Wearable Electronic Device Adhesive
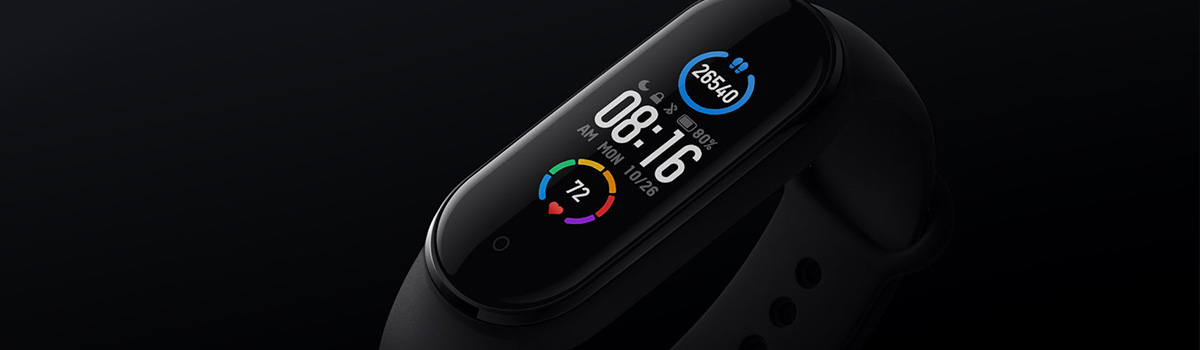
The market for wearable electronic devices has witnessed tremendous growth in recent years, with an increasing number of individuals incorporating these devices into their daily lives. Alongside this surge in popularity, advancements in wearable technology have led to the development of a crucial component: wearable electronic device adhesive. This adhesive plays a pivotal role in ensuring these devices’ comfort, durability, and functionality. From fitness trackers to smartwatches and medical wearables, adhesive technology has revolutionized how we interact with and benefit from wearable electronics. This article explores the importance of wearable electronic device adhesive and its various applications, showcasing how it has transformed the wearable tech landscape.
The Role of Adhesive in Wearable Electronic Devices
Adhesive plays a crucial role in the functionality and reliability of wearable electronic devices. These devices, such as smartwatches, fitness trackers, and medical sensors, are designed to be worn on the body and require a solid and durable bond between their components. Here are some key aspects highlighting the importance of adhesive in wearable electronic devices:
- Component Attachment: Adhesives are used to attach various wearable device components securely. These components include sensors, displays, batteries, circuit boards, and flexible substrates. The adhesive ensures a strong bond between these components, preventing detachment or movement during regular use or physical activities.
- Flexibility and Durability: Wearable devices often require flexibility to conform to the body’s contours and withstand repetitive movements. Adhesives specifically formulated for flexible substrates bond components without compromising the device’s mechanical integrity. These adhesives offer high flexibility, excellent adhesion, and stress resistance, ensuring the device’s durability and longevity.
- Protection from Moisture and Environmental Factors: Wearable devices are exposed to various environmental conditions, including moisture, sweat, dust, and temperature fluctuations. Adhesive materials with moisture-resistant properties help seal the device and protect internal components from water ingress, preventing damage and malfunctions. Additionally, certain adhesives provide protection against chemicals, UV radiation, and other environmental factors that may impact the device’s performance.
- Thermal Management: Electronic components generate heat during operation, and effective heat dissipation is critical to maintaining device performance and user comfort. Adhesives with good thermal conductivity bond heat-generating components, such as processors and batteries, to heat sinks or other cooling elements. These adhesives facilitate efficient heat transfer, preventing overheating and ensuring optimal device operation.
- Biocompatibility: Wearable devices used in medical or healthcare applications require biocompatible adhesives that are safe for prolonged contact with the skin. These adhesives are designed to minimize skin irritation, allergies, and other adverse reactions. Biocompatible adhesives enable comfortable and reliable adhesion, making them suitable for wearable medical sensors, patches, and other healthcare devices.
- Aesthetics and Ergonomics: Adhesive technologies also contribute to the aesthetics and ergonomics of wearable devices. Thin and transparent adhesives are preferred for applications where the display must be directly bonded to the cover glass, ensuring a seamless and visually appealing appearance. Additionally, adhesives with low-profile properties help reduce the device’s thickness, enhancing user comfort and wearability.
Comfort and Flexibility: Enhancing the User Experience
Comfort and flexibility are key factors that significantly impact the user experience of wearable electronic devices. Adhesive materials and technologies play a significant role in enhancing these aspects. Here’s a closer look at how adhesive solutions contribute to comfort and flexibility in wearable devices:
- Skin-Friendly Adhesives: Wearable devices often come in direct contact with the skin for extended periods. Adhesives used in these applications must be skin-friendly to minimize irritation and discomfort. Manufacturers utilize hypoallergenic, breathable, and non-irritating bonds, ensuring a comfortable experience for the wearer. These adhesives adhere securely to the skin without causing any adverse reactions, even during prolonged use.
- Soft and Flexible Bonding: Wearable devices must conform to the body’s movements. Adhesives with high flexibility bond components and substrates without restricting the device’s flexibility. These adhesives have excellent elongation and bending capabilities, allowing the device to flex, twist, and stretch as needed. The soft and flexible bonding these adhesives provide ensures that the device remains comfortable and doesn’t hinder the wearer’s range of motion.
- Breathability and Moisture Management: Adhesive solutions for wearable devices consider the breathability and moisture management requirements. Adhesives with breathable properties enable air circulation between the device and the skin, reducing the accumulation of moisture, sweat, and heat. This helps to prevent discomfort, skin irritation, and the growth of bacteria. Adhesives with moisture-wicking capabilities can absorb and manage moisture, enhancing comfort during physical activities or in humid environments.
- Thin and Low-Profile Adhesives: The thickness and bulkiness of wearable devices can impact their comfort and aesthetics. Light and low-profile adhesive solutions reduce the device’s consistency and enhance user comfort. These adhesives have minimal impact on the device’s profile, ensuring a sleek and discreet design. Wearers can comfortably wear the device without it feeling bulky or cumbersome.
- Stretchable Adhesives: Wearable devices often require adhesives that can withstand stretching and movement without compromising their bond strength. Stretchable adhesives are designed to expand and contract with the device, allowing unrestricted movement while maintaining a strong bond between components. These adhesives are suitable for wearable devices requiring frequent stretching or bending, such as fitness trackers or bright clothing.
- Easy and Pain-Free Removal: Adhesive technologies also focus on providing pain-free and easy removal of wearable devices. Adhesives that offer gentle adhesion and are designed for clean and residue-free removal are preferred. This ensures that users can comfortably remove the device without discomfort or skin irritation.
Adhesive Materials: Choosing the Right Components
Selecting the appropriate adhesive materials is essential for ensuring wearable electronic devices’ performance, reliability, and longevity. The choice of components for wearable device adhesive depends on various factors such as the application, bonded materials, environmental conditions, and specific requirements. Here are some key considerations when choosing adhesive components for wearable electronic devices:
- Adhesive Type: Different adhesive types offer unique properties and characteristics. Common adhesive types used in wearable devices include pressure-sensitive adhesives (PSAs), epoxy adhesives, silicone adhesives, and acrylic adhesives. PSAs are widely used for their ease of application, flexibility, and repositionability. Epoxy adhesives provide excellent bonding strength and temperature resistance. Silicone adhesives offer high flexibility, biocompatibility, and moisture resistance—acrylic adhesives balance strength, flexibility, and resistance to environmental factors.
- Substrate Compatibility: The adhesive should be compatible with the materials being bonded. Wearable devices often contain a combination of different materials, including plastics, metals, glass, and flexible substrates. Selecting an adhesive that adheres well to these materials and provides a solid and durable bond is crucial. Adhesive manufacturers provide compatibility charts and guidelines to assist in choosing the appropriate adhesive for specific substrates.
- Flexibility and Durability: Wearable devices require adhesives that can withstand repetitive movements and flexing without compromising their bond strength. Flexible adhesives that offer high elongation and flexibility are suitable for bonding components in wearable devices. Additionally, the adhesive should resist stress, impact, and vibration well to ensure the device’s longevity under various usage conditions.
- Environmental Resistance: Wearable devices are exposed to environmental factors such as moisture, sweat, temperature changes, and chemicals. Adhesives with moisture resistance are critical to prevent water ingress and damage to internal components. It is essential to consider the environmental conditions to which the device will be exposed and special adhesives that offer the necessary resistance to ensure device performance and reliability.
- Thermal Management: Wearable devices may generate heat during operation, and efficient heat dissipation is crucial to maintain performance and user comfort. Adhesives with good thermal conductivity bond heat-generating components to heat sinks or cooling elements. These adhesives facilitate heat transfer, preventing overheating and ensuring optimal device operation.
- Biocompatibility: Wearable devices used in medical or healthcare applications require biocompatible adhesives that are safe for prolonged skin contact. Biocompatible adhesives minimize skin irritation, allergies, and adverse reactions, making them suitable for wearable medical sensors, patches, and other healthcare devices. These adhesives are formulated to comply with relevant regulations and standards for medical applications.
- Application Method: The adhesive application method should be considered during component selection. Some adhesives are available as tapes or films, facilitating easy and precise application. Others may require dispensing or curing processes. Manufacturers need to assess the specific requirements of their manufacturing process and choose adhesive components accordingly.
Waterproof and Sweat-Resistant Adhesives for Active Lifestyles
Waterproof and sweat-resistant adhesives are essential for wearable electronic devices for active lifestyles. Whether it’s fitness trackers, sports watches, or bright clothing, these devices need to withstand exposure to water, moisture, and sweat without compromising their functionality. Here are some key points highlighting the importance of waterproof and sweat-resistant adhesives for active lifestyles:
- Water Protection: Active individuals engage in various activities such as swimming, running in the rain, or intense workouts that involve heavy sweating. Waterproof adhesives are specifically formulated to provide a reliable barrier against water ingress. They prevent moisture from reaching sensitive electronic components, protecting them from damage and maintaining the device’s functionality even in wet conditions.
- Moisture Resistance: Sweat is common in wearable devices during physical activities. Sweat-resistant adhesives help prevent moisture from seeping into the machine and potentially causing malfunctions or corrosion. These adhesives are designed to repel water and maintain their adhesive strength and integrity in humid environments.
- Adhesion Under Wet Conditions: Adhesives used in active lifestyle devices must maintain their bond strength even when exposed to water or sweat. Waterproof and sweat-resistant adhesives exhibit excellent adhesion properties under wet conditions, ensuring the components remain securely bonded despite moisture exposure. This is crucial for the overall structural integrity and reliability of the device.
- Durability and Longevity: Waterproof and sweat-resistant adhesives contribute to the durability and longevity of wearable devices. They protect against moisture-related damage, such as corrosion or short circuits, which can significantly reduce the device’s lifespan. These adhesives help maintain the device’s performance and extend its operational life by preventing water or sweat infiltration.
- Skin Comfort: Active individuals engage in prolonged physical activities, and sweat accumulation between the device and the skin can cause discomfort and irritation. Sweat-resistant adhesives with breathable properties help to manage moisture and maintain a comfortable interface between the device and the wearer’s skin. They allow for better air circulation, reducing the likelihood of skin irritation and enhancing the overall comfort of the user.
- Versatility: Waterproof and sweat-resistant adhesives can be used in various wearable device applications. They can be applied to different materials, such as plastics, metals, fabrics, and elastomers, ensuring compatibility with a wide range of wearable electronic devices. This versatility allows manufacturers to incorporate these adhesives into different active lifestyle wearables.
- Adhesive Performance Testing: Manufacturers perform rigorous testing to evaluate the performance of waterproof and sweat-resistant adhesives. These tests simulate real-world conditions, including immersion in water, exposure to sweat, and thermal cycling. Manufacturers can ensure that the adhesive materials meet waterproof and sweat-resistant standards for active lifestyle devices by conducting such tests.
Skin-Friendly Adhesives: Avoiding Irritation and Allergies
For wearable electronic devices designed for active lifestyles, skin-friendly adhesives are crucial to ensure user comfort and prevent irritation and allergies. Active individuals engage in intense physical activities, and prolonged contact between the device and the skin can lead to sensitivities. Here are key points highlighting the importance of skin-friendly adhesives for active lifestyles:
- Hypoallergenic Formulations: Skin-friendly adhesives are formulated to minimize the risk of allergic reactions or skin irritations. These adhesives are carefully designed and tested to ensure compatibility with various skin types. They are free from known allergens and harsh chemicals that may trigger adverse skin reactions. Hypoallergenic formulations help reduce the likelihood of skin allergies and make the wearable device suitable for a broader user base.
- Non-Irritating Adhesion: Adhesives used in active lifestyle devices should adhere securely to the skin without causing irritation or discomfort. Skin-friendly adhesives have gentle adhesion properties, minimizing the risk of skin pulling or tugging during application or removal. They provide a reliable bond without causing undue stress or trauma to the skin, ensuring a comfortable experience for the wearer.
- Breathability and Moisture Management: Active individuals often sweat during workouts or physical activities, and moisture accumulation between the device and the skin can lead to discomfort and skin irritation. Skin-friendly adhesives incorporate breathable properties, allowing for proper air circulation and moisture management. This helps to reduce the buildup of sweat and heat, minimizing the risk of skin irritation and maintaining a comfortable interface between the device and the skin.
- Biocompatibility: Wearable devices used for active lifestyles may have prolonged skin contact. Therefore, biocompatible adhesives are essential to ensure safety and minimize adverse skin reactions. Skin-friendly adhesives are formulated to meet biocompatibility standards and regulations, making them suitable for prolonged skin contact without causing allergies, sensitivities, or other adverse effects.
- Adhesive Testing for Skin Compatibility: Manufacturers of skin-friendly adhesives conduct rigorous testing to assess their compatibility with the skin. This testing includes skin irritation and sensitization studies to ensure the adhesive materials meet safety standards. By performing these tests, manufacturers can ensure that their adhesives are suitable for use on the skin during active lifestyles.
- Durability and Reliability: Skin-friendly adhesives maintain their performance and adhesive properties over time, even during intense physical activities. They are designed to withstand sweat, moisture, and movement without compromising their bond strength. This ensures that the wearable device remains securely attached to the skin throughout various activities, enhancing reliability and preventing discomfort or accidental detachment.
- User Satisfaction: Manufacturers prioritize user satisfaction and comfort by utilizing skin-friendly adhesives. Active individuals can wear the device for extended periods without experiencing skin irritations or allergies. Skin-friendly adhesives contribute to a positive user experience, allowing users to focus on their activities without distraction or discomfort.
Durability and Longevity: Ensuring Device Integrity
Durability and longevity are critical factors in ensuring wearable electronic devices’ overall integrity and performance. The adhesive used in these devices plays a crucial role in maintaining structural integrity and functionality over an extended period. Here are key points highlighting the importance of durability and longevity for wearable electronic device adhesive:
- Bond Strength: The adhesive in wearable devices should provide strong and reliable bonding between components. A robust bond strength ensures that the various parts of the device remain securely attached, even during intense physical activities or movements. This prevents members from loosening or detaching, thereby maintaining the overall structural integrity of the device.
- Resistance to Environmental Factors: Wearable devices are subjected to various environmental factors, such as moisture, temperature fluctuations, UV exposure, and chemical exposure. The adhesive should resist these elements to prevent deterioration and ensure long-term reliability. Moisture-resistant adhesives protect against water ingress, reducing the risk of component damage or corrosion. UV-resistant adhesives prevent degradation or yellowing of the adhesive under prolonged exposure to sunlight. Chemical-resistant adhesives protect against potential damage caused by exposure to substances like lotions, sweat, or cleaning agents.
- Flexibility and Impact Resistance: Wearable devices are subjected to constant movement, bending, and potential impacts. The adhesive should be flexible enough to accommodate these motions without compromising the bond strength. Flexible adhesives prevent cracking or detachment when the device undergoes bending or twisting, ensuring durability and longevity.
- Thermal Management: Efficient heat dissipation is crucial for wearable devices to maintain performance and avoid overheating. The adhesive should have good thermal conductivity to transfer heat from heat-generating components to the surrounding environment or heat sinks. This helps prevent excessive heat buildup that could damage the device or reduce its lifespan.
- Fatigue Resistance: Wearable devices often experience repetitive stress and movement during active use. The adhesive should exhibit resistance to fatigue, meaning it can withstand repeated mechanical pressure without degradation. Fatigue-resistant adhesives maintain their bond strength and structural integrity, even after prolonged use, ensuring longevity.
- Adhesive Testing and Validation: Manufacturers of wearable electronic devices conduct thorough testing and validation of the adhesive materials to ensure their durability and longevity. To assess the adhesive’s performance over time, these tests simulate real-world usage conditions, such as mechanical stress, temperature cycling, and environmental exposure. By conducting these tests, manufacturers can identify and select adhesives that meet the required durability standards for wearable devices.
- Maintenance of Aesthetics: Adhesive materials that retain their properties over time contribute to the aesthetic appeal of wearable devices. Adhesives that resist yellowing, discoloration, or degradation maintain the device’s visual integrity, ensuring it remains attractive and appealing to users throughout its lifespan.
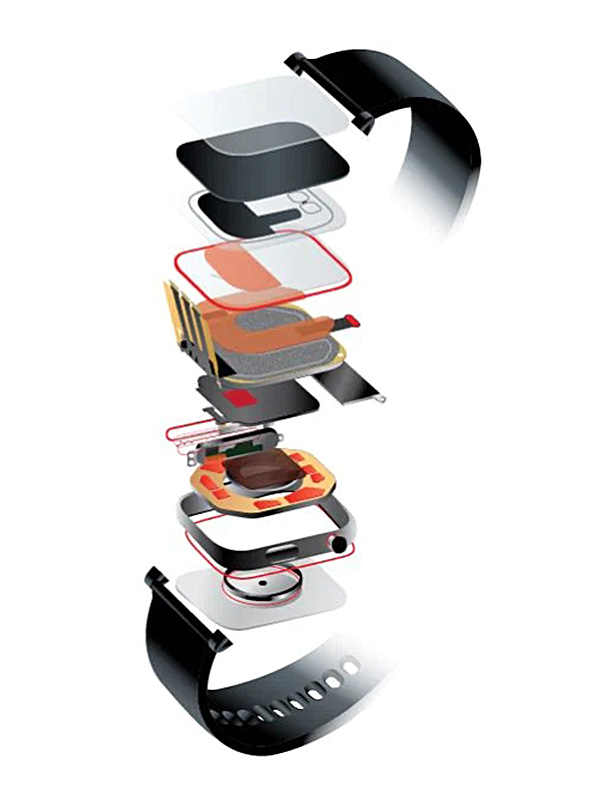
Adhesive Bonding Techniques: Ensuring Secure Attachment
Adhesive bonding techniques are widely used in various industries to ensure secure material attachment. Whether in manufacturing, construction, automotive, aerospace, or everyday applications, adhesive bonding provides an efficient and reliable way to join components. This technique involves adhesives, substances capable of bonding materials by surface attachment.
Several factors need to be considered when applying adhesive bonding techniques to ensure a secure attachment. The choice of adhesive is crucial and depends on the specific application requirements. Different adhesives have varying properties, such as strength, flexibility, temperature, and chemical resistance. Understanding the materials to be bonded and their compatibility with the adhesive is essential for a successful bond.
Surface preparation is another critical aspect of adhesive bonding. Surfaces must be clean, dry, and free from contaminants that could hinder the adhesive’s ability to bond effectively. Cleaning methods may involve solvent wiping, abrasion, or chemical treatments to remove oils, dirt, oxides, or other contaminants. Proper surface preparation promotes better adhesion and enhances the durability of the bond.
The adhesive application method is also crucial for ensuring a secure attachment. Adhesives can be applied in various ways, including brushing, spraying, rolling, or dispensing. The application technique should provide a uniform adhesive coverage on the bonding surfaces, avoiding excess or insufficient amounts. The adhesive should be evenly spread to maximize contact with the bonded characters.
The curing process is an integral part of adhesive bonding. Adhesives can cure through various mechanisms, such as solvent evaporation, chemical reaction, or exposure to heat or ultraviolet (UV) light. Following the manufacturer’s recommendations regarding the curing time and conditions is essential to achieve optimal bond strength. Sufficient curing time allows the adhesive to reach its maximum power and ensures a secure attachment.
In some cases, additional methods can enhance the bond strength and reliability. Structural adhesives, for example, can be reinforced with mechanical fasteners like screws or rivets to provide extra stability. This combination of adhesive bonding and mechanical fastening is often used in critical applications that require high load-bearing capacity and resistance to dynamic forces.
Quality control and testing are essential to ensure the integrity of adhesive bonds. Non-destructive testing methods, such as visual inspection, ultrasonic testing, or bond strength testing, can be employed to assess the quality of the bond. These tests can detect any defects or weaknesses in the adhesive bond and allow corrective measures to be taken if necessary.
Conductive Adhesives: Enabling Seamless Connectivity
Conductive adhesives enable seamless connectivity in various industries, particularly electronics and electrical applications. These adhesives are specifically formulated to possess both adhesive properties and electrical conductivity, allowing them to bond components together while facilitating electrical current flow. With their unique characteristics, conductive adhesives offer several advantages for achieving reliable and efficient connectivity.
One of the critical advantages of conductive adhesives is their ability to replace traditional soldering methods. Unlike soldering, which involves melting a metal alloy to create electrical connections, conductive adhesives provide a simpler and more versatile alternative. They can bond components on various substrates, including flexible materials, without requiring high temperatures or complex soldering equipment. This flexibility makes conductive adhesives suitable for applications where traditional soldering may be impractical or pose challenges.
The composition of conductive adhesives typically includes conductive fillers dispersed in a polymer matrix. Silver, copper, or carbon-based particles are commonly used as fillers to provide electrical conductivity. The filler material selection depends on factors such as the required level of conductivity, cost considerations, and compatibility with the application. The polymer matrix acts as an adhesive, ensuring a solid bond between the components.
Proper surface preparation is crucial for achieving reliable connectivity when using conductive adhesives. Unlike conventional adhesives, surfaces must be clean, dry, and free from contaminants to ensure good adhesion. Additionally, surfaces may require roughening or treatment to enhance the mechanical interlocking between the adhesive and the bonded components. This preparation promotes optimal contact and electrical conductivity between the adhesive and the surfaces.
Conductive adhesives are available in different forms, such as pastes, films, or tapes, providing options for various application methods. Pastes are commonly used for manual or automated dispensing, while movies and tapes offer the advantage of precise and controlled application. The choice of application method depends on factors such as the assembly’s complexity, the components’ size, and the desired level of automation.
In addition to their electrical conductivity, conductive adhesives offer mechanical strength and stability. They can withstand thermal cycling, vibration, and mechanical stress, providing reliable connections in demanding environments. Conductive adhesives can also exhibit excellent adhesion to different substrates, including metals, plastics, ceramics, and glass.
Testing and quality control are essential to ensure the performance and reliability of conductive adhesive bonds. Electrical resistance measurements and adhesion strength tests can be conducted to verify the conductivity and mechanical integrity of the bonded components. These tests help identify any defects or weaknesses in the adhesive bond, allowing corrective measures to be taken if necessary.
Adhesive Solutions for Smartwatches and Fitness Trackers
Smartwatches and fitness trackers have become increasingly popular wearable devices, providing users with various features and functionality to enhance their daily lives. However, one familiar challenge users face is ensuring these devices remain securely attached to their wrists. To address this issue, adhesive solutions have been developed specifically for smartwatches and fitness trackers.
One of the primary considerations when designing adhesives for wearable devices is their compatibility with the materials commonly used to construct smartwatches and fitness trackers. These devices often feature a combination of metal, glass, and various plastics, requiring specialized adhesives to ensure a reliable bond. Silicone-based adhesives, for example, are commonly used due to their excellent adhesion to a wide range of surfaces, including metals and plastics.
The adhesive solution for smartwatches and fitness trackers should also provide sufficient strength to withstand the rigors of daily use. These devices are subjected to constant movement, exposure to moisture, and temperature changes. Therefore, the adhesive must possess high mechanical strength and resistance to environmental factors. Additionally, the adhesive should be flexible to accommodate the bending and flexing of the wrist without compromising the bond.
Another crucial consideration is the comfort of the wearer. Since smartwatches and fitness trackers are worn for extended periods, the adhesive must be skin-friendly and hypoallergenic. Manufacturers often opt for medical-grade bonds free from harmful chemicals and irritants, ensuring a comfortable user experience without causing skin reactions or discomfort.
Furthermore, adhesives designed for wearable devices should enable easy and residue-free removal. Users may need to change straps, clean their devices, or replace components, so the adhesive should allow for effortless detachment without leaving sticky residues behind. This is particularly important when dealing with delicate materials like glass, which can be easily damaged if not handled correctly during removal.
In addition to the adhesive itself, the application method is crucial for user convenience. Many adhesive solutions come in pre-cut and pre-sized adhesive strips or dots, simplifying the attachment process. These pre-cut options ensure precise adhesive placement, reducing the chances of misalignment and facilitating easy installation for users.
Medical Wearables: Adhesive Applications in Healthcare
Medical wearables have emerged as groundbreaking technology in the field of healthcare. These devices, equipped with sensors and advanced technologies, can monitor vital signs, track activity levels, and gather valuable health data. One key component that enables the seamless integration of wearables into healthcare is adhesive applications. Adhesive technologies ensure the secure and comfortable attachment of medical wearables to the human body, enabling continuous and accurate monitoring.
Adhesive applications in medical wearables offer several benefits, including convenience, reliability, and flexibility. These adhesives are designed to adhere to the skin without causing discomfort or irritation. They provide a secure attachment, allowing wearers to go about their daily activities without worrying about the device becoming loose or falling off. Furthermore, adhesives used in medical wearables are hypoallergenic and gentle on the skin, making them suitable for individuals with sensitive skin or allergies.
One area where adhesive applications have significantly contributed is remote patient monitoring. Adhesive patches integrated with sensors can be attached to the patient’s body to monitor vital signs such as heart rate, blood pressure, and oxygen saturation. These patches collect real-time data and transmit it wirelessly to healthcare providers, allowing them to monitor patients’ conditions from a distance. The adhesive ensures that the patches remain securely in place for extended periods, enabling continuous monitoring without causing discomfort to the patient.
In chronic disease management, adhesive applications have revolutionized how patients monitor and manage their conditions. For example, individuals with diabetes can benefit from wearable devices that continuously monitor glucose levels. Adhesive patches with embedded sensors can be attached to the skin, eliminating the need for frequent finger pricks. These patches provide:
- Accurate and continuous glucose readings.
- Helping patients make an informed diet.
- Medication
- Lifestyle decisions.
Adhesive applications have also been instrumental in improving the accuracy of wearable devices. Proper placement of the sensors is crucial for obtaining reliable data, and sticky patches ensure consistent contact between the sensors and the skin, reducing the likelihood of false readings. By minimizing the motion artifacts and environmental interference, these adhesives enhance the overall accuracy of the wearables, making them more valuable for medical professionals in diagnosing and monitoring patients.
Moreover, the adhesive properties of these applications allow for the development of flexible and conformable wearables. Adhesives can adhere to various body parts, including irregular surfaces, enabling the placement of sensors in optimal locations. This flexibility is essential for applications such as electrocardiogram (ECG) monitoring, where accurate placement of the electrodes is necessary for obtaining accurate readings.
ECG and Heart Rate Monitors: Adhesive Electrode Integration
The integration of adhesive electrodes into electrocardiogram (ECG) and heart rate monitors has revolutionized the field of cardiac monitoring. These adhesive electrodes serve as the interface between the device and the human body, allowing for accurate and continuous measurement of electrical signals produced by the heart. This integration has greatly improved the convenience, comfort, and reliability of ECG and heart rate monitoring.
Adhesive electrodes used in ECG and heart rate monitors are designed to securely attach to the skin without causing discomfort or irritation. They are typically made of biocompatible materials that are hypoallergenic and gentle on the skin, ensuring that users can wear them for extended periods without any adverse reactions. The adhesive properties of these electrodes ensure that they stay in place during movement and physical activities, enabling continuous monitoring without the need for frequent readjustments.
One significant advantage of adhesive electrode integration is its ease of use and convenience. Traditional ECG monitoring involved using bulky and cumbersome electrode wires that needed to be connected to the device manually. This process was time-consuming and often required assistance from healthcare professionals. With adhesive electrode integration, users can easily apply the electrodes themselves, eliminating the need for complex wiring setups. This user-friendly approach has made ECG and heart rate monitoring more accessible to individuals outside clinical settings, enabling them to monitor their heart health in their homes.
The integration of adhesive electrodes has also improved the accuracy and reliability of ECG and heart rate monitoring. Proper placement of the electrodes is crucial for obtaining accurate readings. Adhesive electrodes ensure consistent contact between the skin and the sensors, reducing the likelihood of signal interference or loss. This results in more reliable and precise measurements essential for accurate diagnosis and monitoring of cardiac conditions.
Moreover, the adhesive electrode integration allows greater movement freedom during monitoring. Unlike traditional wired electrodes, which restrict movement and limit physical activities, adhesive electrodes offer flexibility and comfort. Users can perform regular activities, including exercise and sports, without the electrodes becoming loose or detaching from the skin. This freedom of movement is particularly beneficial for athletes, as it enables continuous and unobtrusive monitoring of heart rate and ECG during training sessions and competitions.
Furthermore, adhesive electrodes facilitate long-term monitoring of cardiac conditions. Patients with chronic cardiac conditions can wear adhesive electrodes for extended periods, allowing healthcare providers to gather comprehensive data over time. This continuous monitoring provides valuable insights into the patient’s heart health, helping healthcare professionals make informed decisions regarding treatment plans and medication adjustments.
Skin Patch Sensors: Monitoring Vital Signs with Precision
Skin patch sensors have emerged as a groundbreaking technology for monitoring vital signs with precision. These sensors, typically in adhesive patches, are placed directly on the skin and can collect real-time data on various physiological parameters. This innovation has revolutionized healthcare by enabling continuous and non-invasive monitoring of vital signs conveniently and comfortably.
One key advantage of skin patch sensors is their ability to provide accurate and precise measurements of vital signs. These sensors are equipped with advanced technology, including high-resolution sensors and sophisticated algorithms, which enable reliable data collection. They can monitor vital signs, including heart rate, respiratory rate, body temperature, blood oxygen levels, and even hydration levels. The precision of these measurements makes skin patch sensors invaluable for detecting abnormalities and monitoring the progress of medical conditions.
Skin patch sensors offer the advantage of continuous monitoring, providing a comprehensive and dynamic picture of a person’s health. Traditional methods of vital sign measurement, such as manual readings or sporadic measurements in clinical settings, often miss fluctuations and transient changes in vital signs. Skin patch sensors, on the other hand, continuously monitor the selected parameters, allowing healthcare professionals to gain insights into a patient’s health trends, response to treatments, and overall well-being over time.
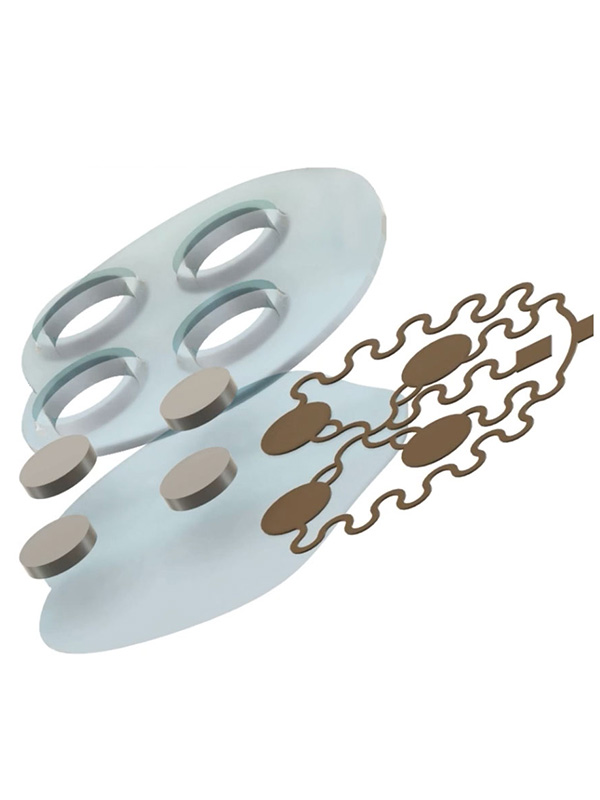
Furthermore, skin patch sensors are non-invasive and comfortable, enhancing patient compliance and convenience. The adhesive patches are designed to adhere securely to the skin without causing discomfort or irritation. Using biocompatible materials ensures that the sensors do not harm the skin, even during long-term wear. This comfort and non-invasiveness make skin patch sensors suitable for many individuals, including infants, elderly patients, and sensitive skin.
Another advantage of skin patch sensors is their real-time capture of data. The collected information is often wirelessly transmitted to a connected device, such as a smartphone or a healthcare provider’s system, allowing for immediate analysis and interpretation. This real-time monitoring enables timely intervention in emergencies or critical changes in vital signs. Healthcare professionals can receive alerts and notifications, allowing them to respond quickly and provide appropriate care.
Skin patch sensors also have the potential to empower individuals to manage their health. These sensors can be integrated with mobile applications and wearable devices, allowing users to track their vital signs and progress over time. By providing individuals access to their health data, skin patch sensors promote self-awareness and encourage proactive healthcare management.
Adhesive Solutions for Augmented Reality (AR) Glasses
Augmented Reality (AR) glasses have gained significant popularity recently, offering users an immersive and interactive experience by overlaying digital content onto the real world. However, ensuring a secure and comfortable fit of AR glasses on the user’s face is crucial for a seamless AR experience. Adhesive solutions are vital in addressing these challenges, providing stability, comfort, and durability for AR glasses.
One of the primary concerns for AR glasses is their ability to stay securely in place on the user’s face. Adhesive solutions can achieve a firm grip by providing a reliable bond between the glasses and the user’s skin. Silicone adhesives, for instance, are commonly used due to their excellent adhesion properties and skin-friendly nature. These adhesives can create a strong bond while allowing easy removal without leaving any residue or causing discomfort.
Comfort is another crucial factor in AR glasses design. Users typically wear these glasses for extended periods, making it essential to minimize pressure points and ensure a comfortable fit. Adhesive materials with cushioning properties, such as gel-based adhesives, can help distribute pressure evenly across the contact area, reducing discomfort and preventing skin irritation. These adhesives provide a soft and conformable interface between the glasses and the user’s face, enhancing overall comfort.
Durability is crucial for AR glasses, considering the wear and tear they may experience during regular use. Adhesive solutions can enhance the robustness of AR glasses by reinforcing critical areas prone to stress or mechanical strain. Structural adhesives, such as acrylic adhesives, can provide high strength and impact resistance, ensuring the integrity of the glasses’ components. They can effectively bond different materials together, such as plastic frames and glass lenses, enhancing the overall durability of the glasses.
Moreover, adhesive solutions can contribute to the optical performance of AR glasses. Transparent adhesives with excellent optical clarity can be used for lens bonding, ensuring minimal interference with the user’s vision. These adhesives offer high light transmission and refractive index matching, minimizing distortions or reflections that could compromise the AR experience.
Regarding user experience, adhesive solutions can also facilitate ease of use and customization of AR glasses. Pressure-sensitive adhesives (PSAs) enable convenient attachment and detachment of additional accessories, such as prescription lens inserts or tracking modules. This versatility allows users to personalize their AR glasses according to their needs.
Adaptable Adhesives: Supporting Different Surface Materials
Adhesives play a critical role in joining and bonding different surface materials together. However, the challenge arises when the surfaces to be bonded are made of diverse materials with varying properties. Flexible adhesives are specially designed to address this challenge by providing reliable bonding solutions for different surface materials, ensuring solid and durable connections. These adhesives offer compatibility, versatility, and superior performance across various substrates.
Compatibility is crucial when bonding different surface materials. Flexible adhesives are formulated to adhere to a wide range of substrates, including metals, plastics, composites, ceramics, glass, and more. They are designed to have excellent wetting properties, enabling them to spread evenly across the surface and establish solid molecular bonds. By promoting adhesion between diverse materials, flexible adhesives overcome the issue of surface mismatch and ensure a robust bond.
Versatility is another crucial characteristic of flexible adhesives. They are engineered to perform excellently in various bonding scenarios, accommodating different material combinations. These adhesives are available in different formulations, including epoxies, acrylics, polyurethanes, and cyanoacrylates, allowing users to select the most suitable adhesive for their specific application. Some flexible adhesives come in different viscosities or cure times, providing further flexibility for additional bonding requirements.
Flexible adhesives offer superior performance by addressing the specific challenges of different surface materials. For instance, when bonding dissimilar materials with different coefficients of thermal expansion, these adhesives can accommodate the resulting stresses and strains. They have good elasticity and flexibility, allowing them to absorb the stresses and maintain the integrity of the bond even under thermal cycling or mechanical loads.
Furthermore, flexible adhesives can enhance chemical resistance and durability across different surface materials. They are designed to withstand exposure to various environmental conditions, such as moisture, temperature fluctuations, UV radiation, and harsh chemicals. This makes them suitable for applications in diverse industries, including automotive, electronics, aerospace, and construction.
To ensure successful bonding, surface preparation is essential when using flexible adhesives. Proper cleaning, degreasing, and surface activation techniques should optimize the adhesion between different materials. Some flexible adhesives are also available with primers or adhesion promoters that further improve bonding performance on challenging surfaces.
Smart Textiles: Adhesive Integration in Clothing and Accessories
Smart textiles, e-textiles, or electronic materials are revolutionizing the fashion and wearable technology industries. These textiles combine traditional fabrics with integrated electronic components, enabling garments and accessories to possess advanced functionalities. One notable innovation in intelligent textiles is adhesive integration, which involves incorporating adhesive materials into clothing and accessories. This integration offers numerous benefits, including enhanced comfort, improved performance, and expanded design possibilities.
Adhesive integration in smart textiles involves strategically placing adhesive materials within garments and accessories. These adhesives can serve multiple purposes, such as bonding electronic components, securing sensors or actuators, and creating seamless connections between fabric layers. By using adhesive materials, designers can eliminate the need for traditional sewing or stitching methods, resulting in more streamlined and lightweight products.
One key advantage of adhesive integration is enhanced comfort. Traditional sewing techniques often involve bulky seams or stitching, creating discomfort and irritation against the skin. Adhesive integration allows for the creation of seamless garments, reducing friction and providing a more comfortable wearing experience. Additionally, adhesives can be applied to ensure flexibility and stretchability, allowing the textile to conform to the body’s movements without restrictions.
Another benefit of adhesive integration is improved performance. Adhesives can securely bond electronic components to the textile substrate, preventing them from detaching during physical activities. This feature is essential in sportswear and fitness apparel, where durability and reliability are crucial. Adhesive integration also enables the integration of sensors and actuators directly onto the fabric, enhancing the functionality of intelligent textiles. For example, pressure sensors integrated into the soles of shoes can provide real-time feedback on foot pressure distribution, optimizing performance and reducing the risk of injury.
Moreover, adhesive integration expands the design possibilities in intelligent textiles. Adhesives offer flexibility regarding where electronic components can be placed, allowing for creative and aesthetic designs. They can embed LEDs, conductive traces, or flexible displays into the fabric, transforming clothing and accessories into interactive and visually striking elements. Adhesive integration also enables the integration of washable electronics, as certain adhesives can withstand repeated washing cycles without compromising performance.
Despite the numerous benefits of adhesive integration, some challenges must be addressed. Adhesive materials must be carefully selected to ensure compatibility with the textile substrate, electronics, and washing requirements. The adhesive’s durability and longevity should be considered to ensure the longevity of the innovative textile product. Additionally, the integration process requires expertise and specialized equipment to achieve optimal results.
Flexible Displays: Enabling Bendable and Foldable Devices
Flexible displays are revolutionizing the electronics industry by enabling the development of bendable and foldable devices. Unlike traditional rigid displays, flexible displays are made with materials that can be bent, curved, or rolled without damaging functionality. This innovation has opened up new possibilities for portable and wearable devices, offering enhanced versatility and user experiences.
The critical component of flexible displays is using flexible substrates, such as plastic or metal foils, instead of rigid glass. These substrates can withstand repeated bending and flexing without cracking or breaking, making them ideal for applications that require durability and portability. Integrating flexible substrates with thin-film transistor (TFT) technology makes it possible to create displays that can be bent, twisted, or folded without compromising their visual quality.
One significant advantage of flexible displays is their ability to create bendable and foldable devices. Traditional rigid displays limit electronic devices’ form factor and design options, such as smartphones and tablets. With flexible displays, manufacturers can create devices that can be folded or rolled, resulting in compact and portable form factors. For example, foldable smartphones can be unfolded to reveal larger screens, providing users with a tablet-like experience while maintaining the convenience of a pocket-sized device. This flexibility in form factor enhances the portability and usability of electronic devices.
Furthermore, flexible displays offer improved durability compared to rigid displays. Using flexible substrates reduces the risk of screen breakage, a common concern for traditional glass-based shows. This durability is particularly beneficial for wearable devices, where flexibility and resistance to impact are essential. Users can wear smartwatches, fitness trackers, or bright clothing with embedded flexible displays without worrying about accidental damage during daily activities.
Flexible displays also provide unique user experiences. The ability to bend or curve the display allows for innovative interactions and intuitive user interfaces. For instance, a curved display can provide a more immersive viewing experience by wrapping the screen around the user’s field of vision. Flexible displays also enable new input methods, such as pressure-sensitive touch sensors, which can detect different levels of pressure applied to the screen. This opens up possibilities for new forms of interaction and user interface designs.
However, there are some challenges associated with flexible displays. The manufacturing process is more complex than rigid displays, requiring specialized techniques and materials. Ensuring consistent and reliable performance across the entire display surface can be challenging due to the flexible nature of the substrates. Additionally, developing flexible electronic components, such as loose batteries and circuits, is necessary to complement flexible displays and fully realize the potential of bendable and foldable devices.
Energy Harvesting: Adhesive-Integrated Power Generation
Energy harvesting refers to capturing and converting ambient energy from the surrounding environment into usable electrical energy. It is a promising technology that has the potential to power various electronic devices and systems without the need for traditional batteries or external power sources. One innovative approach to energy harvesting is adhesive-integrated power generation, which combines the benefits of adhesive materials with energy harvesting capabilities.
Adhesive-integrated power generation involves integrating energy harvesting components, such as piezoelectric or triboelectric materials, within adhesive structures. These materials can generate electric charges when subjected to mechanical stress or friction. Incorporating them into adhesive materials makes it possible to generate electrical energy during normal usage or manipulation of adhesive-based products.
The adhesive-integrated power generation technology offers several advantages. Firstly, it provides a convenient and autonomous power source for low-power electronic devices, eliminating the need for frequent battery replacements or external power connections. This is particularly beneficial in applications where accessibility or maintenance is challenging, such as remote monitoring systems or wearable devices.
Additionally, adhesive-integrated power generation enables energy harvesting from various environmental sources. Mechanical vibrations, such as those generated by human movement or machinery, can be converted into electrical energy through the piezoelectric effect. Frictional forces occurring during the peeling or releasing of adhesive surfaces can be harnessed through triboelectric development. These versatile energy sources make adhesive-integrated power generation suitable for various applications.
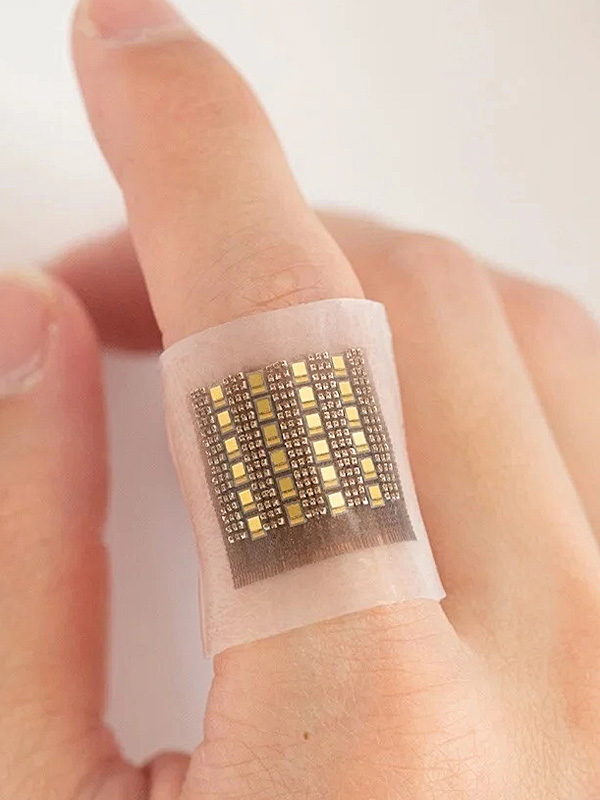
Furthermore, integrating energy harvesting capabilities into adhesive materials does not compromise their primary functions. Adhesive properties, such as bonding strength and durability, can be retained while enabling power generation. This allows for the seamless integration of energy harvesting capabilities into existing adhesive-based products or manufacturing processes without significant design modifications or additional manufacturing steps.
The potential applications of adhesive-integrated power generation are diverse. The consumer electronics sector can power low-power wearable devices, such as fitness trackers or smartwatches, by harnessing the user’s body movements. In the healthcare industry, it can be utilized in medical patches or implants to harvest energy from the patient’s motion or body heat, reducing the need for frequent battery replacements or invasive procedures.
Moreover, adhesive-integrated power generation can find applications in innovative packaging and logistics, where it can power sensor-equipped labels or tags to monitor product conditions or track shipments. It can also be employed in the building and infrastructure sectors. It enables self-powered sensors for structural health monitoring or energy-efficient bright windows that generate electricity from ambient vibrations or wind.
Adhesive Innovations: Research and Development Efforts
Adhesive innovations are crucial in various industries, from manufacturing and construction to healthcare and electronics. Research and development (R&D) efforts in adhesives aim to improve adhesive performance, enhance bonding capabilities, and explore new applications. Here are some critical areas of focus in adhesive R&D:
- Improved Bonding Strength and Durability: A critical aspect of adhesive R&D is to develop adhesives with enhanced bonding strength and durability. Researchers are working on formulating adhesive materials that can withstand harsh environmental conditions, temperature extremes, and mechanical stresses. The goal is to create adhesives that provide long-lasting, reliable bonding solutions for various applications.
- Novel Adhesive Formulations: R&D efforts are focused on developing novel adhesive formulations with improved properties. This includes exploring new chemistries, polymers, and additives that offer better adhesion to various substrates, such as metals, plastics, composites, and even unconventional materials like fabrics or biological tissues. These innovations aim to expand the range of materials that can be effectively bonded together.
- Sustainable and Eco-Friendly Adhesives: With a growing emphasis on sustainability and environmental responsibility, R&D in adhesives is focused on developing eco-friendly formulations. This involves reducing or eliminating toxic or hazardous chemicals, developing bio-based or renewable adhesive materials, and exploring environmentally friendly manufacturing processes. Sustainable adhesives are better for the environment and address the increasing demand for greener products.
- Adhesive Films and Tapes: Research efforts are directed toward developing adhesive films and tapes with unique properties and functionalities. This includes developing thin, flexible, high-strength adhesive films for applications such as electronic devices, packaging, and medical products. R&D in this area also explores advanced adhesive tapes with specialized features like heat resistance, electrical conductivity, or optical properties.
- Functional Adhesives: R&D aims to create adhesives with additional functionalities beyond bonding. For example, researchers are working on developing adhesives with self-healing properties, where the adhesive can repair itself when damaged or stressed. Other functional adhesives under investigation include those with thermal conductivity, electrical conductivity, or even adhesives with antimicrobial properties for healthcare applications.
- Adhesives for Advanced Manufacturing: R&D efforts in adhesives are also driven by the need for adhesive solutions in advanced manufacturing processes. This includes developing adhesives that can withstand high-temperature curing processes, adhesives for 3D printing applications, and adhesives that can bond dissimilar materials or surfaces with complex geometries.
The demand for improved performance, sustainability, and expanding applications across various industries drives these research and development efforts in adhesives. Researchers aim to create innovative adhesive solutions that meet the evolving needs of modern manufacturing, construction, healthcare, and other sectors by continually pushing the boundaries of adhesive technology.
Environmental Impact: Sustainable Adhesive Practices
Sustainable adhesive practices play a vital role in minimizing the environmental impact of various industries. Adhesives are used extensively in the construction, packaging, automotive, and consumer goods sectors. However, traditional adhesives often contain harmful chemicals and generate significant waste during production and application processes. By adopting sustainable adhesive practices, businesses can reduce their ecological footprint and contribute to a greener future.
One key aspect of sustainable adhesive practices is the use of eco-friendly materials. Traditional adhesives often rely on petroleum-based ingredients, contributing to carbon emissions and depleting non-renewable resources. In contrast, sustainable adhesives utilize bio-based or recycled materials as their primary components. These materials can be derived from renewable sources such as plant-based polymers, natural resins, or recycled materials like post-consumer waste. By using these sustainable alternatives, businesses can reduce their reliance on fossil fuels and promote the circular economy.
Another crucial consideration in sustainable adhesive practices is the reduction of hazardous chemicals. Many conventional adhesives contain volatile organic compounds (VOCs) and other toxic substances that can harm human health and the environment. Sustainable adhesives aim to minimize or eliminate the use of these hazardous chemicals by employing safer alternatives. Water-based adhesives, for example, have lower VOC emissions and are less harmful to workers and the surrounding environment. Additionally, technological advances have led to the development of solvent-free adhesives, which further reduce harmful emissions and contribute to healthier indoor air quality.
The application and disposal of adhesives also impact sustainability. Excessive use of adhesive products can result in wastage and unnecessary environmental burdens. Therefore, adopting efficient application techniques and precise dispensing systems can help minimize adhesive usage. Moreover, businesses should consider the end-of-life management of adhesive products. Promoting recyclability and designing adhesives that can be easily separated from substrates during the recycling process can enhance the circularity of materials and reduce waste generation.
Furthermore, sustainable adhesive practices extend beyond product formulation and usage. Manufacturing processes should aim to minimize energy consumption and water usage. Adopting energy-efficient technologies, optimizing production layouts, and implementing water recycling systems can significantly reduce the environmental impact of adhesive manufacturing. Additionally, businesses should strive to obtain certifications and comply with recognized sustainability standards to ensure transparency and accountability.
Future Trends and Potential Applications of Wearable Electronic Device Adhesive
Wearable electronic devices have gained immense popularity in recent years, and adhesive technology plays a crucial role in their design, functionality, and user experience. As the field of wearable electronics continues to evolve, several future trends and potential applications of wearable electronic device adhesive can be identified.
- Skin-friendly and Biocompatible Adhesives: A critical trend in wearable electronics is the development of skin-friendly and biocompatible adhesives. These adhesives should be gentle on the skin, non-irritating, and hypoallergenic to ensure long-term wearability and user comfort. Future advancements may focus on using bio-inspired materials and adhesives that mimic the properties of human skin to enhance adhesion while maintaining skin health.
- Stretchable and Conformable Adhesives: Wearable devices often must adhere to curved and irregular surfaces, such as the human body. Stretchable and conformable adhesives are essential to maintain reliable adhesion, even during movement and physical activities. Future adhesive technologies may incorporate flexible and stretchable materials, such as elastomers and conductive polymers, to enable seamless integration with the contours of the human body.
- Conductive Adhesives: Wearable electronic devices often require electrical connections between different components or with the human body. Conductive adhesives offer a promising solution for creating these connections while providing adhesion. In the future, advancements in conductive adhesive technology may focus on improving electrical conductivity, durability, and resistance to environmental factors, enabling more efficient and reliable wearable devices.
- Self-healing Adhesives: Wearable devices are subjected to various stresses and strains during use, which can lead to adhesive failures. Self-healing adhesives that can repair minor damages and restore adhesion properties offer potential benefits for wearable electronics. These adhesives can enhance the durability and lifespan of devices by autonomously improving themselves when subjected to mechanical stress or small cracks.
- Functional Adhesives: Besides providing adhesion, future wearable electronic device adhesives may have valuable properties. For instance, adhesive materials could incorporate sensors or actuators to enable additional functionalities, such as monitoring vital signs or delivering localized therapies. These functional adhesives can revolutionize the capabilities of wearable devices and open up new opportunities in healthcare, fitness, and other fields.
- Eco-friendly and Sustainable Adhesives: With growing environmental consciousness, developing eco-friendly and sustainable adhesive materials for wearable electronics is a significant future trend. These adhesives should be free from hazardous, recyclable, and biodegradable substances to minimize their environmental impact. Bio-based polymers, natural adhesives, and environmentally friendly manufacturing processes can contribute to more sustainable wearable electronic devices.
As the demand for wearable electronic devices continues to rise, the adhesive technology supporting these devices will also advance. These future trends in wearable electronic device adhesive can lead to improved user experience, enhanced functionality, and increased sustainability, further driving the adoption and integration of wearable technology into our daily lives.
Conclusion
The advent of wearable electronic device adhesive has revolutionized the wearable technology landscape, enhancing user experience, comfort, and functionality. The suitable adhesive material and bonding techniques ensure a secure attachment while maintaining flexibility and durability. From fitness trackers and smartwatches to medical wearables and AR glasses, adhesive technology enables seamless connectivity and precision monitoring. As research and development efforts continue, we expect even more innovative adhesive solutions supporting different surface materials, sustainable practices, and novel applications. With wearable electronic device adhesive at the forefront, the future of wearable technology holds immense potential for improving lives and transforming industries.