Two Component Epoxy Adhesive
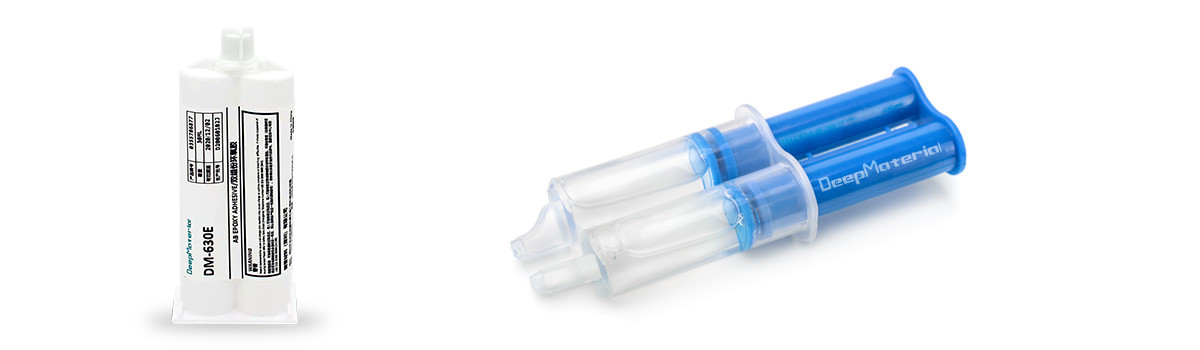
Two Component Epoxy Adhesive (TCEA) is a two-part adhesive system widely used in various industrial and commercial applications due to its exceptional bonding strength, durability, and versatility. It comprises a resin and a hardener that are mixed before application, and the curing time can be adjusted based on the application requirements. In this article, we will explore Two Component Epoxy Adhesive’s properties, applications, and benefits.
What is Two Component Epoxy Adhesive?
Two-component epoxy adhesive is a type of adhesive that consists of two components: resin and hardener. When these two components are mixed in the right proportions, a chemical reaction occurs, resulting in a robust and durable bond between the two materials.
Epoxy adhesives are known for their high strength and excellent adhesion to various materials, including metals, ceramics, plastics, and composites. Two-component epoxy adhesives offer even more increased strength and durability than one-component ones, as they require a curing process that allows the two components to bond together chemically.
The resin component of a two-component epoxy adhesive is typically a liquid or semi-solid material that contains one or more epoxy groups. The hardener component is a liquid or powder with a curing agent, such as amine or anhydride, that reacts with the epoxy groups in the resin to form a crosslinked network.
To use a two-component epoxy adhesive, the two components are typically mixed in a precise ratio, according to the manufacturer’s instructions. The mixture is then applied to one or both surfaces to be bonded together. The surfaces should be clean, dry, and free of contaminants that could interfere with the bonding process.
Once the adhesive has been applied, it can cure a certain amount, depending on the specific product and application. The curing process can be affected by temperature, humidity, and pressure. Once the adhesive has cured, it forms a strong, durable bond between the surfaces resistant to various environmental factors, such as heat, moisture, and chemicals.
How does Two Component Epoxy Adhesive work?
Two-component epoxy adhesive is a type of industrial adhesive widely used in various applications, including construction, electronics, automotive, and aerospace. It is composed of two parts: a resin and a hardener. A chemical reaction occurs when these two components are mixed correctly, resulting in a hard, strong, and durable adhesive.
The resin component of the epoxy adhesive is typically a liquid polymer, which is generally viscous and has a low molecular weight. It is usually made from bisphenol A and epichlorohydrin, although other formulations are available. The hardener component is typically an amine or acid, which reacts with the epoxy resin to form a polymer network.
Curing is The chemical reaction between the resin and the hardener. When the two components are mixed, the curing process begins immediately and proceeds until the adhesive is fully cured. The curing process can be accelerated by increasing the temperature or adding a catalyst, such as a metal salt or an organic compound.
During the curing process, the resin and hardener molecules react to form a three-dimensional polymer network. This network is responsible for the adhesive’s strength and durability. The polymer network is also responsible for the adhesive’s chemical and environmental damage resistance, making it a popular choice for industrial applications.
Two-component epoxy adhesive is handy because it can be formulated with various properties. For example, the ratio of resin to hardener can be adjusted to control the curing time, which can be helpful in applications where rapid bonding is required. Additionally, the choice of resin and hardener can be tailored to the specific application, allowing for adhesives with particular properties, such as flexibility or high-temperature resistance.
The resin and hardener must be mixed in the correct proportions to use a two-component epoxy adhesive. Depending on the application, the mixing process can be performed manually or by using a machine. The mixed adhesive is then applied to the surfaces that need to be bonded. The bond strength and curing time will depend on the specific formulation of the adhesive and the application conditions.
Overall, a two-component epoxy adhesive is a versatile and durable adhesive widely used in industrial applications. Its ability to be tailored to specific applications and its resistance to chemical and environmental damage make it a popular choice for many applications.
Types of Two Component Epoxy Adhesive
Various types of two-component epoxy adhesives are available in the market, each with unique properties and characteristics. Here are some common types of two-component epoxy adhesives:
- Clear Epoxy Adhesive: This type of epoxy adhesive is transparent and ideal for applications where aesthetics are essential. It can bond to various surfaces, including metals, plastics, and ceramics.
- High-Temperature Epoxy Adhesive: This type of epoxy adhesive is designed to withstand high temperatures, typically up to 300 degrees Celsius. It is commonly used in automotive and aerospace applications.
- Flexible Epoxy Adhesive: This type of epoxy adhesive has a lower modulus of elasticity, meaning it is more flexible and can absorb more stress and strain. It is often used in applications where vibration or movement is expected.
- Electrically Conductive Epoxy Adhesive: This type of epoxy adhesive is formulated to be electrically conductive, making it useful for bonding electronic components and creating conductive traces on circuit boards.
- Fast-Curing Epoxy Adhesive: This type of epoxy adhesive is designed to cure quickly, typically within a few minutes to an hour. It is commonly used in applications requiring rapid bonding, such as manufacturing and assembly operations.
- Structural Epoxy Adhesive: This epoxy adhesive is designed to provide high strength and durability. It is commonly used in construction, aerospace, and automotive applications requiring a solid and long-lasting bond.
- Water-Based Epoxy Adhesive: This type of epoxy adhesive is formulated with water as a solvent, making it easier to handle and less hazardous than solvent-based adhesives. It is commonly used in woodworking and other applications where flammability and toxicity are a concern.
- Chemical-Resistant Epoxy Adhesive: This type of epoxy adhesive is designed to resist various chemicals, including acids, bases, and solvents. It is commonly used in industrial settings where exposure to chemicals is expected.
Advantages of Two Component Epoxy Adhesive
Two-component epoxy adhesive is commonly used in various industries due to its excellent bonding strength and durability. This type of adhesive comprises two parts: the resin and the hardener, which are mixed in a specific ratio to create a solid and long-lasting bond. Here are some of the advantages of two-component epoxy adhesive:
- Muscular Bonding Strength: Two-component epoxy adhesive has excellent bonding strength due to the cross-linking reaction that occurs when the resin and hardener are mixed. This type of adhesive can bond various materials, including metals, plastics, ceramics, and composites. It can also bond dissimilar materials, making it ideal for joining materials that are difficult to connect with other types of adhesives.
- High Chemical Resistance: Two-component epoxy adhesive is highly resistant to chemicals, making it suitable for use in harsh environments where exposure to chemicals is daily. This adhesive can withstand exposure to acids, alkalis, solvents, and fuels without losing its bonding strength or degrading.
- Excellent Durability: Two-component epoxy adhesive is highly durable and can withstand extreme temperatures, UV light exposure, and mechanical stress. This adhesive can maintain its bonding strength even under harsh conditions, making it ideal for applications that require long-lasting and reliable bonds.
- Versatility: Two-component epoxy adhesive is versatile and can be used in various applications. It can be used as a structural adhesive, a sealant, a potting compound, or a coating material. This adhesive is compatible with multiple substrates and can bond with different materials, including metals, plastics, and composites.
- Easy to Use: Two-component epoxy adhesive is easy to use and can be applied using various methods, including brush, roller, spray, or dispensing equipment. This adhesive has a long pot life, allowing sufficient time for the application and positioning of the substrates before the adhesive cures.
- Cost-effective: Two-component epoxy adhesive is cost-effective compared to other types of adhesives. Although the initial cost may be higher than other adhesives, the long-term price is lower due to the adhesive’s durability and long-lasting bonding strength. Additionally, the versatile nature of the two-component epoxy adhesive reduces the need for multiple adhesives, thereby saving costs on inventory and production.
Disadvantages of Two-Component Epoxy Adhesive
Two-component epoxy adhesive is a popular choice for bonding a wide range of materials due to its high strength, durability, and resistance to harsh environments. However, like any other adhesive, it has disadvantages that may limit its use in specific applications. Here are some of the disadvantages of two-component epoxy adhesive:
- Health hazards: Two-component epoxy adhesive can pose health risks if improperly handled. The adhesive contains harmful chemicals that can cause skin irritation, respiratory problems, and other health issues. Wearing protective gear like gloves and a respirator while working with the adhesive is essential to minimize the risks.
- Pot life: Two-component epoxy adhesive has a limited pot life, which means it has to be used within a specific time frame after mixing. If the adhesive is not used within the recommended time, it will start to cure and become unusable. This can be a challenge when working with large volumes or complex structures requiring more bonding time.
- Curing time: Two-component epoxy adhesive requires significant time to cure fully. The curing time can range from a few hours to several days, depending on the type of adhesive and the environmental conditions. This can be a disadvantage when working on time-sensitive projects or when the adhesive needs to cure quickly to meet production deadlines.
- Poor gap-filling ability: Two-component epoxy adhesive is unsuitable for filling significant gaps or voids. It has a low viscosity, so it cannot effectively fill large cracks or holes. This can be a problem when bonding materials with uneven surfaces or when dealing with gaps or joints that require significant filling.
- Cost: Two-component epoxy adhesive is relatively expensive compared to other types of adhesives. This can be a disadvantage when working on large projects that require a significant amount of adhesive. However, it is essential to note that the high cost is often justified by the adhesive’s high strength and durability, which make it a suitable choice for demanding applications.
- Brittle: Two-component epoxy adhesive can become brittle over time, especially when exposed to harsh environments or extreme temperatures. This can reduce its strength and make it more prone to cracking or breaking. It is essential to consider the expected conditions of use before selecting an epoxy adhesive and to choose one with suitable properties for the specific application.
Properties of Two Component Epoxy Adhesive
Two-component epoxy adhesive is a type of adhesive that consists of two parts: a resin and a hardener. When the two parts are mixed, a chemical reaction occurs, which results in a solid and durable bond. Due to its unique properties, two-component epoxy adhesive is widely used in various applications. Here are some of the properties of two-component epoxy adhesive:
- High strength: Two-component epoxy adhesive has a high tensile and shear strength, which makes it suitable for bonding materials that require a solid and durable bond. The adhesive can withstand high stress and can be used in applications where high strength is essential.
- Durability: Two-component epoxy adhesive is highly resistant to chemical, environmental, and mechanical stress. It can withstand exposure to harsh environments, including high and low temperatures, humidity, and UV radiation, without losing its strength or integrity.
- Adhesion: Two-component epoxy adhesive has excellent adhesion to various materials, including metals, plastics, ceramics, and composites. It forms a strong bond with the substrate, making it suitable for bonding materials that are difficult to bond with other adhesives.
- Gap-filling ability: Two-component epoxy adhesive has excellent gap-filling ability, which makes it suitable for bonding materials with uneven surfaces or gaps. The adhesive can fill cracks and voids, enhancing its bond strength and improving its overall integrity.
- Low shrinkage: Two-component epoxy adhesive has low shrinkage, so it maintains its original size and shape after curing. This property is essential when bonding materials with tight tolerances or maintaining the bonded components’ shape is crucial.
- Versatility: Two-component epoxy adhesive is versatile and can be used in various applications, including structural bonding, potting and encapsulation, and sealing and gasketing. It is also suitable for multiple industries, including automotive, aerospace, electronics, and construction.
- Temperature resistance: Two-component epoxy adhesive has excellent temperature resistance and can withstand exposure to high and low temperatures without losing its strength or integrity. This makes it suitable for use in applications where temperature resistance is essential.
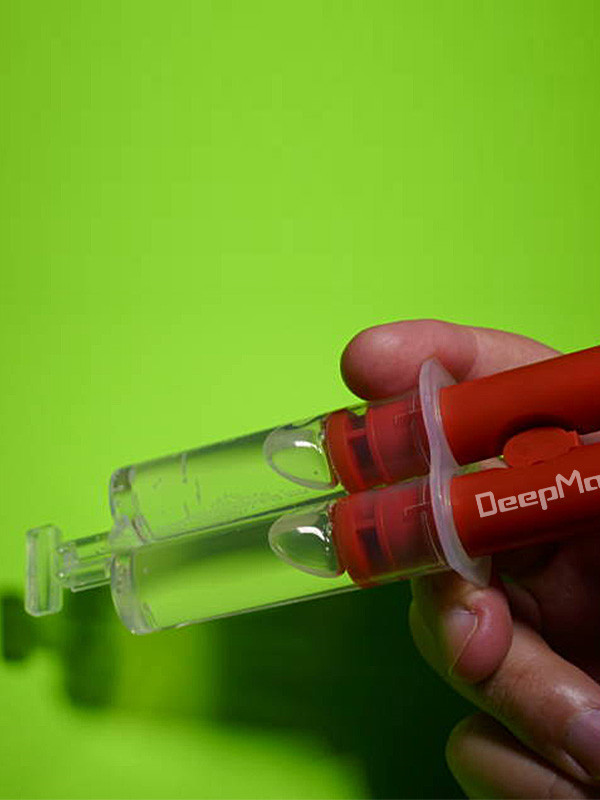
Curing Time of Two Component Epoxy Adhesive
Two-component epoxy adhesive is a type of adhesive that consists of two parts: a resin and a hardener. When these two components are mixed, they form a solid and durable bond resistant to various environmental factors such as moisture, heat, and chemicals. The curing time of two-component epoxy adhesive is an essential factor affecting the bond’s quality and strength.
The curing time of two-component epoxy adhesive can vary depending on several factors, such as the type of adhesive, the environmental conditions, and the thickness of the bond line. Generally, the two-component epoxy adhesive can cure in 5 minutes to 24 hours. Some fast-curing formulations can cure in as little as 5 minutes, while others may take up to 24 hours to fully heal.
The curing time of the two-component epoxy adhesive is affected by the ambient temperature and humidity. Higher temperatures can accelerate the curing process, while lower temperatures can slow it down. Humidity can also affect the curing time, as high humidity can prolong the process.
The thickness of the bond line also plays a role in the curing time of the two-component epoxy adhesive. Thicker bond lines can take longer to cure than thinner bond lines. This is because the curing process’s heat must dissipate through the bond line, and thicker bond lines can trap the heat, slowing the curing process.
To ensure proper curing of two-component epoxy adhesive, following the manufacturer’s instructions and using the correct mixing ratio is essential. The mixing ratio can vary depending on the type of adhesive and the application, and mixing the two components in the right balance ensures that the adhesive cures properly and forms a strong bond.
Sometimes, a post-curing process may be necessary to achieve the desired bond strength. Post-curing involves exposing the bonded parts to elevated temperatures for a specified period, which can improve the bond’s strength and durability.
How to Apply Two-Component Epoxy Adhesive
Two-component epoxy adhesive is a versatile and practical adhesive that can bond various materials, including metal, wood, plastic, and ceramic. It consists of a resin and a hardener that must be mixed to activate the adhesive. Here are the steps for applying two-component epoxy adhesive:
- Preparation: Before starting, make sure that the surfaces to be bonded are clean, dry, and free of any debris, oil, or grease. Sand or roughen smooth surfaces to improve adhesion. You may also need a primer or a surface activator to help the adhesive bond to certain materials.
- Mixing: Carefully measure the correct amount of resin and hardener using a scale or a syringe. The ratio of resin to hardener may vary depending on the manufacturer and the epoxy adhesive used, so be sure to read the instructions carefully. Mix the two components thoroughly, scraping the sides and bottom of the container to ensure all the material is mixed evenly.
- Application: Apply the mixed epoxy adhesive to one of the surfaces to be bonded using a brush, a spatula, or a syringe. Be careful not to apply too much adhesive, which can cause it to drip or ooze out from the bond line. Use a clamp or some other pressure to hold the parts together while the adhesive cures.
- Curing: The curing time for two-component epoxy adhesives will vary depending on the specific product and the environmental conditions. Generally, the adhesive will cure faster at higher temperatures and slower at lower temperatures. Follow the manufacturer’s instructions for fixing time and needs. Letting the adhesive cure completely before subjecting the bond to any stress or load is essential.
- Cleanup: Clean up any excess adhesive or spills immediately using a solvent recommended by the manufacturer. Once the adhesive has cured, removing it may be difficult or impossible.
Precautions to Take While Using Two-Component Epoxy Adhesive
Two-component epoxy adhesives are widely used in various industries for their strong bonding properties. However, they can also be hazardous if not used properly. Therefore, taking certain precautions while using two-component epoxy adhesive is essential to ensure safety and optimal performance. Here are some precautions to take:
- Read the instructions carefully: Always read the manufacturer’s instructions before using the two-component epoxy adhesive. Follow the instructions precisely to ensure that you mix and apply the adhesive properly.
- Wear protective gear: Always wear gloves, safety glasses, and a respirator mask when working with two-component epoxy adhesives. This will protect your skin and eyes from contact with the adhesive and prevent inhalation of harmful vapors.
- Work in a well-ventilated area: Two-component epoxy adhesives emit fumes that can harm your health. Therefore, working in a well-ventilated area is essential to prevent inhaling the fumes. Work in a location with an exhaust fan or open windows to allow for proper air circulation.
- Mix the adhesive properly: Two-component epoxy adhesives require a precise mixing ratio of the resin and hardener to achieve optimal performance. Use a clean mixing container and a clean stirring tool to mix the components evenly.
- Use the adhesive within the specified pot life: Two-component epoxy adhesives have a limited pot life, which is when the adhesive can be used after it has been mixed. Using the adhesive beyond its pot life can result in poor bonding and reduced strength. Always use the adhesive within the specified pot life.
- Use the adhesive in the recommended temperature range: Two-component epoxy adhesives have a recommended temperature range. Using the adhesive outside this range can result in poor bonding and reduced strength. Always use the adhesive within the recommended temperature range.
- Clean surfaces thoroughly before application: For optimal bonding, the characters to be bonded must be clean and free of contaminants such as oil, grease, dirt, and rust. Clean the surfaces with a solvent before applying the adhesive.
- Apply the adhesive evenly: Apply the adhesive evenly to both surfaces to be bonded. Avoid applying too much adhesive, resulting in reduced strength and longer curing times.
- Clamp the surfaces together: To ensure proper bonding, clamp the surfaces together firmly. This will prevent any movement of the characters during curing and help to achieve optimal bonding strength.
- Dispose of the adhesive properly: Two-component epoxy adhesives are hazardous waste and must be disposed of properly. Check with your local regulations on how to dispose of the adhesive and its packaging materials.
Surface Preparation for Two-Component Epoxy Adhesive
Surface preparation is critical in achieving a strong and durable bond when using two-component epoxy adhesive. Proper surface preparation ensures the adhesive can penetrate and bond to the substrate, resulting in a high-strength bond that can withstand stress and environmental conditions.
Here are some critical steps to consider when preparing surfaces for two-component epoxy adhesive:
- Clean the Surface: The first step in surface preparation is thoroughly cleaning the surface. Any oil, grease, dirt, dust, or other contaminants on the surface can prevent the adhesive from bonding properly. Use a solvent like acetone or isopropyl alcohol to remove dirt or oil. You can also use a wire brush or sandpaper to remove loose paint or rust.
- Abrade the Surface: Abrading the surface is essential to ensure the adhesive has a rough surface to bond to. Use a coarse abrasive material like sandpaper or a wire brush to roughen the surface. This step is crucial if the surface is smooth or glossy.
- Etch the Surface: In some cases, etching the surface can improve the bond strength of the adhesive. Etching involves applying an acid to the surface to create a rougher texture to which the adhesive can better bond. Phosphoric acid is commonly used for this purpose.
- Dry the Surface: After cleaning, abrading, and etching the surface, it is essential to dry it thoroughly. Use a clean, dry cloth or compressed air to remove any moisture from the surface. Any water left on the surface can compromise the bond strength of the adhesive.
- Apply the Adhesive: Once the surface is prepared, it is time to apply the adhesive. Follow the manufacturer’s instructions carefully, mixing the adhesive’s two components together thoroughly. Apply the adhesive evenly to the surface using a brush, roller, or spatula.
- Clamp the Substrate: Clamping the substrate after applying the adhesive is essential to achieve the strongest bond possible. Clamping helps hold the two surfaces together, ensuring the adhesive cures evenly and thoroughly. Follow the manufacturer’s instructions for clamping time and pressure.
Applications of Two-Component Epoxy Adhesive in Different Industries
Two-component epoxy adhesive is a versatile, high-performance adhesive used in various industries for its exceptional bonding strength and durability. Here are some typical applications of two-component epoxy adhesives in different sectors.
- Construction Industry: Two-component epoxy adhesive is used in construction for bonding a wide range of materials such as concrete, wood, metal, and plastic. It is used to fix cracks in concrete structures, anchor bolts, and reinforce concrete joints. Epoxy adhesives are also used in the construction of precast concrete elements.
- Automotive Industry: Two-component epoxy adhesive is used in the automotive industry for bonding components such as body panels, windshields, and structural components. It provides high strength and durability, making it ideal for use in automotive manufacturing.
- Electronics Industry: Two-component epoxy adhesive is used in the electronics industry for encapsulating and bonding electronic components. It seals and protects sensitive electronic components such as circuit boards, semiconductors, and sensors from moisture, dust, and other contaminants.
- Aerospace Industry: Two-component epoxy adhesive is used in the aerospace industry for bonding composite materials, such as carbon fiber, to metal components. It is used to manufacture aircraft and spacecraft components, such as wings, fuselages, and engines.
- Marine Industry: Two-component epoxy adhesive is used in the marine industry for bonding and sealing boat parts such as hulls, decks, and superstructures. It is also used to repair and reinforce damaged or cracked parts of boats and yachts.
- Packaging Industry: Two-component epoxy adhesive is used in the packaging industry for bonding and sealing materials such as cardboard, plastic, and metal. It is used to manufacture packaging materials, such as boxes, cartons, and bags.
- Medical Industry: Two-component epoxy adhesive is used in the medical industry for bonding and sealing medical devices and implants. It is used to bond metal, ceramic, and plastic materials in medical devices such as orthopedic implants, dental implants, and prosthetics.
Automotive Industry Applications of Two-Component Epoxy Adhesive
The two-component epoxy adhesive has many applications in the automotive industry due to its excellent bonding properties, durability, and heat, chemicals, and mechanical stress resistance. Here are some typical automotive industry applications of two-component epoxy adhesive:
- Bonding metal parts: Two-component epoxy adhesive is commonly used to bond metal parts, such as engine components, transmission parts, and body panels. The adhesive can provide a strong, permanent bond that can withstand high temperatures and mechanical stress.
- Repairing plastic parts: Two-component epoxy adhesive can improve plastic parts, such as bumpers, dashboards, and interior trim pieces. The adhesive can fill cracks and gaps and provide a robust and durable bond that can withstand exposure to heat, chemicals, and UV radiation.
- Bonding glass: Two-component epoxy adhesive can bond glass to metal or plastic parts, such as windshields, mirrors, and headlights. The adhesive can provide a robust and durable bond that can withstand heat, moisture, and vibration exposure.
- Sealing and coating: Two-component epoxy adhesive can be used as a sealant or coating for automotive parts, such as engine blocks, transmissions, and exhaust systems. The adhesive can protect against moisture, chemicals, and corrosion.
- Bonding composites: Two-component epoxy adhesive can be used to bond composite materials, such as carbon fiber and fiberglass, to metal or plastic parts. The adhesive can provide a robust and durable bond that can withstand heat, moisture, and vibration exposure.
- Bonding rubber: Two-component epoxy adhesive can bond rubber parts, such as hoses, gaskets, and seals. The adhesive can provide a robust and flexible bond that can withstand heat, chemicals, and mechanical stress exposure.
- Assembly of electronic components: Two-component epoxy adhesive can bond electronic components, such as sensors and control units, to automotive parts. The adhesive can provide a robust and durable bond that can withstand heat, moisture, and vibration exposure.
Aerospace Industry Applications of Two-Component Epoxy Adhesive
Two-component epoxy adhesive is widely used in the aerospace industry due to its exceptional bonding properties, durability, and resistance to extreme conditions. This type of adhesive comprises two parts – a resin and a hardener – mixed in specific proportions to create a solid and long-lasting bond.
One of the main applications of two-component epoxy adhesive in the aerospace industry is bonding composite materials. Composite materials are widely used in the aerospace industry due to their high strength-to-weight ratio, but they are often difficult to bond using traditional adhesives. However, Two-component epoxy adhesives have been specifically formulated to bond composite materials and can create strong and durable bonds between composite components, such as wings, fuselage, and tail sections.
Two-component epoxy adhesive is also used for bonding metal parts in the aerospace industry. This adhesive can bond various metals, including aluminum, titanium, and stainless steel. This is important because many aerospace components are made of these materials and require solid and reliable bonds to ensure safe and reliable operation.
Another application of two-component epoxy adhesive in the aerospace industry is bonding electronic components. This adhesive is ideal for connecting electronic components because it has excellent electrical insulation properties and can create a solid, durable bond that can withstand extreme space conditions.
Two-component epoxy adhesive is also used for repairing aircraft components damaged due to impact, wear, or corrosion. This adhesive is ideal for repairing components because it has a high strength-to-weight ratio, can bond a wide range of materials, and can be used in various repair situations.
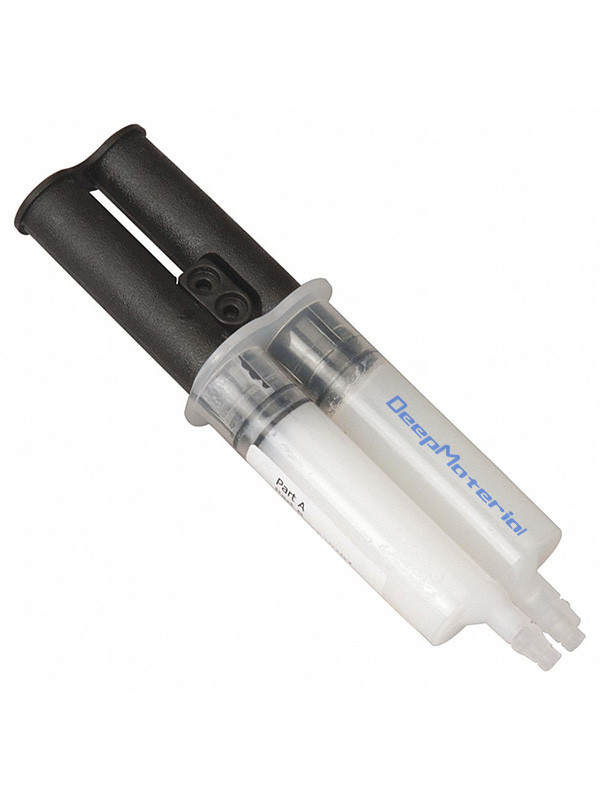
I am text block. Click edit button to change this text. Lorem ipsum dolor sit amet, consectetur adipiscing elit. Ut elit tellus, luctus nec ullamcorper mattis, pulvinar dapibus leo.
In addition to its bonding properties, a two-component epoxy adhesive is known for resisting various chemicals, including fuels, oils, and solvents. This is particularly important in the aerospace industry, where aircraft are exposed to multiple chemicals during operation.
Finally, a two-component epoxy adhesive is also used in the aerospace industry for its heat resistance properties. This adhesive can withstand high temperatures without degrading or losing its bonding properties, making it an ideal adhesive for use in engines and other high-temperature applications.
Construction Industry Applications of Two-Component Epoxy Adhesive
Two-component epoxy adhesives are widely used in the construction industry due to their excellent bonding properties and high durability. These adhesives consist of a resin and a hardener, which are mixed together to create a strong bond.
One common application of two-component epoxy adhesives in the construction industry is anchoring bolts and other fixtures. These adhesives secure bolts into concrete or other surfaces, creating a solid and long-lasting bond. The adhesive is applied to the bolt and then inserted into a hole drilled into the concrete or other surface. As the adhesive cures, it bonds the bolt and the surrounding material, ensuring it remains firmly in place.
Another common construction application for two-component epoxy adhesives is for bonding metal or plastic components. These adhesives often fabricate composite materials like fiberglass-reinforced plastic (FRP) panels. The adhesive is applied to the surfaces of the pieces to be bonded, and then the parts are pressed together. As the adhesive cures, it forms a strong bond between the two elements, creating a single, durable structure.
Two-component epoxy adhesives are also used for structural bonding in construction applications. This can include bonding structural components such as beams, columns, and trusses. These adhesives are ideal for this application because of their high strength and ability to withstand stress and movement. In addition, two-component epoxy adhesives have excellent resistance to water, chemicals, and temperature extremes, making them suitable for harsh environments.
Another application of two-component epoxy adhesives in construction is to repair concrete structures. These adhesives can fill cracks and gaps in concrete and improve damaged areas. The adhesive is applied to the damaged area and then allowed to cure. Once cured, the adhesive forms a strong bond with the surrounding concrete, restoring the strength and integrity of the structure.
Overall, two-component epoxy adhesives are highly versatile and widely used in construction. They offer excellent bonding properties, high durability, and resistance to various environmental factors. From anchoring bolts to structural bonding, these adhesives are essential for construction professionals to create solid, long-lasting structures.
Electronics Industry Applications of Two-Component Epoxy Adhesive
Two-component epoxy adhesives are widely used in the electronics industry due to their excellent adhesive properties, mechanical strength, and electrical insulation properties. Here are some of the applications of two-component epoxy adhesives in the electronics industry:
- Bonding of electronic components: Two-component epoxy adhesives are commonly used for bonding electronic components such as chips, capacitors, and resistors to printed circuit boards (PCBs). The adhesive forms a solid, durable bond that can withstand mechanical stress and thermal cycling.
- Potting and encapsulation: Two-component epoxy adhesives are used for potting and encapsulating electronic components such as transformers, sensors, and circuit boards. The bond protects against moisture, dust, and other contaminants damaging electronic components.
- Coating and sealing: Two-component epoxy adhesives can be used as coatings and sealants for electronic components and assemblies. The adhesive protects against corrosion, moisture, and other environmental factors damaging electronic components.
- Thermal management: Two-component epoxy adhesives are used for thermal management in electronic devices such as power amplifiers, CPUs, and LED lights. The adhesive can be used as a heat sink to dissipate heat generated by electronic components, which helps to prevent overheating and damage to the members.
- Repair and maintenance: Two-component epoxy adhesives are used for repairing and maintaining electronic components and assemblies. The adhesive can fill gaps, cracks, and other defects in electronic components, which helps restore their structural integrity and functionality.
- Optical applications: Two-component epoxy adhesives are used in optical applications such as bonding lenses, prisms, and optical fibers. The bond provides excellent optical clarity and does not yellow or degrade over time.
- Sensors and actuators: Two-component epoxy adhesives are used for bonding and encapsulating sensors and actuators in various electronic devices. The adhesive protects against environmental factors such as moisture, heat, and vibration, which can damage sensitive electronic components.
Marine Industry Applications of Two-Component Epoxy Adhesive
Two-component epoxy adhesive is widely used in the marine industry due to its excellent bonding strength and durability. This type of adhesive comprises two parts, a resin, and a hardener, mixed just before use. Once applied, the mixture cures into a strong, rigid material resistant to water, chemicals, and impact. This article will discuss some of the marine industry applications of two-component epoxy adhesives.
- Boat building and repair: Two-component epoxy adhesive is used extensively in boat building and repair. It is ideal for bonding fiberglass, wood, metal, and other materials commonly used in boats. The adhesive’s ability to form solid and permanent bonds makes it an excellent choice for laminating decks and hulls, attaching hardware and fittings, and repairing damage caused by collisions or grounding.
- Marine maintenance: Two-component epoxy adhesive is an excellent material for marine maintenance. It can repair cracks, holes, and leaks in boat hulls, tanks, and pipes. It can also fill voids, reinforce weak spots, and rebuild damaged areas. The adhesive’s ability to cure underwater makes it ideal for repairing boats that cannot be lifted out of the water.
- Marine metal bonding: Two-component epoxy adhesive is also used for bonding metal components in the marine industry. It can bond stainless steel, aluminum, and other metals commonly used in boats. The adhesive’s ability to form strong, durable bonds makes it ideal for bonding metal fittings, brackets, and other components subject to stress and vibration.
- Propeller Repair: Two-component epoxy adhesive can be used to repair damaged propellers. The adhesive can fill cracks and chips in the propeller blades, restoring the blade’s shape and performance. The adhesive’s ability to withstand the harsh marine environment makes it an ideal choice for propeller repair.
- Fiberglass repair: Two-component epoxy adhesive is commonly used to repair fiberglass components in the marine industry. It can repair cracks, holes, and other damage to fiberglass hulls, decks, and other features. The adhesive’s ability to bond strongly to fiberglass makes it an excellent choice for repairing fiberglass boats.
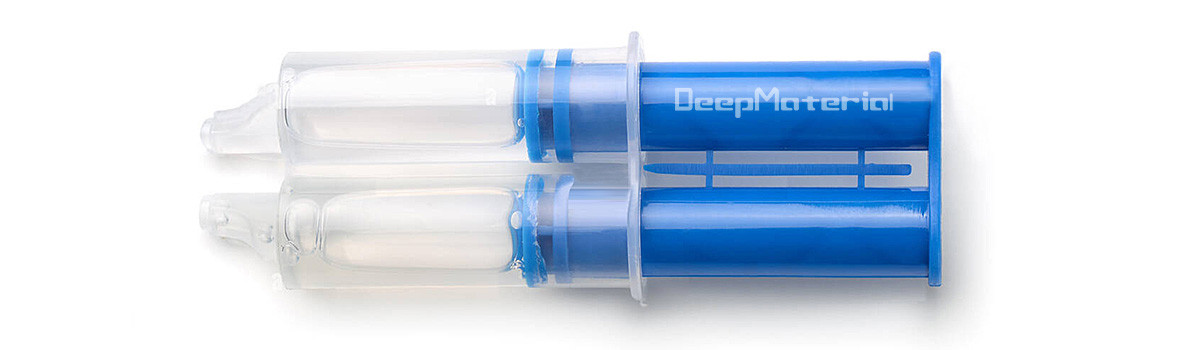
Medical Industry Applications of Two-Component Epoxy Adhesive
Two-component epoxy adhesive is widely used in the medical industry due to its excellent bonding properties, high strength, and chemical and environmental exposure resistance. Here are some applications of two-component epoxy adhesive in the medical industry:
- Medical devices assembly: Two-component epoxy adhesive is used to bond various medical devices, such as catheters, syringes, surgical instruments, and prosthetics. The adhesive provides a strong and durable bond, essential for ensuring medical devices’ reliability and safety.
- Dental applications: Two-component epoxy adhesive is used in dentistry for various applications, such as bonding dental implants, crowns, bridges, and veneers. The adhesive provides a strong and durable bond that can withstand the harsh environment of the oral cavity.
- Wound care products: Two-component epoxy adhesive is used to manufacture wound care products such as medical tapes, bandages, and dressings. The bond provides excellent adhesion to the skin and is also hypoallergenic, making it safe for use on sensitive skin.
- Laboratory equipment: Two-component epoxy adhesive is used to manufacture laboratory equipment such as pipettes, test tubes, and Petri dishes. The adhesive provides a strong bond that can withstand the harsh chemicals used in laboratories.
- Drug delivery systems: Two-component epoxy adhesive is used to manufacture drug delivery systems such as transdermal patches, implantable devices, and inhalers. The adhesive provides a strong and durable bond that can withstand the harsh environment of the body.
- Orthopedic applications: Two-component epoxy adhesive is used in orthopedic applications such as bonding joint prostheses and bone cement. The adhesive provides a strong and durable bond that can withstand the stresses and strains placed on orthopedic implants.
- Medical electronics: Two-component epoxy adhesive is used to manufacture medical electronics such as pacemakers, defibrillators, and neurostimulators. The adhesive provides a strong bond that can withstand the harsh body environment and provides electrical insulation.
Consumer Goods Industry Applications of Two-Component Epoxy Adhesive
The consumer goods industry encompasses a wide range of products, and the applications of two-component epoxy adhesives within this industry are numerous. Two-component epoxy adhesive is a versatile, high-performance adhesive that offers excellent bonding strength, durability, and resistance to various environmental conditions. Let’s explore some typical applications of this adhesive in the consumer goods industry.
- Electronics and Electrical Devices: Two-component epoxy adhesive is extensively used to assemble and manufacture electronics and electrical devices. It strongly bonds circuit boards, components, and connectors, ensuring reliable electrical connections. The adhesive also offers protection against moisture, chemicals, and vibrations, enhancing the durability and performance of electronic products.
- Automotive Industry: Two-component epoxy adhesive plays a crucial role in the automotive industry. It is used for bonding various components, such as body panels, interior trim, and structural parts. The adhesive provides excellent adhesion to metals, composites, and plastics, contributing to the overall strength and integrity of the vehicle. Additionally, it offers resistance to temperature variations, fluids, and mechanical stresses, ensuring long-lasting bonds in challenging automotive environments.
- Appliances and White Goods: In the manufacturing of machines and white goods, two-component epoxy adhesive finds applications in bonding metal, glass, plastic, and ceramic components. It is commonly used for sealing and joining parts in refrigerators, ovens, washing machines, and other household appliances. The adhesive’s resistance to heat, water, and chemicals ensures that the devices maintain performance and withstand daily use.
- Furniture and Woodworking: Two-component epoxy adhesive is widely used in the furniture and woodworking industry for bonding wooden components, laminates, and veneers. The adhesive provides solid and durable bonds, which are essential for the structural integrity of furniture. It also offers moisture, heat, and chemical resistance, preventing delamination and ensuring long-term durability.
- Sporting Goods and Outdoor Equipment: Two-component epoxy adhesive produces sporting goods and outdoor equipment, including bicycles, skis, surfboards, and camping gear. It is used for bonding materials like carbon fiber, fiberglass, metals, and plastics, providing the required strength and durability. The adhesive’s resistance to environmental conditions, such as water, UV rays, and temperature fluctuations, helps maintain the performance and longevity of these products.
- Footwear and Accessories: Two-component epoxy adhesive is used in the footwear industry for bonding shoe soles, uppers, and various components. It offers strong adhesion to different materials, including rubber, leather, fabric, and plastics, ensuring the durability and quality of footwear. The adhesive also provides resistance to moisture, chemicals, and mechanical stresses, contributing to the longevity of shoes and accessories.
Environmental Benefits of Two-Component Epoxy Adhesive
Two-component epoxy adhesive offers several environmental benefits, making it a preferred choice in many industries. Here are some key environmental advantages of using this adhesive:
- Reduced Waste: Two-component epoxy adhesive has a long shelf life and can be stored for extended periods without degradation. Unlike some bonds with a limited pot life once mixed, the epoxy adhesive allows for precise application and reduces the likelihood of excess material going to waste. This minimizes the adhesive that needs to be discarded, resulting in reduced waste generation.
- Lower Volatile Organic Compounds (VOC) Emissions: VOCs are chemicals that can harm human health and contribute to air pollution. Compared to solvent-based adhesives, two-component epoxy adhesives typically have low VOC content. By using epoxy adhesives with low VOC emissions, industries can minimize their impact on air quality and create a safer working environment for employees.
- Durable and Long-Lasting Bonds: Two-component epoxy adhesive forms solid and durable bonds, providing excellent resistance to environmental factors such as moisture, temperature variations, and chemicals. This durability reduces the need for frequent repairs or replacements, thereby extending the lifespan of products. By enhancing product longevity, epoxy adhesive helps reduce the overall demand for new materials and decreases the environmental impact associated with manufacturing and disposal.
- Energy Efficiency: The curing process of a two-component epoxy adhesive typically requires moderate temperatures and can be accelerated by applying heat. Unlike other adhesive options that require higher temperatures or longer curing times, epoxy adhesives can offer energy-efficient curing processes. This reduces energy consumption during manufacturing processes, lowering greenhouse gas emissions and energy costs.
- Recyclability: Some types of two-component epoxy adhesives can be formulated to facilitate the disassembly and recycling of bonded components. This is particularly valuable in electronics and automotive manufacturing industries, where the ability to separate and recycle materials at the end of the product’s life cycle is essential. By enabling easier recycling, epoxy adhesive promotes circular economy principles and reduces the reliance on virgin materials.
- Reduced Environmental Footprint: Using two-component epoxy adhesive in various applications can reduce environmental footprint. Its versatile nature allows for the bonding of different materials, eliminating the need for mechanical fasteners or more resource-intensive joining methods. This can lead to material savings, lighter product designs, and reduced resource consumption throughout manufacturing.
Conclusion: Two-Component Epoxy Adhesive – A Strong and Versatile Bonding Solution
The two-component epoxy adhesive stands out as a powerful and versatile bonding solution in adhesive technology. This unique adhesive offers many benefits, making it a preferred choice in various industries and applications. With its exceptional strength, durability, and adaptability, the two-component epoxy adhesive has cemented its position as a go-to option for bonding a wide range of materials.
One of the key advantages of the two-component epoxy adhesive is its unparalleled strength. It forms a powerful bond between substrates, whether they are metals, plastics, ceramics, or composites. This adhesive exhibits excellent tensile and shear strength, enabling it to withstand substantial loads and stresses. Whether bonding structural components in construction or securing industrial machinery parts, the two-component epoxy adhesive provides a reliable and long-lasting solution.
Furthermore, the versatility of the two-component epoxy adhesive is genuinely remarkable. It is compatible with various materials, allowing for diverse applications across industries. This adhesive adheres well to porous and non-porous surfaces, making it suitable for bonding different substrates. Additionally, it can withstand a wide range of temperatures, from extreme cold to high heat, without compromising its integrity. This versatility makes the two-component epoxy adhesive an ideal choice for applications in aerospace, automotive, electronics, and many other sectors.
The adhesive’s curing process is another noteworthy aspect. As the name suggests, the two-component epoxy adhesive consists of two separate components—a resin and a hardener—that need to be mixed in specific proportions. This feature provides several advantages. Firstly, it allows for precise control over the adhesive’s curing time, ensuring sufficient working time for complex assemblies. Secondly, it enables bonding in challenging environments, such as underwater or extreme weather conditions. Once the epoxy is mixed correctly and applied, it undergoes a chemical reaction that results in a solid and durable bond.
In addition to its mechanical strength, the two-component epoxy adhesive also offers exceptional chemical resistance. It is highly resistant to various chemicals, solvents, and environmental factors, including moisture and UV radiation. This resistance makes it an ideal choice for applications that require exposure to harsh conditions or aggressive substances. Whether sealing joints in chemical processing plants or bonding components in marine environments, the two-component epoxy adhesive maintains its integrity and performance over time.
In conclusion, the two-component epoxy adhesive is a powerful and versatile bonding solution. Its exceptional strength, durability, adaptability, and chemical resistance have become a staple in numerous industries and applications. This adhesive delivers reliable and long-lasting bonds between various materials, from construction and manufacturing to electronics and automotive sectors. As technology advances, the two-component epoxy adhesive continues to evolve, providing even more outstanding performance and expanding its scope of applications. The two-component epoxy is an exceptional choice for those seeking a robust and versatile bond.