What Are Potting Materials for Electronics?
What Are Potting Materials for Electronics?
Protecting electronic devices from the elements and potential damage is nothing to take lightly. This is where potting materials come in – they play a significant role not only in guarding against environmental hazards but also in improving their durability and reliability, plus heat management. These mixtures are designed to safeguard sensitive electronic components from dust, moisture, shocks and more, which could compromise the device’s quality.
So today, let’s go over some of those material types used for potting electronics – uncovering their different characteristics/properties as well as advantages & disadvantages; then move on to looking at applications out there in the industry before wrapping up with a glance at what predictions can be made about its future use.
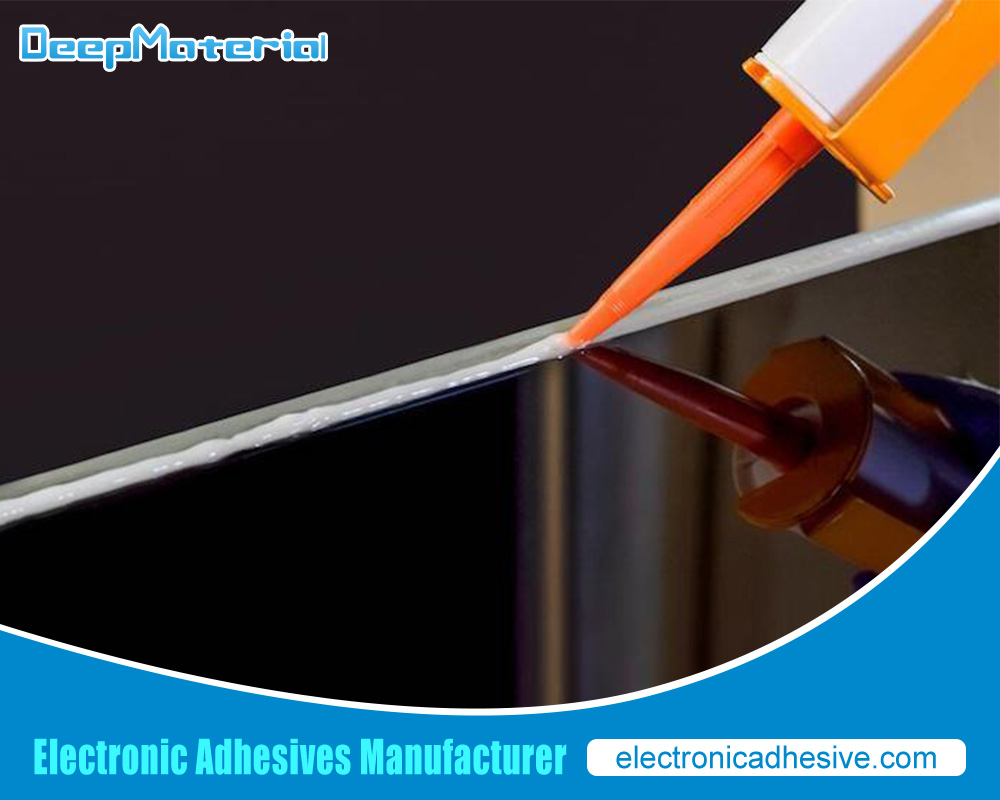
Epoxy Resin as a Popular Potting Material
Epoxy resin is the go-to potting material when it comes to electronic devices for a reason: its impressive characteristics and properties are tough to beat. Its excellent electrical insulating qualities protect against dangerous voltage while delivering great stability to guard everything from shocks to vibrations.
Not only can epoxy resin bind well with several materials from metal to ceramics – making encapsulation of components smoother – but it’s also super easy and fast to mix up and apply, all while curing efficiently at room temperature or even faster with heat.
Unfortunately, though, this pandora of positive attributes does come coupled with some drawbacks because although resilient, on the one hand, epoxy can be pretty brittle and thus prone to cracking under strain – not as flexible as other silicone-based potting materials either.
However, that doesn’t take away much of its glamour given the range of applications where you see it featured, whether they be power supplies or sensors/connectors needing extra moisture/dust/environmental protection.
Silicone-Based Potting Materials for Electronics
Silicone-based potting materials are a popular choice due to their remarkable resistance to moisture, chemicals, and high temperatures. These substances offer good electrical insulation, provide superior tolerance against voltage spikes and have unique self-healing abilities – able to mend minor tears or punctures!
The malleability or flexibility of silicone makes them perfect for complex equipment as they can effortlessly mold themselves around components and deliver reliable protection from shocks and vibrations in the process. Coupled with that, these gels boast outstanding adhesion properties, allowing manufacturers to seal delicate products into their environment with ease.
That said, compared to epoxy resin, there’s a trade-off when you use silicone; its weaker mechanical strength means it may not be suitable for applications where firmness is vital, while heat conduction at lower levels leaves it lagging behind relative competition too slowing dissipating heat build-up more slowly than expected requirements suggest if any device generates serious degrees of warmth.
Even so, many electronic devices worldwide already rely on silicone superiority over other bindings, such as LED lighting fixtures. In addition, automobile parts plus outdoor sensors take advantage of these amazing traits every day.
Polyurethane Potting Materials for Electronics
Polyurethane potting materials are the best of both worlds – they bring together all the great qualities of epoxy resin and silicone-based materials, such as incredible electrical insulation abilities, superior defence against moisture and chemicals, and higher mechanical strength than you can shake a stick at. Its delightful flexibility makes it perfect for those applications that need to handle huge temperature range changes.
But don’t be fooled by their versatility. The high mechanical strength these guys possess means that your components get complete protection from any shock or vibrations – not just resist but thrive! Plus, they have fantastic adhesion capability, so no matter what substrate you’re mounting on, there shouldn’t be an issue.
Of course, there’s always a trade-off – the one in this case being heat dissipation properties. So, if your application lends itself more towards hot temperatures, then polyurethane might not fit quite perfectly into the equation; similarly, its slightly lower suppleness (compared to silicon) means it wouldn’t represent good permeability when dealing with extreme stability demands either.
All considered, though, let’s remember why polyurethane remains popular among many electronic results: When seeking a balance between mechanics and flexes alike – think consumer electronics, industrial control systems and medical devices.
Advantages and Disadvantages of Different Potting Materials
Think twice when selecting a potting material for your electronic devices; Each offers its own set of pros and cons. Epoxy resin provides excellent insulation and strength, but these could be offset by brittleness or the tendency to crack.
Silicone-based materials bring flexibility plus moisture-blocking protection in tough temps, though they can’t match epoxy’s robust supportive power. When looking for an equilibrium, polyurethane materials come close – offering heat dissipation and elasticity – yet not quite reaching their competitors’ levels.
Factors to Consider When Choosing a Potting Material for Electronics
Picking out the perfect potting material for electronics sounds like a serious job. Still, it really isn’t so daunting once you get the hang of it – all you have to do is take into consideration a few key environmental factors, such as being dust-free, staying at an optimal temperature, handling moisture and protecting against any strong chemicals.
Thermal management requirements
Keeping everything cool is vital for electronic devices. If the heat build-up gets too much, there could be a meltdown. So, it’s essential to choose potting materials that have superb heat-shedding properties and top-notch thermal conductivity, which transfers warmth away from essential elements.
Mechanical properties such as flexibility & mechanical strength
Besides having good cooling potential, these should give enough mechanical sturdiness and protection versus vibration or shock. Plus, they’ve got to stick! To guarantee components are entirely encapsulated in place without fail.
Cost is another factor to consider
Sure, epoxy resin costs slightly more than silicone or polyurethane, but if you tailor your pick to specific needs, you’ll save yourself some bucks, plus way more peace of mind.
Potting Techniques and Best Practices for Electronic Devices
Prepping your electronic devices with proper potting techniques and best practices is a must to get that protective coating right! First order of business- scour the equipment for any gunk or debris, then dry them up like nobody’s business. Make sure you have all those parts situated where they should be – no shambling while it sets.
To get that perfect pot, mix the material according to directions for a uniform blend. Ludicrously slather it on evenly so as to dodge any air bubbles in the process – we don’t need gaps in protection.
Curing comes next; following manufacturer guidelines is essential. Ensure that this step is completed for optimal results.
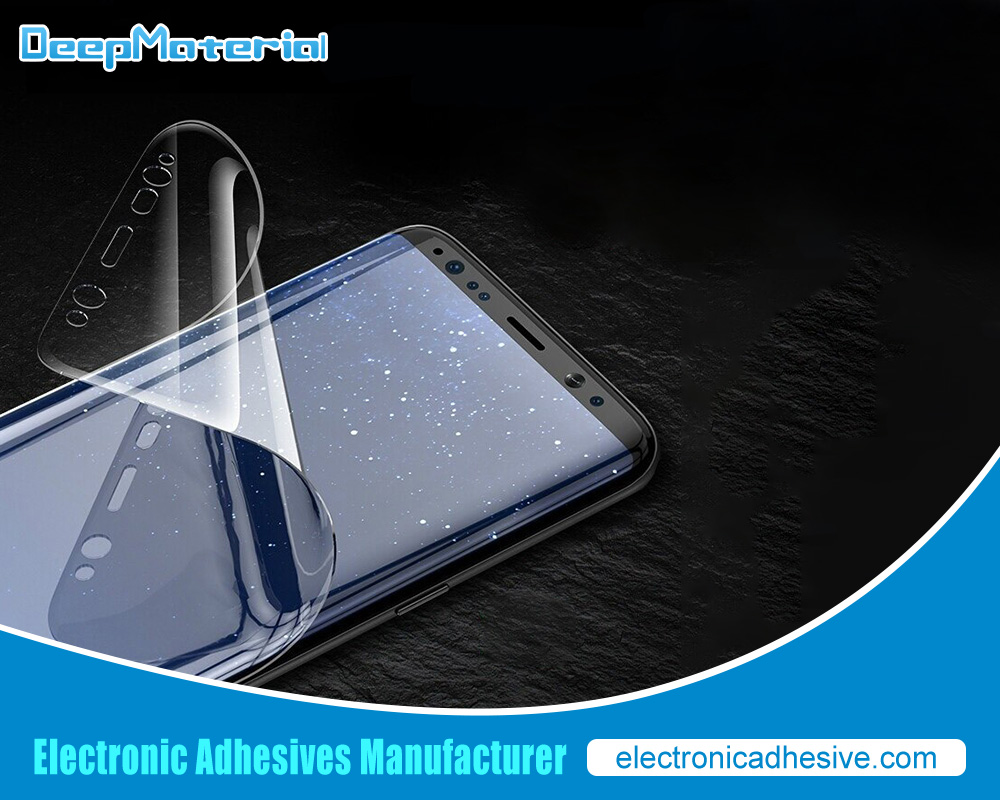
Final Thoughts
Selecting the appropriate material for potting electronics is an integral part of safeguarding gadgets from exterior threats, amplifying their longevity and dependability, and strengthening thermal management. Epoxy resin, silicone-based potting materials, and polyurethane are typically used in electronic instruments due to their prized traits.
When deciding on a material for potting your electronics, you must keep several aspects in mind, like environmental factors, temperature command needs, mechanical characteristics, and cost. In addition to that, properly performing the task of applying protective encapsulation and following best practices also help protect against unfavorable external conditions.
For more about choosing the Potting Materials for Electronics, you can pay a visit to DeepMaterial at https://www.electronicadhesive.com/about/ for more info.