Composite Bonding Adhesive
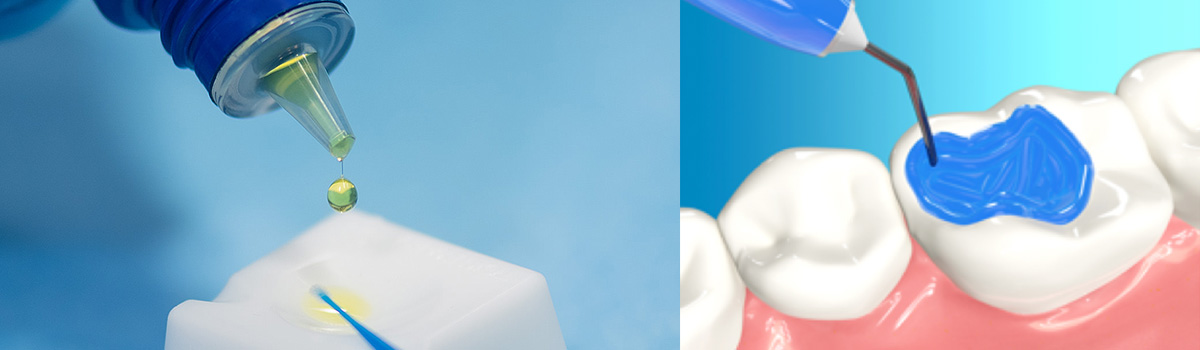
Composite bonding adhesives are used to bond two or more materials, often in the construction, automotive, and aerospace industries. There are several types of composite bonding adhesives available, including:
- Epoxy Adhesives are a popular composite bonding adhesive due to their excellent bonding strength and resistance to chemicals, heat, and moisture. Epoxy adhesives are often used in structural bonding applications.
- Acrylic Adhesives: Acrylic adhesives are known for their high strength and fast-curing properties. They are often used in automotive and industrial applications, as well as in bonding plastics and metals.
- Cyanoacrylate Adhesives: Also known as “super glue,” cyanoacrylate adhesives are fast-curing and provide solid bonds for various materials, including plastics, metals, and rubbers.
- Polyurethane Adhesives: Polyurethane adhesives are flexible and offer good bonding strength for various materials, including wood, plastics, and metals. They are often used in construction and woodworking applications.
- Silicone Adhesives: Silicone adhesives offer excellent resistance to temperature extremes, making them ideal for high-temperature applications. They are often used in automotive and aerospace applications.
- Phenolic Adhesives: Phenolic adhesives are known for their excellent bonding strength and resistance to heat and chemicals. They are often used in the aerospace and automotive industries for bonding metal components.
The choice of composite bonding adhesive will depend on the specific requirements of the application, including the types of materials being bonded, the environmental conditions the bond will be exposed to, and the required bonding strength.
Advantages of composite bonding adhesives
Composite bonding adhesives are used to bond two or more materials, often in the construction, automotive, and aerospace industries. There are several types of composite bonding adhesives available, including:
- Epoxy Adhesives are a popular composite bonding adhesive due to their excellent bonding strength and resistance to chemicals, heat, and moisture. Epoxy adhesives are often used in structural bonding applications.
- Acrylic Adhesives: Acrylic adhesives are known for their high strength and fast-curing properties. They are often used in automotive and industrial applications, as well as in bonding plastics and metals.
- Cyanoacrylate Adhesives: Also known as “super glue,” cyanoacrylate adhesives are fast-curing and provide solid bonds for various materials, including plastics, metals, and rubbers.
- Polyurethane Adhesives: Polyurethane adhesives are flexible and offer good bonding strength for various materials, including wood, plastics, and metals. They are often used in construction and woodworking applications.
- Silicone Adhesives: Silicone adhesives offer excellent resistance to temperature extremes, making them ideal for high-temperature applications. They are often used in automotive and aerospace applications.
- Phenolic Adhesives: Phenolic adhesives are known for their excellent bonding strength and resistance to heat and chemicals. They are often used in the aerospace and automotive industries for bonding metal components.
The choice of composite bonding adhesive will depend on the specific requirements of the application, including the types of materials being bonded, the environmental conditions the bond will be exposed to, and the required bonding strength.
Limitations of composite bonding adhesives
Composite bonding adhesives have become popular in dentistry for various restorative and cosmetic procedures. However, like any dental material, composite bonding adhesives have some limitations, which include the following:
- Moisture sensitivity: Composite bonding adhesives require a dry environment to bond effectively. Even small amounts of saliva or water can compromise the bond strength and durability of the restoration.
- Limited bonding strength to certain materials: Composite bonding adhesives work best on enamel and dentin but may not bond as strongly to materials like metals, ceramics, or some plastics.
- Limited thickness of application: The effectiveness of composite bonding adhesives decreases as the thickness of the adhesive layer increases. Therefore, applying the glue in thin layers is essential to achieve optimal bond strength.
- Sensitivity to light: Many composite bonding adhesives require curing with a light source, which can be a disadvantage in deep cavities or areas that are difficult to access with the curing light.
- Potential for shrinkage: Some composite bonding adhesives may experience shrinkage during the curing process, which can lead to gaps and marginal leakage.
- Degradation over time: Composite bonding adhesives may degrade due to exposure to oral fluids, chewing forces, and thermal cycling. This can lead to discoloration, deterioration of the restoration, and potential failure over time.
Considering these limitations when selecting a bonding agent and determining the appropriate application for composite bonding adhesives is essential.
Factors to consider when choosing composite bonding adhesives
When choosing composite bonding adhesives, several factors should be considered, including:
- Bond strength: The adhesive should be able to provide a solid and durable bond to the composite material and the substrate.
- Compatibility: The adhesive should be compatible with the composite material and the substrate it is bonded to. Incompatibility can result in the failure of the bond.
- Curing time: The adhesive should have an appropriate curing time for the application. Some adhesives cure quickly, while others require more time.
- Viscosity: The viscosity of the adhesive should be appropriate for the application. A low-viscosity adhesive may be easier to apply but may not be suitable for bonding thicker materials.
- Color: The adhesive color should be considered if the bond line will be visible. Some adhesives are available in various colors to match the composite material.
- Shelf life: The shelf life of the adhesive should be considered to ensure that it will remain usable for the required period.
- Chemical resistance: The adhesive should be resistant to the chemicals it will expose in the application.
- Cost: The cost of the adhesive should be considered for its performance and suitability for the application.
- Manufacturer’s recommendations: It is essential to follow the manufacturer’s recommendations for the adhesive, including application methods, curing times, and storage requirements.
How to apply composite bonding adhesives
Composite bonding adhesives are used to bond two or more surfaces together, and they are commonly used in various applications, such as automotive, construction, and manufacturing. Here are the steps to apply composite bonding adhesives:
- Clean the surfaces: It’s essential to thoroughly clean the characters to be bonded to remove any dirt, dust, or debris. Use a solvent such as isopropyl alcohol or acetone to clean the surfaces.
- Prepare the adhesive: Follow the manufacturer’s instructions to prepare the composite bonding adhesive. This may involve mixing two or more components or applying the adhesive directly from a tube.
- Apply the adhesive: Apply the adhesive to one of the surfaces using a brush or applicator. Be sure to apply the adhesive evenly and in a thin layer.
- Join the surfaces: Carefully align the characters to be bonded and press them together firmly. Apply pressure evenly across the covers to ensure a strong bond.
- Allow time to dry: The adhesive must dry and cure before the bond is complete. The amount of time required will vary depending on the type of adhesive and the environmental conditions. Follow the manufacturer’s instructions for the recommended drying and curing time.
- Finish the bond: After the adhesive has dried, you may need to trim or sand any excess material to achieve a smooth and even finish.
It’s important to note that different types of composite bonding adhesives may have other application methods and drying times. Always follow the manufacturer’s instructions and safety guidelines when working with adhesives.
Surface preparation for composite bonding adhesives
Surface preparation is critical for achieving solid and durable bonds between composite materials and adhesives. Here are some general steps for preparing the surface of composites for bonding:
- Clean the surface: Remove any dirt, dust, grease, or other contaminants from the surface of the composite material. Use a clean, lint-free cloth and an appropriate cleaning solution, such as isopropyl alcohol, to clean the surface.
- Sand the surface: Use sandpaper to lightly roughen the surface of the composite material. This will create a better bonding surface for the adhesive.
- Degrease the surface: Use a degreaser to remove any remaining contaminants from the surface of the composite material. Make sure to follow the instructions for the specific degreaser being used.
- Dry the surface: Allow the surface of the composite material to dry completely before applying the adhesive. Moisture can interfere with the bonding process.
- Apply the adhesive: Follow the manufacturer’s instructions for applying the adhesive to the surface of the composite material.
It’s important to note that the specific steps for surface preparation may vary depending on the type of composite material and adhesive being used. Always refer to the manufacturer’s instructions for guidance on proper surface preparation and bonding techniques.
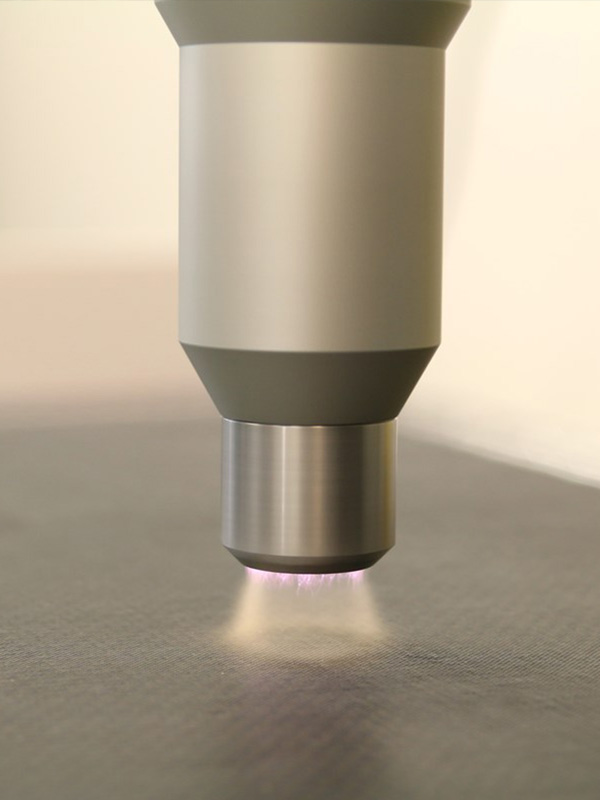
Bond strength of composite bonding adhesives
The bond strength of composite bonding adhesives can vary depending on several factors, including the specific adhesive and composite materials used, the surface preparation process, and the application and curing conditions. Generally, composite bonding adhesives can achieve high bond strength when the surfaces are adequately prepared and the adhesive is applied correctly.
The bond strength of composite bonding adhesives is typically measured using ASTM standards, such as ASTM D1002 for lap shear strength or ASTM D3163 for peel strength. The results of these tests provide information on the maximum load the bond can withstand before failure.
The bond strength of composite bonding adhesives can also be influenced by temperature, humidity, and aging factors. Environmental conditions can sometimes weaken the bond over time, leading to reduced strength and potential failure.
To ensure strong and durable bonds, following the manufacturer’s instructions for the specific adhesive being used and properly preparing the surfaces for bonding is essential. It’s also important to consider the application and environmental conditions to ensure optimal bonding performance.
The durability of composite bonding adhesives
The durability of composite bonding adhesives depends on several factors, including the specific adhesive and composite materials being used, the surface preparation process, the application and curing conditions, and the environmental conditions to which the bond will be exposed.
Composite bonding adhesives are designed to withstand various environmental conditions, including temperature, humidity, and exposure to UV radiation. However, the durability of the bond can be affected by prolonged exposure to extreme temperatures or harsh chemicals, which can weaken the adhesive and cause it to fail over time.
To ensure the durability of composite bonding adhesives, it’s essential to select the suitable adhesive for the specific application and to properly prepare the surfaces for bonding. It’s also important to consider the environmental conditions to which the bond will be exposed and to follow the manufacturer’s instructions for application and curing.
In addition, routine inspections and maintenance can help to identify and address any issues with the bond before they become more severe. This can prolong the bond’s life and ensure optimal performance over time.
Overall, composite bonding adhesives can be highly durable and provide long-lasting bonds when properly selected, prepared, and applied. However, it’s essential to consider the specific application and environmental conditions to ensure optimal bonding performance and durability.
Temperature and environmental resistance of composite bonding adhesives
Composite bonding adhesives are designed to withstand various temperatures and environmental conditions. The specific temperature and environmental resistance of composite bonding adhesives can vary depending on the particular adhesive and composite materials used.
Generally, composite bonding adhesives can withstand temperatures ranging from -40°C to 150°C or higher, depending on the specific adhesive. Some adhesives are specifically designed for high-temperature applications and can withstand temperatures up to 300°C or higher.
In terms of environmental resistance, composite bonding adhesives can be designed to withstand exposure to a variety of environmental conditions, including water, chemicals, and UV radiation. Some adhesives are specifically formulated for harsh environments, such as marine or aerospace applications, and can withstand exposure to saltwater, fuels, and other chemicals.
To ensure optimal temperature and environmental resistance of composite bonding adhesives, it’s essential to select the right adhesive for the specific application and to follow the manufacturer’s instructions for preparation, application, and curing. It’s also important to consider the particular environmental conditions to which the bond will be exposed and choose an adhesive designed to withstand those conditions.
Overall, composite bonding adhesives can provide high temperature and environmental resistance when properly selected and applied, making them a reliable choice for various applications in various industries.
Chemical resistance of composite bonding adhesives
Composite bonding adhesives, also known as structural adhesives, are used to bond materials such as metals, plastics, and composites together. The chemical resistance of these adhesives depends on the specific type of adhesive and the chemicals it comes into contact with.
Generally, composite bonding adhesives resist various chemicals, including acids, bases, solvents, and fuels. However, some substances can degrade or weaken the adhesive bond, mainly if they are in contact with the adhesive for an extended period of time or at high temperatures.
Some examples of chemicals that may affect the chemical resistance of composite bonding adhesives include:
- Strong acids, such as hydrochloric acid or sulfuric acid, can attack the adhesive and weaken the bond.
- Strong bases, such as sodium hydroxide or potassium hydroxide, can also attack the adhesive and weaken the bond.
- Solvents like acetone can dissolve the adhesive and break down the bond.
- Fuel and oil can degrade the adhesive and cause it to lose its strength over time.
It is essential to consider the chemical resistance of the adhesive when selecting a composite bonding adhesive for a specific application. The manufacturer’s datasheet for the adhesive should provide information on the chemical resistance of the adhesive and any limitations or precautions that should be taken when using it with certain chemicals.
Fatigue resistance of composite bonding adhesives
The fatigue resistance of composite bonding adhesives depends on various factors, including the type of adhesive used, the nature of the substrate, and the environmental conditions. Composite bonding adhesives generally have excellent fatigue resistance compared to traditional mechanical fastening methods, such as bolts or screws.
Composite bonding adhesives are typically made of high-strength resins, such as epoxy or acrylic, and are designed to bond two or more materials together. These adhesives can provide a robust and durable bond resistant to fatigue, corrosion, and other forms of degradation.
The fatigue resistance of composite bonding adhesives can be influenced by several factors, including the adhesive’s strength, the adhesive layer’s thickness, and the substrate’s surface preparation. In general, thicker adhesive layers and better surface preparation can improve the fatigue resistance of the bond.
Environmental conditions, such as temperature and humidity, can also affect the fatigue resistance of composite bonding adhesives. Exposure to extreme temperatures or high humidity levels can cause the adhesive to degrade and weaken over time, reducing fatigue resistance.
Overall, composite bonding adhesives can offer excellent fatigue resistance when used correctly and in the right conditions. Proper surface preparation, adhesive selection, and environmental considerations ensure a robust, durable bond that can withstand repeated stress and fatigue.
Cost of composite bonding adhesives
The cost of composite bonding adhesives can vary depending on several factors, such as the type of adhesive, the size of the container, and the quantity purchased. Generally speaking, composite bonding adhesives can be more expensive than traditional mechanical fastening methods such as screws or bolts.
The cost of composite bonding adhesives can also be influenced by the quality and performance of the adhesive. Higher-quality adhesives with better performance characteristics, such as improved fatigue or chemical resistance, may be more expensive than lower-quality adhesives.
The application of composite bonding adhesives can also affect the cost, which can increase if the bonding process requires specialized equipment, such as mixing and dispensing systems. In contrast, manual application methods may be less expensive but provide a different accuracy or consistency level than automated systems.
Another factor that can impact the cost of composite bonding adhesives is the purchase volume, and buying in larger quantities often leads to lower costs per unit.
Overall, the cost of composite bonding adhesives can vary widely depending on several factors. However, the long-term benefits of using adhesives, such as improved durability, reduced weight, and increased design flexibility, can often outweigh the initial cost.
Safety considerations for composite bonding Adhesives
While they offer many advantages over traditional mechanical fastening methods, several safety considerations must be considered when using these adhesives.
- Health Hazards: Many composite bonding adhesives contain chemicals that can be harmful to human health. These chemicals include solvents, isocyanates, and epoxy resins. Proper protective equipment should always be worn, and work areas should be well-ventilated.
- Fire Hazard: Composite bonding adhesives can be flammable or combustible. It is essential to follow proper handling procedures, such as storing adhesives in approved containers and avoiding smoking in work areas.
- Skin and Eye Contact: Exposure to composite bonding adhesives can cause skin and eye irritation or even chemical burns. Gloves and protective eyewear should be worn at all times, and spills or splashes should be cleaned immediately.
- Compatibility: Some composite bonding adhesives may not be compatible with certain materials or surfaces. It is essential to check the manufacturer’s recommendations and conduct compatibility testing before using the adhesive.
- Application and Curing: Composite bonding adhesives must be applied and cured correctly to ensure strength and durability. Following the manufacturer’s instructions carefully and allowing adequate curing time before subjecting the bond to stress or load is essential.
Applications of composite bonding adhesives in aerospace
Composite bonding adhesives are widely used in the aerospace industry for various applications due to their high strength, low weight, and durability. Here are some typical applications of composite bonding adhesives in aerospace:
- Structural Bonding: Composite bonding adhesives join structural components in aircraft, such as wings, fuselage, and tail sections. This adhesive bond provides high strength, which can help reduce the aircraft’s overall weight.
- Composite Repairs: Composite bonding adhesives are used to repair composite components of aircraft, such as wings, fuselage, and radomes. These adhesives provide a strong bond and can restore the component’s structural integrity.
- Filament Winding: Composite bonding adhesives are used to bond fibers to the mandrel in filament winding applications. The adhesive holds the threads in place during the winding process and provides structural support to the final composite component.
- Honeycomb Core Bonding: Composite bonding adhesives are used to bond honeycomb core materials to skins and other components in aircraft. The adhesive provides a strong bond that can withstand high stresses and loads.
- Surface Preparation: Composite bonding adhesives are used to prepare surfaces of composite components for bonding. The adhesive can remove contaminants and create a clean, rough surface that improves the adhesion of the bond.
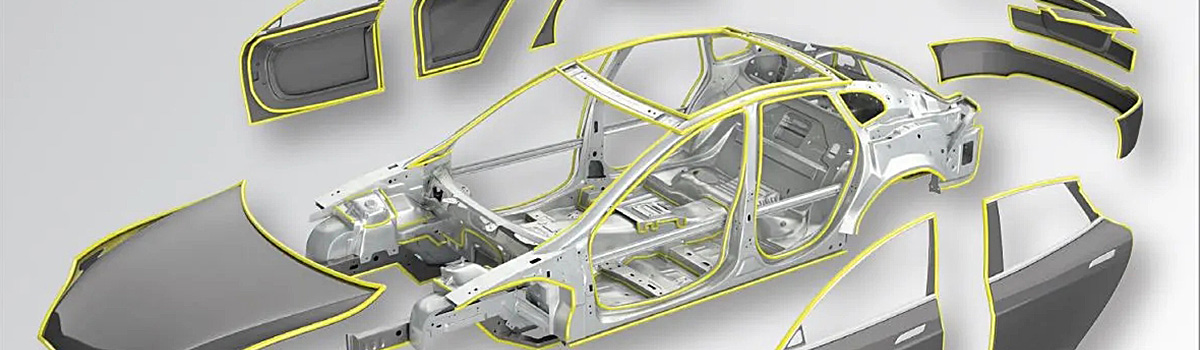
Applications of composite bonding adhesives in automotive
Composite bonding adhesives have become increasingly popular in the automotive industry due to their ability to create strong, lightweight, and durable bonds. Here are some common applications of composite bonding adhesives in automotive:
- Body panel bonding: Composite bonding adhesives often bond body panels such as doors, hoods, and trunk lids to the vehicle frame. The adhesives provide excellent strength and durability while reducing weight and improving the vehicle’s overall structural integrity.
- Windshield bonding: Windshields are typically bonded to the vehicle frame using composite bonding adhesives. This provides a strong bond that can withstand driving stresses and strains while reducing weight and improving fuel efficiency.
- Roof panel bonding: Composite bonding adhesives can be used to bond the roof panel of a vehicle to the body. This creates a strong bond that helps reduce noise and vibration while providing better aerodynamics and fuel efficiency.
- Structural bonding: Composite bonding adhesives can be used to bond structural components of a vehicle together. This includes bonding the chassis to the body, bonding suspension components, and bonding reinforcement structures. This creates a solid and durable bond that can withstand the stresses of driving.
- Interior bonding: Composite bonding adhesives can bond internal components such as dashboard panels, door trims, and seat frames. This provides a strong and durable bond that can withstand the wear and tear of daily use.
Applications of composite bonding adhesives in construction
Composite bonding adhesives are high-performance adhesives used in construction for bonding two or more composite materials. They are known for their excellent bonding properties and ability to withstand extreme environmental conditions. Here are some applications of composite bonding adhesives in construction:
- Aerospace Structures: Composite bonding adhesives are widely used in the aerospace industry for bonding composite materials such as carbon fiber, fiberglass, and Kevlar. These adhesives offer a robust and lightweight bond, essential in constructing aircraft and space vehicles.
- Automotive Manufacturing: Composite bonding adhesives are used in manufacturing cars, trucks, and other vehicles. They provide a strong bond between composite materials used in the bodywork of modern vehicles, reducing the weight of the vehicle while still maintaining structural integrity.
- Wind Turbine Blades: Composite bonding adhesives are used to construct wind turbine blades. These adhesives help to bond the various layers of composite materials that make up the blades, ensuring that they are strong enough to withstand the forces of wind and weather.
- Marine Applications: Composite bonding adhesives are used in marine applications such as boat building and repair. These adhesives provide a strong bond between composite materials used in the construction of boats and other watercraft, ensuring that they are watertight and able to withstand the rigors of marine environments.
- Building and Construction: Composite bonding adhesives are used to construct buildings and other structures. They provide a robust and durable bond between composite materials used in construction, such as composite panels, roofing, and cladding systems.
Applications of composite bonding adhesives in the marine industry
Composite bonding adhesives have become increasingly popular in the marine industry due to their high strength, durability, and corrosion resistance. Here are some applications of composite bonding adhesives in the maritime industry:
- Hull bonding: Composite bonding adhesives are used to bond the hulls of boats and ships. They provide a solid, durable bond resistant to harsh marine environments, including saltwater, UV rays, and extreme temperatures.
- Deck bonding: Composite bonding adhesives are also used to bond decks to the hull of boats and ships. This provides a robust and waterproof bond that can withstand the stresses of the sea.
- Repair of composite structures: Composite bonding adhesives repair damaged composite structures, such as hulls, decks, and other components. They provide a solid and durable bond that can restore the structural integrity of the damaged part.
- Bonding of metal components: Composite bonding adhesives can bond metal components in marine structures. They provide a strong and durable bond that is resistant to corrosion and can withstand the stresses of the sea.
- Bonding of plastic components: Composite bonding adhesives can also bond plastic components in marine structures. They provide a solid, durable bond resistant to UV rays and other environmental factors.
Applications of composite bonding adhesives in sports equipment
Composite bonding adhesives have become increasingly popular in sports equipment manufacturing due to their ability to bond lightweight and durable materials together, resulting in improved performance and durability of the equipment. Here are some applications of composite bonding adhesives in sports equipment:
- Golf clubs: Composite bonding adhesives are used to bond the clubheads to the shafts in golf clubs. This results in a more robust, lighter, and durable club, improving the golfer’s swing and accuracy.
- Hockey sticks: Composite bonding adhesives bond the blade to the shaft of hockey sticks. This results in a lighter and stronger stick, improving the player’s control and shooting accuracy.
- Bicycle frames: Composite bonding adhesives bond carbon fiber tubes to create lightweight and robust bicycle frames. This improves the rider’s performance by reducing the bike’s weight and increasing strength.
- Tennis rackets: Composite bonding adhesives bond the frame and strings together in tennis rackets. This results in a more durable and stronger noise, improving the player’s control and power.
- Ski and snowboard construction: Composite bonding adhesives are used to bond different layers of materials together in ski and snowboard construction. This results in a more durable and stronger ski or snowboard, which improves the rider’s control and performance.
Overall, composite bonding adhesives play a crucial role in manufacturing sports equipment by improving performance, durability, and strength.
Composite bonding adhesives in the medical industry
Composite bonding adhesives are commonly used in the medical industry for various applications. These adhesives are designed to bond to a wide range of materials, including metals, plastics, and ceramics, and they offer several advantages over traditional mechanical fastening methods.
One of the primary advantages of composite bonding adhesives is that they distribute stress evenly across the surface of the bond, which can help to prevent cracks and other types of damage. This can be especially important in medical applications where the adhesive is exposed to repeated stress, such as orthopedic implants.
Composite bonding adhesives are also ideal for use where weight is a concern. Unlike mechanical fasteners, composite bonding adhesives do not add extra weight to the final product. This can be important in medical devices, such as prosthetics, where weight can be a critical factor in patient comfort and mobility.
Another advantage of composite bonding adhesives is that they can be formulated to be biocompatible, which means that they do not elicit an immune response when used in the body. This makes them ideal for medical applications, such as dental fillings, where they can bond composite materials to teeth without causing adverse reactions.
Overall, composite bonding adhesives offer several advantages over traditional mechanical fastening methods in the medical industry, and their versatility and ability to be formulated to be biocompatible make them an ideal choice for many medical applications.
Composite bonding adhesives in the electronics industry
Composite bonding adhesives are commonly used in the electronics industry for bonding various components of electronic devices, such as printed circuit boards (PCBs), electronic modules, and microelectronics. These adhesives offer several advantages over traditional mechanical fastening methods, such as screws, bolts, and clips.
One of the main advantages of composite bonding adhesives is that they can distribute stresses more evenly across the bond line, which reduces the risk of mechanical failure. They also provide excellent adhesion to various substrates, including metals, plastics, ceramics, and composites.
In addition, composite bonding adhesives can improve the overall performance of electronic devices by providing thermal management and electrical insulation. They can also reduce the weight and size of electronic devices, as they eliminate the need for bulky mechanical fasteners.
Different types of composite bonding adhesives are used in the electronics industry, including epoxy, acrylic, cyanoacrylate, and silicone adhesives. Each class has unique properties and advantages, depending on the specific application.
Overall, composite bonding adhesives are versatile and practical for bonding electronic components, offering improved reliability, performance, and design flexibility.
Composite bonding adhesives in the renewable energy industry
Composite bonding adhesives play an essential role in the renewable energy industry, particularly in the manufacturing and assembly of wind turbines, solar panels, and other renewable energy equipment.
In the wind energy industry, composite bonding adhesives are used to bond the various parts of the turbine, such as the blades, nacelle, and tower. These adhesives are also used to bond the blade root to the hub, a critical connection point requiring high strength and durability. Composite bonding adhesives provide a lightweight, strong, and durable bond that can withstand the harsh environmental conditions that wind turbines are exposed to.
In the solar energy industry, composite bonding adhesives attach the solar cells to the panel substrate. These adhesives provide a high-strength bond that can withstand the thermal cycling and weathering that solar panels are exposed to.
Composite bonding adhesives are also used in other renewable energy applications, such as in manufacturing batteries and fuel cells. These adhesives provide a solid and durable bond that can withstand the harsh chemical and thermal environments these devices are exposed to.
Overall, composite bonding adhesives are an essential component of the renewable energy industry, helping to provide robust, lightweight, and durable bonds critical to the performance and reliability of renewable energy equipment.
Recent advancements in composite bonding adhesives
Recent advancements in composite bonding adhesives have focused on improving their strength, durability, and resistance to environmental factors. Some of the notable improvements include:
- Nanocomposite adhesives contain nanoparticles that enhance their mechanical and physical properties. For example, adding nanoparticles to epoxy resins can increase their strength, toughness, and thermal stability.
- Toughened adhesives: These adhesives are designed to improve the toughness and impact resistance of the bonded joint. They contain toughening agents, such as rubber particles or thermoplastic polymers, that can absorb energy and prevent crack propagation.
- Structural acrylic adhesives are gaining popularity in the automotive and aerospace industries due to their high strength, durability, and resistance to environmental factors, such as heat, moisture, and chemicals.
- Bio-based adhesives: These are made from renewable and sustainable sources, such as soybeans, corn, and lignin. They are environmentally friendly and can reduce the carbon footprint of the bonding process.
- Self-healing adhesives: These adhesives can repair themselves when damaged, either through heat, light, or other stimuli. They are helpful in applications where the bonded joint may be subjected to repeated stress or damage.
Overall, these advancements in composite bonding adhesives have improved their performance, reliability, and sustainability, making them suitable for various applications in various industries.
Nanocomposite bonding adhesives
Nanocomposite bonding adhesives are a class of adhesives that incorporate nanoparticles into their formulation to enhance their bonding properties. These adhesives typically contain nanoparticles with high surface area-to-volume ratios, such as clay nanoparticles or carbon nanotubes.
The use of nanoparticles in adhesives can improve their strength, durability, and resistance to environmental factors such as moisture and heat. The nanoparticles can also enhance the adhesion of the bond to a wide range of substrates, including metals, plastics, and composites.
In addition to improving the bonding properties of the adhesive, nanocomposite bonding adhesives can offer other benefits, such as enhanced thermal and electrical conductivity. This makes them useful in various applications, including electronics, aerospace, and automotive industries.
However, using nanoparticles in adhesives also presents challenges, such as ensuring uniform dispersion of the nanoparticles throughout the adhesive matrix and minimizing their agglomeration. Therefore, careful formulation and manufacturing processes are required to provide the optimal performance of nanocomposite bonding adhesives.
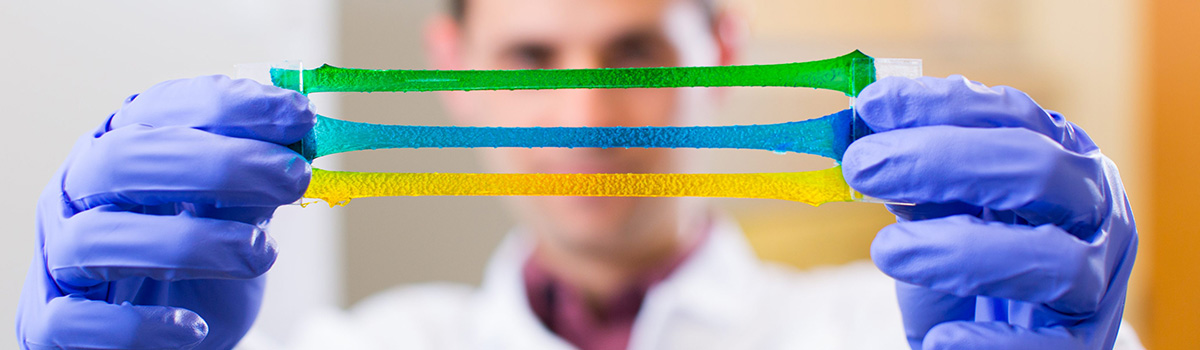
Smart composite bonding adhesives
Smart composite bonding adhesives are advanced adhesives designed for use in composite materials, which are materials made from two or more constituent materials that have significantly different physical or chemical properties. These adhesives are engineered to provide high-strength bonding between different types of materials, such as metals, plastics, and composites.
Innovative composite bonding adhesives typically contain various advanced materials, such as nanoparticles, polymers, and other additives that provide unique properties. For example, some intelligent adhesives are designed to be self-healing, meaning they can repair cracks and damage automatically, improving the durability and longevity of the bonded materials.
Other smart composite bonding adhesives may be designed to respond to external stimuli, such as temperature, pressure, or humidity changes. These adhesives can create “smart” composite materials that adapt to changing environmental conditions and improve their performance and durability.
Overall, intelligent composite bonding adhesives represent a significant advancement in composite materials, offering improved performance, durability, and versatility compared to traditional bonding adhesives.
3D printing of composite bonding adhesives
3D printing of composite bonding adhesives is an emerging technology with great promise for fabricating complex and customizable structures made from composite materials. 3D printing makes it possible to create intricate designs and geometries that would be difficult or impossible to produce with traditional manufacturing methods.
3D printing involves using a computer-controlled printer, which requires layer-by-layer material deposition, typically a thermoplastic or thermosetting polymer. In the case of composite bonding adhesives, the printing material may also contain a range of additives, such as nanoparticles, fibers, or other materials, to enhance the strength, stiffness, or other properties of the final product.
The use of 3D printing for composite bonding adhesives has several advantages. First, it allows for creation of highly customized and intricate structures with minimal waste of materials. Second, the ability to precisely control the composition and microstructure of the printed material can lead to improved mechanical properties, such as strength, stiffness, and toughness. Third, 3D printing can be a faster and more cost-effective manufacturing method than traditional techniques, such as molding or machining.
However, there are also challenges to overcome when using 3D printing for composite bonding adhesives. For example, optimizing the printing parameters, such as the printing speed and temperature, requires more work to achieve optimal bonding between the layers. Additionally, using multiple materials and additives can introduce compatibility issues that can affect the quality and performance of the printed structure.
Challenges in developing composite bonding adhesives
Developing composite bonding adhesives is a complex process that involves addressing several challenges related to these materials’ properties, performance, and application. Some of the critical challenges in developing composite bonding adhesives include the following:
- Compatibility: The compatibility between the bonding adhesive and the composite material is critical to bonding strength and durability. However, achieving good compatibility between dissimilar materials can be challenging due to differences in their physical and chemical properties.
- Adhesion strength: The power of the adhesive bond between the composite materials can be influenced by several factors, including surface preparation, curing conditions, and the properties of the adhesive. Developing adhesives with high adhesion strength and durability can be challenging, especially when bonding dissimilar materials with different coefficients of thermal expansion and other physical properties.
- Durability: Composite bonding adhesives must withstand a range of environmental conditions, including temperature and humidity fluctuations, UV radiation, and exposure to chemicals and other corrosive agents. Developing highly durable bonds that can maintain their strength and adhesion properties over time is essential.
- Processability: Composite bonding adhesives must be easy to apply and process for industrial or field applications. Developing adhesives that can be used quickly and easily without specialized equipment can be challenging.
- Cost: The cost of composite bonding adhesives can be a significant factor in their adoption and use. Developing cost-effective adhesives that can be produced at scale is essential to their commercial viability.
Future prospects of composite bonding adhesives
The future prospects for composite bonding adhesives are promising, as these materials continue to play an increasingly important role in many industries, including aerospace, automotive, construction, and marine. Some of the critical future prospects of composite bonding adhesives include the following:
- Lightweighting: Composite bonding adhesives are a critical technology for lightweight, a significant trend in many industries, including automotive and aerospace. As manufacturers look to reduce the weight of their products to improve efficiency and performance, composite bonding adhesives will play a critical role in enabling lightweight composite materials.
- Sustainability: Composite bonding adhesives can also play a key role in promoting sustainability by enabling the use of recycled or biobased materials. As concerns about environmental sustainability continue to grow, composite bonding adhesives that can be produced from renewable or recycled materials will become increasingly important.
- Innovative materials: The development of intelligent composite bonding adhesives that can respond to environmental stimuli, such as temperature or humidity, will enable the creation of new materials with enhanced performance and functionality.
- Automation: The development of automated manufacturing processes for composite bonding adhesives will enable faster and more efficient production of composite structures. As automation technologies improve, composite bonding adhesives in high-volume manufacturing applications will become increasingly feasible.
- Additive manufacturing: The use of additive manufacturing technologies, such as 3D printing, for composite bonding adhesives, will enable the creation of highly customized and complex structures with minimal waste of materials. As additive manufacturing technologies continue to improve, composite bonding adhesives in additive manufacturing applications will become increasingly widespread.
Choosing the suitable composite bonding adhesive for your project
Choosing the suitable composite bonding adhesive for your project can be critical in ensuring a solid and long-lasting bond. Here are some key factors to consider when selecting the appropriate adhesive:
- Substrate: What materials are you bonding together? Different adhesives work better with certain materials like metal, plastic, or wood.
- Environment: Will your bonded materials be exposed to extreme temperatures, moisture, or harsh conditions? Consider the environmental factors your adhesive will need to withstand.
- Strength: How much load will the bond need to hold? Consider the weight and stress on the bonded materials and choose an adhesive with the appropriate power.
- Curing time: How quickly do you need the adhesive to cure? Some adhesives cure quickly, while others take longer to fully heal.
- Application method: What is the best application method for your project? Some adhesives require specific tools or equipment, while others can be applied by hand.
- Safety: What safety precautions are necessary when working with the adhesive? Consider the potential health hazards and safety requirements for handling the glue.
Conclusion: Prospects and challenges of composite bonding adhesives
Composite bonding adhesives have emerged as an important technology in various automotive, aerospace, and construction industries. These adhesives offer numerous benefits over traditional mechanical fastening methods, including improved strength, durability, and weight reduction.
One of the key prospects of composite bonding adhesives is their ability to join dissimilar materials, which is often difficult to achieve with traditional mechanical fastening. This feature opens up new possibilities for lightweight and efficient designs in various industries, especially automotive and aerospace.
However, there are also several challenges associated with composite bonding adhesives. The primary challenge is achieving a solid and reliable bond between the two materials, and this requires carefully selecting adhesive materials, surface preparation, and proper curing conditions. In addition, the long-term durability of the adhesive bond is a critical factor, particularly in harsh environments such as extreme temperatures and moisture.
Another challenge is the high cost of composite bonding adhesives compared to traditional fastening methods. This is partly due to the complexity of the bonding process, which requires specialized equipment and skilled labor. However, the benefits of using these adhesives may offset the overall cost, such as improved performance and reduced maintenance.
In summary, composite bonding adhesives offer significant prospects for various industries, exceptionally lightweight and efficient designs. However, the challenges associated with achieving a strong and durable bond and the high cost of the bonding process should be carefully considered and addressed. Ongoing research and development in this area will be crucial to overcome these challenges and realize the full potential of composite bonding adhesives.