Electric Motor Epoxy Adhesive
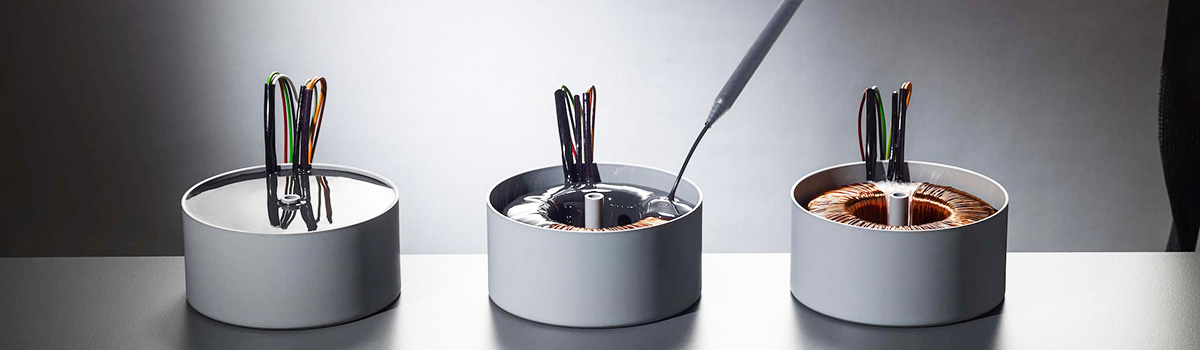
Electric motor epoxy adhesive is a specialized type designed for electric motors. This adhesive bonds various engine components, such as magnets, coils, and laminations, and it seals and protects the motor from environmental factors such as moisture and heat. In this article, we will explore the benefits and applications of electric motor epoxy adhesive and the factors to consider when selecting a suitable adhesive for a particular job.
What is Electric Motor Epoxy Adhesive?
Electric motor epoxy adhesive is a specialized adhesive explicitly designed for bonding and securing components in electric motors. It is a high-strength adhesive that provides excellent adhesion and electrical insulation properties. This epoxy adhesive can withstand high temperatures, vibrations, and harsh operating conditions commonly encountered by electric motors. It effectively bonds various materials, including metals, ceramics, and plastics, ensuring the structural integrity of motor components. Electric motor epoxy adhesive plays a crucial role in enhancing the reliability and performance of electric motors by providing a durable and electrically insulating bond between different parts, thereby minimizing the risk of electrical shorts and mechanical failures.
How Does Electric Motor Epoxy Adhesive Work?
Electric motor epoxy adhesive works by employing a combination of chemical and physical mechanisms to create strong and durable bonds between motor components. Here are the key points explaining how electric motor epoxy adhesive works:
- Chemical Reaction: Electric motor epoxy adhesive comprises a resin and a hardener that require specific ratios for mixing. The components initiate a chemical reaction, causing the epoxy to cure and harden. This chemical reaction forms cross-linked solid polymer chains, contributing to the adhesive’s high strength and stability.
- Adhesive Properties:The cured epoxy adhesive exhibits excellent properties, allowing it to bond with materials commonly found in electric motors, including metals, ceramics, and plastics. The adhesive forms intimate contact with the surfaces of the components, creating strong molecular-level interactions and promoting adhesion.
- Surface Preparation:Properly preparing the motor components’ surfaces is crucial before applying the epoxy adhesive. For optimal adhesion, it is necessary to clean and degrease the surfaces thoroughly to remove any contaminants. Roughening the surfaces through sanding or etching can also enhance the bond strength by increasing the surface area available for adhesion.
- Thermal Resistance: The electric motor epoxy adhesive formulation can withstand the high temperatures generated during motor operation. It maintains its structural integrity and adhesive strength even under extreme thermal conditions, ensuring the bonded components remain securely attached.
- Electrical Insulation: Electric motor epoxy adhesive offers excellent electrical insulation properties besides providing a solid bond. It acts as a barrier, preventing electrical current from passing through the bonded area and minimizing the risk of short circuits. This insulation property is crucial for maintaining electric motors’ reliable and safe operation.
- Vibration and Shock Resistance: Electric motors often experience significant vibrations and shocks during operation. The epoxy adhesive’s high flexibility and ability to absorb mechanical stresses help to prevent the bonded components from loosening or separating under such dynamic conditions. Following this practice, the motor will last longer and be more dependable.
Advantages of Electric Motor Epoxy Adhesive
Electric motor epoxy adhesive offers several advantages that make it a preferred choice for bonding and securing components in electric motors. Here are the key benefits of using electric motor epoxy adhesive:
- Strong Bond: Electric motor epoxy adhesive creates a strong and durable bond between motor components, ensuring their stability and integrity. It forms intimate contact with the surfaces, promoting excellent adhesion and minimizing the risk of component separation or movement.
- Thermal Stability: We formulate electric motor epoxy adhesive to withstand high temperatures generated during motor operation. It maintains its structural integrity and adhesive strength even in extreme thermal conditions, ensuring long-lasting performance and reliability.
- Electrical Insulation: The epoxy adhesive provides effective electrical insulation, preventing electrical current from passing through the bonded area. This insulation property reduces the risk of electrical shorts and improves the safety and reliability of electric motors.
- Chemical Resistance: Electric motor epoxy adhesive exhibits excellent resistance to various chemicals and solvents. It can withstand exposure to oils, fuels, lubricants, and other substances commonly found in motor environments without compromising its adhesive properties or structural integrity.
- Vibration and Shock Absorption: Electric motors experience vibrations and shocks during operation, which can loosen or weaken the bonds between components. The electric motor epoxy adhesive has good flexibility and shock-absorbing properties, effectively dampening vibrations and minimizing the risk of bond failure.
- Versatility: Electric motor epoxy adhesive is compatible with various materials, including metals, ceramics, and plastics. It can bond components, such as stators, rotors, magnets, and coils, offering versatility in motor assembly and repair applications.
- Easy Application:Electric motor epoxy adhesive is typically available in two-component formulations, which are easy to mix and apply. Once mixed, it has a suitable working time before it starts to cure, allowing for proper positioning and adjustment of components. This ease of application contributes to efficient motor assembly and maintenance processes.
- Longevity:Due to its high strength, thermal stability, and resistance to environmental factors, electric motor epoxy adhesive helps extend the lifespan of electric motors. It ensures the durability and reliability of the bonded components, minimizing the need for frequent repairs or replacements.
Exceptional Bonding Strength
The exceptional bonding strength is a crucial characteristic of high-quality adhesives, providing reliable and durable connections between various materials. Here are the key points explaining the significance and factors contributing to exceptional bonding strength:
- Surface Preparation: Proper surface preparation is crucial to achieve exceptional bonding strength. Characters must be thoroughly cleaned, degreased, and, if necessary, roughened to ensure optimal adhesion. Removing contaminants and creating a rough surface increases the contact area between the adhesive and the substrate, enhancing the bond strength.
- Molecular-level Interactions: Adhesives with exceptional bonding strength create molecular-level solid interactions with the substrate materials. Chemical bonding, electrostatic interactions, and intermolecular forces (like Van der Waals) are all ways of achieving this. These interactions increase the adhesive’s ability to withstand external forces and stresses.
- Adhesive Formulation:The formulation of the adhesive plays a vital role in determining its bonding strength. Adhesives with high-strength formulations, such as epoxy or polyurethane adhesives, offer excellent bonding capabilities. Selecting the right adhesive type, based on the bonded materials and intended application, is essential to achieve exceptional bonding strength.
- Curing Process:The curing process of an adhesive significantly impacts its final bonding strength. When adhesives like epoxy undergo a curing process, they form cross-linked polymer networks that make them more robust and stable. Proper curing, including temperature, humidity, and time, is essential to maximize the adhesive’s bonding strength.
- Material Compatibility: Exceptional bonding strength requires compatibility between the adhesive and the substrate materials. Manufacturers formulate adhesives to bond specific types of materials, such as metals, plastics, or composites. Ensuring the adhesive is compatible with the bonded substrates is essential for achieving optimal bonding strength.
- Environmental Factors:Environmental factors, such as temperature, humidity, and exposure to chemicals or UV radiation, can affect the bonding strength of adhesives. High-quality adhesives designed for specific environments, such as automotive or aerospace applications, are formulated to maintain their bonding strength even under challenging conditions.
- Testing and Quality Control:Adhesive manufacturers conduct rigorous testing and quality control measures to ensure exceptional bonding strength. It must undergo different evaluations like shear, peel, or tensile tests to determine how well an adhesive works. Adhesives that meet or exceed industry standards for bonding strength provide reliability and confidence in their performance.
The exceptional bonding strength is essential for applications requiring secure and long-lasting connections. Whether in construction, manufacturing, or everyday products, adhesives with extraordinary bonding strength ensure the integrity and durability of bonded assemblies, contributing to overall product quality and reliability.
High-Temperature Resistance
High-temperature resistance is a crucial characteristic of certain materials and products, especially in applications exposed to elevated temperatures. Here are the key points explaining the significance and factors contributing to high-temperature resistance:
- Material Selection:Materials with high-temperature resistance, such as ceramics, refractory metals, and specific polymers, are chosen for applications that involve exposure to elevated temperatures. These materials possess inherent properties that allow them to withstand thermal stress and maintain their structural integrity under extreme heat.
- Thermal Stability: Materials achieve high-temperature resistance when they exhibit excellent thermal stability. Even at high temperatures, materials with excellent thermal stability maintain their physical and mechanical properties without significant changes in shape, damage, or chemistry.
- Melting Point:The melting point of a material is an essential factor in determining its high-temperature resistance. Materials with high melting points, such as tungsten or certain ceramics, can withstand extreme temperatures without melting or losing their strength.
- Oxidation Resistance:Exposure to high temperatures often involves oxidative environments. Materials with high-temperature resistance exhibit good oxidation resistance, meaning they can resist the harmful effects of oxygen and other reactive gasses at elevated temperatures. Exposure to oxidative conditions can lead to degradation or corrosion of the material. Implementing measures or utilizing materials that resist oxidation is essential to prevent this.
- Thermal Expansion: High-temperature resistance is closely related to the ability of a material to withstand thermal expansion and contraction. Materials with low coefficients of thermal expansion exhibit better resistance to thermal stress, minimizing the risk of cracking or structural failure when exposed to temperature fluctuations.
- Heat Dissipation: High-temperature resistance correlates with efficient heat dissipation in some applications. Materials that can effectively conduct and dissipate heat, such as certain metals or thermal interface materials, contribute to maintaining lower operating temperatures in devices or systems, improving their overall performance and reliability.
- Testing and Certification:Manufacturers often subject materials or products to rigorous testing and certification processes to determine their high-temperature resistance. These tests simulate extreme temperature conditions and evaluate the material’s ability to withstand thermal stress, maintain stability, and meet specific industry standards or requirements.
Chemical Resistance
Chemical resistance is a critical property of certain materials and coatings, allowing them to withstand exposure to various chemicals without undergoing degradation or damage. Here are the key points explaining the significance and factors contributing to chemical resistance:
- Material Selection: Certain materials, such as fluoropolymers (e.g., PTFE), ceramics, or certain metals (e.g., stainless steel), are known for their inherent chemical resistance. Choosing compatible and resistant to specific chemical substances is essential when selecting materials for applications involving contact with chemicals.
- Chemical Inertness: Chemical resistance is often associated with material inertness towards different chemical agents. Inert materials are minimally reactive with chemicals, making them less likely to undergo chemical reactions or degradation when exposed to corrosive or reactive substances.
- Polymerization or Cross-Linking:Some materials, such as epoxies or polyurethanes, can undergo polymerization or cross-linking reactions, forming a dense and chemically resistant network. Industries commonly use these materials as coatings or adhesives in applications that require chemical resistance.
- Barrier Properties: Chemical resistance can also be attributed to a material’s ability to act as a barrier, preventing the permeation or penetration of chemicals. Materials with low permeability, such as glass or certain plastics, can shield the underlying surfaces or substrates from chemical attack.
- Temperature Considerations: Chemical resistance can vary, as certain chemicals may exhibit increased reactivity or aggressiveness at elevated temperatures. Therefore, it is vital to consider the chemical exposure’s temperature range when assessing a material’s chemical resistance.
- Testing and Certification:Manufacturers subject materials or coatings to rigorous testing and certification processes to determine their chemical resistance. These tests typically involve exposing the material to various chemicals, individually and in combinations, and assessing its performance and stability over time. Industry standards or specific requirements guide these testing procedures.
- Compatibility Charts: Chemical compatibility charts or databases are valuable resources for determining the chemical resistance of materials. These references provide information on the compatibility of specific materials with various chemicals, helping engineers and professionals make informed decisions when selecting materials for chemical environments.
Chemical resistance is crucial in industries such as chemical processing, pharmaceuticals, oil and gas, and manufacturing, where materials or coatings come into contact with aggressive or corrosive substances. Materials with excellent chemical resistance ensure the longevity, safety, and performance of equipment, structures, and products, reducing the risk of chemical-induced degradation or failure.
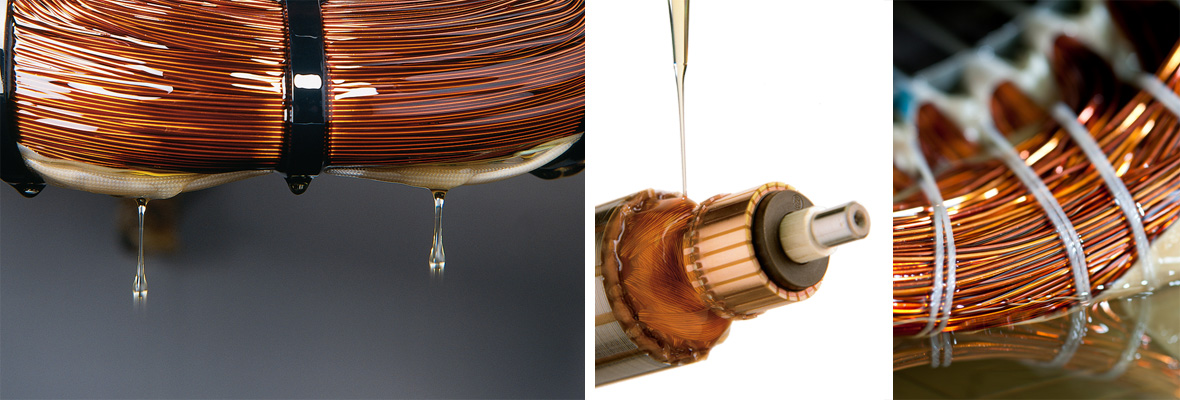
Moisture Resistance
Moisture resistance is a critical property of materials and coatings, enabling them to withstand exposure to moisture or humid environments without undergoing degradation or damage. Here are the key points explaining the significance and factors contributing to moisture resistance:
- Material Selection: Certain materials, such as metals with corrosion-resistant properties (e.g., stainless steel), moisture-resistant polymers (e.g., polyethylene), or moisture-resistant coatings (e.g., epoxy or polyurethane), are specifically chosen for their ability to resist moisture or water intrusion.
- Impermeability: Moisture resistance often involves the ability of a material or coating to act as an impenetrable barrier, preventing the penetration or absorption of water or moisture. Impermeable materials, such as glass or certain plastics, effectively block the passage of water molecules and protect the underlying surfaces or substrates.
- Moisture Vapor Transmission Rate (MVTR): A material’s ability to impede moisture vapor transmission also characterizes its moisture resistance. A low MVTR indicates that the material has a low rate of moisture diffusion, minimizing the passage of water vapor and reducing the potential for moisture-related damage.
- Hydrophobicity: Hydrophobic materials repel or resist the absorption of water. They have a low affinity for water molecules, causing water droplets to bead up and roll off the surface. Hydrophobic coatings or surface treatments enhance moisture resistance by preventing moisture accumulation on the material’s surface.
- Moisture Absorption: Moisture-resistant materials typically have low moisture absorption properties. These materials can only absorb a small amount of water from their surroundings or can only drink water under specific conditions. Low moisture absorption helps maintain the material’s dimensional stability and prevents moisture-induced swelling or warping.
- Testing and Certification: Manufacturers subject materials or coatings to rigorous testing and certification processes to assess their moisture resistance. These tests often involve exposing the material to controlled humidity or water immersion for extended periods and evaluating its performance and stability. Industry standards or specific requirements guide these testing procedures.
- Environmental Considerations:Environmental factors such as temperature, humidity, and the duration of exposure influence the moisture resistance of materials. Materials that exhibit good moisture resistance in one environment may perform differently in another. Materials that exhibit good moisture resistance in one environment may perform differently in another. It is essential to consider the specific moisture conditions the material will encounter during its application or use.
Moisture resistance is essential in various industries and applications, including construction, electronics, packaging, and outdoor equipment. Materials or coatings with excellent moisture resistance ensure the durability, reliability, and longevity of structures, products, and systems, protecting them from moisture-related issues such as corrosion, mold growth, or material degradation.
Versatile Applications
Versatile applications refer to the wide range of uses and adaptability of a product or material across various industries and contexts. Here are the key points explaining the significance and factors contributing to versatile applications:
- Material Flexibility:Versatile materials have various properties that enable them to find applications in diverse fields. They can exhibit strength, flexibility, thermal stability, and chemical resistance characteristics, making them suitable for different environments and requirements.
- Compatibility with Different Substrates:Versatile materials can bond or interact with various substrates, including metals, plastics, ceramics, and composites. This compatibility enables their use in multiple applications, from joining different materials in construction to bonding components in electronics or automotive assemblies.
- Adaptable Formulations:Some materials, such as polymers or adhesives, offer the advantage of being formulated to meet specific requirements or application needs. These materials can be tailored by adjusting their composition, curing process, or additives, allowing them to be used in diverse applications while maintaining their essential properties.
- Wide Temperature Range:Versatile materials can often perform across a wide range. They can maintain their integrity and functionality in extreme hot or cold conditions, making them suitable for aerospace, automotive, or industrial manufacturing applications.
- Multiple Industries: Versatile materials find applications in various industries, including construction, electronics, healthcare, packaging, automotive, and consumer goods. People use them for diverse purposes, such as structural components, insulation, adhesion, sealing, packaging, etc.
- Customization Options:Versatile materials can often be customized or modified to meet specific application requirements. Industries can modify properties like strength, flexibility, color, or surface texture to create customized solutions that meet their needs.
- Advancements in Technology:Technological advancements and material innovations contribute to materials’ versatility and applications. Ongoing research and development efforts lead to introducing new materials with enhanced properties, expanding the possibilities for their utilization.
Versatile materials are vital in driving innovation and facilitating advancements across various industries, enabling creative and efficient solutions to complex challenges.
Types of Electric Motor Epoxy Adhesive
Electric motor epoxy adhesive is available in different types, each offering specific properties and characteristics tailored to meet the requirements of electric motor applications. Here are the key types of electric motor epoxy adhesive:
- Heat-Resistant Epoxy Adhesive: We have designed this epoxy adhesive formulation to withstand the high temperatures generated during motor operation. It maintains its bonding strength and structural integrity even under extreme thermal conditions, making it suitable for applications where elevated temperature resistance is essential.
- Electrical Insulating Epoxy Adhesive:We design electric motor epoxy adhesive with electrical insulating properties to provide adequate insulation between motor components. It prevents the passage of electrical current through the bonded area, reducing the risk of electrical shorts and ensuring the safe and reliable operation of electric motors.
- Fast-Curing Epoxy Adhesive: We formulate fast-curing epoxy adhesives for a short curing time, enabling quick assembly and repair of electric motor components. This type of adhesive is advantageous in high-volume production environments or situations that require rapid turnaround times.
- High-Strength Epoxy Adhesive:High-strength epoxy adhesive offers exceptional bonding capabilities, providing a solid and durable bond between motor components. It withstands mechanical stresses, vibrations, and shocks encountered during motor operation, ensuring the long-term stability and reliability of the motor assembly.
- Chemical-Resistant Epoxy Adhesive:We design electric motor epoxy adhesive with chemical resistance to withstand exposure to various chemicals, solvents, oils, and fuels commonly found in motor environments. It maintains its adhesive properties and structural integrity, even when in contact with aggressive substances.
- Low-Outgassing Epoxy Adhesive: Low-outgassing epoxy adhesive releases minimal amounts of volatile substances when exposed to heat or vacuum. Electric motors commonly use this type of adhesive in vacuum environments or applications where the outgassing of volatile compounds could cause performance issues.
- Flexible Epoxy Adhesive: Flexible epoxy adhesive offers good flexibility and elasticity, allowing for the absorption of vibrations and thermal expansion/contraction in electric motor components. This flexibility helps prevent bond failure or cracking under dynamic conditions, contributing to the overall durability and reliability of the motor assembly.
These electric motor epoxy adhesive types provide a range of options to suit different motor designs, operating conditions, and specific application requirements. Manufacturers can select the appropriate variety of adhesives based on factors such as temperature range, electrical insulation needs, bonding strength, chemical exposure, and flexibility, ensuring optimal performance and longevity of electric motors.
Two-Part Epoxy Adhesive
The two-part epoxy adhesive requires the user to mix two components, a resin, and a hardener, in specific ratios before use. Here are the key points explaining the characteristics and advantages of two-part epoxy adhesive:
- Mixing and Curing: Two-part epoxy adhesives require thoroughly mixing the resin and hardener components to initiate the curing process. Once mixed, the bond starts to cure, typically through an exothermic reaction, transforming from a liquid or paste into a solid. The curing time can vary depending on the specific adhesive formulation and environmental conditions.
- Versatility: Two-part epoxy adhesives offer versatility in bonding various materials, including metals, plastics, composites, ceramics, and more. They can create strong and durable bonds between dissimilar materials, making them suitable for various applications.
- Bond Strength: Two-part epoxy adhesives are known for their exceptional bond strength. They form molecular-level solid interactions with the substrate, providing reliable and long-lasting adhesion. The cured adhesive exhibits high tensile, shear, and peel forces, ensuring the integrity of bonded assemblies.
- Gap Filling: Two-part epoxy adhesives have excellent gap-filling capabilities. They can fill and bond irregular or uneven surfaces, compensating for small gaps or surface imperfections. This property is beneficial when joining parts with varying shapes or sizes.
- Temperature Resistance: Two-part epoxy adhesives exhibit good temperature resistance, maintaining their bond strength even at elevated temperatures. Depending on the specific formulation, they can withstand a wide range of temperatures, making them suitable for applications in high-temperature environments.
- Chemical and Moisture Resistance: Two-part epoxy adhesives resist various chemicals, including solvents, fuels, and oils, as well as moisture and humidity. This resistance helps protect the bond from degradation or weakening when exposed to harsh environments or chemical substances.
- Application Versatility: Two-part epoxy adhesives can be applied using various methods, such as manual mixing, automated dispensing, or injection. They can be used for bonding, sealing, potting, encapsulation, or coating applications, making them suitable for diverse industries, including automotive, electronics, aerospace, and construction.
Two-part epoxy adhesives offer robust, durable, and versatile bonding solutions for various applications. Their ability to create high-strength bonds, fill gaps, and withstand challenging environments makes them a preferred choice in many industries requiring reliable and long-lasting adhesion.
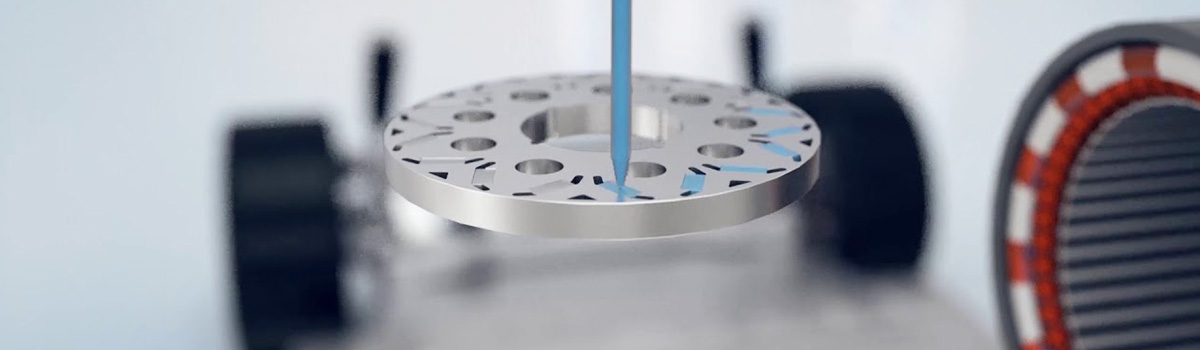
One-Part Epoxy Adhesive
One-part epoxy adhesive is a type of adhesive that comes pre-mixed and ready to use without additional components or mixing. Here are the key points explaining the characteristics and advantages of one-part epoxy adhesive:
- Convenience: One-part epoxy adhesive offers comfort and ease of use since it does not require mixing or measuring. The bond is pre-formulated and ready to apply directly from the container, saving time and effort in preparation.
- Instant Adhesion: One-part epoxy adhesives offer fast initial adhesion. They typically have a short open time, allowing for quick positioning and assembly of parts. Once applied, the glue starts to bond immediately, providing instant tack and initial strength.
- Long Shelf Life: One-part epoxy adhesives have a longer shelf life than two-part epoxy adhesives. They can remain stable and usable for an extended period without the risk of premature curing or degradation, offering flexibility in storage and usage.
- Heat Activation: Some one-part epoxy adhesives require heat activation to achieve complete cure and optimal bond strength. We design these adhesives to cure at elevated temperatures, providing enhanced performance and durability in high-temperature applications.
- Versatility: One-part epoxy adhesives can bond with various materials, including metals, plastics, ceramics, and composites. They offer versatility in applications requiring strong and durable bonds, such as automotive, electronics, construction, and manufacturing.
- Chemical and Moisture Resistance:One-part epoxy adhesives exhibit good resistance to chemicals, including solvents, fuels, and oils, as well as moisture and humidity. This resistance helps protect the bond from degradation or weakening when exposed to harsh environments or chemical substances.
- Application Flexibility: You can apply one-part epoxy adhesives using various methods, including manual dispensing, brush application, or automated systems. They can be used for bonding, sealing, potting, encapsulation, or coating applications, offering flexibility in different manufacturing processes.
One-part epoxy adhesives provide a convenient and efficient solution for bonding applications. Their ease of use, instant adhesion, and versatility suit various industries and applications. Whether for assembly, repairs, or sealing, one-part epoxy adhesives offer reliable adhesion and performance while simplifying the bonding process.
Fast-Curing Epoxy Adhesive
Fast-curing epoxy adhesive is a type of adhesive that offers accelerated curing times, allowing for rapid bonding and assembly of components. Here are the key points explaining the characteristics and advantages of fast-curing epoxy adhesive:
- Rapid Curing:Fast-curing epoxy adhesives have a significantly reduced curing time compared to standard epoxy adhesives. Depending on the specific formulation and environmental conditions, we design them to cure quickly, often within minutes or even seconds. This rapid curing enables faster production processes, increased productivity, and reduced assembly or bonding cycle times.
- Instant Strength:Fast-curing epoxy adhesives provide rapid development of initial bond strength. They offer instant tack and adhesion, allowing for immediate handling or further processing of the bonded parts. This rapid strength development minimizes the need for clamping or fixturing, saving time and improving efficiency.
- High Bond Strength: Despite their fast-curing nature, fast-curing epoxy adhesives still deliver high bond strength. They form strong and durable bonds that can withstand the stresses and loads encountered in various applications. The cured sealant provides excellent tensile, shear, and peel strength, ensuring the integrity and reliability of the bonded assemblies.
- Versatility:Fast-curing epoxy adhesives can bond with various materials, including metals, plastics, ceramics, composites, and more. They offer versatility in applications requiring rapid assembly, repairs, or bonding. The automotive, electronics, aerospace, and manufacturing industries commonly use these adhesives.
- Temperature Resistance:Fast-curing epoxy adhesives often exhibit good temperature resistance. They can maintain their bond strength and performance over various temperatures, ensuring reliable adhesion in low- and high-temperature environments.
- Chemical and Moisture Resistance: Fast-curing epoxy adhesives resist various chemicals, including solvents, fuels, oils, and moisture. This resistance helps protect the bond from degradation or weakening when exposed to harsh environments or chemical substances.
- Application Flexibility:Various methods, such as manual dispensing, automated systems, or dispensing equipment, enable the application of fast-curing epoxy adhesives. They can be used for bonding, sealing, potting, or encapsulation applications, offering flexibility in different manufacturing processes.
Fast-curing epoxy adhesives offer significant advantages in applications where time is critical. By reducing production cycle times and improving efficiency, fast-curing epoxy adhesives increase productivity and cost savings in various industries.
High-Temperature Epoxy Adhesive
Designers create high-temperature epoxy adhesive to withstand elevated temperatures without compromising its bonding properties or integrity. Here are the key points explaining the characteristics and advantages of high-temperature epoxy adhesive:
- Temperature Resistance: High-temperature epoxy adhesive manufacturers design products to maintain bond strength and structural integrity at elevated temperatures. They can withstand extreme heat without softening, degrading, or losing their adhesion properties. These adhesives can operate in temperature ranges typically exceeding 150°C (300°F) and can go up to 300°C (572°F) or higher, depending on the specific formulation.
- Thermal Stability: High-temperature epoxy adhesives exhibit excellent thermal stability, meaning they do not undergo significant changes in physical or chemical properties when exposed to heat. They can maintain their dimensional stability, hardness, strength, and flexibility even under prolonged high-temperature conditions.
- Bond Strength: High-temperature epoxy adhesives offer exceptional bond strength, allowing for reliable bonding of materials subjected to extreme thermal stress. They create strong and durable bonds that can withstand thermal expansion, contraction, and cyclic heating and cooling without compromising the integrity of the bonded assembly.
- Versatility:High-temperature epoxy adhesives can bond with various materials, including metals, ceramics, glass, composites, and plastics. They find applications in automotive, aerospace, electronics, and manufacturing industries, requiring reliable adhesion in high-temperature environments.
- Chemical Resistance:High-temperature epoxy adhesives often resist various chemicals, including solvents, fuels, oils, and some acids. This chemical resistance ensures the stability and durability of the bond even when exposed to harsh chemical environments and high temperatures.
- Application Flexibility: You can apply high-temperature epoxy adhesives using various methods, such as manual dispensing, automated systems, or dispensing equipment. They can be used for bonding, sealing, potting, or encapsulation applications, offering flexibility in different manufacturing processes.
High-temperature epoxy adhesives are critical in applications where bonding materials subjected to extreme heat are necessary. Their ability to withstand high temperatures while maintaining bond strength and stability makes them suitable for demanding environments.
Low Outgassing Epoxy Adhesive
Low-outgassing epoxy adhesive is a specialized type formulated to minimize or eliminate the release of volatile substances, known as outgassing, during and after the curing process. Here are the key points explaining the characteristics and advantages of low-outgassing epoxy adhesive:
- Outgassing Reduction:Designers create low-outgassing epoxy adhesives to minimize the levels of volatile compounds that can escape from the bond after application. This characteristic is especially crucial in applications where outgassing can cause contamination or affect the performance of sensitive components, such as in aerospace, optics, or electronics.
- Low Volatile Content: Low outgassing epoxy adhesives have a low volatile content, which contains reduced substances that can evaporate or off-gas. Low-outgassing epoxy adhesives protect nearby components from potential damage and keep sensitive environments free from contamination by preventing the release of harmful or reactive compounds.
- Compatibility with Delicate Materials:Manufacturers often formulate low-outgassing epoxy adhesives to ensure compatibility with delicate or sensitive materials. They minimize the risk of causing damage or adverse reactions when bonded to materials such as optics, sensors, electronic components, or precision instruments.
- High Bond Strength: Despite their low outgassing properties, these adhesives still provide high bond strength. They create strong and durable bonds that can withstand the stresses and loads encountered in various applications. The cured adhesive exhibits excellent tensile, shear, and peel strength, ensuring reliable adhesion.
- Thermal and Chemical Resistance: Low-outgassing epoxy adhesives typically offer good thermal and chemical resistance. They can withstand temperatures and resist various chemicals, including solvents, fuels, and oils, without compromising their low outgassing properties.
- Application Flexibility:You can apply low-outgassing epoxy adhesives using various methods, such as manual dispensing, automated systems, or dispensing equipment. They can be used for bonding, sealing, potting, or encapsulation applications, offering flexibility in different manufacturing processes.
Factors to Consider When Selecting Electric Motor Epoxy Adhesive
When selecting an electric motor epoxy adhesive to ensure optimal performance and compatibility with the specific application requirements, it is essential to consider several factors. Here are the key factors to consider:
- Temperature Resistance: Evaluate the temperature range the adhesive needs to withstand within the electric motor. Consider the operating temperature and potential temperature spikes during motor operation or nearby heat sources.
- Bonding Strength: Determine the required bond strength for the intended application. Consider the stresses, loads, and vibrations the adhesive must withstand to ensure a durable and reliable bond.
- Substrate Compatibility: Assess the materials to be bonded, such as metals, plastics, composites, or ceramics, and make sure to check the compatibility of the adhesive with those substrates. Some adhesives may require surface preparation or primers for optimal bonding.
- Electrical Insulation Properties:Electric motor epoxy adhesive should provide insulation to prevent electrical current leakage or short circuits. Verify that the bond has suitable dielectric properties to meet the electrical insulation requirements.
- Chemical Resistance:When evaluating the adhesive for use within the motor, it is essential to consider the chemical environment it will be exposed. Evaluate its resistance to oils, fuels, solvents, and other chemicals that may be present, ensuring the bond maintains its performance and integrity.
- Curing Time:Determine the desired curing time for the specific application. Some adhesives offer rapid curing for faster assembly or repair processes, while others may require longer curing times for precise alignment or complex bonding requirements.
- Application Method: Consider the application method that best suits the manufacturing process. Determine if the proper application requires manual dispensing, automated systems, or specific equipment.
- Environmental Considerations: Assess any ecological regulations or restrictions that may apply to the adhesive, such as VOC (volatile organic compound) content or compliance with specific industry standards.
- Shelf Life and Storage Conditions:Verify the adhesive’s shelf life and recommended storage conditions to ensure its stability and usability over time. Some bonds may require specific temperature or humidity conditions for storage.
By carefully considering these factors, one can select the most suitable electric motor epoxy adhesive that meets the specific performance requirements, ensuring optimal bonding, durability, and reliability within electric motors.
Compatibility with Motor Components
When selecting an electric motor epoxy adhesive, compatibility with motor components is an essential factor to consider. The glue should not cause any degradation or damage to the motor components, such as insulation materials, magnets, coils, or bearings. Here are some key considerations for ensuring compatibility:
- Insulation Materials: The adhesive should not degrade or weaken the insulation materials used within the motor, such as varnishes or resins. Verify the glue has appropriate electrical insulation properties to prevent electrical current leakage or short circuits.
- Magnets and Coils: The adhesive should not interfere with the magnetic or electrical properties of the attractions or coils within the motor. Verify that the bond has suitable magnetic permeability and dielectric properties to maintain the motor’s performance.
- Bearings and Shafts:The adhesive should not affect the rotation or movement of the motor’s bearings or shafts. Consider the adhesive’s viscosity, flow properties, and resistance to wear and tear to ensure it does not interfere with the motor’s movement.
- Heat Dissipation: The adhesive should not hinder the motor’s heat dissipation process. Consider the adhesive’s thermal conductivity properties to ensure it does not impede the motor’s ability to dissipate heat and maintain optimal operating temperatures.
- Corrosion Protection: The adhesive should provide corrosion protection to the motor components. Verify that the bond has suitable corrosion resistance properties to prevent rust, oxidation, or other forms of corrosion that may affect the motor’s performance.
By ensuring compatibility with motor components, the electric motor epoxy adhesive can provide optimal bonding, durability, and reliability while maintaining the motor’s performance and integrity.
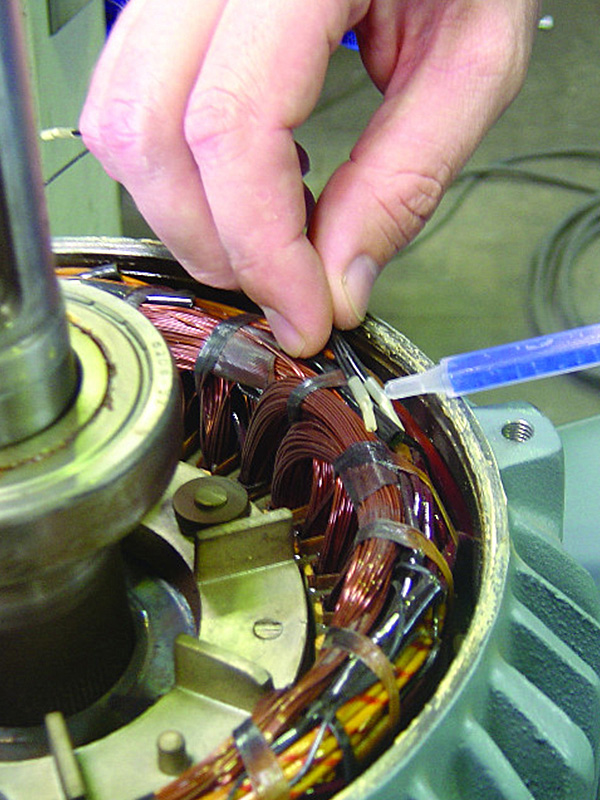
Cure Time
Cure time is a crucial factor to consider when selecting an electric motor epoxy adhesive. It refers to the duration required for the bond to reach its full strength and bonding properties after application. Here are some key points to consider regarding cure time:
- Open Time:Open time refers to when the adhesive can be positioned or adjusted before it starts to cure, remaining workable. Evaluate the desired available time based on the specific application requirements, allowing enough time for proper alignment and assembly of motor components.
- Curing Speed: Consider the desired curing speed of the adhesive. Some adhesives offer fast-curing properties, enabling rapid bonding and reducing assembly time. Others may require longer curing times to achieve optimal bond strength or allow for additional processing steps.
- Ambient Conditions: Ambient conditions such as temperature and humidity can influence the cure time of an epoxy adhesive. Consider the recommended curing conditions the manufacturer provides and ensure they are compatible with the manufacturing environment.
- Acceleration Methods:Depending on the application requirements, it may be necessary to accelerate the cure time of the adhesive. Some epoxy adhesives can be heat activated or can benefit from using accelerators or curing agents to speed up the curing process.
- Pot Life:Pot life refers to the time window during which the adhesive remains usable after it has been mixed or exposed to air. Evaluate the pot life of the epoxy adhesive to ensure it is sufficient for the application process, considering factors such as mixing, dispensing, and application time.
- Post-Cure:Some epoxy adhesives may require a post-cure process to achieve maximum bond strength and desired properties. Consider if post-curing is necessary and the recommended duration or conditions for the post-cure process.
By considering the cure time and its related factors, one can select an electric motor epoxy adhesive that aligns with the application’s specific requirements. Properly assessing the available time, curing speed, ambient conditions, acceleration methods, pot life, and potential post-cure requirements ensures efficient and effective bonding of motor components while meeting production timelines.
Temperature Requirements
Temperature requirements are critical considerations when selecting an electric motor epoxy adhesive. The adhesive must withstand the operating temperatures of the motor without compromising its performance, integrity, or bond strength. Here are some key points to consider regarding temperature requirements:
- Operating Temperature Range:Evaluate the anticipated operating temperature range of the electric motor. Consider the average operating temperature and any potential temperature spikes or fluctuations during motor operation. The adhesive should maintain its bond strength and stability within this temperature range.
- Thermal Stability: Assess the thermal stability of the epoxy adhesive. It should withstand elevated temperatures without softening, melting, or degrading. Please verify that the adhesive retains its physical and chemical properties, such as hardness, flexibility, and adhesion strength, even when exposed to the specified operating temperature range.
- Temperature Resistance: The adhesive should exhibit high-temperature resistance, allowing it to perform reliably in demanding conditions. Ensure that the selected adhesive can withstand the maximum operating temperature of the motor without experiencing any adverse effects on its bond strength or structural integrity.
- Thermal Cycling: Electric motors often undergo thermal cycling, which involves repeated heating and cooling cycles. The adhesive should withstand thermal expansion and contraction during these cycles without compromising the bond between motor components.
- Heat Dissipation:Consider the adhesive’s impact on the motor’s heat dissipation process. It should not impede the transfer of heat generated by the engine. Verify that the bond has suitable thermal conductivity properties, allowing efficient heat dissipation and preventing overheating of critical components.
- Cold Temperature Performance:In addition to high temperatures, consider the performance of the adhesive in cold environments. The adhesive should retain its bond strength and flexibility at low temperatures, ensuring reliable performance even in sub-zero conditions.
- Temperature Testing: It is advisable to conduct temperature testing or consult the adhesive manufacturer’s specifications to verify its suitability for the anticipated temperature requirements. Look for relevant performance data, such as temperature resistance, thermal stability, and other temperature-related properties.
Safety Considerations
Safety considerations are of utmost importance when working with electric motor epoxy adhesives. Here are some key points to consider for ensuring safety during adhesive selection and application:
- Material Safety Data Sheets (MSDS): Obtain and review the Material Safety Data Sheets provided by the adhesive manufacturer. These documents contain important safety information, including hazards, handling precautions, and recommended personal protective equipment (PPE).
- Hazardous Substances: Identify dangerous substances in the adhesive formulation, such as volatile organic compounds (VOCs) or other potentially harmful chemicals. Assess the health risks of these substances and ensure proper ventilation and protective measures are in place.
- Personal Protective Equipment (PPE):Follow the recommendations outlined in the MSDS regarding using PPE, such as gloves, safety glasses, or respiratory protection. Ensure that personnel involved in the adhesive application process receive adequate PPE.
- Ventilation:Ensure the workspace has proper ventilation to minimize exposure to potentially harmful fumes or vapors. If necessary, use local exhaust ventilation or perform adhesive application in a well-ventilated area to prevent the buildup of airborne contaminants.
- Skin Contact:Take precautions to avoid direct skin contact with the adhesive. Use gloves and other protective clothing as the adhesive manufacturer recommends to prevent skin irritation or sensitization.
- Eye Protection:Wear safety glasses or goggles to protect the eyes from accidental splashes or contact with the adhesive. In case of eye exposure, immediately flush with clean water and seek medical attention if necessary.
- Handling and Storage: Follow the adhesive manufacturer’s proper handling and storage procedures. Store the adhesive by recommended temperature and humidity conditions, away from ignition sources or incompatible materials.
- Emergency Preparedness:Be prepared for potential emergencies. Have appropriate spill response measures, such as absorbent materials and spill kits, readily available. Educate personnel on emergency procedures, including first aid measures and reporting incidents.
- Regulatory Compliance: Ensure compliance with applicable safety regulations, such as Occupational Safety and Health Administration (OSHA) standards or local regulatory requirements. Stay updated on any regulatory changes or guidelines related to using epoxy adhesives.
- Training and Education: Provide adequate training and education to personnel involved in the adhesive application process. Ensure they know the potential hazards, safe handling practices, and emergency procedures associated with the adhesive.
By considering these safety considerations, implementing proper handling procedures, and adhering to relevant safety guidelines, one can minimize risks associated with electric motor epoxy adhesive use and create a safer working environment for personnel involved in the application process.
Application Techniques
The application technique is crucial in achieving optimal bonding and ensuring the adhesive’s effectiveness when working with electric motor epoxy adhesive. Here are some key points to consider when selecting and implementing application techniques:
- Dispensing Method: Select the most suitable method based on the specific adhesive formulation and the application’s requirements. Standard techniques include manual dispensing using syringes or cartridges, automated dispensing systems, or meter-mix-dispense equipment for two-component adhesives.
- Mixing: For two-component epoxy adhesives, thoroughly mix the resin and hardener components according to the manufacturer’s instructions. Follow the recommended mixing ratios and techniques to achieve a homogenous mixture.
- Surface Preparation:Proper surface preparation is crucial for achieving solid adhesive bonds. Thoroughly clean and degrease the characters that will be bonded to remove contaminants that may hinder adhesion. Abrade the surfaces if necessary to promote mechanical interlocking and improve bonding.
- Application Tools: Use appropriate tools such as brushes, spatulas, or precision dispensing tips, depending on the nature of the adhesive and the application requirements. Ensure the tools are clean and compatible with the adhesive to prevent any adverse effects on its performance.
- Coverage and Thickness: Apply the adhesive in the recommended range and thickness to ensure proper bonding. Follow the manufacturer’s guidelines regarding the bond required per unit area and the recommended thickness for optimal performance.
- Bond Line Control: Maintain control over the bond line thickness during adhesive application. Use spacers, shims, or other appropriate techniques to achieve consistent and uniform bond line thickness across the bonded surfaces.
- Clamping or Fixturing:Depending on the adhesive and application, clamping or fixturing may be necessary to hold the components in place during the curing process. Follow the recommended clamping pressure and duration to ensure an even pressure distribution and prevent movement that could compromise the bond.
- Curing Conditions: Create the ideal curing conditions for the adhesive. Consider factors such as temperature, humidity, and curing time specified by the adhesive manufacturer. Ensure the curing environment remains consistent and appropriate for the bond to achieve its full strength and performance.
- Quality Control:Implement quality control measures throughout the adhesive application process. Regularly inspect the adhesive bonds to ensure proper coverage, thickness, and integrity. Conduct adhesion tests or other appropriate quality control checks to verify the bond strength and performance.
By considering these application techniques, following manufacturer guidelines, and maintaining consistent quality control measures, one can optimize electric motor epoxy adhesive, ensuring reliable bonding, durability, and overall performance within electric motor applications.
Conclusion
Electric motor epoxy adhesive is a specialized adhesive that is essential for bonding and protecting the components of an electric motor. It provides exceptional bonding strength, high-temperature, chemical, and moisture resistance. The type of adhesive chosen will depend on several factors, including compatibility with motor components, cure time, temperature requirements, and safety considerations. By selecting the suitable electric motor epoxy adhesive and following proper application techniques, you can ensure a reliable and long-lasting bond that withstands the rigorous conditions of an electric motor.