Panel Bonding Adhesive
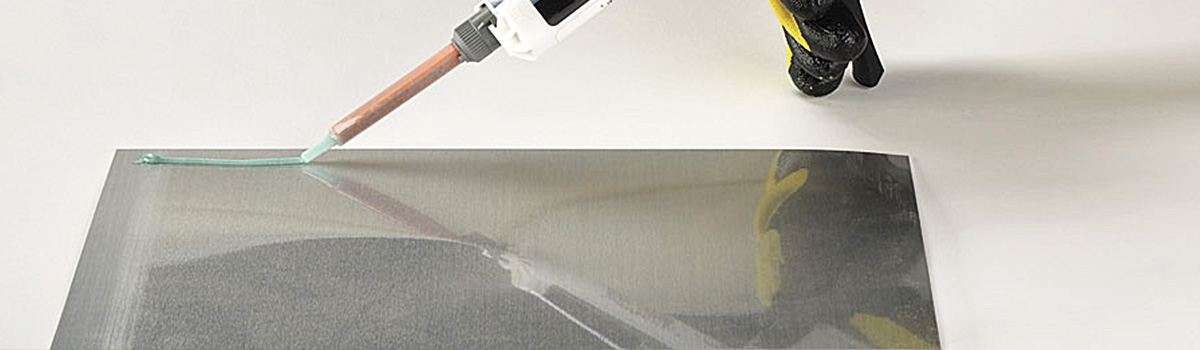
Panel bonding adhesives are high-strength adhesives for bonding metal panels, plastic panels, and other materials. They are commonly used in the automotive industry for repairing damaged panels and replacing rusted or damaged body parts. Panel bonding adhesives offer several advantages over traditional welding techniques, such as a stronger bond, reduced heat distortion, and improved corrosion protection. This guide will explore the different types of panel bonding adhesives, their applications, benefits, and how to use them effectively.
What are Panel Bonding Adhesives?
Panel bonding adhesives are high-strength adhesives for bonding large structural panels in automotive, aerospace, and industrial applications. These adhesives offer several advantages over traditional welding and mechanical fastening techniques, including reduced weight, corrosion resistance, and aesthetics. Panel bonding adhesives are typically two-part epoxies consisting of a resin and a hardener mixed together before application.
The mixed adhesive is then applied to the surfaces to be bonded and allowed to cure. Once cured, the bond created by panel-bonding adhesives is powerful and durable, often surpassing the strength of the related materials. Panel bonding adhesives are ideal for applications where weight reduction and structural integrity are critical, such as aerospace and automotive industries. They are also commonly used in industrial applications for bonding large panels and structures. Overall, panel bonding adhesives offer a versatile and reliable solution for connecting large panels in various applications.
Types of Panel Bonding Adhesives
Several panel bonding adhesives are available today, each with unique properties and benefits. Some of the most common types of panel bonding adhesives include:
- Two-part epoxies: These adhesives are the most widely used type of panel bonding glue and consist of a resin and a hardener mixed together just before application. Two-part epoxies offer excellent strength, durability, and resistance to chemicals and environmental factors.
- Urethane adhesives:Urethane adhesives are another popular panel bonding adhesive with high strength and flexibility. They are often used in automotive applications because they absorb vibration and shock.
- Acrylic adhesives:Acrylic adhesives are known for their excellent bonding strength, resistance to weathering and aging, and ability to bond dissimilar materials. They are often used in aerospace and industrial applications.
- Structural adhesives: Structural adhesives are designed for high-stress applications and offer excellent strength and durability. They can bond with various materials, including metals, plastics, and composites.
- Hybrid adhesives: Hybrid adhesives combine two or more types of bonds, offering the benefits of each type in a single adhesive. They are often used in applications where a combination of strength, flexibility, and resistance to environmental factors is required.
When selecting a panel bonding adhesive, it’s essential to consider the specific application requirements, including the materials being bonded, the stresses and forces involved, and the environmental conditions the bond will be subjected. Choosing the correct type of panel bonding adhesive for the job can ensure a robust and reliable bond that will provide long-lasting performance.
Epoxy Panel Bonding Adhesives
Epoxy panel bonding adhesives are among the most popular types in various applications. They are two-part adhesives consisting of a resin and a hardener mixed together before application. Here are some of the key benefits of using epoxy panel bonding adhesives:
- High strength: Epoxy panel bonding adhesives offer excellent bonding strength and can often create a stronger bond than the materials being bonded.
- Durability: Epoxy panel bonding adhesives are highly resistant to environmental factors such as moisture, chemicals, and temperature fluctuations, making them a reliable option for long-term bonding applications.
- Versatility: Epoxy panel bonding adhesives can bond various materials, including metals, plastics, and composites.
- Easy to use:Epoxy panel bonding adhesives are easy to apply and cure quickly, making them a convenient option for bonding large panels and structures.
- Aesthetic appeal: Epoxy panel bonding adhesives can create a clean, seamless bond between panels, improving the overall appearance of the finished product.
However, there are also some potential drawbacks to using epoxy panel bonding adhesives, including:
- Limited flexibility:Epoxy panel bonding adhesives can be brittle and have limited flexibility, which can be a concern in applications where the bonded materials are subjected to vibration or impact.
- Longer cure times: Epoxy panel bonding adhesives can take longer to cure than other bonds, which can be a concern in applications requiring fast cure times.
Overall, epoxy panel bonding adhesives offer a reliable and versatile solution for bonding large panels and structures in various applications. By carefully considering the specific application requirements and selecting the right epoxy panel connecting adhesive, you can ensure a solid and durable bond that will provide long-lasting performance.
Polyurethane Panel Bonding Adhesives
Polyurethane panel bonding adhesives are another popular type of panel bonding adhesive used in various applications. Here are some of the key benefits of using polyurethane panel bonding adhesives:
- High strength: Polyurethane panel bonding adhesives offer excellent bonding strength, often exceeding the power of the bonded materials.
- Flexibility:Polyurethane panel bonding adhesives are known for their flexibility, making them ideal for bonding materials subject to vibration, movement, or expansion and contraction.
- Resistance to environmental factors: Polyurethane panel bonding adhesives are highly resistant to environmental factors such as moisture, chemicals, and temperature fluctuations, making them a reliable option for long-term bonding applications.
- Versatility:Polyurethane panel bonding adhesives can bond various materials, including metals, plastics, and composites.
- Fast cure times: Polyurethane panel bonding adhesives cure quickly, making them a convenient option for bonding large panels and structures.
However, there are also some potential drawbacks to using polyurethane panel bonding adhesives, including:
- Poor aesthetic appearance: Polyurethane panel bonding adhesives can be difficult to sand and finish, leading to a less-than-ideal formation.
- Strong odor: Polyurethane panel bonding adhesives can have a strong smell, which may be a concern in some applications.
Polyurethane panel bonding adhesives offer a strong and flexible solution for bonding large panels and structures in various applications. By carefully considering the specific application requirements and selecting the appropriate polyurethane panel bonding adhesive, you can ensure a strong and durable bond that will provide long-lasting performance.
Acrylic Panel Bonding Adhesives
Acrylic panel bonding adhesives are another popular adhesive used in various applications. Here are some of the key benefits of using acrylic panel bonding adhesives:
- Excellent aesthetic appearance:Acrylic panel bonding adhesives create a seamless, virtually invisible bond ideal for applications where appearance is essential.
- Fast cure times:Acrylic panel bonding adhesives cure quickly, making them a convenient option for bonding large panels and structures.
- Resistance to environmental factors:Acrylic panel bonding adhesives are highly resistant to environmental factors such as moisture, chemicals, and temperature fluctuations, making them a reliable option for long-term bonding applications.
- Versatility:Acrylic panel bonding adhesives can bond various materials, including metals, plastics, and composites.
- High strength:Acrylic panel bonding adhesives offer excellent bonding strength, often exceeding the power of the bonded materials.
However, there are also some potential drawbacks to using acrylic panel bonding adhesives, including:
- Limited flexibility:Acrylic panel bonding adhesives can be brittle and have limited flexibility, which can be a concern in applications where the bonded materials are subjected to vibration or impact.
- Surface preparation:Acrylic panel bonding adhesives require a clean and properly prepared surface for optimal bonding performance.
Acrylic panel bonding adhesives offer a reliable and aesthetically appealing solution for bonding large panels and structures in various applications. By carefully considering the specific application requirements and selecting the appropriate acrylic panel bonding adhesive, you can ensure a strong and durable bond that will provide long-lasting performance.
Hybrid Panel Bonding Adhesives
Hybrid panel bonding adhesives are a type of adhesive that combines the properties of both polyurethane and silicone adhesives. These adhesives offer many benefits, making them an excellent choice for bonding various materials. Some of the key advantages of hybrid panel bonding adhesives include the following:
- Excellent adhesion to multiple substrates, including metals, plastics, and composites.
- High strength and durability, providing long-lasting bond performance in various applications.
- Resistance to water, chemicals, and temperature extremes makes them ideal for harsh environments.
- Fast curing times allow for quick assembly and production processes.
- Reduced noise and vibration transmission, improving overall product performance and user experience.
Hybrid panel bonding adhesives are versatile and reliable for bonding materials in various applications.
Benefits of Using Panel Bonding Adhesives
Panel bonding adhesives offer various benefits for various industries and applications. Some of the key advantages of using panel bonding adhesives include the following:
- Solid and durable bonds:Panel bonding adhesives provide a reliable and durable bond between two surfaces, which is crucial in many applications, such as the automotive and aerospace industries, where safety is a top priority.
- Enhanced aesthetics:Panel bonding adhesives create a smooth and seamless finish on the bonded surfaces, eliminating the need for rivets, screws, and other fasteners that can detract from the overall appearance of the final product.
- Increased productivity: Using panel bonding adhesives can significantly increase productivity by reducing the time needed for assembly, eliminating the need for drilling or welding, and enabling faster curing times.
- Improved safety: Panel bonding adhesives offer a safer alternative to traditional bonding methods such as welding and brazing, which can produce fumes and heat that can be hazardous to workers.
- Increased design flexibility: Panel bonding adhesives allow for greater design flexibility, as they can bond a wide range of materials and shapes, enabling manufacturers to create complex and intricate designs.
Overall, panel bonding adhesives offer numerous benefits that can improve various applications’ quality, safety, and efficiency, making them a popular choice in many industries.
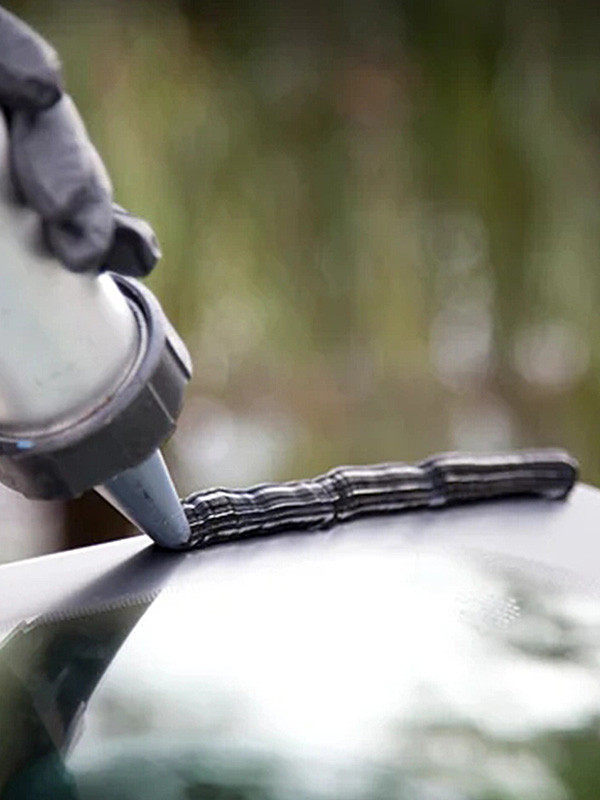
Stronger Bond
A stronger bond is essential for various applications, from automotive and aerospace to construction and manufacturing. A suitable adhesive can make all the difference in achieving a solid and durable bond. Some of the critical factors that contribute to a stronger bond include:
- Proper surface preparation:Before bonding, the surface of the materials must be adequately cleaned and prepared to ensure maximum adhesion.
- Choosing the suitable adhesive:Different adhesives have varying properties, and selecting the right one is crucial for the specific application.
- Correct application technique:Applying the adhesive correctly, following the manufacturer’s instructions and guidelines, is essential to achieving a solid bond.
- Curing time and temperature: The curing time and temperature are critical factors in achieving a solid bond, and it’s essential to follow the manufacturer’s recommended curing time and temperature for the specific adhesive.
- Material compatibility: The adhesive must be compatible with the materials being bonded, ensuring that the bond will withstand the forces and stresses of the specific application.
Achieving a stronger bond requires proper surface preparation, choosing the suitable adhesive, the correct application technique, following recommended curing time and temperature, and ensuring material compatibility. By considering these factors, manufacturers can achieve a stronger bond that will withstand the demands of various applications.
Reduced Heat Distortion
Reducing heat distortion is crucial in various industries, from automotive and aerospace to electronics and manufacturing. Heat distortion occurs when materials are exposed to high temperatures, resulting in warping, buckling, and other deformations. Some of the key factors that contribute to reduced heat distortion include:
- Choosing the suitable adhesive:Different adhesives have varying thermal properties, and selecting a bond that can withstand the specific application’s temperature range is essential.
- Proper application:Applying the adhesive correctly and evenly across the bonding surfaces can help distribute heat evenly and prevent distortion.
- Material compatibility:The adhesive must be compatible with the materials being bonded, ensuring that the bond will withstand the temperature range of the specific application.
- Using heat-resistant materials: Using heat-resistant materials for the bonding surfaces and other components in the application can help reduce heat distortion.
- Controlling heat exposure:Controlling the temperature and duration of exposure to heat can help reduce heat distortion and prevent damage to the bonded materials.
Reducing heat distortion requires choosing a suitable adhesive, proper application, material compatibility, using heat-resistant materials, and controlling heat exposure. By considering these factors, manufacturers can reduce heat distortion and ensure the quality and durability of the final product.
Improved Corrosion Protection
Improved corrosion protection is essential in various industries, from automotive and aerospace to marine and construction. Corrosion can weaken structures, cause failures, and reduce the lifespan of materials. Some of the key factors that contribute to improved corrosion protection include:
- Choosing the suitable adhesive:Different adhesives have varying resistance to corrosion, and it’s essential to select a bond that can withstand the specific application’s exposure to corrosive environments.
- Proper surface preparation:Before bonding, the surface of the materials must be adequately cleaned and prepared to remove any contaminants that could contribute to corrosion.
- Material compatibility:The adhesive must be compatible with the materials being bonded, ensuring that the bond will withstand the corrosive environment of the specific application.
- Providing a barrier: Using an adhesive that provides a barrier between the materials and the corrosive environment can help prevent corrosion.
- Using corrosion-resistant materials: Using corrosion-resistant materials for the bonding surfaces and other components in the application can help improve corrosion protection.
Overall, improved corrosion protection requires choosing a suitable adhesive, proper surface preparation, material compatibility, providing a barrier, and using corrosion-resistant materials. By considering these factors, manufacturers can improve corrosion protection and ensure the quality and durability of the final product.
Improved Aesthetics
Improved aesthetics are essential in various industries, from automotive and aerospace to architecture and interior design. Aesthetics are critical in customer appeal and can impact a product or structure’s perceived quality and value. Some of the key factors that contribute to improved aesthetics include:
- Eliminating visible fasteners:Using adhesives to bond materials together can eliminate the need for visible fasteners such as screws, rivets, and bolts, creating a smoother and more seamless appearance.
- Hiding joints and seams: Adhesives can help hide joints and seams between materials, creating a more continuous and uniform appearance.
- Providing a smooth finish: Adhesives can fill in gaps and imperfections in materials, providing a smooth and consistent surface that enhances the final product’s appearance.
- Enabling design flexibility:Adhesives can bond a wide range of materials, shapes, and sizes, allowing for greater design flexibility and enabling manufacturers to create unique and intricate designs.
- Offering color-matching options:Some adhesives offer color-matching options, allowing manufacturers to choose an adhesive that blends in seamlessly with the bonded materials.
Improved aesthetics require eliminating visible fasteners, hiding joints and seams, providing a smooth finish, enabling design flexibility, and offering color-matching options. By considering these factors, manufacturers can improve the aesthetics of their products and structures, enhancing their appeal and perceived value.
Increased Productivity
Increased productivity is crucial in various industries, from manufacturing and construction to automotive and aerospace. Productivity is the key to meeting production schedules, reducing costs, and increasing profitability. Some of the key factors that contribute to increased productivity include:
- Faster bonding times:Adhesives can bond materials together much faster than traditional mechanical fastening methods, reducing production time and increasing productivity.
- Streamlined processes:Using adhesives can eliminate the need for additional steps in the manufacturing process, such as drilling holes or applying coatings, streamlining the process and reducing production time.
- Eliminating wait times:Adhesives require no curing time, unlike some traditional bonding methods that require waiting for the adhesive to dry or cure. This eliminates wait times, allowing for faster production and increased productivity.
- Reducing material waste: Adhesives require less material than traditional bonding methods, reducing material waste and increasing efficiency.
- Easy application: Adhesives can be applied quickly and easily, reducing the need for specialized tools and equipment and allowing for greater efficiency and productivity.
Increased productivity requires faster bonding times, streamlined processes, eliminated wait times, reduced material waste, and easy application. By considering these factors, manufacturers can increase productivity and reduce production costs, improving their competitiveness in the market.
Applications of Panel Bonding Adhesives
Panel bonding adhesives are versatile and can be used in various applications across various industries. Some of the most common applications of panel bonding adhesives include:
- Automotive: The automotive industry commonly uses panel bonding adhesives to bond body panels, roofs, and structural components. These adhesives offer superior strength, durability, and corrosion protection, improving the overall quality and safety of the vehicle.
- Aerospace:Panel bonding adhesives are also used in the aerospace industry to bond various aircraft components, such as fuselages, wings, and interiors. These adhesives provide lightweight and strong bonds that can withstand the harsh environments of aerospace applications.
- Construction:Panel bonding adhesives are used in the construction industry to bond various materials, such as concrete, stone, and metal. These adhesives provide high-strength bonds that can withstand the stresses of building materials and environmental factors.
- Marine:Panel bonding adhesives are also used in the marine industry to bond various components of boats and ships, such as hulls, decks, and interiors. These adhesives provide excellent corrosion resistance and can withstand the harsh marine environment.
- Electronics:Panel bonding adhesives are used in the electronics industry to bond various electronic components, such as circuit boards and sensors. These adhesives offer strong, reliable bonds that withstand vibration, shock, and temperature changes.
Panel bonding adhesives can be used in various industries, providing superior strength, durability, and other benefits. Manufacturers can ensure their products’ quality, safety, and reliability by choosing the suitable adhesive for the specific application.
Automotive Industry
Due to their many benefits, the automotive industry is one of the most significant panel bonding adhesives users. Some of the key applications of panel bonding adhesives in the automotive industry include:
- Body panel bonding:Panel bonding adhesives bond body panels, such as doors, hoods, and trunks, to the vehicle’s frame or structure. This provides a strong, durable bond that can withstand the stresses of daily use and protect against corrosion.
- Roof bonding:Panel bonding adhesives are also used to bond roofs to the vehicle’s structure, providing a secure and durable bond that can withstand harsh weather conditions and protect against leaks.
- Structural bonding: Panel bonding adhesives are used in the structural bonding of various components, such as frames, chassis, and suspension systems. This provides a strong, lightweight, and corrosion-resistant bond that can improve the overall safety and performance of the vehicle.
- Interior bonding:Panel bonding adhesives bond various internal components, such as dashboards, seats, and trim, providing a seamless and uniform appearance while reducing noise, vibration, and harshness.
- Electric vehicle bonding: Panel bonding adhesives are becoming increasingly crucial in bonding electric vehicle components, such as battery packs and motors, due to their ability to provide excellent electrical insulation and withstand high temperatures.
Panel bonding adhesives provide numerous benefits to the automotive industry, including increased strength, durability, and corrosion protection. By incorporating these adhesives into their production processes, manufacturers can improve the quality, safety, and performance of their vehicles while also reducing costs and improving productivity.
Aerospace Industry
The aerospace industry uses panel bonding adhesives, which bond various aircraft components, including fuselages, wings, and interiors. Some of the key applications of panel bonding adhesives in the aerospace industry include:
- Fuselage bonding:Panel bonding adhesives are used to bond the skin panels of the fuselage, providing a strong, lightweight, and corrosion-resistant bond that can withstand the stresses of flight.
- Wing bonding: Panel bonding adhesives are also used to bond the skins of the wings, providing a strong, durable, and aerodynamic bond that can withstand the high speeds and stresses of flight.
- Interior bonding: Panel bonding adhesives are used to bond various internal components of aircraft, such as seats, cabinetry, and insulation, providing a strong and uniform bond that can withstand the rigors of flight and improve passenger comfort.
- Repair and maintenance:Panel bonding adhesives are also used in the repair and maintenance of aircraft, providing a quick and easy way to bond and reinforce damaged or worn components.
Panel bonding adhesives play a critical role in the aerospace industry, providing lightweight and strong bonds that can withstand the harsh environments and stresses of flight. By incorporating these adhesives into their production processes and maintenance procedures, manufacturers can improve the safety, reliability, and efficiency of their aircraft while also reducing costs and improving productivity.
Marine Industry
The marine industry also makes use of panel-bonding adhesives for various applications. These adhesives offer several benefits, including excellent resistance to saltwater, UV radiation, and harsh environmental conditions. Some of the key applications of panel bonding adhesives in the marine industry include:
- Hull bonding:Panel bonding adhesives are used to bond the hull of boats and ships, providing a strong, durable, and watertight seal that can withstand the stresses of waves and currents.
- Deck bonding: Panel bonding adhesives are also used to bond the deck of boats and ships, providing a firm, slip-resistant, and waterproof surface that can withstand the rigors of marine environments.
- Interior bonding: Panel bonding adhesives are used to bond various internal components of boats and ships, such as cabinetry, flooring, and insulation, providing a strong and uniform bond that can withstand the effects of humidity, salt, and UV radiation.
- Repair and maintenance: Panel bonding adhesives are also used to repair and maintain boats and ships, providing a quick and easy way to bond and reinforce damaged or worn components.
Panel bonding adhesives play an essential role in the marine industry, providing a solid and durable bond that can withstand the harsh environments and stresses of aquatic environments. By incorporating these adhesives into their production processes and maintenance procedures, manufacturers can improve the durability, reliability, and performance of their boats and ships while reducing costs and improving productivity.
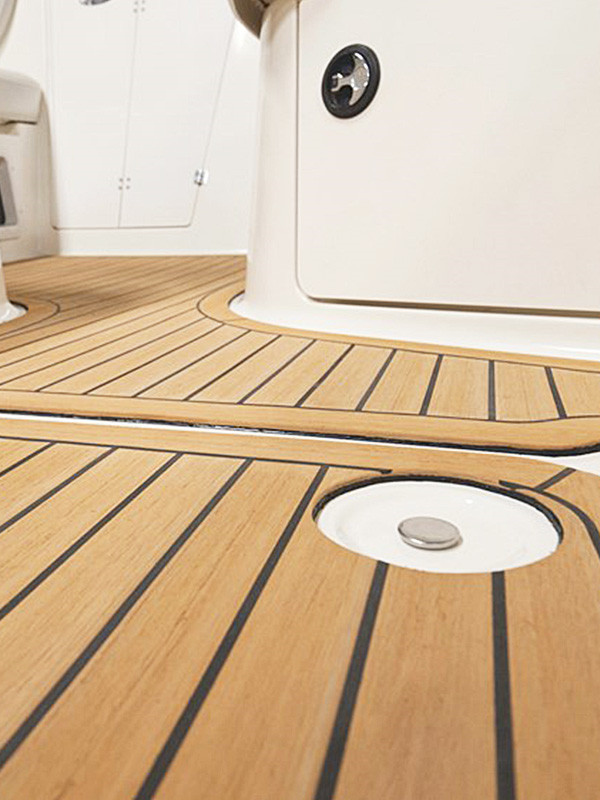
Construction Industry
The construction industry is a crucial player in the global economy, providing essential infrastructure and buildings for businesses, communities, and individuals. The construction industry has evolved rapidly with new technologies and materials, and adhesive technology has become increasingly important. Here are some ways adhesives are used in the construction industry:
- Structural bonding:Adhesives are used for structural bonding in construction projects, creating solid and durable bonds between materials like metal, wood, and composites.
- Flooring and wall coverings: Adhesives are used to install flooring and wall coverings in buildings, providing a quick and easy installation process.
- Sealants:Adhesives are used as sealants to prevent leaks and drafts in buildings, helping to increase energy efficiency.
- Insulation:Adhesives bond insulation materials to walls and roofs, improving insulation efficiency.
- Fire retardancy: Adhesives can be formulated to be fire-resistant, making them helpful in constructing fire-resistant structures.
Adhesive technology has dramatically enhanced the capabilities of the construction industry, enabling faster and more efficient construction with greater flexibility and durability. As the construction industry evolves, adhesives will play an increasingly important role in construction projects.
How to Use Panel Bonding Adhesives
Panel bonding adhesives are commonly used in automotive repair and construction projects. These adhesives are designed to bond metal, plastic, and composite panels together, creating a solid and durable bond. Here are some steps to follow when using panel bonding adhesives:
- Clean and prepare the surface: Clean the surface and ensure it is free of dirt, grease, and other contaminants. Roughen up smooth or glossy surfaces with sandpaper to improve adhesion.
- Apply the adhesive: Apply the panel bonding adhesive to a bonded surface. Use a bead of glue around the panel’s perimeter and apply it in a zig-zag pattern across the middle.
- Place the panel: Place the panel onto the surface with the adhesive. Apply pressure evenly to ensure the panel is seated correctly and the adhesive spreads evenly.
- Clamp the panel:Clamp the board until the glue has cured. Follow manufacturer instructions for clamping time and pressure.
- Finish and sand:Once the glue has cured, finish and sand the surface to achieve a smooth and even finish.
Surface Preparation
Surface preparation is a critical step in the adhesive bonding process, and proper surface preparation can ensure that the adhesive forms a solid and durable bond. Here are some tips for surface preparation when working with adhesives:
- Clean the surface:Ensure the consistency is clean and free of dirt, grease, oil, and other contaminants. Use a cleaning solution recommended by the manufacturer to remove any impurities.
- Sand the surface: Sand the surface lightly to roughen it up and provide better adhesion. This is especially important when bonding to smooth or glossy surfaces.
- Prime the surface:Some surfaces may require priming before applying the adhesive. This can help the adhesive bond better to the surface.
- Dry the surface:Ensure consistency.
- Is completely dry before applying the adhesive. Any moisture on the surface can interfere with the adhesive bond.
- Mask off the area:If necessary, mask off the area around the bonded surfaces to prevent the adhesive from getting onto unwanted sites.
By following these steps, you can ensure that your adhesive project forms a solid and durable bond. Clean the surface, sand the surface, prime the surface if necessary, dry the surface, and mask off the area for a successful adhesive project.
Mixing and Application
Mixing and application are crucial steps in the adhesive bonding process, and proper mixing and application can ensure that the adhesive forms a strong and durable bond. Here are some tips for mixing and application when working with adhesives:
- Follow manufacturer instructions: Read and follow the manufacturer’s instructions for mixing and application. This will ensure that you are using the adhesive correctly and that it will bond properly.
- Mix thoroughly: Mix the adhesive thoroughly according to the manufacturer’s instructions. This will ensure that the adhesive is mixed correctly and will bond evenly.
- Apply evenly:Apply the adhesive evenly to the surfaces being bonded. This will help ensure a strong and durable bond.
- Use the right amount:Use the right amount of adhesive for bonded surfaces. Using too little adhesive can result in a weak bond while using too much glue can cause the excess to squeeze out and create a mess.
- Clean up excess adhesive: Clean up any excess glue before it dries. This will make finishing and sanding the surface easier once the adhesive has cured.
By following these steps, you can ensure that your adhesive project forms a strong and durable bond. Follow the manufacturer’s instructions, mix thoroughly, apply evenly, use the right amount, and clean up excess adhesive for a successful project.
Clamping and Curing
Clamping and curing are crucial steps in the adhesive bonding process. Proper clamping and curing can ensure the adhesive forms a strong and durable bond. Here are some tips for clamping and curing when working with adhesives:
- Apply even pressure:Use a clamp or other device to bond surfaces. This will help ensure a tight bond and prevent air bubbles from forming.
- Allow time for curing: Allow enough time for the adhesive to cure fully before removing the clamp or handling the project. The curing time will vary depending on the adhesive being used.
- Avoid moving or disturbing the project:Do not move or disturb the project while it is curing. This can disrupt the bonding process, resulting in a weak or failed bond.
- Use a heat source:Some adhesives require heat to cure properly. If this is the case, use a heat source such as a heat gun or oven to speed up the curing process.
- Test the bond: Once the adhesive has cured, apply pressure or stress to the project to ensure the bond is solid and durable.
By following these steps, you can ensure that your adhesive project forms a strong and durable bond. Apply even pressure, allow time for curing, avoid moving or disturbing the project, use a heat source if necessary, and test the bond for a successful adhesive project.
Finishing and Sanding
Finishing and sanding are essential steps in any adhesive project. Proper finishing and sanding can improve the project’s overall appearance and help ensure the adhesive is securely bonded to the surface. Here are some tips for finishing and sanding when working with adhesives:
- Allow adhesive to dry completely: Ensure the glue is fully cured before the surface is finished or sanded.
- Sand the surface:Sand the surface to create a rough surface for the adhesive to bond to. Use fine-grit sandpaper to avoid damaging the surface.
- Clean the surface: After sanding, clean the surface thoroughly to remove any dust or debris.
- Apply a finishing coat:Apply a finishing coat to protect the surface and improve its appearance. Choose an appropriate finish for the adhesive and the surface being used.
- Allow to dry: Allow the finishing coat to dry completely before using or handling the project.
Following these steps, you can ensure your adhesive project looks excellent and securely bonded to the surface. Allow the adhesive to dry completely, sand the surface, clean thoroughly, apply a finishing coat, and dry for a successful and attractive adhesive project.
Safety Precautions
Adhesives are helpful in many DIY projects but can also be hazardous if not used correctly. Safety precautions should always be taken to avoid accidents and injuries when working with adhesives. Here are some essential safety precautions to keep in mind:
- Read and follow instructions: Always read and follow the manufacturer’s instructions for using the glue.
- Use in a well-ventilated area: Use adhesives in a well-ventilated area to prevent inhalation of harmful fumes or dust.
- Wear protective gear: Wear gloves, safety glasses, and a respirator if necessary to protect yourself from exposure to chemicals in the adhesive.
- Avoid contact with skin and eyes: Avoid contact with the skin and eyes, and immediately rinse with water if contact occurs.
- Keep out of reach of children and pets:Adhesives can be harmful if ingested, so keep them out of reach of children and pets.
- Store properly:Store adhesives in a cool, dry place away from heat sources and out of reach of children and pets.
Protective Gear
Using protective gear when working with adhesives is essential to avoid exposure to harmful chemicals and prevent skin irritation or other injuries. Protective equipment can include items such as gloves, safety glasses, and respirators. Here are some tips for using protective equipment when working with adhesives:
- Wear gloves:Gloves protect your hands from exposure to chemicals in the adhesive and prevent skin irritation. Choose gloves made of the appropriate material for the glue, such as nitrile gloves for solvents or latex gloves for water-based adhesives.
- Wear safety glasses: Safety glasses protect your eyes from splashes or vapors of adhesive. Choose glasses that are impact-resistant and fit securely to your face.
- Use a respirator: A respirator can protect you from inhaling harmful fumes or dust from the adhesive. Choose a respirator that is appropriate for the type of adhesive being used.
- Follow manufacturer’s instructions: Always follow the manufacturer’s recommendations for protective gear when using adhesives.
Using the proper protective gear when working with adhesives can avoid injury and ensure your safety. Wear gloves, safety glasses, and a respirator when needed, and follow the manufacturer’s instructions to protect yourself from exposure to exposure harmful chemicals.
Proper Ventilation
Proper ventilation is an essential aspect to consider when working with adhesives. Many adhesives contain volatile organic compounds (VOCs), which can be harmful when inhaled. Failing to use bonds in a well-ventilated area can lead to various issues, from headaches and dizziness to more serious respiratory problems. Here are some tips for ensuring proper ventilation when working with adhesives:
- Work in a well-ventilated area: Choose a workspace with good air circulation, such as a room with windows that can be opened or a space with a ventilation system.
- Use a respirator:Wear a respirator when working with adhesives to protect your lungs from harmful vapors.
- Avoid working in confined spaces: Only use adhesives in small, enclosed areas with proper ventilation, such as closets or bathrooms.
- Follow the manufacturer’s instructions: Always follow the manufacturer’s recommendations for ventilation when using adhesives.
By taking the necessary precautions for proper ventilation, you can avoid respiratory issues and other health problems associated with using adhesives. Make sure to work in a well-ventilated area, wear a respirator, and follow the manufacturer’s instructions to ensure your safety while using bonds for your DIY projects.
Handling and Storage
Proper handling and storage of adhesives is crucial to their effectiveness and longevity. When adhesives are stored correctly, it can lead to strong bonds, messy finishes, and damage to the materials. Here are some tips for handling and storing adhesives:
- Follow the manufacturer’s instructions: Always read and follow the manufacturer’s instructions for handling and storage.
- Use protective gear: Wear gloves and other protective equipment when handling adhesives to avoid skin irritation or chemical exposure.
- Keep adhesives away from heat sources: Adhesives should be stored in a cool, dry place away from heat sources such as direct sunlight or radiators.
- Avoid moisture:Exposure to moisture can cause adhesives to deteriorate or lose effectiveness. Keep them away from sources of humidity, such as bathrooms or basements.
- Seal the container properly: Seal the adhesive container tightly after each use to prevent it from drying out or becoming contaminated.
By taking the time to properly handle and store adhesives, you can ensure that they will perform as expected and produce the best results for your DIY projects. By following these simple tips, you can extend the shelf life of your adhesives and avoid common issues that can arise from improper storage and handling.
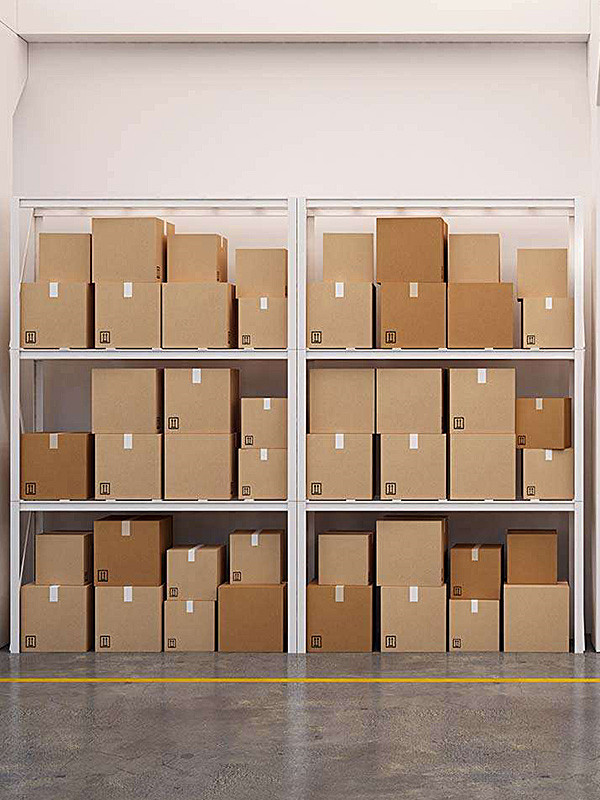
Shelf Life
Shelf life is an essential factor to consider when working with adhesives. The shelf life of a bond refers to the amount of time it can be stored before it starts to degrade and lose effectiveness. Using glue that has exceeded its shelf life can lead to various issues, including weak bonds, messy finishes, and damage to the materials. Here are some tips for managing the shelf life of adhesives:
- Check the expiration date:Always check the expiration date on the adhesive container before using it.
- Store the adhesive properly:Adhesives should be stored in a cool, dry place away from direct sunlight and heat sources.
- Use the glue on time: Once opened, bonds should be used within a certain amount to ensure they are still effective.
By paying attention to the shelf life of adhesives and taking the proper precautions, you can ensure that your DIY projects are successful and long-lasting.
Common Mistakes When Using Panel Bonding Adhesives
Panel bonding adhesives are popular for many DIY projects but can be tricky to use correctly. Failing to properly use panel bonding adhesives can lead to issues, from weak bonds to messy finishes. Here are some common mistakes to avoid when using panel bonding adhesives:
- Not preparing the surface properly: With proper surface preparation, panel bonding adhesives may adhere adequately, resulting in strong bonds or finishes that easily peel or flake.
- Using too much or too little glue: Overusing or underusing adhesive can cause problems such as weak bonds, messy finishes, and wasted materials.
- Not allowing enough curing time: Panel bonding adhesives need adequate time to cure before they can be used, and failing to allow enough curing time can result in weak bonds or failure of the project.
Using the Wrong Type of Adhesive
Choosing the suitable adhesive for a DIY project can be daunting, but choosing the correct type for the materials and conditions is essential. Using the wrong glue can lead to issues, including weak bonds, messiness, and damage to the materials involved. Here are some reasons why using the wrong type of adhesive is a mistake:
- Weak bonds: Different materials require different types of adhesive, and using the wrong type can result in weak bonds that can cause the project to fall apart.
- Messy finishes: Using the wrong adhesive can result in messy, uneven finishes that detract from the project’s appearance.
- Damage to materials: Some adhesives can cause damage to certain types of materials, such as wood, plastic, or fabric.
Choosing the correct type of adhesive for the project is essential to avoid these issues. Here are some tips to help:
- Read the instructions: Always read the manufacturer’s instructions carefully to ensure you use the correct type of adhesive for the project.
- Consider the materials involved: Make sure to choose an appropriate adhesive for the materials you will be working with.
- Test the adhesive first: Before starting the project, test the glue on a small, inconspicuous area to ensure it works properly.
By choosing the right type of adhesive for the project, you can ensure a strong, clean bond that will last. Taking the time to select the suitable adhesive may seem like a small step, but it can make a big difference in the success of your DIY project.
Not Preparing the Surface Properly
Before starting any DIY project, it is crucial to properly prepare the surface that will be worked on. Failing to do so can result in various issues, from poor adhesion to uneven finishes. Here are some reasons why not preparing the surface properly is a mistake:
- Poor adhesion: With proper preparation, adhesives, and coatings may adhere appropriately to the surface, resulting in strong bonds or finishes that easily peel or flake.
- Uneven finishes:Surface irregularities such as bumps, cracks, and holes can lead to varying finishes that detract from the project’s appearance.
- Reduced durability:A poorly prepared surface can compromise the project’s durability. Without proper preparation, coatings may not provide adequate protection from moisture, UV radiation, and other elements that can cause damage over time.
To avoid these issues, it is vital to properly prepare the surface before starting a project. Here are some tips to help:
- Clean the surface thoroughly: Remove any dirt, dust, or debris from the surface before beginning the project.
- Repair any damage:Fill in any cracks or holes in the surface and sand down any bumps or rough spots.
- Follow manufacturer’s instructions:Always follow the manufacturer’s instructions for any cleaning or preparation products used.
Overusing or Underusing the Adhesive
Adhesives are essential to many DIY projects, but misusing them can lead to various issues. Overusing or underusing adhesive is a common mistake that can cause problems such as weak bonds, messy finishes, and wasted materials. Here are some reasons why it is essential to use the right amount of adhesive:
- Weak bonds: Using too little adhesive can result in weak or incomplete bonds, which can cause the project to fall apart or fail to function as intended. On the other hand, using too much adhesive can create gaps and air pockets, weakening the bond.
- Messy finishes: Overusing adhesive can lead to a messy, uneven finish that detracts from the project’s appearance. This can be particularly problematic for projects that require a clean, professional-looking finish.
- Wasted materials: Adhesives can be expensive, and overusing them can quickly add to unnecessary expenses. Additionally, using too much adhesive can make repositioning or adjusting the materials difficult, resulting in wasted materials if the project needs to be started over.
The right amount of adhesive for the project is essential to avoid these issues. Here are some tips to help:
- Read the instructions:Always read the manufacturer’s instructions before using an adhesive. This will guide the amount of glue and other essential details.
- Start with a small amount: When in doubt, start with a small amount of adhesive and add more as needed. It is easier to add more glue than to remove excess.
- Consistent application:Consistently apply the adhesive to ensure an even bond. This can be done with a brush, roller, or another application tool.
Not Following the Recommended Curing Time
When it comes to DIY projects that involve paint, one of the most crucial steps is the curing time. Curing allows the paint to fully dry and harden, ensuring it will last long. Unfortunately, many people skip or ignore this step, leading to paint that has easy chips or peels. Here are some reasons why not following the recommended curing time is a big mistake:
- Lack of durability:Curing time ensures the paint fully dries and hardens. If the paint cannot cure properly, it can be more susceptible to damage and wear. This can result in chips, peeling, and a need for touch-ups or repaints.
- Reduced lifespan:The purpose of painting is often to improve the appearance of a surface, but it is also intended to protect it. If the paint cannot cure fully, it may not provide the necessary protection, leading to more frequent repairs and replacements.
- Appearance issues: Not following the recommended curing time can also affect the appearance of the finished project. If the paint is still soft or tacky, it may not dry evenly, leaving visible marks or smudges. It can also be more challenging to achieve a smooth finish if the paint has not had enough time to dry properly.
It can be tempting to rush through the painting process and skip the curing time, but it is important to remember that this step is essential for a quality finish.
Here are some tips for ensuring that you follow the recommended curing time:
- Check the manufacturer’s instructions: The curing time for paint can vary depending on the type of paint and the surface it is being applied to. Always read the manufacturer’s instructions carefully to determine the appropriate curing time.
- Be patient: While waiting for the paint to dry can be frustrating, rushing through the process can ultimately lead to more work and less-than-desirable results. Make sure to allow enough time for the paint to cure fully before using or handling the painted surface.
- Avoid humidity: Humidity can slow down the drying process and affect the quality of the finish. Try to paint in low humidity conditions and avoid exposing the painted surface to high moisture levels while curing.
In conclusion, underusing adhesive can lead to weak or incomplete bonds, resulting in product failure and customer dissatisfaction. It is essential to follow the recommended application instructions and use the appropriate amount of adhesive to ensure a secure and long-lasting bond. Proper adhesive usage can improve product performance, durability, and overall customer satisfaction.