Camera Module Bonding Adhesives
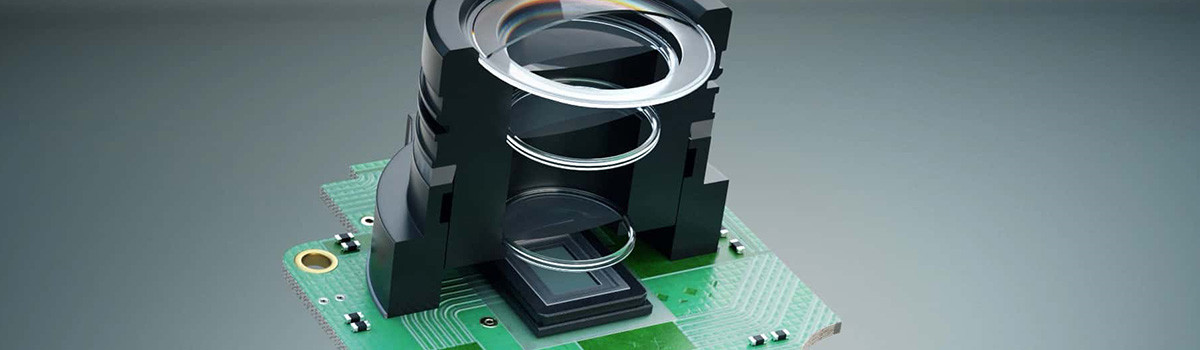
Camera module adhesive plays a critical role in the assembly and performance of modern smartphone cameras. The adhesive is responsible for securely holding the camera module, preventing it from shifting or becoming misaligned during use. This comprehensive guide will cover everything you need to know about camera module adhesive, including its types, application methods, advantages, disadvantages, and more.
What is Camera Module Adhesive?
A camera module adhesive is a type of adhesive or bonding material used to attach a camera module to the main circuit board of a device, such as a smartphone or a tablet computer. The camera module adhesive plays an essential role in ensuring that the module stays securely in place and does not move or shift over time, which could affect the quality of the images or videos captured by the camera.
Camera module adhesives are typically made of a strong and durable material that can withstand the stresses and strains of daily use. Depending on the specific requirements of the device and the intended application, they may be designed to be heat-resistant, water-resistant, or shock-resistant.
The application of camera module adhesive typically involves a precise and careful process, as the camera module must be aligned correctly with the circuit board to ensure proper functionality. Manufacturers may use specialized equipment or techniques to apply the adhesive and provide a robust and reliable bond between the camera module and the circuit board.
Why is Camera Module Adhesive Important?
Camera module adhesive is an essential component in manufacturing electronic devices with camera modules, such as smartphones, tablets, laptops, and cameras. It is used to bond the camera module to the device’s printed circuit board (PCB) or cover lens, ensuring the camera is securely fixed.
The adhesive is crucial in maintaining the camera module’s position and alignment, which is critical for producing high-quality images and videos. The camera module adhesive must provide a robust and durable bond that can withstand the rigors of daily use, including shocks, vibrations, and temperature changes.
In addition to its functional properties, the camera module adhesive also serves an aesthetic purpose, and it can be applied precisely to create a seamless, clean finish between the camera module and the device’s surface.
Overall, camera module adhesive is essential to the reliability, performance, and appearance of electronic devices with camera modules.
Types of Camera Module Adhesive
Camera module adhesive is a specialized adhesive used to secure camera modules to electronic devices such as smartphones, tablets, laptops, and other devices. There are various types of camera module adhesive, including:
- Acrylic adhesive: Acrylic adhesive is a camera module adhesive that provides high adhesion strength and excellent environmental resistance. This adhesive is commonly used for camera modules that require high bonding strength and long-term durability.
- Epoxy adhesive: Epoxy adhesive is a two-part adhesive with high bonding strength and excellent environmental resistance. This adhesive is commonly used for camera modules that require high bonding strength and long-term durability.
- Silicone adhesive: Silicone adhesive is a camera module adhesive that provides good adhesion strength and flexibility. This adhesive is commonly used for camera modules that require flexibility and vibration damping.
- UV-curing adhesive: UV-curing adhesive is a camera module adhesive that cures when exposed to UV light. This adhesive provides fast curing times and excellent adhesion strength. It is commonly used for camera modules that require fast curing times.
- Pressure-sensitive adhesive: Pressure-sensitive adhesive is a camera module adhesive with good adhesion strength and easy application. This adhesive is commonly used for camera modules that require easy application and temporary bonding.
The choice of camera module adhesive depends on the specific application requirements and the type of camera module being used.
Liquid Adhesive vs. Tape Adhesive
Liquid and tape adhesive are commonly used to bond materials together, but they have some key differences.
Liquid adhesive, or glue, is a viscous liquid substance that is applied directly onto the surfaces to bond. It can come in different forms, such as white, clear, super, and epoxy. Liquid adhesive creates a strong, permanent bond and is suitable for paper, wood, metal, and plastics. It is also versatile in terms of application methods, such as brush, roller, or spray, depending on the type of adhesive.
On the other hand, tape adhesive is a thin layer of adhesive material coated onto a flexible backing material such as paper, film, or cloth. The most common types of tape adhesive are double-sided tape and masking tape. Double-sided tape has adhesive on both sides, allowing it to bond two surfaces together, while the masking video has adhesive on one side and is mainly used for temporarily holding objects in place during painting, decorating, or other applications. Tape adhesive is quick and easy to apply and can be removed without leaving residue in most cases.
Conductive Adhesive vs. Non-Conductive Adhesive
Conductive and non-conductive adhesives are two types of adhesives used in different applications.
Conductive adhesive is an adhesive that can conduct electricity. This type of adhesive is commonly used in electronic applications where electrical conductivity is required, such as bonding electronic components to printed circuit boards (PCBs) or attaching electrodes to biomedical sensors. Conductive adhesives usually contain conductive fillers like silver, copper, or nickel particles.
Non-conductive adhesive, on the other hand, is an adhesive that does not conduct electricity. This type of adhesive is used in applications where electrical conductivity is not required, such as bonding materials in construction or packaging applications. Non-conductive adhesives can be made from various materials, including acrylics, epoxies, or cyanoacrylates.
When selecting an adhesive, it is essential to consider the application requirements. If electrical conductivity is required, a conductive adhesive should be used. A non-conductive adhesive may be more suitable if electrical conductivity is not required. It is also essential to consider other factors, such as the bonding strength, cure time, and environmental conditions to ensure the adhesive will perform as expected.
UV-curing Adhesive vs. Thermal-curing Adhesive
UV-curing and thermal-curing adhesives are two different types of adhesives commonly used in industrial and manufacturing processes.
As the name suggests, UV-curing adhesive cures when exposed to UV light. This type of adhesive typically has a fast curing time, which allows for high throughput in production processes. The UV-curing adhesive is commonly used in electronics, optics, and medical devices.
Thermal-curing adhesive, on the other hand, cures when exposed to heat, and this type of adhesive typically requires a longer curing time than UV-curing adhesive. However, the thermal-curing adhesive can provide a stronger bond and higher temperature resistance, making it suitable for applications such as the aerospace and automotive industries.
Both adhesive types have advantages and disadvantages depending on the specific application requirements. The UV-curing adhesive is preferred for applications that require a fast cure time and low heat generation, whereas the thermal-curing adhesive is preferred for applications that require high strength and temperature resistance.
Advantages of Camera Module Adhesive
Camera module adhesive offers several advantages for the manufacturing and assembly of electronic devices, especially for those that require a camera module. Some of these advantages include:
- Strong adhesion: Camera module adhesive is designed to provide robust and reliable adhesion between the camera module and the device’s substrate. This ensures the camera remains securely in place, even in harsh or high-vibration environments.
- Improved camera performance: Camera module adhesive can also help improve camera performance by reducing vibration, shock, and other factors impacting image quality. This can lead to better image stabilization, sharper images, and improved overall camera performance.
- Cost-effective: Camera module adhesive is often more cost effective than traditional mechanical fasteners or clips, as it requires fewer parts and is easier to assemble.
- Reduced thickness: Camera module adhesive can also help reduce the overall thickness of a device, making it more compact and lightweight.
- Improved manufacturing efficiency: Camera module adhesive can be applied quickly and easily, allowing for faster manufacturing and assembly times. This can help reduce production costs and improve overall efficiency.
Overall, camera module adhesive is a reliable and cost-effective solution for securing camera modules in electronic devices, offering improved performance and manufacturing efficiency.
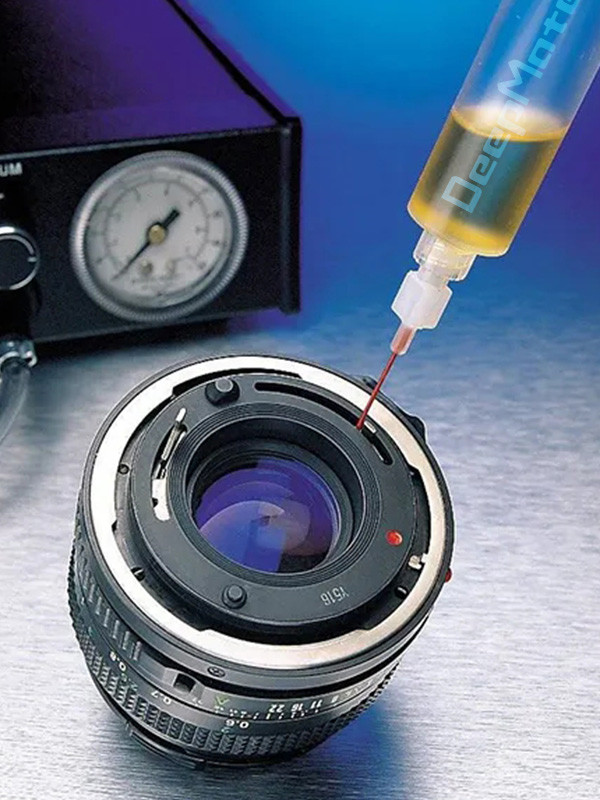
Disadvantages of Camera Module Adhesive
There are a few disadvantages to using a camera module adhesive to attach a camera module to a device or surface. Some of these include:
- Limited flexibility: The camera module is permanently attached to the surface once the adhesive is applied. Any adjustments or repairs to the camera module become difficult or impossible.
- Difficult to remove: If the camera module needs to be removed, it can be challenging to do so without damaging the device or surface it was attached. Removing the adhesive may require using solvents or other chemicals that could damage the device or surface.
- Inconsistent application: Adhesive application requires a certain level of skill and experience. Inexperienced or untrained individuals may apply too much or too little adhesive, which could lead to problems with the camera module’s alignment, stability, and overall performance.
- Susceptible to environmental factors: Camera module adhesive can be affected by environmental factors such as temperature, humidity, and UV radiation. This could cause the glue to degrade or become less effective over time, leading to problems with the camera module’s stability or performance.
- Limited durability: The adhesive to attach a camera module may not be as durable as other attachment methods, such as screws or clips. This means the camera module may become detached over time, especially if exposed to frequent or significant movement or vibration.
Factors to Consider When Choosing Camera Module Adhesive
When choosing a camera module adhesive, there are several factors to consider:
- Bonding strength: The adhesive should be strong enough to hold the camera module in place and withstand any vibrations or shocks that may occur during use.
- Compatibility: The adhesive should be compatible with the materials of both the camera module and the device it is attached to. This will ensure that it does not react or damage any components.
- Temperature resistance: The adhesive should withstand the temperature range the device will be exposed to during use. This is especially important for devices that may be used in extreme conditions.
- Moisture resistance: The adhesive should be resistant to moisture and humidity, as this can cause it to degrade over time and potentially affect the performance of the camera module.
- Application method: The adhesive should be easy to apply and not require specialized equipment or training.
- Curing time: The adhesive should have a reasonable curing time to bond correctly and securely to the device.
- Cost: The adhesive’s cost should be considered, as some options may be more expensive than others.
Overall, it is essential to choose an adhesive that meets the specific requirements of the device and its intended use while also considering factors such as bonding strength, compatibility, temperature and moisture resistance, application method, curing time, and cost.
Compatibility with Camera Module Materials
The compatibility of camera module materials depends on several factors, such as the type of camera module, the environmental conditions the camera will be exposed to, and the intended use of the camera module.
For example, if the camera module is intended for harsh environmental conditions such as high temperature or humidity, choosing materials that can withstand those conditions is essential. Similarly, materials with UV resistance may be necessary if the camera module is intended for outdoor applications.
Camera module materials should be able to provide optical clarity, mechanical stability, and durability. Common materials used for camera modules include glass, plastic, and ceramic.
Glass is popular due to its optical clarity and scratch resistance, but it can be heavy and brittle. Plastic materials such as polycarbonate and acrylic are lightweight and durable, but they may scratch easily and can degrade over time with exposure to UV radiation.
Ceramic materials offer a good balance of optical clarity and durability, but they can be challenging to manufacture and may be more expensive than other materials.
Ultimately, the choice of camera module materials will depend on the specific requirements of the application and the trade-offs between optical performance, mechanical stability, and durability.
Viscosity and Rheology
Viscosity is a measure of a fluid’s resistance to flow. It is a property of liquids that describes their internal friction or the molecules’ resistance to moving past each other. High-viscosity fluids are thick and flow slowly, while low-viscosity fluids are thin and flow quickly.
Rheology studies the deformation and flow of matter, including liquids, solids, and gases. It encompasses the study of both viscosity and elasticity and other properties such as yield stress, shear stress, and strain rate.
Viscosity and rheology are closely related, as consistency is one of the critical parameters used in rheological studies. A material’s rheology describes how it behaves under stress or strain and how it responds to changes in temperature, pressure, and other variables. Rheological measurements can be used to determine the flow properties of a fluid, the mechanical properties of a solid, and other essential characteristics that affect its performance in various applications.
Curing Time and Temperature
Curing time and temperature are essential factors in various industries, such as manufacturing, construction, and coatings.
Curing refers to allowing a material to set or harden through a chemical reaction or physical process. The time and temperature required for curing depend on the type of material and the desired properties of the finished product.
For example, in the manufacturing of composites, curing time and temperature are critical factors that affect the final product’s strength, stiffness, and durability. The curing process involves applying heat and pressure to the composite material, which activates the resin and causes it to harden. The temperature and duration of the curing process will depend on the specific resin system used, as well as the size and thickness of the composite parts.
Curing time and temperature are also critical factors in the coatings industry in achieving a durable and long-lasting finish. The curing process involves a chemical reaction between the coating and the substrate, creating a solid bond. The curing time and temperature will depend on the type of coating and the conditions of the environment in which the coating is applied.
In construction, curing time and temperature are essential factors in the setting and hardening of concrete. The curing process involves keeping the concrete moist and at a consistent temperature for a specified period of time to allow the cement to hydrate and harden. The curing time and temperature will depend on the type of cement used, the ambient conditions, and the size and thickness of the concrete.
The proper curing time and temperature are critical to ensuring the desired properties and performance of various materials and products.
Bond Strength and Durability
Bond strength refers to the ability of an adhesive to hold two surfaces together. It is typically measured in pounds per square inch (psi) and depends on factors such as the type of adhesive, the materials being bonded, and the surface preparation.
Durability refers to the ability of the bond to withstand external stresses, such as temperature changes, moisture, and mechanical forces, without losing its strength or integrity over time.
The bond strength and durability of an adhesive are closely related. A strong bond is generally more durable, as it can withstand more stress without breaking. However, the durability of the bond also depends on other factors, such as the environment in which it is used and the materials being bonded.
To ensure a strong and durable bond, it is essential to select the suitable adhesive for the materials being bonded, prepare the surfaces correctly, and follow the manufacturer’s instructions for application and curing. Regular maintenance and monitoring of the bond can also ensure its long-term durability.
Ease of Application and Dispensing
Ease of application and dispensing refers to the convenience and simplicity with which a product can be applied or dispensed. It is essential for many consumer products, especially those used frequently, such as personal care items, cleaning supplies, and food products.
Ease of application and dispensing can be influenced by several factors, including the design of the product packaging, the viscosity and texture of the product, and the type of dispensing mechanism used.
For example, a lotion in a pump bottle may be easier to apply than one in a jar, as it eliminates the need for the user to scoop the product out with their fingers. Similarly, a cleaning product in a spray bottle may be easier to dispense and apply than one pouring from a larger container.
Manufacturers strive to create products that are easy to apply and dispense, as they can improve the user experience and increase customer satisfaction. However, it is also important to balance ease of use with other factors, such as product safety, efficacy, and cost.
Cost and Availability
Ease of application and dispensing refers to the convenience and simplicity with which a product can be applied or dispensed. It is essential for many consumer products, especially those used frequently, such as personal care items, cleaning supplies, and food products.
Ease of application and dispensing can be influenced by several factors, including the product packaging design, the product’s viscosity and texture, and the type of dispensing mechanism used.
For example, a lotion in a pump bottle may be easier to apply than one in a jar, as it eliminates the need for the user to scoop the product out with their fingers. Similarly, a cleaning product in a spray bottle may be easier to dispense and apply than one pouring from a larger container.
Manufacturers strive to create products that are easy to apply and dispense, as they can improve the user experience and increase customer satisfaction. However, it is also important to balance ease of use with other factors, such as product safety, efficacy, and cost.
How is Camera Module Adhesive Applied?
The process of applying adhesive to a camera module can vary depending on the specific type of adhesive being used and the manufacturing process of the camera module. However, here is a general overview of the steps involved in applying adhesive to a camera module:
- Prepare the camera module: The module must be clean and dry before applying adhesive. Any dust, dirt, or moisture on the camera module’s surface can affect the adhesive’s bonding.
- Apply the adhesive: Depending on the type of adhesive being used, it may be applied manually or with the help of an automated dispenser. The adhesive is involved in a specific pattern to ensure it covers the areas where the camera module will be attached to the device.
- Place the camera module: Once the adhesive has been applied, the camera module is carefully positioned onto the device. The camera module must be aligned correctly to ensure it is positioned perfectly.
- Cure the adhesive: Depending on the adhesive being used, it may need to be cured before the camera module can be used. Curing can be done through various methods, such as heat or UV light.
- Test the camera module: After the adhesive has been cured, it is tested to ensure it is securely attached to the device and functioning correctly.
Overall, applying adhesive to a camera module requires precision and careful attention to detail to ensure that the camera module is attached securely and functions correctly.
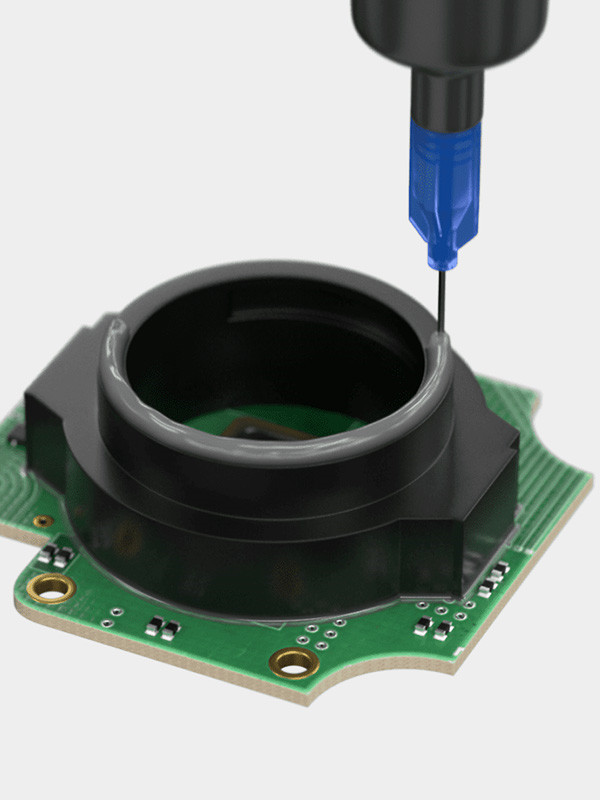
Manual Application vs. Automated Application
Manual and automated applications refer to two different methods of completing a task or process, one done by human labor and the other by software or machines. Here are some key differences between manual and automated applications:
Manual application:
- Done by human labor
- It can be time-consuming and prone to errors
- It can require a high degree of skill or training
- Offers flexibility in adapting to unique or changing situations
- It can be difficult to scale or replicate across multiple instances
Automated application:
- Done by software or machines
- It can be faster and more accurate than a manual application
- Can be programmed to perform complex tasks
- Offers consistent results and reduces the likelihood of errors
- Can handle large volumes of data or tasks
- It can be expensive to develop and maintain
- It may not be as flexible as a manual application in adapting to unique or changing situations
Surface Preparation and Cleaning
Surface preparation and cleaning are critical in various industries, such as manufacturing, construction, and automotive. These steps are necessary to ensure that surfaces are free from contaminants and are adequately prepared for further processing or coating.
The following are some standard methods of surface preparation and cleaning:
- Mechanical cleaning involves physically removing contaminants from the surface using methods such as sandblasting, shot blasting, or scrubbing with abrasive pads. This method often removes rust, paint, and other coatings from metal surfaces.
- Chemical cleaning involves using chemicals to dissolve or break down contaminants on the surface. Examples of chemicals used in this method include acids, alkalis, and solvents. Chemical cleaning is often used for removing oils, greases, and other organic contaminants.
- Electrochemical cleaning involves using an electrical current to remove contaminants from the surface. This method is often used for removing rust and other metal oxides.
- Thermal cleaning: This involves using heat to remove contaminants from the surface. Examples of thermal cleaning methods include flame cleaning and baking. This method often removes paint and other coatings from metal surfaces.
- High-pressure water cleaning involves using a high-pressure water jet to remove contaminants from the surface. This method is often used to clean concrete and other complicated characters with other methods.
It is essential to choose the appropriate surface preparation and cleaning method based on the type of surface and the type of contaminants present. Proper surface preparation and cleaning can improve the adhesion of coatings and ensure the character’s longevity.
Dispensing Techniques and Equipment
Dispensing techniques and equipment are essential tools for delivering medications accurately and efficiently. Here are some standard techniques and equipment used in medication dispensing:
- Automated dispensing systems (ADS): These computerized systems dispense medication using barcodes and scanners to ensure accuracy.
- Medication carts are mobile carts used to store and transport medication from one location to another, often used in healthcare settings.
- Unit-dose packaging: This involves dispensing individual doses of medication into unique packaging labeled with information about the medication.
- Multi-dose packaging: This involves dispensing multiple doses of medication into a single container labeled with information about the medication and the dosing schedule.
- Syringes and needles: These are used to draw up and administer medication orally or through injection.
- Oral syringes: These are used to measure and dispense liquid medications for oral administration.
- Pill crushers and pill cutters: These are used for crushing or cutting pills into smaller pieces to make them easier to swallow.
- Electronic prescribing (e-prescribing): This technology allows healthcare providers to electronically send prescriptions to pharmacies, eliminating the need for paper prescriptions.
- IV pumps: These are used to administer the medication directly into a patient’s bloodstream through an intravenous (IV) line.
- Inhalers and nebulizers: These are used to deliver medication directly to the lungs for respiratory conditions.
These techniques and equipment help ensure accurate and safe medication dispensing, essential for patient health and well-being.
Handling and Storage of Camera Module Adhesive
Camera module adhesive is a specialized adhesive used to attach camera modules to electronic devices such as smartphones, laptops, and tablets. Handling and storing camera module adhesive is essential to remain effective and safe. Here are some guidelines for handling and storing camera module adhesive:
- Handling: When handling camera module adhesive, wearing appropriate personal protective equipment (PPE), such as gloves and safety glasses, is essential. This will help to prevent skin contact and eye exposure to the adhesive. Always follow the manufacturer’s instructions for handling and application of the adhesive.
- Storage: Camera module adhesive should be stored in a cool, dry place away from direct sunlight and heat sources. Exposure to heat and sunlight can cause the adhesive to deteriorate and lose effectiveness. The adhesive should also be stored in a tightly sealed container to prevent contamination and moisture absorption.
- Shelf life: The shelf life of the camera module adhesive varies depending on the manufacturer and the specific product. Always check the expiration date on the container before using the adhesive. The expired adhesive should be disposed of properly.
- Application: Follow the manufacturer’s instructions carefully when applying the camera module adhesive. Use only the recommended amount of adhesive to ensure proper bonding. Excessive application of adhesive can lead to incomplete bonding and may cause damage to the device.
- Disposal: Unused or expired camera module adhesive should be disposed of properly according to local regulations. Do not dispose of adhesive in the regular trash or pour it down the drain.
Proper handling and storage of camera module adhesive are essential to remain effective and safe. Always follow the manufacturer’s instructions and take appropriate precautions when handling and applying the adhesive.
Shelf Life and Expiration
The shelf life and expiration of camera module adhesive can vary depending on several factors, such as the type of adhesive, storage conditions, and manufacturing date.
Generally, most camera module adhesives have a shelf life of approximately six months to one year from the date of manufacture as long as they are stored in a cool, dry place away from direct sunlight and extreme temperatures. However, some types of adhesives may have a longer or shorter shelf life.
It is important to note that the shelf life of the camera module adhesive does not necessarily indicate its expiration date, instead, it refers to the period during which the adhesive can be stored and used while maintaining its proper properties and performance. After the expired shelf life, the adhesive may degrade and lose effectiveness, resulting in reduced bonding strength and other issues.
To determine the actual expiration date of a camera module adhesive, it is recommended to check the product label or consult the manufacturer’s documentation for specific guidance. Following proper storage and handling procedures is essential to ensure the adhesive maintains its effectiveness for as long as possible.
Precautions and Safety Measures
Camera module adhesive can be hazardous if not handled and used correctly. Following precautions and safety measures is essential to ensure the adhesive is used safely and effectively. Here are some necessary precautions and safety measures to keep in mind when working with camera module adhesive:
- Wear protective gear: Always wear protective gear such as gloves, safety glasses, and a mask when handling camera module adhesive. This will protect you from any fumes or irritants released during application.
- Work in a well-ventilated area: Use camera module adhesive in a well-ventilated area to avoid inhaling any harmful fumes. Open windows or use exhaust fans to ensure proper ventilation.
- Avoid skin contact: Avoid direct skin contact with the adhesive, as it can cause skin irritation or allergic reactions. If skin contact occurs, immediately wash the affected area with soap and water.
- Store the adhesive correctly: Store the adhesive in a cool, dry place away from direct sunlight and extreme temperatures. Follow the manufacturer’s instructions for proper storage and handling.
- Use the adhesive as intended: Only use it for its intended purpose and follow the manufacturer’s instructions carefully.
- Dispose of the adhesive properly: Dispose of any unused adhesive or packaging material according to local regulations and guidelines.
By following these precautions and safety measures, you can minimize the risks associated with camera module adhesive and ensure it is used safely and effectively.
Common Issues with Camera Module Adhesive
Camera module adhesive is an essential component of camera manufacturing, and any issues can impact the final product’s quality and reliability. Here are some common problems with camera module adhesive that manufacturers may encounter:
- Poor bonding: One of the most common issues with camera module adhesive is poor bonding. This can occur due to improper application, inadequate curing time, or using an incompatible glue for the camera module material.
- Uneven adhesive distribution: Uneven adhesive distribution can result in an inconsistent bond and cause issues with image quality. This can occur if the adhesive is not applied evenly or if the camera module is not pressed firmly against the adhesive during the bonding process.
- Air bubbles: Air bubbles trapped in the adhesive layer can cause bonding issues and affect image quality. This can occur if the adhesive needs to be appropriately mixed or applied in a controlled environment.
- Delamination occurs when the adhesive bond between the camera module and the device housing fails, resulting in separation. This can happen due to environmental factors such as high temperatures or humidity exposure.
- Contamination: Contamination of the adhesive with dust, oil, or other particles can impact its bonding performance and result in poor image quality.
- Compatibility issues: Using an incompatible adhesive with the camera module material can cause bonding issues and impact the overall quality and reliability of the camera module.
To minimize these issues, it is essential to use a high-quality adhesive compatible with the camera module material, follow proper application procedures, and conduct thorough quality control tests during manufacturing.
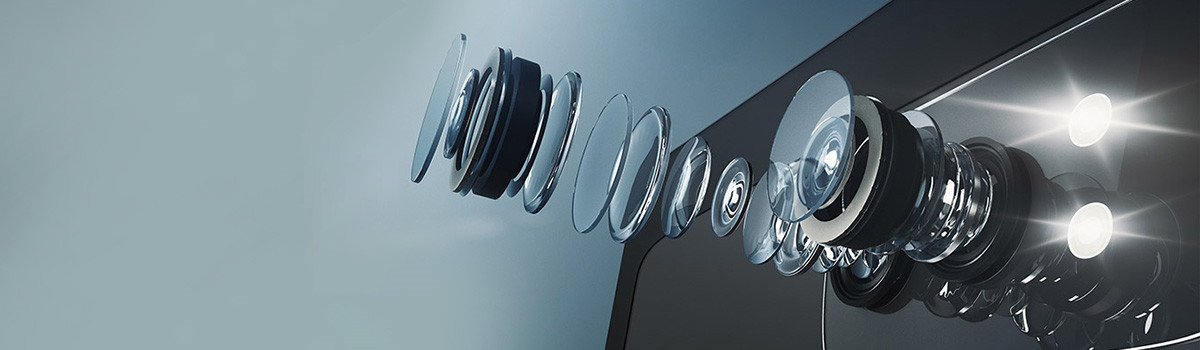
Adhesive Residue and Contamination
Adhesive residue and contamination are common in various industries, including manufacturing, automotive, and construction. Sticky residue refers to the leftover adhesive material that remains after removing a previously applied adhesive. Contamination, on the other hand, occurs when unwanted foreign particles or substances adhere to a surface or material, affecting its quality and performance.
Adhesive residue can be challenging and require specialized cleaning agents and tools. Some standard methods for removing adhesive residue include using solvents, scraping, sanding, or heat. Following proper safety precautions when handling solvents or heat is essential, as they can be hazardous to your health.
Contamination can occur for various reasons, such as improper handling, storage, or processing. Contaminants can include dust, dirt, oil, or chemicals and can impact the product’s or material’s performance and safety. Preventing contamination involves following proper handling procedures, using appropriate protective equipment, and maintaining clean workspaces and tools.
Overall, it’s crucial to address adhesive residue and contamination promptly and effectively to ensure the safety and quality of the product or material.
Inconsistent Bond Strength
The inconsistent bond strength of camera module adhesive can be caused by various factors, including variations in the manufacturing process, differences in the materials used, or environmental factors such as temperature and humidity.
One possible solution is to carefully control the manufacturing process to ensure consistent adhesive application and monitor the environmental conditions during production. This can reduce the variability in the bond strength of the adhesive.
Another solution is to use a different type of adhesive that is less prone to bond strength variability. For example, some manufacturers may switch from a solvent-based adhesive to a heat-cured adhesive, which can provide more consistent results.
It is also essential to test and validate the adhesive’s bond strength under various conditions, such as temperature and humidity, to ensure that it will perform consistently over time. This can help identify potential issues early on and prevent problems from occurring later.
Overall, the inconsistent bond strength of the camera module adhesive can be a challenging problem to solve. Still, it is possible to minimize variability and ensure consistent performance by carefully controlling the manufacturing process and testing the adhesive under various conditions.
Thermal and Environmental Degradation
Thermal and environmental degradation are two types of material degradation that occur over time and can negatively affect the properties and performance of a material.
Thermal degradation is when a material breaks down or loses its strength and integrity due to exposure to high temperatures. This can happen for several reasons, such as exposure to heat, radiation, or chemical reactions at high temperatures. For example, when a plastic material is exposed to high temperatures, it may break down and release toxic gasses.
On the other hand, environmental degradation is the process by which a material breaks down due to exposure to environmental factors such as moisture, sunlight, and chemicals. This can happen for several reasons, such as exposure to UV radiation, chemicals, or contact with water. For example, when a metal material is exposed to water, it may corrode and lose its strength and integrity.
Both types of degradation can harm materials and lead to reduced performance and durability. To prevent thermal and environmental degradation, selecting suitable materials and protective coatings that can withstand specific environmental conditions and temperature ranges is essential. Proper maintenance and storage practices can also help prevent or minimize degradation over time.
Failure Modes and Analysis
Camera module adhesive issues can lead to various failure modes, such as poor image quality, camera module detachment, and complete failure of the camera system. A failure mode and effects analysis (FMEA) can be conducted to identify potential failure modes and their causes and to develop strategies for preventing or mitigating them.
The following are some of the potential failure modes and their causes:
- Poor image quality can occur if the camera module is not securely attached to the device, resulting in movement or vibration during image capture. This can be caused by insufficient adhesive strength, poor coverage, or improper curing.
- Camera module detachment: This can occur if the adhesive does not provide sufficient bond strength or if contaminants are being bonded on the surfaces. Contaminants can prevent proper bonding and weaken the adhesive strength.
- Complete failure of the camera system can occur if the camera module becomes detached from the device or if the adhesive degrades over time. This can be caused by exposure to high temperatures, humidity, or chemicals that can weaken or degrade the adhesive.
To prevent or mitigate these failure modes, several strategies can be employed, including:
- Using a high-strength adhesive appropriate for the specific application and environmental conditions.
- Ensuring proper surface preparation, including cleaning and removing any contaminants from the surfaces to be bonded.
- Ensuring proper curing and handling of the adhesive to achieve the desired bond strength.
- Conducting regular quality control checks ensures that the adhesive performs as expected.
- Consider using additional mechanical fasteners or other bonding methods to provide redundancy and improve overall reliability.
By identifying potential failure modes and implementing strategies to prevent or mitigate them, camera module adhesive issues can be minimized or eliminated, resulting in improved camera performance and reliability.
How to Troubleshoot Camera Module Adhesive Issues
If you are experiencing adhesive issues with your camera module, there are several steps you can take to troubleshoot the problem. Here are some possible solutions:
- Clean the adhesive surface: First, make sure the surface where the adhesive is supposed to stick is clean and debris-free. Use a soft, lint-free cloth and some isopropyl alcohol to clean the surface.
- Use a stronger adhesive: If the current adhesive isn’t holding the camera module securely in place, try using a stronger adhesive. You can purchase stronger adhesives from hardware stores or online. However, make sure the adhesive you choose is safe for electronic components and won’t cause damage to the camera module.
- Replace the adhesive: If it is old or has been exposed to extreme temperatures, it may have lost its effectiveness. In this case, you may need to replace the adhesive with a new one.
- Reapply the adhesive: If the adhesive is still in good condition, but the camera module is not sticking correctly, try reapplying the adhesive. Remove the old adhesive from the camera module and the surface it’s supposed to stick to. Apply a new adhesive layer, ensuring it’s evenly distributed and covers the entire surface area.
- Seek professional help: If none of these solutions work, it may be time to seek professional help. Take your camera module to an experienced technician who can assess the issue and provide a solution.
Overall, it’s essential to be careful when troubleshooting camera module adhesive issues. Mishandling the camera module or using the wrong type of adhesive can cause damage to the camera module or render it unusable.
Removal and Replacement of Camera Module Adhesive
Removing and replacing camera module adhesive can be a delicate process, as the camera module is a sensitive component in most electronic devices such as smartphones, tablets, and laptops. Here are the steps to remove and replace the camera module adhesive:
- Turn off the device and remove the battery if possible. This will prevent any electrical current from flowing through the machine and minimize the risk of damage.
- Use a plastic pry tool or a thin metal spudger to gently pry the camera module away from the device. Be careful not to damage any other components or flex cables that may be in the way.
- Use a heat gun or a hairdryer to heat the adhesive around the camera module. This will make the adhesive more pliable and easier to remove.
- Gently lift the camera module off the adhesive. If the adhesive is particularly stubborn, you can use a plastic pry tool to help lift it off.
- Use a clean cloth or alcohol wipe to clean the area around the camera module. Make sure there is no residue or debris left behind.
- Apply a small amount of new adhesive to the back of the camera module. Be careful not to apply too much, as this can cause the module to be misaligned or challenging to reattach.
- Carefully reattach the camera module to the device, ensuring it is aligned correctly. Press down firmly to ensure a secure fit.
- Leave the device to rest for at least 24 hours before using it again. This will give the adhesive time to cure and set properly.
It is important to note that the above steps are general guidelines and may not apply to all devices. It is always recommended to refer to the manufacturer’s instructions or seek professional assistance if \you need clarification on the process.
Recycling and Disposal of Camera Module Adhesive
The recycling and disposal of camera module adhesive depend on the adhesive used. In general, camera module adhesive can be categorized into thermal and optical adhesive.
Thermal adhesive is commonly used in camera modules to bond the lens holder and image sensor. This adhesive can be removed by heating the camera module to a high temperature, softening it, and allowing it to be scraped off. The removed adhesive can be disposed of as regular waste.
The optical adhesive is used to bond the lens to the lens holder and is more difficult to remove than thermal adhesive. This adhesive requires special solvents to dissolve it, and the process must be done carefully to avoid damaging the lens or other components. After removing the adhesive, the solvent and residue should be disposed of correctly as hazardous waste.
Generally, it is best to consult with the manufacturer or professional recycling service to determine the appropriate recycling method or disposal of the camera module adhesive. Handling any hazardous waste with care and following local regulations to protect the environment and human health is essential.
Future Trends and Developments in Camera Module Adhesive Technology
Camera module adhesive technology is a critical aspect of smartphone manufacturing. As consumers demand more advanced camera features, camera module adhesive technology must evolve to meet those demands. Here are some potential future trends and developments in camera module adhesive technology:
- Thinner adhesives: As smartphones become thinner and more compact, camera module adhesives will also need to become thinner. This will require developing new adhesive materials that strengthen bonding while being light enough to fit into tight spaces.
- Stronger adhesives: With more advanced camera features, such as higher resolution and optical zoom, camera module adhesives must be more robust to ensure the camera module remains stable and does not shift during use.
- Higher temperature resistance: As smartphone processors become more powerful, they generate more heat, which can affect the adhesive holding the camera module in place. Camera module adhesives with higher temperature resistance will be necessary to ensure the module remains secure even under high operating temperatures.
- Improved vibration resistance: Vibration can cause the camera module to shift, resulting in blurred images or other issues. Improved vibration resistance in camera module adhesives can help ensure the camera remains stable even under high vibration conditions.
- More environmentally friendly adhesives: Consumers are increasingly concerned about the environmental impact of their products. Camera module adhesive technology that uses more environmentally friendly materials, such as bio-based adhesives or adhesives that can be easily recycled, will be more in demand in the future.
- Improved automated manufacturing processes: As smartphone production volumes increase, camera module adhesive applications must become more automated and efficient. New manufacturing processes, such as robotic adhesive applications, will be necessary to keep up with the demand for smartphones with advanced camera features.
Overall, camera module adhesive technology will continue to evolve in response to the demand for more advanced smartphone camera features. The development of thinner, stronger, and more environmentally friendly adhesives, as well as improvements in temperature and vibration resistance, will be essential to ensure that smartphone manufacturers can meet the needs of consumers in the future.