Glass Bonding Adhesive
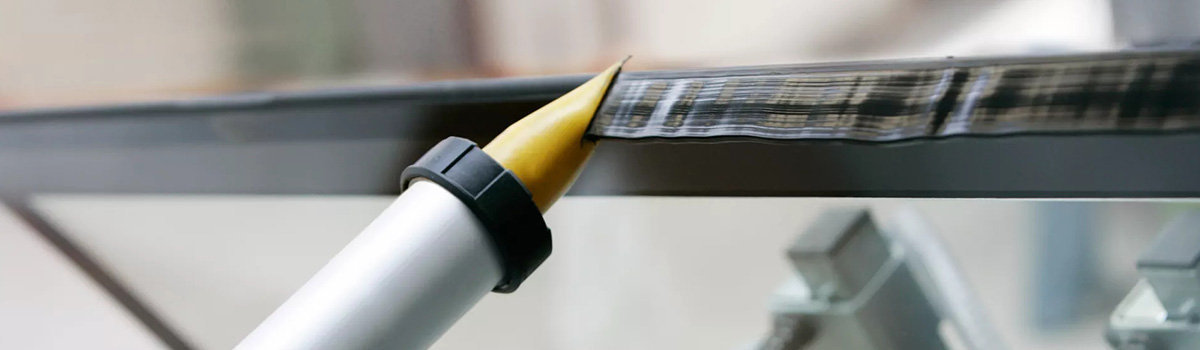
Introduction: Glass bonding adhesives are a type of adhesive used to bond glass to other materials, such as metals or plastics. They offer a high-strength bond, excellent durability, and can withstand harsh environmental conditions. There are several types of glass bonding adhesives available, each with its own set of properties and advantages. In this guide, we will explore the various types of glass bonding adhesives, their applications, advantages, and considerations for their use.
What are Glass Bonding Adhesives?
Glass bonding adhesives are specialized adhesives used to bond glass to other surfaces, typically in industrial or commercial applications. These adhesives are formulated to provide high strength, durability, and resistance to environmental factors like heat, moisture, and chemicals.
Several types of glass bonding adhesives are available, including epoxy, acrylic, and silicone adhesives. Epoxy adhesives are typically the most robust and durable, while acrylic adhesives are known for their fast-curing properties and good resistance to UV light. Silicone adhesives are often used for applications where flexibility is essential, such as bonding glass to materials that expand and contract at different rates.
Glass bonding adhesives are used in various applications, including automotive manufacturing, aerospace, electronics, and construction. Some common uses include bonding windshields to car bodies, attaching glass panels to building facades, and securing glass components in electronic devices.
Types of Glass Bonding Adhesives
Several types of glass bonding adhesives are available, each with unique properties and applications. Here are some of the most common types:
- Epoxy Adhesives: Epoxy adhesives are two-part adhesives that provide robust and durable bonds. They are typically used for bonding glass to metals, plastics, and other materials. Epoxy adhesives have good chemical and moisture resistance and are often used in harsh environments.
- Acrylic Adhesives: Acrylic adhesives are fast-curing adhesives with high strength and good durability. They are typically used for bonding glass to metals and plastics and are often used in automotive and aerospace applications. Acrylic adhesives have good resistance to UV light and weathering.
- Silicone Adhesives: Silicone adhesives are flexible adhesives that can accommodate materials’ thermal expansion and contraction. They are typically used for bonding glass to plastics and metals and are often used in electronic and medical device applications. Silicone adhesives have good electrical insulation properties and are resistant to moisture and chemicals.
- UV Curing Adhesives: UV curing adhesives are single-part adhesives that cure when exposed to UV light. They provide fast curing times and can bond glass to various materials. UV curing adhesives have good adhesion to drink and are often used in optical and electronic applications.
- Cyanoacrylate Adhesives: Cyanoacrylate adhesives, also known as superglues, are fast-curing adhesives that provide high-strength bonds. They are typically used to bond small glass components to other materials, such as electronics and jewelry manufacturing. Cyanoacrylate adhesives have good resistance to chemicals and can connect with dissimilar materials.
Epoxy Adhesives for Glass Bonding
Epoxy adhesives are commonly used for bonding glass because they have excellent adhesive strength and can withstand high stress and temperature conditions. Here are some tips for using epoxy adhesives for glass bonding:
- Clean the glass surface thoroughly with a suitable cleaner to remove dirt, grease, or oil. Any impurities on the glass surface can affect the bonding strength of the epoxy.
- Roughen the glass surface with sandpaper to create a roughened texture to improve the bond strength.
- Apply the epoxy adhesive to one of the glass surfaces and spread it evenly with a spatula or a brush.
- Place the second glass piece on top of the first and apply pressure to ensure the two components are well bonded.
- Allow the epoxy to cure according to the manufacturer’s instructions before subjecting the bonded glass to any stress or temperature changes.
It is important to note that epoxy adhesives are sensitive to UV light and may yellow over time, especially when exposed to sunlight. To avoid discoloration, using UV-resistant epoxy or keeping the bonded glass away from direct sunlight is recommended.
Silicone Adhesives for Glass Bonding
Silicone adhesives are commonly used for bonding glass due to their strong adhesive properties and moisture and temperature change resistance. Here are some factors to consider when selecting a silicone adhesive for glass bonding:
- Type of silicone adhesive: There are various silicone adhesives, such as one-part and two-part silicone adhesives. One-part silicone adhesives are ready to use and do not require any mixing. Two-part silicone adhesives require mixing before application but offer higher strength and durability.
- Bond strength: The bond strength of silicone adhesives can vary, depending on the type and application method. Selecting a silicone adhesive with sufficient bond strength is essential to meet your requirements.
- Curing time: Silicone adhesives typically require a curing time to reach full strength. Some adhesives cure quickly, while others may take longer. Consider the time available for the bond to cure when selecting a product.
- Temperature resistance: Glass bonding applications may be subject to temperature changes. Select a silicone adhesive that is capable of withstanding the expected temperature range.
- Moisture resistance: Moisture can weaken some adhesives over time. If the application is exposed to moisture, select a water-resistant silicone adhesive.
When selecting a silicone adhesive for glass bonding, consider the specific requirements of your application and choose a product that meets those needs. Following the manufacturer’s instructions for proper application and curing is also essential.
UV Curable Adhesives for Glass Bonding
UV-curable adhesives are popular for glass bonding applications due to their fast cure times, high strength, and clarity. These adhesives typically consist of monomers, oligomers, photoinitiators, and additives that polymerize when exposed to UV light.
When selecting a UV-curable adhesive for glass bonding, it’s essential to consider several factors, including:
- Adhesion strength: The adhesive should provide a strong bond between the glass surfaces, and it should be able to withstand the stresses and strains that the bonded assembly will experience in its intended application.
- Cure time: The adhesive’s curing time should be fast enough to allow for efficient production but not so fast that there needs to be more time to properly position and align the glass components before bonding.
- Transparency: The adhesive should be as transparent as possible to maintain the clarity of the glass surfaces.
- Chemical resistance: The adhesive should resist the chemicals or solvents the bonded assembly may be exposed to during its service life.
Some commonly used UV-curable adhesives for glass bonding include:
- Acrylic-based adhesives: These adhesives provide excellent adhesion strength and transparency, and they can cure in just a few seconds with exposure to UV light.
- Epoxy-based adhesives are known for their high strength and chemical resistance, making them suitable for bonding glass in harsh environments.
- Cyanoacrylate-based adhesives: Also known as “super glue,” these adhesives cure rapidly and provide high-strength bonding for glass components.
Following the manufacturer’s instructions when working with UV-curable adhesives for glass bonding is essential to ensure proper curing and maximum bond strength.
Polyurethane Adhesives for Glass Bonding
When selecting a polyurethane adhesive for glass bonding, it’s essential to consider factors such as:
- Cure time: Polyurethane adhesives come in various cure times, from fast-curing to slow-curing. The choice of cure time will depend on the specific application and the amount of time available for the adhesive to cure.
- Bond strength: The bond strength required for the application will depend on the type of glass and the substrate being bonded. In general, polyurethane adhesives offer excellent bonding strength, but choosing the appropriate adhesive for the specific application is essential.
- Compatibility: Polyurethane adhesives can be used with various substrates, but ensuring that the bond is compatible with both the glass and the substrate is essential.
- Environmental resistance: Polyurethane adhesives generally resist temperature changes, water, and chemicals. However, it’s essential to consider the specific ecological conditions the adhesive will be exposed to in the application.
- Application method: Polyurethane adhesives can be applied using various ways, such as spray, brush, or roller. The choice of application method will depend on the specific application and the size and shape of the glass and substrate.
Polyurethane adhesives are an excellent choice for glass bonding due to their bonding properties, flexibility, and durability. When selecting a polyurethane adhesive, it’s essential to consider factors such as cure time, bond strength, compatibility, environmental resistance, and application method to ensure the best results for the specific application.
Acrylic Adhesives for Glass Bonding
Here are some types of acrylic adhesives commonly used for glass bonding:
- UV-curable acrylic adhesives cure quickly when exposed to UV light, making them ideal for high-speed production. They also offer excellent bonding strength and resistance to environmental factors.
- Two-part acrylic adhesives: These adhesives consist of a resin and hardener that must be mixed together before use. They offer high bonding strength and are suitable for bonding large surfaces or substrates with different thermal expansion coefficients.
- One-part acrylic adhesives are ready to use and cure at room temperature. They offer good bonding strength and are suitable for bonding small to medium-sized surfaces.
When using acrylic adhesives for glass bonding, following the manufacturer’s instructions carefully and preparing the glass surface properly is essential. This may involve cleaning the surface to remove dirt, grease, or other contaminants and applying a primer to improve the adhesive’s adhesion to the glass.
Considerations for Choosing Glass Bonding Adhesives
When choosing a glass bonding adhesive, several important considerations must be remembered. Here are some key factors to consider:
- Bond Strength: The bond strength of the adhesive is a crucial consideration when choosing a glass bonding adhesive. The power of the bond should be appropriate for the application and able to withstand any mechanical or environmental stresses that the bond may be subjected to.
- Curing Time: The curing time of the adhesive is another critical consideration. Some adhesives may cure quickly, while others may take longer. The curing time should be appropriate for the application and the bonded materials.
- Transparency: If the bonded joint is visible, the clarity of the adhesive is an essential factor to consider. Some adhesives may turn yellow or cloud over time, which can impact the appearance of the bond.
- Chemical Resistance: The adhesive should withstand exposure to any chemicals or fluids the bond may be subjected to.
- Temperature Resistance: The adhesive should withstand any extreme temperatures the bond may be exposed to.
- Surface Preparation: Proper surface preparation is crucial for ensuring a solid bond. The adhesive should be compatible with the characters being bonded, and the appropriate surface preparation should be undertaken.
- Application Method: The application method of the adhesive should be appropriate for the application and the materials being bonded. Some adhesives may require special equipment or techniques for application.
Overall, choosing the suitable glass bonding adhesive requires careful consideration of these factors and an understanding of the application’s specific needs. Consulting with an adhesive specialist can help select the appropriate adhesive for the job.
Surface Preparation for Glass Bonding
Surface preparation is a critical step in bonding glass to other materials. The success of the bonding process largely depends on the quality of the preparation of the glass surface. Here are some steps to follow for surface preparation for glass bonding:
- Clean the surface: The first step is to thoroughly clean the surface of the glass. Any contaminants, such as dust, oil, or fingerprints, can affect the adhesion of the bonding agent. Use a solvent such as acetone or isopropyl alcohol to clean the surface.
- Remove any coatings: If the glass has any coatings, such as tinting, paint, or a protective film, it must be removed. These coatings can interfere with the bonding process. Use an appropriate solvent or abrasive to remove the layer.
- Abrasion: Abrasion is necessary to create a rough surface for the adhesive to bond to. Use a fine abrasive material such as sandpaper or a diamond pad to create a uniformly rough surface on the glass.
- Apply a primer: Applying a primer to the glass surface can help improve adhesion. The primer should be chosen based on the type of adhesive being used. The primer can be applied using a spray or brush.
- Apply the adhesive: Apply the adhesive to the glass surface according to the manufacturer’s instructions. Ensuring that the adhesive is applied evenly and thoroughly over the entire surface is essential.
- Cure: Once the adhesive is applied, it must be allowed to cure according to the manufacturer’s instructions. The curing time can vary depending on the adhesive used and the environmental conditions.
Following these steps, you can prepare the glass surface for bonding and ensure a strong and durable bond.
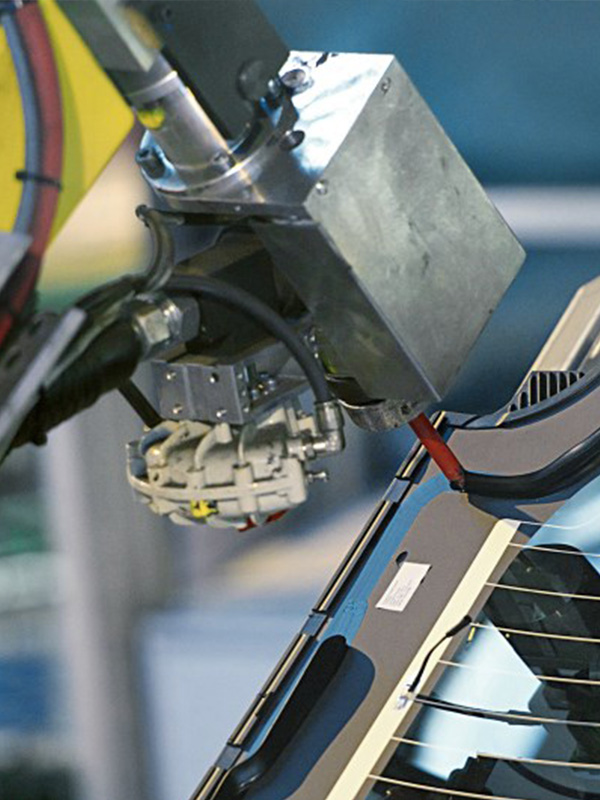
Factors Affecting Glass Bonding Adhesion
Several factors can affect the adhesion of glass bonding, including:
- Surface preparation: The glass surface must be cleaned thoroughly to remove contaminants such as dirt, oil, or fingerprints that may affect adhesion.
- Type of adhesive: Different adhesives are designed for different applications and have different bonding strengths. The choice of adhesive depends on the specific application requirements.
- Temperature and humidity: The temperature and humidity conditions during the bonding process can affect the adhesive’s curing and the bond’s final strength.
- Substrate material: The substrate material, such as metal or plastic, can affect the adhesion of the adhesive to the glass surface.
- Glass type: Different types of glass, such as tempered or laminated glass, may require specific adhesives and surface preparations for proper bonding.
- Collaborative design: The collaborative design can affect the stress distribution in the bond and influence the overall strength of the bond.
- Surface energy: The surface energy of the glass surface can affect the wetting and spreading of the adhesive, which can affect the overall bond strength.
- Aging and durability: The long-term durability of the bond can be affected by factors such as UV exposure, temperature cycling, and moisture exposure.
Considering these factors when selecting the adhesive and designing the bonding process is essential to ensure a solid and durable bond.
Advantages of Glass Bonding Adhesives
Glass bonding adhesives offer several advantages, including:
- Strong bonding: Glass bonding adhesives create a strong bond that can withstand high stress and pressure.
- Clear and transparent: Glass bonding adhesives are typically transparent or clear, making them ideal for use in applications where appearance is essential, such as in the automotive and electronics industries.
- Chemical resistance: Many glass bonding adhesives are highly resistant to chemicals, including acids and solvents, which makes them ideal for harsh environments.
- Versatility: Glass bonding adhesives can bond to various materials, including metal, plastic, ceramic, and other materials.
- Easy to use: Glass bonding adhesives are typically easy to use and can be applied quickly and easily using various application methods, including syringes, spray nozzles, or applicator tips.
- Improved safety: Glass bonding adhesives can be a safer alternative to traditional mechanical fasteners, which can cause damage to the glass and create potential safety hazards.
Overall, glass bonding adhesives offer a reliable and efficient way to bond glass to other materials while providing several benefits over traditional mechanical fastening methods.
Applications of Glass Bonding Adhesives in Various Industries
Glass bonding adhesives are used in various industries, including automotive, construction, electronics, aerospace, and medical. Here are some specific applications of glass bonding adhesives in these industries:
- Automotive: Glass bonding adhesives are used in automotive manufacturing for windshield installation, rearview mirror bonding, and other glass components.
- Construction: Glass bonding adhesives are used in the construction industry for bonding glass facades, shower enclosures, and other glass components in buildings.
- Electronics: Glass bonding adhesives are used in the electronics industry for bonding glass substrates in flat panel displays, touchscreens, and other electronic devices.
- Aerospace: Glass bonding adhesives are used in the aerospace industry for bonding cockpit windows, cabin windows, and other glass components in aircraft.
- Medical: Glass bonding adhesives are used in the medical industry for bonding glass components in medical devices, such as syringes and vials.
In addition to the above industries, glass bonding adhesives are used in other applications, such as bonding glass components in furniture, jewelry, and art. The use of glass-bonding adhesives has become increasingly popular due to their high strength, durability, and ability to bond dissimilar materials.
Automotive Applications of Glass Bonding Adhesives
Glass bonding adhesives play an essential role in the automotive industry, where they are used for bonding automotive glass components. Here are some specific applications of glass bonding adhesives in the automotive industry:
- Windshield installation: Glass bonding adhesives are commonly used in vehicle windshield installation. The adhesive provides a strong and durable bond between the windshield and the vehicle frame, ensuring that it remains in place and provides a secure barrier against the elements.
- Rearview mirror bonding: Glass bonding adhesives are also used for bonding rearview mirrors to the windshield or vehicle body. This provides a secure and stable mounting for the mirror, reducing vibration and improving visibility.
- Sunroof installation: Glass bonding adhesives are used for bonding sunroofs to the vehicle roof, providing a secure and weather-tight seal.
- Glass panel bonding: Glass bonding adhesives are used for bonding glass panels to vehicle bodywork, such as side windows, backlights, and quarter lights.
- Headlamp bonding: Glass bonding adhesives are used for bonding headlamp lenses to the headlamp body, providing a secure and weather-tight seal.
The use of glass bonding adhesives in the automotive industry has several advantages, including increased strength, improved durability, and reduced weight compared to traditional bonding methods such as mechanical fasteners or welding. Additionally, glass bonding adhesives can provide a more aesthetically pleasing finish with no visible fixings or fasteners.
Aerospace Applications of Glass Bonding Adhesives
Glass bonding adhesives are widely used in aerospace applications due to their excellent bonding properties, durability, and resistance to harsh environmental conditions. Some of the key aerospace applications of glass bonding adhesives are:
- Windshields and windows: Glass bonding adhesives bond aircraft windshields and windows to the fuselage, providing a strong and durable bond that can withstand the high stresses and vibrations experienced during flight.
- Composite structures: Glass bonding adhesives are also used to construct composite structures such as wings, fuselages, and tail sections. These adhesives provide a strong and durable bond between the different layers of composite materials, resulting in a lightweight and highly stable structure.
- Electrical components: Glass bonding adhesives bonds electrical components such as sensors, antennas, and control systems to the aircraft structure. These adhesives provide a secure and reliable bond that can withstand the harsh environmental conditions experienced during flight.
- Interior components: Glass bonding adhesives bonds interior components such as overhead bins, lavatories, and galleys to the aircraft structure. These adhesives provide a solid and durable bond that can withstand the wear and tear of daily use.
Overall, glass bonding adhesives play a crucial role in the construction and maintenance of modern aircraft, providing a robust and reliable bond that helps ensure the safety and reliability of these complex machines.
Medical Applications of Glass Bonding Adhesives
Glass bonding adhesives are versatile materials widely used in various medical applications. Some of the critical medical applications of glass bonding adhesives include:
- Dental Applications: Glass bonding adhesives are commonly used in dentistry to bond tooth-colored restorative materials to teeth. These adhesives offer excellent bonding strength, pleasing aesthetics, and durability, making them an ideal choice for dental restorations.
- Medical Device Assembly: Glass-bonding adhesives bond various medical devices, such as syringes, catheters, and surgical instruments. These adhesives offer good biocompatibility, sterilization resistance, and bonding strength, making them an ideal choice for assembling medical devices.
- Wound Closure: Glass bonding adhesives are used in wound closure applications as an alternative to traditional sutures or staples. These adhesives offer excellent strength, flexibility, and biocompatibility and are particularly useful in wound closure applications where traditional closure methods are not feasible.
- Orthopedic Implants: Glass bonding adhesives are used in orthopedic implants to bond prosthetic components to bones. These adhesives offer excellent bonding strength, biocompatibility, and corrosion resistance, making them an ideal choice for orthopedic implant applications.
- Tissue Engineering: Glass bonding adhesives are used in tissue engineering applications to bond different types of tissue and cells together. These adhesives offer good biocompatibility, cell adhesion, and mechanical strength, making them an ideal choice for tissue engineering applications.
Overall, glass bonding adhesives offer a wide range of benefits for medical applications, including good biocompatibility, excellent bonding strength, and durability, making them an essential component of modern medical devices and applications.
Electronics Applications of Glass Bonding Adhesives
Glass bonding adhesives have a variety of applications in electronics due to their high bonding strength and resistance to thermal and mechanical stress. Here are some examples:
- Display manufacturing: Glass bonding adhesives produce flat panel displays like LCD and OLED displays. They bond the glass substrate to the display panel, providing a robust, durable, and optically clear bond.
- Touchscreen manufacturing: Touchscreens comprise multiple layers, including a glass cover, a touch sensor, and an LCD display. Glass bonding adhesives are used to bond these layers together, providing a robust and reliable bond.
- LED packaging: Glass bonding adhesives bond the LED die to the package substrate. They provide excellent thermal conductivity, which helps to dissipate heat from the LED failure, ensuring reliable operation.
- Solar panel manufacturing: Glass bonding adhesives are used to assemble solar panels, bonding the glass cover to the solar cells. This provides a durable and weather-resistant bond that can withstand the harsh outdoor environment.
- MEMS device manufacturing: MEMS (Micro-Electro-Mechanical Systems) devices are tiny machines that can sense and control their environment. Glass bonding adhesives assemble MEMS devices, bonding the glass cover to the substrate.
Overall, glass-bonding adhesives play an essential role in the electronics industry, providing solid and reliable bonds that are critical for the performance and durability of electronic devices.
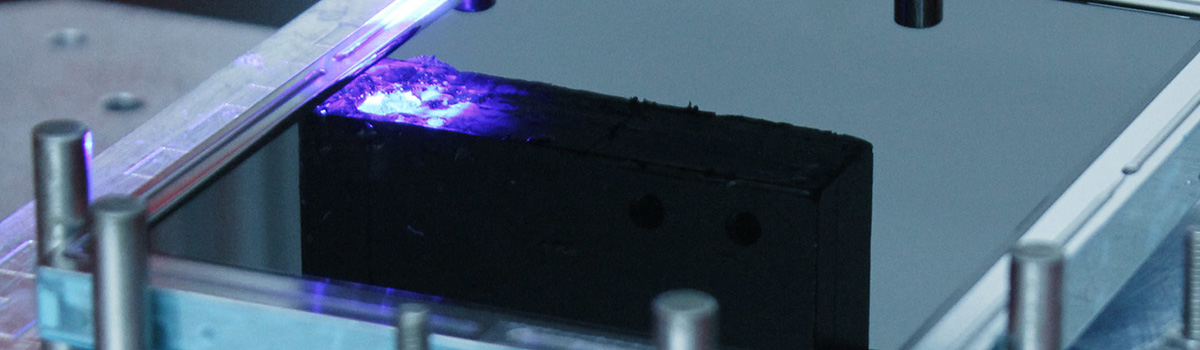
Optical Applications of Glass Bonding Adhesives
Glass bonding adhesives are used in various applications in the optical industry due to their excellent optical properties and strong bonding capabilities. Some typical optical applications of glass bonding adhesives include:
- Display screens: Glass bonding adhesives are used to bond the glass panels of display screens for smartphones, tablets, laptops, and televisions. These adhesives provide high bond strength, excellent optical clarity, and durability.
- Optical lenses: Glass-bonding adhesives bond optical lenses to form complex assemblies. These adhesives provide high optical clarity and can bond different types of glass and other materials, such as plastics and metals.
- Optical filters: Glass bonding adhesives bond different glass filters to create complex optical filters with multiple layers. These adhesives provide high optical clarity and can bond various types of glass and other materials, such as plastics and metals.
- Fiber optic components: Glass bonding adhesives bond different fiber optics components, such as connectors, couplers, and splices. These adhesives provide high bond strength, low insertion loss, and low reflectance.
- Medical devices: Glass bonding adhesives manufacture medical devices such as surgical and diagnostic equipment. These adhesives provide high bond strength, excellent biocompatibility, and resistance to sterilization.
Overall, glass-bonding adhesives play an essential role in the optical industry by providing strong and durable bonds between glass and other materials while maintaining high optical clarity.
Architectural Applications of Glass Bonding Adhesives
Glass bonding adhesives have become increasingly popular in architectural applications due to their unique properties and versatility. Some typical applications of glass bonding adhesives in architecture include:
- Structural Glazing: Structural glazing involves bonding glass panels to a building’s frame without any visible mechanical fasteners. This creates a sleek, modern look and allows maximum natural light to enter the building. Glass bonding adhesives are the preferred choice for structural glazing as they offer high strength and durability and the ability to withstand extreme weather conditions.
- Glass Facades: Glass facades are another popular architectural application of glass bonding adhesives. These facades can be used for commercial and residential buildings and create an eye-catching design while allowing natural light to filter in. Glass bonding adhesives are used to bond the glass panels to the building’s frame, providing a secure and secure and long-lasting connection.
- Glass Balustrades: Glass balustrades are used for balconies, staircases, and terraces to provide a safe barrier while allowing for unobstructed views. Glass bonding adhesives bond the glass panels to the supporting structure, creating a solid and stable wall.
- Glass Canopies: Glass canopies provide shelter from the elements while allowing natural light to enter the building. Glass bonding adhesives bond the glass panels to the supporting structure, creating a secure and long-lasting connection.
Advancements in Glass Bonding Adhesives
Glass bonding adhesives have come a long way in recent years, with several advancements in their formulations and performance. Some of the notable improvements in glass bonding adhesives include:
- Improved bonding strength: Glass bonding adhesives now have greater bonding strength, thanks to advancements in the formulations of the adhesives. These adhesives can directly bond various glass substrates, including tempered, laminated, and annealed.
- Fast curing: With the advent of new curing technologies, glass bonding adhesives can now cure faster, which reduces the time required for assembly and increases productivity.
- UV resistance: Many glass bonding adhesives now have excellent resistance to UV light, which makes them ideal for outdoor applications where exposure to sunlight is a concern.
- Thermal stability: Glass bonding adhesives now have improved thermal stability, which allows them to withstand high temperatures without degrading.
- Reduced VOCs: Volatile organic compounds (VOCs) harm the environment and human health. Many glass-bonding adhesives now have reduced VOC emissions, which makes them safer and more environmentally friendly.
- Versatility: Glass bonding adhesives are now formulated to bond not just glass but also a wide range of materials, including metal, plastic, and composites.
- Enhanced flexibility: Glass bonding adhesives are now available, allowing them to withstand stress and movement without cracking or losing their bond.
Overall, these advancements in glass bonding adhesives have resulted in more robust, versatile, and safer products better suited to modern manufacturing and construction applications.
Future of Glass Bonding Adhesives
The future of glass bonding adhesives is promising, as their demand is expected to continue to increase in the coming years. Here are some of the trends and developments that will shape the future of glass-bonding adhesives:
- Improved Performance: The demand for glass bonding adhesives with enhanced performance characteristics such as better adhesion, durability, and resistance to heat, moisture, and chemicals is expected to increase. Manufacturers are developing new formulations that offer superior bonding strength and flexibility while being more environmentally friendly.
- Innovation in Application: The use of glass bonding adhesives is expanding beyond traditional applications in the automotive and aerospace industries. New applications are emerging in the construction industry, where glass-bonding adhesives bond glass facades, windows, and doors. As the need for sustainability and energy efficiency increases, glass-bonding adhesives are also used to manufacture solar panels.
- Advancements in Manufacturing Technologies: The development of new manufacturing technologies, such as 3D printing, is expected to drive the growth of glass-bonding adhesives. With 3D printing, manufacturers can create complex shapes and designs that are impossible with traditional manufacturing techniques. This will lead to the creation of new products and applications that will require innovative glass-bonding adhesives.
- Increased Environmental Awareness: There is a growing concern about the impact of industrial processes on the environment. This has led to the development of more environmentally friendly glass-bonding adhesives free of volatile organic compounds (VOCs) and other harmful chemicals.
Advantages of Glass Bonding Adhesives over Mechanical Fasteners
Glass bonding adhesives offer several advantages over mechanical fasteners, such as:
- Better aesthetics: Glass bonding adhesives can provide a cleaner and more seamless look since they do not require visible screws or bolts.
- Increased durability: Glass bonding adhesives distribute stress and load evenly across the surface, which reduces the chance of cracking or breaking compared to the concentrated forces of mechanical fasteners.
- Improved insulation: Glass bonding adhesives can provide better insulation than mechanical fasteners, creating gaps and allowing heat or cold to pass through.
- Enhanced safety: Glass bonding adhesives create a secure bond that reduces the risk of accidents or injuries caused by loose or detached fasteners.
- More versatile: Glass bonding adhesives can bond a broader range of materials, including glass, plastic, metal, and composites, which mechanical fasteners may not do effectively.
- Reduced manufacturing and installation time: Glass bonding adhesives can eliminate the need for drilling, tapping, or welding, saving time and labor costs during manufacturing and installation processes.
Overall, glass bonding adhesives can offer a more efficient, reliable, and cost-effective solution than traditional mechanical fasteners, especially when a high aesthetic finish and superior performance are critical.
Challenges with Glass Bonding Adhesives
Glass bonding adhesives have gained popularity recently due to their ability to join glass with other materials such as metals, plastics, and ceramics. However, there are several challenges associated with the use of glass bonding adhesives, including:
- Surface Preparation: Glass surfaces are typically smooth, non-porous, and chemically inert, which makes them difficult to bond using adhesives. Proper surface preparation is essential to remove contaminants, such as oils, dust, and fingerprints, and create a roughened surface to increase adhesion.
- Bond Strength: Achieving a solid and durable bond between the glass and another material can be challenging. Glass bonding adhesives typically require long curing and may need elevated temperatures or UV light to achieve maximum bond strength.
- Compatibility: Not all glass bonding adhesives are compatible with all types of glass. Some bonds may react with the glass surface or cause discoloration or haze, which can affect the optical properties of the glass.
- Thermal Expansion: Glass has a low coefficient of thermal expansion, which means it expands and contracts minimally with temperature changes. If the bonded materials have different coefficients of thermal expansion, the bond may fail due to stresses caused by temperature changes.
- Cost: Glass bonding adhesives can be more expensive than traditional mechanical fasteners or welding techniques, making them less cost-effective for some applications.
Overall, glass bonding adhesives can provide a robust and reliable bond between the glass and other materials, but they require careful surface preparation and selection of the appropriate adhesive for the specific application.
Safety Considerations for Glass Bonding Adhesives
Glass bonding adhesives are used to bond glass to various substrates in different industries, including automotive, aerospace, construction, and electronics. While these adhesives provide many benefits, including excellent strength and durability, they also require careful consideration for safety. Here are some safety considerations for glass bonding adhesives:
- Chemical hazards: Glass bonding adhesives can contain hazardous chemicals, such as isocyanates, which can cause respiratory problems, skin irritation, and allergic reactions. Before using any adhesive, always review the safety data sheet (SDS) to understand the risks and follow appropriate safety precautions.
- Ventilation: Adequate ventilation is essential when working with glass bonding adhesives. The fumes released during the curing process can be harmful if inhaled. Always work in a well-ventilated area or use local exhaust ventilation.
- Personal protective equipment (PPE): Always wear the appropriate PPE when working with glass bonding adhesives. This may include gloves, safety glasses, respirators, and protective clothing.
- Surface preparation: Proper surface preparation ensures a solid bond between the glass and substrate. This may involve cleaning the surface with a solvent, sanding or abrading the surface, or using a primer. Always follow the adhesive manufacturer’s instructions for surface preparation.
- Curing time and temperature: Curing time and temperature can affect the strength of the bond. Always follow the manufacturer’s instructions for fixing time and temperature.
- Storage and handling: Proper storage and handling of glass bonding adhesives are essential for maintaining their effectiveness and safety. Store adhesives in their original containers in a cool, dry place, and keep them out of reach of children and pets.
- Disposal: Dispose of used adhesive and its containers properly, following local regulations and guidelines.
Environmental Considerations for Glass Bonding Adhesives
Glass bonding adhesives play an essential role in manufacturing many products, from automobiles to electronics and construction materials. When considering the environmental impact of glass bonding adhesives, several factors should be taken into account:
- Toxicity: The toxicity of the adhesive and its components should be evaluated to ensure that they do not hurt the environment or human health.
- Emissions: Adhesives that emit volatile organic compounds (VOCs) can contribute to air pollution and negatively affect human health. Low VOC or VOC-free adhesives are preferred to minimize their environmental impact.
- Disposal: The disposal of unused adhesive and waste materials from the bonding process should be appropriately managed to avoid environmental contamination. Bonds that can be easily recycled or disposed of without ecological harm are preferred.
- Energy consumption: The manufacturing process of adhesives requires energy, and the energy sources used can have varying levels of impact on the environment. Sealants produced using renewable energy sources or with a low carbon footprint are preferable.
- Packaging: Adhesive packaging should be designed with the environment in mind, using recyclable or biodegradable materials whenever possible.
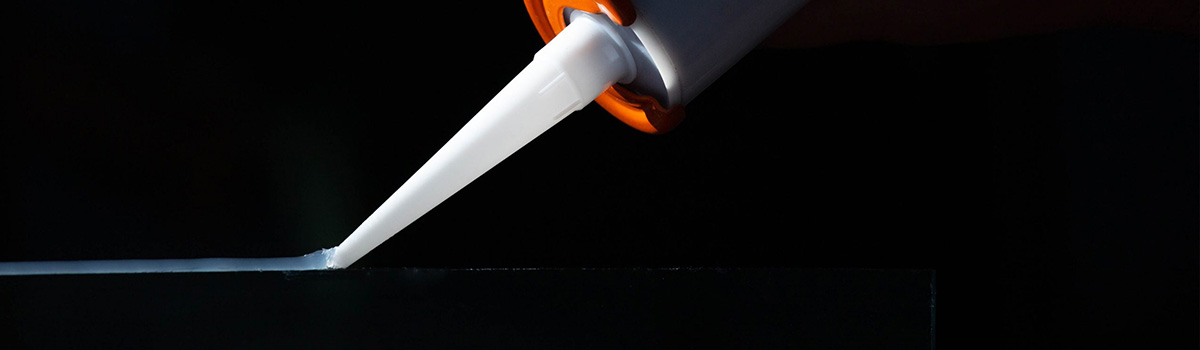
Tips for Successful Glass Bonding Adhesive Applications
Here are some tips for successful glass bonding adhesive applications:
- Surface preparation: Make sure the glass surfaces to be bonded are clean, dry, and free of contaminants. Use a suitable solvent, such as isopropyl alcohol, to remove any residue or dirt from the surface.
- Select the suitable adhesive: Different adhesives have different bonding properties, and not all may be suitable for bonding glass. Choose a bond designed explicitly for glass bonding that meets the requirements of your application.
- Proper application: Apply the adhesive according to the manufacturer’s instructions, making sure to use the right amount and avoid air bubbles. Be sure to apply the adhesive evenly to avoid any areas with excess or insufficient adhesive.
- Clamping and curing: After applying the adhesive, clamp the glass together and allow the adhesive to cure for the recommended time. The curing time may vary depending on the adhesive used and the environmental conditions.
- Environmental considerations: Consider the environment in which the glass will be used, as this can affect the performance of the adhesive. For example, extreme temperatures or moisture exposure can affect some adhesives’ bond strength.
- Safety precautions: Follow all safety precautions when handling and applying adhesives, as some may be hazardous. Wear appropriate protective equipment and work in a well-ventilated area.
Following these tips ensures a successful glass bonding adhesive application and a robust and reliable bond.
Glass Bonding Adhesive Testing Methods
Glass bonding adhesives are commonly used in various industries, including automotive, construction, and electronics. Testing methods for glass bonding adhesives are essential to ensure the adhesive bond is strong and durable. Here are some commonly used testing methods for glass bonding adhesives:
- Lap shear test: This test involves bonding two glass substrates together using the adhesive and then subjecting the bonded sample to a shear force. The test measures the force required to shear the related sample apart.
- Tensile strength test: This test involves bonding two glass substrates together using the adhesive and then subjecting the related sample to a tensile force. The test measures the amount of
- The force required to pull the related sample apart.
- Peel strength test: This test involves bonding two glass substrates together using the adhesive and then subjecting the related sample to a peeling force. The test measures the force required to peel the bonded selection apart.
- Impact resistance test: This test involves bonding a glass substrate to a metal substrate using the adhesive and then subjecting the related sample to an impact force. The test measures the ability of the adhesive bond to withstand impact.
- Accelerated aging test: This test involves subjecting the bonded sample to various environmental conditions, such as heat, humidity, and UV light, to simulate long-term exposure. The test measures the ability of the adhesive bond to maintain its strength and durability over time.
- Microscopic examination: This test involves examining the adhesive bond using a microscope to check for defects or inconsistencies.
It is important to note that the testing method will depend on the specific application and requirements of the glass bonding adhesive.
Quality Control and Assurance for Glass Bonding Adhesives
Quality control and assurance are critical for glass bonding adhesives to ensure that the adhesive’s performance meets the desired standards and provides the necessary bonding strength to hold the glass in place. Here are some of the critical aspects to consider when implementing quality control and assurance for glass bonding adhesives:
- Raw Material Selection: The selection of raw materials used in manufacturing is essential to ensure that the adhesive will bond well with the glass surface. Careful consideration should be given to the quality of the raw materials to ensure consistency and minimize batch-to-batch variation.
- Manufacturing Process: The manufacturing process should be controlled to ensure that the adhesive is consistently produced to the required quality standards. The production process should be monitored, and any variations or deviations should be identified and corrected promptly.
- Testing and Validation: Comprehensive testing and validation procedures should be established to verify the adhesive’s performance, including bond strength, durability, and resistance to environmental factors such as temperature and humidity. The adhesive’s performance should be tested to ensure it can perform reliably in different applications.
- Documentation and Traceability: Comprehensive documentation and traceability systems should be in place to ensure that the adhesive’s quality can be tracked and traced back to its source. This includes maintaining accurate records of raw materials, manufacturing processes, and testing procedures.
- Quality Management Systems: A quality management system should be in place to ensure that all aspects of the manufacturing process are controlled and that any issues or concerns are identified and addressed promptly.
Common Issues with Glass Bonding Adhesives and How to Address Them
Glass bonding adhesives are commonly used in various automotive, construction, and electronics industries. However, they can be prone to specific issues affecting their performance. Here are some common problems with glass bonding adhesives and how to address them:
- Poor adhesion: One of the most common issues with glass bonding adhesives is poor adhesion. This can be caused by various factors, including contamination of the glass surface, insufficient curing time, or improper adhesive application. To address this issue, ensure the glass surface is clean and contaminant-free before applying the adhesive. Follow the manufacturer’s instructions for curing time and ensure the adhesive is applied evenly and correctly.
- UV degradation: Some glass bonding adhesives can be prone to UV degradation, which can cause them to break down and lose their strength over time. To address this issue, choose a bond designed to resist UV degradation. You can also consider using a UV-resistant coating or film to protect the adhesive from UV exposure.
- Thermal expansion: Glass and many adhesives have different coefficients of thermal expansion, which can cause the adhesive to fail over time as the glass expands and contracts with temperature changes. To address this issue, choose an adhesive designed to have a similar coefficient of thermal expansion as the glass. Consider using a flexible adhesive that can accommodate the movement of the glass.
- Shear failure occurs when the adhesive fails in response to a shearing force. This can be caused by improper application of the adhesive or using an adhesive that is not strong enough. To address this issue, ensure the adhesive is applied evenly and in the correct quantity. Choose an adhesive that is designed to withstand the shearing forces that will be present in the application.
- Environmental factors: Environmental factors such as moisture, chemicals, and temperature can affect glass bonding adhesives. To address this issue, choose an adhesive designed to withstand your application’s specific environmental conditions. Ensure the adhesive is stored and applied within the manufacturer’s recommended temperature and humidity range.
Best Practices for Glass Bonding Adhesive Storage and Handling
Proper storage and handling of glass bonding adhesives are critical for ensuring their effectiveness and longevity. Here are some best practices to follow:
- Store in a cool, dry place: Glass bonding adhesives should be stored in a cool, dry place away from direct sunlight and sources of heat or moisture. This will help to prevent the adhesive from degrading or curing prematurely.
- Keep containers tightly sealed: Adhesive containers should be tightly sealed when not in use to prevent moisture or other contaminants from entering the container and affecting the adhesive’s performance.
- Follow manufacturer’s recommendations: The manufacturer’s instructions should be followed for storing and handling glass bonding adhesives. This may include storage temperature, shelf life, and container type recommendations.
- Use clean tools and surfaces: Adhesives should be applied using clean tools and onto clean surfaces to prevent contamination that could affect bonding performance.
- Use appropriate protective equipment: Depending on the adhesive and application method, proper protective equipment may be necessary, such as gloves, safety glasses, or a respirator.
- Use adhesive within its shelf life: Glass bonding adhesives have a limited shelf life and should be used within the recommended time frame. Using expired adhesive can result in reduced effectiveness and weaker bonds.
By following these best practices, you can ensure that your glass bonding adhesive is stored and handled correctly and will perform effectively for your bonding needs.
Training and Education for Glass Bonding Adhesive Applications
Training and education for glass bonding adhesive applications can vary depending on the specific type of adhesive and the industry in which it is being used. However, some general steps can be taken to ensure proper training and education in this area:
Understand the basics of adhesive bonding: It is essential to understand the fundamental principles of adhesive bonding, including surface preparation, adhesive selection, and curing methods. This can be done through reading literature, attending seminars, or taking courses on adhesive bonding.
Identify the appropriate adhesive for your application: Many different types of adhesives are available, and each has unique properties and requirements. It is essential to identify the proper sealant for your specific application and to understand how to properly handle, apply, and cure the adhesive.
Practice safe handling and application: Many adhesives can be hazardous if not properly handled. Practicing secure handling and application techniques is essential to ensure the adhesive is used safely and effectively.
Receive hands-on training: Hands-on training is essential for adequately handling, applying, and curing adhesives. This can be done through apprenticeships, internships, or on-the-job training with experienced professionals.
Stay up-to-date with industry developments: The adhesive bonding industry is constantly evolving, and it is essential to stay up-to-date with the latest developments in adhesive technology, safety regulations, and industry best practices. This can be done through attending conferences, reading industry publications, and networking with other professionals in the field.
Proper training and education in glass bonding adhesive applications require theoretical knowledge, hands-on experience, and ongoing professional development. By taking these steps, professionals in this field can ensure that they use adhesives safely and effectively to achieve the best results.
Conclusion: The Benefits of Glass Bonding Adhesives
Glass bonding adhesives offer a range of benefits for various applications. Here are some of the key advantages:
- Strong and durable bond: Glass bonding adhesives provide a solid and durable bond that can withstand various environmental conditions, including extreme temperatures, humidity, and vibration.
- Versatile: Glass bonding adhesives can bond to various materials, including glass, metals, plastics, and composites, making them ideal for multiple applications.
- Clear and transparent: Many glass bonding adhesives are clear and transparent, which makes them ideal for bonding glass components that require a seamless, invisible bond.
- Easy to apply: Glass bonding adhesives can be used easily with minimal preparation, reducing the need for complex or time-consuming application methods.
- Cost-effective: Using glass bonding adhesives can be cost-effective compared to traditional bonding methods, such as welding or mechanical fastening.
Overall, glass bonding adhesives offer numerous benefits and can be an excellent choice for various industrial, automotive, and aerospace applications.