Consumer Electronics Bonding Adhesive and its Compatibility with Different Materials
Consumer Electronics Bonding Adhesive and its Compatibility with Different Materials
With the constant evolution of technology, devices are becoming increasingly compact, intricate, and robust. As a result, the demand for adhesives that can match these advancements is of utmost importance. This is precisely where the consumer electronics bonding adhesive comes into the picture.
This adhesive is specifically designed to meet the unique demands of consumer electronics, offering superior bonding strength, durability, and versatility. But what sets this adhesive apart from others on the market? Its compatibility with a wide range of materials. From metals and plastics to ceramics and glass, Consumer Electronics Bonding Adhesive provides a secure bond that can withstand the rigors of everyday use.
In this blog post, we will delve deeper into the world of Consumer Electronics Bonding Adhesive, exploring its unique properties and how it interacts with different materials. We will discuss its application in various consumer electronics devices and how it contributes to their overall performance and longevity.
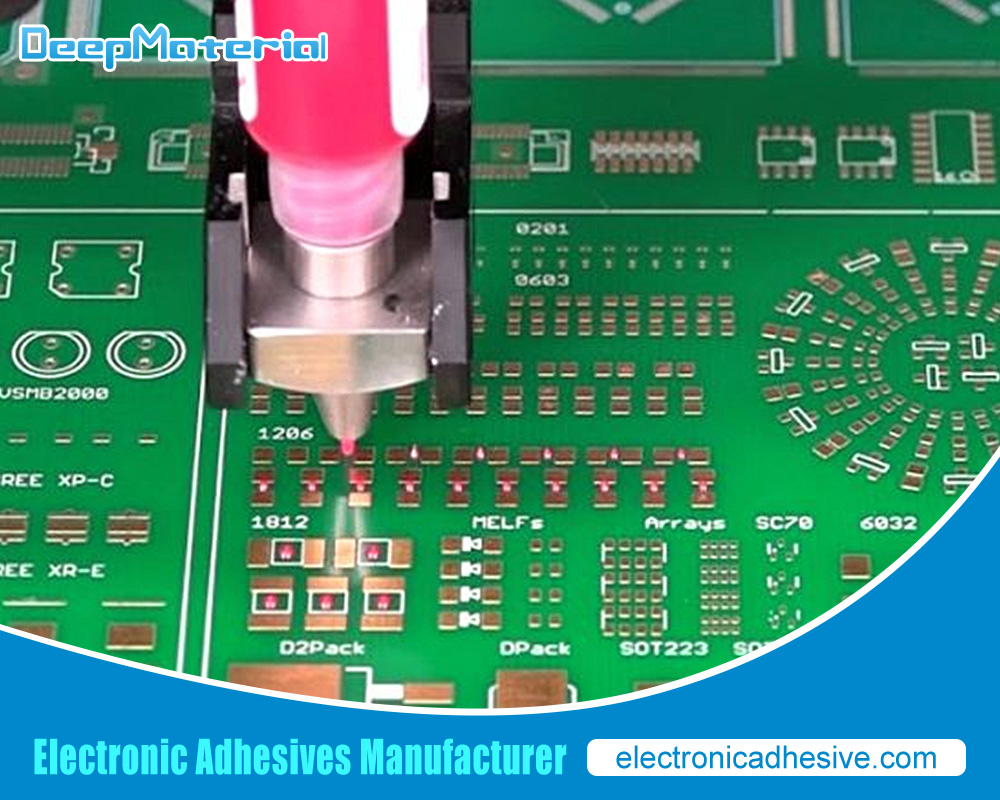
Factors Affecting Compatibility of Bonding Adhesives with Different Materials
Several factors can affect the compatibility of bonding adhesives with different materials. These factors include the chemical composition of the materials, surface energy, and environmental conditions such as temperature and humidity.
The chemical composition of materials plays a significant role in determining their compatibility with bonding adhesives. Different materials have different chemical properties, and some may react with certain types of adhesives. It is crucial to consider the chemical compatibility between the adhesive and the materials to ensure a strong and durable bond.
Surface energy is another important factor that affects compatibility. The surface energy of a material determines its ability to wet out and bond with the adhesive. Materials with high surface energy are easier to bond with adhesives, while those with low surface energy may require surface treatment or the use of specific adhesives to achieve a strong bond.
Temperature and humidity can also impact the compatibility of bonding adhesives. Some adhesives may require specific temperature and humidity conditions for optimal bonding. It is important to consider these factors during the bonding process to ensure the adhesive cures properly and forms a strong bond.
Compatibility of Consumer Electronics Bonding Adhesive with Plastics
The versatility, lightweight nature, and cost-effectiveness of plastics have made them a popular choice for use in a wide range of consumer electronics. However, not all plastics are compatible with the same bonding adhesives. Different types of plastics have different chemical compositions and surface energies, which can affect their compatibility with bonding adhesives.
There are various types of plastics used in consumer electronics, including ABS, polycarbonate, polyethylene, and polypropylene, among others. Each type of plastic requires a specific bonding adhesive that is compatible with its chemical composition and surface energy.
For example, ABS plastics are commonly used in electronic enclosures and require adhesives that can bond well with their low surface energy. Polycarbonate plastics, on the other hand, have high surface energy and can be bonded effectively with a wide range of adhesives.
Applications where bonding adhesives are used with plastics in consumer electronics include bonding display screens to plastic frames, attaching plastic buttons or knobs to electronic devices, and bonding plastic housings or covers together.
Compatibility of Consumer Electronics Bonding Adhesive with Metals
Metals are another common material used in consumer electronics, particularly for connectors, circuit boards, and structural components. Like plastics, different types of metals require specific bonding adhesives that are compatible with their chemical composition and surface properties.
Common types of metals used in consumer electronics include aluminum, stainless steel, copper, and brass, among others. Each type of metal has different surface properties and requires a bonding adhesive that can effectively bond with its surface.
Aluminum has a low surface energy and requires adhesives that can bond well with its surface. Stainless steel, on the other hand, has a high surface energy and can be bonded effectively with a wide range of adhesives.
Examples of applications where bonding adhesives are used with metals in consumer electronics include bonding metal connectors to circuit boards, attaching metal frames or brackets to electronic devices, and bonding metal components together.
Compatibility of Consumer Electronics Bonding Adhesive with Glass
Glass is commonly used in consumer electronics for display screens, touch panels, and camera lenses. Bonding adhesives used with glass need to be compatible with its chemical composition and surface properties to ensure a strong and durable bond.
There are different types of glass used in consumer electronics, including soda-lime glass, borosilicate glass, and aluminosilicate glass. Each type of glass requires a specific bonding adhesive that is compatible with its chemical composition and surface energy.
Compatibility of Consumer Electronics Bonding Adhesive with Ceramics
Ceramics are used in consumer electronics for various applications, including insulators, substrates, and capacitors. Bonding adhesives used with ceramics need to be compatible with their chemical composition and surface properties to ensure a strong and durable bond.
There are different types of ceramics used in consumer electronics, including alumina, zirconia, and silicon nitride, among others. Each type of ceramic requires a specific bonding adhesive that is compatible with its chemical composition and surface energy.
Compatibility of Consumer Electronics Bonding Adhesive with Composites
Composites are increasingly used in consumer electronics for their lightweight and high strength-to-weight ratio. Bonding adhesives used with composites need to be compatible with their chemical composition and surface properties to ensure a strong and durable bond.
There are different types of composites used in consumer electronics, including carbon fiber composites, fiberglass composites, and aramid fiber composites, among others. Each type of composite requires a specific bonding adhesive that is compatible with its chemical composition and surface energy.
Testing Methods for Compatibility of Bonding Adhesives with Different Materials
Testing the compatibility of bonding adhesives with different materials is crucial to ensure the effectiveness and longevity of the bond. There are various testing methods available to determine the compatibility between adhesives and materials.
Some common testing methods include lap shear testing, peel testing, and T-peel testing. These tests measure the strength and durability of the bond between the adhesive and the material. Other tests, such as contact angle measurement and surface energy measurement, can be used to assess the wettability and adhesion properties of the adhesive on the material’s surface.
It is important to conduct these tests under relevant conditions, including temperature and humidity, to simulate the actual operating conditions of the electronic device. This ensures that the bonding adhesive will perform optimally in real-world applications.
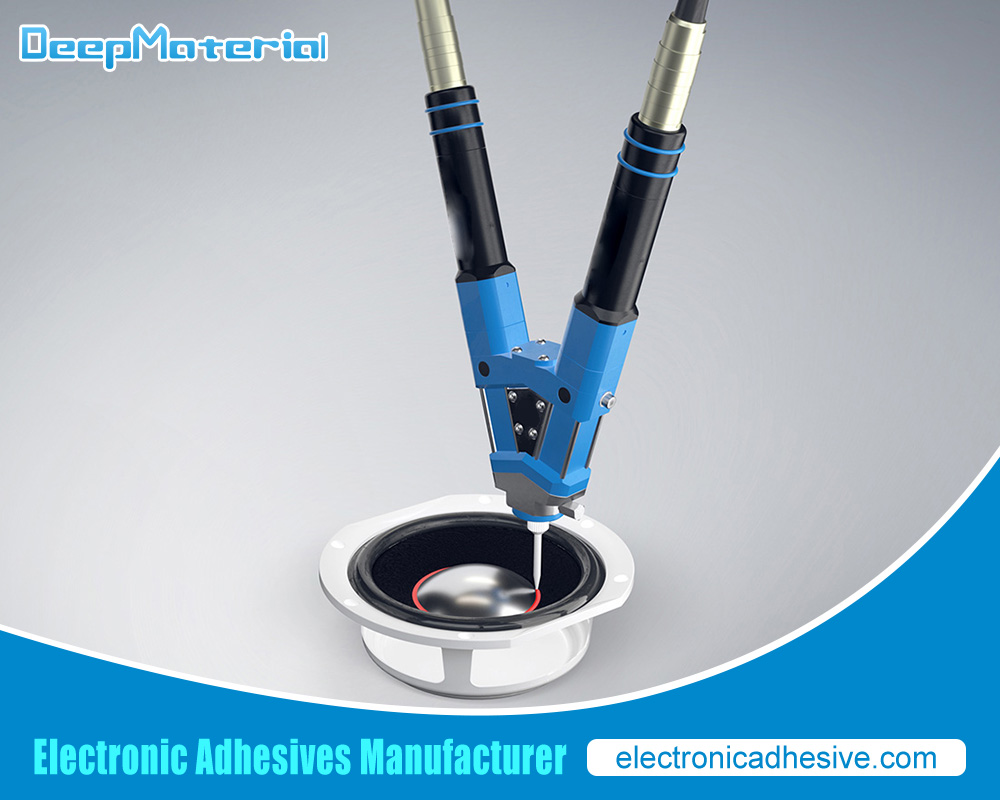
Conclusion: Choosing the Right Bonding Adhesive for Consumer Electronics
Choosing the right bonding adhesive for consumer electronics is crucial to ensure a strong and durable bond between different materials. Compatibility with the materials used in electronic devices is essential to prevent issues such as weak bonds, delamination, or failure of the bond.
When choosing a bonding adhesive, it is important to consider factors such as the chemical composition and surface energy of the materials, as well as the environmental conditions in which the adhesive will be used. Conducting compatibility testing using appropriate methods can help determine the suitability of the adhesive for the specific application.
For more about choosing the Consumer Electronics Bonding Adhesive and its Compatibility with Different Materials, you can pay a visit to DeepMaterial at https://www.electronicadhesive.com/about/ for more info.