Metal Bonding Adhesive
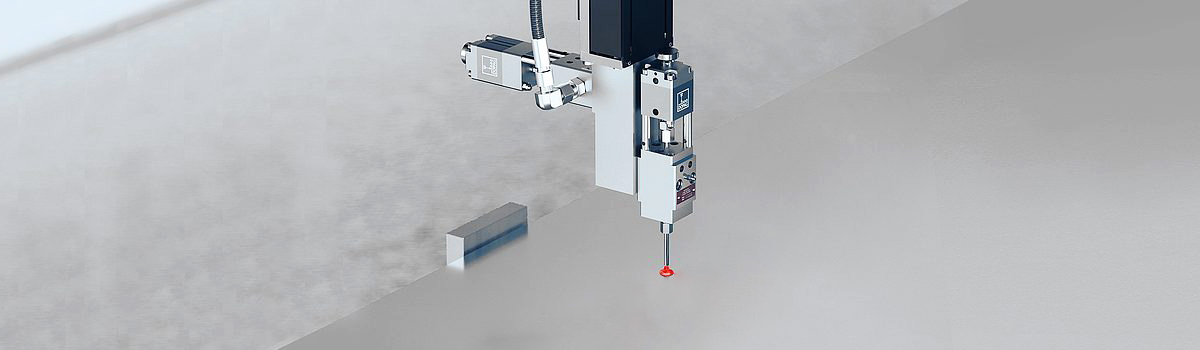
Metal bonding adhesives are specialized types of adhesives designed to bond metals to other metals or substrates. They are widely used in industries such as automotive, aerospace, electronics, and construction, among others. Metal bonding adhesives offer a variety of advantages over traditional bonding methods, including improved strength, durability, and corrosion resistance. In this article, we will discuss the properties, types, and applications of metal bonding adhesives.
What are metal bonding adhesives?
Metal bonding adhesives are adhesives specifically designed for bonding metal surfaces together. These adhesives use a variety of chemical mechanisms to bond metals, including chemical reactions, electrostatic attraction, and mechanical interlocking.
Some metal bonding adhesives are epoxy-based, which means they are composed of two components that must be mixed together before application. Others are cyanoacrylate-based, which means they are fast-acting and can bond metal surfaces together in seconds.
Metal bonding adhesives have many applications, including automotive, construction, and industrial settings. They bond metal parts, such as panels, brackets, and housings. They can also be used to repair metal objects or bond dissimilar metals together. Metal bonding adhesives offer several advantages over traditional welding and mechanical fastening, including faster curing times, lower equipment costs, and the ability to bond a wider variety of materials.
How do metal bonding adhesives work?
Metal bonding adhesives form a solid and durable bond between two metal surfaces through a chemical reaction. These adhesives typically contain a combination of chemicals, including a resin or polymer that forms the base of the adhesive and a hardener that initiates the bonding process.
When the adhesive is applied to the metal surfaces, the chemicals react and form solid covalent bonds with the metal, creating a permanent bond. To improve their performance, some metal bonding adhesives may also contain additional compounds, such as fillers or accelerators.
The bonding strength of metal bonding adhesives depends on several factors, including the type of metal being bonded, the surface preparation of the metal, and the application method of the adhesive. In general, however, metal bonding adhesives are known for their high strength, resistance to impact and vibration, and ability to bond dissimilar metals.
Examples of metal bonding adhesives include epoxy adhesives, cyanoacrylate adhesives, and acrylic adhesives. Each adhesive type has unique properties and is suitable for different applications, such as automotive, aerospace, and construction.
Properties of metal bonding adhesives
Metal bonding adhesives are designed to bond metals to one another or other materials. These adhesives typically have the following properties:
- High strength: Metal bonding adhesives are known for providing high-strength bonding. They can create strong bonds even between dissimilar metals.
- Resistance to temperature and chemical exposure: These adhesives are formulated to withstand high temperatures and exposure to chemicals, oils, and solvents, making them ideal for harsh environments.
- Fast curing: Many metal bonding adhesives cure quickly, allowing for quick assembly and production times.
- Good gap-filling properties: Metal bonding adhesives are often used to bond metals with uneven or irregular surfaces, and they have good gap-filling properties that allow them to create strong bonds even in areas with rough or uneven surfaces.
- Corrosion resistance: Metal bonding adhesives are formulated to resist corrosion, making them ideal for use in outdoor or marine environments.
- High durability: These adhesives are designed to provide long-lasting, reliable bonds that withstand stress, vibration, and other harsh conditions.
- Ease of use: Many metal bonding adhesives are easy to apply, with uncomplicated mixing and dispensing methods that require minimal training or expertise.
Metal bonding adhesives are versatile and reliable for bonding metals and other materials in various applications.
Advantages of using metal bonding adhesives
Metal bonding adhesives offer several advantages over traditional mechanical fastening methods, such as screws, bolts, and welding. Some of the benefits of using metal bonding adhesives include:
- Enhanced durability: Metal bonding adhesives can create strong, durable bonds that withstand high stress and strain, vibration, and temperature changes.
- Weight reduction: Adhesive bonding can reduce the overall weight of the assembly compared to traditional mechanical fastening methods, which can improve fuel efficiency and reduce emissions in the case of vehicles and aircraft.
- Improved aesthetics: Adhesive bonding provides a clean, smooth appearance compared to traditional mechanical fastening methods, which can have visible screw heads, welds, or rivets.
- Corrosion protection: Metal bonding adhesives can provide an effective barrier against corrosion, extending the assembly’s lifespan.
- Improved structural integrity: Adhesive bonding can distribute loads more evenly across the surface, enhancing structural integrity and reducing the likelihood of stress concentrations and subsequent failures.
- Improved design flexibility: Adhesive bonding can provide more design flexibility by allowing for the bonding of dissimilar materials and the creation of complex shapes.
- Reduced production costs: Adhesive bonding can be faster and more cost-effective than traditional mechanical fastening methods, requiring fewer parts and less equipment.
Overall, metal bonding adhesives offer a versatile and cost-effective solution for joining metals, with many advantages over traditional mechanical fastening methods.
Types of metal bonding adhesives
Metal bonding adhesives come in different forms and chemical compositions, each with properties and applications. Here are some common types of metal bonding adhesives:
- Epoxy adhesives: Epoxy adhesives are two-part adhesives typically consisting of a resin and a hardener. They create a solid and durable bond that can withstand high loads and extreme environments when mixed together. Epoxy adhesives are often used in automotive, aerospace, and construction applications.
- Cyanoacrylate adhesives: Cyanoacrylate adhesives, also known as superglue, are one-part adhesives that cure quickly and create a strong bond between metal surfaces. They are often used for bonding small metal parts and for general-purpose applications.
- Acrylic adhesives: Acrylic adhesives are two-part adhesives that cure quickly and provide high strength and durability. They are often used in industrial and construction applications, such as bonding metal panels and components.
- Polyurethane adhesives: Polyurethane adhesives are one- or two-part adhesives that provide a flexible and strong bond between metal surfaces. They are often used in automotive and construction applications, such as bonding metal panels and sealing joints.
- Silicone adhesives: Silicone adhesives are one-part adhesives that cure at room temperature to form a flexible and durable bond between metal surfaces. They are often used in electronic and automotive applications, such as bonding sensors and sealing electrical components.
- Anaerobic adhesives: Anaerobic adhesives are one-part adhesives that cure in the absence of air and in the presence of metal surfaces. They are often used for locking and sealing threaded metal components, such as bolts and screws.
- UV-curing adhesives: UV-curing adhesives are one-part adhesives that cure when exposed to UV light. They are often used in electronic and optical applications, such as bonding metal components in LCD displays and bonding metal wires in electronic circuits.
Epoxy adhesives for metal bonding
Epoxy adhesives are popular for bonding metals due to their high strength and durability. Here are some tips for using epoxy adhesives for metal bonding:
- Surface preparation: The key to a successful bond is proper surface preparation. Ensure the metal surfaces to be bonded are clean, dry, and free from contaminants such as oil, grease, or rust. You can use a degreaser and sandpaper to prepare the surfaces.
- Mix the epoxy adhesive: Follow the manufacturer’s instructions for mixing the epoxy adhesive. Usually, you will need to mix equal parts of the resin and hardener.
- Apply the epoxy adhesive: Apply the epoxy adhesive to one of the metal surfaces using a brush or a spatula. Make sure to spread the adhesive evenly over the surface.
- Join the metal surfaces: Press the two metal surfaces together, aligning them properly. Apply pressure to the bond area for a few minutes to ensure a strong bond.
- Allow to cure: Leave the bonded metals to fix for the recommended time specified by the manufacturer. The curing time will depend on the epoxy adhesive you use.
- Finishing: Once the adhesive has cured, sand or file the bonded area to achieve a smooth finish.
It’s important to note that epoxy adhesives can be toxic and may cause skin or eye irritation. Always follow the safety instructions provided by the manufacturer and wear protective gloves and goggles when handling epoxy adhesives.
Cyanoacrylate adhesives for metal bonding
Cyanoacrylate adhesives, also known as superglue, are a type of fast-acting adhesive that can bond various materials, including metals. Cyanoacrylate adhesives can create a strong and durable bond when used for metal bonding.
Before using cyanoacrylate adhesives for metal bonding, it’s essential to ensure that the metal surfaces are clean and free from dirt, oil, or debris. This can be achieved using a solvent or degreaser to clean the surfaces.
A small amount should be applied to one of the metal surfaces to apply the cyanoacrylate adhesive. The surfaces should then be pressed together firmly for several seconds to allow the adhesive to bond.
It’s important to note that cyanoacrylate adhesives are not recommended for bonding load-bearing or high-stress metal components. For these types of applications, it’s better to use a specialized structural adhesive designed to withstand higher stresses and loads.
Overall, cyanoacrylate adhesives can be a valuable option for bonding metal components, but it’s essential to choose the suitable adhesive for the application and to follow the manufacturer’s instructions carefully to ensure a robust and reliable bond.
Acrylic adhesives for metal bonding
Acrylic adhesives can be a good choice for bonding metal, as they offer several benefits, such as high strength, durability, and resistance to chemicals and weathering. Here are some tips for using acrylic adhesives for metal bonding:
- Surface preparation: Proper surface preparation is critical to ensure a strong bond. The metal surfaces should be thoroughly cleaned and degreased to remove any dirt, oil, or other contaminants that could interfere with the bonding process.
- Select the suitable adhesive: Different types of acrylic adhesives are available, each with its own properties and recommended applications. Consider factors such as the type of metal being bonded, the desired strength of the bond, and the environmental conditions the bond will be subjected to when selecting an adhesive.
- Apply the adhesive: Follow the manufacturer’s instructions carefully when applying the adhesive. Typically, acrylic adhesives are applied in thin layers using a brush, roller, or spray gun. Some adhesives require mixing before application.
- Cure time: Allow sufficient time for the adhesive to cure before subjecting the bond to any stress or load. The curing time will depend on the type of adhesive and the environmental conditions, such as temperature and humidity.
- Testing: Always test the bond strength before putting it to use. This can be done by applying a force to the bonded parts and measuring the force required to break the bond.
Overall, acrylic adhesives can be a reliable and practical choice for bonding metal, provided the proper surface preparation, adhesive selection, and application techniques are followed.
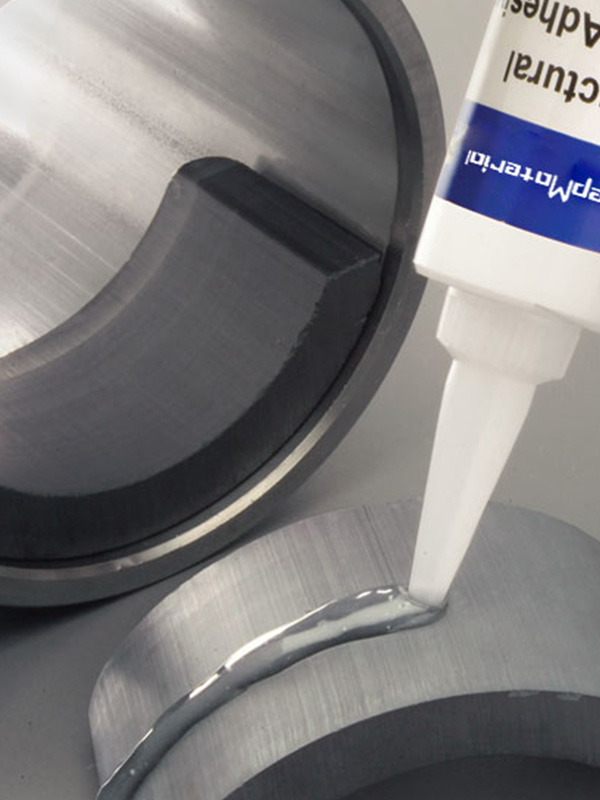
Polyurethane adhesives for metal bonding
Polyurethane adhesives are popular for bonding metals due to their high strength and durability. They can provide solid and permanent bonds that withstand heavy loads and extreme temperatures.
When choosing a polyurethane adhesive for metal bonding, it is essential to consider the specific requirements of your application. Factors such as the type of metal being bonded, the surface preparation required, and the curing time needed will all affect the choice of adhesive.
Polyurethane adhesives are generally best suited for bonding metals with relatively low surface energy, such as aluminum, stainless steel, and copper. These adhesives typically require a clean and dry surface for optimal bonding and may also need a primer or activator to improve adhesion.
Some standard polyurethane adhesives used for metal bonding include one-part moisture-curing polyurethanes, two-part polyurethanes, and structural polyurethanes. One-part moisture-curing polyurethanes are easy to use and can be applied directly to the metal surface, while two-part polyurethanes require mixing before application. Structural polyurethanes are designed for high-stress applications and provide exceptional strength and durability.
Polyurethane adhesives are an excellent choice for metal bonding due to their strength, durability, and versatility. However, proper surface preparation and adhesive selection are critical to ensure a robust and reliable bond.
Silicone adhesives for metal bonding
Here are some key considerations when selecting a silicone adhesive for metal bonding:
- Substrate compatibility: Make sure the silicone adhesive matches the metal substrate you are bonding. Some metals may require a primer or surface treatment to improve adhesion.
- Cure time: Consider the cure time required for the application. Some silicone adhesives cure quickly, while others need more time.
- Strength: Determine the power required for the bond. Silicone adhesives typically have good shear strength but may need to be stronger in tension or peel.
- Temperature resistance: Consider the temperature range the bond will be exposed to. Silicone adhesives resist high temperatures, but some may break down or lose adhesion at shallow temperatures.
- Chemical resistance: Consider the chemicals the bond will be exposed to. Silicone adhesives resist many chemicals, but some may be more resistant.
Phenolic adhesives for metal bonding
Phenolic adhesives are thermosetting adhesives that can be used for bonding metals. They are based on phenol-formaldehyde resins, cured by heat and pressure to form a solid and durable bond. Phenolic adhesives are known for their high heat, chemicals, and moisture resistance, making them ideal for applications in harsh environments.
When used for metal bonding, phenolic adhesives can provide a strong, permanent bond that can withstand various conditions. They can be used for bonding a variety of metals, including steel, aluminum, copper, and brass. The adhesive can be applied in various ways, such as by brush, roller, spray, or dipping.
One of the advantages of phenolic adhesives is their ability to cure at room temperature or with low heat, which can save energy and time compared to other adhesive systems that require high-temperature curing. They also have good gap-filling properties, which can help bond uneven surfaces.
However, there are some limitations to consider when using phenolic adhesives. They tend to have relatively low flexibility, making them less suitable for applications where the bonded joint will be subjected to significant movement or vibration. They also tend to have a relatively high viscosity, making them difficult to work with for some applications.
Phenolic adhesives can be a good choice for bonding metals when a solid and durable bond is required in harsh conditions. However, it is essential to carefully consider the application’s specific requirements to ensure that phenolic adhesives are the best choice.
UV-cured adhesives for metal bonding
When selecting a UV-cured adhesive for metal bonding, it’s essential to consider factors such as the type of metal being bonded, the strength of the bond required, and the environmental conditions the bond will be exposed to. Here are some common types of UV-cured adhesives used for metal bonding:
- Acrylic-based UV adhesives offer excellent bonding strength and durability, making them ideal for bonding metals. They also provide good resistance to heat and chemicals.
- Epoxy-based UV adhesives: These adhesives provide exceptional bonding strength and are particularly well-suited for bonding metals that are difficult to bond with other adhesives. They also offer good chemical and moisture resistance.
- Cyanoacrylate-based UV adhesives offer fast curing times and muscular bonding strength, making them a popular choice for metal bonding applications. However, they may not provide the same chemical and moisture resistance level as other types of UV-cured adhesives.
- Polyurethane-based UV adhesives are known for their flexibility and excellent bonding strength. They are particularly well-suited for bonding metals subject to vibration or other stresses.
Hybrid metal bonding adhesives
Hybrid metal bonding adhesives are a type of adhesive that combines the advantages of two or more different adhesive technologies to create a stronger, more versatile bond. These adhesives are typically used in industrial applications requiring a robust and durable bond.
Hybrid metal bonding adhesives may combine the benefits of epoxy, polyurethane, silicone, or other types of adhesives. For example, a mixed adhesive may combine an epoxy adhesive’s fast curing time and strong bonding properties with the flexibility and resistance to UV light of a silicone adhesive.
One of the key advantages of hybrid metal bonding adhesives is their ability to bond dissimilar materials. For example, they can bond metals to plastics or composites, which can be difficult with traditional adhesives. They are often more resistant to temperature extremes, chemicals, and other environmental factors than conventional adhesives.
Overall, hybrid metal bonding adhesives are versatile and practical for various industrial bonding applications.
Factors to consider when selecting a metal bonding adhesive
When selecting a metal bonding adhesive, there are several factors to consider:
- Substrate materials: The type of metal surfaces being bonded together is an important consideration. Different metals may require other adhesives or surface preparation.
- Strength requirements: The strength required for the bond will determine the type of adhesive to be used.d is required, and an epoxy adhesive may be a strong bond is needed.
- Environmental conditions: The environmental conditions to which the bond will be exposed will also play a role in selecting the adhesive. Factors such as temperature, humidity, exposure to chemicals, and UV light can affect the performance of the adhesive.
- Cure time: The amount of time required for the adhesive to cure is essential, especially if the bond needs to be used quickly.
- Application method: The adhesive’s application method can also be a factor in the selection process. Some adhesives may require special equipment or tools to apply.
- Compatibility with other materials: The adhesive should be compatible with any other materials in contact with the bonded surfaces.
- Cost: The cost of the adhesive is also a consideration, as it can vary widely depending on the type and quality of the adhesive.
Considering these factors, you can select the suitable metal bonding adhesive for your specific application.
Surface preparation for metal bonding adhesives
Surface preparation is critical in ensuring a solid and durable bond between metal surfaces and adhesives. Here are some common steps for surface preparation for metal bonding adhesives:
- Clean the surfaces: The first step in surface preparation is to clean the metal surfaces to remove any dirt, oil, grease, or other contaminants that can interfere with the adhesive bond. Use a suitable solvent or cleaning solution to thoroughly clean the surfaces.
- Abrade the surfaces: Abrading the metal surfaces can help to create a rough surface that provides more surface area for the adhesive to bond to. Use sandpaper, abrasive pads, or a wire brush to abrade the surfaces. The degree of abrasion required will depend on the adhesive used.
- Etch the surfaces: Etching the metal surfaces can help improve the adhesive’s adhesion. This is particularly important for non-porous metals such as stainless steel. Use an acid-based etching solution to etch the surfaces.
- Apply a primer: Applying a primer can help to promote adhesion and improve the performance of the adhesive. Choose a primer compatible with both the metal and the adhesive being used.
- Allow the surfaces to dry: After the surface preparation, allow the characters to dry completely before applying the adhesive. Follow the manufacturer’s recommended drying time.
It is important to note that the specific surface preparation steps may vary depending on the type of metal and adhesive being used. Always refer to the manufacturer’s instructions for clear guidance on surface preparation.
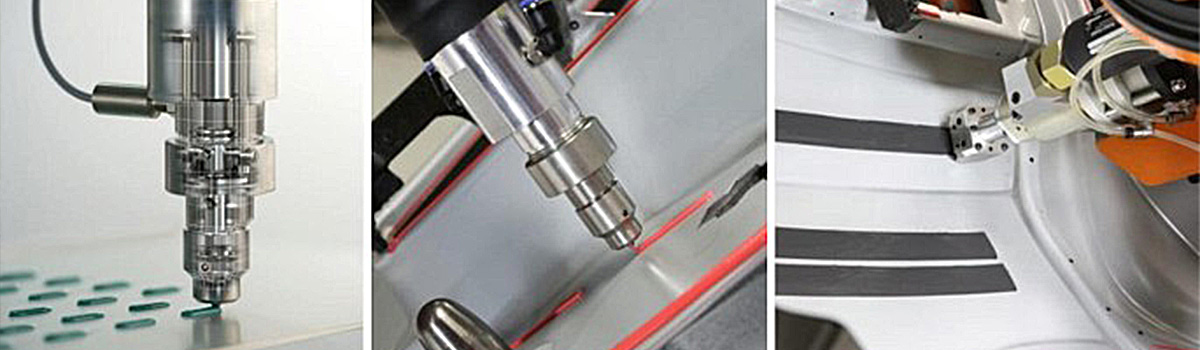
Joint design for metal bonding adhesives
Designing a joint for metal bonding adhesives requires careful consideration of several factors to ensure a solid and durable bond. Here are some key factors to consider:
- Surface Preparation: Proper surface preparation is critical to achieving a solid bond. The metal surfaces should be cleaned and free from any dirt, oil, rust, or other contaminants that could interfere with the adhesive bond.
- Adhesive Selection: Choose an adhesive specifically designed for bonding metal surfaces. Some sealants are better suited for certain types of metals, so it’s essential to select a suitable adhesive for the job.
- Joint Design: The joint design should provide maximum surface area for the adhesive bond. Joints with a lap-shear configuration are typically the strongest for metal bonding adhesives.
- Adhesive Application: Apply the adhesive evenly and with the correct coverage. Too little adhesive will result in a weak bond, while too much adhesive can cause the joint to fail due to excess stress.
- Clamping and Curing: Clamping the joint together during the curing process can help to ensure a strong bond. Follow the adhesive manufacturer’s recommended curing time and temperature for best results.
- Testing: Always test the bond strength of the joint before putting it into service. This can help to identify any issues early on and prevent potential failures.
By considering these factors and following best practices for metal bonding adhesives, you can design a joint that will provide a robust and reliable bond for your application.
Application methods for metal bonding adhesives
Some standard methods of applying metal bonding adhesives include:
- Brushing: This method involves applying the adhesive using a brush, which can help apply the adhesive to small or hard-to-reach areas.
- Spraying: This method involves using a spray gun to apply the adhesive evenly over a surface. It is a fast and efficient application method commonly used in industrial settings.
- Roller coating: This method involves using a roller to apply the adhesive evenly over a surface. It helps apply adhesive to large areas quickly.
- Dispensing: This method involves using a dispensing tool to apply the adhesive in a precise and controlled manner. It is commonly used for applying small amounts of adhesive to specific areas.
- Injection: This method involves injecting the adhesive into a joint or gap between two surfaces. It is helpful for bonding metal parts that are difficult to access or have complex shapes.
- Film laminating: This method involves applying a thin film of adhesive to a metal surface and then bonding the surface to another metal surface. It is commonly used for connecting large metal sheets.
Curing time for metal bonding adhesives
The curing time for metal bonding adhesives can vary depending on the specific adhesive used and the environmental conditions in which the adhesive is applied.
In general, metal bonding adhesives will have a specified curing time listed by the manufacturer, typically ranging from a few hours to several days.
Factors that can influence curing time include the type of metal being bonded, the surface preparation of the metal, the humidity and temperature of the environment, and the kind of adhesive used.
It is essential to follow the manufacturer’s instructions carefully when using metal bonding adhesives, including the recommended curing time, to ensure a solid and durable bond is achieved.
Testing and evaluation of metal bonding adhesives
Testing and evaluating metal bonding adhesives are crucial to ensure their reliability and performance in various applications. Here are some standard tests used to evaluate the bonding strength and quality of metal bonding adhesives:
- Lap shear test: This test measures the strength of the adhesive bond between two metal substrates under shear stress. The adhesive is applied between two metal substrates and cured, and then the substrates are pulled apart in a controlled manner. The force required to break the bond is measured, and the bond strength is calculated.
- T-peel test: This test measures the strength of the adhesive bond between a metal substrate and a flexible material, such as a polymer. The adhesive is applied to the metal substrate and cured, and then the elastic material is pulled away from the metal substrate at a 180-degree angle. The force required to peel the flexible material away from the metal substrate is measured, and the bond strength is calculated.
- Cleavage test: This test measures the adhesive bond strength under tensile stress. The adhesive is applied between two metal substrates and cured, and then the substrates are pulled apart in a controlled manner perpendicular to the plane of the bond. The force required to break the bond is measured, and the bond strength is calculated.
- Environmental testing: The adhesive bond strength should also be tested under various environmental conditions, such as exposure to temperature, humidity, and chemical agents, to determine the adhesive’s resistance to these conditions.
- Durability testing: This test evaluates the adhesive bond strength over an extended period. The adhesive bond is subjected to cyclic loading, temperature cycling, and other stressors to determine its long-term durability.
By conducting these tests, manufacturers can ensure that their metal bonding adhesives meet the necessary strength and durability requirements for their intended applications.
Structural bonding with metal bonding adhesives
Metal bonding adhesives are specialized types of structural adhesives that are designed to bond metals together. They create a solid and durable bond between two or more metal surfaces, which can be as strong or stronger than traditional welding or mechanical fastening methods.
Metal bonding adhesives can be used to bond a variety of metals, including steel, aluminum, titanium, and copper. They are typically two-part adhesives, which consist of a resin and a hardener. They undergo a chemical reaction that creates a strong, permanent bond when mixed.
There are several advantages to using metal bonding adhesives over traditional welding or mechanical fastening methods. These include:
- Improved aesthetics: Metal bonding adhesives can create a seamless bond between two metal surfaces, improving the overall appearance of a finished product.
- Increased flexibility: Metal bonding adhesives can absorb stress and movement, which can help prevent the bond’s cracking or failure.
- Reduced weight: Metal bonding adhesives are typically lighter than traditional mechanical fasteners, which can reduce the overall weight of a finished product.
- Increased durability: Metal bonding adhesives can create a solid and durable bond that can withstand harsh environmental conditions, such as heat, moisture, and chemicals.
Automotive applications of metal bonding adhesives
Metal bonding adhesives have become increasingly popular in the automotive industry due to their ability to improve vehicle performance and reduce manufacturing costs. Here are some of the automotive applications of metal bonding adhesives:
- Structural bonding: Metal bonding adhesives are commonly used in the automotive industry to bond structural components, such as frame rails, body panels, and pillars. These adhesives offer excellent strength and durability, and they can help to reduce the weight of the vehicle, which can improve fuel efficiency.
- Panel bonding: Metal bonding adhesives are also used to bond exterior body panels, such as hoods, trunks, and doors. These adhesives create a strong bond between the panel and the body of the vehicle, which can improve the vehicle’s overall rigidity and reduce noise, vibration, and harshness.
- Glass bonding: Metal bonding adhesives are used to bond windshields and other automotive glass. These adhesives provide excellent adhesion to the glass and the metal frame, and they can help to reduce the risk of leaks and breakage.
- Brake bonding: Metal bonding adhesives are used to bond brake pads to their metal backing plates. This adhesive bond provides a secure attachment that can withstand the high temerature helpres of braking, and it can help to reduce noise and vibration.
- Engine bonding: Metal bonding adhesives are used in engine assembly to bond various components, such as cylinder heads, oil pans, and vers. The Engine’s weight to reduce weight of the engine, improve its performance, and reduce assembly time and costs.
Overall, metal bonding adhesives offer many benefits to the automotive industry, including improved vehicle performance, reduced weight, and lower manufacturing costs.
Aerospace applications of metal bonding adhesives
Metal bonding adhesives are extensively used in the aerospace industry for various applications. Here are a few examples of aerospace applications of metal bonding adhesives:
- Structural bonding: Adhesives bond metal parts together in aerospace structures. This includes bonding composite materials with metal, metal-to-metal bonding, and bonding of different metal alloys.
- Repair and maintenance: Adhesives can be used to repair cracks, dents, and other damage to metal components in aircraft. These adhesives can help restore the strength and integrity of the damaged parts.
- Noise reduction: Adhesives can be used as vibration-damping materials to reduce noise in aircraft interiors. These adhesives can absorb and dampen the vibrations and noise generated by the engines and other sources.
- Aerodynamic improvements: Adhesives can attach fairings, winglets, and other aerodynamic components to aircraft. These components can help reduce drag, improve fuel efficiency, and increase the plane’s range.
- Electrical bonding: Adhesives can bond metal parts for electrical conductivity, such as grounding straps, connectors, and other electrical components.
Overall, metal bonding adhesives offer several advantages in aerospace applications, including weight savings, improved strength and durability, and the ability to bond dissimilar materials.
Electronics applications of metal bonding adhesives
Here are some typical applications of metal bonding adhesives in the electronics industry:
- Bonding metal parts: Metal bonding adhesives bond different metal components, such as aluminum, copper, brass, stainless steel, and other metals used in the electronics industry. This bonding method can help improve the overall product’s mechanical strength, durability, and reliability.
- Bonding heat sinks: Heat sinks are essential components in electronic devices to dissipate heat generated during operation. Metal bonding adhesives can bond heat sinks to electronic components, such as microprocessors, graphics cards, and other high-performance electronics. This bonding method helps to improve the thermal conductivity and efficiency of heat transfer, leading to better overall performance.
- Bonding electronic components: Metal bonding adhesives are also used to bond electronic components such as sensors, transducers, and other electronic devices to the substrate. This bonding method helps improve the overall product’s mechanical strength, stability, and reliability.
- Bonding printed circuit boards: Metal bonding adhesives bond the layers of printed circuit boards (PCBs) together. This bonding method helps to improve the mechanical strength and durability of the PCB, leading to better performance and reliability.
- Bonding electronic enclosures: Metal bonding adhesives bond the metal enclosure to the electronic device. This bonding method helps to provide a strong, durable, and reliable bond, protecting the electronic device from environmental factors such as moisture, dust, and vibrations.
Overall, metal bonding adhesives are essential in the electronics industry because they provide high-strength, reliable, and durable bonds between different metal components, leading to better electronic device performance, reliability, and durability.
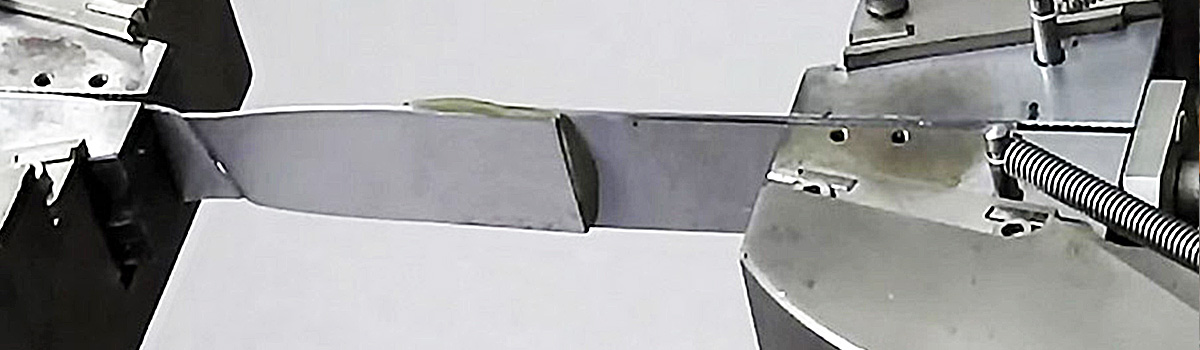
Construction applications of metal bonding adhesives
Metal bonding adhesives have numerous applications in the construction industry. Some common uses include:
- Bonding metal panels: Metal bonding adhesives are often used to bond metal panels together, such as in constructing metal buildings, roofs, and cladding systems. These adhesives can provide a robust, durable bond that can withstand weathering and other environmental factors.
- Attaching metal to other materials: Metal bonding adhesives can also be used to attach metal to other materials, such as wood, plastic, and concrete. This can be useful in constructing bridges, buildings, and other structures using different materials.
- Bonding metal brackets and fasteners: Metal bonding adhesives can bond metal brackets and fasteners to other materials. This can be useful in constructing metal stairs, handrails, and other metal structures.
- Repairing metal structures: Metal bonding adhesives can also improve metal structures, such as bridges and buildings. These adhesives can fill cracks and holes in metal and provide a robust and durable bond that can help extend the structure’s life.
- Bonding metal pipes: Metal bonding adhesives can bond metal pipes together, which can be helpful in plumbing and HVAC applications.
Overall, metal bonding adhesives are a versatile and valuable tool in the construction industry, providing a robust and durable bond that can help ensure the longevity and stability of structures and materials.
Marine applications of metal bonding adhesives
Here are some of the typical marine applications of metal bonding adhesives:
- Bonding metal structures: Metal bonding adhesives are often used to bond metal structures together in marine vessels, including ships, boats, and submarines. These adhesives can create strong and durable bonds between metals like aluminum, stainless steel, and titanium.
- Bonding deck fittings: Deck fittings on boats and ships, such as cleats, hatches, and rails, are often bonded in place using metal bonding adhesives. These adhesives provide a secure bond that can withstand the stresses of use and exposure to seawater.
- Repairing metal parts: Metal bonding adhesives are also used to improve marine vessels’ metal parts. For example, if a propeller or rudder is damaged, metal bonding adhesives can repair the damage and restore the function to its original strength and integrity.
- Bonding composite materials: In addition to bonding metal structures, metal bonding adhesives can be used to bond composite materials, such as carbon fiber or fiberglass, to metal structures. This is useful in applications where lightweight materials are desirable, such as in the construction of racing sailboats.
Overall, metal bonding adhesives play a crucial role in the marine industry by providing strong and durable bonds that can withstand the harsh conditions of the marine environment.
Medical applications of metal bonding adhesives
Metal bonding adhesives can be used in a wide range of medical applications, including:
- Dental Restorations: Metal bonding adhesives are commonly used in dental restorations, such as fillings, inlays, and crowns. These adhesives bond metal materials to the tooth structure, creating a reliable and durable repair.
- Orthopedic Implants: Metal bonding adhesives can also be used in orthopedic implants, such as hip and knee replacements. These adhesives can bond the metal implant to the surrounding bone tissue, promoting faster healing and reducing the risk of implant failure.
- Surgical Instruments: Metal bonding adhesives can bond metal parts together in surgical instruments, such as forceps and scissors. This creates a strong bond that can withstand repeated sterilization and use.
- Medical Devices: Metal bonding adhesives can bond metal parts, such as pacemakers, defibrillators, and insulin pumps. This creates a solid and durable bond that can withstand the harsh conditions inside the body.
Overall, metal bonding adhesives have a wide range of medical applications and are essential for creating solid and durable bonds between metal parts in various medical devices and applications.
Challenges of using metal bonding adhesives
Metal bonding adhesives can offer many advantages over traditional mechanical fasteners or welding, including improved flexibility, weight reduction, and durability. However, several challenges are associated with using these types of adhesives. Some of the challenges of using metal bonding adhesives include:
- Surface preparation: One of the most significant challenges of using metal bonding adhesives is ensuring proper surface preparation. To ensure good adhesion, metal surfaces must be thoroughly cleaned and free of contaminants, such as oil, grease, or rust. Any residues left on the surface can negatively impact the adhesive’s ability to bond to the metal.
- Bond strength: Metal bonding adhesives may provide a different power than traditional mechanical fasteners or welding. Adhesive strength may be compromised in extreme temperatures or when the bond is exposed to chemicals or moisture.
- Cure time: The cure time for metal bonding adhesives can be longer than other types of bonds. This can impact production time and require additional processing steps to ensure proper curing.
- Cost: Metal bonding adhesives can be more expensive than traditional mechanical fasteners or welding. Additionally, some bonds require specialized equipment or training to apply, which can further increase costs.
- Compatibility: Not all metal bonding adhesives are compatible with all metals. Selecting the suitable adhesive for the bonded metal is essential to ensure proper adhesion and avoid any chemical reactions that could compromise the bond.
Overall, metal bonding adhesives offer many benefits but present challenges that must be carefully considered and addressed to ensure proper bonding and long-lasting adhesion.
Safety considerations for metal bonding adhesives
However, several safety considerations should be considered when working with these adhesives. Here are some important safety considerations for metal bonding adhesives:
- Proper ventilation: Metal bonding adhesives can emit vapors that can be harmful if inhaled. Using these adhesives in a well-ventilated area or using appropriate respiratory protection is essential.
- Skin protection: Metal bonding adhesives can irritate the skin and cause dermatitis or other skin conditions. Wear gloves and protective clothing to avoid direct skin contact with the adhesive.
- Eye protection: Metal bonding adhesives can also cause eye irritation or injury if they come in contact with the eyes. Wear appropriate eye protection when handling these adhesives.
- Proper storage: Metal bonding adhesives should be stored in a cool, dry place, away from direct sunlight and heat sources. This will help prevent the adhesive from deteriorating or becoming unstable.
- Proper handling: Follow the manufacturer’s instructions for handling and applying the adhesive. Avoid prolonged exposure to the adhesive, and always use the recommended amount.
- Clean-up: Proper clean-up of metal bonding adhesives is essential to prevent accidental exposure or injury. Use the recommended cleaning materials and procedures to clean up spills or excess adhesive.
Following these safety considerations can reduce the risk of injury or harm when working with metal bonding adhesives. Always read and follow the manufacturer’s instructions and consult with a safety professional if you have any questions or concerns.
Environmental considerations for metal bonding adhesives
When selecting metal bonding adhesives, there are several environmental considerations to remember. Some of the critical factors to consider include:
- Temperature: Adhesives can be affected by high or low temperatures, so choosing an adhesive that is suitable for the intended operating temperature range of the bonded assembly is essential. If the community is exposed to extreme temperatures, selecting an adhesive specifically designed for high-temperature or cryogenic applications may be necessary.
- Humidity: Some adhesives are sensitive to moisture, affecting their ability to bond correctly. Choosing an adhesive that can withstand the humidity levels of the environment in which it will be used is essential.
- Chemical exposure: If the bonded assembly is exposed to chemicals, selecting an adhesive that is resistant to those chemicals is essential. This will help to ensure that the bond remains strong over time.
- UV exposure: If the bonded assembly is exposed to sunlight or other sources of UV radiation, selecting an adhesive resistant to UV degradation is essential. This will help to ensure that the bond remains strong over time.
- Sustainability: Environmental sustainability is an increasingly important consideration in adhesive selection. Some adhesives may contain hazardous chemicals or have high carbon footprints, so it is essential to consider the environmental impact of the bond in addition to its bonding properties.
By considering these environmental considerations, you can choose a metal bonding adhesive that will provide reliable bonding performance while also meeting your ecological requirements.
Quality assurance and control for metal bonding adhesives
Quality assurance and control are critical for ensuring the effectiveness and safety of metal bonding adhesives. Here are some essential steps that can be taken to ensure the quality of metal bonding adhesives:
- Raw Material Selection: It is important to select high-quality raw materials that meet the desired specifications for the adhesive. This includes choosing the appropriate resin, hardener, and other additives, such as fillers or accelerators.
- Formulation and Mixing: The formulation and mixing process should be controlled and standardized to ensure the consistent quality of the adhesive. This can involve using precise measurements, equipment, and strict process controls.
- Testing: The adhesive should undergo rigorous testing to meet the required performance specifications. This includes tests for strength, durability, and chemical resistance.
- Application Process: The application process should be carefully controlled to ensure the adhesive is applied evenly and at the correct thickness. This can involve using automated dispensing equipment or other specialized tools.
- Curing Process: Curing is critical for ensuring the adhesive develops strength and bonding properties. This can involve controlling temperature, humidity, and other environmental factors during curing.
- Quality Control: Regular quality control checks should ensure the adhesive meets the required specifications. This can include visual inspections and more sophisticated testing methods, such as X-ray fluorescence or scanning electron microscopy.
By following these steps, manufacturers can ensure that their metal bonding adhesives are of consistent quality and meet the required performance specifications.
Future trends in metal bonding adhesives
In recent years, there have been several trends in the development of metal-bonding adhesives that are likely to shape their future. Some of these trends are:
- Development of new adhesive chemistries: There is a growing trend toward developing new chemistries that offer improved performance over traditional epoxy-based adhesives. For example, cyanoacrylates and urethanes are gaining popularity due to their ability to bond with a broader range of metals and offer improved durability and toughness.
- Increased use of nanotechnology: Advances in nanotechnology are driving the development of metal-bonding adhesives with enhanced properties. For example, nanoparticles can improve adhesion strength, toughness, and corrosion resistance.
- Growing demand for eco-friendly adhesives: As environmental concerns continue to grow, there is a growing demand for eco-friendly metal bonding adhesives. New formulations are being developed free from volatile organic compounds (VOCs) and other harmful chemicals.
- Integration with other materials: Metal bonding adhesives are increasingly combined with other materials, such as composites, plastics, and ceramics. This trend is driven by the need to create lightweight structures with high strength and stiffness.
- Use of automation and robotics: The use of automation and robotics in manufacturing is increasing, and this trend is likely to continue. Metal bonding adhesives are well-suited to automated manufacturing processes, and new formulations are being developed that can be easily dispensed and cured using mechanical equipment.
Overall, the future of metal bonding adhesives looks promising, with continued development and innovation likely to improve performance, sustainability, and cost-effectiveness.
Conclusion: The growing importance of metal bonding adhesives
In conclusion, metal bonding adhesives are becoming increasingly important in various industrial applications, such as automotive, aerospace, electronics, and construction.
The development of new adhesive chemistries, the use of nanotechnology, the growing demand for eco-friendly adhesives, integration with other materials, and the use of automation and robotics will likely shape the future of metal bonding adhesives.
These trends are driven by the need to create lightweight structures with high strength and stiffness and the demand for more sustainable and cost-effective manufacturing processes. As such, metal-bonding adhesives are set to play an increasingly important role in the industrial sector in the coming years.