Magnet Bonding Adhesive
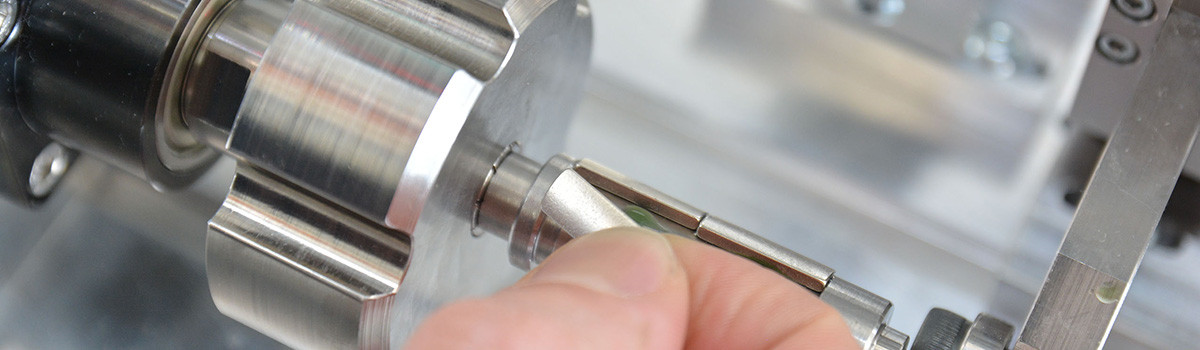
Introduction: Magnet bonding adhesive, also known as magnetic glue or magnet adhesive, is a type of adhesive that is used to bond magnets to a variety of surfaces. It has become increasingly popular due to its unique properties that allow for easy installation and strong hold. In this article, we will delve into the world of magnet bonding adhesive and explore its features, benefits, applications, and more.
What is Magnet Bonding Adhesive?
Magnet bonding adhesive is a type of adhesive that is used to connect magnets to different surfaces. This adhesive is specifically designed to provide a solid and durable bond between the magnet and the surface it is attached to.
The adhesive is typically a two-part epoxy mixed and applied to the magnet and the surface. The epoxy cures over time, creating a permanent bond between the two objects.
Magnet bonding adhesive is commonly used in various industries, including automotive, electronics, and manufacturing. It is often used to attach magnets to metal surfaces, such as motors or speakers, but it can also be used to adhere magnets to non-metal surfaces, such as plastic or glass.
When using magnet bonding adhesive, it is essential to follow the manufacturer’s instructions carefully to ensure a proper bond and to ensure safety precautions are taken.
How does Magnet Bonding Adhesive work?
Magnet bonding adhesive, or magnetic glue or magnet adhesive, is used to bond magnets to other materials. The adhesive uses a two-part system, typically consisting of a resin and a hardener, that is mixed together just before use.
The resin and hardener combine to form a strong, durable polymer that can attach magnets to various surfaces. When the adhesive is applied to the attraction, it creates a chemical bond between the two materials that are difficult to break.
The key to the effectiveness of magnet bonding adhesive is its ability to create a strong, permanent bond between the magnet and the material it is attached to. This is achieved through chemical bonding and physical adhesion, which create a solid bond to hold the magnet in place.
Overall, magnet bonding adhesive is a reliable and effective way to attach magnets to various surfaces, providing a strong, permanent bond that can withstand the rigors of daily use.
Types of Magnet Bonding Adhesive
There are several types of adhesive used for magnet bonding. Some of the most common types include:
- Two-part epoxy: This is a popular adhesive for bonding magnets because it creates a strong bond. It can connect attractions to various surfaces, including metal, plastic, and wood.
- Cyanoacrylate (super glue): This fast-drying adhesive creates a strong bond between magnets and other materials. It works well for small interests and can be used on various surfaces.
- Acrylic adhesive: This adhesive is ideal for bonding magnets to non-metallic surfaces. It creates a strong bond and is often used in automotive and electronic applications.
- Silicone adhesive: This is flexible and can bond magnets to various surfaces, including plastic and rubber. It is often used in applications where vibration or movement is a concern.
- Polyurethane adhesive: This adhesive is known for its strength and durability. It can be used for bonding magnets to various surfaces and is often used in automotive and industrial applications.
Advantages of Magnet Bonding Adhesive
Magnet bonding adhesive is a type of adhesive that is used to connect magnets to various surfaces. Some advantages of magnet bonding adhesive include the following:
- Strong Bonding: Magnet bonding adhesive provides a strong bond between the magnet and the surface it is being attached to, making it ideal for applications where a secure hold is necessary.
- Easy Application: Magnet bonding adhesive is easy to apply and can be used on various surfaces, including metals, plastics, and ceramics.
- Versatility: Magnet bonding adhesive can be used with many magnet types, including neodymium, ceramic, and samarium cobalt magnets.
- Durability: Magnet bonding adhesive is resistant to water, heat, and most chemicals, making it ideal for harsh environments.
- Cost-effective: Magnet bonding adhesive is a cost-effective solution compared to other methods of magnet attachment, such as mechanical fasteners or welding.
- Aesthetically Pleasing: Magnet bonding adhesive creates a clean, seamless appearance as it is invisible, leaving no visible fixings or holes on the magnet or the surface.
- Enhanced Performance: Magnets bonded with this adhesive have higher shock and vibration resistance and improved magnetic field strength compared to traditional adhesive bonding.
Magnet bonding adhesive is an excellent solution for many applications where strong, durable, and reliable magnet attachment is needed.
Disadvantages of Magnet Bonding Adhesive
Magnet bonding adhesive, used to attach magnets to various surfaces, has some disadvantages that should be considered before use. Here are a few:
- Limited bonding strength: Magnet bonding adhesives may not have the same strength as other adhesives. This is because the adhesive needs to allow for the magnetic field to pass through, which can affect its ability to hold the magnet in place.
- Limited temperature range: Magnet bonding adhesive may have a narrow temperature range, affecting its ability to hold the magnet in place. High temperatures can cause the adhesive to soften or break down, while low temperatures can cause it to become brittle.
- Limited chemical resistance: Magnet bonding adhesive may not resist certain chemicals, such as solvents, which can cause the adhesive to break down or lose its bonding strength.
- Surface preparation required: To ensure proper adhesion, the surface to which the magnet bonding adhesive is applied must be clean, dry, and debris-free. This may require additional preparation time and effort.
- Limited application options: Magnet bonding adhesive may not be suitable for all applications. For example, it may need to work better on uneven, curved, or textured surfaces.
While magnet bonding adhesive can be a valuable tool for attaching magnets to surfaces, some applications may have better choices. It’s essential to consider the project’s specific needs and the adhesive’s limitations before use.
Applications of Magnet Bonding Adhesive
Magnet bonding adhesive has several applications across various industries. Some of the standard applications of magnet bonding adhesive are:
- Automotive Industry: Magnet bonding adhesive is used in the automotive industry for various applications, including attaching trim pieces, emblems, and badges to the car’s body. It also attaches sensors and other electronic components to the vehicle.
- Electronics Industry: Magnet bonding adhesive is used in the electronics industry to attach magnets to electronic components such as speakers, microphones, and motors.
- Medical Industry: Magnet bonding adhesive is used in the medical industry for attaching medical devices such as prosthetic limbs, hearing aids, and pacemakers.
- Advertising Industry: Magnet bonding adhesive is used in the advertising industry for attaching promotional magnets to surfaces such as cars, refrigerators, and other metal surfaces.
- Aerospace Industry: Magnet bonding adhesive is used in the aerospace industry for attaching sensors and other electronic components to spacecraft and satellites.
- Industrial Applications: Magnet bonding adhesive is used in industrial applications to attach magnets to surfaces such as metal sheets, pipes, and conveyor belts.
Overall, magnet bonding adhesive has a wide range of applications in various industries where the need to attach magnets to surfaces is required.
Automotive Industry and Magnet Bonding Adhesive
Magnet bonding adhesive, also known as magnetic glue, is a type of adhesive that is used to bond magnets to various surfaces in the automotive industry. It is a popular alternative to traditional mechanical fastening methods because it gives a stronger bond and a cleaner, more aesthetically pleasing appearance.
In the automotive industry, magnet bonding adhesive is used to bond magnets to various surfaces, including metal, plastic, and glass. One common application is in manufacturing electric motors, where magnets generate the electromagnetic fields that drive the motor. Magnet bonding adhesive is also used to produce speakers, sensors, and other electronic components that require magnets.
One advantage of using magnet bonding adhesive in the automotive industry is that it can help reduce the vehicle’s weight. Magnets are lighter than traditional mechanical fasteners, such as bolts and screws. In addition, using magnet bonding adhesive can also help reduce the overall size of the vehicle, as it allows for more compact and efficient designs.
Another advantage of using magnet bonding adhesive is that it can improve the durability and longevity of the vehicle. This is because the adhesive creates a strong, permanent bond between the magnet and the surface, which helps to prevent the interest from becoming dislodged or damaged over time.
Magnet bonding adhesive has become increasingly popular in the automotive industry due to its numerous benefits, including improved efficiency, reduced weight, and increased durability. As a result, it will likely continue to be used in producing a wide range of automotive components.
Electronics Industry and Magnet Bonding Adhesive
The electronics industry relies heavily on adhesives for bonding, sealing, and insulating components. Magnet bonding adhesive is used in electronics to connect attractions to various substrates.
Magnet bonding adhesives are typically two-component, room-temperature-curing epoxy adhesives. They are designed to provide strong, durable bonds between magnets and substrates such as metal, plastic, and ceramic. The adhesives are formulated to provide excellent adhesion to the magnet surface and the substrate and high strength and resistance to environmental factors such as temperature, humidity, and chemicals.
One of the main advantages of magnet-bonding adhesives is that they allow for the precise placement of magnets on substrates. This is particularly important in the electronics industry, where small and accurate components are often used. The adhesives can also help reduce electronic devices’ overall size and weight, as they eliminate the need for mechanical fasteners such as screws or clips.
However, it is essential to note that using adhesives in the electronics industry requires careful consideration of material compatibility, curing time, and environmental conditions. It is also necessary to ensure that the adhesive is applied correctly and that the bond strength meets the required specifications.
Overall, magnet-bonding adhesives play a critical role in the electronics industry by providing strong and durable bonds between magnets and substrates, helping to improve the performance and reliability of electronic devices.
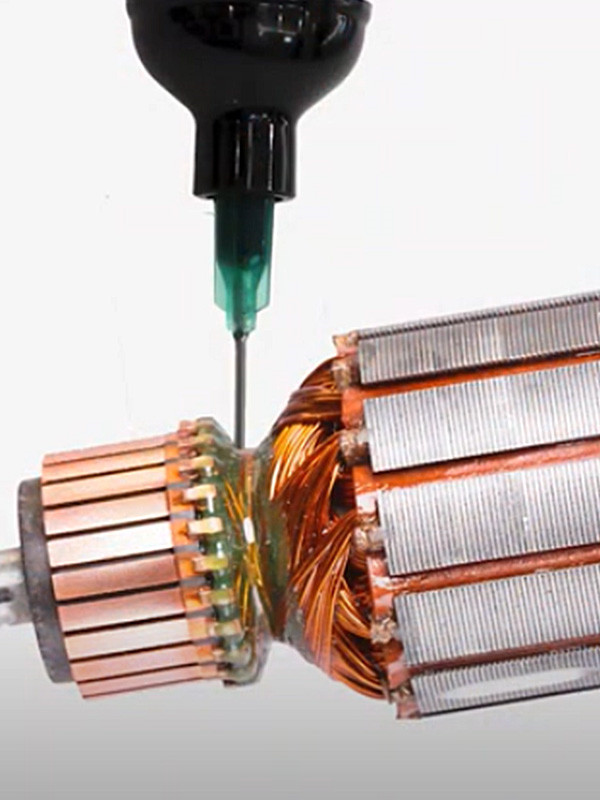
Medical Industry and Magnet Bonding Adhesive
Magnet-bonding adhesives are becoming increasingly popular in the medical industry due to their ability to securely bond and hold small medical devices in place. These adhesives are commonly used in applications such as pacemakers, hearing aids, and drug delivery systems.
One of the critical benefits of magnet-bonding adhesives is their ability to withstand harsh environmental conditions, such as exposure to bodily fluids and heat. They can also maintain their adhesive properties over long periods, which is essential in medical applications where devices need to remain securely in place for extended periods.
Another advantage of magnet-bonding adhesives is that they can be designed to be biocompatible, which means they do not cause any harm or adverse reactions when they come into contact with living tissue. This is particularly important in medical applications where the adhesive is in direct contact with the body.
Overall, magnet bonding adhesives offer several advantages over traditional bonding methods in the medical industry, and their use is expected to increase as more medical device manufacturers adopt this technology.
Aerospace Industry and Magnet Bonding Adhesive
The aerospace industry relies heavily on advanced materials and technology to ensure the safety and efficiency of aircraft. One such material is magnet bonding adhesive, which is a type of adhesive that is used to bond magnets to various surfaces.
Magnet bonding adhesive is handy in the aerospace industry because it provides a robust and durable bond that can withstand the harsh conditions of flight. This type of adhesive can be used to bond magnets to a variety of surfaces, including metals, plastics, and composites.
One of the critical advantages of magnet bonding adhesive is that it can create lightweight, high-strength bonds. This is particularly important in the aerospace industry, where weight is a crucial factor in the design and operation of aircraft. By using lightweight materials and adhesives, engineers can reduce the plane’s overall weight, leading to improved fuel efficiency and performance.
In addition to its strength and durability, magnet bonding adhesive is also resistant to various environmental conditions, including temperature extremes, moisture, and vibration. This makes it an ideal choice for aircraft where these conditions are expected.
Overall, magnet bonding adhesive is an essential material in the aerospace industry, where it is used to create strong, durable, and lightweight bonds that help ensure aircraft safety and efficiency.
Construction Industry and Magnet Bonding Adhesive
Magnet bonding adhesives are commonly used in the construction industry for various applications. These adhesives provide a strong, durable bond between magnets and multiple surfaces, making them useful in many construction projects.
One of the most common uses of magnet-bonding adhesives in the construction industry is attaching signs and other decorative elements to metal surfaces. You can attach these items securely and easily without drilling or screws using a magnet bonding adhesive.
Another use of magnet bonding adhesives in construction is attaching metal studs to walls and ceilings. These adhesives provide a strong bond that can hold heavy loads, making them an ideal choice for construction projects requiring a strong and durable connection.
Magnet bonding adhesives can also be used to construct modular buildings and prefabricated structures. Builders can connect different system parts by using these adhesives, creating a sturdy and reliable final product.
In addition, magnet-bonding adhesives can be used to construct furniture and other interior elements. By using these adhesives, designers can create unique and innovative pieces that are functional and aesthetically pleasing.
Magnet bonding adhesives are a versatile and valuable tool in the construction industry. They provide a solid and durable bond for various applications, making them a popular choice among builders and designers.
Consumer Goods Industry and Magnet Bonding Adhesive
The consumer goods industry includes a wide range of products manufactured and sold to end-users, such as household appliances, electronics, personal care items, and toys. Magnet bonding adhesive is a type of adhesive commonly used in manufacturing consumer goods that incorporate magnets.
Magnet bonding adhesive is a type of adhesive that is formulated to bond magnets to various substrates, including metals, plastics, and ceramics. This adhesive is typically a two-part system that includes a resin and a hardener that are mixed together to create a robust and durable bond. The resin is often formulated with a high degree of flexibility to accommodate the expansion and contraction that occurs when the bonded materials are exposed to temperature changes.
In the consumer goods industry, magnet bonding adhesive is commonly used to manufacture products that incorporate magnets, such as speakers, motors, and magnetic closures on bags and purses. This adhesive is also used to manufacture toys that include interests, such as magnetic building blocks and games.
The use of magnet bonding adhesive in the consumer goods industry is driven by the need to create durable, reliable products that meet the end-users performance requirements. By using magnet bonding adhesive, manufacturers can develop products that can withstand the stresses and strains of everyday use and provide a high-performance level over a long period.
Factors to Consider when Choosing Magnet Bonding Adhesive
When choosing a magnet bonding adhesive, there are several factors to consider, including:
- Magnet type: Different magnet types (such as neodymium, ceramic, or samarium cobalt) require different adhesive properties to bond effectively.
- Surface preparation: The surface of the magnet and the substrate must be clean and free of contaminants, as this can affect the strength of the bond.
- Bond strength: The adhesive’s bond strength should be appropriate for the intended application. Factors such as temperature, shear, and tension must also be considered.
- Curing time: The adhesive’s curing time must be suitable for the application. Some adhesives require longer curing times than others; some can cure at room temperature, while others require elevated temperatures.
- Chemical compatibility: The adhesive must be compatible with both the magnet and the substrate, as some adhesives can react with certain materials, leading to failure.
- Environmental factors: The adhesive should withstand environmental factors such as moisture, UV exposure, and temperature fluctuations.
- Application method: The adhesive must be applied in a manner suitable for the application, such as a manual or automated application.
- Cost: The cost of the adhesive must be considered the application’s requirements and the desired performance.
Surface Preparation for Magnet Bonding Adhesive
When bonding magnets with adhesive, it is essential to have proper surface preparation to ensure a solid and durable bond. Here are some steps you can follow for surface preparation:
- Clean the surfaces: Use a solvent such as acetone or isopropyl alcohol to clean the surfaces where the adhesive will be applied. This will remove any dirt, oil, or other contaminants that could interfere with bonding.
- Sand the surfaces: Use sandpaper to roughen the surfaces slightly. This will create a better feeling for the adhesive to bond to. Be sure to use fine-grit sandpaper to avoid scratching the magnet.
- Wipe the surfaces: Use a clean, lint-free cloth to remove debris or dust after sanding. This will ensure pure consistency for bonding.
- Apply primer: Some adhesives require a primer to improve adhesion. Check the adhesive manufacturer’s instructions to see if a primer is necessary and follow their recommendations.
- Apply the adhesive: Apply the adhesive to one surface and then carefully align the magnet before pressing the two surfaces together. Follow the adhesive manufacturer’s instructions for curing time and temperature.
By following these steps, you can ensure a solid and durable bond between the magnets and the adhesive.
Handling and Storage of Magnet Bonding Adhesive
Proper handling and storage of magnet bonding adhesive are essential to ensure the quality and effectiveness of the adhesive. Here are some guidelines to follow:
- Storage Conditions: Magnet bonding adhesive should be stored in a cool, dry place at temperatures between 10°C and 25°C (50°F and 77°F). Avoid exposure to direct sunlight, heat sources, and humidity.
- Handling: When handling magnet bonding adhesive, wearing appropriate protective gear, such as gloves and safety glasses, is essential. Ensure the adhesive is not exposed to contaminants, such as dust, dirt, or grease.
- Mixing: Magnet bonding adhesive typically comes in two parts that must be mixed together before use. Follow the manufacturer’s instructions for the proper mixing ratio and method.
- Application: Apply the adhesive to the substrate surface bonded to the magnet. Use a clean applicator or brush to ensure a smooth, even application.
- Curing: Allow the adhesive to cure completely before subjecting it to any stress or load. The curing time will depend on the type of adhesive and the conditions in which it is applied.
Following these guidelines ensures that your magnet bonding adhesive will perform effectively and maintain its quality over time.
How to Apply Magnet Bonding Adhesive
Magnet bonding is a specialized adhesive used to bond magnets to different materials. Here are the steps to apply magnet bonding adhesive:
- Clean the surface: Thoroughly clean the surface where you will be bonding the magnet using a cleaning solvent or rubbing alcohol. This will remove any oils, dirt, or debris that could prevent the adhesive from bonding properly.
- Prepare the adhesive: Mix the magnet bonding adhesive according to the manufacturer’s instructions. Make sure you use the correct mixing ratio, as this will affect the strength of the bond.
- Apply the adhesive: Using a small brush, apply a thin layer to the surface where you will bond the magnet. Make sure you spread the adhesive evenly and cover the entire surface.
- Position the magnet: Carefully place the interest onto the adhesive. Make sure it is positioned correctly, as it will be difficult to reposition it once it has bonded.
- Apply pressure: Apply pressure to the magnet to ensure a strong bond. You can use a clamp or a heavy weight to hold the interest in place while the adhesive sets.
- Allow to dry: The adhesive will dry according to the manufacturer’s instructions. Depending on the adhesive and environmental conditions, this can take anywhere from a few hours to a full day.
- Test the bond: Once the adhesive is dry, test the bond by gently pulling on the magnet. If it feels secure, the bond is booming. If it comes loose, you may need to reapply or try a different type of adhesive.
Always follow the manufacturer’s instructions when using magnet bonding adhesive, and work in a well-ventilated area to avoid inhaling fumes.
Testing and Quality Control of Magnet Bonding Adhesive
Magnet bonding adhesives are used to bond magnets to various substrates. To ensure the adhesive’s quality, it is essential to perform testing and quality control measures. Here are some steps that can be taken:
- Adhesive Testing: The adhesive used for magnet bonding should be tested to ensure it meets the required specifications. This can be done by testing the adhesive’s tensile strength, shear strength, and other relevant properties. The adhesive’s properties should be tested using standardized procedures to ensure accurate and consistent results.
- Substrate Preparation: Before bonding the magnet, it is essential to prepare the substrate properly. The substrate should be free of dust, oil, and other contaminants that can affect the adhesive’s bond. The substrate surface should also be roughened or cleaned with a primer to improve adhesion.
- Magnet Placement: The magnet should be carefully placed on the substrate and held in position until the adhesive cures. The magnet’s work should be checked to ensure it is in the correct location, and the spacing between magnets should be consistent.
- Curing Time: The adhesive’s curing time should be carefully monitored to ensure it has fully cured before the magnet is used. The curing time can be affected by factors such as temperature and humidity, so following the manufacturer’s recommendations is essential.
- Quality Control: To ensure consistent and high-quality bonding, it is essential to implement quality control measures. This can include performing regular tests on samples of the bonded magnets to check for adhesion strength, consistency, and other properties.
By following these steps, you can ensure that the magnet bonding adhesive is high quality and that the bond between the magnet and substrate is solid and reliable.
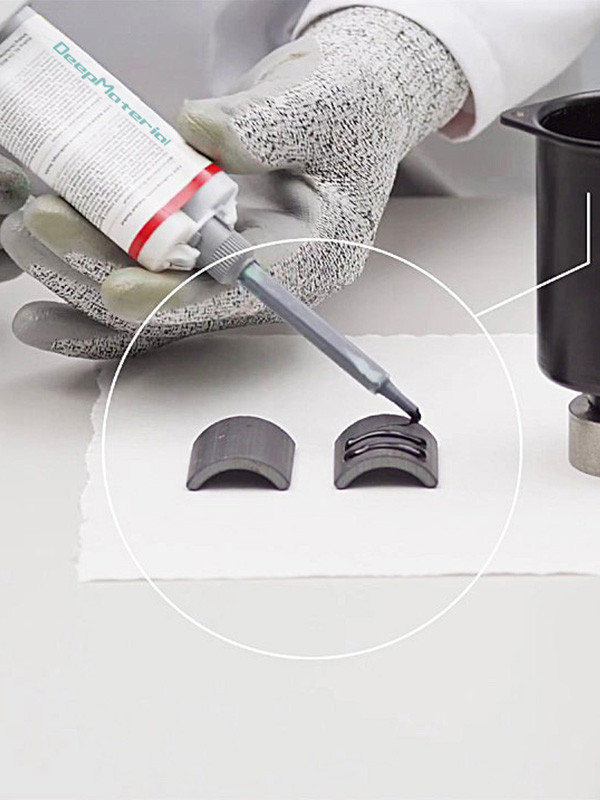
Durability and Longevity of Magnet Bonding Adhesive
The durability and longevity of magnet bonding adhesive depend on several factors, such as the type of adhesive used, the strength of the magnetic field, the temperature and humidity conditions, and the kind of surface the adhesive is applied to.
Generally, when using a high-quality magnet bonding adhesive, the bond should last long, even under extreme conditions. However, heat, moisture, and chemical exposure can weaken the bond over time, and repeated stress or mechanical forces on the bond can also cause it to fail.
To ensure the best possible bond durability and longevity, following the manufacturer’s guidelines for preparing, applying, and curing the adhesive is essential. Choosing an appropriate adhesive for the specific magnets and surfaces you work with is also necessary.
Regular maintenance and inspection of the bond can also help prolong its lifespan. This includes checking for any signs of damage, such as cracking or peeling, and repairing or replacing the adhesive as needed.
Factors Affecting the Performance of Magnet Bonding Adhesive
The performance of this adhesive is influenced by several factors, including:
- Surface preparation: The surface to which the magnet is bonded must be clean, dry, and free of any oils, dust, or other contaminants. Proper surface preparation is critical to achieving a solid bond.
- Temperature and humidity: The performance of magnet bonding adhesive is influenced by temperature and humidity. High temperatures and humidity can accelerate the curing process of the adhesive, while low temperatures and humidity can slow it down.
- Adhesive type: There are different types of magnet bonding adhesives available, including two-part epoxy adhesives, cyanoacrylate adhesives, and acrylic adhesives. The type of adhesive used can affect the bonding strength and durability.
- Magnet size and shape: The size and shape of the magnet can also affect the performance of the adhesive. Giant interests require more adhesive to strengthen bonds, while irregularly shaped magnets may require special handling or application techniques.
- Application method: The method of applying the adhesive can also affect the performance of the bond. Improper application, such as using too much or too little adhesive, can result in a weak bond or uneven distribution of the adhesive.
- Curing time: Magnet bonding adhesives require time to cure and achieve their full strength. Curing time can be affected by factors such as temperature, humidity, and the type of adhesive used.
- Environmental factors: The performance of magnet bonding adhesive can also be influenced by environmental factors such as exposure to sunlight, water, and chemicals. The adhesive should be chosen based on the intended use and the environmental conditions it will be exposed to.
Common Issues with Magnet Bonding Adhesive
Magnet bonding adhesive, or magnetic glue, connects attractions to various surfaces. While it is a valuable adhesive, some common issues can arise when using magnet-bonding adhesive. Some of these issues include:
- Inadequate Bond Strength: One of the most common issues with magnet bonding adhesive is inadequate bond strength. This can be caused by several factors, including insufficient adhesive coverage, improper surface preparation, or using the wrong adhesive for the job.
- Poor Adhesion to Certain Surfaces: Some surfaces are more challenging to bond magnets to than others. For example, non-metallic surfaces may require a particular adhesive or surface treatment to ensure proper adhesion.
- Premature Magnet Movement: Another common issue is early magnet movement before the adhesive can fully cure. This can be caused by improper application or insufficient curing time.
- Magnet Misalignment: If the magnets are not properly aligned during the bonding process, they may not function as intended. This can result in reduced magnetic strength or other performance issues.
- Temperature Sensitivity: Some magnet bonding adhesives are sensitive to temperature changes, affecting their performance. Choosing an appropriate adhesive for the intended use and environmental conditions is essential.
To avoid these common issues, choosing the suitable adhesive for the job is essential, as following the manufacturer’s instructions carefully and adequately preparing the surfaces to be bonded. It may also be helpful to perform a test bond before committing to a large-scale project to ensure proper adhesion and performance.
Safety Precautions for Magnet Bonding Adhesive
Magnet bonding adhesive is a type of adhesive used to bond magnets to various surfaces. When working with this adhesive, it is essential to take certain safety precautions to ensure that you do not harm yourself or others. Here are some safety precautions to keep in mind:
- Use protective equipment: When working with magnet bonding adhesive, wear protective equipment such as gloves, safety glasses, and respirators. This will protect you from any potential chemical or physical hazards.
- Proper ventilation: Ensure you are working in a well-ventilated area, preferably with a fume hood, to prevent inhalation of fumes from the adhesive.
- Read the label: Before using the adhesive, carefully read the label and follow the instructions for use, storage, and disposal.
- Store the adhesive properly in a cool, dry place, away from direct sunlight, heat sources, and incompatible materials. Keep the adhesive container tightly closed when not in use.
- Avoid skin contact: Avoid skin contact with the adhesive. In communication, wash the affected area thoroughly with soap and water. Seek medical attention if necessary.
- Handle with care: Handle the adhesive carefully and avoid spilling or splashing it. Clean up any spills immediately with a suitable absorbent material.
- Disposal: Dispose of the adhesive and its containers following local regulations. Do not pour the adhesive down the drain or throw it in the trash.
Following these safety precautions allows you to work with magnet-bonding adhesive safely and effectively.
Environmental Considerations of Magnet Bonding Adhesive
Magnet bonding or magnetic adhesive is a glue used to attach magnets to surfaces. While magnet-connecting adhesive can be a valuable and convenient solution for magnet applications, it is essential to consider its environmental impact.
One potential concern is the disposal of the adhesive. If not properly disposed of, the bond could end up in landfills or waterways, harming wildlife or contaminating the environment. Some types of magnet bonding adhesive may also contain hazardous chemicals that could risk human health if not handled properly.
Additionally, the manufacturing and transportation of magnet bonding adhesive could have environmental impacts. The production process may generate emissions or waste, and the adhesive transport could contribute to greenhouse gas emissions and other environmental impacts.
To mitigate these concerns, choosing a magnet-bonding adhesive designed with environmental considerations in mind is essential. Look for bonds made with non-toxic, biodegradable, or recyclable materials. You can also consider the manufacturing and transportation processes of the adhesive, such as choosing a product that is produced using renewable energy sources or shipped using carbon-neutral methods.
Proper disposal of magnet bonding adhesive is also essential. Follow the instructions provided by the manufacturer for removal, and consider recycling the adhesive or disposing of it at a hazardous waste disposal facility if necessary.
Comparison of Magnet Bonding Adhesive to Other Adhesives
Magnet bonding adhesive is a type of adhesive specifically designed for connecting magnets. However, it is essential to note that many different types of adhesives are available on the market, each with its strengths and weaknesses. Here is a comparison of magnet bonding adhesive to other common types of adhesives:
- Epoxy: Epoxy is a powerful adhesive often used for bonding metals, plastics, and other materials. It can also bond magnets, but magnet bonding adhesive may be less effective. Epoxy typically requires mixing two components before use and can take several hours to cure.
- Cyanoacrylate (super glue): Cyanoacrylate is a fast-drying adhesive commonly used for bonding plastics, rubber, and other materials. It can also bond magnets but may be weaker than magnet-bonding adhesive.
- Acrylic: Acrylic adhesive is a type of adhesive that is often used for bonding plastics and other materials. It can also bond magnets but may not be as effective as the magnet-bonding adhesive.
- Silicone: Silicone adhesive is a flexible adhesive often used for bonding materials requiring some flexibility. It can also bond magnets but may be weaker than magnet-bonding adhesive.
Overall, magnet bonding adhesive is designed for connecting attractions and is likely the most effective. However, other types of adhesives can also be used to bond magnets, depending on the specific application and requirements.
Cost of Magnet Bonding Adhesive
The cost of magnet bonding adhesive can vary widely depending on the type and brand, the quantity needed, and the supplier or retailer. Generally, prices range from a few dollars to hundreds per unit or package.
You should check with a supplier or retailer directly or search for prices online to get a more accurate estimate. Remember that the cheapest option may only sometimes be the best in quality and performance. Choosing an adhesive that is suitable for your specific application and meets any necessary standards or requirements is essential.
Maintenance and Repair of Magnet Bonding Adhesive
Magnet bonding adhesives are commonly used in various industries, including electronics, automotive, aerospace, and medical. These adhesives are designed to bond magnets to other materials, such as metal or plastic, and provide a strong, permanent bond.
Proper maintenance and repair of magnet bonding adhesives are essential to ensure the longevity and reliability of the bond. Here are some tips on how to maintain and repair magnet bonding adhesives:
- Regular Inspection: Regular bond inspection is essential to detect any signs of wear or damage. This can include cracks, chips, or other signs of damage to the adhesive or the magnet. If any damage is detected, it should be repaired immediately to prevent further damage to the bond.
- Cleaning: Proper cleaning of the bonding surfaces is essential to ensure a strong bond. The characters should be clean and free from dirt, grease, or other contaminants before applying the adhesive.
- Proper Storage: Proper adhesive storage is essential to ensure its effectiveness. The adhesive should be stored in a cool, dry place and away from heat sources or direct sunlight.
- Repair: If any damage is detected, it is essential to repair the bond as soon as possible. The damaged area should be cleaned and dried, and a new adhesive layer should be applied. Following the manufacturer’s instructions for application and curing times is essential.
- Replacement: If the bond cannot be repaired or the adhesive has reached the end of its useful life, the magnet and adhesive should be removed and replaced with a new bond.
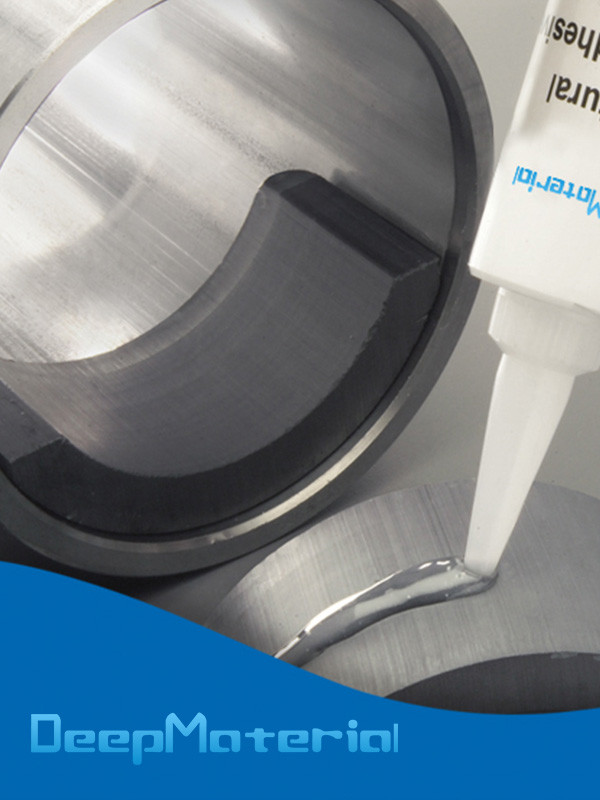
Innovations and Advancements in Magnet Bonding Adhesive
Magnet-bonding adhesives have been gaining popularity in various industries, such as automotive, electronics, and renewable energy, due to their ability to bond magnets to multiple substrates. Recent advancements and innovations in appeal bonding adhesive technology have improved performance, efficiency, and durability. Some of these advancements include:
- Nanotechnology: Magnet bonding adhesives incorporating nanotechnology can enhance the strength and adhesion of the adhesive. Nanoparticles can be added to the adhesive to increase its bonding strength and reduce the risk of delamination.
- UV-curable adhesives: These adhesives cure quickly when exposed to UV light, resulting in faster production times and higher efficiency. UV-curable adhesives also provide high bond strength and excellent heat, chemicals, and moisture resistance.
- Hybrid adhesives: These adhesives combine the benefits of both epoxy and acrylic adhesives, providing high bond strength and excellent resistance to environmental factors such as heat, moisture, and chemicals. Hybrid adhesives are also highly durable and flexible.
- Modified epoxy adhesives: Modified epoxy adhesives have been developed with improved adhesion to various substrates, including metals, plastics, and composites. They are also highly resistant to impact, vibration, and temperature changes.
- Flexible magnet bonding adhesives: These adhesives bond magnets to flexible substrates such as plastic and rubber. They provide excellent adhesion and flexibility, making them ideal for automotive and industrial applications.
- High-temperature adhesives: High-temperature magnet bonding adhesives are designed to withstand extreme temperatures, making them suitable for use in high-temperature environments such as automotive engines and electronics.
Overall, the advancements and innovations in magnet bonding adhesive technology have improved performance, efficiency, and durability, making them a popular choice in various industries.
FAQs about Magnet Bonding Adhesive
- What is magnet bonding adhesive?
Magnet connecting adhesive is a type of adhesive designed specifically for bonding magnets to various substrates. It is a two-part adhesive system that consists of a resin and a hardener.
- What types of magnets can be bonded with magnet bonding adhesive?
Magnet bonding adhesive can connect various interests, including neodymium magnets, ceramic magnets, samarium cobalt magnets, and alnico magnets.
- What substrates can magnet bonding adhesive bond to?
Magnet bonding adhesive can bond to various substrates, including metal, plastic, glass, and wood.
- How is magnet bonding adhesive applied?
Magnet bonding adhesive is typically used by mixing the resin and hardener and then applying the mixture to the magnet and substrate. The bond is usually allowed to cure for several hours before handling.
- What are the advantages of using magnet bonding adhesive?
Magnet bonding adhesive provides a strong and durable bond between magnets and substrates, even in harsh environments. It also allows for precise magnet placement, not requiring mechanical fasteners.
- What are some typical applications for magnet bonding adhesives?
Magnet bonding adhesive manufactures electronic devices, sensors, motors, and generators. It is also used in the automotive, aerospace, and medical industries.
- Are there any precautions to be taken when using magnet-bonding adhesive?
Magnet bonding adhesive should be used in a well-ventilated area, and protective gloves and goggles should be worn during application. The adhesive should also be stored in a cool, dry place, away from direct sunlight and heat sources.
Tips and Tricks for Using Magnet Bonding Adhesive
Magnet bonding adhesive is a popular adhesive used to attach magnets to different surfaces. Here are some tips and tricks for using magnet bonding adhesive:
- Clean the surfaces: Before applying the adhesive, make sure the surfaces you are bonding are clean and debris-free. Use a cleaning agent like alcohol or acetone to remove oil, dirt, or dust particles.
- Apply a thin layer: Magnet bonding adhesive is strong and requires only a thin layer to create a strong bond. Apply a small amount of adhesive to one surface and spread it evenly using a toothpick or a small brush.
- Position the magnets: Once you have applied the adhesive, position the magnets on the surface and press them firmly in place. Make sure the magnets are aligned correctly.
- Wait for the adhesive to dry: Magnet bonding adhesive requires time to dry and cure properly. The curing time can vary depending on the type of adhesive you use. Follow the manufacturer’s instructions for the recommended drying time.
- Avoid moving the magnets: Once you have positioned them, avoid moving them until the adhesive has fully cured. Moving the magnets could weaken the bond and cause them to come loose.
- Store the adhesive properly: Magnet bonding adhesive should be stored in a cool, dry place away from direct sunlight. Make sure the lid is tightly sealed to prevent air from getting in.
- Choose the suitable adhesive: Different magnet bonding adhesives are available for magnets and surfaces. Make sure you choose the suitable adhesive for your specific application.
Following these tips and tricks can ensure a strong and long-lasting bond when using magnet bonding adhesive.
Final Thoughts on Magnet Bonding Adhesive
Magnet bonding adhesive is an excellent choice for bonding magnets to different surfaces, and it provides a robust and durable bond that is ideal for a range of applications. When using magnet bonding adhesive, it’s essential to follow the manufacturer’s instructions carefully and the tips and tricks outlined above.
One of the advantages of magnet bonding adhesive is that it is easy to apply and can bond quickly. It is also a cost-effective solution for bonding magnets, eliminating the need for screws or other hardware. Additionally, magnet bonding adhesive can be used on various surfaces, including metal, plastic, and wood.
It’s important to note that different types of magnet bonding adhesives are available, and the suitable adhesive for your specific application will depend on several factors, including the type of magnet and surface you are bonding, as well as the environmental conditions in which the bond will be exposed. Some adhesives are designed for high-temperature environments, while others are formulated to resist moisture or chemicals.
Magnet bonding adhesive is a versatile, cost-effective solution for bonding magnets to various surfaces. By following the tips and tricks outlined above, you can achieve a robust and long-lasting bond that will meet your application’s demands.