Rubber Bonding Adhesive
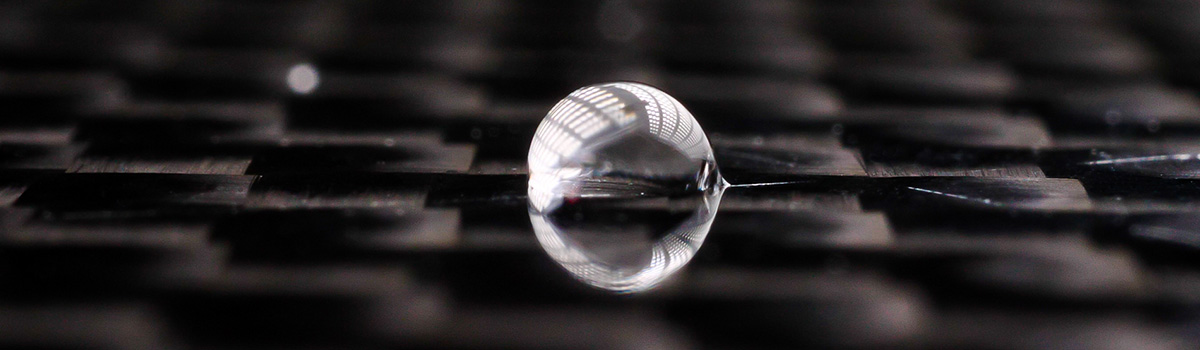
Rubber bonding adhesives are crucial in various automotive, aerospace, medical, and electronics industries. They bond different types of rubber to multiple substrates, including metal, plastic, glass, wood, and concrete. These adhesives offer several advantages, including good chemical resistance, flexibility, and bonding with dissimilar materials. This blog post will discuss the properties, types, applications, and best practices for rubber bonding adhesives.Rubber bonding adhesives are designed to create a strong bond between rubber materials and other substrates. They come in various forms, including contact adhesives, pressure-sensitive adhesives, two-part adhesives, epoxy adhesives, and cyanoacrylate adhesives. Each adhesive type has unique properties and is suitable for specific applications.
The advantages of rubber bonding adhesives include bonding dissimilar materials, good chemical resistance, flexibility and resilience, and the ability to bond irregular or curved surfaces. These advantages make rubber bonding adhesives preferred in various industries, including automotive, aerospace, medical, and electronics.
The following sections will discuss the types, properties, applications, and best practices for rubber bonding adhesives. We will also look at how to bond rubber to different substrates, the factors affecting rubber bonding adhesives, and the testing and evaluation of these adhesives. We will conclude with future trends and innovations in rubber bonding adhesives.
Types of Rubber Bonding Adhesives
Rubber bonding adhesives come in various forms with unique properties and characteristics. The type of adhesive used depends on the application, substrate, and environment. Here are the most common types of rubber bonding adhesives:
- Contact Adhesives: Contact adhesives are solvent-based adhesives applied to both surfaces and allowed to dry before bonding. They create a strong, permanent bond and are suitable for bonding large surfaces. Contact adhesives are commonly used in the automotive industry for bonding rubber to metal and plastic.
- Pressure-Sensitive Adhesives: Pressure-sensitive adhesives are tacky adhesives that require only light pressure to bond. They do not require solvents or curing and can be used for bonding thin or delicate materials. Pressure-sensitive adhesives are commonly used in the medical and electronics industries.
- Two-Part Adhesives: Two-part adhesives require mixing two components, a resin, and a hardener, to create a strong bond. They offer excellent bonding strength and are suitable for bonding rubber to various substrates. Two-part adhesives are commonly used in the aerospace industry for bonding rubber to metal and composite materials.
- Epoxy Adhesives: Epoxy adhesives are high-strength adhesives that offer excellent bonding strength and durability. Creating a strong bond requires mixing two components, a resin and a hardener. Epoxy adhesives are commonly used in the automotive and aerospace industries for bonding rubber to metal and composite materials.
- Cyanoacrylate Adhesives: Cyanoacrylate adhesives, also known as superglue, are fast-setting adhesives that bond quickly and easily. They are suitable for bonding small surfaces and require minimal surface preparation. Cyanoacrylate adhesives are commonly used in the medical and electronics industries for bonding rubber to plastic and metal.
Properties of Rubber Bonding Adhesives
Rubber bonding adhesives offer several advantageous properties that make them ideal for various industries. Here we will discuss the most common properties of rubber bonding adhesives.
- Good Chemical Resistance: Rubber bonding adhesives resist various chemicals, including acids, bases, solvents, and oils. They offer good chemical resistance, making them suitable for use in harsh environments where exposure to chemicals is daily.
- Good Flexibility and Resilience: Rubber bonding adhesives are flexible and resilient and withstand stress, strain, and movement without cracking or breaking. They offer good shock absorption and vibration dampening, making them ideal for automotive and aerospace applications.
- Ability to Bond Dissimilar Materials: Rubber bonding adhesives can bond different materials, including rubber, metal, plastic, glass, wood, and concrete. This ability to connect dissimilar materials is essential in various industries where other materials must be joined together.
- Ability to Bond Irregular or Curved Surfaces:Rubber bonding adhesives can bond irregular or curved surfaces, making them ideal for automotive and aerospace applications, where characters may not be flat. They can conform to the shape of the surface and create a strong, permanent bond.
Advantages of Using Rubber Bonding Adhesives
Rubber bonding adhesives offer several advantages over other types of bonds. In this section, we will discuss the most common benefits of using rubber bonding adhesives.
- Ability to Bond Dissimilar Materials: One of the significant advantages of rubber bonding adhesives is their ability to bond different materials. They can bond rubber to metal, plastic to glass, and many other combinations. This property is essential in various industries where materials must be combined.
- Good Chemical Resistance: Rubber bonding adhesives resist multiple chemicals, including acids, bases, solvents, and oils. This property is essential in industries where exposure to harsh chemicals is daily. Rubber bonding adhesives provide a durable bond, even in harsh environments.
- Good Flexibility and Resilience: Rubber bonding adhesives are flexible and resilient, which means they can withstand stress, strain, and movement without cracking or breaking. This property makes them ideal for use in automotive and aerospace applications. They offer good shock absorption and vibration dampening.
- Ability to Bond Irregular or Curved Surfaces: Rubber bonding adhesives can bond irregular or curved surfaces, which is essential in industries where surfaces may not be flat. They can conform to the shape of the surface and create a strong, permanent bond. This property makes them ideal for use in automotive and aerospace applications.
Applications of Rubber Bonding Adhesives
Rubber bonding adhesives have a wide range of applications in various industries. This section will discuss the most common applications of rubber bonding adhesives.
- Automotive and Transportation: Rubber bonding adhesives are widely used in the automotive and transportation industry. They are used to bond rubber to metal, plastic, and glass. Rubber bonding adhesives provide a durable bond that can withstand harsh environments, vibrations, and high temperatures. They are used to manufacture cars, buses, trucks, trains, and airplanes.
- Aerospace and Defense: The aerospace and defense industry uses rubber bonding adhesives. They are used to bond materials that are exposed to extreme conditions, such as high temperatures, pressure, and vibration. Rubber bonding adhesives are used to manufacture aircraft, spacecraft, and missiles.
- Medical and Healthcare: Rubber bonding adhesives are used in the medical and healthcare industry to bond medical devices and equipment. They are used to bond rubber to plastic, metal, and glass. Rubber bonding adhesives provide a strong, durable bond that can withstand sterilization processes and exposure to body fluids. They are used to manufacture medical devices, such as catheters, implants, and surgical instruments.
- Electronics and Appliances: Rubber bonding adhesives are used in the electronics and appliances industry to bond components and parts. They are used to bond rubber to metal, plastic, and glass. Rubber bonding adhesives provide a strong, durable bond that can withstand high temperatures, humidity, and vibrations. They are used to manufacture smartphones, computers, TVs, and home appliances.
Best Practices for Using Rubber Bonding Adhesives
Rubber bonding adhesives provide a strong and durable bond, but the bond strength can be affected by several factors, including surface preparation, application techniques, and safety considerations. Here we will discuss some of the best practices for rubber bonding adhesives.
Surface Preparation: Surface preparation is critical for the success of rubber bonding adhesives. A clean, dry, and rough surface provides a better bonding surface for the glue. The surface should be free of dust, oil, grease, and other contaminants. To prepare the surface for bonding, follow these steps:
- Clean the surface using a suitable solvent or detergent.
- Sand the surface to create a rough surface.
- Dry the surface thoroughly before applying the adhesive.
Application Techniques: The application technique is also critical for the success of rubber bonding adhesives. The adhesive should be applied evenly and in the right amount. Over-application or under-application can affect the bond strength. To apply the glue correctly, follow these steps:
- Apply the glue evenly on both surfaces.
- Use the recommended amount of adhesive.
- Apply the adhesive at the recommended temperature and humidity.
Safety Considerations: Rubber bonding adhesives contain chemicals that can harm health. It is essential to follow safety guidelines when handling and using rubber bonding adhesives. Some of the safety considerations include:
-
- Wear personal protective equipment, such as gloves, goggles, and respirators.
- Use the adhesive in a well-ventilated area.
- Store the adhesive in a cool, dry, and well-ventilated place.
- Dispose of the adhesive and the container correctly.
Bonding Rubber to Metal
Rubber to metal bonding is standard in various industries, including automotive, electronics, and plumbing. Rubber bonding adhesives provide a strong and durable bond between rubber and metal. Here are some key considerations of the applications of bonding rubber to metal.
- Automotive Weatherstripping: Automotive weatherstripping is an essential barrier between the vehicle’s interior and the outside environment. Weatherstripping is made of rubber and bonded to the vehicle’s metal body using rubber bonding adhesives. The adhesive must provide a strong and durable bond to ensure that the weatherstripping stays in place and performs effectively.
- Rubber Seals for Electronics and Appliances: Rubber seals are commonly used in electronics and appliances to provide a water-tight seal. The seals are rubber and bonded to the metal components using rubber bonding adhesives, and the glue must offer a strong and durable bond to ensure the seal stays in place and prevents water from entering the device.
- Rubber Gaskets for Piping and Plumbing Applications: Rubber gaskets are used in piping and plumbing applications to provide a water-tight seal between two pipes or plumbing fixtures. The gaskets are made of rubber and are bonded to the metal pipes or fixtures using rubber bonding adhesives. The adhesive must provide a strong and durable bond to ensure the gasket stays in place and prevents water from leaking.
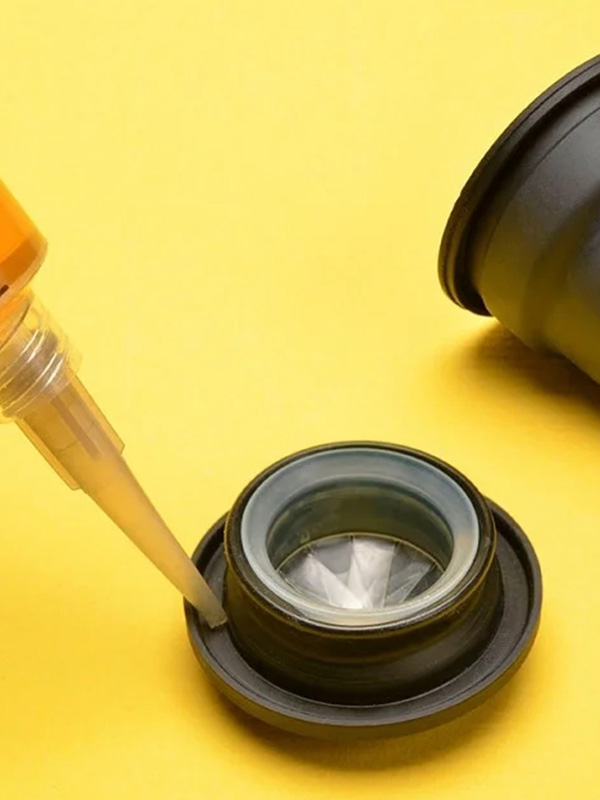
Bonding Rubber to Plastic
Bonding rubber to plastic is standard in various industries, including electronics, plumbing, and medical devices. Rubber bonding adhesives provide a strong and durable bond between rubber and plastic. This segment will explore some of the uses of adhering rubber to plastic.
- Rubber Seals for Electronics and Appliances: Rubber seals are commonly used in electronics and appliances to provide a water-tight seal. The seals are rubber and bonded to the plastic components using rubber bonding adhesives, and the glue must offer a strong and durable bond to ensure the seal stays in place and prevents water from entering the device.
- Rubber Gaskets for Piping and Plumbing Applications: Rubber gaskets are used in piping and plumbing applications to provide a water-tight seal between two plastic pipes or plumbing fixtures. The gaskets are made of rubber and are bonded to plastic pipes or fixtures using rubber bonding adhesives. The adhesive must provide a strong and durable bond to ensure the gasket stays in place and prevents water from leaking.
- Rubber Components for Medical Devices: Rubber components, such as syringe plungers, catheters, and surgical instruments, are commonly used in medical devices. These components are often made of rubber and are bonded to plastic parts using rubber bonding adhesives. The adhesive must provide a strong and durable bond to ensure the element stays in place and performs effectively.
Best Practices for Bonding Rubber to Plastic
- Surface Preparation: The surfaces to be bonded must be clean and free from any contaminants, such as oil, grease, or dust. The surfaces can be cleaned using solvents or abrasives.
- Proper Adhesive Selection: The type of adhesive used will depend on the specific application and the bonded materials. Contact adhesives and cyanoacrylate adhesives are commonly used for bonding rubber to plastic.
- Application Techniques: The adhesive should be applied evenly and thinly to both surfaces. The surfaces should then be pressed together firmly to ensure a strong bond.
Bonding Rubber to Rubber
Rubber-to-rubber bonding is a common requirement in various applications, such as automotive, industrial, and medical devices. The challenge of bonding two rubber surfaces lies in their low surface energy and the presence of contaminants that may prevent proper adhesion. A suitable adhesive and surface preparation can overcome these challenges and create a solid and durable bond.
Rubber seals for automotive and industrial applications
Rubber seals are used in automotive and industrial applications to prevent the leakage of fluids or gasses. The following are some types of rubber seals that require rubber-to-rubber bonding:
- O-rings
- Gaskets
- Sealing strips
To achieve a strong and durable bond, it is essential to use an adhesive with good rubber adhesion and proper surface preparation techniques.
Rubber components for medical devices
Medical devices often require the bonding of rubber components to ensure a tight seal, prevent contamination, and ensure functionality. Some common examples of rubber components that need bonding in medical devices include the following:
- Rubber tubing
- Diaphragms
- Seals
To achieve a strong and durable bond in medical devices, it is essential to use adhesives that are safe for medical use and have excellent adhesion to rubber. The adhesives must also withstand sterilization processes and other environmental factors.
Here are some best practices for bonding rubber to rubber
- Surface preparation: Proper surface preparation is essential for achieving a solid and durable bond. The surfaces to be bonded must be clean, dry, and free of contaminants such as oils, dirt, and dust. Abrading the surface with sandpaper or a wire brush can improve adhesion by creating a rough surface for the adhesive to bond to. Solvent cleaning or degreasing can also be done to ensure a clean surface.
- Choosing the suitable adhesive: Choosing the right adhesive is crucial to achieving a strong and durable bond. Some adhesives that work well for rubber-to-rubber bonding include cyanoacrylate, epoxy, and neoprene adhesives.
- Applying the adhesive: The adhesive must be applied evenly to both surfaces to ensure a uniform bond. Excess adhesive must be removed as it can cause the glue to fail. The adhesive should be allowed to dry completely before the two surfaces are brought together.
- Curing time: The curing time for the adhesive must be followed to ensure a strong and durable bond. Following the manufacturer’s instructions for the adhesive’s curing time is essential, as it varies depending on the adhesive used.
Bonding Rubber to Glass
Rubber bonding adhesives can also be used to bond rubber to glass, which is a challenging task due to the different properties of the materials. However, a strong bond can be achieved with a suitable adhesive and proper surface preparation.
Rubber seals for electronics and appliances
Rubber seals are commonly used in electronic devices and appliances to protect internal components from moisture and dust. Bonding rubber seals to glass requires a strong adhesive that can withstand the environmental conditions and vibrations of the device. Some typical applications of rubber seals bonded to glass include:
- Glass display panels for electronic devices
- Glass windows for appliances such as ovens and refrigerators
- Glass panels for photovoltaic cells in solar panels
Rubber components for laboratory and medical applications
Rubber is often used in laboratory and medical applications for its chemical resistance and flexibility. Bonding rubber to glass is necessary for creating components such as tubing and stoppers for laboratory equipment and medical devices. Some examples of applications where the rubber is bonded to glass include:
- Glass pipettes with rubber bulbs for transferring liquids in a laboratory.
- Rubber stoppers for glass vials used in medical research and storage
- Rubber tubing for connecting glass components in laboratory equipment
Best practices for bonding rubber to glass
- Surface preparation is crucial for achieving a strong bond. Both the rubber and glass surfaces should be clean and free from contaminants such as dust or oil.
- Use an adhesive that is specifically designed for bonding rubber to glass. Silicone-based adhesives are commonly used for this application due to their ability to withstand extreme temperatures and harsh chemicals.
- Apply the adhesive evenly and thinly on both surfaces. Too much glue can result in a weak bond or excess adhesive needing removal.
- Allow sufficient curing time for the adhesive to reach its maximum strength. The curing time will depend on the specific adhesive used and the environmental conditions during application.
Bonding Rubber to Wood
Rubber bonding adhesives can also bond rubber to wood in various applications. The primary challenge of bonding rubber to wood is ensuring a strong and durable bond that can withstand mechanical stresses and environmental conditions. Here are some typical applications and best practices for bonding rubber to wood.
Rubber seals for construction applications
Rubber seals are commonly used in construction applications to provide waterproofing, sound insulation, and vibration damping. These seals may be attached to wooden frames or panels to create a tight seal that prevents water, air, or noise from entering or exiting a building. Here are some best practices for bonding rubber seals to wood:
- Surface preparation: Clean the wood surface thoroughly to remove any dirt, dust, or contaminants that may interfere with the adhesive bond. Sand the surface lightly to roughen it and provide better adhesion.
- Choose the suitable adhesive: Select an adhesive compatible with the rubber and wood substrates. A contact adhesive or a two-part epoxy adhesive may suit this application.
- Apply the adhesive: Apply a thin, even layer of glue to the rubber and the wood surfaces using a brush or roller. Allow the adhesive to dry for the recommended time before pressing the surfaces together.
- Apply pressure: Press the rubber and wood surface firmly using clamps or weights. Apply pressure evenly across the surface to ensure a strong and uniform bond.
- Allow to cure: Allow the adhesive to cure fully according to the manufacturer’s instructions before subjecting the seal to any stress or environmental conditions.
Rubber components for tools and equipment
Rubber components such as grips, handles, or bumpers may be attached to wooden tools or equipment to improve grip, comfort, or durability. Here are some best practices for bonding rubber to wood in this application:
- Surface preparation: Clean the wood surface thoroughly to remove any dirt, dust, or contaminants that may interfere with the adhesive bond. Sand the surface lightly to roughen it and provide better adhesion.
- Choose the suitable adhesive: Select an adhesive compatible with the rubber and wood substrates. A contact adhesive or a two-part epoxy adhesive may suit this application.
- Apply the adhesive: Apply a thin, even layer of glue to the rubber and the wood surfaces using a brush or roller. Allow the adhesive to dry for the recommended time before pressing the surfaces together.
- Position the rubber component: Position the rubber component on the wood surface, ensuring that it is aligned and level.
- Apply pressure: Press the rubber component firmly onto the wood surface using your hands or a clamp. Apply pressure evenly across the surface to ensure a strong and uniform bond.
- Allow to cure: Allow the adhesive to cure fully according to the manufacturer’s instructions before using the tool or equipment.
Bonding Rubber to Concrete
Rubber bonding adhesives are also suitable for bonding rubber to concrete surfaces. Concrete is a popular building material used in many industries, such as construction, manufacturing, and automotive. Bonding rubber to concrete can create a durable, water-resistant seal that can withstand harsh environments and extreme temperatures.
Here are some applications of rubber bonding adhesives for bonding rubber to concrete:
- Flooring and walls: Rubber seals can seal gaps between concrete floors or walls, preventing water or air leakage. Rubber flooring can also be installed using bonding adhesives.
- Surface preparation: The concrete surface should be clean, dry, and free from debris or contaminants. Before bonding, cracks or gaps should be filled with a suitable filler or sealant.
- Application techniques: The adhesive should be applied evenly to rubber and concrete surfaces using a brush or roller. The surfaces should then be pressed firmly together, and any excess glue should be removed immediately.
- Curing time: The adhesive should be given sufficient time to cure before the bonded surfaces are subjected to stress or pressure. The curing time can vary depending on the type of adhesive and the environmental conditions.
Rubber bonding adhesives are available in different types, formulations, and strengths, making them suitable for various industrial applications. Whether you need to bond rubber to metal, plastic, glass, wood, or concrete, a rubber bonding adhesive can meet your needs.
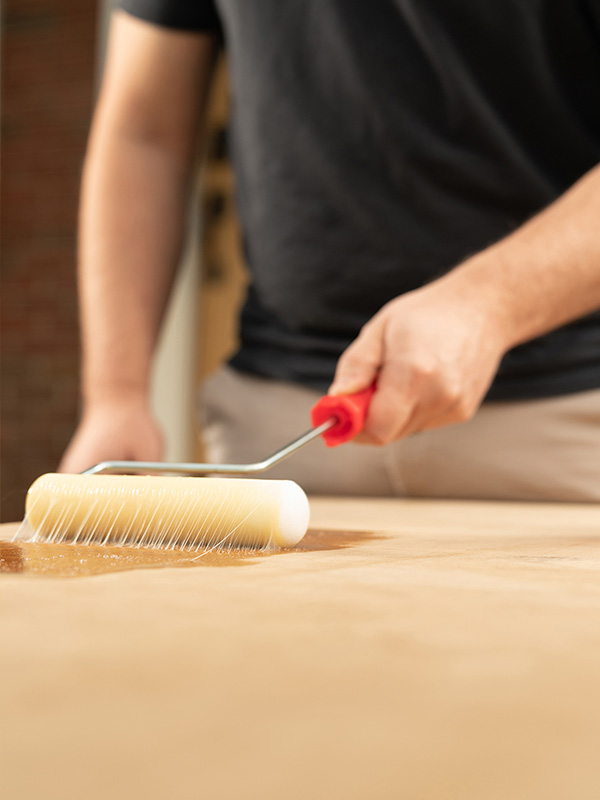
Factors Affecting Rubber Bonding Adhesives
Rubber bonding adhesives are designed to provide a solid and durable bond between rubber and various substrates. However, certain factors can affect the adhesive’s performance and the bond’s strength. Here we will discuss some of the factors that can affect the bonding of rubber adhesives.
Temperature
Temperature plays a critical role in the bonding of rubber adhesives, and the adhesive must withstand the temperature extremes that the bond will be exposed to during use. For example, in automotive applications, rubber seals and gaskets must withstand the high temperatures generated by the engine while remaining flexible at low temperatures.
Humidity
Humidity can also affect the bonding of rubber adhesives. High humidity levels can cause moisture to seep into the bond, weakening the glue and reducing the bond’s strength. This is particularly important in outdoor applications where the adhesive may be exposed to rain or other forms of moisture.
Chemical Exposure
Chemical exposure is another factor that can affect the performance of rubber bonding adhesives. The adhesive must withstand exposure to chemicals such as oils, fuels, and solvents, which can break down the glue and weaken the bond. This is particularly important in industrial applications where the adhesive may be exposed to various chemicals.
To ensure a strong and durable bond between the rubber and other substrates, it is crucial to consider these factors and select an adhesive designed to withstand the specific conditions of the application.
Some additional points to consider are:
- The adhesive manufacturer should provide information on the recommended operating temperature range and humidity levels.
- Surface preparation is critical to ensure a strong bond. The surfaces to be bonded must be clean, dry, and free of any oils, grease, or other contaminants that could interfere with the glue.
- Selecting an adhesive compatible with the bonded materials and the environment in which the bond will be used is vital. For example, if the bond is exposed to chemicals, the adhesive must withstand chemical exposure without breaking down.
- Proper application techniques should be followed to ensure the adhesive is applied evenly without any air pockets that could weaken the bond. This may include using a primer or activator to promote adhesion between the rubber and the substrate.
By considering these factors and following best practices for bonding rubber adhesives, it is possible to achieve a strong and durable bond that can withstand the demands of various applications.
Testing and Evaluating Rubber Bonding Adhesives
Rubber bonding adhesives are used in a wide range of industries for their ability to create strong and durable bonds between various materials. However, testing and evaluating its properties is essential to ensure the adhesive performs as expected. We will talk about the numerous tests in this area that can be used to gauge how well rubber bonding adhesives operate.
- Tensile Strength: One of the most common tests used to evaluate the strength of an adhesive is the tensile strength test. This test measures the force required to pull apart a bonded joint. The test is performed by applying constant pressure to the bonded joint until it separates. The strength needed to break the bond is then measured and recorded.
- Shear Strength: Another standard test used to evaluate adhesive strength is the shear strength test. This test measures the force required to cause the adhesive to fail when a shear pressure is applied. The test uses a constant shear power on the bonded joint until it separates. The energy required to break the bond is then measured and recorded.
- Peel Strength: The peel strength test measures the force required to peel apart a bonded joint. The test is performed by peeling a bonded joint apart at a constant rate of speed, and the strength needed to peel the joint apart is then measured and recorded.
Other Tests
In addition to the above tests, several other tests can be used to evaluate the performance of rubber bonding adhesives. These tests include:
- Lap shear strength: measures the force required to shear a bonded joint at a 90-degree angle
- Fatigue resistance: measures the adhesive’s ability to withstand repeated stress cycles without failure
- Impact resistance: measures the adhesive’s ability to withstand impact without failure
- Environmental exposure: evaluates the adhesive’s performance when exposed to various environmental factors, such as temperature, humidity, and chemicals
When evaluating the performance of a rubber bonding adhesive, it is vital to select the appropriate test method for the intended application. In addition, the testing should be performed under the proper conditions to ensure accurate and reliable results.
Troubleshooting Rubber Bonding Adhesives
Rubber bonding adhesives are widely used in various industries due to their ability to bond different materials, including rubber, metal, plastic, glass, wood, and concrete. However, sometimes issues arise that can cause problems with adhesion and bonding. We’ll look at some typical cases with rubber bonding adhesives in this section, along with solutions.
Poor Adhesion
Poor adhesion occurs when the adhesive fails to bond to the substrate or maintains the bond over time. This can be caused by some factors, including:
- Surface contamination: If the surface is not adequately cleaned and prepared, contaminants such as dirt, oil, and grease can interfere with the bonding process.
- Incompatible materials: Some materials are more difficult to bond than others, and some combinations of materials may need to be connected better.
- Improper application:If the adhesive is not applied correctly, it may not bond properly.
To troubleshoot poor adhesion, try the following
- Clean and prepare the surface properly: Make sure the surface is free of contaminants and is roughened or etched to promote adhesion.
- Use a different adhesive:If the materials are incompatible, try an additional adhesive designed for those materials.
- Check the application process: Ensure the adhesive is applied correctly and according to the manufacturer’s instructions.
Bond Failure
Bond failure occurs when the bond between the adhesive and the substrate fails completely. This can be caused by many factors, including:
- Incompatible materials:Some materials do not bond well and may require a different adhesive or bonding method.
- Improper surface preparation: The adhesive may only bond properly if the surface is correctly cleaned and prepared.
- Improper application: If the adhesive is not applied correctly, it may not bond properly.
To troubleshoot bond failure, try the following
- Use a different adhesive: If the materials are incompatible, try a separate adhesive designed for those materials.
- Clean and prepare the surface properly: Make sure the surface is free of contaminants and is roughened or etched to promote adhesion.
- Check the application process:Ensure the adhesive is applied correctly and according to the manufacturer’s instructions.
Delamination
Delamination occurs when the bond between the adhesive and the substrate begins to weaken, and the layers start to separate. This can be caused by some factors, including:
- Stress: If the bond is under pressure from movement or temperature changes, it may weaken over time.
- Incompatible materials: Some materials may expand and contract at different rates, causing the bond to weaken.
- Improper application:If the adhesive is not applied correctly, it may not bond properly.
To troubleshoot delamination, try the following
- Check the application process:Ensure the adhesive is applied correctly and according to the manufacturer’s instructions.
- Use a different adhesive: If the materials are incompatible, try another adhesive designed for those materials.
- Consider using mechanical fasteners: In some cases, it may be necessary to use mechanical fasteners in addition to the adhesive to provide additional strength and stability.
Safety Considerations for Rubber Bonding Adhesives
Rubber bonding adhesives are widely used in various industries for bonding rubber to substrates such as metals, plastics, glass, and concrete. While these adhesives offer numerous benefits, it is crucial to consider safety considerations when handling and using them.
- Proper ventilation: Rubber bonding adhesives often contain volatile organic compounds (VOCs) that can be hazardous to human health. These compounds can cause eye, nose, and throat irritation, headaches, nausea, dizziness, and long-term health effects such as liver and kidney damage. Therefore, using these adhesives in well-ventilated areas is crucial to reduce the risk of exposure to these compounds. Proper ventilation can be achieved by using exhaust fans, opening windows, and doors, or working outside.
- Protective gear:It is essential to wear protective equipment to minimize the risk of exposure to the harmful compounds found in rubber bonding adhesives. Some crucial protective gear that must be worn includes safety goggles, gloves, and respiratory masks. Safety goggles protect the eyes from splashes and fumes, while gloves protect the hands from direct contact with the adhesive. Respiratory masks can protect the lungs from inhaling harmful fumes.
- Handling and storage: Proper handling and storage of rubber bonding adhesives can help reduce the risk of accidents and exposure. These adhesives must be handled carefully and stored in a cool, dry, well-ventilated area away from heat sources, sparks, and open flames. The containers must be tightly sealed when not in use to prevent the adhesive from drying out or becoming contaminated. It is also essential to carefully read and follow the manufacturer’s instructions to ensure safe handling and use.
In addition to these general safety considerations, there are a few additional precautions that must be taken when working with specific types of rubber bonding adhesives:
- Due to their high VOC levels, contact adhesivesmust be used in well-ventilated areas. The bond must be applied with a brush or roller rather than spraying to reduce the risk of inhalation. It is also essential to avoid smoking, eating, or drinking while using contact adhesives, as these can increase the risk of exposure.
- Cyanoacrylate adhesives: Cyanoacrylate adhesives are fast-setting and require careful handling to prevent accidental fingers and other body parts bonding. Gloves must be worn when working with these adhesives, and the adhesive must not be applied to wet surfaces as this can cause a reaction that generates heat and can lead to burns.
- Two-part adhesives: Two-part adhesives require mixing two components, which can generate heat and cause the adhesive to cure rapidly. It is crucial to wear gloves and protective eyewear when handling these adhesives to prevent skin and eye contact. To avoid inhaling fumes, the bond must also be mixed in a well-ventilated area.
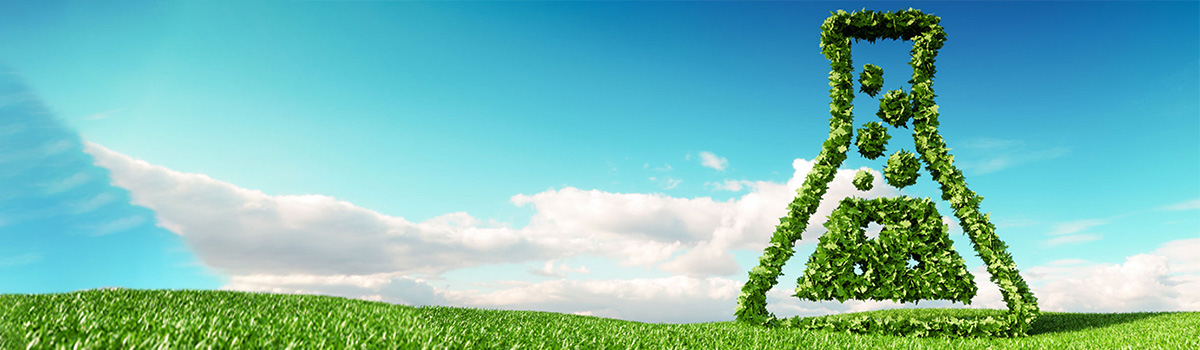
Environmental Considerations for Rubber Bonding Adhesives
Rubber bonding adhesives are essential in many industries due to their unique properties and ability to bond different materials. However, in addition to their functionality, it’s vital to consider their impact on the environment. This brings us to the topic of environmental considerations for rubber bonding adhesives.
Here are some key points to consider:
Biodegradability
- Some rubber bonding adhesives are designed to biodegrade over time, making them a more environmentally-friendly option. These adhesives are typically made from natural materials, such as plant-based oils or starches.
- Biodegradable adhesives can help reduce the environmental impact of industrial processes, as they break down into harmless components and don’t contribute to landfill waste.
Toxicity
- Some rubber bonding adhesives contain toxic materials that can harm the environment if disposed of improperly. For example, some bonds may contain solvents that can release volatile organic compounds (VOCs) into the air, causing air pollution.
- It’s important to carefully read rubber bonding adhesives’ labels and safety data sheets to determine their toxicity levels and proper handling procedures.
Recycling
- Rubber bonding adhesives can make recycling the materials they bond together tricky, contributing to waste and pollution.
- However, some companies have developed innovative solutions for recycling bonded materials, such as separating the materials using heat or solvents. Some rubber bonding adhesives can also be designed for easier disassembly and recycling.
Considering these environmental considerations when choosing and using rubber bonding adhesives can help reduce our environmental impact and promote sustainable practices in the industry.
Innovations in Rubber Bonding Adhesives
Rubber bonding adhesives have come a long way in functionality and sustainability. Here we’ll talk about a few recent advancements in this sector.
- Nanotechnology: One of the most significant innovations in rubber bonding adhesives is the incorporation of nanotechnology. Nanoparticles can be added to the adhesive to improve its mechanical properties, such as strength and toughness. They can also enhance the adhesive’s resistance to heat, moisture, and other environmental factors. Additionally, nanoparticles can provide a larger surface area for the adhesive to bond to, increasing the strength of the bond.
- Sustainable adhesives:Another major innovation in rubber bonding adhesives is the development of sustainable bonds. With a growing emphasis on sustainability in all industries, the adhesive industry is no exception. Some manufacturers now produce adhesives from renewable resources, such as plant-based materials. These adhesives are not only more environmentally friendly but also have the potential to reduce the carbon footprint of the manufacturing process.
Case Studies: Rubber Bonding Adhesives in Action
Rubber bonding adhesives have various applications across various industries, including automotive, aerospace, medical, and electronics. Here we demonstrate how rubber bonding adhesives have been employed in different sectors, and we shall present a few case studies.
Automotive industry
Rubber bonding adhesives are widely used in the automotive industry for bonding various components such as weatherstripping, gaskets, and seals. These adhesives provide a reliable bond resistant to heat, water, and chemicals, making them ideal for automotive applications. In the automotive industry, rubber bonding adhesives have been used in a range of applications, including:
- Bonding weatherstripping to car doors and windows
- Bonding rubber gaskets to engine components
- Bonding rubber seals to fuel tanks
Aerospace industry
Rubber bonding adhesives are also widely used in the aerospace industry for bonding various components, and these adhesives must withstand extreme temperatures, vibrations, and other harsh conditions. In the aerospace industry, rubber bonding adhesives have been used in a range of applications, including:
- Bonding rubber seals to aircraft doors and windows
- Bonding rubber gaskets to engine components
- Bonding rubber insulation to spacecraft components
Medical industry
Rubber bonding adhesives are also used in the medical industry for bonding various components, such as tubing and catheters. These adhesives must be biocompatible and safe for use in medical applications. In the medical sector, rubber bonding adhesives have been used in a range of applications, including:
- Bonding rubber tubing to medical devices
- Bonding rubber catheters to medical devices
Electronics industry
Rubber bonding adhesives are also used in the electronics industry for bonding various components, such as sensors and connectors. These adhesives must withstand high temperatures, moisture, and other harsh conditions. In the electronics industry, rubber bonding adhesives have been used in a range of applications, including:
- Bonding rubber seals to electronic enclosures
- Bonding rubber connectors to electronic components
Future Trends in Rubber Bonding Adhesives
Rubber bonding adhesives have come a long way since their inception, and their uses are expanding into diverse applications. As technology advances, so do the capabilities of adhesives, resulting in new innovations and future trends. In this piece, we’ll discuss innovative and high-performance adhesives, two key trends in rubber bonding adhesives.
Smart or intelligent adhesives are a recent innovation in the adhesive industry. These adhesives are designed to have the ability to respond to changes in their environment, such as temperature, humidity, and pressure. The technology behind these adhesives is similar to intelligent materials, which can change their properties in response to external stimuli. Innovative adhesives can alter their bonding strength, viscosity, or cure time based on the environment, making them ideal for applications that require precise and adaptable bonding properties.
High-performance adhesives are designed to exceed the capabilities of traditional bonds, and they offer superior bonding strength, durability, and chemical resistance. These adhesives are ideal for applications that require long-term durability and performance, even in harsh environments. High-performance adhesives are also engineered to provide improved productivity, reducing downtime and the need for rework.
Some of the benefits of these future trends in rubber bonding adhesives include:
- Increased efficiency:Smart adhesives and high-performance adhesives provide better productivity, reducing downtime and the need for rework.
- Enhanced durability:High-performance adhesives offer superior bonding strength, durability, and chemical resistance, ensuring the bond lasts long.
- Improved precision:Smart adhesives can change their bonding strength, viscosity, or cure time based on the environment, making them ideal for applications that require precise and adaptable bonding properties.
- Cost-effective: These adhesives’ increased efficiency and durability reduce maintenance, repairs, and replacement costs.
In conclusion, rubber bonding adhesives offer reliable and effective bonding solutions for a wide range of rubber-based materials. They provide strong and durable bonds that can withstand various environmental factors, contributing to the overall quality and longevity of the products. Manufacturers and consumers can rely on rubber bonding adhesives for secure and long-lasting bonds in various applications.