Microelectronics Adhesives
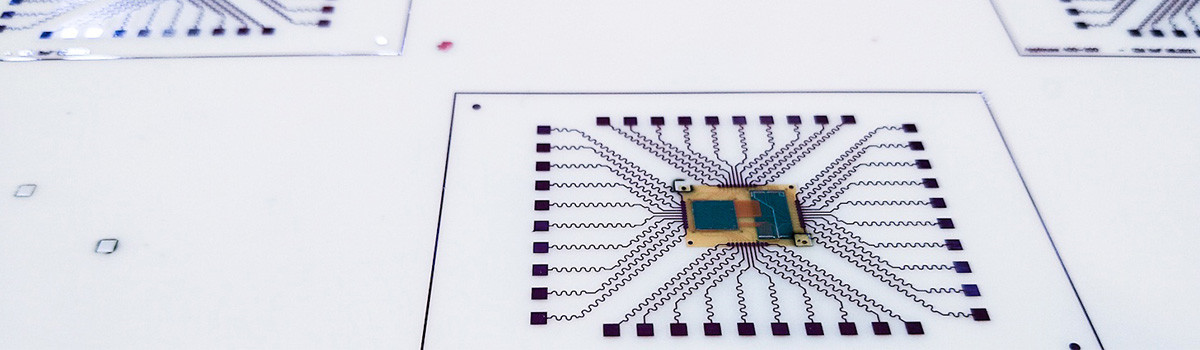
Microelectronics adhesives play a crucial role in the manufacturing and assembly of small electronic devices, such as integrated circuits, printed circuit boards, sensors, and other electronic components. These adhesives provide strong bonding capabilities, electrical insulation, thermal management, and protection against environmental factors. With the constant advancement in microelectronic technology, the demand for reliable, high-performance adhesives has grown significantly. This article explores the various aspects and applications of microelectronics adhesives, highlighting their importance in ensuring the functionality and durability of electronic devices.
Types of Microelectronics Adhesives
Microelectronics adhesives are essential components in the assembly and packaging of electronic devices. They play a critical role in bonding various materials used in electronic manufacturing, such as semiconductors, metals, plastics, and ceramics. There are different types of microelectronics adhesives, each with its unique properties and applications. Here are some of the most common types:
- Conductive adhesives: These adhesives conduct electricity and find applications where electrical conductivity is necessary. Electronic components like flip-chip connections, surface-mounted devices, and wire bonding commonly utilize these adhesives.
- Non-conductive adhesives: These adhesives provide electrical insulation and find applications where electrical insulation is necessary. They are commonly used to protect electronic components from short circuits and damage caused by electrostatic discharge.
- Thermally conductive adhesives:These adhesives transfer heat away from electronic components and find everyday use in applications where heat dissipation is critical, such as in power electronics and LED lighting.
- UV-curing adhesives: These adhesives cure using ultraviolet light and find common use in applications where fast curing is necessary. They also find use in applications where heat cannot cure the adhesive.
- Epoxy adhesives: These adhesives have a reputation for high strength and durability and find everyday use in applications that require a strong bond. They are also resistant to chemicals and can withstand high temperatures.
- Silicone adhesives: These adhesives exhibit excellent flexibility and find everyday use in applications that anticipate thermal expansion and contraction. They also find use in applications where water and moisture resistance is critical.
The choice of microelectronics adhesive depends on the specific requirements of the application. When there is a need for electrical conductivity, people use conductive adhesives, whereas they employ non-conductive adhesives for electrical insulation purposes. People use thermally conductive adhesives when heat dissipation is critical, while they use UV-curing adhesives when fast curing is necessary. People use epoxy adhesives when they require high strength and durability, while they use silicone adhesives when flexibility and moisture resistance are critical.
Epoxy Adhesives: The Go-To Choice
Epoxy adhesives are the go-to choice for numerous bonding applications due to their versatility, strong bonding capabilities, chemical and temperature resistance, gap-filling properties, a wide range of formulations, and enhanced durability. Whether in construction, manufacturing, or DIY projects, epoxy adhesives provide reliable and robust bonding solutions that deliver exceptional results.
- Versatility:Epoxy adhesives are renowned for their versatility, making them the go-to choice for various applications. Whether you need to bond metals, plastics, wood, ceramics, or even glass, epoxy adhesives offer exceptional bonding capabilities across multiple materials. They provide durable and reliable bonds that withstand demanding conditions, making them suitable for indoor and outdoor projects.
- Strong Bonding:One of the key reasons why epoxy adhesives are highly favored is their ability to create strong bonds. When properly mixed and applied, epoxy adhesives form incredibly robust connections that exhibit excellent tensile, shear, and peel strength. These materials are perfect for tasks involving carrying weight or where a lot of pressure is applied.
- Chemical and Temperature Resistance:Epoxy adhesives resist chemicals and extreme temperatures. They can withstand exposure to solvents, fuels, oils, and other substances without losing their adhesive properties. Additionally, they offer impressive thermal stability, remaining effective even in high-temperature environments. This resilience makes epoxy adhesives suitable for automotive, aerospace, and industrial applications where resistance to harsh conditions is crucial.
- Gap Filling:Epoxy adhesives have excellent gap-filling properties, enabling them to bridge small gaps and uneven surfaces. This characteristic is particularly beneficial when bonding materials with irregular or rough surfaces, ensuring a secure and complete bond. Epoxy adhesives can fill voids and imperfections, creating a solid bond that effectively distributes stress across the joint area.
- Wide Range of Formulations:Epoxy adhesives come in various formulations, allowing users to select the most suitable type for their needs. Whether it’s a fast-curing epoxy for quick assembly or a slow-curing epoxy for precise positioning, an epoxy adhesive formulation is available to meet diverse requirements. Moreover, different formulations offer different viscosities, working times, and handling properties, providing flexibility and customization options.
- Enhanced Durability:Epoxy adhesives possess exceptional durability and resistance to environmental factors such as moisture, UV radiation, and aging. These adhesives maintain their structural integrity over time, ensuring long-lasting bonds that stand up to wear and tear. Their ability to resist degradation and maintain performance makes them preferred for applications subjected to constant use and exposure.
Conductive Adhesives: Enabling Electrical Connectivity
Conductive adhesives are crucial in enabling electrical connectivity in various industries and applications. These versatile adhesives possess unique properties that make them an attractive alternative to traditional soldering or mechanical fastening methods. Here are some key points highlighting the significance of conductive adhesives:
- Versatility:Conductive adhesives offer compatibility with a wide range of substrates, including metals, plastics, ceramics, and glass. This versatility allows their use in diverse industries, such as electronics, automotive, aerospace, and medical devices.
- Electrical conductivity:These adhesives provide excellent electrical conductivity, enabling the transmission of electrical signals and power between components. They exhibit low resistance, comparable to solder joints, ensuring efficient and reliable electrical connections.
- Joining dissimilar materials:Conductive adhesives are particularly useful for joining dissimilar materials, such as bonding metal to plastic or glass to electronics. Their ability to bridge the gap between different substrates enables the integration of diverse components in complex assemblies.
- Temperature resistance:Many conductive adhesives exhibit high-temperature resistance, which ensures stable electrical connections even in harsh operating conditions. This feature is crucial for applications with elevated temperatures or thermal cycling.
- Flexibility and durability:Conductive adhesives offer excellent flexibility, allowing them to withstand vibrations, shocks, and mechanical stresses without compromising electrical performance. Their durability ensures long-term reliability, making them suitable for demanding environments.
- Process compatibility:These adhesives offer compatibility with different manufacturing processes as they can be applied using various methods, including screen printing, dispensing, or film lamination. This versatility simplifies integration into existing production lines.
- Environmental benefits:Conductive adhesives are often lead-free and comply with environmental regulations. They eliminate the need for hazardous soldering processes, reducing the release of harmful substances and promoting sustainable manufacturing practices.
- Miniaturization and weight reduction:Conductive adhesives allow for the miniaturization of electronic components and assemblies due to their ability to create fine-pitch interconnections. Additionally, they contribute to weight reduction in applications where lightweight materials are essential.
These advantages make conductive adhesives indispensable for achieving reliable and efficient electrical connectivity in various industries.
Thermal Management Adhesives: Ensuring Device Reliability
Thermal management adhesives ensure device reliability by efficiently dissipating heat from electronic components. These specialized adhesives offer unique characteristics that aid heat transfer and thermal stability. Here are key points highlighting the significance of thermal management adhesives:
- Heat dissipation:Thermal management adhesives possess excellent thermal conductivity, enabling efficient transfer of heat from heat-generating components to heat sinks or other cooling mechanisms. Preventing overheating is crucial to avoid device malfunction or reduced lifespan.
- Bonding and sealing:These adhesives provide strong bonding and sealing properties, allowing for the practical attachment of heat sinks, thermal interface materials, and other cooling devices to electronic components. The secure bond ensures optimal heat transfer and maintains long-term device reliability.
- Compatibility with different substrates:Thermal management adhesives exhibit compatibility with a wide range of substrates, including metals, ceramics, glass, and plastics. This versatility enables their use in diverse applications across electronics, automotive, telecommunications, and energy industries.
- Thermal stability:Many thermal management adhesives exhibit high-temperature resistance and remain stable under extreme thermal cycling conditions. This characteristic ensures the adhesive maintains its performance and integrity over time, even in demanding operating environments.
- Electrical insulation:In addition to thermal conductivity, thermal management adhesives often possess excellent electrical insulation properties. Device safety and reliability are enhanced by preventing electrical shorts and maintaining proper isolation between components.
- Gap filling and conformability:Thermal management adhesives can fill microscopic gaps and irregularities between components and heat sinks, improving the thermal interface and heat transfer efficiency. Their conformability enables effective contact even in complex geometries, ensuring consistent thermal performance.
- Process compatibility:These adhesives can be applied using methods such as dispensing, screen printing, or film lamination, making them compatible with different manufacturing processes. Efficient assembly of thermal management solutions is possible through easy integration into existing production lines.
- Environmental considerations:Manufacturers often formulate thermal management adhesives to be environmentally friendly, ensuring compliance with regulations and promoting sustainable manufacturing practices. They may be free of hazardous substances such as volatile organic compounds (VOCs) and halogens, reducing environmental impact.
UV Curing Adhesives: Rapid and Precise Bonding
UV-curing adhesives are valuable for rapid and precise bonding in various industries. These adhesives offer unique properties that make them ideal for applications where quick curing, precision, and versatility are essential. Here are key points highlighting the significance of UV-curing adhesives:
- Rapid curing:UV curing adhesives cure rapidly upon exposure to ultraviolet (UV) light, allowing for fast assembly and increased production throughput. The curing process can be completed in seconds, significantly reducing assembly time and enabling shorter manufacturing cycles.
- High bond strength:UV curing adhesives provide excellent bond strength, ensuring robust and reliable adhesive joints. They form strong bonds to various substrates, including metals, plastics, glass, and ceramics, offering a versatile solution for bonding diverse materials.
- Precise control:UV curing adhesives enable specific bonding due to their instant cure upon UV light exposure. By allowing accurate alignment and positioning of components before curing, the result is precise and repeatable bond lines while minimizing misalignment risk.
- Low heat generation:UV curing adhesives generate minimal heat during the process, making them suitable for temperature-sensitive materials or delicate components. This feature reduces the risk of heat-induced damage to electronic or optical devices.
- Versatility in applications:UV curing adhesives find applications in various industries, including electronics, medical devices, optics, automotive, and aerospace. They can be used for bonding, sealing, encapsulating, and coating, offering a versatile solution for manufacturing processes.
- Improved productivity:The rapid curing capability of UV curing adhesives allows for increased production efficiency and enhanced productivity. Manufacturers can achieve faster assembly times, reduced work-in-progress inventory, and shorter manufacturing cycles.
- Environmentally friendly:Manufacturers often formulate UV curing adhesives to be environmentally friendly, ensuring they contain no volatile organic compounds (VOCs) or hazardous solvents. The absence of heat and low energy consumption during curing contributes to their eco-friendliness.
- Enhanced quality control:UV curing adhesives facilitate quality control processes by enabling immediate inspection and testing after curing. The instant cure allows for prompt bond strength evaluation, ensuring that only adequately fixed adhesive joints proceed to the next manufacturing steps.
These properties make UV-curing adhesives practical for industries seeking rapid and precise bonding solutions.
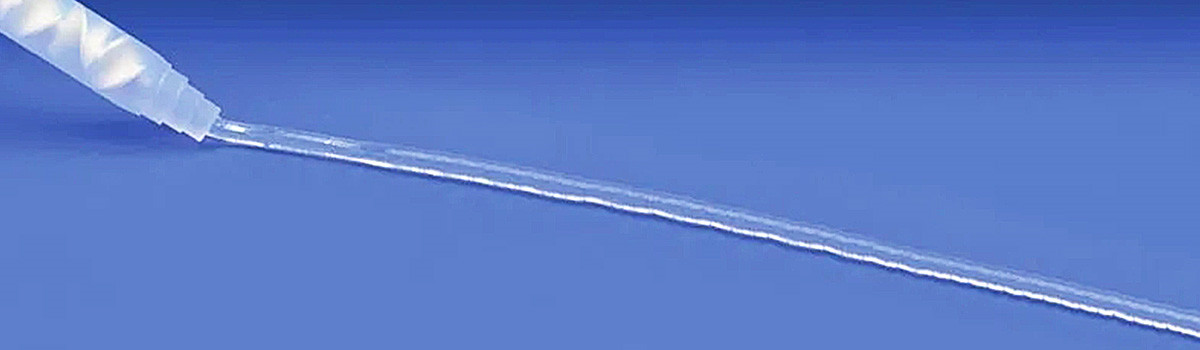
Silicone Adhesives: Superior Environmental Resistance
Silicone adhesives are highly regarded for their superior environmental resistance, making them an ideal choice for applications where durability and reliability in challenging conditions are paramount. These adhesives offer unique properties that set them apart in their ability to withstand extreme temperatures, moisture, chemicals, and other environmental factors. Here are key points highlighting the significance of silicone adhesives:
- Temperature resistance:Silicone adhesives exhibit exceptional temperature resistance, maintaining their performance and integrity across a wide temperature range. They can withstand high and low temperatures, making them suitable for applications exposed to extreme heat or cold.
- Moisture and water resistance:Silicone adhesives possess excellent resistance to moisture and water, making them highly reliable in environments with high humidity, water exposure, or immersion. This characteristic ensures long-term adhesion and protects against moisture-related issues such as corrosion or electrical failures.
- Chemical resistance:Silicone adhesives offer excellent resistance to various chemicals, including solvents, acids, bases, and fuels. This property makes them suitable for automotive, aerospace, and chemical processing applications, where exposure to various chemicals is daily.
- UV and weather resistance:Silicone adhesives exhibit outstanding resistance to ultraviolet (UV) radiation and weathering, including opposition to sunlight, ozone, and oxidation. These adhesives can be used outdoors, even with extended exposure to sunlight and harsh weather, without experiencing the degradation that other adhesives might.
- Flexibility and elasticity:Silicone adhesives possess excellent flexibility and elasticity, allowing them to accommodate bonded substrates’ thermal expansion and contraction. This flexibility helps to absorb mechanical stresses and vibrations, enhancing overall durability and resistance to failure.
- Electrical insulation:Many silicone adhesives offer excellent electrical insulation properties, making them suitable for critical electrical isolation applications. They can prevent electrical shorts and maintain proper insulation between components, ensuring device safety and reliability.
- Aging and durability:Silicone adhesives exhibit excellent long-term aging and durability properties, maintaining their performance and adhesion strength over extended periods. This characteristic contributes to the longevity and reliability of bonded assemblies in various applications.
- Compatibility with diverse substrates:Silicone adhesives demonstrate compatibility with a wide range of substrates, including metals, plastics, glass, and ceramics. This versatility allows their use in diverse industries such as electronics, automotive, medical devices, and construction.
Low Outgassing Adhesives: Critical for Space Applications
Low-outgassing adhesives play a critical role in space applications where the prevention of contamination and maintenance of a vacuum environment are of utmost importance. These specialized adhesives offer unique properties that minimize the release of volatile organic compounds (VOCs) and other outgassing byproducts that could negatively impact sensitive equipment and optics. Here are key points highlighting the significance of low-outgassing adhesives in space applications:
- Vacuum compatibility:Manufacturers formulate low-outgassing adhesives with minimal volatile content, ensuring their compatibility with the vacuum conditions prevalent in space. They release deficient levels of gases or vapors that could contaminate surrounding surfaces or interfere with delicate instruments.
- Contamination prevention:Designers create these adhesives to minimize the generation of particulate matter or debris that could contaminate sensitive components, optics, or spacecraft surfaces. Their low outgassing properties help maintain cleanliness and prevent the accumulation of contaminants that could degrade performance or hinder functionality.
- Optics and sensor applications:Low-outgassing adhesives are crucial for optical systems and sensors in space missions. They ensure that optics remain clear and unobstructed, preventing fogging, hazing, or visual performance degradation due to outgassing byproducts.
- Adhesion and reliability:While prioritizing low outgassing properties, these adhesives also offer reliable adhesion to various substrates encountered in space applications, including metals, composites, ceramics, and plastics. They provide strong and durable bonds, ensuring the integrity and longevity of assemblies even in demanding space environments.
- Thermal stability:Low-outgassing adhesives often exhibit excellent thermal stability, allowing them to withstand extreme temperature variations in space. They maintain their properties and adhesion strength over a wide temperature range, ensuring reliable performance in the harsh space environment.
- Radiation resistance:Space missions expose adhesives to various forms of radiation, including ionizing radiation, solar radiation, and cosmic rays. Formulators design low-outgassing adhesives with radiation-resistant properties, ensuring they can withstand radiation exposure without compromising their low-outgassing characteristics or overall performance.
- Materials compatibility:Low-outgassing adhesives are compatible with various materials commonly used in space applications, such as spacecraft structures, satellite components, and scientific instruments. Their formulation aims to minimize interactions and degradation when in contact with different materials, thus maintaining their low outgassing properties over time.
- Stringent standards and testing:Adhesives used in space applications must undergo rigorous testing and adhere to strict standards to ensure low outgassing properties. These standards, such as those set by NASA, ensure that adhesives meet the stringent requirements for space missions regarding outgassing levels, cleanliness, and performance.
Flip Chip Adhesives: Enabling Miniaturization
Flip chip adhesives are crucial in enabling miniaturization in various industries, particularly electronics. These specialized adhesives offer unique properties that facilitate the assembly and interconnection of microelectronic devices with high-density interconnects. Here are key points highlighting the significance of flip chip adhesives in enabling miniaturization:
- Size reduction:Flip chip adhesives allow for direct bonding of microchips or dies onto substrates, eliminating the need for wire bonding or through-hole interconnections. This direct connection significantly reduces the size of electronic packages and devices, supporting the trend toward smaller and more compact designs.
- High-density interconnects:Flip chip adhesives facilitate the creation of high-density interconnects, enabling the integration of many microchips or dies on a single substrate. This density increase contributes to the miniaturization of electronic components and enhances the device’s overall functionality.
- Improved electrical performance:Flip chip adhesives provide shorter and more direct electrical paths than traditional bonding methods, reducing resistance, inductance, and capacitance in the interconnections. This improvement in electrical performance allows for faster signal transmission, lower power consumption, and enhanced device reliability.
- Enhanced thermal management:Flip chip adhesives enable the direct attachment of microchips to heat sinks or other thermal management solutions, improving heat dissipation. This direct thermal path enhances the device’s ability to dissipate heat efficiently, enabling compact and thermally efficient electronic systems design.
- Mechanical stability:Flip chip adhesives offer excellent mechanical strength and reliability, ensuring secure and robust connections between microchips and substrates. This stability is critical in mechanical stress, vibration, or thermal cycling applications, where the adhesive must maintain its bond integrity.
- Process compatibility:Flip chip adhesives are compatible with various manufacturing processes, including reflow soldering, thermocompression bonding, and underfilling. This compatibility facilitates their integration into existing production lines and allows for efficient and cost-effective assembly of flip chip packages.
- Broad substrate compatibility:Flip chip adhesives offer compatibility with various substrates such as silicon, glass, ceramics, and organic materials. This versatility enables their use in diverse applications across consumer electronics, automotive, medical devices, and telecommunications industries.
- Reliability testing and standards:Flip chip adhesives undergo stringent reliability testing to ensure their performance and longevity under various environmental conditions. Standards and guidelines, such as those set by the IPC (Association Connecting Electronics Industries), govern the use of flip chip adhesives and assure their reliability.
These properties make flip chip adhesives an indispensable solution for enabling miniaturization and enhancing the performance of microelectronic devices in various industries.
Die to Attach Adhesives: Bonding Semiconductors to Substrates
Die-to-attach adhesives are crucial in bonding semiconductors or microchips to substrates, ensuring reliable electrical and mechanical connections. These specialized adhesives offer unique properties that enable precise placement, strong bonding, and efficient heat transfer between the die and the substrate. Here are key points highlighting the significance of die-attached adhesives:
- Precise placement:Die attach adhesives allow for accurate positioning and alignment of the semiconductor die onto the substrate. This specific placement ensures proper electrical connections and optimal microchip performance within the assembly.
- Muscular bond strength:Die-to-attach adhesives provide excellent bond strength, ensuring a secure and reliable attachment between the die and the substrate. This strong bond withstands mechanical stress, temperature cycling, and environmental factors, enhancing the durability and longevity of the semiconductor package.
- Efficient heat transfer:Die-to-attach adhesives are formulated with high thermal conductivity to facilitate heat transfer from the die to the substrate or heat sink. This property helps dissipate the heat generated by the microchip, preventing overheating and maintaining optimal operating conditions.
- Compatibility with different substrates:Die-to-attach adhesives exhibit compatibility with various substrates commonly used in semiconductor packaging, including ceramics, metals, and organic materials. This versatility allows their use in diverse applications across industries such as electronics, automotive, telecommunications, and medical devices.
- Electrical insulation:Many die-attached adhesives offer excellent electrical insulation properties, ensuring proper electrical isolation between the semiconductor die and the substrate. This insulation prevents electrical shorts and promotes the reliable operation of the microchip within the package.
- Process compatibility:Manufacturers design die-to-attach adhesives to be compatible with different manufacturing processes, including screen printing, dispensing, or film lamination. This compatibility facilitates their integration into existing production lines, enabling efficient and cost-effective assembly of semiconductor packages.
- Bond line thickness control:Die-to-attach adhesives allow precise bond line thickness control between the die and the substrate. This control ensures uniformity and consistency in the bonding process, resulting in reliable electrical and mechanical connections.
- Adherence to industry standards:Die to attach adhesives adhere to industry standards and specifications, ensuring their reliability and performance. These standards, such as those set by the IPC (Association Connecting Electronics Industries), provide guidelines and quality assurance for die attach processes.
Underfill Adhesives: Protecting Against Thermal Stress
Underfill adhesives protect electronic components, particularly flip-chip packages, against thermal stress and mechanical failures. These specialized adhesives offer unique properties that provide reinforcement and improve the reliability of solder joints between the chip and the substrate. Here are key points highlighting the significance of underfill adhesives in protecting against thermal stress:
- Stress mitigation:Designers create underfill adhesives to mitigate the effects of thermal stress on flip-chip packages. They fill the voids between the chip and the substrate, reducing the mechanical stress caused by the difference in coefficients of thermal expansion (CTE) between the materials. This stress mitigation prevents the formation of cracks and delamination that can lead to electrical failures.
- Enhanced reliability:Underfill adhesives enhance the overall reliability of flip-chip packages by strengthening the solder joints. The adhesive creates a robust bond between the chip and the substrate, improving mechanical and thermal cycling, vibration, and shock resistance.
- Improved thermal management:Underfill adhesives have high thermal conductivity, allowing them to efficiently transfer heat from the chip to the substrate or heat sink. This property helps dissipate the heat generated by the chip, reducing the risk of overheating and maintaining optimal operating temperatures.
- Protection against moisture and contaminants:Underfill adhesives provide a protective barrier that seals the solder joints and prevents the ingress of moisture, contaminants, or corrosive agents. This protection enhances the reliability and longevity of the flip chip package, especially in harsh environments or high humidity conditions.
- Reduces solder fatigue:Underfill adhesives lessen the strain on the solder joints caused by thermal expansion and contraction. By absorbing and distributing the mechanical stress, they help to minimize solder fatigue, prolonging the operational lifespan of the package.
- Process compatibility:Underfill adhesives are compatible with various assembly processes, including capillary underfill, no-flow underfill, and molded underfill. This compatibility allows for their integration into existing production lines, enabling efficient and cost-effective manufacturing of flip chip packages.
- Adherence to industry standards:Underfill adhesives adhere to industry standards and specifications, ensuring their reliability and performance. These standards, such as those set by the IPC (Association Connecting Electronics Industries), provide guidelines and quality assurance for underfill processes.
- Materials compatibility:Underfill adhesives exhibit compatibility with different substrates and encapsulants used in flip chip packaging, including silicon, ceramics, and various polymers. This versatility enables their use in diverse electronic applications.
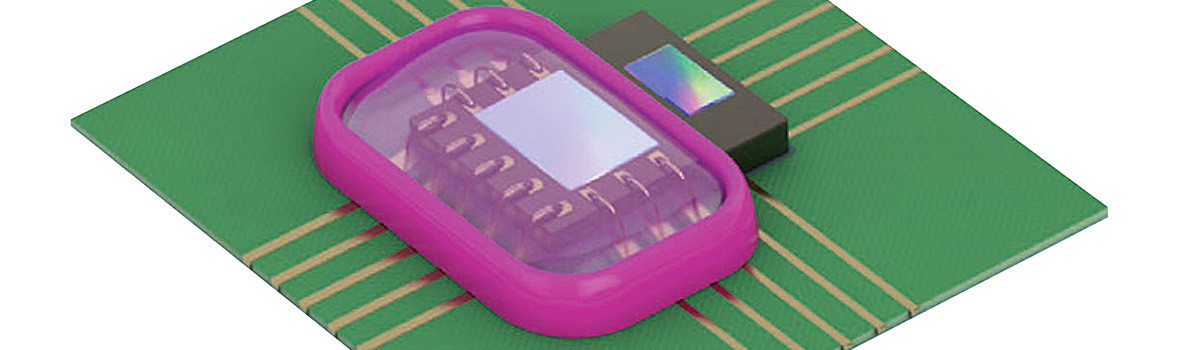
Wire Bonding Adhesives: Ensuring Reliable Electrical Connections
Wire bonding adhesives play a crucial role in the electronics industry by ensuring reliable electrical connections between semiconductor devices and their packages or substrates. These specialized adhesives offer unique properties that facilitate the bonding of fine wires to pads or leads, providing secure electrical interconnections. Here are key points highlighting the significance of wire-bonding adhesives in ensuring reliable electrical connections:
- Wire attachment:Wire bonding adhesives extend fine wires, typically made of gold, aluminum, or copper, to the designated bonding pads or leads on semiconductor devices. This attachment ensures proper electrical conductivity and signal transmission within the electronic assembly.
- Bond strength:Wire bonding adhesives provide strong adhesion between the wire and the bonding pad, forming a reliable and durable electrical connection. This bond strength withstands mechanical stress, temperature variations, and vibration, ensuring the integrity and longevity of the wire bond.
- Electrical conductivity:Formulators create wire bonding adhesives to have excellent electrical conductivity, minimizing resistance in the wire bond connection. This conductivity ensures efficient signal transfer and reliable electrical performance of the semiconductor device.
- Thermal stability:Wire bonding adhesives exhibit high thermal stability, allowing them to withstand the temperature variations encountered during subsequent assembly processes such as encapsulation or reflow soldering. This stability ensures the longevity of the wire bond connection and prevents thermal failures.
- Compatibility with different substrates:Wire bonding adhesives are compatible with various substrate materials used in semiconductor packaging, including ceramics, metals, and organic materials. This compatibility allows for their use in diverse applications across industries such as electronics, automotive, telecommunications, and medical devices.
- Bond line control:Wire bonding adhesives enable precise bond line thickness control between the wire and the bonding pad. This control ensures uniformity and consistency in the wire bonding process, contributing to reliable electrical connections and consistent performance.
- Process compatibility:Designers ensure that wire bonding adhesives are compatible with different wire bonding techniques, including ball and wedge bonding. This compatibility facilitates integration into existing production lines and provides efficient and cost-effective wire bonding processes.
- Adherence to industry standards:Wire bonding adhesives adhere to industry standards and specifications, ensuring their reliability and performance. These standards, such as those set by the IPC (Association Connecting Electronics Industries), provide guidelines and quality assurance for wire bonding processes.
Encapsulants: Protecting Sensitive Components
Encapsulants play a critical role in protecting sensitive components in various industries, particularly electronics. These specialized materials provide a protective barrier around delicate components, shielding them from external factors and ensuring long-term reliability. Here are key points highlighting the significance of encapsulants in protecting sensitive components:
- Environmental protection:Encapsulants create a protective enclosure around sensitive components, safeguarding them against moisture, dust, dirt, and other environmental contaminants. This protection is crucial in harsh or challenging operating conditions, preventing corrosion, electrical shorts, or performance degradation.
- Mechanical protection:Encapsulants provide mechanical support and reinforcement to fragile components, enhancing their resistance to physical stress, vibration, and impact. This protection reduces the risk of mechanical failures and extends the operational lifespan of the parts.
- Thermal management:Encapsulants with high thermal conductivity help dissipate heat generated by sensitive components, ensuring optimal operating temperatures and preventing overheating. This thermal management capability enhances the overall performance and reliability of the components.
- Electrical insulation:Encapsulants offer excellent electrical insulation properties, providing electrical isolation and preventing electrical shorts or interference between components. This insulation ensures the proper functioning and integrity of sensitive electronic circuits.
- Chemical resistance:Formulators can formulate encapsulants to exhibit chemical resistance, protecting sensitive components from exposure to corrosive substances or aggressive chemicals. This resistance enhances the longevity and reliability of the features, particularly in industries with demanding chemical environments.
- Vibration and shock resistance:Encapsulants with vibration and shock resistance properties help protect sensitive components from mechanical vibrations or sudden impacts. This resistance minimizes the risk of disconnection, damage, or performance degradation due to external forces.
- Process compatibility:Designers ensure encapsulants are compatible with various manufacturing processes, including potting, encapsulation, or molding. This compatibility facilitates their integration into existing production lines, providing efficient and cost-effective encapsulation of sensitive components.
- Adherence to industry standards:Encapsulants adhere to industry standards and specifications, ensuring their reliability and performance. These standards, such as those set by the IPC (Association Connecting Electronics Industries), provide guidelines and quality assurance for encapsulation processes.
- Materials compatibility:Encapsulants exhibit compatibility with different substrate materials and component types, including silicon, ceramics, metals, and polymers. This versatility allows their use in diverse applications across industries, including electronics, automotive, aerospace, and medical devices.
Adhesive Dispensing Techniques: Precision and Efficiency
Adhesive dispensing techniques play a crucial role in various industries, ensuring precise and efficient application of adhesives for bonding and assembly processes. These techniques utilize specialized equipment and methods to control the dispensing of adhesives, providing accuracy, consistency, and optimization of adhesive usage. Here are key points highlighting the significance of adhesive dispensing techniques in achieving precision and efficiency:
- Controlled adhesive flow:Adhesive dispensing techniques enable precise control of adhesive flow, ensuring accurate placement and distribution of the adhesive material. This control allows consistent and uniform coverage, minimizing waste and optimizing adhesive usage.
- Dispensing precision:These techniques offer high precision in depositing adhesives, allowing for fine lines, dots, or specific patterns as required by the application. This precision ensures proper adhesion, component alignment, and overall product quality.
- Speed and efficiency:Designers develop adhesive dispensing techniques to deliver adhesives quickly and efficiently, reducing production time and increasing productivity. High-speed dispensing systems can apply adhesives rapidly, keeping up with demanding production requirements.
- Repeatable and consistent results:By utilizing programmable parameters and automated systems, adhesive dispensing techniques provide repeatable and consistent results across multiple production runs. This consistency ensures the reliability and quality of the adhesive bond in various applications.
- Dispensing versatility:These techniques can accommodate various adhesive types, viscosities, and materials, including liquid adhesives, pastes, gels, or sealants. This versatility allows for the use of different adhesive formulations to suit specific bonding requirements.
- Customizable dispensing patterns:Adhesive dispensing techniques offer the flexibility to create customized dispensing patterns to match the application’s unique requirements. This customization ensures optimal adhesive placement, coverage, and bond strength, tailored to specific design specifications.
- Process integration:Manufacturers can integrate adhesive dispensing techniques into existing manufacturing processes, such as automated assembly lines or robotic systems. This integration allows seamless coordination between adhesive dispensing and other production steps, improving overall workflow and efficiency.
- Reduces human error:By automating the adhesive dispensing process, these techniques minimize human error and variability, resulting in the consistent and reliable adhesive application. This reduction in human error enhances product quality and reduces the risk of adhesive-related defects.
- Adherence to industry standards:Adhesive dispensing techniques comply with industry standards and guidelines, ensuring adherence to specific quality and performance requirements. These standards provide assurance of reliable adhesive dispensing processes and the resulting bond integrity.
Reliability Testing: Assessing Adhesive Performance
Reliability testing is a crucial step in assessing the performance of adhesives. Adhesives are vital in various industries, from automotive and aerospace to electronics and construction. The reliability of a sealant is critical to ensure that bonded materials or components maintain their integrity under different operating conditions. This article will discuss the importance of reliability testing and some key aspects to consider.
Reliability testing involves subjecting adhesive bonds to rigorous tests to evaluate their performance and durability. The goal is to simulate real-world conditions and determine how well the adhesive will hold up over time. This type of testing provides valuable insights into the long-term behavior of bonds and helps identify potential weaknesses or failure modes.
One important aspect of reliability testing is assessing the adhesive’s strength and bond integrity. This can be done through tensile strength, shear strength, and peel strength tests. Tensile strength tests measure the maximum load a bonded joint can withstand before breaking, while shear strength tests evaluate the resistance to sliding forces. Peel strength tests assess the adhesive’s ability to resist separation between bonded surfaces. These tests help determine whether the adhesive can withstand the expected stresses and forces in its intended application.
Another critical factor in reliability testing is the adhesive’s resistance to environmental conditions. Adhesives may be exposed to temperature fluctuations, humidity, UV radiation, chemicals, or mechanical vibrations. Accelerated aging tests can be performed to evaluate the adhesive’s performance under these conditions over an extended period. These tests help predict the adhesive’s long-term stability and identify any potential degradation or loss of performance.
Furthermore, reliability testing should also consider the impact of different substrate materials on adhesive performance. Adhesives may need to bond to various surfaces, including metals, plastics, composites, or glass. Compatibility tests can be conducted to assess the adhesive’s effectiveness on different substrates and evaluate any potential issues related to adhesion or compatibility with specific materials.
In addition to these tests, evaluating the adhesive’s resistance to dynamic loading and cyclic fatigue is essential. Adhesives may experience repetitive loads or vibrations during their lifetime, especially in applications such as automotive or aerospace. Fatigue tests help assess how well the adhesive withstands these cyclic stresses without compromising its bond strength or integrity.
Reliability testing should also include considerations for manufacturing and application processes. Curing time, temperature, and surface preparation techniques can significantly influence the adhesive’s performance. Therefore, it is crucial to simulate these conditions during testing to ensure that the adhesive meets the requirements of the intended application.
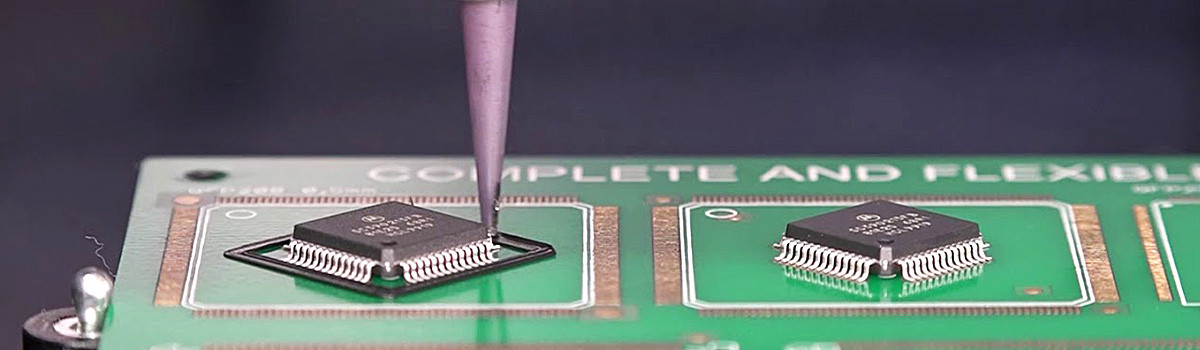
Environmental Considerations in Microelectronics Adhesives
Environmental considerations play a crucial role in developing and using adhesives for microelectronics applications. Microelectronics, which encompass various devices such as integrated circuits, sensors, and electronic components, require adhesives that provide reliable bonding and meet specific environmental requirements. This article will discuss the key environmental considerations associated with microelectronics adhesives.
One of the primary environmental considerations is the thermal stability of adhesives. Microelectronics often operate in demanding thermal environments, experiencing temperature fluctuations and high operating temperatures. Adhesives used in these applications must withstand these conditions without degrading or losing their bonding properties. Thermal cycling and high-temperature aging tests are commonly performed to assess the adhesive’s stability and reliability under extreme temperatures.
Another important consideration is the adhesives’ resistance to humidity and moisture. Microelectronic devices are frequently exposed to humid environments or can encounter water during their lifespan. Moisture can cause corrosion, delamination, or electrical shorts, leading to failure. Therefore, adhesives with excellent moisture resistance properties are essential. Moisture absorption and humidity aging tests can be conducted to evaluate the adhesive’s ability to resist moisture ingress and maintain its performance over time.
Chemical resistance is also critical in microelectronics applications. Adhesives may come into contact with various chemicals during assembly, operation, or cleaning. It is crucial to ensure that the adhesive remains stable and does not undergo degradation or react with these chemicals, which could compromise the device’s performance. Chemical compatibility tests are performed to assess the adhesive’s resistance to specific chemicals and confirm its suitability for the intended application.
Additionally, the impact of environmental factors such as UV radiation or other forms of radiation should be considered. Adhesives used in outdoor or space applications may be exposed to UV radiation, which can degrade the adhesive over time. Radiation resistance tests can be conducted to evaluate the adhesive’s ability to withstand such environmental conditions without compromising its performance or integrity.
Furthermore, environmental considerations also extend to the manufacturing and disposal of microelectronics adhesives. Manufacturers must evaluate the environmental impact of the adhesive’s production process, including factors like energy consumption, waste generation, and hazardous substances. Adhesives manufactured with minimal environmental impact and comply with relevant regulations contribute to sustainable manufacturing practices.
Similarly, the disposal of microelectronics adhesives at the end of a device’s life cycle should be considered. Adhesives that are environmentally friendly and can be easily removed or recycled without causing harm to the environment are desirable. Developing adhesives with low toxicity and reduced environmental impact supports circular economy principles and responsible waste management.
Trends and Innovations in Microelectronics Adhesives
Microelectronics adhesives play a critical role in assembling and packaging electronic components, enabling reliable connections and protecting sensitive devices from environmental factors. As technology advances, microelectronics adhesives have seen several notable trends and innovations. This article will highlight some of these developments within a concise 450-word limit.
One significant trend in microelectronics adhesives is the demand for higher-performance materials to support the miniaturization of electronic devices. As electronic components become smaller and more complex, the adhesive materials must provide excellent adhesion strength, thermal conductivity, and electrical insulation properties. Manufacturers are developing adhesives with nanoscale fillers, such as graphene or carbon nanotubes, to enhance thermal conductivity and ensure efficient heat dissipation from electronic components. These advanced adhesives enable better device performance, reliability, and longevity.
Another key trend is the growing emphasis on environmentally friendly and sustainable adhesives. With increasing awareness of environmental concerns, there is a shift towards adhesives with reduced volatile organic compound (VOC) emissions and lower environmental impact. Manufacturers invest in developing adhesives based on renewable resources, such as bio-based polymers or water-based formulations. These eco-friendly adhesives meet regulatory requirements and offer improved worker safety and reduced waste generation during manufacturing processes.
Innovations in microelectronics adhesives also encompass new bonding techniques and assembly processes. One notable advancement is the development of conductive adhesives, eliminating the need for soldering in specific applications. Conductive adhesives, often based on nanoscale silver particles, provide reliable electrical connections, especially in flexible or temperature-sensitive substrates. This innovation offers advantages like lower processing temperatures, reduced thermal stress, and compatibility with thin, lightweight electronic devices.
Furthermore, there is a growing demand for adhesives with enhanced reliability in harsh operating conditions. The proliferation of electronics in automotive, aerospace, and industrial applications drives this requirement. Sealants with improved resistance to temperature extremes, humidity, vibration, and chemical exposure are being developed to ensure long-term performance and durability. These advanced adhesives enable electronics to withstand challenging environments, making them suitable for automotive sensors, avionics, and industrial control systems.
Lastly, the advent of 5G technology and the Internet of Things (IoT) has sparked the need for adhesives that can withstand high-frequency signals and enable efficient signal transmission. Adhesives with low dielectric constants and loss tangents are crucial for maintaining signal integrity and minimizing electromagnetic interference. Manufacturers are developing specialized adhesives that offer superior electrical properties while maintaining their adhesion and mechanical strength.
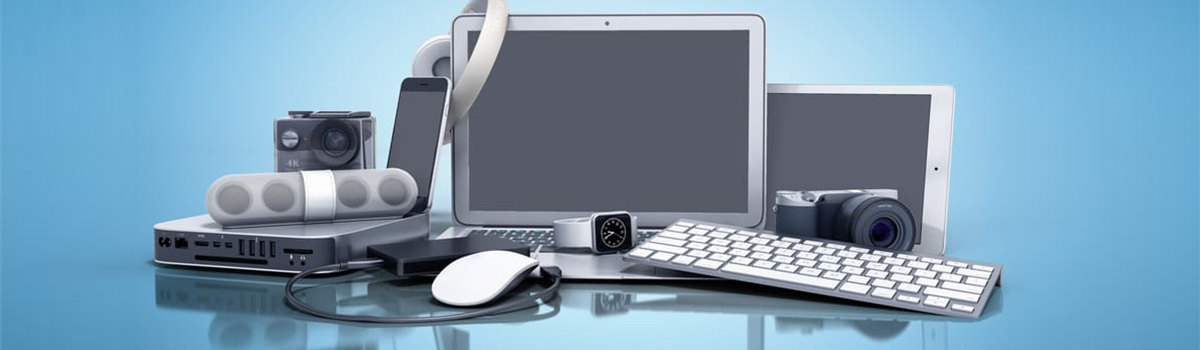
Application Areas: Automotive, Consumer Electronics, and More
Rapid technological advancements have revolutionized various industries, opening up new possibilities and enhancing our everyday lives. Among the numerous areas benefiting from these advancements, automotive and consumer electronics have emerged as key application sectors. In this blog post, we will explore the application areas of automotive, consumer electronics, and more, highlighting the transformative impact of technology in these industries.
Automotive
The automotive industry has witnessed remarkable transformations driven by technological advancements. Here are some key application areas:
- Autonomous Vehicles:Self-driving cars are at the forefront of automotive innovation, with companies investing heavily in developing this technology. Autonomous vehicles have the potential to improve road safety, enhance transportation efficiency, and redefine the concept of mobility.
- Electric Vehicles (EVs):The rise of electric vehicles is reshaping the automotive landscape, addressing environmental concerns, and reducing reliance on fossil fuels. With advancements in battery technology, charging infrastructure, and range capabilities, EVs are becoming more accessible and practical for consumers.
- Connected Cars:Connectivity has become a significant focus in the automotive sector. Connected cars enable the seamless integration of vehicles with intelligent devices, networks, and infrastructure. This connectivity enhances the driving experience, improves safety features, and allows real-time data collection and analysis.
Consumer Electronics
The consumer electronics industry constantly evolves to meet the demands of tech-savvy consumers. Here are some essential application areas:
- Smart Home Technology:Integrating technology into our homes has given rise to smart home devices. These technologies offer convenience, energy efficiency, and increased control over various home functions, from voice-activated assistants to smart thermostats and security systems.
- Wearable Devices:Wearable technology, including smartwatches, fitness trackers, and augmented reality (AR) glasses, has gained popularity. These devices enable users to track their health, receive notifications, access information, and interact with the digital world innovatively.
- Virtual Reality (VR) and Augmented Reality (AR): VR and AR technologies have expanded beyond gaming and entertainment. They find applications in various fields, including education, healthcare, architecture, and training simulations. VR immerses users in virtual environments, while AR overlays digital content onto the real world, enhancing experiences and offering practical solutions.
Healthcare
The healthcare industry is experiencing a profound impact from technological advancements. Here are a few application areas:
- Telemedicine:Telemedicine has emerged as a crucial solution for remote patient care, enabling virtual consultations, remote monitoring, and access to medical expertise from anywhere. It has become especially relevant during the COVID-19 pandemic, ensuring healthcare continuity while minimizing physical contact.
- Digital Health Solutions:From mobile health apps to wearable health trackers, digital health solutions empower individuals to monitor their well-being, track vital signs, manage chronic conditions, and access personalized healthcare information. These technologies enhance preventive care and facilitate better patient-doctor communication.
- Precision Medicine:Technological advancements have facilitated the development of precision medicine, tailoring treatment plans based on an individual’s genetic profile, lifestyle, and specific health characteristics. This approach allows for more targeted therapies, improved patient outcomes, and a shift toward personalized healthcare.
Future Prospects and Opportunities
The world constantly evolves, with new prospects and opportunities for various industries. From technological advancements to changing market dynamics, the future holds immense potential for growth and innovation. Let’s explore some of the key prospects and opportunities across different sectors:
Technological Advancements
- Rapid technological advancements such as artificial intelligence (AI), the Internet of Things (IoT), and 5G connectivity are reshaping industries and creating new opportunities.
- These technologies drive automation, data analytics, and connectivity, enabling businesses to improve efficiency, develop innovative products and services, and enhance customer experiences.
Sustainability and Green Initiatives
- The growing emphasis on sustainability and environmental responsibility presents significant business opportunities to develop eco-friendly solutions.
- Companies prioritizing renewable energy, waste reduction, recycling, and carbon footprint reduction can gain a competitive edge and appeal to environmentally conscious consumers.
Digital Transformation
- The digital transformation wave opens new avenues for businesses to streamline operations, enhance productivity, and deliver personalized experiences.
- Investing in digital technologies like cloud computing, big data analytics, and e-commerce can drive business growth and enable companies to adapt to evolving customer expectations.
Healthcare and Life Sciences
- The healthcare and life sciences sectors will experience significant growth as the aging population drives demand for innovative medical treatments and technologies.
- Advancements in personalized medicine, genomics, telemedicine, and wearable health devices offer exciting prospects for improving patient care and outcomes.
Renewable Energy
- The global shift towards renewable energy sources, driven by climate change concerns and energy security, creates opportunities in the solar, wind, and hydroelectric power sectors.
- Investing in renewable energy technologies, energy storage systems, and grid infrastructure can contribute to a sustainable future and generate economic growth.
Smart Cities
- Urbanization and the need for sustainable urban development create prospects for innovative city initiatives.
- Integrating IoT, smart grids, intelligent transportation systems, and efficient infrastructure can improve resource management, enhance the quality of life, and drive economic development in cities.
E-commerce and Digital Retail
- The rise of e-commerce and digital retail continues transforming how consumers shop, presenting opportunities for businesses to adapt and innovate.
- Companies that leverage online platforms, enhance their supply chain capabilities, and provide seamless omnichannel experiences can tap into a global customer base and drive growth.
Artificial Intelligence and Automation
- AI and automation technologies are revolutionizing industries by improving operational efficiency, enabling predictive analytics, and enhancing decision-making processes.
- Organizations that embrace AI and automation can streamline operations, optimize resource allocation, and unlock new business opportunities.
Cybersecurity
- The increasing reliance on digital technologies and interconnected systems creates a greater need for robust cybersecurity solutions.
- Companies specializing in cybersecurity services, threat intelligence, and data protection can capitalize on the growing demand for safeguarding sensitive information.
Collaboration and Partnerships
- Collaborative efforts between organizations across industries and borders offer innovation and market expansion opportunities.
- Partnerships facilitate the sharing of expertise, resources, and technologies, leading to the development of novel products and services.
Importance of Collaboration in Advancing Microelectronics Adhesives
Microelectronics play a critical role in our modern world, powering devices and technologies that have become integral to our daily lives. Collaboration among various stakeholders is crucial to ensure continuous advancement and innovation in microelectronics. In particular, collaboration in developing and improving microelectronics adhesives is of utmost importance. These adhesives are essential for bonding and protecting delicate electronic components, and their performance directly impacts the reliability, functionality, and longevity of microelectronic devices. Let’s explore the importance of collaboration in advancing microelectronics adhesives:
Technology Advancement
- Collaboration allows for pooling knowledge, expertise, and resources from different organizations, including adhesive manufacturers, electronic component manufacturers, research institutions, and end-users.
- By working together, stakeholders can share insights, exchange ideas, and collectively develop innovative solutions that address microelectronics’ evolving needs and challenges. This collaborative approach fosters technological advancement and drives the development of next-generation adhesives.
Tailored Formulations
- Microelectronics applications require specific adhesive formulations that meet stringent requirements such as electrical conductivity, thermal conductivity, low outgassing, and compatibility with sensitive components.
- Collaboration between adhesive manufacturers and electronic component manufacturers enables the development of tailored adhesive formulations that address the unique demands of microelectronics. We ensure their effectiveness by optimizing adhesives for performance, reliability, and compatibility with different electronic materials.
Process Optimization
- Effective collaboration allows for optimizing adhesive application processes, including dispensing, curing, and assembly techniques.
- By working together, adhesive manufacturers, equipment suppliers, and end-users can identify process challenges and develop innovative approaches to improve efficiency, reduce production costs, and enhance the overall manufacturing process of microelectronic devices.
Reliability and Quality
- Collaboration in developing microelectronics adhesives ensures the production of high-quality, reliable products.
- Through shared expertise and testing capabilities, stakeholders can perform extensive reliability testing, assess material compatibility, and validate adhesive performance under various environmental conditions.
- This collaborative effort helps identify potential failure modes, enhance adhesive performance, and ensure microelectronic devices’ long-term reliability and functionality.
Industry Standards and Regulations
- Collaboration among industry stakeholders is crucial for developing industry standards and regulations related to microelectronics adhesives.
- Working together, organizations can establish standard guidelines, performance metrics, and quality control measures that promote consistency, reliability, and safety in selecting, applying, and using microelectronics adhesives.
- These standards and regulations provide a framework for manufacturers, suppliers, and end-users to ensure compliance and meet the stringent requirements of the microelectronics industry.
Environmental Sustainability
- Collaboration can drive the development of environmentally sustainable microelectronics adhesives.
- By sharing research findings, knowledge, and best practices, stakeholders can work towards reducing the environmental impact of adhesives, such as minimizing the use of hazardous substances, promoting recyclability, and improving energy efficiency during manufacturing processes.
Conclusion
Microelectronics adhesives are the backbone of the ever-evolving world of miniaturized electronic devices. Their ability to provide strong bonds, electrical insulation, thermal management, and environmental protection makes them indispensable in ensuring the performance and reliability of microelectronic components. As technology advances, the development of innovative adhesive solutions and collaboration between manufacturers, researchers, and end-users will be crucial in meeting the growing demands and challenges of the microelectronics industry. By harnessing the potential of microelectronics adhesives, we can pave the way for even smaller, more efficient, and reliable electronic devices that power our modern world.