How Does Silicone Conformal For PCB Work?
How Does Silicone Conformal For PCB Work?
PCBs are integral to our electronic devices – but those pesky environmental factors like moisture, dust and other contaminants can wreak havoc on them! So, it’s an absolute must to give them a protective barrier.
That’s where conformal coating made of silicone comes in; this layer will make sure your circuits stick with you for the long haul, all while keeping up their performance.
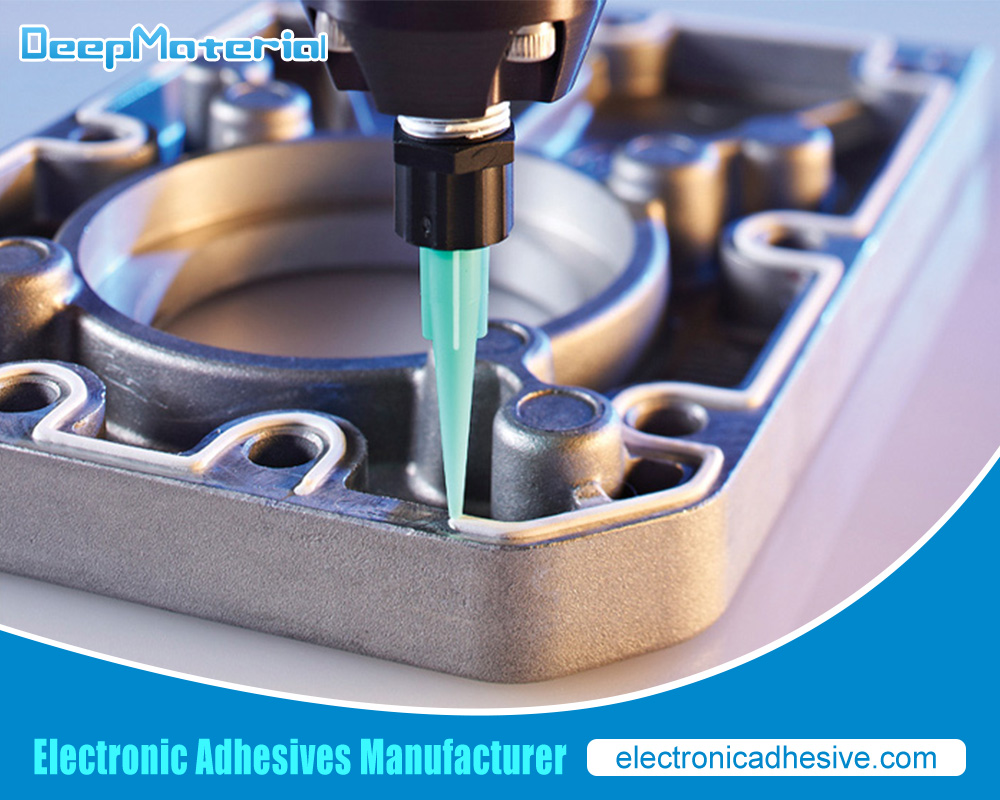
Understanding the Purpose of Conformal Coating on PCBs
Conforming to function, conformal coating is like a cladding for PCBs, providing essential protection from dirt, moisture and other external elements that could corrode delicate electronic parts. This shield creates a protective lag between the board and unforeseen threats like electrical shorts or corrosion.
A range of coatings exists in today’s market; acrylic, epoxy, urethane, and silicone are among them, each granting specific benefits – however, it’s a silicone that stands out with its remarkable defense against moisture as well as excellent insulation, not to mention its fantastic heat resistance which makes it an ideal choice for grim conditions.
How Does Silicone Conformal Coating Protect PCBs from Environmental Factors?
A coating of silicone conformal creates a barrier that shields the delicate components of your PCB from moisture, dust and any other roughhousing. It forms a fragile covering that bonds easily to the board’s surface – blocking out the outside environment as if its fortress walls keep intruders at bay. Moisture or pollutants will have no access to ruin what’s beneath this protective layer.
It also stops issues caused by outside forces like corrosion due to excessive wetness. Without this trusty, faithful guard, metal traces and other boards would be exposed to problematic elements to do their damage – leading to longer-term problems with performance and reducing lifespan.
Moreover, connective insulation across all parts is essential to work when dealing with electrical shorts and wanting to avoid extra Voltage flying in between connected pieces on your PCB. The dielectric qualities within that same Placido protect circuit boards from unwanted contact, meaning you can depend upon expected operation while using electronic devices.
The Role of Silicone Conformal Coating in Preventing Corrosion on PCBs
Corrosion on PCBs is an all-too-familiar problem, emerging when components and traces are exposed to moisture or corrosive elements. Sadly, this kind of corrosion creates severe issues for the device itself; functioning starts getting erratic until it eventually fails altogether.
But with a layer of silicone conformal coating as protection against corrosion, you can dramatically reduce its toll on your electronic board. This barrier efficiently blocks out moisture, which otherwise would enable the formation of electrolytes – basically chemical agents that bring this type of metal degradation about in the first place.
On top of forging an effective shield against substances apt to corrode your circuitry, it impedes destruction from a vast selection of chemicals and solvents, so you won’t be left cruising toward disaster anytime soon.
How Does Silicone Conformal Coating Improve the Lifespan of PCBs?
Environments can be brutal foes of PCBs, with moisture and dust making their impact via corrosion and electrical shorts. But there is a shield for saving these delicate components: silicone conformal coating.
It forms a protective barrier that keeps damaging elements at bay, like moistness-stopping corrosion, heat protection against thermal stressors, and superior insulation to stave off electric pathways causing damage or short circuits. All this adds up to one big boost in preserving the life of these invaluable electronic devices.
Factors to Consider When Selecting the Right Silicone Conformal Coating for PCBs
When selecting the suitable silicone conformal coating for a specific application, several factors need to be considered:
Environmental factors
Taking into account environmental factors like humidity is non-negotiable when selecting a conformal coating for your PCB. If you’re working in an incredibly moist environment, deploying a silicone coating with reliable moisture resistance would be your best bet. It’s always worth considering these sorts of variables before approving the finished product.
Temperature range
Factoring in the temperature range your PCB will have to face is absolutely paramount. Different silicone conformal coatings boast different heat-endurance limits, so it’s critical that you zero in on one with enough grit for your device’s climate conditions – no two ways about it.
Application method
How big and intricate the PCB is will decide which application mode of silicone conformal coating would be best. Specific coatings are better suited when brushing, whereas others perform optimally when sprayed or dipped in.
Compatibility with other materials
It’s critical to inspect PCBs with other components or materials that interact with the silicone conformal coating and make sure they’re compatible. If not, there can be negative repercussions like disruption of performance or harm.
Regulatory requirements
With varying industries and applications, different rules may apply. It’s essential to snag a rubberized sealant that abides by those regulations; think RoHS or, say, UL standards. Sure, it might take some work to find the right one – but trust us when we say you’ll be glad you did.
Maintenance and Repair of PCBs with Silicone Conformal Coating
It’s not too difficult to maintain and repair PCBs with silicone conformal coating, though you should keep a few things in mind.
First off, it’s a good idea to do regular inspections of your board. If there are any areas of the protective coating that have become damaged, make sure to fix them.
When cleaning your PCB, be sure to remove all dirt and dust from its surface – using something like isopropyl alcohol or detergent works well for this.
Of course, if the silicone has worn down over time, then you’ll need to re-coat the whole thing. Just follow the same application process as before.
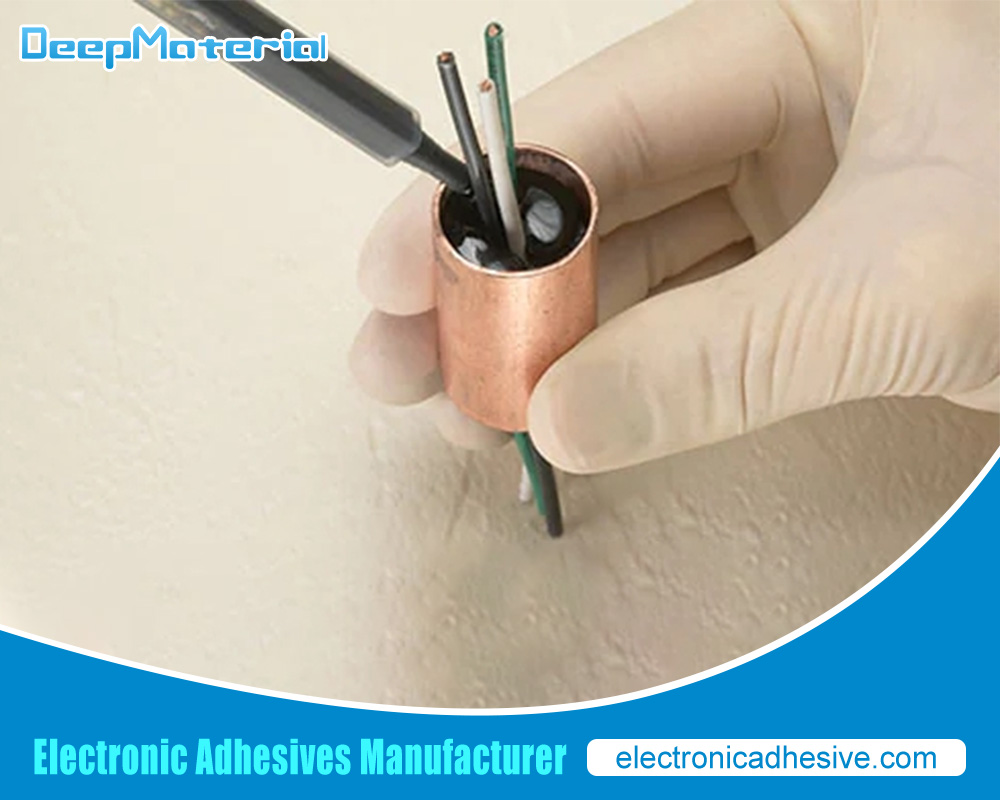
Final Thoughts
Wrapping up, it’s clear that silicone conformal coatings are essential for shielding PCBs from humidity, dust and extreme temperatures. When applied correctly, they act as an adequate safeguard against the elements interfering with delicate components on the board and keep them in top running condition long-term.
What’s more, by opting for this type of coating, you get a wide range of desirable qualities: exceptional moisture protection, high heat tolerances, impressive electrical insulation properties, plus ease of application and repair. All these features combine to form a reliable defense system preventing corrosion or malfunction due to environmental factors from sneaking in.
For optimal PCB coverage, consider tailoring your choice to fit respective requirements – qualified advice comes in handy here, too! Following this guidance allows extending boards’ lifespan while keeping their dependability intact no matter where they’re used!
For more about choosing the Silicone Conformal For PCB, you can pay a visit to DeepMaterial at https://www.electronicadhesive.com/about/ for more info.