Comparing Different Types of Industrial Bonding Adhesives: A Comprehensive Review
Comparing Different Types of Industrial Bonding Adhesives: A Comprehensive Review
Industrial bonding adhesives are key in making and building stuff. They stick different materials together without needing screws or nails. This means things look better, work better, and are made more efficiently.
These adhesives can stick together metals, plastics, and lots more. They’re tough against heat, water, and chemicals, making sure things stay stuck for a long time. You’ll find them in cars, planes, electronics, and all sorts of other products.
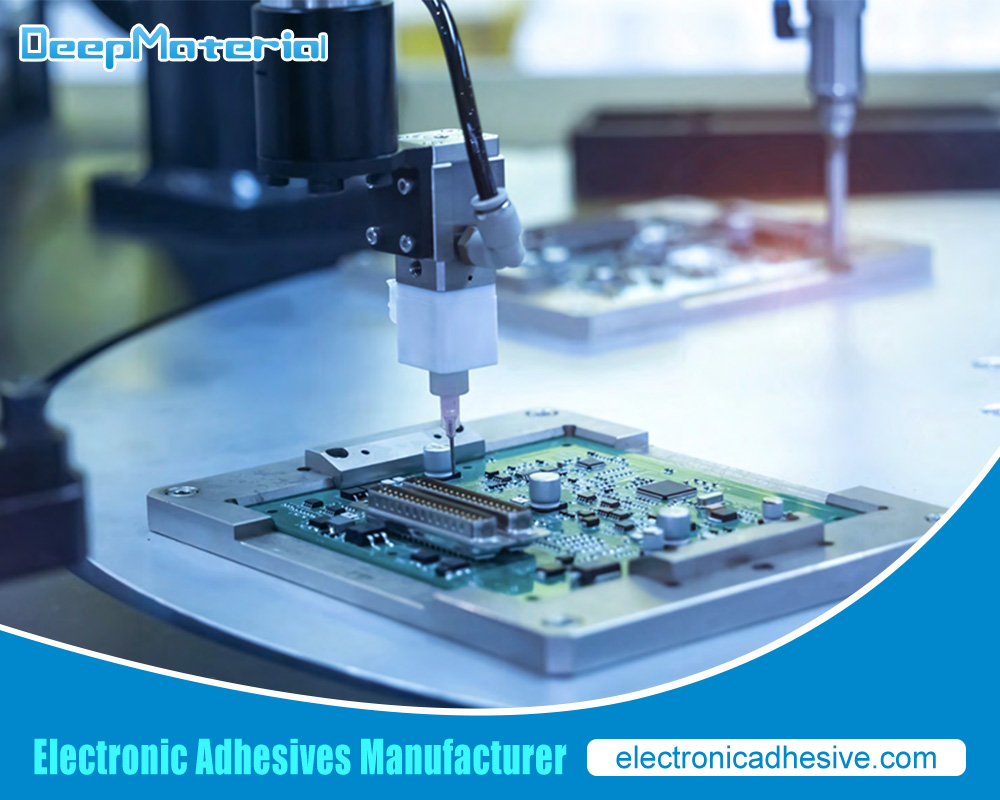
Types of Industrial Bonding Adhesives
Lots of different adhesives are out there, each with its own special features for certain jobs. Here’s a look at a few common ones:
Epoxy Adhesives: Epoxy is very strong and lasts a long time. It sticks to many things and can handle chemicals, heat, and water. It’s great for really important jobs where things need to stay stuck.
Acrylic Adhesives: Acrylic is flexible and sticks to lots of materials. It’s good in the sun and doesn’t get old fast. This is good for when you need a little give in what you’re sticking together.
Cyanoacrylate Adhesives: Also called super glues, these set very fast and stick to many things. They’re perfect when you need something stuck right now and lined up just right.
Comparison of Epoxy Adhesives
Epoxy adhesives are a favorite for many because they’re so strong and versatile. They stick to almost anything and are really resistant to chemicals. But, they take a while to set, and mixing them just right can be tricky. They’re not so good if you need something flexible or if you’re in a huge rush.
Even with these downsides, epoxy is used all over. Cars, planes, electronics, and buildings often use epoxy to make sure parts stay together. It’s especially good for big, important jobs where you need that bond to last.
Comparison of Acrylic Adhesives
Acrylic adhesives offer a balance between strength, flexibility, and ease of use. They provide good bond strength on a variety of substrates and offer excellent resistance to weathering, UV radiation, and aging. However, like any adhesive type, acrylic adhesives have their own set of advantages and disadvantages.
One of the main advantages of acrylic adhesives is their versatility. They can bond a wide range of materials, including plastics, metals, glass, and ceramics. Acrylic adhesives also offer good resistance to environmental factors such as moisture, temperature fluctuations, and chemicals. They are often used in applications that require flexibility, such as bonding plastic components or joining dissimilar materials.
However, acrylic adhesives may not provide the same level of strength as epoxy adhesives. They are generally not recommended for applications that require high load-bearing capabilities or structural bonding. Acrylic adhesives also have a relatively short shelf life compared to other adhesive types, and they may require special surface preparation for optimal bonding.
Despite these limitations, acrylic adhesives find widespread use in various industries. They are commonly used in signage and display manufacturing, automotive assembly, and electronics assembly. Acrylic adhesives are also popular in the construction industry for bonding glass panels, installing windows, and sealing joints.
Comparison of Cyanoacrylate Adhesives
Cyanoacrylate adhesives, or super glues, are famous for setting really fast and sticking really well. They’re great because they bond quickly, stick to lots of materials, and are pretty strong. But, there are a few things to watch out for.
One big plus is they dry in seconds, which speeds up building stuff. They work on metals, plastics, rubber, and ceramics really well. But, they’re not good at filling gaps and can be brittle. They also don’t last long once you open them, and aren’t the best for jobs that need to last a really long time.
Still, they’re used a lot. You’ll find them in making electronics, medical devices, and cars. They’re also handy for quick fixes in woodworking.
Comparison of Polyurethane Adhesives
Polyurethane adhesives are strong, flexible, and stick to many things. They’re resistant to changes in temperature, water, and chemicals. Like all glues, though, they have their ups and downs.
They’re really strong and work on a bunch of materials. They handle the weather and chemicals like champs. But, they take a while to set and might need you to hold stuff together while they dry. They’re also picky about moisture when they’re setting and might need the surfaces to be prepped first.
Despite these issues, they’re used a lot. Car makers use them for putting together body parts and interiors. In building stuff, they’re used for sticking together concrete, wood floors, and insulation.
Comparison of Silicone Adhesives
Silicone adhesives are special because they can handle extreme weather, moisture, and chemicals without a problem. They’re perfect for sealing and sticking things together in tough spots. But they have their pros and cons too.
Their resistance to heat is a big deal. They don’t break down in high temperatures and keep out water, UV light, and chemicals. But, they’re not as strong as some other glues and aren’t great for heavy-duty sticking. They also take a while to dry and might need the surfaces to be prepped to stick well.
Still, they’re really useful. They seal and gasket things in cars and protect electronics. They’re also used in building for sealing up gaps and sticking glass panels together.
Comparison of Hot Melt Adhesives
Hot melt adhesives are great for lots of jobs because they stick fast and work on many materials. They cool and set quickly, speeding up how fast things get made. They stick to plastics, metals, wood, and fabric well.
But, they’re not the strongest glues out there. They’re not the best choice for heavy or structural jobs. Also, they don’t hold up well against water and chemicals.
Still, they’re really useful. You see them a lot in packaging, making furniture, and in clothes for sticking things together. They’re also used in cars for putting together interior parts and organizing wires.
Comparison of UV Curing Adhesives
UV curing adhesives cure very fast under UV light, stick really well, and can handle heat and chemicals. They’re perfect for many projects.
Their quick cure time speeds up work. They create strong bonds on plastics, metals, glass, and ceramics.
But, you need UV light to make them work. This might not be doable for all projects. They might also need special gear to cure evenly. Plus, they’re not great if you need something flexible or tough against impacts.
Despite these points, they’re widely used. Electronics use them for putting parts together and sealing. They’re also big in medical devices for bonding and protecting components.
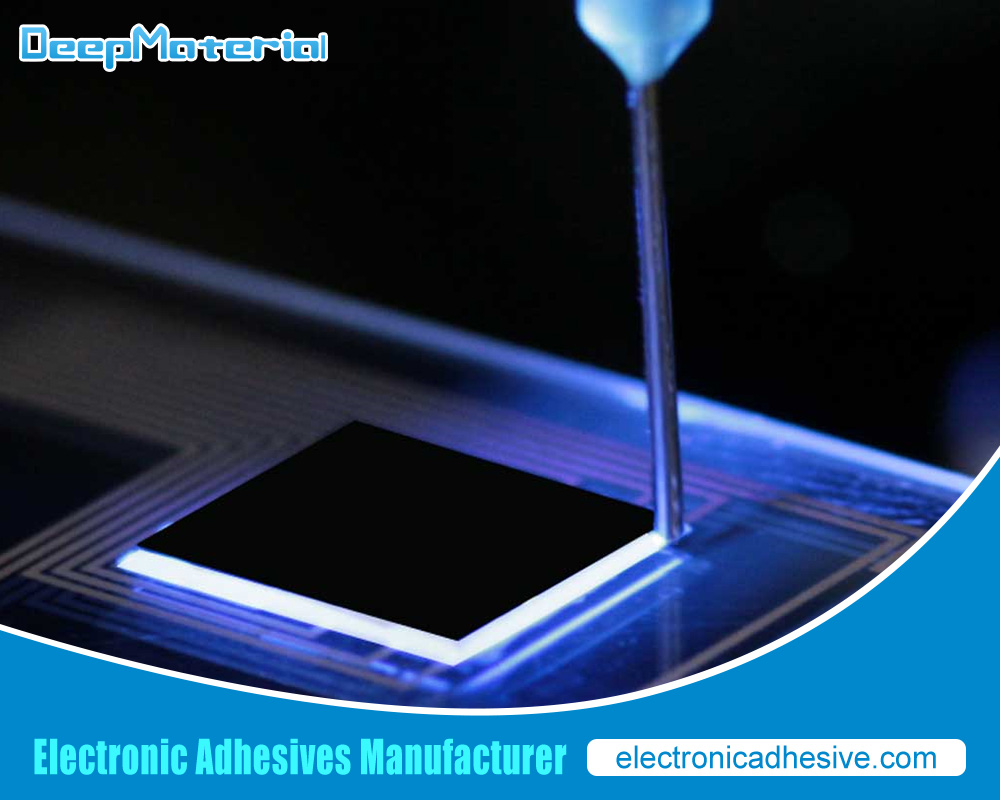
Conclusion and Recommendations for Industrial Bonding Adhesives
To wrap up, industrial adhesives are key for sticking different materials together across many industries. Epoxy adhesives are strong and resist chemicals, making them great for serious bonding. Acrylic adhesives are flexible and good for sticking different things together. Cyanoacrylate adhesives bond quickly and strongly, perfect for fast jobs.
Polyurethane adhesives are both strong and flexible, useful for many tasks. Silicone adhesives resist heat and moisture, ideal for sealing and bonding. Hot melt adhesives bond quickly and work on lots of materials, great for packaging and woodworking. UV curing adhesives cure fast and create strong bonds, suited for electronics and medical devices.
When picking an adhesive, think about what you’re sticking together, how strong it needs to be, the environment, how you’ll apply it, and safety. Talking to adhesive experts can help pick the best glue for your project. Choosing carefully helps get the best results and efficiency in your work.
For more about comparing differenttypes of industrial bonding adhesives, you can pay a visit to DeepMaterial at https://www.electronicadhesive.com/ for more info.