Electrical Bonding Adhesive
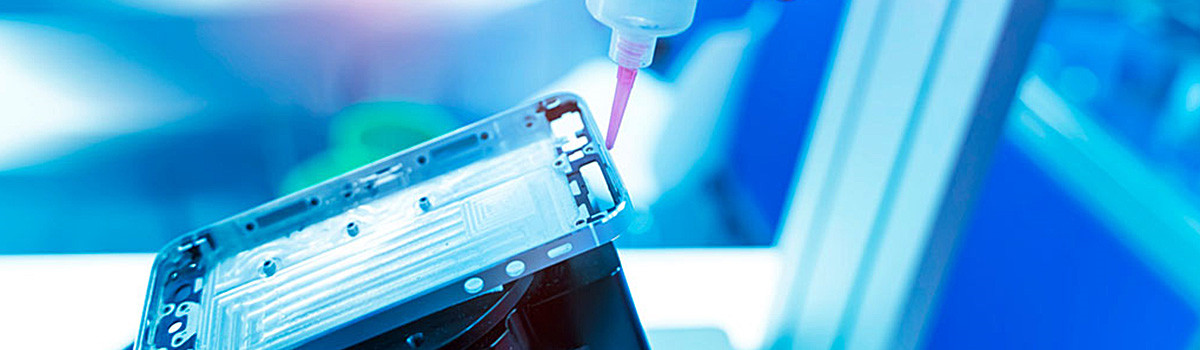
Electrical bonding adhesives are specialized adhesives used for bonding and sealing electrical applications. They provide:
- Excellent electrical conductivity and thermal stability.
- Making them ideal for electronic devices.
- Automotive components.
- Aerospace applications.
These adhesives play a crucial role in ensuring the safety and reliability of electrical systems by providing a secure bond and preventing the formation of electrical arcing or sparks.
What are Electrical Bonding Adhesives?
Electrical bonding adhesives are specialized adhesives used in electrical and electronic applications to create a secure bond between different conductive components. These adhesives are designed to provide reliable electrical connections, ensure grounding, and protect against electromagnetic interference (EMI). They are crucial in various industries, including automotive, aerospace, telecommunications, and consumer electronics.
The primary function of electrical bonding adhesives is to establish a low-resistance path between two or more conductive surfaces, such as metal components or circuit boards. This path allows for the efficient transfer of electrical current, helps prevent static discharge, and reduces the risk of electrical failures. By creating a solid bond, these adhesives also offer mechanical support and enhance the overall durability of the assembled components.
Several vital characteristics make electrical bonding adhesives suitable for their intended applications. Firstly, they have excellent electrical conductivity, which means they can conduct electricity effectively, minimizing resistance and ensuring a reliable connection. Conductive fillers such as silver, copper, or graphite are often incorporated into the adhesive formulation to enhance conductivity.
Secondly, electrical bonding adhesives typically have good thermal conductivity properties. This enables them to dissipate heat generated by electrical components, preventing overheating and potential damage to sensitive electronic devices.
Moreover, these adhesives are formulated to have high strength and bond integrity. They can withstand mechanical stresses, vibration, and thermal cycling without compromising the electrical connection. This is crucial, especially in applications where the bonded components may be exposed to harsh environmental conditions.
Electrical bonding adhesives come in various forms, including pastes, films, tapes, or liquids. The choice of adhesive depends on factors such as the application requirements, the type of materials being bonded, and the assembly process. For instance, conductive adhesive films or tapes are commonly used to assemble flexible circuits. In contrast, conductive paste adhesives are often utilized for bonding surface-mount components on printed circuit boards.
In addition to providing electrical and mechanical bonding, some adhesives offer EMI shielding properties. They contain conductive fillers that create a conductive barrier, preventing electromagnetic radiation from interfering with the operation of nearby electronic components.
Proper surface preparation is crucial when using electrical bonding adhesives to ensure optimal bond strength and performance. Surfaces should be thoroughly cleaned, free from contaminants, and, in some cases, may require surface activation or priming to enhance adhesion.
Electrical bonding adhesives are essential in modern electrical and electronic manufacturing. They enable reliable and efficient electrical connections while offering mechanical support and protection against EMI. With ongoing advancements in materials and adhesive technologies, these adhesives play a vital role in developing innovative and reliable electronic devices and systems.
Types of Electrical Bonding Adhesives
Electrical bonding adhesives create secure and reliable electrical connections between conductive components. These adhesives are designed to provide excellent electrical conductivity while offering strong mechanical bonding properties. Here are some common types of electrical bonding adhesives:
- Conductive Epoxy Adhesives: Conductive epoxy adhesives are widely used in electrical bonding applications. They consist of a two-part system, typically a resin and a hardener, which must be mixed before use. These adhesives contain conductive fillers, such as silver, copper, or graphite, which enable the flow of electric current. Conductive epoxy adhesives offer excellent adhesion to various substrates, providing electrical conductivity and mechanical strength.
- Electrically Conductive Adhesive Tapes: Electrically conductive adhesive tapes consist of a backing material coated with an adhesive that contains conductive particles. The backing material provides mechanical support and insulation, while the conductive adhesive ensures electrical continuity. These tapes are easy to apply, versatile, and can conform to irregular surfaces. They are commonly used for bonding flexible circuits, grounding applications, and EMI/RFI shielding.
- Conductive Silver Adhesives: Conductive silver adhesives are formulated with silver particles suspended in a polymer matrix. Silver is an excellent conductor of electricity, offering high electrical conductivity. These adhesives provide strong adhesion to various substrates, including metals, ceramics, and plastics. They are commonly used in electronic assembly, bonding of electrical components, and repairing electrical circuits.
- Electrically Conductive Silicone Adhesives: Electrically conductive silicone adhesives are formulated with silicone polymers and conductive fillers, such as silver, nickel, or carbon. They offer good electrical conductivity, flexibility, and thermal stability. These adhesives are often used in applications requiring flexibility and environmental resistance, such as bonding flexible circuits, sealing connectors, and potting electronic components.
- Electrically Conductive Polyurethane Adhesives: Electrically conductive polyurethane adhesives are designed to provide both electrical conductivity and strong bonding properties. They are formulated with polyurethane polymers and conductive fillers, such as carbon or metal particles. These adhesives offer good adhesion to various substrates, resistance to environmental factors, and durability. They are commonly used in electronic manufacturing, grounding applications, and bonding of dissimilar materials.
- Conductive Instant Adhesives: Conductive instant adhesives, also known as cyanoacrylate adhesives, are single-component adhesives that cure rapidly upon contact with moisture. These adhesives, such as metal or graphite particles, contain conductive fillers that provide electrical conductivity. They offer fast bonding and high strength, making them suitable for applications that require quick assembly and good electrical performance.
It is important to note that the choice of electrical bonding adhesive depends on the specific application requirements, such as the substrate materials, environmental conditions, and desired electrical conductivity. Consulting with adhesive manufacturers or experts in the field can help select the most appropriate adhesive for a particular application.
Conductive vs. Non-Conductive Adhesives
Conductive and non-conductive adhesives are two distinct categories used in various applications, and the primary difference between them lies in their electrical conductivity properties. Here’s an overview of conductive and non-conductive adhesives:
Conductive Adhesives: Conductive adhesives are formulated to allow the flow of electric current. They contain conductive fillers, such as metallic or carbon particles, that provide electrical conductivity. Conductive adhesives are commonly used in applications where electrical continuity is required. Some key characteristics of conductive adhesives include:
- Electrical Conductivity: Conductive adhesives offer excellent electrical conductivity due to the presence of conductive fillers. They can create reliable electrical connections between conductive components, such as bonding electrical traces on circuit boards or grounding applications.
- Bonding and Mechanical Strength: Conductive adhesives provide electrical conductivity and mechanical solid bonding properties. They can create robust bonds between substrates, ensuring structural integrity and long-term reliability.
- Application Flexibility: Conductive adhesives come in various forms, including epoxy, silicone, and polyurethane, offering flexibility regarding application methods and substrates. They can be dispensed as liquids, films, or pastes, allowing versatility in different assembly processes.
- EMI/RFI Shielding: Conductive adhesives are often used for shielding electromagnetic interference (EMI) and radio frequency interference (RFI). They can create conductive paths, effectively minimizing the impact of electromagnetic radiation on sensitive electronic components.
Non-Conductive Adhesives: Non-conductive or insulating adhesives do not conduct electricity, and they are formulated to provide electrical insulation between components or substrates. Non-conductive adhesives are widely used in applications where electrical isolation is required. Here are some critical characteristics of non-conductive adhesives:
- Electrical Insulation: Non-conductive adhesives have high resistivity, preventing the flow of electric current. They are used to create electrical barriers, insulating components from each other or the surrounding environment.
- Dielectric Strength: Non-conductive adhesives exhibit high dielectric strength, which can withstand electrical stress without breakdown. This property is crucial in applications with high voltages, such as power electronics or electrical insulation.
- Thermal Stability: Non-conductive adhesives often possess excellent thermal stability, allowing them to maintain their electrical insulation properties under elevated temperatures. This characteristic is essential in applications where heat dissipation is a concern.
- Environmental Resistance: Non-conductive adhesives are designed to withstand various environmental factors, including moisture, chemicals, and temperature fluctuations. They offer long-term reliability in challenging operating conditions.
Non-conductive adhesives can be found in various forms, such as epoxy, acrylic, or silicone-based formulations, providing flexibility in application and substrate compatibility.
Advantages of Using Electrical Bonding Adhesives
Electrical bonding adhesives offer several advantages when creating secure and reliable electrical connections. Here are some key benefits of using electrical bonding adhesives:
- Electrical Conductivity: Electrical bonding adhesives are formulated to provide excellent electrical conductivity. They allow for the flow of electric current, ensuring reliable electrical connections between conductive components. This is crucial in applications with essential electrical continuity, such as electronic assembly, circuit board bonding, or grounding applications.
- Bonding Strength: Besides electrical conductivity, bonding adhesives offer strong mechanical bonding properties. They can create robust and durable bonds between substrates, enhancing the overall structural integrity of the assembly. This is particularly important in applications where vibration, thermal cycling, or mechanical stress may occur.
- Compatibility with Various Substrates: Electrical bonding adhesives are designed to bond to various substrates, including metals, ceramics, plastics, and composites. This versatility allows for connecting dissimilar materials and simplifies the assembly process. It eliminates the need for additional mechanical fasteners, such as screws or soldering, reducing assembly time and costs.
- Stress Distribution: Bonding adhesives distribute stress more evenly across the bonded area than other fastening methods. They can dissipate stress and reduce concentration points, minimizing the risk of localized failures or cracks in the assembly.
- Improved Heat Dissipation: Some electrical bonding adhesives, such as thermally conductive adhesives, can enhance heat dissipation in electronic devices. They provide a thermally conductive path between heat-generating components and heat sinks, allowing for efficient heat transfer and improved thermal management.
- Environmental Resistance: Electrical bonding adhesives are formulated to withstand various environmental factors, including temperature fluctuations, moisture, chemicals, and UV exposure. They offer good resistance to aging and degradation, ensuring long-term reliability in different operating conditions.
- Design Flexibility: Adhesives offer design flexibility, allowing for bonding complex shapes or irregular surfaces. They can conform to contours, fill gaps, and create strong bonds in hard-to-reach areas, enabling more versatile and efficient designs.
- Cost-Effective Solution: In many cases, using electrical bonding adhesives can be cost-effective compared to other traditional bonding methods. They eliminate the need for additional hardware or complex assembly processes, reducing material and labor costs.
- EMI/RFI Shielding: Conductive bonding adhesives can provide effective electromagnetic interference (EMI) and radio frequency interference (RFI) shielding. They create conductive paths, minimizing the impact of electromagnetic radiation on sensitive electronic components.
Overall, electrical bonding adhesives offer numerous advantages, including electrical conductivity, muscular bonding strength, compatibility with various substrates, stress distribution, heat dissipation, environmental resistance, design flexibility, cost-effectiveness, and EMI/RFI shielding. These benefits make them an important choice for many electrical and electronic applications.
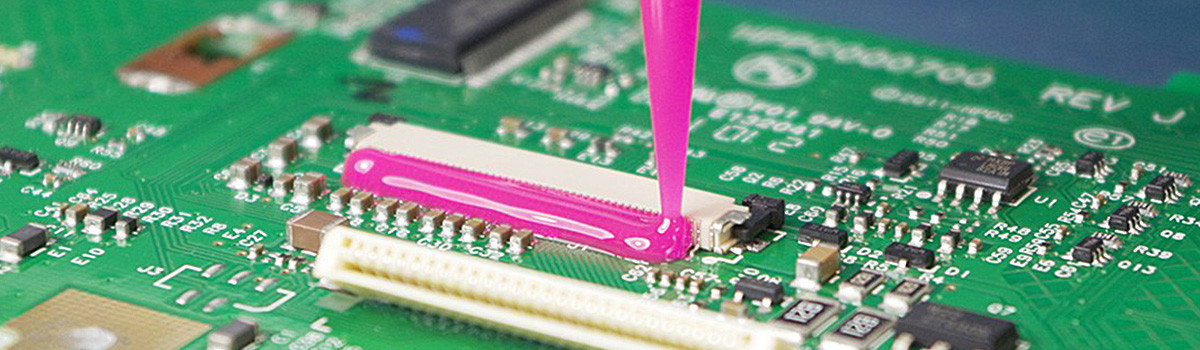
Applications of Electrical Bonding Adhesives
Electrical bonding adhesives find numerous applications across various industries where secure and reliable electrical connections are required. These adhesives offer unique properties that make them suitable for multiple applications. Here are some typical applications of electrical bonding adhesives:
- Electronics Manufacturing: Electrical bonding adhesives play a vital role in assembling and bonding electronic components. They create electrical connections between circuit boards, bonding wire leads and attach surface-mounted pieces and potting-sensitive electronic devices. These adhesives provide electrical conductivity and mechanical bonding strength, ensuring electronic device performance and long-term durability.
- Automotive Industry: The automotive industry relies on electrical bonding adhesives for various applications. They are used for bonding and grounding electrical components, such as sensors, connectors, and wiring harnesses. These adhesives ensure secure electrical connections, withstand vibration and thermal cycling, and provide environmental resistance in automotive applications.
- Aerospace and Aviation: In the aerospace and aviation sectors, electrical bonding adhesives are crucial for bonding electrical components in aircraft, satellites, and spacecraft. They are used for bonding avionics systems, antennas, sensors, and grounding applications. These adhesives must offer high reliability, durability, and resistance to extreme temperature variations and vibrations.
- Medical Devices: Electrical bonding adhesives manufacture medical devices and equipment. They are used for bonding electrodes, connectors, sensors, and wiring in various medical applications, including monitoring devices, diagnostic equipment, and implantable devices. These adhesives must meet stringent requirements for biocompatibility, sterilization resistance, and long-term reliability.
- Renewable Energy: Electrical bonding adhesives are used in the renewable energy sector, particularly in manufacturing solar panels. They are used for bonding and grounding electrical connections within solar panels, such as bonding solar cells, attaching bus bars, and connecting electrical cables. These adhesives must provide reliable electrical conductivity, weather resistance, and long-term durability in outdoor environments.
- Telecommunications: In the telecommunications industry, electrical bonding adhesives are employed for bonding electrical connections in communication devices, antennas, connectors, and fiber optic components. These adhesives ensure secure electrical connections, EMI/RFI shielding, and resistance to environmental factors, such as moisture and temperature variations.
- Consumer Electronics: Electrical bonding adhesives assemble consumer electronics, including smartphones, tablets, laptops, and wearable devices. They are utilized for bonding electrical components, attaching displays, bonding flexible circuits, and grounding applications. These adhesives provide reliable electrical conductivity, mechanical bonding strength, and flexibility to accommodate miniaturized designs.
- Industrial Equipment: Electrical bonding adhesives find applications in various industrial equipment, such as control panels, industrial sensors, motors, and transformers. They are used for bonding electrical connections, grounding components, and EMI/RFI shielding. These adhesives must withstand harsh industrial environments, including temperature extremes, vibrations, and chemical exposure.
These are just a few examples of the wide range of applications for electrical bonding adhesives. These adhesives’ versatility, reliability, and performance make them indispensable in industries where secure electrical connections are critical for optimal functionality and safety.
Bonding and Sealing in Electronic Devices
Bonding and sealing are two essential processes in assembling and manufacturing electronic devices, and they play a crucial role in ensuring electronic components’ reliability, functionality, and protection. Here’s an overview of bonding and sealing in electronic devices:
Bonding refers to joining two or more components using an adhesive material. In electronic devices, bonding is used for various purposes, including electrical connections, mechanical support, and thermal management. Here are some critical aspects of bonding in electronic devices:
- Electrical Connections: Bonding adhesives create electrical connections between components, such as bonding wires to pads on circuit boards or attaching conductive traces. These adhesives provide electrical conductivity, ensuring reliable electrical continuity in the device.
- Component Attachment: Bonding attaches components to circuit boards or substrates. Adhesive materials include epoxy or silicone-based adhesives, bond components like surface-mounted devices (SMDs), connectors, sensors, or displays. This ensures secure and mechanically strong adhesion of components.
- Structural Support: Bonding adhesives provide structural support to electronic components. They create strong bonds that help withstand mechanical stresses, vibrations, and thermal cycling. This is especially important for features that may experience mechanical strain or external forces.
- Heat Dissipation: In devices with critical heat dissipation, bonding adhesives with thermal conductivity properties are used. These adhesives help transfer heat from heat-generating components, such as power transistors or LEDs, to heat sinks or other thermal management solutions.
Sealing: Sealing involves the application of a protective material to prevent the ingress of moisture, dust, or other contaminants into electronic devices. Sealing is essential to enhance the reliability and longevity of electronic components and systems. Here are some critical aspects of sealing electronic devices:
- Environmental Protection: Sealing adhesives, such as silicone-based materials, create a barrier that protects electronic components from moisture, humidity, and environmental contaminants. This is particularly important for devices exposed to harsh environments, such as outdoor electronics or automotive applications.
- Waterproofing: Sealing is critical for achieving water or dust resistance in electronic devices, especially in outdoor or rugged environments. Sealing materials are applied to enclosures, connectors, or openings to prevent water or dust penetration, ensuring device performance and longevity.
- Chemical Resistance: Sealing adhesives can resist chemical exposure, protecting electronic components from corrosive substances or chemical vapors. This is important in applications where electronic devices may come into contact with chemicals or aggressive environments.
- Insulation and Dielectric Properties: Sealing materials often possess excellent insulating properties, providing electrical insulation between components or traces. This helps prevent short circuits and electrical failures. Sealing adhesives with high dielectric strength are used in applications requiring electrical isolation.
- Vibration and Shock Resistance: Sealing adhesives help enhance the mechanical stability of electronic devices by providing resistance to vibrations and shocks. They prevent internal components from loosening or shifting due to mechanical stress, ensuring the long-term reliability of the device.
Bonding and sealing are crucial processes in assembling and manufacturing electronic devices, and they ensure reliable electrical connections, mechanical stability, protection against environmental factors, and longevity of the devices. The choice of bonding and sealing materials depends on the device’s application, operating conditions, and desired performance characteristics.
Automotive Applications
Electrical bonding adhesives have numerous applications in the automotive industry, where they play a crucial role in ensuring reliable electrical connections, structural integrity, and overall performance. Here are some critical automotive applications of electrical bonding adhesives:
- Wire Harness Assembly: Wire harnesses are essential components in automotive electrical systems that transmit electrical signals and power throughout the vehicle. Electrical bonding adhesives secure and protect wire harnesses, providing mechanical support, strain relief, and resistance to vibration and temperature fluctuations. These adhesives ensure the longevity and reliability of wire harnesses in challenging automotive environments.
- Sensor Bonding: Various sensors are employed in automotive systems, including engine sensors, position sensors, and proximity sensors. Electrical bonding adhesives bond these sensors to their mounting locations, providing secure attachment and ensuring accurate and reliable sensor readings. These adhesives offer mechanical stability, protection against vibrations, and resistance to temperature and moisture.
- Connector Bonding: Connectors are critical components in automotive electrical systems, facilitating electrical connections between subsystems and components. Electrical bonding adhesives bond connectors to circuit boards or other mounting surfaces, ensuring secure electrical connections and mechanical stability. These adhesives resist shock, vibration, and temperature cycling, which are common in automotive applications.
- Electronic Control Units (ECUs): ECUs are central components in modern automotive systems, responsible for controlling various functions, such as engine management, braking, and safety systems. Electrical bonding adhesives assemble ECUs, providing electrical connections, mechanical support, and protection against environmental factors. These adhesives offer excellent electrical conductivity, thermal management, and resistance to moisture, chemicals, and temperature variations.
- Lighting Systems: Automotive lighting systems, including headlights, taillights, and interior lighting, require secure bonding for electrical connections and mechanical stability. Electrical bonding adhesives attach lighting components, such as LEDs, to their mounting locations, ensuring reliable electrical connections and resistance to vibrations and thermal cycling. These adhesives offer high transparency, allowing optimal light transmission and long-term durability.
- Battery Pack Assembly: In electric and hybrid vehicles, battery packs are critical components that require secure bonding for electrical connections and structural integrity. Electrical bonding adhesives are used in battery pack assembly, providing adhesion and sealing properties to ensure reliable electrical conductivity, vibration resistance, and protection against moisture and thermal cycling. These adhesives contribute to the safety and performance of electric vehicle batteries.
- EMI/RFI Shielding: Electrical bonding adhesives with conductive properties are used for electromagnetic interference (EMI) and radio frequency interference (RFI) shielding in automotive applications. They create conductive paths, reducing the impact of electromagnetic radiation on sensitive electronic components. EMI/RFI shielding adhesives are used in areas such as electronic modules, antennas, and wiring to ensure the proper functioning of automotive electronics.
- Structural Bonding: In some automotive applications, electrical bonding adhesives are used for structural bonding purposes. They provide strong adhesion between different substrates, enhancing the overall structural integrity of automotive components. Structural bonding adhesives, for example, are used in bonding vehicle body panels, reinforcing brackets, or bonding composite materials, contributing to weight reduction and improved vehicle performance.
These are just a few examples of the wide range of automotive applications for electrical bonding adhesives. The properties of these adhesives, such as electrical conductivity, mechanical strength, environmental resistance, and thermal management, make them essential in the assembly and performance of automotive electrical systems and components.
Aerospace Applications
Electrical bonding adhesives play a critical role in aerospace applications, where they are used for various purposes, including electrical bonding, grounding, structural bonding, and protection against environmental factors. Here are some critical aerospace applications of electrical bonding adhesives:
- Avionics Systems: Avionics systems, including flight control systems, communication systems, and navigation systems, rely on secure electrical connections and grounding. Electrical bonding adhesives bond and ground components within avionics enclosures, ensuring reliable electrical continuity, mechanical stability, and protection against vibrations, temperature variations, and electromagnetic interference.
- Aircraft Wiring and Harnesses: Aircraft wiring and harnesses are complex networks of electrical cables and connectors that transmit power and signals throughout the aircraft. Electrical bonding adhesives protect the wiring and harnesses, providing strain relief, mechanical support, and resistance to vibration and environmental factors. These adhesives ensure the longevity and reliability of electrical connections in demanding aerospace environments.
- Antenna Mounting: Antennas are crucial in aerospace applications, enabling communication, navigation, and data transmission. Electrical bonding adhesives bond antennas to their mounting surfaces, providing secure attachment, electrical continuity, and resistance to mechanical stress, vibrations, and temperature variations. These adhesives contribute to the performance and durability of aerospace antenna systems.
- Composite Bonding: Aerospace structures increasingly incorporate composite materials offering high strength-to-weight ratios. Electrical bonding adhesives are used for composite components, such as fuselage panels, wing systems, and control surfaces. These adhesives provide strong and durable bonds, contributing to the structural integrity of the aircraft and reducing weight.
- Satellite and Spacecraft Electronics: Satellites and spacecraft require reliable electrical connections and protection against harsh space conditions. Electrical bonding adhesives assemble satellite and spacecraft electronics, such as electronic control units, sensors, and communication systems. These adhesives offer electrical conductivity, mechanical stability, resistance to thermal cycling and vacuum conditions, and protection against radiation.
- Lightning Strike Protection: Lightning strikes pose a significant risk to aircraft. Electrical bonding adhesives and conductive materials are used in lightning strike protection systems. These adhesives help create conductive paths that safely channel lightning current away from critical components, reducing the risk of damage and ensuring the aircraft’s and its occupants’ safety.
- EMI/RFI Shielding: In aerospace applications, electromagnetic interference (EMI) and radio frequency interference (RFI) shielding are crucial to prevent interference with sensitive electronic systems. Electrical bonding adhesives with conductive properties are used for EMI/RFI shielding. They provide a conductive path, reducing the impact of electromagnetic radiation on electronic components and ensuring proper functionality.
- Thermal Management: Aerospace systems often face extreme temperature variations. Electrical bonding adhesives with thermal conductivity properties are used for effective heat dissipation and thermal management. They help transfer heat away from heat-generating components, such as power electronics or thermal interfaces, to improve aerospace systems’ overall performance and reliability.
These are just a few examples of the wide range of aerospace applications for electrical bonding adhesives. The properties of these adhesives, such as electrical conductivity, mechanical strength, environmental resistance, and thermal management, are critical for ensuring the reliability, functionality, and safety of aerospace components and systems.
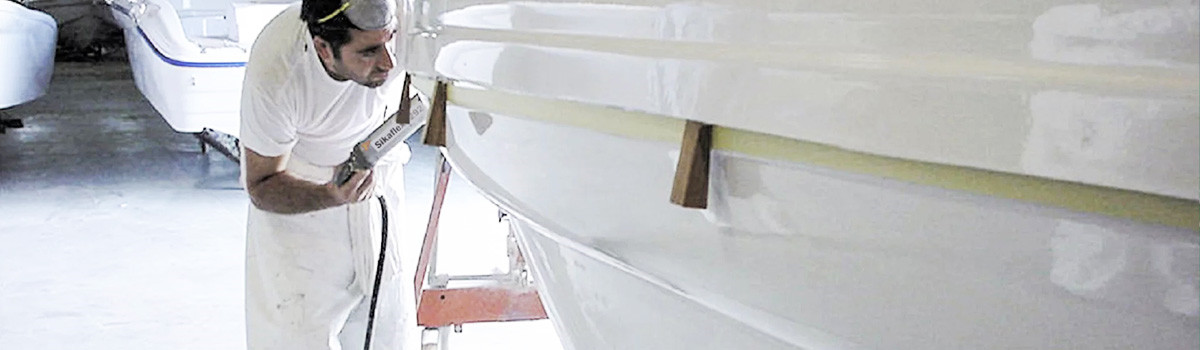
Marine Applications
Electrical bonding adhesives have significant applications in the marine industry, where they are used for various purposes, including electrical bonding, grounding, corrosion protection, and sealing. Here are some critical marine applications of electrical bonding adhesives:
- Electrical Bonding and Grounding: Electrical bonding adhesives create reliable electrical connections and grounding in marine vessels. They bond and secure electrical cables, connectors, and grounding straps, ensuring proper electrical continuity and minimizing the risk of electrical faults or failures. These adhesives provide excellent conductivity, resistance to corrosion, and mechanical stability in marine environments.
- Electronics and Instrumentation: Marine vessels rely on complex electronic systems for navigation, communication, control, and monitoring. Electrical bonding adhesives are used to assemble and install electronic components, such as control panels, instrumentation systems, and communication devices. These adhesives ensure secure bonding, electrical connections, and protection against environmental factors like moisture, vibrations, and temperature variations.
- Lighting Systems: Electrical bonding adhesives find applications in marine lighting systems, including navigation lights, interior lights, and underwater lights. They bond light fixtures, LED modules, or lighting components to the vessel’s structure, ensuring electrical connections and mechanical stability. These adhesives resist water ingress, corrosion, and vibrations, contributing to the longevity and performance of marine lighting systems.
- Anticorrosion Protection: Marine vessels are constantly exposed to corrosive seawater, which can damage metal components and structures. Electrical bonding adhesives with anticorrosion properties protect metal surfaces from corrosion. These adhesives form a protective barrier, preventing direct contact with seawater and offering resistance to corrosion. They are applied to areas such as hulls, deck fittings, and underwater equipment to enhance the durability and lifespan of marine vessels.
- Sealing and Waterproofing: Sealing adhesives are employed in marine applications to provide waterproofing and sealing properties. They seal cable entries, connectors, through-hull fittings, and other openings in the vessel’s structure. These adhesives prevent water ingress, protecting sensitive electrical components and maintaining the integrity of the vessel. They resist saltwater, UV radiation, and temperature fluctuations, ensuring long-term sealing effectiveness.
- Bonding of Fiberglass and Composite Components: Fiberglass and composite materials are extensively used in the construction of marine vessels due to their lightweight and high-strength properties. Electrical bonding adhesives are utilized for bonding and securing fiberglass and composite components, such as hulls, decks, and structural reinforcements. These adhesives provide strong and durable bonds, enhancing the vessel’s structural integrity.
- EMI/RFI Shielding: Marine vessels often have sensitive electronic equipment that requires protection against electromagnetic interference (EMI) and radio frequency interference (RFI). Electrical bonding adhesives with conductive properties are used for EMI/RFI shielding in marine applications. They create conductive paths, reducing the impact of electromagnetic radiation on electronic components and ensuring proper functionality and reliability.
- Repair and Maintenance: Electrical bonding adhesives are also used for repair and maintenance purposes in the marine industry. They can fix electrical connections, secure loose components, repair damaged wiring, and reinforce weakened structures. These adhesives offer quick and reliable bonding solutions, allowing for efficient repairs and minimizing downtime.
These are just a few examples of the wide range of marine applications for electrical bonding adhesives. The properties of these adhesives, such as electrical conductivity, corrosion resistance, sealing effectiveness, and mechanical strength, make them essential for ensuring reliable electrical connections, protection against environmental factors, and the overall performance of marine vessels and equipment.
Medical Applications
Electrical bonding adhesives have essential applications in the medical field, where they are used for various purposes, including electrode attachment, medical device assembly, patient monitoring, and electrical stimulation. Here are some critical medical applications of electrical bonding adhesives:
- Electrode Attachment: Electrical bonding adhesives attach electrodes to the skin for medical monitoring and diagnostic purposes. These adhesives provide secure bonding, ensuring reliable electrical contact between the electrode and the skin. They offer excellent biocompatibility, conformability, and adhesion properties to maintain proper electrode placement, enhance signal quality, and minimize patient discomfort.
- Medical Device Assembly: Electrical bonding adhesives are crucial in assembling various medical devices. They bond and secure components such as sensors, connectors, printed circuit boards, and cables within medical devices. These adhesives provide electrical conductivity, mechanical stability, and protection against environmental factors, contributing to the overall performance and reliability of the devices.
- Patient Monitoring: Electrical bonding adhesives are utilized in patient monitoring systems, such as ECG (electrocardiogram), EEG (electroencephalogram), and EMG (electromyogram) devices. They are used to attach electrodes or sensors to the patient’s body, ensuring proper electrical connections and signal acquisition. These adhesives offer strong bonding, reliable electrical conductivity, and long-term adhesion, enabling accurate and continuous patient monitoring.
- Electrical Stimulation: Electrical bonding adhesives play a role in electrical stimulation therapies, such as transcutaneous electrical nerve stimulation (TENS) or neuromuscular electrical stimulation (NMES). They are used to attach stimulation electrodes to the skin, delivering electrical currents to targeted areas. These adhesives provide secure bonding, reliable electrical contact, and patient comfort during stimulation treatments.
- Wound Closure: Electrical bonding adhesives find applications in techniques such as electrical wound closure (EWC) or electrosurgical procedures. They secure wound edges and facilitate electrical current flow during the healing process. These adhesives offer strong bonding, electrical conductivity, and compatibility with the surrounding tissues, aiding in wound closure and healing.
- Medical Sensors and Wearables: Electrical bonding adhesives assemble medical sensors and wearable devices, such as biosensors, glucose monitors, and health trackers. They provide secure attachment of sensors to the skin or other surfaces, ensuring proper signal acquisition and reliable data transmission. These adhesives offer biocompatibility, flexibility, and long-term adhesion to facilitate comfortable and accurate monitoring.
- Rehabilitation and Prosthetics: Electrical bonding adhesives play a role in repair and prosthetic devices. They are used to attach electrodes, sensors, or components of assistive devices to the body or prosthetic interfaces. These adhesives provide reliable electrical connections, mechanical stability, and long-lasting adhesion, contributing to the functionality and usability of rehabilitation and prosthetic systems.
- Medical Research and Development: Electrical bonding adhesives are employed in medical research and development settings. They are used for prototyping, testing, and assembly of custom electronic circuits, sensors, or experimental setups. These adhesives offer flexibility, ease of use, and reliable electrical connections, allowing researchers to create innovative medical devices and systems.
These are just a few examples of the wide range of medical applications for electrical bonding adhesives. The properties of these adhesives, such as biocompatibility, electrical conductivity, adhesion strength, and environmental resistance, are critical for ensuring safe and reliable performance in medical settings.
Factors to Consider when Choosing Electrical Bonding Adhesives
When choosing electrical bonding adhesives, several factors should be considered to ensure the suitability and effectiveness of the adhesive for the intended application. Here are some key factors to consider:
- Electrical Conductivity: The electrical conductivity of the adhesive is crucial for applications where electrical connections or grounding is required. Depending on the specific requirements, such as low resistance or specific conductivity levels, the adhesive should have appropriate conductivity properties to ensure reliable electrical performance.
- Substrate Compatibility: Consider the types of substrates involved in the bonding application. The adhesive should be compatible with bonded materials like metals, plastics, composites, or glass. Compatibility includes both chemical compatibilities to avoid degradation or corrosion of the substrate and mechanical compatibility to ensure strong adhesion to the substrate surface.
- Environmental Resistance: Evaluate the environmental conditions to which the adhesive will be exposed. Consider factors such as temperature variations, moisture, chemicals, UV radiation, and other specific environmental conditions relevant to the application. The adhesive should resist these conditions to maintain its performance and adhesion strength over time.
- Bond Strength and Durability: Assess the required bond strength and durability for the specific application. Factors such as load-bearing capacity, resistance to vibrations, impact, and cyclic stress should be considered. The adhesive should provide sufficient bond strength and durability to ensure long-term reliability and performance in operating conditions.
- Cure Time and Process: Consider the adhesive’s curing mechanism and cure time. Depending on the application requirements, choose between adhesives that cure at room temperature (ambient cure) or those that require heat, moisture, or UV exposure for curing. The cure time should align with the production or assembly process to allow for efficient bonding and minimize production time.
- Application Method: Consider the application method and equipment available for applying the adhesive. Some adhesives are suitable for manual application, while others may require specialized dispensing or application equipment. The viscosity and rheological properties of the adhesive should be compatible with the chosen application method to ensure proper adhesive coverage and bonding.
- Regulatory Compliance: Adherence to specific industry standards and regulations may be required for certain applications, such as medical devices or aerospace components. Ensure that the chosen adhesive complies with relevant industry standards, such as biocompatibility, flammability, or safety regulations, to meet the application’s specific requirements.
- Service and Support: Evaluate the availability of technical support, product documentation, and assistance from the adhesive manufacturer or supplier. Consider their expertise in the field and ability to provide guidance or address any questions or concerns related to the adhesive selection, application, or performance.
By carefully considering these factors, you can select the most suitable electrical bonding adhesive for your specific application, ensuring optimal performance, reliability, and longevity of the bonded components or systems.
Cure Time and Temperature
Cure time and temperature are important considerations when working with electrical bonding adhesives. The cure time refers to the duration required for the bond to reach its full strength and bonding properties. The temperature, on the other hand, affects the cure rate and the adhesive’s overall performance. Here are some key points to understand about cure time and temperature in electrical bonding adhesives:
Cure Time:
- Cure time can vary significantly depending on the type of adhesive and its formulation. It can range from a few minutes to several hours or even days.
- Faster cure times are desirable in many applications as they reduce assembly time and allow for quick handling and further processing of bonded components.
- Longer cure times may be necessary for applications where precise alignment or adjustments are required before the adhesive sets.
- Cure time can be influenced by factors such as adhesive thickness, environmental conditions (humidity, temperature), and the presence of accelerators or curing agents.
Temperature Considerations:
- Adhesive manufacturers provide recommended curing temperature ranges for their products. It is essential to follow these guidelines for optimal adhesive performance.
- Temperature affects the rate of cure. Higher temperatures generally accelerate the curing process, while lower temperatures slow it down. However, excessively high temperatures can cause adhesive degradation or undesirable side effects.
- Adhesives may have a minimum and maximum temperature range for curing. Operating outside these temperature limits can result in incomplete or compromised curing, reducing bond strength and durability.
- Some adhesives require specific curing temperature profiles involving a gradual increase or decrease in temperature to achieve optimal bonding properties.
- It is crucial to consider the temperature limitations of the substrates being bonded. Some materials may be sensitive to high temperatures and deform or experience thermal damage.
Heat Curing vs. Room Temperature Curing:
- Some electrical bonding adhesives require heat curing, subjecting the bond to specific elevated temperatures for a defined duration. Heat curing can provide faster cure times and improved adhesive properties.
- Room temperature curing adhesives, or ambient cure adhesives, cure naturally without additional heat. They cure at average room temperature and typically require longer cure times compared to heat-cured bonds.
- The choice between heat curing and room temperature curing depends on the specific application requirements, production processes, and equipment availability.
It is essential to carefully follow the manufacturer’s instructions and recommendations regarding cure time and temperature for the specific adhesive. Deviating from the recommended guidelines may compromise the adhesive’s performance, resulting in weakened bonds or adhesive failure. Proper cure time and temperature control contribute to achieving the desired bond strength, durability, and overall reliability of the bonded assemblies or components.
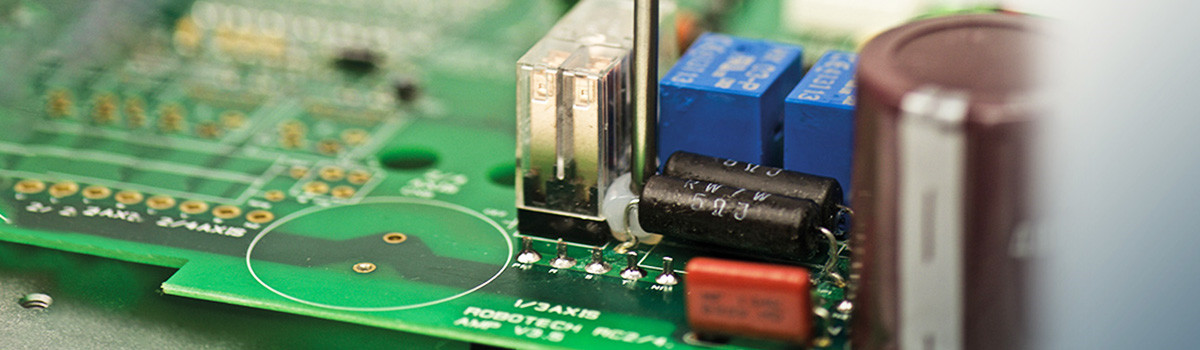
Chemical Resistance
Chemical resistance is an important consideration when selecting electrical bonding adhesives, especially in applications that expose the adhesive to various chemicals, solvents, or aggressive environments. The chemical resistance of a bond determines its ability to maintain its integrity, adhesion strength, and overall performance when in contact with specific chemicals. Here are some key points to understand about the chemical resistance of electrical bonding adhesives:
- Chemical Compatibility: Different adhesives have varying levels of resistance to specific chemicals. It is crucial to assess the compatibility of the adhesive with the chemicals it may come into contact with during its service life. This includes considering the types of chemicals, their concentrations, and the duration of exposure.
- Chemical Types: Chemical resistance can vary depending on the specific chemical types, such as acids, bases, solvents, oils, fuels, cleaning agents, or industrial chemicals. Some adhesives may exhibit good resistance to certain chemicals but may be susceptible to others. It is essential to evaluate the compatibility of the adhesive with the specific chemicals relevant to the application.
- Swelling and Degradation: When an adhesive is exposed to chemicals, it may swell, soften, or undergo degradation, leading to a loss of adhesion strength and overall performance. Selecting an adhesive that exhibits minimal or no swelling and degradation when in contact with the expected chemicals is essential.
- Temperature Considerations: Chemical resistance can also be influenced by temperature. Some adhesives may exhibit good resistance to certain chemicals at ambient temperatures but may be less resistant at elevated temperatures. Considering the operating temperature range and assessing the adhesive’s chemical resistance under those conditions is essential.
- Testing and Data: Adhesive manufacturers typically provide data sheets or technical information that specify the chemical resistance properties of their products. These resources can help evaluate the adhesive’s compatibility with specific chemicals and aid in selecting the appropriate adhesive for the intended application.
- Coatings and Sealants: In some cases, additional protective coatings or sealants may be applied over the adhesive to enhance chemical resistance. These coatings can provide an extra layer of protection against chemicals and further enhance the bonded assembly’s overall durability and chemical compatibility.
- Application-Specific Requirements: Different applications have different chemical exposure requirements. For example, in the automotive industry, adhesives used in fuel system components must exhibit excellent resistance to fuels and hydrocarbons. It is essential to understand the specific chemical exposure conditions of the application and choose an adhesive that meets those requirements.
Considering the chemical resistance of electrical bonding adhesives is crucial to ensure the long-term reliability and performance of the bonded assemblies or components. Selecting an adhesive with appropriate chemical resistance properties for the specific application helps prevent adhesive failure, maintain strong bonds, and ensure the system’s overall integrity in the presence of aggressive chemical environments.
Electrical Conductivity
The electrical conductivity of electrical bonding adhesives is a critical property in applications where electrical connections or grounding is required. Electrical conductivity refers to the ability of a material to allow the flow of electrical current. Here are some key points to understand about the electrical conductivity of electrical bonding adhesives:
Conductive vs. Non-Conductive Adhesives: Electrical bonding adhesives can be broadly categorized into two types based on their electrical conductivity: conductive and non-conductive adhesives.
- Conductive Adhesives: These adhesives are formulated with conductive fillers, such as metallic particles or fibers, that facilitate the flow of electrical current. Conductive adhesives offer low electrical resistance, allowing efficient electrical conduction between the bonded components. They are commonly used in applications requiring electrical continuity, such as grounding, electromagnetic interference (EMI) shielding, or electrical connections.
- Non-Conductive Adhesives: Non-conductive adhesives, as the name suggests, do not possess inherent electrical conductivity. These adhesives are typically used in applications requiring electrical isolation or insulation. They prevent the flow of electrical current between the bonded components and can provide electrical insulation or dielectric properties.
- Electrical Resistance: The electrical conductivity of an adhesive is often expressed in terms of electrical resistance or resistivity. Electrical resistance is a measure of the opposition to the flow of electrical current through the material. Lower resistance values indicate better electrical conductivity.
- Fillers and Additives: Conductive adhesives contain fillers or additives that enhance electrical conductivity. These fillers, such as silver, copper, carbon, or graphite particles, establish conductive pathways within the adhesive matrix, facilitating the flow of electrical current. The type, size, and concentration of these fillers can influence the electrical conductivity of the adhesive.
- Electrical Connection and Grounding: Conductive adhesives are commonly used to create electrical connections between components or for grounding. They are employed in various industries, including electronics, automotive, aerospace, and telecommunications, where reliable electrical conductivity is essential for proper device functionality and performance.
- EMI Shielding: Conductive adhesives with good electrical conductivity properties are utilized in electromagnetic shielding applications. They provide a conductive pathway for the dissipation of electromagnetic interference, protecting sensitive electronic devices or circuits from external electromagnetic radiation or noise.
- Electrical Contact Reliability: The electrical conductivity of bonding adhesives directly impacts the reliability of electrical contacts. Conductive adhesives ensure proper and consistent electrical contact between the bonded surfaces, minimizing contact resistance and preventing intermittent or unreliable connections.
- Adhesive Thickness and Contact Area: The electrical conductivity of an adhesive can be influenced by the thickness of the adhesive layer and the contact area between the bonded surfaces. Thinner adhesive layers and larger contact areas generally offer better electrical conductivity.
- Testing and Verification: The electrical conductivity of adhesives can be measured using various techniques, including four-point or two-point probe methods. These tests help assess the adhesive’s conductivity properties and ensure compliance with the required electrical specifications.
It is essential to select the appropriate type of electrical bonding adhesive based on the specific electrical conductivity requirements of the application. Conductive adhesives are suitable when electrical continuity or grounding is necessary, while non-conductive adhesives provide electrical isolation or insulation. Understanding the electrical conductivity properties of the adhesive helps ensure optimal performance, reliability, and safety in electrical bonding applications.
Thermal Stability
Thermal stability is an essential characteristic of electrical bonding adhesives, particularly in applications where the bond will be exposed to elevated temperatures. The thermal stability of an adhesive refers to its ability to maintain its integrity, adhesion strength, and overall performance under high-temperature conditions. Here are some key points to understand about the thermal stability of electrical bonding adhesives:
- Temperature Range: Adhesives have specific temperatures to maintain their performance and stability. The thermal stability of an adhesive is often described by its maximum continuous operating temperature or peak temperature resistance. Choosing a bond that can withstand the expected temperature range of the application is essential.
- Thermal Degradation: Excessive heat can cause adhesive degradation, changing physical and chemical properties. This can result in reduced adhesion strength, loss of mechanical properties, and diminished overall performance. A thermally stable adhesive resists degradation even at high temperatures, maintaining its original properties.
- Bond Strength Retention: The thermal stability of an adhesive is closely related to its ability to maintain bond strength under elevated temperatures. When exposed to high temperatures, a thermally stable adhesive should exhibit minimal bond strength reduction. It should possess a solid, durable bond between the adhered surfaces, even in challenging thermal conditions.
- Glass Transition Temperature (Tg): The glass transition temperature is an important parameter to consider when evaluating the thermal stability of an adhesive. It is the temperature at which the adhesive transitions from a rigid, glassy state to a softer, rubbery state. Adhesives with higher Tg values generally offer better thermal stability, as they can withstand higher temperatures before softening or losing their mechanical properties.
- Thermal Cycling: Some applications involve exposure to repeated thermal cycles, where the adhesive experiences alternating high and low temperatures. Thermal stability is essential in such cases, as the adhesive should withstand these temperature fluctuations without significant degradation or loss of adhesion strength. A thermally stable adhesive maintains its performance even after multiple thermal cycles.
- Heat Resistance: Adhesives used in applications involving heat-generating components or environments, such as electronics, power electronics, or lighting systems, require good heat resistance. Heat-resistant adhesives can withstand the heat generated by these components and maintain their performance without softening, melting, or losing adhesion strength.
- Thermal Conductivity: In some applications, thermal conductivity is an important consideration. Thermal conductivity refers to the ability of a material to conduct heat. Adhesives with high thermal conductivity can effectively transfer heat away from heat-sensitive components, ensuring efficient heat dissipation and preventing thermal damage.
- Testing and Data: Adhesive manufacturers typically provide technical data sheets that specify the thermal stability properties of their products. This information includes the recommended operating temperature range, thermal resistance, and other relevant thermal properties. It is essential to review this data to ensure that the adhesive meets the specific thermal stability requirements of the application.
Choosing a thermally stable adhesive is crucial to ensure long-term reliability and performance, especially in applications involving high temperatures or thermal cycling. A thermally stable adhesive maintains its adhesion strength, mechanical properties, and overall performance under high-temperature conditions, contributing to the durability and integrity of the bonded assemblies or components.
Viscosity
Viscosity is an essential property of electrical bonding adhesives that determines their flow behavior and application characteristics. It refers to the thickness or resistance to the flow of the adhesive. Understanding viscosity is crucial for proper adhesive selection and application process. Here are some key points to understand about the viscosity of electrical bonding adhesives:
- Definition and Measurement: Viscosity measures a fluid’s resistance to flow. It determines the adhesive’s ability to spread, wet surfaces, and fill gaps. Viscosity is typically measured in units such as centipoise (cP) or Pascal-seconds (Pa·s).
- Viscosity Range: Electrical bonding adhesives can have various viscosities, from low-viscosity liquids to high-viscosity pastes or gels. The appropriate viscosity depends on the application requirements, such as the size of the bond line, gap-filling capability, and ease of application.
- Flow Behavior: Adhesives can exhibit different flow behaviors depending on their viscosity. Newtonian fluids have a constant thickness regardless of the shear rate applied. On the other hand, non-Newtonian fluids may exhibit shear-thinning (decrease in density with increasing shear rate) or shear-thickening (increase in viscosity with increasing shear rate) behavior. Understanding the flow behavior helps predict the adhesive’s behavior during application and under different conditions.
- Application Methods: Viscosity affects the applicability of adhesives using various methods such as manual dispensing, automated dispensing, screen printing, or syringe dispensing. Low-viscosity adhesives flow easily and are suitable for automatic dispensing, while high-viscosity adhesives may require manual application methods or dispensing equipment capable of handling thicker materials.
- Gap Filling Capability: Viscosity plays a role in the adhesive’s ability to fill gaps or irregular bond surfaces. Lower-viscosity adhesives can flow into tight spaces or narrow gaps more efficiently, while higher-viscosity adhesives tend to stay in place and provide better gap-filling capability.
- Substrate Compatibility: Viscosity is also important when considering the compatibility of the adhesive with the substrates being bonded. Adhesives with appropriate viscosity levels ensure good wetting and contact with the substrate surfaces, promoting strong adhesion.
- Thixotropy: Some adhesives exhibit thixotropic behavior, where their viscosity decreases when subjected to shear stress or agitation but recovers when at rest. Thixotropic adhesives are easy to apply and spread during application but regain thickness quickly after application, preventing unwanted flow or sagging.
- Temperature Dependency: Viscosity can be temperature-dependent, meaning it changes with temperature. Some adhesives may become less viscous at higher temperatures, making them easier to apply or dispense. Others may exhibit higher viscosity at lower temperatures, requiring preheating or warming for optimal flow and workability.
- Material Handling: Viscosity affects the ease of material handling, such as mixing, stirring, or transferring adhesives. Higher viscosity adhesives may require additional mixing or equipment to ensure uniformity and homogeneity.
Understanding the viscosity of electrical bonding adhesives is crucial for successful application and achieving the desired bond quality. The appropriate viscosity selection ensures proper wetting and adhesion to the substrates, effective gap-filling, and ease of application. It is essential to consider the specific application requirements and consult the adhesive manufacturer’s recommendations for viscosity specifications to ensure optimal performance.
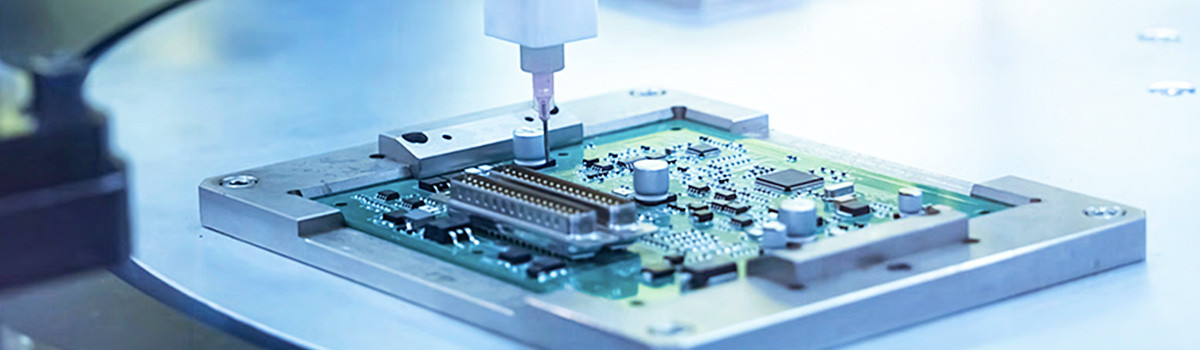
Shelf Life
The shelf life of electrical bonding adhesives refers to the period during which the adhesive can be stored and remain suitable for use. It is essential to understand the shelf life of adhesives to ensure their effectiveness and reliability when applied. Here are some key points to know about the shelf life of electrical bonding adhesives:
- Definition: The shelf life is the duration the adhesive can be stored under specified conditions without significant changes in its properties, performance, or quality.
- Expiration Date: Adhesive manufacturers typically provide an expiration date or recommended product shelf life. This date indicates the point after which the adhesive may degrade or lose effectiveness. It is essential to adhere to this expiration date to ensure optimal performance.
- Factors Affecting Shelf Life: Several factors can influence the shelf life of electrical bonding adhesives:
- Storage Conditions: Adhesives should be stored in controlled conditions to maintain stability. Factors such as temperature, humidity, and exposure to light can affect the adhesive’s shelf life. Adhesives should be stored in cool, dry areas away from direct sunlight or extreme temperature fluctuations.
- Packaging: Proper packaging is crucial in preserving the adhesive’s shelf life. Adhesives should be stored in tightly sealed containers to prevent moisture ingress, evaporation, or contamination. Containers should be labeled appropriately with the adhesive type, batch number, and expiration date for easy identification.
- Chemical Stability: Adhesives may undergo chemical reactions over time that can lead to changes in their properties. Factors such as moisture, oxygen, or exposure to reactive substances can accelerate these reactions and reduce the shelf life. Adhesives formulated with stabilizers or antioxidants may have improved chemical stability and longer shelf life.
- Storage Recommendations: Manufacturers provide specific storage recommendations for their adhesive products. These recommendations may include temperature ranges, humidity levels, and clear storage containers or conditions. It is essential to follow these guidelines to ensure the adhesive’s quality and longevity.
- Testing and Verification: If an adhesive has been stored for an extended period or beyond its expiration date, it is recommended to perform adhesive tests to verify its suitability. These tests may include measuring viscosity and adhesion strength or conducting bonding trials to assess the adhesive’s performance.
- Product Segregation: Adhesives should be stored and used on a first-in, first-out basis to ensure that older materials are used before newer ones. This practice helps prevent expired or degraded adhesives and provides the best results.
- Manufacturer’s Guidance: It is essential to refer to the manufacturer’s documentation, such as product data sheets or technical bulletins, for specific information regarding the shelf life of the adhesive. The manufacturer’s guidance considers the adhesive formulation, storage conditions, and expected performance over time.
Understanding the shelf life of electrical bonding adhesives is crucial for maintaining their effectiveness and ensuring proper performance. Adhesives that have exceeded their shelf life may exhibit reduced adhesion strength, changes in viscosity, or other detrimental effects. Adhering to appropriate storage practices, following the manufacturer’s guidelines, and regularly monitoring the expiration dates of adhesives help ensure their reliability and consistent performance when applied.
Surface Preparation
Surface preparation is a critical step in the application of electrical bonding adhesives. Proper surface preparation ensures optimal adhesion and bond strength between the adhesive and the substrate. Here are some key points to understand about surface preparation for electrical bonding adhesives:
- Cleaning: The first step in surface preparation is thoroughly cleaning the substrate surfaces. The surfaces must be free from contaminants such as dirt, dust, grease, oil, moisture, or oxidation. Cleaning can be done using solvents, detergents, or specific cleaning agents recommended by the adhesive manufacturer. The cleaning process may involve wiping, brushing, or using ultrasonic cleaning techniques depending on the substrate and the nature of the contaminants.
- Surface Roughening: In some cases, it may be necessary to roughen the substrate surface to enhance the adhesive bond strength. This is typically done using mechanical methods such as sanding, grinding, or abrasive blasting. Roughening the surface increases the surface area and provides mechanical interlocking, allowing the adhesive to form a stronger bond.
- Surface Activation: Some substrates, such as metals or certain plastics, may require surface activation to promote adhesion. Surface activation methods include chemical treatments, plasma treatments, primers, or adhesion promoters. These treatments modify the surface properties, improving the wetting and bonding characteristics of the adhesive.
- Removal of Oxidation: Removing oxidation layers is crucial for metallic substrates to ensure good adhesion. Oxidation can hinder the adhesive’s ability to bond with the substrate. Mechanical methods such as sanding or chemical treatments like acid pickling can remove the oxide layers and expose a clean surface for bonding.
- Drying and Degreasing: After cleaning and surface treatment, it is essential to thoroughly dry the substrate surfaces to remove any moisture or cleaning agents. Moisture can interfere with the adhesive’s curing process and compromise the bond strength. Additionally, degreasing the surfaces helps eliminate residual oils or contaminants that may hinder the adhesive’s ability to bond effectively.
- Surface Compatibility: Considering the compatibility between the adhesive and the substrate surface is essential. Some bonds may require specific surface characteristics or treatment methods to ensure proper bonding. The adhesive manufacturer’s recommendations should be followed to determine the appropriate surface preparation techniques for the particular adhesive and substrate combination.
- Adhesive Application: Once the surface preparation is complete, the adhesive can be applied to the prepared surfaces. Following the adhesive manufacturer’s instructions regarding the application method recommended adhesive thickness, and available time is essential. Proper application techniques, such as uniform spreading or controlled dispensing, ensure consistent coverage and bond strength.
Proper surface preparation is crucial for achieving solid and durable bonds when using electrical bonding adhesives. It promotes optimal adhesion, minimizes adhesive failure risk, and ensures bonded assemblies’ long-term reliability. Following the recommended surface preparation procedures specified by the adhesive manufacturer helps maximize the adhesive’s performance and provides successful bonding.
Handling and Storage
Proper handling and storage of electrical bonding adhesives are essential to maintain their effectiveness, quality, and shelf life. Improper handling or storage can damage adhesive, compromising performance and reducing bond strength. Here are some key points to understand about the handling and storage of electrical bonding adhesives:
Handling Precautions: When handling adhesives, it is essential to follow certain precautions to ensure safety and avoid contamination:
- Wear appropriate personal protective equipment (PPE) as the adhesive manufacturer recommends. This may include gloves, safety glasses, and protective clothing.
- Avoid contact with skin, eyes, or clothing. In case of accidental contact, rinse thoroughly with water and seek medical attention if necessary.
- Use proper ventilation in the work area to ensure adequate airflow and minimize exposure to fumes or vapors.
- Follow the manufacturer’s instructions for the proper handling techniques, including mixing ratios (if applicable) and any specific precautions.
Storage Conditions: Adhesive storage conditions are crucial in maintaining quality and effectiveness. Consider the following factors when storing electrical bonding adhesives:
- Temperature: Adhesives should be stored within the manufacturer’s recommended temperature range. Extreme high and low temperatures can affect the adhesive’s performance and shelf life. Keeping adhesives in a cool, dry place away from direct sunlight and heat sources is generally recommended.
- Humidity: Moisture can negatively impact the adhesive’s properties and cause premature curing or degradation. Adhesives should be stored in low-humidity environments to prevent moisture absorption. Keep containers tightly sealed to minimize moisture ingress.
- Shelf Life Monitoring: Adhesive containers should be labeled with the batch number, manufacture date, and expiration date. Implement a first-in, first-out (FIFO) system to use older adhesive inventory first and prevent the use of expired materials.
- Compatibility: Some adhesives may have specific storage requirements based on their formulation. Follow the manufacturer’s recommendations for storage temperature, humidity levels, and other instructions to maintain the adhesive’s quality.
Container Handling: Adhesive containers should be handled with care to prevent leaks, spills, or contamination:
- Ensure containers are tightly sealed after use to prevent air exposure and moisture ingress. Follow the manufacturer’s instructions for proper closure techniques.
- Avoid dropping or mishandling adhesive containers, as this can cause damage to the packaging or compromise the integrity of the adhesive.
- Clean the external surfaces of the containers before opening them to prevent contamination from entering the adhesive.
- Segregation and Labeling: Store adhesives separately from incompatible materials to prevent cross-contamination or reactions. Proper labeling of containers with adhesive type, batch number, and other relevant information helps identify and track inventory accurately.
- Transportation: When transporting adhesives, ensure they are adequately packaged and secured to prevent leakage or damage. Follow any applicable regulations or guidelines for the safe transportation of adhesive materials.
Proper handling and storage of electrical bonding adhesives are crucial for maintaining their quality, performance, and shelf life. Adhering to recommended storage conditions, handling precautions, and following the manufacturer’s instructions ensure that the adhesive remains effective and reliable for bonding applications.
Safety Precautions
Safety precautions should be taken when working with electrical bonding adhesives to protect individuals and ensure a safe working environment. Adhesives may contain chemicals that can be hazardous if not handled properly. Here are some essential safety precautions to consider when working with electrical bonding adhesives:
- Personal Protective Equipment (PPE): Wear appropriate PPE to protect yourself from potential hazards. This may include gloves, safety glasses or goggles, lab coats or protective clothing, and respiratory protection if required. The PPE requirements should be determined based on the adhesive’s Material Safety Data Sheet (MSDS) and the manufacturer’s recommendations.
- Ventilation: Ensure proper ventilation in the work area to minimize exposure to fumes, vapors, or airborne particles generated during adhesive application or curing. Use local exhaust ventilation or work in well-ventilated areas to maintain air quality.
- Hazardous Chemicals: Electrical bonding adhesives may contain chemicals that can be hazardous to health. Familiarize yourself with the adhesive’s MSDS to understand the specific hazards associated with the product. Follow the manufacturer’s recommendations for safe handling, storage, and disposal of the adhesive.
- Skin Contact: Avoid direct skin contact with the adhesive. Some adhesives can cause skin irritation or allergic reactions. Wear protective gloves resistant to the specific adhesive to prevent skin contact. In case of accidental contact, wash the affected area with soap and water and seek medical attention if necessary.
- Eye Protection: Adhesives can cause eye irritation or injury if they come into contact with the eyes. Wear safety glasses or goggles to protect your eyes when working with adhesives. In case of accidental eye contact, flush the eyes with water for at least 15 minutes and seek immediate medical attention.
- Inhalation: Minimize inhalation of adhesive fumes or vapors. Work in a well-ventilated area or use respiratory protection if necessary. Follow the manufacturer’s recommendations for the appropriate respiratory protection equipment.
- Fire and Ignition Sources: Some adhesives may be flammable or have specific flammability characteristics. Take precautions to prevent the adhesive from contacting open flames, sparks, or other ignition sources. Store and use adhesives away from heat sources, and follow appropriate fire safety measures.
- Chemical Compatibility: Be aware of the adhesive’s compatibility with other materials or substances. Avoid mixing adhesives with incompatible chemicals or materials that may cause hazardous reactions.
- Storage and Disposal: Store adhesives following the manufacturer’s instructions to prevent leaks, spills, or accidental exposure. Follow appropriate guidelines for safely storing and disposing of adhesive containers and waste materials.
- Emergency Preparedness: Be prepared for emergencies by having emergency eyewash stations, safety showers, and fire suppression equipment readily available in the work area. Familiarize yourself with the appropriate emergency procedures and protocols.
It is essential to consult the adhesive manufacturer’s specific safety data and instructions. Following proper safety precautions and guidelines helps protect individuals, prevent accidents, and ensure a safe working environment with electrical bonding adhesives.
Conclusion
In conclusion, electrical bonding adhesives play a critical role in ensuring the reliability and safety of electrical systems. They provide an excellent bonding and sealing solution for various applications, from electronic devices to aerospace components. Choosing a suitable adhesive requires careful consideration of several factors, including cure time, chemical resistance, and electrical conductivity. With proper handling and storage, electrical bonding adhesives can provide a long-lasting and secure bond, ensuring the optimal performance of electrical systems.