Insulating Epoxy Coating
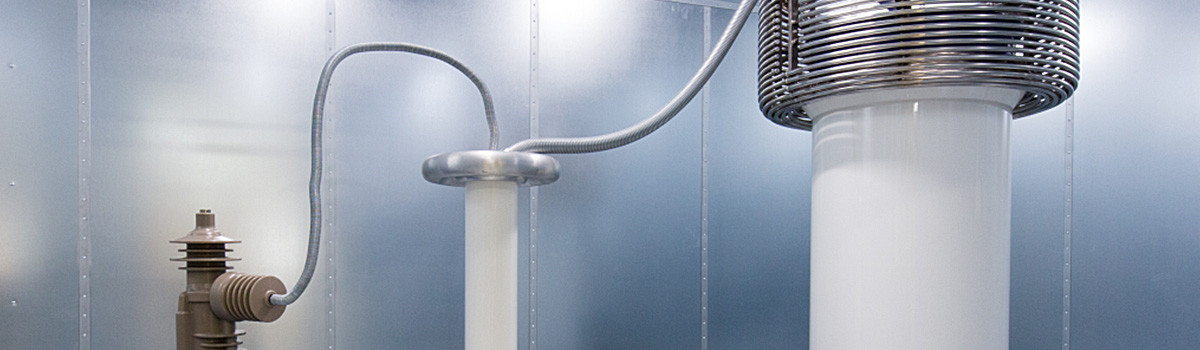
Insulating epoxy coating is a versatile and widely used material with excellent electrical insulation properties. Various industries commonly employ it to protect electrical components, circuit boards, and other sensitive equipment from moisture, dust, chemicals, and physical damage. This article aims to delve into insulating epoxy coating, highlighting its applications, benefits, and critical considerations for selecting the suitable layer for specific needs.
Understanding Insulating Epoxy Coating
Insulating epoxy coating is a protective coating that provides insulation and electrical conductivity resistance to various surfaces. It is commonly used in electronics, electrical, automotive, and aerospace industries to protect and enhance the performance of electrical components.
The primary purpose of insulating epoxy coatings is to prevent the flow of electric current between conductive materials. These coatings are applied to surfaces vulnerable to electrical short circuits, corrosion, or damage from environmental factors. The epoxy material acts as an insulator, preventing the transfer of electrons and minimizing the risk of electrical failures or malfunctions.
Insulating epoxy coatings are typically made from a combination of epoxy resin, a thermosetting polymer, and a hardening agent. The epoxy resin provides excellent adhesion, chemical resistance, and mechanical strength, while the hardening agent triggers the cross-linking reaction that converts the liquid epoxy into a solid, durable coating.
The application of insulating epoxy coatings involves several steps. First, the surface to be coated is thoroughly cleaned and prepared to ensure proper adhesion. Any dirt, grease, or contaminants must be removed to create a clean bonding surface. Then, the epoxy coating is mixed according to the manufacturer’s instructions and applied to the surface using spraying, brushing, or dipping techniques.
Once applied, the epoxy coating undergoes a curing process, during which it hardens and forms a protective barrier. Curing can be achieved through various methods, including heat, chemicals, or both. Curing enhances the coating’s mechanical properties, adhesion strength, and chemical resistance.
Insulating epoxy coatings offer several benefits:
- They provide electrical insulation, preventing the flow of electric current and reducing the risk of short circuits or electrical breakdowns.
- These coatings offer excellent protection against environmental factors such as moisture, chemicals, and abrasion, extending the lifespan of coated components.
- Insulating epoxy coatings can enhance surfaces’ thermal stability and flame resistance, making them suitable for applications in high-temperature environments.
The Importance of Electrical Insulation
Electrical insulation plays a crucial role in maintaining electrical systems’ safety, reliability, and efficiency. It involves using materials and techniques to prevent the flow of electric current between conductive components or surfaces. Here are some key reasons highlighting the importance of electrical insulation:
- Protection against electrical shocks: Electrical insulation prevents direct contact with live conductors, reducing the risk of electric shock. It acts as a barrier that inhibits the flow of electric current through non-conductive materials, safeguarding individuals from potential harm.
- Prevention of short circuits and electrical fires: Insulation helps prevent unintended electrical contact between conductive materials, which can lead to short circuits and electrical fires. Insulating wires, cables, and electrical components minimize the likelihood of electrical arcing, sparks, and overheating, significantly reducing the risk of fires and equipment damage.
- Enhanced electrical performance: Insulation materials with high dielectric strength and low electrical conductivity improve the overall performance of electrical systems. They maintain proper voltage levels, prevent leakage currents, and reduce signal interference or distortion, ensuring the optimal functioning of electrical circuits and devices.
- Protection against environmental factors: Electrical insulation materials resist moisture, chemicals, dust, and other contaminants. This protection helps prevent corrosion, degradation, and insulation breakdown caused by external factors, thereby maintaining the longevity and reliability of electrical components.
- Increased energy efficiency: Insulation reduces energy loss and improves the efficiency of electrical systems. By preventing current leakage, insulation minimizes power wastage and enhances the transmission and distribution of electrical energy, resulting in reduced energy consumption and lower operational costs.
- Compliance with safety standards and regulations: Electrical insulation is essential for meeting safety standards and regulations set by authorities and industry organizations. Compliance with these requirements ensures that electrical installations and equipment are designed and operated to minimize risks to personnel, property, and the environment.
- Protection of sensitive equipment: Insulation is critical in protecting sensitive electrical and electronic equipment from electrical disturbances and voltage surges. Insulating materials, such as varnishes or coatings, shield delicate components from electromagnetic interference (EMI) and electrostatic discharge (ESD), preserving their functionality and extending their lifespan.
Applications of Insulating Epoxy Coating
Insulating epoxy coating is a specialized coating that offers excellent electrical insulation properties, making it suitable for various applications. This coating typically comprises an epoxy resin, providing insulating capabilities and protective qualities. Here are some of the critical applications of insulating epoxy coating:
- Electronics and Electrical Components: Insulating epoxy coating is extensively used in the electronics and electrical industry. It is applied to components such as circuit boards, transformers, capacitors, and coils to provide electrical insulation, preventing short circuits and enhancing these components’ overall reliability and lifespan. The coating also protects against moisture, dust, and other environmental contaminants.
- Power Generation and Transmission: Insulating epoxy coatings are crucial in power generation and transmission systems. They are applied to insulators, switchgear, busbars, and other high-voltage equipment to prevent electrical leakage, corona discharge, and flashovers. By providing high dielectric strength, the coating helps maintain the integrity and safety of electrical infrastructure.
- Motors and Generators: Electric motors and generators require insulation to prevent electrical breakdown and ensure efficient performance. Insulating epoxy coatings are applied to these machines’ windings and other critical parts. The coating enhances electrical insulation, improves heat dissipation, and offers protection against chemicals, moisture, and mechanical stress.
- Automotive Industry: Insulating epoxy coatings find various applications in the automotive sector. They insulate electrical connections, terminals, and wiring harnesses in vehicles. The layer helps maintain electrical integrity, prevents short circuits, and safeguards against corrosion, vibration, and thermal cycling. It is also used for insulating components in hybrid and electric vehicles.
- Aerospace and Defense: Insulating epoxy coatings is vital in the aerospace and defense sectors. They are applied to electronic systems, avionics, radar equipment, and communication systems to ensure reliable performance in challenging environments. The coating protects against electrical interference, radiation, humidity, and extreme temperatures.
- Coating for Printed Circuit Boards (PCBs): PCBs are the backbone of electronic devices. Epoxy coatings protect PCBs’ circuitry and solder joints from moisture, dust, and other contaminants. The coating also provides insulation between the conductive layers, preventing short circuits and enhancing the overall durability of the boards.
- Chemical and Corrosion Resistance: Insulating epoxy coatings offer excellent chemical resistance and can protect surfaces from corrosive substances. They are used in chemical processing, oil and gas, and wastewater treatment. The coating prevents chemical attacks, enhances equipment longevity, and minimizes maintenance requirements.
- Electrical Encapsulation: Insulating epoxy coatings are utilized for electrical encapsulation, particularly in applications where moisture or other contaminants pose a risk. It is commonly used for potting and encapsulating electronic components, sensors, and connectors. The coating forms a protective barrier against environmental factors and mechanical stress.
Protection for Electronic Components
Protection for electronic components is crucial to ensure their proper functioning and longevity. Electronic components are often sensitive to environmental factors such as temperature, humidity, electrical noise, and physical stress. With adequate protection, these components can be protected and even rendered inoperable. Here are some standard methods and techniques used to safeguard electronic components:
- Enclosures: Electronic components can be housed in protective enclosures, such as cases, cabinets, or boxes. Sections provide physical protection against dust, moisture, and other contaminants. They also shield the components from accidental impact or mishandling.
- EMI/RFI Shielding: Electromagnetic interference (EMI) and radio frequency interference (RFI) can disrupt the regular operation of electronic components. EMI/RFI shielding involves using conductive materials, such as metal coatings or conductive gaskets, to create a Faraday cage effect. This shielding prevents external electromagnetic signals from interfering with the sensitive electronics.
- Thermal Management: Electronic components generate heat during operation, and excessive heat can degrade their performance and reliability. Thermal management techniques like heat sinks, fans, and thermal pads help dissipate heat and maintain optimal operating temperatures. Heat sinks absorb and dissipate heat, while fans facilitate airflow. Thermal pads provide a thermal interface between the component and the heat sink for efficient heat transfer.
- Surge Protection: Power surges caused by lightning strikes, electrical faults, or switching transients can damage electronic components. Surge protection devices, like surge suppressors or metal oxide varistors (MOVs), divert excess voltage to protect the members. These devices limit the voltage levels and prevent transient spikes from reaching the sensitive components.
- Environmental Sealing: In specific applications, electronic components need protection from harsh environmental conditions, such as moisture, chemicals, or extreme temperatures. Environmental sealing techniques, such as conformal coatings, potting compounds, or hermetic sealing, create a barrier that safeguards the components from these elements.
- Circuit Protection: Electronic components can be vulnerable to overvoltage, overcurrent, and electrostatic discharge (ESD). Circuit protection devices, such as fuses, circuit breakers, transient voltage suppressors (TVS diodes), and ESD protection diodes, are employed to limit and redirect excessive current, voltage, or static charges away from the components.
- Grounding and Bonding: Proper grounding and bonding techniques are essential for protecting electronic components from electrical noise and ensuring safety. Grounding provides a path to the dissipation of unwanted electrical charges. In contrast, bonding reduces potential differences that could cause damage. Grounding and bonding techniques include using ground planes, wires, and typical ground connections.
- Filtering: Electrical noise and interference from various sources can affect the performance of electronic components. Filters like low-pass, high-pass, or electromagnetic interference filters can eliminate or reduce unwanted signals and ensure clean power delivery to the members.
- Anti-Static Measures: Electrostatic discharge (ESD) can cause significant damage to electronic components. Anti-static measures, such as ESD-safe workstations, wrist straps, and packaging materials, prevent static charges from accumulating and discharging into sensitive parts.
- Regular Maintenance and Testing: Regular maintenance, inspection, and testing are essential to identify potential issues with electronic components. Periodic checks ensure that protective measures function correctly and that any faults or failures are promptly addressed.
Electronic components can be safeguarded from environmental hazards, electrical disturbances, and physical damage by employing these protection techniques. This ensures their reliable operation and extends their lifespan, leading to improved performance and reduced downtime.
Circuit Board Coating
Circuit board coating is a crucial process in electronics manufacturing that involves applying a protective layer over the printed circuit board (PCB). This coating provides insulation, protection against environmental factors, and enhances the reliability and longevity of the circuitry. In this article, we will explore the importance of circuit board coating and the different types of coatings used.
The primary purpose of circuit board coating is to safeguard the delicate electronic components from various environmental stresses. These stresses include moisture, dust, dirt, chemicals, and temperature fluctuations, which can lead to corrosion, short circuits, and other failures. The coating acts as a barrier, preventing these harmful elements from reaching the circuitry and causing damage.
There are several types of coatings available for circuit boards, each offering specific benefits depending on the application requirements. One common type is conformal coating, which is a thin protective film applied directly onto the PCB surface. Conformal coatings can be made of various materials, including acrylics, urethanes, silicones, and epoxy resins. These coatings conform to the shape of the circuit board, covering all components and exposed traces, and provide excellent protection against moisture, dust, and chemical contaminants.
Another type of coating is the encapsulation or potting compound, which is a thicker material that covers the entire PCB, encapsulating it completely. Potting compounds are typically made of epoxy or polyurethane and offer superior protection against mechanical stress, vibration, and extreme temperatures. They are commonly used in applications where the circuit boards are exposed to harsh environments or high levels of physical stress.
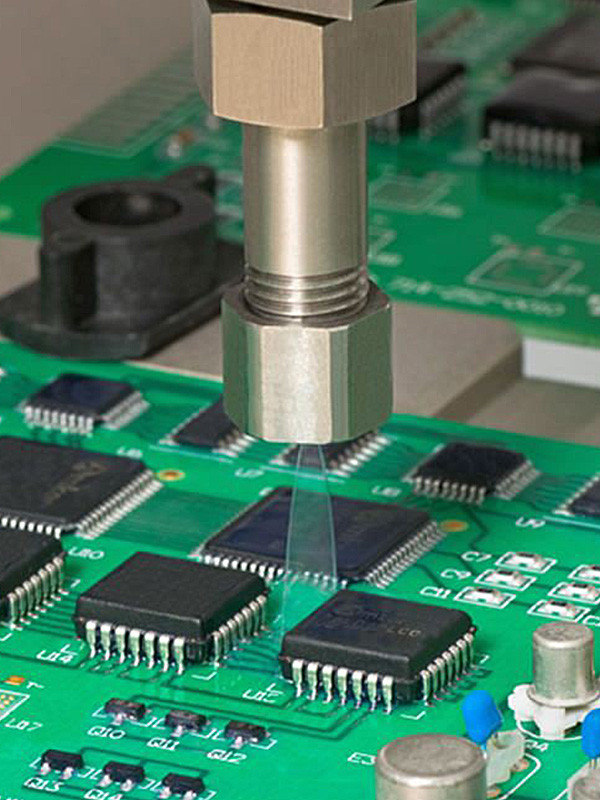
The coating process itself involves careful application techniques to ensure uniform coverage and proper adhesion. Different methods can be employed, such as spray coating, dip coating, or selective coating. Spray coating involves using a spray gun or atomizer to apply a fine mist of the coating material onto the PCB. Dip coating, on the other hand, immerses the PCB into a bath of the coating material, allowing it to fully coat the board. Selective coating is a precise method that applies the coating only to specific areas of the PCB, leaving other components uncoated for accessibility.
In addition to environmental protection, circuit board coatings also offer electrical insulation properties. The coating material has a high dielectric strength, which prevents the leakage of current between closely spaced traces or components. This is especially important in high-voltage applications where electrical isolation is critical.
Motor and Transformer Insulation
Protection for electronic components is crucial to ensure their proper functioning and longevity. Electronic components are often sensitive to environmental factors such as temperature, humidity, electrical noise, and physical stress. With adequate protection, these components can be protected and even rendered inoperable. Here are some standard methods and techniques used to safeguard electronic components:
- Enclosures: Electronic components can be housed in protective enclosures, such as cases, cabinets, or boxes. Sections provide physical protection against dust, moisture, and other contaminants. They also shield the components from accidental impact or mishandling.
- EMI/RFI Shielding: Electromagnetic interference (EMI) and radio frequency interference (RFI) can disrupt the regular operation of electronic components. EMI/RFI shielding involves using conductive materials, such as metal coatings or conductive gaskets, to create a Faraday cage effect. This shielding prevents external electromagnetic signals from interfering with the sensitive electronics.
- Thermal Management: Electronic components generate heat during operation, and excessive heat can degrade their performance and reliability. Thermal management techniques like heat sinks, fans, and pads help dissipate heat and maintain optimal operating temperatures. Heat sinks absorb and dissipate heat, while fans facilitate airflow. Thermal pads provide a thermal interface between the component and the heat sink for efficient heat transfer.
- Surge Protection: Power surges caused by lightning strikes, electrical faults, or switching transients can damage electronic components. Surge protection devices, like surge suppressors or metal oxide varistors (MOVs), divert excess voltage to protect the members. These devices limit the voltage levels and prevent transient spikes from reaching the sensitive components.
- Environmental Sealing: In specific applications, electronic components need protection from harsh environmental conditions, such as moisture, chemicals, or extreme temperatures. Environmental sealing techniques, such as conformal coatings, potting compounds, or hermetic sealing, create a barrier that safeguards the components from these elements.
- Circuit Protection: Electronic components can be vulnerable to overvoltage, overcurrent, and electrostatic discharge (ESD). Circuit protection devices, such as fuses, circuit breakers, transient voltage suppressors (TVS diodes), and ESD protection diodes, are employed to limit and redirect excessive current, voltage, or static charges away from the components.
- Grounding and Bonding: Proper grounding and bonding techniques are essential for protecting electronic components from electrical noise and ensuring safety. Grounding provides a path to the dissipation of unwanted electrical charges. In contrast, bonding reduces potential differences that could cause damage. Grounding and bonding techniques include using ground planes, wires, and typical ground connections.
- Filtering: Electrical noise and interference from various sources can affect the performance of electronic components. Filters like low-pass, high-pass, or electromagnetic interference filters can eliminate or reduce unwanted signals and ensure clean power delivery to the members.
- Anti-Static Measures: Electrostatic discharge (ESD) can cause significant damage to electronic components. Anti-static measures, such as ESD-safe workstations, wrist straps, and packaging materials, prevent static charges from accumulating and discharging into sensitive parts.
- Regular Maintenance and Testing: Regular maintenance, inspection, and testing are essential to identify potential issues with electronic components. Periodic checks ensure that protective measures function correctly and that any faults or failures are promptly addressed.
Electronic components can be safeguarded from environmental hazards, electrical disturbances, and physical damage by employing these protection techniques. This ensures their reliable operation and extends their lifespan, leading to improved performance and reduced downtime.
Cable and Wire Insulation
Cable and wire insulation plays a crucial role in electrical systems by providing protection, insulation, and safety. It refers to the outer covering or jacket that surrounds electrical conductors, preventing the flow of electric current to unintended areas and protecting the conductors from environmental factors. The choice of insulation material depends on factors such as voltage rating, temperature range, environmental conditions, and the intended application.
One of the commonly used insulation materials is thermoplastic. Thermoplastic insulation is flexible, durable, and resistant to abrasion and chemicals. Polyvinyl chloride (PVC) is a popular thermoplastic material known for its affordability and wide range of applications. It is commonly used in low-voltage applications such as household wiring and general-purpose cables. PVC insulation provides good electrical properties and is flame-retardant.
Another widely used insulation material is thermoset. Unlike thermoplastics, thermoset insulation cannot be re-melted or reformed once set. Cross-linked polyethylene (XLPE) is a commonly used thermoset material known for its excellent electrical properties, resistance to high temperatures, and resistance to moisture and chemicals. XLPE insulation is often used in medium and high-voltage power cables, including underground transmission and distribution systems.
In addition to thermoplastics and thermosets, other specialized insulation materials are designed for specific applications. For instance, silicone rubber insulation is known for its high-temperature resistance, making it suitable for applications in extreme environments such as aerospace and automotive industries. Fluoropolymers, such as polytetrafluoroethylene (PTFE), are used in high-temperature and high-frequency applications due to their excellent electrical properties and resistance to chemicals and heat.
The voltage rating and the cable or wire’s intended use determine the insulation layer’s thickness. Higher voltage applications require thicker insulation layers to withstand the higher electric fields and prevent electrical breakdown. The insulation thickness also affects the overall diameter and flexibility of the cable.
Insulation materials are subjected to various tests to ensure their performance and safety. These tests may include measuring electrical properties such as dielectric strength and insulation resistance, evaluating resistance to temperature variations, flame resistance, and mechanical properties like flexibility and abrasion resistance. Compliance with industry standards and regulations is essential to ensure the reliability and safety of electrical systems.
Aerospace and Automotive Industries
Insulating epoxy coatings find essential applications in both the aerospace and automotive industries. These coatings offer numerous advantages, including electrical insulation, corrosion resistance, and thermal protection. This response will explore the critical uses of insulating epoxy coatings within the aerospace and automotive sectors while adhering to the 450-word limit.
Aerospace Industry:
- Aircraft Structures: Insulating epoxy coatings protect aircraft structures from environmental factors, such as moisture, chemicals, and UV radiation. These coatings act as a barrier, preventing corrosion and extending the lifespan of critical components. Additionally, they provide electrical insulation, reducing the risk of electrical interference and enhancing safety.
- Electronic Components: Insulating epoxy coatings are applied to electronic components in aerospace systems, including circuit boards, connectors, and sensors. These coatings offer excellent electrical insulation properties, safeguarding sensitive electronics from static discharge, moisture, and contaminants. The layers also help with heat dissipation, ensuring optimal performance and reliability of electronic systems.
- Radomes: Radomes, which are protective enclosures for radar antennas, require insulating epoxy coatings to ensure signal transparency and protection against environmental elements. These coatings provide insulation against electromagnetic interference (EMI) while maintaining the structural integrity of the radome. They also offer resistance to erosion and weathering, maintaining radar system performance.
Automotive Industry:
- Electric Vehicle (EV) Batteries: Insulating epoxy coatings are crucial for protecting electric vehicle batteries. These coatings prevent the penetration of moisture and contaminants, ensuring the integrity and longevity of the battery cells. They also provide electrical insulation, minimizing the risk of short circuits and enhancing the safety of EVs.
- Engine Components: Insulating epoxy coatings are used on engine components to protect them from corrosion, heat, and chemical exposure. These coatings improve the durability and performance of engine parts, such as cylinder heads, intake manifolds, and exhaust systems. The layers also provide thermal insulation, reducing heat transfer and improving engine efficiency.
- Electrical Systems: Insulating epoxy coatings are applied to electrical systems within vehicles, including wiring harnesses, connectors, and circuit boards. These coatings offer electrical insulation, preventing short circuits and ensuring reliable performance. They also protect against moisture, chemicals, and temperature variations, increasing the lifespan of electrical components.
- Chassis and Underbody Protection: Insulating epoxy coatings protect the chassis and underbody of vehicles from corrosion caused by moisture, salt, and road debris. These coatings form a robust barrier, preventing the penetration of corrosive substances and extending the vehicle’s lifespan. Additionally, they provide thermal insulation, reducing heat transfer and improving passenger comfort.
Marine and Offshore Applications
Insulating epoxy coatings play a crucial role in marine and offshore applications by providing a protective barrier against corrosion, abrasion, and electrical conductivity. These specialized coatings offer numerous benefits and are widely used in marine and offshore environments.
- Marine Vessels: Insulating epoxy coatings are extensively used on marine vessels, including ships, barges, and offshore platforms. These coatings protect the hulls from the corrosive effects of saltwater, chemicals, and marine organisms. They provide a durable protective barrier that extends the vessel’s lifespan and reduces maintenance requirements.
- Offshore Oil and Gas Platforms: In offshore oil and gas exploration and production, insulating epoxy coatings are essential for maintaining the integrity of platforms and equipment. They safeguard the structures against harsh environmental conditions, including corrosive saltwater, high temperatures, and chemical exposure. Insulating coatings also provide electrical insulation, preventing electrical currents from interfering with sensitive equipment and ensuring safety.
- Pipelines and Subsea Applications: Insulating epoxy coatings are applied to channels and subsea equipment to protect them from corrosion caused by seawater, moisture, and chemicals. These coatings act as a barrier, preventing the penetration of corrosive substances and maintaining the integrity of the infrastructure. They also provide electrical insulation, reducing the risk of electrical interference or damage.
- Offshore Wind Farms: Insulating epoxy coatings are utilized in constructing and maintaining offshore wind farms. They protect wind turbine structures, including towers, foundations, and subsea cables, from corrosion and environmental degradation. These coatings also provide electrical insulation, ensuring safe and efficient power transmission.
- Marine and Offshore Equipment: Epoxy coatings are applied to various marines and offshore equipment, such as pumps, valves, tanks, and mooring systems. These coatings protect the equipment from corrosion, abrasion, and chemical exposure, extending their service life and reducing maintenance costs. The insulating properties of these coatings also prevent electrical conductivity issues, improving the safety and reliability of the equipment.
- Floating Production Storage and Offloading (FPSO) Vessels: FPSOs are widely used in offshore oil and gas production. Insulating epoxy coatings are applied to the hulls and internal structures of FPSOs to protect them from corrosion, abrasion, and chemical exposure. These coatings provide long-term protection and ensure the structural integrity of the vessel.
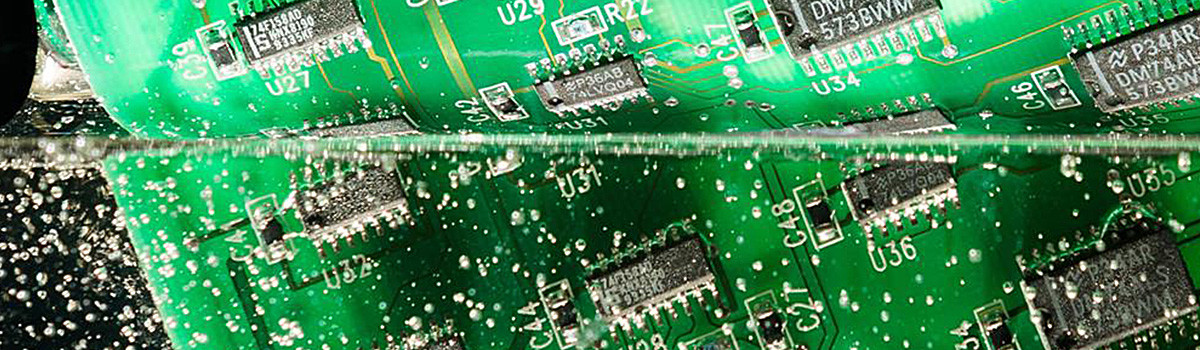
Chemical and Corrosion Resistance
Insulating epoxy coatings are widely used in various industries to protect against corrosion and electrical insulation. These coatings offer excellent chemical resistance, making them suitable for harsh environments where exposure to corrosive substances is a concern.
Chemical resistance is crucial for insulating epoxy coatings, as they are often exposed to a wide range of chemicals, including acids, alkalis, solvents, and fuels. Epoxy coatings resist many corrosive substances due to their dense molecular structure and cross-linked polymer network. This structure creates a barrier that prevents the penetration of corrosive agents, thus protecting the underlying substrate.
One of the primary factors contributing to the chemical resistance of epoxy coatings is their high cross-link density. Cross-linking refers to the chemical bonding between the epoxy molecules, resulting in a three-dimensional network. This network enhances the coating’s resistance to chemical attack by creating a barrier preventing the diffusion of corrosive substances. As a result, the coated substrate remains protected against corrosion.
Furthermore, epoxy coatings can be formulated with various additives and reinforcements to enhance their chemical resistance. For instance, the addition of corrosion inhibitors can further improve the protective properties of the coating by inhibiting the corrosion process and reducing the degradation of the epoxy. Reinforcements such as glass fibers or nanoparticles can also enhance the coating’s mechanical and chemical resistance.
In addition to chemical resistance, insulating epoxy coatings offer excellent corrosion resistance. Corrosion occurs when a material reacts with its environment, leading to its deterioration and potential failure. Epoxy coatings act as a barrier between the corrosive environment and the substrate, preventing the contact of moisture, oxygen, and other corrosive agents with the underlying metal surface.
Epoxy coatings also provide excellent adhesion to various substrates, ensuring long-term protection against corrosion. The strong bond between the layer and the substrate prevents the ingress of moisture and corrosive substances, reducing the likelihood of corrosion initiation and progression.
It is important to note that the chemical and corrosion resistance of insulating epoxy coatings can be influenced by temperature, exposure time, and the specific chemical environment. While epoxy coatings offer excellent resistance to various chemicals, highly aggressive substances may still cause damage over extended periods or under extreme conditions.
To ensure optimal performance, selecting the appropriate epoxy coating formulation is essential based on the specific application requirements. When choosing the right epoxy coating system, the operating environment, chemical exposure, temperature, and expected service life should be considered.
Thermal Conductivity and Heat Dissipation
Thermal conductivity and heat dissipation are essential in various fields, including engineering, electronics, and materials science. They are crucial in determining the efficiency and reliability of systems that generate or handle heat. Let’s explore these concepts further within the given word limit.
Thermal conductivity refers to the ability of a material to conduct heat, and it is a property that characterizes how easily heat can transfer through a substance. Materials with high thermal conductivity allow heat to flow quickly, while those with low thermal conductivity impede heat transfer. The unit of measurement for thermal conductivity is watts per meter-kelvin (W/mK).
Various factors affect the thermal conductivity of a material. One of the critical factors is the molecular or atomic structure. Substances with closely packed atoms or molecules tend to have higher thermal conductivity. Metals like copper and aluminum are known for their high thermal conductivity due to their metallic bonding and close-packed crystal structures.
On the other hand, materials with complex molecular structures or large voids, such as polymers or insulators like wood or rubber, have relatively lower thermal conductivity. Air and other gases are poor conductors of heat, which is why materials with trapped air pockets, like insulation materials, exhibit low thermal conductivity.
Heat dissipation, however, refers to transferring or dissipating heat away from a system or component to prevent overheating and maintain optimal operating conditions. Efficient heat dissipation is crucial for the longevity and performance of devices, particularly those that generate significant amounts of heat, such as electronic components, power systems, and engines.
There are various methods of heat dissipation, depending on the specific application. Some standard techniques include conduction, convection, and radiation.
Conduction involves the transfer of heat through direct physical contact between objects. Efficient heat-conducting materials, such as metals or materials with high thermal conductivity, facilitate heat transfer between heat-generating components and heat sinks or cooling systems.
Convection involves the transfer of heat through the movement of fluids, such as air or liquid. This process relies on the circulation of the fluid, either naturally or with fans or pumps, to carry away heat from the source. Heat sinks with extended surfaces are often utilized to increase the surface area for convective heat transfer.
Radiation refers to the emission and absorption of thermal radiation, which is electromagnetic radiation emitted by objects due to their temperature. All objects above absolute zero temperature emit thermal radiation. Heat dissipation through radiation occurs when the emitted radiation carries away heat from the source to more relaxed surroundings.
Various techniques and technologies are employed to enhance heat dissipation, including heat sinks, heat pipes, thermal interface materials, fans, liquid cooling systems, and advanced thermal management solutions.
Electrical Insulation Performance
Insulating epoxy coatings is crucial in providing electrical insulation in various industries, including electronics, electrical equipment, and power systems. These coatings are designed to prevent the flow of electric current and protect against electrical breakdowns or short circuits. Let’s explore the electrical insulation performance of insulating epoxy coatings within the given word limit.
One of the fundamental properties contributing to the electrical insulation performance of epoxy coatings is their high dielectric strength. Dielectric strength refers to the maximum electric field a material can withstand without experiencing an electrical breakdown. Insulating epoxy coatings are formulated to have high dielectric strength, allowing them to withstand high voltage levels and prevent electrical leakage or arcing.
Several factors, including the resin formulation, curing process, and filler materials, influence the dielectric strength of insulating epoxy coatings. Epoxy resins with high molecular weight and cross-linking density exhibit higher dielectric strength. The curing process also plays a role, as proper curing ensures the formation of a dense and uniform coating that can withstand electrical stress.
Filler materials can be added to epoxy coatings to enhance electrical insulation performance. Fillers, such as glass fibers or mineral fillers, can increase the dielectric strength by reducing the occurrence of voids or weak points within the coating. These fillers improve the coating’s overall homogeneity and structural integrity, minimizing the risk of electrical breakdown.
Insulating epoxy coatings also offer good electrical resistivity, which refers to the material’s ability to resist the flow of electric current. High electrical resistivity is crucial for preventing leakage currents and maintaining the integrity of electrical insulation. Epoxy coatings typically have high resistivity values, contributing to their effectiveness as electrical insulators.
Another important aspect of electrical insulation performance is the ability of insulating epoxy coatings to withstand environmental factors that may impact their electrical properties. Factors such as humidity, temperature variations, and exposure to chemicals can affect the dielectric strength and resistivity of the coating. Therefore, it is essential to select epoxy coatings with appropriate formulations and additives to provide long-term electrical insulation performance under specific environmental conditions.
Furthermore, insulating epoxy coatings should exhibit good adhesion to the substrate to ensure long-term electrical insulation. A strong bond between the layer and the underlying surface prevents the formation of voids or gaps that could compromise the electrical insulation performance. Surface preparation, coating application techniques, and the compatibility between the coating and the substrate influence adhesion.
To summarize, insulating epoxy coatings offer excellent electrical insulation performance by providing high dielectric strength, electrical resistivity, and good adhesion to the substrate. Their formulation, curing process, and use of fillers contribute to their ability to withstand electrical stress and prevent electrical breakdown. Proper selection and application of insulating epoxy coatings are vital to ensure effective electrical insulation in various applications, ranging from electronics to power systems.
Types of Insulating Epoxy Coatings
Several types of insulating epoxy coatings are available, each designed to meet specific requirements and provide varying levels of electrical insulation. Here are some common types of protecting epoxy coatings:
- Standard Insulating Epoxy Coatings: These are general-purpose epoxy coatings formulated to provide primary electrical insulation. They offer good dielectric strength and electrical resistivity, making them suitable for various applications.
- High-Temperature Insulating Epoxy Coatings: These coatings are specifically formulated to withstand elevated temperatures without compromising their electrical insulation performance. They can be used in applications where exposure to high heat is expected, such as motors, transformers, or electrical components in the automotive or aerospace industries.
- Thermal Conductive Insulating Epoxy Coatings: These coatings provide electrical insulation and have the added property of thermal conductivity. They are designed to dissipate heat efficiently while maintaining electrical insulation. These coatings are commonly used in applications requiring electrical insulation and effective heat dissipation, such as in power electronics.
- Flame-Retardant Insulating Epoxy Coatings: Flame-retardant epoxy coatings are formulated to provide electrical insulation while offering resistance to flame spread and combustion. These coatings are commonly used in applications where fire safety is a concern, such as electrical panels, switchgear, or wiring.
- Chemical-Resistant Insulating Epoxy Coatings: These coatings are designed to provide electrical insulation while offering excellent resistance to various chemicals and corrosive substances. They are suitable for applications where exposure to harsh chemicals or corrosive environments is expected, such as in chemical processing plants or marine applications.
- UV-Resistant Insulating Epoxy Coatings: UV-resistant coatings are formulated to provide electrical insulation while offering protection against the damaging effects of ultraviolet (UV) radiation. These coatings are commonly used in outdoor applications or environments where sunlight exposure is significant, such as solar panels or outdoor electrical equipment.
- Flexible Insulating Epoxy Coatings: Flexible epoxy coatings are designed to provide electrical insulation in applications where the coated substrate undergoes mechanical stress or movement. These coatings offer good adhesion and flexibility, allowing them to withstand bending or stretching without cracking or compromising the electrical insulation.
It’s important to note that selecting the appropriate insulating epoxy coating type depends on the specific application requirements, environmental factors, and performance expectations. Consulting with coating manufacturers or industry experts can help determine the most suitable insulating epoxy coating for a particular application.
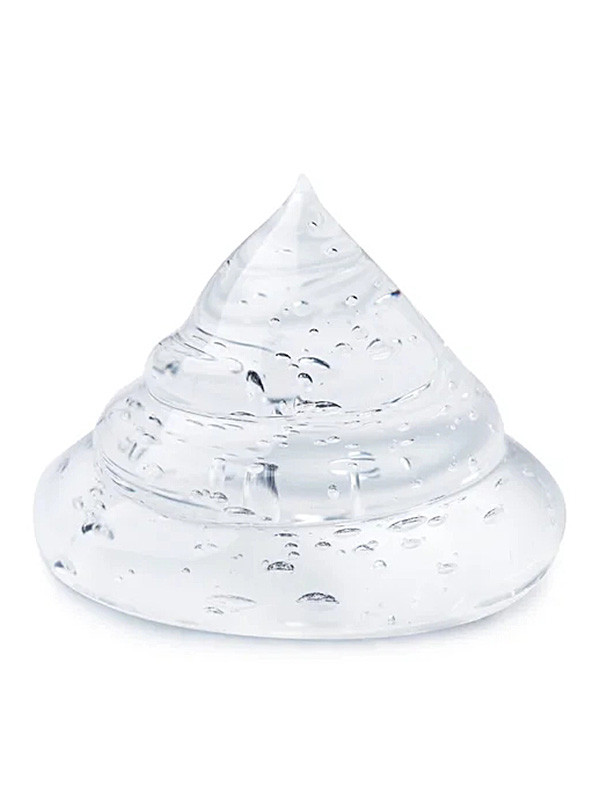
Two-Part Epoxy Coatings
Two-part epoxy coatings are widely used in various industries for their exceptional durability, chemical resistance, and versatility. These coatings consist of two components: a resin and a hardener. When combined in the correct ratio, they undergo a chemical reaction known as curing, resulting in a solid and protective coating. Here, we will explore two-part epoxy coatings’ key characteristics, applications, and benefits.
Characteristics: Two-part epoxy coatings offer several key features that make them highly desirable in many applications. Firstly, they provide excellent adhesion to various substrates, including concrete, metal, wood, and fiberglass. This adhesion ensures long-lasting performance and prevents issues such as peeling or delamination. Additionally, epoxy coatings exhibit high chemical resistance, making them suitable for use in environments exposed to corrosive substances, chemicals, or solvents. They are also known for their exceptional hardness, abrasion resistance, and impact resistance, contributing to their longevity and durability. Furthermore, depending on the desired aesthetic and functional requirements, epoxy coatings can be formulated to have various finishes, including glossy, matte, or textured.
Applications: Two-part epoxy coatings find applications across various industries due to their versatility and performance characteristics. In the industrial sector, they are commonly used to protect concrete floors in manufacturing plants, warehouses, and garages. The epoxy coating creates a seamless, durable surface that can withstand heavy traffic, impacts, and chemical spills. In the marine industry, epoxy coatings are utilized for boat hulls, decks, and other structures, protecting against water intrusion, UV radiation, and corrosion. These coatings are also employed in the automotive industry to provide a protective layer on car bodies, engine components, and underbody coatings, enhancing their resistance to abrasion, chemicals, and weathering. Additionally, two-part epoxy coatings are widely used in the construction sector for waterproofing, concrete repairs, and decorative flooring systems.
Benefits: Using two-part epoxy coatings offers numerous advantages to industrial and commercial users. Firstly, their exceptional durability and resistance to wear and tear ensure a longer lifespan for coated surfaces, reducing maintenance and replacement costs. Epoxy coatings are also relatively easy to apply, allowing for efficient installation and minimizing downtime in industrial settings. Their seamless and non-porous nature makes them hygienic and easy to clean, ideal for environments that require high levels of cleanliness, such as healthcare facilities or food processing plants. Furthermore, epoxy coatings can be customized to meet specific requirements, including anti-slip properties, heat resistance, or electrical conductivity. This versatility allows for tailored solutions in various applications. Lastly, two-part epoxy coatings are environmentally friendly as they are low in volatile organic compounds (VOCs), making them safer for workers and the environment.
One-Part Epoxy Coatings
One-part epoxy coatings are single-component coatings that offer many advantages over traditional two-part epoxy coatings but with simplified application processes. These coatings are formulated with a resin that contains both the epoxy resin and the curing agent, eliminating the need for a separate hardener. This article will explore the characteristics, applications, and benefits of one-part epoxy coatings.
Characteristics: One-part epoxy coatings possess several key features that make them popular in various industries. These coatings exhibit excellent adhesion to different substrates, including concrete, metal, and wood, ensuring a solid bond and long-lasting protection. They provide good chemical resistance, offering protection against corrosive substances, chemicals, and solvents. Additionally, one-part epoxy coatings provide good abrasion resistance and durability, making them suitable for surfaces subject to heavy traffic or wear. They can also be formulated with different finishes, such as glossy or matte, to achieve the desired aesthetic appeal.
Applications: One-part epoxy coatings find applications across various industries and surfaces. In the construction industry, they are commonly used to protect and enhance concrete floors, providing a seamless and durable cover in settings such as warehouses, retail spaces, and commercial buildings. These coatings also find applications in the automotive industry, where they are used for corrosion protection on vehicle undercarriages, chassis components, and other metal surfaces. Furthermore, one-part epoxy coatings are utilized in the marine industry for boat decks, swimming pools, and marine structures, providing resistance to water, UV radiation, and chemicals. They can also be used on metal surfaces, such as machinery, equipment, or storage tanks, to protect against corrosion and wear.
Benefits: One-part epoxy coatings offer several advantages that make them advantageous for many applications. One of the key benefits is their ease of use and application. Since they come pre-mixed, there is no need for measuring and mixing multiple components, simplifying the coating process and reducing the potential for errors. This makes them ideal for smaller projects or users with limited experience with epoxy coatings. Additionally, one-part epoxy coatings often have a longer pot life than two-part systems, allowing for extended working time and more straightforward application. They also offer excellent adhesion, durability, and chemical resistance, ensuring long-lasting protection for coated surfaces. Moreover, one-part epoxy coatings are typically low in volatile organic compounds (VOCs), making them environmentally friendly and safer for users.
Selecting the Right Insulating Epoxy Coating
Selecting the insulating epoxy coating is crucial to ensure adequate insulation and protection for various applications. Insulating epoxy coatings are designed to provide electrical insulation and thermal resistance, preventing electrical conductivity and heat transfer. Here are some key factors to consider when choosing the suitable insulating epoxy coating:
- Electrical Properties: The primary function of an insulating epoxy coating is to provide electrical insulation. Therefore, it is essential to consider the electrical properties of the coating, such as dielectric strength, volume resistivity, and surface resistivity. Dielectric strength determines the maximum voltage the coating can withstand before the breakdown, while resistivity measures the material’s ability to resist the flow of electric current. Ensure that the layer meets the required electrical standards for your specific application.
- Thermal Resistance: Insulating epoxy coatings are also expected to offer thermal resistance to prevent heat transfer. Consider the coating’s ability to withstand high temperatures and provide effective thermal insulation. Look for layers with low thermal conductivity to minimize heat transfer and maintain temperature stability.
- Substrate Compatibility: Evaluate the compatibility of the epoxy coating with the substrate material. Insulating epoxy coatings are commonly used on copper, aluminum, or steel metals. Ensure the coating is formulated to adhere well to the specific substrate material, providing a strong bond and long-term performance.
- Application Method: Consider the application method and the ease of application for the chosen insulating epoxy coating. Some coatings are suitable for spray application, while others are more suitable for brush or roller application. Choose a layer that aligns with the available application equipment and the project requirements.
- Environmental Resistance: Assess the ecological conditions the coating will be exposed to, such as humidity, moisture, chemicals, or UV radiation. Insulating epoxy coatings should offer excellent resistance to these environmental factors to ensure long-term performance and protection. Consider coatings with high chemical resistance and UV stability if exposed to harsh environments.
- Certifications and Standards: Certain certifications or standards may be required depending on the application. For example, insulating epoxy coatings may need to meet specific electrical standards or certificates in the electrical industry. Ensure that the chosen coating meets industry standards and certifications to ensure compliance and performance.
- Performance and Durability: Consider the overall performance and durability of the insulating epoxy coating. Look for layers with excellent adhesion, abrasion resistance, and long-term durability to ensure sustained insulation and protection. Assess the coating’s resistance to physical damage, such as impact or scratching, which could compromise the insulation properties.
- Cost and Value: Finally, evaluate the cost and value of the insulating epoxy coating. Consider factors such as the initial cost, the expected lifespan of the layer, and the potential maintenance or replacement costs over time. Balancing the upfront investment with long-term performance and durability will help determine the overall value of the coating.
Environmental Considerations
Environmental considerations play a significant role in the selection and use of insulating epoxy coatings. Choosing coatings that provide adequate insulation and minimize environmental impact throughout their lifecycle is essential. Here are some critical ecological considerations to keep in mind when selecting insulating epoxy coatings:
- VOC Content: Volatile Organic Compounds (VOCs) are chemicals that can contribute to air pollution and have potential health effects. When choosing insulating epoxy coatings, opt for low-VOC or VOC-free formulations. These coatings emit fewer harmful fumes during application and contribute to better indoor and outdoor air quality.
- Hazardous Substances: Evaluate the presence of dangerous substances in the epoxy coating formulation. Certain additives, solvents, or heavy metals may harm human health or the environment. Look for coatings free from or have reduced levels of hazardous substances, ensuring safer handling, disposal, and long-term environmental impact.
- Biodegradability: Consider the biodegradability of the insulating epoxy coating. Coatings that are biodegradable break down naturally over time, reducing their impact on the environment. Look for layers that are derived from renewable resources or that have been tested and certified for their biodegradability.
- Energy Efficiency: Insulating epoxy coatings often improves energy efficiency by reducing heat transfer. By selecting coatings with high thermal resistance properties, you can enhance energy efficiency in applications such as electrical insulation, building insulation, or thermal barriers. This can lead to reduced energy consumption and lower environmental impact.
- Durability and Longevity: Choose insulating epoxy coatings with excellent durability and longevity. Coatings more resistant to wear, corrosion, or degradation require less frequent maintenance, reapplication, and disposal. This reduces the overall environmental impact associated with the use of the coatings.
- Packaging and Waste: Consider the insulating epoxy coatings’ packaging and the waste generation during their use. Opt for coatings that are packaged in recyclable or eco-friendly materials. Additionally, coatings that minimize waste generation during the application, such as those with reduced overspray or minimal mixing requirements, can help reduce environmental impact.
- Environmental Certifications: Look for insulating epoxy coatings that have achieved ecological certifications or comply with recognized environmental standards. Examples include certificates like LEED (Leadership in Energy and Environmental Design) or adherence to ISO 14001 environmental management standards. These certifications ensure that the coatings have undergone rigorous testing and meet specific environmental performance criteria.
- Proper Disposal and Recycling: Consider the appropriate disposal and recycling options for insulating epoxy coatings. Check local regulations and guidelines to ensure the coatings can be disposed of or recycled appropriately at the end of their lifecycle. Some coatings may have specific recycling programs or options available.
Considering these environmental considerations, you can select insulating epoxy coatings that provide adequate insulation and minimize their ecological impact. Choosing environmentally friendly coatings contributes to sustainability efforts, reduces pollution, and promotes a healthier ecosystem.
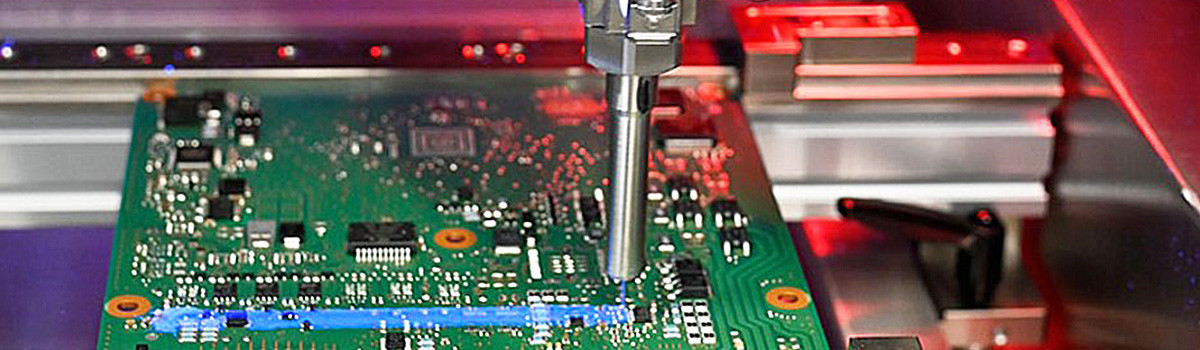
Application Techniques and Tips
Proper application techniques are essential for achieving optimal results when insulating epoxy coatings. The following tips will help ensure a successful application and enhance the performance of the layer:
- Surface Preparation: Thoroughly clean and prepare the surface before applying the insulating epoxy coating. Remove any dirt, dust, grease, or existing coatings that may interfere with adhesion. Surface preparation techniques may include sanding, degreasing, or using appropriate cleaning agents. Follow the manufacturer’s guidelines for surface preparation specific to the coating and substrate.
- Mixing Ratios and Pot Life: Carefully follow the manufacturer’s instructions regarding mixing ratios and pot life. Insulating epoxy coatings are typically two-part systems that require accurate mixing of resin and hardener components. Improper mixing can result in incomplete curing or compromised performance. Pay attention to the pot life and the working time available once the ingredients are mixed. Avoid exceeding the pot life to ensure proper application.
- Application Method: Choose the appropriate application method for the insulating epoxy coating based on the surface and project requirements. Standard application methods include brush, roller, or spray application. Use brushes and rollers for smaller areas or when precision is required. Spray application is suitable for larger rooms or a more uniform finish. Follow the manufacturer’s recommendations for the specific coating regarding application method and equipment.
- Temperature and Humidity: Consider the ambient temperature and humidity conditions during application. Insulating epoxy coatings may have specific temperature and humidity requirements for optimal performance. Follow the manufacturer’s guidelines regarding the recommended temperature range and humidity conditions during application and curing. Extreme temperatures or high humidity can affect the coating’s cure time and overall performance.
- Application Thickness: Apply the insulating epoxy coating to the recommended thickness for the desired insulation and protection. A sufficient coating thickness may compromise the insulating properties, while excessive thickness may lead to curing issues or improper adhesion. Use a wet film thickness gauge to ensure consistent and accurate coating thickness throughout the application.
- Ventilation and Safety: Ensure proper ventilation in the application area to minimize the inhalation of fumes or vapors. Use appropriate personal protective equipment (PPE) as the manufacturer recommends, such as gloves, goggles, or respiratory protection. Follow safety guidelines and regulations to protect yourself and others during the application process.
- Curing and Drying Time: Allow sufficient curing and drying time for the insulating epoxy coating. Follow the manufacturer’s instructions regarding the recommended curing time and environmental conditions for proper adhesion and performance. Avoid subjecting the coated surface to excessive moisture or mechanical stress until the coating has fully cured.
- Inspection and Maintenance: Regularly inspect the coated surface for any signs of damage or wear. Perform routine maintenance to ensure the continued effectiveness of the insulating epoxy coating. Address any issues promptly to prevent further injury or deterioration.
By following these application techniques and tips, you can achieve successful results when applying insulating epoxy coatings. Proper surface preparation, accurate mixing, suitable application methods, and adherence to curing guidelines will help ensure your application’s desired insulation and protection.
Curing and Drying Process
The curing and drying process for insulating epoxy coatings is a critical step that determines the final properties and performance of the coating. Proper curing ensures a strong, durable, and fully insulating layer. Here are the key factors and considerations for the curing and drying process of insulating epoxy coatings:
- Follow Manufacturer’s Instructions: Always refer to the manufacturer’s instructions and technical data sheet for specific guidance on curing and drying times and the environmental conditions required for the coating. Different epoxy coatings may have varying curing processes and recommended drying times.
- Ambient Temperature: The curing process of epoxy coatings is temperature-dependent. Most epoxy coatings require a minimum and maximum ambient temperature range for proper curing. Ensure the ambient temperature falls within the specified range throughout the curing and drying process. Extreme hot and cold temperatures can adversely affect the curing process and the final performance of the coating.
- Relative Humidity: Humidity levels can also impact the curing and drying of insulating epoxy coatings. In high-humidity environments, the curing time may be prolonged due to the slow evaporation of moisture from the layer. Conversely, low humidity may cause the coating to cure too quickly, compromising its integrity. Maintain the recommended humidity levels specified by the manufacturer for optimal curing.
- Ventilation: Adequate ventilation is crucial during curing and drying to ensure proper air circulation and the dissipation of fumes or vapors. Good ventilation helps facilitate the curing process and reduces the risk of solvent entrapment, which could affect the coating’s performance.
- Curing Time: The curing time for insulating epoxy coatings can vary depending on the specific formulation, the thickness of the applied layer, and ambient conditions. It is essential to allow the recommended curing time specified by the manufacturer to ensure complete cross-linking and the development of desired properties. Premature exposure to moisture, dust, or mechanical stress during the curing process can compromise the coating’s performance.
- Drying Time: Drying time refers to when the solvent evaporates from the coating. The drying time may vary based on coating thickness, temperature, humidity, and ventilation. It is crucial to allow the recommended drying time for the coating to achieve proper film formation and avoid premature handling or exposure.
- Complete Cure: While the coating may feel dry to the touch after the recommended drying time, it is essential to note that complete curing may take longer. Full cure refers to the epoxy coating’s complete chemical cross-linking and hardening. Follow the manufacturer’s instructions regarding the recommended full cure time before subjecting the coated surface to heavy loads, abrasion, or other stressors.
- Post-Curing: Some insulating epoxy coatings may benefit from post-curing to enhance their properties further. Post-curing involves subjecting the cured layer to elevated temperatures for a specified duration. This process can improve the coating’s chemical resistance, hardness, and adhesion. If applicable, refer to the manufacturer’s guidelines regarding the recommended post-curing process.
By carefully following the manufacturer’s instructions, maintaining suitable ambient conditions, allowing proper curing and drying times, and ensuring adequate ventilation, you can achieve optimal results in insulating epoxy coatings. Properly cured and dried coatings will provide the desired electrical insulation and thermal resistance for the intended application.
Maintenance and Repair of Insulating Epoxy Coatings
Insulating epoxy coatings are widely used in various industries to protect and insulate electrical equipment and infrastructure. These coatings provide a durable protective barrier that prevents moisture, chemicals, and other contaminants from reaching the underlying surfaces. However, like any other coating system, insulating epoxy coatings may require maintenance and repair to ensure their effectiveness and longevity.
Maintenance of insulating epoxy coatings primarily involves regular inspection and cleaning. Inspect the coated surfaces periodically to identify any signs of damage, such as cracks, blistering, or peeling. Please pay close attention to areas exposed to harsh conditions or mechanical stress, as they are more prone to damage. If any issues are detected, address them promptly to prevent further deterioration.
Cleaning the coated surfaces is essential to remove dirt, dust, oils, and other contaminants that may accumulate over time. Use mild, non-abrasive cleaners and soft brushes or cloths to clean the surfaces gently. Avoid harsh chemicals or abrasive materials that scratch or degrade the coating. Regular cleaning helps maintain the insulating properties of the epoxy coating and prevents the buildup of conductive materials that could compromise its effectiveness.
When it comes to repair, the approach may vary depending on the extent of the damage. You can use epoxy repair kits specifically designed for insulating coatings for minor injuries like small cracks or chips. These kits typically include epoxy filler and instructions on correctly applying it. Clean the damaged area thoroughly, follow the instructions provided with the equipment, and use the epoxy filler on the damaged portion. Allow it to cure according to the manufacturer’s recommendations.
In cases where the damage is more significant, removing the damaged section of the coating may be necessary as applying a new layer of insulating epoxy. This requires careful surface preparation, including cleaning and roughening the area surrounding the damage to ensure proper adhesion of the new coating. Follow the manufacturer’s guidelines regarding applying the new epoxy coating, including curing times and temperature requirements.
In some instances, it may be more practical to seek professional assistance to maintain and repair insulating epoxy coatings. Experienced contractors or coating specialists can assess the extent of the damage, recommend the most suitable repair method, and ensure that the improved coating meets the necessary standards and requirements.
Remember that regular inspection and preventive maintenance are crucial for extending the lifespan of insulating epoxy coatings. By addressing minor issues early on and following proper cleaning procedures, you can minimize the need for extensive repairs and ensure the continued effectiveness of the coating in protecting and insulating electrical equipment and infrastructure.
Conclusion
Insulating epoxy coatings is crucial in safeguarding electrical components and equipment from various external factors. With applications ranging from electronic components to circuit boards, motors, and cables, these coatings provide essential protection against moisture, chemicals, and physical damage. The proper insulating epoxy coating selection depends on environmental conditions, performance requirements, and application techniques. By understanding the benefits and considerations associated with insulating epoxy coatings, industries can make informed choices to enhance their electrical systems and equipment’s durability, reliability, and longevity.