One Component Epoxy Adhesive
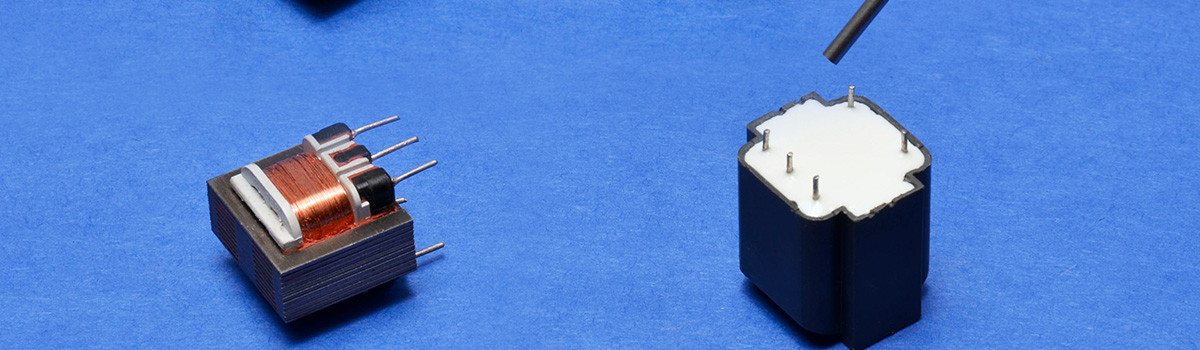
One Component Epoxy Adhesive (OCEA) is a single-part, heat-curing adhesive system that has gained popularity in various industrial applications due to its excellent bonding strength, toughness, and thermal resistance. It eliminates the need for mixing two components and reduces the risk of errors during the application process. This article will discuss the properties, applications, and advantages of One Component Epoxy Adhesive.
What is One Component Epoxy Adhesive?
In adhesives, one component epoxy adhesive (OCEA) stands out as a versatile and reliable bonding solution. Its unique characteristics and ease of use make it a popular choice across various industries. Here we will delve into the features, benefits, and applications of OCEA.
One component epoxy adhesive is a type of adhesive that consists of a resin and a hardener combined into a single package. Unlike two-component epoxies that require mixing before use, OCEA simplifies the bonding process by eliminating manual blending. Once applied, it cures through a chemical reaction triggered by heat, moisture, or a combination of both. This curing process transforms the adhesive into a strong and durable bond, providing excellent adhesion to various substrates.
One component epoxy adhesive offers several noteworthy features and benefits that contribute to its popularity. Firstly, its single-component nature simplifies handling and eliminates the risk of incorrect mixing ratios. Implementing this can save time, reduce waste, and achieve consistent results. OCEA also exhibits excellent chemical resistance, making it suitable for applications exposed to harsh environments, chemicals, and temperature variations.
Additionally, OCEA provides exceptional bond strength, even in challenging conditions. Its high tensile and shear strength can withstand significant loads and stresses. The adhesive’s ability to bond dissimilar materials, such as metals, plastics, and composites, further expands its utility in diverse industries.
Furthermore, OCEA’s quick cure time enhances productivity by reducing assembly or curing waiting periods. It can cure at room temperature or be accelerated with heat, allowing for efficient production processes. Moreover, OCEA offers good electrical insulation properties, ensuring reliable electronic and electrical applications performance.
Due to its versatility and superior bonding properties, OCEA finds application in a wide range of industries. Automotive manufacturers commonly use one component of epoxy adhesive to bond various features, including metal panels, plastic trims, and electronic modules. The aerospace sector derives significant benefits from one component epoxy adhesive (OCEA) due to its lightweight and high-strength characteristics, which are instrumental in bonding structures, composites, and interior components.
How does One Component Epoxy Adhesive work?
One component epoxy adhesive (OCEA) is an excellent bonding solution known for its simplicity and reliability. Understanding how OCEA works can shed light on its effectiveness in creating solid and durable bonds. Here we will explore the working mechanism of OCEA, highlighting its key steps and benefits.
Working Mechanism of One Component Epoxy Adhesive
One component of epoxy adhesive works through a precise chemical reaction that transforms it from a liquid form into a solid, high-strength bond. Here’s an overview of the key steps involved:
- Resin and Hardener:OCEA comprises a resin and a hardener within a single package. Manufacturers carefully formulate these components to ensure optimal curing properties and bond strength in one component epoxy adhesive.
- Application:You must directly apply OCEA onto the surfaces that require bonding, and you can dispense it using various methods, such as syringes, nozzles, or automated equipment. The adhesive should be applied evenly and in the desired quantity, considering the bonding area and substrate requirements.
- Curing Process:Once applied, OCEA initiates the curing process. The curing mechanism can be triggered by heat, moisture, or a combination of both, depending on the specific formulation of the adhesive. Following the manufacturer’s guidelines regarding curing conditions, including temperature and humidity requirements, is crucial.
- Chemical Reaction:During the curing process, the resin and hardener undergo a chemical reaction known as polymerization. This reaction causes the adhesive to cross-link and form a robust molecular network. As a result, the liquid adhesive transforms into a solid material, creating a durable bond.
Benefits of One Component Epoxy Adhesive
One component epoxy adhesive offers several advantages stemming from its working mechanism:
- Simplified Application:The single-package nature of OCEA eliminates the need for manual mixing, saving time and reducing errors in the blending process. This simplification streamlines the application and ensures consistent results.
- Solid and Durable Bonds:OCEA forms bonds with exceptional strength and durability through the chemical reaction and cross-linking process. It provides excellent adhesion to various substrates, including metals, plastics, and composites.
- Versatile Performance:OCEA offers versatility in bonding various materials and can withstand challenging conditions such as temperature variations, chemicals, and mechanical stresses.
- Efficient Curing:OCEA’s process allows for fast assembly or production turnaround times. Depending on the specific adhesive formulation and application requirements, you can cure it at room temperature or accelerate the curing process with heat.
Types of One Component Epoxy Adhesive
Various industries widely use one component epoxy adhesives for bonding and sealing applications. These adhesives offer excellent adhesion, durability, and resistance to chemicals and heat. They earn the name “one component” because they do not need the addition of a curing agent or mixing before application. Here are some common types of one component epoxy adhesives:
Heat Cure Epoxy Adhesives
- These adhesives require heat to initiate the curing process.
- They offer high strength and bond integrity once fully cured.
- Industries commonly use heat-cure epoxy adhesives in applications that demand high durability and resistance to extreme temperatures.
UV Cure Epoxy Adhesives
- These adhesives cure upon exposure to ultraviolet (UV) light.
- They offer rapid curing times, making them suitable for high-speed production lines.
- Electronics, optics, and medical device assembly often utilize UV-cure epoxy adhesives.
Moisture Cure Epoxy Adhesives
- These adhesives cure in the presence of moisture in the air or on the substrate surface.
- They are convenient because they do not require additional curing agents or heat.
- Construction, automotive, and general-purpose bonding applications commonly employ moisture-cure epoxy adhesives.
Dual Cure Epoxy Adhesives
- These adhesives combine two different curing mechanisms: heat and UV or moisture and heat.
- Dual-cure epoxy adhesives provide versatility and find applications in scenarios where multiple curing conditions exist.
- They provide enhanced bond strength and flexibility.
Anaerobic Epoxy Adhesives
- Anaerobic epoxy adhesives cure in the absence of air or oxygen.
- Various industries frequently use these items for thread locking, sealing, and gasketing.
- Anaerobic epoxy adhesives are ideal for securing fasteners and preventing loosening due to vibrations or thermal expansion.
Electrically Conductive Epoxy Adhesives
- These adhesives enable electrical conductivity between components through their design.
- They find common usage in electronics and electrical applications, such as bonding electronic circuits or grounding devices.
- Electrically conductive epoxy adhesives ensure reliable electrical connections and help dissipate heat.
Thermal Conductive Epoxy Adhesives
- Manufacturers formulate these adhesives to have high thermal conductivity.
- They bond heat-generating components to heat sinks or other cooling devices.
- Thermal conductive epoxy adhesives help transfer heat efficiently, preventing overheating and improving component performance.
Advantages of One Component Epoxy Adhesive
Various industries widely use one component epoxy adhesives due to their numerous advantages. These adhesives offer a range of benefits that make them a preferred choice for bonding and sealing applications. Here are some key advantages of one component epoxy adhesive:
Convenience and Ease of Use
- One component epoxy adhesives are ready to use straight from the container, eliminating the need for measuring, mixing, or adding additional components.
- They simplify the adhesive application and save time, especially in high-speed production environments.
Excellent Adhesion
- One component of epoxy adhesives provides exceptional bonding strength and adhesion to various substrates, including metals, plastics, ceramics, and composites.
- They create strong, durable, long-lasting bonds, ensuring reliable performance in demanding applications.
Chemical and Environmental Resistance
- These adhesives offer excellent resistance to chemicals, solvents, oils, and fuels, making them suitable for applications exposed to harsh environments.
- They can withstand exposure to moisture, humidity, and extreme temperatures, maintaining their adhesive properties and bond integrity.
Versatility
- One component epoxy adhesives are available in various formulations, allowing versatility in selecting the suitable adhesive for specific application requirements.
- They can customize one component epoxy adhesives to meet different bond strengths, curing time, and flexibility needs, making them suitable for various industries and applications.
Gap Filling and Flexibility
- One component of epoxy adhesives can fill gaps and irregular bond surfaces, ensuring a strong and uniform bond line even in challenging bonding scenarios.
- They offer flexibility and accommodate slight movements or vibrations, reducing the risk of bond failure due to thermal expansion or mechanical stress.
Electrical and Thermal Properties
- Some one component epoxy adhesives possess electrical conductivity by design, making them ideal for electronic applications that require reliable electrical connections or grounding.
- Thermal conductive epoxy adhesives facilitate efficient heat transfer, making them suitable for bonding heat-generating components to heat sinks or cooling devices.
Long Shelf Life
- One component epoxy adhesives typically have a long shelf life, allowing for extended storage without compromising their adhesive properties.
- These tools suit small and large-scale projects, making them convenient for any application.
Disadvantages of One Component Epoxy Adhesive
One component epoxy adhesive, in particular, offers convenience and ease of use as it doesn’t require mixing with a catalyst or hardener. However, despite its advantages, there are some notable disadvantages associated with this type of adhesive. This article will explore the limitations of one component epoxy adhesive to help you make informed decisions when choosing the suitable adhesive for your applications.
Limited Shelf Life
- One component of epoxy adhesives has a finite shelf life once opened. The exposure to air causes them to cure over time, reducing their effectiveness gradually.
- Users must carefully monitor and manage inventory to avoid using expired adhesives, leading to wastage and increased costs.
Limited Cure Speed
- One component epoxy adhesives generally have a longer cure time than two-component systems.
- This slower curing process can delay production schedules and limit the overall productivity of manufacturing processes.
Limited Heat Resistance
- One component epoxy adhesives often have lower heat resistance than their two-component counterparts.
- They may degrade or lose their bond strength when exposed to high temperatures, which can be a disadvantage in applications where thermal stability is crucial.
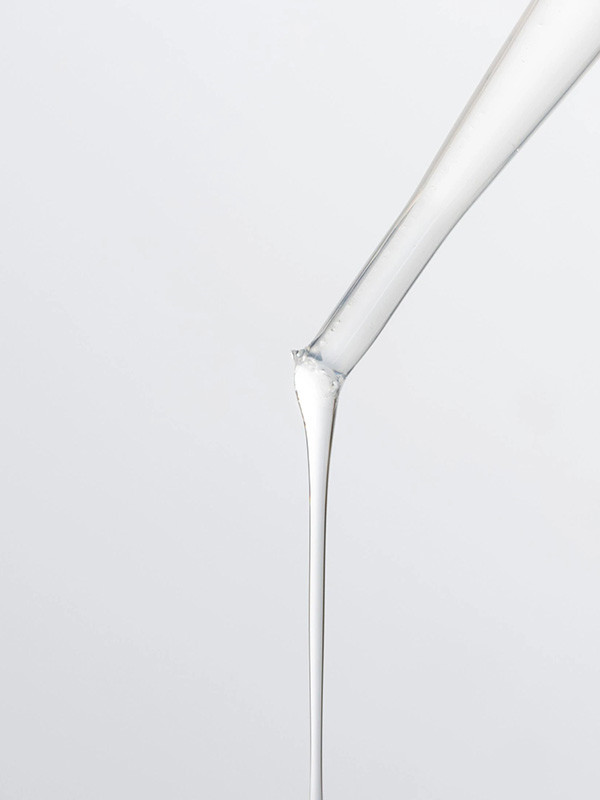
Limited Bond Strength
- While one component epoxy adhesives offer good adhesion, their bond strength may be lower than that of two-component systems.
- This limitation can restrict their use in applications that require superior strength and load-bearing capabilities.
Limited Application Flexibility
- One component of epoxy adhesives may not be suitable for bonding specific substrates or materials.
- They might exhibit poor adhesion on certain plastics, metals, or surfaces with low surface energy, limiting their application range.
Lack of Mixing Control
- Unlike two-component epoxy adhesives, which allow precise control over the mixing ratio, one component adhesives lack this advantage.
- This absence of control can lead to consistency in curing and bonding performance, affecting the overall quality of the adhesive joint.
Properties of One Component Epoxy Adhesive
One type of epoxy adhesive that is particularly popular is the one-component epoxy adhesive. This adhesive offers several advantages over other types, making it a preferred choice for many applications. Here we will explore the properties of one-component epoxy adhesive and uncover the reasons behind its wide usage.
- Single-component convenience:One of the key advantages of one-component epoxy adhesive is that it comes in a ready-to-use form. Unlike two-component bonds that require mixing before application, one-component epoxy adhesive eliminates the need for mixing, making it highly convenient. It saves time and effort, allowing for efficient application in various projects.
- Excellent bonding strength:One-component epoxy adhesive offers exceptional bonding strength, making it suitable for demanding applications. It forms a strong bond between various materials, including metals, ceramics, composites, and plastics. This adhesive can withstand heavy loads, vibrations, and impact, ensuring a durable and long-lasting bond.
- Versatility:One-component epoxy adhesive exhibits versatility in its application. It can bond, seal, pot, encapsulate, and even be a coating material. This adhesive can adapt to different requirements, whether joining two surfaces, closing gaps, or encapsulating electronic components, making it highly versatile.
- Heat and chemical resistance:One-component epoxy adhesive possesses excellent heat and chemical resistance properties. It can withstand high temperatures, making it suitable for applications with elevated temperatures. Additionally, it resists a wide range of chemicals, including solvents, fuels, and acids, ensuring the bond remains intact in harsh environments.
- Fast curing time: One-component epoxy adhesive cures quickly, allowing for more rapid production and assembly processes. Once applied, it undergoes a chemical reaction that results in a strong bond. Depending on the specific adhesive formulation, the curing time can be further accelerated by heat or ultraviolet light.
- Good electrical insulation:One-component epoxy adhesive provides excellent electrical insulation properties. It effectively insulates against the electrical current, preventing leakage and short circuits. This feature makes it ideal for electronic applications, such as bonding or encapsulating delicate components.
- Resistance to moisture and environmental factors:One-component epoxy adhesive demonstrates resistance to water, humidity, and other environmental factors. It maintains its bond integrity even in humid or wet conditions, making it suitable for indoor and outdoor applications.
- Long shelf life:One-component epoxy adhesive typically has a long shelf life, allowing for extended storage without losing its adhesive properties. Storing unused adhesive for later use without compromising performance makes it cost-effective.
Curing Time of One Component Epoxy Adhesive
One-component epoxy adhesive is a versatile and widely used bonding material in various industries. When working with this adhesive, one crucial aspect is its curing time. Curing refers to the adhesive transitioning from a liquid or semi-liquid state to a solid state, forming a strong and durable bond. Here we will delve into the concept of curing time for one-component epoxy adhesive, its factors, and its significance in different applications.
Understanding Curing Time
Curing time refers to the duration required for the one-component epoxy adhesive to heal and achieve optimal bonding strength fully. The curing time can vary depending on several factors, including the adhesive formulation, environmental conditions, and the specific application requirements. Following the manufacturer’s guidelines and recommendations is crucial to ensure proper curing and maximize the adhesive’s performance.
Factors Affecting Curing Time
Several factors can influence the curing time of one-component epoxy adhesive:
- Adhesive Formulation: The specific formulation of the epoxy adhesive, including its chemical composition, viscosity, and curing agents, can impact the curing time. Different formulations are designed for particular applications and may have varying curing characteristics.
- Temperature:Temperature plays a significant role in the curing process. Generally, higher temperatures accelerate the curing time, while lower temperatures can slow it down. It is essential to consider the recommended temperature range for curing the adhesive to achieve optimal results.
- Humidity:Humidity levels can affect the curing process of epoxy adhesives. Moisture can influence the curing of some adhesives that undergo a chemical reaction. High humidity can extend the curing time, while low humidity may speed it up. It is essential to control the humidity conditions during the curing process, especially in sensitive applications.
Significance in Applications
The curing time of one-component epoxy adhesive holds great importance in various applications:
- Production Efficiency:A shorter curing time enables faster production cycles, increasing efficiency and reducing overall production time. It’s crucial to prioritize this when dealing with industries requiring massive manufacturing or projects with tight deadlines.
- Assembly and Handling:Depending on the curing time, holding or clamping the bonded components in place during the curing process may be necessary. Understanding the expected curing time helps plan the assembly and handling procedures accordingly.
- Serviceability:Curing time also affects the serviceability of the bonded product. In some cases, the adhesive may reach sufficient initial strength within a relatively short time, allowing for subsequent processing or usage. However, achieving maximum bond strength might take longer, and it is essential to consider this aspect in applications where load-bearing or high-stress conditions are involved.
How to Apply One Component Epoxy Adhesive
One component of epoxy adhesive is a popular choice for bonding and sealing applications due to its excellent strength, durability, and versatility. Whether working on a DIY project or a professional job, correctly applying one epoxy adhesive component is crucial to ensure a successful bond. This blog post will guide you through using this adhesive effectively.
Preparation
- Begin by gathering all the necessary tools and materials, including the one component epoxy adhesive, a clean and dry surface to bond, and any required applicators or brushes.
- Ensure the surface you plan to bond is free from dust, grease, oil, or other contaminants. Clean it thoroughly using a suitable cleaning agent.
- Wearing gloves and protective eyewear during the application process is essential to ensure your safety and avoid any contact with the adhesive.
Application steps
- Open the adhesive container and read the manufacturer’s instructions and safety guidelines carefully. Follow them precisely to ensure the best results and safe adhesive handling.
- If the adhesive requires mixing or stirring, do so according to the instructions provided. You may need to shake or stir some one component epoxy adhesives to ensure uniformity.
- Apply the adhesive directly onto the surface you wish to bond. Use a brush, applicator, or nozzle depending on the consistency and requirements of the adhesive.
- Apply an even and consistent adhesive layer covering the entire bonding area. Avoid excessive adhesive, which may result in weaker bonds or overflow during curing.
- You can use clamps or other mechanical support to hold the bonded parts together while the adhesive cures. Follow the manufacturer’s recommendations regarding clamping pressure and curing time.
- Once the adhesive is applied, allow it to cure according to the instructions. The curing time can vary depending on the type of adhesive and environmental conditions, and it is essential to provide adequate curing time for a solid and durable bond.
Tips for best results
- Store the adhesive properly in a cool, dry place, following the manufacturer’s instructions. Exposure to heat or moisture can degrade the adhesive’s performance.
- If you need to remove any excess adhesive, do so immediately after applying an appropriate solvent or cleaner recommended by the manufacturer.
- Avoid touching the adhesive or the bonded area until fully cured to prevent any disturbance in the bonding process.
- Ensure proper ventilation in the working area to prevent the buildup of potentially harmful fumes.
- If you encounter difficulties during the application process or have specific questions, consult the adhesive manufacturer’s technical support or seek professional advice.
Precautions to Take While Using One Component Epoxy Adhesive
One component epoxy adhesive is a powerful and versatile bonding solution commonly used in various applications. While it offers numerous benefits, cautiously handling and utilizing this adhesive is crucial to ensure safety and achieve the desired results. Here we will discuss essential precautions to take when using one component of epoxy adhesive.
Read and follow the manufacturer’s instructions
- Carefully read the instructions and safety guidelines provided by the manufacturer before using the adhesive.
- Familiarize yourself with the recommended application techniques, curing time, and specific precautions.
Use proper personal protective equipment (PPE)
- Wear protective gloves, safety glasses, and, if necessary, a respiratory mask to protect yourself from direct contact with the adhesive and potential fumes.
- Make sure you use personal protective equipment (PPE) that suits your specific adhesive and provides adequate protection.
Work in a well-ventilated area
- Provide adequate ventilation in the working area to minimize the buildup of fumes.
- If working indoors, use fans or open windows to promote air circulation and maintain a safe environment.
Prepare the bonding surfaces properly
- Ensure you clean, dry, and remove any dust, grease, or other contaminants from the surfaces you intend to bond.
- Use appropriate cleaning agents recommended by the adhesive manufacturer to prepare the surfaces.
Apply the adhesive in a controlled manner
- Apply the adhesive precisely using brushes, applicators, or nozzles as the manufacturer directs.
- Avoid excessive adhesive, leading to weak bonds or overflow during curing.
Use proper clamping techniques
- If necessary, use clamps or other mechanical supports to hold the bonded parts together during curing.
- Follow the adhesive manufacturer’s recommendations regarding clamping pressure and duration.
Allow sufficient curing time
- Respect the recommended curing time provided by the manufacturer. Premature handling or stress on the bonded parts can compromise the strength of the bond.
- As specified in the instructions, provide adequate curing conditions, such as temperature and humidity.
Store and dispose of the adhesive safely
- Store the adhesive in a cool, dry place, following the manufacturer’s instructions.
- Dispose of unused adhesive or empty containers according to local regulations and guidelines.
Seek professional advice if needed
- If you encounter difficulties or have specific questions regarding the application or handling of the adhesive, consult the adhesive manufacturer’s technical support or seek professional advice.
Surface Preparation for One Component Epoxy Adhesive
Surface preparation is a critical step in achieving a strong and durable bond when using one component of epoxy adhesive. Properly preparing the surfaces to be bonded ensures optimal adhesion and enhances the overall performance of the adhesive. This blog post will discuss essential steps and techniques for surface preparation when working with one component epoxy adhesive.
Clean the surfaces thoroughly
- Begin by cleaning the surfaces to be bonded using a suitable cleaning agent or solvent recommended by the adhesive manufacturer.
- Remove any dust, dirt, oil, grease, or other contaminants that may hinder the adhesive’s ability to bond effectively.
- Use lint-free cloths, brushes, or compressed air to ensure a clean, debris-free surface.
Remove old adhesives or coatings
- If the surfaces have existing adhesives, coatings, or paints, removing them before applying the one component epoxy adhesive is essential.
- Use mechanical methods such as sanding, scraping, or grinding to remove the old adhesive layers.
- You can also use chemical strippers or solvents, but check their compatibility with the substrate and follow proper safety precautions.
Ensure dryness
- Ensure that the surfaces are dehydrated before applying the adhesive. Moisture can negatively affect the bonding process and compromise the adhesive’s performance.
- Allow sufficient drying time after cleaning or any water-based cleaning methods.
- In humid environments, use drying methods such as air blowers or heat guns to eliminate moisture before applying the adhesive.
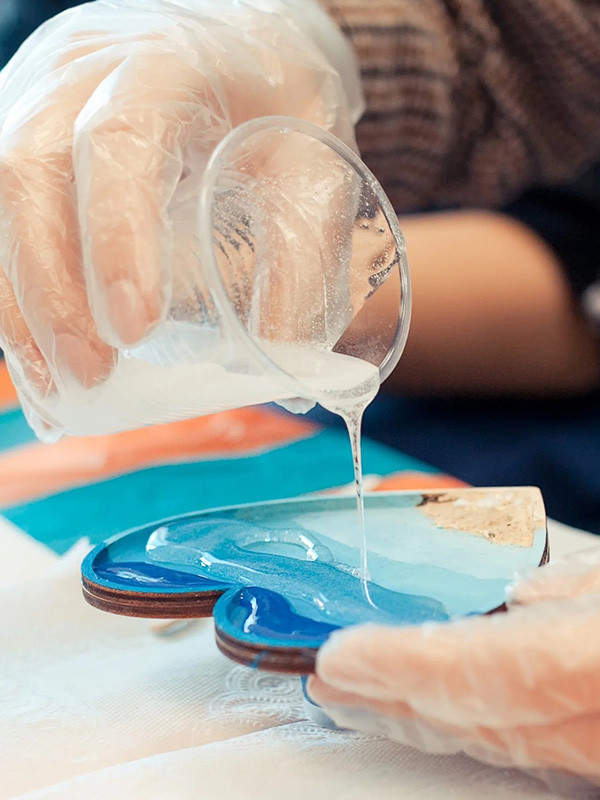
Roughen the surface
- In some cases, roughening the surface can improve the bond strength by increasing the surface area for adhesion.
- Use sandpaper, abrasive pads, or mechanical methods to create a roughened surface texture.
- Be careful not to damage the substrate or create deep gouges that may weaken the overall structure.
Consider surface priming
- Depending on the nature of the substrate and the adhesive you are using, you may need to prime the surface.
- Surface primers enhance adhesion, promote better adhesive wetting, and improve overall bonding performance.
- Consult the adhesive manufacturer’s guidelines to determine if they recommend surface priming, and follow their instructions accordingly.
Evaluate compatibility
- It is crucial to ensure compatibility between the adhesive and the substrate material.
- Some substrates may require unique surface treatments or primers to enhance adhesion and compatibility with the adhesive.
- Refer to the adhesive manufacturer’s recommendations and conduct compatibility tests if necessary.
Follow adhesive-specific instructions
- Always refer to the manufacturer’s instructions and guidelines for surface preparation specific to the one component epoxy adhesive you use.
- Different adhesives may have unique requirements and considerations regarding surface preparation techniques, curing conditions, and compatibility.
Applications of One Component Epoxy Adhesive in Different Industries
One component epoxy adhesive is a versatile and high-performance adhesive that finds applications in various industries. Its unique formulation and characteristics make it suitable for multiple bonding, sealing, and encapsulating applications. Here we will explore the diverse applications of one component of epoxy adhesive in different industries.
Automotive Industry
- Bonding of various components:One component, epoxy adhesive, is extensively used in the automotive industry for bonding metal, plastic, and composite parts. It provides excellent adhesion strength, durability, and resistance to vibration, heat, and chemicals.
- Structural bonding:It is used for the structural bonding of body panels, roof systems, and windshield bonding, ensuring enhanced strength and safety.
- Sealing and encapsulation:One component, epoxy adhesive, is used for sealing and encapsulating electrical connectors, sensors, and electronic components, protecting them from moisture, corrosion, and harsh environmental conditions.
Electronics Industry
- Component bonding:One component epoxy adhesive is commonly used for bonding and securing electronic components onto circuit boards. It offers excellent electrical insulation, thermal conductivity, and resistance to temperature cycling.
- Potting and encapsulation:It is used for potting and encapsulating electronic assemblies, protecting against moisture, dust, and mechanical stress.
- Display and touch panel assembly:One component of epoxy adhesive is utilized for bonding displays and touch panels in electronic devices, ensuring reliable adhesion, optical clarity, and durability.
Aerospace Industry
- Composite bonding:One component, epoxy adhesive, plays a crucial role in adhesion and repairing composite structures in the aerospace industry. It offers high strength, lightweight properties, and resistance to extreme temperatures.
- Panel bonding:It is used for bonding interior and exterior panels in aircraft, providing structural integrity and reducing weight.
- Metal-to-metal bonding:One component epoxy adhesive provides superior strength and durability when bonding metal components such as brackets, fasteners, and inserts.
Construction Industry
- Concrete bonding and repair:One component, epoxy adhesive, is utilized for bonding concrete elements, repairing cracks and spalls, and securing anchors and dowels. It provides excellent adhesion to concrete, high chemical resistance, and durability.
- Flooring applications:It is used for bonding floor tiles, resilient flooring, and coatings, ensuring long-lasting adhesion and resistance to heavy traffic and chemicals.
- Structural glazing:Manufacturers employ one component of epoxy adhesive in structural glazing applications to bond glass panels to metal or concrete frames, ensuring high strength, weather resistance, and aesthetics.
Medical and Dental Industry
- Device assembly:One component epoxy adhesive is used for bonding and assembling medical devices, such as catheters, sensors, and prosthetics, offering biocompatibility and sterilization resistance.
- Dental restoration:It is utilized for bonding dental restorations, such as crowns, bridges, and veneers, ensuring strong adhesion, aesthetics, and durability.
- Wound closure:One component epoxy adhesive is used as an alternative to traditional sutures for wound closure, providing rapid, secure, and painless closure.
Automotive Industry Applications of One Component Epoxy Adhesive
The automotive industry constantly seeks innovative solutions to enhance performance, safety, and longevity. One solution that has gained significant traction in recent years is using one component of epoxy adhesive. This versatile adhesive offers several benefits and finds numerous applications across the automotive sector. Here we will explore how the automotive industry utilizes one component of epoxy adhesive in various ways.
Bonding and Sealing Components
One component epoxy adhesive is a reliable bonding agent for a wide range of automotive components. Its ability to adhere to different materials, such as metal, plastic, and composites, makes it an ideal choice for joining various parts. It ensures structural integrity, reduces vibration and noise, and enhances overall durability. This adhesive also functions as an effective sealing agent, preventing the ingress of moisture, dust, and other contaminants.
Vehicle Assembly
During the assembly process, automotive manufacturers employ one component of an epoxy adhesive for various applications. Some key areas include:
- Body Structure:The adhesive is used for bonding roof panels, side panels, and structural reinforcements, improving overall vehicle rigidity and crash resistance.
- Interior Assembly: It facilitates the bonding of interior components like instrument panels, consoles, and door panels, enhancing their strength and reducing rattling or squeaking noises.
- Glass Bonding:One component, epoxy adhesive, plays a crucial role in bonding windshields, rear windows, and sunroofs, providing structural integrity and preventing water leakage.
Electrical Component Encapsulation
Electrical components in vehicles require protection against moisture, heat, and vibrations. One element of epoxy adhesive provides excellent electrical insulation and acts as a protective encapsulant. It ensures the longevity and reliability of sensitive electronic systems like sensors, control units, and wiring harnesses.
Thermal Management
Modern vehicles utilize advanced powertrain technologies, which generate significant heat. Effective thermal management is crucial to prevent overheating and ensure optimal performance. One component epoxy adhesive with high thermal conductivity properties is employed to bond heat sinks, electronic modules, and powertrain components. It facilitates efficient heat dissipation, extending the lifespan of critical vehicle systems.
Safety Features
The automotive industry places a high emphasis on safety, and one component of epoxy adhesive plays a role in enhancing various safety features:
- Crash Sensors: Adhesive bonding secures crash sensors to the vehicle’s structure, ensuring accurate detection and response during an impact.
- Airbag Systems: Airbag initiators use an epoxy adhesive to bond and ensure proper deployment during a collision.
- Anti-lock Braking Systems (ABS): One component of epoxy adhesive helps secure ABS sensors and prevent their misalignment, ensuring accurate wheel speed detection.
Aerospace Industry Applications of One Component Epoxy Adhesive
The demand for reliable and high-performance adhesive solutions is crucial in the dynamic world of aerospace engineering. One component epoxy adhesive has emerged as a versatile and efficient option for various applications within the aerospace industry. This blog post explores the significant applications of one component epoxy adhesive and highlights its benefits in this demanding field.
Bonding and Assembly
- One component, epoxy adhesive, plays a vital role in bonding and assembling aerospace components, including metal, composite, and plastic materials.
- It provides exceptional adhesion strength, enabling secure and durable bonds that withstand extreme temperature fluctuations, vibrations, and other challenging conditions.
- The adhesive’s ability to fill gaps and voids helps achieve uniform stress distribution, enhancing the overall structural integrity of the assembled parts.
Composite Manufacturing
- Aerospace structures extensively utilize composite materials due to their high strength-to-weight ratio. One component epoxy adhesive is an ideal choice for hybrid manufacturing processes.
- It facilitates bonding composite panels, honeycomb structures, and laminates, ensuring a robust and reliable bond.
- The adhesive’s low shrinkage and excellent resistance to moisture and chemicals enhance the longevity and durability of composite structures.
Surface Protection and Coating
- Aerospace components face rigorous challenges due to extreme environmental conditions, including exposure to UV radiation, temperature variations, and corrosive agents. One element of epoxy adhesive provides an effective protective coating.
- It forms a barrier against moisture, chemicals, and oxidation, safeguarding critical components from degradation and maintaining their performance over time.
- The adhesive’s high electrical insulation properties also protect sensitive electronic systems in aerospace applications.
Repair and Maintenance
- One component epoxy adhesive offers a reliable solution for repair and maintenance tasks within the aerospace industry.
- It can repair cracks, delaminations, and other damage in composite structures, providing structural reinforcement and restoring the integrity of the component.
- The adhesive’s fast curing properties allow for efficient repairs, minimizing downtime and increasing the overall operational efficiency of aerospace systems.
Benefits of One Component Epoxy Adhesive in Aerospace Applications
- High adhesion strength:Provides secure and durable bonds between various materials.
- Thermal stability: Withstands extreme temperatures experienced in aerospace environments.
- Chemical resistance: Protects against moisture, chemicals, and corrosive agents.
- Excellent gap-filling properties:Ensures uniform stress distribution and enhances structural integrity.
- Quick curing: Enables fast repairs and reduces downtime for maintenance tasks.
- Electrical insulation: The application of one component epoxy adhesive safeguards electronic systems from electrical interference and potential damage.
Construction Industry Applications of One Component Epoxy Adhesive
The construction industry constantly seeks innovative solutions to enhance efficiency, durability, and safety in various applications. One such game-changing advancement is the utilization of one epoxy adhesive component, which is transforming the execution of construction projects with its unique properties and versatility. Here we will explore the various applications of one component of epoxy adhesive and how it is revolutionizing the construction industry.
Bonding and Structural Strength
- One component epoxy adhesive offers exceptional bonding strength, enabling it to securely bond various materials such as concrete, wood, metal, and composites.
- It enhances structural integrity by creating a solid bond between components, improving load-bearing capabilities and overall stability.
- It provides a durable and long-lasting bond, even under extreme conditions, making it ideal for critical structural applications.
Waterproofing and Sealing
- One component epoxy adhesive possesses excellent water resistance properties, making it a practical choice for waterproofing applications.
- It creates a reliable seal, preventing water penetration, moisture, and other environmental elements, safeguarding the structure against corrosion and degradation.
- It can be used for sealing joints, cracks, and gaps in various construction materials, ensuring a watertight and airtight barrier.
Flooring and Tiling
- One component, epoxy adhesive, is widely used in flooring and tiling applications due to its superior bonding strength and chemical resistance.
- It securely bonds tiles, stone, and other flooring materials to different substrates, ensuring long-lasting adhesion and preventing loosening or cracking.
- Its chemical resistance makes it suitable for areas exposed to chemicals, such as laboratories, commercial kitchens, and industrial facilities.
Concrete Repair and Restoration
- One component, epoxy adhesive, plays a vital role in concrete repair and restoration projects.
- It effectively fills cracks and spalls in concrete structures, restoring their integrity and preventing further deterioration.
- It provides a strong bond between existing concrete surfaces and new concrete overlays, ensuring seamless repair and enhancing structural strength.
Anchoring and Doweling
- One component, epoxy adhesive, is widely used for anchoring and doweling applications in construction.
- It securely anchors bolts, rebar, and other fixtures into concrete or masonry, providing reliable stability and load distribution.
- Its high bond strength and resistance to vibration and dynamic loads make it suitable for critical anchoring applications, such as bridges, high-rise buildings, and infrastructure projects.
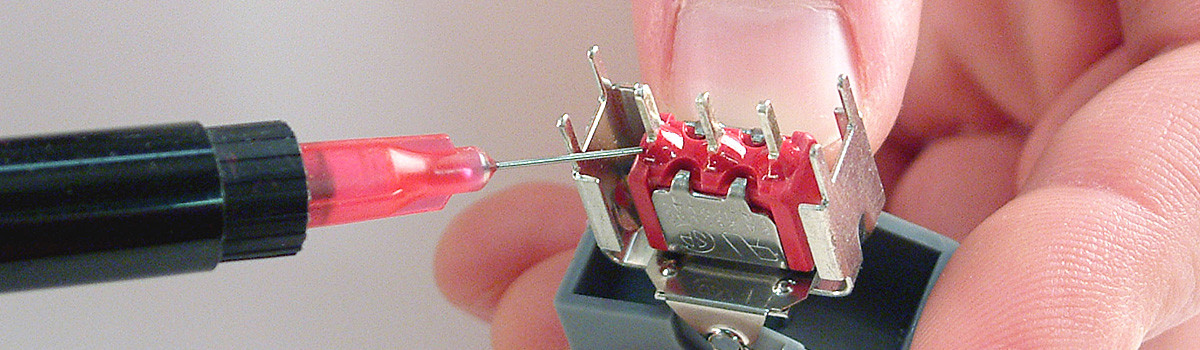
Electronics Industry Applications of One Component Epoxy Adhesive
The electronics industry is constantly evolving, with new technological advancements emerging rapidly. One key element that enables these innovations is reliable and high-performance adhesives. Among them, one component of epoxy adhesive stands out for its exceptional properties and versatility. Here we will explore the various applications of one component epoxy adhesive in the electronics industry.
Circuit Board Assembly
- One component, epoxy adhesive, is widely used in circuit board assembly.
- It provides excellent bonding strength and electrical insulation properties.
- It ensures the secure attachment of components to the board, preventing mechanical stress or movement.
- Its heat resistance and stability suit high-temperature applications, such as automotive electronics and industrial equipment.
Potting and Encapsulation
- People commonly employ one-component epoxy adhesive for potting and encapsulating electronic components.
- It provides a protective barrier against moisture, chemicals, and physical damage.
- This adhesive offers excellent adhesion to various substrates, including plastics, metals, and ceramics.
- It ensures long-term reliability and enhances the overall lifespan of electronic devices, even in harsh environments.
Bonding and Sealing
- One component epoxy adhesive is an ideal choice for bonding and sealing applications in electronics.
- It forms strong bonds between different materials, such as metal to metal, metal to plastic, or plastic to plastic.
- It is high strength and resistance to vibration make it suitable for bonding components in electronic assemblies.
- The adhesive’s ability to seal against moisture, dust, and other contaminants ensures the longevity and reliability of electronic devices.
Underfill Applications
- One component, epoxy adhesive, is extensively used for underfilling applications in flip-chip technology.
- It fills the gap between the chip and the substrate, enhancing mechanical stability and preventing solder joint failures.
- The adhesive’s low coefficient of thermal expansion (CTE) matches the CTE of the chip and substrate, reducing stress during thermal cycling.
- It improves the overall performance of flip-chip devices, especially in applications like microprocessors, memory modules, and integrated circuits.
Thermal Management
- One component of epoxy adhesive is a valuable asset in thermal management solutions for electronic devices.
- It efficiently transfers heat from sensitive components, such as processors or power modules.
- The adhesive’s high thermal conductivity ensures effective heat dissipation, preventing overheating and maintaining optimal device performance.
- You can apply it as a thermal interface material (TIM) between heat-generating components and heat sinks or spreaders.
Marine Industry Applications of One Component Epoxy Adhesive
In the marine industry, this adhesive plays a crucial role in ensuring numerous applications’ integrity, durability, and performance. From shipbuilding and repairs to underwater structures and equipment, the marine industry extensively utilizes one component epoxy adhesive for its exceptional bonding capabilities and resistance to harsh marine environments.
In this article, we will explore the diverse applications of one component epoxy adhesive in the marine industry, highlighting its benefits and advantages.
Shipbuilding and Repairs
- Bonding of structural components:One component epoxy adhesive provides excellent bonding strength for joining various structural elements in shipbuilding, such as hull panels, decks, bulkheads, and reinforcements.
- Patching and sealing:It repairs cracks, holes, and damage in the ship’s structure, ensuring water tightness and structural integrity.
- Deck and flooring applications:One component, epoxy adhesive, is suitable for securing deck coverings, non-slip flooring, and other interior/exterior marine flooring materials.
Bonding and Sealing Underwater Structures
- Subsea pipelines and cables:The adhesive’s underwater curability allows for reliable bonding and sealing of subsea pipelines and lines, ensuring long-term performance and protection against water ingress.
- Offshore platforms and structures:One component, epoxy adhesive, is used for bonding underwater structures, such as offshore platforms, underwater supports, and equipment, providing excellent corrosion resistance and durability.
Marine Electronics
- Potting and encapsulation:It is commonly employed for potting and encapsulating electronic components, protecting them from moisture, vibrations, and mechanical stress.
- Thermal interface material (TIM): One component of epoxy adhesive can be applied as a thermal interface between heat-generating components and heat sinks or spreaders, improving heat dissipation and overall performance.
Marine Equipment and Fittings
- Bonding and sealing of fittings:The adhesive is used for bonding and sealing various marine equipment and fittings, including windows, hatches, doors, and vents, ensuring water-tightness and resistance to extreme weather conditions.
- Attachment of hardware:One component epoxy adhesive provides reliable bonding strength for attaching hardware components, such as handrails, brackets, and fixtures.
Benefits of One Component Epoxy Adhesive in the Marine Industry:
- One component of epoxy adhesive demonstrates excellent adhesion to various substrates, including metals, composites, and plastics.
- High strength and durability, ensuring long-lasting bonds in harsh marine environments.
- One component of epoxy adhesive exhibits resistance to water, salt water, chemicals, and UV exposure, providing enhanced durability and protection.
- One component epoxy adhesive possesses exceptional thermal and electrical insulation properties, ensuring reliable performance in diverse marine applications.
- One component of epoxy adhesive can cure underwater, facilitating repairs and enabling applications in submerged conditions.
- Reduced labor and application time due to its one-component nature eliminates the need for mixing or additional curing agents.
Medical Industry Applications of One Component Epoxy Adhesive
Various industries, including the medical sector, widely use one component epoxy adhesives. These adhesives offer several advantages, such as fast curing, high strength, and excellent chemical resistance, making them suitable for various medical applications. From device assembly to wound closure, one component of epoxy adhesives plays a crucial role in ensuring the safety and efficacy of medical products. Let’s explore some of the key medical industry applications of one component epoxy adhesive:
Medical Device Assembly
- Medical professionals commonly use one component epoxy adhesives for bonding and assembling medical devices. These adhesives provide high bond strength and durability, ensuring the devices’ long-term performance and reliability.
- They are suitable for bonding various materials used in medical devices, including metals, plastics, ceramics, and glass. This versatility makes them ideal for applications such as attaching components, encapsulating electronics, and sealing joints.
Surgical Instrument Bonding
- One component, epoxy adhesives, finds application in the bonding and repair of surgical instruments. These adhesives can securely bond different materials used in surgical instruments, such as stainless steel, titanium, and plastics.
- They offer excellent resistance to sterilization methods, including steam autoclaving, gamma irradiation, and ethylene oxide (EtO) sterilization. By following this process, you can be sure that the adhesive connections will remain sturdy and dependable throughout the entire life of the instrument.
Dental Applications
- Dentists utilize one component epoxy adhesives in various dental applications, including bonding crowns, bridges, and orthodontic appliances. These adhesives provide intense and long-lasting bonds between dental restorations and natural teeth.
- They offer excellent resistance to oral fluids, temperature changes, and chemical exposure commonly encountered in the oral cavity. We can guarantee patient satisfaction by enhancing the longevity and reliability of dental restorations.
Wound Closure
- One component, epoxy adhesives, is used as wound closure adhesives in specific medical procedures. These adhesives provide a non-invasive alternative to traditional sutures or staples.
- They offer quick and easy application, reducing procedure time and patient discomfort. Additionally, they provide a flexible and waterproof bond, promoting faster wound healing and reducing the risk of infection.
Medical Electronics
- One component of epoxy adhesives is crucial in assembling and encapsulating electronic medical devices. These adhesives provide excellent electrical insulation properties, protecting sensitive electronics from moisture, chemicals, and mechanical stress.
- They ensure the reliability and longevity of electronic medical devices, such as pacemakers, defibrillators, and monitoring equipment. The adhesives also offer high thermal conductivity, allowing efficient heat dissipation, essential for devices that generate heat.
Consumer Goods Industry Applications of One Component Epoxy Adhesive
One component of epoxy adhesives finds widespread application in the consumer goods industry. These adhesives offer several advantages, such as solid bonding, durability, and versatility, making them suitable for various consumer product applications. From household appliances to electronics and automotive accessories, one component of epoxy adhesives plays a crucial role in ensuring the performance and reliability of consumer goods. Let’s explore some of the key applications of one component epoxy adhesive in the consumer goods industry:
Appliance Assembly
- Manufacturers commonly use one component epoxy adhesives to assemble household appliances such as refrigerators, washing machines, and dishwashers. They provide strong and durable bonds between different materials used in appliance construction, including metal, plastic, and glass.
- These adhesives offer resistance to temperature fluctuations, moisture, and chemical exposure, ensuring the longevity and reliability of appliance components. They also provide vibration and impact resistance, contributing to the overall durability of appliances.
Electronics and Electrical Components
- One component epoxy adhesives find extensive use in the electronics and electrical industry for component bonding, encapsulation, and sealing applications. They provide excellent adhesion to various substrates, including printed circuit boards (PCBs), metal, and plastics.
- These adhesives offer high electrical insulation properties, ensuring electronic components’ reliable performance and protection from moisture, dust, and other environmental factors. They also exhibit thermal conductivity, facilitating efficient heat dissipation in electronic devices.
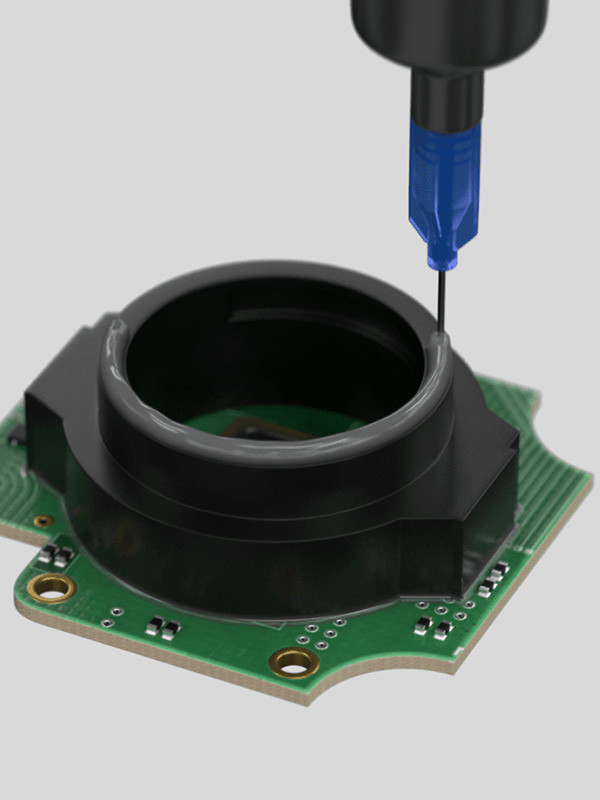
Automotive Accessories and Trim
- One component epoxy adhesives are utilized in the automotive industry for bonding and attaching various accessories and trim components. They provide strong and durable bonds between metal, plastic, and composite materials in automotive interiors and exteriors.
- These adhesives offer resistance to temperature extremes, moisture, and automotive fluids, ensuring the longevity and performance of attached components. They also contribute to noise and vibration damping, enhancing the overall comfort and quality of the vehicle.
Sporting Goods and Outdoor Equipment
- One component, epoxy adhesives, finds application in the manufacturing and repair of sporting goods and outdoor equipment, including bicycles, skis, and camping gear. They provide strong and durable bonds between materials such as metal, carbon fiber, and composites.
- These adhesives offer resistance to impact, weathering, and exposure to outdoor elements, ensuring the reliability and durability of sporting goods and equipment. They also provide flexibility and shock absorption, contributing to the overall performance and safety of the products.
Furniture and Woodworking
- The furniture and woodworking industry uses one component of epoxy adhesives for bonding and assembling wooden parts. They provide strong and durable bonds between different types of wood, laminates, and other materials used in furniture construction.
- These adhesives offer resistance to temperature changes, moisture, and wood movement, ensuring furniture pieces’ structural integrity and longevity. They also enable the construction of intricate designs and joints by providing high bond strength.
Environmental Benefits of One Component Epoxy Adhesive
One component of epoxy adhesives offers excellent performance and versatility and provides several environmental benefits. As the world continues to prioritize sustainability and environmental responsibility, these adhesives significantly reduce the ecological impact of various industries. From reducing waste to lowering energy consumption, one component of epoxy adhesives contributes to a greener and more sustainable future. Let’s explore some of the key environmental benefits of one component epoxy adhesive:
Reduced Material Waste
- One component epoxy adhesives require minimal material usage compared to traditional mechanical fastening methods such as screws or rivets. Doing this decreases the amount of waste produced during manufacturing and assembly processes.
- By eliminating the need for additional fasteners, these adhesives help to minimize material consumption and decrease the overall environmental footprint of products. Paying attention to the number of pins used is especially crucial in the automotive, aerospace, and electronics industries, as these industries typically utilize them in large quantities.
Energy Efficiency
- One component epoxy adhesives offer fast curing times and can achieve high bond strength at room temperature, reducing the need for energy-intensive heating or curing processes.
- Unlike thermal bonding methods requiring elevated temperatures or curing ovens, these adhesives can cure rapidly with minimal energy input. By adopting this approach, manufacturers can reduce energy consumption during manufacturing, saving energy and decreasing greenhouse gas emissions.
Durability and Longevity
- One component of epoxy adhesives provides solid and durable bonds, enhancing the lifespan of assembled products. This approach is more efficient and sustainable by reducing the need for repairs, replacements, and waste generation.
- The longevity of adhesive bonds helps extend the product life cycle, minimizing the environmental impact associated with manufacturing, transportation, and disposal. Industries like construction, automotive, and electronics require reliable and long-lasting bonds, making this particularly advantageous.
Eco-Friendly Formulations
- Many manufacturers offer one component epoxy adhesives with eco-friendly formulations that comply with various environmental regulations and standards.
- These adhesives may be free of harmful substances such as volatile organic compounds (VOCs), heavy metals, and hazardous solvents. Using adhesives with low or no VOC content helps to improve indoor air quality and reduce environmental pollution.
Waste Reduction and Recycling
- One component of epoxy adhesives can contribute to reducing waste by enabling the use of thinner and lighter materials in product design.
- Some manufacturers design epoxy adhesives to be easily recyclable or compatible with recycling processes. By bonding components with adhesive, separating and recycling them becomes more accessible, reducing waste that would otherwise end up in landfills.
Design Flexibility
- One epoxy adhesive component provides excellent bonding capabilities between different materials, including dissimilar substrates. With this capability, users can design one-of-a-kind products utilizing environmentally friendly materials that exhibit desirable features.
- Designers can explore lightweight and sustainable materials, reducing the overall weight of products and improving fuel efficiency in transportation applications.
One Component Epoxy Adhesive – A Versatile and Reliable Bonding Solution
One component epoxy adhesive is a versatile and reliable bonding solution that finds applications in various industries. This adhesive offers several advantages, including muscular bonding strength, excellent chemical resistance, and fast curing times. Whether in automotive, electronics, construction, or other sectors, one component epoxy adhesive provides a reliable and efficient bonding solution. Let’s explore the key features and benefits of this versatile adhesive:
Versatility
- One component of epoxy adhesive is compatible with various substrates, including metals, plastics, ceramics, and composites. It provides a versatile bonding solution for different material combinations, enabling the assembly of diverse components and structures.
- This adhesive is suitable for various applications, such as bonding, sealing, encapsulation, and potting, making it a valuable tool for different industries and manufacturing processes.
Strong Bonding Strength
- One component epoxy adhesive offers excellent bonding strength, creating robust and durable bonds between materials. It forms a solid molecular bond that withstands mechanical stress, temperature variations, and environmental factors.
- With its high bond strength, this adhesive ensures the reliability and longevity of bonded assemblies, contributing to the overall performance and safety of products.
Chemical Resistance
- One component of epoxy adhesive exhibits exceptional resistance to chemicals, solvents, and environmental factors. It maintains its bond strength and integrity even when exposed to harsh conditions, such as moisture, oils, acids, and alkalis.
- This chemical resistance makes it suitable for applications in demanding environments, including automotive, aerospace, and industrial settings, where exposure to corrosive substances is daily.
Fast Curing Time
- One component epoxy adhesive offers fast curing times, allowing for efficient production processes. It can reach handling strength relatively quickly, reducing assembly time and increasing productivity.
- The fast curing feature is particularly beneficial for high-volume manufacturing or when a quick turnaround is required, enabling speedier assembly and production cycles.
Temperature and Thermal Stability
- One component of epoxy adhesive provides excellent temperature and thermal stability. It maintains its bonding strength and integrity even under extreme temperatures, such as high or low temperatures.
- The thermal stability of one component epoxy adhesive makes it suitable for applications in industries like automotive and electronics, where components experience wide temperature ranges and thermal cycling.
Durability
- One component of epoxy adhesive forms durable bonds that withstand various stresses, including mechanical, thermal, and environmental factors. It enhances the longevity and reliability of assembled parts, reducing the need for frequent repairs or replacements.
- Its durability makes it a preferred choice for critical applications that require long-term performance and structural integrity.
Easy Application
- Applying one component of epoxy adhesive is easy, and it allows for different application methods, such as manual dispensing, automated equipment, or syringe dispensers. It provides convenience and flexibility during the assembly process.
- The adhesive’s viscosity can be adjusted to suit specific application requirements, ensuring proper coverage and penetration for a strong bond.
Conclusion
One Component Epoxy Adhesive is a high-performance bonding solution widely used in various industrial and commercial applications. It offers many advantages, such as high bonding strength, excellent thermal and chemical resistance, and easy application. Applications that require a reliable and durable bonding solution find OCEA an ideal choice, and experts anticipate its popularity to grow. To ensure safety while handling OCEA, one must take proper precautions, and achieving optimal bonding results requires performing the critical surface preparation step. Overall, One Component Epoxy Adhesive is a versatile and reliable adhesive system that can meet the bonding needs of various industries.