How Electronic Adhesive Glue Enables Miniaturization in Electronics Manufacturing
How Electronic Adhesive Glue Enables Miniaturization in Electronics Manufacturing
Miniaturization has become a crucial aspect of electronics manufacturing in recent years. As technology continues to advance, the demand for smaller and more compact electronic devices has increased. This has led to the need for innovative solutions that can enable the production of smaller and more efficient electronic components. One such solution is electronic adhesive glue, which plays a vital role in enabling miniaturization in electronics manufacturing.
Electronic adhesive glue is a specialized type of adhesive that is designed to bond electronic components together. It is used in various stages of the manufacturing process, from attaching small components to circuit boards to sealing and protecting delicate electronic parts. By using electronic adhesive glue, manufacturers are able to create smaller and more compact devices without compromising on performance or reliability.
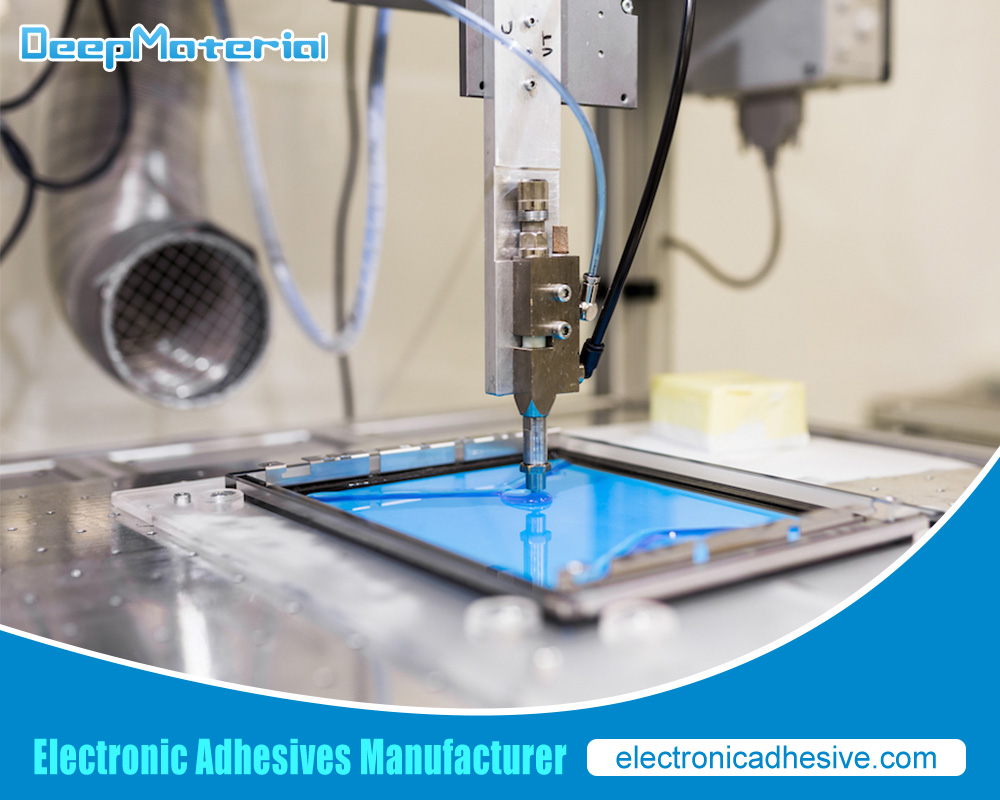
The Importance of Miniaturization in Electronics Manufacturing
Miniaturization is of utmost importance in electronics manufacturing for several reasons. Firstly, smaller devices are more portable and convenient for consumers. Whether it’s a smartphone, a laptop, or a wearable device, people prefer devices that are lightweight and easy to carry around. Miniaturization allows manufacturers to meet this demand by reducing the size and weight of their products.
Secondly, miniaturization enables the integration of more features and functionalities into a single device. As electronic components become smaller, manufacturers can pack more of them into a limited space. This means that devices can offer a wider range of capabilities without increasing in size. For example, smartphones today are able to perform tasks that previously required multiple devices, such as cameras, music players, and GPS systems.
Lastly, miniaturization also leads to energy efficiency. Smaller electronic components require less power to operate, resulting in longer battery life and reduced energy consumption. This is particularly important in today’s world where sustainability is a key concern. By reducing the size of electronic devices, manufacturers can contribute to a greener and more sustainable future.
How Electronic Adhesive Glue Enables Miniaturization
Electronic adhesive glue plays a crucial role in enabling miniaturization in electronics manufacturing. It provides a strong and reliable bond between electronic components, allowing them to be securely attached to circuit boards or other surfaces. This is essential for creating compact and durable devices.
Electronic adhesive glue works by forming a chemical bond between the surfaces it is applied to. It is typically made up of a polymer resin and a curing agent. When the adhesive is applied, the curing agent reacts with the resin, causing it to harden and form a strong bond. This bond is resistant to heat, moisture, and other environmental factors, ensuring the longevity and reliability of the electronic device.
In addition to providing a strong bond, electronic adhesive glue also offers other benefits that enable miniaturization. For example, it can be applied in very thin layers, allowing for precise and accurate placement of components. This is particularly important when working with small and delicate electronic parts. Furthermore, electronic adhesive glue can also act as an insulator, protecting components from electrical interference and preventing short circuits.
Advantages of Electronic Adhesive Glue in Electronics Manufacturing
The use of electronic adhesive glue in electronics manufacturing offers several advantages. Firstly, it provides a strong and reliable bond between electronic components, ensuring the longevity and reliability of the device. This is particularly important in applications where the device may be exposed to harsh environments or subjected to mechanical stress.
Secondly, electronic adhesive glue allows for precise and accurate placement of components. It can be applied in very thin layers, allowing for tight tolerances and precise alignment. This is crucial when working with small and delicate electronic parts, as even a slight misalignment can lead to performance issues or failure.
Furthermore, electronic adhesive glue also acts as an insulator, protecting components from electrical interference and preventing short circuits. This is particularly important in applications where the device may be exposed to electromagnetic radiation or other sources of electrical noise.
In addition to these advantages, electronic adhesive glue also offers cost savings in the manufacturing process. It can be applied using automated dispensing systems, reducing the need for manual labor and increasing production efficiency. Furthermore, electronic adhesive glue is typically less expensive than other bonding methods, such as soldering or welding.
Best Practices for Using Electronic Adhesive Glue in Electronics Manufacturing
To overcome the challenges associated with using electronic adhesive glue in electronics manufacturing, there are several best practices that manufacturers can follow. Firstly, it is important to properly prepare the surfaces that will be bonded. This includes cleaning the surfaces to remove any contaminants or residues that may affect adhesion. It may also involve roughening the surfaces to improve bonding strength.
Secondly, manufacturers should carefully select the appropriate type of electronic adhesive glue for their application. This involves considering factors such as the materials being bonded, the environmental conditions the device will be exposed to, and the required bond strength. Consulting with adhesive suppliers or experts can help ensure the right adhesive is chosen.
Future Trends in Electronic Adhesive Glue for Miniaturization in Electronics Manufacturing
The future of electronic adhesive glue in electronics manufacturing looks promising. As technology continues to advance, the demand for smaller and more compact devices will only increase. This will drive the need for innovative adhesive solutions that can enable miniaturization without compromising on performance or reliability.
One of the future trends in electronic adhesive glue is the development of new materials with enhanced properties. For example, researchers are exploring the use of nanomaterials in adhesive formulations to improve bond strength and thermal conductivity. This could enable the production of even smaller and more efficient electronic devices.
Another trend is the development of adhesive solutions that are compatible with emerging technologies, such as flexible or stretchable electronics. These technologies require adhesives that can withstand repeated bending or stretching without losing their adhesive properties. Researchers are working on developing adhesives that can meet these requirements and enable the production of flexible and wearable devices.
Furthermore, there is also a growing focus on sustainability in electronics manufacturing. Manufacturers are increasingly looking for adhesive solutions that are environmentally friendly and can be easily recycled or disposed of. This has led to the development of bio-based adhesives that are derived from renewable sources and have a lower environmental impact.
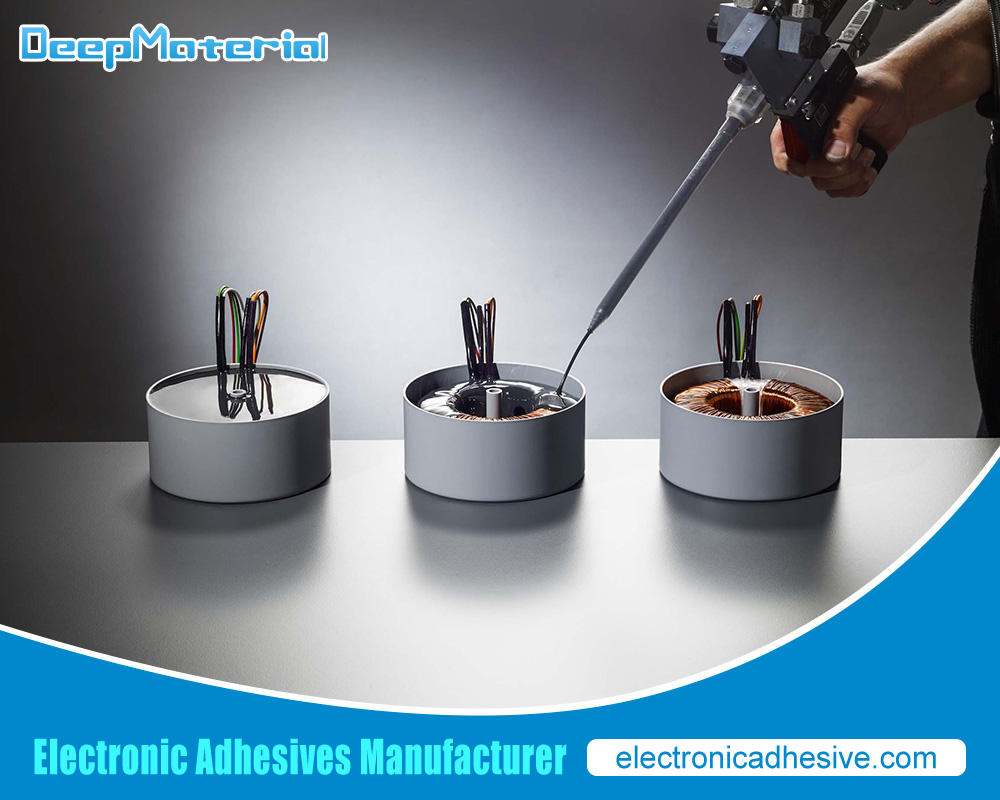
Best
Final Words
In conclusion, electronic adhesive glue plays a vital role in enabling miniaturization in electronics manufacturing. It provides a strong and reliable bond between electronic components, allowing for the creation of smaller and more compact devices. Electronic adhesive glue offers several advantages, including precise placement of components, protection against electrical interference, and cost savings in the manufacturing process.
For more about choosing the Electronic Adhesive Glue Enables Miniaturization in Electronics Mnufacturing, you can pay a visit to DeepMaterial at https://www.electronicadhesive.com/about/ for more info.