FPC Bonding Adhesive
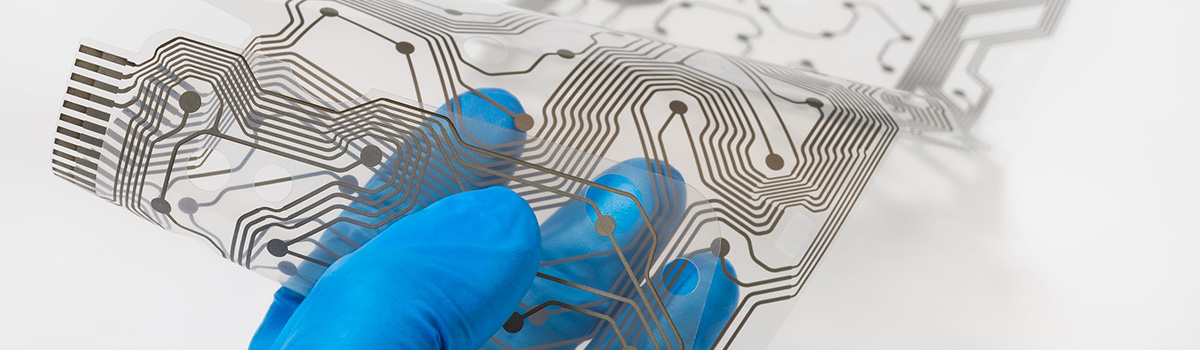
FPC bonding adhesive is a crucial component in the manufacturing and assembly of flexible printed circuit (FPC) boards, which are widely used in various electronic devices, including smartphones, wearables, and automotive applications. These adhesives provide strong bonding capabilities, electrical insulation, and protection against environmental factors while ensuring the flexibility and durability of FPC boards. As the demand for flexible and reliable electronic devices grows, the importance of high-performance and reliable FPC bonding adhesives has become more critical. This article will explore the various types, applications, and challenges of FPC bonding adhesives, highlighting their crucial role in enabling flexibility and reliability in electronic devices.
Types of FPC Bonding Adhesive
FPC (Flexible Printed Circuit) bonding adhesives are essential for assembling and connecting flexible circuits in various electronic devices. These adhesives ensure a reliable and durable bond between the flexible circuit and the target substrate. Several types of FPC bonding adhesives are available in the market, each with unique characteristics and applications. This response will provide an overview of some common types of FPC bonding adhesives.
- Acrylic-based Adhesives: Acrylic-based bonding adhesives are popular due to their excellent adhesion to various substrates, including metals, plastics, and glass. They offer flexibility, thermal stability, and resistance to moisture and chemicals. Acrylic adhesives are available in various forms, such as tapes, films, and liquid adhesives, making them versatile for different FPC bonding applications.
- Epoxy-based Adhesives: Epoxy-based adhesives provide high bond strength and are widely used for FPC bonding. They offer excellent adhesion to various substrates and provide good electrical insulation properties. Epoxy adhesives are available in different formulations, including one-component and two-component systems, providing options for multiple bonding processes and curing conditions.
- Silicone-based Adhesives: Silicone-based adhesives are known for their flexibility, high-temperature resistance, and excellent electrical insulation properties. They can withstand extreme temperatures and provide good resistance to moisture, making them suitable for demanding environments. Silicone adhesives are commonly used in applications with critical thermal management and reliability.
- Pressure-sensitive Adhesives (PSAs): PSAs are adhesive materials that form an instant bond when pressure is applied. They eliminate the need for other curing processes, making them convenient for FPC bonding applications. PSAs offer good adhesion to various substrates and can be easily removed without leaving residue, making them ideal for temporary bonding or rework.
- UV-curable Adhesives: UV-curable adhesives are liquid adhesives that cure rapidly when exposed to ultraviolet light. They offer fast curing times, high bond strength, and excellent adhesion to different substrates. UV-curable adhesives are commonly used in FPC bonding applications where quick assembly and increased productivity are required.
- Conductive Adhesives: Conductive adhesives are specially formulated for bonding and electrical conductivity. They contain conductive fillers, such as silver or carbon, that allow the adhesive to establish electrical connections between circuit components. Conductive adhesives are widely used in FPC bonding for applications like EMI shielding, grounding, and electrical interconnections.
- Thermally Conductive Adhesives: Thermally conductive adhesives are designed to provide both bonding and efficient heat transfer properties. They are used in FPC bonding applications where thermal management is critical, such as bonding flexible circuits to heat sinks or other thermally conductive substrates.
It’s important to note that choosing an FPC bonding adhesive depends on various factors, including the specific application requirements, substrate materials, environmental conditions, and manufacturing processes. Consulting adhesive manufacturers or suppliers can provide more detailed information and guidance on selecting the most suitable adhesive for a specific FPC bonding application.
Acrylic Adhesives: The Most Common Choice
Acrylic adhesives are popular in various industries due to their versatility, strong bonding capabilities, and ease of use. These adhesives are composed of acrylic polymers, which provide excellent adhesion to a wide range of substrates. Here, we will explore why acrylic adhesives are the most common choice within 450 words.
One of the critical advantages of acrylic adhesives is their ability to bond different materials together. Acrylic adhesives can create durable and reliable bonds, whether bonding plastics, metals, ceramics, wood, or even glass. This versatility makes them suitable for various automotive, construction, electronics, and signage applications.
Acrylic adhesives also offer excellent bonding strength and can form strong bonds that withstand high stress, temperature variations, and environmental conditions. This makes them ideal for applications where durability and long-term performance are crucial.
Another reason for the popularity of acrylic adhesives is their fast curing time. Compared to other adhesive types, acrylic adhesives have relatively short curing times, allowing for faster production cycles. They can often achieve handling strength in minutes, reducing assembly time and increasing productivity.
Furthermore, acrylic adhesives are known for resisting moisture, chemicals, and UV radiation. They have excellent water resistance and can maintain their adhesive properties even in wet environments. This characteristic makes them suitable for outdoor applications and environments where exposure to harsh conditions is expected.
Acrylic adhesives also provide excellent thermal stability. They can withstand a wide temperature range, from extreme cold to high heat, without compromising their bonding strength. This thermal resistance makes them suitable for applications where temperature fluctuations are common, such as in the automotive and electronics industries.
In addition to their physical properties, acrylic adhesives are easy to handle and apply. They are available in various forms, including liquids, pastes, films, and tapes, offering flexibility in application methods. They can be applied using automated dispensing systems or manually, depending on the application’s specific requirements.
Moreover, acrylic adhesives are generally odorless and have low volatile organic compound (VOC) content. This makes them safer than solvent-based adhesives, which may emit strong odors or contain harmful chemicals.
Silicone Adhesives: Superior Environmental Resistance
Silicone adhesives are a class of adhesives known for their superior environmental resistance. They offer exceptional performance and durability in various applications, making them highly sought after in the automotive, electronics, aerospace, construction, and medical industries.
One of the critical advantages of silicone adhesives is their ability to withstand extreme temperatures. They can resist high and low temperatures without losing their adhesive properties or becoming brittle. This makes them suitable for applications where temperature fluctuations are common, such as in automotive engines or electronic devices.
Silicone adhesives also exhibit excellent resistance to moisture and water. Unlike many other adhesive types, they can maintain strength and integrity even when exposed to water or humid environments. This property is crucial in applications requiring water resistance, such as sealing gaskets, bonding underwater components, or protecting electronic circuits from moisture damage.
Furthermore, silicone adhesives offer exceptional resistance to UV radiation and weathering. They can withstand prolonged exposure to sunlight, rain, snow, and other environmental factors without degrading or losing their adhesive properties. This makes them ideal for outdoor applications, such as sealing outdoor signage, bonding solar panels, or protecting outdoor electronic devices.
Chemical resistance is another area where silicone adhesives excel. They can resist various chemicals, including solvents, oils, fuels, and acids. This resistance is significant in industries such as automotive and aerospace, where exposure to multiple chemicals is daily. Even in aggressive chemicals, silicone adhesives can maintain their integrity and adhesion, ensuring long-term performance and reliability.
In addition to their environmental resistance, silicone adhesives offer excellent electrical insulation properties. They have a high dielectric strength and can provide insulation against electrical currents. This makes them ideal for bonding and sealing electronic components, where electrical isolation and protection are crucial.
Silicone adhesives are available in various forms, including one-part or two-part systems, as well as different curing mechanisms like heat cure, moisture cure, or UV cure. This versatility allows for a wide range of applications and bonding requirements.
It is worth noting that while silicone adhesives offer exceptional environmental resistance, they may not have the same high initial bond strength as some other adhesive types. However, they compensate for this with their flexibility, durability, and long-term performance in harsh conditions.
UV Curing Adhesives: Rapid and Precise Bonding
UV-curing adhesives, also known as ultraviolet-curable adhesives, have gained significant popularity in various industries due to their ability to provide rapid and precise bonding. These adhesives offer numerous advantages over traditional adhesive systems, making them a preferred choice for applications that require fast and reliable adhesion.
UV-curing adhesives are formulated with special photoinitiators that initiate the process when exposed to ultraviolet light. The curing reaction occurs almost instantaneously, allowing for rapid bond formation. Unlike conventional adhesives that use heat or chemical reactions to cure, UV-curing adhesives provide a virtually instant bond, saving valuable production time and increasing efficiency.
One of the critical advantages of UV-curing adhesives is their precise bonding capability. The curing reaction is highly controlled and localized, ensuring the adhesive only cures in the desired area. This enables precise positioning and alignment of components, even in complex assemblies. Manufacturers can achieve tight tolerances and maintain high product quality using UV-curing adhesives.
The fast curing time of UV adhesives is particularly advantageous in industries where quick production turnaround is crucial. For example, in electronics manufacturing, UV-curing adhesives allow for the rapid bonding of components, reducing assembly time and increasing productivity. Similarly, in the medical device industry, UV adhesives provide fast and reliable bonding of various materials, enabling quick assembly of intricate medical devices.
UV-curing adhesives offer excellent bond strength and durability. Once cured, these adhesives form strong bonds that withstand various environmental conditions, including temperature fluctuations, moisture, and chemicals. The bonds exhibit high resistance to yellowing or degradation over time, ensuring long-term performance and reliability.
UV-curing adhesives are versatile and compatible with various substrates, including plastics, metals, glass, and ceramics. They can bond dissimilar materials together, expanding the range of applications where they can be used. From clicking plastic components in the automotive industry to assembling electronic devices, UV-curing adhesives offer a reliable solution for diverse bonding needs.
Moreover, UV-curing adhesives are solvent-free, eliminating the need for volatile organic compounds (VOCs) and reducing environmental impact. They also offer health and safety benefits by minimizing exposure to hazardous chemicals. The absence of solvents and VOCs contributes to a cleaner and healthier working environment for operators.
Epoxy Adhesives: High Bond Strength and Chemical Resistance
Epoxy adhesives are popular in various industries due to their high bond strength and excellent chemical resistance properties. They offer numerous advantages over other adhesive options, making them versatile and reliable for multiple applications.
One of the critical benefits of epoxy adhesives is their exceptional bond strength. They create powerful bonds that can withstand significant stress and load when properly applied, making them suitable for applications requiring a durable and long-lasting bond. Epoxy adhesives can bond different materials, including metals, plastics, ceramics, glass, and composites, providing a reliable joining solution for various industries.
In addition to their high bond strength, epoxy adhesives exhibit excellent chemical resistance. They can withstand various chemicals, including solvents, acids, bases, oils, and fuels. This resistance to chemical attack ensures that the adhesive remains stable and maintains its bond strength even in harsh environments. Consequently, epoxy adhesives are commonly used in automotive, aerospace, electronics, and chemical processing industries, where exposure to chemicals is a concern.
The chemical resistance of epoxy adhesives is attributed to their unique molecular structure. Epoxy adhesives consist of a resin and a hardener that react chemically to form a crosslinked network. This crosslinked structure provides the adhesive with its strength and resistance to chemicals. The curing process of epoxy adhesives can be adjusted to achieve different levels of chemical resistance, allowing for customization based on specific application requirements.
Furthermore, epoxy adhesives offer excellent temperature resistance, another crucial factor in many industries. They can maintain their bond strength and integrity at high and low temperatures, making them suitable for applications exposed to extreme temperature variations. This property is fundamental in industries such as aerospace and automotive, where components may experience significant temperature fluctuations.
Another advantage of epoxy adhesives is their versatility in terms of application methods. Various techniques, including manual dispensing, syringe dispensing, spray application, and automated dispensing systems, can apply them. This flexibility in application methods enables efficient and precise bonding in different production environments.
It is important to note that proper surface preparation and adhesive application techniques are essential for achieving optimal bond strength and chemical resistance with epoxy adhesives. Surfaces should be clean, dry, and contaminant-free to ensure maximum adhesion. Additionally, the adhesive should be mixed according to the manufacturer’s instructions, considering the correct ratio of resin to hardener and appropriate curing conditions.
In conclusion, epoxy adhesives offer high bond strength and excellent chemical resistance, making them an ideal choice for various applications. Their ability to bond different materials, withstand harsh chemicals, and perform well under extreme temperatures makes them indispensable in the automotive, aerospace, electronics, and chemical processing industries. With proper surface preparation and application techniques, epoxy adhesives can provide durable and reliable bonds, contributing to the overall performance and longevity of the assembled components.
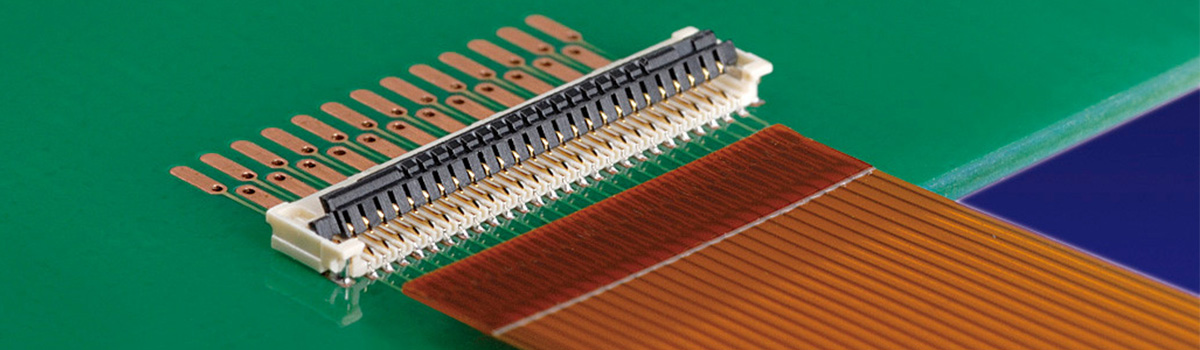
Conductive Adhesives: Enabling Electrical Connectivity
Conductive adhesives play a crucial role in enabling electrical connectivity in various applications. These innovative materials provide an effective alternative to traditional soldering or mechanical fastening methods by offering excellent electrical conductivity, ease of use, and versatility. This article will explore the key features and applications of conductive adhesives.
Conductive adhesives are formulated using a combination of conductive fillers, such as silver, copper, or carbon, and a polymeric binder. The conductive fillers facilitate the flow of electrical current, while the binder ensures adhesion to different substrates. This unique composition allows conductive adhesives to provide reliable electrical connections even in challenging environments.
One of the primary advantages of conductive adhesives is their compatibility with a wide range of materials. They can bond metals, ceramics, glass, plastics, and even flexible substrates, making them suitable for various industries. Connecting dissimilar materials is particularly advantageous in the electronics industry, where components with different thermal expansion coefficients must be joined together.
Conductive adhesives offer excellent electrical conductivity, comparable to traditional soldering. This property enables them to replace solder joints in specific applications effectively. Moreover, conductive adhesives exhibit better resistance to thermal cycling, mechanical stress, and vibration than soldered connections. These attributes make them ideal for applications with frequent temperature fluctuations or automatic movements.
The ease of application is another significant advantage of conductive adhesives. They are typically available in convenient forms, such as syringes, or dispensed as films or tapes. This allows for precise and controlled dispensing, making them suitable for automated and manual assembly processes. Unlike soldering, which requires specialized equipment and expertise, conductive adhesives can be easily applied with minimal training.
Conductive adhesives find applications in various industries. In the electronics sector, they are used for component attachment, die bonding, wire bonding, and as an alternative to soldering in printed circuit board (PCB) assembly. They are also employed in the manufacture of flexible electronics, where traditional soldering methods are not feasible due to the flexibility of the substrates.
In the automotive industry, conductive adhesives are utilized for bonding sensors, antennas, and lighting systems. They offer excellent adhesion to materials used in automotive applications, including plastics and composites. Moreover, their ability to withstand harsh environmental conditions, such as temperature variations, humidity, and chemical exposure, makes them an ideal choice for automotive electronics.
Conductive adhesives also play a significant role in the medical field. They assemble medical devices, such as sensors, electrodes, and implantable devices. The biocompatible variants of conductive adhesives ensure they are safe for contact with human tissues.
Low Outgassing Adhesives: Critical for Space Applications
Low-outgassing adhesives play a critical role in space applications where materials must withstand the extreme conditions of the space environment. Outgassing refers to releasing volatile compounds from materials when exposed to a vacuum or high temperatures. In space, these volatile compounds can pose significant risks to the functionality and reliability of sensitive equipment and instruments.
In the vacuum of space, outgassed materials can condense on nearby surfaces, such as optical lenses or sensors, causing contamination and degradation of performance. Contamination can impair the accuracy of measurements, reduce signal quality, and even lead to the failure of critical components. Moreover, the condensed outgassed materials may accumulate over time, forming a layer that can absorb or scatter light, impacting optical systems and imaging devices.
Low-outgassing adhesives are specifically formulated to minimize the release of volatile compounds. They are designed to have low vapor pressure, which means they release fewer gases and vapors when exposed to vacuum conditions. This characteristic helps to prevent the contamination and degradation of sensitive surfaces and components.
Spacecraft and satellites rely on low-outgassing adhesives for various applications. One important use is in the bonding and encapsulation of electronic components. These adhesives provide solid and reliable bonds between different materials while minimizing the risk of contamination and outgassing-related issues. They ensure components’ structural integrity and electrical connectivity, allowing them to withstand the vibrations and shocks experienced during launch and operation in space.
Low-outgassing adhesives are also essential for optical systems used in space telescopes, cameras, and sensors. The adhesives used in these systems must have minimal impact on the clarity and performance of lenses, mirrors, and detectors. By reducing outgassing, these adhesives maintain optical properties and prevent the formation of contamination layers that could degrade image quality or interfere with precise measurements.
Additionally, thermal management is a critical consideration in space applications. Low-outgassing adhesives bond heat sinks, thermal interface materials, and other components involved in heat dissipation. These adhesives ensure efficient heat transfer while minimizing the risk of contamination that could impair the performance of thermal management systems.
To meet the stringent requirements of space applications, low-outgassing adhesives undergo rigorous testing and certification processes. The materials are subjected to thermal cycling, vacuum exposure, and analysis to assess their outgassing characteristics. Adhesives that meet the standards set by organizations like NASA’s outgassing requirements (such as ASTM E595) are considered suitable for space missions.
Thermally Conductive Adhesives: Managing Heat in Electronic Devices
Thermally conductive adhesives play a crucial role in managing heat in electronic devices. As electronic components continue to shrink in size and operate at higher power densities, effective heat dissipation becomes increasingly essential to ensure optimal performance and reliability. Thermally conductive adhesives provide a viable solution by efficiently transferring heat from heat-generating components to heat sinks or other heat dissipation mechanisms. This article will explore the critical aspects of thermally conductive adhesives and their role in managing heat in electronic devices.
Thermally conductive adhesives are specially formulated materials with both adhesive properties and high thermal conductivity. They are designed to form strong bonds between heat-generating components, such as integrated circuits or power devices, and heat sinks or other cooling elements. The adhesive nature of these materials ensures a reliable attachment, while their high thermal conductivity enables efficient heat transfer.
One of the primary advantages of thermally conductive adhesives is their ability to fill small gaps and irregularities between mating surfaces, thereby minimizing thermal resistance. This feature is particularly beneficial when attaching components with non-flat surfaces or when dealing with microscopic air gaps hindering heat flow. By filling these gaps, thermally conductive adhesives establish intimate contact between the characters, enhancing heat transfer and reducing the risk of thermal hotspots.
Another critical aspect of managing heat in electronic devices is the ability to withstand temperature cycling and mechanical stresses. Electronic devices are subjected to varying temperature conditions and mechanical vibrations during operation. Thermally conductive adhesives are formulated to maintain their adhesive strength and thermal performance across a wide temperature range, ensuring reliable heat dissipation even under challenging conditions.
Moreover, thermally conductive adhesives offer electrical insulation properties, preventing electrical shorts between components. This feature is crucial in electronic devices where multiple pieces are densely packed, and there is a risk of accidental contact between conductive elements.
Thermally conductive adhesives can be applied using various methods, including dispensing, screen printing, or film lamination. These adhesives are available in different viscosities and cure mechanisms, allowing for flexibility in the manufacturing process. Some thermally conductive adhesives cure at room temperature, while others require elevated temperatures or UV light. Manufacturers can select the bond that best suits their specific production requirements.
Peel-and-Stick Adhesives: Easy to Use and Apply
Peel-and-stick adhesives have revolutionized how we approach various projects and tasks requiring bonding materials. These adhesives are incredibly easy to use and apply, making them popular among professionals and DIY enthusiasts. With their convenience and versatility, peel-and-stick adhesives have become a go-to solution for many applications.
One of the primary advantages of peel-and-stick adhesives is their simplicity. Unlike traditional adhesives that often require mixing or specialized tools, peel-and-stick adhesives come pre-applied to a backing material, ready to use from the package. This eliminates the need for additional equipment or extensive preparation, saving time and effort.
The application process for peel-and-stick adhesives is straightforward and user-friendly. All you need to do is peel off the backing paper to expose the adhesive side and firmly press it onto the desired surface. The adhesive bonds quickly and securely, providing instant adhesion without clamps or drying time. This makes peel-and-stick adhesives ideal for quick repairs, temporary installations, or time-sensitive projects.
Another advantage of peel-and-stick adhesives is their versatility. They are available in various forms, such as tapes, sheets, or dots, to accommodate different applications and materials. Whether you need to attach lightweight objects, mount decorations, or certain heavy-duty items, a peel-and-stick adhesive is suitable for the task. They adhere well to various surfaces, including wood, metal, glass, plastic, and fabric, offering flexibility and compatibility with different materials.
Peel-and-stick adhesives are also known for their clean application. Unlike traditional adhesives that can be messy and require cleanup, peel-and-stick adhesives leave no residue when properly applied and removed. This is especially advantageous when working on delicate or finished surfaces you want to protect from damage.
In addition to their ease of use, peel-and-stick adhesives often exhibit strong bonding capabilities. The adhesives are designed to provide a reliable and durable bond, ensuring that the attached items stay in place securely. However, choosing the right type of adhesive for your project and following the manufacturer’s guidelines for optimal results is essential.
Adhesive Films: Enhancing Efficiency and Consistency
Adhesive films are versatile materials that offer various applications in various industries. They are thin layers of sticky substances coated onto a backing material, such as paper, plastic, or fabric. These films provide numerous benefits, enhancing efficiency and consistency in various processes. This article will explore how adhesive films improve efficiency and consistency in different applications.
One key advantage of adhesive films is their ease of application. Unlike traditional adhesives, which may require mixing or specialized equipment, adhesive films come ready to use. They can be easily cut into desired shapes and sizes, making them ideal for quick and precise application. This saves manufacturing and assembly processes time and resources, increasing overall efficiency.
Moreover, adhesive films offer consistent bonding performance. Their uniform thickness and controlled adhesive properties ensure reliable adhesion between different materials. Whether joining two surfaces, laminating layers, or attaching components, adhesive films provide a consistent bond strength, minimizing the risk of failure or rework. This consistency improves product quality, reduces waste, and increases productivity.
Another way adhesive films enhance efficiency is through their compatibility with automation systems. With the growing trend of automation in various industries, adhesive films are designed to be compatible with robotic assembly and packaging processes. They can be easily integrated into automated production lines, allowing for high-speed and precise bonding operations. This not only improves efficiency but also reduces labor costs and human errors.
In addition, adhesive films offer enhanced efficiency in sealing and protection applications. They provide a barrier against moisture, dust, and contaminants, preventing damage to sensitive components or products. Whether sealing electronic devices, packaging food products, or protecting surfaces from corrosion, adhesive films offer reliable and consistent protection. This contributes to the longevity and reliability of the products, reducing the need for frequent maintenance or replacements.
Furthermore, adhesive films enable efficient customization and design flexibility. They can be tailored to specific requirements, such as different bonding strengths, temperature resistance, or optical properties. This allows manufacturers to optimize the adhesive properties based on their application needs, ensuring the best performance and reliability. Additionally, adhesive films can be easily printed or decorated, offering branding opportunities and aesthetic appeal.
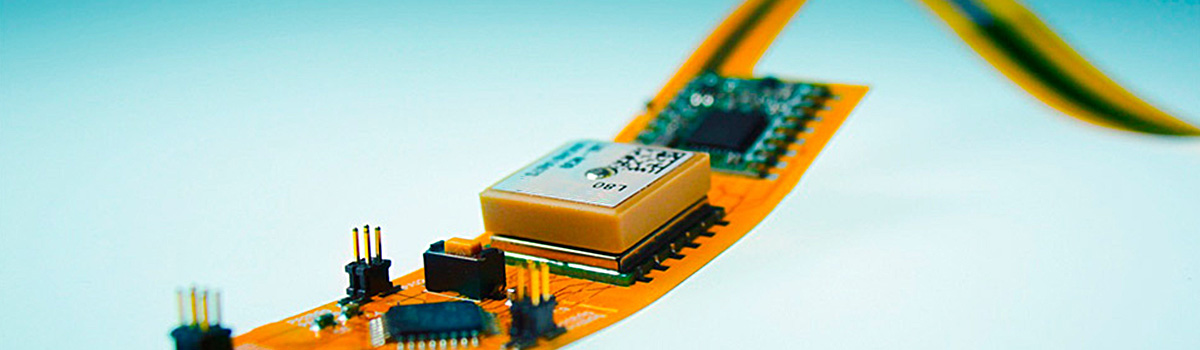
Hot Melt Adhesives: Fast and Durable Bonding
Hot melt adhesives (HMAs) are versatile adhesives that offer fast and durable bonding solutions across various industries and applications. These adhesives, or hot glue, are thermoplastic materials that are melted to a liquid state and applied molten. Upon cooling, they solidify and create a strong bond between substrates. Here’s a closer look at hot melt adhesives’ characteristics, benefits, and applications.
One of the critical advantages of HMAs is their rapid bonding capabilities. These adhesives liquefy quickly when heated, allowing for efficient and high-speed application. They eliminate the need for solvent evaporation or chemical reactions, unlike other types of adhesives. The quick solidification of hot melt adhesives results in shorter assembly and production times, increasing productivity and cost savings.
Furthermore, hot melt adhesives provide exceptional durability in bonded joints. They exhibit excellent resistance to moisture, chemicals, and temperature fluctuations. This resilience makes them suitable for demanding environments and applications that require long-lasting and reliable bonding. HMAs also offer flexibility and impact resistance, enabling them to withstand vibrations and shocks without compromising the bond integrity.
HMAs find applications in various industries, including packaging, woodworking, automotive, electronics, textiles, and construction. Hot melt adhesives are widely used in packaging for case and carton sealing, tamper-evident closures, and bonding labels and tapes. They provide secure and tamper-resistant seals, ensuring product integrity and preventing pilferage.
Woodworking applications of HMAs include edgebanding, veneering, and laminating operations. The fast-setting nature of hot melt adhesives facilitates efficient assembly line processes. They create strong bonds in wooden joints, enhancing furniture and cabinetry’s structural integrity and longevity.
Automotive manufacturers rely on hot melt adhesives for interior and exterior trim bonding, wire harnessing, and gasket sealing. These adhesives’ durability and heat resistance make them ideal for automotive applications, where performance under extreme conditions is essential.
Electronics assembly and manufacturing often utilize hot melt adhesives for component bonding, wire tacking, and encapsulation. Their ability to bond dissimilar materials, such as plastics, metals, and glass, makes them suitable for diverse electronic applications.
Textile industry hot melt adhesives applications include fabric lamination, hemming, and appliqué bonding. They enable precise and clean bonding without sewing, stitching, or other mechanical fastening methods.
In the construction sector, HMAs are used for flooring installation, paneling, insulation, and tile bonding. Their fast-setting characteristics facilitate rapid construction processes and ensure reliable adhesion in various construction materials.
Pressure Sensitive Adhesives: Ensuring Consistent Adhesion
Pressure-sensitive adhesives (PSAs) are versatile materials used in various industries, from automotive and electronics to packaging and medical devices. These adhesives offer unique advantages such as ease of application, immediate bonding, and the ability to adhere to a wide range of surfaces. However, ensuring consistent adhesion can be a challenge when working with PSAs. Here are some key considerations to achieve reliable and consistent adhesion with pressure-sensitive adhesives.
- Surface Preparation: Proper surface preparation is crucial for achieving consistent adhesion with PSAs. Surfaces must be clean, dry, and free from dust, oil, grease, and moisture contaminants. Cleaning the surface with suitable solvents or cleaners and using techniques like abrasion or plasma treatment can improve adhesion by enhancing surface energy and removing potential barriers to bonding.
- Material Compatibility: Ensuring the PSA is compatible with the substrate material is essential. Some PSAs may exhibit poor adhesion or compatibility issues with certain surfaces. Understanding the chemical composition and properties of both the adhesive and the substrate can help select the appropriate adhesive for the specific application, ensuring consistent adhesion.
- Application Technique: The application technique plays a significant role in achieving consistent adhesion. Pressure, temperature, and dwell time during application can affect the bond strength. It is essential to follow the manufacturer’s recommendations regarding the application parameters, including the proper pressure to apply and the recommended temperature range for bonding.
- Cure Time: PSAs typically require a certain amount of time to develop their full adhesive strength. This curing or “dwell” time allows the adhesive to flow and form strong bonds with the substrate. It is essential to allow sufficient cure time before subjecting the bonded assembly to stress or load. Rushing the process can result in weaker adhesion or even adhesive failure.
- Environmental Factors: Environmental conditions can impact the performance of PSAs. Factors such as temperature, humidity, and exposure to chemicals or UV radiation can affect the adhesive’s properties and adhesion performance. Understanding the specific environmental conditions the adhesive will be exposed to and selecting an adhesive with appropriate resistance to these factors can help ensure consistent adhesion over time.
- Testing and Quality Control: Regular testing and quality control measures are essential to ensure consistent adhesion. Various test methods, such as peel adhesion, shear strength, and tack, can assess the adhesive’s performance. Establishing proper testing protocols and conducting regular quality checks during production can help identify any inconsistencies or issues early on and ensure consistent adhesion in the final product.
- Storage and Shelf Life: Proper storage conditions and adherence to shelf life guidelines are essential for maintaining the adhesive’s performance. PSAs can degrade over time due to heat, light, or air exposure, affecting their adhesive properties. Storing the bonds in controlled environments and using them within their recommended shelf life can help maintain consistent adhesion.
Adhesive Dispensing Techniques: Precision and Efficiency
Adhesive dispensing techniques are crucial in various industries, ensuring precision and efficiency in bonding applications. Whether it’s for manufacturing, assembly, or repairs, the proper dispensing method can significantly impact the quality and reliability of adhesive bonds. This article will explore critical techniques that help achieve precision and efficiency in adhesive dispensing within a limited word count.
- Manual Dispensing: Manual adhesive dispensing is commonly employed in small-scale operations or complex applications. It involves using handheld devices such as syringes, squeeze bottles, or brushes to apply adhesive precisely. While this method offers flexibility and control, it depends on the operator’s skill and consistency.
- Time/Pressure Dispensing: Time/pressure dispensing is a widely used technique that provides consistent and controlled adhesive application. It involves using pneumatic or electric dispensers with pressure regulators and timers. By adjusting the dispensing time and pressure, operators can accurately control the adhesive amount applied. This technique is suitable for medium to high-viscosity adhesives.
- Jetting: Jetting is a dispensing technique that utilizes a high-velocity stream of adhesive to apply precise and small quantities of adhesive onto the target surface. It is commonly used in applications requiring fast and accurate placement, such as electronics assembly or micro bonding. Jetting systems use piezoelectric or pneumatic actuation to create controlled adhesive droplets.
- Spray Dispensing: Spray dispensing is an efficient technique for covering large areas or achieving uniform coverage. It involves atomizing the adhesive into fine droplets and directing them onto the surface using air pressure or an automatic spray gun. Spray dispensing is commonly used in automotive, woodworking, or packaging industries, where fast and even coverage is required.
- Robotic Dispensing: Robotic dispensing systems offer precise and repeatable adhesive applications through programmable automation. They are equipped with advanced sensors and dispensing valves that can be programmed to follow intricate patterns and contours. Robotic dispensing ensures consistency and accuracy, making it ideal for high-volume production lines and complex assembly processes.
- Film/Swirl Coating: Film or swirl coating is a technique used to apply a uniform layer of adhesive onto a substrate. It involves using a rotating mechanism or applicator to spread the adhesive in a thin, continuous film. This method is commonly employed in automotive, aerospace, and construction industries, where controlled adhesive thickness is critical for optimal performance.
Challenges in FPC Bonding Adhesive Application
FPC (Flexible Printed Circuit) bonding adhesive application poses several challenges that must be addressed for successful bonding and reliable performance. These challenges primarily stem from the unique properties and requirements of FPCs. In this response, I will outline some key challenges encountered in FPC bonding adhesive application.
- Substrate Compatibility: FPCs are made of flexible materials such as polyimide, polyester, or thin copper, with different surface characteristics than rigid substrates. The bonding adhesive must be compatible with the FPC material to ensure proper adhesion without causing delamination or damage to the substrate.
- Surface Preparation: Proper surface preparation is critical for adhesive bonding. FPC surfaces often have residues, oils, or contaminants that can hinder adhesion. The challenge lies in selecting the correct cleaning method or surface treatment to remove these impurities without compromising the integrity of the FPC.
- Bond Line Thickness Control: Achieving uniform bond line thickness is essential for reliable performance. Inconsistent adhesive thickness can lead to variations in electrical conductivity, mechanical strength, and thermal management. Ensuring precise control over the bond line thickness can be challenging due to the flexible nature of FPCs.
- Thermal Management: FPCs are often used in applications where temperature variations are expected. The adhesive used for bonding must have good thermal conductivity to dissipate heat effectively, preventing localized hotspots that could damage the FPC or its components. Achieving optimal thermal management without compromising the flexibility and electrical properties of the FPC is a challenge.
- Adhesive Curing: FPC bonding adhesives typically require curing processes such as heat or UV. The challenge lay ensuring uniform and completed curing across the bond line, especially in complex or densely packed FPC designs. Inadequate curing can result in stronger adhesion or incomplete bonding, leading to reliability issues.
- Flexibility and Durability: FPCs are designed to be flexible, and the bonding adhesive must accommodate this flexibility without compromising its integrity. The bond must withstand repeated bending, flexing, and stretching without cracking, delaminating, or losing adhesion strength. Finding a bond that can maintain both flexibility and durability can be challenging.
- Electrical Conductivity: FPCs often carry electrical signals, making electrical conductivity a critical requirement. The bonding adhesive should not introduce high resistance that could interfere with the circuit’s performance. Achieving good electrical conductivity across the bond line while ensuring mechanical integrity poses a challenge.
- Process Automation: Automating the adhesive application process becomes necessary in industries where FPC bonding is performed at scale. The challenge lies in developing automated systems that can consistently apply the adhesive with precision and efficiency, accounting for variations in FPC sizes, shapes, and designs.
Addressing these challenges requires a comprehensive understanding of FPC materials, bonding adhesives, and the application’s specific requirements. It often involves careful material selection, process optimization, and testing to ensure the adhesive’s compatibility, performance, and reliability in FPC bonding applications.
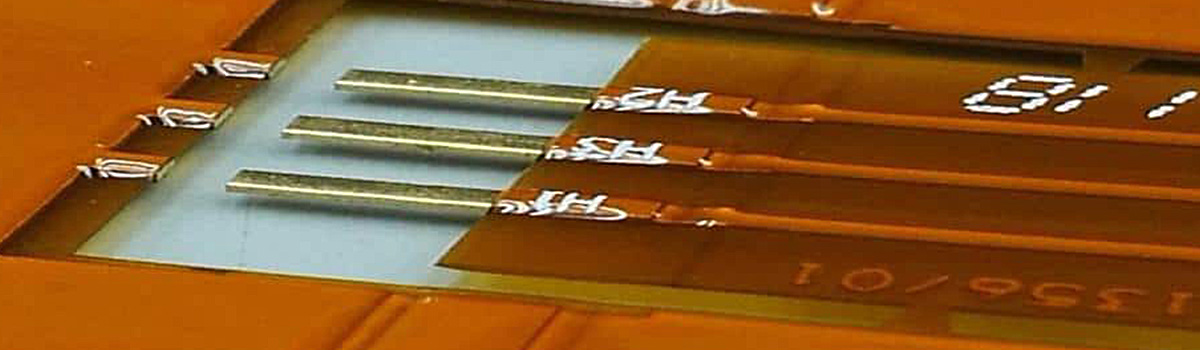
Reliability Testing: Assessing Adhesive Performance
Reliability testing is a crucial step in assessing the performance of adhesives. Adhesives are widely used in various industries, including automotive, aerospace, electronics, and construction, to bond different materials. The reliability of adhesive bonds is essential to ensure the final product’s safety, durability, and overall performance.
Reliability testing involves subjecting adhesive bonds to various conditions and stressors that simulate real-world environments and usage scenarios. The goal is to evaluate the adhesive’s ability to maintain its bond strength and integrity over time. Here are some key aspects to consider when assessing adhesive performance in reliability testing:
- Bond Strength: The adhesive’s initial bond strength is evaluated using standardized tests such as lap shear, peel, or tensile tests. These tests measure the force required to break the adhesive bond. It provides a baseline for comparison with the bond strength after exposure to different conditions.
- Environmental Exposure: Adhesives are often exposed to harsh environmental conditions such as temperature extremes, humidity, UV radiation, and chemicals. Reliability testing involves subjecting adhesive samples to accelerated aging tests that simulate these conditions over an extended period. This helps assess the adhesive’s resistance to environmental degradation and its ability to maintain bond strength under adverse conditions.
- Thermal Cycling: Temperature variations can cause materials’ expansion and contraction, which can stress adhesive bonds. Thermal cycling tests involve subjecting adhesive samples to repeated temperature cycles, from low to high extremes, to assess the adhesive’s resistance to thermal stress and its ability to maintain bond integrity.
- Mechanical Stress: Adhesive bonds may experience different types of mechanical stress during service, such as tension, compression, shear, and vibration. Reliability testing involves subjecting adhesive samples to mechanical stress through cyclic fatigue, impact, or flexural tests. These tests help evaluate the adhesive’s ability to withstand automatic loading without bond failure.
- Durability and Aging: Adhesive bonds are expected to have long-term durability and should resist degradation over time. Reliability testing includes long-term aging tests that simulate the product’s anticipated lifespan. This may involve subjecting adhesive samples to prolonged exposure to environmental factors, such as temperature, humidity, and UV radiation, and periodically assessing bond strength and integrity.
- Compatibility: Adhesives must be compatible with the materials they are intended to bond. Reliability testing involves assessing the adhesive’s compatibility with different substrates, including metals, plastics, composites, and other materials commonly used in the industry. Compatibility tests evaluate the adhesive’s bond strength, resistance to chemical interaction, and any adverse effects on the substrate.
Reliability testing provides valuable information about the performance and limitations of adhesives under various conditions. It helps manufacturers select the most suitable adhesive for their application and ensures its reliability and durability in real-world scenarios. By conducting rigorous reliability testing, manufacturers can mitigate the risk of adhesive bond failure, enhance product quality, and improve customer satisfaction.
Environmental Considerations in FPC Bonding Adhesive
FPC (Flexible Printed Circuit) bonding adhesives play a critical role in the assembly and reliability of electronic devices. As environmental awareness and sustainability become increasingly important, it is essential to consider the ecological impact of these adhesives. Here are some critical environmental considerations related to FPC bonding adhesives:
- Toxicity: One of the primary concerns is the toxicity of the adhesive and its constituents. Adhesives may contain harmful chemicals such as volatile organic compounds (VOCs) or hazardous air pollutants (HAPs). These substances can have detrimental effects on human health and the environment. Manufacturers should strive to minimize or eliminate toxic chemicals in their adhesive formulations.
- Emissions and Air Quality: During the manufacturing and application processes, FPC bonding adhesives can release VOCs and other air pollutants into the atmosphere. These emissions contribute to air pollution and can adversely affect air quality. Environmentally conscious adhesive manufacturers aim to reduce these emissions by formulating low-VOC or zero-VOC adhesives.
- Energy Consumption: The production of FPC bonding adhesives requires energy, which often comes from non-renewable sources. To minimize the environmental impact, manufacturers should implement energy-efficient processes and explore using renewable energy sources.
- Waste Generation: Adhesive application processes can generate waste, including excess adhesive material, packaging, and cleanup materials. Proper waste management practices, such as recycling or reusing waste materials whenever possible, should be followed. Additionally, manufacturers should explore the development of adhesives with a longer shelf life to reduce waste from expired or unused products.
- End-of-Life Considerations: Disposing of electronic devices containing FPC bonding adhesives is a significant environmental concern. Adhesives that are not easily degradable or have hazardous components can contribute to pollution when devices are discarded. Adhesive manufacturers should strive to develop environmentally friendly products that are compatible with recycling or disposal processes, such as adhesives that can be easily separated from circuit boards during recycling.
- Sustainability and Green Initiatives: Adhesive manufacturers should incorporate sustainability into their business practices. This can include using renewable raw materials, implementing eco-friendly manufacturing processes, and adhering to recognized environmental standards and certifications. Additionally, companies can participate in green initiatives, such as product take-back programs or partnerships with recycling facilities.
- Life Cycle Assessment: Conducting a comprehensive life cycle assessment (LCA) of FPC bonding adhesives is crucial for understanding their environmental impact from raw material extraction to disposal. LCAs help identify areas where improvements can be made, such as reducing greenhouse gas emissions, minimizing resource consumption, and enhancing recyclability.
Trends and Innovations in FPC Bonding Adhesive
FPC (Flexible Printed Circuit) bonding adhesives constantly evolve, driven by the demand for higher performance, miniaturization, and improved reliability in electronic devices. Here are some notable trends and innovations in FPC bonding adhesives:
- Miniaturization and Thinness: As electronic devices become smaller and thinner, there is a growing need for FPC bonding adhesives to accommodate these form factor requirements. Manufacturers are developing ultra-thin and low-profile adhesives that provide strong bonding while minimizing the overall thickness of the assembly.
- High-Temperature Resistance: Many electronic devices, particularly those in automotive, aerospace, and industrial applications, operate in high-temperature environments. FPC bonding adhesives with enhanced heat resistance are being developed to ensure reliable performance under extreme temperature conditions, preventing delamination or bond failure.
- Low-Pressure Curing: Traditional adhesive curing processes often require high temperatures or long curing times, which can be challenging for heat-sensitive components or delicate substrates. Innovations in low-pressure techniques, such as UV-curing or moisture-curing adhesives, offer more gentle curing options, enabling compatibility with temperature-sensitive components and substrates.
- Conductive Adhesives: The demand for FPC bonding adhesives with electrical conductivity is increasing in applications that require electrical connections between circuit elements. Conductive adhesives eliminate the need for different soldering processes, enabling faster assembly and reducing the risk of thermal damage to sensitive components.
- Improved Flexibility and Durability: Flexibility and durability are crucial for FPC bonding adhesives to withstand bending, twisting, and vibration in flexible electronic devices. Advancements in polymer chemistry and formulation techniques result in adhesives with improved flexibility, elongation, and resistance to mechanical stress, ensuring reliable bonding in dynamic environments.
- Environmental Friendliness: Environmental considerations, including using sustainable raw materials and reducing toxic substances, are becoming more prominent in adhesive development. Manufacturers are exploring bio-based and renewable materials as alternatives to petroleum-based ingredients. Additionally, eco-friendly manufacturing processes and recyclable adhesive formulations are being developed to minimize the environmental impact.
- Improved Dispensing and Application: Efficient and precise adhesive application is crucial for achieving consistent and reliable bonds. Innovations in dispensing technologies, such as automated dispensing systems and jetting methods, allow for controlled and accurate deposition of adhesives, even in complex FPC designs with delicate pitch components.
- Adhesive Film Technology: Adhesive films are gaining popularity in FPC bonding due to their ease of handling and precise placement. These pre-formed films offer uniform adhesive thickness, excellent wetting properties, and simplified assembly processes. Manufacturers continuously improve adhesive film formulations to enhance their bonding performance and compatibility with various substrates.
- Reliability Enhancements: To ensure long-term reliability, FPC bonding adhesives are being developed with improved resistance to factors such as moisture, chemicals, and aging. These adhesives undergo rigorous testing to assess their performance under harsh environmental conditions, ensuring consistent functionality and bond integrity over the product’s lifespan.
- Customization and Application-Specific Solutions: FPC bonding adhesives are being tailored to meet the specific requirements of different applications, such as automotive, consumer electronics, medical devices, and wearable technology. Manufacturers are collaborating closely with device designers and manufacturers to develop customized adhesive solutions that address each application’s unique challenges and performance demands.
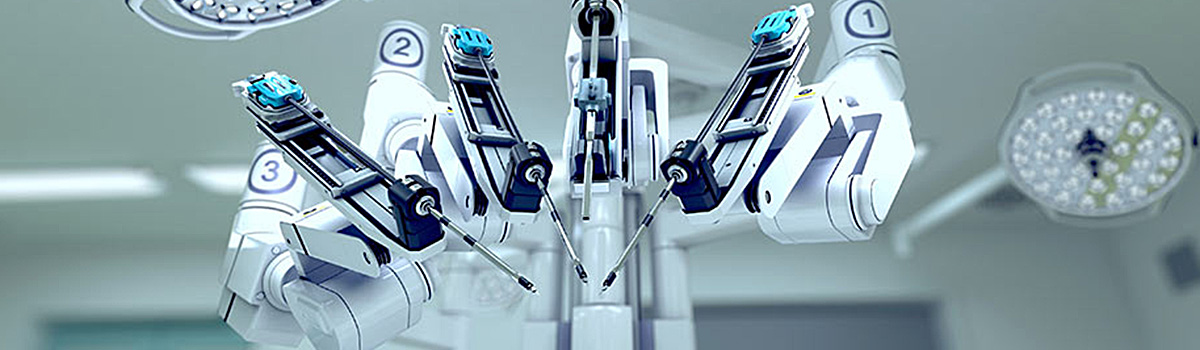
Application Areas: Consumer Electronics, Automotive, Medical Devices, and More
Consumer Electronics: Consumer electronics encompass a wide range of products designed for personal use and entertainment. These include smartphones, tablets, laptops, gaming consoles, smart TVs, smart home devices, wearables, and more. The application of consumer electronics has revolutionized the way people communicate, work, and entertain themselves. Technological advancements have made consumer electronics more powerful, compact, and affordable, providing users with seamless connectivity, immersive experiences, and convenience.
Automotive: The automotive industry has witnessed significant advancements in recent years, primarily driven by technology integration. From electric vehicles (EVs) to autonomous driving systems, automotive applications have transformed how we travel. Electric cars are gaining popularity due to their eco-friendly nature and the reduction of carbon emissions. Moreover, automotive manufacturers are incorporating innovative features like advanced driver-assistance systems (ADAS), connectivity, infotainment systems, and telematics to enhance the driving experience, improve safety, and enable efficient vehicle management.
Medical Devices: Medical devices have played a crucial role in diagnosing, monitoring, and treating various medical conditions. They range from simple devices like thermometers and blood pressure monitors to advanced equipment like MRI machines and robotic surgical systems. Medical devices enable healthcare professionals to provide accurate diagnoses, perform minimally invasive procedures, and monitor patient health remotely. They have revolutionized the healthcare industry, improving patient outcomes, reducing hospital stays, and enhancing the overall quality of care.
Internet of Things (IoT): The Internet of Things (IoT) is a network of interconnected devices embedded with sensors, software, and connectivity capabilities. It enables data exchange and communication between devices, leading to automation, data analysis, and improved decision-making. IoT has applications in various industries, including healthcare, agriculture, manufacturing, and energy. In healthcare, IoT devices can monitor patient vitals, track medication adherence, and enable remote patient monitoring. IoT devices can optimize irrigation, monitor soil conditions, and enhance crop management in agriculture. IoT has the potential to revolutionize industries by making them more efficient, sustainable, and data-driven.
Industrial Automation: Industrial automation involves using technology and control systems to automate industrial processes and tasks. This includes robotics, machine vision systems, sensors, and programmable logic controllers (PLCs). Industrial automation enhances productivity, improves safety, reduces operational costs, and finds applications in manufacturing, logistics, energy, and other sectors. With artificial intelligence (AI) and machine learning (ML) integration, industrial automation can optimize processes, detect anomalies, and enable predictive maintenance, improving efficiency and reducing downtime.
Future Prospects and Opportunities
FPC (Flexible Printed Circuit) bonding adhesive is a critical component in the manufacturing of electronic devices. It is crucial in ensuring reliable and robust connections between flexible circuits and other parts. As we look into the future, several prospects and opportunities for FPC bonding adhesive are worth considering.
- Advancements in Flexible Electronics: The field of flexible electronics is rapidly evolving, with a growing demand for flexible displays, wearable devices, and intelligent textiles. FPC bonding adhesives will continue to be in high order to enable the assembly and interconnection of flexible circuits in these innovative applications.
- Miniaturization and Slimmer Devices: As consumer electronics become increasingly compact and slim, thinner and more flexible interconnect solutions are paramount. FPC bonding adhesives can facilitate the assembly of ultra-thin flexible circuits, creating sleeker and more lightweight devices.
- Enhanced Bonding Performance: Manufacturers continuously seek adhesive solutions that offer superior bonding performance, such as high shear strength, excellent electrical conductivity, and thermal stability. Future FPC bonding adhesives will likely incorporate advanced materials and formulations to meet these demanding requirements.
- Integration with Advanced Manufacturing Processes: Emerging manufacturing technologies like 3D printing, roll-to-roll processing, and hybrid integration open up new possibilities for producing flexible circuits. FPC bonding adhesives must adapt and be compatible with these manufacturing processes, offering optimized adhesion and reliability.
- Flexible Hybrid Electronics (FHE): FHE combines traditional rigid electronics with adaptable components, creating devices with unique form factors and functionalities. FPC bonding adhesives will be instrumental in assembling these hybrid systems, seamlessly connecting flexible and rigid elements.
- Sustainability and Environmental Considerations: The increasing focus on sustainability and environmental responsibility presents an opportunity to develop eco-friendly FPC bonding adhesives. Future formulations may incorporate renewable or recyclable materials, reducing the environmental impact of electronic waste.
- Integration of Smart Features: With the rise of the Internet of Things (IoT) and interconnected devices, FPC bonding adhesives can potentially incorporate intelligent features such as embedded sensors, self-healing capabilities, or thermal management properties. These advancements would enhance the functionality and reliability of electronic devices.
- Medical and Healthcare Applications: The medical field is experiencing a surge in wearable devices, implantable sensors, and intelligent healthcare technologies. FPC bonding adhesives that are biocompatible, sterilizable, and capable of adhering to various substrates will find significant applications in this domain.
- Automotive and Aerospace Industries: The automotive and aerospace sectors increasingly adopt flexible circuits for their lightweight and space-saving benefits. FPC bonding adhesives that can withstand extreme temperatures, vibrations, and mechanical stresses will be in high demand for these demanding environments.
- Research and Development: Continued research and development efforts in FPC bonding adhesives will lead to further advancements. Innovations in adhesive chemistries, manufacturing techniques, and process optimization will drive the industry forward, enabling new applications and improved performance.
Importance of Collaboration in Advancing FPC Bonding Adhesive Technology
Collaboration is pivotal in advancing FPC (Flexible Printed Circuit) bonding adhesive technology. It enables the exchange of knowledge, resources, and expertise among different stakeholders, leading to accelerated innovation and progress. Here are the key reasons highlighting the importance of collaboration in advancing FPC bonding adhesive technology:
- Cross-Disciplinary Expertise: FPC bonding adhesive technology involves various domains, including materials science, chemistry, electronics manufacturing, and engineering. Collaboration brings together experts from these diverse fields, fostering interdisciplinary approaches to problem-solving. By combining their knowledge and perspectives, researchers and industry professionals can address complex challenges and develop novel solutions more effectively.
- Knowledge Sharing: Collaboration facilitates information sharing, research findings, and best practices among different entities. Manufacturers, suppliers, researchers, and academic institutions can collaborate to disseminate valuable insights and technical knowledge about FPC bonding adhesive technology. This shared knowledge helps avoid redundant efforts, promotes standardization, and accelerates overall development.
- Access to Resources: Collaborative efforts allow access to a broader range of resources, including funding, equipment, facilities, and materials. Partnering with organizations, research institutes, or government agencies can provide access to specialized resources that may not be available individually. This access enables more extensive experimentation, testing, and prototyping, leading to improved FPC bonding adhesive formulations and manufacturing processes.
- Accelerated Innovation: Collaboration fosters an environment of open innovation and creativity. By bringing together diverse perspectives and expertise, new ideas and concepts can emerge, pushing the boundaries of FPC bonding adhesive technology. Collaborative projects can also leverage the strengths of each partner, combining their unique capabilities and resources to develop innovative solutions at an accelerated pace.
- Market Insights and Industry Trends: Collaborating with industry partners and end-users provides valuable insights into market demands, emerging trends, and customer requirements. This understanding helps align the development of FPC bonding adhesive technology with the evolving needs of the industry. Collaborative efforts allow for early feedback and validation, ensuring that the developed solutions are practical, relevant, and commercially viable.
- Quality Assurance and Standardization: Collaboration facilitates the establishment of quality assurance measures and industry standards for FPC bonding adhesive technology. Partnering with standards organizations and regulatory bodies ensures that the developed adhesives meet safety, reliability, and performance requirements. Collaboration also enables sharing testing methodologies and validation protocols, leading to more consistent and standardized bonding processes.
- Validation and Real-World Application: Collaborating with end-users, manufacturers, and system integrators allows for the confirmation of FPC bonding adhesive technology in real-world applications. By working together, adhesive manufacturers can gain valuable performance, usability, and manufacturability feedback. This feedback loop helps refine and improve the adhesive formulations, ensuring their suitability for various applications and environments.
- Risk Mitigation: Collaboration spreads the risks associated with research and development efforts. Partners can collectively tackle challenges and mitigate individual risks by pooling resources and expertise. Collaboration also enables sharing of intellectual property and patent rights, fostering a more cooperative and less competitive environment.
Conclusion
FPC bonding adhesive is vital in enabling flexibility and reliability in electronic devices. The ability of these adhesives to provide strong bonding capabilities, electrical insulation, and protection against environmental factors while ensuring the flexibility and durability of FPC boards is crucial in the manufacturing and assembly of various electronic devices. As technology advances, developing innovative adhesive solutions and collaborating between manufacturers, researchers, and end-users will be crucial in meeting the growing demands and challenges of the electronics industry. By harnessing the potential of FPC bonding adhesive, we can pave the way for even more flexible, durable, and reliable electronic devices that power our modern world.