The importance of Non Conductive Coating for Electronics: A Comprehensive Guide
The importance of Non Conductive Coating for Electronics: A Comprehensive Guide
Non conductive coating plays a crucial role in protecting electronic devices from various environmental factors and ensuring their longevity and performance. With the increasing complexity and miniaturization of electronic components, the need for effective protection against moisture, dust, and other contaminants has become more important than ever. Non conductive coating provides a barrier that prevents electrical shorts and other issues that can arise from exposure to these elements.
In this article, we will explore the importance of non conductive coating for electronics, its role in electronic devices, the benefits it offers, different types of coating materials, application techniques, maintenance and repair, common issues, industry standards, and future developments in this technology.
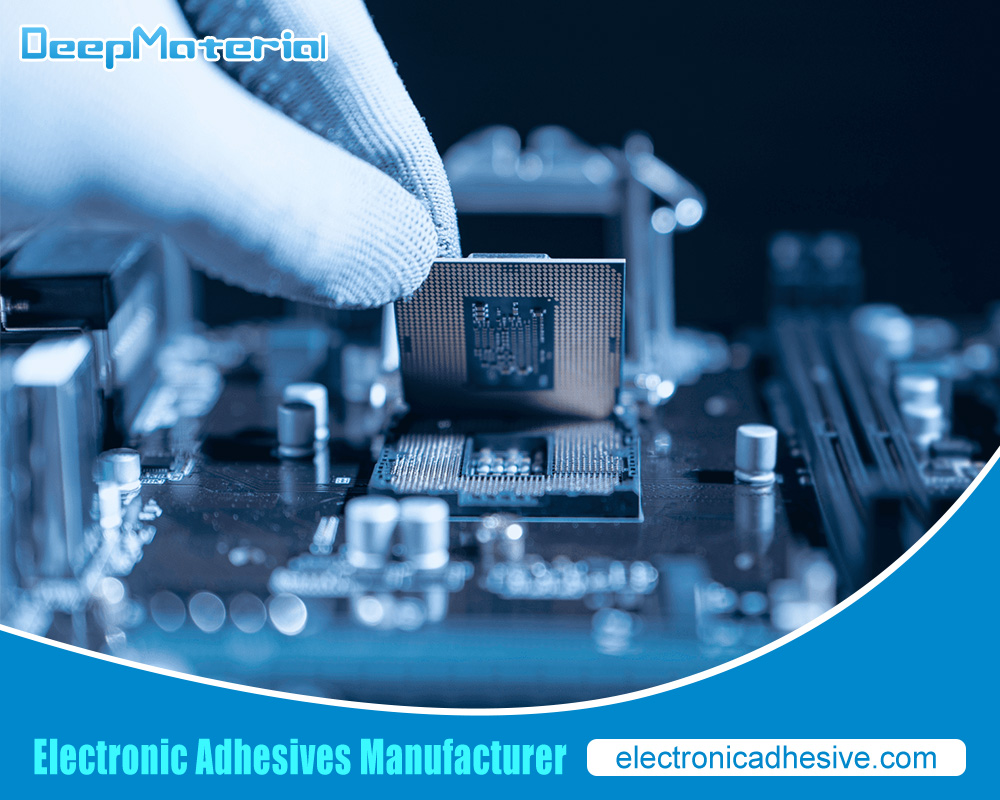
Understanding Non Conductive Coating for Electronics
Non conductive coating is a thin layer of material that is applied to the surface of electronic components to provide insulation and protection. It is designed to prevent the flow of electricity and protect the components from dust, chemicals, moisture, and other contaminants. The coating acts as a barrier between the components and the external environment, ensuring their safety and functionality.
Non conductive coating works by creating a protective layer that prevents electrical conductivity. It is typically made of materials that have high resistivity, such as acrylic, silicone, epoxy, or polyurethane. These materials have low electrical conductivity and high dielectric strength, which means they can withstand high voltages without breaking down. When applied to electronic components, the coating forms a thin film that covers the surface and fills in any gaps or crevices, providing a uniform layer of insulation.
The Role of Non Conductive Coating in Electronic Devices
Its major role is to protect the components from moisture, dust, and other contaminants that can cause damage or malfunction. Moisture is one of the biggest threats to electronic devices as it can lead to corrosion, short circuits, and other electrical issues. Dust and other contaminants can also accumulate on the surface of the components and interfere with their performance.
Non conductive coating acts as a barrier that prevents moisture, dust, and other contaminants from reaching the components. It seals the surface and fills in any gaps or crevices, ensuring that the components are fully protected. By providing insulation, the coating helps prevent electrical shorts and other issues that can arise from exposure to moisture or contaminants. It also helps to maintain the integrity of the components and extend their lifespan.
Benefits of Non Conductive Coating for Electronic Components
Non conductive coating offers several benefits for electronic components. Firstly, it increases the durability and longevity of the devices by protecting them from moisture, dust, and other contaminants. This helps to prevent corrosion, short circuits, and other electrical issues that can lead to device failure. By extending the lifespan of the components, non conductive coating reduces the need for frequent repairs or replacements, saving time and money.
Secondly, non conductive coating improves the performance and reliability of electronic devices. By providing insulation, it helps to maintain the integrity of the components and prevent electrical shorts or other issues that can affect their functionality. This ensures that the devices operate at their optimal level and deliver consistent performance over time.
Lastly, non conductive coating reduces the risk of damage from environmental factors. It acts as a protective barrier that shields the components from moisture, dust, chemicals, and other contaminants. This is particularly important in harsh or demanding environments where electronic devices are exposed to extreme humidity, temperatures, or corrosive substances. The coating helps to maintain the performance and reliability of the devices under these conditions, ensuring their functionality and longevity.
Application Techniques for Non Conductive Coating on Electronic Devices
There are several application techniques that can be used to apply non conductive coating on electronic devices. The choice of application method depends on factors such as the size and shape of the components, the desired thickness of the coating, and the specific requirements of the application. Some of the most commonly used application methods include spray, dip, and brush.
Spray application is a popular method for applying non conductive coating as it allows for fast and uniform coverage. It involves using a spray gun or aerosol can to apply the coating in a fine mist onto the surface of the components. Spray application is suitable for large or complex components that require a thin and even coating. It is also ideal for applications that require a high level of precision or control over the thickness of the coating.
Dip application involves immersing the components into a bath of non conductive coating material. The components are dipped into the bath and then removed, allowing the excess coating to drain off. Dip application is suitable for small or simple components that can be easily immersed in the coating material. It is a cost-effective method that allows for fast and efficient coverage of multiple components at once.
Brush application involves using a brush to apply the non conductive coating onto the surface of the components. The brush is dipped into the coating material and then used to spread it evenly over the surface. Brush application is suitable for small or irregularly shaped components that require a thicker or more controlled coating. It allows for precise application and can be easily adjusted to achieve the desired thickness.
When choosing an application method, it is important to consider factors such as the size and shape of the components, the desired thickness of the coating, and the specific requirements of the application. It is also important to ensure that the application is carried out in a controlled environment to minimize the risk of contamination or other issues.
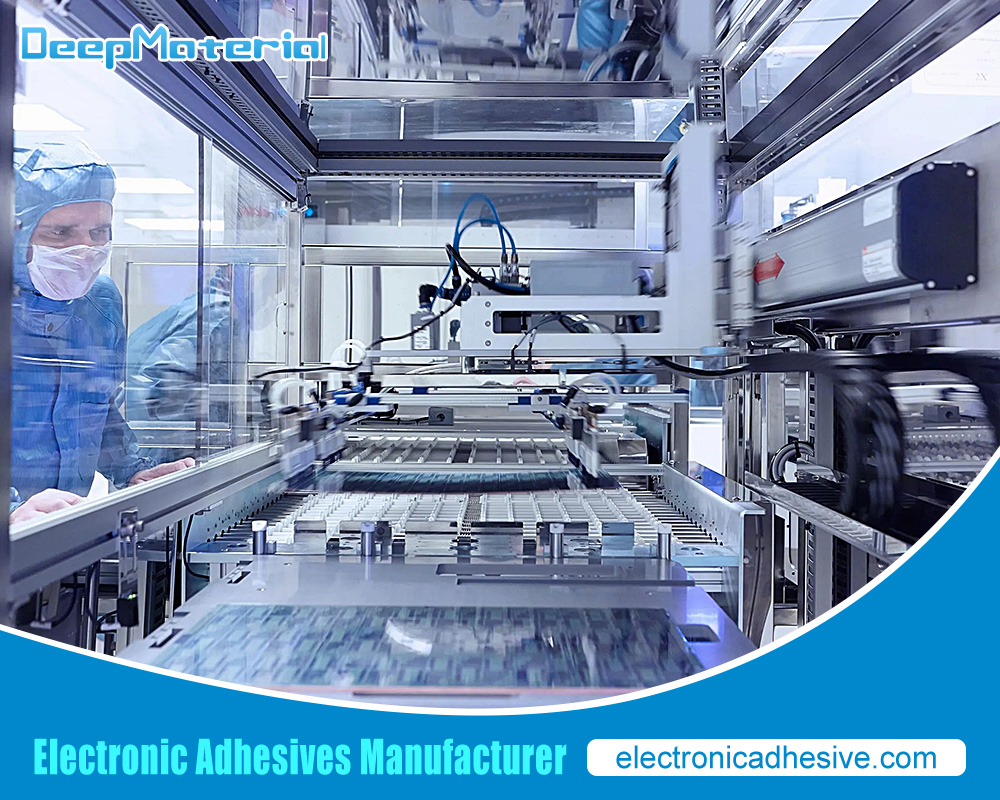
Conclusion
Non conductive coating plays a crucial role in protecting electronic devices from moisture, dust, and other contaminants, ensuring their longevity and performance. It provides insulation and prevents electrical shorts and other issues that can arise from exposure to these elements. Non conductive coating offers several benefits for electronic components, including increased durability and longevity, improved performance and reliability, and reduced risk of damage from environmental factors.
For more about choosing the Non Conductive Coating for Electronics, you can pay a visit to DeepMaterial at https://www.electronicadhesive.com/about/ for more info.