Silicone Sealant
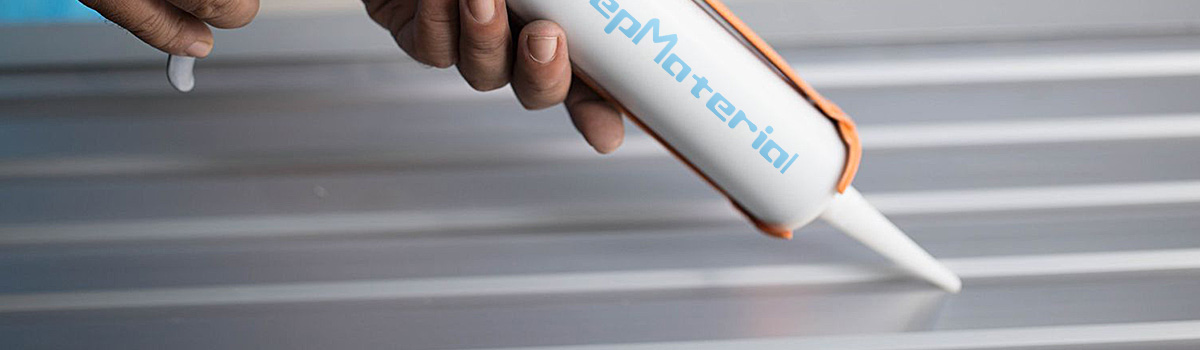
Silicone sealant is a highly versatile and durable adhesive material used for various applications, including construction, automotive, and household. Its unique properties make it a popular choice for sealing and bonding different materials, including metal, plastic, glass, and ceramics. This comprehensive guide will explore the various types of silicone sealants available, their uses, and their benefits.
What is Silicone Sealant?
Silicone sealant is a versatile adhesive and sealing compound widely used in construction, automotive, and other industries. It is a type of elastomer, a substance with rubber-like properties, composed of silicone polymers. When applied to various surfaces, silicone sealants are known for forming a flexible, durable, and watertight seal.
The main ingredient in silicone sealants is silicone, a synthetic compound of silicon, oxygen, carbon, and hydrogen atoms. This combination gives silicone sealant unique properties, such as excellent resistance to extreme temperatures, UV radiation, moisture, and chemicals. It remains flexible over a wide temperature range, from shallow to high heat, without becoming brittle or losing its sealing capabilities.
Silicone sealants are available in different formulations, including acetoxy and neutral cure. Acetoxy sealants release acetic acid during the curing process, which gives off a vinegar-like smell, while neutral cure sealants do not release any strong odors. Both types offer excellent adhesion to various materials, including glass, metal, ceramics, plastics, and many building materials.
One of the primary uses of silicone sealant is for sealing joints and gaps in buildings. It is commonly applied around windows, doors, and other openings to prevent water, air, and dust from infiltrating. The flexibility of silicone sealant allows it to accommodate the natural movements of buildings caused by factors like temperature changes and settling.
In addition to its sealing properties, silicone sealant is also used as an adhesive. It provides a strong bond between surfaces, making it useful for bonding materials like glass, metal, and plastic. This makes it valuable in various applications, including automotive assembly, electronics manufacturing, and DIY projects.
Silicone sealants come in various colors to match different surfaces or for aesthetic purposes. They can be applied using a caulking gun or squeeze tubes, depending on the project size. After application, silicone sealant cures by reacting with moisture in the air, forming a flexible and durable rubber-like seal.
History and Development of Silicone Sealant
Silicone sealant is a versatile and widely used adhesive product known for its excellent sealing properties. Its history and development span several decades, with significant advancements in technology and formulation. In this brief overview, we will explore the key milestones and advances in the history of silicone sealants.
The development of silicone sealants can be traced back to the early 20th century when scientists began exploring the properties of silicone polymers. Silicone is a synthetic material from silicon, oxygen, carbon, and hydrogen atoms. Its unique characteristics, such as heat resistance, flexibility, and excellent adhesion, make it an ideal choice for sealant applications.
In the 1940s, General Electric (GE) introduced the first commercially available silicone sealant called GE Silicones. This product revolutionized the industry by offering a durable and long-lasting sealant solution. Initially, it was primarily used for industrial applications, such as sealing electrical components and gaskets.
Silicone sealants gained popularity throughout the 1950s and 1960s and were further developed to meet specific needs. New formulations were created to enhance adhesion to various substrates, including glass, metal, and plastic. The improved adhesion properties allowed silicone sealants to be used in construction, automotive, and household applications.
In the 1970s, the development of one-component silicone sealants brought further convenience to users. One-component adhesives do not require mixing or curing agents and can be directly applied from the container. This innovation simplified the application process, making silicone sealants more accessible to more users.
The 1980s witnessed advancements in the formulation of silicone sealants, particularly in terms of their resistance to ultraviolet (UV) radiation and weathering. UV-resistant silicone sealants were developed to withstand prolonged exposure to sunlight without deteriorating or losing their sealing properties. This made them suitable for outdoor applications, such as sealing windows, doors, and roofs.
Recently, eco-friendly and low-VOC (volatile organic compound) silicone sealants have gained popularity due to increased environmental awareness. Manufacturers have focused on developing adhesives with reduced emissions and improved sustainability profiles, making them safer for users and the environment.
Today, silicone sealants continue to evolve with advancements in technology and formulation. They are available in various forms, such as paste, liquid, or aerosol, to accommodate different application methods. The versatility of silicone sealants has made them indispensable in numerous industries, including construction, automotive, electronics, and manufacturing.
Types of Silicone Sealant
Silicone sealants are versatile products used for sealing and bonding applications in various industries, including construction, automotive, electronics, and manufacturing. They provide excellent adhesion, flexibility, and resistance to temperature, moisture, and chemicals. Silicone sealants come in different types, each with specific properties and applications. Here are some common types of silicone sealants:
- General Purpose Silicone Sealant: This type of silicone sealant is widely used for available sealing and bonding applications. It offers good adhesion to various substrates like glass, metal, plastic, and ceramics. General-purpose silicone sealants are commonly used in household repairs, plumbing, and construction projects.
- High-Temperature Silicone Sealant: Designed to withstand extreme heat, high-temperature silicone sealants can resist temperatures ranging from 500°F (260°C) to over 1000°F (538°C). They are ideal for sealing joints and gaps in applications involving engines, ovens, exhaust systems, and industrial equipment.
- Low-Temperature Silicone Sealant: These sealants are formulated to remain flexible and effective at low temperatures, making them suitable for outdoor applications in cold climates. They resist freezing and maintain adhesion, making them helpful in sealing windows, doors, and other exterior components.
- Acetic Cure Silicone Sealant: Also known as acid-cure silicone sealants, these products release acetic acid as they cure. They offer excellent adhesion to glass and ceramics, making them popular for applications like aquariums, glass windows, and showers. However, they are not recommended for use on certain metal surfaces prone to corrosion.
- Neutral Cure Silicone Sealant: Neutral cure silicone sealants release alcohol or other non-acidic substances as they cure. They have low odor and are non-corrosive, making them suitable for various applications. Neutral cure sealants are often used for sealing sensitive substrates like stone, concrete, and certain metals.
- Structural Silicone Sealant: This type of silicone sealant is designed for structural glazing applications, providing bonding and weatherproofing properties. Structural adhesives offer high tensile strength, excellent adhesion, and long-term durability. They are commonly used in curtain wall systems, glass facades, and high-rise construction.
- Electrical Silicone Sealant: Electrical-grade silicone sealants are specially formulated for electrical and electronic applications. They provide excellent insulation properties and protect against moisture, dust, and chemicals. Electrical silicone sealants are used for sealing electrical boxes, connectors, and cables.
- Weatherproof Silicone Sealant: As the name suggests, weatherproof silicone sealants are designed to provide adequate protection against the elements. They resist UV radiation, temperature fluctuations, and moisture ingress. These sealants are commonly used for outdoor applications such as sealing windows, doors, and roofing materials.
- Aquarium Silicone Sealant: Aquarium sealants are non-toxic, 100% silicone sealants formulated specifically for sealing aquariums and fish tanks. They resist water, chemicals, and saltwater environments, ensuring a safe and secure seal without harming aquatic life.
- Sanitary Silicone Sealant: Sanitary sealants are designed for applications in areas exposed to water and moisture, such as kitchens, bathrooms, and sanitary fixtures. They offer excellent mold and mildew resistance, making them suitable for sealing joints in tiles, sinks, bathtubs, and shower enclosures.
These are just a few examples of silicone sealants available in the market. It’s essential to select the appropriate type of sealant based on the specific application requirements, substrate materials, and environmental conditions to achieve the desired sealing and bonding performance.
Uses of Silicone Sealant in Construction
Silicone sealants are crucial in the construction industry, offering various applications and benefits. Here are some common uses of silicone sealants in construction:
- Window and Door Installation: Silicone sealants are widely used for sealing gaps and joints around windows and doors. They provide excellent weatherproofing and prevent water, air, and noise infiltration. Silicone sealants ensure a tight seal, improving energy efficiency and reducing heating and cooling costs.
- Expansion Joints: Construction materials expand and contract due to temperature variations and structural movement. Silicone sealants create flexible expansion joints that accommodate these movements, preventing cracks and leaks. They are commonly applied in concrete slabs, bridges, highways, and other structures to maintain their integrity over time.
- Curtain Wall Systems: Curtain wall systems are used in high-rise buildings to provide a protective envelope while allowing natural light to enter. Silicone sealants bond and weatherproof these systems’ glass panels and aluminum frames. They provide excellent adhesion and durability, ensuring a long-lasting and secure seal.
- Roofing: Silicone sealants are utilized in various roofing applications. They are used to seal joints, flashings, and penetrations on flat, sloped, and metal roofs. Silicone sealants offer excellent resistance to UV radiation, temperature extremes, and moisture, making them ideal for long-term roof sealing and maintenance.
- Concrete and Masonry Sealing: Silicone sealants are used for sealing cracks, joints, and gaps in concrete and masonry structures. They prevent water infiltration, reinforce structural integrity, and protect against the damaging effects of moisture, freeze-thaw cycles, and chemical exposure. Silicone sealants are commonly used in foundations, driveways, sidewalks, and retaining walls.
- Bathroom and Kitchen Applications: Silicone sealants are essential for sealing joints and gaps in bathrooms and kitchens where moisture is present. They crowd around sinks, bathtubs, showers, tiles, and countertops, preventing water penetration and mold growth. Silicone sealants offer excellent resistance to water, humidity, and cleaning chemicals, ensuring a hygienic and durable seal.
- HVAC Systems: Silicone sealants are used in HVAC (Heating, Ventilation, and Air Conditioning) systems for sealing ducts, joints, and connections. They prevent air leakage, improving energy efficiency and maintaining proper air circulation. Silicone sealants can withstand temperature fluctuations and resist chemicals commonly found in HVAC systems.
- Firestopping: Silicone sealants are employed in fire-stopping applications to seal penetrations and prevent the spread of fire, smoke, and toxic gases. They provide fire resistance and maintain the integrity of fire-rated walls, floors, and ceilings. Silicone sealants used for fire stopping are specially formulated to meet stringent fire safety standards.
- Waterproofing: Silicone sealants are effective in waterproofing applications, such as sealing basements, foundations, and below-grade structures. They create a watertight barrier, preventing water infiltration and protecting the building from moisture-related issues like dampness, mold, and structural damage.
- Specialty Applications: Silicone sealants are also used in various specialty applications in construction, such as glazing, acoustic sealing, vibration damping, and automotive applications. They provide excellent adhesion, flexibility, and durability in these specialized areas.
Automotive Applications of Silicone Sealant
Silicone sealant is a versatile material widely used in various automotive applications. With its excellent adhesive and sealing properties and resistance to high temperatures and harsh environmental conditions, silicone sealant plays a crucial role in ensuring the integrity and longevity of automotive components. Here are some critical automotive applications of silicone sealant:
- Gasketing: Silicone sealants are commonly used for creating gaskets in engines, transmissions, and other automotive systems. They provide a reliable seal between mating surfaces, preventing fluids such as oil, coolant, and transmission fluid leaks. Silicone sealants resist high temperatures and maintain their elasticity over time, allowing them to withstand the stresses and vibrations experienced in engine compartments.
- Bonding and sealing: Silicone sealants are used for bonding and sealing various automotive components, including windshields, windows, and sunroofs. They provide a robust and flexible bond, ensuring a watertight and airtight seal. Silicone sealants also have excellent UV resistance, which helps to prevent the degradation and yellowing of bonded components exposed to sunlight.
- Electrical applications: Silicone sealants are utilized in automotive electrical systems to protect connections, wires, and terminals from moisture, dust, and vibrations. They provide electrical insulation, preventing short circuits and corrosion. Silicone sealants are also used to protect electronic components, such as sensors and control units, from environmental hazards.
- Underbody coating: Silicone sealants are employed for underbody coating to protect the vehicle’s chassis and undercarriage from corrosion caused by exposure to water, salt, and other corrosive substances. The sealant forms a durable, waterproof barrier that prevents moisture intrusion and inhibits rust formation, thereby extending the vehicle’s lifespan.
- Weatherstripping: Silicone sealants and rubber seals around doors, windows, and hoods are used in weatherstrips. They provide a tight seal that removes water, wind, and noise from the vehicle interior. Silicone sealants maintain elasticity and adhesion even in extreme temperatures, ensuring long-lasting performance.
- Engine assembly: Silicone sealants are applied during engine assembly to seal various components, such as oil pans, valve covers, and timing covers. They provide a reliable seal against oil and coolant leaks, maintaining the engine’s performance and preventing potential damage.
- Brake systems: Silicone sealants are utilized in brake systems to seal hydraulic connections and prevent fluid leaks. They are compatible with brake fluids and resistant to high temperatures, ensuring the integrity and safety of the braking system.
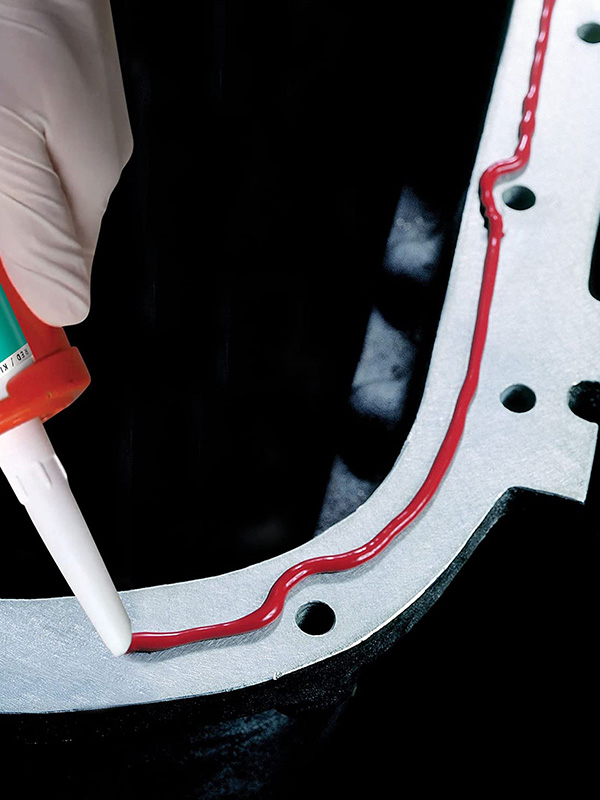
Household Uses of Silicone Sealant
Silicone sealant is a versatile product with numerous applications in household settings. Its unique properties, such as flexibility, durability, and resistance to water and extreme temperatures, make it an ideal choice for various sealing and bonding tasks. Here are some common household uses of silicone sealant:
- Bathroom and kitchen sealing: Silicone sealant is commonly used to seal joints and gaps in bathrooms and kitchens. It provides a watertight seal around sinks, bathtubs, showers, and countertops, preventing water penetration and minimizing the risk of water damage, mold, and mildew growth. Silicone sealant is resistant to moisture and flexible, making it suitable for areas exposed to water and high humidity.
- Window and door sealing: Silicone sealant is widely used to close gaps around windows and doors, preventing drafts, air leakage, and moisture infiltration. It helps improve energy efficiency by reducing heat loss or gain, thus lowering utility costs. Silicone sealant adheres well to various materials, including glass, wood, and metal, providing a durable and long-lasting seal.
- Plumbing repairs: Silicone sealant is commonly used for minor plumbing repairs, such as sealing leaky pipe joints and fittings. It creates a reliable, waterproof seal that prevents leaks and helps maintain the integrity of the plumbing system. Silicone sealant is compatible with different pipe materials, including PVC, copper, and stainless steel.
- Household repairs: Silicone sealant is helpful for a wide range of household repairs. It can fix cracks and gaps in walls, ceilings, and floors, providing an effective barrier against air and moisture infiltration. It can also seal gaps around electrical outlets and switches, preventing drafts and improving insulation.
- Glass and mirror mounting: Silicone sealant is often used for mounting glass and mirrors in various household applications. It provides a robust and flexible bond that securely holds the glass or mirror. Silicone sealant is transparent and does not yellow over time, ensuring a clean and aesthetically pleasing finish.
- Crafts and DIY projects: Silicone sealant is popular in crafts and do-it-yourself (DIY) projects. It can bond different materials, such as wood, plastic, and metal, in various creative applications. Silicone sealant is paintable and can be used as an adhesive for attaching decorations or repairing household items.
- Outdoor applications: Silicone sealant is suitable for outdoor use due to its resistance to weathering and UV rays. It can seal gaps and cracks in outdoor fixtures, such as gutters, downspouts, and outdoor lighting fixtures, protecting against water infiltration and preventing corrosion.
Benefits of Using Silicone Sealant
Silicone sealant is a versatile adhesive and sealing material that offers numerous benefits across various applications. Whether you’re working on a DIY project at home or involved in a professional construction project, silicone sealant can be a valuable tool. Here are some of the key benefits of using silicone sealant:
- Excellent Adhesion: Silicone sealants have strong adhesive properties, allowing them to bond to various materials, including glass, metal, plastic, ceramics, and wood. This makes them ideal for sealing joints, gaps, and cracks in different surfaces.
- Flexibility: Silicone sealants are highly flexible, which means they can withstand movement and vibration without cracking or losing their sealing properties. This makes them suitable for regular expansion and contraction applications, such as in windows, doors, and plumbing systems.
- Water Resistance: Silicone sealants are highly resistant to water and provide an effective barrier against moisture. This makes them ideal for sealing bathroom fixtures, sinks, showers, and outdoor applications where exposure to water is every day. Silicone sealants also prevent water penetration, helping to prevent mold, mildew, and water damage.
- Temperature Resistance: Silicone sealants have excellent temperature resistance properties, allowing them to withstand high and low temperatures. They can remain flexible and maintain their sealing integrity in extreme conditions, such as automotive engines, HVAC systems, and outdoor applications, subject to varying temperatures.
- UV Resistance: Silicone sealants are highly resistant to ultraviolet (UV) radiation, which means they won’t degrade or become discolored when exposed to sunlight. This makes them suitable for outdoor applications, such as sealing windows, roofs, and exterior joints, where they can provide long-lasting protection against UV rays.
- Chemical Resistance: Silicone sealants resist various chemicals, oils, solvents, and household cleaning agents. This makes them suitable for sealing applications in kitchens, laboratories, industrial settings, and areas where exposure to chemicals is every day.
- Easy Application and Cleanup: Silicone sealants are easy to apply and come in various forms, including cartridges, squeeze tubes, and aerosol cans. Depending on the project size, they can be applied using a caulking gun or by hand. Additionally, silicone sealants can be cleaned with water, making the application process convenient and hassle-free.
- Longevity: Silicone sealants have excellent durability and can maintain their sealing properties for an extended period. They resist weathering, aging, and degradation, ensuring a long-lasting seal. This reduces the need for frequent reapplication and helps to save time and money in the long run.
- Versatility: Silicone sealants have various applications across various industries and sectors. They are used in construction, automotive, marine, electronics, household repairs, etc. Their versatility makes them a go-to choice for many sealing and bonding needs.
Advantages of Silicone Sealant over Other Adhesives
Silicone sealant is a versatile adhesive that offers several advantages over other types of bonds. Here are some of the key benefits of using silicone sealant:
- Flexibility: Silicone sealant remains flexible even after it cures, making it ideal for applications where movement and expansion may occur. This flexibility allows it to withstand changes in temperature, vibration, and other stresses without cracking or losing its adhesive properties. This makes silicone sealant suitable for both indoor and outdoor applications.
- Waterproof and weather resistance: Silicone sealant is resistant to water, moisture, and weather conditions. It forms a watertight and airtight seal, perfect for sealing joints, gaps, and cracks in areas exposed to water or extreme weather. It can be used in bathrooms, kitchens, windows, and outdoor structures to prevent water leakage and moisture intrusion.
- Temperature resistance: Silicone sealant has a high-temperature tolerance, allowing it to maintain its adhesive properties in high- and low– temperature environments. It can withstand extreme temperatures without melting, cracking, or losing effectiveness. This makes it suitable for sealing applications in areas exposed to heat, such as around ovens, fireplaces, and engines.
- Chemical resistance: Silicone sealant exhibits excellent resistance to various chemicals, including acids, bases, solvents, and oils. It is not easily affected by exposure to chemicals, which makes it an ideal choice for sealing applications in laboratories, manufacturing facilities, and chemical processing plants.
- UV resistance: Silicone sealant has good resistance to sun ultraviolet (UV) radiation. This property allows it to maintain its integrity and adhesive strength when exposed to sunlight for extended periods. It helps prevent the sealant’s degradation, discoloration, and breakdown, making it suitable for indoor and outdoor applications.
- Excellent adhesion: Silicone sealant adheres well to various surfaces, including glass, metal, ceramics, plastics, and many building materials. It provides a strong and durable bond, ensuring long-lasting performance. Its ability to adhere to different surfaces makes it a versatile adhesive for various applications.
- Easy to use and apply: Silicone sealant is available in various forms, including cartridges, tubes, and squeeze bottles, making it easy to apply using a caulking gun or directly from the container. It has a smooth and pliable consistency, allowing for easy spreading and filling of gaps. Additionally, it can be easily tooled or smoothed with a putty knife or a finger to achieve a neat finish.
- Mold and mildew resistance: Silicone sealant has inherent mold and mildew growth resistance. Its non-porous surface discourages the growth of microorganisms, making it suitable for sealing applications in humid and damp environments, such as bathrooms and kitchens.
How to Apply Silicone Sealant
Applying silicone sealant is handy for various household projects, such as sealing gaps around windows, sinks, or showers. Silicone sealant creates a waterproof and airtight seal, preventing water leakage and improving insulation. Here’s a step-by-step guide on how to apply silicone sealant:
- Gather the necessary materials: You’ll need silicone sealant, a caulking gun, a utility knife, masking tape, a rag or sponge, and a caulk smoothing tool.
- Prepare the area: Clean the surface where you’ll apply the silicone sealant. Remove any old caulk or debris using a utility knife or scraper. Clean the surface with a mild detergent and water, and ensure it is scorched before proceeding.
- Apply masking tape: If you want a clean and precise seal, apply masking tape on both sides of the joint or gap where you’ll use the silicone sealant. The video acts as a guide and helps in creating straight lines.
- Load the caulk gun: Open the caulking gun by pulling back the metal rod and inserting the silicone sealant tube into the gun. Cut off the tip of the sealant tube at a 45-degree angle, making a small opening. Screw on the nozzle tightly.
- Test the flow: Squeeze the caulk gun’s trigger gently to test the flow of the sealant. Adjust the flow by releasing or tightening the rod. Aim for a consistent and controlled flow.
- Apply the sealant: Hold the caulk gun at a 45-degree angle and apply the silicone sealant to the joint or gap. Begin at one end and move steadily along the entire length. Apply even pressure on the trigger to ensure a consistent sealant line.
- Smooth the sealant: Immediately after applying the silicone sealant, use a caulk smoothing tool or your finger to smooth and shape the adhesive. Wetting your finger or the smoothing tool with a mild soapy water solution can help prevent sticking. Smooth the sealant with gentle, even strokes to achieve a neat finish.
- Remove the masking tape: If you use it, carefully remove it before the sealant matures. Pull the tape away at a 45-degree angle to avoid disturbing the freshly applied sealant.
- Clean up: Wipe away any excess sealant with a damp rag or sponge. Avoid smearing the sealant onto surrounding surfaces. If any adhesive gets on your hands or skin, use a silicone sealant remover or rubbing alcohol to clean it off.
- Allow curing time: Follow the manufacturer’s instructions for the recommended curing time of the silicone sealant. It typically takes several hours to cure fully. Avoid disturbing or exposing the adhesive to water until it is completely fixed.
Following these steps, you can apply silicone sealant and achieve a professional-looking seal. Remember to work carefully, take your time, and practice good cleanup habits to ensure a satisfactory result.
Precautions and Safety Measures for Using Silicone Sealant
Silicone sealants are versatile and commonly used for various sealing and bonding applications. They offer excellent adhesion and durability, but taking certain precautions and safety measures is essential to ensure safe handling and optimal results. Here are some guidelines to follow:
- Read and follow instructions: Before using a silicone sealant, carefully read and understand the manufacturer’s instructions, warnings, and safety data sheet (SDS). Adhere to the recommended procedures for application, drying time, and cleanup.
- Work in a well-ventilated area: Silicone sealants emit volatile organic compounds (VOCs) during application and curing. To prevent inhalation of these fumes, ensure proper ventilation in the working area. Open windows or use exhaust fans to improve air circulation.
- Wear personal protective equipment (PPE): Always wear appropriate PPE when working with silicone sealants. This typically includes safety glasses, gloves, and a respiratory mask or respirator, especially when working in enclosed spaces or if prolonged exposure is expected.
- Avoid skin contact: Silicone sealants can cause irritation or allergic reactions upon skin contact. Wear gloves made of nitrile or neoprene to protect your skin. If contact occurs, immediately wash the affected area with soap and water. If irritation persists, seek medical attention.
- Use eye protection: Protect your eyes from potential splashes or accidental contact with the sealant. Wear safety glasses or goggles at all times during application and cleanup.
- Store properly: Store silicone sealants in a cool, dry place away from direct sunlight and ignition sources. Ensure that containers are tightly sealed to prevent drying or leakage. Follow any specific storage instructions provided by the manufacturer.
- Keep away from children and pets: Silicone sealants should be kept out of reach. They are not intended for ingestion and can be harmful if swallowed.
- Test compatibility: Before applying silicone sealant, test its compatibility with the surface or materials you intend to seal. Apply a small amount in an inconspicuous area and check for any adverse reactions, such as discoloration or damage.
- Clean up spills promptly: In case of spills or drips, clean them up immediately using a suitable solvent recommended by the manufacturer. Avoid spreading the sealant or allowing it to cure on unintended surfaces.
- Disposal: Dispose of used silicone sealant and empty containers according to local regulations and guidelines. Please do not dispose of them in regular trash or pour them down the drain.
- Fire safety: Silicone sealants are generally non-flammable, but some may release flammable vapors during curing. Avoid exposing the uncured adhesive to open flames, sparks, or heat sources. Take precautions to prevent accidental fires.
Remember, these precautions and safety measures are general guidelines. Always consult the specific instructions the silicone sealant manufacturer provides for the best practices and safety recommendations for their particular product.
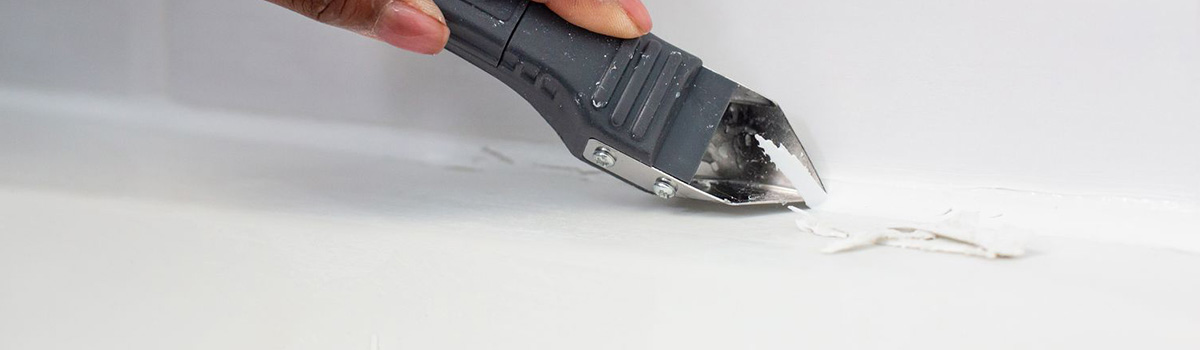
How to Remove Silicone Sealant
Removing silicone sealant can be challenging, but with the right tools and techniques, it can be done effectively. Here are some steps to help you remove silicone sealant:
- Gather the necessary tools: You’ll need a utility knife or a silicone sealant removal tool, a scraper, rubbing alcohol or a silicone sealant remover, rags or paper towels, and gloves for protection.
- Soften the sealant: If it is old and hardened, you may need to soften it before removal. Apply heat using a hairdryer or a heat gun set to a low temperature. Gently heat the sealant for a few minutes, making it more pliable and easier to remove.
- Cut and scrape: Use a utility knife or a silicone sealant removal tool to cut through the sealant along the edges carefully. Start at one end and work your way along the entire length. Take care not to damage the underlying surfaces. Once the edges are cut, use a scraper to lift and remove the sealant from the surface gently. Apply steady pressure and work slowly to avoid scratching or damaging the surface.
- Clean the residue: After removing the bulk of the sealant, deposition may be left behind. Use a silicone sealant remover or rubbing alcohol to clean the area. Apply the remover or alcohol to a rag or paper towel and gently scrub the residue until completely removed. Be cautious when using solvents, as they may affect certain surfaces, so test them in an inconspicuous area first.
- Rinse and dry: Once the residue is removed, rinse the area with water to remove any remaining traces of the sealant remover or rubbing alcohol. Dry the surface thoroughly with a clean cloth.
- Check for completeness: After the area is dry, inspect it to ensure all the silicone sealant has been removed. Repeat the process or consider using a specialized silicone sealant remover designed explicitly for stubborn residue if there are any remaining traces.
- Dispose of waste properly: Collect the used rags, paper towels, and other waste materials in a sealed plastic bag. Dispose of them according to local regulations and guidelines.
Remember, the effectiveness of the removal process can vary depending on the type of silicone sealant and the surface it is applied to. It’s always a good idea to first test the removal method on a small, inconspicuous area to ensure it doesn’t damage the surface. Consult a professional for assistance if you are unsure or dealing with a complex situation.
Cleaning and Maintaining Silicone Sealant
Removing silicone sealant can be challenging, but with the right tools and techniques, it can be done effectively. Here are some steps to help you remove silicone sealant:
- Gather the necessary tools: You’ll need a utility knife or a silicone sealant removal tool, a scraper, rubbing alcohol or a silicone sealant remover, rags or paper towels, and gloves for protection.
- Soften the sealant: If it is old and hardened, you may need to soften it before removal. Apply heat using a hairdryer or a heat gun set to a low temperature. Gently heat the sealant for a few minutes, making it more pliable and easier to remove.
- Cut and scrape: Use a utility knife or a silicone sealant removal tool to cut through the sealant along the edges carefully. Start at one end and work your way along the entire length. Take care not to damage the underlying surfaces. Once the edges are cut, use a scraper to lift and remove the sealant from the surface gently. Apply steady pressure and work slowly to avoid scratching or damaging the surface.
- Clean the residue: After removing the bulk of the sealant, deposition may be left behind. Use a silicone sealant remover or rubbing alcohol to clean the area. Apply the remover or alcohol to a rag or paper towel and gently scrub the residue until completely removed. Be cautious when using solvents, as they may affect certain surfaces, so test them in an inconspicuous area first.
- Rinse and dry: Once the residue is removed, rinse the area with water to remove any remaining traces of the sealant remover or rubbing alcohol. Dry the surface thoroughly with a clean cloth.
- Check for completeness: After the area is dry, inspect it to ensure all the silicone sealant has been removed. Repeat the process or consider using a specialized silicone sealant remover designed explicitly for stubborn residue if there are any remaining traces.
- Dispose of waste properly: Collect the used rags, paper towels, and other waste materials in a sealed plastic bag. Dispose of them according to local regulations and guidelines.
Remember, the effectiveness of the removal process can vary depending on the type of silicone sealant and the surface it is applied to. It’s always a good idea to first test the removal method on a small, inconspicuous area to ensure it doesn’t damage the surface. Consult a professional for assistance if you are unsure or dealing with a complex situation.
Storage and Shelf Life of Silicone Sealant
Silicone sealants are commonly used in various applications, including construction, automotive, and household repairs. Understanding their storage requirements and shelf life is essential to ensure optimal performance and longevity. Here’s a concise explanation of silicone sealants’ storage and shelf life.
Storage: Proper storage plays a crucial role in maintaining the quality and effectiveness of silicone sealants. Here are some key points to consider:
- Temperature: Silicone sealants should be stored at temperatures recommended by the manufacturer. Generally, the ideal temperature range for storage is between 40°F (5°C) and 80°F (27°C). Extreme heat or cold can degrade the sealant’s performance and shorten its shelf life.
- Humidity: Moisture can affect the consistency and curing properties of silicone sealants. Storing them in a dry environment is essential to prevent water absorption. Keep the sealant containers tightly closed when not in use to minimize moisture exposure.
- Sunlight: Prolonged exposure to direct sunlight can accelerate the degradation of silicone sealants. Store them away from direct sunlight or UV radiation sources to maintain their integrity.
- Packaging: Sealant containers should be tightly sealed to prevent air and moisture infiltration. Ensure the lids are properly closed after each use. If the original container is damaged, transfer the sealant to an airtight, moisture-resistant alternative.
Shelf Life: Silicone sealants have a finite shelf life, beyond which their quality and performance may decline. The shelf life can vary depending on various factors, including the formulation, storage conditions, and manufacturer specifications. Here are some general guidelines:
- Expiration Date: Check the expiration date provided by the manufacturer on the sealant container. This date indicates when the sealant is expected to retain its quality when stored properly. Avoid using adhesives beyond their expiration date.
- Manufacturer Recommendations: Follow the specific guidelines provided by the manufacturer regarding the shelf life of their silicone sealant products. Some sealants may have a shelf life of one year, while others can last longer.
- Visual Inspection: Before using a silicone sealant, visually inspect it for any signs of degradation or changes in consistency. If the sealant appears lumpy, discolored or has separated into layers, it may have exceeded its shelf life or been stored improperly. In such cases, it is advisable to discard the sealant.
- Curing Test: If you need more clarification about the sealant’s quality, perform a small curing test on a sample surface. Apply a small amount of sealant and allow it to cure according to the manufacturer’s instructions. Evaluate the cured sealant’s strength, flexibility, and adhesion properties. If the results are unsatisfactory, the sealant may have exceeded its shelf life.
It’s important to note that these guidelines provide a general understanding of silicone sealant storage and shelf life. Always refer to the specific recommendations provided by the manufacturer for accurate information. By storing silicone sealants correctly and using them within their designated shelf life, you can ensure optimal performance and achieve the desired results in your applications.
Factors to Consider When Choosing Silicone Sealant
When choosing a silicone sealant, several essential factors must be considered to ensure you select the right product for your specific application. Here are some key factors to keep in mind:
- Application: Consider the specific purpose for which you require the silicone sealant. Different sealants are designed for various applications such as plumbing, automotive, construction, or general household use. Ensure that the sealant you choose is suitable for your intended application.
- Cure Time: Take into account the curing time of the silicone sealant. Some sealants cure quickly, while others may require more time to set and create a strong bond entirely. Consider your project timeline and select a sealant that aligns with your requirements.
- Adhesion: Evaluate the adhesion properties of the silicone sealant. Determine the surfaces you need to bond and ensure the sealant adheres to those materials. It should have good adhesion to various substrates like glass, metal, plastic, and ceramics.
- Flexibility: Consider the flexibility of the silicone sealant. If you anticipate movement or expansion in the joint or surface you are sealing, choose a sealant designed to accommodate such activity without cracking or losing its bond.
- Temperature Resistance: Assess the temperature range in which the silicone sealant will be exposed. Different sealants have varying temperature resistance capabilities. If your application involves extreme temperatures, select a sealant that can withstand those conditions without degradation.
- Chemical Resistance: Determine whether the sealant needs to resist exposure to chemicals, solvents, or other corrosive substances. Certain adhesives are formulated to withstand chemical exposure, making them suitable for applications where contact with such substances is expected.
- UV Resistance: If the sealant is exposed to sunlight or UV radiation, choose a silicone sealant with UV resistance. UV-resistant sealants prevent degradation and color fading when exposed to prolonged sunlight.
- Color and Appearance: Consider the aesthetic requirements of your project. Silicone sealants are available in various colors, so choose one that matches or complements the surface or material you are sealing. Additionally, decide whether you prefer a translucent or opaque sealant.
- Application Method: Determine the method of application that suits your needs. Silicone sealants, such as cartridges, tubes, or squeeze bottles, come in different forms. Consider the ease of application and the tools required to apply the sealant effectively.
- Brand and Quality: Research reputable brands that are known for producing high-quality silicone sealants. Review reviews and consult professionals if necessary to ensure you select a reliable and durable product.
By considering these factors, you can make an informed decision when choosing a silicone sealant that meets your specific requirements and ensures a successful outcome for your project.
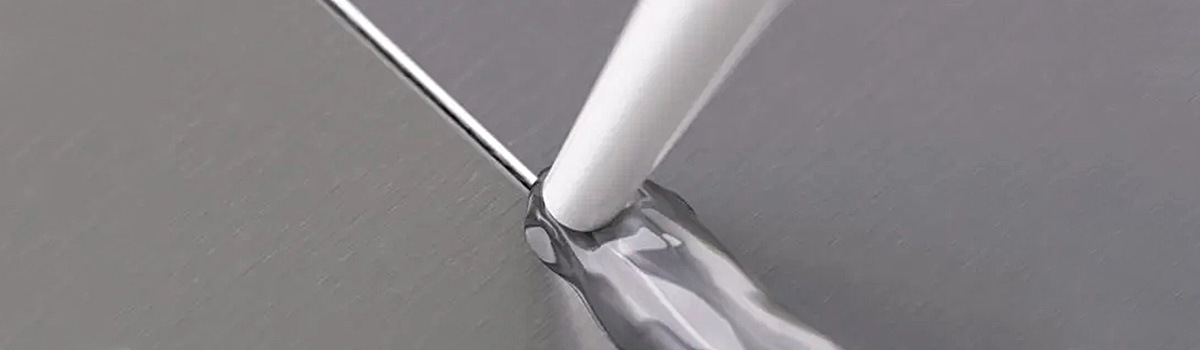
Popular Brands of Silicone Sealant
Silicone sealants are versatile products widely used for sealing and bonding applications in various industries and household projects. They provide excellent adhesion, flexibility, and resistance to temperature, moisture, and chemicals. If you’re looking for famous brands of silicone sealant, here are some well-known names in the market:
- GE Silicones: GE Silicones, a subsidiary of General Electric, offers various silicone sealants for different applications. Their products are known for their high-performance properties and durability. GE Silicone II and GE Silicone 1 are popular choices among consumers.
- DAP: DAP is a leading manufacturer of sealants and adhesives, offering a comprehensive range of silicone sealants. DAP’s silicone sealants are known for their strong adhesion and flexibility. DAP 100% Silicone and DAP Alex Plus are commonly used products in their lineup.
- Loctite: Loctite, a brand under Henkel, is known for its quality adhesives and sealants. They offer a variety of silicone sealants designed for specific applications, such as Loctite Clear Silicone and Loctite Marine Silicone. These products provide excellent resistance to water, weathering, and UV rays.
- 3M: 3M is a well-established company known for innovative solutions in various industries. They offer a range of high-quality silicone sealants, including 3M Marine Adhesive Sealant and 3M Fire Barrier Silicone Sealant. These products are designed to withstand harsh environments and provide reliable performance.
- Sika: Sika is a global brand specializing in construction chemicals and industrial adhesives. They have a selection of silicone sealants suitable for interior and exterior applications. SikaSil is one of their famous lines, offering products like SikaSil-GP and SikaSil-WS. These sealants provide excellent adhesion and weather resistance.
- Permatex: Permatex is a trusted brand in the automotive and repair industry. They offer a range of silicone sealants designed for automotive applications, such as engine gaskets and weatherstripping. Permatex Black Silicone Adhesive Sealant and Permatex Clear RTV Silicone Adhesive Sealant are widely used for their durability and heat resistance.
- Gorilla: Gorilla is known for its solid and reliable adhesive products. They also offer a silicone sealant called Gorilla 100% Silicone Sealant. This sealant is versatile and can be used for indoor and outdoor projects. It provides a strong bond and excellent resistance to moisture and weathering.
- Red Devil: Red Devil is a brand that offers a variety of sealants and adhesives for different applications. Their silicone sealants, such as Red Devil Silicone Sealant, are known for their durability and flexibility. These products can seal gaps and cracks in windows, doors, and other surfaces.
Remember to read the specific product descriptions and instructions before using silicone sealant. Different brands may offer variations in cure time, color options, and specific application requirements. Choose a brand that best suits your project needs, and always follow the manufacturer’s recommendations for optimal results.
Silicone Sealant vs. Acrylic Sealant: Which One to Choose?
Two standard options for sealing and bonding applications are silicone sealant and acrylic sealant. Both have advantages and considerations, so let’s explore the characteristics of each to help you make an informed decision.
Properties and Performance:
- Silicone Sealant: Silicone sealants are known for their excellent flexibility, adhesion, and resistance to temperature, moisture, and chemicals. They maintain their elasticity over a wide temperature range and offer superior durability. Silicone sealants are suitable for indoor and outdoor applications and particularly effective in high-moisture environments.
- Acrylic Sealant: Acrylic sealants are known for their fast curing and paintability. They have good adhesion to various surfaces, including wood, metal, and drywall. Acrylic adhesives typically dry to a more complex finish compared to silicone sealants. They are often used for interior applications where flexibility and resistance to extreme conditions are not critical.
Applications:
- Silicone Sealants: Due to their excellent resistance to moisture, temperature, and chemicals, they are widely used in areas exposed to water or harsh environments. They are commonly used in bathrooms, kitchens, and other areas prone to water exposure and for sealing windows, doors, and exterior gaps. Silicone sealants are also suitable for bonding glass, ceramics, and plastics.
- Acrylic Sealant: Acrylic sealants are commonly used for interior applications such as sealing gaps around baseboards, trim, and crown molding. They are also suitable for filling cracks in walls, repairing drywall, and general caulking projects. Acrylic sealants are often chosen for their paintability, allowing seamless integration with the surrounding surfaces.
Flexibility:
- Silicone Sealant: Silicone sealants offer excellent flexibility, allowing them to accommodate movement and expansion without cracking or losing adhesion. This flexibility makes them ideal for sealing joints and gaps that experience frequent activity, such as windows, doors, and expansion joints.
- Acrylic Sealant: Acrylic sealants are relatively less flexible compared to silicone sealants. While they can accommodate minimal movement, they are more prone to cracking or losing adhesion in areas with significant joint movement. Therefore, they may not be suitable for applications where flexibility is crucial.
Cost Considerations:
- Silicone Sealant: Silicone sealants are generally more expensive than acrylic sealants due to their superior performance and durability. However, their long-term benefits and reliability often outweigh the initial cost.
- Acrylic Sealant: Acrylic sealants are more affordable than silicone sealants, making them a budget-friendly option for interior sealing projects. They offer satisfactory performance for applications that do not require extreme flexibility or resistance to moisture.
Silicone Sealant vs. Polyurethane Sealant: A Comparison
Silicone and polyurethane sealants are popular options for various sealing and bonding applications. While both are effective at creating watertight and airtight seals, they have different properties and are suited for other purposes. In this comparison, we will explore the characteristics and applications of silicone sealant and polyurethane sealant.
Silicone sealant is a versatile and widely used sealant known for its excellent flexibility and resistance to extreme temperatures. It is made from silicone polymers and contains a curing agent allowing it to transform from liquid to solid. Silicone sealant has superb adhesive properties and adheres well to various materials, including glass, metal, ceramic, and most plastics. Its flexibility allows it to withstand expansion and contraction caused by temperature variations without losing its sealing properties. Silicone sealant is also highly resistant to UV radiation, moisture, and chemicals, making it ideal for outdoor applications such as sealing windows, doors, and joints.
On the other hand, polyurethane sealant is a solid and durable adhesive that offers excellent adhesion and high tensile strength. It comprises polyurethane polymers and a curing agent that triggers the hardening process. Polyurethane sealant forms a rigid, elastic seal that can withstand heavy loads and mechanical stresses. It is commonly used in construction applications, such as sealing concrete joints, bonding concrete to other materials, and filling structural gaps and cracks. Polyurethane sealant provides good moisture, chemicals, and abrasion resistance, making it suitable for indoor and outdoor applications.
When it comes to application, silicone sealant is easier to work with due to its smooth and non-sticky consistency. It can be easily applied using a caulking gun and tooled to achieve a neat finish. Silicone sealant also has a longer shelf life than polyurethane sealant and does not require a primer in most cases. However, it has a slower curing time, typically taking 24 to 48 hours to cure fully.
Polyurethane sealant, on the other hand, has a faster curing time, usually ranging from a few hours to a day. It has a thicker consistency and may require a primer, especially when bonding to certain materials. Polyurethane sealant also has a strong odor during curing, which may be a consideration in confined spaces.
In summary, silicone and polyurethane sealants have unique properties and applications. Silicone sealant offers excellent flexibility, resistance to extreme temperatures, and UV stability, making it suitable for various sealing tasks. Polyurethane sealant, on the other hand, provides high strength, durability, and faster curing times, making it ideal for heavy-duty bonding and construction applications. Choosing between the two depends on the specific requirements of the project at hand.
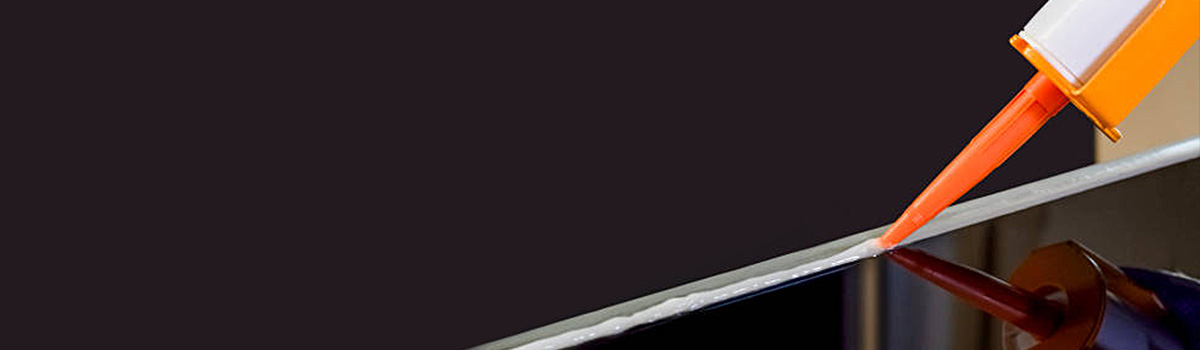
Frequently Asked Questions About Silicone Sealant
Q: What is silicone sealant? A: Silicone sealant is an adhesive material commonly used for sealing and bonding applications. It is made from silicone polymers and is known for its flexibility, durability, and resistance to extreme temperatures.
Q: What are the applications of silicone sealant? A: Silicone sealant has a wide range of applications. It is commonly used for sealing gaps and joints in windows, doors, and other construction materials. It is also used for waterproofing and weatherproofing applications, such as sealing roofs, gutters, and flashings. Silicone sealant is frequently used in plumbing to create watertight seals around pipes and fixtures. Additionally, it is used in automotive, electronics, and various industrial applications.
Q: What are the advantages of silicone sealant? A: Silicone sealant offers several advantages. Its excellent flexibility allows it to withstand movement and expansion/contraction of materials without losing its sealing properties. Silicone sealant is resistant to UV radiation, moisture, and chemicals, making it suitable for outdoor applications. It has good adhesive properties and adheres well to various surfaces, including glass, metal, ceramic, and most plastics. Silicone sealant has a long shelf life and can maintain its properties over time.
Q: How do you apply silicone sealant? A: Silicone sealant is typically applied using a caulking gun. Before applying, the surface should be clean and dry. Cut the nozzle of the sealant tube at a 45-degree angle to the desired bead size. Load the tube into the caulking gun, then squeeze the trigger to apply a continuous bead of sealant along the joint or gap. To create a neat finish, smooth the sealant with a tool or a finger dipped in soapy water. Allow the sealant to cure as per the manufacturer’s instructions.
Q: How long does silicone sealant take to cure? A: The curing time of silicone sealant can vary depending on factors such as temperature, humidity, and the thickness of the applied sealant. Generally, silicone sealant takes 24 to 48 hours to cure fully. However, it forms skin within 15 to 30 minutes and can be touched or exposed to water after that initial skin formation.
Q: Can silicone sealant be painted over? A: Yes, silicone sealant can be painted over. However, it is essential to ensure the sealant is fully cured before applying paint, and silicone sealant is not paintable while still in the curing process.
Q: Can silicone sealant be used underwater? A: Yes, silicone sealant is often used for underwater applications, and it is water-resistant and can maintain its sealing properties even when submerged. There are specific silicone sealants designed for underwater use, so choosing the appropriate product for the specific application is essential.
Q: Is silicone sealant heat resistant? A: Yes, silicone sealant is known for its excellent resistance to high temperatures, and it can withstand extreme heat without losing its sealing properties or degrading. Silicone sealants are commonly used in applications that involve exposure to high temperatures, such as sealing around ovens, stoves, and fireplaces.
Q: Can silicone sealant be removed? A: Yes, silicone sealant can be removed. Silicone sealant removers are available that can help dissolve and soften the sealant for easier removal. Additionally, mechanical methods such as scraping or cutting can remove the sealant. Following the manufacturer’s instructions and taking appropriate safety precautions when removing silicone sealant is essential.
Q: Is silicone sealant toxic? A: Generally, silicone sealant is considered to be non-toxic once it has fully cured. However, during the curing process, some silicone seal
Common Mistakes to Avoid When Using Silicone Sealant
When using silicone sealant, following proper application techniques is essential to ensure a successful and durable seal. However, there are some everyday things that people often need to correct when working with silicone sealants. You can achieve better results and avoid potential issues by avoiding these mistakes. Here are some common mistakes to avoid when using silicone sealant:
- Insufficient surface preparation: One of the most common mistakes is neglecting proper surface preparation. Before applying silicone sealant, it is crucial to clean the surface thoroughly to remove dirt, dust, grease, and old sealant residue. Failing to prepare the surface adequately can lead to poor adhesion and an ineffective seal.
- Using the wrong type of silicone: Silicone sealants come in different formulations designed for specific applications. Using the wrong type of silicone for your intended purpose can lead to problems. For example, using a bathroom silicone sealant in high-temperature areas like around stoves or fireplaces can cause the adhesive to break down and fail. Always choose a silicone sealant compatible with the surface and conditions where it will be applied.
- Applying too much sealant: Another common mistake is using excessive silicone sealant. Overapplication can lead to messy results, extended curing times, and wastage of the product. Applying the sealant in a thin, even bead is essential to ensure proper adhesion and avoid excessive squeeze-out.
- Improper tooling: Tooling refers to smoothing and shaping the applied sealant using a tool or your finger. Please properly tool the silicone sealant to ensure a smooth finish and good adhesion. Use a tool or your finger dipped in a soapy water solution to smooth the sealant, ensuring it fills the gap or joint.
- Not allowing sufficient curing time: Silicone sealants require adequate time to cure and form a strong bond. Many people need to enable more healing time before exposing the adhesive to water, moisture, or movement. Following the manufacturer’s instructions regarding the recommended curing time is essential before subjecting the sealant to any stress or smoke.
- Ignoring temperature and humidity guidelines: Temperature and humidity can significantly impact the curing and performance of silicone sealants. Applying silicone sealant in extremely hot or cold temperatures can affect its ability to cure properly. High humidity levels can also delay curing and affect the final seal’s quality. Always check the product instructions for the application’s recommended temperature and humidity range.
- Failure to maintain cleanliness during application: Maintaining a clean work environment is crucial when using silicone sealant. Any dirt, debris, or moisture that comes into contact with the uncured adhesive can compromise its adhesion and effectiveness. Keep the work area clean and avoid touching the uncured adhesive with dirty hands or tools.
By avoiding these common mistakes, you can ensure better results and maximize the performance of silicone sealants. Remember to read and follow the manufacturer’s instructions for your specific adhesive, as different products may have unique requirements and recommendations.
Future Trends and Innovations in Silicone Sealant Technology
- Silicone sealants have been widely used in various industries and applications due to their excellent adhesive properties, flexibility, and resistance to extreme temperatures and weathering. As technology continues to advance, the future of silicone sealant technology holds promising developments and innovations. Here are some trends and advancements expected in the field within the next few years.
- Enhanced Performance: Future silicone sealants will likely exhibit even better performance characteristics. This includes improved adhesion to a wide range of substrates, higher elongation, and flexibility, increased resistance to UV radiation, and improved durability in harsh environments. These advancements will expand the applications of silicone sealants in industries such as construction, automotive, electronics, and aerospace.
- Sustainable Formulations: With growing environmental concerns, there is a strong focus on developing sustainable sealant formulations. Future silicone sealants are expected to have reduced volatile organic compound (VOC) emissions and lower environmental impact. Manufacturers are investing in research to develop bio-based silicone sealants derived from renewable sources, contributing to a more sustainable and eco-friendly industry.
- Innovative Sealants: Integrating smart technologies into silicone sealants is an emerging trend. Future adhesives may incorporate sensors or indicators to detect temperature, pressure, or moisture changes. These innovative sealants can provide real-time information about the condition of sealed joints or surfaces, allowing for proactive maintenance and preventing potential failures.
- Self-Healing Properties: Researchers are exploring the development of silicone sealants with self-healing capabilities. These sealants can repair minor cracks or damages autonomously using encapsulated healing agents or shape memory polymers. Self-healing sealants will significantly enhance the lifespan and performance of seals, reducing the need for frequent replacements.
- Rapid Curing: Speed and efficiency are crucial factors in many industries. Future silicone sealants are expected to offer faster curing times, allowing for quicker assembly or repair processes. Advances in curing technologies, such as UV-curable or moisture-curable sealants, will enable rapid bonding and sealing without compromising the strength and quality of the joint.
- Advanced Bonding Techniques: Innovations in bonding techniques will play a vital role in silicone sealant technology. New methods, such as plasma treatment or nanotechnology-based surface modifications, will enhance the adhesion properties of silicone sealants, enabling more robust and more durable bonds. These advancements will expand the range of substrates that can be effectively sealed with silicone sealants.
- Improved Safety: The future of silicone sealant technology will prioritize safety aspects. Manufacturers are investing in developing sealants with reduced toxicity, lower odor emissions, and improved handling characteristics. These advancements will ensure safer working environments for professionals and reduce health risks associated with sealant application and usage.
Conclusion
Silicone sealant is a versatile and durable adhesive material that offers many benefits over other adhesives. It has many uses, including construction, automotive, and household applications. Choosing the proper silicone sealant for your needs requires considering factors such as the type of materials being bonded and the conditions it will be subjected to. With proper application, maintenance, and safety precautions, silicone sealant can provide a long-lasting and reliable solution for your bonding needs.