Industrial Strength Epoxy Adhesive
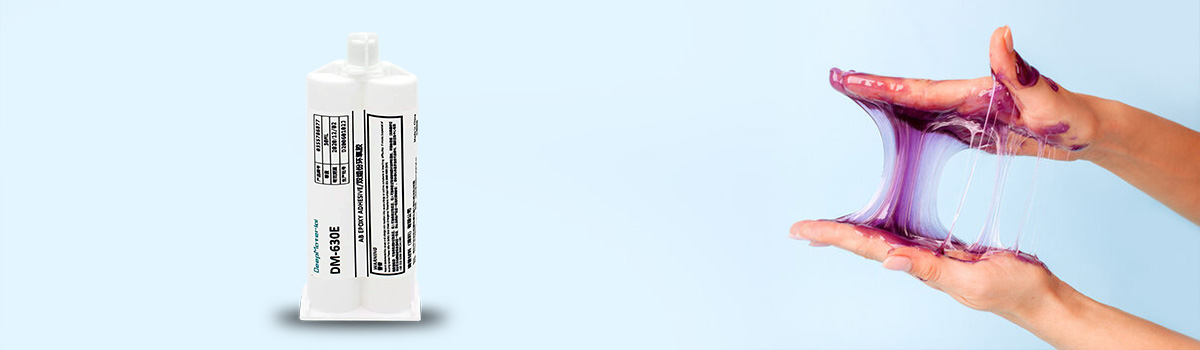
Various industries use epoxy adhesives in various applications due to their strong bonding properties. Manufacturers specifically design industrial strength epoxy adhesives for heavy-duty applications that require exceptional bonding strength, durability, and resistance to environmental factors such as heat, moisture, and chemicals. This article will explore the benefits and applications of industrial strength epoxy adhesive and the factors to consider when selecting the suitable adhesive for a particular job.
What is Industrial Strength Epoxy Adhesive?
Industrial strength epoxy adhesive is a reliable choice for bonding materials with unmatched strength and durability. This unique adhesive is widely used across industries and offers power, versatility, and resilience. This blog post will delve into industrial strength epoxy adhesive, understanding its composition, applications, and the benefits it provides in various sectors.
Industrial strength epoxy adhesive is a two-part system composed of epoxy resin and a hardening or curing agent. These components are typically supplied in separate containers and must be mixed in the correct ratio to activate the adhesive. The chemical reaction initiates cross-linking, forming a solid bond with exceptional adhesion properties. This adhesive offers remarkable heat, chemicals, and moisture resistance, making it ideal for demanding applications where conventional adhesives fall short.
The versatility of industrial strength epoxy adhesive lends itself to various applications. It often bonds concrete, steel, and other materials, providing structural integrity in bridges, buildings, and infrastructure projects. In manufacturing, epoxy adhesive securely joins various components in the automotive, aerospace, and electronics industries, ensuring longevity and reliability.
Additionally, it finds extensive use in woodworking, crafts, and DIY projects, providing a durable bond for furniture, flooring, and decorative items. The adhesive’s resistance to extreme temperatures and chemicals makes it suitable for oil and gas, marine, and chemical processing applications.
The advantages of industrial strength epoxy adhesive are numerous. Its exceptional bond strength and durability ensure long-lasting results even under extreme conditions. The ability to withstand high temperatures, harsh chemicals, and moisture makes it a reliable choice for demanding environments. The adhesive also offers excellent gap-filling properties, effectively bonding uneven surfaces. Furthermore, its versatility and compatibility with various materials make it a popular choice for diverse applications.
How Does Epoxy Adhesive Work?
Epoxy adhesive is a type of adhesive that consists of two components: epoxy resin and a hardener. A chemical reaction is triggered when these two components are combined, resulting in a solid and durable bond. The epoxy resin, a thick and viscous liquid, acts as the adhesive base, while the hardener, usually a liquid or powder, initiates the curing process. The key to epoxy’s effectiveness lies in this curing process.
- Chemical Reaction:The epoxy resin and hardener undergo a chemical reaction known as cross-linking. This reaction involves the formation of strong covalent bonds between the molecules, creating a three-dimensional network structure.
- Curing Process:Once the epoxy resin and hardener are mixed, the curing process begins. The reaction can be exothermic, generating heat or requiring external activation. Once cured, the epoxy adhesive typically undergoes an irreversible process, meaning it cannot be easily reversed or softened.
- Bonding Strength:Epoxy adhesive exhibits exceptional bonding strength due to the cross-linking of molecules during the curing process. The resulting bond is resistant to shear, tension, and compression, making it ideal for applications requiring high load-bearing capabilities.
- Versatility:Epoxy adhesive can bond various materials, including metals, plastics, ceramics, glass, and wood. Many industries commonly use it in construction, automotive, aerospace, electronics, and other sectors.
- Chemical and Environmental Resistance:Epoxy adhesive is known for its excellent resistance to chemicals, solvents, and environmental factors such as moisture, heat, and UV radiation. This resilience ensures the durability and longevity of the bonded surfaces.
- Gap Filling:Epoxy adhesive can fill gaps and irregularities between surfaces, providing a robust and uniform bond. This feature is handy when working with uneven or mismatched materials.
- Working Time and Curing Time:Epoxy adhesives offer varying working times, allowing users to apply the glue and make adjustments before it begins to cure. Curing time depends on temperature, humidity, and the specific epoxy formulation.
Advantages of Industrial Strength Epoxy Adhesive
We cannot overstate the importance of solid and reliable adhesives in industrial manufacturing and construction. When bonding materials, industrial strength epoxy adhesive emerges as a go-to solution. This unique adhesive offers many advantages, making it an indispensable choice for various applications. This blog post will explore the key benefits of industrial strength epoxy adhesive, highlighting its versatility and superior performance.
Versatility
Industrial strength epoxy adhesive is renowned for its versatility, as it can bond a wide range of materials, including metals, plastics, ceramics, wood, and even glass. This flexibility allows seamless integration into automotive, aerospace, construction, electronics, and more industries.
Advantages
- Exceptional Bonding Strength:Epoxy adhesives offer unparalleled bonding strength, creating durable and long-lasting bonds. They can withstand extreme forces, including tension, compression, and shear, ensuring structural integrity in demanding applications.
- Chemical Resistance:Industrial strength epoxy adhesive exhibits excellent resistance to chemicals, acids, solvents, and other corrosive substances. This attribute makes it ideal for applications that require resistance to environmental factors or exposure to harsh conditions.
- Temperature Resistance:Epoxy adhesives can withstand various temperatures, from extreme cold to high heat, without compromising their bonding capabilities. This resistance makes them suitable for use in different climates and environments.
- Versatile Cure Times:Industrial strength epoxy adhesives offer different cure times, allowing for flexibility in application and assembly processes. Some epoxy adhesives cure rapidly, providing quick turnaround times, while others allow for longer working times for intricate or complex projects.
- Gap-Filling Properties:Epoxy adhesives possess excellent gap-filling properties, enabling them to effectively bond irregular or uneven surfaces. This feature is particularly advantageous in applications where a precise fit may be challenging.
- Enhanced Durability:The inherent toughness and resilience of epoxy adhesives contribute to their enhanced durability. They can resist impact, vibrations, and other mechanical stresses, providing long-term reliability and minimizing the need for frequent repairs or replacements.
- Easy Application:Industrial strength epoxy adhesive is user-friendly, making it easy to apply. It is available in various forms, such as two-part systems or pre-measured cartridges, allowing for convenient mixing and precise application.
Exceptional Bonding Strength
We can witness exceptional bonding strength in various aspects of life, including friendships, familial ties, and romantic partnerships. These bonds transcend ordinary connections, offering unwavering support, shared experiences, and profound empathy. The individuals involved in these relationships serve as pillars, offering stability, comfort, and encouragement during challenging times. Whether it’s a friend who has been by your side through thick and thin, a sibling who understands you better than anyone else, or a partner who complements your strengths and weaknesses, these outstanding bonds bring immeasurable joy and resilience.
- Trust:People build exceptional bonds on a foundation of trust. The individuals involved have established a deep faith and confidence in each other, allowing them to be vulnerable, open, and authentic. This trust creates a safe space where personal growth, support, and understanding flourish.
- Communication:Effective communication is vital in maintaining exceptional bonds. Honest and transparent conversations pave the way for shared values, aspirations, and concerns. When individuals can express themselves without fear of judgment, they foster an environment where the bond strengthens, as they quickly resolve misunderstandings and cultivate empathy.
- Shared experiences:People often forge exceptional bonds through shared experiences. Whether traveling together, overcoming challenges, or celebrating milestones, these shared moments create a tapestry of memories that further strengthen the connection. Such experiences build a sense of unity, fostering a deeper understanding and relationship between individuals.
- Mutual respect:In exceptional bonds, individuals exhibit high mutual respect. Each individual recognizes and appreciates the other’s strengths, accomplishments, and uniqueness. This respect forms the basis for continuous support, encouragement, and belief in each other’s abilities.
- Empathy and compassion:Exceptional bonds thrive on kindness and compassion. Individuals in these relationships possess the remarkable ability to truly understand and share the feelings and experiences of the other person. This empathy creates a strong bond of emotional connection, where both parties provide comfort, solace, and a shoulder to lean on.
High Durability
When making purchasing decisions, durability is a crucial factor that often determines the value and longevity of a product. The high durability ensures that an item can withstand the test of time, frequent use, and various environmental conditions, providing users with long-lasting satisfaction. This blog post will explore the significance of high durability and its benefits across different domains.
Definition of High Durability
- High durability refers to the ability of a product or material to resist wear, damage, or degradation over an extended period.
- It implies robustness, strength, and reliability, enabling an item to endure harsh conditions and maintain its functionality and aesthetics.
Benefits of High Durability
- Longevity:Durability ensures that a product lasts longer, reducing the need for frequent replacements or repairs.
- Cost-effectiveness: Investing in durable products pays off in the long run by minimizing expenses associated with replacements and repairs.
- Environmental sustainability:Durable products reduce the overall environmental impact and create less waste by consuming fewer resources during production.
- Customer satisfaction:High durability contributes to a positive user experience, as customers can rely on a product’s performance and trust its quality.
Industries and Products Emphasizing Durability
- Electronics:Devices like smartphones, laptops, and cameras benefit from high durability to withstand accidental drops, temperature variations, and daily wear and tear.
- Automotive:Car manufacturers strive to improve vehicle durability, ensuring they can endure years of driving, changing weather conditions, and rough terrains.
- Construction:Durable materials are vital in the construction industry to ensure the stability and longevity of buildings, bridges, and infrastructure.
- Outdoor gear:Products like hiking boots, camping equipment, and outdoor clothing rely on high durability to withstand rugged terrains, extreme weather conditions, and repeated use.
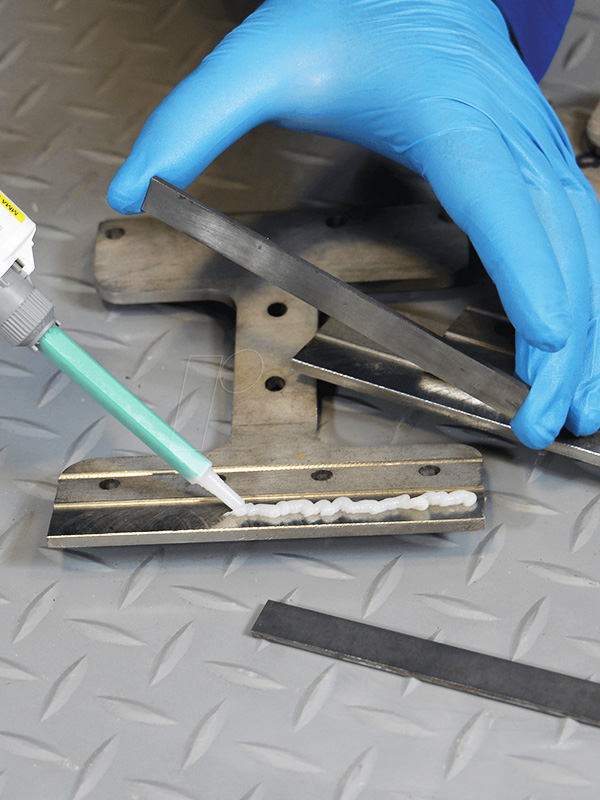
Factors Influencing Durability
- Material selection: Choosing high-quality materials with proven durability, such as stainless steel, reinforced plastics, or rugged fabrics, significantly impacts the lifespan of a product.
- Design considerations: Thoughtful design, including reinforced structures, protective elements, and proper weight distribution, can enhance a product’s durability.
- Manufacturing processes:Utilizing advanced manufacturing techniques, quality control measures, and rigorous testing ensures the production of durable products.
Chemical Resistance
In various industries, the ability of products to withstand exposure to chemicals is paramount. When faced with corrosive substances, chemical resistance ensures that materials, equipment, and products maintain integrity, functionality, and safety. Here we will delve into the significance of chemical resistance and its benefits across different sectors.
Definition of Chemical Resistance
- Chemical resistance refers to the capability of a material or product to resist degradation, corrosion, or damage when exposed to chemicals, including acids, solvents, fuels, and cleaning agents.
- It involves the ability to withstand chemical reactions, maintain structural integrity, and prevent leakage, contamination, or failure.
Benefits of Chemical Resistance
- Longevity and reliability:Chemically resistant materials or products offer extended lifespan and reliable performance even in harsh environments, reducing the need for frequent replacements or repairs.
- Safety assurance:Chemical resistance is crucial in safeguarding against leaks, spills, or accidents resulting from chemical interactions, and it effectively protects workers, users, and the environment from potential harm.
- Cost-effectiveness: Investing in chemically resistant materials or products saves costs by reducing downtime, minimizing maintenance expenses, and preventing product failures.
- Compliance with regulations:In industries like pharmaceuticals, food processing, or oil and gas, chemical resistance is essential to meet stringent regulatory requirements regarding safety, sanitation, and environmental protection.
Industries and Applications Emphasizing Chemical Resistance
- Chemical manufacturing: Equipment and storage containers used in chemical production require high chemical resistance to withstand corrosive substances and prevent contamination or spills.
- Pharmaceuticals: Chemical resistance is crucial for pharmaceutical packaging, ensuring the integrity of medications and preventing interactions between drugs and packaging materials.
- Automotive: Components exposed to automotive fluids, such as engine parts, fuel systems, and hoses, rely on chemical resistance to prevent degradation and maintain optimal performance.
- Food processing:Materials used in food processing, such as conveyor belts, storage containers, and seals, must exhibit chemical resistance to prevent contamination and ensure food safety.
Factors Influencing Chemical Resistance
- Material selection:Choosing chemically resistant materials such as stainless steel, high-density polyethylene (HDPE), or fluoropolymers ensures protection against specific chemicals.
- Coatings and finishes:Applying chemical-resistant coatings or finishes to surfaces enhances their ability to withstand chemical exposure and prevents corrosion.
- Testing and certification:Rigorous testing and certification processes help identify and validate the chemical resistance properties of materials and products.
Heat Resistance
Heat resistance is a crucial characteristic that determines the reliability and durability of materials in various applications. From everyday products to cutting-edge technologies, the ability to withstand high temperatures is essential for optimal performance and safety. Here we will explore the significance of heat resistance and its impact on our lives.
Why Heat Resistance Matters
- Enhanced Safety:Heat-resistant materials actively contribute to aerospace, automotive, and construction industries as they withstand high temperatures commonly encountered in these sectors. These materials prevent structural deformations, ensuring the safety of both users and the surrounding environment.
- Extended Lifespan:The longevity of products directly depends on heat resistance. Materials that can withstand extreme temperatures exhibit superior durability and remain functional over extended periods, reducing the need for frequent replacements.
- Efficient Energy Usage:Heat-resistant materials minimize energy losses in heat transfer applications, such as power generation and electronic devices. By retaining thermal energy within systems, these materials contribute to higher energy efficiency and lower operational costs.
- Versatile Applications:Heat resistance is crucial in various applications, including cookware, fire protection, insulation, and space exploration. From non-stick pans that can withstand high cooking temperatures to flame-retardant materials used in buildings, heat-resistant materials serve various purposes in our daily lives.
Materials with Exceptional Heat Resistance
- Ceramics:Ceramics are known for their outstanding heat resistance, making them suitable for high-temperature applications such as kilns, jet engines, and automotive exhaust systems. Their ability to retain strength and resist thermal expansion at extreme temperatures makes ceramics a reliable choice.
- Refractory Metals:Tungsten, molybdenum, and niobium are refractory metals that exhibit excellent heat resistance. These metals can withstand extreme temperatures and maintain their structural integrity, making them valuable in aerospace components, lighting filaments, and nuclear reactors.
- Heat-Resistant Alloys:Engineers design alloys such as stainless steel, nickel-based, and titanium alloys to retain strength and integrity even at elevated temperatures. Chemical processing plants, power plants, and the automotive industry commonly utilize these alloys in high-temperature environments, demonstrating their widespread applicability.
- Advanced Polymers:Some polymers, such as polyimides and polybenzimidazoles (PBI), exhibit exceptional heat resistance. They are widely used in electrical insulation, aerospace components, and protective clothing for firefighters, as they can withstand high temperatures without compromising their mechanical properties.
Future Trends and Innovations
- Nanotechnology:Researchers are exploring the potential of nanomaterials to enhance heat resistance. Researchers are revolutionizing the electronics and energy storage industries by developing nanostructured coatings and composites that they can tailor for specific applications, resulting in improved thermal stability.
- Bio-inspired Materials:Scientists are developing heat-resistant materials based on the unique properties of organisms like extremophiles, drawing inspiration from nature. These materials could find applications in extreme environments, such as space exploration or geothermal energy production.
Moisture Resistance
Moisture resistance is a critical characteristic that affects the longevity and performance of various materials and products. From electronics and building materials to textiles and coatings, the ability to repel or withstand moisture ensures durability and functionality. Here we will explore the significance of moisture resistance, its applications in different industries, and how it contributes to the overall quality of products.
Understanding Moisture Resistance
- Moisture resistance refers to the ability of a material or product to repel, resist, or withstand the effects of moisture.
- It prevents the ingress of water or steam, which can lead to degradation, corrosion, mold growth, and other undesirable effects.
- Various mechanisms, including barrier coatings, hydrophobic surface treatments, and moisture-resistant materials, achieve moisture resistance.
Applications in Different Industries
Electronics and Electrical Systems
- Moisture resistance is crucial for electronic components, circuit boards, and devices.
- It prevents damage caused by moisture, such as short circuits, corrosion, and electrical failures.
- Moisture-resistant coatings and encapsulation techniques protect delicate electronic systems from humidity and moisture-related issues.
Construction and Building Materials
- Moisture resistance is essential in construction materials like paints, sealants, adhesives, and roofing materials.
- It helps to maintain structural integrity, prevent water intrusion, and protect against mold and mildew growth.
- Moisture-resistant materials are used in foundations, walls, and flooring to ensure long-term durability and maintain a healthy indoor environment.
Textiles and Apparel
- Moisture resistance plays a significant role in outdoor clothing, sportswear, and performance textiles.
- It helps to repel water and moisture, keeping the wearer dry, comfortable, and protected from the elements.
- Moisture-wicking fabrics draw moisture away from the skin, allowing for quick evaporation and improved comfort.
Benefits of Moisture Resistance
Enhanced Durability
- Moisture-resistant materials have a longer lifespan due to reduced susceptibility to corrosion, rot, and degradation caused by moisture exposure.
- Products with moisture resistance require less frequent replacement, leading to cost savings and reduced environmental impact.
Improved Performance
- Moisture resistance ensures the reliable functioning of electronic devices, even in humid environments.
- Construction materials with moisture resistance provide better insulation, weatherproofing, and protection against water-related damages.
Health and Safety
- Moisture resistance helps to prevent the growth of mold, mildew, and bacteria, which can lead to respiratory issues and other health concerns.
- In the construction industry, moisture resistance creates healthier indoor environments by preventing water damage and maintaining optimal humidity levels.
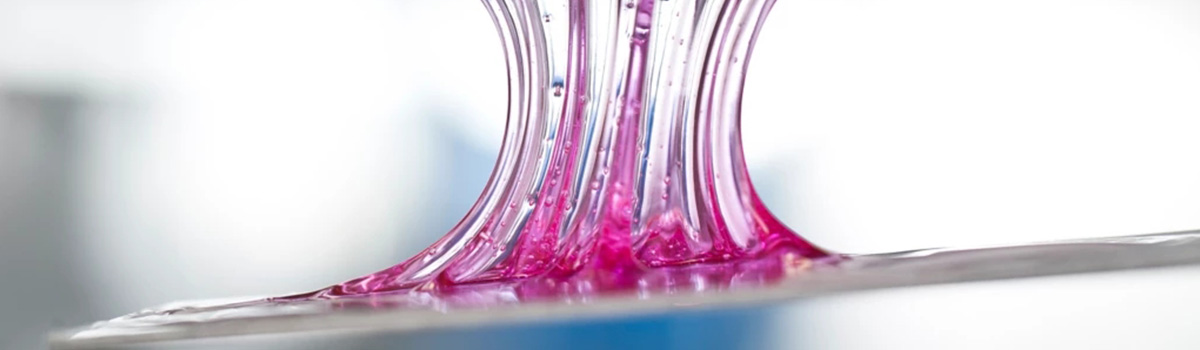
Versatile Applications
Consumers and industries seek versatility in products and technologies in today’s fast-paced world. Adapting and excelling in different applications is crucial to their success. Here we will delve into versatile applications, highlighting their significance across various industries. From cutting-edge materials to advanced technologies, we will explore how versatility drives innovation and unlocks new possibilities.
Understanding Versatile Applications
- Versatile applications describe how products, materials, or technologies adapt and find utility in multiple contexts or industries.
- Adaptable design, flexible functionality, and compatibility with diverse environments or requirements actively achieve versatility.
- Versatile solutions offer cost-effectiveness, time-saving benefits, and simplified processes.
Versatility in Different Industries
Automotive Sector
- Automotive manufacturing utilizes lightweight alloys, composite materials, and flexible plastics.
- They enable the development of fuel-efficient vehicles, improved safety features, and customizable designs.
- Versatile applications enhance performance, reduce weight, and optimize energy efficiency.
Construction and Architecture
- Versatile building materials, such as modular systems, adaptable coatings, and sustainable composites, offer flexibility in construction projects.
- They allow for efficient customization, quick assembly, and adaptability to changing needs or designs.
- Versatile applications in construction foster sustainable practices, reduce waste, and provide cost-effective solutions.
Information Technology and Electronics
- Versatile software platforms, applications, and devices cater to user needs and scenarios.
- They offer seamless integration, interoperability, and scalability, allowing efficient data management and connectivity.
- Versatile applications in IT and electronics empower businesses and consumers with adaptable solutions for productivity, communication, and entertainment.
Benefits and Advantages of Versatile Applications
Cost-Effectiveness
- Versatile solutions eliminate the need for specialized products, reducing inventory management and training costs.
- They provide long-term value by adapting to evolving requirements and minimizing the need for frequent replacements or upgrades.
Enhanced Efficiency
- Versatile applications streamline processes, workflows, and operations, improving productivity and resource utilization.
- They simplify logistics, reduce complexity, and optimize performance, saving time and energy.
Innovation and Adaptability
- Versatile applications drive innovation by fostering creative problem-solving and enabling novel applications.
- They allow businesses and individuals to adapt to changing trends, market demands, and technological advancements.
Types of Industrial Strength Epoxy Adhesive
Industrial strength epoxy adhesives are versatile and powerful bonding agents widely used in various industries. Whether metal, plastic, concrete, or wood, epoxy adhesives offer exceptional strength and durability for bonding different materials. However, not all epoxy adhesives are the same, and various types are available, each with unique properties and applications. This blog post will explore some common types of industrial strength epoxy adhesives and their uses.
Two-Component Epoxy Adhesives
- Two-component epoxy adhesives are the most common type used in industrial applications.
- They comprise a resin and a hardener that users must mix before applying.
- These adhesives offer excellent bonding strength, chemical resistance, and durability.
- They suit various materials, including metal, ceramics, plastics, and composites.
- The construction, automotive, and aerospace industries often utilize two-component epoxy adhesives.
One-Component Epoxy Adhesives
- One-component epoxy adhesives come pre-mixed and ready to use.
- They do not require mixing or measuring, making them convenient for quick applications.
- These adhesives are ideal for bonding small parts, filling gaps, and sealing joints.
- They offer good resistance to heat, chemicals, and impact.
- The electronics, jewelry, and crafts industries commonly use one-component epoxy adhesives.
Structural Epoxy Adhesives
- Engineers design structural epoxy adhesives for high-strength bonding applications.
- They provide exceptional load-bearing capabilities and are often used to replace mechanical fasteners.
- These adhesives create strong bonds that distribute stress evenly, improving overall structural integrity.
- They are commonly used to construct bridges, buildings, and heavy machinery.
Heat-Resistant Epoxy Adhesives
- Formulators create heat-resistant epoxy adhesives to withstand high temperatures.
- They maintain their strength and bonding properties even in extreme heat conditions.
- These adhesives are suitable for applications such as bonding metal components in engines or appliances.
- The automotive, aerospace, and manufacturing industries often utilize heat-resistant epoxy adhesives.
Chemical-Resistant Epoxy Adhesives
- Designers formulate chemical-resistant epoxy adhesives to withstand exposure to various chemicals and solvents.
- They provide a reliable bond even in harsh chemical environments.
- Laboratories, chemical processing plants, and oil refineries commonly use these adhesives.
Conductive Epoxy Adhesives
- Conductive epoxy adhesives contain conductive fillers that allow them to conduct electricity.
- They bond electronic components, create electrical connections and repair circuit boards.
- The electronics and telecommunications industries widely use conductive epoxy adhesives.
Two-Part Epoxy Adhesive
Two-part epoxy adhesive, or two-component epoxy adhesive, consists of a resin and a hardener. Users must mix these components in a specific ratio before applying the glue. Once mixed, the glue starts to cure and form a strong bond. Here are some key features and benefits of two-part epoxy adhesive:
Exceptional Bonding Strength
- Two-part epoxy adhesive provides exceptional bonding strength, creating solid and durable bonds between different materials.
- It forms a robust adhesive layer evenly distributing stress, enhancing the bonded parts’ overall structural integrity.
Versatility
- Two-part epoxy adhesive is compatible with various materials, including metals, plastics, ceramics, composites, and more.
- This versatility makes it suitable for multiple construction, automotive, aerospace, electronics, and manufacturing applications.
Chemical Resistance
- The two-part epoxy adhesive offers good resistance to chemicals, solvents, and environmental factors, ensuring long-term durability in harsh conditions.
- It can withstand exposure to fuels, oils, moisture, and many other substances, making it suitable for demanding applications.
Flexibility and Impact Resistance
- The two-part epoxy adhesive exhibits excellent flexibility and impact resistance, allowing it to absorb vibrations and shocks.
- This property makes two-part epoxy adhesive ideal for bonding parts that undergo dynamic loads or applications where movement and stress are likely.
Gap Filling and Gap Bridging
- The two-part epoxy adhesive has excellent gap-filling capabilities, effectively bonding irregular or uneven surfaces.
- It can fill gaps and voids, providing a uniform and strong bond even in challenging bonding scenarios.
Temperature Resistance
- Two-part epoxy adhesive offers good temperature resistance, allowing it to maintain its bonding properties in various temperatures.
- Some specialized formulations can withstand high temperatures, making them suitable for automotive engines, appliances, and more applications.
Applications of Two-Part Epoxy Adhesive
- Construction:Industries commonly use a two-part epoxy adhesive to bond structural elements, perform concrete repairs, anchor bolts, and complete laminating applications.
- Automotive and Aerospace:It finds applications in vehicle assembly, bonding metal and composite parts, panel bonding, and aircraft repairs.
- Electronics:Two-part epoxy adhesive is used for bonding circuit boards, encapsulating electronic components, potting, and sealing applications.
- Manufacturing:It is used for general bonding, assembling parts, fabricating components, and securing industrial equipment.
- Crafts and DIY Projects:Two-part epoxy adhesive is popular among hobbyists and DIY enthusiasts for various bonding and crafting applications.
One-Part Epoxy Adhesive
One product stands out in adhesives for its versatility, strength, and convenience – the one-part epoxy adhesive. This adhesive formulation has gained immense popularity across various industries due to its exceptional bonding capabilities and user-friendly application process. Here we will delve into the world of one-part epoxy adhesives, exploring their composition, benefits, and typical applications.
Composition and Features
One-part epoxy adhesives typically comprise an epoxy resin and a curing agent blended in a single component. The adhesive remains in a liquid or paste form until it is exposed to heat, ultraviolet (UV) light, or moisture, triggering the curing process. Some key features of one-part epoxy adhesives include:
- Strength:These adhesives offer outstanding bonding strength, often surpassing the power of the joined materials. They create durable, long-lasting bonds that withstand various stresses and environmental conditions.
- Versatility:One-part epoxy adhesives are compatible with many substrates, including metals, plastics, ceramics, and composites. They can effectively bond different materials together, enhancing structural integrity and enabling diverse applications.
- Chemical resistance:Once cured, one-part epoxy adhesives exhibit excellent resistance to chemicals, solvents, and harsh environments. This property makes them suitable for applications that require resistance to corrosion, moisture, and other chemical exposures.
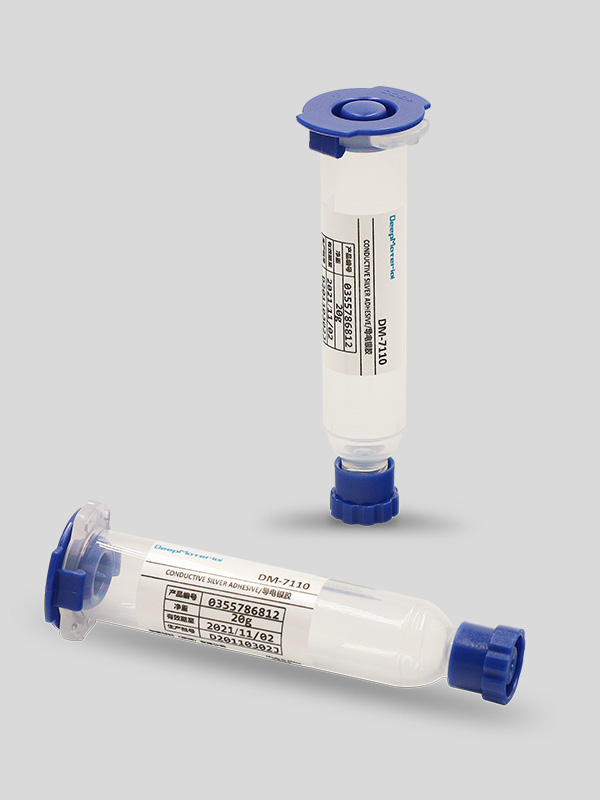
Benefits and Advantages
Using one-part epoxy adhesives provides several advantages, making them a preferred choice in numerous industries:
- Simplified application:Unlike two-part epoxy adhesives that require mixing before use, one-part epoxy adhesives are pre-mixed and ready to apply. By eliminating the need for precise mixing ratios, users can reduce the chances of errors and ensure consistent performance.
- Time efficiency:One-part epoxy adhesives cure at room temperature or with minimal external activation, saving valuable time compared to bonds that require heat or UV light for curing.
- Reduced equipment and setup:The one-part formulation eliminates the need for complex equipment, special storage, or mixing apparatus, streamlining the adhesive application process.
Common Applications
One-part epoxy adhesives find wide-ranging applications across numerous industries, including:
- Electronics:They are extensively used for bonding electronic components, securing wires, encapsulating circuits, and protecting sensitive assemblies from moisture, vibration, and thermal stress.
- Automotive:One-part epoxy adhesives provide solid bonds for vehicle assembly, interior trims, bonding plastic parts, and sealing applications, ensuring enhanced durability and safety.
- Aerospace:In the aerospace industry, one-part epoxy adhesives are crucial in connecting aircraft components, assembling composite structures, and sealing joints. These adhesives contribute to the lightweight design and structural integrity of aircraft.
- Construction:They are employed for bonding concrete, stone, and other building materials, offering high strength, weather resistance, and durability in construction applications.
Fast-Curing Epoxy Adhesive
In the world of adhesives, speed, and efficiency are crucial. That’s where fast-curing epoxy adhesive is revolutionizing how we bond materials. With its rapid-setting properties and exceptional strength, this adhesive has become a game-changer in numerous industries. This article will explore the wonders of fast-curing epoxy adhesives and their diverse applications.
What is Fast-Curing Epoxy Adhesive?
- Fast-curing epoxy adhesive is a two-component adhesive that consists of a resin and a hardener.
- Depending on the specific product, the curing process occurs rapidly, typically within minutes or hours.
- It offers excellent bonding strength and durability, making it suitable for various applications.
Advantages of Fast-Curing Epoxy Adhesive
- Quick setting:Fast-curing epoxy adhesive improves productivity and efficiency by significantly reducing assembly time.
- Strong bonding:Once cured, this adhesive forms a robust bond that can withstand heavy loads and extreme conditions.
- Versatility:It bonds various materials such as metals, plastics, composites, ceramics, and more, expanding its application possibilities.
- Chemical resistance:Fast-curing epoxy adhesive exhibits chemical resistance, making it suitable for applications exposed to harsh environments.
- Temperature resistance:It can withstand elevated temperatures, ensuring the adhesive’s integrity in demanding conditions.
Applications of Fast-Curing Epoxy Adhesive
- Electronics and electrical components:Industries commonly use a fast-curing epoxy adhesive to bond circuit boards, connectors, and semiconductors.
- Automotive industry: It finds application in vehicle assembly, bonding plastic and metal components, and securing electrical connections.
- Aerospace and aviation:In aircraft manufacturing and maintenance, professionals utilize fast-curing epoxy adhesive for structural bonding, repairs, and composite component assembly.
- Construction industry:It is ideal for bonding concrete, stone, and other materials, providing durability and structural integrity.
- Marine applications:Due to its water and chemical resistance, this adhesive is utilized for bonding boat hulls, deck components, and sealing joints and fittings.
Tips for Working with Fast-Curing Epoxy Adhesive
- Proper surface preparation:To achieve optimal adhesion, clean, dry, and eliminate contaminants from the surfaces you intend to bond.
- Mixing ratios:Follow the manufacturer’s instructions regarding the correct mixing ratios of the epoxy resin and hardener for the best results.
- Application temperature:Consider the recommended temperature range for the adhesive during the application, as it can affect the curing process.
- Working time:Fast-curing epoxy adhesive sets quickly, so plan and prepare materials before applying the adhesive to avoid rushing the process.
- Safety precautions:Wear appropriate personal protective equipment, such as gloves and safety glasses, and work in a well-ventilated area using epoxy adhesives.
High-Temperature Epoxy Adhesive
The demand for high-performance adhesives that can withstand extreme temperatures is rising in today’s fast-paced world. Industries such as aerospace, automotive, electronics, and manufacturing often encounter high-temperature environments where traditional adhesives fail to deliver. However, high-temperature epoxy adhesives have revolutionized how these industries tackle bonding challenges in harsh conditions. This blog post will explore the benefits and applications of high-temperature epoxy adhesives.
Benefits of High-Temperature Epoxy Adhesive
- Exceptional Heat Resistance:High-temperature epoxy adhesives withstand extreme temperatures, ranging from -50°C to over 200°C (-58°F to 392°F), thanks to their specially formulated composition. This heat resistance allows them to maintain structural integrity, preventing bond failure even in the most demanding environments.
- Solid and Durable Bonds:These adhesives offer excellent bonding strength on various substrates, including metals, ceramics, glass, and composites. They create robust, long-lasting bonds that endure thermal cycling, mechanical stress, and environmental exposure without compromising performance.
- Chemical Resistance:High-temperature epoxy adhesives exhibit exceptional resistance to various chemicals, solvents, fuels, and oils. This property makes them suitable for industrial applications where corrosive substances are exposed daily.
- Electrical Insulation:Many high-temperature epoxy adhesives have excellent electrical insulation properties. They can bond and seal electronic components, protecting them from moisture, dust, and other contaminants while ensuring reliable electrical conductivity.
Applications of High-Temperature Epoxy Adhesive
- Aerospace Industry:High-temperature epoxy adhesives play a crucial role in aerospace applications, such as composite bonding structures, sealing fuel tanks, and assembling critical engine components. They provide the required strength and durability to withstand extreme temperature variations experienced during flight.
- Automotive Sector:In the automotive industry, manufacturers utilize high-temperature epoxy adhesives to bond exhaust systems, heat shields, engine components, and other parts that experience high temperatures. They ensure a secure and reliable bond, contributing to enhanced performance and durability of vehicles.
- Electronics and Electrical Engineering:The electronics industry widely employs high-temperature epoxy adhesives for encapsulating and potting electronic components. They offer excellent thermal management, electrical insulation, and protection against environmental factors, thus ensuring the longevity of delicate electronic circuits.
- Industrial Manufacturing:Manufacturers rely on high-temperature epoxy adhesives for bonding metal components, heat exchangers, furnace linings, and other equipment used in high-temperature processes. These adhesives withstand the rigors of industrial environments, maintaining structural integrity even under extreme heat and stress.
UV Resistant Epoxy Adhesive
In the world of adhesives, UV resistant epoxy adhesive stands out as a powerful and versatile solution. With its unique properties and exceptional resistance to ultraviolet (UV) rays, this adhesive offers various industrial applications. From construction to automotive, electronics to marine, the UV resistant epoxy adhesive is a reliable choice for protecting bonds and ensuring long-lasting durability.
UV Resistance
- UV resistance is a crucial property of adhesives, especially in outdoor applications, as exposure to sunlight can degrade and weaken traditional adhesives over time.
- UV resistant epoxy adhesive is specially formulated to withstand the damaging effects of UV radiation, maintaining the integrity and strength of bonded materials even under prolonged exposure to sunlight.
- It provides enhanced protection against discoloration, yellowing, cracking, and deterioration, ensuring a longer lifespan for bonded surfaces.
Benefits and Applications
- Superior bonding strength: UV resistant epoxy adhesive forms strong and reliable bonds between various materials, including metals, plastics, glass, ceramics, and composites.
- Versatile applications:This adhesive finds application in multiple industries, including construction, electronics, aerospace, automotive, marine, and more.
- Outdoor durability:Its resistance to UV radiation makes it an ideal choice for outdoor applications, such as exterior bonding signage, solar panels, outdoor furniture, and architectural structures.
- Electronics protection:Many industries actively utilize UV-resistant epoxy adhesive to encapsulate and protect delicate electronic components. It provides insulation and safeguards against moisture, dust, and UV exposure.
- Chemical and temperature resistance:It exhibits excellent resistance to chemicals, including solvents, oils, and fuels, making it suitable for harsh environments. Additionally, it can withstand high temperatures without compromising its bonding properties.
- Optically clear bonds:This adhesive is available in formulations, ensuring seamless bonding of transparent materials like glass or plastics without compromising clarity or aesthetics.
- Easy application:UV resistant epoxy adhesive is typically known as a two-component system that cures rapidly upon exposure to UV light. This feature saves time and boosts productivity by enabling accurate positioning and speedy assembly.
Factors to Consider When Selecting Epoxy Adhesive
Epoxy adhesives are versatile and widely used in various industries for bonding and joining applications. Their strong adhesive properties and ability to bond with different materials make them famous. However, selecting the suitable epoxy adhesive for a specific application requires careful consideration of several factors. This blog post will discuss the key factors to consider when choosing an epoxy adhesive.
Bonding Materials
Consider the materials you need to bond together. Epoxy adhesives are available in different formulations, each designed for specific materials such as metals, plastics, composites, or wood. Ensure that the epoxy you choose is compatible with the materials you are bonding.
Strength Requirements
Evaluate the strength requirements of your application. Epoxy adhesives come in various strengths, ranging from general-purpose to high-strength formulations. If you need a strong bond, opt for epoxy adhesives with higher tensile and shear forces.
Cure Time
Cure time is an essential consideration, especially when working on time-sensitive projects. Some epoxy adhesives cure quickly, while others require more extended curing periods. Consider the necessary assembly and healing time to ensure it aligns with your project timeline.
Temperature Resistance
Take into account the operating temperature range of your application. Epoxy adhesives have different temperature resistance capabilities. If your application requires your bonded components to withstand extreme temperatures, ensure that you choose an epoxy adhesive capable of withstanding those conditions.
Chemical Resistance
If your application involves exposure to chemicals, consider the chemical resistance of the epoxy adhesive. Some epoxy formulations are more resistant to certain chemicals, acids, or solvents than others. Ensure that the bond can withstand the specific chemical environment it will encounter.
Flexibility
Specific applications require the bonded materials to have some degree of flexibility or ability to absorb vibrations. In such cases, look for epoxy adhesives that offer flexibility or have elastomeric properties.
Dispensing and Mixing
Consider the ease of dispensing and mixing the epoxy adhesive. Some epoxy adhesives are available in dual-component cartridges, while others require separate measuring and mixing. Choose an epoxy that suits your preferred application method and provides a consistent mix.
Shelf Life
Check the shelf life of the epoxy adhesive. Epoxy formulations can have varying shelf lives, so selecting one that matches your usage frequency is crucial. Using expired epoxy can lead to poor adhesive performance.
Application Environment
Consider evaluating the conditions in which you will apply the epoxy adhesive. Factors like humidity, cleanliness, and surface preparation are vital in achieving a successful bond. Consider whether the epoxy adhesive requires special surface preparation or performs well in different environmental conditions.
Bonding Surface Material
When creating strong and long-lasting bonds between two surfaces, the choice of bonding surface material is crucial. Whether in the construction industry, automotive manufacturing, or even DIY projects, selecting the suitable material can significantly impact the overall performance and durability of the bond. Here we will explore the importance of bonding surface materials and highlight key factors to consider for optimal results.
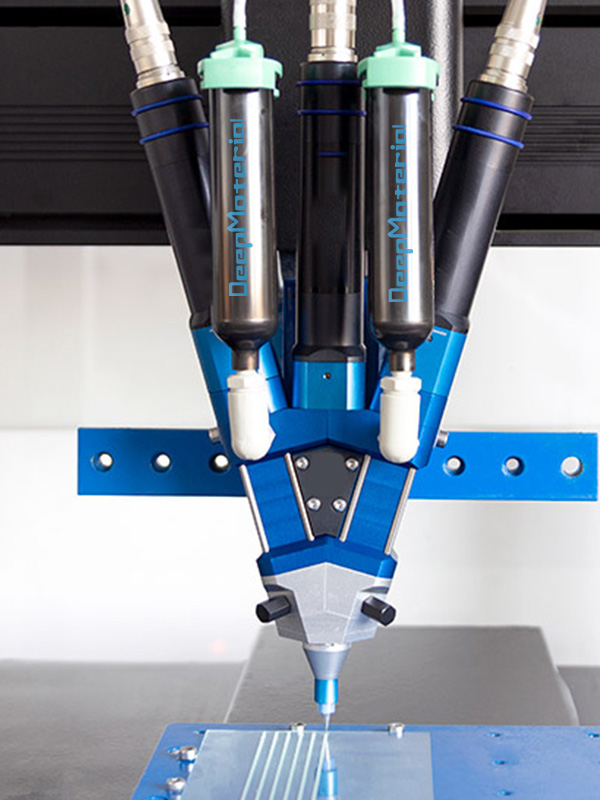
Compatibility
- The bonding surface material should be compatible with the adhesive or bonding agent. Ensure that both materials work well together and create a strong bond.
- Consider the surfaces’ chemical composition, porosity, and texture to ensure proper adhesion.
Surface Preparation
- Before bonding, it is essential to prepare the surfaces properly. The characters are usually cleaned, roughened, or treated to promote adhesion.
- Some materials require specific surface treatments to enhance bonding capabilities, such as sanding, degreasing, or applying primers.
Common Bonding Surface Materials
- Metals:Various metals, such as aluminum, steel, and stainless steel, require specific bonding techniques. Surface treatments like anodizing or phosphating can improve adhesion on metal surfaces.
- Plastics:Plastics, including polyethylene, polypropylene, and PVC, have low surface energy, making bonding challenging. Specialized adhesives or surface treatments, like corona or flame treatment, can enhance adhesion on plastic surfaces.
- Composites:Composite materials like carbon fiber or fiberglass often have a resin matrix that requires compatible bonding agents for adequate adhesion. Surface preparation techniques like sanding or chemical treatments may be necessary.
- Glass:Bonding glass requires specialized adhesives and surface treatments, such as silane primers or UV curing, to achieve firm and durable bonds.
- Wood:Wood surfaces can benefit from sanding or applying primers to enhance adhesion. Consider the type of wood and its moisture content when selecting bonding surface materials.
Considerations for Specific Applications
- Temperature resistance:Some applications require bonding materials that can withstand high or low temperatures. Ensure the bonding surface material can handle the intended environment.
- Chemical resistance:In specific industries, such as chemical processing or automotive manufacturing, the bonding surface material should resist corrosive substances or particular chemicals.
- Outdoor exposure:If sunlight, moisture, or other environmental factors expose the bond, choose a bonding surface material with appropriate weather resistance properties.
- Structural requirements:When establishing load-bearing or structural bonds, selecting materials that can provide sufficient strength and stability is crucial.
Cure Time
When it comes to medical treatments and procedures, one often hears the term “cure time.” It refers to the duration required for a treatment or medication to take effect and produce the desired results. Understanding cure time is essential for patients, medical professionals, and caregivers. Here we will delve into the concept of cure time, its significance, and how it influences various aspects of healthcare.
What is Cure Time?
The cure time represents the span between administering a treatment or medication and when the treatment’s intended effects fully manifest. Various factors, including the treatment of the specific condition, the type and dosage of medication, and individual patient characteristics, determine the cure time. This time frame allows the body to respond to the treatment and heal or recover appropriately.
Significance of Cure Time
Cure time plays a crucial role in medical decision-making and patient management. Here’s why it’s important:
- Treatment Effectiveness:Understanding the cure time helps patients and medical professionals evaluate the effectiveness of treatment. It allows for realistic expectations and helps monitor progress during the healing process.
- Dosage and Frequency:Cure time helps determine the appropriate dosage and frequency of medication administration. Medical professionals consider the optimal cure time to ensure the medication remains effective without causing harm or complications.
- Treatment Planning:Knowing the cure time is essential for planning medical interventions, such as surgeries or follow-up procedures. It allows healthcare providers to schedule appointments, allocate resources, and manage patient care effectively.
- Patient Education:Educating patients about cure time empowers them to participate in their treatment journey actively. They can understand the importance of adherence to medication schedules and follow medical advice for the recommended duration to achieve desired outcomes.
Factors Influencing Cure Time
Several factors affect the cure time of different treatments:
- Medication Formulation:The formulation of a medication, such as tablets, capsules, or injections, can impact its absorption and the time required to reach therapeutic levels in the body.
- The severity of the Condition:The cure time can vary depending on the condition under treatment. Mild ailments tend to have shorter cure times, while chronic or complex conditions may require extended periods for a full recovery.
- Individual Variations:Each person’s body reacts differently to treatments, and factors like age, overall health, metabolism, and genetics can influence the cure time.
- Treatment Approach: The chosen treatment approach, such as surgical interventions, physical therapy, or lifestyle modifications, can significantly affect the cure time.
Temperature Requirements
Temperature is crucial in our daily lives, impacting our comfort, health, and overall well-being. Understanding temperature requirements is essential for creating optimal living conditions, Whether in our homes, workplaces, or outdoor environments. Here we will explore the significance of temperature control and outline the key factors to consider when determining temperature requirements.
Comfort and Productivity
- Maintaining an appropriate temperature is vital for creating a comfortable environment. Whether it’s a cozy winter warmth or a refreshing summer cool, the right temperature enhances our overall well-being.
- Comfortable temperatures have a direct impact on productivity levels. Studies have shown that individuals working in environments with optimal temperatures tend to be more focused, motivated, and efficient.
Health and Safety
- Extreme temperatures can have adverse effects on our health. Excessive heat or cold can lead to heat exhaustion, heatstroke, hypothermia, or other health complications. It is crucial to maintain suitable temperatures to prevent such risks.
- Specific temperature requirements are essential for preserving the quality and safety of certain products. For instance, vaccines, medications, and perishable goods often require controlled temperatures to remain effective and safe for consumption.
Energy Efficiency
- Optimizing temperature requirements contributes to energy efficiency and cost savings. By setting appropriate temperatures, we can reduce the energy consumption of heating and cooling systems.
- Programmable thermostats and intelligent devices can automatically adjust temperatures based on occupancy or time of day, ensuring comfort when needed and conserving energy when spaces are unoccupied.
Environmental Considerations
- Controlling temperature requirements can have a positive impact on the environment. By reducing energy consumption, we contribute to lower greenhouse gas emissions, helping combat climate change.
- Utilizing energy-efficient appliances, improving insulation, and promoting sustainable practices are effective ways to minimize the environmental footprint associated with temperature control.
Geographic Variations
- Different regions have varying temperature requirements due to climate variations. Understanding the specific needs of each area is crucial for designing appropriate heating and cooling systems.
- Proper insulation, window treatments, and landscaping techniques can help mitigate the effects of extreme temperatures, optimizing indoor comfort levels while reducing energy consumption.
Safety Considerations
Safety should be a top priority in every aspect of our lives. Taking the necessary precautions to ensure a secure environment is crucial at home, work, or in public spaces. This blog post will explore some important safety considerations that can help us protect ourselves and those around us.
Home Safety
- Install smoke detectors and carbon monoxide detectors in key areas of your home.
- Regularly check and maintain fire extinguishers.
- Keep emergency contact numbers readily accessible.
- Secure your doors and windows with sturdy locks to enhance safety.
- Implement a home security system or surveillance cameras.
Workplace Safety
- Familiarize yourself with the emergency exit routes and evacuation procedures.
- Report any potential hazards or safety concerns to the appropriate authorities.
- Use protective equipment (PPE), gloves, goggles, or helmets, when necessary.
- Practice good ergonomics to prevent repetitive strain injuries or musculoskeletal disorders.
- Conduct regular safety training sessions to educate employees about potential risks and safety protocols.
Road Safety
- Observe traffic rules and regulations at all times.
- Buckle up and make sure you properly restrain all passengers in the vehicle.
- Avoid distractions while driving, such as texting or using mobile devices.
- Adhere to speed limits and adjust driving behavior according to road conditions.
- Stay vigilant and aware of pedestrians and cyclists sharing the road.
Cybersecurity
- Use strong and unique passwords for all online accounts.
- Regularly update software and operating systems to patch security vulnerabilities.
- Be cautious when clicking on unfamiliar links or downloading files from unknown sources.
- Enable two-factor authentication for added account security.
- Please educate yourself about common phishing scams and how to identify them.
Public Spaces Safety
- Be aware of your surroundings and trust your instincts.
- Avoid walking alone in poorly lit or deserted areas, especially at night.
- Stay in well-populated and well-lit areas when possible.
- Use designated crosswalks and follow traffic signals when crossing roads.
- Report any suspicious activities to the authorities.
Conclusion
In conclusion, industrial strength epoxy adhesive is essential for heavy-duty bonding applications across various industries. It provides exceptional bonding strength, durability, and resistance to environmental factors such as heat, moisture, and chemicals. The type of adhesive chosen will depend on several factors, including the bonding surface material, cure time, temperature requirements, and safety considerations. By selecting the suitable industrial strength epoxy adhesive and following proper application techniques, you can ensure a reliable, long-lasting bond that withstands even the harshest conditions.