Membrane Bonding Adhesive
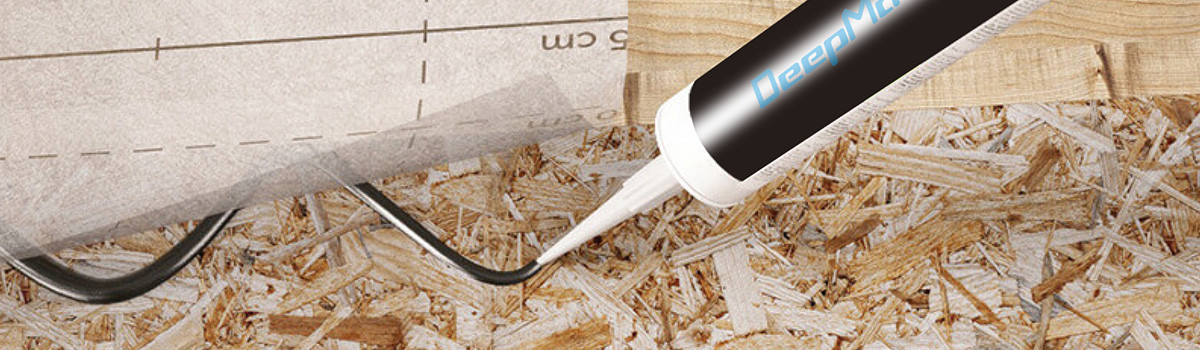
Membrane bonding is a specialized adhesive critical in various industries, including construction, automotive, and manufacturing. It is specifically designed to bond and secure different types of membranes, such as waterproofing membranes, roofing membranes, and automotive membranes. This article will explore the world of membrane-communing adhesives, their applications, benefits, and considerations for selecting suitable adhesives for specific membrane bonding needs.
Understanding Membrane Bonding Adhesive
Membrane bonding adhesive refers to a type of adhesive that is specifically designed for bonding or joining different kinds of membranes together. Membranes are thin sheets or films made of materials such as plastics, rubber, or fabrics, and they are commonly used in various industries for applications like waterproofing, air barriers, insulation, and roofing.
The primary function of membrane bonding adhesives is to create a solid and durable bond between two or more membranes, ensuring their effective performance as a cohesive system. These adhesives are formulated to provide excellent adhesion to a wide range of membrane materials, including polyethylene, polypropylene, PVC, EPDM, TPO, and modified bitumen.
The key characteristics and properties of membrane bonding adhesives include:
- Adhesion strength: Membrane bonding adhesives are designed to provide high bond strength between membranes, ensuring a reliable and long-lasting connection. The adhesion strength is typically tested under various environmental conditions, such as temperature changes, humidity, and exposure to UV radiation, to ensure performance in real-world applications.
- Flexibility: Since membranes are often subjected to movement, expansion, and contraction due to temperature changes or structural stresses, the adhesive must be flexible to accommodate such activities without compromising the bond. Flexibility also helps distribute stress and load evenly across the bonded area, enhancing the overall durability of the system.
- Chemical resistance: Membranes are often exposed to chemicals, water, or other substances, depending on the application. A suitable membrane bonding adhesive should exhibit resistance to these chemicals to ensure the longevity and integrity of the bond. Chemical resistance prevents the adhesive from degrading or weakening when exposed to harsh environments.
- Weather resistance: Outdoor applications of membranes require adhesives that can withstand extreme weather conditions, such as temperature variations, UV radiation, rain, snow, and wind. Weather-resistant sealants maintain their bond strength and overall performance even in harsh outdoor environments, protecting the membranes from premature failure.
- Ease of application: Membrane bonding adhesives are formulated to be user-friendly, allowing easy and efficient application. Depending on the specific application requirements, they may come in different forms, including liquids, tapes, or sheets. Ease of application improves productivity and ensures a uniform bond across the membranes.
- Compatibility: Membrane bonding adhesives must be compatible with the bonded materials. Manufacturers often provide guidelines and compatibility charts to ensure proper adhesive selection for specific membrane materials. Compatibility ensures optimal adhesion and minimizes the risk of bond failure.
Following the manufacturer’s instructions for surface preparation, adhesive application, and curing time is essential to achieve the best results when using membrane-bonding adhesives. Professional consultation or assistance may be necessary, especially for complex applications or specialized membranes.
Overall, membrane-bonding adhesives are critical in creating strong, durable, and reliable bonds between membranes. Their unique properties enable effective membrane systems that provide benefits such as waterproofing, insulation, and air barrier functions in various industries and applications.
The Importance of Effective Membrane Bonding
Adequate membrane bonding is of utmost importance in various industries and applications. Here are some key reasons why it is crucial:
- Structural integrity: Membranes are often used in applications that contribute to a system’s structural integrity. Adequate bonding ensures that the membranes stay securely in place, maintaining the overall stability and strength of the structure. For example, properly bonding waterproofing membranes in roofing systems prevents water leakage and protects the underlying structure from damage.
- Waterproofing and moisture control: Membrane bonding is critical in achieving effective waterproofing and moisture control. When membranes are properly bonded together, they create a continuous barrier preventing water, moisture, or vapor ingress. This is crucial in building envelopes, tunnels, and basements, where moisture intrusion can lead to structural damage, mold growth, and compromised indoor air quality.
- Air and vapor barriers: Membranes are often used as air and vapor barriers to control air and moisture flow in building assemblies. Adequate bonding ensures the continuity and integrity of the barrier system, minimizing air leakage and preventing moisture-related issues such as condensation. Proper air and vapor barrier performance contribute to energy efficiency, occupant comfort, and long-term durability of buildings.
- Energy efficiency: In applications such as insulation systems, membranes enhance energy efficiency by reducing heat transfer or air leakage. Adequate bonding ensures that the insulation membranes are appropriately installed, eliminating gaps or voids that could compromise the thermal performance. This leads to improved energy efficiency, reduced heating and cooling costs, and a more comfortable indoor environment.
- Durability and longevity: Membrane bonding directly impacts the durability and longevity of the system. A well-bonded membrane assembly can withstand external forces, such as wind, temperature fluctuations, and building movement, without compromising performance. It resists degradation and maintains its integrity over time, reducing the need for frequent repairs or replacements and extending the system’s service life.
- Safety and reliability: In specific applications, such as membranes used in hazardous environments or critical infrastructure, adequate bonding is essential for safety and reliability. For example, reliable bonding ensures that the membranes contain the substances securely, minimizing the risk of leaks or environmental contamination in containment systems for chemicals or hazardous waste.
Adequate membrane bonding is crucial for achieving desired performance, functionality, and longevity in various applications. It ensures structural integrity, waterproofing, moisture control, energy efficiency, durability, and safety. Choosing suitable adhesives and following proper installation techniques are crucial to achieving robust and reliable bonds between membranes, ultimately contributing to the success of the overall system or structure.
Applications of Membrane Bonding Adhesive
Membrane bonding adhesives find a wide range of applications across various industries. Here are some typical applications:
- Roofing: Membrane bonding adhesives are extensively used in roofing systems, especially for single-ply membranes such as EPDM, TPO, and PVC. These adhesives create a strong bond between membrane sheets, ensuring a watertight and durable roof. They provide excellent resistance to weathering, UV radiation, and temperature fluctuations, enhancing the roofing system’s longevity.
- Waterproofing: Membrane bonding adhesives are essential for waterproofing applications in construction. They are used to join waterproofing membranes, such as bituminous membranes or liquid-applied membranes, creating a seamless and reliable barrier against water intrusion. These adhesives ensure a tight and secure bond, preventing leaks and protecting structures from moisture-related damage.
- Air and vapor barriers: Membrane bonding adhesives are vital in installing air and vapor barrier systems in buildings. They are used to bond membrane layers, creating a continuous barrier that prevents air leakage and controls the movement of water vapor. These adhesives help maintain energy efficiency, improve indoor air quality, and protect against moisture-related issues like condensation and mold growth.
- Automotive: Membrane bonding adhesives are used in the automotive industry for various applications. They bond interior trim panels, headliners, carpeting, and other components to vehicle structures. These adhesives provide solid and reliable bonds that withstand automotive environments’ vibrations, temperature changes, and other stresses.
- Aerospace: In the aerospace industry, membrane bonding adhesives are employed for bonding and sealing applications. They bond lightweight composite materials in aircraft structures, such as carbon fiber-reinforced polymers. These adhesives offer high strength, light characteristics, and resistance to extreme temperature conditions, ensuring aerospace components’ structural integrity and performance.
- Medical devices: Membrane bonding adhesives find application in the assembly of medical devices. They bond membranes or films in devices such as catheters, wound dressings, and transdermal patches. These adhesives provide biocompatibility, sterile bonding, and flexibility, meeting the stringent requirements of the medical industry.
- Industrial applications: Membrane bonding adhesives are used in various industrial applications where membranes or films must be joined. For example, they produce flexible packaging, laminated materials, inflatable structures, and fabric composites. These adhesives provide reliable bonding for various materials, including plastics, fabrics, and elastomers.
It is worth noting that the specific adhesive requirements may vary depending on the application and the materials being bonded. Manufacturers provide adhesive systems tailored to different membrane types, ensuring compatibility and optimal performance in specific applications.
Waterproofing Membranes in Construction
Waterproofing membranes play a crucial role in protecting structures from water intrusion and moisture-related damage in the construction industry. These membranes are used in various applications, such as basements, roofs, foundations, and below-grade structures. Here are some critical aspects of waterproofing membranes in construction:
- Types of Waterproofing Membranes: Different types of waterproofing membranes are available for construction applications. Some common types include bituminous membranes (modified bitumen or APP/SBS-modified), liquid-applied membranes (polyurethane or acrylic-based), thermoplastic membranes (PVC, TPO, or EPDM), and cementitious membranes. Each type has advantages, installation methods, and compatibility with different substrates.
- Function and Benefits: Waterproofing membranes create a continuous barrier that prevents water, moisture, and vapor penetration into the building structure. They protect against water damage, mold growth, and deterioration of building materials. Waterproofing membranes also contribute to energy efficiency, as they prevent the loss of conditioned air and reduce the potential for condensation.
- Application Areas: Various building areas use waterproofing membranes to provide adequate moisture protection. These include:
- Roofs: Waterproofing membranes are applied to protect flat or sloped ceilings, ensuring they are watertight and weather-resistant. Membranes such as EPDM, TPO, or PVC are commonly used in roofing applications.
- Foundations: Waterproofing membranes are applied to the exterior of below-grade foundations to prevent water infiltration. They help keep the foundation dry, reducing the risk of cracks, mold, and structural damage.
- Basements: To prevent seepage and dampness, waterproofing membranes are essential for basements. They are applied to the interior or exterior walls and floors to create a barrier against groundwater and moisture.
- Wet Areas: Waterproofing membranes are used in wet areas like bathrooms, showers, and swimming pools to prevent water leaks and seepage. They ensure a durable and watertight environment.
- Installation Methods: Installing waterproofing membranes depends on the type of membrane used. Some membranes are self-adhered, while others require the application of adhesive or heat for bonding. Liquid-applied membranes are typically sprayed, rolled, or brushed onto the surface. Proper surface preparation, including cleaning, priming, and leveling, ensures a secure and long-lasting bond.
- Quality Assurance: Quality assurance is essential in waterproofing membrane installations to ensure the effectiveness and durability of the system. This includes proper surface preparation, accurate membrane application, and thorough inspection of seams and overlaps. Quality control measures, such as leak testing and adherence to manufacturer guidelines, should be followed to validate the performance of the waterproofing system.
- Maintenance and Repair: Regular maintenance and timely repair are necessary to preserve the integrity of waterproofing membranes. Inspections should be conducted to identify any signs of damage or deterioration, such as cracks, blisters, or tears. Prompt repairs should be carried out using compatible materials and techniques to prevent water infiltration and maintain the effectiveness of the waterproofing system.
Roofing Membranes for Weather Protection
Roofing membranes are essential components of a building’s envelope, providing crucial weather protection. These membranes are a barrier against water infiltration, wind damage, and other environmental elements. They are designed to create a waterproof, weather-resistant layer that safeguards the underlying structure, insulation, and interior spaces. This article will explore the importance of roofing membranes and discuss some common types used for weather protection.
The primary purpose of roofing membranes is to prevent water from penetrating the roof system. Water infiltration can lead to significant damage, including structural deterioration, mold growth, and compromised insulation. Roofing membranes act as a protective shield, ensuring water drains off the roof surface without seeping into the underlying layers.
One popular type of roofing membrane is the thermoplastic olefin (TPO) membrane. TPO membranes are made from a blend of polypropylene and ethylene-propylene rubber. They offer excellent resistance to ultraviolet (UV) radiation, ozone, and chemical exposure. TPO membranes are highly flexible, making them suitable for roof designs and shapes. They are also heat-weldable, which ensures seamless installation and reduces the risk of leaks.
Another commonly used roofing membrane is the ethylene propylene diene terpolymer (EPDM) membrane. EPDM is a synthetic rubber membrane that exhibits outstanding weather resistance and can withstand extreme temperatures, UV radiation, and ozone exposure without degradation. EPDM membranes are available in large sheets, minimizing the number of seams and joints, which are vulnerable areas for water penetration. They are also highly durable and have a long lifespan.
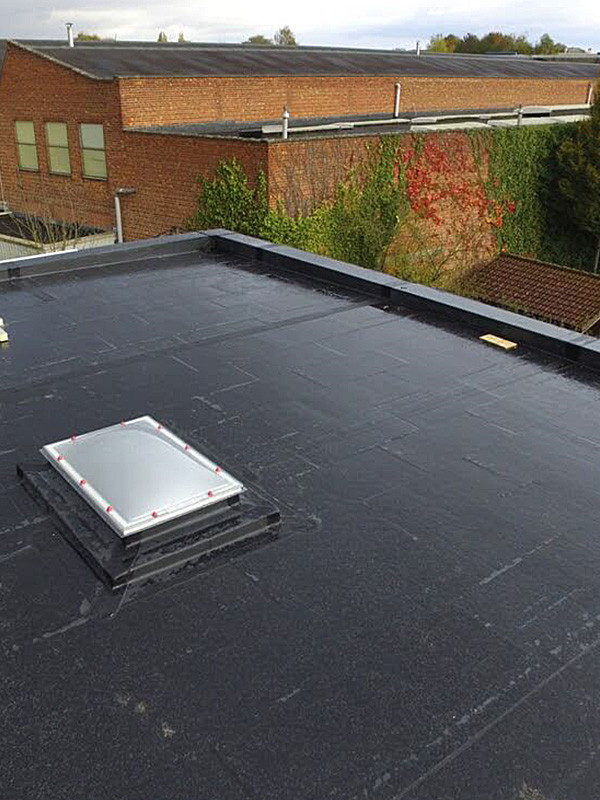
Polyvinyl chloride (PVC) roofing membranes are also popular in the industry. PVC membranes are reinforced with polyester or fiberglass, providing excellent strength and durability. They have high resistance to chemicals, UV radiation, and fire. PVC membranes are known for their energy efficiency as they reflect heat and reduce the cooling load of a building. They are in different colors and can be heat-welded for a watertight seal.
Additionally, modified bitumen membranes are widely used for weather protection. These membranes consist of asphalt modified with polymers to enhance their performance characteristics. Modified bitumen membranes are flexible, easy to install, and offer excellent resistance to water, UV radiation, and thermal stresses. They are available in various forms, including self-adhesive sheets, which simplify installation and minimize the use of open flames.
Automotive Membranes for Noise and Vibration Control
Noise and vibration control are essential for vehicle design and manufacturing, as they significantly impact the comfort and overall driving experience. Automotive membranes have emerged as an effective solution for reducing vehicle noise and vibration. These specially engineered membranes are designed to absorb and dampen vibrations and noise generated by various sources within the vehicle.
Automotive membranes are typically made from high-quality materials such as rubber, elastomers, or composite materials. They are strategically placed in different areas of the vehicle, including the engine compartment, doors, floor, and interior panels, to mitigate noise and vibration effectively.
One of the primary functions of automotive membranes is vibration control. When a vehicle is in motion, various components and systems, such as the engine, transmission, and road contact, can generate vibrations. These vibrations can be transmitted throughout the vehicle structure, resulting in undesirable noise and discomfort for the occupants. Automotive membranes act as vibration isolators by absorbing and dissipating these vibrations, preventing them from propagating to other vehicle parts. This helps to reduce the overall noise levels and enhances the smoothness of the ride.
In addition to vibration control, automotive membranes are crucial in noise reduction. They are designed to absorb and dampen airborne and structure-borne noise within the vehicle. Airborne noise refers to sounds generated by external sources, such as road and wind, while the vehicle’s mechanical components produce structure-borne noise. By incorporating membranes into the vehicle’s construction, the transmission of these noises can be significantly reduced. The membranes absorb the sound energy and convert it into heat, minimizing its impact on the occupants.
Furthermore, automotive membranes offer additional benefits beyond noise and vibration control. They can improve the vehicle’s overall structural integrity by reducing the stress and strain on components subjected to vibrations. This, in turn, can enhance the durability and lifespan of various parts, leading to improved vehicle reliability.
Moreover, automotive membranes contribute to weight reduction initiatives in modern vehicles. By replacing traditional heavy materials with lightweight membranes, manufacturers can save weight without compromising performance or safety. This weight reduction helps improve fuel efficiency and reduces carbon emissions, aligning with the industry’s ongoing efforts toward sustainability.
Industrial and Manufacturing Applications
Membrane bonding adhesive plays a critical role in various industrial and manufacturing applications where the joining and bonding of membranes are required. These adhesive products are specifically formulated to provide robust and durable bonds between different types of membranes, creating reliable and long-lasting structures. Here are some critical applications of membrane bonding adhesive:
- Construction and Roofing: The construction industry extensively uses membrane bonding adhesive, mainly for roofing applications. It allows the secure attachment of roofing membranes, such as EPDM (ethylene propylene diene monomer), PVC (polyvinyl chloride), TPO (thermoplastic olefin), and modified bitumen. The adhesive ensures water-tight seals and resistance against weathering, UV radiation, and extreme temperature conditions.
- Automotive Manufacturing: In the automotive industry, membrane bonding adhesive is utilized for various applications, including the bonding of interior and exterior trim components. These adhesives enable the secure attachment of membranes for headliners, door panels, dashboards, and other vehicle interior elements. The adhesive’s properties ensure strong bonds that withstand vibration, temperature changes, and exposure to chemicals and moisture.
- Aerospace and Aviation: Membrane bonding adhesive finds extensive use in the aerospace and aviation sectors for applications such as aircraft interiors, insulation systems, and composite bonding. It provides reliable adhesion of membranes in aircraft cabins, ensuring structural integrity and fire resistance. The adhesive’s lightweight properties are particularly beneficial in aerospace applications where weight reduction is crucial.
- Marine Industry: Membrane bonding adhesive is employed in the marine industry for applications such as boat construction, deck bonding, and sealing. It enables the adhesion of membranes for decks, hulls, bulkheads, and other marine components. The adhesive’s resistance to water, salt, and environmental elements ensures long-term durability and waterproofing.
- Medical Device Manufacturing: In the medical industry, membrane bonding adhesive is used to assemble various medical devices and equipment. It facilitates the bonding of membranes in surgical instruments, diagnostic devices, and wearable medical sensors. The adhesive’s biocompatibility and sterilization resistance make it suitable for medical applications, ensuring safety and reliability.
- Electronics and Electrical Industry: Membrane bonding adhesive is utilized in the electronics and electrical sectors to bond flexible circuit boards, touchscreens, and display panels. The adhesive enables the attachment of membranes to electronic components, providing electrical conductivity, protection against moisture and dust, and mechanical stability.
- Filtration Systems: Membrane bonding adhesive is crucial in producing filtration systems in industries such as water treatment, pharmaceuticals, and food processing. The adhesive securely bonds membranes to filter housings, ensuring efficient filtration performance and preventing bypass or leakage.
- Energy Sector: Membrane bonding adhesive finds applications in the renewable energy sector, particularly for the manufacturing and installing photovoltaic (PV) modules. The bond facilitates the bonding of membranes, such as encapsulant films, to PV cells and backsheet materials, ensuring proper sealing, weather resistance, and electrical insulation.
These are just a few examples of the diverse range of industrial and manufacturing applications utilizing membrane bonding adhesive. The adhesive’s properties, such as solid bonding, durability, resistance to environmental factors, and compatibility with different materials, make it a valuable solution in various industries, contributing to the production of reliable and high-performance structures and products.
Types of Membrane Bonding Adhesive
Membrane bonding adhesive plays a critical role in various industrial and manufacturing applications where the joining and bonding of membranes are required. These adhesive products are specifically formulated to provide robust and durable bonds between different types of membranes, creating reliable and long-lasting structures. Here are some critical applications of membrane bonding adhesive:
- Construction and Roofing: The construction industry extensively uses membrane bonding adhesive, mainly for roofing applications. It allows the secure attachment of roofing membranes, such as EPDM (ethylene propylene diene monomer), PVC (polyvinyl chloride), TPO (thermoplastic olefin), and modified bitumen. The adhesive ensures water-tight seals and resistance against weathering, UV radiation, and extreme temperature conditions.
- Automotive Manufacturing: In the automotive industry, membrane bonding adhesive is utilized for various applications, including the bonding of interior and exterior trim components. These adhesives enable the secure attachment of membranes for headliners, door panels, dashboards, and other vehicle interior elements. The adhesive’s properties ensure strong bonds that withstand vibration, temperature changes, and exposure to chemicals and moisture.
- Aerospace and Aviation: Membrane bonding adhesive finds extensive use in the aerospace and aviation sectors for applications such as aircraft interiors, insulation systems, and composite bonding. It provides reliable adhesion of membranes in aircraft cabins, ensuring structural integrity and fire resistance. The adhesive’s lightweight properties are particularly beneficial in aerospace applications where weight reduction is crucial.
- Marine Industry: Membrane bonding adhesive is employed in the marine industry for applications such as boat construction, deck bonding, and sealing. It enables the adhesion of membranes for decks, hulls, bulkheads, and other marine components. The adhesive’s resistance to water, salt, and environmental elements ensures long-term durability and waterproofing.
- Medical Device Manufacturing: In the medical industry, membrane bonding adhesive is used to assemble various medical devices and equipment. It facilitates the bonding of membranes in surgical instruments, diagnostic devices, and wearable medical sensors. The adhesive’s biocompatibility and sterilization resistance make it suitable for medical applications, ensuring safety and reliability.
- Electronics and Electrical Industry: Membrane bonding adhesive is utilized in the electronics and electrical sectors to bond flexible circuit boards, touchscreens, and display panels. The adhesive enables the attachment of membranes to electronic components, providing electrical conductivity, protection against moisture and dust, and mechanical stability.
- Filtration Systems: Membrane bonding adhesive is crucial in producing filtration systems in water treatment, pharmaceuticals, and food processing industries. The adhesive securely bonds membranes to filter housings, ensuring efficient filtration performance and preventing bypass or leakage.
- Energy Sector: Membrane bonding adhesive finds applications in the renewable energy sector, particularly for the manufacturing and installing photovoltaic (PV) modules. The bond facilitates the bonding of membranes, such as encapsulant films, to PV cells and backsheet materials, ensuring proper sealing, weather resistance, and electrical insulation.
These are just a few examples of the diverse range of industrial and manufacturing applications utilizing membrane bonding adhesive. The adhesive’s properties, such as solid bonding, durability, resistance to environmental factors, and compatibility with different materials, make it a valuable solution in various industries, contributing to the production of reliable and high-performance structures and products.
Water-Based Membrane Bonding Adhesive
Water-based membrane bonding adhesive is a type of adhesive that is formulated with water as the primary carrier. It is widely used in various industrial and manufacturing applications where membrane bonding and joining are required. Water-based adhesives offer several advantages, including environmental friendliness, ease of use, and versatility. Here are some critical aspects of water-based membrane bonding adhesive:
- Environmental Friendliness: One of the significant advantages of water-based adhesives is their reduced environmental impact. Water-based adhesives have lower levels of volatile organic compounds (VOCs), known to contribute to air pollution, than solvent-based adhesives. As the primary carrier in these adhesives, water minimizes the emission of harmful substances during application and curing. This makes water-based adhesives a more environmentally friendly option, particularly in applications where reducing VOC emissions is a priority.
- Non-Flammability: Water-based adhesives are non-flammable, making them safer to handle and store than solvent-based adhesives. This non-flammable nature eliminates the need for additional safety precautions associated with flammable adhesives, reducing the risk of accidents and fire hazards in the workplace.
- Easy Clean-Up: Water-based adhesives offer easy clean-up and removal. They can be easily cleaned with water, eliminating the need for harsh solvents or chemicals. This simplifies the maintenance and cleaning, contributing to a safer and more efficient working environment.
- Good Adhesion Properties: Water-based adhesives provide reliable bonding properties for various membrane materials. They offer good adhesion to different surfaces, including metals, plastics, fabrics, and composite materials. Water-based adhesives can effectively bond membranes such as EPDM, PVC, TPO, and modified bitumen, commonly used in roofing, construction, and other industrial applications.
- Versatility: Water-based adhesives can be used in various application methods, including spraying, roller coating, and brush application. They can be easily adjusted and optimized for specific bonding requirements, allowing flexibility in different manufacturing processes. Additionally, water-based adhesives can be formulated with additives to enhance specific properties, such as flexibility, heat resistance, or improved bond strength, to meet the unique needs of different applications.
- Lower Odor: Water-based adhesives generally have lower odor compared to solvent-based counterparts. This makes them more suitable for indoor applications, especially in areas where strong odors, such as occupied buildings or manufacturing facilities, are a concern.
- Wide Range of Applications: Water-based membrane bonding adhesive finds applications in various industries and sectors. It is commonly used in construction and roofing for bonding roofing membranes, providing effective waterproofing and weather resistance. Water-based adhesives are also utilized in automotive manufacturing for interior trim bonding, marine applications for deck bonding, and other industrial applications where reliable and durable membrane bonding is required.
Water-based membrane bonding adhesive offers several benefits, including environmental friendliness, non-flammability, ease of clean-up, and good adhesion properties. Its versatility and suitability for various applications make it a preferred choice in industries prioritizing performance and sustainability. Using water-based adhesives aligns with the growing demand for eco-friendly and safe bonding solutions in industrial and manufacturing processes.
Solvent-Based Membrane Bonding Adhesive
In various industries, strong and durable bonding solutions are paramount. Regarding joining membranes and other flexible materials, solvent-based membrane bonding adhesives have proven to be a practical choice. This adhesive type offers excellent adhesion, versatility, and reliability in various applications. This article will explore the key features, benefits, and applications of solvent-based membrane bonding adhesives.
Key Features: Solvent-based membrane bonding adhesives are formulated with high-quality synthetic polymers dissolved in solvents. This composition provides several key features that make them ideal for bonding applications:
- Strong Adhesion: Solvent-based adhesives exhibit exceptional bonding strength, creating reliable and long-lasting bonds between membranes. They form a durable connection, even in demanding conditions, ensuring structural integrity.
- Versatility: These adhesives are compatible with various membrane materials, including PVC, EPDM, TPO, and modified bitumen. This versatility allows them to be used in multiple industries, such as roofing, construction, automotive, and packaging.
- Fast Drying Time: Solvent-based adhesives have a quick evaporation rate, enabling rapid drying. This characteristic improves productivity by reducing assembly time and allowing faster processing.
- Excellent Heat and Chemical Resistance: The cured bonds created by solvent-based adhesives exhibit exceptional resistance to high temperatures and chemicals. This makes them suitable for applications where exposure to extreme conditions or harsh environments is expected.
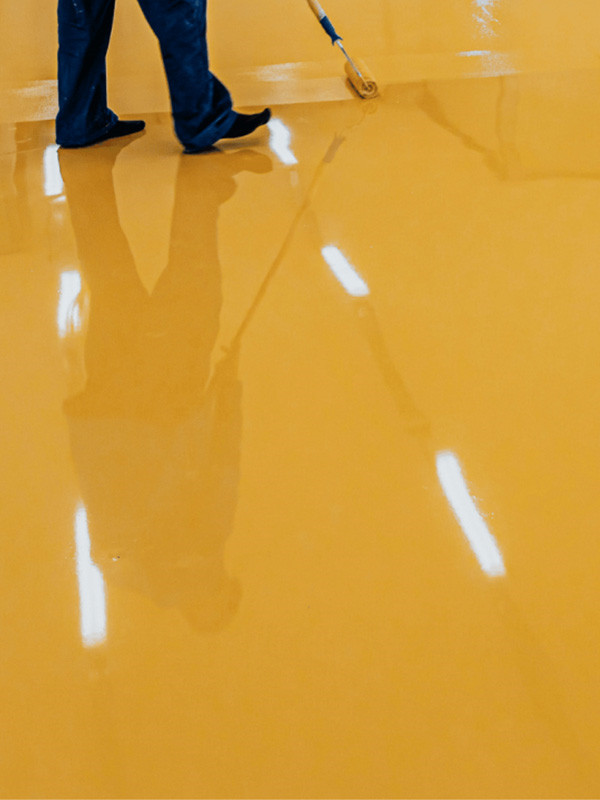
Benefits: The utilization of solvent-based membrane bonding adhesives provides several notable benefits:
- Enhanced Durability: The strong and resilient bonds these adhesives form ensure long-lasting performance, withstanding the rigors of daily use and environmental stresses. This durability contributes to improved product lifespan and reduces the need for frequent repairs or replacements.
- Improved Waterproofing: Membrane bonding adhesives help create watertight seals, preventing water infiltration and protecting underlying structures. This is particularly crucial in roofing applications, where water resistance is essential for maintaining the integrity of the building envelope.
- Cost-Effective Solution: Solvent-based adhesives offer a cost-effective bonding solution due to their efficient application and long-lasting performance. Their ability to adhere to a wide range of materials eliminates the need for multiple adhesive types, reducing inventory costs.
Applications: Solvent-based membrane bonding adhesives find extensive applications across various industries:
- Roofing: These adhesives are widely used in roofing to bond single-ply membranes, such as PVC and TPO, providing secure and leak-resistant seals.
- Construction: Solvent-based adhesives are employed for bonding architectural membranes, vapor barriers, and insulation materials in construction projects, ensuring structural integrity and energy efficiency.
- Automotive: They are utilized in the automotive sector for bonding flexible components, such as door panels, headliners, and carpeting, offering strength, and durability even in challenging driving conditions.
- Packaging: Solvent-based adhesives provide effective bonding solutions for flexible packaging materials, such as films and laminates, ensuring secure seals and product protection.
Two-Component Membrane Bonding Adhesive
A reliable and robust adhesive solution is essential for bonding membranes and other flexible materials. Two-component membrane bonding adhesives have emerged as a popular choice in various industries due to their exceptional strength, versatility, and reliability. This article will delve into the key features, benefits, and applications of two-component membrane bonding adhesives.
Key Features: Two-component membrane bonding adhesives consist of two separate components, typically a resin and a hardener, mixed just before application. This unique composition provides several key features that make them highly effective:
- Superior Strength: Two-component adhesives offer exceptional bonding strength, creating robust and durable membrane connections. They can withstand significant stress, ensuring long-lasting and reliable bonds.
- Adjustable Cure Time: The cure time of two-component adhesives can be adjusted by altering the ratio of resin to hardener or by selecting different curing agents. This versatility allows for tailored application, ensuring sufficient working time and desired cure speed.
- High Chemical Resistance: These adhesives exhibit excellent chemical resistance, making them suitable for applications where exposure to harsh substances is expected. They can maintain their integrity even in chemically aggressive environments.
- Versatile Substrate Compatibility: Two-component adhesives are compatible with various membrane materials, including PVC, EPDM, TPO, and polyurethane. This versatility makes them suitable for diverse industries and applications.
Benefits: Utilizing two-component membrane bonding adhesives provides several notable benefits:
- Exceptional Bond Strength: The solid and durable bonds formed by two-component adhesives ensure structural integrity and longevity. They can withstand extreme conditions and heavy loads, making them suitable for demanding applications.
- Increased Flexibility: These adhesives offer flexibility regarding cure time and adhesive properties. They can be adjusted to match the specific requirements of a project, allowing for enhanced customization and optimization.
- Enhanced Resistance: Two-component adhesives resist temperature variations, moisture, UV exposure, and other environmental factors. This resistance ensures long-term performance and minimizes the risk of bond failure.
- Versatile Applications: These adhesives find applications in various industries. They are commonly used in roofing, construction, automotive, and marine sectors, where strong and reliable bonding of membranes is crucial.
Applications: Two-component membrane bonding adhesives have a wide range of applications:
- Roofing: They are extensively used in roofing systems for bonding membranes, including EPDM, TPO, and PVC, ensuring secure and weather-resistant seals that withstand harsh environmental conditions.
- Construction: Two-component adhesives are employed for bonding architectural membranes, such as vapor barriers and waterproofing membranes, providing robust connections and protection against moisture intrusion.
- Automotive: They find applications in the automotive industry for bonding flexible components, such as interior trim, upholstery, and sound-deadening materials, offering strength, durability, and vibration resistance.
- Marine: These adhesives bond marine-grade membranes and materials, such as boat hulls, decks, and interior panels, ensuring watertight seals and structural integrity in challenging marine environments.
Flexible Membrane Bonding Adhesive
Flexible membranes are widely used in the construction, automotive, and packaging industries for their versatility and performance. A specialized adhesive is required to achieve secure and durable bonding between flexible membranes. Flexible membrane bonding adhesives are formulated to provide excellent adhesion and flexibility, ensuring solid and reliable bonds. This article will explore the key features, benefits, and applications of flexible membrane bonding adhesives.
Key Features: Flexible membrane bonding adhesives are designed with specific properties to meet the requirements of bonding flexible materials. Here are some key features of these adhesives:
- Flexibility: These adhesives exhibit a high degree of flexibility, allowing them to accommodate the natural movements and expansions of flexible membranes without compromising the bond. This flexibility helps prevent bond failure and ensures long-term durability.
- Good Adhesion to Flexible Substrates: Flexible membrane bonding adhesives are formulated to establish strong adhesion to a wide range of flexible materials. They bond effectively to substrates such as PVC, EPDM, TPO, polyurethane, and other elastomeric membranes commonly used in various industries.
- Weather Resistance: These adhesives resist weathering elements such as UV radiation, moisture, temperature variations, and chemical exposure. This weather resistance ensures the longevity of the bond, even in harsh environments.
- Easy Application: Flexible membrane bonding adhesives are designed for ease of use. They can be applied using various methods, including a brush, roller, or spray, depending on the application’s specific requirements. Their formulation allows for smooth and consistent application.
Benefits: Utilizing flexible membrane bonding adhesives provides several significant advantages:
- Solid and Durable Bonds: These adhesives create strong and durable bonds between flexible membranes, ensuring the integrity and longevity of the assembly. They can withstand stress, movement, and environmental conditions, providing reliable performance.
- Improved Flexibility: By maintaining flexibility even after curing, these adhesives allow the bonded membranes to move and expand without causing cracks or failures. This flexibility enhances the overall performance and lifespan of the bonded assembly.
- Enhanced Watertight Seals: Flexible membrane bonding adhesives help create watertight seals between membranes, providing adequate protection against water infiltration. This is particularly crucial in applications such as roofing and waterproofing, where water resistance is essential.
- Versatile Applications: Flexible membrane bonding adhesives find applications in various industries. They are commonly used in roofing systems, automotive manufacturing, flexible packaging, and other applications that require bonding flexible membranes and materials.
Applications: Flexible membrane bonding adhesives have a wide range of applications across industries:
- Roofing: These adhesives are extensively used in roofing systems to bond flexible roofing membranes, such as TPO, PVC, and EPDM, providing reliable and long-lasting waterproofing and weather resistance.
- Automotive: They find applications in the automotive industry for bonding flexible components such as weatherstripping, door seals, interior trim, and upholstery, ensuring solid and durable connections that can withstand the dynamic movements of vehicles.
- Packaging: Flexible membrane bonding adhesives are used in the packaging industry for bonding flexible films and laminates, providing secure seals and maintaining the integrity of the packaged products.
- Construction: These adhesives are employed in the construction industry for bonding architectural membranes, vapor barriers, and insulation materials, ensuring airtight and weather-resistant assemblies.
Fast-Curing Membrane Bonding Adhesive
Fast-curing adhesive solutions are highly sought after in industries where efficiency and productivity are critical. Fast-curing membrane bonding adhesives are formulated to provide rapid assembly and bonding of membranes and flexible materials. This article will explore the key features, benefits, and applications of fast-curing membrane-bonding adhesives.
Key Features: Fast-curing membrane bonding adhesives offer unique features that enable quick and efficient bonding processes. Here are some key features of these adhesives:
- Rapid Cure Time: These adhesives are designed to cure quickly and achieve strong bonds. They offer significantly reduced cure times compared to traditional adhesives, allowing for faster production cycles and improved productivity.
- High Initial Strength: Fast-curing adhesives exhibit high initial strength shortly after application. This enables faster handling and assembly of bonded components, minimizing the need for extended clamping or curing times.
- Versatile Application Methods: These adhesives can be applied using various methods, including spray, roller, or brush application. This versatility allows for efficient and precise application, catering to different bonding requirements and production processes.
- Compatibility with Multiple Substrates: Fast-curing membrane bonding adhesives are formulated to bond a wide range of substrates, including PVC, EPDM, TPO, and other flexible materials commonly used in industries such as roofing, construction, and automotive.
Benefits: Utilizing fast-curing membrane bonding adhesives offers several notable benefits:
- Increased Efficiency: The rapid cure time of these adhesives significantly reduces the assembly and production cycle, resulting in improved efficiency and faster turnaround times. This enables manufacturers to increase output without compromising bond strength or quality.
- Time and Cost Savings: Faster curing reduces labor costs and energy consumption. The ability to quickly move on to the next production step or shipment can lead to substantial time and cost savings in manufacturing processes.
- Improved Productivity: Fast-curing adhesives enhance productivity by minimizing waiting or idle times. They allow quick assembly, reduce production lead times, and meet tight deadlines.
- Reliable Bond Strength: Despite their fast curing properties, these adhesives maintain high bond strength and durability. They provide reliable and long-lasting bonds, ensuring the structural integrity and performance of the assembled components.
Applications: Fast-curing membrane bonding adhesives find applications across various industries:
- Roofing: These adhesives are commonly used in roofing applications, such as bonding single-ply membranes like TPO, PVC, or EPDM. Fast curing allows for efficient installation and ensures watertight seals, enhancing the speed and quality of roofing projects.
- Construction: Fast-curing adhesives are employed in construction for bonding architectural membranes, insulation materials, and vapor barriers. Their quick cure time enables faster construction processes and helps meet project deadlines.
- Automotive: They find applications in the automotive industry for bonding flexible components, such as door panels, headliners, and carpeting. The rapid cure time ensures efficient assembly on the production line without compromising bond strength or quality.
- General Manufacturing: Fast-curing adhesives are used in various manufacturing processes involving flexible bonding materials. They enable quick assembly and bonding of items such as flexible packaging, membranes for inflatable structures, and flexible composite parts.
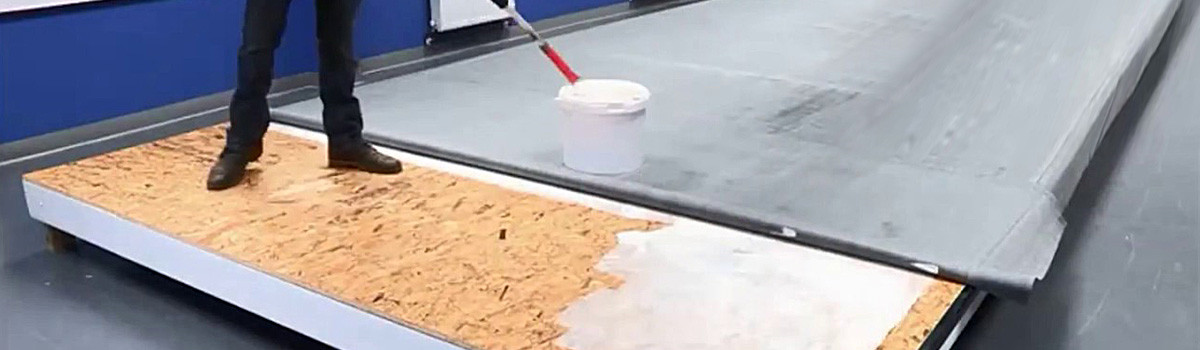
Considerations for Selecting Membrane Bonding Adhesive
When selecting a membrane bonding adhesive, several key considerations should be considered to ensure a successful and durable bond. These considerations include substrate compatibility, environmental conditions, application requirements, and adhesive properties. Here are some essential points to consider:
- Substrate Compatibility: Assess the bonded materials to ensure compatibility with the adhesive. Different adhesives have varying affinities for other substrates such as metals, plastics, rubber, or composites. Consider the substrate’s surface energy, roughness, and chemical composition to determine the adhesive’s suitability.
- Environmental Conditions: Evaluate the conditions the bonded membrane will encounter, including temperature extremes, humidity, and exposure to UV radiation, chemicals, or water. Select an adhesive that can withstand these conditions without compromising its bond strength or durability.
- Bond Strength and Durability: Determine the required strength of the bond based on the application’s mechanical stress and load-bearing requirements. Consider factors such as shear, tensile, and peel strength, as well as the anticipated lifespan of the bonded assembly. Ensure the selected adhesive can provide the necessary strength and long-term durability.
- Application Method: Consider the available methods for applying the adhesive. Some adhesives are supplied as liquids, films, or tapes, while others may require mixing or curing processes. Choose a bond compatible with the application method and easily applied to the membrane and substrate.
- Curing Time and Process: Understand the curing time and process of the adhesive. Some adhesives require heat, UV light, or moisture to initiate or accelerate the curing process, while others cure at room temperature. Consider the available curing equipment and time constraints to select an adhesive that meets the application’s requirements.
- Chemical Resistance: Evaluate the adhesive’s resistance to chemicals or solvents that may come into contact with the bonded assembly. Specific applications may involve exposure to fuels, oils, acids, or cleaning agents. Please verify that the adhesive can withstand such substances without degrading or compromising its bond strength.
- Flexibility and Elasticity: Consider the flexibility and elasticity requirements of the bonded assembly. Some applications may undergo significant thermal expansion, contraction, or vibration. Choose an adhesive that can accommodate these movements without causing stress concentrations or bond failure.
- Regulatory Compliance: Determine if any specific regulatory requirements or industry standards apply to the application. Ensure the selected adhesive meets compliance standards for flammability, toxicity, or food contact.
- Cost and Availability: Assess the cost-effectiveness of the adhesive, taking into account factors such as the quantity required, shelf life, and ease of procurement. Consider the availability of the adhesive from reputable suppliers and its long-term availability for potential repairs or replacements.
- Testing and Validation: Conduct thorough testing and validation of the adhesive in relevant conditions and application-specific scenarios. Perform adhesion and durability tests, and simulate the anticipated service conditions to ensure the bond performs as expected.
By carefully considering these factors, you can select a membrane bonding adhesive compatible with the materials, application requirements, and environmental conditions, ensuring a robust and reliable bond for your specific application.
Membrane Compatibility and Substrate Preparation
Membrane compatibility and substrate preparation are crucial considerations when selecting an adhesive for membrane bonding. Proper surface preparation and compatibility assessment plays a significant role in achieving a solid and durable bond. Here’s a detailed explanation of these factors:
- Membrane Compatibility: Ensuring the adhesive is compatible with the membrane material is essential. Membranes can be made of various materials such as PVC, EPDM, TPO, or PTFE. Each material may have different surface properties, chemical composition, or surface energy. Some adhesives work better with certain membrane materials, while others may not bond effectively. Consult the manufacturer’s guidelines or conduct compatibility tests to determine the best adhesive for the specific membrane material.
- Substrate Preparation: Proper substrate preparation is crucial for ensuring good adhesion. The substrate should be clean, dry, and free from contaminants that may hinder the bonding process. Follow these steps for substrate preparation:
- Cleaning: Remove dust, dirt, grease, or oils from the substrate surface. Use appropriate cleaning solvents or detergents and ensure thorough rinsing to eliminate residue.
- Surface Roughening: In some cases, it may be necessary to roughen the substrate surface to improve adhesive bonding. This can be achieved through methods such as sanding, grit blasting, or using chemical etching agents. The goal is to create a roughened surface that enhances mechanical interlocking between the adhesive and the substrate.
- Priming: Depending on the substrate material, a primer may be required to enhance adhesion. Primers help improve the wetting and bonding ability of the adhesive to the substrate. Following the manufacturer’s instructions, they can be applied by brushing, spraying, or dipping.
- Membrane Surface Treatment: Similar to substrates, the membrane surface may require treatment to enhance bonding. Some membranes have a smooth or non-porous surface, making it challenging for adhesives to adhere effectively. Consider the following treatments:
- Membrane Cleaning: Clean the membrane surface thoroughly to remove any dirt, dust, or oils that could interfere with the adhesive bond.
- Surface Activation: Some membranes may benefit from surface activation techniques such as corona or flame treatment. These methods modify the surface energy of the membrane, improving the wettability and bonding characteristics.
- Surface Priming: Certain membrane materials may require the application of a primer to enhance adhesion. The primer promotes better adhesion between the membrane and the adhesive. Ensure the primer is compatible with both the membrane and the adhesive.
- Adhesive Selection: Consider the adhesive’s membrane compatibility and substrate preparation recommendations. Adhesive manufacturers often provide guidelines and recommendations for surface preparation techniques, primers, or cleaners to be used with their products. Follow these recommendations closely to ensure optimal bonding performance.
By considering membrane compatibility and implementing proper substrate preparation techniques, you can improve the chances of achieving a solid and durable bond. Adhering to the manufacturer’s guidelines, conducting compatibility tests, and following recommended surface preparation methods will help maximize the effectiveness of the adhesive and ensure long-lasting membrane bonding.
Environmental Factors and Resistance Properties
Environmental factors play a critical role in membrane-bonding adhesives’ performance and resistance properties. Membrane bonding adhesives are used in various industries, including construction, automotive, and electronics, to bond membranes to different substrates securely. The adhesive’s ability to withstand environmental stressors is crucial for maintaining the integrity and durability of the bonded membranes.
One of the critical environmental factors that impact membrane bonding adhesives is temperature. Adhesives are often subjected to various temperatures, from extreme cold to high heat. Temperature fluctuations can affect the adhesive’s viscosity, curing time, and bond strength. Adhesives designed for cold environments must remain flexible and retain bonding properties even at low temperatures. On the other hand, adhesives used in high-temperature applications must have excellent heat resistance to prevent bond failure or degradation.
Moisture and humidity levels also significantly influence the resistance properties of membrane-bonding adhesives. Excessive moisture can negatively impact the adhesive’s performance by reducing bond strength and causing adhesive failure. Water can also trigger chemical reactions or swelling in certain adhesives, leading to dimensional changes or loss of adhesion. Therefore, moisture resistance properties, such as moisture-curing or waterproof adhesives, are often preferred for applications where exposure to water or high humidity is expected.
Chemical exposure is another important environmental factor to consider. Depending on the application, adhesives may come into contact with various chemicals, such as solvents, acids, or alkalis. Certain chemicals can degrade the adhesive, leading to bond failure. It is essential to select adhesives with chemical resistance properties that can withstand exposure to specific substances encountered in the environment.
Ultraviolet (UV) radiation from the sun can also impact the resistance properties of membrane-bonding adhesives. Prolonged exposure to UV rays can cause the adhesive to degrade, leading to reduced bond strength and adhesive failure. UV-resistant sealants, often formulated with special additives or polymers, can protect against UV radiation and maintain their performance in outdoor applications.
Mechanical stressors, such as vibration, impact, or shear forces, are common environmental challenges membrane-bonding adhesives face. Adhesives used in applications where mechanical stress is prevalent, such as automotive or aerospace industries, require high resistance to these forces. Toughened adhesives or flexible formulations are often employed to enhance the adhesive’s resistance to mechanical stress and prevent bond failure.
Application Techniques and Methods
Applying membrane bonding adhesives correctly is crucial for achieving solid and durable bonds. The application technique and method can significantly impact the adhesive’s performance and the overall quality of the bonded membrane. Here are some important considerations and strategies for effectively applying membrane bonding adhesives:
- Surface Preparation: Proper surface preparation is vital to ensure good adhesion. The surfaces to be bonded should be clean, dry, and free from contaminants, such as dust, oil, grease, or loose particles. Depending on the substrate material, surface cleaning methods may include solvent wiping, sanding, or using a surface primer to promote adhesion.
- Adhesive Mixing: If the membrane bonding adhesive requires mixing, follow the manufacturer’s instructions carefully to achieve the correct ratio and thorough mixing. Inadequate mixing can result in incomplete curing, reduced bond strength, or uneven adhesive properties.
- Application Method: The choice of application method depends on the specific adhesive and the size and shape of the bonding area. Standard application methods for membrane bonding adhesives include:
- Brush/Roller: Suitable for large bonding areas, a brush or roller can evenly spread the adhesive over the surface. This method is commonly used in construction or roofing applications.
- Spray: Using a spray system allows for quick and uniform adhesive application. It is beneficial for large areas or when a thin and even adhesive layer is required.
- Trowel/Notched Trowel: Ideal for thicker adhesives or when a specific adhesive thickness is needed. The notched trowel ensures proper coverage and uniform distribution of the adhesive.
- Extrusion: In some cases, adhesives are dispensed using extrusion equipment, such as a caulking gun or specialized dispensing systems. This method allows precise application and control of the adhesive bead size.
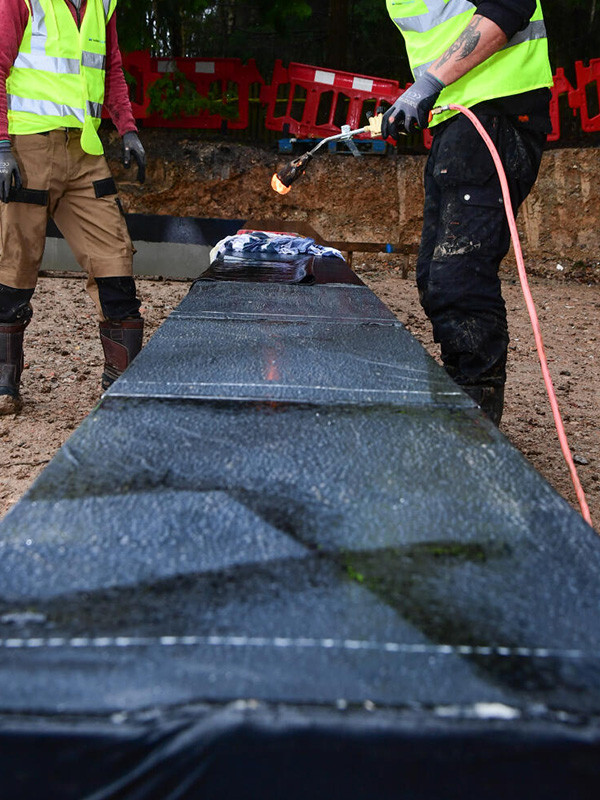
- Open Time and Pot Life: The available time refers to when the adhesive remains workable after application, allowing for positioning and adjusting the membrane. It is essential to know the adhesive’s open time and work efficiently within that timeframe. The pot life refers to the time the mixed adhesive remains usable before it begins to cure. Adhesives should be applied and used within the specified pot life.
- Bonding and Pressing: After applying the adhesive, carefully position the membrane onto the adhesive-coated surface. Use appropriate tools, such as rollers or press pads, to apply even pressure across the entire bonded area. This step helps ensure proper contact and adhesion between the membrane and the substrate.
- Curing and Drying: Adhesives have specific curing or drying times, which should be followed for optimal bonding. Allow sufficient time for the adhesive to cure or dry according to the manufacturer’s recommendations before subjecting the bonded membrane to stress or loading.
- Quality Control and Testing: It is crucial to perform quality control checks and testing to verify the strength and integrity of the bond. This may involve conducting pull, shear, or other relevant tests to ensure the adhesive has achieved the desired performance.
Always refer to the manufacturer’s guidelines and instructions for the specific membrane bonding adhesive being used. Adhering to proper application techniques and methods, along with appropriate surface preparation, will help ensure successful bonding and enhance the longevity and performance of the bonded membrane.
Durability and Longevity of Bonded Membranes
Bonded membranes are widely used in various industries and applications due to their exceptional durability and longevity. These membranes provide a protective barrier, enhance structural integrity, and prevent moisture infiltration or other harmful substances. Here, we will explore the key factors contributing to bonded membranes’ durability and longevity.
- Material Selection: The choice of materials for bonded membranes is crucial in determining their durability. High-quality materials such as synthetic rubbers, modified bitumens, or thermoplastic olefins (TPO) are commonly used due to their excellent resistance to weathering, UV radiation, and chemical exposure. These materials offer superior strength, flexibility, and resilience, ensuring long-term performance and longevity.
- Bonding Technology: The bonding technology employed during the installation of membranes significantly affects their durability. Proper surface preparation, adhesive selection, and application techniques are critical for achieving a solid and durable bond between the membrane and the substrate. Advanced bonding methods like heat-welding or solvent welding create robust, seamless connections that resist separation, cracking, or peeling over time.
- Structural Design: The design of bonded membranes is vital to their longevity. Reinforcement layers, such as polyester or fiberglass, are often incorporated within the membrane structure to enhance its strength and resistance to tearing or puncturing. The membrane’s thickness and composition are also tailored to meet specific performance requirements, considering load-bearing capacity, anticipated movement, and environmental conditions.
- Weather Resistance: Durability in outdoor environments heavily depends on a bonded membrane’s ability to withstand weather extremes. High-quality membranes are engineered to resist temperature fluctuations, thermal cycling, and ultraviolet (UV) radiation exposure. UV stabilizers and reflective coatings can be added to the membrane surface to enhance its resistance to UV degradation, reducing the risk of cracking, embrittlement, or color fading.
- Maintenance and Inspections: Regular maintenance and inspections are essential for ensuring the long-term durability of bonded membranes. Assessments can identify early signs of damage or deterioration, enabling timely repairs and preventing more significant issues. Proper cleaning and maintenance procedures, as the membrane manufacturer recommends, help preserve the membrane’s performance characteristics and extend its lifespan.
- Quality Assurance: Adhering to industry standards and regulations and engaging reputable manufacturers and contractors is crucial to ensure the durability of bonded membranes. Reliable suppliers offer high-quality products with rigorous testing and certification processes, providing confidence in their long-term performance.
Maintenance and Repair of Membrane Bonding Adhesive
Proper maintenance and timely repairs are crucial for ensuring membrane bonding adhesives’ optimal performance and longevity. These adhesives are used to create solid and durable bonds between membranes and substrates, and their effectiveness can be affected by various factors such as environmental conditions, aging, and wear. Here, we will discuss the critical aspects of maintenance and repair for membrane bonding adhesives.
- Regular Inspections: Conducting routine inspections is essential to identify any signs of damage, deterioration, or adhesive failure. Inspections should be carried out periodically, following the manufacturer’s recommendations, and any issues should be addressed promptly to prevent further damage or compromise to the bonded membrane system.
- Cleaning: Proper cleaning of the bonded membrane system can help maintain the adhesive’s performance and extend its lifespan. Remove any debris, dirt, or contaminants from the membrane surface and the substrate using suitable cleaning agents or methods recommended by the adhesive manufacturer. This ensures a clean and smooth character for optimal bonding performance.
- Adhesive Compatibility: When repairs are needed, using an adhesive compatible with the existing bonding system is crucial. Check the adhesive manufacturer’s guidelines to ensure compatibility with the specific membrane material and substrate. Using incompatible adhesives can lead to poor adhesion, reduced durability, or even damage to the membrane or substrate.
- Surface Preparation: Proper surface preparation is essential before applying the adhesive for repairs. Thoroughly clean the bonding surfaces, removing contaminants, loose particles, or old adhesive residue. Additional surface preparation steps such as sanding, priming, or applying a bonding agent may be required depending on the specific bond and substrate. Following the manufacturer’s instructions is crucial for optimal bonding strength and durability.
- Application Techniques: When applying adhesive for repairs, carefully follow the recommended application techniques provided by the manufacturer. Apply the adhesive evenly and at the recommended thickness to ensure proper bonding and avoid excessive or insufficient adhesive application. Adequate temperature and humidity conditions during application should also be maintained as the adhesive manufacturer specifies.
Future Developments in Membrane Bonding Adhesive
The field of membrane bonding adhesive is continually evolving, driven by advancements in materials science, manufacturing processes, and industry demands. Future developments can be expected in membrane bonding adhesives to enhance performance, sustainability, and ease of use. Here are some potential effects to look out for:
- Environmentally Friendly Formulations: With a growing emphasis on sustainability, there is a rising demand for membrane-bonding adhesives with minimal environmental impact. Future developments may focus on formulating adhesives with reduced volatile organic compounds (VOCs) and hazardous substances, ensuring compliance with environmental regulations. Biodegradable or bio-based adhesives may also be developed, offering a more eco-friendly alternative.
- Enhanced Durability and Performance: Pursuing longer-lasting and high-performing bonding adhesives will continue. Research and development efforts may focus on improving adhesive formulations to strengthen resistance against extreme weather conditions, UV radiation, chemical exposure, and aging. This would result in adhesives that maintain strength and bond integrity for extended periods, even in harsh environments.
- Novel Bonding Technologies: Advancements in bonding technologies may lead to the development of innovative adhesive systems. For example, introducing smart adhesives that can self-heal or adapt to changing conditions could revolutionize the field. Integrating nanotechnology into adhesive formulations may enhance adhesive strength, flexibility, and other desired properties.
- Faster Cure Times: Traditional adhesive systems often require significant curing time before reaching their maximum strength. Future developments may accelerate the curing process through novel curing mechanisms, such as UV or moisture-activated adhesives. This would allow for faster installation and reduce downtime in various applications.
- Improved Compatibility: Membrane bonding adhesives must be compatible with various membrane materials, substrates, and surface conditions. Future developments aim to enhance the compatibility of adhesives, ensuring solid and reliable bonds across diverse applications. This could involve developing adhesives with broader adhesion capabilities or specific formulations tailored for different materials and substrates.
- Ease of Application: Simplifying the application process is another area for potential development. Adhesive manufacturers may focus on creating adhesives with improved ease of use, such as pre-mixed or pre-applied adhesive systems. These advancements would streamline the installation process, reduce the risk of application errors, and potentially enable less experienced workers to achieve high-quality bonding.
- Advanced Quality Control: As the demand for reliability and consistency increases, future developments may involve advanced quality control measures for adhesive production. This could include implementing automated inspection systems, real-time monitoring of adhesive properties during the application, and using advanced analytics and machine learning algorithms to optimize adhesive formulations.
Conclusion
Membrane bonding adhesive is versatile and essential in various industries, providing secure and reliable bonding for membranes used in construction, automotive, and manufacturing applications. By selecting the appropriate adhesive based on factors such as membrane compatibility, environmental conditions, and application techniques, industries can ensure bonded membranes’ long-lasting and effective performance. As advancements continue, future developments in membrane bonding adhesive are expected to enhance bonding strength, durability, and application efficiency.