The Impact of Humidity on the Performance of Conformal Coatings for Electronics Applications
The Impact of Humidity on the Performance of Conformal Coatings for Electronics Applications
Conformal coatings act as a shield for electronic components and circuit boards, safeguarding against common environmental nasties like dust, moisture, and harsh chemicals. Keeping these coatings in top shape is paramount to the longevity and optimal functioning of any device relying on them – but that’s an easier said than done task.
You see, with tech devices, one of the biggest super villains is often humidity (which can seriously erode the effectiveness of conformal Coatings). So, understanding how to combat this enemy should be at front-of-mind when designing and fabricating any digital device!
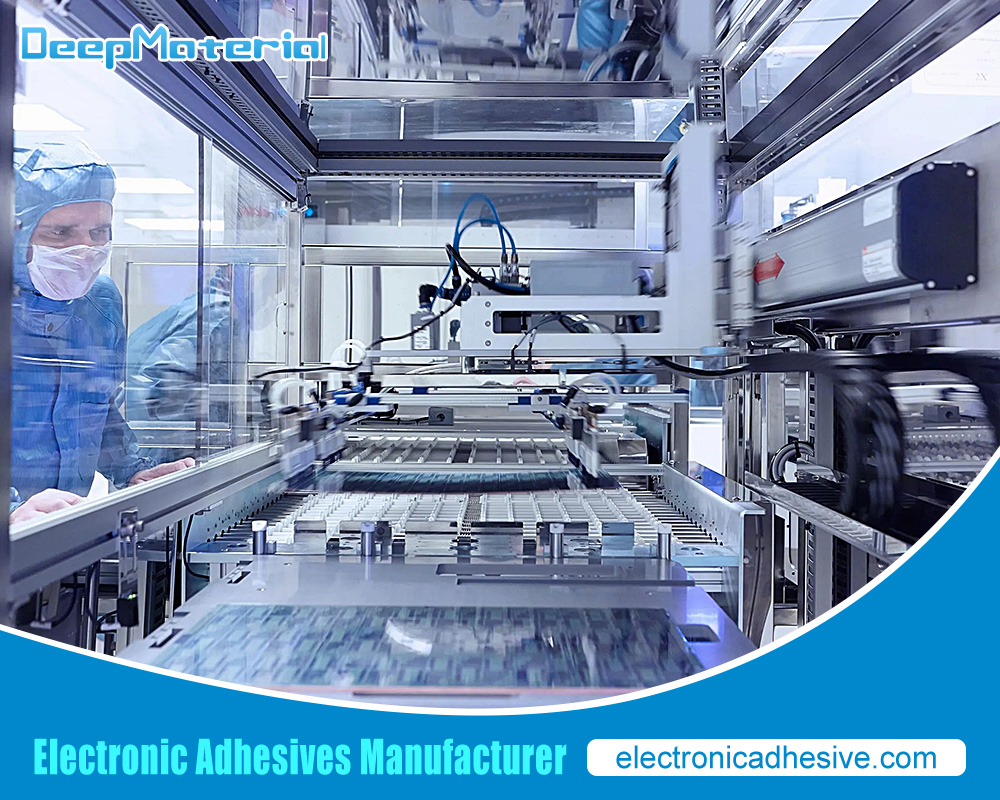
Role of Humidity in Electronics Performance
Humidity can have a detrimental effect on electronic components. Moisture can cause corrosion, which can lead to the degradation of electrical connections and the overall performance of the device. In addition, high humidity levels can also lead to the growth of mold and fungi, which can further damage electronic components. Therefore, it is important to control humidity levels in electronics manufacturing facilities to prevent these issues.
Humidity control is particularly important during the manufacturing process. When electronic components are exposed to high humidity levels during assembly, it can lead to the formation of condensation on the surface of the components. This can result in poor adhesion of conformal coatings, leading to reduced protection against moisture and other environmental factors. Therefore, it is crucial to maintain proper humidity levels in manufacturing facilities to ensure the effectiveness of conformal coatings.
The Effects of Humidity on Conformal Coatings
Humidity can have a significant impact on the performance of conformal coatings. When exposed to high humidity levels, some coatings may absorb moisture, leading to swelling and delamination. This can compromise the protective properties of the coating and expose the electronic components to moisture and other environmental factors.
In addition, high humidity levels can also lead to the formation of bubbles or blisters in the coating. This can occur when moisture becomes trapped between the coating and the surface of the electronic component. These bubbles or blisters can weaken the adhesion of the coating and create pathways for moisture to penetrate the coating, leading to potential damage to the electronic components.
Factors Affecting the Performance of Conformal Coatings in Humid Environments
Several factors can affect the performance of conformal coatings in humid environments. One of the key factors is temperature. High temperatures can increase the rate of moisture absorption by the coating, leading to swelling and delamination. Therefore, it is important to consider the temperature conditions in which the electronic device will be operating when selecting a conformal coating.
Another factor that can impact the performance of conformal coatings in humid environments is the substrate material. Different materials have different levels of moisture absorption and permeability. Some materials may be more prone to moisture absorption, which can lead to swelling and delamination of the coating. Therefore, it is important to select a conformal coating that is compatible with the substrate material to ensure optimal performance in humid environments.
The thickness of the coating can also affect its performance in humid environments. A thicker coating may provide better protection against moisture, but it can also increase the risk of trapping moisture and forming bubbles or blisters. Therefore, it is important to find the right balance between coating thickness and moisture protection when selecting a conformal coating for humid environments.
Testing and Evaluation of Conformal Coatings in High Humidity Environments
Testing and evaluation of conformal coatings in high humidity environments is essential to ensure their effectiveness. There are several methods for testing coating performance in humid conditions. One common method is the salt fog test, which involves exposing coated samples to a salt fog environment to simulate the effects of high humidity and corrosive conditions. This test can help determine the resistance of the coating to moisture and corrosion.
Another method for testing coating performance in high humidity environments is the humidity chamber test. This test involves placing coated samples in a controlled humidity chamber and monitoring the performance of the coating over time. This test can help evaluate the resistance of the coating to moisture absorption, swelling, delamination, and other issues that may arise in humid environments.
It is also important to conduct real-world testing of conformal coatings in high humidity environments. This involves exposing coated electronic devices to actual operating conditions and monitoring their performance over an extended period of time. Real-world testing can provide valuable insights into the long-term performance of the coating and help identify any potential issues that may arise in humid environments.
Best Practices for Applying Conformal Coatings in Humid Conditions
To optimize the performance of conformal coatings in humid conditions, it is important to follow best practices for application. One key tip is to ensure that the surface of the electronic components is clean and free from contaminants before applying the coating. Any dirt, dust, or oils on the surface can interfere with the adhesion of the coating and compromise its effectiveness.
It is also important to apply the coating in a controlled environment with proper humidity and temperature conditions. This can help minimize the risk of moisture absorption and ensure optimal adhesion and performance of the coating. In addition, it is important to follow the manufacturer’s guidelines for application, including the recommended thickness and curing time for the coating.
Proper curing of the coating is also crucial for optimizing its performance in humid conditions. Curing refers to the process of drying or hardening the coating to ensure its adhesion and protective properties. It is important to follow the recommended curing time and temperature for the specific type of coating being used to ensure optimal performance in humid environments.
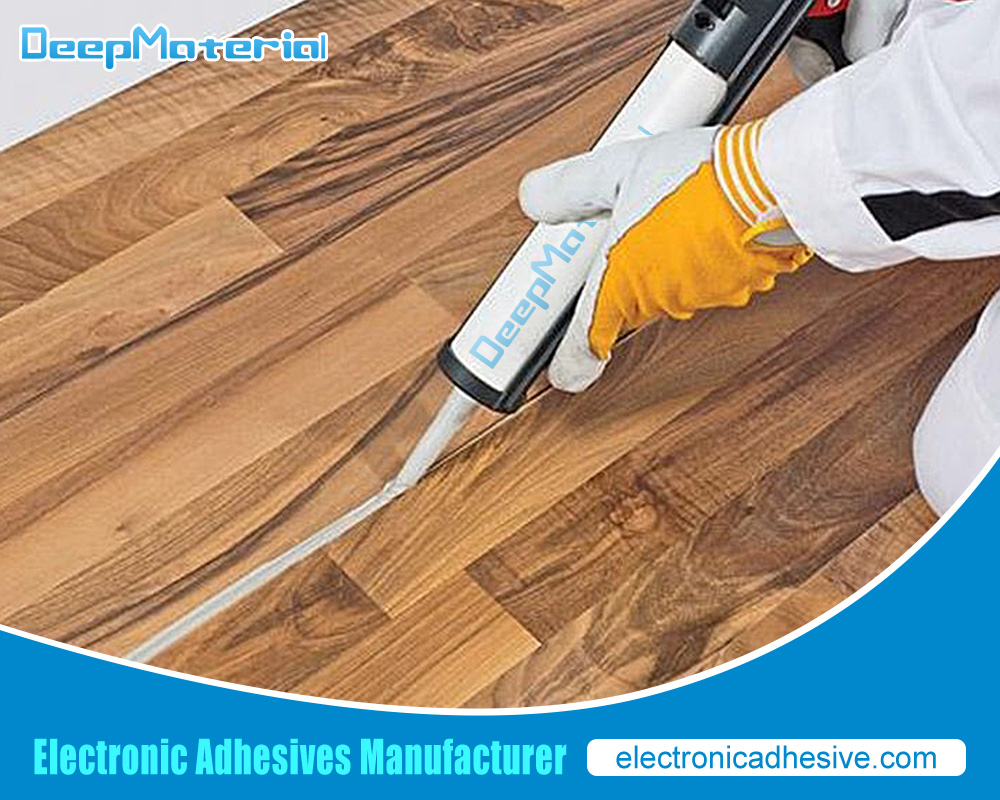
Final Thoughts on Strategies for Optimizing Conformal Coating Performance in Humid Environments
In conclusion, humidity can have a significant impact on the performance of conformal coatings for electronics. It is important to understand the role of humidity in electronics performance and the effects of humidity on conformal coatings. Factors such as temperature, substrate material, and coating thickness can affect the performance of coatings in humid environments.
For more about choosing the Impact of Humidity on the Performance of Conformal Coatings for Electronics Applications, you can pay a visit to DeepMaterial at https://www.electronicadhesive.com/about/ for more info.