Fiber Optic Adhesives
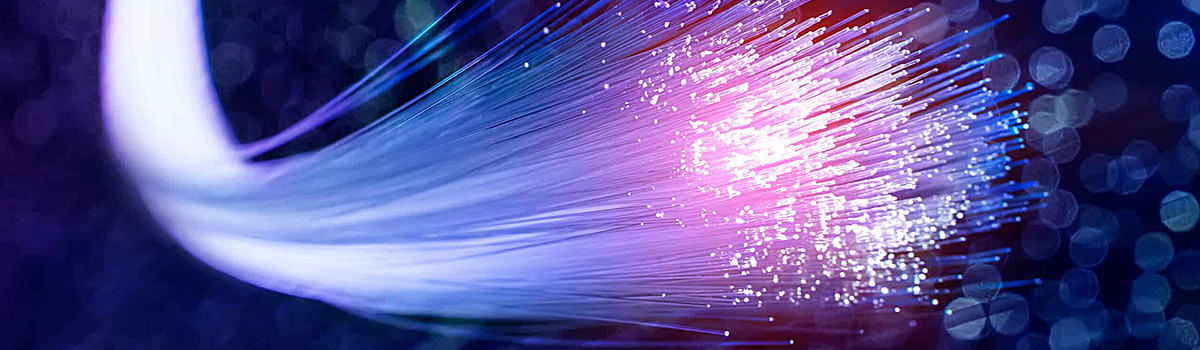
Fiber optic adhesive is a critical component in the manufacturing and installation of fiber optic cables. It is used to bond the fiber optic connectors and ferrules to the fiber optic cable, ensuring a secure and stable connection. Fiber optic adhesive comes in different forms and compositions, each with its own set of properties and applications. In this article, we will discuss everything you need to know about fiber optic adhesive, including its types, properties, applications, and best practices.
What is Fiber Optic Adhesive?
Fiber optic adhesive is a type of specialized adhesive used to assemble and install fiber optic cables. It is a two-part epoxy resin designed to bond the various components of fiber optic cables together.
Fiber optic adhesive typically consists of a resin and a hardener mixed together in a specific ratio just before use. Once the adhesive is mixed, it cures and hardens, creating a strong bond between the fiber optic components.
The adhesive is typically used to bond fiber optic connectors to the fiber optic cable and to bond the connector’s various components. The adhesive also produces fiber optic patch cords and other fiber optic components.
Fiber optic adhesive is specifically designed to have low shrinkage and low outgassing, which helps to ensure that the bond remains strong over time. It is also intended to have a low viscosity, making it easy to apply and allowing it to flow into small gaps and crevices.
Types of Fiber Optic Adhesive
There are several types of adhesives used for fiber optic applications, including:
- Epoxy-based Fiber Optic Adhesive
- Acrylic-based Fiber Optic Adhesive
- Silicone-based Fiber Optic Adhesive
- UV-curable Fiber Optic Adhesive
- Dual-cure Fiber Optic Adhesive
Epoxy-based Fiber Optic Adhesive
Epoxy-based fiber optic adhesives are two-part adhesives that consist of a resin and a hardener. They are commonly used in telecommunications to bond and terminate optical fibers. These adhesives have high mechanical strength and excellent chemical resistance, which makes them ideal for fiber optic applications.
When using an epoxy-based fiber optic adhesive, following the manufacturer’s instructions carefully is essential to ensure proper curing and bonding. The adhesive should be applied in a thin layer, and the fiber should be inserted immediately before the adhesive starts to set. Ensuring the fiber is aligned correctly before the adhesive sets is also essential.
Some epoxy-based fiber optic adhesives are formulated with special additives to improve their optical properties, such as low attenuation and high refractive index. These properties help to minimize signal loss and maximize the efficiency of the fiber optic system.
Acrylic-based Fiber Optic Adhesive
Acrylic-based fiber optic adhesive is used to assemble and install fiber optic cables. It is a two-part adhesive that consists of a resin and a hardener. When mixed, the adhesive forms a strong bond resistant to moisture, heat, and chemicals.
Acrylic-based fiber optic adhesive is commonly used to attach connectors to fiber optic cables and bond fibers to substrates. It also produces fiber optic components, such as couplers, attenuators, and splitters.
One of the main advantages of acrylic-based fiber optic adhesive is its fast cure time; it typically cures in less than 10 minutes, which makes it a popular choice in high-volume manufacturing environments. The acrylic-based adhesive is relatively easy to handle and requires no special application equipment.
However, acrylic-based fiber optic adhesive does have some limitations. It is unsuitable for high-temperature environments, as it can degrade and lose its adhesive properties. Additionally, it may not bond well with certain plastics and metals, so selecting the appropriate adhesive for the specific application is essential.
Silicone-based Fiber Optic Adhesive
Silicone-based fiber optic adhesives are specialized for bonding and securing optical fibers in various applications, including telecommunications, data centers, medical equipment, and industrial automation. These adhesives are specifically formulated to provide strong bonding and excellent adhesion to multiple substrates, including glass, plastic, and metals.
Silicone-based fiber optic adhesives offer several benefits, such as high-temperature resistance, excellent thermal stability, low shrinkage, and low outgassing. They also offer excellent mechanical properties, such as high strength, elongation, and flexibility, ensuring reliable bonding and long-term durability in fiber optic applications.
Silicone-based fiber optic adhesives are available in various forms, including one-part or two-part systems, which can be cured by heat or UV light. Depending on the application requirements, they can be applied by various methods, such as dipping, brushing, or syringe dispensing.
When selecting a silicone-based fiber optic adhesive, it is essential to consider factors such as the curing time, bonding strength, thermal and mechanical properties, and compatibility with the optical fibers and substrates. It is also essential to follow the manufacturer’s storage, handling, and application instructions to ensure optimal performance and long-term reliability.
UV-curable Fiber Optic Adhesive
UV-curable fiber optic adhesives are a type of adhesive used to bond optical fibers together in various applications, including telecommunications, data centers, and medical devices. These adhesives typically consist of a polymer resin and a photoinitiator that reacts with UV light to harden and cure the adhesive.
UV-curable fiber optic adhesives offer several advantages over traditional adhesives, including faster curing times, lower shrinkage rates, and higher bond strength. UV-curable adhesives are more environmentally friendly than solvent-based adhesives since they do not contain harmful volatile organic compounds (VOCs).
One important consideration when working with UV-curable fiber optic adhesives is the wavelength of the UV light used to cure the adhesive. The photoinitiator in the adhesive is designed to react with a specific wavelength of UV light, typically 300-400 nm. Using the wrong wavelength of light can result in incomplete curing and weakened bonds.
Overall, UV-curable fiber optic adhesives are a reliable and effective solution for bonding optical fibers in various applications, and they offer several advantages over traditional adhesives.
Dual-cure Fiber Optic Adhesive
Dual-cure fiber optic adhesive is a type of adhesive that is commonly used in fiber optic applications. This adhesive is designed to cure using either UV light or heat, allowing for a more flexible and versatile bonding solution.
The dual-cure aspect of the adhesive means that it can cure using both UV light and heat, which makes it ideal for a wide range of applications. For example, in some applications, UV light may not be able to penetrate all areas of the adhesive, but heat can, and vice versa. The adhesive can cure completely and evenly by having both curing methods available, ensuring a solid bond.
In addition, dual-cure fiber optic adhesive is often used because it has a low shrinkage rate during curing. This is important because shrinkage can cause stress on the fiber optic components, leading to problems such as signal loss or breakage.
Properties of Fiber Optic Adhesive
Fiber optic adhesive, also known as optical adhesive or epoxy, is a type of adhesive used to bond optical fibers to various components in fiber optic systems. Some of the properties of fiber optic adhesive include:
- Low shrinkage: Fiber optic adhesive is designed to have very low shrinkage when it cures. This is important because any shrinkage can cause stress on the fiber and lead to signal loss or damage.
- High optical clarity: Fiber optic adhesive is formulated to be highly transparent, so it does not interfere with light transmission through the optical fiber.
- High-temperature resistance: Fiber optic adhesive is designed to withstand high temperatures without degrading or losing bonding strength.
- Low viscosity: Fiber optic adhesive typically has a low density, making it easy to work with, and can be applied in small, precise amounts.
- Low outgassing: Fiber optic adhesive is formulated to have low outgassing, which releases very little gas during curing. This is important because any gas that is released can cause contamination of the optical system.
- Good adhesion: Fiber optic adhesive is formulated to provide strong adhesion to the optical fiber and the other components it is bonded to.
Curing Time
Curing time refers to the time it takes for a material, such as a coating, adhesive, or concrete, to fully dry or harden. The curing time can vary depending on the type of material, the temperature and humidity of the environment, and other factors.
For example, water-based paint may take a few hours to dry to the touch, but it can take several days to fully cure and reach its maximum hardness and durability. A two-part epoxy adhesive may have a shorter curing time, typically a few hours, but may require several days to get full strength.
Following the manufacturer’s recommended curing time is essential to ensure the material reaches its maximum strength and performance. Rushing the curing process can result in a weaker and less durable final product.
Tensile Strength
Tensile strength refers to the maximum amount of tensile stress a material can withstand before it fractures or breaks, and it measures the material’s ability to resist being pulled apart or stretched.
Tensile strength is usually expressed in units of force per unit area, such as pounds per square inch (psi) or newtons per square meter (N/m^2). For example, the tensile strength of steel can range from 400 to 2,500 megapascals (MPa) or 58,000 to 363,000 psi, depending on the type of steel and the manufacturing process.
Tensile strength is an essential property for materials used in applications subjected to stretching or pulling forces, such as construction, engineering, and manufacturing. It is commonly tested using a tensile testing machine, which removes a material specimen until it fractures while measuring the force and deformation.
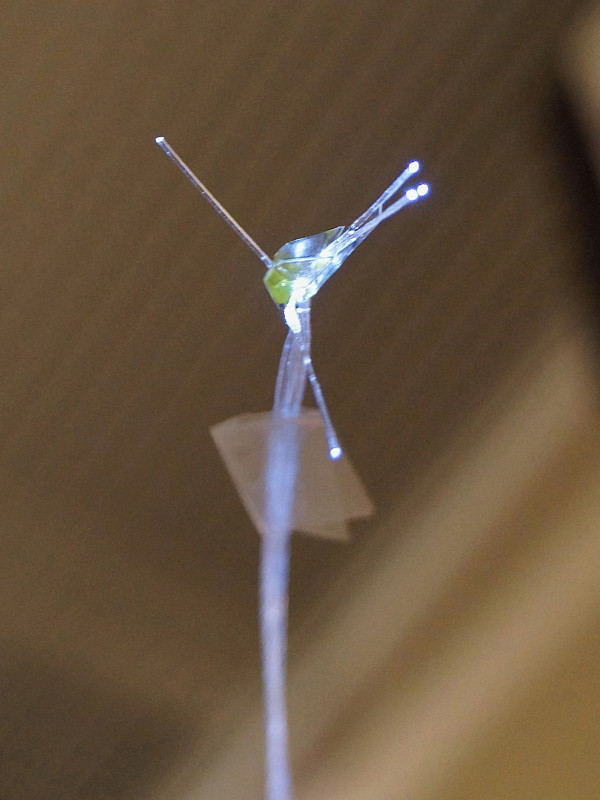
Shear Strength
Shear strength is the ability of a material to resist forces that are applied parallel or tangential to its surface, causing one part of the material to slide or shear relative to another position. It is an important mechanical property of metals, polymers, and composites.
Shear strength is typically measured using a shear test, which involves applying a force perpendicular to the surface of a material while maintaining a parallel displacement of the material’s top and bottom surfaces. The maximum shear stress the material can withstand before it fails is its shear strength.
In engineering and structural design, the shear strength of a material is a critical parameter that determines the maximum load a structure can withstand before it experiences failure due to shearing forces. It is also essential to understand the behavior of materials under various loading conditions and in designing materials and structures that can withstand such forces.
Peel Strength
Peel strength is the force required to peel two bonded materials apart from a surface, such as adhesive tape. It measures the adhesive strength of a material or a bond between two materials. Peel strength is usually expressed in pounds per inch (lb/in) or Newtons per meter (N/m). The peel strength of a material or bond can be influenced by various factors, such as the type of adhesive used, the surface preparation of the materials being bonded, the temperature and humidity during bonding, and the test method used to measure peel strength.
Temperature Resistance
Temperature resistance refers to the ability of a material or substance to maintain its physical and chemical properties under different temperature conditions. Other materials have additional temperature resistance capabilities.
For example, some materials like metals, ceramics, and certain plastics can withstand high temperatures, while others, like organic materials and some plastics, may degrade or melt at high temperatures.
Temperature resistance is an essential factor to consider when selecting materials for various applications. For instance, in the aerospace industry, materials used for engine components must withstand extremely high temperatures. In contrast, in the food industry, materials used for packaging must withstand a range of temperatures without degrading or leaching harmful substances.
Factors that can affect temperature resistance include the composition and structure of the material, as well as the heating or cooling rate. Generally, higher temperature resistance is achieved by using materials with higher melting points or by adding heat-stabilizing additives.
Chemical Resistance
Chemical resistance refers to the ability of a material or substance to withstand exposure to various chemicals without undergoing significant deterioration, degradation, or other adverse effects. Chemical resistance is an essential property for many industrial materials, such as coatings, plastics, and metals, as well as for personal protective equipment (PPE), such as gloves and respirators.
Chemical resistance can be affected by various factors, including the type and concentration of the chemical, the temperature and pressure conditions, and the duration of exposure. Some materials may resist certain chemicals but not others and different materials may have different resistance levels to the same chemical.
A material’s chemical resistance can be determined through testing using various methods, such as immersion testing, exposure to vapor, or spot testing. The results of these tests help determine the suitability of a material for a particular application and guide the selection of appropriate PPE for workers handling hazardous chemicals.
Index Matching
Index matching is a technique that reduces reflection losses at the interface between two materials with different refractive indices. When light passes from a fabric with a higher refractive index to a material with a lower refractive index, some of the light is reflected at the interface, leading to a loss of energy and a reduction in signal strength. Index matching involves placing a thin material layer with an intermediate refractive index between the two materials to minimize the difference in refractive index and reduce reflection losses.
Index matching is commonly used in optical applications such as lenses, prisms, and fibers to improve transmission efficiency and reduce unwanted reflections. The choice of index-matching material depends on the specific application and the refractive indices of the matched materials. Some common index-matching materials include optical adhesives, fluids, gels, and films.
Applications of Fiber Optic Adhesive
Fiber optic adhesive is a specialized adhesive used to manufacture and install fiber optic cables. Here are some of the applications of fiber optic adhesive:
- Cable manufacturing: Fiber optic adhesive is used in the manufacturing of fiber optic cables to bond the fiber optics components, such as the fibers, buffer tubes, and strength members, together.
- Cable installation: Fiber optic adhesive is used to install fiber optic cables to secure the line to its mounting hardware, splice enclosures, and other equipment.
- Fiber termination: Fiber optic adhesive is used to terminate fiber optic cables to attach the fiber to connectors, ferrules, or other termination devices.
- Splicing: Fiber optic adhesive is used in splicing fiber optic cables together to create a continuous optical path between two fibers.
- Maintenance and repair: Fiber optic adhesive is used in maintenance and repair activities to secure loose or damaged components of fiber optic cables.
Fiber Optic Cable Manufacturing
Here are the main steps involved in fiber optic cable manufacturing:
- Perform production: The first step is to produce a glass preform, which is a cylindrical glass rod that serves as the basis for the fiber optic cable. The preform is made by melting high-purity silica glass in a specialized furnace and then carefully cooling it to form a solid, transparent rod.
- Fiber drawing: Once the preform is produced, it is placed in a fiber drawing tower. The tower heats the preform and draws a thin, flexible fiber optic strand. This process is repeated several times to produce multiple strands twisted together to form a cable.
- Coating: The fiber strands are then coated with a protective layer of polymer material to prevent damage during installation and use. The coating material is applied using a precision process to ensure that it is evenly distributed around the fiber.
- Cabling: Once the fiber strands are coated, they are twisted together to form a cable. The line is reinforced with additional protective materials, such as Kevlar, for strength and durability.
- Testing: Finally, the finished cable is tested to ensure it meets the required specifications for data transmission. This involves testing the line for parameters such as attenuation, bandwidth, and signal-to-noise ratio.
Fiber Optic Connector Assembly
Fiber optic connector assembly involves terminating a fiber optic cable with a connector that connects it to other devices or cables. The process typically involves the following steps:
- Prepare the cable: The first step is to prepare the fiber optic cable by stripping off the outer jacket and the protective coating to expose the bare fiber.
- Cleaving the fiber: The next step is to cleave the fiber to achieve a clean, flat end face.
- Cleaning the fiber: The cleaved end of the thread is then washed to remove any dust, oil, or other contaminants that might affect the quality of the connection.
- Inserting the fiber: The fiber is then inserted into the connector body and secured with a crimp sleeve or other mechanism.
- Polishing the end face: The final step is to polish the end face of the fiber to achieve a smooth surface that allows light to pass through with minimal loss.
The entire process must be performed carefully to ensure the connector provides a reliable, low-loss connection.
Fusion Splicing
Fusion splicing joins two optical fibers by melting their ends and fusing them using an electric arc. The resulting joint, or splice, is permanent and has a shallow signal loss, making it ideal for high-performance fiber optic networks.
The fusion splicing process involves several steps. First, the fibers are prepared by stripping off their protective coatings and cleaning them to ensure a clean surface for fusion. The fibers are then aligned using a specialized fusion splicer machine with cameras and microscopes to ensure perfect alignment. Once aligned, an electric arc melts the thread ends together and forms a permanent bond.
Fusion splicing is preferred over other splicing methods, such as mechanical splicing because it offers better signal loss and reliability performance. It is commonly used in long-haul and high-speed fiber optic networks and in applications such as fiber optic sensors and medical equipment.
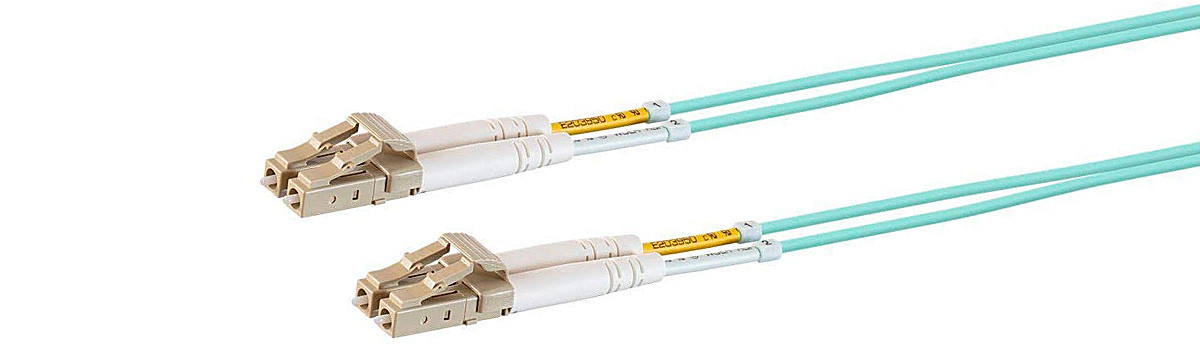
Fiber Optic Termination
Fiber optic termination refers to terminating or connecting the ends of fiber optic cables to different devices or components, such as transmitters, receivers, switches, and patch panels.
The termination process involves carefully stripping the protective coating or jacket off the end of the fiber optic cable, cleaning and polishing the exposed fiber, and then attaching a connector or adapter to the end of the thread. This connector can then be plugged into the appropriate device or component.
Various types of fiber optic connectors are available, including SC, LC, ST, and MTRJ connectors, each with advantages and disadvantages. Proper termination is crucial for ensuring the high-quality transmission of data over fiber optic cables, as any imperfections or misalignments in the connection can cause signal loss, attenuation, or other performance issues.
Fiber Optic Inspection
Fiber optic inspection examines the physical condition of a fiber optic cable, connector, or splice. This inspection is critical in ensuring that the fiber optic system is functioning optimally, as any damage or imperfections in the fiber can negatively impact signal transmission and quality.
There are several methods of fiber optic inspection, including visual inspection, microscope inspection, and video inspection. Visual inspection involves using the naked eye to look at the connector or cable end face for any visible defects or damage. Microscope inspection uses a specialized microscope to magnify the connector or cable end face and identify weaknesses or damage in more detail. Video inspection involves using a specialized camera to capture images or video of the connector or cable end face and analyzing the footage for defects or damage.
Fiber optic inspection is essential for several applications, including telecommunications, medical imaging, and military and defense systems. Regular inspection and maintenance of fiber optic systems can ensure optimal performance and prevent costly downtime.
Best Practices for Using Fiber Optic Adhesive
Here are some best practices for using fiber optic adhesive:
- Choose the Right Adhesive: Different types of fiber optic adhesives are available in the market, and each type is designed for a specific application. Some bonds are better suited for low-temperature environments, while others can withstand high-temperature environments. Choosing a suitable adhesive based on the particular application requirements is essential.
- Follow Manufacturer’s Instructions: Always follow the manufacturer’s instructions when using fiber optic adhesive. This includes the mixing ratios, curing times, and application methods. Failure to follow the instructions can result in poor bonding and can compromise the performance of the fiber optic components.
- Clean the Surfaces: The surfaces that need to be bonded should be clean and free of dirt, dust, or oils. Use a lint-free cloth and a cleaning solution recommended by the manufacturer to clean the surfaces. Any residue left on the surfaces can affect the bond strength.
- Use the Right Amount: Use the recommended amount of adhesive as the manufacturer specifies. Too much adhesive can cause the excess to squeeze out and result in a messy application. Using too little adhesive can result in a weak bond.
- Apply Uniform Pressure: Apply uniform pressure on the bonded surfaces to ensure proper contact between the surfaces and the adhesive. This can be done using a specialized tool or by applying pressure by hand.
- Allow for Proper Curing Time: Allow the adhesive to cure for the recommended time before using the fiber optic component. Premature use can compromise the bond strength and affect the performance of the fiber optic component.
- Store Properly: Store fiber optic adhesive in a cool and dry place, away from direct sunlight and heat sources. Follow the manufacturer’s instructions for storage conditions and shelf life.
Surface Preparation
Many different techniques and tools can be used for surface preparation, depending on the type of surface and the desired outcome. Some standard methods include:
- Cleaning: The surface should be cleaned thoroughly to remove dirt, grease, oil, or other contaminants. This can be done using solvents, detergents, or other cleaning agents.
- Sanding: Sanding is used to smooth rough surfaces and remove old coatings or paint. This can be done using sandpaper or a sanding machine.
- Grinding: Grinding removes any high spots or rough areas on the surface. This can be done using a grinding wheel or a diamond disc.
- Blasting removes rust, paint, or other stubborn contaminants from the surface. This can be done using sandblasting or other abrasive blasting techniques.
- Priming: Once the surface is clean and smooth, a primer can help the coating or paint adhere properly. The type of primer used will depend on the surface type and the coating or paint being applied.
Proper surface preparation is essential for the longevity of any coating or paint applied to the surface. If the surface is not prepared correctly, the coating or color may not adhere properly, leading to peeling, cracking, or other issues.
Mixing Ratio
The mixing ratio, also known as the mass or moisture mixing ratio, measures the amount of water vapor in a mixture of air and water vapor. It is defined as the mass of water vapor per unit of dry air in the mix.
The mixing ratio is typically expressed in grams of water vapor per kilogram of dry air (g/kg) or in parts per million (ppm) by mass. It is a valuable measure in meteorology and atmospheric science, as it is a conserved quantity in adiabatic processes, meaning that it remains constant as air rises or sinks in the atmosphere.
The mixing ratio is related to other measures of atmospheric moisture, such as relative humidity and dew point temperature, but provides a more direct measure of the actual amount of water vapor in the air.
Dispensing Technique
The following are some essential steps involved in dispensing medication:
- Verification of the prescription – The pharmacist or pharmacy technician verifies the prescription to ensure the medication, dosage, and directions are accurate and appropriate.
- Labeling of the medication – The pharmacist or pharmacy technician labels the medication container with the patient’s name, medication name, dosage, and instructions for use.
- Measuring the medication – The pharmacist or pharmacy technician measures the medication accurately using a calibrated measuring device such as a syringe, graduated cylinder, or electronic balance.
- Transferring the medication – The medication is transferred to the patient’s container, such as a bottle, blister pack, or inhaler.
- Quality control – Before dispensing the medication, the pharmacist or pharmacy technician checks to ensure the drug has been accurately measured and transferred.
- Counseling – The pharmacist or pharmacy technician counsels the patient on how to use the medication correctly and answers any questions the patient may have.
It is essential to follow dispensing techniques accurately to avoid medication errors and ensure patient safety. Pharmacists and pharmacy technicians are trained to follow standardized procedures to ensure that medication is dispensed safely and accurately.
Curing Conditions
It is essential to seek medical advice from a qualified healthcare professional for any health concerns. They can diagnose properly and recommend appropriate treatments based on your needs and medical history.
Some common treatments for health conditions may include medication, surgery, physical therapy, counseling, and lifestyle changes such as diet and exercise. The effectiveness of treatment can vary depending on the specific condition and individual circumstances, so it is essential to follow the guidance of your healthcare provider.
Storage and Handling
Some common principles for storage and handling include:
- Temperature control: Many products require specific temperature ranges for optimal storage and handling, such as refrigeration for perishable foods or excellent, dry conditions for pharmaceuticals.
- Humidity control: Products sensitive to moisture, such as electronics or paper products, may require special packaging or storage conditions to prevent damage.
- Protection from light: Some products, such as medications or certain chemicals, can be affected by exposure to sunlight and may require opaque or light-blocking packaging.
- Proper packaging: Products should be stored in appropriate materials to prevent damage or contamination during handling and transport.
- Clean and organized storage areas: Storage areas should be clean and organized to prevent cross-contamination and ensure easy product access when needed.
- Proper procedures: Products should be handled carefully to prevent damage or contamination, and any required safety procedures should be followed.
By following these principles, businesses and individuals can help ensure their products are stored and handled safely and effectively.
Health and Safety Precautions
Some everyday health and safety precautions include:
- Personal protective equipment (PPE): This includes gloves, masks, and safety glasses, which can help protect individuals from exposure to harmful substances or infectious diseases.
- Proper ventilation: Adequate ventilation is essential to prevent the buildup of harmful gases, fumes, or particles in enclosed spaces.
- Fire safety includes measures such as smoke detectors, fire extinguishers, and emergency exit plans to prevent and respond to fires.
- Ergonomics: Proper ergonomics can help prevent workplace injuries such as strains, sprains, and repetitive motion injuries.
- Hazard communication: Employers and other organizations must communicate potential hazards to employees and others exposed.
- Proper handling and disposal of hazardous materials: This includes following appropriate protocols for the handling, storage, and disposal of chemicals, batteries, and other dangerous materials.
- Sanitation and hygiene: Regular cleaning and disinfecting of surfaces and facilities can help prevent spreading of infectious diseases.
- Safe driving practices include obeying traffic laws and avoiding distractions while driving to prevent accidents.
By implementing these and other health and safety precautions, individuals and organizations can help prevent injuries, illnesses, and other harm to themselves and others.
Common Problems with Fiber Optic Adhesive
Fiber optic adhesive bonds optical fibers to other components, such as connectors, ferrules, and splice trays. However, several common problems can occur with fiber optic adhesive:
- Poor bonding strength: One of the most common problems with fiber optic adhesive is poor bonding strength, which can result in fiber breakage or signal loss. This can occur if the adhesive needs to be adequately mixed or if the surface needs to be cleaned and prepared before applying the adhesive.
- Curing time: Fiber optic adhesive requires a specific amount of time to cure, which can vary depending on the type of adhesive and the environmental conditions. If the adhesive is not given enough time to cure, it may not bond properly or result in a weak bond.
- Contamination: Even small amounts of contamination can affect the performance of fiber optic adhesive. Dust, oil, and other contaminants can interfere with bonding, resulting in a weak bond or signal loss.
- Shelf life: Fiber optic adhesive has a limited shelf life and can expire or become less effective over time. It is essential to check the bond’s expiration date and storage conditions before use.
- Compatibility: Different types of fiber optic adhesive are designed for specific applications and may not be compatible with certain materials or components. It is essential to choose the correct adhesive for the particular application and to ensure compatibility with all components involved.
- Dispensing: Proper dispensing of fiber optic adhesive is critical for achieving a solid bond. Improper dispensing, such as applying too much or too little adhesive, can result in a weak bond or signal loss.
- Safety: Fiber optic adhesive can be hazardous if not handled properly. Following all safety guidelines and wearing protective equipment when working with the adhesive is essential.
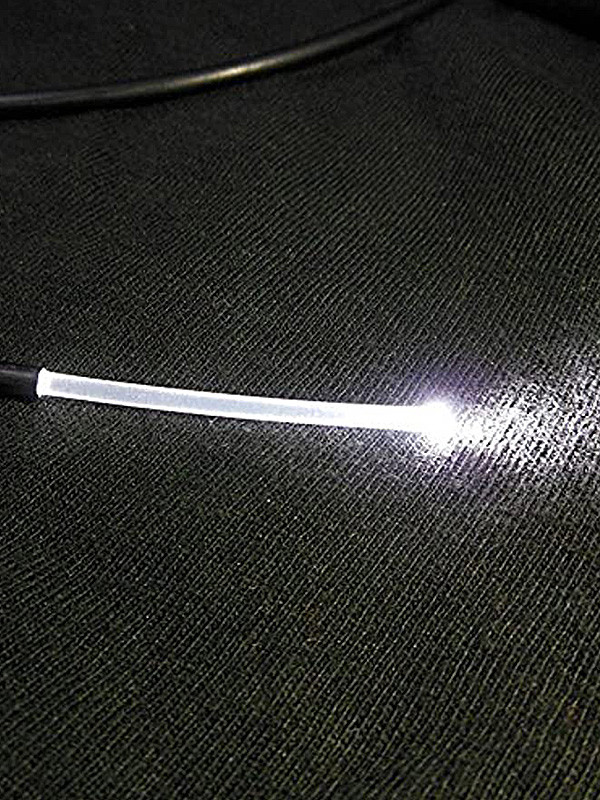
Troubleshooting Tips
Here are some general troubleshooting tips that can be applied in various situations:
- Start with the basics: Ensure everything is plugged in, turned on, and connected correctly.
- Restart: Sometimes, restarting the device or software can solve the problem.
- Check for updates: Check if any updates are available for the device or software, and install them if necessary.
- Check for error messages: Look for any error messages or codes that may indicate the problem.
- Try a different approach: If one method isn’t working, try a different approach or method to see if it solves the problem.
- Check for conflicts: Make sure there are no conflicts with other devices or software that may be causing the problem.
- Seek help: If you still need help solving the problem, seek help from customer support, online forums, or a professional.
- Document the problem: Keep track of any steps you’ve taken to troubleshoot the problem and any error messages or codes you encounter to make it easier to communicate the issue to others who can help.
The Impact of Fiber Optic Adhesive on Telecommunications Infrastructure
Fiber optic adhesive is an essential component of the telecommunications infrastructure, and it significantly impacts its performance and reliability. The adhesive bonds the fiber optic cables to the connectors, ensuring a secure and stable connection that can withstand harsh environmental conditions.
One of the most significant advantages of fiber optic adhesive is its ability to provide a low-loss connection between the fiber optic cable and the connector. This is crucial in telecommunications infrastructure, where even small losses can significantly impact signal quality and data transmission rates.
Another essential benefit of fiber optic adhesive is its ability to provide a secure and stable connection that can withstand a variety of environmental factors. This includes extreme temperatures, moisture, vibration, and mechanical stress. The adhesive helps prevent cable damage and signal loss, ensuring the telecommunications infrastructure remains reliable and efficient.
In addition to its performance benefits, fiber optic adhesive is also easy to apply and can be used in various applications. This makes it an ideal choice for telecommunications infrastructure, where it is used in everything from fiber optic cables to connectors and splice trays.
Overall, the impact of fiber optic adhesive on telecommunications infrastructure is significant. It helps to ensure reliable and efficient data transmission, even in challenging environmental conditions and is an essential component of modern telecommunications networks.
The Impact of Fiber Optic Adhesive on IoT and Smart Devices
Fiber optic adhesive can significantly impact IoT (Internet of Things) and bright devices. Fiber optic adhesive bonds fiber optic connectors to the fibers, ensuring a robust and reliable connection between the devices. Here are a few ways in which fiber optic adhesive can impact IoT and smart devices:
- Improved connectivity: Fiber optic adhesive can improve the connectivity between devices. It ensures a robust and reliable connection, essential for the smooth functioning of IoT and bright devices. Fiber optic adhesive significantly reduces the risk of data loss or slow data transmission.
- Faster data transmission: Fiber optic adhesive can help achieve faster data transmission speeds. This is because fiber optic cables can transmit data at very high speeds, and with a reliable connection provided by fiber optic adhesive, the data can be transmitted without any interruptions or delays.
- Increased reliability: IoT and smart devices must be reliable to function correctly. Fiber optic adhesive can improve the reliability of the devices by ensuring that the connection between the devices is secure and stable. This can lead to a reduction in downtime and maintenance costs.
- Enhanced security: Fiber optic cables are known for their high level of protection. They are difficult to hack or intercept, and fiber optic adhesive helps secure the connection between the devices. This can be particularly important for IoT and smart devices that contain sensitive information.
Fiber Optic Adhesive for Fiber Optic Sensing Applications
Here are some factors to consider when selecting an adhesive for fiber optic sensing applications:
- Refractive index: The adhesive’s refractive index should be similar to that of the fiber optic material. This will minimize the amount of light lost at the adhesive-fiber interface, which can affect measurement accuracy.
- Temperature stability: The adhesive should be able to maintain its mechanical and optical properties over a wide temperature range. This is particularly important for applications that involve high-temperature environments or temperature cycling.
- Chemical resistance: The adhesive should resist the chemicals and environmental factors it may be exposed to during the sensing application. This is important to prevent any degradation of the adhesive over time, which can affect the accuracy of the measurement.
- Curing time: The adhesive’s curing time should be appropriate for the application. Sometimes, a faster curing time may be necessary to minimize downtime or reduce processing time.
- Ease of use: The adhesive should be easy to apply and handle. This is important to minimize errors during the adhesive application process.
Some examples of commonly used adhesives for fiber optic sensing applications include UV-curable adhesives, epoxy-based adhesives, and cyanoacrylate-based adhesives. Ultimately, the selection of the best adhesive for a specific fiber optic sensing application will depend on the particular requirements of that application.
The Importance of Consistency in Fiber Optic Adhesive Manufacturing
Consistency is crucial in fiber optic adhesive manufacturing for several reasons:
- Quality Assurance: Fiber optic adhesive is critical in producing fiber optic cables. Any inconsistency in the manufacturing process can lead to variations in the quality of the final product, which can compromise the performance of the fiber optic cables.
- Performance: Fiber optic adhesive ensures that the optical fibers in a cable are securely held in place. The inconsistent adhesive application can result in the fibers shifting or becoming loose, affecting the cable’s overall performance.
- Cost: Inconsistent manufacturing processes can lead to wastage of materials, resulting in increased production costs. The inconsistent adhesive application can also lead to product failure, resulting in warranty claims and returns, further increasing costs.
- Reputation: Consistency is essential in building a reputable brand in the fiber optic industry. Companies that consistently produce high-quality products are likely to build a loyal customer base, while inconsistent manufacturers may need help to gain market share.
The Future of Fiber Optic Adhesive: Emerging Technologies and Applications
Fiber optic adhesive technology has advanced significantly in recent years, and it continues to be an essential component in the manufacturing of optical fiber cables. Emerging technologies and applications of fiber optic adhesive include the following:
- Nanoparticle-enhanced adhesive: One of the emerging technologies in the field of fiber optic adhesive is the use of nanoparticles to enhance the properties of the adhesive. Nanoparticles such as carbon nanotubes and graphene can be added to the adhesive to improve its mechanical strength, thermal stability, and electrical conductivity.
- UV-curable adhesive: Another emerging technology in the field of fiber optic adhesive is the use of UV-curable adhesive. This type of adhesive can be cured quickly using UV light, significantly reducing the manufacturing time of optical fiber cables.
- Low-temperature adhesive: Low-temperature adhesive is another emerging technology that has the potential to revolutionize the manufacturing of optical fiber cables. This type of adhesive can be cured at temperatures as low as -40°C, reducing energy consumption and improving the manufacturing process’s efficiency.
- Adhesive for harsh environments: There is a growing demand for fiber optic cables that can withstand harsh environments such as extreme temperatures, humidity, and exposure to chemicals. Adhesive manufacturers are developing new formulations that can withstand these harsh conditions, such as high-temperature epoxy and silicone adhesives.
- 3D printing of fiber optic components: 3D printing technology can revolutionize the manufacturing of fiber optic components. Adhesive manufacturers are developing new formulations that can be used in 3D printing to create customized fiber optic components quickly and efficiently.
- Medical applications: Fiber optic adhesive is also finding new applications in the medical field. For example, it can attach optical fibers to medical devices such as endoscopes and catheters.