Choosing The Best Adhesive Glue For Electronics
Choosing The Best Adhesive Glue For Electronics
Choosing the right adhesive for electronics is crucial for ensuring the proper functioning and longevity of electronic components. Adhesives play a critical role in bonding various materials together in electronic devices, such as circuit boards, sensors, and displays. The wrong adhesive can lead to damage, malfunction, or even failure of these components. Therefore, it is essential to understand the importance of selecting the right adhesive and consider various factors before making a decision.
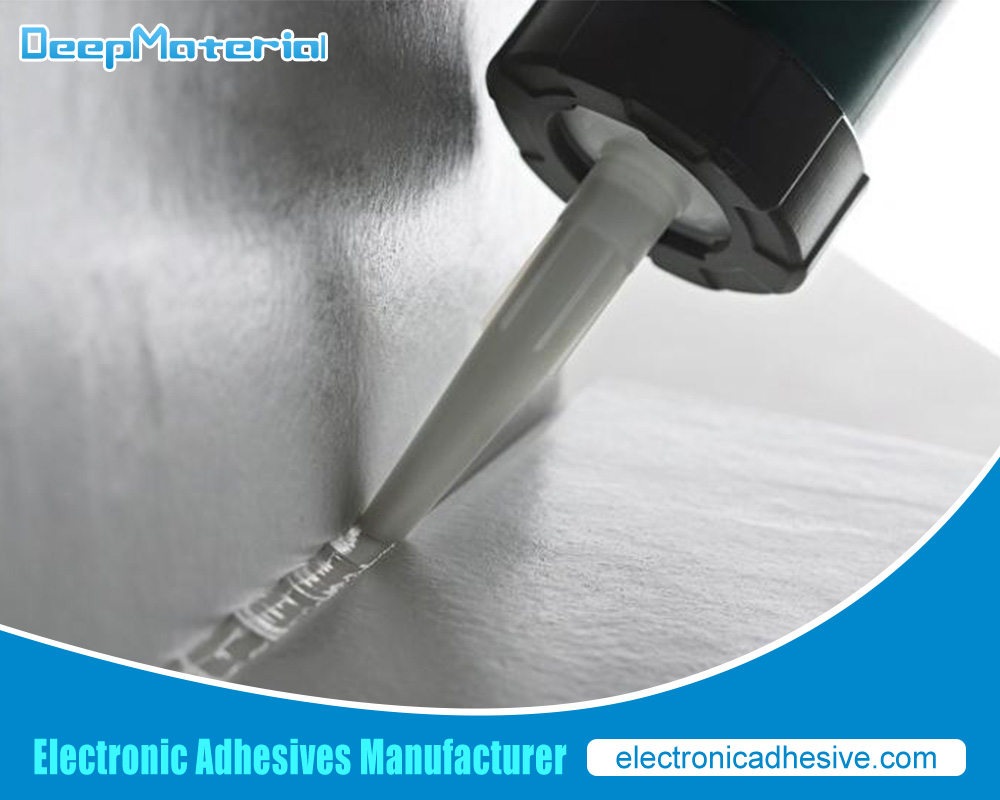
Types of adhesives commonly used in electronics
There are several types of adhesives commonly used in electronics, each with its own advantages and disadvantages. Epoxy adhesives are widely used due to their excellent bonding strength and resistance to temperature and chemicals. They are suitable for bonding various materials and provide long-term durability. However, epoxy adhesives can be brittle and may require careful handling during application.
Cyanoacrylate adhesives, also known as super glues, are popular for their fast-curing time and strong bonding strength. They are suitable for bonding small components and provide instant adhesion. However, cyanoacrylate adhesives may not be suitable for applications that require high temperature resistance or flexibility.
Silicone adhesives are known for their flexibility and resistance to moisture and temperature. They are commonly used in sealing and bonding applications where flexibility is required. However, silicone adhesives may not provide the same level of bonding strength as epoxy or cyanoacrylate adhesives.
Factors to consider when choosing an adhesive for electronics
When choosing an adhesive for electronics, several factors need to be considered:
Adhesive strength and durability for electronic components
These are crucial factors to consider when choosing an adhesive for electronic components. The adhesive should provide sufficient bonding strength to withstand the stresses and strains experienced by electronic components during operation. This is especially important for components that are subjected to vibrations, shocks, or thermal cycling.
In some cases, a stronger adhesive may be necessary to ensure the longevity of electronic components. For example, in high-stress applications such as automotive electronics or aerospace systems, where components are exposed to extreme conditions, a stronger adhesive with higher bonding strength may be required. It is important to consider the specific requirements of the application and choose an adhesive that can provide the necessary strength and durability.
Temperature resistance and compatibility with electronic materials
Temperature resistance and compatibility with electronic materials are critical factors to consider when choosing an adhesive for electronics. Electronic devices can be exposed to a wide range of temperatures, from extreme cold to high heat. It is important to choose an adhesive that can withstand these temperature fluctuations without losing its bonding strength or causing damage to the electronic components.
Additionally, the adhesive should be compatible with the materials used in electronic components. Different materials have different coefficients of thermal expansion, which can cause stress on the adhesive bond during temperature changes. Choosing an adhesive that is compatible with the materials can help minimize the risk of delamination or failure of the bond.
Adhesive application methods for electronics
There are several common application methods for adhesives in electronics, each with its own advantages and disadvantages. The choice of application method depends on the specific requirements of the application and the type of adhesive being used.
Dispensing is a common application method for adhesives in electronics. It involves applying the adhesive directly onto the surface of the component or substrate using a syringe or dispenser. Dispensing allows for precise control of the adhesive amount and location, making it suitable for applications that require accuracy and consistency. However, it can be time-consuming and may require additional equipment for proper dispensing.
Spraying is another application method that is commonly used for adhesives in electronics. It involves spraying the adhesive onto the surface of the component or substrate using a spray gun or nozzle. Spraying allows for quick and uniform coverage of large areas, making it suitable for high-volume production. However, it may not be suitable for applications that require precise control of the adhesive amount or location.
Safety considerations when working with adhesives for electronics
When working with adhesives for electronics, it is important to consider safety precautions to protect yourself and others from potential hazards. Adhesives can contain hazardous chemicals that may pose health risks if not handled properly.
Some adhesives can be toxic if inhaled, ingested, or absorbed through the skin. If you’re going work with that adhesive, it’s important to take precautions. Make sure you’re in an area where air circulates decently and don the proper protective gear like gloves and goggles — these items foster a safeguard from getting blasted by fumes or contact with your skin.
Flammability is another safety consideration when working with adhesives. Some adhesives are highly flammable and can pose a fire hazard if not handled properly. It is important to store adhesives in a cool, dry place away from sources of ignition and follow proper storage and handling procedures.
Cost-effectiveness of different adhesive options for electronics
The cost of the adhesive is an important factor to consider when choosing an adhesive for electronics. While it may be tempting to choose a cheaper adhesive to save costs, it is important to consider the long-term costs associated with potential failures or rework due to using an inadequate adhesive.
A more expensive adhesive may provide better performance and durability, which can result in fewer failures and rework. This can ultimately save costs in terms of time, labor, and materials. It is important to weigh the upfront cost of the adhesive against the potential costs of failures or rework to determine the most cost-effective option.
Additionally, it is important to consider the overall cost of the adhesive, including any additional equipment or tools required for application. Some adhesives may require specialized equipment or tools, which can add to the overall cost. It is important to factor in these additional costs when comparing different adhesive options.
Best practices for storing and handling electronic adhesives
Proper storage and handling of electronic adhesives are crucial for ensuring their effectiveness and longevity. Adhesives should be stored in a cool, dry place away from direct sunlight and sources of heat or ignition. Exposure to extreme temperatures or moisture can degrade the adhesive and affect its performance.
It is important to keep adhesives tightly sealed when not in use to prevent moisture or air from entering the container. This can help prolong the shelf life of the adhesive and maintain its effectiveness.
Safety first! When slathering on the glue, keep these few tips in mind to avoid any troubles. Put on those gloves and eye coverings for extra protection from getting stuck – sorry, I digress – and open a window or two to let out any fumes you don’t want wafting through the air. Get acquainted with each adhesive by reading up on manufacturer instructions as well as their safety information; they may have some handy tricks or info that is unique to that specific bottle of goop.
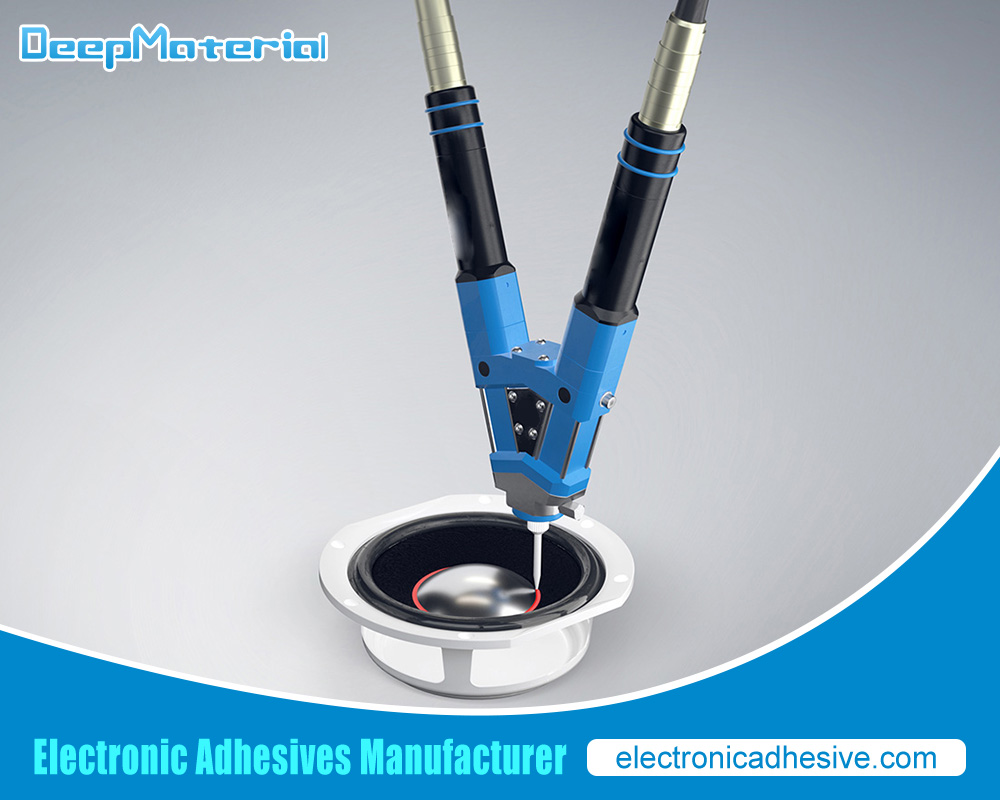
Final thoughts
Choosing the right adhesive for electronics is crucial for ensuring the proper functioning and longevity of electronic components. The wrong adhesive can lead to damage, malfunction, or even failure of these components. Therefore, it is important to understand the importance of selecting the right adhesive and consider various factors, such as temperature resistance, compatibility with electronic materials, adhesive strength and durability, application method, safety considerations, and cost-effectiveness.
For more about choosing the Best Adhesive Glue For Electronics, you can pay a visit to DeepMaterial at https://www.electronicadhesive.com/about/ for more info.