Adhesives for Potting and Encapsulation
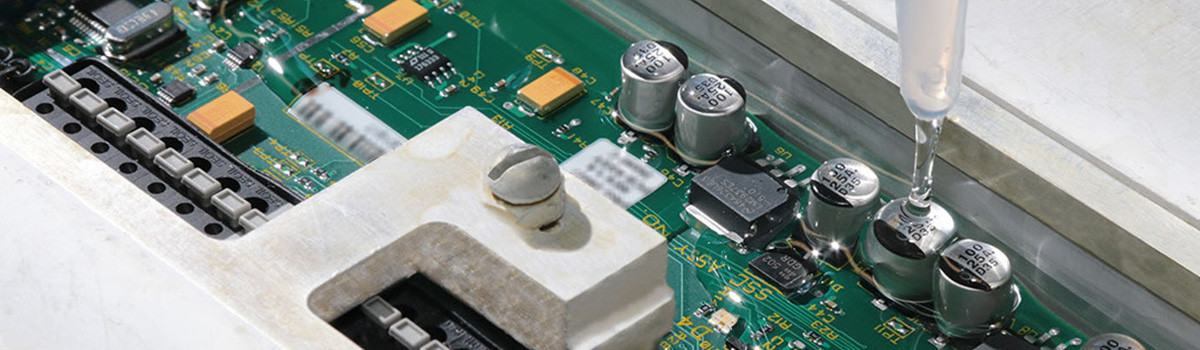
Adhesive flows over and around a component or fills in a chamber to protect components therein. Examples include heavy duty electrical cords and connectors, electronics in plastic cases, circuit boards and concrete repair.
A seal must be highly elongating and flexible, durable, and fast setting. By definition, mechanical fasteners almost always require a secondary seal because penetrations in a surface allow fluid and vapor to freely flow into an assembly.
Peel, Compression and Tension Stresses when Sealing, Potting or Encapsulating
If the assembly requires two overlaps or butt joints to be sealed, the sealant is often exposed to peel forces. Foot traffic over doorway thresholds or wind on a railcar roof continually attempt to peel a sealant, whether tape or adhesive, off the part. If the application is potted or encapsulated, the adhesive (tapes are not a good fit here) often sees compression and tension as the part experiences thermal expansion or contraction. Many potted parts, on circuit boards for example, can see all three stresses – peel, compression and tension.
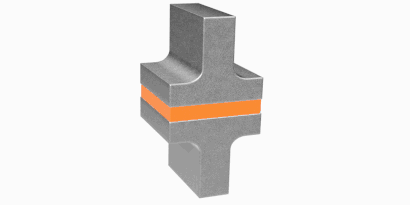
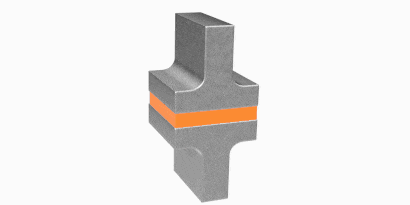
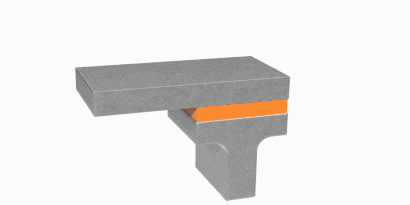
Deepmaterial line of products consists of epoxies, silicones, polyurethanes and UV curable systems. They are used in low, medium, high voltage applications and feature outstanding electrical insulation properties, superior adhesive strength, thermal stability and superb chemical resistance. Products provide reliable long term performance for microelectronic, electronic, electrical devices, components including:
*Power supplies
*Switches
*Ignition coils
*Electronic modules
*Motors
*Connectors
*Sensors
*Cable harness assemblies
*Capacitors
*Transformers
*Rectifiers
Properties of Potting, Encapsulation and Casting Systems
From “under the hood” to photovoltaic junction box assembly LED packaging to marine modules to submersible pumps Master Bond potting, encapsulation, casting materials are impervious to hostile environmental conditions. They offer the following advantages:
*Enhanced thermal management properties
*Exceptionally low coefficients of thermal expansion
*Crack resistance
*Protection against corrosion
*Elevated temperature and cryogenic serviceability
*Withstand rigorous thermal cycling and shock
Specific grades are used for tamper proofing, infiltrating densely packed components, sealing tightly wound coils, underfills, for high voltage indoor/outdoor applications where arcing/tracking are a concern and high vacuum situations. Additionally Master Bond offers optically clear UV curable systems including dual cure (UV/heat curable) compounds for “shadowed out” areas that pass 1000 hours at 85°C/85% RH testing.
Low viscosity, self leveling rigid, semi-rigid and flexible compositions eliminate gas entrapment and are ideal for high volume production applications. These solvent free 100% solid systems feature low shrinkage, outstanding dimensional stability, excellent mechanical properties and can be dispensed manually/automatically. They guard against abrasion, shock, vibration, impact, UV, fungus, moisture exposure including salt water immersion. Specific grades exhibit superior thermal dissipation characteristics and have high glass transition temperatures. Heat activiated systems can be cured at low temperatures and exhibit low exotherm even in various wide cross section thicknesses. Soft, low durometer, resilient compositions have excellent stress relief properties for fragile, sensitive components. All products are ROHS compliant.
Ensure longer lasting electronics performance with Deepmaterial potting
From portable digital devices to transportation, electronics are increasingly present in our daily lives. Whether automotive, consumer electronics or industrial electronic systems, the technologies we depend on use a variety of components like sensors, actuators and circuit boards that require protection.
Deepmaterial’s one- and two-part potting compound materials fit your needs with Deepmaterial solutions. These produce a hermetic-like seal to protect sensitive electronic devices against environmental influences such as dust, moisture and temperature variations to preserve the integrity of their components and ensure performance for longer.
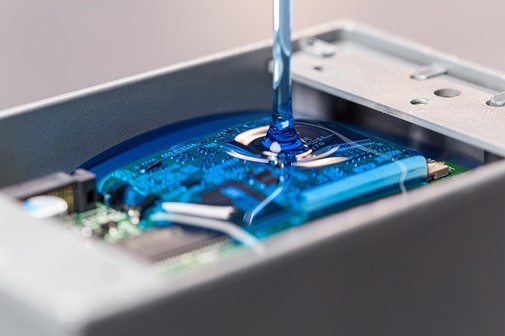
compounds is to reinforce components by:
*Improving mechanical and thermal performance;
*Providing insulation and resistance to vibration and shock;
*Preventing corrosion from moisture;
*Providing chemical resistance;
*Improving heat dissipation.
Why use Deepmaterial for sensitive electronics?
*Ensure protection of materials from environmental factors;
*Improve the reliability of the end application;
*Maintain the integrity of components;
*Preserve performance for longer.
Typical potting applications
*PCBs and junction boxes;
*LED encapsulation;
*Solar modules;
*Power electronics;
*Heat transfer for thermal management.