Personal Electronic Devices Adhesive
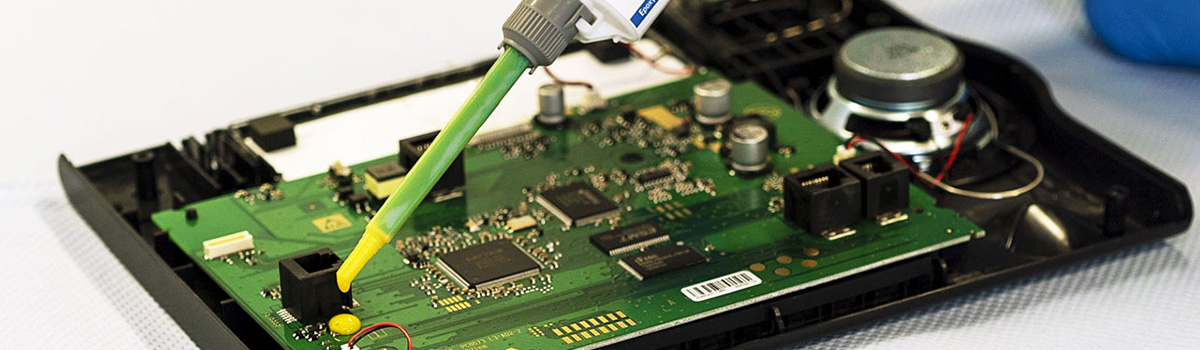
The use of adhesives and sealants in the electronics industry is now widespread and they contribute directly not only to the manufacture of electronics products but also to their long-term operation and longevity. Major uses of adhesives in the electronic industry include bonding of surface-mount components (SMCs), wire tacking and potting or encapsulating components. The basic building block of the electronics industry is the printed wiring board or, as it is more commonly called, the printed circuit board (PCB). The PCB makes use of adhesive materials in bonding surface-mount components, wire tacking, conformal coatings and in encapsulating (potting) components.
Three different processing phases must be considered when selecting an adhesive for electronics (or any other) applications: the uncured or liquid-resin phase, the curing (transitional) phase and the cured or solid-material phase.
The performance of the cured adhesive is ultimately the most important because it affects reliability.
The method of applying the adhesive is also of great importance, in particular because of the need to ensure that the correct amount is applied in the correct place.
Major methods of applying adhesives in electronics applications are screen printing (squeezing the adhesive through patterns in a screen), pin transfer (using multi-pin grids which convey patterns of adhesive drops to the board) and syringe application (in which shots of adhesive are delivered by a pressure-regulated syringe). Syringe application is probably the most popular method, usually by way of electro-pneumatically-controlled syringes for moderate production of many different types of PCB.
The various types of adhesive will now be considered.
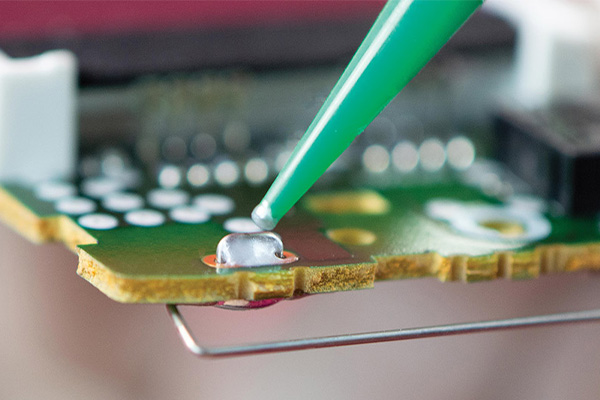
By their nature, most adhesives, both organic and inorganic, are not electrically conductive. This applies to the main types used in electronic applications such as epoxies, acrylics, cyanoacrylates, silicones, urethane acrylates and cyanoacrylates. However, in many applications, including integrated circuits and surface-mount devices, electrically conductive adhesives are required.
The usual way of converting non-conductive adhesives to electrically conductive materials is to add suitable filler to the base material; usually the latter is an epoxy resin.
Typical fillers used to confer electrical conductivity are silver, nickel and carbon. Silver is the most widely used. The conductive adhesives themselves are either in a liquid or pre-form (reinforced adhesive films die-cut before bonding to the shape required).
There are two types of electrically conductive adhesives – isotropic and anisotropic. Anisotropic adhesives conduct in all directions but an isotropic adhesive conducts in the vertical (z-axis) direction only and is thus uni-directional.
The isotropic adhesives lend themselves to fine-line interconnection. It should be noted that, useful as conductive adhesives are, they cannot be simply ‘dropped in’ as solder alternatives. They are not good with tin (or tincontaining alloys) or with aluminium, nor where there are large gaps or where they are likely to be exposed to wet (damp, moist) conditions in service.
Electrically conductive adhesives
By their nature, most adhesives, both organic and inorganic, are not electrically conductive. This applies to the main types used in electronic applications such as epoxies, acrylics, cyanoacrylates, silicones, urethane acrylates and cyanoacrylates. However, in many applications, including integrated circuits and surface-mount devices, electrically conductive adhesives are required.
The usual way of converting non-conductive adhesives to electrically conductive materials is to add suitable filler to the base material; usually the latter is an epoxy resin.
Typical fillers used to confer electrical conductivity are silver, nickel and carbon. Silver is the most widely used.
The conductive adhesives themselves are either in a liquid or pre-form (reinforced adhesive films die-cut before bonding to the shape required).
There are two types of electrically conductive adhesives – isotropic and anisotropic. Anisotropic adhesives conduct in all directions but an isotropic adhesive conducts in the vertical (z-axis) direction only and is thus uni-directional.
The isotropic adhesives lend themselves to fine-line interconnection. It should be noted that, useful as conductive adhesives are, they cannot be simply ‘dropped in’ as solder alternatives. They are not good with tin (or tincontaining alloys) or with aluminium, nor where there are large gaps or where they are likely to be exposed to wet (damp, moist) conditions in service.
Thermally conductive adhesives
Miniaturisation of electronic circuitry may result in problems of heat build-up, which can cause premature failure of electronic components if their maximum operating temperature is exceeded. Thermally conductive adhesive can be used to provide a heat-conducting path, fastening transistors, diodes or other power devices to suitable heat sinks to ensure such a heat build-up does not occur.
Metallic (electrically conductive) or non-metallic (insulating) powders are blended into the adhesive formulation to make high-viscosity (paste) adhesives, which are highly thermally conductive (in comparison with unfilled adhesives). The most common thermally conductive systems are formulated with epoxy, silicone and acrylics.
Ultraviolet-curing adhesives
Light-curing adhesives, coatings and encapsulants are being used in the electronics manufacturing industry with increasing frequency because they meet the requirements for materials and processing within this industry. Those factors include environmental demands (environmentallydamaging solvents and additives are not required), manufacturing-yield improvement and product cost. Light-curing adhesives are simple to use, and are quickly cured without the need for elevated temperature curing.
The adhesives are normally acrylic-based formulations and contain photo-initiators which, when activated by ultraviolet radiation, form free radicals to initiate the polymer-forming (curing) process. Ultraviolet light must be able to penetrate into the uncured resin – a drawback of lightcuring adhesives. Deposits of resin that are dark-coloured, inaccessible or very thick are difficult to cure.