropylene is preferred in the automotive industry due to its low cost, lightweight nature, and excellent chemical resistance. However, bonding polypropylene poses challenges because of its soft surface energy and poor adhesion properties. Polypropylene bonding adhesives are specifically formulated to overcome these challenges and enable adequate bonding of polypropylene automotive components.
One of the primary applications of polypropylene bonding adhesives in car manufacturing is interior components. These adhesives bond various polypropylene parts such as instrument panels, door panels, consoles, and trim pieces. They provide strong adhesion and structural integrity, ensuring the interior components remain securely attached despite constant vibration and temperature variations.
Polypropylene bonding adhesives are also essential for exterior applications in car manufacturing. They bond polypropylene parts like bumpers, fenders, grilles, and body panels. These adhesives create durable bonds that can withstand the rigors of the road, including impacts, weathering, and exposure to UV radiation. By eliminating the need for mechanical fasteners, bonding adhesives contribute to improved aesthetics and streamlined production processes.
In addition to interior and exterior applications, polypropylene bonding adhesives are employed to assemble automotive modules and sub-assemblies. They are used for bonding plastic-to-plastic, plastic-to-metal, and plastic-to-glass interfaces. By providing excellent adhesion on these different substrates, these adhesives enable the integration of various components, contributing to the overall strength and performance of the assembled parts.
Polypropylene bonding adhesives offer several advantages in the automotive industry. They ensure enhanced safety by providing structural integrity and crash resistance. These adhesives distribute stress and absorb energy, reducing the risk of component detachment during accidents. Moreover, they contribute to weight reduction, as bonds allow for the replacement of heavier mechanical fasteners, leading to improved fuel efficiency and reduced emissions.
Furthermore, polypropylene bonding adhesives contribute to noise and vibration reduction in vehicles. They create a uniform bond that minimizes the transmission of vibrations, resulting in quieter and more comfortable rides for drivers and passengers. This is especially important for interior components, where the adhesives act as a damping layer to reduce noise and rattling.
Consumer Goods Industry: Packaging and Assembly Applications
The consumer goods industry encompasses various products manufactured and sold to end consumers. Within this industry, packaging and assembly applications play a crucial role in ensuring that products are presented attractively, protected during transportation, and easily accessible to consumers. Let’s explore the significance of packaging and assembly within the consumer goods industry.
Packaging serves multiple purposes in the consumer goods industry. First and foremost, it protects the product from damage during transit and storage. Manufacturers use various materials such as cardboard, plastic, and metal to create packaging solutions that safeguard products from external factors like moisture, temperature variations, and physical impact.
Moreover, packaging is an essential marketing tool. It conveys brand identity and communicates important information to consumers, such as product features, usage instructions, and safety warnings. Eye-catching designs, logos, and colors can attract consumers’ attention and differentiate products from competitors on store shelves.
In addition to protection and marketing, packaging also facilitates product assembly. Many consumer goods require multiple components to be assembled before being used. Packaging can be designed to streamline this process, providing a convenient assembly experience for the end consumer. For example, packaging may include compartments or trays that hold different components in an organized manner, making it easier for consumers to identify and assemble the parts correctly.
Assembly applications in the consumer goods industry involve combining various components to create finished products. This process typically takes place in manufacturing facilities or assembly lines. Automation plays a significant role in streamlining assembly operations, improving efficiency, and reducing costs. Robotic systems are often employed to handle repetitive tasks, such as fastening screws, applying adhesives, or attaching small components. This increases productivity and ensures consistency and accuracy in the assembly process.
Furthermore, assembly applications contribute to quality control. Assembled products can undergo rigorous testing and inspection to meet predetermined standards. This includes checking for proper alignment, functional integrity, and adherence to safety regulations. Defective products can be identified and removed from the production line, minimizing the chances of faulty goods reaching the market.
Overall, packaging and assembly applications are integral to the consumer goods industry. Packaging provides protection, marketing, and facilitates product assembly, while assembly applications ensure efficient production and quality control. These processes work hand in hand to deliver consumer goods that are visually appealing but also functional and reliable. As the industry continues to evolve, advancements in materials, technology, and sustainability practices will shape the future of packaging and assembly, driving innovation and improving the overall consumer experience.
Medical Industry: Safe and Reliable Bonding Solutions
In the medical industry, safe and reliable bonding solutions are critical in various applications, including medical device assembly, wound care, and surgical procedures. These bonding solutions ensure that components are securely joined, tissues are correctly sealed, and medical devices function effectively. Let’s explore the significance of safe and reliable bonding solutions in the medical industry.
Medical device assembly often requires bonding different materials such as plastics, metals, and ceramics. The strength and durability of these bonds are crucial for the proper functioning and longevity of medical devices. Bonding solutions, such as adhesives, tapes, and sealants, are carefully formulated to provide solid and reliable bonds that can withstand the demands of medical applications.
Safety is one of the essential requirements for bonding solutions in the medical industry. Medical devices often come into direct contact with the human body, making the bonding materials necessary to be biocompatible and not cause adverse reactions or harm to patients. Manufacturers adhere to strict regulations and standards, such as ISO 10993, to ensure that bonding solutions used in medical devices are safe and suitable for their intended use.
Wound care is another area where bonding solutions play a vital role. Adhesive-based wound dressings and tapes are commonly used to secure and protect wounds, providing a barrier against external contaminants while allowing the wound to heal. These bonding solutions must be gentle on the skin, hypoallergenic, and provide reliable adhesion to ensure the dressings stay in place throughout the healing process.
In surgical procedures, bonding solutions are used for tissue sealing and hemostasis. Surgical adhesives and sealants are applied to close incisions, seal blood vessels, and secure tissue flaps. These bonding solutions provide the following:
- An alternative to traditional sutures or staples.
- Offering advantages such as reduced tissue trauma.
- Improved cosmetic outcomes.
- Shorter procedure times.
They must exhibit muscular bonding strength, biocompatibility, and compatibility with bodily fluids to ensure safe and effective wound closure.
Reliability is a critical factor in bonding solutions for the medical industry. Medical professionals rely on these bonds to withstand the stresses and demands of various applications, ensuring that medical devices remain intact, wound dressings stay in place, and surgical incisions are securely closed. Bonding solutions undergo rigorous testing and validation to ensure their reliability under specific conditions, including temperature variations, exposure to body fluids, and mechanical stress.
Moreover, bonding solutions in the medical industry are constantly evolving to meet the industry’s changing needs. Advances in adhesive technologies, such as biodegradable and tissue-engineered adhesives, continue to drive innovation in medical bonding applications, offering new possibilities for improved patient outcomes, faster healing, and enhanced surgical techniques.
Electronics Industry: High Bond Strength and Temperature Resistance
High bond strength and temperature resistance are crucial properties required in various applications in the electronics industry. These properties ensure reliable and long-lasting bonding of electronic components, protection against temperature fluctuations, and the ability to withstand harsh operating conditions. Let’s delve into the significance of high bond strength and temperature resistance in electronics.
High bond strength is essential for securely joining different electronic components together. Electronic devices consist of various materials such as metals, plastics, ceramics, and glass. Strong bonds are necessary to ensure the structural integrity of the devices, prevent component detachment, and maintain electrical connectivity. Bonding solutions such as adhesives, soldering, and welding techniques are utilized to achieve high bond strength in electronic assembly.
Adhesive bonding plays a vital role in the electronics industry. Adhesives offer advantages such as uniform stress distribution, improved shock resistance, and the ability to bond dissimilar materials. High-strength adhesives, such as epoxy or acrylic-based formulations, are commonly used to bond components, such as circuit boards, integrated circuits, and connectors. These adhesives provide exceptional bond strength, ensuring reliable connections even under mechanical stress or vibration.
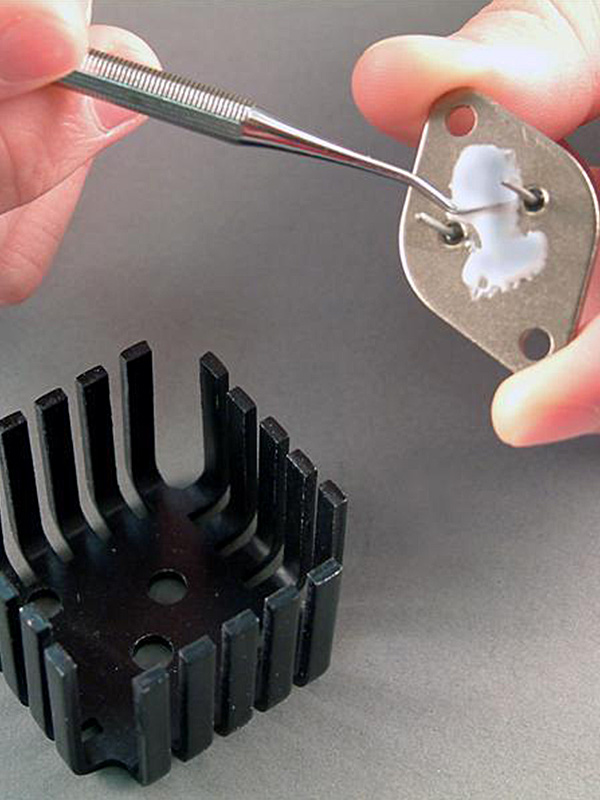
Temperature resistance is another critical requirement in the electronics industry. Electronic devices are subject to temperature fluctuations during operation, and components may generate heat. Bonding solutions must withstand these high temperatures without losing their strength or integrity. This is particularly important in applications such as power electronics, automotive electronics, and aerospace, where devices are exposed to extreme temperatures.
Soldering is widely used in electronics assembly, particularly for joining electrical components to circuit boards. Solder joints provide electrical connections and mechanical support. The solder must have a high melting point to ensure its stability and reliability during manufacturing and subsequent operation. Lead-free solders, such as tin-silver-copper (SAC) alloys, are commonly employed due to their high-temperature resistance and compliance with environmental regulations.
Furthermore, thermal management is crucial in the electronics industry to dissipate heat and prevent component failure. Bonding solutions with high-temperature resistance help create efficient heat transfer paths, ensuring that heat generated by components is dissipated effectively. Thermal interface materials, such as thermally conductive adhesives or phase-change materials, provide a reliable bond between heat-generating members and sinks, allowing efficient heat dissipation.
The demand for high bond strength and temperature resistance continues to increase in electronics as devices become smaller, more powerful, and operate in more challenging environments. Manufacturers and researchers are continually developing advanced bonding solutions that offer enhanced performance. These include high-temperature adhesives, solder alloys with improved thermal stability, and innovative thermal management materials to meet the evolving needs of the industry.
Construction Industry: Adhesives for Structural Bonding
In the construction industry, adhesives play a significant role in structural bonding applications. They provide an alternative to traditional mechanical fastening methods such as nails, screws, and welding. Adhesive bonding offers several advantages, including improved aesthetics, increased load-bearing capacity, enhanced durability, and the ability to bond dissimilar materials. Let’s explore the significance of adhesives for structural bonding in the construction industry.
Adhesives used in structural bonding applications are formulated to provide high bond strength and long-term durability. They are designed to withstand the structural loads and stresses that buildings and infrastructure endure throughout their lifetimes. These adhesives distribute the stress evenly across the bonded area, improving load-bearing capacity and overall structural integrity.
One of the critical advantages of adhesive bonding in construction is its ability to bond dissimilar materials. Adhesives can join materials such as metals, concrete, glass, wood, and composites, allowing for the construction of composite structures that leverage the best properties of each material. This flexibility enables architects and engineers to design innovative and visually appealing layouts.
Adhesive bonding also offers aesthetic benefits. Unlike traditional mechanical fasteners, adhesives create seamless and clean bond lines, eliminating the need for visible fasteners or welding marks. This results in a visually appealing finish, particularly in applications where aesthetics are essential, such as architectural facades, interior design elements, and furniture construction.
Durability is a critical requirement in the construction industry, and adhesives excel in providing long-term bond strength. They are formulated to withstand environmental factors such as temperature variations, moisture, UV radiation, and chemical exposure. This ensures that adhesive-bonded structures can withstand the rigors of different climates and maintain their performance over time.
Additionally, adhesive bonding offers advantages in terms of installation speed and ease. Adhesives can be applied quickly and efficiently, reducing assembly time compared to traditional mechanical fastening methods. They also provide better stress distribution along the bonded area, minimizing the risk of localized stress concentrations that can occur with mechanical fasteners.
Moreover, adhesives can contribute to improved energy efficiency in construction. They can reduce thermal bridging, air leakage, and energy loss when used in insulation systems or sealing applications. This enhances the overall energy performance of buildings, leading to reduced energy consumption and lower heating and cooling costs.
In the construction industry, adhesives for structural bonding undergo rigorous testing and evaluation to ensure compliance with industry standards and building codes. Various factors, including bond strength, durability, fire resistance, and environmental impact, are considered during the selection process to ensure the suitability of adhesives for specific applications.
As the construction industry continues to evolve, advancements in adhesive technologies are driving innovation. This includes the development of environmentally friendly adhesives with low volatile organic compound (VOC) emissions, improved fire resistance, and enhanced sustainability.
Aerospace Industry: Lightweight and Durable Bonding Solutions
In the aerospace industry, lightweight and durable bonding solutions ensure the structural integrity and performance of aircraft, spacecraft, and related components. These bonding solutions combine various materials, such as metals, composites, and plastics, while providing strength, reliability, and longevity. In this article, we will explore some key advancements and considerations in the aerospace industry’s lightweight and durable bonding solutions.
One of the primary objectives in aerospace design is to reduce weight without compromising structural strength and safety. Lightweight bonding solutions offer significant advantages in this regard. Advanced adhesives, such as epoxy, acrylic, and polyurethane-based formulations, have been developed to provide high strength-to-weight ratios. These adhesives exhibit excellent bonding properties, allowing for the effective joining of lightweight materials like carbon fiber-reinforced composites, which are increasingly used in aerospace applications due to their exceptional strength and low weight.
To ensure durability and long-term performance, bonding solutions in the aerospace industry must withstand extreme conditions. These conditions include temperature variations, high humidity, exposure to harsh chemicals, and cyclic loading. Adhesives formulated with enhanced thermal stability and resistance to environmental factors are employed to meet these challenges. Additionally, adhesive bonding processes are carefully optimized to minimize stress concentrations and maximize load transfer across the bonded joints.
Surface preparation is a critical aspect of achieving durable bonds. Aerospace manufacturers employ various techniques, such as surface cleaning, sanding, and chemical treatments, to remove contaminants, enhance adhesion, and promote interfacial bonding. Proper surface preparation ensures maximum contact area and improves the mechanical strength of the bonded joint.
In recent years, advancements in nanotechnology have contributed to developing novel bonding solutions. Nanocomposite adhesives, reinforced with nanoparticles such as carbon nanotubes or graphene, offer improved mechanical properties, such as enhanced strength, toughness, and resistance to fatigue. These nanomaterials can also provide electrical conductivity or thermal management capabilities, enabling multifunctional bonding solutions for aerospace applications.
Another area of innovation in lightweight and durable bonding solutions is the development of structural adhesives with self-healing properties. These adhesives contain microcapsules filled with healing agents that are released upon the occurrence of cracks or damage in the bond line. The healing agents flow into the cracks, react, and restore the structural integrity of the adhesive joint. Self-healing adhesives can significantly enhance the durability and reliability of bonded structures in aerospace applications.
Marine Industry: Saltwater and UV Resistance
The marine industry operates in harsh environments that expose equipment and materials to constant contact with saltwater and ultraviolet (UV) radiation. The challenges posed by saltwater and UV resistance are significant and require specialized solutions to ensure the longevity and performance of marine equipment and structures. This article will explore the importance of saltwater and UV resistance in the maritime industry.
Saltwater Resistance: Saltwater is highly corrosive and can cause severe damage to metals, coatings, and other materials commonly used in marine applications. It contains electrolytes that accelerate corrosion, leading to the degradation and weakening of structures and equipment. Therefore, saltwater resistance is crucial to prevent premature failure and increase the lifespan of marine components.
One effective method of achieving saltwater resistance is using corrosion-resistant materials such as stainless steel, aluminum alloys, and non-metallic composites. These materials have excellent resistance to saltwater corrosion and can withstand prolonged exposure without significant deterioration.
In addition to material selection, protective coatings play a vital role in saltwater resistance. Epoxy-based coatings, for instance, provide a barrier between the metal surface and saltwater, preventing direct contact and corrosion. Anti-fouling coatings are also used to deter the growth of marine organisms, reducing the risk of biofouling and further protecting against corrosion.
UV Resistance: UV radiation from the sun is another primary concern in the marine industry. Prolonged exposure to UV rays can cause degradation, fading, and brittleness of materials, particularly polymers, composites, and coatings. Constant exposure to UV radiation can lead to reduced structural integrity and aesthetic appearance of marine components.
Materials and coatings need to be specifically formulated with UV stabilizers and inhibitors to ensure UV resistance. These additives absorb or reflect UV radiation, preventing it from penetrating the material and causing damage. UV-stabilized polymers, such as polyethylene and polyvinyl chloride (PVC), are commonly used in marine applications due to their inherent UV resistance.
In addition to material selection, surface treatments, and coatings can enhance UV resistance. Clear protective coatings with UV-blocking properties can be applied to surfaces exposed to direct sunlight, such as fiberglass hulls, to protect against UV degradation. Regular maintenance, including cleaning and reapplication of UV-protective coatings, is essential to maintain the long-term UV resistance of marine equipment.
Overall, saltwater and UV resistance are crucial considerations in the marine industry. Manufacturers and operators can ensure the durability, performance, and aesthetics of marine equipment and structures by selecting appropriate materials, utilizing corrosion-resistant alloys, applying protective coatings, and incorporating UV stabilizers. By addressing these challenges, the maritime industry can thrive in the demanding marine environment and enhance the safety and reliability of its operations.
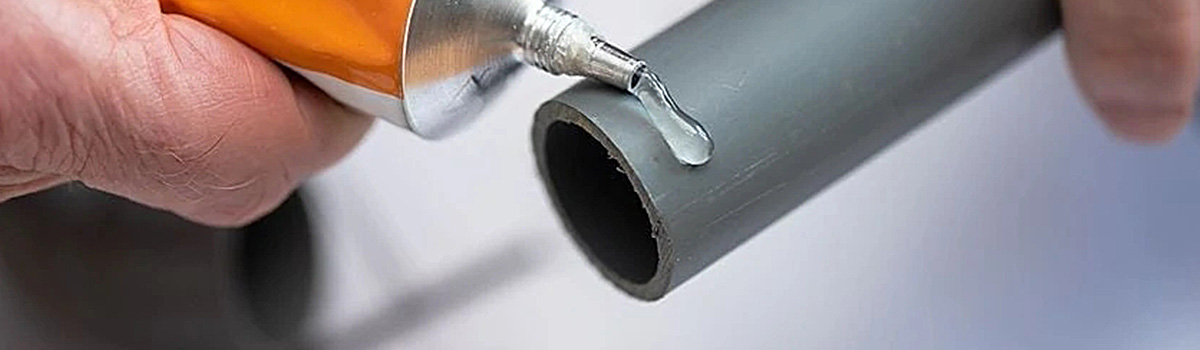
Choosing the Right Polypropylene Bonding Adhesive
When it comes to bonding polypropylene (PP), a challenging material due to its low surface energy, selecting the suitable adhesive is crucial. Polypropylene bonding adhesives are designed to provide robust and durable bonds with PP substrates. This article will explore key considerations for choosing the right polypropylene bonding adhesive.
- Adhesive Compatibility: The adhesive must be compatible with polypropylene. PP has low surface energy, making it difficult for adhesives to adhere to. Look for adhesives that are specifically formulated for bonding PP or have good adhesion properties on low-energy surfaces. It’s essential to consult the adhesive manufacturer’s technical data sheet or contact their technical support team to ensure compatibility with polypropylene.
- Surface Preparation: Proper surface preparation is crucial for successful bonding. PP surfaces should be cleaned to remove contaminants, oils, or release agents hindering adhesion. Techniques such as solvent cleaning, plasma, or flame treatment can enhance surface energy and promote bonding. Some adhesives may require specific surface preparation methods, so following the manufacturer’s guidelines is essential.
- Bond Strength: Consider the required strength of the bond for your application. Different adhesives offer varying levels of bond strength. Structural adhesives are often preferred for high-strength bonding applications, while non-structural adhesives may be suitable for lighter loads. The manufacturer’s technical data sheet should provide information on the bond strength properties of the adhesive.
- Cure Time: The cure time of the adhesive is an important consideration, especially if you have time-sensitive projects or production schedules. Some adhesives require extended curing periods, while others offer faster curing options. Additionally, consider the ambient temperature and humidity conditions necessary for optimal curing. More rapid-curing adhesives can help improve productivity but ensure sufficient time for proper bonding.
- Environmental Resistance: Evaluate the environmental conditions to which the bonded PP parts will be exposed. Consider temperature variations, moisture, chemicals, and UV exposure. Choose an adhesive that offers excellent resistance to specific environmental conditions to ensure the long-term durability and performance of the bond. The adhesive manufacturer should provide information on the adhesive’s resistance properties.
- Application Method: Consider the preferred application method for the adhesive. Adhesives are available in various forms, such as tapes, films, liquids, or pastes. The choice depends on factors such as the size and geometry of the bonding area, production requirements, and ease of application. Adhesive tapes or films offer convenience and speed, while liquid adhesives may provide better coverage and flexibility for complex shapes.
- Testing and Validation: Conducting and validating the adhesive before full-scale production or critical applications is recommended. Perform bond strength tests, environmental exposure tests, and other relevant evaluations to ensure the adhesive meets your requirements.
Remember, it’s crucial to consult with adhesive manufacturers or technical experts to ensure you select the right polypropylene bonding adhesive for your application. They can provide guidance based on their expertise and help address any specific challenges you may encounter during the bonding process.
Future Trends in Polypropylene Bonding Adhesives
The field of polypropylene bonding adhesives is constantly evolving, driven by the need for more robust, efficient, and environmentally friendly bonding solutions. As technology advances and new materials and manufacturing processes emerge, several future trends are expected to shape the development of polypropylene bonding adhesives. Here are some key trends to watch out for:
- Improved Adhesion on Low-Energy Surfaces: Enhancing the adhesion properties of polypropylene bonding adhesives on low-energy surfaces remains a significant focus. Manufacturers are developing adhesives with better wetting capabilities and improved surface interaction, allowing for stronger bonds on difficult-to-bond materials like polypropylene.
- Sustainable and Green Solutions: As sustainability becomes increasingly important across industries, the demand for eco-friendly bonding adhesives is growing. Future trends in polypropylene bonding adhesives will likely include developing environmentally friendly options, such as solvent-free adhesives or those made from renewable or recycled materials. These adhesives will offer comparable or superior performance while minimizing environmental impact.
- Faster Curing and Processing: There is a growing demand for polypropylene bonding adhesives with speedier curing times to improve production efficiency. Sealants that can achieve strong bonds more quickly will help reduce assembly and processing time, leading to higher productivity and throughput. Advancements in curing technologies, such as UV-curable or moisture-curing adhesives, may play a significant role in achieving faster curing times.
- Increased Bond Strength and Durability: Future polypropylene bonding adhesives are expected to offer even higher bond strengths and improved durability. This is particularly crucial for applications that require long-term reliability and resistance to harsh conditions. Formulations with enhanced chemical resistance, temperature resistance, and mechanical properties will be developed to meet the demanding requirements of various industries.
- Customization and Application-Specific Solutions: With the diversity of applications and bonding requirements, the future of polypropylene bonding adhesives will likely involve more customization and tailored solutions. Adhesive manufacturers may work closely with customers to develop specific formulations that address unique challenges, considering substrates, environmental conditions, and desired performance criteria. Customized adhesive solutions can lead to optimized bonding processes and improved product performance.
- Integration of Smart Technologies: Integrating innovative technologies into polypropylene bonding adhesives is an emerging trend. This may include incorporating functionalities such as self-healing properties, on-demand curing, or embedded sensors to monitor bond integrity. These advancements can enhance the reliability and performance of bonded assemblies and enable real-time monitoring and maintenance.
As the demand for efficient and reliable polypropylene bonding adhesives grows, the industry will witness materials, formulations, and application methods advancements. Through ongoing research and development, manufacturers are likely to address the challenges associated with bonding polypropylene and push the boundaries of adhesive technology, resulting in improved performance, increased sustainability, and enhanced productivity in the future.
Conclusion
Polypropylene bonding adhesives have revolutionized how we join polypropylene and other substrates in various industries, including automotive, consumer goods, medical, electronics, construction, aerospace, and marine. The different types of polypropylene bonding adhesives offer a range of benefits, including high bond strength, temperature and chemical resistance, easy application and removal, and low cost. Choosing the suitable adhesive for the substrate and application ensures a reliable and long-lasting bond. As research and development efforts continue, we can expect even more innovative polypropylene bonding adhesives that offer superior performance, sustainability, and versatility. Polypropylene bonding adhesives are set to play an increasingly important role in manufacturing and industry, enabling us to join different materials more efficiently and effectively.