Heat Exchangers Adhesive
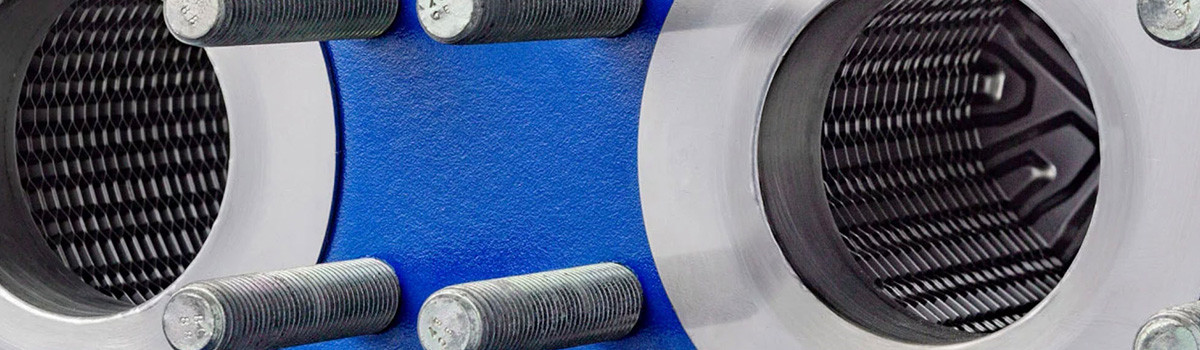
Heat exchanger assembly gluing
For the assembly of heat exchangers, Deepmaterial has several hotmelts in the range, from product assembly adhesives that attach to a variety of substrates, plastics (plastics), metals, foils, foams, etc.
Various air / air heat exchangers are assembled with Deepmaterial adhesives, the adhesives are moisture resistant, cold, and heat resistant and durable according to customer specifications.
The assembly of these dissipation blocks can be manufactured from all kinds of materials, such as plastics, metals such as aluminum sheets that are bonded together with spacers and various fasteners, possibly also with hot melt. The air / air heat exchangers created channels for the flow of indoor and outdoor air in opposite directions, hot melt can also be used instead of mounting kit and sealants. Any Polyamide hotmelts can even be used to pour in electrical components. Finally, even the filters at these heat exchangers can even be produced with our assembly and filtering hotmelts.
High temperature resistant adhesives, sealants and coatings for heat exchanger applicationsDesigned for the efficient heat transfer from one area to another, heat exchangers are widely used in a variety of industries such as power generation, food processing, automotive, chemical, HVAC, mining and oil processing. Heat from a fluid passes to a second fluid without coming into direct contact. They are usually classified in one or two ways, depending on their flow arrangement–either by parallel flow or counter flow (which is able to transfer more heat). Master Deepmaterial’s wide range of thermally conductive, high temperature resistant, toughened adhesives, sealants, coatings and encapsulation compounds are frequently selected as the right choice for heat exchanger assembly.
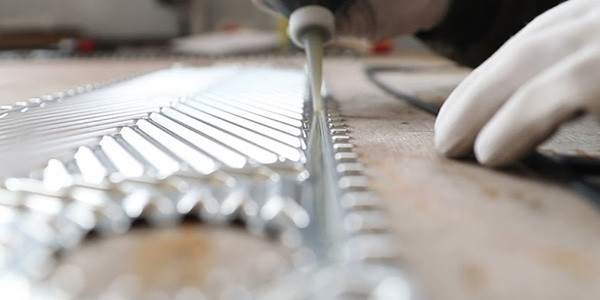
Careful consideration of flow rate, temperature differentials, ratio of heat transfer area to volume are necessary to select the proper formulation to optimize performance and best meet design parameters. Our products have proven effective in sealing tubes into end plates. They are also used for bonding heat exchange fins, bonding rubber gaskets and potting/sealing flutes in cooling devices. Most important they adhere well to metallic substrates such as aluminum, brass, copper, steel, stainless steel and many dissimilar substrates. As a substitute for welding, brazing especially when processing is a concern, these formulations offer the benefits of being easy/convenient to handle, easy to dispense, have versatile cure schedules and avoid pin prick weld holes or warping. These electrically insulative compounds prevent galvanic and crevice corrosion. They also are noted for enhancing the aesthetic appearance of the heat exchanger and offer manufacturers cost saving when purchased in small or larger quantities.
Reducing hot-melt adhesive products’ time-to-cool period prior to forming is a productivity goal for adhesives manufacturers. Often, it can take 6 to 18 hours to form and package a standard batch of adhesives, depending on the finished product form. Every minute of cooling time that can be reduced results in increased productivity as well as a process cost reduction. For some applications, says its manufacturer, the Deepmaterial’s hot-melt adhesives help the heat exchanger has been effective in reducing time-to-cool when handling viscous.
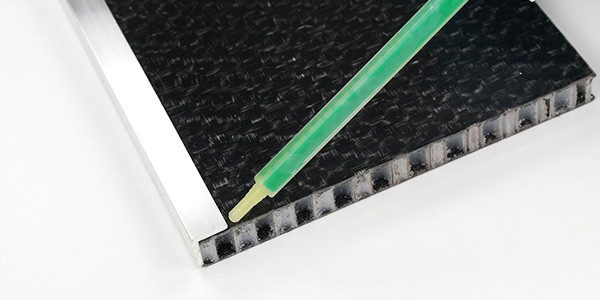
Recent years have seen an increase in the use of what are known as sealing adhesives. These are systems that come originally from sealing applications but that are also very efficient as adhesives. Most of these preferably single-component adhesive sealants have as their basis either polyurethane (PUR) or what are referred to as silane-terminated polymers (STP, MS). The term hybrid adhesive is also often used. Individual 2‑component systems and so‑called booster systems also perform well.
The strength of this process, often referred to as sealing bonding or thick-film bonding, is that the bonded joint maintains a certain degree of elasticity and thereby compensates for stresses, expansions or vibrations. This property is popular in the construction of vehicles, heat exchanger, machines and ventilation systems. In other words, applications in which vibrations and oscillations place stress on a bond. So that such sealing adhesives deliver the expected levels of performance, it is in most cases necessary to maintain a defined minimum joint coating thickness in these applications. Due to the cross-linking mechanism (also known as curing), these products tend to be applied more in streaks and beads and rarely on large surface areas.