PCB Potting Compound
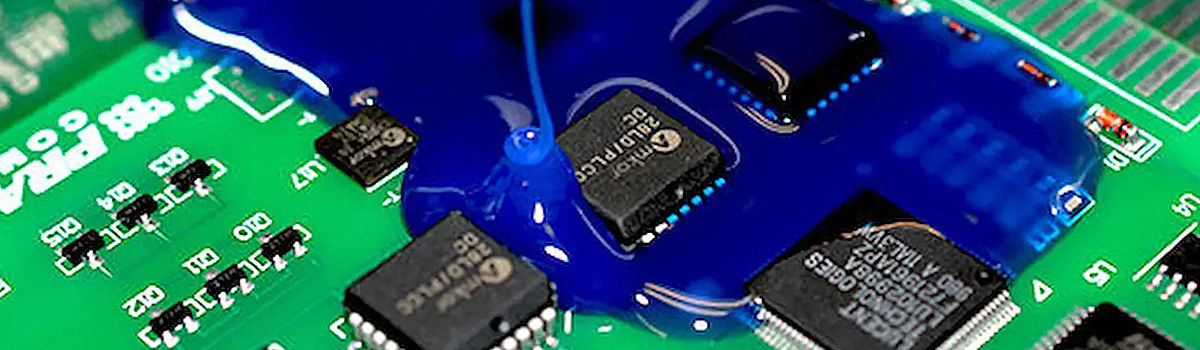
PCB potting compound, also known as an encapsulant, is a material used to protect and insulate electronic components on printed circuit boards (PCBs). The potting compound is applied to the elements and PCB and then cured to form a hard, protective shell. This process protects the electronics from environmental factors such as moisture, dust, and vibration and can enhance thermal performance. In this article, we will explore the benefits of using PCB potting compounds and how they can improve the longevity and reliability of electronic systems.
What is PCB Potting Compound?
PCB potting compound is a protective resin encapsulating electronic components on a printed circuit board (PCB). It forms a solid barrier, shielding the PCB from environmental factors like moisture, dust, and temperature fluctuations. The potting compound improves the mechanical strength of the PCB, provides electrical insulation, and enhances its overall reliability. It is commonly used in electronics manufacturing, automotive, aerospace, and telecommunications to ensure the longevity and performance of electronic devices and systems.
How Does PCB Potting Compound Work?
PCB potting compound is a specialized material that encapsulates and protects electronic components on a printed circuit board (PCB). Here’s how PCB potting compound works:
- Encapsulation: PCB potting compound is applied to the PCB by pouring or dispensing it onto the components. It flows around the elements and fills up voids, creating a solid, protective enclosure.
- Environmental Protection: Once cured, the potting compound forms a robust barrier that shields the components from environmental factors such as moisture, dust, and chemicals. It prevents these elements from reaching the sensitive electronics, safeguarding them against corrosion, short circuits, and other potential damage.
- Insulation: PCB potting compound provides excellent electrical insulation properties. It isolates the components from each other, preventing electrical short circuits and maintaining the integrity of the circuitry. This insulation is crucial in applications with closely spaced features or high voltage differentials.
- Mechanical Stability: The potting compound improves the mechanical stability of the PCB assembly. It enhances the structural integrity, dampens vibrations, and reduces the risk of component displacement or damage due to mechanical stress. It is especially crucial to consider this factor in situations where the printed circuit board may experience rough conditions, vibrations, or impacts.
- Thermal Management: PCB potting compound can also provide effective thermal management. It helps dissipate heat generated by the components, preventing overheating and prolonging their lifespan. Some potting mixes have high thermal conductivity, efficiently transferring heat from the elements.
- Dielectric Properties:PCB potting compounds are formulated with dielectric properties, enabling them to withstand high voltages without conducting electricity. This characteristic is vital in critical electrical insulation applications, such as high-voltage power supplies or electrical equipment.
- Compatibility and Adhesion: PCB potting compounds adhere well to various substrates used in PCB manufacturing, such as epoxy, FR-4, or metal. They form a strong bond with the components and the PCB, providing reliable protection and ensuring long-term performance.
Advantages of Using PCB Potting Compound
Using PCB potting compounds offers several advantages in electronic device manufacturing and protection. Here are some key benefits:
- Environmental Protection:PCB potting compound forms a protective barrier that shields electronic components from moisture, dust, chemicals, and other environmental factors. It helps prevent corrosion, short circuits, and damage caused by exposure to harsh conditions.
- Electrical Insulation: Potting compounds provide excellent electrical insulation, isolating components and preventing electrical shorts. Insulation is crucial in applications with closely spaced elements or high voltages.
- Mechanical Stability: Potting compound enhances the mechanical stability of the PCB assembly. It improves structural integrity, reduces vibrations, and protects against mechanical stress, ensuring reliable performance even in rugged environments.
- Vibration and Shock Resistance: Potting compound helps dampen vibrations and absorb shocks, protecting components from damage due to mechanical stress. Constant movements in applications such as the automotive or aerospace industries make it particularly important to have this insulation in place.
- Heat Dissipation: Some potting compounds have high thermal conductivity, enabling efficient heat dissipation. They help dissipate heat generated by components, preventing overheating and prolonging their lifespan.
- Chemical Resistance:PCB potting compounds resist various chemicals, protecting components from exposure to corrosive substances or solvents. This resistance ensures the long-term reliability of the PCB assembly.
- Customization and Design Flexibility: Formulating potting compounds enables meeting specific requirements, providing customization and design flexibility. Tailoring potting compounds allows for providing desired properties such as hardness, flexibility, flame resistance, or precise environmental tolerances.
- Protection from Physical Damage: Potting compound creates a protective layer around components, safeguarding them from physical damage caused by impacts or rough handling during transportation or installation.
- Easy Application:PCB potting compounds are typically easy to apply. Pouring, injecting, or dispensing potting compounds onto the PCB assembly allows them to conform to the shape of the components and effectively fill voids.
- Long-Term Reliability: By providing robust protection and insulation, potting compounds contribute to the long-term reliability of electronic devices and systems. They help extend the lifespan of components, reducing maintenance and replacement costs.
Protection from Environmental Factors
Protection from environmental factors is crucial in electronic device manufacturing, and PCB potting compound provides adequate safeguards against various elements. Here are some key points highlighting the protection offered by PCB potting compound:
- Moisture Barrier: PCB potting compound creates a moisture-resistant barrier that prevents water or humidity from reaching sensitive electronic components. This protection is vital in applications exposed to moisture-rich environments, such as outdoor electronics or industrial settings.
- Dust and Particle Protection: Potting compounds seal the components and PCB, preventing the ingress of dust, dirt, and other particles. This barrier helps maintain optimal performance by reducing the risk of contamination or clogging of sensitive electronic circuits.
- Chemical Resistance:Manufacturers often formulate potting compounds with excellent chemical resistance properties. They can withstand exposure to various chemicals, including solvents, acids, oils, and cleaning agents. This protection is essential in environments where chemical exposure is prevalent, such as industrial or laboratory settings.
- Corrosion Prevention: PCB potting compounds provide a protective layer that shields components from corrosive substances. They minimize the risk of corrosion, which can degrade performance and lead to component failure over time.
- UV Resistance: Manufacturers design specific potting compounds to offer resistance against ultraviolet (UV) radiation. This protection is crucial for outdoor applications or devices exposed to direct sunlight, as UV radiation can cause discoloration, degradation, or premature aging of materials.
- Thermal Stability: Potting compounds can provide thermal stability by resisting temperature fluctuations. They help protect components from excessive heat or cold, ensuring their reliable operation in extreme temperature variations.
- Mechanical Protection:Potting compounds enhance the automatic protection of electronic components by providing a durable and resilient encapsulation. This protection shields components from physical impacts, vibrations, or mechanical stresses, reducing the risk of damage or failure.
- Electric Insulation: PCB potting compounds offer excellent electrical insulation properties. They prevent electrical shorts and leakage by providing a non-conductive barrier between components or conductive traces on the PCB.
- EMI/RFI Shielding: Some potting compounds can incorporate materials that offer electromagnetic interference (EMI) or radio frequency interference (RFI) shielding. This feature helps prevent unwanted interference or disturbances caused by electromagnetic radiation or signals.
- Environmental Compliance: Manufacturers design certain potting compounds to meet specific environmental standards or regulations, such as RoHS (Restriction of Hazardous Substances) or REACH (Registration, Evaluation, Authorization, and Restriction of Chemicals). These compounds ensure compliance with environmental guidelines and contribute to sustainable manufacturing practices.
PCB potting compound provides comprehensive protection from various environmental factors, including moisture, dust, chemicals, corrosion, UV radiation, temperature fluctuations, mechanical stress, electrical issues, and electromagnetic interference. This protection helps ensure electronic devices’ longevity, reliability, and performance in diverse applications and environments.
Enhanced Thermal Performance
Electronic device design and operation critically rely on enhanced thermal performance, which designers can achieve through various techniques and materials. Here are some key points highlighting the benefits and methods for attaining enhanced thermal performance:
- Efficient Heat Dissipation:Effective heat dissipation is crucial to prevent overheating and maintain optimal operating temperatures for electronic components. By utilizing advanced cooling solutions such as heat sinks, heat pipes, or thermal pads, thermal energy can be efficiently transferred away from the elements, reducing the risk of performance degradation or failure.
- Thermal Interface Materials: Thermal interface materials, such as thermal pastes, pads, or phase change materials, improve heat transfer between the component and the cooling system. These materials help fill air gaps or microscopic imperfections on the interface, reducing thermal resistance and enhancing thermal conductivity.
- Heat Spreading Techniques:Heat-spreading techniques involve using materials with high thermal conductivity, such as copper or aluminum, to distribute heat evenly across the device. Maintaining an even temperature distribution is essential to avoid overheating specific areas.
- Thermal Design Considerations:Effective thermal design involves carefully considering factors such as component placement, heat sink sizing and positioning, and overall airflow within the device. Optimizing these aspects minimizes hotspots and improves heat dissipation.
- Ventilation and Airflow Management: Adequate ventilation and airflow management are crucial to remove heat from the device and maintain a cooler operating environment. Maintaining a continuous flow of fresh air is essential to dissipate heat effectively. One way to achieve this is by utilizing fans, vents, or ducting.
- Thermal Simulation and Testing:Using thermal simulation software and testing methodologies enables engineers to analyze and optimize the thermal performance of electronic devices. Iterative improvements in design, component selection, and cooling solutions would allow engineers to achieve better thermal management.
- Advanced Cooling Technologies:Innovative cooling technologies, such as liquid or vapor chamber solutions, can significantly enhance thermal performance in high-power or space-constrained applications. These technologies provide superior heat dissipation capabilities and can effectively manage the thermal demands of advanced electronic systems.
- Material Selection: Choosing materials with high thermal conductivity, low thermal resistance, and excellent heat dissipation properties can enhance thermal performance. To ensure efficient thermal management, engineers should choose substrates, adhesives, and encapsulants specifically engineered for this purpose.
- Active Thermal Management:Active thermal management techniques, such as dynamic fan speed control or temperature-based power throttling, can help regulate temperatures based on real-time conditions. Enabling maximum heat dissipation ensures that components function within safe temperature limits.
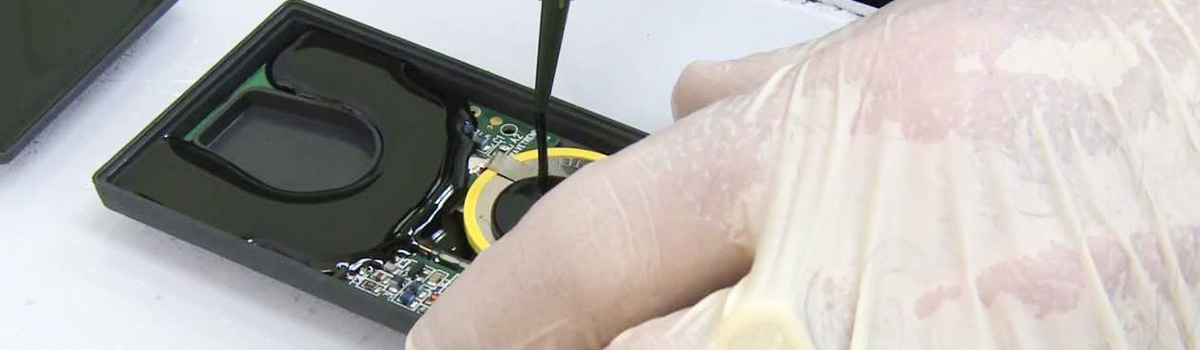
Improved Mechanical Strength
Improved mechanical strength is a critical factor in ensuring the durability and reliability of electronic devices. Here are some key points highlighting the benefits and methods for achieving improved mechanical strength:
- Reinforced Enclosures: One approach to enhancing mechanical strength is using reinforced enclosures, such as ruggedized or impact-resistant casings. Designers create these enclosures to withstand physical stress, vibrations, and potential impacts, protecting the internal components from damage.
- Structural Design Optimization:By employing advanced design techniques, such as finite element analysis (FEA) or computer-aided design (CAD), engineers can optimize the structural integrity of electronic devices. Pinpointing areas that need improvement alleviating stress concentrations, and fortifying critical points are essential to enhance mechanical strength.
- High-Quality Materials:The selection of high-quality materials is crucial for improving mechanical strength. Choosing materials with superior tensile strength, impact resistance, and dimensional stability can significantly enhance the robustness and reliability of electronic devices.
- Reinforcements and Bracing:In applications that require additional mechanical strength, designers can incorporate struts and bracing elements. These may include metal brackets, support beams, or ribs that provide additional structural integrity and resistance to bending or torsion.
- Adhesive Bonding:Utilizing robust adhesive bonding techniques can improve the mechanical strength of device assemblies. High-strength adhesives ensure secure bonding between components, preventing separation or loosening due to mechanical stress or vibrations.
- Reinforced Connectors and Mounting Points: Connectors and mounting points, such as screws or fasteners, can be strengthened to enhance mechanical strength. By using more substantial materials or incorporating additional support, these components can better withstand mechanical forces and maintain reliable connections.
- Impact Absorption and Shock Resistance: Incorporating materials or structures that absorb and dissipate impact energy can enhance mechanical strength. Designers can use protective measures such as shock-absorbing materials, cushioning elements, or coatings to safeguard components and prevent damage from sudden impacts or drops.
- Compliance with Industry Standards: Compliance with industry standards, such as those defined by organizations like the International Electrotechnical Commission (IEC) or the Institute of Electrical and Electronics Engineers (IEEE), ensures that electronic devices meet specified mechanical strength requirements. Adhering to these standards helps ensure consistent and reliable performance in various operating conditions.
- Robust Packaging and Handling: Proper packaging and handling techniques during manufacturing, transportation, and installation play a crucial role in maintaining mechanical strength. Protective packaging, anti-static measures, and safe handling procedures minimize the risk of physical damage and maintain the device’s integrity.
Reduction of Electrical Noise
Reducing electrical noise is critical to electronic device design and operation to ensure reliable performance and signal integrity. Here are some key points highlighting the benefits and methods for reducing electrical noise:
- Grounding and Shielding:Proper grounding techniques and shielding mechanisms help minimize electrical noise by providing a low-impedance path for unwanted electrical currents. Grounding shields and conductive enclosures help contain and redirect electromagnetic interference (EMI) and radio frequency interference (RFI), reducing their impact on sensitive components.
- Filtering and Decoupling:Filterings and decoupling components, such as capacitors, inductors, and ferrite beads, help suppress electrical noise by attenuating high-frequency components. These components are strategically placed near sensitive circuits or power supply lines to prevent noise from propagating further.
- Signal Isolation: Signal isolation techniques, such as optocouplers or transformers, break the electrical connection between circuits to minimize the transfer of electrical noise. Isolating sensitive signals from noise sources helps maintain signal integrity and reduces the risk of data corruption or interference.
- PCB Layout and Routing: Careful PCB layout and routing practices are crucial for reducing electrical noise. Proper separation of analog and digital circuits, minimizing trace lengths, and employing ground planes or signal isolation techniques can help mitigate the effects of noise coupling and electromagnetic radiation.
- Shielded Cables and Connectors: Shielded cables and connectors help minimize noise pickup or emission. Protecting cables with conductive materials, such as braided or foil shields, provides a barrier against external electromagnetic interference.
- Grounding Techniques:Implementing proper grounding techniques, such as star grounding or ground planes, ensures a common reference point for electrical signals and helps prevent ground loops that can introduce electrical noise.
- EMI/RFI Filters: Including EMI/RFI filters at the input or output stages of power supplies or signal lines can significantly reduce electrical noise. These filters attenuate high-frequency noise components and prevent their propagation into sensitive circuits.
- Component Selection:Choosing components with low noise characteristics, such as low-noise amplifiers or precision voltage references, can help reduce electrical noise at the source. Selecting components with high immunity to noise or interference also contributes to noise reduction.
- Electromagnetic Compatibility (EMC) Testing: Performing EMC testing during the design and manufacturing stages helps identify potential sources of electrical noise and evaluate the device’s compliance with electromagnetic compatibility standards. This testing ensures the device operates within acceptable noise limits and minimizes interference with other electronic equipment.
- Grounding and Bonding Practices:Proper grounding and bonding practices throughout the device’s installation and operation help reduce electrical noise. It is essential to create strong grounding connections, connect metal components to a shared ground, and use cable management methods to reduce interference.
Increased Lifespan of Electronics
Increasing the lifespan of electronics is a crucial consideration for both manufacturers and consumers. Here are some key points highlighting the benefits and methods for increasing the lifespan of electronics:
- Efficient Thermal Management: Proper thermal management techniques, such as adequate heat dissipation, can significantly extend the lifespan of electronic components. Maintaining optimal operating temperatures minimizes thermal stress on the elements, reducing the risk of degradation or failure.
- Robust Design and Construction: Designing electronics with powerful and durable components, such as high-quality connectors, resistors, capacitors, and integrated circuits, can enhance their longevity. When choosing parts, it’s essential to consider their longevity, reliability, and ability to handle the proper voltage and temperature levels.
- Good Power Supply and Voltage Regulation: Ensuring a stable and clean power supply is essential for increasing the lifespan of electronics. Proper voltage regulation, surge protection, and high-quality power supplies or voltage regulators help prevent overvoltage or voltage fluctuations that can damage sensitive components.
- Adequate ESD Protection:Implementing proper electrostatic discharge (ESD) protection measures safeguards electronics from damage caused by static electricity. Utilizing ESD-safe workstations, grounding straps, and ESD-shielded packaging ensures safety during manufacturing, handling, and installation.
- Regular Maintenance and Cleaning: Regular maintenance, including cleaning and inspection, can help identify and address potential issues before they escalate. Removing dust, debris, and contaminants from electronic devices and ensuring proper airflow and ventilation can prevent overheating and component failure.
- Adequate Protection from Environmental Factors: Protecting electronics from environmental factors, such as moisture, humidity, extreme temperatures, and corrosive substances, is crucial for longevity. Designers can achieve this by using proper enclosures, conformal coatings, or potting compounds that provide insulation and protection against harsh conditions.
- Proper Handling and Storage:Handling electronics with care, following reasonable installation procedures, and storing them in controlled environments when not in use can help prevent physical damage and extend their lifespan. We safeguard against physical shocks, static discharge, excessive heat, moisture, or dust exposure.
- Firmware and Software Updates:Keeping firmware and software up to date helps ensure optimal performance, compatibility, and security. Regular updates often include bug fixes, performance improvements, and enhanced compatibility, thereby prolonging the useful life of electronics.
- Environmental Considerations:Designing electronics with ecological considerations in mind, such as using energy-efficient components, reducing power consumption in standby modes, and implementing recycling or disposal programs, contributes to their overall lifespan. It also promotes sustainability and reduces electronic waste.
- Quality Control and Testing: Implementing rigorous quality control measures and thorough testing during manufacturing helps identify and rectify potential defects or issues. We can improve their lifespan by ensuring only high-quality and dependable electronics are available.
Types of Potting Compounds
Designers use potting compounds to encapsulate and protect electronic components, providing insulation, environmental resistance, and mechanical support. Various potting compounds are available, each offering specific properties and benefits. Here are some common types of potting compounds:
- Epoxy Resin: Epoxy resin is a popular choice for potting applications due to its excellent electrical insulation properties, high strength, and resistance to chemicals and temperature variations. It provides good adhesion to many substrates and reliable protection against moisture and environmental contaminants.
- Polyurethane: Polyurethane potting compounds offer flexibility, impact resistance, and excellent vibration resistance. They provide adequate protection against moisture, chemicals, and UV radiation. Polyurethane compounds frequently use applications requiring shock absorption or thermal cycling.
- Silicone: Silicone potting compounds have outstanding thermal stability, high-temperature resistance, and excellent flexibility over a wide temperature range. They offer good electrical insulation and are highly resistant to moisture, chemicals, and UV exposure. Designers commonly use silicone compounds in applications that require extreme temperature resistance or exposure to harsh environments.
- Acrylic:People value acrylic potting compounds for their fast curing time, low shrinkage, and good electrical insulation properties. They provide a cost-effective solution for many potting applications and offer resistance to moisture, chemicals, and thermal cycling. People often use acrylic compounds when they desire a balance between cost, performance, and ease of use.
- Polyamide: Polyamide potting compounds, known as nylon-based compounds, offer excellent resistance to high temperatures, chemicals, and mechanical stress. They provide good adhesion to various substrates and offer reliable protection in demanding environments. Manufacturers commonly use polyamide compounds in automotive, aerospace, and industrial applications.
- UV Cure:UV cure potting compounds possess a unique feature: they cure using ultraviolet light. They offer fast curing times, allowing for high productivity in manufacturing processes. UV cure compounds provide excellent adhesion, electrical insulation, and resistance to moisture and chemicals. They often find use in applications that require rapid curing and precise control over the curing process.
- Thermal Interface Materials (TIM): Thermal interface materials, such as thermal greases, thermal pads, or phase change materials, are used for potting applications where the efficient transfer of heat is crucial. These materials help improve thermal conductivity and ensure effective heat dissipation, preventing overheating of electronic components.
It’s essential to consider the application’s specific requirements when selecting a potting compound. To choose the most suitable potting compound for optimal performance and protection of electronic components, one should consider factors such as temperature range, chemical exposure, mechanical stress, electrical insulation, and curing time.
Epoxy Potting Compound
Various industries widely use epoxy potting compounds due to their exceptional properties and versatile applications. Here are some key points highlighting the characteristics and advantages of epoxy potting compounds:
- Superior Adhesion: Epoxy potting compounds exhibit excellent adhesion to various substrates, including metals, ceramics, plastics, and printed circuit boards (PCBs). This strong bond provides mechanical stability and prevents moisture ingress, enhancing the overall reliability of electronic devices.
- Electrical Insulation:Epoxy potting compounds offer excellent electrical insulation properties, effectively isolating and protecting sensitive electronic components from electrical currents and potential short circuits. This insulation helps prevent malfunctions, performance degradation, and damage caused by electrical leakage.
- High-Temperature Resistance:Epoxy potting compounds can withstand high operating temperatures, making them suitable for applications in harsh environments or with heat-generating components. They maintain their structural integrity and performance even under elevated temperatures, ensuring the long-term reliability of the potted electronics.
- Chemical and Environmental Resistance: Epoxy potting compounds resist various chemicals, including solvents, fuels, oils, and acids. This resistance helps protect electronic components from chemical corrosion or degradation, extending their lifespan in demanding environments.
- Mechanical Strength:Epoxy potting compounds provide excellent mechanical strength and structural integrity, making them suitable for applications that require vibration resistance and shock absorption. They help protect delicate components from mechanical stress, impacts, and vibrations, ensuring reliable performance even in rugged conditions.
- Low Shrinkage: Epoxy potting compounds typically have low shrinkage during the curing process. This characteristic provides minimal stress on the potted components and reduces the risk of cracking or delamination, enhancing the overall stability and durability of the encapsulated electronics.
- Versatile Application:Epoxy potting compounds find application in various industries, including electronics, automotive, aerospace, and telecommunications. They find use in encapsulating and protecting multiple devices, such as power supplies, sensors, motors, LED modules, and electronic control units (ECUs).
- Easy Processing: Epoxy potting compounds are typically easy to handle and process. They offer the convenience of being easily mixed, poured, or dispensed into molds or onto components, enabling efficient production and assembly processes. Their manageable viscosity and cure time enable precise application and facilitate high-volume manufacturing.
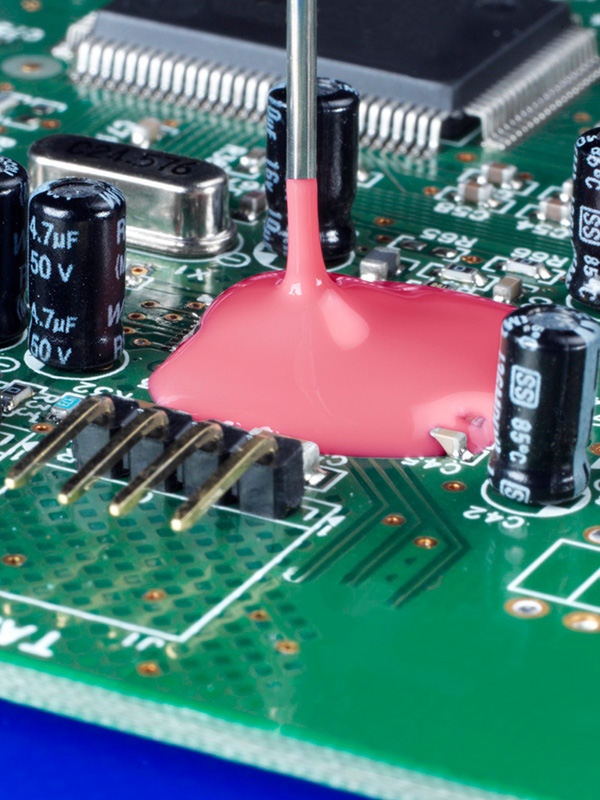
Silicone Potting Compound
Silicone potting compounds are highly versatile materials for extensive use in various industries. Here are some key points highlighting the characteristics and advantages of silicone potting compounds:
- Flexibility and Low-Temperature Performance: Silicone potting compounds offer exceptional flexibility and elasticity, making them suitable for applications that require dynamic movements or vibration resistance. They can maintain their properties even at low temperatures, ensuring reliable performance in cold environments.
- Excellent Moisture Resistance: Silicone potting compounds exhibit excellent moisture and water ingress resistance. They create a reliable barrier against moisture, protecting sensitive electronic components from corrosion and damage caused by exposure to humidity or damp environments.
- UV and Weather Resistance: Silicone potting compounds have inherent UV and weather resistance, allowing them to withstand prolonged exposure to sunlight and outdoor elements. Silicone potting is perfect for outdoor use as it protects against UV radiation and environmental factors. Additionally, it boasts good dielectric properties. Compounds possess good dielectric properties, making them effective insulators for electrical components. They can prevent electrical leakage and provide reliable insulation, reducing the risk of short circuits and electrical failures.
- Thermal Stability: Silicone potting compounds exhibit excellent thermal stability and can withstand various temperatures. They remain flexible and maintain their properties over a broad temperature range, ensuring consistent performance in hot and cold environments.
- Chemical Resistance: Silicone potting compounds resist various chemicals, including oils, solvents, and many common industrial chemicals. This resistance protects electronic components from chemical corrosion and degradation, enhancing their lifespan and reliability in challenging environments.
- Easy Processing and Cure:Silicone potting compounds are typically easy to handle and process. They have a manageable viscosity, allowing for precise application and easy filling of complex shapes or voids. They also offer a relatively fast cure time, enabling efficient production and assembly processes.
- Compatibility with Sensitive Components:Silicone potting compounds are known for their compatibility with a wide range of sensitive components, such as sensors, connectors, and delicate electronic circuits. Their gentle and non-abrasive nature protects the potted components without compromising their functionality.
- Wide Range of Applications:Various industries, including electronics, automotive, aerospace, medical devices, and renewable energy, widely use silicone potting compounds. They find employment in encapsulating and protecting electronic modules, LED lighting, sensors, power supplies, and other critical components.
These properties make them a preferred choice for potting and encapsulation, ensuring reliable protection and long-term performance of electronic devices in diverse industries.
Polyurethane Potting Compound
Various industries widely utilize polyurethane potting compounds for their unique properties and versatile applications. Here are some key points highlighting the characteristics and advantages of polyurethane potting compounds:
- Excellent Mechanical Strength: Polyurethane potting compounds provide exceptional mechanical strength, making them suitable for applications that require robust protection against mechanical stress, vibrations, and impacts. They offer excellent resistance to deformation, ensuring the long-term stability and durability of encapsulated components.
- Vibration Damping and Shock Absorption:Polyurethane potting compounds exhibit excellent vibration-damping properties, allowing them to absorb and dissipate vibrations. In demanding environments, vibrations can negatively impact sensitive electronic components. Having protection measures in place is vital to ensure reliable performance.
- Chemical and Environmental Resistance:Polyurethane potting compounds resist various chemicals, including oils, solvents, and common industrial substances. They also provide resistance against moisture, humidity, and other environmental factors, safeguarding electronic components from corrosion and degradation.
- Thermal Stability:Polyurethane potting compounds demonstrate excellent thermal stability, enabling them to withstand high operating temperatures without compromising their properties or integrity. This characteristic makes them suitable for applications involving heat-generating components or exposure to elevated temperatures.
- Electrical Insulation: Polyurethane potting compounds exhibit good electrical insulation properties, effectively isolating and protecting electronic components from electrical currents, potential short circuits, and electrical interference. They contribute to the reliable performance and longevity of encapsulated devices.
- Adhesion to Various Substrates:Polyurethane potting compounds adhere well to various substrates, including metals, plastics, ceramics, and PCBs. This strong bond enhances the overall mechanical stability of encapsulated components, preventing moisture ingress and promoting reliable operation.
- Low Shrinkage:Polyurethane potting compounds generally have low shrinkage during the curing process. This characteristic minimizes stress on the encapsulated components, reducing the risk of cracking, delamination, or damage caused by internal stresses.
- Versatile Application: Polyurethane potting compounds find application in diverse industries, such as electronics, automotive, aerospace, and renewable energy. They use it to encapsulate and protect various devices, including sensors, connectors, power electronics, and control modules.
- Ease of Processing:Polyurethane potting compounds are typically easy to handle and process. They offer the convenience of being easily mixed, poured, or dispensed into molds or onto components, enabling efficient production and assembly processes. Their manageable viscosity and cure time enable precise application and facilitate high-volume manufacturing.
Factors to Consider When Choosing a Potting Compound
One should consider several factors when choosing a potting compound for a specific application. Here are some key points to consider when choosing a potting mix:
- Application Requirements: Assess the specific requirements of the application, including temperature range, chemical exposure, moisture resistance, UV resistance, mechanical stress, and electrical insulation properties. Determine the level of protection needed for the components to ensure the potting compound can meet the desired performance standards.
- Compatibility:Ensure the potting compound is compatible with encapsulated materials, such as PCBs, connectors, sensors, or other electronic components. Consider factors like adhesion, coefficient of thermal expansion (CTE), and potential interactions between the potting compound and the encapsulated materials.
- Curing Time and Process:Evaluate the curing time and process of the potting compound. Consider factors such as pot life, cure temperature, and cure time. Determine whether the curing process aligns with the manufacturing or assembly process and if it allows for efficient production and adequate handling time.
- Mechanical Strength:Consider the mechanical strength requirements of the application. Assess the potential for vibration, impact, or mechanical stress and choose a potting compound that can provide the necessary strength and durability to withstand such conditions.
- Thermal Conductivity:Evaluate the thermal conductivity requirements of the application. Choose a potting compound that can effectively transfer heat away from heat-generating components depending on the heat dissipation needs, ensuring optimal thermal management.
- Electrical Properties: Consider the electrical insulation properties of the potting compound. Ensure it offers the required dielectric strength and resistance to prevent electrical leakage or short circuits. If electromagnetic interference (EMI) is a concern, consider potting compounds with enhanced EMI shielding properties.
- Environmental Considerations: Assess the ecological conditions to which the potting compound will be exposed. Evaluate factors such as moisture, humidity, UV radiation, and chemical exposure. Choose a potting compound that can protect and withstand specific environmental challenges.
- Process Compatibility: Consider the compatibility of the potting compound with the manufacturing or assembly process. Assess viscosity, pot life, mixing requirements, dispensing methods, and curing conditions. Ensure that the potting compound can integrate easily into the existing production processes.
- Regulatory Compliance: Ensure the chosen potting compound complies with relevant industry standards and regulations, such as RoHS (Restriction of Hazardous Substances) or REACH (Registration, Evaluation, Authorization, and Restriction of Chemicals). By doing this, we guarantee that the end product is both safe and compliant.
Considering these factors, one can make an informed decision when selecting a potting compound that best meets the application’s requirements, ensuring optimal protection and performance of the encapsulated electronic components.
Compatibility with Electronics
Compatibility with electronics is a crucial factor to consider when choosing a potting compound for encapsulating electronic components. Here are some key points to consider regarding the compatibility of potting compounds with electronics:
- Chemical Compatibility:Ensure that the potting compound is chemically compatible with the materials used in the electronic components, such as PCBs, connectors, and sensitive electronic circuits. Compatibility ensures that the potting compound will not react with or degrade the ingredients, leading to malfunction or damage.
- Adhesion: Consider the potting compound’s adhesion properties to the electronic components’ surfaces. It should adhere well to the encapsulated materials, providing a strong bond and preventing any gaps or voids that could compromise the protection offered by the potting compound.
- Dielectric Properties: Evaluate the dielectric properties of the potting compound. It should possess good electrical insulation properties to ensure the encapsulated components are effectively isolated from each other and external electrical currents. Doing this avoids the possibility of short circuits or electrical interference.
- Thermal Conductivity: Consider the thermal conductivity requirements of the electronics. Depending on the application, the potting compound should have the appropriate thermal conductivity to dissipate heat generated by the components. Maintaining optimal operating temperatures is crucial to prevent overheating, which can cause performance issues or component failure.
- Thermal Expansion Coefficient: Consider the potting compound’s thermal expansion coefficient (CTE) and its compatibility with the electronic components. Similar CTE values between the potting compound and the encapsulated materials reduce the risk of stress-induced cracking or delamination due to thermal cycling.
- Moisture and Environmental Resistance:Evaluate the potting compound’s resistance to moisture, humidity, and other environmental factors. Electronics frequently face exposure to harsh environments, requiring the potting compound to provide reliable protection against moisture ingress. This protection helps prevent corrosion and damage to the components.
- Compatibility with Manufacturing Processes:Consider the compatibility of the potting compound with the manufacturing or assembly processes. Assess viscosity, pot life, mixing requirements, and curing conditions. Ensure that the potting compound integrates easily into the existing production processes without causing delays or complications.
- Regulatory Compliance:Ensure that the potting compound complies with relevant industry regulations and standards, such as RoHS (Restriction of Hazardous Substances) or REACH (Registration, Evaluation, Authorization, and Restriction of Chemicals). Compliance ensures that the potting compound contains no harmful substances that could harm human health or the environment.
Curing Time
Curing time is an essential factor to consider when choosing a potting compound for encapsulating electronic components. Here are some key points to consider regarding curing time:
- Pot Life: Pot life refers to the duration during which the potting compound remains workable after mixing the components. It is essential to understand the pot life of the compound to ensure sufficient time for proper application and positioning of the components before the material begins to cure.
- Cure Time:Cure time is required for the potting compound to harden and achieve its desired properties fully. Selecting a potting compound with a cure time that aligns with the production schedule or assembly process is crucial. Long cure times may cause production delays, while short cure times may require rapid processing.
- Ambient Conditions: Consider the effect of ambient conditions, such as temperature and humidity, on the curing time of the potting compound. Some compounds may require specific temperature or humidity conditions for optimal curing. Ensure that the ambient conditions during the curing process can be easily controlled and maintained.
- Acceleration Techniques:Some potting compounds offer accelerated curing options through heat, UV light, or chemical additives. This method leads to quicker curing times, making it advantageous for high-volume production settings or when a fast turnaround is necessary.
- Post-Cure Considerations:Understand whether the potting compound requires any post-cure steps, such as additional heat treatment or UV exposure, to attain its complete properties. When assessing the practicality of the potting compound, it is essential to consider how post-cure measures may impact the overall production timeline.
- Handling and Workability Time:Consider the handling and workability time of the potting compound, which refers to the duration during which the material remains in a state suitable for mixing, pouring, or dispensing; choosing potting compound that provides adequate handling time for an efficient application while ensuring consistent quality.
- Is importantCure Shrinkage: Evaluate the potential shrinkage of the potting compound during the curing process. Excessive shrinkage can cause stress on the encapsulated components and may lead to cracking or delamination. Choosing a potting compound with minimal shrinkage helps maintain the integrity and reliability of the encapsulated electronics.
- Optimization and Testing:It is advisable to conduct thorough testing and optimization of the curing process for the selected potting compound. One must consider component size, complexity, desired mechanical strength, and thermal performance to ensure the appropriate curing time for a specific application.
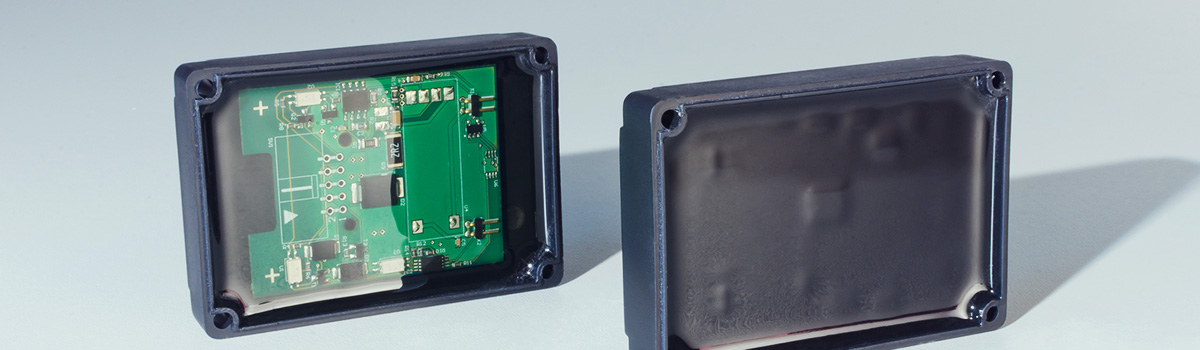
Temperature Resistance
When selecting a potting compound for electronic components, it is crucial to consider temperature resistance, especially in applications where the materials will be exposed to extreme temperatures. Here are some key points to consider regarding temperature resistance:
- Operating Temperature Range: Evaluate the expected operating temperature range of the electronic components and choose a potting compound that can withstand those temperatures without degradation or loss of performance. Consider the high and low-temperature extremes the elements may encounter during operation.
- Thermal Cycling: Assess the ability of the potting compound to withstand thermal cycling, which involves repeated temperature fluctuations. Components that undergo temperature changes may expand and contract, potentially leading to stress on the encapsulating material. Choose a potting compound with a suitable coefficient of thermal expansion (CTE) to minimize stress and prevent cracking or delamination.
- High-Temperature Resistance:Select a potting compound with excellent heat resistance if the application involves high-temperature environments. Look for a compound that can maintain its mechanical strength, electrical insulation properties, and other performance characteristics at elevated temperatures.
- Low-Temperature Resistance:Choose a potting compound with good low-temperature resistance for applications that require operation in icy conditions. It should remain flexible and retain its functionality even at sub-zero temperatures, ensuring the integrity of the encapsulated components.
- Thermal Conductivity:Consider the thermal conductivity of the potting compound, especially in applications where heat dissipation is critical. A potting compound with good thermal conductivity can effectively transfer heat away from the encapsulated components, helping to maintain optimal operating temperatures and prevent overheating.
- Insulation Properties: Ensure that the potting compound maintains its electrical insulation properties across the temperature range of the application. It should effectively insulate the electronic components and prevent the risk of electrical leakage or short circuits, even under extreme temperature conditions.
- Compatibility with Thermal Management Solutions:If you use thermal management solutions such as heat sinks or thermal pads with the potting compound, check the compatibility between the potting compound and these components. By ensuring efficient heat transfer, we can achieve maximum thermal efficiency.
- Testing and Validation: Conduct thorough testing and validation of the potting compound’s temperature resistance. To ensure the reliability and performance of the material, you may need to subject it to temperature cycling, thermal shock, or prolonged exposure to extreme temperatures.
Cost Considerations
Cost considerations are significant when selecting a potting compound for electronic components, directly impacting the overall project budget. Here are some key points to consider regarding cost considerations:
- Material Cost: Evaluate the cost of the potting compound itself. Different types of potting compounds, such as epoxy, silicone, or polyurethane, vary in price. Consider the material needed for the project and compare the cost per unit of volume for each type.
- Application Efficiency:Assess the potting compound’s ease of application and workability. Some compounds may require specialized equipment or skilled labor for proper application, increasing overall labor costs. Choose a potting compound that you can easily apply using existing manufacturing processes or with minimal additional investment in equipment.
- Waste and Cleanup: Consider the amount of waste generated during the potting process and the ease of cleanup. Some potting compounds may have specific disposal requirements, which can add to the overall project cost. Opt for materials that generate minimal waste and have straightforward cleanup procedures.
- Production Time: Analyze the potting compound’s curing time and pot life. Longer curing times can increase production, leading to additional labor costs and potential delays. Select a potting compound with a cure time that aligns with the production schedule to optimize efficiency and reduce costs.
- Performance Requirements: Balance the potting compound’s cost with the electronic components’ desired performance requirements. Cheaper options may offer different protection or performance than more expensive ones. Assess the criticality of the application and select a potting compound that meets the necessary performance standards without unnecessary over-specification.
- Reliability and Longevity: Consider the long-term cost implications of the potting compound. Investing in a higher-quality, more expensive potting compound may increase the encapsulated electronics’ reliability and longevity. Reducing failures, repairs, and replacements throughout the project’s lifespan can save costs.
- Supplier Support and Warranty:Evaluate the support provided by the potting compound supplier and any associated warranty or guarantees. A reputable supplier with excellent customer service can offer technical assistance, troubleshooting, and warranty coverage, contributing to cost savings in case of any issues or concerns.
- Regulatory Compliance: Consider the cost implications of regulatory compliance. Ensure that the chosen potting compound complies with relevant industry regulations and standards. Non-compliance can lead to penalties or project setbacks, which may incur additional costs.
By carefully considering cost considerations and related factors, one can select a potting compound that balances affordability and meets the necessary performance and reliability requirements for the encapsulated electronic components.
Application Techniques
Application techniques for potting compounds involve encapsulating electronic components with the chosen material. Here are some key points to consider regarding application techniques:
- Dispensing: Dispensing is a common application technique where the potting compound is dispensed directly onto the electronic components. You can do it manually using syringes or automate it using dispensing equipment. Dispensing allows for precise application and control over the amount of material used.
- Vacuum Potting: Vacuum potting involves placing the electronic components in a vacuum chamber and then introducing the potting compound. The vacuum helps remove air bubbles and ensures proper penetration and coverage of the compound around the elements. This technique helps achieve void-free encapsulation.
- Injection Molding: Injection molding is a more automated and high-volume application technique. The potting compound is heated and injected into a mold cavity containing the electronic components. After curing, open the mold and remove the encapsulated parts. Injection molding offers efficient and consistent encapsulation, making it suitable for large-scale production.
- Potting Bags:Potting bags are pre-formed bags made of plastic or silicone-filled with the potting compound. Place the electronic components inside the bag and seal it before starting the curing process. This technique is proper when dealing with complex shapes or features that require a specific orientation during encapsulation.
- Conformal Coating:Conformal coating involves applying a thin layer of potting compound onto the surface of the electronic components. It protects against environmental factors without completely encapsulating the components. Conformal coating is suitable for applications where accessibility or reworkability of the ingredients is essential.
- Vacuum Encapsulation: Vacuum encapsulation involves combining vacuum potting with placing a protective film or bag around the electronic components. The vacuum removes air from the package, introducing the potting compound to fill the voids. Then, seal the film or bag to create a hermetically sealed container. This technique is helpful for applications that require high-level protection from moisture and other contaminants.
- Film Casting: Film casting involves pouring or spreading a liquid potting compound onto a flat surface and allowing it to cure into a thin film. The film is then cut and shaped to match the dimensions of the electronic components. This technique suits applications that desire a flexible and thin encapsulation layer.
- Robotic Application:Robotic application involves using mechanical systems to apply the potting compound onto the electronic components. Robotic arms or automated dispensing systems ensure precise and consistent application. This technique finds common use in high-volume production settings.
Common Applications of PCB Potting Compound
PCB potting compounds find extensive use in various applications where protection, insulation, and enhanced reliability of electronic components are essential. Here are some typical applications of PCB potting compounds:
- Automotive Electronics:Automotive electronics widely use PCB potting compounds, including control modules, sensors, ignition systems, and lighting. They protect against vibrations, moisture, and temperature fluctuations, ensuring the durability and performance of electronic components in harsh automotive environments.
- Consumer Electronics: Consumer electronics such as smartphones, tablets, laptops, and home appliances utilize potting compounds. They offer protection against mechanical stress, moisture, dust, and impact, extending the lifespan and reliability of electronic devices.
- Industrial Equipment:Industrial equipment such as power supplies, motor drives, control panels, and automation systems employ PCB potting compounds. They safeguard sensitive electronic components from environmental hazards, including chemical exposure, vibrations, extreme temperatures, and electrical interference.
- Renewable Energy Systems: Potting compounds are vital in renewable energy systems such as solar panels, wind turbines, and energy storage devices. They protect sensitive electronics from outdoor conditions, including UV radiation, moisture, and temperature variations, ensuring the long-term functionality and performance of renewable energy systems.
- LED Lighting:LED lighting applications widely use PCB potting compounds, including LED drivers, modules, and outdoor lighting fixtures. They offer protection against heat, moisture, and vibrations, enabling reliable operation and prolonged lifespan of LED lighting systems.
- Aerospace and Defense:Potting compounds find application in aerospace and defense electronics, including avionics, communication systems, radar equipment, and military vehicles. They protect against extreme temperatures, shock, vibration, and moisture ingress, ensuring the reliable operation of critical electronic components in demanding environments.
- Medical Devices: Medical devices such as diagnostic equipment, patient monitoring systems, and implantable devices use PCB potting compounds. They offer protection against moisture, chemicals, and sterilization processes, ensuring the integrity and longevity of sensitive electronic components in medical environments.
- Marine and Offshore Equipment:Potting compounds find use in marine and offshore applications, including navigation systems, underwater sensors, and communication equipment. They protect against water ingress, saltwater corrosion, and vibrations, ensuring reliable performance and longevity in challenging marine environments.
- Telecommunications:Telecommunications equipment, including base stations, network switches, and communication devices, utilize potting compounds. They offer protection against moisture, dust, and temperature variations, ensuring the uninterrupted operation of critical communication infrastructure.
- Electronic Modules and Assemblies:Various industries use PCB potting compounds to encapsulate electronic modules and assemblies. These include power electronics, control systems, PCB assemblies, and electronic subassemblies. Potting compounds protect environmental factors, enhancing the reliability and performance of encapsulated electronics.
The Importance of Using PCB Potting Compound
PCB potting compound is a crucial material for electronic components’ protection and long-term reliability. Potting or encapsulating an electronic device can safeguard it against the environment, thermal stress, physical shock, and chemical exposure. Here are some reasons why using PCB potting compound is essential:
- Environmental Protection:Potting compound creates a barrier that protects electronic components from moisture, dust, and other environmental factors that can lead to corrosion or short circuits.
- Improved Durability: Potting can add physical strength and impact resistance to electronic components, making them more durable and less prone to damage from vibration or shock.
- Increased Reliability: By eliminating air pockets, potting compounds can reduce the risk of thermal shock and improve the overall reliability of the electronics.
- Enhanced Thermal Management: Potting compounds can improve heat dissipation, which can help extend the life of components that generate a lot of heat.
- Reduced Noise: Potting can help reduce electrical noise, improving the electronics’ overall performance.
- Cost Savings:By protecting electronic components from damage, potting can help reduce repair and replacement costs. Additionally, using potting compounds can help reduce the likelihood of warranty claims and improve customer satisfaction.
Using PCB potting compounds can help ensure electronic components’ long-term reliability and performance, which is crucial in a wide range of industries and applications.
Conclusion
PCB potting compound is a crucial component for ensuring the longevity and reliability of electronic systems. It provides protection from environmental factors, enhances thermal performance, improves mechanical strength, and reduces electrical noise. The type of potting compound chosen will depend on several factors, including compatibility with electronics, curing time, temperature resistance, and cost. By selecting and applying the suitable potting compound correctly, electronic components can be protected from harsh conditions, ultimately increasing their lifespan and reliability.