Solving Common Challenges with Electronic Assembly Adhesive
Solving Common Challenges with Electronic Assembly Adhesive
Electronic assembly adhesive is a type of adhesive used in the manufacturing of electronic devices. It is a critical component in the assembly process, as it helps to bond different parts of the device together. Electronic assembly adhesive is used in a variety of applications, including bonding components to printed circuit boards, attaching heat sinks to electronic components, and sealing electronic enclosures.
The importance of electronic assembly adhesive in electronic manufacturing cannot be overstated. Without it, electronic devices would not be able to function properly. The adhesive helps to ensure that the components are securely bonded together, which is essential for the device to operate correctly. In addition, electronic assembly adhesive can help to protect the device from environmental factors such as moisture and dust.
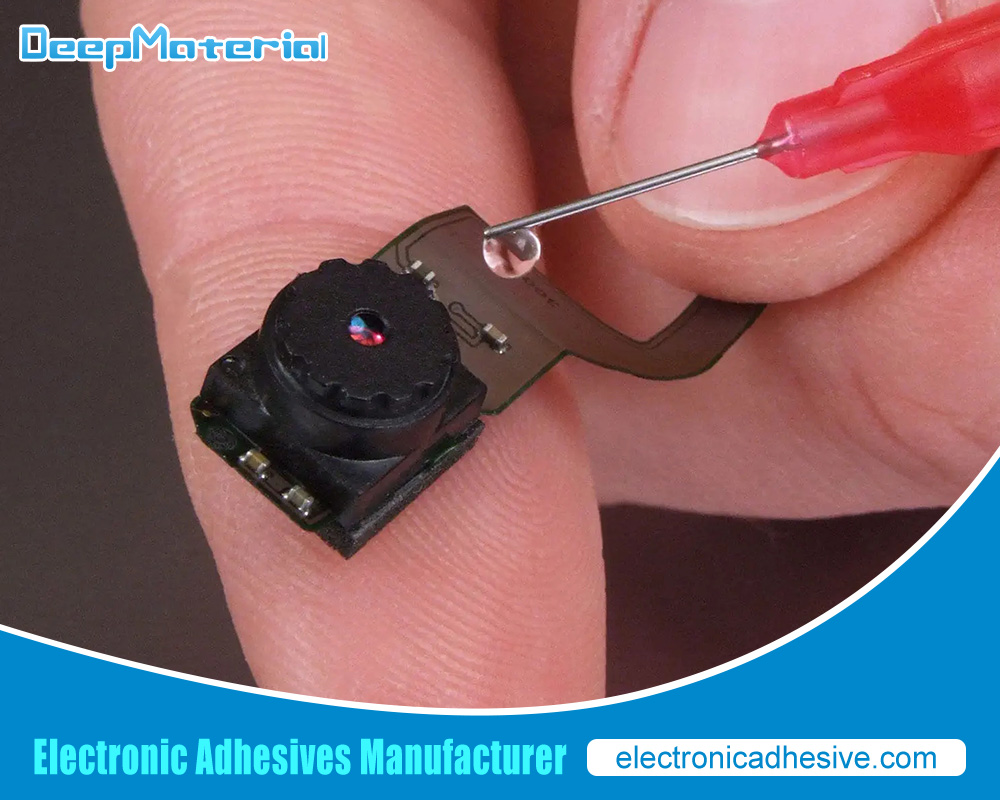
Common Challenges in Electronic Assembly Adhesive and their Solutions
Insufficient Bond Strength
Electronic assembly adhesive is a critical component in the manufacturing of electronic devices. It is used to bond various components together, such as printed circuit boards, chips, and other electronic parts. However, one of the most common challenges that manufacturers face is insufficient bond strength. This can occur for several reasons, including improper surface preparation, incorrect adhesive selection, and inadequate curing time.
Surface preparation is crucial to ensure that the adhesive can bond properly. If the surface is not clean or free from contaminants, the adhesive will not adhere correctly, resulting in weak bonds. Similarly, if the surface is too smooth or too rough, the adhesive may not be able to grip it firmly enough.
In order to enhance the strength of the bond, it is imperative to guarantee that the surface is immaculate and devoid of any impurities prior to the application of the adhesive. Furthermore, the selection of the appropriate adhesive for the specific application is of utmost importance. Ultimately, allocating sufficient time for the curing process will facilitate the assurance that the adhesive has successfully adhered to the substrate.
Poor Dispensing Control
Poor dispensing control is a common challenge faced by manufacturers in electronic assembly adhesive. This issue arises when the adhesive is not dispensed uniformly, leading to an uneven application of the adhesive. This can cause weak bonds between the components, which can result in product failure or malfunction.
Additionally, uneven application of the adhesive can lead to other issues such as excess adhesive buildup, which can interfere with the functioning of the electronic components. To overcome this challenge, manufacturers must ensure that their dispensing equipment is properly calibrated and maintained to ensure consistent and accurate application of the adhesive.
To enhance dispensing control, it is crucial to utilize dispensing equipment of superior quality that is meticulously calibrated and maintained. Furthermore, opting for an adhesive possessing exceptional flow properties can guarantee uniform application.
Inconsistent Curing
Inconsistent curing is a common issue that can arise with electronic assembly adhesive. This occurs when the adhesive does not cure evenly, resulting in weak bonds or other issues. Inconsistent curing can be caused by a variety of factors, including improper mixing of the adhesive components, incorrect application of the adhesive, or inadequate curing time.
When the adhesive does not cure properly, it can lead to a range of problems, such as poor adhesion, reduced strength, and decreased durability. To avoid inconsistent curing, it is important to follow the manufacturer’s instructions carefully and to ensure that all components are properly mixed and applied.
Compatibility Issues with Substrates
These can also be a challenge when using electronic assembly adhesive. This can occur when the adhesive reacts with the substrate or when there is a mismatch between the coefficients of thermal expansion (CTE) of the substrate and the adhesive.
To improve compatibility, it is important to select an adhesive that is compatible with the substrate material. In addition, selecting an adhesive with a similar CTE to the substrate can help to reduce stress on the bond line.
Environmental Factors Affecting Adhesive Performance
Environmental factors such as temperature, humidity, and exposure to chemicals can also affect the performance of electronic assembly adhesive.
To improve performance in different environments, it is important to select an adhesive that is designed for the specific application and environment. In addition, proper storage and handling of the adhesive can help to ensure that it maintains its performance properties over time.
Overcoming Challenges with Proper Surface Preparation
Proper surface preparation is critical for ensuring strong bonds when using electronic assembly adhesive. This involves cleaning and preparing the surface before applying the adhesive.
Best practices for surface preparation include using a solvent or cleaning agent to remove any contaminants from the surface. In addition, roughening or etching the surface can help to improve adhesion by increasing surface area.
Choosing the Right Electronic Assembly Adhesive
This involves considering factors such as substrate material, environmental conditions, and performance requirements.
Types of electronic assembly adhesives include epoxies, acrylics, silicones, and polyurethanes. Each type has its own unique properties and applications.
Epoxies are known for their high strength and chemical resistance and are used in applications where high bond strength is required.
Acrylics are known for their fast cure time and good adhesion to a variety of substrates.
Silicones are known for their flexibility and resistance to high temperatures and are used in applications where thermal cycling is a concern.
Polyurethanes are known for their toughness and durability and are usually used in applications where impact resistance is required.
Best Practices for Electronic Assembly Adhesive Application and Maintenance
These include using high-quality dispensing equipment that is properly calibrated and maintained. In addition, following proper curing procedures and allowing adequate curing time will help to ensure strong bonds.
Maintenance tips for ensuring optimal performance of electronic assembly adhesive include storing it at recommended temperatures and humidity levels and using it before its expiration date.
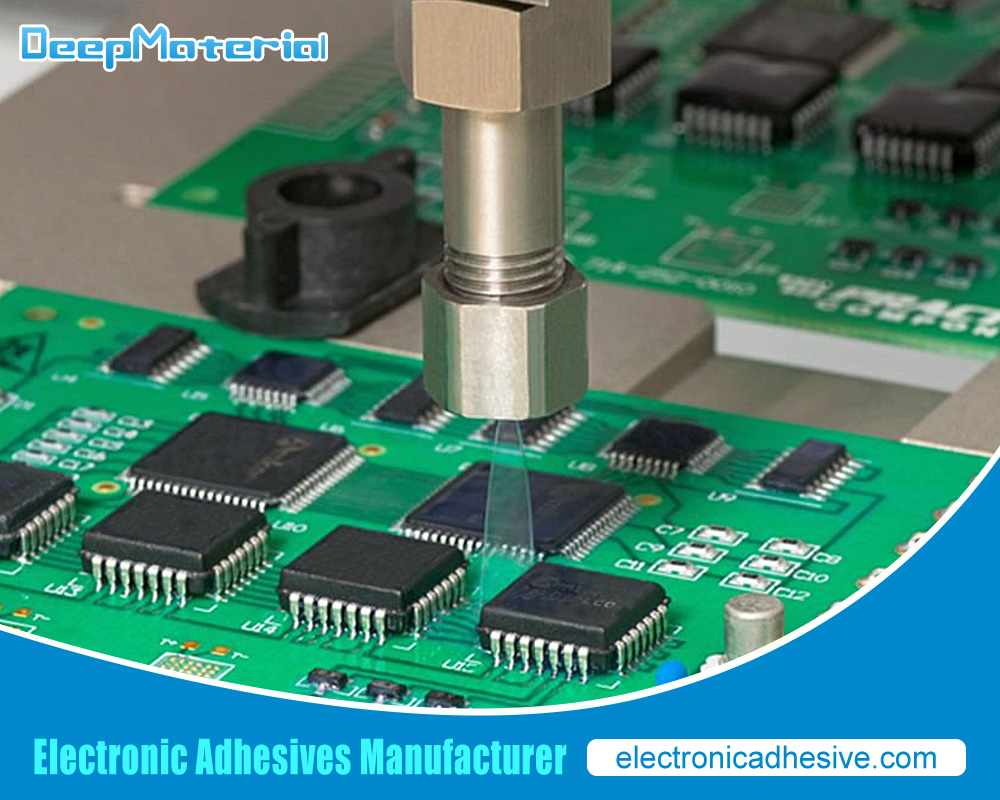
Conclusion
Electronic assembly adhesive plays a critical role in electronic manufacturing by helping to bond different parts of devices together. However, there are several common challenges that can arise when using this type of adhesive. By understanding these challenges and implementing best practices for surface preparation, adhesive selection, application, and maintenance, manufacturers can overcome these challenges and ensure strong bonds that will stand up over time.
For more about choosing the Electronic Assembly Adhesive, you can pay a visit to DeepMaterial at https://www.electronicadhesive.com/about/ for more info.