A Complete Guide of Electronic Adhesives
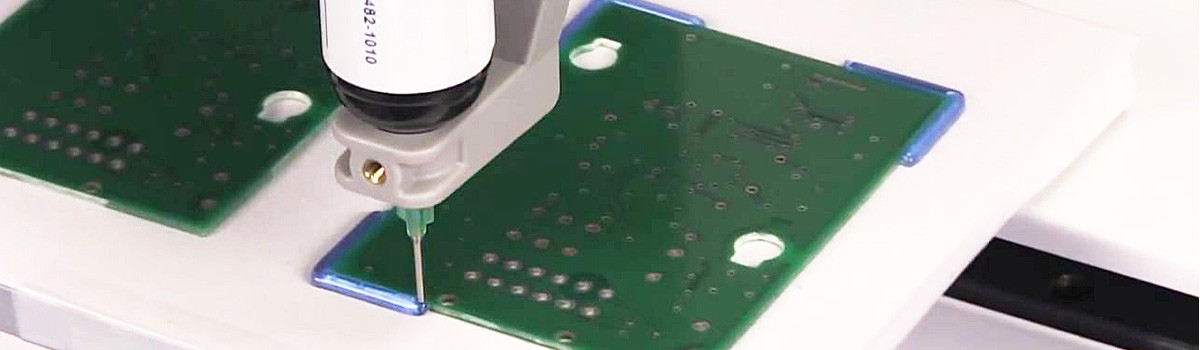
Electronic Adhesives
Electronic adhesives are specialized materials that bond electronic components, such as integrated circuits, resistors, capacitors, and transistors, to circuit boards, substrates, and other electronic devices. These adhesives ensure electronic products’ reliability, performance, and longevity.
Electronic adhesives come in various types, including conductive and non-conductive adhesives, thermal and electrically conductive adhesives, and UV-curable adhesives. We formulate them to withstand extreme temperatures, chemicals, moisture, vibration, and other environmental factors that electronic devices may encounter during their lifespan.
Various industries widely use electronic adhesives, including automotive, aerospace, telecommunications, medical, and consumer electronics. They enable electronic devices’ miniaturization, speed, and functionality and their resistance to harsh conditions.
The Importance of Electronic Adhesives in Modern Technology
Electronic adhesives are an essential component of modern technology. They play a vital role in ensuring the reliability and longevity of electronic devices, as well as their miniaturization, speed, and functionality. Here are some of the reasons why electronic adhesives are so important in modern technology:
Miniaturization: As manufacturers miniaturize electronic devices, they must also miniaturize the components used in their construction. Electronic adhesives allow manufacturers to bond these small components with precision and stability, enabling the development of smaller, more complex devices.
Durability: Harsh environmental conditions, including temperature changes, humidity, and shock, often expose electronic devices. We formulate electronic adhesives to withstand these conditions, ensuring the components remain securely bonded and the device continues functioning correctly.
Functionality: One can also use electronic adhesives to create conductive paths between components, enabling the flow of electricity through the device. It allows for the development of more complex circuits and increased functionality in electronic devices.
Speed: Using electronic adhesives in manufacturing can help streamline production and reduce assembly time. Electronic sealants can be applied quickly and accurately, saving time and increasing efficiency.
Reliability: Even a minor failure can cause significant problems in electronic devices. Electronic adhesives provide a reliable and secure bond between components, reducing the risk of loss and ensuring that the device functions correctly.
Types of Electronic Adhesives: A Comprehensive Overview
Electronic adhesives come in various types, each with unique properties and advantages. The choice of adhesive depends on the device’s specific application and requirements, and manufacturers must choose a suitable device adhesive to ensure reliability, functionality, and longevity. Here are the different types of electronic adhesives commonly used in the industry:
- Conductive Adhesives:Electronic manufacturers use conductive adhesives to create electrical connections between electronic components. They contain conductive particles, such as silver or copper, that enable the flow of electricity through the glue. Manufacturers commonly use these adhesives to manufacture touchscreens, sensors, and other electronic devices.
- Non-Conductive Adhesives:Manufacturers use non-conductive adhesives to electronic bond components that do not require electrical connections. They are often used in circuit board assembly, providing mechanical stability and insulation between members.
- Thermal Conductive Adhesives: Thermal conductive adhesives dissipate heat from electronic components. They contain thermally conductive particles, such as ceramic or carbon, that enable heat to flow through the glue. Manufacturers use these adhesives to manufacture power supplies, LED lighting, and other devices that generate significant amounts of heat.
- Electrically Conductive Adhesives:Electrically conductive adhesives are similar to conductive adhesives but have higher electrical conductivity. They are often used to assemble high-performance electronic devices, such as microprocessors and memory chips.
- UV-Curable Adhesives: One can cure UV-curable adhesives using ultraviolet light. They are fast-curing and provide excellent adhesion to a variety of substrates. Manufacturers commonly use these adhesives to manufacture medical devices, optical equipment, and other devices that require fast curing times.
- Epoxy Adhesives: Epoxy adhesives are known for their high strength and durability. They commonly assemble electronic devices that require a strong bond, such as smartphones, tablets, and laptops.
Conductive Adhesives: Their Role in Electrical Circuitry
Conductive adhesives are essential materials in the manufacturing of electronic devices. They provide a method for creating electrical connections between electronic components, which is crucial for the functionality of these devices. This blog post will discuss the role of conductive adhesives in electrical circuitry.
Conductive adhesives are formulated with conductive particles like silver, copper, or nickel, enabling electricity to flow through the glue. These particles create a conductive pathway between the electronic components, ensuring the device functions properly. Manufacturers commonly use conductive adhesives to manufacture touchscreens, sensors, and other electronic devices.
One advantage of using conductive adhesives in electrical circuitry is their ability to provide a secure bond between components. These adhesives create a robust and stable connection that can withstand the environmental stresses of electronic devices. The glue can also distribute current evenly across the circuit, preventing hot spots and ensuring all components receive the correct power.
One can also use conductive adhesives to create flexible circuits, which is essential for flexible devices, such as wearable electronics or medical devices. Conductive adhesives can be applied to flexible substrates, creating courses that bend, twist, or stretch.
One of the challenges of using conductive adhesives is their conductivity may degrade over time, especially when exposed to harsh environmental conditions. Manufacturers continually develop new formulations with improved durability and conductivity to address this issue.
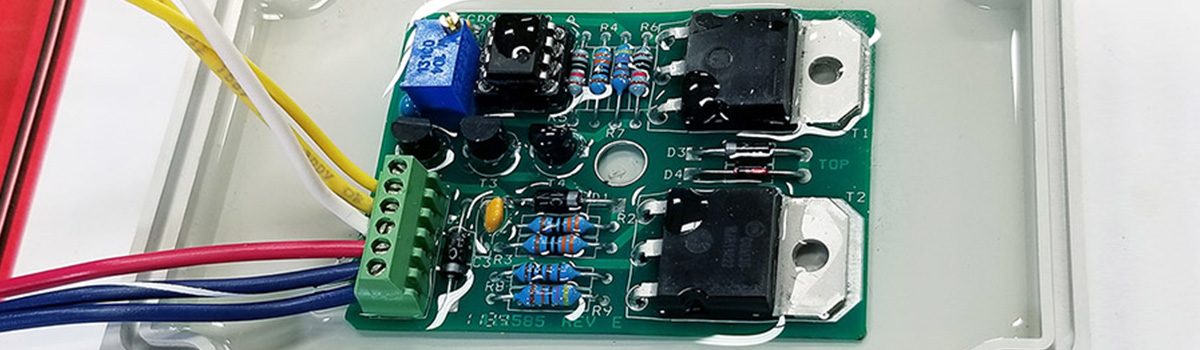
Understanding Thermally Conductive Adhesives
Thermally conductive adhesives are an essential component in many modern electronic devices. These adhesives bond and transfer heat between two surfaces, improving thermal management and preventing overheating. In this post, we will explore what thermally conductive adhesives are, their properties, and their applications.
Thermally conductive adhesives are a type of adhesive that has a high thermal conductivity, and this means that they can transfer heat efficiently between two surfaces. The typical composition of conductive adhesives includes a combination of a polymer matrix, such as epoxy or silicone, and conductive particles, such as aluminum oxide or boron nitride.
Thermally conductive adhesives’ properties depend on the type of polymer matrix and conductive particles used. Fundamental properties include thermal conductivity, viscosity, and curing time. The most critical property of the adhesive is its thermal conductivity, as it determines how effectively heat transfers between the surfaces. The viscosity of the adhesive determines how easy it is to apply, and the curing time determines how long it takes for the adhesive to cure and fully reach its maximum thermal conductivity.
Thermally conductive adhesives have many applications, including in the automotive, aerospace, and electronics industries. In the electronics industry, thermally conductive adhesives bond components to heat sinks and spreaders, improving thermal management and preventing overheating. They are also used to bond LED lighting components to substrates, which generate a lot of heat.
In the automotive industry, thermally conductive adhesives are used to bond power electronics components to heat sinks, which helps improve thermal management. They also connect sensors to engine components, which must operate in high-temperature environments.
Dielectric Adhesives: Ensuring Insulation in Electrical Components
Dielectric adhesives are essential materials used in the electronics industry to provide insulation and protection to electrical components. In applications where electrical conductivity is a concern, or a high degree of insulation is needed, thermally conductive adhesives are used instead of traditional adhesives that cannot meet these requirements. Dielectric adhesives have excellent insulation properties and can withstand high temperatures, making them ideal for use in electronic devices.
Here are some of the benefits of using dielectric adhesives:
- Insulation:Dielectric adhesives provide excellent insulation properties, preventing electrical current from flowing through them and ensuring their bonding components are electrically isolated.
- Heat Resistance:Dielectric adhesives can withstand high temperatures and maintain their properties over time, which makes them well-suited for applications that generate significant heat, such as motors and transformers.
- Chemical Resistance: Dielectric adhesives resist chemicals, making them suitable for use in harsh environments where other adhesives would fail.
- Durability: Dielectric adhesives have excellent bonding properties and can withstand high stress and strain, making them ideal for use in applications with mechanical stress.
- Easy Application:Dielectric adhesives can be applied quickly and efficiently, allowing rapid assembly and production.
- Versatility:You can use dielectric adhesives in various applications, such as electronic devices, automotive components, and medical equipment.
Dielectric adhesives are available in various formulations, including epoxies, silicones, and acrylics. We design each formulation with unique properties that suit specific applications.
UV-Curable Adhesives: A Quick Fix for Electronic Assembly
Electronic devices have become an integral part of our lives. We rely on electronics for almost everything from smartphones to laptops, automobiles to medical devices. Electronic assembly involves joining different components, and adhesives play a crucial role. UV-curable adhesives are gaining popularity among various adhesives due to their quick curing time and high bond strength.
UV-curable adhesives are reactive adhesives that cure when exposed to ultraviolet light. Curing occurs within seconds, making them an ideal choice for high-volume production environments. UV-curable adhesives eliminate the need for heating or drying, reducing the assembly time and production cost.
The high bond strength of UV-curable adhesives makes them suitable for various substrates, including metals, plastics, and glass. They offer excellent adhesion to difficult-to-bond materials, such as polypropylene, polyethylene, and polycarbonate. The adhesive bond formed by UV-curable adhesives is solid and durable, and it can withstand harsh environments, such as high temperatures, chemicals, and moisture.
Another advantage of UV-curable adhesives is their ability to cure in a specific area. The adhesive can be applied precisely to the bonding area, and the curing process can be triggered by exposing the site to UV light. This feature makes them ideal for applications requiring precise positioning and components alignment.
UV-curable adhesives are also environmentally friendly and do not contain solvents or emit volatile organic compounds (VOCs) during curing. It makes them safe to use in confined spaces and reduces the environmental impact.
Selecting the Right Electronic Adhesive: Key Factors to Consider
Selecting suitable electronic adhesives is crucial in ensuring the longevity and reliability of electronic devices. Electronic adhesives bond components and protect against external factors such as moisture, dust, and temperature fluctuations. Here we will discuss the key factors to consider when selecting a suitable electronic adhesive.
Chemical Properties
Compatibility: The adhesive must be compatible with the materials it will bond to, including metals, plastics, and glass.
Chemical Resistance: The adhesive must resist chemicals that may come into contact with the electronic device, such as cleaning agents or solvents.
Thermal Properties: The adhesive must withstand operating temperatures and fluctuations.
Application Properties
Viscosity: To ensure proper application, you must consider the thickness of the adhesive, as it needs to flow evenly and cover the surfaces that you want to bond together.
Cure Time: The adhesive must have a cure time compatible with the assembly process. A long cure time can slow production, while a short cure time may not allow proper bonding.
Adhesion Strength: The adhesive must have sufficient adhesion strength to bond the components of the device and ensure longevity.
Environmental Properties
Moisture Resistance: The adhesive must protect against moisture, which can damage electronic components.
UV Resistance: The adhesive must protect against UV radiation, which can cause discoloration and degradation of materials.
Impact Resistance: The adhesive must protect against physical impacts like drops or shocks.
Selecting suitable electronic adhesives is crucial in ensuring the longevity and reliability of electronic devices. By considering the adhesive’s chemical, application, and environmental properties, manufacturers can ensure that the adhesive will bond components properly and protect against external factors.
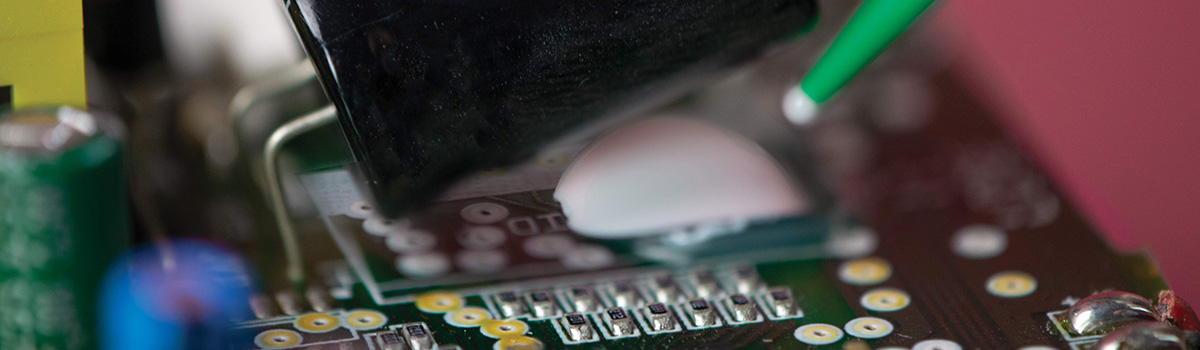
Compatibility with Substrates: Ensuring Adhesion and Stability
Compatibility with substrates ensures adhesion and stability in various industries, such as automotive, construction, and packaging. The success of applying a coating or adhesive to a substrate depends on how compatible the two materials are. In this discussion, we will emphasize the significance of ensuring compatibility with substrates and outline the steps to achieve it.
Importance of Compatibility with Substrates
Adhesion: To ensure the coating or adhesive remains in place, it must adhere to the substrate’s surface when applied. Compatibility with substrates is essential to ensure that the coating or adhesive bonds with the substrate and remains stable.
Stability: A coating or adhesive incompatible with the substrate can lead to instability and cause the coating or sealant to fail. It can lead to significant problems, such as building structural failure or product loss during use.
Ensuring Compatibility with Substrates
Surface preparation: To prepare the substrate surface for applying a coating or adhesive, clean it and remove contaminants. It will allow the coating or sealant to bond correctly with the substrate.
Testing: You should conduct compatibility testing before applying a coating or adhesive to ensure the two materials are compatible. You can use various methods, such as pull-off or lap shear testing, to perform compatibility testing.
Material selection: Selecting the suitable coating or adhesive for the substrate is essential. Consider the chemical and physical properties of the layer or adhesive and the substrate.
The implications of a lack of compatibility with substrates can be severe, leading to failures and high time and money costs. You can achieve adhesion and stability and ensure a successful and long-lasting application by ensuring compatibility with substrates.
Environmental Resistance: Factors to Consider
Environmental resistance refers to the natural factors that limit the growth, distribution, and abundance of organisms in an ecosystem. These factors can be biotic (living) or abiotic (non-living) and include a range of physical, chemical, and biological conditions. In this blog post, we will discuss the factors contributing to environmental resistance and the implications of these factors on ecosystem health.
Biotic Factors
- Competition: Organisms compete for food, water, and shelter resources. It can limit a population’s growth by reducing resource availability.
- Predation: Predators can restrict the size of a person by consuming individuals. It can also lead to a decrease in the overall population size of a species.
- Disease: Diseases can spread rapidly through a population, causing a decline in individuals over time.
Abiotic Factors
- Temperature:Organisms have a range of optimal temperatures to survive and reproduce. Extreme temperatures can limit the growth and distribution of organisms.
- Water: Water is essential for life, and organisms require a certain amount of water to survive. Lack of water can limit the growth and distribution of organisms.
- Light: Light is necessary for photosynthesis in plants, which is how they produce food. Lack of sunlight can limit the development and distribution of plants.
Implications of Environmental Resistance
- Maintaining balance: Environmental resistance helps to maintain balance in ecosystems by preventing one species from dominating and causing imbalance.
- Biodiversity: Environmental resistance promotes biodiversity by creating niches for different species, thereby increasing the number of species in an ecosystem.
- Ecosystem health:Environmental resistance plays a crucial role in maintaining ecosystem health. Disruption of these factors can lead to the decline or extinction of species, which can have cascading effects on the entire ecosystem.
Application Method: Choosing the Right Dispensing Technique
When manufacturing, choosing the proper application method for your product is crucial. The dispensing process of development can heavily influence its performance and appearance.
That’s why it’s essential to carefully evaluate your options and choose the technique that best suits your needs.
Here are some factors to consider when choosing the proper dispensing technique:
- Viscosity: The viscosity of the material you’re dispensing is an important consideration. Low-viscosity materials like water or solvents may require different dispensing styles than high-viscosity materials like adhesives or pastes. For low-viscosity materials, spray or atomization techniques may be more effective, while high-viscosity materials may require a more controlled approach, like precision dispensing.
- Material properties: When selecting a dispensing method, you should consider the properties of the material you plan to dispense. For example, some materials may be sensitive to air or temperature changes and require dispensing methods that minimize exposure to these factors. Similarly, materials that require a certain level of precision or accuracy may need more specialized dispensing equipment.
- Product design: The design of your product can also influence the choice of dispensing technique. For example, if your product has intricate or delicate features, a manual dispensing process may be more appropriate than an automated one. On the other hand, if your product requires high-volume output, a mechanical or robotic dispensing technique may be necessary.
- Environmental factors: Finally, environmental factors can also impact the choice of dispensing method. If you need to dispense your product in a cleanroom environment, you may require specialized equipment that meets particular cleanliness standards, for instance. Similarly, if your product is flammable or hazardous, you may need to choose a dispensing technique that minimizes the risk of accidents or fires.
Curing Process: Understanding the Impact of Heat and Time
Curing is a crucial process that ensures the longevity and durability of products in several industries. From automotive to construction, curing is essential to ensure that the end products are solid and resistant to environmental factors. The curing process involves the application of heat and time to the development, which affects its mechanical properties and overall quality.
Heat is one of the critical factors that influence the curing process. The temperature range and duration of heat application significantly impact the product’s strength and stiffness. The heat activates the chemical reactions that lead to the formation of cross-links in the material. These cross-links increase the power of the material by creating bonds between the molecular chains.
The duration of the curing process is another critical factor. The longer the curing time, the more cross-links are formed, resulting in a more robust and stiffer product. However, too much curing time can lead to brittleness and reduced flexibility. It is finding the right balance between curing time and strength, depending on product requirements.
The appropriate curing method depends on the product type and the required properties. For instance, in the automotive industry, a paint-curing oven is used to apply heat to the car’s body, ensuring that the paint dries and adheres to the metal. In the construction industry, concrete is cured by adding water and allowing it to harden over time, increasing its strength.
The curing process is essential not only for the product’s mechanical properties but also for its appearance. The heat and time applied during curing affect the product’s texture, color, and finish. Therefore, controlling the curing process is crucial to ensure the product meets the desired aesthetic and functional requirements.
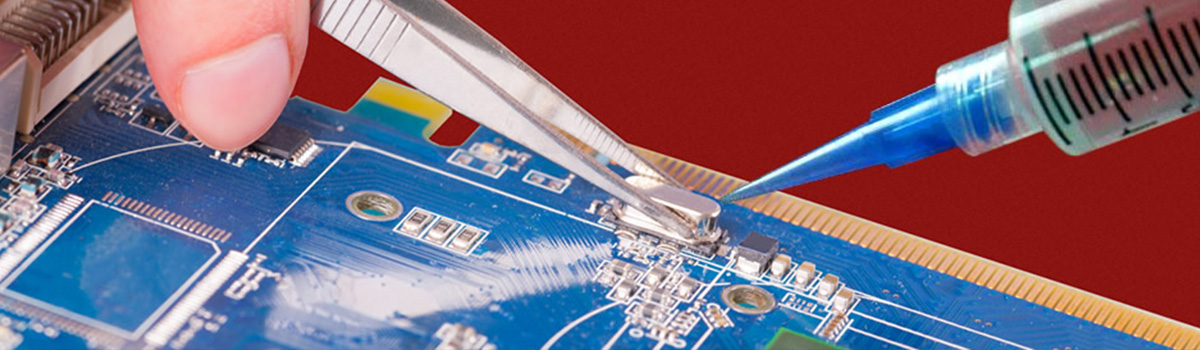
Storage and Handling: Tips to Maintain Adhesive Quality
Proper storage and handling are crucial to ensure the effectiveness of adhesives. Improper storage and handling can lead to the degradation of adhesive quality and ultimately result in product failure. Here are some tips for maintaining adhesive quality:
- Temperature Control: Adhesive materials are sensitive to temperature changes, and exposure to extreme temperatures can damage their quality. High temperatures can cause adhesive materials to lose their viscosity and adhesion strength, while low temperatures can cause them to become brittle and difficult to use. Therefore, storing adhesives in a cool, dry place, away from direct sunlight, and at a consistent temperature is essential.
- Humidity Control: Humidity can also impact the quality of adhesive materials. Moisture can cause adhesives to break down, reducing their adhesive strength. To maintain adhesive quality, one must keep sticky containers tightly sealed and store them in an area with controlled humidity.
- Proper Handling: Proper handling of adhesive materials is crucial to their longevity. It is essential to avoid dropping or shaking sticky containers, as this can lead to the formation of air bubbles, affecting the adhesive quality. Additionally, mixing adhesives properly before use is essential, as inadequate mixing can lead to uneven adhesive quality and performance.
- Shelf Life: Adhesive materials have a limited shelf life, and using them within the specified time frame is essential. Over time, adhesive materials can begin to break down, causing them to lose their adhesive strength and viscosity. It is crucial to use adhesives before expiration to ensure their effectiveness.
- Compatibility: Manufacturers design different adhesive materials for specific surfaces and applications. It is essential to ensure that the adhesive material is compatible with the texture and the application requirements. Using incompatible adhesive materials can result in product failure and damage to surfaces.
Common Applications of Electronic Adhesives
Electronic adhesives are specialized adhesives that bond and seal electronic components and systems. The aerospace and automotive industries and consumer electronics are among the various applications that utilize them. Here are some of the most common applications of electronic adhesives:
- Consumer electronics:Electronic adhesives are used extensively in consumer electronics, including smartphones, laptops, and tablets. They bond and seal electronic components like displays, touchscreens, and batteries. Electronic adhesives also protect against moisture and other environmental factors damaging electronic components.
- Automotive industry: The automotive industry relies heavily on electronic adhesives to ensure the reliability and safety of modern cars. Electronic adhesives bond and seal electronic components, structural components, and electrical connections. Manufacturers also use them to bond and seal composite materials, such as carbon fiber, which are becoming more prevalent in modern car construction.
- Aerospace industry: The aerospace industry requires specialized adhesives that can withstand extreme environmental stresses, including high-temperature changes and exposure to saltwater. Electronic adhesives are used extensively in the aerospace industry for bonding and sealing electronic components, structural components, and electrical connections.
- Medical devices: Medical device manufacturers use electronic adhesives in products such as pacemakers, defibrillators, and insulin pumps. They are used to bond and seal electronic components, ensuring that they function correctly and reliably.
- LED lighting:Manufacturers use electronic adhesives to produce LED lighting, including automotive lighting and streetlights. These adhesives bond and seal electronic components to protect them from moisture and other environmental factors that can cause damage.
- Renewable energy: The industry uses electronic adhesives to bond and seal solar panels, wind turbines, and batteries. They are used to protect the electronic components from moisture and other environmental factors, ensuring that they remain reliable and functional over the life of the equipment.
Automotive Industry: The Role of Electronic Adhesives in Car Manufacturing
The automotive industry is constantly evolving, and car manufacturers always look for ways to improve their vehicles’ safety, reliability, and efficiency. One critical component that plays a vital role in the construction of modern cars is electronic adhesives. Electronic adhesives are used extensively in the automotive industry for various applications, including bonding and sealing electronic components, structural components, and electrical connections.
Electronic adhesives find application in several crucial ways during car manufacturing:
- Bonding and sealing electronic components:Electronic adhesives bond and fill electronic details such as sensors, control systems, and displays. Electronic adhesives guarantee these components can function correctly, even when subjected to extreme conditions.
- Bonding and sealing structural components:Electronic adhesives bond and fill structural elements, such as body panels and chassis. Using electronic adhesives guarantees that the car components remain securely attached, even when subjected to the stresses of everyday driving.
- Electrical conductivity: Car manufacturers use electronic adhesives to guarantee dependable electrical conductivity between car components. Secure electrical connections between parts are particularly crucial in hybrid and electric vehicles, as they ensure the safe and efficient operation of the car.
- Vibration resistance:EDesigners create electronic adhesives that absorb vibrations and shock, preventing components from falling loose or failing. Preventing elements from coming loose or dying is essential in high-performance vehicles, where the parts undergo high stress.
- Environmental protection:Designers create electronic adhesives to safeguard components from environmental factors such as moisture, dust, and other agents that can damage or degrade them. Electronic bonds guarantee that the parts stay dependable and operational throughout the vehicle’s life.
Car manufacturers also use electronic adhesives during the manufacturing process, in addition to their critical applications. Car manufacturers use electronic adhesives to bond and seal composite materials, like carbon fiber, that are increasingly common in modern car construction. Using composite materials results in lighter, stronger, and more fuel-efficient vehicles, but it also requires specialized adhesive systems to ensure the components are correctly bonded and sealed.
Aerospace Industry: How Electronic Adhesives Ensure Safety in Aircraft
The aerospace industry is one of the world’s most complex and demanding industries. The safety of passengers and crew members on board aircraft is paramount, and any failure in the materials or components used in aircraft construction can have catastrophic consequences. Manufacturers, designers, and engineers cannot overstate the importance of electronic adhesives in ensuring aircraft safety.
Electronic adhesives are used extensively in the aerospace industry for various applications. They are used to bond and seal electronic components, such as sensors and control systems, to ensure they function correctly under extreme conditions. They also connect and seal structural elements, such as wings and fuselage sections, to ensure they remain firmly in place during flight.
One of the primary concerns in aircraft construction is the impact of moisture and other environmental factors on the integrity of the components. Designers create electronic adhesives that can withstand environmental stresses, such as extreme temperature changes and high humidity, which can compromise the aircraft’s performance. Designers also design electronic adhesives to offer long-lasting protection against corrosion, a significant issue in planes exposed to corrosive environments like salt water.
Electronic adhesives also play a crucial role in the manufacturing process of aircraft. Electronic adhesives bond and seal composite materials, like carbon fiber, are increasingly becoming common in modern aircraft construction. Using composite materials results in lighter, stronger, and more fuel-efficient aircraft, but it also requires specialized adhesive systems to ensure the components are correctly bonded and sealed.
Besides serving structural and protective purposes, the aerospace industry employs electronic adhesives for electrical conductivity. They are used to bond and seal electronic circuits and components, ensuring they function correctly and reliably. Electronic adhesives guarantee that the aircraft’s electrical connections remain secure, minimizing the risk of electrical failure.
Medical Industry: The Role of Adhesives in Medical Devices
The medical industry relies on technology to provide effective and efficient patient treatments. Medical devices are critical in diagnosing, treating, and monitoring various medical conditions. Adhesives are essential to medical devices, offering a reliable and safe way to bond components and ensure the device’s functionality. Here we will explore the role of adhesives in medical devices.
Here are some of the ways adhesives play a crucial role in medical devices:
- Bonding: Adhesives are used to bond components of medical devices together, ensuring that they stay in place and function as intended. Correct placement and operation of components are crucial in devices like pacemakers and insulin pumps since it can be a matter of life or death, making electronic adhesives essential for ensuring secure placement and reliable function.
- Sealing: Medical device manufacturers use adhesives to seal devices and prevent leakage and contamination. For example, in catheters and IV lines, sealants are used to seal the connection between the device and the patient’s skin, preventing the entry of bacteria.
- Durability:Medical devices must be durable enough to withstand the stresses of daily use. Adhesives play a crucial role in ensuring the durability of medical devices by providing a solid and long-lasting bond between components.
- Biocompatibility: Adhesives used in medical devices must be biocompatible, meaning they are safe to use in the human body and will not cause harm or irritation. Manufacturers must use adhesives tested and approved for use in medical devices.
- Flexibility: Some medical devices must conform to the body’s shape. Manufacturers use adhesives to bond flexible components while preserving the device’s flexibility.
Consumer Electronics: Ensuring Durability in Everyday Devices
Consumer electronics have become an essential part of our daily lives, and we rely on them for everything from communication to entertainment. With such heavy usage, durability is a critical factor in ensuring that our devices can withstand the wear and tear of everyday use. Here we will explore some ways manufacturers can ensure durability in consumer electronics.
- Robust Design: One of the essential factors in ensuring durability in consumer electronics is design. Manufacturers must create devices with solid materials and components that can withstand the stresses of everyday use. They should also consider water, drop, and scratch resistance factors.
- Testing:Testing is an essential part of ensuring durability in consumer electronics. Manufacturers should conduct rigorous testing of their devices to ensure they can withstand different environmental conditions and usage scenarios. Manufacturers can perform various tests, including water resistance, drop resistance, temperature resistance, and more, to ensure the durability and reliability of the products.
- Quality Control: Quality control is crucial in ensuring that each device meets the manufacturer’s standards for durability. Manufacturers should have a rigorous quality control process to identify defects or issues that may impact the device’s durability.
- Repair and Maintenance: Consumers should also be able to repair and maintain their appliances easily. Manufacturers should design devices that are easy to disassemble and reassemble, with replacement parts readily available. By conducting these tests, manufacturers ensure that consumers can maintain their devices’ good working conditions for longer.
- User Education: Finally, manufacturers should educate consumers on how to use their devices to promote durability. Manufacturers may include instructions on proper cleaning and maintaining the machine and information on avoiding common causes of damage, such as dropping or exposing the device to water.
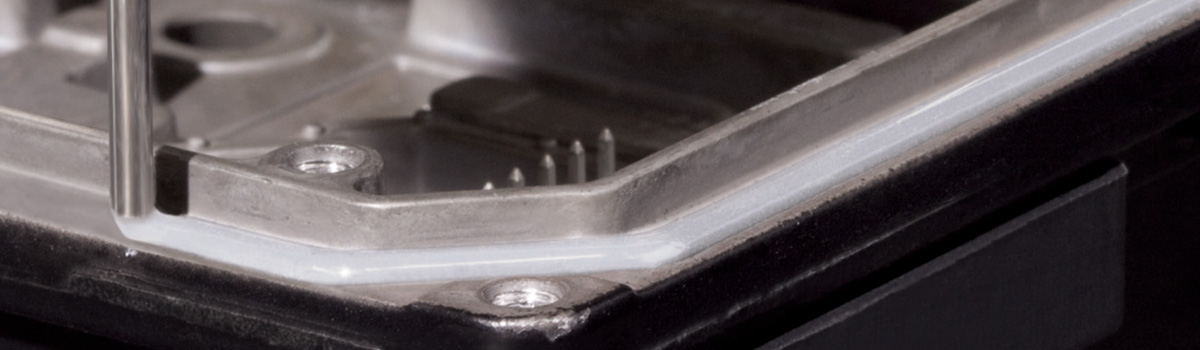
Future of Electronic Adhesives: Emerging Trends and Innovations
As technology continues to evolve at an unprecedented pace, the future of electronic adhesives is also transforming. Emerging trends and innovations are shaping the industry, offering new possibilities for electronic device manufacturers to improve the performance and durability of their products. This blog post will explore some of the most promising developments in electronic adhesives and their potential impact.
Here are some of the emerging trends and innovations in the field of electronic adhesives:
- High Thermal Conductivity Adhesives:With the increasing demand for high-power electronic devices, there is a growing need for adhesives that can effectively dissipate heat. High thermal conductivity adhesives offer a solution by improving thermal management and enabling higher performance.
- Flexible Adhesives:Flexible sealants are becoming increasingly popular in flexible electronics, wearable devices, and medical applications. These adhesives offer flexibility, strength, and durability, making them ideal for instruments that bend, twist, or conform to various shapes.
- Eco-Friendly Adhesives:With environmental concerns becoming more prominent, there is a growing need for eco-friendly and sustainable adhesives. Innovations in this area include bonds made from renewable materials such as natural rubber and glues that can be easily recycled or reused.
- Miniaturization: As electronic devices continue to shrink in size, there is a need for adhesives that can keep up with the trend. Miniaturized sealants with high bonding strength are becoming more popular, allowing for smaller, more compact devices.
- Innovative Adhesives:Developers create innovative adhesives with self-healing, shape memory, and conductivity features. These adhesives enable electronic device manufacturers to develop more intelligent and responsive products.
Future Trends and Innovations in Electronic Adhesive Technology
Electronic adhesive technology is constantly evolving, and new trends and innovations are emerging to meet the changing needs of the electronics industry. Here are some of the future trends and innovations in electronic adhesive technology:
- Miniaturization:As electronics become smaller and more compact, the demand for adhesives that can work on a microscale is increasing. Adhesives that can bond small and delicate components without damaging them are becoming more critical.
- Conductive Adhesives: Electronic manufacturers increasingly use conductive adhesives as an alternative to soldering. The benefits include lower operating temperatures, simplified assembly processes, and improved reliability.
- Thermal Management: With the increased power density of electronic devices, heat dissipation has become a critical challenge. Adhesives that can conduct heat away from components are essential for improving the longevity and reliability of electronic devices.
- Flexible Adhesives: As electronics become more flexible and wearable, flexible adhesives are becoming more critical. These adhesives can withstand bending and twisting without cracking, ensuring electronic components remain bonded even under stress.
- Environmentally Friendly Adhesives:As sustainability becomes increasingly important, there is a growing demand for environmentally friendly adhesives. Adhesives made from biodegradable or recycled materials are becoming more common.
- Innovative Adhesives:Researchers are developing intelligent adhesives that can change their properties in response to external stimuli like temperature or light. These adhesives have potential applications in sensors, actuators, and other electronic devices.
Common Challenges Faced When Using Electronic Adhesive and How to Overcome Them
Electronic adhesives are an essential component in the manufacturing of electronic devices, but they can also present various challenges. Here are some of the common challenges faced when using electronic adhesive and how to overcome them:
- Poor Adhesion:Poor adhesion can occur when the adhesive does not bond correctly to the substrate, leading to component failure. The solution is to ensure the surface is clean and free from contaminants before applying the adhesive. Additionally, using a primer or surface treatment can improve the adhesion of the bond.
- Curing Time:Adhesives can take a long to cure, leading to production delays. The solution is to use fast-curing adhesives or optimize the curing conditions, such as temperature and humidity, to accelerate the process.
- Moisture Sensitivity:Moisture-sensitive adhesives can degrade when exposed to humidity, leading to a loss of adhesion and electrical performance. The solution is to use moisture-resistant adhesives or to store and handle the glue properly, such as keeping it in a dry environment and using sealed packaging.
- Thermal Expansion: Adhesives can experience thermal expansion and contraction, leading to mechanical stress and component failure. The solution is to use adhesives with a low coefficient of thermal expansion or to design an electronic system to accommodate thermal expansion and contraction.
- Compatibility: Adhesives can be incompatible with certain materials, such as plastics or metals, leading to poor adhesion or chemical reaction. The solution is to use adhesives compatible with the materials in the electronic system or to perform compatibility testing before applying the glue.
Dispensing adhesives can be challenging, especially when dealing with small and delicate components. We can solve the issue by using precision dispensing equipment or pre-manufactured adhesive films or tapes that individuals can easily apply to the parts.
The Role of Electronic Adhesives in Wearable Technology
Wearable technology has become increasingly popular over the last decade, with a wide range of devices now available for consumers. These devices, such as smartwatches and fitness trackers, rely on electronic components that must be securely attached to the wearable device. In situations requiring strong and reliable bonding of electronic components, electronic adhesives play a crucial role.
Manufacturers use electronic adhesives to bond sensors, LEDs, batteries, and other components to wearable devices, ensuring they function correctly and remain durable. These adhesives must withstand the stresses of daily use, including exposure to moisture, heat, and physical impact. With wearable technology, they must also be flexible to allow for bending and stretching.
One of the key benefits of electronic adhesives in wearable technology is their ability to provide a seamless and streamlined appearance. If there were no bonds, manufacturers would have to use screws or other mechanical fasteners to attach components, which could increase the weight and size of the device. On the other hand, manufacturers can apply adhesives in a thin, uniform layer almost invisible to the naked eye.
Another important consideration when choosing electronic adhesives for wearable technology is biocompatibility. To ensure that wearables do not cause any irritation or allergic reactions when worn directly against the skin, manufacturers must use non-irritating and hypoallergenic glue. For medical wearables, such as glucose or ECG monitors used by people with specific health conditions, it is especially critical to ensure that the adhesive does not cause any irritation or allergic reactions, given their direct contact with the skin.
As wearable technology continues to evolve, the demand for electronic adhesives that can meet the unique needs of these devices will continue to grow. Adhesive manufacturers are already developing new formulations that can withstand extreme temperatures, resist moisture, and provide improved flexibility. As a result, wearable technology will become even more comfortable, reliable, and functional.
Dispensing Techniques for Electronic Adhesives: Tips and Best Practices
Electronic adhesives are essential in the manufacturing of electronic devices. However, dispensing them can be a challenging task, especially when it comes to small and intricate parts. Here are some tips and best practices for dispensing electronic adhesives:
- Choose the proper dispensing method: There are several dispensing methods available for electronic adhesives, including manual dispensing, syringe dispensing, and automated dispensing. Choose the way that best suits your application.
- Use the correct dispensing tip: The dispensing tip must match the adhesive’s viscosity and the bonded part’s size. Minor information is ideal for smaller portions, while more considerable information is suitable for more important details.
- Dispense in a clean environment: A clean environment prevents contamination and ensures a strong bond. Use a clean work area and wear gloves to prevent skin oils from getting onto the adhesive.
- Ensure proper storage: Proper storage is crucial for the longevity of electronic adhesives. Keep the items excellent and dry, and seal the container tightly.
- Apply the adhesive evenly:Ensure that the adhesive is applied evenly to prevent air pockets, which can weaken the bond. Use a steady hand and apply the glue in a continuous motion.
- Control the flow rate: You need to control the flow rate of the adhesive to avoid excess glue from oozing out and making a mess. Use a slow and steady flow rate, especially when working with small parts.
- Clean the dispensing tip regularly:Clean the dispensing tip regularly to prevent clogs and ensure a smooth flow of adhesive. Use an appropriate cleaning solution and follow the manufacturer’s instructions.
- Practice safety precautions:Manufacturers often use chemicals in electronic adhesives that can pose health hazards. Use protective gear such as gloves and goggles when handling them.
By following these tips and best practices, you can successfully dispense electronic adhesives and ensure a strong bond for your electronic devices.
Conclusion
In conclusion, electronic adhesives play a critical role in modern technology. They are essential for creating reliable and long-lasting bonds between electronic components, protecting them from environmental factors such as moisture, heat, and vibration. Electronic adhesives also enable the miniaturization of electronic devices, making them smaller and more portable.
As technology continues to advance, electronic adhesives will become even more critical. They will need to keep up with the growing demand for more robust and compact electronic devices while also addressing concerns about sustainability and environmental impact.
Furthermore, electronic adhesives must meet the specific requirements of different industries and applications, from medical devices to automotive electronics to aerospace and defense systems. Thus, continuous research and development in this field will be necessary to meet these changing demands.