Smart Card Chip Adhesive
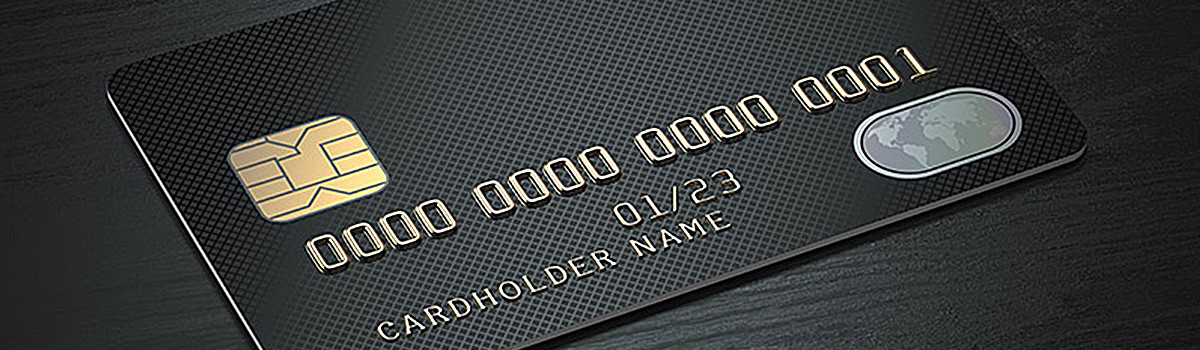
Smartcards are widely used in various applications, including banking, healthcare, transportation, and access control. The chips used in smartcards require a secure bond to ensure their stability and prevent unauthorized access to sensitive data. The suitable Adhesive can provide a reliable bond while ensuring the longevity of the smartcard. This article will explore the factors to consider while selecting the best Adhesive for smartcard chip manufacturing.
Importance of choosing the suitable Adhesive for smartcard chip manufacturing
Smart Cards have become ubiquitous in our daily lives and are used in credit cards, identification cards, access cards, and many other applications. The manufacturing of smartcards involves using different materials, including plastic, metal, and paper. These materials need to be bonded to form a solid structure, where adhesives come into play. The choice of adhesive is critical in smartcard chip manufacturing for several reasons:
- Ensuring reliable adhesion: The adhesive used in smartcard chip manufacturing must provide reliable adhesion between the different layers of the card. If the adhesion is not strong enough, the layers may separate, resulting in a defective card.
- Compatibility with the materials: The adhesive must be compatible with the materials used in the smartcard manufacturing process. The bond may react with the materials if it is inconsistent, causing damage or delamination.
- Chemical resistance: Smartcards are exposed to various chemicals during their lifespan, such as cleaning agents, oils, and solvents. The adhesive used in manufacturing must resist these chemicals to prevent degradation and delamination.
- Electrical conductivity: The adhesive used in smartcard chip manufacturing must have good electrical conductivity to allow for the proper functioning of the card.
- Temperature resistance: Smartcards may be exposed to various temperatures during their lifespan, from freezing to high temperatures. The adhesive used must withstand these temperature changes without degrading or delaminating.
- Compliance with regulations: The adhesive used in smartcard chip manufacturing must comply with various laws, such as RoHS, REACH, and FDA regulations, to ensure the safety of the users.
Factors to consider while selecting Adhesive for smartcard chip manufacturing
Smartcards are ubiquitous in various industries, including banking, healthcare, transportation, and security. The manufacturing of smartcards involves multiple steps, including attaching the chip module to the card’s surface using an adhesive. Selecting the suitable adhesive for smartcard chip manufacturing ensures the card’s reliability, durability, and security. Here are some factors to consider while choosing the adhesive:
- Compatibility: The adhesive must be compatible with the chip material and the card substrate. Any chemical reaction between the cement and the chip or substrate can affect the card’s performance and lifespan.
- Bond Strength: The adhesive must provide a robust and reliable bond between the chip and the card substrate. It must withstand the stresses of daily use, including bending, twisting, and abrasion.
- Adhesive Thickness: The adhesive’s thickness should be uniform and appropriate for the card’s design and application. Too thick adhesive can cause the chip to protrude from the card surface, while too thin adhesive can result in a weak bond.
- Temperature Resistance: Smartcards are exposed to various temperature conditions during their lifespan, such as high temperatures during card lamination or low temperatures during storage and transportation. The adhesive must withstand these temperature variations without losing its bond strength.
- Chemical Resistance: Smartcards can come in contact with various chemicals during their lifespan, such as solvents, oils, and cleaning agents. The adhesive must resist these chemicals to prevent the chip from delaminating from the card surface.
- Conductivity: The adhesive must not interfere with the chip’s electrical conductivity and should not cause any signal loss or interference.
- Environmental impact: The adhesive should comply with environmental regulations, and its disposal should not cause any harm to the environment.
Types of Adhesive for smartcard chip manufacturing
Smartcards are electronic payment cards that use an embedded microchip to store and process data. The manufacturing of smartcard chips requires adhesives to attach the chip to the card. There are different types of adhesives used in smartcard chip manufacturing, including:
- Epoxy Adhesives: Epoxy adhesives are widely used in smartcard chip manufacturing due to their excellent bonding strength, chemical resistance, and thermal stability. Depending on the specific formulation, epoxy adhesives can be cured at room temperature or elevated temperatures. They are typically applied in a liquid or paste form and then cured to form a complex, durable bond.
- Acrylic Adhesives: Acrylic adhesives are another adhesive used in smartcard chip manufacturing. They offer good bonding strength, excellent chemical resistance, and UV stability. Acrylic adhesives are typically applied in a liquid or paste form and then cured by UV light or heat exposure.
- Polyurethane Adhesives: Polyurethane adhesives are a type of adhesive that offers excellent flexibility and impact resistance. They are typically used in smartcard chip manufacturing applications that require a high degree of flexibility, such as when bonding chips to plastic substrates.
- Silicone Adhesives: Silicone adhesives are used in smartcard chip manufacturing when a high level of flexibility is required. They offer excellent temperature and chemical resistance, making them ideal for applications where the smartcard chip may be exposed to harsh environments.
- Pressure-Sensitive Adhesives: Pressure-sensitive adhesives (PSAs) are used in smartcard chip manufacturing when a strong, temporary bond is required. PSAs are typically applied in a tape form and can be easily removed without leaving residue. They are often used in the manufacturing of temporary smartcard chips.
Epoxy Adhesive for smartcard chip manufacturing
Epoxy adhesives are widely used in the manufacturing of smartcard chips due to their excellent bonding strength, chemical resistance, and thermal stability. They typically attach the microchip to the card body, providing a secure and durable bond.
Epoxy adhesives consist of two parts: a resin and a hardener. A chemical reaction occurs when these two parts are mixed, resulting in a cured, hard adhesive. The curing time depends on the specific formulation of the epoxy adhesive and can range from a few minutes to several hours.
One of the primary benefits of epoxy adhesives is their high bonding strength. They can bond to various materials, including metals, plastics, and ceramics, making them ideal for smartcard chip manufacturing. Epoxy adhesives also offer excellent chemical resistance, essential in applications where the smart card may be exposed to harsh environments or chemicals.
Epoxy adhesives also offer excellent thermal stability, which can withstand high temperatures without losing bonding strength. This is particularly important in manufacturing, as the chips and cards are often subjected to high temperatures during the bonding process.
Another advantage of epoxy adhesives is their versatility. They can be formulated to have different properties, such as low viscosity for easy dispensing or high viscosity for gap filling. Depending on the specific application requirements, they can also be prepared to cure at room temperature or elevated temperatures.
However, there are also some limitations to epoxy adhesives. They can be brittle and may crack under certain conditions, such as extreme temperature changes or vibration. Additionally, some epoxy adhesives may turn yellow when exposed to UV light over time.
Acrylic Adhesive for smartcard chip manufacturing
Acrylic adhesives are widely used in intelligent card chip manufacturing due to their excellent bonding properties, durability, and resistance to various environmental factors. They commonly assemble smart cards, particularly in bonding the chip module to the plastic card body.
Smart card manufacturing involves several stages: card body production, module assembly, and personalization. Acrylic adhesives are primarily used in the module assembly stage, where the chip module is bonded to the card body, the adhesive is applied to the module, and then the module is aligned and pressed onto the card body.
Acrylic adhesives are preferred for smart card manufacturing because of their excellent bonding properties. They can bond with various materials, including plastic, metal, and glass. They offer high initial tack, meaning the adhesive will connect immediately after application. They also provide a robust and durable bond, which is essential for the longevity of the smart card.
Another advantage of acrylic adhesives is their resistance to environmental factors such as temperature, humidity, and UV radiation. This makes them suitable for use in smart cards exposed to various environmental conditions. They also offer good chemical resistance, meaning they will not degrade or lose their adhesive properties when exposed to chemicals.
Acrylic adhesives are also easy to apply and cure quickly. They can be applied using automated dispensing equipment, which ensures consistent application and reduces the likelihood of human error. They also fix quickly, which means that the manufacturing process can proceed faster.
Polyurethane Adhesive for smartcard chip manufacturing
Polyurethane adhesives are a popular choice for intelligent card chip manufacturing due to their excellent bonding properties, flexibility, and resistance to environmental factors. They are commonly used in the assembly of smart cards, particularly in bonding the chip module onto the plastic card body.
Smart card manufacturing involves several stages: card body production, module assembly, and personalization. Polyurethane adhesives are primarily used in the module assembly stage, where the chip module is bonded to the card body, the adhesive is applied to the module, and then the module is aligned and pressed onto the card body.
Polyurethane adhesives are preferred for intelligent card manufacturing because they offer excellent bonding strength and flexibility. They can bond with various materials, including plastic, metal, and glass, and they provide a robust and durable bond that can withstand stress and strain without cracking or breaking. This is particularly important for smart cards exposed to frequent bending and flexing.
Another advantage of polyurethane adhesives is their resistance to environmental factors such as temperature, humidity, and UV radiation. This makes them suitable for smart cards exposed to various environmental conditions. They also offer good chemical resistance, meaning they will not degrade or lose their adhesive properties when exposed to chemicals.
Polyurethane adhesives are also easy to apply and cure quickly. They can be applied using automated dispensing equipment, which ensures consistent application and reduces the likelihood of human error. They also heal soon so that the manufacturing process can proceed faster.
Silicone Adhesive for smartcard chip manufacturing
Silicone adhesives play a crucial role in smart card chip manufacturing due to their unique properties that make them well-suited for this application. They offer excellent bonding strength, thermal stability, and protection against moisture and environmental factors. Silicone adhesives are commonly used to assemble smart cards, particularly in bonding the chip module onto the plastic card body.
Smart card manufacturing involves various stages, including card body production, module assembly, and personalization. Silicone adhesives are primarily utilized in the module assembly stage. The bond is applied to the chip module, which is then aligned and pressed onto the card body.
Silicone adhesives are highly valued for smart card manufacturing because they provide reliable bonding strength. They form strong, durable bonds with different materials like plastic, metal, and glass. The adhesive ensures a secure attachment between the chip module and the card body, even under demanding conditions like frequent flexing or bending.
Thermal stability is another critical advantage of silicone adhesives. Smart cards may encounter varying temperatures during their lifespan, and silicone adhesives can withstand these fluctuations. They exhibit good resistance to high temperatures, ensuring the adhesive remains intact and does not degrade over time.
Moisture and environmental protection are critical factors in smart card manufacturing, as the cards are exposed to various conditions. Silicone adhesives offer excellent resistance to moisture, humidity, and other environmental factors. This protects the internal chip module from potential damage, ensuring the long-term reliability of the smart card.
Furthermore, silicone adhesives have good chemical resistance, which prevents degradation or loss of adhesive properties when exposed to chemicals. This is beneficial during manufacturing, as the adhesives remain stable when in contact with cleaning agents or other substances used in the assembly.
Silicone adhesives are easy to apply and cure efficiently, and they can be applied using automated dispensing equipment, ensuring precise and consistent application. Moreover, silicone adhesives have relatively fast curing times, allowing the manufacturing process to proceed efficiently.
UV Curable Adhesive for smartcard chip manufacturing
UV-curable adhesives are famous for smartcard chip manufacturing due to their quick curing time, ease of use, and strong bonding properties. These adhesives consist of monomers and oligomers activated by ultraviolet light to initiate polymerization and create a crosslinked network, resulting in a durable bond.
Smart Card chips, also known as integrated circuits or ICs, are used in various applications, including banking, identification, and security systems. The adhesive used in smartcard chip manufacturing must meet several critical requirements, including excellent adhesion, low shrinkage, and high thermal stability.
UV-curable adhesives have several advantages over other adhesive types. They offer a quick curing time, typically in just a few seconds, which is critical in high-volume manufacturing settings where time is of the essence. They also have a long shelf life and do not require special storage conditions, making them convenient and easy to use.
One of the critical benefits of UV-curable adhesives is their ability to form strong and durable bonds with various substrates, including metals, plastics, and ceramics. This is especially important in smartcard chip manufacturing, where the adhesive must bond the chip to the substrate with high reliability and accuracy.
UV-curable adhesives are also resistant to heat and moisture, which is critical in smartcard applications that may be exposed to harsh environmental conditions. The bond must maintain strength and stability under extreme conditions, such as exposure to high temperatures, humidity, or chemicals.
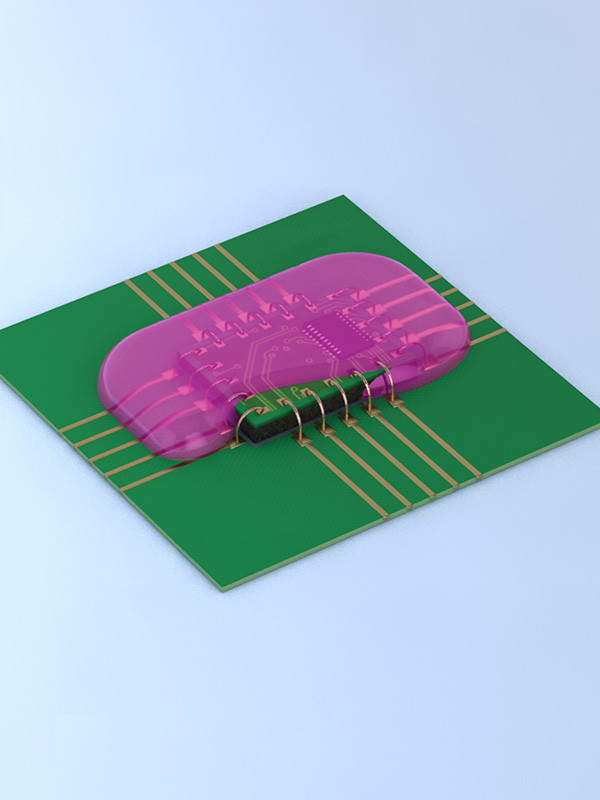
UV-curable adhesives are an excellent choice for smartcard chip manufacturing due to their quick curing time, ease of use, and strong bonding properties. They offer excellent adhesion, low shrinkage, and high thermal stability, making them ideal for high-volume manufacturing. With their exceptional performance and durability, UV-curable adhesives are a reliable and efficient choice for smartcard chip manufacturing applications.
Conductive Adhesive for smartcard chip manufacturing
Conductive adhesives are a critical component in manufacturing smartcard chips, as they provide a solid and reliable electrical connection between the chip and the substrate. These adhesives consist of a mixture of conductive particles and a polymer matrix and are designed to provide a highly conductive path while also providing adhesion to the substrate.
Smartcard chips are used in various applications, including banking, security, and identification. In these applications, the smartcard chip must provide a secure and reliable connection between the card and the reader, and the conductive adhesive plays a critical role in this process.
The conductive particles used in these adhesives are typically silver, copper, or nickel, as they provide high electrical conductivity. The polymer matrix is designed to hold the conductive particles in place while providing adhesion to the substrate. The conductive particles form a conductive pathway between the chip and the substrate, allowing electrical signals to be transmitted with high accuracy and reliability.
Conductive adhesives offer several advantages over traditional soldering techniques. They are easier to use and do not require the high temperatures and specialized equipment needed for soldering. They are also more flexible than solder, allowing for greater flexibility in the design and layout of the smartcard chip.
Conductive adhesives must meet several critical requirements to be suitable for smartcard chip manufacturing. They must have high electrical conductivity, low resistance, and high thermal stability to withstand the harsh environmental conditions that smartcards may be exposed to. They must also be compatible with many substrates and have good adhesion properties to ensure a reliable bond between the chip and the substrate.
Overall, conductive adhesives are critical in manufacturing smartcard chips, providing a solid and reliable electrical connection between the chip and the substrate. With their high electrical conductivity, low resistance, and high thermal stability, conductive adhesives are an ideal choice for smartcard chip manufacturing applications, offering a reliable and efficient solution for secure and accurate data transmission.
Thermal Conductive Adhesive for smartcard chip manufacturing
Thermal conductive adhesive plays a crucial role in the manufacturing of smartcard chips. Smartcards are widely used in various industries for secure data storage and communication. The chip within a smartcard generates heat during operation, and efficient heat dissipation is essential to maintain its performance and reliability. Thermal conductive adhesive provides a solution for effective heat transfer in smartcard chip manufacturing.
Thermal conductive adhesives are formulated to have excellent thermal conductivity properties while maintaining adhesive strength. These adhesives typically comprise a polymer matrix filled with thermally conductive particles, such as ceramics or metal oxides. The particles facilitate heat transfer by creating a conductive path within the adhesive.
During smartcard manufacturing, the thermal conductive adhesive is applied between the chip and the substrate or carrier material. The adhesive is a thermal interface material, ensuring optimal heat transfer between the chip and the surrounding environment. Filling microscopic gaps and irregularities enhances the contact between the chip and the substrate, minimizing thermal resistance.
Thermal conductive adhesives offer several advantages in smartcard chip manufacturing. Firstly, they provide a reliable and long-lasting bond between the chip and the substrate, ensuring mechanical stability. This is crucial as smartcards are subjected to various stresses and environmental conditions. Additionally, the adhesive prevents the ingress of moisture and contaminants, protecting the chip from potential damage.
Furthermore, thermally conductive adhesives exhibit high thermal conductivity, enabling efficient heat dissipation from the chip. By minimizing temperature rise and hot spots, they enhance the overall performance and longevity of the smartcard. The adhesive’s thermal properties also aid in maintaining consistent operating temperatures, preventing overheating and potential malfunction.
Manufacturers consider various factors when selecting a thermally conductive adhesive for smartcard chip manufacturing. These include the adhesive’s thermal conductivity, viscosity, curing time, and compatibility with the chip and substrate materials. Bonds with lower density ensure more accessible application and better coverage, while a suitable curing time allows for efficient production processes.
Dielectric Adhesive for smartcard chip manufacturing
The dielectric adhesive is a critical component in the manufacturing of smartcard chips. Smart Cards are widely used for secure data storage and communication, and a reliable and efficient bonding mechanism is necessary to maintain their performance and reliability. Dielectric adhesive provides a solution for effectively bonding the chip to the substrate or carrier material while offering electrical insulation.
Dielectric adhesives are formulated to have excellent dielectric properties while maintaining adhesive strength. These adhesives typically comprise a polymer matrix filled with insulating particles, such as ceramics or glass. The particles facilitate the electrical insulation by creating a barrier between the chip and the substrate.
The dielectric adhesive is applied between the chip and the substrate during the smartcard manufacturing process. The adhesive acts as a bonding agent, ensuring optimal electrical contact between the chip and the surrounding environment. Filling microscopic gaps and irregularities enhances the connection between the chip and the substrate, minimizing electrical resistance.
Dielectric adhesives offer several advantages in smartcard chip manufacturing. Firstly, they provide a reliable and long-lasting bond between the chip and the substrate, ensuring mechanical stability. This is crucial as smartcards are subjected to various stresses and environmental conditions. Additionally, the adhesive prevents the ingress of moisture and contaminants, protecting the chip from potential damage.
Furthermore, dielectric adhesives exhibit high dielectric strength, enabling efficient electrical insulation between the chip and the substrate. By minimizing leakage and reducing electrical noise, they enhance the overall performance and longevity of the smartcard. The adhesive’s dielectric properties also aid in maintaining consistent electrical characteristics, preventing potential malfunction.
Manufacturers consider various factors when selecting a dielectric adhesive for smartcard chip manufacturing. These include the adhesive’s dielectric strength, viscosity, curing time, and chip and substrate materials compatibility. Bonds with lower density ensure more accessible application and better coverage, while a suitable curing time allows for efficient production processes.
Resistance to temperature and humidity
Smart card chips are commonly used in various applications, such as payment cards, identification cards, and access control systems. To ensure the longevity and reliability of smart card chips, it is essential to use adhesives with high resistance to temperature and humidity.
Adhesives used for smart card chips should resist high temperatures as the chip may be exposed to extreme temperatures during manufacturing and throughout its lifespan. Adhesives that can withstand high temperatures are less likely to degrade or lose their adhesive properties, ensuring the long-term reliability of the smart card chip.
In addition to high-temperature resistance, adhesives for intelligent card chips should also have good resistance to humidity. Smart card chips are often exposed to varying humidity levels, which can cause moisture to penetrate the chip and damage its internal components. Adhesives resistant to humidity can help prevent this, ensuring the smart card chip remains functional and reliable.
To ensure the best resistance to temperature and humidity, choosing adhesives specifically designed and tested for use with intelligent card chips is essential. Manufacturers of wise card chips may guide the best adhesives to use, and it is important to follow their recommendations to ensure the best performance and reliability of the smart card chip.
Resistance to chemicals
Intelligent card chips are vital components in various applications, and they must possess a range of desirable properties to ensure their longevity and functionality. In addition to factors like temperature and humidity resistance, chemical resistance plays a pivotal role in maintaining the integrity of smart card chip adhesives.
Throughout their lifespan, intelligent card chips may come into contact with various chemicals, including cleaning agents, solvents, oils, and fuels. These substances can cause degradation or loss of adhesive properties if the adhesives are not resistant. Consequently, the failure of the smart card chip may ensue, compromising its overall performance.
Chemical resistance is a fundamental requirement for adhesives used in intelligent card chips, and it refers to the adhesive’s ability to withstand exposure to various chemicals without being affected or degraded. The adhesive can maintain its structural integrity by possessing good chemical resistance, ensuring that the smart card chip remains securely attached to its substrate.
To guarantee the adhesive’s chemical resistance, it is crucial to consider the specific chemicals to which the chip may be exposed. Each chemical has unique properties that can interact with adhesives differently. Therefore, it is imperative to test the adhesive against these chemicals to evaluate its ability to withstand exposure without degradation.
In the realm of intelligent card chip manufacturing, the guidance provided by chip manufacturers is invaluable. These manufacturers possess extensive knowledge about the behavior of their chips and the chemicals they may encounter in their respective applications. Based on this expertise, considering the chemicals involved, they can recommend the most suitable adhesives. Adhering to their recommendations ensures optimal performance, reliability, and longevity of the smart card chip.
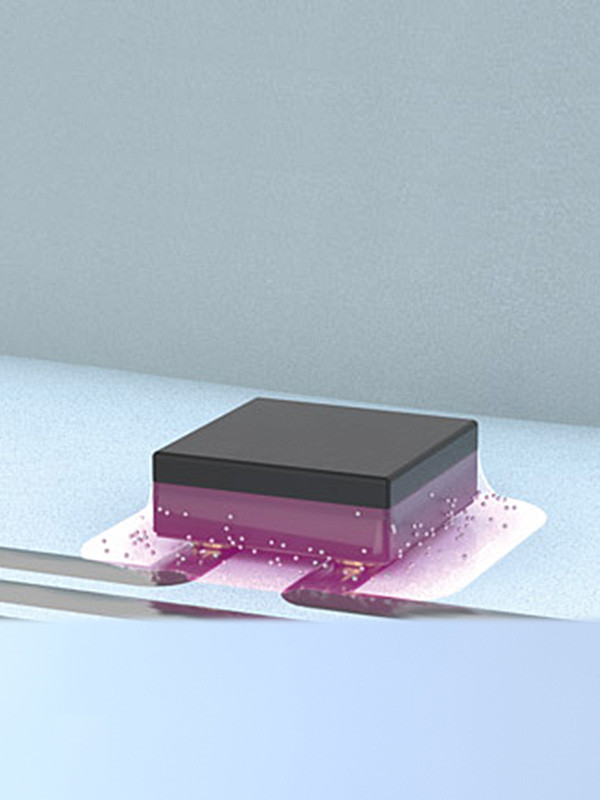
Compatibility with chip materials
The compatibility of adhesives with the materials used in smart card chips is crucial when selecting adhesives. If an adhesive is not compatible with the chip materials, it may damage or damage the chip, which could lead to failure.
Smart card chips are typically made from semiconductor materials, like silicon, and may contain metallic components such as gold or copper. Therefore, the adhesive used for smart card chips should be compatible with these materials and not cause any corrosion or other damage.
To ensure compatibility with chip materials, it is necessary to choose adhesives that are specifically designed and tested for use with intelligent card chips. Manufacturers of smart card chips can guide the best adhesives to use based on the specific materials used in their chips. It is essential to follow their recommendations to ensure the optimal performance and reliability of the smart card chip.
In addition to compatibility with chip materials, it is also crucial to consider the compatibility of adhesives with the substrate to which the smart card chip is attached. The substrate can be made of materials like PVC or polycarbonate, and the adhesive should be compatible with these materials to ensure a secure bond.
Choosing the suitable adhesive is essential in ensuring the durability and longevity of smart card chips. Therefore, it is crucial to consider the compatibility of bonds with both the chip materials and the substrate. By choosing adhesives specifically designed and tested for use with intelligent card chips, you can ensure that the adhesive will provide a secure bond without causing any damage or degradation to the chip or substrate.
Shelf life and storage conditions
Shelf life refers to when a product can maintain its quality and safety when stored properly. The shelf life of a product depends on various factors, including the nature of the product, the processing and packaging methods, and the storage conditions. Proper storage conditions can help extend the shelf life of products, while inadequate storage conditions can lead to shorter shelf life or even spoilage.
Temperature is one of the most critical factors affecting the shelf life of products. Most products have an optimal storage temperature range, and deviations from this range can cause spoilage. For example, perishable foods such as dairy, meat, and fish should be stored below 40°F (4°C) to prevent bacterial growth and spoilage. On the other hand, some products, such as canned foods and dry goods, can be stored at room temperature, but high temperatures can cause them to deteriorate and lose quality.
Humidity is another factor that can affect the shelf life of products. High humidity can promote mold and bacteria growth, leading to spoilage. Therefore, it is essential to store products in a dry environment and avoid exposing them to moisture.
Light can also affect the shelf life of some products. For example, exposure to sunlight can cause fats and oils to become rancid, and it can also cause discoloration and nutrient loss in some foods. Therefore, light-sensitive products should be stored in opaque containers or dark environments.
Oxygen is another factor that can affect the shelf life of products. Oxygen can cause oxidative rancidity in products that contain fats and oils, leading to a shorter shelf life. Therefore, storing products in airtight containers or vacuum-sealed packaging is essential to prevent oxygen exposure.
Ease of application and curing time
Smartcards are electronic devices for secure identification, payment, and data storage applications. These cards often contain a small chip that is embedded within the card. An adhesive is used during the manufacturing process to ensure that the chip is securely attached to the card. The adhesive must be easy to apply and have a reasonable curing time to ensure that the production process is efficient and cost-effective.
Ease of Application:
Smartcard chip adhesives are typically applied using a dispensing system that delivers a precise amount of adhesive onto the chip. The adhesive should have a low viscosity to allow it to flow easily and fill gaps between the chip and the card. Additionally, the adhesive should have a long pot life to allow sufficient time for the dispensing process, and it should only cure slowly, which could cause the dispensing system to become clogged.
One of the most commonly used adhesives for smartcard chips is epoxy. Epoxy adhesives have a low viscosity and are easy to dispense, and they are also highly resistant to chemicals, heat, and moisture, making them ideal for smartcard applications.
Curing Time:
Curing time refers to the time it takes for the adhesive to reach its full strength and for the card to be ready for further processing. The curing time for smartcard chip adhesives is typically short, as manufacturers need to produce cards quickly and efficiently.
Epoxy adhesives typically cure within 24 hours, but some formulations can cure in a few minutes. The curing time depends on various factors, including the temperature, humidity, and the thickness of the adhesive layer. Manufacturers must carefully control these factors to ensure that the adhesive cures correctly and that the chip is securely attached to the card.
Other factors that can affect the curing time of smartcard chip adhesives include the type of substrate used, the amount of adhesive applied, and the curing method. For example, UV-curable adhesives can cure in seconds when exposed to UV light, making them ideal for high-speed manufacturing.
Precautions to take while applying Adhesive to smartcard chips
Smartcards are widely used in various applications, including banking, identification, and access control systems. These cards contain a small chip embedded within the card and must be securely attached to the card to ensure reliable performance. Adhesives are commonly used to attach the chip to the card, but certain precautions must be taken to ensure that the adhesive is applied correctly and does not damage the chip or the card.
Here are some precautions to take while applying adhesive to smartcard chips:
- Avoid Over-application:
Applying too much adhesive can cause it to flow onto the chip’s surface, potentially damaging the delicate electronics. It can also cause the chip to shift during curing, leading to misalignment or detachment. To prevent this, use a precise dispensing system to apply the adhesive in a controlled manner and ensure that only the required amount of adhesive is applied.
- Avoid Under-application:
Under-application of adhesive can lead to poor adhesion between the chip and the card, which can cause the chip to become dislodged over time. To prevent this, ensure the adhesive layer is uniform and covers the entire chip surface.
- Proper Cleaning:
Before applying adhesive, ensure that the chip and the card surfaces are thoroughly cleaned to remove dust, debris, or contaminants. Any residue left on the surface can affect the adhesion and lead to poor chip performance.
- Temperature Control:
Adhesive curing can be sensitive to temperature fluctuations, and high temperatures can cause the adhesive to cure too quickly, leading to inadequate bonding. It can also cause the chip to malfunction due to heat damage. Ensure that the manufacturing environment is adequately temperature-controlled to prevent any issues.
- Proper Handling:
Smartcard chips are delicate and can be easily damaged by rough handling. Use a gentle touch when handling the chips to avoid damage and ensure the chip is aligned correctly during adhesive application.
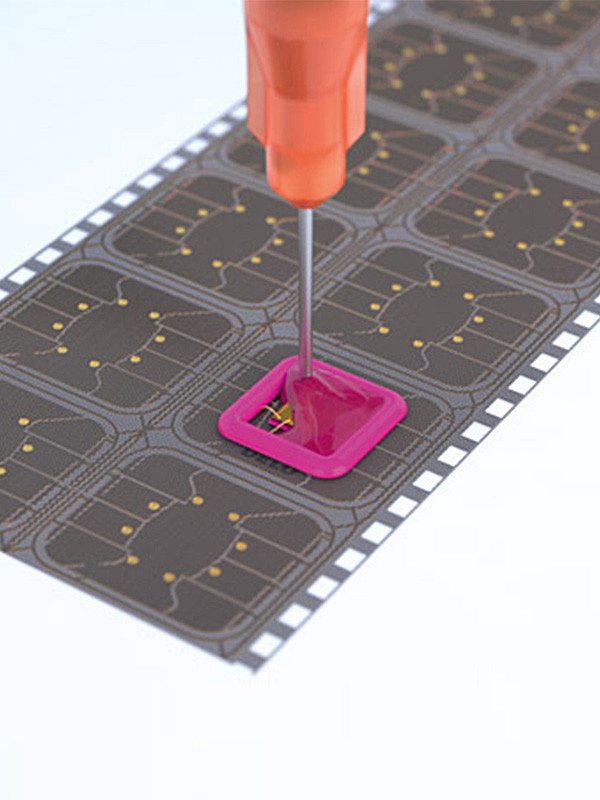
Common mistakes to avoid while applying Adhesive to smartcard chips
Smartcard chips are sensitive electronic devices requiring careful handling during adhesive application. The adhesive must be carefully applied to avoid common mistakes that can result in poor adhesion, misalignment, or even damage to the chip. Here are some common mistakes to avoid while using adhesive on smartcard chips:
- Using too much adhesive:
Over-application of adhesive is a common mistake that can lead to several issues. It can cause the adhesive to flow onto the chip’s surface, damaging the delicate electronics. It can also cause the chip to shift during curing, leading to misalignment or detachment. To prevent over-application, use a precise dispensing system and apply only the required amount of adhesive.
- Applying too little adhesive:
Under-application of adhesive can also cause issues, as it can lead to poor adhesion between the chip and the card, which can cause the chip to become dislodged over time. Ensure that the adhesive layer is uniform and covers the entire chip surface.
- Not cleaning the chip surface:
Before applying adhesive, it is essential to thoroughly clean the chip surface to remove any dust, debris, or contaminants. Any residue left on the surface can affect the adhesion and lead to poor chip performance.
- Not aligning the chip correctly:
Alignment is crucial when applying adhesive to smartcard chips. Failure to align the chip correctly can cause the chip to shift during the curing process, leading to misalignment or even detachment. Ensure that the chip is aligned correctly before applying the adhesive.
- Not controlling the curing conditions:
The curing conditions, including temperature and humidity, can affect the adhesion of the adhesive. Failure to control these conditions can result in inadequate bonding and poor chip performance. Ensure that the manufacturing environment is properly temperature and humidity controlled.
Benefits of using the suitable Adhesive for smartcard chip manufacturing
Adhesives play a critical role in manufacturing smartcard chips, as they attach the chip to the card and provide a secure, reliable bond. The selection of a suitable adhesive for smartcard chip manufacturing is essential as it can significantly impact the overall performance and reliability of the smartcard. Here are some benefits of using the suitable glue for smartcard chip manufacturing:
- Enhanced reliability:
Suitable adhesives can enhance the reliability of intelligent card chips by providing a robust and durable bond between the chip and the card. This can help to prevent issues such as chip detachment or misalignment, which can result in poor chip performance or even complete failure.
- Improved security:
Smartcards are often used in applications that require a high level of security, such as banking or identification systems. Suitable adhesives can help ensure the chip is securely attached to the card, reducing the risk of tampering or fraud.
- Increased durability:
Smartcards are often subjected to harsh environmental conditions, such as temperature and humidity fluctuations, and physical stress, such as bending or twisting. Suitable adhesives can increase the durability of the smartcard by providing a robust and flexible bond that can withstand these conditions.
- Enhanced manufacturing efficiency:
Suitable adhesives can enhance manufacturing efficiency by providing a fast, reliable bonding solution. This can reduce manufacturing time and costs while ensuring consistent, high-quality bond performance.
- Improved customer satisfaction:
Smartcard users expect their cards to be reliable and durable. Using a suitable adhesive in smartcard chip manufacturing can help to ensure that the cards meet these expectations, improving customer satisfaction and loyalty.
Choosing the Best Adhesive for Smart Card Chip Manufacturing
When it comes to smartcard chip manufacturing, choosing the suitable adhesive is crucial. The glue is critical in ensuring that the chip is securely bonded to the card body and that the electrical contacts between the chip and the card are reliable and durable. Several factors to consider when selecting an adhesive for smartcard chip manufacturing include the adhesive’s strength, viscosity, curing time, and compatibility with the materials used in the card and chip.
One important consideration when selecting an adhesive is its strength. The adhesive must securely bond the chip to the card body and withstand the stresses the card may face during everyday use. The adhesive should maintain its strength over time, even when exposed to environmental factors such as heat, humidity, and chemical exposure.
Viscosity is another essential factor to consider. The adhesive must be able to flow into the narrow gaps between the chip and the card body to ensure a secure bond. However, the glue should be thick enough to run or drip, which can lead to uneven bonding and poor electrical contact between the chip and the card.
Curing time is also essential. The adhesive should cure quickly enough to ensure that the manufacturing process can be completed efficiently, but not so quickly that there needs to be more time to adjust the chip’s position before the adhesive sets. Additionally, the adhesive should cure completely to ensure maximum strength and durability.
Finally, compatibility with the materials used in the card and chip is critical. The adhesive must bond well with the card body and chip material to ensure a solid and durable bond. Additionally, the adhesive should not degrade or damage the materials it is bonding to over time.
In general, two types of adhesives are used in smartcard chip manufacturing: conductive and non-conductive. Conductive adhesives create the electrical contacts between the chip and the card body, while non-conductive adhesives bond the chip to the card body. Conductive adhesives typically consist of silver or gold particles suspended in a polymer matrix, while non-conductive adhesives are typically epoxy-based.
Overall, the best adhesive for smartcard chip manufacturing will depend on the application’s specific requirements. Factors such as the materials used in the card and chip, the manufacturing process, and the expected environmental conditions will all play a role in determining the optimal adhesive for the job. Working with an experienced supplier and testing different adhesive options can help ensure that the final product meets the required performance and reliability standards.
Conclusion
Selecting the suitable Adhesive for smartcard chip manufacturing is crucial to ensure the longevity and security of the smartcard. Various factors such as resistance to temperature and humidity, chemicals, and compatibility with chip materials should be considered while choosing the best Adhesive for smartcard manufacturing. The suitable Adhesive can provide a reliable bond while ensuring the chip remains stable and secure. Proper precautions must be taken while applying Adhesive to smartcard chips, and common mistakes should be avoided to ensure optimal results. The suitable Adhesive is a crucial component of a secure smartcard manufacturing process, and selecting the best one can provide long-term benefits.