Choosing the Right Non Conductive Epoxy For Electronics
Choosing the Right Non Conductive Epoxy For Electronics
Non conductive epoxy is a type of adhesive that is specifically designed for use in electronics. It is used to insulate and protect electronic components from electrical currents and environmental factors. Choosing the right non conductive epoxy is crucial to ensure the proper functioning and longevity of electronic devices. In this article, we will explore the importance of choosing the right non conductive epoxy and discuss the factors to consider when making a selection.
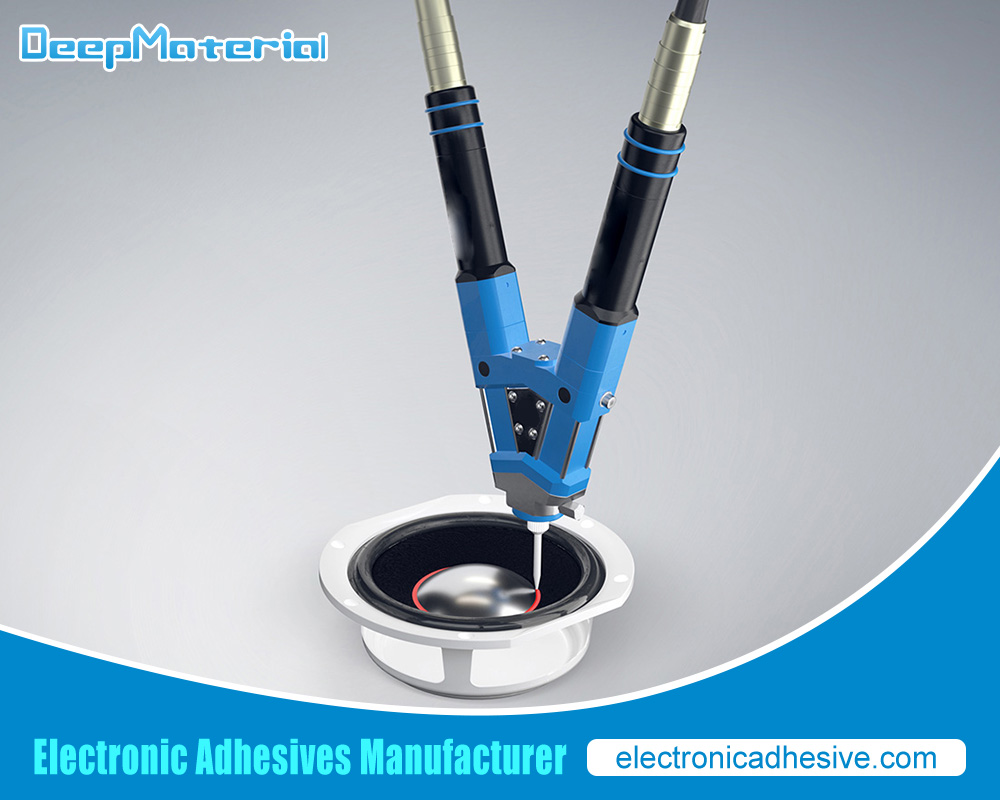
The Importance of Choosing the Right Non Conductive Epoxy
Choosing the right non conductive epoxy is essential for ensuring proper insulation and protection for electronic components. Electronic devices are often exposed to various environmental factors such as moisture, heat, and chemicals. Without the proper insulation, these factors can cause damage to the components and lead to failure of the device. Non conductive epoxy provides a barrier between the components and the environment, preventing any potential damage.
In addition to insulation, non conductive epoxy also plays a crucial role in preventing electrical failures. When electronic components are not properly insulated, there is a risk of electrical currents flowing through unintended paths, leading to short circuits or other malfunctions. By using non conductive epoxy, these unintended paths are blocked, ensuring that the electrical currents flow only through the intended paths.
Types of Non Conductive Epoxy and Their Properties
There are several types of non conductive epoxy available, each with its own unique properties. The most common types include silicone-based epoxy, acrylic-based epoxy, and polyurethane-based epoxy.
Silicone-based epoxy is known for its excellent temperature resistance and flexibility. It can withstand high temperatures without losing its adhesive properties and can also withstand extreme cold temperatures. Silicone-based epoxy is also highly resistant to moisture and chemicals, making it suitable for applications that require protection against these factors.
Acrylic-based epoxy is known for its fast curing time and high strength. It has good adhesion properties and can bond well with a variety of substrates. Acrylic-based epoxy is also resistant to chemicals and has good electrical insulation properties. However, it may not have the same level of temperature resistance as silicone-based epoxy.
Polyurethane-based epoxy is known for its excellent chemical resistance and durability. It can withstand exposure to a wide range of chemicals without degrading or losing its adhesive properties. Polyurethane-based epoxy also has good electrical insulation properties and can provide excellent protection against moisture. However, it may not have the same level of temperature resistance as silicone-based epoxy.
When choosing the right non conductive epoxy for your application, it is important to consider the specific properties of each type and how they align with your application requirements.
How to Determine the Right Viscosity for Your Application
Viscosity is an important factor to consider when choosing non conductive epoxy for electronics. The viscosity of the epoxy determines its flowability and thickness. It is important to choose the right viscosity for your application to ensure proper insulation and protection.
Viscosity is typically measured in centipoise (cP) or Pascal-seconds (Pa·s). The viscosity of the epoxy can be influenced by several factors, including temperature, filler content, and curing agents. Higher temperatures generally result in lower viscosity, while higher filler content and curing agents can increase viscosity.
To determine the right viscosity for your application, you need to consider the specific requirements of the project. If the epoxy is too thin, it may not provide adequate insulation and protection. On the other hand, if the epoxy is too thick, it may be difficult to apply and may not spread evenly. It is important to choose a viscosity that allows for easy application and provides sufficient coverage.
Temperature and Chemical Resistance
Temperature and chemical resistance are important factors to consider when choosing non conductive epoxy for electronics. Electronic devices are often exposed to various temperature fluctuations and chemicals, and the epoxy used should be able to withstand these conditions without degrading or losing its adhesive properties.
Temperature resistance refers to the ability of the epoxy to withstand high or low temperatures without degrading or losing its adhesive properties. Different types of epoxy have different temperature resistance capabilities. Silicone-based epoxy, for example, is known for its excellent temperature resistance and can withstand high temperatures without losing its adhesive properties. Acrylic-based and polyurethane-based epoxy may have lower temperature resistance capabilities.
Chemical resistance refers to the ability of the epoxy to resist exposure to various chemicals without degrading or losing its adhesive properties. Electronic devices are often exposed to chemicals such as solvents, oils, and cleaning agents. The epoxy used should be able to withstand exposure to these chemicals without deteriorating. Silicone-based epoxy is known for its excellent chemical resistance, while acrylic-based and polyurethane-based epoxy may have varying degrees of chemical resistance.
Curing Time and Shelf Life
Curing time and shelf life are important factors to consider when choosing non conductive epoxy for electronics. Curing time refers to the time it takes for the epoxy to fully harden and reach its maximum strength. Shelf life refers to the period of time during which the epoxy can be stored and used before it starts to degrade.
Curing time can vary depending on the type of epoxy and the specific curing agents used. Some epoxies may have a fast curing time, while others may take longer to fully cure. It is important to consider the specific requirements of your application and choose an epoxy with a curing time that aligns with those requirements.
Shelf life is also an important consideration, especially if you need to store the epoxy for an extended period of time before using it. The longevity of its shelf life can be impacted by various factors, such as temperature fluctuations, exposure to air, and the presence of moisture. It is important to choose an epoxy with a shelf life that allows for sufficient storage and use before it starts to degrade.
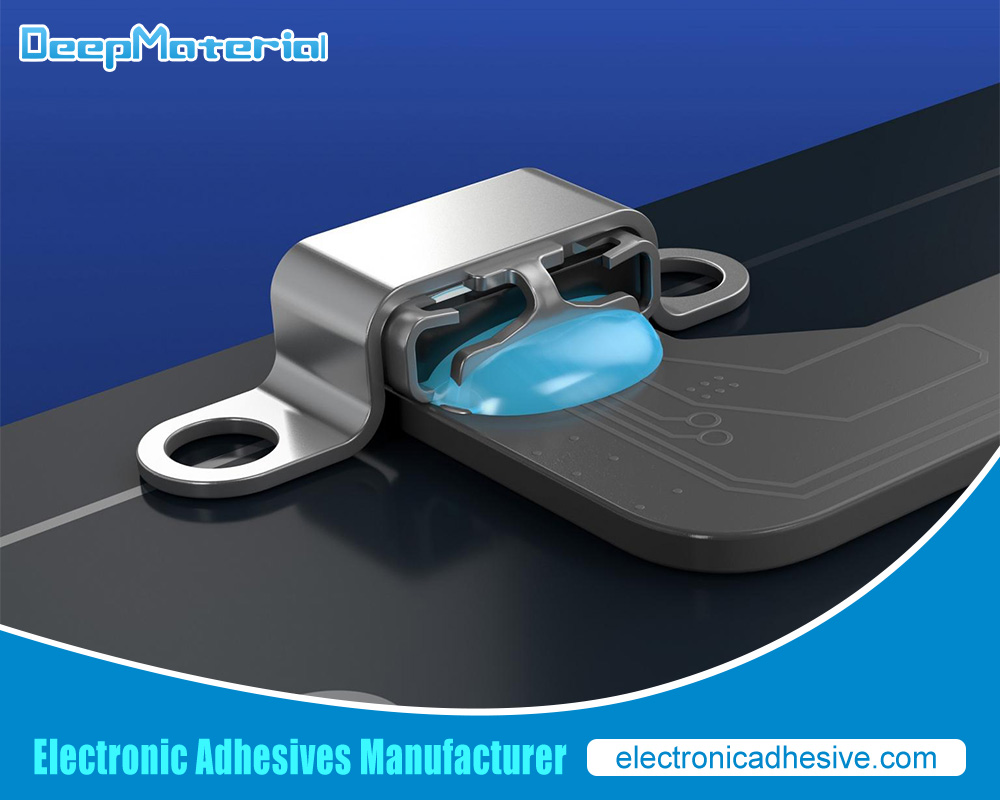
Conclusion: Choosing the Best Non Conductive Epoxy for Your Electronics Project
In conclusion, choosing the right non conductive epoxy is crucial for ensuring proper insulation and protection for electronic components. Factors to consider when choosing non conductive epoxy include application requirements, chemical and temperature resistance, curing time and shelf life, and viscosity. Different types of non conductive epoxy, such as silicone-based, acrylic-based, and polyurethane-based epoxy, have different properties and are suitable for different applications. It is important to consider the specific requirements of your project and choose an epoxy that aligns with those requirements.
For more about the Non Conductive Epoxy for Electronics, you can pay a visit to DeepMaterial at https://www.electronicadhesive.com/electrical-bonding-adhesive/ for more info.