Optical Bonding Adhesive
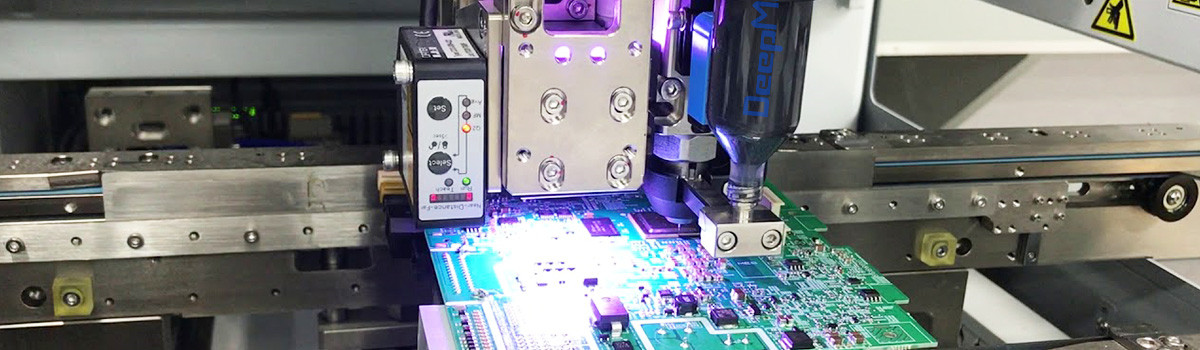
Optical bonding adhesive is a technology that produces touchscreen displays to improve performance and functionality. It is a process of attaching a protective layer or cover glass to the touch panel using a unique adhesive.
The adhesive improves the optical performance of the display by reducing the amount of reflection, glare, and color shift, resulting in better image quality and readability. This technology is widely used in various applications, including automotive, medical, military, aerospace, industrial, consumer electronics, and wearable devices. This article will focus on the benefits, types, applications, and future trends of optical bonding adhesive for touchscreen displays.
We will also discuss the factors to consider when choosing optical bonding adhesive and the limitations and cost considerations of this technology. Finally, we will highlight the importance of optical bonding adhesive in display technology and its role in improving the user experience.
What is Optical Bonding Adhesive?
Optical bonding adhesive is an adhesive material used to bond optical components together. Optical bonding aims to eliminate the air gap between the two surfaces, which can cause reflection, refraction, and other visual distortions.
The adhesive used for optical bonding is typically a clear epoxy or silicone-based material that is transparent and has a low refractive index to minimize visual distortion. It is applied thinly to one or both optical components and cured under heat or UV light.
Optical bonding adhesive is commonly used to manufacture displays for electronic devices, such as smartphones, tablets, and TVs, where high image quality and clarity are essential. Optical bonding helps reduce glare and improve contrast, making the display easier to read and view in bright lighting conditions.
How Does Optical Bonding Adhesive Work?
Optical bonding adhesive attaches a cover glass or touchscreen to a display module. It fills the gap between the cover glass and the display module with a transparent adhesive that hardens to create a unified piece.
Here is a brief overview of how optical bonding adhesive works:
- Cleaning and preparation: The cover glass and display module must be thoroughly cleaned before the adhesive is applied to ensure a strong bond. Any dust, oils, or debris can weaken the bond and cause problems later.
- Adhesive application: The adhesive is used in a thin, uniform layer on the surface of the display module. The adhesive is typically an optically clear epoxy resin designed to fill any gaps between the cover glass and the display module.
- Cover glass placement: Once the adhesive is applied, the cover glass is carefully placed on top of the display module. The cover glass is pressed firmly to ensure it is in contact with the adhesive.
- Curing: The adhesive is then cured using heat or ultraviolet light. This process hardens the adhesive and creates a strong bond between the cover glass and the display module.
- Quality control: Finally, the bonded assembly is inspected for defects such as bubbles, delamination, or improper alignment. Any issues are addressed before the assembly is shipped to the customer.
Optical bonding adhesive provides several benefits, including improved visual performance, increased durability, and resistance to moisture, dust, and other environmental factors.
Advantages of Optical Bonding Adhesive
Optical bonding is a process that involves applying a unique adhesive between two surfaces, typically a display and a protective cover, to enhance clarity, durability, and performance. Here are some of the advantages of using optical bonding adhesive:
- Improved Optical Performance: Optical bonding helps to eliminate the air gap between the display and cover, which reduces reflections and glare and improves contrast, color accuracy, and overall visibility.
- Increased Durability: The adhesive used in optical bonding forms a strong bond between the display and cover, improving the device’s overall structural integrity. This makes it more resistant to shock, vibration, and other mechanical stress, which helps prevent damage to the display and increases its lifespan.
- Enhanced Touchscreen Functionality: Optical bonding improves the accuracy and responsiveness of touchscreen displays by reducing the distance between the touch sensor and the show. This makes it easier to use and reduces the likelihood of errors or misinterpretations.
- Improved Resistance to Environmental Factors: Optical bonding can enhance the ability of the display to withstand environmental factors such as temperature changes, humidity, and exposure to sunlight, which can cause degradation or damage to the collection over time.
- Better Aesthetics: Optical bonding can improve the overall appearance of the display by reducing the visibility of the border between the show and the cover, which gives it a sleek and seamless appearance.
Overall, optical bonding adhesive offers a range of benefits that can help enhance the performance, durability, and aesthetics of displays used in various applications, from consumer electronics to industrial and medical devices.
Types of Optical Bonding Adhesive
There are several types of optical bonding adhesive available in the market, including:
- Epoxy adhesives: These are two-part adhesives that cure when mixed together. They are known for their high strength and durability, making them a popular choice for optical bonding.
- UV-cured adhesives cure when exposed to ultraviolet light, making them a faster alternative to epoxy adhesives. They are also known for their high transparency and low yellowing.
- Silicone adhesives: Silicone adhesives are flexible and have good resistance to temperature and moisture. They are a popular choice for bonding displays to curved surfaces.
- Acrylic adhesives: These adhesives offer good optical clarity and have excellent resistance to UV light and weathering. They are also known for their high strength and good adhesion to various surfaces.
- Cyanoacrylate adhesives: These adhesives cure quickly and have good adhesion to various surfaces. However, they are not recommended for bonding displays as they can cause damage due to their high acidity.
The choice of adhesive will depend on the application’s specific requirements, including factors such as the size and shape of the display, the type of device, and the environmental conditions in which the device will be used.
Applications of Optical Bonding Adhesive
Optical bonding adhesive is used in various applications where displays or touchscreens must be attached to a device. Some of the standard applications of optical bonding adhesive include:
- Industrial displays: Optical bonding is widely used in industrial displays, such as manufacturing facilities or control rooms. The adhesive helps to protect the collection from environmental factors such as dust, moisture, and temperature fluctuations.
- Medical devices: Optical bonding is commonly used in medical devices, such as ultrasound machines or patient monitoring systems. The adhesive helps improve the display’s clarity and protects it from damage due to frequent cleaning.
- Aviation displays: Optical bonding is used in aviation displays, such as those used in aircraft cockpits or navigation systems. The adhesive helps to improve visibility and reduce glare in bright sunlight.
- Outdoor displays: Optical bonding is used in outdoor displays, such as digital signage or kiosks. The adhesive helps to protect the collection from environmental factors such as rain, wind, and sunlight.
- Consumer electronics: Optical bonding is used in electronics such as smartphones and tablets. The adhesive helps improve the display’s clarity and protect it from damage due to everyday use.
Overall, optical bonding adhesive is used in applications where improved visibility, durability, and display protection are required.
Optical Bonding Adhesive for Touchscreen Displays
Optical bonding adhesive is used to manufacture touchscreen displays to improve their performance and durability. This process involves attaching the touch panel to the show by filling the air gap between the two surfaces with a transparent adhesive. This strengthens the display, enhances its visual clarity, and reduces the chances of internal reflection or glare.
The type of adhesive used for optical bonding depends on the specific application and the desired results. Some of the commonly used adhesives include acrylics, silicones, and polyurethanes. Acrylics are widely used because they have excellent optical clarity and are easy to work with. Silicones are also popular due to their flexibility and resistance to high temperatures, and polyurethanes are known for their high strength and durability.
Optical bonding adhesive must be carefully selected and applied to avoid any negative impact on the touchscreen’s performance. This requires expertise and precision, so it’s best to seek professional help from experienced adhesive manufacturers or suppliers. Proper handling, storage, and application of the adhesive are crucial to ensure the quality and reliability of the touchscreen display.
Optical Bonding Adhesive for Automotive Displays
Optical bonding adhesive is a type of adhesive that is commonly used in the manufacturing of automotive displays. It bonds the display panel to the cover glass or touch screen, providing a strong, optically clear bond between the two components.
Several types of optical bonding adhesives are available for automotive displays, including silicone, acrylic, and polyurethane-based adhesives. Each type of adhesive has its own set of advantages and disadvantages, and the choice of adhesive will depend on the specific requirements of the display.
Silicone-based adhesives are the most commonly used optical bonding adhesive for automotive displays. They provide excellent optical clarity, are resistant to UV radiation and temperature changes, and have high flexibility. They are also resistant to moisture and chemicals, making them ideal for harsh automotive environments.
Acrylic-based adhesives are another popular option for automotive displays. They are known for their high optical clarity and excellent adhesion properties. They are also resistant to UV radiation and temperature changes, making them a good choice for automotive displays.
Polyurethane-based adhesives are less commonly used in automotive displays but offer several advantages over other adhesives. They have high chemical resistance, water and moisture resistance, and excellent adhesion properties. They are also very flexible, which makes them ideal for use in displays that may be subjected to a lot of vibration or movement.
Overall, the choice of optical bonding adhesive for an automotive display will depend on various factors, including the specific requirements of the production, the operating environment, and the desired performance characteristics. It is essential to consult a qualified specialist to choose a suitable adhesive for the specific application.
Optical Bonding Adhesive for Outdoor Displays
When selecting an optical bonding adhesive for outdoor displays, there are a few key factors to consider:
- UV resistance: Outdoor displays are exposed to sunlight and other sources of UV radiation. A UV-resistant adhesive is essential to ensure that the bonding material does not degrade over time and cause the display to fail.
- Temperature resistance: Outdoor displays are also exposed to various temperatures, from hot summer days to cold winter nights. The adhesive material must withstand these temperature extremes without losing its bond strength.
- Impact resistance: Outdoor displays are more susceptible to damage from impacts and vibrations. An adhesive with good impact resistance can help protect the collection and prevent cracks or other damage.
- Clarity: The adhesive used in optical bonding should be as straightforward as possible to avoid any distortion or haziness that could affect the display’s readability.
- Adhesion strength: The adhesive material should have sufficient power to ensure a solid and long-lasting bond between the display and cover glass.
Many different optical bonding adhesives are available on the market, and selecting one that meets your specific requirements for outdoor displays is essential. Some popular options include silicone, epoxy, and acrylic-based adhesives. It’s recommended to consult with a bonding expert or adhesive manufacturer to determine the best choice for your specific application.
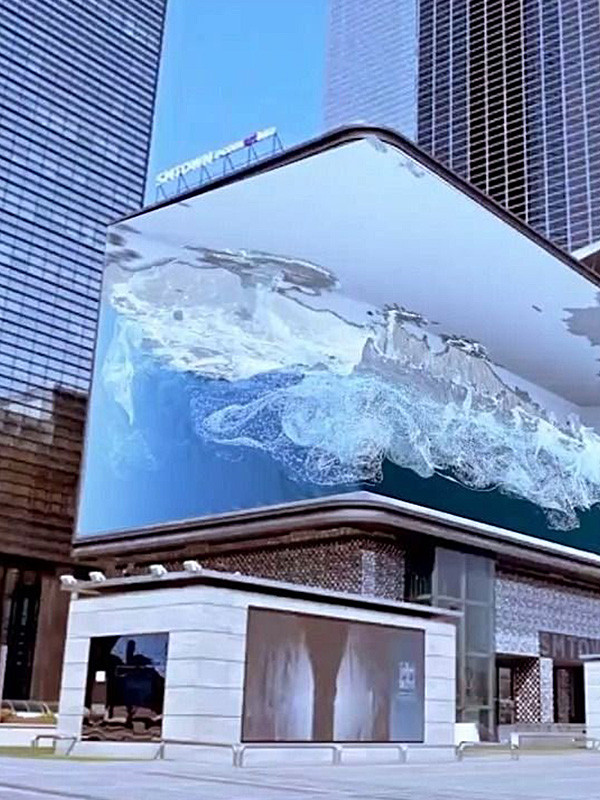
Optical Bonding Adhesive for Medical Displays
Optical bonding adhesive is a process used to attach the cover glass or touch panel to the LCD panel of a display. It involves filling the gap between the two surfaces with a transparent adhesive with optical properties similar to glass ones. Optical bonding adhesive is commonly used in medical displays to improve the display’s durability, readability, and safety.
When selecting an optical bonding adhesive for medical displays, it is essential to consider several factors, such as biocompatibility, chemical resistance, and optical clarity. The adhesive should be biocompatible and not cause any harm to the patient or user, and it should also be able to withstand exposure to harsh chemicals and disinfectants commonly used in medical environments.
In addition, the adhesive should have excellent optical clarity to ensure the display is easy to read and provides accurate information. It is also essential to consider the adhesive’s curing time, as this can affect the overall production time of the display.
Some examples of optical bonding adhesives suitable for medical displays include silicone-based adhesives, polyurethane-based adhesives, and acrylic-based adhesives. It is essential to consult a qualified supplier to determine the best adhesive for a specific application.
Optical Bonding Adhesive for Military Displays
Optical bonding is attaching a layer of optically clear adhesive between a display panel and a cover glass or touch screen. This process helps to eliminate air gaps between the two surfaces, which can lead to reflections, reduced contrast, and other optical distortions.
In military applications, displays must be rugged and durable, capable of withstanding extreme environments and harsh conditions. Therefore, the optical bonding adhesive used in military displays must withstand high temperatures, humidity, vibration, and shock.
Some commonly used optical bonding adhesives for military displays include silicone, epoxy, and acrylic. Silicone adhesives are known for their high-temperature resistance and flexibility, making them ideal for use in military displays exposed to extreme environments. Epoxy adhesives are known for their high strength and resistance to shock and vibration, while acrylic adhesives are known for their optical clarity and low shrinkage.
When choosing an optical bonding adhesive for military displays, it is essential to consider factors such as temperature range, moisture resistance, bonding strength, and visual performance. It is also necessary to ensure that the adhesive meets military specifications and standards for reliability and durability.
Optical Bonding Adhesive for Aerospace Displays
Optical bonding is attaching a protective glass or plastic cover to an electronic display using an adhesive. Optical bonding is commonly used in aerospace displays to protect the collection from damage caused by vibration, temperature changes, and other environmental factors.
The adhesive used in optical bonding must meet strict requirements for aerospace applications, including high-temperature resistance, low outgassing, and compatibility with the materials used in the display and cover. Some common types of adhesives used in aerospace applications include epoxy, silicone, and acrylic.
Epoxy adhesives are known for their strength and durability, and they are commonly used in aerospace applications where high-strength bonding is required. Silicone adhesives are known for their flexibility and are often used in applications where vibration and shock resistance are critical. Acrylic adhesives are known for their low outgassing properties and are often used in applications where display contamination is a concern.
When selecting an adhesive for optical bonding in aerospace displays, it is essential to consider the application’s specific requirements and choose a bond that meets those requirements. It is also necessary to work with a supplier who has experience in aerospace applications and can provide guidance on adhesive selection and application.
Optical Bonding Adhesive for Wearable Devices
Optical bonding is a process used to attach a cover glass or touch panel to an LCD or OLED display to improve the visual performance of the device. The adhesive used in optical bonding is critical, as it must provide both strong bonding and high optical clarity.
A high-performance adhesive is essential for wearable devices, where the display is often smaller, and the device may be subjected to more physical stress. Several types of adhesive can be used for optical bonding, including silicone, acrylic, and polyurethane.
Silicone adhesives are often used in wearable devices because they offer good optical clarity and flexibility, which can help to prevent cracking or damage to the display. They also have good adhesion to various substrates, which can be crucial in wearables where the collection may be attached to a curved or irregular surface.
Acrylic adhesives are another option known for their high optical clarity and excellent bonding strength. They are also resistant to yellowing and can withstand exposure to UV light, making them a good choice for wearables that may be exposed to sunlight.
Polyurethane adhesives are less commonly used in optical bonding, but they can offer excellent bonding strength, durability, and good optical properties. They are often used in applications where the display may be exposed to extreme temperatures or harsh environments.
Ultimately, the choice of adhesive will depend on the specific requirements of the wearable device, including the size and shape of the display, the materials being bonded, and the environmental conditions in which the device will be used. Working with a qualified supplier who can guide selecting the best adhesive for your application is essential.
Optical Bonding Adhesive for Virtual Reality Headsets
Optical bonding is the process of attaching a layer of material to the surface of a display panel, typically a touch screen or LCD screen, to reduce the amount of light reflection and glare. In the context of virtual reality headsets, optical bonding is used to improve the visual quality and immersion of the VR experience by reducing the amount of light that is reflected off the surface of the headset’s display panels.
To perform optical bonding, a particular type of adhesive is required. This adhesive needs to be transparent, flexible, and able to bond to various materials, including glass, plastic, and metal. The adhesive should also have good thermal stability, as VR headsets can generate significant heat during use.
There are a few types of adhesives that are commonly used for optical bonding in VR headsets:
- Optical clear adhesive (OCA): This thin, transparent film is applied to the surface of the display panel. OCA has excellent optical properties and can improve the display’s contrast, color, and brightness.
- Liquid optically clear adhesive (LOCA): This liquid adhesive is applied between the display panel and the cover glass or plastic. LOCA is typically used for curved displays, as it can conform to the curved surface more quickly than OCA.
- Epoxy: Epoxy adhesives are often used for bonding glass to metal or plastic and can provide a robust and durable bond. However, they are less commonly used for optical bonding in VR headsets, as they can introduce air bubbles or other defects that can affect the optical properties of the display.
Optical Bonding Adhesive for Industrial Displays
Optical bonding is attaching a protective glass or plastic cover to a display using an adhesive to improve its optical properties, such as contrast and clarity. In industrial environments, exhibitions are exposed to harsh conditions, such as high temperatures, humidity, and dust, affecting their performance and longevity. Optical bonding adhesive can help protect the display from these conditions and enhance its durability.
Various types of optical bonding adhesives are available on the market, each with unique features and benefits. Some of the commonly used adhesive types for industrial displays include:
- Epoxy Adhesive: Epoxy adhesive is a popular choice for optical bonding because of its excellent bonding strength and durability. It is resistant to chemicals and can withstand high temperatures, making it suitable for harsh industrial environments.
- UV-curing Adhesive: UV-curing adhesive is a fast-curing adhesive that hardens quickly when exposed to UV light. It is ideal for applications that require fast production times and high bonding strength.
- Silicone Adhesive: Silicone adhesive is known for its flexibility and excellent resistance to high temperatures, humidity, and UV radiation. It is commonly used in industrial environments where displays are exposed to extreme conditions.
- Acrylic Adhesive: Acrylic adhesive is versatile and provides excellent bonding strength and durability. It is resistant to weathering, chemicals, and UV radiation, making it suitable for industrial environments.
Optical Bonding Adhesive for Consumer Electronics
Optical bonding adhesive is a process of bonding a layer of adhesive material between two optical surfaces, such as a display panel and a cover glass, to improve the visibility and durability of the display. In consumer electronics, optical bonding is commonly used in smartphones, tablets, laptops, and other portable devices to enhance the display quality and user experience.
Different types of optical bonding adhesives are available in the market, such as silicone, acrylic, and polyurethane adhesives. Each adhesive has unique characteristics and properties; the selection depends on the specific application requirements.
Silicone adhesive is famous for consumer electronics because of its excellent optical clarity, high-temperature resistance, and flexibility. It also provides a good bond strength and is easy to apply. However, it can be more expensive than other adhesives.
Acrylic adhesive is another option that offers good optical clarity and bond strength. It is also more affordable than silicone adhesive, making it a preferred choice for budget-conscious manufacturers. However, it may not be as flexible as silicone adhesive, and its bond strength may decrease over time due to exposure to UV light.
Polyurethane adhesive is a durable and robust adhesive that can withstand extreme temperatures and harsh environments. It provides excellent bond strength and can be used to bond different materials. However, it may offer better optical clarity than silicone or acrylic adhesives.
Manufacturers must consider optical clarity, bond strength, temperature resistance, flexibility, and durability when selecting the adhesive.
Factors to Consider When Choosing Optical Bonding Adhesive
When choosing an optical bonding adhesive, here are some factors to consider:
- Compatibility: The adhesive you choose must be compatible with the materials you are bonding. Some adhesives work well with certain materials, while others may not. Ensure the adhesive is consistent with the cover and display panel.
- Refractive index: The refractive index of the adhesive is crucial in optical bonding. The refractive index must match that of the display panel to reduce the amount of light reflection and refraction, which can cause distortion or glare.
- Curing time: The adhesive’s curing time is the time required for the adhesive to reach its full strength. The curing time depends on the adhesive’s chemistry, ranging from a few minutes to several hours. Consider the curing time when choosing an adhesive for your project.
- Operating temperature: The adhesive’s operating temperature is the temperature range in which the adhesive will perform optimally. It is essential to consider the temperature range of the application environment when selecting the adhesive.
- Mechanical properties: The adhesive must have good mechanical properties, such as high tensile strength and resistance to shear and peeling. These properties ensure the adhesive can withstand mechanical stress and maintain the bond over time.
- Environmental resistance: The adhesive must resist ecological factors such as moisture, UV light, and temperature changes. These factors can cause the adhesive to deteriorate, leading to a weakened bond.
- Cost: Finally, consider the cost of the adhesive. Opt for a bond that offers a balance between performance and cost-effectiveness.
Bonding Strength of Optical Bonding Adhesive
The bonding strength of optical bonding adhesive typically depends on various factors, including the type of adhesive used, the bonded materials, the surface preparation, and the curing process.
Generally, optical bonding adhesives are designed to provide high bonding strength and durability while maintaining optical clarity. They are formulated to provide a robust and reliable bond between the optical components, such as the display and the cover glass, without affecting their optical properties.
The bonding strength of the adhesive is usually measured in terms of its shear power or tensile strength. Shear strength refers to the ability of the adhesive to resist sliding or shearing forces, while tensile strength refers to its ability to resist pulling or stretching muscles.
The bonding strength can be affected by the surface preparation of the bonded materials. It is essential to ensure the surfaces are clean, dry, and free of contaminants, such as oils, dust, or fingerprints. Surface treatments, such as plasma cleaning or corona discharge, may also enhance the bonding strength.
The curing process of the adhesive is also critical to achieving a solid bond. The curing time and temperature can vary depending on the type of adhesive and the materials being bonded. It is essential to follow the manufacturer’s recommendations for curing to ensure optimal bonding strength.
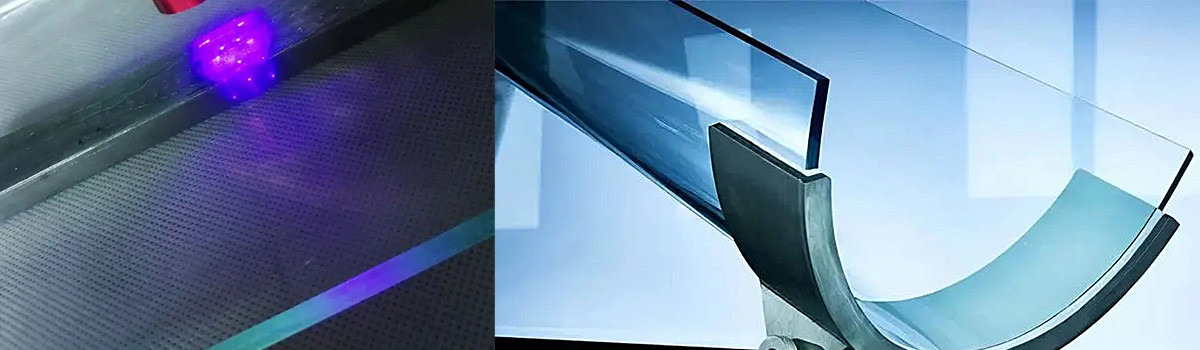
Optical Clarity of Optical Bonding Adhesive
The optical clarity of an optical bonding adhesive refers to its ability to transmit light without causing significant scattering or absorption. In other words, it measures the adhesive’s transparent to visible light.
The optical clarity of an adhesive is influenced by several factors, including its refractive index, viscosity, and thickness. Adhesives with a high refractive index tend to have better optical clarity because they can better match the refractive index of the materials they are bonding, resulting in less reflection and refraction of light.
Viscosity also plays a role in optical clarity, as adhesives with a low density tend to spread more evenly and create a thinner bond line, resulting in less distortion and light scattering. However, adhesives with very low viscosity may be more challenging to handle and apply.
The thickness of the adhesive layer is another important factor, as thicker layers can create more distortion and reduce optical clarity. Therefore, it is essential to use the appropriate amount of adhesive to minimize the thickness of the bond line.
Overall, selecting an optical bonding adhesive with high optical clarity is essential for applications with critical transparency and visibility, such as touchscreens, displays, and optical filters.
Chemical Resistance of Optical Bonding Adhesive
The chemical resistance of an optical bonding adhesive depends on the specific type of adhesive used. Generally, optical bonding adhesives are designed to resist various chemicals, including solvents, acids, and bases, but their resistance to specific chemicals can vary.
For example, some optical bonding adhesives may be resistant to alcohol and some types of oils, while others may not be. It is essential to consult the manufacturer’s specifications and recommendations for the specific adhesive used to determine its chemical resistance.
Factors that can affect the chemical resistance of an optical bonding adhesive include the composition of the adhesive, the curing process, and the type of substrate to which it is being bonded. It is essential to choose an appropriate adhesive for the specific application and conditions in which it will be used, including exposure to different chemicals.
In general, it is recommended to test the chemical resistance of an optical bonding adhesive in the specific application and conditions in which it will be used before finalizing its use. This can help ensure that the adhesive will perform as expected and provide the necessary level of chemical resistance.
Temperature Resistance of Optical Bonding Adhesive
The temperature resistance of optical bonding adhesive can vary depending on the specific adhesive used and its intended application. Generally, optical bonding adhesives are designed to withstand a wide range of temperatures, including extreme temperatures that can cause damage to other types of bonds.
Some optical bonding adhesives are capable of withstanding temperatures as low as -55°C (-67°F) and as high as 150°C (302°F). However, it’s important to note that these values can vary greatly depending on the specific adhesive formulation, the bonded materials, and the use conditions.
In addition to temperature resistance, other essential factors to consider when selecting an optical bonding adhesive include its optical properties, adhesion strength, curing time, and chemical compatibility with the bonded materials. It’s always best to consult with the adhesive manufacturer or a knowledgeable technical expert to ensure that the adhesive selected is appropriate for the intended application and environmental conditions.
UV Resistance of Optical Bonding Adhesive
The UV resistance of optical bonding adhesive is an important consideration when selecting an adhesive for outdoor or other applications that will be exposed to sunlight or other sources of UV radiation. Some optical bonding adhesives are designed to be highly resistant to UV radiation, while others may degrade or yellow over time when exposed to UV radiation.
UV resistance is often achieved through special additives in the adhesive formulation that absorb or reflect UV radiation. Some adhesives may also be formulated with inhibitors that prevent the breakdown of the adhesive due to UV exposure.
When selecting an optical bonding adhesive for outdoor or other UV-exposed applications, it’s essential to consider the adhesive’s UV resistance and its overall performance characteristics. Adhesives with high UV resistance may have different optical or mechanical properties than adhesives that are not UV resistant. Additionally, the specific materials being bonded and the application method may affect the adhesive’s UV resistance.
As with any adhesive selection, it’s always best to consult with the manufacturer or a knowledgeable technical expert to ensure that the adhesive selected is appropriate for the intended application and environmental conditions.
Moisture Resistance of Optical Bonding Adhesive
Optical bonding adhesives can have varying degrees of moisture resistance depending on the specific adhesive used. However, optical bonding adhesives are generally designed to have good moisture resistance, as they are often used in outdoor or harsh environments where exposure to moisture is likely.
One crucial factor in the moisture resistance of an optical bonding adhesive is the type of adhesive chemistry used. Some adhesives, such as acrylics or polyurethanes, are inherently more moisture-resistant than others, such as epoxies. In addition, the specific formulation of the adhesive can also affect its moisture resistance.
Another factor that can impact the moisture resistance of an optical bonding adhesive is the thickness of the adhesive layer. Thicker adhesive layers can be more prone to moisture ingress, as there is more material for moisture to penetrate. Therefore, it is essential to carefully control the thickness of the adhesive layer during the bonding process.
Overall, optical bonding adhesives can be designed to have excellent moisture resistance, but it is essential to carefully consider the specific adhesive chemistry and formulation, as well as the bonding process parameters, to ensure optimal performance in harsh environments.
Shelf Life of Optical Bonding Adhesive
The shelf life of optical bonding adhesive can vary depending on the specific type and brand of adhesive. However, most manufacturers recommend using the adhesive within 6 to 12 months of production for optimal performance.
It’s important to note that the shelf life can be affected by several factors, such as storage conditions and exposure to heat, humidity, and light. If the adhesive is not stored correctly or is exposed to unfavorable conditions, its shelf life may be significantly reduced.
To ensure that the optical bonding adhesive is still usable, it’s always recommended to check its consistency and properties before use, especially if it has been stored for an extended period. If the adhesive changes in texture or appearance or no longer adhere appropriately, it should be discarded and replaced with a fresh batch.
Storage and Handling of Optical Bonding Adhesive
Proper storage and handling of optical bonding adhesive ensure its effectiveness and longevity. Here are some guidelines to follow:
- Storage temperature: Optical bonding adhesive should be stored in a cool, dry place at a temperature between 5°C and 25°C (41°F and 77°F). Storage at temperatures outside of this range can affect the adhesive’s properties and reduce its effectiveness.
- Shelf life: The shelf life of optical bonding adhesive can vary depending on the type and manufacturer. Always check the manufacturer’s guidelines for the recommended shelf life.
- Handling: Optical bonding adhesive should be handled with care to prevent contamination. Always wear gloves and use clean tools when taking the adhesive.
- Mixing: Some types of optical bonding adhesive require mixing before use. Follow the manufacturer’s instructions carefully and mix the adhesive thoroughly to ensure proper bonding.
- Application: Optical bonding adhesive should be applied evenly and thinly to the surfaces to be bonded. Excessive adhesive can cause bubbles or other defects in the bond.
- Curing: Optical bonding adhesive usually requires curing at a specific temperature and humidity for a particular time. Follow the manufacturer’s guidelines for curing to ensure proper bonding.
- Disposal: According to local regulations, unused or expired optical bonding adhesives should be disposed of properly.
Following these guidelines will help ensure the proper storage and handling of optical bonding adhesive, resulting in better performance and longevity of the bond.
Preparation and Application of Optical Bonding Adhesive
The optical bonding process improves the display’s durability and visibility by reducing the amount of air between the cover glass and the display panel, thereby minimizing reflection, glare, and refraction. Here are the steps for preparing and applying optical bonding adhesive:
Preparation:
- Clean the surfaces: Clean the cover glass and display panel surfaces to remove dirt, dust, or debris. Use a lint-free cloth and a cleaning solution compatible with the adhesive.
- Apply the primer: Apply a thin layer of primer to both the cover glass and display panel surfaces. The primer enhances the bonding strength of the adhesive.
- Mix the adhesive: Mix the optical bonding adhesive according to the manufacturer’s instructions. Wear gloves and follow the recommended safety precautions.
Application:
- Dispense the adhesive: Dispense the adhesive onto one of the surfaces in a continuous, uniform bead. Use a dispensing tool that allows precise control of the adhesive flow.
- Spread the adhesive: Use a roller or a spreader to spread the adhesive evenly over the surface. Make sure the adhesive is applied uniformly to avoid bubbles or voids.
- Align the surfaces: Carefully align the cover glass with the display panel, ensuring the adhesive is evenly distributed between them.
- Press the surfaces: Apply pressure evenly across the surface of the cover glass to press it onto the display panel. Use a laminating machine or a vacuum laminator to apply the required pressure.
- Cure the adhesive: Cure the adhesive according to the manufacturer’s instructions. The curing process may involve heat or UV light, which may take several hours.
- Inspect the bond: Inspect the bond between the cover glass and display panel to ensure it is uniform, without any bubbles or voids.
Quality Control of Optical Bonding Adhesive
Quality control of optical bonding adhesive is essential to manufacturing optical displays, touch screens, and other optical components. Here are some of the critical steps involved in ensuring the quality of optical bonding adhesive:
- Raw Material Inspection: The quality control process begins with inspecting raw materials used to manufacture the adhesive. To meet the desired specifications, the materials should be checked for their purity, viscosity, and other properties.
- Mixing Process: The mixing process should be closely monitored to ensure the adhesive is mixed thoroughly and in the correct proportions. Any deviations from the specified mixing process could result in variations in the adhesive properties.
- Curing Process: The process is critical to ensure that the adhesive has the desired strength and optical properties. The curing time, temperature, and humidity should be carefully monitored to ensure that the adhesive cures properly.
- Adhesive Testing: The adhesive should be tested to ensure it meets the desired optical, mechanical, and thermal properties. The testing should be performed using standardized procedures and equipment to ensure reliable results.
- Visual Inspection: Once the adhesive is applied to the optical component, it should be inspected visually to ensure no defects, such as bubbles or uneven application.
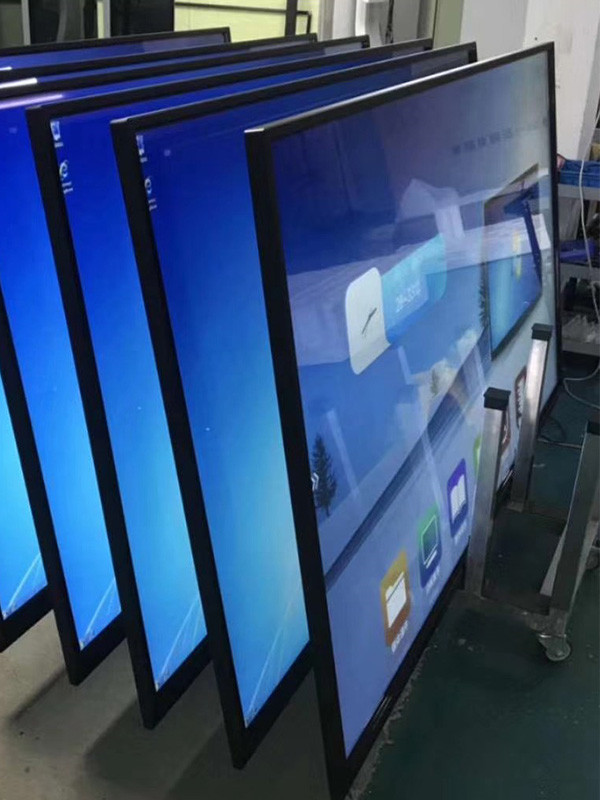
Testing and Certification of Optical Bonding Adhesive
The testing and certification of optical bonding adhesive involve several steps, including:
- Adhesive material testing: The adhesive material is tested for its physical properties, viscosity, hardness, and adhesion strength. The testing ensures that the adhesive can withstand the stresses and strains it will experience in real-world applications.
- Compatibility testing: The adhesive is tested for its compatibility with different substrates and coatings to ensure that it does not cause any damage or discoloration to the bonded surface.
- Optical performance testing: The optical performance of the adhesive is tested using a spectrophotometer to measure the amount of light reflected and transmitted through the adhesive. The testing is done to ensure that the adhesive does not affect the display quality of the device.
- Environmental testing: The adhesive is tested for its ability to withstand different environmental conditions, such as temperature, humidity, and UV exposure. The testing ensures the adhesive remains stable and does not degrade over time.
- Certification: After the adhesive has undergone all the necessary testing, it is certified by independent testing agencies, such as Underwriters Laboratories (UL), Intertek, or TUV Rheinland. The certification ensures that the adhesive meets the required standards and is safe for use in electronic devices.
Cost Considerations of Optical Bonding Adhesive
The cost of optical bonding adhesive can vary based on several factors, including the type and quality of the adhesive, the size and complexity of the display assembly, and the quantity required for the manufacturing process.
Some additional cost considerations for optical bonding adhesive include:
- Material cost: The cost of the adhesive material itself can vary depending on the type and quality of the adhesive. For example, some adhesives may require a higher purity level or a more complex manufacturing process, which can increase the cost.
- Labor cost: The optical bonding process requires skilled labor to apply the adhesive and bond the components together. The labor cost can vary depending on the assembly’s complexity and the labor force’s experience level.
- Equipment cost: Optical bonding equipment can be expensive, especially for larger or more complex displays. The equipment cost can impact the manufacturing process’s overall cost.
- Warranty and repair costs: Optical bonding can improve the durability of the display assembly, but it may also increase the cost of repairs or warranty claims if the bonding fails or the components need to be replaced.
Future Trends in Optical Bonding Adhesive
As technology advances, the future trends in optical bonding adhesive are likely to include:
- Advancements in materials: There is likely to be a continued focus on developing new and improved materials for optical bonding adhesives, such as new polymers and adhesives offering better optical properties and durability.
- Increased use of flexible displays: With the growing popularity of flexible shows, there is likely to be an increased demand for optical bonding adhesives that can bond flexible materials together while maintaining excellent optical clarity and durability.
- Smaller and thinner devices: As devices become smaller and lighter, optical bonding adhesive must become more delicate and precise to accommodate the trend. This may involve the development of new application methods and equipment.
- Improved UV resistance: As UV exposure can degrade optical bonding adhesive over time, there is likely to be an increased demand for adhesives with enhanced UV resistance to extend the life of optical devices.
- Integration with other technologies: As optical devices become more integrated with other technologies, such as sensors and touchscreens, there may be a need for optical bonding adhesive that can also bond these additional components together.
Overall, the future trends in optical bonding adhesive will likely involve advancements in materials, increased use of flexible displays, smaller and thinner devices, improved UV resistance, and integration with other technologies.
Limitations of Optical Bonding Adhesive
While optical bonding adhesive has many advantages, such as improved visibility, increased durability, and reduced reflection, it also has several limitations. Some of these limitations include:
- Cost: Optical bonding adhesives can be expensive compared to other bonds, making it prohibitive for some manufacturers.
- Complexity: Optical bonding adhesive requires a high level of expertise and specialized equipment to apply correctly. This can make the bonding process more time-consuming and expensive.
- Limited application: Optical bonding adhesive is unsuitable for all displays or touch panels. It may not be effective in bonding certain materials or substrates, which can limit its application.
- Temperature sensitivity: Optical bonding adhesive may be sensitive to high or low temperatures, affecting performance. Extreme temperatures can cause the adhesive to weaken or break down, leading to display or touch panel failure.
- Maintenance: Optical bonding adhesive requires regular maintenance to remain effective. Any damage or degradation to the adhesive can compromise its bonding strength and reduce the durability of the display or touch panel.
Conclusion: The Importance of Optical Bonding Adhesive in Display Technology
Optical bonding adhesive plays a critical role in display technology by improving displays’ visual performance and durability. This adhesive helps to eliminate the air gap between the display panel and the cover glass or touch panel, which minimizes reflections, glare, and distortion, resulting in improved image clarity, contrast, and color accuracy.
Additionally, optical bonding adhesive provides a protective layer against environmental factors such as moisture, dust, and scratches, thereby enhancing the durability and longevity of the display. Optical bonding adhesive is essential for achieving optimal display performance and ensuring a high-quality user experience.