SMT Adhesive

In the ever-evolving world of electronics manufacturing, Surface Mount Technology (SMT) adhesive has emerged as a game-changer. This advanced Adhesive plays a crucial role in ensuring the seamless integration of electronic components onto printed circuit boards (PCBs). From enhancing product reliability to streamlining production processes, SMT adhesive has become an indispensable tool for manufacturers. This blog post will explore the various aspects of SMT adhesive and its significance in the electronics industry.
Understanding SMT Adhesive: A Brief Overview
SMT adhesive, or surface mount technology adhesive, is used in the electronics industry to attach surface mount devices (SMDs) to printed circuit boards (PCBs).
SMT adhesive is typically made of synthetic resins, solvents, and additives. The Adhesive is applied to the PCB using a dispenser or stencil. Then the SMDs are placed onto the Adhesive before it dries.
Several types of SMT adhesives are available, including epoxy, acrylic, and silicone-based adhesives. Each type has its unique properties and advantages. For example, epoxy adhesives are known for their high strength and durability, while acrylic adhesives offer excellent electrical insulation properties.
SMT adhesive is critical to the success of SMT manufacturing, as it helps to hold the SMDs in place during the assembly process. The Adhesive also improves the final product’s reliability and durability by providing mechanical support to the SMDs.
One of the critical considerations when selecting an SMT adhesive is its curing time. Curing time refers to the time required for the Adhesive to fully harden and bond to the PCB and SMD. The curing time can vary depending on the type of Adhesive and the environmental conditions in which the Adhesive is applied.
In addition to curing time, other factors to consider when selecting an SMT adhesive include its viscosity, thixotropy, and thermal and chemical resistance.
Overall, SMT adhesive is a critical component of the SMT manufacturing process, helping to ensure the reliability and durability of electronic devices. Choosing the suitable Adhesive can help ensure the success of SMT assembly and improve the final product’s performance.
The Importance of SMT Adhesive in Electronics Manufacturing
SMT adhesive is crucial in electronics manufacturing, particularly in assembling surface mount devices (SMDs) onto printed circuit boards (PCBs). The use of SMT adhesive ensures that the SMDs are securely attached to the PCB, providing mechanical support and improving the reliability and durability of the final product.
One of the main advantages of SMT adhesive is its ability to hold SMDs in place during the assembly process. Without Adhesive, SMDs could shift or move during manufacturing, leading to defects or failures in the final product. SMT adhesive helps to prevent these issues by holding the SMDs in place until they are soldered to the PCB.
SMT adhesive also helps improve electronic device performance by providing mechanical support to SMDs. This is particularly important in applications that may expose the device to vibration or other mechanical stresses. The Adhesive helps to absorb these stresses and prevent damage to the SMDs, ensuring that the device continues to function correctly over time.
In addition to mechanical support, SMT adhesive can provide electrical insulation and thermal conductivity properties. This is important in applications where the SMDs generate heat, as the Adhesive can help to dissipate this heat and prevent overheating and damage to the device.
Choosing a suitable SMT adhesive is crucial to the success of electronics manufacturing. Factors such as curing time, viscosity, thixotropy, and chemical and thermal resistance should all be considered when selecting an adhesive. Choosing the wrong Adhesive could lead to defects or failures in the final product, which could be costly and time-consuming.
Types of SMT Adhesive: An Overview of Variants
Several types of SMT (Surface Mount Technology) Adhesive are available, each with its unique properties and advantages. The selection of the correct type of Adhesive depends on the application’s specific requirements, including the types of surfaces to be bonded, the environmental conditions, and the curing time.
- Epoxy Adhesive: Epoxy adhesives are the most commonly used SMT adhesive in electronics manufacturing. They offer high strength and excellent durability, making them ideal for applications where mechanical stress and high temperatures are expected. Epoxy adhesives cure quickly, which makes them a preferred choice for high-volume production environments.
- Acrylic Adhesive: Acrylic adhesives are known for their excellent electrical insulation properties. They offer good bonding strength and can cure at room temperature, making them suitable for applications where high temperatures are not required. Acrylic adhesives also resist environmental factors like moisture, chemicals, and UV radiation.
- Silicone Adhesive: Silicone adhesives offer excellent flexibility, making them ideal for applications where thermal expansion and contraction are expected. They also provide good resistance to moisture, chemicals, and UV radiation. However, silicone adhesives have lower bonding strength than epoxy and acrylic adhesives.
- UV Curable Adhesive: UV curable adhesives cure when exposed to UV light, making them a preferred choice for applications where fast curing is required. They offer excellent bonding strength and are ideal for applications where high temperature and mechanical stress are not expected.
- Hot Melt Adhesive: Hot melt adhesives are thermoplastic materials heated to a molten state and applied to the surface. They cure quickly and offer good bonding strength. However, they are not suitable for applications where high temperatures are expected.
Factors to Consider When Choosing SMT Adhesive
Choosing the right SMT (Surface Mount Technology) adhesive is critical to the success of electronics manufacturing. Several factors should be considered when selecting a bond, including:
- Substrate Materials: The types of substrates to be bonded play a crucial role in determining the type of Adhesive to be used. Some adhesives are better suited for bonding specific materials such as glass, ceramic, or metal.
- Environmental Conditions: The environment in which the final product will be used should also be considered. Factors such as temperature, humidity, and exposure to chemicals can affect the performance of the Adhesive. It is essential to select an adhesive that is resistant to the specific environmental conditions.
- Curing Time: The Adhesive’s curing time is an essential factor to consider. The curing time should be compatible with the production cycle of the product. Quick-curing adhesives are ideal for high-volume production environments. In contrast, slower-curing adhesives may be suitable for low-volume production.
- Viscosity and Thixotropy: The thickness and thixotropy of the Adhesive are crucial factors to consider, especially when bonding small components or uneven surfaces. An adhesive with low viscosity is ideal for connecting small components. In contrast, an adhesive with high thixotropy is suitable for bonding uneven surfaces.
- Chemical and Thermal Resistance: The Adhesive should resist the chemicals and thermal conditions expected during the product’s life cycle. This is particularly important in high-temperature applications, where the Adhesive must withstand extreme heat and thermal cycling.
- Application Method: The method of application is another critical factor to consider. Some adhesives are applied using dispensers, while others use stencil printing or jet dispensing methods. The selected Adhesive should be compatible with the application method.
The Role of SMT Adhesive in Component Placement
Surface mount technology (SMT) Adhesive is critical in component placement in electronics manufacturing. The Adhesive is applied to the surface of the printed circuit board (PCB) to hold the components in place before soldering.
The following are the critical roles of SMT adhesive in component placement:
- Secure Component Placement: SMT adhesive secures the components onto the PCB. This is important because the components are very small and lightweight and may move or shift during manufacturing. The Adhesive helps to hold the components in place and prevent them from going or falling off the board.
- Prevent Solder Bridging: SMT adhesive is also used to avoid solder bridging, a common issue in electronics manufacturing. Solder bridging occurs when an unintended connection joins together two adjacent solder joints. This can cause a short circuit and damage the components. The Adhesive helps to keep the components separated and prevent solder bridging.
- Improve Solder Joint Quality: SMT adhesive can also improve the quality of the solder joint. The Adhesive holds the pieces in place, which reduces the risk of movement during the soldering process. This results in a more consistent and reliable solder joint.
- Enhance Manufacturing Efficiency: SMT adhesive can also enhance manufacturing efficiency. The Adhesive is applied before the components are placed on the PCB, which reduces the time required for manual alignment and placement. This results in a faster and more efficient manufacturing process.
- Improve Product Reliability: SMT adhesive can improve the reliability of the final product. By holding the components in place during the manufacturing process, the Adhesive helps to ensure that the details are correctly aligned and securely attached to the PCB. This reduces the risk of component failure or malfunction due to movement or vibration.
Achieving Strong and Reliable Bonds with SMT Adhesive
Achieving solid and reliable bonds with SMT (Surface Mount Technology) adhesive is critical to the success of electronics manufacturing. SMT adhesive holds components in place on a printed circuit board (PCB) before they are soldered. Here are some tips for achieving solid and reliable bonds with SMT adhesive:
- Select the Right Adhesive: Choosing the suitable SMT adhesive is essential. Factors to consider when selecting an adhesive include substrate materials, environmental conditions, curing time, viscosity, thixotropy, chemical and thermal resistance, and application method. Choosing a sealant compatible with the project’s specific requirements will help ensure a robust and reliable bond.
- Prepare the Surface: The surface of the PCB must be clean and free of contaminants such as oils, dirt, and dust. This can be achieved using a cleaning agent and a lint-free cloth or a plasma cleaner. Proper surface preparation is critical to achieving a robust and reliable bond.
- Apply the Adhesive Correctly: The Adhesive should be applied in the correct amount and the right location. Dispensing equipment such as syringes, needles, and dispensers can be used to apply the Adhesive. The Adhesive should be applied evenly and in the correct amount to ensure that the components are held in place securely.
- Ensure Proper Curing: The Adhesive must be given sufficient time to cure before the components are soldered. Curing time can vary depending on the Adhesive and the environmental conditions. Follow the manufacturer’s instructions to ensure proper curing.
- Monitor Environmental Conditions: The environmental conditions in the manufacturing environment can affect the performance of the Adhesive. Temperature, humidity, and exposure to chemicals can all impact the strength and reliability of the bond. Monitor these conditions and take appropriate measures to ensure they are within the recommended range.
- Use Quality Components: Quality components are essential for achieving a robust and reliable bond. Poor-quality components may have irregularities or inconsistencies that can affect the bonding process. Use ingredients that meet the required specifications and are sourced from reputable suppliers.
- Test the Bond: Testing the bond is essential in ensuring that the Adhesive has formed a robust and reliable bond. Various methods can be used to test the bond, including pull testing, shear testing, and thermal cycling testing. Testing can help identify any issues with the bonding process and ensure the final product is reliable and durable.
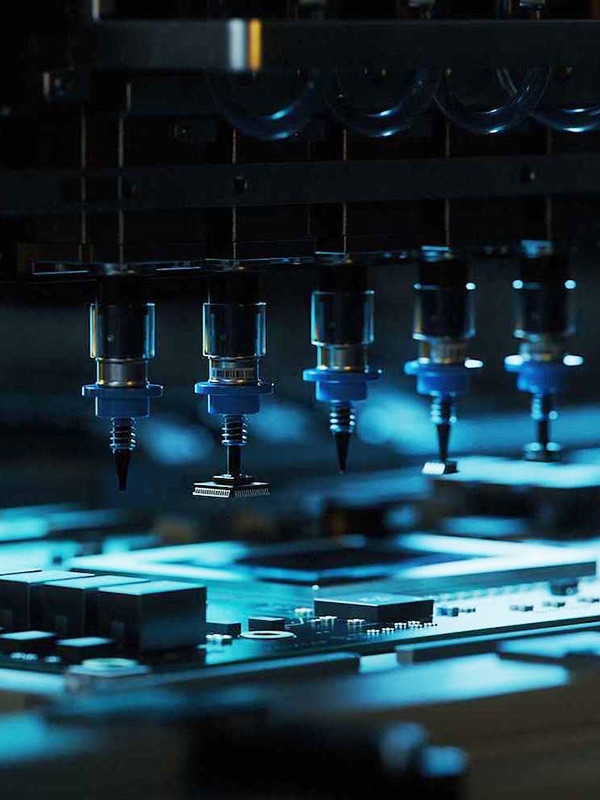
SMT Adhesive Dispensing Techniques and Best Practices
SMT (Surface Mount Technology) adhesive dispensing is critical in electronics manufacturing. The Adhesive holds components in place on a printed circuit board (PCB) before they are soldered. Here are some dispensing techniques and best practices for SMT adhesive:
- Manual Dispensing: Manual dispensing is a cost-effective technique requiring a skilled operator. Manual dispensing can be done using a syringe or a dispensing pen. This technique allows for precise control over the amount of Adhesive dispensed, making it ideal for small-scale projects.
- Automated Dispensing: Automated dispensing is a faster and more efficient technique ideal for large-scale production. Automated dispensing systems use equipment such as robots, pumps, and valves to apply the Adhesive to the PCB. This technique allows for consistent dispensing and can increase production efficiency.
- Jet Dispensing: Jet dispensing is a high-speed dispensing technique that uses a pneumatic dispenser to apply the Adhesive in a fine stream. This technique is ideal for high-volume production and can dispense small amounts of Adhesive with high precision.
- Screen Printing: Screen printing is a widely used dispensing technique that involves applying the Adhesive through a stencil. This technique is ideal for applying many Adhesives to a PCB. Screen printing is a cost-effective and efficient dispensing method that can be used for both small-scale and large-scale production.
- Best Practices: Following best practices to dispense SMT adhesive is essential. Some best practices include:
- Ensure the dispensing equipment is clean and free of contaminants.
- Use the correct dispensing tip or nozzle for the Adhesive being used.
- Ensure the dispensing information or nozzle is sized for the bonded component.
- Maintain the proper distance between the dispensing tip or nozzle and the PCB.
- Keep the dispensing tip or nozzle perpendicular to the surface of the PCB.
- Dispense the Adhesive in a continuous motion without stopping.
- Ensure the Adhesive is dispensed evenly and in the correct amount.
- Monitor the viscosity and thixotropy of the Adhesive to ensure proper dispensing.
Overcoming Challenges in SMT Adhesive Application
SMT (Surface Mount Technology) adhesive application can be challenging due to various factors, such as the Adhesive’s viscosity, the components’ size and shape, and the complexity of the PCB layout. Here are some common challenges in SMT adhesive application and how to overcome them:
- The viscosity of the Adhesive: SMT adhesives are available in different viscosities, ranging from low to high. The consistency of the Adhesive can affect the dispensing process and the bond strength. Low-viscosity adhesives flow more efficiently, while high-viscosity adhesives may require higher dispensing pressure. To overcome this challenge, manufacturers should select an adhesive with the appropriate viscosity for the specific application and adjust the dispensing parameters accordingly.
- Component Size and Shape: SMT components come in various sizes and shapes, and some may be difficult to bond due to their small size or irregular shape. In addition, features that are too close together may require special dispensing techniques to avoid adhesive bleeding or bridging. To overcome this challenge, manufacturers should select a dispensing technique that can handle the size and shape of the components, such as a fine dispensing tip or nozzle for small features or a jet dispensing system for members that are close together.
- PCB Layout: The complexity of the PCB layout can also affect the SMT adhesive application. Components placed too close to the edge of the PCB may require special dispensing techniques to avoid adhesive overflow. In addition, PCBs with high component density may require a dispensing approach that can apply Adhesive in a precise and controlled manner. To overcome this challenge, manufacturers should carefully review the PCB layout and select a dispensing technique that can accommodate the layout.
- Environmental Factors: Environmental factors such as temperature, humidity, and air pressure can affect the SMT adhesive application process. For example, high humidity can cause the Adhesive to cure too quickly. In contrast, low humidity can cause the Adhesive to cure too slowly. To overcome this challenge, manufacturers should carefully monitor the environmental conditions and adjust the dispensing parameters accordingly.
- Adhesive Curing: SMT adhesives require curing to achieve the desired bond strength. The curing process can be affected by factors such as temperature, humidity, and the thickness of the adhesive layer. To overcome this challenge, manufacturers should follow the adhesive manufacturer’s curing time and temperature recommendations and ensure that the environmental conditions are within the recommended range.
The Impact of SMT Adhesive on Thermal Management
Surface mount technology (SMT) adhesives play an essential role in the thermal management of electronic devices. The thermal management of electronic devices is crucial as it ensures that the machine operates efficiently and reliably and prevents damage caused by excessive heat. SMT adhesives can impact thermal management in several ways, as discussed below.
Firstly, SMT adhesives can provide a thermally conductive pathway for heat dissipation. These adhesives are designed to have high thermal conductivity, allowing them to transfer heat away from heat-generating components to the device’s heat sink. This heat transfer helps to maintain the device’s temperature within safe operating limits.
Secondly, SMT adhesives can also impact thermal management by providing a thermal barrier. These adhesives can act as a thermal insulator, preventing heat from escaping from the device. This can be useful when maintaining a consistent temperature is critical, such as in medical equipment or scientific instruments.
Thirdly, SMT adhesives can affect thermal management through their cure characteristics. Some adhesives cure at higher temperatures, which can cause thermal stress on the device. This can lead to mechanical failures, such as cracking or delamination of the Adhesive. Therefore, choosing an adhesive that cures at a temperature that does not exceed the device’s operating temperature is essential.
Fourthly, the adhesive thickness can also affect thermal management. A thicker adhesive layer can create a thermal barrier that can hinder heat dissipation, increasing temperatures in the device. On the other hand, a thinner adhesive layer can allow heat to transfer more efficiently, improving thermal management.
Lastly, SMT adhesive can impact the device’s overall thermal performance. Different bonds have different thermal conductivities, cure characteristics, and thicknesses. Choosing an adhesive specifically designed for thermal management can help ensure the device’s optimal performance.
SMT Adhesive and its Contribution to Vibration and Shock Resistance
Surface mount technology (SMT) adhesives impact thermal management and contribute significantly to electronic device vibration and shock resistance. Vibration and shock can cause damage to electronic devices, and SMT adhesives are essential in mitigating this risk.
SMT adhesives provide mechanical support and reinforcement to the soldered components. They act as a buffer between the details and the substrate, distributing vibration and shock forces across a wider area. This reduces the stress on the solder joints and prevents them from cracking or breaking under the applied pressure.
The adhesive material used in SMT applications also plays a critical role in vibration and shock resistance. The Adhesive should be solid and durable enough to withstand the forces applied to the device without breaking or cracking. Additionally, the Adhesive should have some degree of elasticity to allow for movement and flexibility in the machine without compromising its structural integrity.
SMT adhesive can also contribute to the damping of vibrations in the device. Damping is the dissipation of energy that reduces a system’s vibrations amplitude. The Adhesive can absorb and dissipate some of the power from vibrations, reducing the amplitude of the oscillations and preventing them from causing damage to the device.
The thickness of the adhesive layer can also affect the vibration and shock resistance of the device. A thicker adhesive layer can provide cushioning and shock absorption. A thinner layer can be more rigid and offer less shock resistance. The thickness of the adhesive layer should be selected based on the specific needs of the device and the level of vibration and shock it will be subjected to.
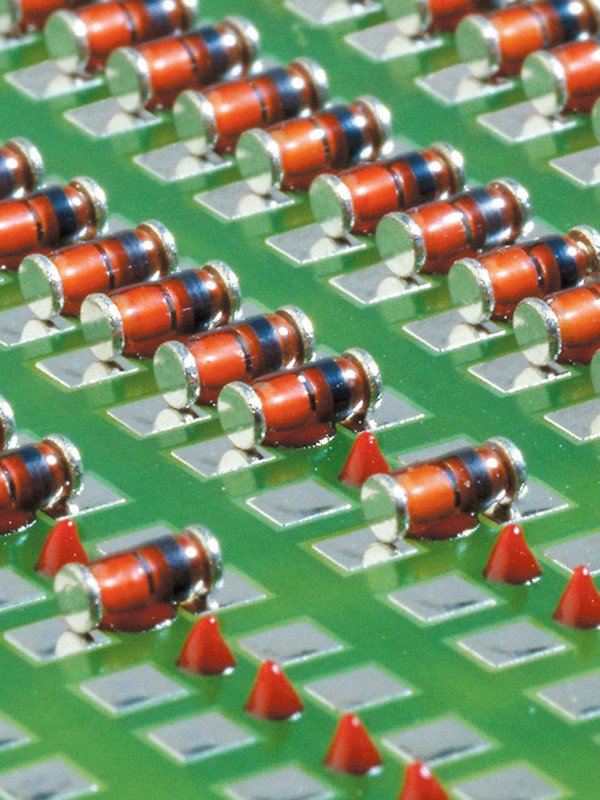
Advantages Of SMT Adhesive
Surface mount technology (SMT) Adhesive is a critical component in the manufacturing of electronic devices. It is a type of Adhesive specifically designed to bond surface-mount parts to printed circuit boards (PCBs) during manufacturing. Here are some of the advantages of using SMT adhesive:
- Improved reliability: SMT adhesive provides a strong bond between surface mount components and PCBs, improving electronic devices’ reliability and performance. It helps prevent components from becoming dislodged or damaged during operation, leading to failures or malfunctions.
- Reduced rework and repairs: By using SMT adhesive to secure components, manufacturers can reduce the need for rework and repairs. This can save time and money in the manufacturing process and improve the finished product’s overall quality.
- Enhanced thermal management: SMT adhesive can help improve electronic device thermal management by providing a heat sink between components and the PCB. This helps dissipate heat and prevent overheating, leading to failures or malfunctions.
- Miniaturization: SMT adhesive enables manufacturing of smaller and more compact electronic devices. It allows for the use of smaller components. It reduces the space needed for component placement, which can result in more efficient and cost-effective designs.
- Improved electrical performance: SMT adhesive can improve the electrical performance of electronic devices by reducing the resistance between components and the PCB. This can result in improved signal integrity, reduced noise, and better overall performance.
- Versatility: SMT adhesive is available in various formulations and viscosities to meet the specific needs of different applications. This makes it a versatile bond for multiple electronic devices, including consumer electronics, medical appliances, and automotive electronics.
Overall, the use of SMT adhesive provides many advantages in the manufacturing of electronic devices. Providing a robust and reliable bond between surface mount components and PCBs can improve electronic devices’ performance, reliability, and efficiency while reducing the need for rework and repairs. It is a versatile adhesive used in various applications, making it an essential component in the electronics industry.
Disadvantages Of SMT Adhesive
Surface Mount Technology (SMT) adhesive is a type of adhesive that is commonly used in the manufacturing of electronic circuits and devices. It is a glue that holds surface mount components in place during soldering. While SMT adhesive has its advantages, there are also several disadvantages to using this type of adhesive.
- Difficulty in removal: One of the main disadvantages of SMT adhesive is that it can be difficult to remove. Once the adhesive has cured, removing the surface mount component can be challenging without causing damage to the circuit board. This can make it challenging to repair or replace parts in the future.
- Cost: SMT adhesive can be expensive, making it difficult to use in high-volume production environments. This is especially true if the adhesive is of high quality, which is necessary to ensure reliable adhesion of the components.
- Curing time: SMT adhesive requires a certain amount of time to cure before the pieces can be soldered in place. This can increase the overall production time of electronic devices and circuits.
- Shelf life: SMT adhesive has a limited shelf life, so it must be used within a specific timeframe. This can lead to waste if the adhesive is unused before it expires.
- Quality control: SMT adhesive can be challenging in high-volume production environments. Variations in the application of the bond can lead to inconsistencies in the adhesion of the components, which can lead to defects in the final product.
- Environmental concerns: SMT adhesive contains chemicals that can harm the environment if not disposed of properly. This can concern companies committed to sustainable and environmentally responsible manufacturing practices.
- Potential for damage to components: SMT adhesive can damage the features that it is meant to hold in place. This can occur if the adhesive is applied too thickly or not evenly applied.
- Lack of flexibility: SMT adhesive can be brittle, which means it may not be suitable for components requiring flexibility. This can limit the types of features used in electronic devices and circuits.
Environmental Considerations: Lead-Free SMT Adhesive Solutions
Lead-free surface mount technology (SMT) adhesive solutions have become increasingly important due to environmental concerns. The RoHS (Restriction of Hazardous Substances) directive in the EU and similar regulations in other countries have restricted the use of lead in electronic devices. Therefore, lead-free SMT adhesives have become a popular alternative to traditional lead-containing bonds.
Lead-free SMT adhesives typically contain other metals, such as silver, copper, or tin, which are considered less harmful to the environment than lead. These alternative metals have become more prevalent as manufacturers seek to reduce their environmental impact while maintaining high-quality product performance.
Manufacturing lead-free SMT adhesives has a lower environmental impact than traditional lead-containing bonds. The production of lead-containing adhesives often requires the use of toxic chemicals, which can be harmful to workers and the environment. In contrast, lead-free adhesives are produced using cleaner, more environmentally friendly methods.
Another environmental consideration for lead-free SMT adhesives is their disposal. Traditional lead-containing adhesives are considered hazardous waste and require special disposal procedures. In contrast, lead-free adhesives are not classified as hazardous waste. They can be disposed of using standard waste disposal methods.
Lead-free SMT adhesives have been shown to perform similarly to traditional lead-containing bonds regarding thermal management, vibration, and shock resistance. Therefore, they can be used as a direct replacement for lead-containing adhesives without compromising the device’s performance.
SMT Adhesive in Miniaturized Electronics: Ensuring Precision
Surface mount technology (SMT) adhesives play a critical role in ensuring the precision of miniaturized electronics. As electronic devices continue to shrink in size, the placement and bonding of components become increasingly critical. SMT adhesives provide mechanical support and reinforcement to the soldered parts, preventing them from shifting or moving during operation.
In miniaturized electronics, the placement of components is crucial to ensure proper functioning. SMT adhesives provide a method to secure parts in place during assembly and operation. The Adhesive must be applied precisely to ensure the components are in the correct location and orientation. Even the slightest misalignment can cause performance issues or render the device unusable.
The precision of SMT adhesive application can be improved through advanced dispensing technologies. These technologies use high-precision dispensers to apply the Adhesive in the exact amount and location required for each component. This ensures that the details are properly secured and aligned during assembly.
The choice of adhesive material is also essential for precision in miniaturized electronics. The Adhesive should have a low viscosity and a high degree of accuracy in its placement. It should also have a rapid cure time, allowing for quick assembly and turnaround times.
In addition to precision in placement, SMT adhesives can also impact the performance of miniaturized electronics. The Adhesive must have excellent thermal conductivity to ensure efficient heat transfer from the components to the substrate. The Adhesive should also have high electrical insulation properties to prevent short circuits and other performance issues.
Overall, SMT adhesives play a critical role in ensuring the precision and performance of miniaturized electronics. The Adhesive must be applied precisely, with high accuracy, and the choice of material must be carefully considered to meet the application’s specific needs. Advanced dispensing technologies can improve the precision of adhesive application, ensuring that the components are properly secured and aligned during assembly. By choosing the suitable Adhesive, manufacturers can ensure the performance and longevity of their miniaturized electronic devices.
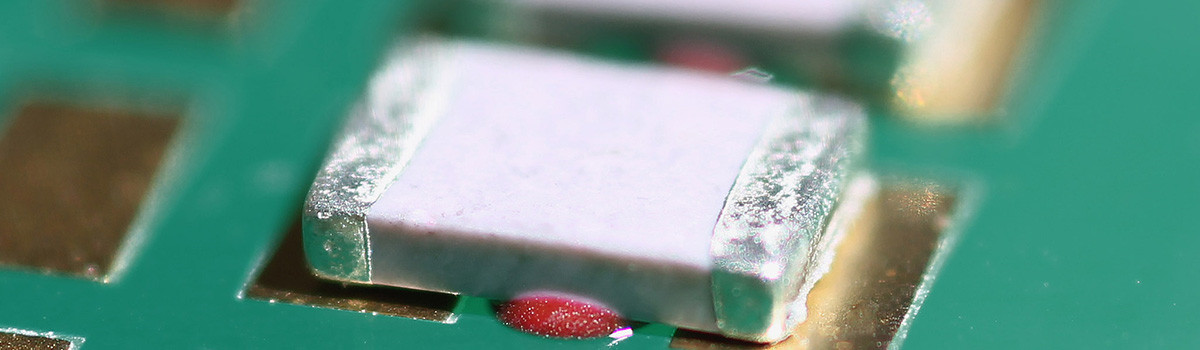
Enhancing Yield and Efficiency with SMT Adhesive
Surface mount technology (SMT) adhesives play a critical role in ensuring the precision of miniaturized electronics. As electronic devices continue to shrink in size, the placement and bonding of components become increasingly critical. SMT adhesives provide mechanical support and reinforcement to the soldered parts, preventing them from shifting or moving during operation.
In miniaturized electronics, the placement of components is crucial to ensure proper functioning. SMT adhesives provide a method to secure parts in place during assembly and operation. The Adhesive must be applied precisely to ensure the components are in the correct location and orientation. Even the slightest misalignment can cause performance issues or render the device unusable.
The precision of SMT adhesive application can be improved through advanced dispensing technologies. These technologies use high-precision dispensers to apply the Adhesive in the exact amount and location required for each component. This ensures that the details are properly secured and aligned during assembly.
The choice of adhesive material is also essential for precision in miniaturized electronics. The Adhesive should have a low viscosity and a high degree of accuracy in its placement. It should also have a rapid cure time, allowing for quick assembly and turnaround times.
In addition to precision in placement, SMT adhesives can also impact the performance of miniaturized electronics. The Adhesive must have excellent thermal conductivity to ensure efficient heat transfer from the components to the substrate. The Adhesive should also have high electrical insulation properties to prevent short circuits and other performance issues.
Overall, SMT adhesives play a critical role in ensuring the precision and performance of miniaturized electronics. The Adhesive must be applied precisely, with high accuracy, and the choice of material must be carefully considered to meet the application’s specific needs. Advanced dispensing technologies can improve the precision of adhesive application, ensuring that the components are properly secured and aligned during assembly. By choosing the suitable Adhesive, manufacturers can ensure the performance and longevity of their miniaturized electronic devices.
Addressing Reliability Concerns with SMT Adhesive
Surface mount technology (SMT) Adhesive plays an essential role in ensuring the reliability of electronic devices. The Adhesive secures components in place, preventing movement and minimizing the risk of damage or failure during operation. However, there are several reliability concerns associated with SMT adhesive that manufacturers must address to ensure the long-term performance of their products.
One of the main reliability concerns with SMT adhesive is its long-term durability. The Adhesive must withstand various environmental factors such as temperature changes, humidity, and mechanical stress. Over time, exposure to these factors can cause the Adhesive to deteriorate, leading to component movement and potential failure. Therefore, manufacturers must select an adhesive with excellent durability and resistance to environmental factors to ensure long-term reliability.
Another concern with SMT adhesive is its potential to create voids or air bubbles during application. These voids can cause issues with heat transfer and lead to premature component failure. Manufacturers must carefully control their adhesive application process to prevent void formation and maintain reliable heat transfer.
Storage conditions and handling can also impact the reliability of SMT adhesive. Suppose the Adhesive is not stored correctly or mishandled during manufacturing. In that case, it can become contaminated or degraded, reducing performance and reliability.
To address these reliability concerns, manufacturers can take several steps. They can choose an adhesive with proven durability and resistance to environmental factors, ensuring it can withstand long-term use rigors. The adhesive application process can also be carefully controlled to prevent the void formation and maintain reliable heat transfer. Proper storage and handling of the Adhesive can also help to keep its performance and reliability.
In addition, manufacturers can perform extensive testing and quality control measures to ensure the reliability of their products. This can include accelerated aging tests, environmental testing, and functional testing to identify potential issues and ensure the Adhesive performs as expected.
SMT Adhesive and its Role in Rework and Repair Processes
Surface mount technology (SMT) Adhesive is essential in reworking and repairing electronic devices. Rework and repair processes are standard in the electronics industry, as defects and issues can arise during manufacturing or use. SMT adhesive can be used to re-secure components that have become loose or detached or to repair damaged parts.
When performing rework or repair with SMT adhesive, choosing the suitable Adhesive for the application is essential. The Adhesive must have suitable properties to ensure strong adhesion to the component and the substrate. Additionally, the Adhesive should be easy to apply, with a rapid cure time to minimize downtime and reduce repair costs.
One everyday use of SMT adhesive in rework and repair is for reattaching components that have become loose or detached. This can occur due to mechanical stress, temperature fluctuations, or other environmental factors. The Adhesive can secure the piece back in place and prevent further movement or detachment. This can help extend the electronic device’s life and reduce the need for replacement.
SMT adhesive can also repair damaged components, such as cracked or broken solder joints. The Adhesive can be applied to the damaged area to provide additional support and reinforcement, helping to restore the component to its original function. In some cases, SMT adhesive can also be used to repair damaged circuit boards, providing an effective solution for minor damage or issues.
In addition to its use in rework and repair processes, SMT adhesive can also prevent the need for rework or repair in the first place. The Adhesive can be used during the initial manufacturing process to ensure proper component placement and to avoid movement or detachment. This can help minimize the risk of defects or issues that may require rework or repair.
The Future of SMT Adhesive: Advancements and Innovations
The surface mount technology (SMT) adhesive market is expected to grow significantly in the coming years, driven by advancements and innovations in adhesive technology. Manufacturers are constantly seeking new and improved adhesive solutions to meet the ever-increasing electronics industry demands.
One area of innovation in SMT adhesive is the development of more environmentally friendly solutions. With an increased focus on sustainability and reduced environmental impact, manufacturers are looking for adhesives that meet these requirements. New adhesive solutions are being developed that use less harmful chemicals and are easier to recycle, reducing waste and improving sustainability.
Another area of innovation is the development of adhesives with improved thermal management properties. Effective thermal management is becoming increasingly important with the trend toward smaller, more compact electronic devices. Bonds that can improve heat dissipation and transfer can help improve electronic device performance and reliability.
In addition, there is growing interest in adhesives with enhanced electrical properties. Bonds that can improve conductivity or provide electrical insulation can help improve electronic device performance and reliability. This can include bonds with high dielectric strength or low electrical resistance.
Advancements in nanotechnology are also driving innovation in SMT adhesives. Nanoparticles can be added to adhesives to improve their properties, such as thermal conductivity, adhesion strength, and electrical conductivity. This can lead to adhesives with enhanced performance and reliability in various applications.
Lastly, dispensing and application technology advancements also drive innovation in SMT adhesives. New dispensing equipment and methods can help improve adhesive application accuracy and consistency, leading to improved quality and reliability of electronic devices.
Industry Spotlight: Case Studies and Success Stories
Many success stories and case studies highlight the importance and effectiveness of SMT adhesives in the electronics industry. Here are a few examples:
- Mobile Phone Manufacturing: A major mobile phone manufacturer was experiencing device issues, including loose components and poor performance in extreme temperatures. They began using a high-performance SMT adhesive to secure parts in place and improve thermal management. This led to significant improvements in device reliability and performance, as well as a reduction in the need for rework and repairs.
- Automotive Electronics: A manufacturer of automotive electronics was experiencing issues with components becoming dislodged due to vibrations and shocks. They began using a highly resilient SMT adhesive specifically designed to withstand these environmental factors. This led to a significant reduction in component failures and an increase in the overall reliability of the electronic systems.
- Medical Devices: A manufacturer of medical devices was experiencing issues with the adhesion of components during the manufacturing process. They began using a specialized SMT adhesive to provide high adhesion strength and excellent electrical properties. This led to improvements in the quality and reliability of medical devices, as well as a reduction in manufacturing defects and rework.
- Consumer Electronics: A consumer electronics manufacturer was experiencing issues with their devices overheating due to poor thermal management. They began using a high-performance SMT adhesive to improve heat dissipation and transfer. This led to improvements in device performance and reliability, as well as a reduction in the need for repairs and replacements.
These case studies and success stories highlight the importance and effectiveness of SMT adhesives in various applications within the electronics industry. By choosing the suitable Adhesive for the application and ensuring proper application and curing, manufacturers can improve the reliability and performance of their electronic devices while reducing the need for rework and repairs.
Best Practices for Handling, Storage, and Disposal of SMT Adhesive
Proper handling, storage, and disposal of surface mount technology (SMT) adhesive is essential for ensuring its effectiveness and minimizing potential hazards. Here are some best practices to follow:
- Handling: When handling SMT adhesive, it is essential to wear appropriate personal protective equipment (PPE) such as gloves, safety glasses, and a respirator if necessary. This will help to minimize exposure to any harmful chemicals. It is also essential to follow the manufacturer’s instructions for use, including proper mixing, application, and curing.
- Storage: SMT adhesive should be stored in a cool, dry place away from direct sunlight, heat, and moisture. The temperature and humidity conditions should be by the manufacturer’s recommendations to ensure the Adhesive remains effective. Additionally, SMT adhesive should be stored in its original container with a tightly sealed lid to prevent contamination or evaporation.
- Disposal: Proper disposal of SMT adhesive is essential to minimize potential environmental impact. Any unused or expired adhesives should be disposed of per local regulations and guidelines. This may include taking it to a hazardous waste disposal facility or contacting a specialized waste management company for proper disposal.
- Spills and leaks: In the event of a fall or leak, cleaning up the area immediately is essential to prevent further contamination. This may include using absorbent materials such as sand or clay to contain the spill and cleaning the area with a suitable solvent or cleaner.
- Training: Proper training and education should be provided to employees who handle SMT adhesives. This should include information on the proper handling, storage, and disposal of the Adhesive and the proper use of PPE and emergency response procedures in the event of an accident or spill.
By following these best practices for handling, storage, and disposal of SMT adhesive, manufacturers can ensure the safety and effectiveness of the Adhesive while minimizing any potential hazards or environmental impact. It is essential to consult the manufacturer’s instructions, local regulations, and guidelines for specific recommendations and requirements.
Conclusion:
SMT adhesive has revolutionized electronics manufacturing by improving product reliability and enabling precise component placement. The wide range of available adhesive options, advancements in dispensing techniques, and environmental considerations have made SMT adhesive an essential component in modern manufacturing processes. As the industry evolves, manufacturers must stay updated with the latest developments and best practices associated with SMT adhesives to maximize efficiency, yield, and overall product quality. By harnessing the power of SMT adhesive, manufacturers can unlock new possibilities in electronics manufacturing, leading to enhanced performance and customer satisfaction.