How to Evaluate Industrial Epoxy Adhesive Suppliers for Quality and Reliability
How to Evaluate Industrial Epoxy Adhesive Suppliers for Quality and Reliability
Industrial epoxy adhesive is a bonding agent which is used in everything from automotive and aerospace industries to electronics and construction, offering unparalleled strength and durability. However, not all epoxy adhesives are created equal, and the supplier you choose can significantly impact the quality and reliability of your products.
This blog post aims to guide you through the process of evaluating industrial epoxy adhesive suppliers for quality and reliability. We will delve into the key factors to consider, from the supplier’s reputation and experience to their quality control measures and customer service.
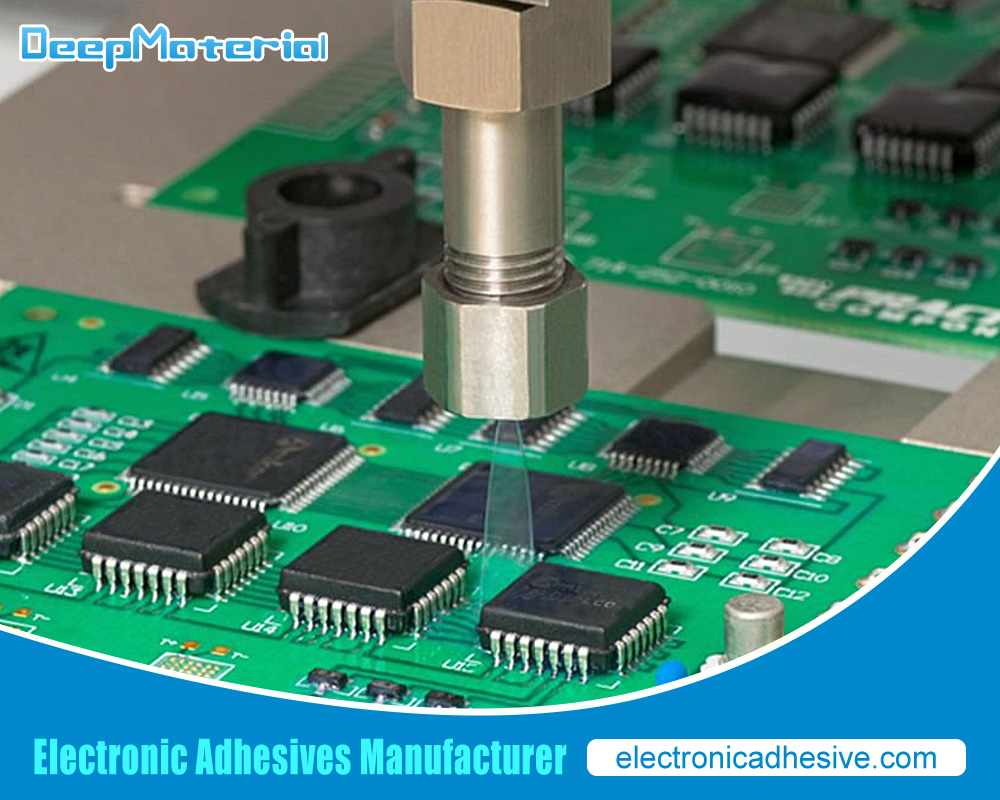
Assessing the Supplier’s Experience and Expertise in Industrial Adhesives
Choosing a supplier with experience and expertise in industrial adhesives is crucial to ensure that you are getting the right product for your specific application. An experienced supplier will have a deep understanding of the different types of adhesives available and their performance characteristics. They will be able to provide guidance and recommendations based on their knowledge and expertise.
When evaluating a supplier’s expertise, you can ask them about their experience in the industry, the types of industries they have served, and any specific projects or applications they have worked on. You can also ask for references or case studies to get a better understanding of their capabilities and track record.
Evaluating the Quality of the Supplier’s Industrial Epoxy Adhesive Products
The quality of the adhesive products is a critical factor to consider when evaluating a supplier. High-quality adhesives should meet industry standards and customer requirements, and they should be able to withstand the specific conditions and stresses of the application.
When evaluating the quality of the supplier’s adhesive products, you should consider factors such as the raw materials used, the manufacturing process, and the testing and certification processes. The supplier should be able to provide documentation and evidence of their quality control measures, such as test reports and certifications.
Examining the Supplier’s Manufacturing Processes and Quality Control Measures
The supplier’s manufacturing processes and quality control measures play a crucial role in ensuring the quality and reliability of their adhesive products. A reliable supplier should have well-documented manufacturing processes that are efficient and consistent. They should also have strict quality control measures in place to ensure that each batch of adhesive meets the required specifications.
When evaluating a supplier’s manufacturing processes, you can ask them about their production facilities, equipment, and quality control procedures. You can also inquire about their testing methods and frequency to ensure that they have robust processes in place.
Reviewing the Supplier’s Certifications and Industry Standards Compliance
Certifications and industry standards compliance are important indicators of a supplier’s commitment to quality and safety. A reliable supplier should have the necessary certifications and comply with industry standards to ensure that their adhesive products meet the required specifications.
There are certain standards one should look for when seeking an industrial epoxy adhesive supplier. ISO 9001 provides a quality management system, 14001 ensures environmental soundness and 45001 covers occupational health and safety. For a specific application’s needs, UL or MIL-SPEC certifications may be necessary too. So, if you want your resin project to go off without a hitch, pay attention to the qualifications!
Analyzing the Supplier’s Technical Support and Customer Service Capabilities
Technical support and customer service are crucial when working with an industrial epoxy adhesive supplier. A reliable supplier should have a dedicated technical support team that can provide assistance and guidance in selecting the right adhesive for your specific application. They should also have excellent customer service capabilities to address any concerns or issues that may arise.
When evaluating a supplier’s technical support and customer service capabilities, you can ask them about their response time, availability of technical experts, and their process for handling customer inquiries or complaints. It is also helpful to inquire about any additional services they offer, such as on-site support or training.
Evaluating the Supplier’s Delivery and Logistics Capabilities
Timely delivery is crucial in industrial applications, as any delays can disrupt production schedules. A reliable supplier should have reliable delivery and logistics capabilities to ensure that the adhesive products are delivered on time.
When evaluating a supplier’s delivery and logistics capabilities, you can ask them about their average lead times, their shipping methods, and their track record for on-time deliveries. It is also important to inquire about their packaging and handling procedures to ensure that the adhesive products are protected during transit.
Assessing the Supplier’s Pricing and Payment Terms
While price should not be the sole determining factor when choosing a supplier, it is important to consider the supplier’s pricing and payment terms to ensure that they are fair and reasonable. It is also important to consider the overall value that the supplier provides, including the quality of their products, their technical support capabilities, and their delivery reliability.
When evaluating a supplier’s pricing and payment terms, you can compare their prices with other suppliers in the market to ensure that they are competitive. You can also inquire about any discounts or volume pricing options that may be available. Additionally, it is important to review the supplier’s payment terms to ensure that they are flexible and align with your company’s financial requirements.
Building a Long-Term Relationship with a Reliable Industrial Epoxy Adhesive Supplier
Building a long-term relationship with a reliable industrial epoxy adhesive supplier is beneficial for both parties. A strong supplier relationship can lead to better communication, improved product quality, and enhanced customer service. It also allows for better collaboration and problem-solving, as the supplier becomes more familiar with your specific needs and requirements.
To build a long-term relationship with a supplier, it is important to communicate openly and regularly. Provide feedback on the adhesive products and the supplier’s performance, and address any concerns or issues promptly. It is also helpful to establish clear expectations and requirements from the beginning to ensure that both parties are aligned.
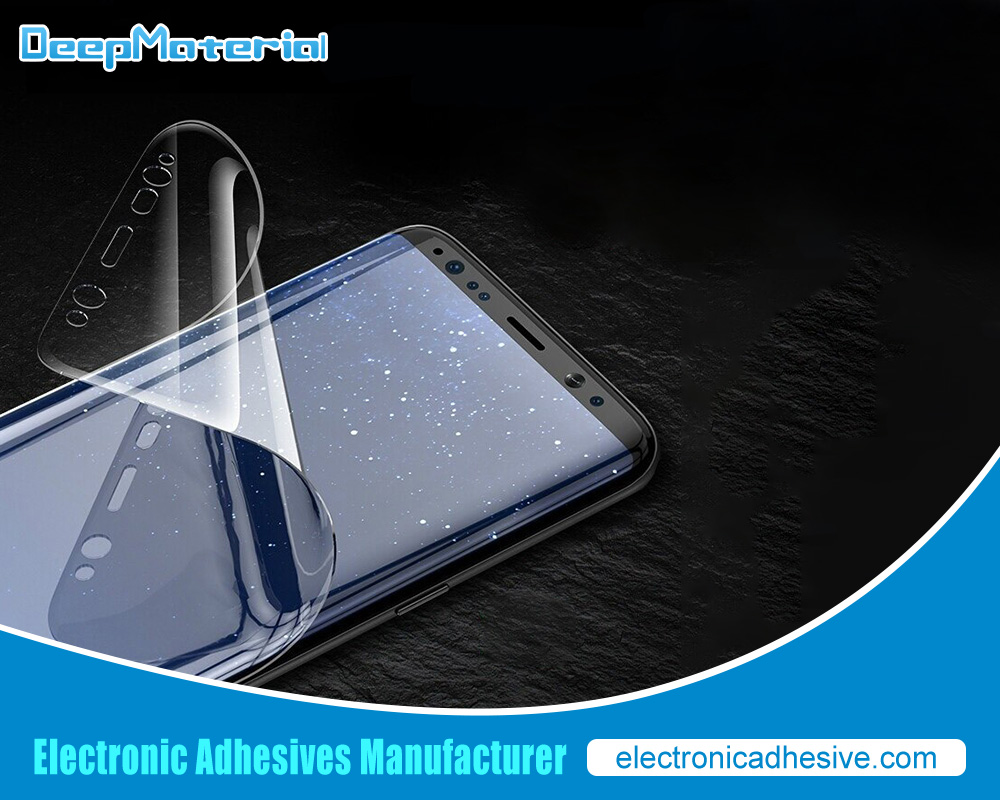
Final thoughts
In conclusion, the quality and reliability of industrial epoxy adhesive are crucial for the performance and safety of the final product. Choosing the right supplier is essential to ensure that you are getting a high-quality product that meets your specific requirements. When evaluating suppliers, it is important to consider factors such as their experience and expertise, the quality of their products, their manufacturing processes and quality control measures, their certifications and industry standards compliance, their technical support and customer service capabilities, their delivery and logistics capabilities, and their pricing and payment terms.
For more about choosing the Industrial Epoxy Adhesive Suppliers for Quality and Reliability, you can pay a visit to DeepMaterial at https://www.electronicadhesive.com/about/ for more info.