PVC Bonding Adhesive
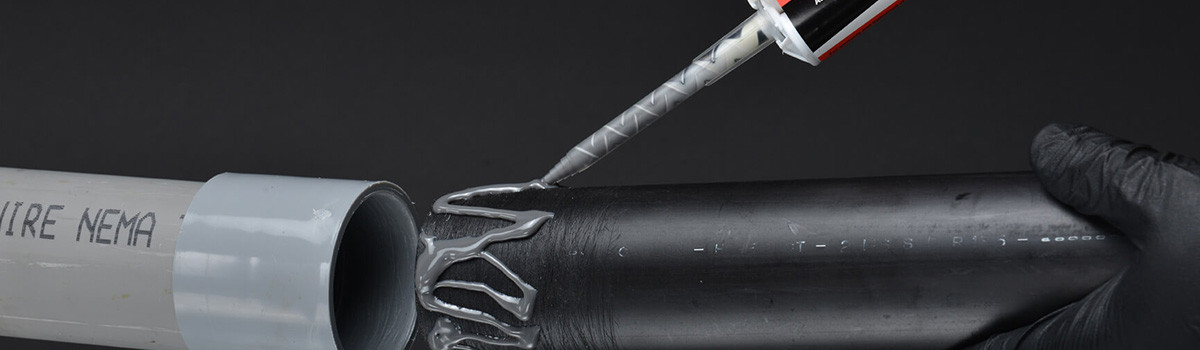
PVC, or polyvinyl chloride, is a widely used synthetic polymer in various industries, including construction, plumbing, and automotive. PVC materials require a strong, durable bond to maintain their integrity and performance, and that’s where PVC bonding adhesives come in. These adhesives provide a reliable bond between PVC materials, eliminating the need for mechanical fasteners. This article will provide a comprehensive guide to PVC bonding adhesives, including their types, properties, applications, and safety considerations.
Definition of PVC bonding adhesives
PVC bonding adhesives are formulated to create a strong and permanent bond between PVC materials. These adhesives contain chemicals that react with the PVC molecules to create a durable bond. PVC bonding adhesives come in different forms, including solvent-based adhesives, reactive adhesives, and two-component adhesives. The choice of adhesive will depend on the type of PVC materials being bonded and the application requirements.
PVC bonding adhesives can be traced back to the 1940s when PVC was first developed. At that time, PVC was considered an inert material challenging to bond. However, as the use of PVC increased in various applications, the need for a strong and reliable bonding adhesive also increased. In the 1950s, the first solvent-based PVC bonding adhesives were developed, revolutionizing the use of PVC in the construction industry. Since then, PVC bonding adhesives have continued to evolve, with new formulations and technologies designed to meet different industries’ changing needs.
Types of PVC bonding adhesives: solvent-based
Polyvinyl chloride (PVC) bonding adhesives create solid and long-lasting bonds between PVC materials. Various PVC bonding adhesives are available, each with unique properties and applications. Here we will explore one of the most common PVC bonding adhesives – solvent-based adhesives.
Solvent-Based PVC Bonding Adhesives
Solvent-based PVC bonding adhesives are formulated using a mixture of solvents and resins. These adhesives are typically fast-drying, creating a solid and durable bond between PVC materials. They are commonly used in construction for bonding PVC pipes, fittings, and other components.
Applications of Solvent-Based PVC Bonding Adhesives
Solvent-based PVC bonding adhesives are ideal for applications that require a quick-drying, strong, and durable bond. Some of the standard applications of these adhesives include:
- Construction Industry: Solvent-based PVC bonding adhesives are widely used in the construction industry for bonding PVC pipes and fittings. They create a leak-proof bond that can withstand high pressures and temperatures, making them ideal for plumbing applications.
- Automotive Industry: Solvent-based PVC bonding adhesives are used in the automotive industry to bond PVC components. These adhesives create a strong bond that can withstand the vibrations and stresses of the vehicle.
- Manufacturing Industry: Solvent-based PVC bonding adhesives are used in the manufacturing industry to bond PVC materials together. They commonly produce PVC flooring, furniture, and other consumer goods.
Benefits of Solvent-Based PVC Bonding Adhesives
Solvent-based PVC bonding adhesives offer several advantages over other types of adhesives, including:
- Quick-Drying: Solvent-based PVC bonding adhesives dry quickly, allowing for faster production times and installation.
- High Strength: Solvent-based PVC bonding adhesives create a solid and durable bond between PVC materials that can withstand various stresses and strains.
- Cost-Effective:Solvent-based PVC bonding adhesives are typically less expensive than other adhesives, making them an affordable choice for many industries.
- Versatility: Solvent-based PVC bonding adhesives can bond various PVC materials, making them ideal for multiple industries and applications.
Types of PVC bonding adhesives: water-based
Polyvinyl chloride (PVC) bonding adhesives are essential for creating strong, long-lasting bonds between PVC materials. Various PVC bonding adhesives are available, each with unique properties and applications. Here we will explore one of the most common PVC bonding adhesives – water-based adhesives.
Water-Based PVC Bonding Adhesives
Water-based PVC bonding adhesives are formulated using water as a carrier and resins as the primary adhesive component. These adhesives are low in VOC (volatile organic compounds) and are an eco-friendly alternative to solvent-based adhesives. They are typically non-toxic, non-flammable, and easy to clean with water.
Applications of Water-Based PVC Bonding Adhesives
Water-based PVC bonding adhesives are ideal for applications that require a low-VOC, non-toxic, and easy-to-use adhesive. Some of the standard applications of these adhesives include:
- Home Renovations: Water-based PVC bonding adhesives are ideal for bonding PVC tiles and vinyl flooring during home renovations. They are easy to apply and clean up, making them a popular choice for DIY enthusiasts.
- Textile Industry: Water-based PVC bonding adhesives are used in the textile industry to bond PVC fabrics together. They are non-toxic and safe to use on clothing and other textiles.
- Packaging Industry: Water-based PVC bonding adhesives are used in the packaging industry to bond PVC films and other materials together. They are low in VOCs and are safe to use for food packaging.
Benefits of Water-Based PVC Bonding Adhesives
Water-based PVC bonding adhesives offer several advantages over other types of adhesives, including:
- Eco-Friendly: Water-based PVC bonding adhesives are low in VOCs and are an eco-friendly alternative to solvent-based adhesives.
- Non-Toxic: Water-based PVC bonding adhesives are typically non-toxic and safe for various applications.
- Easy Cleanup: Water-based PVC bonding adhesives can be easily cleaned with water, making them easy to use and less messy than other adhesives.
- Versatility:Water-based PVC bonding adhesives can bond various PVC materials, making them ideal for multiple industries and applications.
Types of PVC bonding adhesives: two-part epoxy
When it comes to bonding PVC materials, there are various types of adhesives, and two-part epoxy is one of the most commonly used PVC bonding adhesives. Here we will explore the benefits and applications of two-part epoxy PVC bonding adhesives.
Two-Part Epoxy PVC Bonding Adhesives
Two-part epoxy PVC bonding adhesives are composed of resin and hardener, creating a solid and durable bond that can withstand high stresses and loads when mixed. Two-part epoxy PVC bonding adhesives can bond PVC materials to each other and other materials such as metal, wood, and concrete.
Applications of Two-Part Epoxy PVC Bonding Adhesives
Two-part epoxy PVC bonding adhesives are commonly used in a variety of applications, including:
- Construction: Two-part epoxy PVC bonding adhesives are used in the construction industry to bond PVC pipes, fittings, and other materials together. They provide a strong, long-lasting bond that can withstand harsh weather conditions and high-stress levels.
- Automotive Industry: Two-part epoxy PVC bonding adhesives are used in the automotive industry to bond PVC materials to other materials, such as metal and glass. They provide a strong, durable bond that withstands high-stress levels and vibrations.
- Marine Industry: Two-part epoxy PVC bonding adhesives are used in the marine industry to bond PVC materials to other materials, such as fiberglass and wood. They provide a solid and durable bond that can withstand harsh marine environments.
Benefits of Two-Part Epoxy PVC Bonding Adhesives
Two-part epoxy PVC bonding adhesives offer several benefits over other types of adhesives, including:
- High Strength: Two-part epoxy PVC bonding adhesives create a solid, durable bond that can withstand high stresses and loads.
- Chemical Resistance: Two-part epoxy PVC bonding adhesives resist chemicals, making them ideal for harsh environments.
- Easy to Use: Two-part epoxy PVC bonding adhesives are easy to mix and apply, making them a popular choice for DIY enthusiasts.
- Versatility:Two-part epoxy PVC bonding adhesives can bond PVC materials to various other materials, including metal, wood, and concrete.
Properties of PVC bonding adhesives: Strength
When it comes to bonding PVC materials, the properties of the adhesive are of utmost importance. One of the most essential properties of PVC bonding adhesives is strength. Here we will explore the properties of PVC bonding adhesives, explicitly focusing on strength.
Strength of PVC Bonding Adhesives
The strength of a PVC bonding adhesive is a measure of its ability to hold materials together under stress. When bonding PVC materials, choosing an adhesive that is strong enough to withstand the pressures and loads that the materials will be subjected to is essential. The strength of a PVC bonding adhesive is determined by several factors, including:
- Chemical Composition:The chemical composition of the adhesive determines its strength. Adhesives that are composed of more vital chemicals will generally have higher power.
- Application Method: The application method can also affect the strength of the adhesive. Adhesives that are applied evenly and thoroughly will generally have higher energy.
- Curing Time: The adhesive’s curing time can also affect its strength. Adhesives that can cure for more extended periods will generally have higher power.
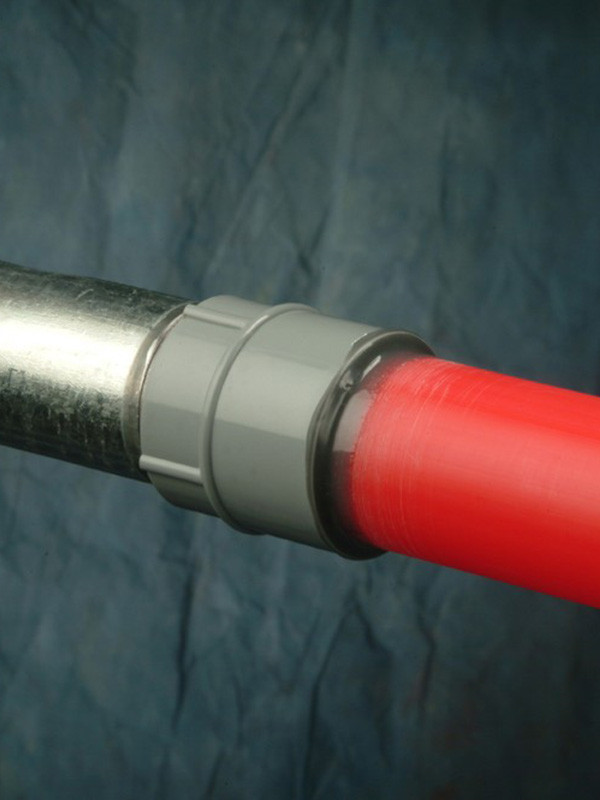
Applications of PVC Bonding Adhesives with High Strength
PVC bonding adhesives with high strength are commonly used in a variety of applications, including:
- Construction:PVC bonding adhesives with high strength are used in the construction industry to bond PVC pipes, fittings, and other materials together. They provide a strong, long-lasting bond that can withstand harsh weather conditions and high-stress levels.
- Automotive Industry: PVC bonding adhesives with high strength are used in the automotive industry to bond PVC materials to other materials, such as metal and glass. They provide a solid, durable bond that withstands high-stress levels and vibrations.
- Marine Industry: PVC bonding adhesives with high strength are used in the marine industry to bond PVC materials to other materials, such as fiberglass and wood. They provide a solid and durable bond that can withstand harsh marine environments.
Benefits of PVC Bonding Adhesives with High Strength
PVC bonding adhesives with high strength offer several benefits over weaker adhesives, including:
- Increased Durability:High-strength adhesives provide a long-lasting bond to withstand high-stress levels and load.
- Improved Safety:Adhesives with high strength provide a safer bond, reducing the risk of failure and accidents.
- Reduced Maintenance: High-strength adhesives require less maintenance and repair, saving time and money.
Properties of PVC bonding adhesives: Durability
PVC bonding adhesives are used to create a strong bond between PVC materials. One of the most important properties of these adhesives is durability. Here we will explore the properties of PVC bonding adhesives, explicitly focusing on durability.
The durability of PVC Bonding Adhesives
Durability measures how long an adhesive will maintain its strength and bond. PVC bonding adhesives must be durable to ensure the bond between PVC materials remains solid and long-lasting. The durability of PVC bonding adhesives is determined by several factors, including:
- Chemical Composition: The chemical composition of the adhesive can affect its durability. Adhesives that are made with more vital chemicals will generally be more durable.
- Environmental Factors:The environment in which the bonded materials are placed can affect the durability of the adhesive. Exposure to heat, moisture, and chemicals can weaken the bond and reduce the adhesive’s durability.
- Curing Time: The adhesive’s curing time can also affect its durability. Adhesives that can cure for more extended periods will generally be more durable.
Applications of PVC Bonding Adhesives with High Durability
PVC bonding adhesives with high durability are commonly used in a variety of applications, including:
- Plumbing: PVC bonding adhesives with high durability bond PVC pipes and fittings together. These adhesives can withstand exposure to water and chemicals, ensuring a long-lasting bond.
- Automotive Industry: PVC bonding adhesives with high durability are used in the automotive industry to bond PVC materials to other materials, such as metal and glass. These adhesives can withstand exposure to heat and chemicals, ensuring a long-lasting bond.
- Construction:PVC bonding adhesives with high durability are used in construction applications to bond PVC materials together, such as flooring and roofing. These adhesives can withstand exposure to moisture and temperature changes, ensuring a long-lasting bond.
Benefits of PVC Bonding Adhesives with High Durability
PVC bonding adhesives with high durability offer several benefits over weaker adhesives, including:
- Long-lasting Bond: Adhesives with high durability provide a solid and durable bond that can withstand environmental factors and exposure to chemicals.
- Reduced Maintenance: High-durability adhesives require less maintenance and repair, saving time and money.
- Improved Safety: Adhesives with high durability provide a safer bond, reducing the risk of failure and accidents.
Properties of PVC bonding adhesives: flexibility
PVC bonding adhesives are widely used in many applications, from plumbing and construction to automotive and marine industries. A critical property of these adhesives is flexibility. Here we will explore the properties of PVC bonding adhesives, explicitly focusing on flexibility.
The flexibility of PVC Bonding Adhesives
Flexibility measures how well an adhesive can bend and stretch without losing its bond strength. PVC bonding adhesives need to be flexible to accommodate the natural movement of PVC materials and to maintain a strong bond over time. The flexibility of PVC bonding adhesives is determined by several factors, including:
- Chemical Composition:The chemical composition of the adhesive can affect its flexibility. Adhesives that are made with more flexible chemicals will generally be more flexible.
- Environmental Factors:The environment in which the bonded materials are placed can affect the flexibility of the adhesive. Exposure to heat and cold can affect the adhesive’s ability to flex.
- Application Method: The method used to apply the adhesive can also affect its flexibility. Adhesives applied in thin layers will generally be more flexible than those in thick layers.
Applications of PVC Bonding Adhesives with High Flexibility
PVC bonding adhesives with high flexibility are commonly used in a variety of applications, including:
- Automotive Industry: PVC bonding adhesives with increased flexibility are used in the automotive industry to bond PVC materials to other materials, such as metal and glass. These adhesives can accommodate the natural movement of the materials, ensuring a strong bond over time.
- Marine Industry:PVC bonding adhesives with high flexibility are used in the marine industry to bond PVC materials to other materials, such as fiberglass and metal. These adhesives can withstand exposure to water and sunlight while maintaining a solid bond.
- Construction: PVC bonding adhesives with high flexibility are used in construction applications to bond PVC materials together, such as flooring and roofing. These adhesives can accommodate the natural movement of the materials due to temperature changes, ensuring a strong bond over time.
Benefits of PVC Bonding Adhesives with High Flexibility
PVC bonding adhesives with high flexibility offer several benefits over less flexible adhesives, including:
- Long-lasting Bond:Highly flexible Adhesives provide a solid and durable bond that can withstand the natural movement of PVC materials over time.
- Improved Performance:Highly flexible Adhesives can improve PVC materials’ performance by allowing them to move without compromising the bond.
- Reduced Risk of Failure: Highly flexible Adhesives provide a more reliable bond, reducing the risk of failure and accidents.
Properties of PVC bonding adhesives: temperature resistance
PVC bonding adhesives are used in a wide range of industries and applications. A critical property of these adhesives is their ability to resist high temperatures. Here we will explore the properties of PVC bonding adhesives, explicitly focusing on temperature resistance.
Temperature Resistance of PVC Bonding Adhesives
Temperature resistance measures how well an adhesive can withstand exposure to high temperatures without losing its bond strength. PVC bonding adhesives must be temperature-resistant to accommodate the extreme temperature fluctuations that can occur in many applications. The temperature resistance of PVC bonding adhesives is determined by several factors, including:
- Chemical Composition:The chemical composition of the adhesive can affect its temperature resistance. Adhesives that are made with more temperature-resistant chemicals will generally be more temperature-resistant.
- Environmental Factors: The environment in which the bonded materials are placed can affect the temperature resistance of the adhesive. Exposure to extreme heat or cold can affect the adhesive’s ability to resist temperature changes.
- Application Method: The method used to apply the adhesive can also affect its temperature resistance. Adhesives applied in thin layers generally have better temperature resistance than those in thick layers.
Applications of PVC Bonding Adhesives with High-Temperature Resistance
PVC bonding adhesives with high-temperature resistance are commonly used in a variety of applications, including:
- Automotive Industry:PVC bonding adhesives with high-temperature resistance are used in the automotive industry to bond PVC materials to other materials, such as metal and glass. These adhesives can withstand exposure to high temperatures in engine compartments, ensuring a strong bond over time.
- Construction: PVC bonding adhesives with high-temperature resistance are used in construction applications to bond PVC materials together, such as roofing and flooring. These adhesives can withstand extreme temperatures due to exposure to the sun and other environmental factors.
- Industrial Applications: PVC bonding adhesives with high-temperature resistance are used in various industrial applications, such as electronics and aerospace, where exposure to high temperatures is expected.
Benefits of PVC Bonding Adhesives with High-Temperature Resistance
PVC bonding adhesives with high-temperature resistance offer several benefits over less temperature-resistant adhesives, including:
- Long-lasting Bond: Adhesives with high-temperature resistance provide a solid and durable bond that can withstand exposure to extreme temperatures over time.
- Improved Performance: Adhesives with high-temperature resistance can improve the performance of PVC materials by allowing them to withstand radical temperature changes without compromising the bond.
- Reduced Risk of Failure: Adhesives with high-temperature resistance provide a more reliable bond, reducing the risk of failure and accidents.
Properties of PVC bonding adhesives: chemical resistance
PVC bonding adhesives are used in various applications, including construction, automotive, and industrial settings. One of the most important properties of these adhesives is their ability to resist chemicals. Here we will explore the properties of PVC bonding adhesives, explicitly focusing on chemical resistance.
Chemical Resistance of PVC Bonding Adhesives
Chemical resistance measures how well an adhesive can withstand chemical exposure without losing its bond strength. PVC bonding adhesives must be chemically resistant to accommodate the various chemicals encountered in many applications. The chemical resistance of PVC bonding adhesives is determined by several factors, including:
- Chemical Composition:The chemical composition of the adhesive can affect its chemical resistance. Adhesives that are made with more chemical-resistant chemicals will generally be more chemical-resistant.
- Environmental Factors: The environment in which the bonded materials are placed can affect the chemical resistance of the adhesive. Exposure to certain chemicals can affect the adhesive’s ability to resist chemical changes.
- Application Method:The method used to apply the adhesive can also affect its chemical resistance. Adhesives applied in thin layers generally have better chemical resistance than those in thick layers.
Applications of PVC Bonding Adhesives with Chemical Resistance
PVC bonding adhesives with chemical resistance are commonly used in a variety of applications, including:
- Construction:PVC bonding adhesives with chemical resistance are used in construction applications to bond PVC materials together, such as roofing and flooring. These adhesives can resist exposure to environmental chemicals, ensuring a strong bond over time.
- Automotive Industry: PVC bonding adhesives with chemical resistance are used in the automotive industry to bond PVC materials to other materials, such as metal and glass. These adhesives can resist exposure to various chemicals in engine compartments, ensuring a strong bond over time.
- Industrial Applications: PVC bonding adhesives with chemical resistance are used in multiple industrial applications, such as electronics and aerospace, where chemical exposure is expected.
Benefits of PVC Bonding Adhesives with Chemical Resistance
PVC bonding adhesives with chemical resistance offer several benefits over less chemically-resistant adhesives, including:
- Long-lasting Bond:Adhesives with chemical resistance provide a strong, long-lasting bond that can resist exposure to various chemicals over time.
- Improved Performance:Adhesives with chemical resistance can improve the performance of PVC materials by allowing them to resist exposure to multiple chemicals without compromising the bond.
- Reduced Risk of Failure:Adhesives with chemical resistance provide a more reliable bond, reducing the risk of failure and accidents.
Properties of PVC bonding adhesives: cure time
Regarding PVC bonding adhesives, cure time is an important property to consider. Cure time refers to the time required for the adhesive to reach its full strength and hardness. Here we will explore the properties of PVC bonding adhesives, explicitly focusing on cure time.
Cure Time of PVC Bonding Adhesives
The cure time of PVC bonding adhesives can vary depending on several factors, including:
- Type of Adhesive:Different PVC bonding adhesives may have different cure times. For example, two-part epoxy adhesives typically have a longer cure than solvent-based adhesives.
- Application Method: The method used to apply the adhesive can also affect its cure time. Adhesives applied in thicker layers may take longer to cure than those involved in thinner layers.
- Temperature and Humidity: The temperature and humidity of the environment in which the adhesive is applied can also affect its cure time. Higher temperatures and lower humidity can speed up the cure time, while lower temperatures and higher humidity can slow it down.
Applications of PVC Bonding Adhesives with Cure Time
PVC bonding adhesives with shorter cure times are commonly used in applications where fast curing is required, such as:
- Construction:PVC bonding adhesives with shorter cure times are used in construction applications requiring fast bonding, such as bonding PVC pipes.
- Automotive Industry: PVC bonding adhesives with shorter cure times are used in the automotive industry where fast bonding is required, such as bonding plastic parts.
- Electrical Industry: PVC bonding adhesives with shorter cure times are used in the electrical industry to bond PVC materials to other materials, such as metal and glass.
Benefits of PVC Bonding Adhesives with Shorter Cure Times
PVC bonding adhesives with shorter cure times offer several benefits over longer-curing adhesives, including:
- Faster Bonding:Adhesives with quicker cure times provide more immediate bonding, reducing production time and improving efficiency.
- Improved Productivity:Shorter cure times allow for faster production cycles, improving productivity.
- Reduced Downtime: Adhesives with shorter cure times can minimize downtime by allowing for more immediate repairs and maintenance.
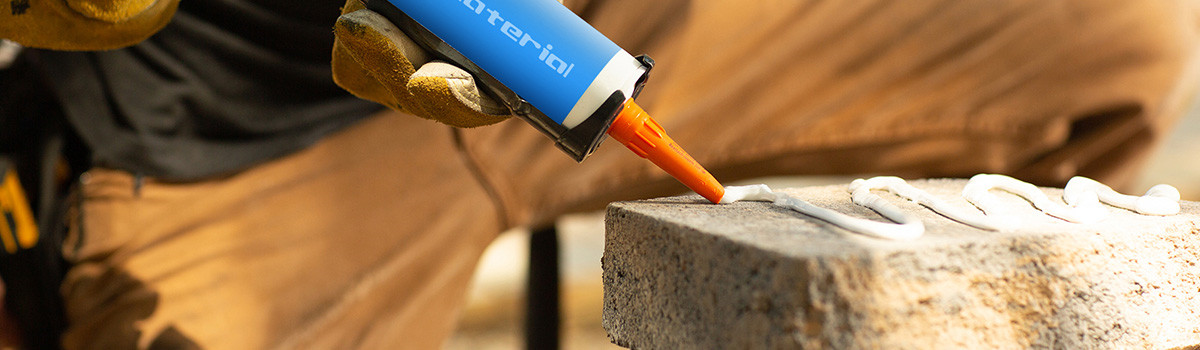
Benefits of Using PVC Bonding Adhesives in the Construction Industry
- Easy to Use: PVC bonding adhesives are easy to apply, making them an ideal choice for construction applications.
- Solid and Durable:PVC bonding adhesives provide a strong, durable bond that can withstand heavy loads and harsh environmental conditions.
- Time-Saving: Using PVC bonding adhesives can save time in the construction process, as they require less preparation and cure time than traditional bonding methods.
- Cost-Effective:PVC bonding adhesives are cost-effective compared to other bonding methods, requiring less material and labor.
Applications of PVC bonding adhesives in the plumbing industry
PVC bonding adhesives are extensively used in the plumbing industry for bonding PVC pipes and fittings. These adhesives offer strong and leak-proof bonding that ensures long-lasting performance. Here we will explore the various applications of PVC bonding adhesives in the plumbing industry.
Applications of PVC Bonding Adhesives in the Plumbing Industry
- Bonding PVC Pipes: PVC bonding adhesives bond PVC pipes in plumbing systems. These adhesives offer a strong, leak-proof bond between PVC pipes and fittings.
- Pipe Insulation: PVC bonding adhesives attach insulation to PVC pipes. These adhesives provide a strong bond that can withstand high temperatures and humidity.
- Duct Work: PVC bonding adhesives are used in HVAC systems to bond PVC ductwork. These adhesives provide a strong bond that can withstand extreme temperatures and pressure.
Benefits of Using PVC Bonding Adhesives in the Plumbing Industry
- Easy to Use: PVC bonding adhesives are easy to apply, making them an ideal choice for plumbing applications.
- Leak-Proof Bonding:PVC bonding adhesives offer leak-proof bonding that ensures long-lasting performance and prevents leaks in the plumbing system.
- Fast Curing: PVC bonding adhesives cure quickly, allowing for faster installation and repair work.
- Chemical Resistance:PVC bonding adhesives offer high chemical resistance, making them suitable for various plumbing applications.
Applications of PVC bonding adhesives in the automotive industry
PVC bonding adhesives are widely used in the automotive industry for bonding a variety of components, from interior trim to exterior body panels. These adhesives offer several benefits, including improved design flexibility, weight reduction, and performance. Here we will explore the various applications of PVC bonding adhesives in the automotive industry.
Applications of PVC Bonding Adhesives in the Automotive Industry
- Body Panel Bonding:PVC bonding adhesives bond exterior body panels in the automotive industry. These adhesives offer improved strength and durability, which helps to reduce weight and improve fuel efficiency.
- Interior Trim Bonding: PVC bonding adhesives bond interior trim components like the dashboard and door panels. These adhesives offer improved design flexibility and reduce the need for mechanical fasteners, which can reduce weight and improve aesthetics.
- Windshield Bonding: PVC bonding adhesives bond windshields to the vehicle frame. These adhesives offer improved safety and durability, which helps to prevent the windscreen from becoming dislodged during an accident.
Benefits of Using PVC Bonding Adhesives in the Automotive Industry
- Improved Design Flexibility:PVC bonding adhesives offer improved design flexibility, which allows for more innovative and lightweight designs.
- Reduced Weight:PVC bonding adhesives can help reduce weight by eliminating the need for mechanical fasteners, improving fuel efficiency.
- Improved Performance: PVC bonding adhesives offer improved strength and durability, which helps to improve the overall performance of automotive components.
Applications of PVC bonding adhesives in the marine industry
PVC bonding adhesives are widely used in the marine industry for bonding a variety of components, from hulls to interior trim. These adhesives offer several benefits, including improved durability, water resistance, and ease of use. Here we will explore the various applications of PVC bonding adhesives in the marine industry.
Applications of PVC Bonding Adhesives in the Marine Industry
- Hull Bonding: PVC bonding adhesives bond hulls in the marine industry. These adhesives offer improved strength and durability, which helps to reduce maintenance and repair costs.
- Interior Trim Bonding: PVC bonding adhesives bonds interior trim components, such as cabinetry and fixtures. These adhesives offer improved water resistance, which helps prevent damage from moisture exposure.
- Deck Bonding:PVC bonding adhesives are used to bond decks in the marine industry. These adhesives offer improved durability and water resistance, which helps to prevent damage from exposure to the elements.
Benefits of Using PVC Bonding Adhesives in the Marine Industry
- Improved Durability:PVC bonding adhesives offer improved durability, which helps to reduce maintenance and repair costs.
- Water Resistance: PVC bonding adhesives provide improved water resistance, which helps prevent damage from moisture exposure.
- Ease of Use: PVC bonding adhesives are easy to use, which helps to reduce labor costs and improve efficiency.
Applications of PVC bonding adhesives in the electrical industry
PVC bonding adhesives are widely used in the electrical industry for bonding a variety of components, from wire insulation to circuit boards. These adhesives offer several benefits, including improved insulation, temperature resistance, and ease of use. Here we will explore the various applications of PVC bonding adhesives in the electrical industry.
Applications of PVC Bonding Adhesives in the Electrical Industry
- Wire Insulation: PVC bonding adhesives are used to bond wire insulation in the electrical industry. These adhesives offer improved insulation, which helps to reduce the risk of electrical shock.
- Circuit Board Bonding: PVC bonding adhesives bond circuit boards in the electrical industry. These adhesives offer improved temperature resistance, which helps to prevent damage from exposure to high temperatures.
- Component Bonding: PVC bonding adhesives bond various electrical components, such as connectors and switches. These adhesives offer improved durability, which helps to reduce maintenance and repair costs.
Benefits of Using PVC Bonding Adhesives in the Electrical Industry
- Improved Insulation:PVC bonding adhesives offer improved insulation, which helps to reduce the risk of electrical shock.
- Temperature Resistance:PVC bonding adhesives offer improved temperature resistance, which helps to prevent damage from exposure to high temperatures.
- Ease of Use: PVC bonding adhesives are easy to use, which helps to reduce labor costs and improve efficiency.
Safety considerations when using PVC bonding adhesives
When using PVC bonding adhesives, it is essential to take certain safety precautions to avoid any accidents or harm to yourself and others. Here are some safety considerations to keep in mind:
- Proper Ventilation:Ensure you are working in a well-ventilated area to avoid inhaling fumes from the adhesive.
- Personal Protective Equipment:Wear protective gloves and eye goggles to prevent skin contact and eye irritation from the adhesive.
- Flammability: PVC bonding adhesives are flammable, so avoid using them near open flames or heat sources.
- Storage: Store the adhesive in a cool and dry place, away from heat and ignition sources.
- Cleanup: Clean up any spills or excess adhesive immediately with a solvent or water before drying.
Benefits of Following Safety Considerations
- Avoid Accidents: The following safety considerations can help you avoid accidents and injuries using PVC bonding adhesives.
- Improve Work Efficiency: Taking the necessary precautions can help you work efficiently and effectively without worrying about harming yourself or others.
- Increase Productivity: Following safety measures can increase productivity by reducing the risk of accidents or injuries.
Potential hazards of PVC bonding adhesives
PVC bonding adhesives are widely used for bonding PVC materials, but they also pose specific hazards that users should be aware of. Here are some potential dangers of PVC bonding adhesives:
Potential Hazards of PVC Bonding Adhesives
- Toxic Fumes:The solvents in PVC bonding adhesives can release toxic fumes that can cause eye, nose, and throat irritation if inhaled.
- Skin Irritation: Direct contact with PVC bonding adhesives can cause skin irritation or chemical burns.
- Flammability: PVC bonding adhesives are highly flammable and can ignite when exposed to heat or flames.
- Environmental Damage:Improper disposal of PVC bonding adhesives can cause ecological damage by contaminating soil and water.
- Health Risks:Long-term exposure to PVC bonding adhesives can lead to respiratory problems, liver and kidney damage, and other health risks.
Precautions to Avoid Hazards
- Use in Well-Ventilated Areas: Always use PVC bonding adhesives to avoid inhaling toxic fumes in well-ventilated areas.
- Wear Protective Gear:Use protective gloves and goggles when working with PVC bonding adhesives to prevent skin and eye irritation.
- Avoid Heat Sources:Keep PVC bonding adhesives away from heat sources or open flames to prevent fire hazards.
- Proper Disposal: Dispose of PVC bonding adhesives properly to avoid environmental damage.
Personal protective equipment (PPE) when working with PVC bonding adhesives
When working with PVC bonding adhesives, it is essential to use personal protective equipment (PPE) to prevent potential hazards. Here are some critical PPE to consider when working with PVC bonding adhesives:
Personal Protective Equipment (PPE) for Working with PVC Bonding Adhesives
- Gloves: Chemical-resistant gloves are necessary to protect your hands from skin irritation or chemical burns.
- Goggles or Face Shield: Goggles or face shields can protect your eyes from chemical splashes or fumes.
- Respirator: A respirator can protect your lungs from inhaling toxic fumes.
- Apron or Lab Coat: A chemical-resistant apron or lab coat can protect your clothing and skin from chemical spills.
- Boots or Closed-Toe Shoes: Wearing boots or closed-toe shoes can protect your feet from chemical spills.
Precautions to Consider
Select chemical-resistant PPE appropriate for the type of PVC bonding adhesive you use.
- Ensure that your PPE fits properly to avoid exposure to hazardous chemicals.
- Train employees on the proper use and maintenance of PPE.
- Always check your PPE before each use to ensure it is in good condition.
- Dispose of PPE according to appropriate guidelines to prevent environmental damage.
Proper storage and disposal of PVC bonding adhesives
PVC bonding adhesives are commonly used in various industries for their strong bonding properties. However, proper handling and storing of these adhesives is essential to prevent any harm to the environment and individuals. Here are some tips for the appropriate storage and disposal of PVC bonding adhesives:
- Store PVC bonding adhesives in a cool, dry, well-ventilated area away from heat, direct sunlight, and ignition sources.
- Keep the adhesive containers tightly sealed to prevent evaporation and contamination.
- Avoid storing PVC bonding adhesives near incompatible materials, such as oxidizing agents, acids, or bases, as they can cause hazardous reactions.
- Dispose of PVC bonding adhesives following local, state, and federal regulations.
- Do not pour adhesive down the drain or throw it in the trash.
- Empty containers should be rinsed with a suitable solvent, and the rinse solution should be added to the original container or disposed of according to local regulations.
- Follow any specific disposal instructions provided by the adhesive manufacturer.
By following these guidelines, individuals can ensure that PVC bonding adhesives are handled, stored, and disposed of safely and responsibly. It is essential to take proper precautions to protect individuals and the environment.
How to select the suitable PVC bonding adhesive for your application
Several factors must be considered when selecting the suitable PVC bonding adhesive for your application. The type of adhesive, its properties, and its intended use all play a role in determining the best option for your specific needs. Here are some tips for selecting the suitable PVC bonding adhesive:
- Identify the materials to be bonded:PVC bonding adhesives may work differently on different materials, so it’s important to know what you will be bonding to ensure the adhesive is compatible.
- Consider the application: Will the bonded materials be subjected to temperature extremes or chemical exposure? Will the bond need to be flexible or rigid? These factors will help determine the required properties of the adhesive.
- Choose the correct type of adhesive: Solvent-based, water-based, and two-part epoxy adhesives have different properties and applications. Choose the style that best fits your specific needs.
- Consult with a supplier:A knowledgeable supplier can guide selecting the suitable adhesive and offer additional advice on proper application and curing.
By considering these factors and consulting with a supplier, you can ensure that you select the suitable PVC bonding adhesive for your application. This will help ensure a solid and durable bond that meets your needs.
Factors to consider when selecting a PVC bonding adhesive
Various industries and applications use PVC bonding adhesives for their excellent bonding properties. However, selecting the suitable adhesive for a particular application is crucial for achieving a solid and durable bond. Here are some factors to consider when choosing a PVC bonding adhesive:
- Substrate type:The type of substrate being bonded is an essential factor to consider, as different adhesives have varying compatibility with various substrates.
- Environment: The environment in which the bond will be exposed is an essential factor to consider. For example, an adhesive with higher temperature or chemical resistance should be selected if the bond is exposed to high temperatures or chemicals.
- Cure time:The required cure time for the adhesive can impact the production process and may influence the selection of an adhesive.
- Bond strength: The required bond strength will vary based on the application. Some adhesives offer higher bond strengths than others, so selecting an adhesive that meets the bond strength requirements is essential.
- Application method: The application method is also essential, as some adhesives are better suited for specific application methods, such as spray or brush.
Considering these factors, you can select the appropriate PVC bonding adhesive for your application, ensuring a solid and durable bond.
Preparation of surfaces before PVC bonding adhesive application
The surface preparation can directly affect the strength and durability of the bond. Here are some key steps to follow:
- Clean the surfaces: The surfaces to be bonded should be free from any dirt, dust, grease, oil, or other contaminants that may interfere with the adhesion process. Use a solvent such as acetone or alcohol to clean the surfaces.
- Sand the surfaces: Sanding the surfaces will help to create a rough surface that promotes better adhesion. Use fine-grit sandpaper to gently sand the surfaces.
- Degrease the surfaces:Use a degreaser to remove any remaining oils or contaminants from the surface. This will ensure that the surface is clean and ready for bonding.
- Dry the surfaces:Ensure that the surfaces are completely dry before applying the PVC bonding adhesive. Moisture can interfere with the adhesive process and weaken the bond.
Following these steps ensures that the surfaces are adequately prepared for applying PVC bonding adhesives, which will help create a durable bond for years.
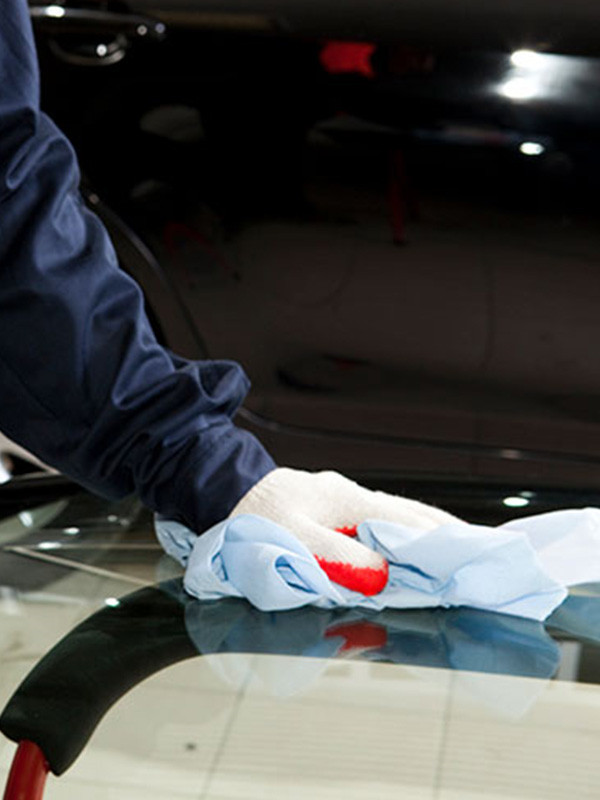
Tips for achieving a successful bond with PVC bonding adhesives
However, achieving a successful bond with these adhesives requires proper preparation and application techniques. Here are some tips to help you achieve a successful bond with PVC bonding adhesives:
- Properly clean and dry the surfaces that will be bonded. Any dirt, grease, or moisture can affect the adhesive’s bondability.
- Roughen the surface to be bonded with sandpaper or a wire brush. This will help the adhesive penetrate the surface and create a stronger bond.
- Apply the adhesive evenly and in the right amount. Too much adhesive can create excess glue, while too little can weaken bonds.
- Follow the manufacturer’s instructions for curing time and temperature. This will ensure that the adhesive reaches its maximum strength and durability.
- Use clamps or other tools to hold the surfaces while the adhesive cures. This will prevent any movement that can weaken the bond.
- Avoid exposing the bonded surfaces to excessive heat or moisture, which can weaken the bond over time.
By following these tips, you can ensure a successful bond with PVC bonding adhesives and achieve the desired results in your application. Remember to always use proper safety precautions when handling these adhesives.
Common mistakes when using PVC bonding adhesives
PVC bonding adhesives are commonly used in various industries for their strong bonding properties. However, despite their effectiveness, inevitable mistakes can compromise the success of the bond. Below are some of the most common mistakes when using PVC bonding adhesives and how to avoid them:
- Inadequate surface preparation: Proper surface preparation is crucial to achieving a successful bond with PVC bonding adhesives. Ensure the surfaces to be bonded are clean, dry, and free of any contaminants before application.
- Incorrect mixing ratio:For two-part epoxy PVC bonding adhesives, following the manufacturer’s instructions carefully regarding the mixing ratio is essential. A wrong ratio can result in a weaker bond.
- Incomplete curing: Allow adequate time for the adhesive to cure completely before subjecting the bonded surfaces to stress or pressure. Failure to do so can result in a weakened bond.
- Inappropriate adhesive selection: Choosing the suitable adhesive for the specific application can result in a strong bond or failure. Consider factors such as temperature resistance, chemical resistance, and flexibility when selecting an adhesive.
- Insufficient adhesive application: Ensure adequate adhesive is applied to bond both surfaces. A thin layer may not be sufficient for a strong bond.
Advantages of using PVC bonding adhesives over other bonding methods
Due to their excellent bonding properties and durability, PVC bonding adhesives have become increasingly popular in various industries. PVC bonding adhesives offer advantages over other bonding methods, such as mechanical fastening or welding.
Here are some advantages of using PVC bonding adhesives over other bonding methods:
- Strong bonding: PVC bonding adhesives provide a strong, long-lasting bond that can withstand various stresses and strains.
- Easy to apply:Applying PVC bonding adhesives is relatively simple and quick, without requiring specialized equipment or extensive training.
- Versatile: PVC bonding adhesives can bond various materials, including PVC, ABS, polycarbonate, acrylics, and other thermoplastics.
- Aesthetically pleasing: Unlike mechanical fastening methods that often require visible fasteners, PVC bonding adhesives can provide a clean, seamless appearance.
- Reduced weight:Bonding with PVC adhesives minimizes the product’s weight, making it ideal for applications where weight is a concern.
- Cost-effective: Due to reduced labor and material costs, PVC bonding adhesives are often more cost-effective than other bonding methods.
Limitations of PVC bonding adhesives
Due to their strong bonding properties, durability, and flexibility, PVC bonding adhesives are popular for bonding PVC materials. However, like any bonding method, PVC bonding adhesives have limitations to consider before selecting them for application.
Here are some of the limitations of PVC bonding adhesives:
- Not suitable for all materials: PVC bonding adhesives are specifically designed for bonding PVC materials and may not be suitable for other materials.
- Limited temperature resistance: While PVC bonding adhesives offer good temperature resistance, they may not be suitable for extremely high or low temperatures.
- Limited chemical resistance:PVC bonding adhesives may not resist all types of chemicals, and exposure to certain chemicals may weaken the bond.
- Cure time: PVC bonding adhesives may have a longer cure time than other bonding methods, impacting production timelines.
- Not reversible:Once the bond is formed, it cannot be easily reversed or adjusted, which may be a limitation in specific applications.
It’s essential to carefully consider the limitations of PVC bonding adhesives before selecting them for application. While they offer many advantages, their rules must be regarded to ensure a successful bonding process.
How to apply PVC bonding adhesives
PVC bonding adhesives are popular for joining PVC pipes, sheets, and other materials. These adhesives are easy to apply and provide a strong bond that can withstand various conditions. However, following the correct application technique is essential to ensure the adhesive performs optimally. Here are some tips on how to apply PVC bonding adhesives:
- Clean the surface: Before using the adhesive, thoroughly clean the surface. Any dirt, grease, or other contaminants can affect the bond’s strength.
- Apply the primer:Apply a PVC primer to the surface to be bonded. This will help prepare the adhesive surface and ensure a strong bond.
- Apply the adhesive: Apply the PVC bonding adhesive to one of the surfaces to be joined. Be sure to apply enough adhesive to ensure that the joint is fully covered.
- Join the surfaces: Once the adhesive is applied, join the surfaces immediately. Make sure to apply enough pressure to ensure that the surfaces are fully bonded.
- Allow time to dry:Give the adhesive enough time to dry and cure thoroughly. This time will vary depending on the adhesive used, so follow the manufacturer’s instructions.
Troubleshooting common issues with PVC bonding adhesives
Due to their high strength and durability, PVC bonding adhesives are popular for bonding PVC materials. However, like any bonding method, issues can arise during the bonding process. Here are some common problems that can occur and some troubleshooting tips:
Problem: Poor bonding or bond failure
Possible causes: inadequate surface preparation, incorrect adhesive selection, insufficient curing time, improper application technique
Troubleshooting tips: ensure surfaces are clean and dry, select the appropriate adhesive for the materials being bonded, allow sufficient curing time, follow proper application technique
Problem: Adhesive not curing or curing too slowly
Possible causes: incorrect adhesive selection, improper mixing, low temperature or humidity
Troubleshooting tips: ensure the adhesive is appropriate for the materials being bonded, follow proper mixing instructions, and increase temperature and humidity if necessary
Problem: Excessive adhesive squeeze-out or messiness
Possible causes: too much adhesive applied, improper application technique
Troubleshooting tips: apply adhesive in a thin, even layer, use the proper application tool, and avoid over-applying
Problem: Adhesive discoloration or yellowing
Possible causes: exposure to UV light or heat
Troubleshooting tips: select an adhesive that is resistant to UV and heat exposure, and limit exposure to these elements
By following proper application techniques and troubleshooting any issues, PVC bonding adhesives can provide a solid and durable bond for PVC materials.
Maintenance and repair of PVC-bonded materials
PVC bonding adhesives are widely used in various industries, including construction, plumbing, automotive, marine, and electrical. They are known for their strength, durability, and flexibility, making them an ideal choice for bonding PVC materials. However, PVC bonding adhesives require proper maintenance and repair to ensure longevity, like any other bonding method. Here are some tips on how to maintain and repair PVC-bonded materials:
- Regular cleaning: Regularly cleaning the bonded surfaces is essential to prevent the buildup of dirt, dust, and other debris that can compromise the bond strength.
- Inspection: Periodic inspection of the bonded surfaces can help identify any cracks or signs of damage, allowing for timely repairs.
- Repairing cracks: If gaps are detected, it is crucial to correct them promptly using the same PVC bonding adhesive that was used initially. This will help maintain the integrity of the bond and prevent further damage.
- Use compatible materials: When making repairs or replacing parts, using materials consistent with the PVC bonding adhesive is vital to ensure a solid and durable bond.
- Follow manufacturer’s instructions:Always follow the manufacturer’s instructions when applying PVC bonding adhesives or making repairs to ensure optimal performance and longevity.
Regulatory standards and certifications for PVC bonding adhesives
Due to their excellent bonding properties, PVC bonding adhesives are widely used in various industries. However, ensuring that your bond meets regulatory standards and certifications is essential. Here are some of the most common regulatory standards and certifications for PVC bonding adhesives:
- ASTM D2564: This is a standard specification for solvent cement for thermoplastic materials. It covers requirements for both clear and pigmented solvent cement for PVC plastics.
- NSF/ANSI 61: This standard specifies drinking water system components requirements, including PVC bonding adhesives. Products that meet this standard have been tested for their effects on drinking water safety.
- UL 746C: This standard covers the performance of polymeric materials, including PVC bonding adhesives, under various conditions of use. Products that meet this standard have been evaluated for their resistance to fire, electrical hazards, and other safety concerns.
- Green Seal: This certification is awarded to products that meet rigorous environmental standards. PVC bonding adhesives certified by Green Seal have been evaluated for their impact on human health and the environment.
- RoHS: The Restriction of Hazardous Substances Directive restricts using certain hazardous materials in electrical and electronic equipment. PVC bonding adhesives that comply with RoHS do not contain substances such as lead, mercury, and cadmium.
Future developments in PVC bonding adhesives technology
PVC bonding adhesives have been widely used in various industries due to their unique properties, such as flexibility, durability, and temperature resistance. The development of this technology has been continuous, with manufacturers striving to improve their products to meet the ever-increasing demands of the industry.
Here are some of the future developments in PVC bonding adhesives technology:
- Enhanced sustainability: There has been a growing trend towards sustainable and eco-friendly products. In the future, PVC bonding adhesives will likely be developed to reduce their environmental impact, such as using more renewable resources and minimizing waste.
- Improved performance: Manufacturers are continuously working to improve the performance of PVC bonding adhesives. This includes enhancing their bonding strength, reducing cure time, and improving their chemical and temperature resistance.
- New applications: As technology advances, new applications for PVC bonding adhesives will likely emerge. For example, there may be a need for adhesives that can bond PVC to other materials such as metal or glass.
- Innovative adhesives:In the future, intelligent PVC bonding adhesives may be developed to detect and respond to changes in their environment. This could include adhesives that change color when exposed to UV light or temperature changes.
- Regulations and certifications: As the industry continues to grow, there will likely be an increase in rules and certifications for PVC bonding adhesives. This will help ensure the product’s safety and quality and give customers peace of mind.
Conclusion and final thoughts on PVC bonding adhesives
In conclusion, PVC bonding adhesives are versatile and reliable bonding solutions with various applications in various industries. They offer numerous benefits, such as high strength, temperature resistance, chemical resistance, and flexibility. However, it is essential to consider the limitations and potential hazards of using these adhesives and take necessary safety precautions when handling and disposing of them. Additionally, selecting the suitable adhesive and adequately preparing the surfaces to be bonded are key factors in achieving a successful bond. As with any bonding method, proper maintenance and repair are essential to ensure the longevity of the related materials.